Compac EP100 D User manual

(EN) EP100D G7 XXX (EN)_Midlertidig_SN.docx 1/31 2019-09-18 SN
Knowhow is the difference
Operation Manual for Compac
Workshop Press
Model EP 100 D G7
Original instructions
Upon request, this operation manual is also available in other languages at no additional cost.
Please carefully read all information within this manual, before using this product,

(EN) EP100D G7 XXX (EN)_Midlertidig_SN.docx 2/31 2019-09-18 SN
Knowhow is the difference

(EN) EP100D G7 XXX (EN)_Midlertidig_SN.docx 3/31 2019-09-18 SN
Knowhow is the difference
Use of COMPAC workshop press
As a manufacturer of workshop presses, we often receive questions concerning equipment on the
press in relation to work safety. In the following, we define the limitations in the use of Compac
workshop presses.
The press is manufactured and sold as a workshop press. In the operating manual is a reservation
whereby the press must only be used for normal workshop use and not as a production press.
The Compac workshop press is such a press if it is used for ordinary repair work in a workshop or for
testing tools, without any structural changes made to the workshop press.
If the owner of the press allows the press to be used in production or in production-like conditions or
processes, it is the owner's responsibility to convert or fit out the press so it is compliant with the work
safety requirements in effect in the EU system and the national requirements in the country where the
press is used.
Compac further underscores that it is always the owner's responsibility to ensure that the purchased
equipment is safe to use for the work in question.
For this reason, it is also the owner's responsibility to have a risk assessment of the work made before
buying and commissioning the press, in order to determine whether a workshop press can in fact be
used for the work.
Workshop presses are covered by the Machinery Directive 2006/42/EC.
Compac cannot advise customers on safety matters relating to its products if they are used for
purposes other than their original purpose. For owners wishing to use the product in other contexts or
with other equipment fitted on the product, we refer you to EU legislation concerning production
presses and the individual countries' work environment legislation.
As an example, in Denmark we refer you to:
The Executive Order Consolidating the Work Environment Act.
The Danish Ministry of Employment's ministerial act concerning Chapter 4, section 15 Ordinary
Obligations of the Employer The employer must ensure that the working conditions comply with all
health and safety requirements.
Before commissioning of the workshop press, Compac will accept the return of the press if after a risk
assessment of the work at hand, the owner recognizes that it will not be possible to use the press safely
for the intended work. The terms of such a return are that the customer and/or the distributor returns the
press freight-free and in unused condition.

(EN) EP100D G7 XXX (EN)_Midlertidig_SN.docx 4/31 2019-09-18 SN
Knowhow is the difference
Content
Use of COMPAC workshop press ............................................................................................................................. 3
Specifications............................................................................................................................................................. 5
Electrical Specifications............................................................................................................................................. 5
To the owner/user ...................................................................................................................................................... 6
Warranty ................................................................................................................................................................ 6
Safety......................................................................................................................................................................... 7
Safety symbols ...................................................................................................................................................... 7
The required safety and information labels on the press........................................................................................... 8
Safety instructions ................................................................................................................................................... 12
Component overview ............................................................................................................................................... 13
Description of Operation ...................................................................................................................................... 13
Transport and installation of the press..................................................................................................................... 14
Press transport .................................................................................................................................................... 14
Pre-commissioning preparation:.......................................................................................................................... 15
Operating instruction................................................................................................................................................ 15
Lifting and lowering of the table ...........................................................................................................................15
Preparation of press table and v blocks...............................................................................................................16
Positioning the object/work-piece ........................................................................................................................ 16
V-Block or straightening plate..............................................................................................................................17
Side movement of cylinder ..................................................................................................................................17
Setting of hinged swivel-type pump .....................................................................................................................19
Operation of the press .........................................................................................................................................20
Maintenance instructions ......................................................................................................................................... 21
General maintenance .......................................................................................................................................... 21
Cleaning...............................................................................................................................................................21
Storing the press.................................................................................................................................................. 21
Repair .................................................................................................................................................................. 21
Oil level ................................................................................................................................................................ 21
Oil information......................................................................................................................................................21
Annual maintenance ............................................................................................................................................ 21
Disposal/destruction ............................................................................................................................................ 21
Periodic maintenance and inspection...................................................................................................................... 22
Service log ............................................................................................................................................................... 28
Press accessories.................................................................................................................................................... 29
Appendix –supplied on delivery of the press ........................................................................................................... 31

