COPES-VULCAN 700 User manual

COPES-VULCAN INSTRUCTION MANUAL
MODEL 700 DIRECT-ACTING ACTUATOR
Rev.5 (08/10) Page 1 of 20 Form 01:P224:37
DIRECT-ACTING 700 ACTUATOR

COPES-VULCAN INSTRUCTION MANUAL
MODEL 700 DIRECT-ACTING ACTUATOR
Rev.5 (08/10) Page 2 of 20 Form 01:P224:37
TABLE OF CONTENTS
1.0 INTRODUCTION
1.1 Scope of Manual
1.2 Description of Equipment
1.3 Specifications
2.0 INSTALLATION
2.1 On Receipt
2.2 Actuator Mounting
2.3 Stem Connector and Travel Adjustment
2.4 Spring Adjustment
2.5 Air Connection
3.0 MAINTENANCE
3.1 General
3.2 Precautions
3.3 Direct-Acting Actuator
3.4 Top-Mounted Handwheel Assembly
3.5 Adjustable Up/Down Travel Stops
3.6 Fixed Travel Stops
3.7 Side-Mounted Handwheel Assembly
FIGURES
1 Exploded View of Direct-Acting Series 700 Actuator Assembly
2 Exploded View of Top-Mounted Handwheel Assembly
3 Exploded View of Side-Mounted Handwheel Assembly
4 Exploded View of Adjustable Up/Down Travel Stop Assembly

COPES-VULCAN INSTRUCTION MANUAL
MODEL 700 DIRECT-ACTING ACTUATOR
Rev.5 (08/10) Page 3 of 20 Form 01:P224:37
TABLE OF CONTENTS (Cont’d)
ATTACHMENTS
Drawing D-360837 Mounting Arrangements
REFERENCE DRAWINGS
Drawing D-357643 Material List
Drawing C-357187 Actuator Option List
Drawing C-357183 Direct-Acting Actuator Assembly
Drawing C-357184 Direct-Acting Actuator with Top-Mounted Handwheel
Drawing C-358357 Direct-Acting Actuator with Adjustable Travel Stops
Drawing C-357058 Direct-Acting Manual Actuator Assembly
Drawing D-360436 Fixed Travel Stop (Down) Assembly

COPES-VULCAN INSTRUCTION MANUAL
MODEL 700 DIRECT-ACTING ACTUATOR
Rev.5 (08/10) Page 4 of 20 Form 01:P224:37
1.0 INTRODUCTION
1.1 SCOPE OF MANUAL
This instruction manual provides instructions for all sizes of the direct-acting Model 700 actuator and
includes instructions for top-mounted handwheels, side-mounted handwheels, adjustable travel stops
and fixed travel stops.
1.2 DESCRIPTION
The Model 700 direct-acting pneumatic actuator is a spring-opposed diaphragm actuator that is used
for the operation of control valves. The actuators are available in sizes 60, 100, 160, and 160-5, with
travel up to 5" (125 mm).
For the direct-acting actuator, the spring tends to retract the actuator stem and air pressure acting on
the diaphragm will extend the actuator stem. The initial spring force, or spring preload, is adjustable
and, for the case of a direct-acting actuator on a direct-seated valve, the preload is normally set to a
low value. The spring preload can be expressed as the diaphragm pressure at which stem movement
begins.
The actuator can be attached to the valve bonnet with a screwed ring or with four studs. The valve
stem is connected to the actuator by use of a threaded ring which is locked between surfaces of the
stem connector.
The top-mounted handwheel is designed to extend the actuator stem against the spring force but not
to retract the actuator stem.
The side-mounted handwheel is a worm gear coupled to an ACME thread and provides a large
mechanical advantage and the means to both extend and retract the actuator stem.
Two different types of travel stops can be supplied: an adjustable up/down stop and a fixed down
stop. The up stop provides a means of preventing the actuator from fully retracting, while the down
stop prevents the actuator from fully extending.
For control valve applications, the actuator will almost always require a positioner.

COPES-VULCAN INSTRUCTION MANUAL
MODEL 700 DIRECT-ACTING ACTUATOR
Rev.5 (08/10) Page 5 of 20 Form 01:P224:37
1.3 SPECIFICATIONS
GENERAL SPECIFICATIONS - 700 DIRECT-ACTING ACTUATOR
Size 60 100 160 160-5
Effective Area, in2
Effective Area, cm2
60
387
100
645
160
1032
160
1032
Nominal Travel, in.
Nominal Travel, mm
1
25
2
50
3
80
5
125
Pressure Connection 1/4" NPT 3/8" NPT 1/2" NPT 1/2" NPT
Maximum Operating Air Pressure, psig
Maximum Operating Air Pressure, bar
80
5.5
80
5.5
80
5.5
80
5.5
Maximum Test Air Pressure, psig
Maximum Test Air Pressure, bar
100
7
100
7
100
7
100
7
Maximum Temperature, deg. F
Maximum Temperature, deg. C
150
65
150
65
150
65
150
65
Maximum Spring Adjuster Travel, in.
Maximum Spring Adjuster Travel, mm
1.79
45.5
2.03
51.6
2.12
53.8
2.52
64
Available Stem Diameters, in. 3/4" 3/4" 3/4" & 1" * 3/4" & 1" *
Available Mounting Styles ring or stud ring or stud ring or stud ring or stud
* The 1" stem is available only with stud type mounting

