ComNav 1001 User manual

Installation & Operation Manual
ComNav 1001 Autopilot
COMPLIES WITH
CE REGULATIONS
P/N 29010007


WARRANTY NOTICE
Prior to the installation and/or operation of the Equipment, ensure
that you read, understand and accept the conditions of the warranties
as detailed on the following pages.
OPERATORS WARNING
This Autopilot will automatically steer your vessel however, it
is only an aid to navigation. Its performance can be affected
by many factors including equipment failure, environmental
conditions and improper handling or use. This system does
not reduce your responsibility for the control of the vessel
when underway. You must always be in a position to monitor
the course, supervise the Autopilot, and resume manual
control if the need to do so arises.
Whenever underway, your vessel must be under the control of
a qualified and alert person.

1
TABLE OF CONTENTS
1001 AUTOPILOT SYSTEM DRAWING _________________________________________ 3
BASIC OPERATION __________________________________________________________ 3
AUTOPILOT _____________________________________________________________________ 4
REMOTE CONTROL _____________________________________________________________ 6
INTRODUCTION ____________________________________________________________ 7
SPECIFICATIONS ___________________________________________________________ 8
1001 AUTOPILOT INTERCONNECTION DIAGRAM ______________________________ 9
OPTIONAL DRIVE SYSTEMS ________________________________________________ 11
INSTALLATION INSTRUCTIONS_____________________________________________ 12
AUTOPILOT____________________________________________________________________ 12
COMPASS______________________________________________________________________ 13
DISTRIBUTION BOX ____________________________________________________________ 18
RUDDER FOLLOWER___________________________________________________________ 21
NAVIGATION INTERFACE __________________________________________________ 24
CROSS TRACK ERROR RESPONSE ______________________________________________ 26
CHECKSUM EVALUATION______________________________________________________ 27
DOCKSIDE SET-UP _________________________________________________________ 28
SETTING OF RUDDER TRAVEL LIMITS __________________________________________ 28
ADJUST RUDDER ANGLE INDICATOR (if installed) ________________________________ 29
CONFIGURING THE COMPASS __________________________________________________ 30
NAVIGATION EQUIPMENT INTERFACING _______________________________________ 30
SEA TRIALS________________________________________________________________ 31
CONTROLS ________________________________________________________________ 36
MASTER SELECT SWITCH ______________________________________________________ 36
MEMBRANE KEYPAD___________________________________________________________ 37
SPECIAL TURNS____________________________________________________________ 40
EMERGENCY TURN ____________________________________________________________ 40
CONTINUOUS TURN____________________________________________________________ 40
U TURN ________________________________________________________________________ 41
OPERATION _______________________________________________________________ 42
STANDBY ______________________________________________________________________ 42
POWER STEER _________________________________________________________________ 43

2
PILOT _________________________________________________________________________ 44
NAV ___________________________________________________________________________ 47
REMOTE CONTROLS ___________________________________________________________ 48
REMOTE CONTROLS _______________________________________________________ 50
COMNAV 101 REMOTE CONTROL _______________________________________________ 50
COMNAV 201 REMOTE CONTROL _______________________________________________ 53
COMNAV 211 REMOTE CONTROL _______________________________________________ 54
ERROR CHECKING _________________________________________________________ 55
PROBLEM SOLVING ____________________________________________________________ 59
CE COMPLIANCE __________________________________________________________ 62

