NSK Megatorque Motor EGA User guide

MEGATORQUE MOTORTM SYSTEM
Start-up Guide
(Driver Model EGA)
NSK Ltd.
DocumentNo.C20195-02

1
1. Preface
This manual describes necessary procedure to perform PB motor operation as a startup guide. Refer manual
M-E099GA0C2-191 for detail.
Please use application software “MEGATORQUE MOTOR SETUP”to set parameter setting value of model
EGA driver. “MEGATORQUE MOTOR SETUP”is a free software which can be downloaded from NSK
Website.
(http://www.nsk.com/)
2. System configuration
Noise filter
Installed to protect power line from
external noise.
防
ぐために
取
り
付
けます
。
Citcuit Breaker
Used to protect power line.
Turns off the power supply when
overload runs.
MEGATORQUE
MOTOR SETUP
Enables parameter set up and monitoring
through communication with a PC.
Host equipment
Switches power On/Off.
Please place safeguard circuit.
T S R
Electromagnetic contactor
Converter cable
Motor cable
RS-232C
Motor
For high-frequency operation, use an external
regenerative resistor.
External regenerative resistor
Converter

2
3. Motor of installation
Install and secure the Motor on a rigid base, otherwise mechanical vibrations may occur. And fail to magnetic
pole detecting.
OK
NG
■Checking the operating conditions
The MEGATORQUE MOTOR system involves significantly larger moment of inertia for load compared to
the moment of inertial for rotor.
✔Remember to check for appropriate allowable moment load, allowable axial load and allowable
radial load for your specific applications of the motor.
Table
Table fixing bolt
MEGATORQUE
MOTOR
Mounting base
Motor fixing bolt
Flatness of mounting
surface: 0.02 mm or less.
Load
The load is not directly
applied to the motor rotor.
The motor is not directly
installed on the mounting
base. Mounting base
MEGATORQUE
MOTOR

3
CN1 signal and Pin number.
■CN110150-3000PE (Soldering side view)
Signal name and its function. (shipping set)
Terminal
number
Signal
name
Description
Terminal
number
Signal
name Description
1 - Do not connect
30 MON1 Analog monitor output
2 - Do not connect
31 SG Common for pin 30
3 A0 A phase pulse output
13 CONT7 Position command pulse
disabled function/shutdown at
zero velocity function
4 A0 /A phase pulse output
14 CONT7
5 BO B phase pulse output
15 CONT8 Alarm reset function
6 BO /B phase pulse output
16 CONT8
7 ZO Z phase pulse output
38 SG Common for pins 13 to 16
8 ZO /Z phase pulse output
32 CONT6 CW over travel function
9 PS Resolver signal output
33 CONT5 CCW over travel function
10 PS /Resolver signal output
34 CONT4 Deviation clear function
11 ZOP Z phase pulse output
35 CONT3 Magnetic pole position estimation input
12 SG Common for pins 3 to 11
36 CONT2 Emergency stop function
17 - Do not connect
37 CONT1 Servo-ON function
18 - Do not connect
50 CONT-COM
General input power supply
19 - Do not connect
39 OUT1 In-Position window
20 - Do not connect
40 OUT2 Magnetic pole position estimation ready
21 - Do not connect
41 OUT3 Operation setup completion
22 T-COMP
Torque compensation input
42 OUT4 Magnetic pole position estimation end
23 SG Common for pin 22
43 OUT5 Alarm code bit 5
26 F-PC CW command pulse input
44 OUT6 Alarm code bit 6
27 F-PC CW command pulse input
45 OUT7 Alarm code bit 7
28 R-PC CCW command pulse input
46 OUT8 Alarm status
29 R-PC CCW command pulse input
49 OUT-PWR
Power source for general output
47 SG Common for pins 26 and 27
24 OUT-COM
General output Common
48 SG Common for pins 28 and 29
25 OUT-COM
General output Common
24
22
20
18
16
14
12
10
8
6
4
2
25
23
21
19
17
15
13
11
9
7
5
3
1
49
47
45
43
41
39
37
35
33
31
29
27
50
48
46
44
42
40
38
36
34
32
30
28
26

