CTI FB800E User manual

«
-
GSD
8
uiuiii
*
*
*
*
*
*
**
***
***
*
*
*
*
***
***
*
FB
600
E
*
*
*
*
t
k
k
STATIC
RELAY
*
k
INSTRUCTION
MANUAL
*
*
*
*
*
*
*
*
*
**
*
*
*
*
**
*
*
*
**
*
***
*
Carriere
Technical
Industries
Division
of
Derlan
Manufacturing
Inc
.
5621
Finch
Ave
.
E
.
Scarborough
,
Ontario
Canada
Tel
:
Fax
:
M
1
B
2
T
9
(
416
)
297
-
8738
(
416
)
297
-
0421
Part
No
.
FB
600
E
-
M
01
/
91
(
1601
-
0027
)
Rev
.
D
6
Courtesy of NationalSwitchgear.com

FB
600
E
INSTRUCTION
MANUAL
TABLE
OF
CONTENTS
f
1.0
INTRODUCTION
1.1
PRODUCT
DESCRIPTION
1.2
FEATURES
1.3
ACCURACY
1.4
MAXIMUM
INPUTS
.
.
1.5
ENVIRONMENT
.
.
.
.
2
2
4
4
4
2.0
INSTALLATION
2.1
PHYSICAL
DIMENSIONS
2.2
MOUNTING
2.3
EXTERNAL
CONNECTIONS
2.3
.
1
No
Ground
Fault
Detection
2.3
.
2
Zero
Sequence
Ground
Fault
2.3
.
3
Solidly
Grounded
3
Wire
System
/
Residual
Ground
Fault
2.3
.
4
Solidly
Grounded
4
Wire
/
Residual
Ground
Fault
.
.
2.4
CURRENT
TRANSFORMERS
2.5
ACTUATOR
2.6
SYSTEM
GROUNDING
5
6
7
7
8
9
10
11
12
12
3.0
SETUP
AND
OPERATION
3.1
COMMISSIONING
JUMPER
.
.
-
.
3.2
INSTANTANEOUS
TRIP
SETTINGS
3.3
SHORT
TIME
OVERLOAD
SETTINGS
3.4
LONG
TIME
SETTINGS
.
.
.
.
3.5
GROUND
FAULT
SETTINGS
.
.
.
1
13
13
15
16
19
4.0
TESTING
4.1
SECONDARY
INJECTION
TESTING
4.2
PRIMARY
INJECTION
TESTING
.
4.3
INSTANTANEOUS
TRIP
TESTING
4.4
SHORT
TIME
OVERLOAD
TESTING
4.5
LONG
TIME
OVERLOAD
TESTING
4.6
GROUND
FAULT
TESTING
.
..
4.7
FINAL
SETTING
TEST
...
.
22
25
25
25
26
26
27
1
Courtesy of NationalSwitchgear.com