3
1001 AUTOPILOT SYSTEM DRAWING

4
BASIC OPERATION
AUTOPILOT
1. TO INITIALIZE THE AUTOPILOT\
STANDBY MODE
zTurn the master select switch to
the STANDBY position. The display will
show the vessel's current compass
heading. If the heading displayed by the
autopilot does not agree with the
compass, press the ADJUST key twice to
display the current heading offset, and
then use the up or down ARROW key to
adjust the offset by the amount of the
error.
zTo turn on the speed sensitivity
that switches between FAST and SLOW
when in PILOT or NAV, with the Pilot in
Standby press the ADJUST key until
'SP: 0' is displayed. Press the up
ARROW key until the desired speed is
displayed.
zTo turn off the speed sensitivity,
press the down ARROW key until the
display reads 'SP: 0'.
zIf the display is too bright or too
dim when viewed in full darkness, press
the ADJUST key until 'Lt ' is displayed,
and then use the up or down ARROW
key to adjust the minimum brightness
level between 0-9.
zTo select a Special Turn as
described in (4) below, press the TURN
key followed by either the red or green
ARROW key.
zTo initiate a Full Reset, press and
hold both the up and down ARROW keys
for one second. This will reset all autopilot
parameters back to factory settings and
the Pilot will go into Reset mode. A
dockside set-up will be required after
every Full Reset.
2. TO POWER STEER THE VESSEL\
POWER STEER MODE
zTo turn the rudder to port and to
starboard, turn the master select switch to
the POWER STEER position. While
either the red or green ARROW key is
pressed, the display will show the
vessel’s rudder angle and will show the
vessel's current compass heading at all
other times.
zTo display the vessel's rudder
angle, press the TURN key once. To
return compass information to the display,
press the TURN key again.
zTo zero the digital rudder angle
display, turn the rudder to dead ahead,
press the ADJUST key until the flashing
rudder angle display appears and press
the up or down ARROW key until the
rudder angle display shows ' :00'.
3. TO BEGIN AUTOPILOT CONTROL
OF THE VESSEL:
zTo have the vessel continue on its
present heading under autopilot control,
turn the master select switch to the
PILOT position.
zTo select either the 'FASt' (High
Speed) mode or the 'Slow' (Low Speed)
mode, press the ADJUST key once
followed by the up or down ARROW key.
This will be done automatically if the
speed sensitive switching has been
turned on in (1) above.
zTo adjust the rudder gain setting
for the High or Low speed mode, press
the ADJUST key until 'rud' is displayed,
followed by the up or down ARROW
keys. Similarly adjust the counter rudder
('ctr') and yaw ('YAW') settings for best
steering.

5
4. TO CHANGE THE VESSEL'S
COURSE:
zTo obtain the desired course,
leave the master select switch in the
PILOT position. Estimate the number of
degrees of course change required.
zUntil the display shows the desired
course, alter the course in one degree
steps by pressing and releasing either the
red or green ARROW key.
--- Or ---
Alter course by ten degrees per second
by pressing and holding either the red or
green ARROW key.
zTo select a special turn (U-turn,
Emergency Turn, or Continuous Turn),
with the Pilot in Standby mode, press the
Turn key once followed by the Green key
until the desired Turn is displayed.
zTo adjust the rate at which the
vessel will turn to the new course, press
the ADJUST key until 'trn' is displayed
and then press the up or down ARROW
key
5. TO DODGE THE VESSEL OFF
COURSE\PILOT MODE
zTo avoid obstacles in the water,
press either the red or green DODGE key
for a panic turn in the desired direction.
zTo keep the vessel off course,
after it has turned far enough to clear the
obstacle, press and hold both DODGE
keys.
zTo return to the programmed
course at the rate set by the turn rate
control. Release the DODGE key
6. TO INTERFACE WITH A
NAVIGATION COMPUTER\NAV MODE
zStart navigating towards a
selected route or waypoint, using a
Navigation Computer which has an
NMEA 0183 output.
zTurn the autopilot master select
switch to the NAV position. The autopilot
will set its own course using information
sent to it by the Navigation Computer.
zTo select the response to cross
track error (normal or reversed), press the
TURN key and then the green ARROW
key.
zThe DODGE keys operate as
described in (5) above, except that the
vessel will return to the original track to
the waypoint, rather than the original
course, when the DODGE keys are
released.
For more complete operating instructions,
refer to the CONTROLS and
OPERATION sections.