4
4. CN1 wiring example
In-Position window
Magnetic pole position estimation ready
Operation setup completion
Magnetic pole position estimation end
Alarm status
Polarity of the power supply may be
reversed to minus common.
Servo-ON function
Emergency stop function
Magnetic pole position estimation input
Deviation clear function
CCW over travel function
CW over travel function
Host equipment Driver model EGA
Z phase pulse output
B phase pulse output
A phase pulse output
5/12/24 [VDC]
V
DC
SG
50
CONT-COM
37
CONT1
36
CONT2
35
CONT3
34
CONT4
33
CONT5
32
CONT6
13
CONT7
38
SG
15
CONT8
38
SG
26
F-PC
27
/F-PC
47
SG
28
R-PC
29
/R-PC
48
SG
49
OUT-PWR
39
INP
40
CSETRDY
41
S-RDY
42
CSETCMP
46
ALM
24,25
OUT-COM
3
AO
4
/AO
5
BO
6
/BO
7
ZO
8
/ZO
12
SG
CN
1
FG
5/12/24 [VDC]
V
DC
Position command pulse disabled function
SG
SG
SG
CW command pulse input
CCW command pulse input
Alarm reset function
SG

5
5. Initial setting
Please change parameter setting value of Model EGAdriver required according to the conditions to be used.
Use application software “MEGATORQUE MOTOR SETUP”to set the parameters.
◆Single phase AC main power
Change “System parameter_ID01 : main circuit power input type”to “01 : AC Single-phase”, then connect
AC power line
to terminal R and T of connector CNA.
◆CN1 I/O signal configuration
The pin-out arrangement and polarity of signals from CONT1 to CONT8 can be changed by setting of
parameter “Gr.9_Function enabling condition settings”, and pin-out arrangement of signals from OUT1 to OUT8
can be changed by “Gr.A_General output terminal output condition / Monitor output selection / Serial
communication settings”.
Input signals “Gr.9_ID00:CW Over Travel function(F-OT)”, “Gr.9_ID01:CCW CW Over Travel
function(R-OT)”, and “Gr.9_ID42:Emergency Stop Function(EMR)”are normal close polarity input as
shipping set.
To enable motor operation, wire these input signals properly, or change its polarity by parameter setting value.
6. Operation sequence
0 msec (Min)
Control source
Main circuit power
Magnetic Pole Position Estimation
ready signal (output)
Magnetic Pole Position Estimation
input signal (input)
Magnetic Pole Position Estimation
end signal (output)
Servo On signal (input)
Motor speed
Operation set up completion signal (output)
Pulse command
In Position window (output)
:
The magnetic pole position estimation must be conducted everytime when
power is turned on.
Magnetic pole position estimation will cause the motor rotation reciprocally
maximum of +/-18 degree.
Do not apply external and/or unbalanced force to the motor to complete
magnetic pole position estimation process properly.
Start motor operation after completion of magnetic pole estimation process.
:
Install external Home sensor if homing operation is required.
Motor incorporates incremental sensor, no absolute sensor is incorporated.