1.0
INTRODUCTION
7
1.1
PRODUCT
DESCRIPTION
The
FB
600
E
is
a
static
.
trip
relay
used
to
cause
a
low
voltage
breaker
to
open
under
fault
conditions
.
Its
primary
application
is
as
a
retrofit
to
600
volt
breakers
for
upgrading
existing
protection
.
By
using
special
CT
'
s
with
both
1
amp
signal
windings
and
a
separate
power
winding
,
the
FB
600
E
relay
requires
no
control
power
to
operate
.
An
output
pulse
from
the
FB
600
E
relay
is
used
to
drive
an
actuator
which
causes
the
breaker
to
trip
.
The
FB
600
E
will
trip
on
overloads
with
separately
adjustable
,
instan
-
taneous
,
short
time
and
long
time
pickup
levels
.
The
short
and
long
delay
times
are
also
adjustable
.
A
long
time
pickup
LED
is
provided
to
assist
in
verifying
the
pickup
threshold
.
To
help
determine
the
cause
of
trip
,
an
indicator
is
provided
for
instantaneous
,
or
short
time
,
trip
and
'
a
separate
indicator
is
used
for
long
time
trip
.
Also
included
with
the
FB
600
E
is
a
ground
fault
trip
and
a
latched
ground
fault
indicator
to
diagnose
the
cause
of
trip
.
1.2
FEATURES
INSTANTANEOUS
OVERLOAD
4
2
/
4
/
6
/
8
/
10
/
12
times
CT
rating
or
defeat
50
ms
maximum
at
>
150
%
of
pickup
setting
(
peak
detector
)
100
ms
maximum
at
>
150
%
of
pickup
setting
(
phase
signal
averaging
)
Pickup
Level
:
Pickup
Time
:
SHORT
TIME
OVERLOAD
Pickup
Level
:
2.5
/
3
/
3.5
/
4
/
4.5
/
5
/
5.5
/
6
/
6.5
/
7
/
7.5
/
8
/
8.5
/
9
/
9.5
/
10
times
CT
rating
or
defeat
Pickup
Time
:
0.15
/
0.25
/
0.4
seconds
at
>
150
%
of
pickup
threshold
LONG
TIME
OVERLOAD
Pickup
Level
:
0.5
/
.
55
/
.
6
/
.
65
/
.
7
/
.
75
/
.
8
/
.
85
/
.
9
/
.
95
/
1
/
1.05
/
1.1
/
1.15
/
1.2
/
1.25
times
CT
rating
or
defeat
Pickup
Time
:
2.5
/
5
/
7.5
/
10
/
12.5
/
15
/
17.5
/
20
seconds
at
6
times
pickup
level
.
Other
times
vary
as
current
squared
.
Actual
times
for
any
overload
condition
can
be
determined
from
the
time
/
overcurrent
curves
,
(
see
fig
.
3.5
)
2
Courtesy of NationalSwitchgear.com

GROUND
FAULT
TRIP
Methods
of
ground
fault
detection
with
the
FB
600
E
are
as
follows
:
Solidly
grounded
3
phase
,
3
wire
systems
.
Residual
connection
(
figure
2.4
)
Solidly
grounded
3
phase
,
3
wire
systems
.
Zero
sequence
connection
(
figure
2.3
)
Solidly
grounded
3
phase
,
4
wire
systems
.
Residual
connection
plus
an
additional
CT
in
the
neutral
conductor
(
figure
2.5
)
Resistance
grounded
3
phase
,
4
wire
systems
.
Use
only
the
zero
sequence
connection
(
figure
2.3
)
a
)
b
)
c
)
d
)
Pickup
Level
:
a
)
ZERO
SEQUENCE
(
SEPARATE
CT
)
.
1
/
.
2
/
.
3
/
.
4
/
.
5
/
.
6
/
.
7
/
.
8
times
G
/
F
CT
rating
or
defeat
i
or
b
)
RESIDUAL
GROUND
FAULT
(
PHASE
CT
SECONDARY
SENSING
)
.
1
/
.
2
/
.
3
/
.
4
/
.
5
/
.
6
/
.
7
/
.
8
times
phase
CT
primary
rating
or
defeat
0.05
sec
minimum
/
0.12
/
0.2
/
0.4
seconds
at
>
150
%
of
pickup
threshold
Pickup
Time
:
*
INDICATORS
i
\
i
:
Long
time
pickup
LED
on
while
long
time
pickup
level
exceeded
.
Latched
instantaneous
or
short
time
trip
indicator
.
Latched
long
time
trip
indicator
.
Latched
ground
fault
trip
indicator
!
i
•
i
I
i
•
TRIP
INDICATORS
Fault
indicators
are
provided
to
determine
the
cause
of
trip
.
Each
indicator
remains
set
after
a
trip
loss
of
control
power
.
Indicators
are
automatically
reset
when
a
load
of
>
40
%
of
the
CT
rating
is
re
-
applied
to
the
breaker
.
i
•
i
i
Instantaneous
/
Short
Time
:
set
if
the
instantaneous
pickup
level
has
been
exceeded
for
50
ms
maximum
(
peak
detector
)
,
100
ms
maximum
(
phase
signal
averaging
)
or
the
short
time
pickup
level
has
been
exceeded
for
the
selected
delay
time
.
Long
Time
:
set
if
the
long
time
or
short
time
pickup
level
has
been
exceeded
for
the
selected
delay
time
.
Ground
Fault
:
set
if
the
ground
fault
pickup
level
has
been
exceeded
for
the
selected
ground
fault
delay
time
.
)
J
3
Courtesy of NationalSwitchgear.com