6
REMOTE CONTROL
The autopilot master control unit must be on to use any remote control. The
vessel’s compass heading is shown at all times on the display of the unit that is
NOT in control. As a further reminder, the function indicator (see Figure 8) will be
flashing on the display of the unit that is NOT in control.
1. TO USE THE COMNAV 101
REMOTE CONTROL:
zTo take control at the Remote,
press both its pushbuttons for one
second. The command point on all
displays will move to the REMOTE
position. This control operates identically
to the autopilot, except that there is a
toggle switch, used together with one of
the pushbuttons, to dodge or to initiate a
special turn.
zTo recall the vessels last course,
hold the toggle switch in the DODGE
position while turning the master select
switch from POWER STEER to PILOT.
The course that the autopilot was steering
when it was last in PILOT will be recalled.
(If the autopilot has not been in PILOT
since it was turned on, the course the
vessel was on at the moment the
autopilot was turned on will be recalled.)
2. TO USE THE COMNAV 1101
SECOND STATION:
zTo take control at the Second
Station, press both DODGE keys for one
second. The Command Point on all
displays will move to the REMOTE
position.
zThe 1101 second station operates
identically to the autopilot, except that the
OFF/FUNCTION will not operate. The
autopilot must be turned ON and OFF
from the autopilot front panel.
3. TO TAKE CONTROL AT THE
AUTOPILOT FRONT PANEL:
zTo take control at the autopilot
front panel, press both the red and green
ARROW keys on the autopilot front panel
for one second. The command point on
all displays will move back to the
MASTER position.
For more complete operating
instructions refer to the REMOTE
CONTROLS section.
WARNING
If the unit that will take control is
not in the same mode as the unit
currently in control, a sudden
course change could occur.

7
INTRODUCTION
This autopilot is a microprocessor
operated PID (Proportional-Integral-
Differential) controller, working from either
a high quality, externally gimballed
magnetic ships steering compass fitted
with a fluxgate sensor or a direct earth’s
field sensing fluxgate compass.
Heading information is compared against
the programmed heading, and the
desired rudder position determined. The
desired rudder position is compared
against the actual rudder position
transmitted by the rudder follower. If they
are not the same, either the Port or
Starboard output line is activated.
The Port and Starboard output lines are
active low (i.e. switch to ground), and can
drive a load of up to 3 amps. They are
designed to operate solenoid valves in a
hydraulic steering system.
A speed control signal is also available for
use with variable speed rudder drives.
The outputs, either by themselves or with
an optional solid state drive box, can be
adapted to operate a wide variety of
power steering systems.
If the autopilot is installed as a retrofit, it is
usually possible to use the existing power
steering installation. The autopilot can
operate from either 12 or 24 VDC power
systems.
The autopilot has our unique Ghost
Rudder feature. In case of a rudder
follower failure the autopilot will
automatically switch to Ghost Rudder,
which calculates the rudder position
instead of measuring it, and continue to
operate at a reduced performance level.
The autopilot is equipped to interface with
a GPS, Loran C, or any other navigation
computer which outputs one of the NMEA
0183 formats at 4800 Baud.
The autopilot is designed to accept one
remote control.
By adding the optional REMOTE
EXPANDER, the autopilot can support
any combination of up to four remote
controls or second stations.
Figure 1 shows the possible
interconnections between the autopilot,
it’s accessories, and external equipment.

8
SPECIFICATIONS
Operating Voltage: 10 VDC TO 30 VDC
For Use With 12 or 24 VDC Battery Systems only
Operating Current: 0.18 Amps (minimum)
Operating Temperature Range: -15 To +60 °C
Heading Resolution: 0.25 Degree
Heading Accuracy: + 2.0 Degrees
Course Set Resolution: 1.0 Degree
PORT/STBD Output Type: Open Collector, 3 Amps Max
Speed Control Output: 2.50 VDC for No Movement
5.00 VDC for Maximum Speed Port
0.00 VDC for Maximum Speed Starboard
10K ohm Source Impedance
Navigation Input: NMEA 0183 (4800 BAUD): RMA, RMB, RMC, APB,
APA, XTE, BOD, WBD, HSC, VBW, VHW, VTG
Rudder Angle Indicator Output: + 500 Micro-Amp Full Scale Deflection
Size
Wide: 8.25 inches (210mm)
High: 3.75 inches (95mm)
Deep: 2.25 inches (57mm)
3.0inches(76mm) required behind unit for cabling
Weight: 4.0 lbs (1.6 kg)