(EN) EP100D G7 XXX (EN)_Midlertidig_SN.docx 5/31 2019-09-18 SN
Knowhow is the difference
Specifications
Type
Max. Capacity
kg
Net weight
kg
Stroke length
mm
Piston speed
mm/sec
Oil, quantity
liters
EP100 G7
100,000
(100 tons)
970
300
10
19
Electrical Specifications
Voltage
Frequency
Current drain
Triangle
Current drain
Star
Power
Revolutions
3 x 230V (Star)
3 x 400V (Triangle)
50 Hz
7.95 A
4.59 A
2.2 Kw
2,870 rpm
The press's A-weighted sound pressure level is under 70 dB(A)

(EN) EP100D G7 XXX (EN)_Midlertidig_SN.docx 6/31 2019-09-18 SN
Knowhow is the difference
To the owner/user
Thank you for buying this Compac workshop press.
With correct use and care, this product will give you many years of safe and reliable service.
Read this operating and safety manual before using the machine for the first time, for correct and safe
use of your shop press.
Keep this operation and safety manual with the product at all times.
Yours sincerely
Manufacturer
Compac Hydraulik A/S
Strandhusevej 43
DK-7130 Juelsminde
Denmark
Tel.: (+45) 75 69 37 22
Fax: (+45) 75 69 54 18
Web: www.compac.dk
Warranty
Compac Hydraulik A/S provides a 36-month warranty, from the date of purchase, against faulty
materials and workmanship.
Compac Hydraulik A/S disclaims any responsibility for improper use, alterations in construction, use of
non-original parts and repairs and adjustments made by unauthorized personnel.
Compac Hydraulik A/S reserves the right to make changes to the product without notice, if it can be
done without significant changes to the technical specifications.
Owner:
This unit was manufactured in accordance with the provisions in the COUNCIL
DIRECTIVE OF 2006 (2006/42/EC).

(EN) EP100D G7 XXX (EN)_Midlertidig_SN.docx 7/31 2019-09-18 SN
Knowhow is the difference
Safety
Important: Read and understand the operating manual before transport, installation and operation!
All operators must read, understand and follow all instructions and safety warnings within this operation
manual and on the safety labels placed on the product before using the shop press.
All operating personnel must be able to operate the press safely and care for it in accordance with this
operation manual.
If the operator is not fluent in the language in which the manual is written, it is the owner’s responsibility
to furnish a manual in the correct language, so that the product may be used and cared for in
accordance with to our instructions.
In the event of there being any questions regarding proper and safe use of this press, or if spare parts,
new safety labels or copy operation manuals are required, then please refer to the contact information
provided on page 3 of this manual, or on the product’s rating plate.
Safety symbols
Safety symbols alert the operator of a danger or unsafe use that
can result in serious injury or death.
Symbols concerning general information mandatory for the
product’s safe operation and care etc.
RISK OF TIPPING
Safety symbol indicates that the product may risk tipping over and
cause serious injury or death

(EN) EP100D G7 XXX (EN)_Midlertidig_SN.docx 8/31 2019-09-18 SN
Knowhow is the difference
The required safety and information labels on the press
14

(EN) EP100D G7 XXX (EN)_Midlertidig_SN.docx 9/31 2019-09-18 SN
Knowhow is the difference
Pos 1
Pos 2
Pos 3
Pos 4

(EN) EP100D G7 XXX (EN)_Midlertidig_SN.docx 10/31 2019-09-18 SN
Knowhow is the difference
Pos 5
Pos 6
Pos 7
Pos 8
Pos 9
Pos
10
Pos
11
Pos
12
WARNING
When performing work with the
press and operating the winch,
fingers, hands and other body parts
must not be at risk of becoming
trapped !
The operator may not use the press:
•If there are others nearby the
control.
•If there is a risk that the
operator or others could be
subjected to tooling or
objects being ejected from
the press.