COPES-VULCAN INSTRUCTION MANUAL
MODEL 700 DIRECT-ACTING ACTUATOR
Rev.5 (08/10) Page 6 of 20 Form 01:P224:37
2.0 INSTALLATION
2.1 ON RECEIPT
When the actuator and valve are shipped together, the actuator normally is mounted on the valve.
Follow the valve instructions in the instruction manual when installing the valve in the pipeline. The
actuator may be installed vertically or horizontally either above or below the valve, but, whenever
possible, the valve assembly should be installed with the actuator located above the valve.
If the actuator is shipped separately from the valve, refer to the following instructions for mounting
the actuator to the valve.
2.2 ACTUATOR MOUNTING
There are two available methods of mounting the actuator to the valve bonnet: a screwed ring
using a 2.75"-12UN thread and a stud connection using four 9/16"-12UNC studs. The mounting
styles are not interchangeable. The bonnet and actuator mounting styles must match.
2.2.1 Screwed Ring Mounting Type (Refer to Drawing D-360837)
To mount the actuator on the valve using the screwed ring mounting method:
A. Place the yoke nut on the base of the yoke, then lower the actuator over the valve stem and
onto the valve bonnet.
B. Screw the yoke nut tightly onto the bonnet to secure the actuator to the valve. Use a steel
bar and hammer to engage the cast protrusions of the yoke nut to apply torque.
2.2.2 Stud Mounting Type (Refer to Drawing D-360837)
To mount the actuator on the valve using the stud mounting method:
A. Lower the actuator over the valve stem and onto the valve bonnet.
B. Fully engage the four 9/16"-12UNC studs in the tapped holes in the bonnet. Install the four
lockwashers and hex nuts on the studs. Torque the nuts to 54 ft-lb (73 Nm).

COPES-VULCAN INSTRUCTION MANUAL
MODEL 700 DIRECT-ACTING ACTUATOR
Rev.5 (08/10) Page 7 of 20 Form 01:P224:37
2.3 STEM CONNECTOR AND TRAVEL ADJUSTMENT
2.3.1 Direct-Seated Valve Without Backseat
A direct-seated valve is closed by applying downward force on the valve stem.
For the case of a direct-seated valve where a valve backseat is not present, the actuator will be set
up so that upward, or opening, motion of the valve stem is limited by the internal stop in the
actuator and downward, or closing, motion of the stem will be limited by the valve mainseat.
Note that Tandem valve trim, which has an internal valve spring, requires a different procedure
than that outlined below and is discussed separately in this section. For other trim types, proceed
as follows:
A. Referring to the assembly drawing and to Figure 1, place the stem lock plate (Item 28) over
the valve stem, then thread the stem clamp (Item 27) fully on the valve stem thread. Thread
the upper stem weldment (Item 22) onto the actuator stem (Item 16) so that the bottom
surface of the upper stem weldment is approximately 0.06" (1.5 mm) above the bottom of the
actuator stem.
B. Refer to the valve specification sheet for the required valve travel. With the actuator fully
open and the valve seated, adjust the position of the stem clamp on the valve stem so that
the distance from the bottom of the actuator stem to the top surface of the stem clamp is
equal to the desired travel. Tighten the setscrew in the stem clamp to 15 ft-lb (20 Nm). Note
that, for proper seating to occur, the available travel of the actuator must be larger than the
required valve travel.
C. Connect an air line to the NPT connection in the upper diaphragm casing. Slowly increase air
pressure and allow the bottom of the actuator stem to contact the stem clamp on the valve
stem. Do not permit air pressure to exceed 80 psig (5.5 bar).
WARNING! Never exceed the actuator allowable air pressure rating. Property
damage, injury or death may occur.
D. Pull up the stem lock plate and install the four 7/16"-14 socket head cap screws (Item 23)
with lockwashers (Item 24). Torque the cap screws to 24 ft-lb (33 Nm). Maintain parallelism
between the stem lock plate and the upper stem flange.
E. If necessary, adjust the position of the indicator plate (Item 8 on the assembly drawing).
2.3.2 Direct-Seated Valve With Backseat
The stem connector is assembled in the same manner as detailed in Section 2.3.1 except that, in
Step B, adjust the air pressure so that the actuator stem is approximately 1/8" (3 mm) away from
the fully open position. Some trial-and-error adjustment of the position of the stem clamp on the
valve stem may be required to assure that proper mainseat and backseat contact is achieved.