9
1001 AUTOPILOT INTERCONNECTION DIAGRAM

10
DRIVE SYSTEM OPTOINS

11
OPTIONAL DRIVE SYSTEMS
For all commercial and pleasure
vessels over 50 ft where heavy usage
will be the norm (hydraulic steering):
- CPUFC Flow Control Uniblock
12, 24 or 32 VDC
or
- CPUTS & CT5 - Two Speed Uniblock
12, 24 or 32 VDC
And
- Belt Driven Pump
Or
- Direct Driven Pump
For vessels with hydraulic cylinder
displacements from 7 to 18 cu.in.): - 18CI Reversing Motor Pump &
CT2-20A Drive Box (12 or 24 VDC)
For vessels with hydraulic cylinder
displacements from 15 to 30 cu.in.): - 30CI Reversing Motor Pump &
CT2-20A Drive Box (12 or 24 VDC)
For vessels with hydraulic cylinder
displacements from 30 to 60 cu.in.): - 60CI Reversing Motor Pump &
CT2-20A Drive Box (12 or 24 VDC)
For pleasure vessels with mechanical
steering up to 70 feet: - Hydraulic Linear Actuator &
CT2-20A Drive Box (12 or 24 VDC)
To retrofit to vessels with an existing
autopilot drive system which uses a 2
wire (permanent magnet), 4 wire (shunt
field), or 5 wire (compound) reversing
electric motor:
- CT2-20A or CT2-40A Single Speed
Reversing Electric Motor Drive
To retrofit to vessels with an autopilot
drive system using a 3 wire (split field)
reversing electric motor:
- CT3 Split Field Reversing Electric Motor
Drive Box
To retrofit to vessels with an autopilot
drive system using a 12 or 24 VDC
solenoid operated 4-way valve:
- Nothing Extra Required (consult factory
on 32 VDC systems)
To retrofit to vessels with an autopilot
drive system using a 110 or 220 VAC
solenoid operated 4-way valve:
- CT4 AC Solenoid Drive Box
(100 to 240 VAC)
To retrofit vessels with an autopilot
drive system using proportional valve: - CT6 or Z-Drive Isolation Amplifier
(consult with factory)
Regardless of the type of drive unit being used, the hardover to hardover time must
be checked. For peak performance this time must be 10 - 15 seconds.

12
INSTALLATION INSTRUCTIONS
AUTOPILOT
The autopilot is normally mounted in the
vessel's wheelhouse. It can also be
mounted in a more exposed location,
such as the flying bridge of a sports
fisherman, (if it is flush mounted and the
rear of the autopilot is protected from
spray).
Select either the bag containing the flush
mount bezel and cutting template, or the
bag containing the mounting bracket and
knobs. BRACKET MOUNT
zPosition the mounting bracket so
that the front of the autopilot will be easily
visible. There must be a minimum of
three inches (76 millimetres) of clearance
behind the autopilot to allow for cabling.
zScrew the knobs part way into the
threaded holes on both sides of the
autopilot rear cover. Insert the autopilot
into the mounting bracket, making sure
that the rubber spacer is between the
cover and the bracket, and the plastic one
is between the bracket and the head of
the knob. Tilt the autopilot to the desired
angle, and tighten the knobs securely.
FLUSH MOUNT
zEnsure that there is at least five
inches (127 millimetres) of depth in the
mounting cavity to allow clearance behind
the autopilot for cabling.
zIf the autopilot is being flush
mounted in an exposed location, care
should be taken to ensure that the rear of
the autopilot is not exposed to salt spray
or other moisture. The flush mount bezel
reduces the effectiveness of the sealing
gasket on the rear of the autopilot.
zPosition the cutting template on
the panel where the autopilot is to be
mounted, and mark the opening onto the
panel. Cut the opening in the panel
around the outside of the markings. To
improve the seal on the rear of the
autopilot, an extra gasket for the rear
cover has been supplied.
zUnscrew the two large screws
from the rear of the autopilot and remove
the rear cover. Peel the protective
backing off the extra gasket, and carefully
position it on top of the one already in the
rear cover.
zApply the protective gasket to
the back of the flush mount bezel.
zSlide the flush mount bezel over
the autopilot chassis, and replace the rear
cover and screws. Tighten the screws
only enough to slightly compress the
gaskets. Slide the autopilot into the hole
in the panel, and mark the positions of the
four mounting holes. Use the supplied
screws to mount the autopilot.
zIf you have access to the rear of
the mounting panel, the autopilot can be
easily removed from the panel by simply
unscrewing the two large screws in the
rear and sliding the autopilot out, without
having to remove the bezel from the
panel.
zThe autopilot is supplied with a
cover over the remote control receptacle
on the back. If the receptacle is unused,
the cover should be left on. The
receptacle is weather-resistant only with
the cover on or when a plug is connected
to it. Damage caused by exposing a
receptacle to the elements will NOT be
repaired under warranty.