(EN) EP100D G7 XXX (EN)_Midlertidig_SN.docx 11/31 2019-09-18 SN
Knowhow is the difference
Pos
13
Pos
14
1. Rating plate
2. WARNING. The foot must not rest on cross members or columns
3. Oil type AWS Hyspin 32 (Or the equivalent)
4. WARNING. Risk of being caught between table and pin
5. WARNING. Operation of the press
6. Adjustment of piston pressure -Turning counter clockwise increases the pressure
7. Adjustment of piston movement up/down - neutral stops piston movement
8. Direction of motor rotation
9. Danger of electric shock
10. Mandatory. Protective footwear with toe protection is mandatory
11. Mandatory. The wearing of safety goggles is mandatory
12. Mandatory. The wearing of gloves is mandatory
13. Mandatory. Read and understand the operation manual before use
14. WARNING. Risk of becoming caught

(EN) EP100D G7 XXX (EN)_Midlertidig_SN.docx 12/31 2019-09-18 SN
Knowhow is the difference
Safety instructions
Failure to observe the following may result in serious body injury or death, as
well as possible damage to property.
The work press is intended only for normal shop use and not as a production press.
The press's maximum load is stated in the CE certificate and on the press's product label.
When operating the press, the following means of protection must be used:
Protective footwear –
Safety shoes with steel
toe-caps
Safety goggles
Work gloves
The foot must not rest on cross members or columns.
•The press must be secured to a flat, strong floor.
•The electrical connection must be performed by a certified electrician.
•Never make any alterations to the product’s construction.
•Do not use the press in a way that exceeds its intended use and capacity.
•The press must not be used if it is damaged, leaking oil, or if the unit is functioning in a way that is
different from the description in the operation manual. If this is the case, stop using the press
immediately, contact an authorized service technician for full inspection and, if necessary arrange
repair, so that the press may be used safely again.
•The table must not be raised or lowered if v-blocks, tooling or other equipment is sitting on the
table.
•For all pressing operations, the table must be supported by both pins, and wire/winch must be
slack.
•V-blocks or other tooling must be correctly positioned on the press table before use.
•The press should be visually inspected prior to each use. Check for broken, cracked or bent parts,
or loose or missing parts, and any other condition which could affect its proper and safe operation.
•Assess the risk of any work-pieces being ejected during use.
•Keep at an appropriate, safe distance from the press/work-piece whilst using the press.
•When operating the machine, make sure that hands and other body parts are not at risk of
becoming trapped.
•The operator should not use the press with others standing near the controls, or if they are in
danger of being hit by objects or tooling..
•Any inspection must be carried out by a qualified individual at least once a year.
•Use only original spare parts for safe and reliable operation.
•Make sure that all warning and information signs on the product are legible and intact at all times.

(EN) EP100D G7 XXX (EN)_Midlertidig_SN.docx 13/31 2019-09-18 SN
Knowhow is the difference
Component overview
Description of Operation
If the operating lever (H) is pulled up, then the piston goes back in the cylinder.
Raise/lower the table (N) into the working position using the winch (B), and place the pins (M) in the
holes in the press's chassis.
Place the v-blocks (A) so that they adequately support the object.
Place the object under the cylinder's piston (P).
Press the operating lever (H) down and actuate until the piston's pressure head (O) is directly above
the object.
Then continue pressing on the operating lever until the desired working pressure is built up and the
press work has been satisfactorily completed. It is possible to set the maximum pressure for the
operating lever (K).
To return the piston, pull up lever (H) and the piston movement will stop when the handle is released.
Pos.
Name
A
V-Block
B
Winch
C
Frame
D
Cylinder
E.
Pressure gauge
F
Motor
G
Protective motor switch/
Electrical connection
H
Control lever up down
I
Inspection glass
J
Drainage plug
K
Pressure regulation
L
Oil container
M
Pin
N
Table
O
Compression and tension
flange
P
Piston
Q
Oil filling