COPES-VULCAN INSTRUCTION MANUAL
MODEL 700 DIRECT-ACTING ACTUATOR
Rev.5 (08/10) Page 8 of 20 Form 01:P224:37
2.3 STEM CONNECTOR AND TRAVEL ADJUSTMENT (CONT’D.)
2.3.3 Reverse-Seated Valve
A reverse-seated valve is closed by applying upward force on the valve stem.
For the case of a reverse-seated valve where a valve backseat is not present, the actuator will be
set up so that downward, or opening, motion of the valve stem is limited by the internal stop in the
actuator and upward, or closing, motion of the stem will be limited by the valve mainseat.
A. Place the stem lock plate over the valve stem, then thread the stem clamp (Item 27) fully onto
the valve stem. Thread the upper stem weldment (Item 22) onto the actuator stem (Item 16)
so that the bottom surface of the upper stem weldment is approximately 0.06" (1.5 mm)
above the bottom of the actuator stem.
B. Position the valve stem to the full open position. Tighten the packing nuts as necessary to
hold the valve stem in this position. The full open position can be established by first pulling
the valve stem up to the seated position, then lowering the stem by an amount equal to the
travel given on the valve specification sheet.
C. Apply sufficient air pressure so that the actuator stem is fully extended, but do not exceed 80
psig (5.5 bar).
WARNING! Never exceed the actuator allowable air pressure rating. Property
damage, injury or death may occur.
Rotate the stem clamp up on the valve stem so that contact is made with the bottom of the
actuator stem. Pull up the stem lock plate and install the four 7/16"-14 socket head cap
screws (Item 23) with lockwashers (Item 24). Torque the cap screws to 24 ft-lb (33 Nm).
Maintain parallelism between the stem lock plate and the upper stem flange.
D. If necessary, adjust the position of the indicator plate (Item 8 on the assembly drawing).

COPES-VULCAN INSTRUCTION MANUAL
MODEL 700 DIRECT-ACTING ACTUATOR
Rev.5 (08/10) Page 9 of 20 Form 01:P224:37
2.3 STEM CONNECTOR AND TRAVEL ADJUSTMENT (CONT’D.)
2.3.4 Tandem Trim Valves
Assembly of the stem connector for a tandem trim valve is similar to that for a normal direct-seated
valve except that, due to the presence of an internal valve spring, which tends to prevent the valve
from seating, a trial-and-error procedure in which the stem clamp is successively moved up on the
valve stem will be necessary. Proceed as follows:
A. Referring to the assembly drawing, place the stem lock plate (Item 28) over the valve stem,
then thread the stem clamp (Item 27) fully on the valve stem thread. Thread the upper stem
weldment (Item 22) onto the actuator stem (Item 16) so that the bottom surface of the upper
stem weldment is approximately 0.06" (1.5 mm) above the bottom of the actuator stem.
B. Loosen the packing nuts and allow the valve stem to position itself against the valve pilot
spring. Mark the location of the valve stem.
C. With the actuator stem fully retracted, rotate the stem clamp so that the distance from the
bottom of the actuator stem to the top surface of the stem clamp is less than the required
valve travel. Then, pressurize the actuator so that the actuator stem contacts the valve stem
clamp and causes the valve to seat.
WARNING! Never exceed the actuator allowable air pressure rating. Property
damage, injury or death may occur.
Mark the valve stem position. Release the air pressure from the actuator so that the actuator
stem is fully retracted. The inner plug travel is the difference between the two marked
locations.
D. With the valve positioned against the pilot spring as in Step B and the actuator fully retracted,
set the distance between the bottom of the actuator stem and the stem clamp equal to the
required travel minus the inner plug travel minus 1/8" (3 mm).
E. If necessary, adjust the position of the indicator plate (Item 8 on the assembly drawing).