6
7. Motor operation
Ste Content
1
Confirm wiring for Input and Output signals.
Confirm wiring for Input / Output signals work properly by Host equipment and application software
“MEGATORQUE MOTOR SETUP”.
2
Set Tuning mode and Load inertia moment ratio.
Set Tuning mode “Gr.0_ID00 : Tuning mode (TUNMODE)”to 01:AutoTun_JRAT-Fix”.
Set the ratio of Load moment inertia against Motor rotor inertia to “Gr.1_ID14:Load inertia moment ratio 1
(JRAT1)”.
JRAT1 setting value = (Load moment inertia) / (Motor rotor inertia) × 100 [%]
3
ExecuteMagnetic pole position estimation.
Close “Magnetic pole position estimation”input after confirming “Magnetic pole position estimation ready”
output. Motor will start maximum +/-18 degree reciprocal motion.
4
Close Servo On.
Close Servo On input signal. Confirm motor servo against external force, and 7 segment display on the front
panel of model EGA driver shows character “8”.
5
Input pulse command.
Input Pulse command to model EGA driver.
In case of no motor motion, please check pulse command from host equipment to model EGA driver which can
be confirmed by monitor function “Monitor _ID13:Command pulse frequency (FMON1)”.
No number (“0”) appears on monitor if Model EGA driver does not receive position command pulse from host
equipment.
Please check wiring from host equipment to model EGA driver.
※
Note:
Apply slow motor speed pulse command to confirm motor speed and motor rotating direction with secured
interlock signals such as Emergency stop and Over travel.
Stop motor operation immediately in case of any abnormal motion.
Shipping set of Tuning mode “Gr.0_ID00 : Tuning mode (TUNMODE)”is “00”as Auto-tuning for such as
servo gain and is valid.
■Display of the Digital operator
NO
Display Description Check points to get proper state
1 Control power supply established.
Control power supply (r, t) is established,
and driver
ready (RDY) is ON.
-
2 Main circuit power supply established.
Main power supply (R, S and T) is
established, but operation preparation
completion signal is OFF.
・Confirm main AC voltage line
connected to model EGA driver.
3
Operation preparation completion signal is
established.
Main power supply (R, S and T) is
established, and operation preparation
completion signal is ON.
・Confirm input signal polarity of Over
travel and Emergency stop.
・Confirm magnet pole position
estimation has completed properly.
4 Servo is ON.
Segment repeats on and off individually to
display character “8”.
・Confirm Servo On input signal is closed
properly.

7
8. Important notation.
8.1Ratio of Load moment inertia against Motor rotor inertia.
Model EGAdriver features Auto Tuning function which generates servo parameters automatically by parameter
setting value of ratio of Load moment inertia against Motor rotor inertia, and motor responsiveness. No Manual
tuning is required if motor performance is fully satisfied.
Before starting motor operation, change parameter setting of “Gr.0_ID00:Tuning mode(TUNMODE)”to “01:
AutoTun_JRAT-Fix”(This setting changes a mode from a real time auto tuning mode to an auto tuning mode), then
enter ratio of Load moment inertia against motor rotor inertia to “Gr.1_ID14:Load inertia moment ratio 1
(JRAT1)”.
Please refer PB motor catalog for the value of Motor rotor inertia. Motor operation does not required to enter
value to “Gr.1_ID14:Load inertia moment ratio 1 (JRAT1)”.
Formula for Load inertia moment ratio JRAT1:
JRAT1 = (Load moment of inertia) / (Motor rotor moment of inertia) × 100 [%]
【Example】
・Load moment of inertia:0.026 [kg・m2]
・Motor rotor moment of inertia : M-PB1006JN001:0.0026 [kg・m2]
JRAT1 setting value = (0.026 / 0.0026) × 100 = 1000 [%]
If Load moment of inertia value is not available, enter value listed in the table below as a temporary setting
value.
Temporary setting value of Load moment of inertia ratio
Load moment of inertia
JRAT1 : Load moment of inertia ratio
[%]
Relatively small 1000
Relatively large 5000
Although temporary setting value for JRAT1 may able to provide some degree of performance, enter proper
JRAT1 value for faster motor speed and better accuracy positioning operation.
To improve responsiveness of motor motion and positioning settling time, increase “Gr.0_ID00:Auto-Tuning
response (ATRES)”setting value gradually. Decrease “Gr.0_ID00:Auto-Tuning response (ATRES)”setting value
to reduce motor oscillation.
Manual tuning is recommended if motor performance is not sufficient using Auto Tuning function. Please refer
manual M-E099GA0C2-190 how to implement manual tuning.
8.2Magnetic pole position estimation
Model EGAdriver requires Magnetic pole position estimation every time when power is turned on.
In case of situation described in below which may affect Magnetic pole position estimation, please adjust
“Gr.B_ID01:Excitation Command Frequency setting (EMPFREQ)”and “Gr.B_ID02:Acceleration threshold
(ACC)”with considering conditions of equipment.
◆Conditions which may affect Magnetic pole position estimation.
・Motor has external and/or unbalanced force.
・Low rigidity of equipment. (Base, Load, Installation)
・Excessive Load moment of inertia.
・Frequency setting value of “Gr.B_ID01:Excitation Command Frequency setting (EMPFREQ)”is close to
resonance frequency of equipment.
・Motor combined with improper converter unit.
◆Parameter setting procedure to solve “Magnetic pole position estimation error”.
①Adjust setting value of “Gr.B_ID01:Excitation Command Frequency setting (EMPFREQ)”
②Adjust setting value of “Gr.B_ID02:Acceleration threshold (ACC)”.