1.3
ACCURACY
V
Long
Time
/
Short
Time
/
Instantaneous
/
Ground
Fault
pickup
level
:
+
/
-
10
%
Long
/
Short
/
Ground
Fault
trip
time
:
+
/
-
20
%
at
>
150
%
of
pickup
threshold
50
ms
maximum
at
>
150
%
of
pickup
level
(
when
100
ms
maximum
at
>
150
%
of
pickup
level
Instantaneous
trip
:
configured
as
peak
detector
)
,
(
when
configured
as
phase
signal
averaging
)
.
Stated
accuracy
applies
over
the
full
operating
range
of
-
25
to
+
60
°
C
.
CT
input
is
a
50
/
60
Hz
sinewave
.
1.4
MAXIMUM
INPUTS
Phase
/
Ground
Fault
CT
'
s
:
(
terminals
1
/
5
,
2
/
5
,
3
/
5
,
4
/
5
)
4
amps
input
from
secondary
.
.
.
continuous
20
times
rated
current
.
.
.
!
second
1.5
ENVIRONMENT
Operating
temperature
range
:
-
25
°
C
to
+
60
°
C
a
4
Courtesy of NationalSwitchgear.com

2.0
INSTALLATION
•
V
2.1
PHYSICAL
DIMENSIONS
The
FB
600
E
is
housed
in
a
metal
chassis
with
a
hinged
cover
to
protect
its
components
yet
allow
access
to
the
setting
selector
switches
.
Figure
2.1
shows
the
physical
dimensions
of
the
FB
600
E
.
Four
threaded
holes
are
provided
on
-
the
base
to
accept
8
-
32
x
1
/
4
"
screws
for
mounting
the
FB
600
E
to
the
breaker
chassis
.
If
this
orientation
is
not
convenient
other
mounting
holes
must
be
drilled
to
suit
the
mounting
scheme
.
FB
600
E
PHYSICAL
DIMENSIONS
Figure
2.1
8
-
32
-
THflEAO
I
K
in
m
-
<
r
-
<
P
-
I
5.1
"
2.2
"
6.0
“
8.6
"
FB
6
Q
0
E
RELAY
i
5
Courtesy of NationalSwitchgear.com

2.2
MOUNTING
r
To
allow
access
to
selector
switch
settings
,
a
hinged
cover
with
a
spring
release
catch
is
provided
.
This
allows
pickup
levels
and
time
delays
to
be
quickly
set
or
modified
without
the
need
of
tools
.
When
mounting
the
FE
600
E
,
provision
should
be
made
for
the
cover
to
partially
open
to
allow
access
to
the
selector
switches
.
The
latched
trip
indicators
and
external
wiring
terminals
are
mounted
outside
the
hinged
cover
.
Orient
the
relay
on
the
breaker
to
allow
access
to
the
terminal
block
for
relay
testing
and
to
ensure
that
the
indicators
are
visible
when
the
breaker
is
drawn
out
.
?
6
Courtesy of NationalSwitchgear.com