COPES-VULCAN INSTRUCTION MANUAL
MODEL 700 DIRECT-ACTING ACTUATOR
Rev.5 (08/10) Page 10 of 20 Form 01:P224:37
2.4 SPRING ADJUSTMENT
The spring was properly adjusted at the factory and, unless the actuator has been disassembled,
only minor adjustments should be necessary.
The initial spring preload (or bench-set) pressure is defined as the pressure at which stem motion
is initiated and is set by rotating the spring adjuster (Item 21). Rotate the spring adjuster upward in
the actuator yoke to increase the initial spring compression. Spring preload should be set to the
value given in the valve specification sheet.
The preload should be set with the stem packing loose or not installed since the value given in the
valve specification sheet is based on the assumption that there is no friction. If friction or valve
pressure is present, the following procedure should be applied:
A. Install an accurate pressure gage on the actuator air line.
B. Slowly pressurize the actuator and record the gage pressure at a point near mid-travel.
Continue to increase pressure so that the valve travels past mid-travel.
C. Slowly decrease air pressure and read the gage pressure when the valve reaches the open
position at which the previous pressure reading was made.
D. The friction force in terms of actuator pressure is equal to one-half the difference in the two
pressure readings.
E. Add this pressure to the value given in the valve specification sheet to obtain the new
precompression pressure. For example, if the opening and closing pressure readings were
36 and 30 psig (2.5 and 2.1 bar) respectively and the value in the valve specification sheet
was 6 psig (0.4 bar), then the target precompression pressure would be 9 psig (0.6 bar).
2.5 AIR CONNECTION
Accessories such as a positioner, air regulator, etc. will normally be assembled at the factory, and
the only air connection required at installation will be the supply line to the air regulator.
The size 100, 160, and 160-5 actuators will normally have 3/8" x 1/4" and 1/2" x 1/4" bushings
installed in the diaphragm cover. To increase stroking speed, such as when a volume booster is
employed, these bushings may be removed and a larger tubing line installed.

COPES-VULCAN INSTRUCTION MANUAL
MODEL 700 DIRECT-ACTING ACTUATOR
Rev.5 (08/10) Page 11 of 20 Form 01:P224:37
3.0 MAINTENANCE
3.1 GENERAL
Actuator parts are subject to normal wear and must be inspected and replaced when necessary.
The frequency of inspection and part replacement depends on the severity of the service
conditions. Normally, only the diaphragm will require replacement.
3.2 PRECAUTIONS
Be aware that large pressure and spring forces are required to actuate a valve. Sudden release of
these forces or of valve or actuator pressure has the potential to cause personal injury or damage
to property.
Before starting to disassemble the actuator, proceed as follows:
A. Isolate the valve from the line pressure.
B. Release fluid pressure from the valve.
C. Release air pressure from the diaphragm chamber of the actuator.
D. Remove all actuator spring preload. Note that, if the actuator travel has been set up to be
less than nominal, it may not be possible to remove all preload with the spring adjuster alone.
In this case, it will be necessary to disassemble the stem connector to remove the remaining
spring preload.
3.3 DIRECT-ACTING ACTUATOR (Refer to Figure 1 and the Actuator Assembly Drawing)
3.3.1 Disassembly
A. Bypass or isolate the valve and reduce the diaphragm pressure to atmospheric.
B. Rotate the spring adjuster (Item 21) downward on the actuator stem until all spring preload is
removed.
C. If necessary, remove the stem connector by removing the four socket head cap screws
(Item 23). Loosen the setscrew in the stem clamp (Item 27) and remove the stem clamp from
the actuator stem.
D. If necessary, remove the actuator from the valve by unthreading the hold-down nut or studs
and nuts, as applicable.
E. Remove the hex head cap screws (Item 4) and hex nuts (Item 5) and remove the cover
(Item 3).

COPES-VULCAN INSTRUCTION MANUAL
MODEL 700 DIRECT-ACTING ACTUATOR
Rev.5 (08/10) Page 12 of 20 Form 01:P224:37
3.3 DIRECT-ACTING ACTUATOR (Refer to Figure 1 and the Actuator Assembly Drawing)
3.3.1 Disassembly (Cont’d.)
F. If the diaphragm is not being replaced, remove the stem and diaphragm plate assembly
(Items 11, 12, 13, 14, and 16). If the diaphragm is being replaced, unscrew the flat head
screw (Item 11), then remove the diaphragm stop (Item 12), the diaphragm (Item 14), and the
diaphragm plate (Item 13).
G. If necessary, remove the actuator stem (Item 16), the spring (Item 15), the spring plate
(Item 17), and the thrust washer (Item 18).
H. If necessary, remove the base (Item 2) by removing the hex head cap screws (Item 7) and
lockwashers (Item 10).
3.3.2 Assembly
A. If the diaphragm is being replaced, apply gasket compound (CV P/N 197077 or equivalent) to
the surface of the diaphragm (Item 14) where the diaphragm stop (Item 12) seats. Assemble
the diaphragm, diaphragm plate (Item 13), and diaphragm stop to the actuator stem (Item 16)
using the flat head screw (Item 11). Torque the flat head screw to the value shown on the
assembly drawing.
B. Install the spring adjuster (Item 21) in the yoke (Item 1).
C. Assemble the base (Item 2) to the yoke using hex head cap screws (Item 7) and lockwashers
(Item 10). Torque the screws to the value given on the assembly drawing.
D. Place the thrust washer (Item 18), the spring plate (Item 17), and the spring (Item 15) in the
yoke.
E. Place the stem assembly in the yoke and through the spring plate and thrust washer. Align
the bolt holes in the diaphragm with the bolt holes in the base.
F. Place the cover (Item 3), with bushing (Item 41) when required, on the base and install the
hex head cap screws (Item 4), hex nuts (Item 5), and eyebolts (Item 6). Torque the fasteners
to the value on the assembly drawing.
G. Place the upper stem weldment (Item 22) on the stem so that the bottom surface of the upper
stem weldment is approximately 0.06" (1.5 mm) above the bottom of the stem.
H. After the actuator is mounted on a valve, place the stem lock plate (Item 28) over the valve
stem, then install the stem clamp (Item 27) on the valve stem. Position the stem clamp as
required for valve seating and travel, then tighten the setscrew in the stem clamp. Install the
socket head cap screws (Item 23) with lockwashers (Item 24). Torque the fasteners to the
value on the assembly drawing.