13
COMPASS
FOR COMNAV FLUX-GATE COMPASS
zThe compass MUST be mounted
as close as practical to the vessels centre
of pitch and roll. This is typically low in the
vessel, at about the waterline, and slightly
aft of the centre of the vessel.
zYou must keep the compass at
least three feet away from engines,
electric motors, and other magnetic
objects. If this is not possible, their effects
may be compensated for as described in
the SEA TRIALS section of this manual.
zTo reduce or eliminate the effect of
the vessels vertical field, a HEELING
ADJUST control is provided on the
ComNav Fluxgate Compass, (although
the sensitivity to the earth’s vertical
magnetic field remains.)
zBecause of the sensitivity of the
fluxgate compass to the earth's vertical
magnetic fields, it is NOT recommended
for use at latitudes higher than 50
degrees (North or South).
zUse the HEELING ADJUST
control on the compass to eliminate the
effect of the vessel's vertical magnetic
field as described in the SEA TRIALS
section of this manual. The HEELING
ADJUST control is turned OFF when it is
in the centre of its travel.
zPlug the end of the cable into the
compass receptacle on the rear of the
autopilot. If the length of cable supplied
with the compass is not adequate, obtain
an extra plug-in length from your dealer.
Cutting and splicing the compass cable is
NOT recommended.
FOR OTHER FLUXGATE COMPASSES
zThe autopilot can be used with a
Fluxgate Compass which outputs DC
Sine and Cosine signals of up to +/- 3
volts amplitude about a 0 to 6 VDC
reference.
zIf the compass does not have a
HEELING ADJUST control (i.e. other
makes of fluxgate compasses), it should
NOT be used on steel vessels either.
zThe interface has been tested with
Fluxgate Compasses manufactured by
KVH, Brookes and Gatehouse, and VDO.
Some of these compasses have to be
specially ordered in order to have the
required DC Sine and Cosine outputs.
zThe autopilot has been supplied
with a 10 ft cable which is plugged into
the Compass receptacle on the rear of
the autopilot. The other end of the cable
is terminated in flying leads. See 0 for
colour & function of each lead.
z+12 Volts will appear on the wire
connected to Plug Pin 7 when the
autopilot is turned on. Up to 100 milliamps
can be supplied by this wire to power the
fluxgate compass.
zIf the compass is separately
powered, the tinned ends should be cut
off of the wires connected to Plug Pins 7
& 4. The wires should then be taped back
against the cable to prevent accidentally
shorting out the +12V power supply inside
the autopilot.
Any other unused wires should also have
their tinned leads cut off and be taped
back against the cable.

14
CONNECTION FOR NON-1001 FLUXGATE COMPASSES
PLUG PIN
NUMBERS 1001
FLUXGATE COMNAV
FUNCTION NON-COMNAV
CONNECTIONS
1 BLUE COSINE COSINE *
2 RED DRIVE P1 N/C
3 BLACK DRIVE P2 N/C
4 SHIELD GROUND GROUND
5 WHITE REFERENCE REFERENCE
6 YELLOW SINE SINE *
7 GREEN +12V +12V
* If the reading is reversed, swap these two wires.
zIn testing, the Brookes and
Gatehouse Halcyon 3 compass proved to
have a 'floating' reference. The reference
from the autopilot is also 'floating'. In
order for the interface to work, one of the
references must be fixed to a voltage.
The reference is fixed to +2.5 Volts inside
the autopilot by selecting Compass Type
3 (CPS.3) during the Dockside Set-up.
Compass Type 2 (CPS.2) should be
selected for all other fluxgate compasses.
zIf the reading on the Digital Display
of the autopilot increases when the
heading of the vessel is decreasing,
reverse the Sine and Cosine leads.
zIf the reading on the autopilot
display does not agree with the vessel's
actual heading, place the Master Select
Switch on the autopilot in the STANDBY
position and press the ADJUST key twice
to display the compass offset. Then press
either the up or down ARROW key to
adjust the offset by the amount of the
error.
zIf the compass is self-
compensating, do not run the autopilot
compensation routine during Dockside
Set-up (press either the up or down
ARROW key when 'CAdJ' is shown on
the display).
zIf the compass is not self-
compensating, run the autopilot
compensation routine to correct the
compass during Dockside Set-up (press
the ADJUST key when 'CAdJ' is shown
on the display).
MAGNETIC COMPASS
zThe advantage of using a
magnetic compass with a fluxgate sensor
is that the autopilot is sensing the position
of the magnets on the compass card
rather than sensing the earth's magnetic
field directly.
zAs the card of the compass has
physical inertia, it does not react
immediately to the changes in the
magnetic field it is immersed in, but only
to those changes which persist long
enough to overcome the resistance of the
compass card to movement.
This means that the compass is a more
stable heading reference than a fluxgate
compass. The magnetic compass will
largely ignore changes in the magnetic
field in the plane of the compass card
caused by vessel motion that the fluxgate
compass will react to.