ij
iot
>
ya
ST
*
2.3
EXTERNAL
CONNECTION
^
6
*
2.0
Sic
‘
External
wiring
of
the
FB
600
E
will
depend
on
the
grounding
scheme
used
.
2.3
.
1
No
Ground
Fault
Detection
:
The
simplest
wiring
configuration
is
the
FB
600
E
connected
to
detect
short
circuit
and
overloads
but
no
ground
faults
as
shown
in
figure
2.2
.
Each
of
the
specially
wound
phase
current
transformers
(
CT
'
s
)
has
a
signal
winding
and
a
.
power
winding
thus
eliminating
the
need
for
an
external
control
power
source
.
When
a
trip
condition
occurs
,
a
short
pulse
is
provided
to
the
spring
loaded
actuator
which
triggers
the
breaker
to
open
.
The
CT
signal
winding
common
(
terminals
)
may
be
externally
connected
to
ground
.
However
,
the
power
winding
common
terminal
(
10
)
and
actuator
terminals
(
11
,
12
)
must
not
be
externally
grounded
or
connected
to
signal
common
(
5
)
on
the
FB
600
E
or
it
will
not
operate
correctly
.
Fig
.
2.2
EXTERNAL
WIRING
FOR
NO
GROUND
FAULT
DETECTION
30
SUPPLY
BREAKER
111
Wh
i
te
<
2
T
2
}
-
BREAKER
ACTUATOR
OUTPUT
MR
500
ACTUATOR
f
Rea
<
^
~
T
]
01
SIGNAL
01
C
/
T
$
2
]
02
SIGNAL
02
C
/
T
FB
60
DE
~
3
~
|
03
SIGNAL
~
5
~
~
]
S
IGNAL
COM
.
$
03
C
/
T
jT
]
G
.
F
.
SIGNAL
6
L
1
<
01
}
L
1
C
0
2
D
L
1
C
0
3
D
L
1
CG
.
FO
7
V
V
V
LOAD
L
2
10
*
00
NOT
EXTERNALLY
GROUND
L
2
CTEEM
INAL
1
Gj
7
Courtesy of NationalSwitchgear.com

*
•
V
•
'
I
-
TT
'
—
2.3
.
2
Zero
Sequence
Ground
Fault
:
solidly
grounded
3
wire
systems
,
where
the
On
resistance
grounded
or
phase
conductors
run
in
a
cable
outside
the
breaker
,
the
zero
sequence
ground
fault
detection
scheme
can
be
used
(
figure
2.3
)
.
The
cable
passes
through
the
window
of
a
separate
CT
outside
the
breaker
which
senses
the
zero
sequence
component
of
the
3
currents
.
If
a
ground
shield
is
present
in
the
3
phase
cable
,
it
must
pass
outside
the
window
CT
.
v
?
y
,
of
the
ground
fault
sensing
is
detected
,
the
3
phase
currents
instan
-
Providing
no
ground
fault
taneously
sum
to
zero
and
there
is
no
CT
output
.
Under
ground
fault
this
CT
generates
a
signal
and
power
for
the
FB
600
E
.
The
to
this
external
CT
is
v
;
*
-
a
4
extra
breaker
connecting
fingers
.
conditions
,
wiring
The
CT
signal
winding
common
(
terminals
)
may
be
externally
connected
to
ground
.
However
,
the
power
winding
common
terminal
(
10
)
and
actuator
terminals
(
11
,
12
)
must
not
be
externally
grounded
or
connected
to
signal
common
(
5
)
on
the
FB
600
E
or
it
will
not
operate
correctly
.
EXTERNAL
WIRING
FOR
ZERO
SEQUENCE
GROUND
FAULT
DETECTION
Fig
.
2.3
30
SUPPLY
BREAKER
wn
i
te
T
2
\
-
BREAKER
ACTUATOR
TTL
OUTPUT
MR
60
Q
.
ACTUATOR
*
;
*
Hea
2
~
1
~
|
01
SIGNAL
T
01
C
/
T
T
]
02
SIGNAL
©
02
ic
:
FBBDQE
c
/
r
~
5
~
l
03
SIGNAL
T
]
SIGNAL
COM
.
T
03
C
/
T
ft
:
T
]
G
.
F
.
SIGNAL
>
f
.
>
f
,
%
V
L
1
0
1
)
L
1
0
23
L
1
0
33
L
1
CG
.
F
.
3
30
CABLE
&
T
©
ZERO
SEQUENCE
L
2
£
A
GF
.
C
/
T
NOTE
-
PASS
NEUTRAL
CONDUCTOR
THROUGH
G
.
F
.
C
/
T
IN
4
WIRE
SYSTEMS
*
00
NOT
EXTERNALLY
GROUND
L
2
C
TERM
INAL
103
LOAD
4
8
Courtesy of NationalSwitchgear.com