(EN) EP100D G7 XXX (EN)_Midlertidig_SN.docx 14/31 2019-09-18 SN
Knowhow is the difference
Transport and installation of the press
RISK OF TIPPING OVER
With regard to safe transport of the shop press, please be aware that the press's center
of gravity is very high.
When shipped, the press is secured to the transport pallet with screws and metal strips,
which should only be removed when setting up the press.
Press transport
Failure to observe the instructions below can result in serious damage and injury
1. With a forklift: Place the forks under the top frame. The lifting points are marked on the transport
packing material. (see Fig. 1).
2. With a crane: Use only approved hoisting straps with a capacity of at least the total weight of the
press.
Note: mount the straps only at the top of the press, and protect them from sharp edges.
On receipt of the press:
Check the packing material and the press for visible damage, cracks and leakage.
The carrier must be notified of any damage occurring during transport.
Installation of the press:
The press must be secured to the floor using expansion bolts, for safe and stable installation.
Fig. 1
This lifting instruction is printed on the
transport packing material at the top of the
press.
LIFT HERE
CAUTION ! –THE PRESS IS TOP HEAVY
THE PRESS MUST BE FIRMLY SECURED
WITH STRAPS ON THE VEHICLE

(EN) EP100D G7 XXX (EN)_Midlertidig_SN.docx 15/31 2019-09-18 SN
Knowhow is the difference
Pre-commissioning preparation:
An experienced operator must visually inspect the press for leakage and damage. Such inspection
must furthermore take place at least once a year.
The press comes filled with hydraulic oil.
Connection of electricity
The power connection must be carried out by a professionally trained electrician, furthermore, should
be in accordance with the wiring instructions found inside of the motor's top cover. It must be then
checked that the motor's direction of rotation is as shown on the arrow on the end cover.
Bleeding of the hydraulic system
Activate the piston to full/maximum stroke length and return. Repeat this three times.
Operating instruction
Lifting and lowering of the table
The table must be free of v-blocks, other tooling, and work-pieces, when lifting and
lowering.
To lift and lower the table to the desired working height, the press is equipped with a winch.
Before raising/lowering the table, return the piston of the press by pulling the operating lever up.
Firstly, flip down the handle-grip (See Fig. 3) and then turn the winch's handle clockwise to pull the
table free from the pins.
Remove the pins, and place the table in the desired working position. Lift the table slightly over the
holes, to allow the pins (I) to be inserted in the column of the press.
Now insert the pins correctly in the holes just under the table. (See Fig. 7)
Next, turn the handle, which has a built-in sliding clutch, counter clockwise, to lower the table onto both
pins. Please ensure that the winch/wire is always slack before using the press. You can now fold back
the handle-grip by firstly pulling it out and then placing it against the arm.
Fig. 3
Handle
UP
DOWN
Fig. 4
Lock

(EN) EP100D G7 XXX (EN)_Midlertidig_SN.docx 16/31 2019-09-18 SN
Knowhow is the difference
NOTE: Because the table hangs freely from the winch during positioning, there is a risk of
the table falling and causing damage or injury. Therefore, do not release the handle until
one of the winch's locks is engaged with the turntable (see Fig. 4) before removing the pins.
Preparation of press table and v blocks
1. The table must be placed as close to the returned rod as possible, so that the piston always has
the least possible projection (the shortest possible stroke length). In this way, the stress during the
pressing operation will be minimised, reducing the risk of damage to the press cylinder, piston or
frame.
2. It is important that the pins are placed correctly and that the piston is perpendicular (not off-center)
to table/plate (see Fig. 7) for proper use/set-up. The table must be correctly supported by both pins
before the press can be used.
Mount the pins as shown in Fig. 7, with the washer between the table and frame, and the piston should
press perpendicularly on the object. If the pins are located incorrectly, with the washer outside the table
as shown in Fig. 8, then there is a significant risk of serious damage or injury.
Fig. 7
Fig. 8
Positioning the object/work-piece
Place the object (4) so that the piston (3) is perpendicular and centered in relation to and the table/plate
(2) (see Fig.9). The object should not move during the pressing operation.