15
This is particularly important in high
latitudes, (such as Alaska, Labrador or
the North Sea), where the horizontal
component of the earth's magnetic field
(which is the portion the compass is trying
to detect) is very small relative to the
magnetic field of the vessel.
zThe disadvantage of the magnetic
compass is that in very rough weather
with the vessel going to windward, it is
possible for the vessel motion to upset or
'tumble' the compass card, disabling the
autopilot.
zBecause of the relative insensitivity
of the magnetic compass to both the
earth's and the vessel's vertical magnetic
fields, (due to its inertia), it IS
recommended for use at latitudes higher
than 50 degrees (North or South), AND
for use on steel vessels when the optional
quadrantal spheres are included.
zLocate and mount the compass in
a position which minimizes magnetic
interference. It should be at least three
feet away from such equipment as
radios, radars, depth sounders, and
engine instruments.
zThe compass can be used as a
steering compass if desired. If the amount
of cable supplied is too short to reach the
rear of the autopilot, obtain an extra plug-
in length of cable from your dealer.
Cutting and splicing the compass
cable is NOT recommended.
zTo reduce the possibility of the
card 'tumbling' in rough weather, mount
the compass as close as practical to the
centre of pitch. Mounting the compass
far forward under a bunk or similar
location is a poor choice for rough
weather performance.

16
IMPORTANT
It is important to remember that the compass is a vital part of the autopilot system. Locating it properly,
particularly on steel hulled vessels, is essential to ensure proper operation of the autopilot. We
recommend that the services of a qualified compass adjuster be used to select the best installation
location and to compensate the compass properly for deviation, including that caused by heeling error.
Care must be taken not to place compensating magnets too close to the compass, as this will cause
the Fluxgate Sensor, mounted underneath the compass, to read incorrectly. To correct compass
deviation on steel vessels, or on other vessels with magnetic compensating problems due to
interference from adjacent iron masses such as an engine block or winches, the use of a pair of 3-1/4
inch (83 millimetre) Compensating Quadrantal Spheres is recommended.
Figure 4 -Test Points
MOUNTING THE SENSOR TO NON-
STANDARD COMPASSES
The fluxgate sensor supplied with the
autopilot can be mounted to a wide
variety of "externally gimballed"
compasses. The sensor should not be
mounted to "internally gimballed"
compasses (where the compass card is
gimballed and the bowl of the compass is
not), because the compass card does not
remain parallel to the sensor when the
vessel rolls or pitches, resulting in large
errors between the compass and
autopilot.
Mounting the sensor above the compass
reduces the possibility of compensating
magnets interfering with the operation of
the sensor, but also reduces the visibility
of the compass if it is to be used as a
steering compass.
Remove the rear cover from the autopilot.
Fasten a pair of voltmeter probes
between the SIN and +2.5V testpoints on
the Processor Board (see figure 4).
Turn the master select switch on the
autopilot to the STANDBY position. Hold
the sensor either above or below the
compass, and rotate it until a maximum
level is observed on the voltmeter.