2.3
.
3
Solidly
Grounded
3
Wire
System
/
Residual
Ground
Fault
:
In
a
3
wire
system
where
it
is
inconvenient
to
run
the
3
phases
through
(
a
separate
ground
fault
CT
,
the
residual
or
common
return
current
of
the
3
phase
CT
'
s
can
be
sensed
for
ground
fault
detection
as
in
figure
2.4
.
Providing
no
ground
fault
is
present
,
the
3
primary
currents
and
hence
phase
CT
secondary
currents
cancel
to
zero
.
When
a
ground
fault
occurs
,
the
current
that
is
sensed
by
summing
the
return
current
in
each
CT
secondary
is
no
longer
zero
and
the
FB
600
E
will
trip
after
the
appropriate
ground
fault
pickup
level
time
delay
has
been
exceeded
.
The
CT
signal
winding
common
(
terminals
)
may
be
externally
connected
to
ground
.
However
,
the
power
winding
common
terminal
(
10
)
and
actuator
terminals
(
11
,
12
)
must
not
be
externally
grounded
or
connected
to
signal
common
(
5
)
on
the
FB
600
E
or
it
will
not
operate
correctly
.
EXTERNAL
WIRING
FOR
3
WIRE
RESIDUAL
GROUND
FAULT
DETECTION
Fig
.
2.4
30
SUPPLY
BREAKER
Wh
i
te
12
}
-
BREAKER
ACTUATOR
OUTPUT
MRSOO
ACTUATOR
#
i
.
~
T
\
01
SIGNAL
01
C
/
T
IE
<
2
9
~
T
\
02
SIGNAL
f
02
C
/
T
FB
600
E
~
3
~
l
03
SIGNAL
31
G
.
F
.
SIGNAL
-
03
C
/
T
M
Q
\
5
~
]
SIGNAL
COM
rrn
6
L
1
(
0
*
0
L
1
C
02
D
L
1
C
0
3
D
L
1
CG
.
F
.
)
V
V
V
3
LOAD
L
2
10
A
*
DO
NOT
EXTERNALLY
GROUND
L
2
CTERWINAL
10
)
9
Courtesy of NationalSwitchgear.com

2.3
.
4
Solidly
Grounded
4
Wire
/
Residual
Ground
Fault
Sensing
:
In
a
4
wire
system
where
it
is
inconvenient
to
run
the
3
phases
and
neutral
through
a
separate
ground
fault
CT
the
wiring
scheme
of
figure
2.5
can
be
used
.
The
residual
current
in
the
return
wire
of
the
3
phase
CT
'
s
is
sensed
.
Under
unbalanced
conditions
this
current
will
not
be
zero
even
with
no
ground
fault
since
the
residual
current
will
flow
in
the
fourth
neutral
wire
.
Consequently
,
a
separate
CT
of
the
same
ratio
as
the
phase
CT
is
used
to
sense
the
neutral
current
and
is
connected
to
exactly
cancel
the
.
phase
CT
residual
current
.
Now
if
a
ground
fault
occurs
,
the
residual
current
will
no
longer
be
cancelled
by
the
neutral
wire
current
and
the
FB
600
E
will
trip
when
the
appropriate
pickup
level
and
time
delay
is
obtained
.
The
CT
signal
winding
common
(
terminals
)
may
be
externally
connected
to
ground
.
However
,
the
power
winding
common
terminal
(
1.0
)
and
actuator
terminals
(
11
,
12
)
must
not
be
externally
grounded
or
connected
to
signal
common
(
5
)
on
the
FB
600
E
or
it
will
not
operate
correctly
.
Fig
.
2.5
EXTERNAL
WIRING
FOR
4
WIRE
RESIDUAL
GROUND
FAULT
DETECTION
30
SUPPLY
BREAKER
t
'
t
t
,
A
White
12
]
-
BREAKER
ACTUATOR
OUTPUT
<
2
MR
6
QQ
ACTUATOR
Tieo
©
r
~
T
]
0
1
SI
GNAL
01
C
/
T
ii
.
d
T
~
l
02
SIGNAL
:
02
C
/
T
FBBOOE
9
"
IH
03
SIGNAL
2
03
*
C
/
T
K
:
]
G
.
F
.
SIGNAL
4
-
:
GF
.
5
SIGNAL
COM
.
L
1
L
1
L
1
C
0
3
^
L
1
CG
.
FO
£
C
/
T
6
K
:
7
1
1
10
L
2
V
V
V
V
LOAD
*
*
DO
NOT
EXTERNALLY
GROUND
L
2
CJERMINAL
10
}
10
Courtesy of NationalSwitchgear.com