COPES-VULCAN INSTRUCTION MANUAL
MODEL 700 DIRECT-ACTING ACTUATOR
Rev.5 (08/10) Page 13 of 20 Form 01:P224:37
3.3 DIRECT-ACTING ACTUATOR (Refer to Figure 1 and the Actuator Assembly Drawing)
3.3.2 Assembly (Cont’d.)
I. Drill holes in the yoke as directed by the assembly drawing, then install the indicator plate
(Item 8) and ID plate (Item 19) using drive screws (Item 20).
J. Apply preload to the spring by rotating the spring adjuster.
K. Cycle the actuator slowly several times to verify that no binding occurs during operation.
Pressurize the actuator from 80 to 100 psig (5.5 to 7 bar) and check for leaks. Binding, noise
or leakage is not acceptable.
3.4 TOP-MOUNTED HANDWHEEL ASSEMBLY (Refer to Figure 2)
3.4.1 Disassembly
A. Remove the hex nuts and lockwashers (Items A4 and A5). Remove the housing (Item A3).
B. If necessary, remove the gasket (Item A2).
C. Remove the retaining ring (Item A10), then remove the thrust base (Item A9) and thrust
washer (Item A8).
D. If necessary, remove the handwheel (Item A14) and key (Item A13) by first removing the
upper retaining ring (Item A12).
E. Remove the actuator stem (Item A7) from the housing (Item A3).
F. Remove the U-cup seal (Item A6) from the housing.
G. Proceed with actuator disassembly per Paragraph 3.3.1, if required.
3.4.2 Assembly
A. Assemble the actuator per Steps A through F in Paragraph 3.3.2.
B. Apply gasket compound (CV P/N 197077 or equivalent) to both surfaces of the gasket
(Item A2), then place the gasket onto the cover assembly (Item A1).
C. Place the thrust washer (Item A8) and thrust base (Item A9) on the actuator stem (Item A7),
then install the retaining ring (Item A10).
D. Apply o-ring grease to the U-cup seal (Item A6). Install the U-cup seal in the housing
(Item A3) with the ‘U’ facing down.

COPES-VULCAN INSTRUCTION MANUAL
MODEL 700 DIRECT-ACTING ACTUATOR
Rev.5 (08/10) Page 14 of 20 Form 01:P224:37
3.4 TOP-MOUNTED HANDWHEEL ASSEMBLY (Refer to Figure 2)
3.4.2 Assembly (Cont’d.)
E. Carefully push the actuator stem assembly through the U-cup seal and thread the stem fully
into the housing.
F. Place the housing assembly onto the cover assembly and install the lockwashers (Item A4)
and hex nuts (Item A5). Torque the nuts to the value shown on the assembly drawing.
G. Thread the jam nut (Item A11) on the stem, then install the lower retaining ring (Item A12),
the handwheel (Item A14), the key (Item A13), and the upper retaining ring (Item A12).
H. Continue with assembly per Steps G through K in Paragraph 3.3.2.
3.5 ADJUSTABLE UP/DOWN TRAVEL STOP (Refer to Figure 4)
3.5.1 Disassembly
A. Remove the wing nut (Item 43), the lockwasher (Item 44), the flat washer (Item 45), and the
cover assembly (Item 42).
B. Remove the upper threaded collar (Item 37)
C. If necessary, remove the hex nut (Item E11) and cover stud (Item E10).
D. Remove the four hex bolts (Item E7) and lockwashers (Item E6), then remove the stop plate
(Item E9) and four spacers (Item E8).
E. Remove the lower threaded collar (Item 37).
F. If necessary, remove the base plate (Item E3) and gasket (Item E2) by first removing the six
hex nuts (Item E5) and lockwashers (Item E4).
G. If necessary, remove the U-cup seal (Item E12) from the base plate.
H. Proceed with actuator disassembly per Paragraph 3.3.1, if required.
3.5.2 Assembly
A. Assemble the actuator per Steps A through F in Paragraph 3.3.2.
B. Apply gasket compound (CV P/N 197077 or equivalent) to both surfaces of the gasket
(Item E2), then place the gasket onto the cover assembly (Item E1).