8
◆Alarm code for “Magnetic pole position estimation error”.
8.3Homing
Motor does not incorporate home sensor. Homing must be operated by host equipment using external home
sensor referring homing sequence and home sensor setting position described in below.
Example of homing sequence
To secure home position by detecting rise up of Z phase signal properly, turn off point of home sensor must be
adjusted at the middle point between Z phase signal described in below. Adjust home sensor turn off position
around 32767 [pulse] by monitoring motor position using “Monitor_ID80:Resolver sensor electric
angle(RESANG)”.
Home sensor turn off position
Driver condition code at alarm 9 : Implementing Magnetic pole position estimation
Alarm code 44 : Magnetic pole position
estimation error
Start homing
Motor motion
Home sensor
Z phase signal pulse
Homing completion
ON
OFF
ON
OFF
ON
OFF
ON
OFF
Home
Z phase signal
Home sensor
ON
OFF
ON
OFF
Motor angle 4.5°
Middle point
Home
Riseup of 1st Z phase signal
(Home)
Read out
RESANG
[Pulse]
0
65535

9
9. Related document
・Please refer manual M-E099GA0C2-191 about the detail of Parameters, Tuning procedure, Alarm and
Optional parts.
・Please use application software ”MEGATORQUE MOTOR SETUP”to Edit parameters, and Monitor
signals. Refer HELP for instruction manual.
10.Major section and page number to refer in manual M-E099GA0C2-191
Item Section Page no.
Motor specifications 2 2-1
Specifications of driver 2-3
Specifications of converter 2-12
Motor installation 3 3-4
Set main circuit power input type as Single phase AC
power 5 5-1
Motor and signal state at occurrence of alarm 5-12
Monitor Input / Output signal state 5-16
Parameters for tuning. 5-29
Servo Tuning functions and basic adjustment procedure 6 6-1
Set Load inertia moment 6-9
Manual tuning 6-13
Digital operator 7 7-1
List of warning and alarm 8 8-3
Trouble shooting when alarm activated 8-7
Optional parts 9 9-7
Install product in safety. Safety precautions
ⅰ〜ⅹⅰ
Other NSK Engine manuals
Popular Engine manuals by other brands

Nice
Nice Era-Era Star Head EMPC quick guide

Ingersoll-Rand
Ingersoll-Rand AF0860 Series Operator's manual
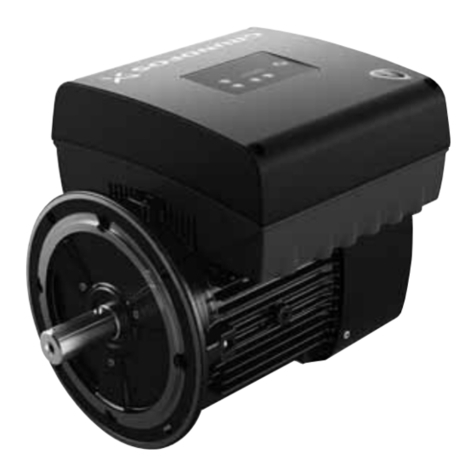
Grundfos
Grundfos MGE 112 Service Kit Instructions