2.4
CURRENT
TRANSFORMERS
t
Any
current
transformer
having
both
a
signal
and
power
winding
can
be
used
with
the
FB
600
E
,
Primary
current
ratios
may
cover
any
range
typically
from
100
to
4000
amps
in
suitable
increments
or
CT
'
s
may
have
several
taps
.
A
few
notes
of
caution
are
in
order
regarding
the
CT
'
s
used
in
conjunction
with
the
FB
600
E
.
These
notes
are
:
The
signal
winding
must
have
an
output
of
1
amp
at
the
rated
primary
current
into
a
nominal
resistive
burden
of
0.5
ohms
.
The
power
winding
should
saturate
below
the
CT
rated
amps
and
provide
approximately
10
VA
max
.
The
zero
sequence
ground
fault
CT
is
similar
to
the
phase
CT
.
The
FB
600
E
power
inputs
will
increase
in
burden
with
increased
power
input
.
At
the
worst
case
,
the
FB
600
E
power
inputs
will
burden
the
power
windings
to
a
point
where
the
burden
voltage
is
100
volts
.
Figure
2.6
describes
the
loading
on
the
power
windings
of
the
CT
'
s
.
If
the
power
windings
of
the
CT
'
s
do
not
limit
(
or
saturate
)
their
power
outputs
as
described
in
(
b
)
,
damage
to
the
FB
600
E
may
.
result
.
Carriere
can
provide
specially
designed
CT
'
s
from
stock
which
will
limit
output
power
from
the
power
windings
.
These
Carriere
CT
'
s
are
available
in
several
ratios
.
Please
contact
the
factory
or
a
Carriere
agent
for
more
information
.
In
order
to
ensure
proper
operation
of
all
FB
600
E
functions
,
the
power
windings
must
be
able
to
provide
(
individually
)
at
least
4.5
VA
of
power
.
Carriere
CT
'
s
provide
this
power
at
0.5
x
CT
rating
.
(
a
)
(
b
)
(
c
)
(
d
)
(
e
)
I
Fig
2.6
CT
POWER
WINDING
BURDEN
gsses
gs
*
-
FB
60
DE
Input
Impedance
y
—
+
24
V
Regulated
l
/
V
b
CT
Shunt
Regulator
72
Volt
CMax
}
Power
Winding
?
/
V
100
Volts
(
Maxj
Full
Wave
Rectifier
i
11
Courtesy of NationalSwitchgear.com

.
»
—
-
«
i
*
.
-
-
>
.
-
t
/
•
.
i
.
v
.
*
>
•
'
:
.
*
•
i
•
.
'
f
When
a
trip
condition
is
detected
a
pulse
of
\
DC
.
current
will
be
supplied
to
an
external
actuator
.
The
magnetic
>
f
'
ield
Produced
causes
the
spring
loaded
actuator
to
move
a
plungei
-
thus
,
tripping
the
breaker
.
The
actuator
linkage
mechanism
used
will
depend
'
bn
th
^
|
lyp
?
e
of
breaker
to
which
the
FB
600
E
is
installed
.
/
1
’
,
'
•
•
:
v
-
2.5
ACTUATOR
•
.
•
>
'
-
*
d
-
-
.
,
f
*
mechanism
v
.
i
-
*
2
.
1
•
<
.
,
*
.
k
*
*
v
*
.
/
v
:
N
.
*
.
/
>
vs
-
"
1
2.6
SYSTEM
'
GROUNDING
.
v
.
i
-
•
»
.
V
>
•
jtV
The
CT
signal
windings
,
power
windings
and
actuator
are
connected
to
different
points
in
the
circuitry
of
the
FB
600
E
'
.
Using
a
common
external
ground
for
the
signal
winding
common
-
'
{
terminal
5
)
,
power
winding
common
(
terminal
10
)
or
actuator
(
11
,
12
)
will
cause
the
FB
600
E
to
operate
incorrectly
.
Consequently
,
only
the
CT
signal
winding
common
should
be
connected
to
an
external
ground
as
shown
in
the
wiring
diagrams
of
figures
2.2
-
2.5
.
The
power
winding
common
and
actuator
are
indirectly
referenced
to
ground
internally
by
the
circuitry
.
i
12
Courtesy of NationalSwitchgear.com