(EN) EP100D G7 XXX (EN)_Midlertidig_SN.docx 17/31 2019-09-18 SN
Knowhow is the difference
If the object is angled or asymmetrical, there is a significant risk of injury or damage to the press's
cylinder, piston or chassis (see Fig. 10).
Do not press on work items that could burst or break, because this can injure persons or damage the
press's cylinder, rod or frame. (see Fig. 11).
V-Block or straightening plate
The v-blocks must always be used for support. (see Fig 12)
Side movement of cylinder
For work-pieces which require more space between the press's vertical columns, it is possible to move
the cylinder out to the side/off-center. (see Fig. 13)
The cylinder's four bolts (1) are loosened with a 24 mm open-end wrench, and the cylinder can now be
moved to the desired position.
2
3
4
Fig. 9
Fig. 10
Fig. 11
Fig. 12

(EN) EP100D G7 XXX (EN)_Midlertidig_SN.docx 18/31 2019-09-18 SN
Knowhow is the difference
Ensure that all cylinder bolts are retightened again before commencing any work.
If the cylinder is able to move while under pressure, then there is a risk of injury or damage.
Fig. 13
1

(EN) EP100D G7 XXX (EN)_Midlertidig_SN.docx 19/31 2019-09-18 SN
Knowhow is the difference
Setting of hinged swivel-type pump
The hinged pump unit can be moved to three positions, to suit specific workpiece and application.
If the pump is turned 90 degrees, it is then possible to insert longer items from the side.
Turn the pump by pulling on the spring-loaded lock
(Fig. 14) and pulling the pump into the required
position.
Lock the pump in one of the three positions (Fig. 15).
Fig. 14
Fig. 15
Normal position
Turned 45 degrees
Turned 90 degrees