COPES-VULCAN INSTRUCTION MANUAL
MODEL 700 DIRECT-ACTING ACTUATOR
Rev.5 (08/10) Page 15 of 20 Form 01:P224:37
3.5 ADJUSTABLE UP/DOWN TRAVEL STOP (Refer to Figure 4)
3.5.2 Assembly (Cont’d.)
C. Apply o-ring grease to the U-cup seal (Item E12), then install the U-cup seal in the base
plate (Item E3) with the ‘U’ facing down.
D. Place the base plate assembly over the stop stem and onto the cover. Install the
lockwashers (Item E4) and hex nuts (Item E5). Torque the nuts to the value shown on the
assembly drawing.
E. If an up stop is required, thread the threaded collar (Item 37) onto the stop stem.
F. Assemble the spacers (Item E8), stop plate (Item E9), lockwashers (Item E6), and hex bolts
(Item E7). Torque the bolts to the value shown on the assembly drawing.
G. If a down stop is required, thread the threaded collar (Item 37) onto the stop stem.
H. Thread the cover stud (Item E10) with hex nut (Item E11) into the stop plate, then torque the
nut.
I. Install the cover assembly (Item 42), the flat washer (Item 45), the lockwasher (Item 44), and
the wing nut (Item 43).
J. After the actuator is attached to the valve, set the positions of the threaded collar(s).
K. Continue with assembly per Steps G through K in Paragraph 3.3.2.
3.6 FIXED TRAVEL STOPS (Refer to Drawing D-360436)
Assembly and disassembly of the direct-acting actuator with travel stops is the same as described
in Paragraph 3.3 except that the hex head cap screws (Item 7) are replaced with hexagonal
fasteners with customized length.
3.7 SIDE-MOUNTED HANDWHEEL (Refer to Figure 3)
3.7.1 Disassembly
A. With the handwheel in the open position, remove the cover cap (Item 48), cover nipple
(Item 47), and threaded collar (Item 37).
B. Remove the socket head cap screws (Item C12), lockwashers (Item C13), and top plate
(Item C10).
C. If necessary, remove the handwheel (Item C20) from the worm shaft (Item C16) by removing
the retaining rings (Item C19) and handwheel key (Item C18).

COPES-VULCAN INSTRUCTION MANUAL
MODEL 700 DIRECT-ACTING ACTUATOR
Rev.5 (08/10) Page 16 of 20 Form 01:P224:37
3.7 SIDE-MOUNTED HANDWHEEL (Refer to Figure 3)
3.7.1 Disassembly (Cont’d.)
D. Remove the two remaining retaining rings (Item C19), remove the two worm shaft bearings
(Item C17), then rotate and remove the worm shaft (Item C16).
E. Lift the threaded sleeve weldment (Item C11) and worm gear (Item C14) subassembly from
the gear housing (Item C9).
F. Remove the socket head cap screws (Item C6), hex nuts (Item C8) and lockwashers
(Item C7), then remove the gear housing from the clearance chamber (Item C3).
G. Remove the clearance chamber (Item C3) by unthreading the hex nuts (Item C5) and
lockwashers (Item C4).
H. If necessary, remove the handwheel actuator stem (Item 11) by unthreading the stem from
actuator stem.
3.7.2 Assembly
A. Assemble the actuator per Steps A through F in Paragraph 3.3.2, except, in Step A, install
the handwheel actuator stem (Item 11) instead of the flat head screw (Item 11 in Figure 1).
Torque the stem to the value shown on the assembly drawing.
B. To assemble the handwheel, follow the steps in Paragraph 3.7.1 in reverse order. Apply
grease to the worm gear teeth and the threaded sleeve weldment threads. For assembly
torques, refer to the assembly drawing.
C. Set the position of the threaded collar so that, when the actuator is open and the handwheel
is in the open position, there is gap of approximately 0.06" (1.5 mm) between the threaded
collar and the threaded sleeve weldment (Item C11).

COPES-VULCAN INSTRUCTION MANUAL
MODEL 700 DIRECT-ACTING ACTUATOR
Rev.5 (08/10) Page 17 of 20 Form 01:P224:37
Figure 1

COPES-VULCAN INSTRUCTION MANUAL
MODEL 700 DIRECT-ACTING ACTUATOR
Rev.5 (08/10) Page 18 of 20 Form 01:P224:37
Figure 2

COPES-VULCAN INSTRUCTION MANUAL
MODEL 700 DIRECT-ACTING ACTUATOR
Rev.5 (08/10) Page 19 of 20 Form 01:P224:37
Figure 3