17
Move the sensor towards or away from
the compass until a new maximum level
is observed. This is the optimum distance
from the compass to mount the sensor.
Any closer and the sensor may interfere
with the operation of the compass.
The accuracy of the sensor, and its
sensitivity to external fields, will slowly
weaken as it is moved further from the
compass. If the reading on the autopilot
display decreases when the heading on
the compass is increasing, turn the
sensor over. Rotate the sensor until the
heading on the display of the autopilot
matches the reading on the compass,
and tighten the mounting screw.
Rotate the compass through 360
degrees, comparing readings every 20
degrees. The readings should agree
within +/- 2 degrees (4 degrees total
error) if the compass is compatible with
the sensor.
As a further test, tilt the bowl of the
compass so the card tilts relative to the
sensor. The heading on the display of the
autopilot should not change more than
two degrees, with the compass still
indicating the same heading.
If the heading changes more than two
degrees, the magnets on the compass
card are not powerful enough, and the
compass is not compatible with the
sensor.
If the accuracy of the compass and
sensor combination cannot be made at
least +/- 2 degrees, then the compass is
not compatible with the autopilot sensor.
Your dealer can supply a compass
specifically designed for the ComNav
1001 autopilot.
Table of contents
Other ComNav Autopilot System manuals
Popular Autopilot System manuals by other brands
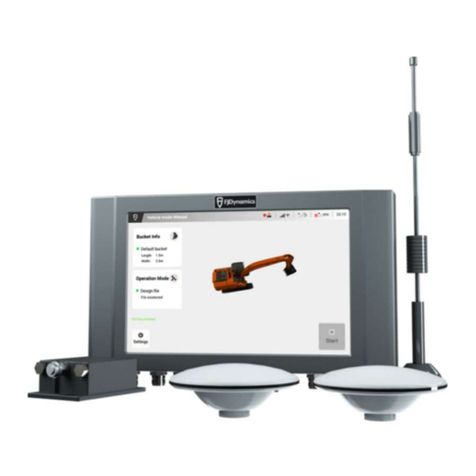
FJDynamics
FJDynamics FJD 3D Hardware installation manual
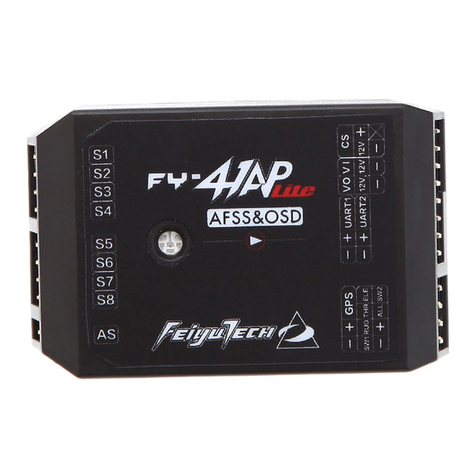
FeiYu Tech
FeiYu Tech FY-41AP Lite Installation & operation manual