(EN) EP100D G7 XXX (EN)_Midlertidig_SN.docx 20/31 2019-09-18 SN
Knowhow is the difference
Operation of the press
Adjust the table to the required work height, and then place the v-blocks upon the table.
Note! At pressures over 40% of the maximum capacity both v-blocks must be supporting the object.
Pull the operating lever (H) up so that the piston moves returns to its start position.
Raise/lower the table (N) to the required working position using the winch (B), and then place the pins
(M) in the holes which are in the press's frame.
Place the v-blocks (A) so that they adequately support the workpiece.
Place the workpiece underneath the cylinder's piston (P).
Press the operating lever (H) down until the piston's pressure head/nose (Q) is directly above the
workpiece.
Then continue pressing on the operating lever until the required working pressure is reached and the
press work has been satisfactorily completed. It is possible to set the maximum pressure for the
operating lever (K).
Never use the press without the pressure head/nose mounted, as in doing so will damage the piston.
Return
To return the piston, pull handle (H) up, and the piston movement will stop when you let go of the
handle.
WARNING! Do not exceed the maximum pressure and maximum stroke, as this can
damage the cylinder's seals. Therefore, ensure that the pump's handle is always released
when the press has reached the full stroke length.
Other manuals for EP100 D
1
Table of contents
Other Compac Power Tools manuals
Popular Power Tools manuals by other brands
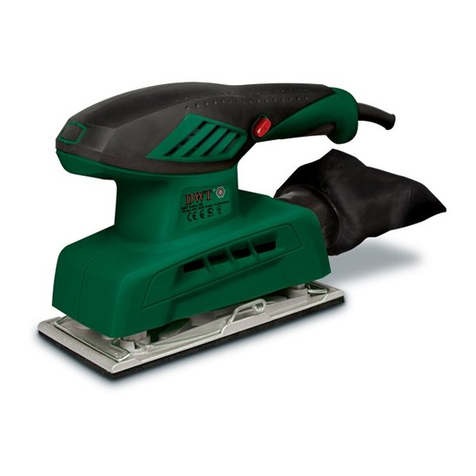
DWT
DWT ESS02-187 T Original instructions
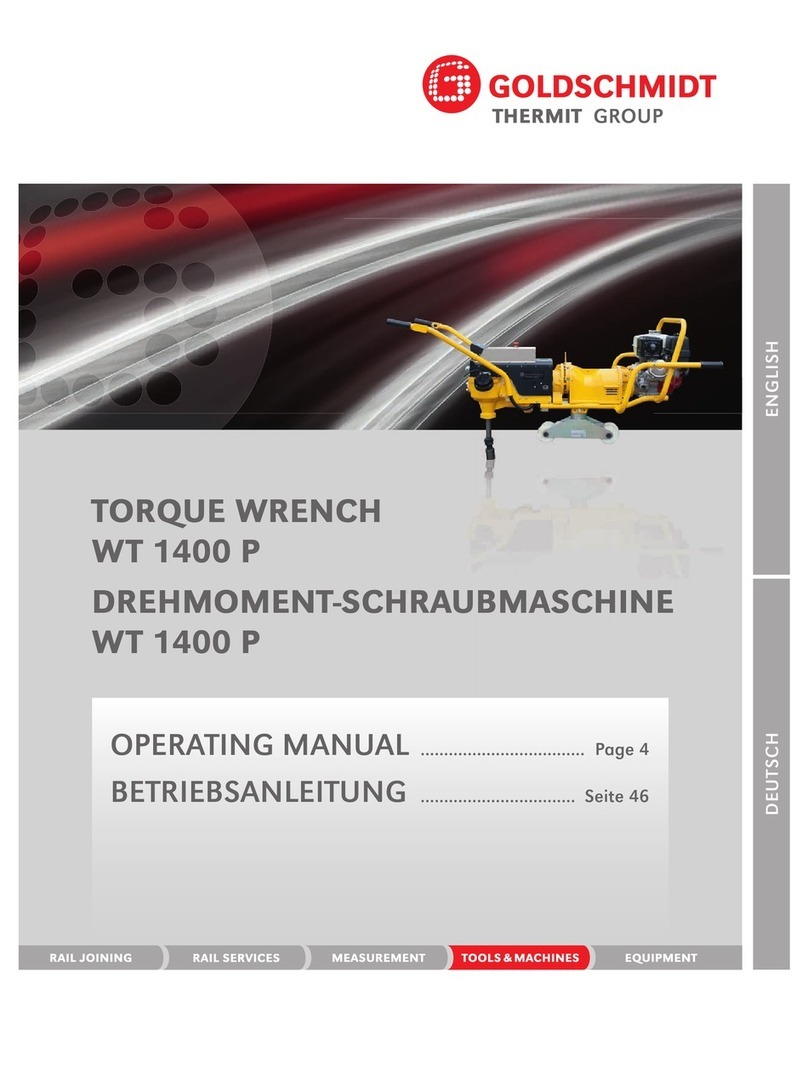
Goldschmidt
Goldschmidt WT 1400 P operating manual
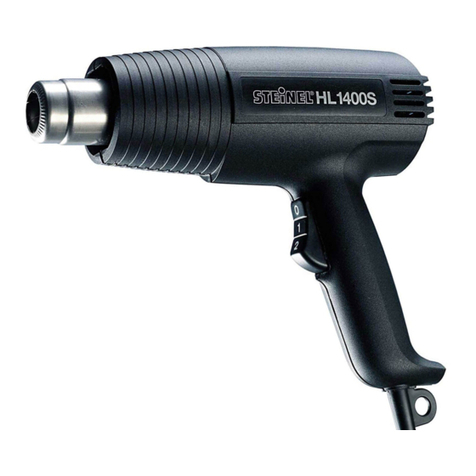
STEINEL
STEINEL HL 1400 S Information
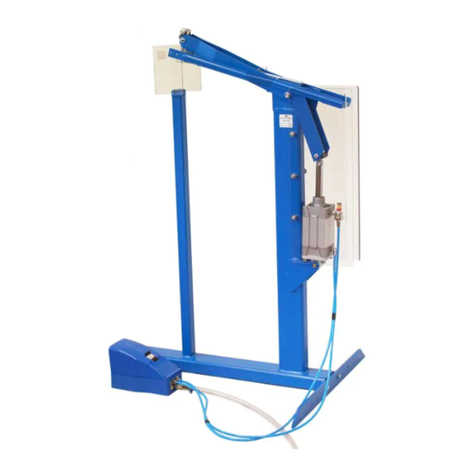
Josef Kihlberg
Josef Kihlberg B53 Operating and service instructions

HEIN-WERNER AUTOMOTIVE
HEIN-WERNER AUTOMOTIVE HW93300 Operating instructions & parts manual

Rothewald
Rothewald 10002598 Instructions for use