COPES-VULCAN INSTRUCTION MANUAL
MODEL 700 DIRECT-ACTING ACTUATOR
Rev.5 (08/10) Page 20 of 20 Form 01:P224:37
Figure 4
Table of contents
Popular Controllers manuals by other brands
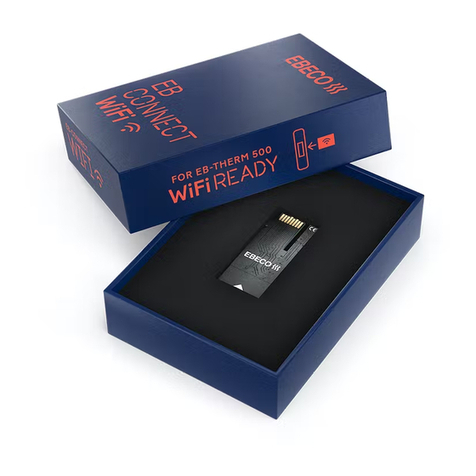
EBECO
EBECO EB-Connect WiFi manual
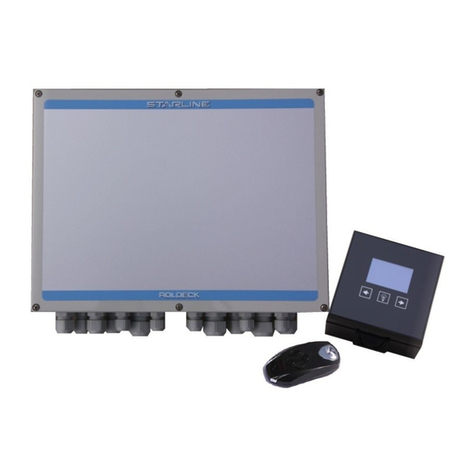
Starline
Starline ROLDECK CONTROL RD 2013 manual