Perkins
Perkins 1106C-E70TA Operation and maintenance manual
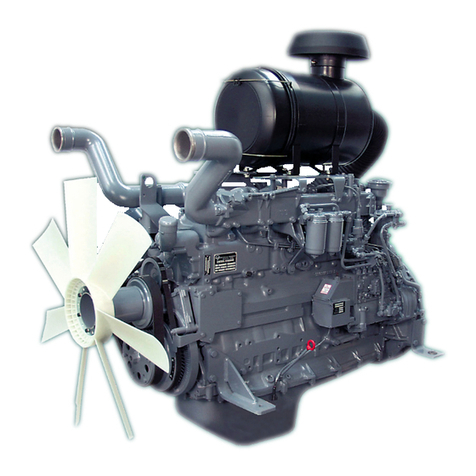
Man
Man D 2876 LE 201 Repair manual
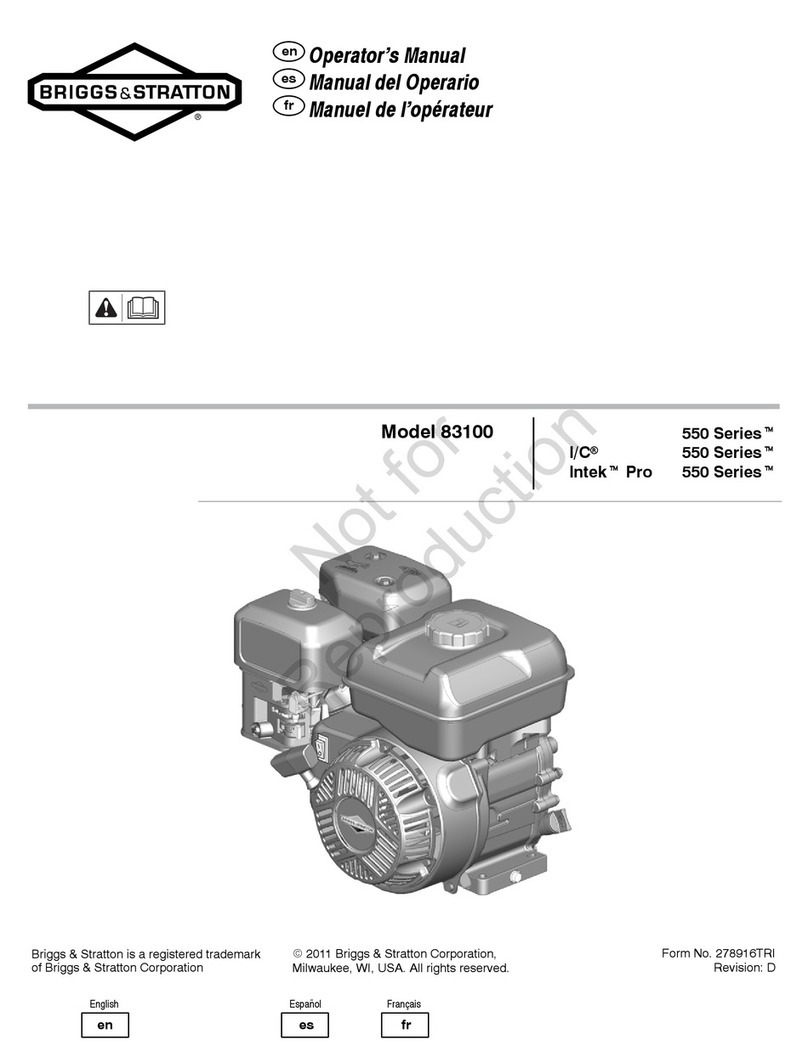
Briggs & Stratton
Briggs & Stratton 550 series Operator's manual