MyFlyDream
MyFlyDream Crosshair manual
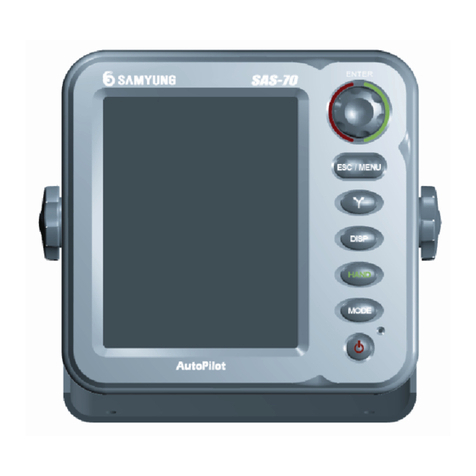
Samyung ENC
Samyung ENC SAS-70 instruction manual
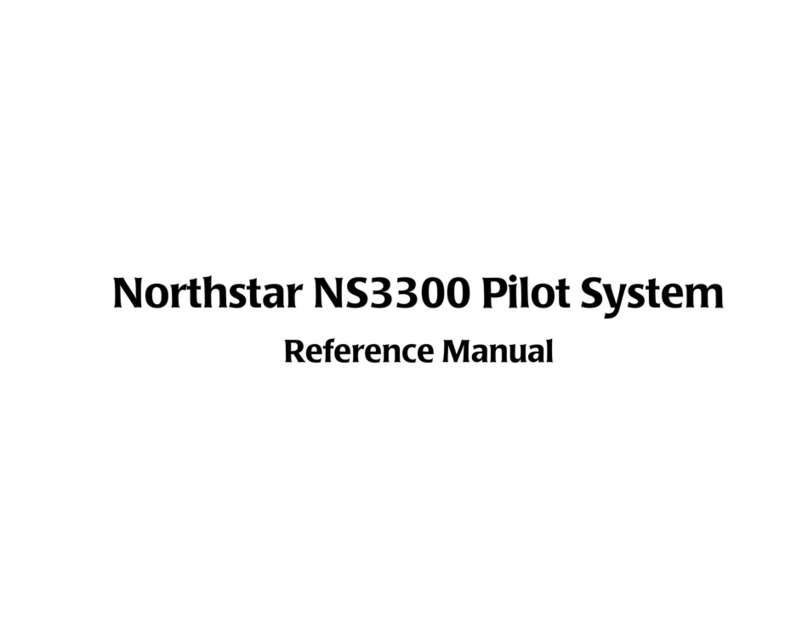
NorthStar
NorthStar Pilot System NS3300 Reference manual
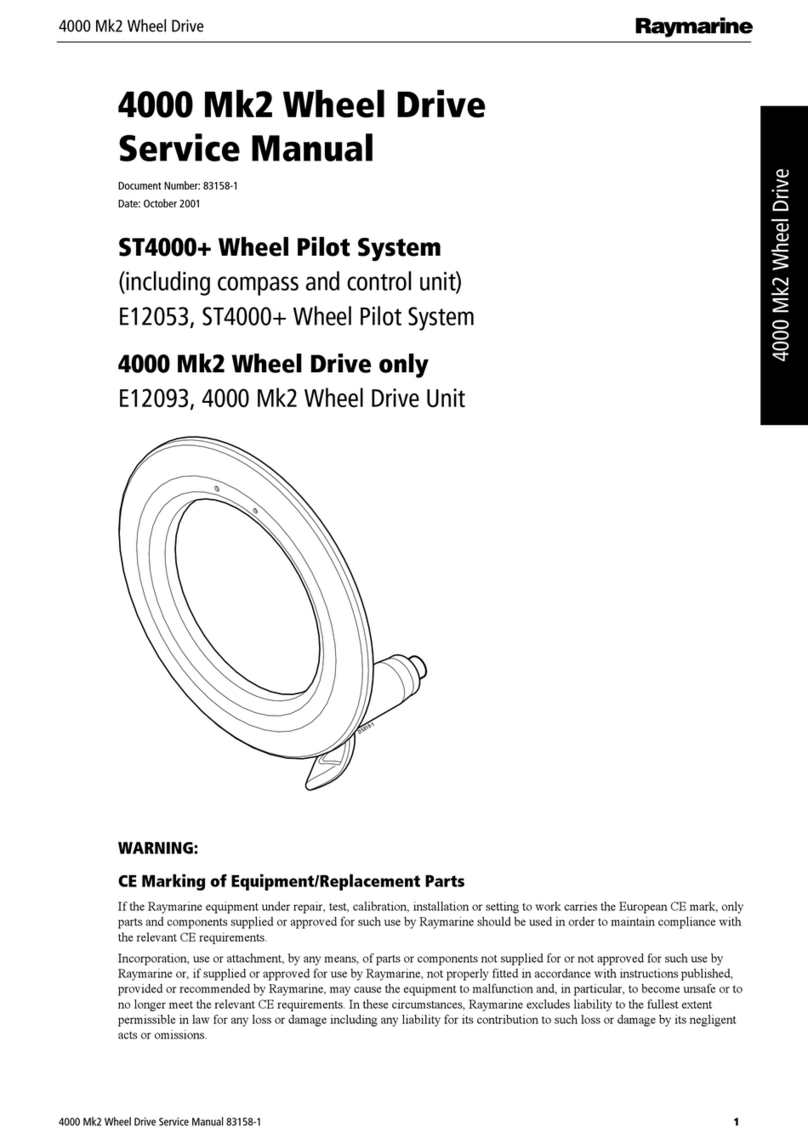
Raymarine
Raymarine 4000 mk2 Wheel Drive Service manual