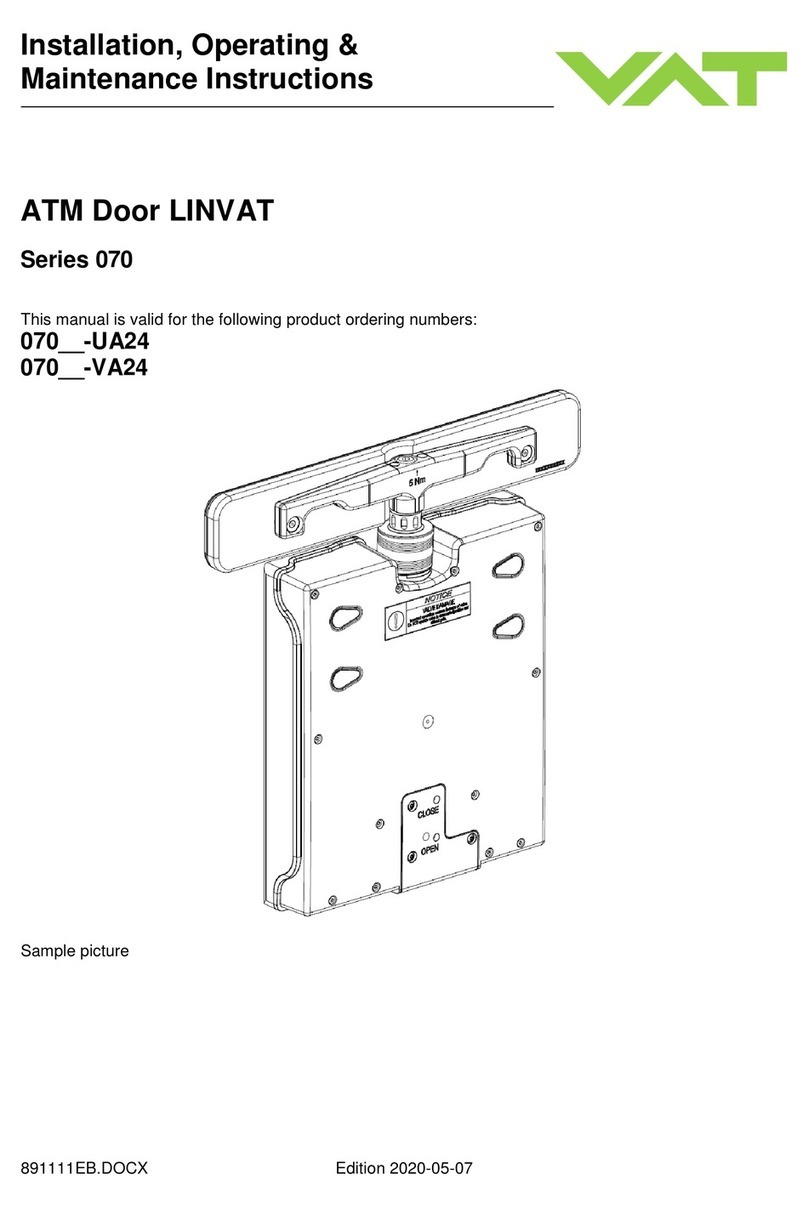
VAT
VAT LINVAT 070 Series Installation, operating, & maintenance instructions
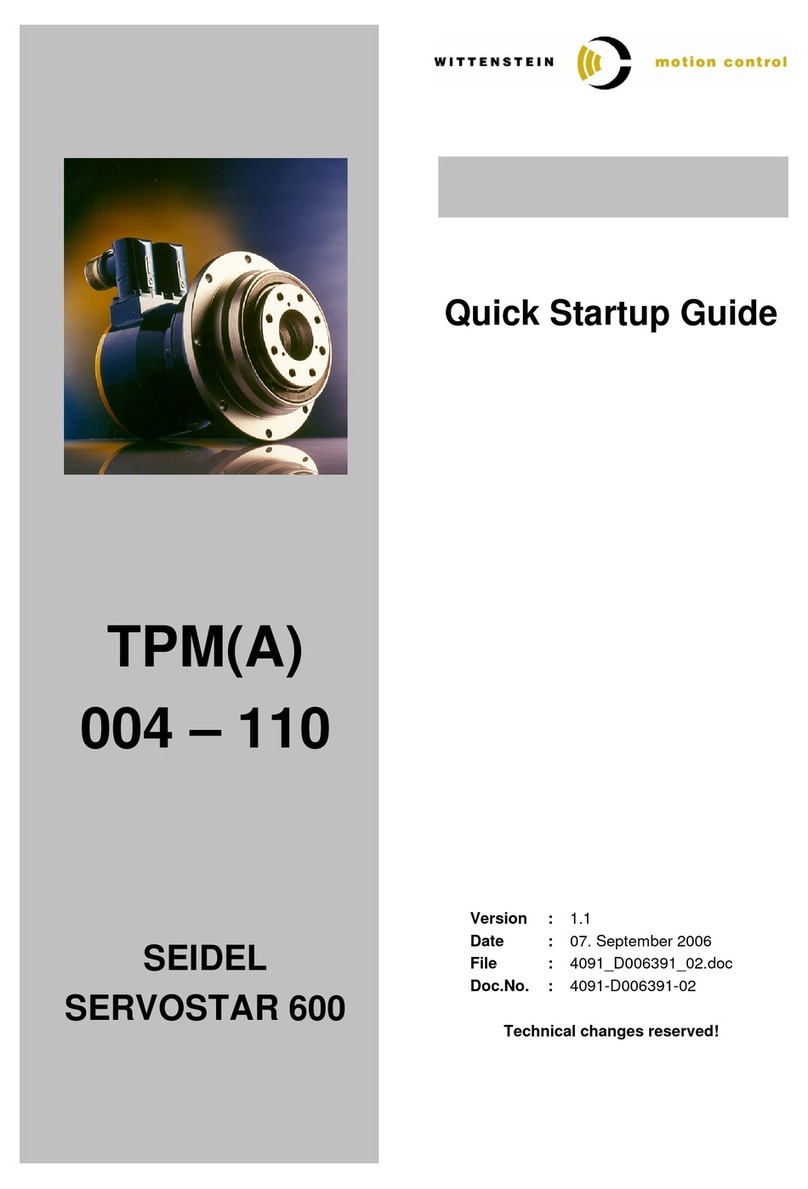
Wittenstein
Wittenstein TPM Series Quick start up guide
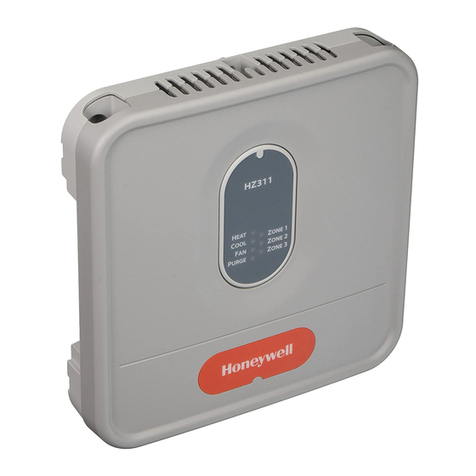
Honeywell
Honeywell TrueZONE HZ311 manual
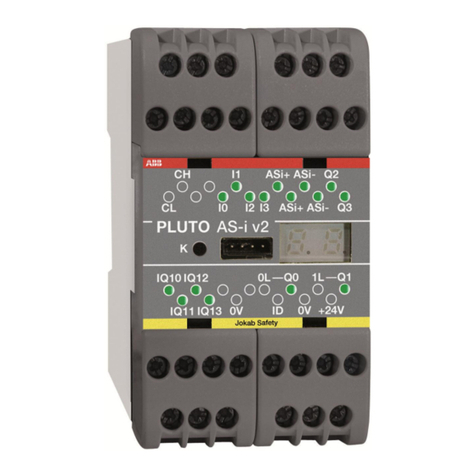
ABB
ABB PLUTO Safety-PLC operating instructions