i
.
3.0
SETUP
AND
OPERATION
i
3.1
COMMISSIONING
JUMPER
The
jumper
should
be
ON
whenever
the
unit
is
not
ready
,
(
ie
.
all
DIP
switches
have
not
been
programmed
)
.
When
this
jumper
is
in
place
,
the
FB
600
E
will
trip
.
each
time
current
is
applied
to
any
of
the
CT
inputs
.
This
jumper
is
in
place
as
a
failsafe
measure
to
ensure
that
the
unit
is
set
up
before
commissioning
.
(
a
)
!
The
jumper
must
be
removed
after
the
unit
is
set
up
for
commis
-
sioning
.
(
b
)
11
D
41
R
98
R
12
U
12
JU
1
1
Cl
W
4
A
173
Fig
.
3.2
INSTANTANEOUS
TRIP
TIME
DELAY
CURVES
3.2
INSTANTANEOUS
TRIP
SETTINGS
Instantaneous
tripping
without
any
intentional
delay
is
used
to
provide
protection
against
short
circuits
.
Switches
SI
4
and
SI
5
are
used
to
choose
between
phase
signal
averaging
and
peak
detector
and
consequently
the
pickup
time
.
The
pickup
level
is
controlled
by
switches
SI
1
to
SI
3
to
select
a
trip
level
of
2
(
curve
A
)
to
12
(
curve
B
)
times
the
CT
rating
as
shown
in
figure
3.2
.
Various
short
circuit
pickup
levels
can
be
selected
according
to
figure
3.1
.
This
feature
may
be
defeated
by
setting
switch
SIS
off
.
i
023
*
027
-
2
TRIP
TIME
insian
-
A
jtoneousy
L
>
level
V
.
SI
1
-
SI
3
(
SEC
)
V
0.10
phase
signal
averaging
V
v
0.05
peak
detector
i
12
2
CURRENT
(
Multiples
of
CT
Ratio
)
13
Courtesy of NationalSwitchgear.com

Fig
.
3.1
INSTANTANEOUS
TRIP
SWITCH
SETTINGS
INSTANTANEOUS
TRIP
SWITCH
SETTINGS
SWITCHES
SI
12345678
FUNCTION
LEVEL
111
-
-
Oil
1
0
1
T
5
0
0
1
110
0
1 0
2
X
CT
Rating
4
X
CT
Rating
6
X
CT
Rating
4
X
CT
Rating
10
X
CT
Rating
12
X
CT
Rating
:
Instantaneous
Pickup
Level
1
1
1
cr
1
i
0
'
Instant
.
Disable
'
'
SO
1
0
ms
delay
peak
detector
0
1
100
ms
delay
phase
signal
averaging
Trip
Indicator
:
0
=
off
1
=
on
Inst
.
/
Short
Time
no
effect
o o
1 1
o
o o
i
o
*
cT
:
b
\
n
3
14
Courtesy of NationalSwitchgear.com

3.3
SHORT
TIME
OVERLOAD
SETTINGS
Fig
.
3.4
SHORT
TIME
DELAY
TIME
/
OVERCURRENT
CURVES
•
V
Short
time
delay
tripping
is
provided
for
use
in
coordinated
protection
systems
to
shut
down
only
pickup
levels
of
2.5
-
10
times
the
CT
rating
and
time
delays
of
0.15
to
0.4
seconds
can
be
selected
using
switches
SSI
to
SS
8
as
shown
in
figure
3.3
.
This
feature
can
also
be
defeated
for
'
test
purposes
b
.
y
setting
SS
8
off
.
The
effect
o
.
f
these
switches
on
the
time
/
overcurrent
curves
is
•
-
,
jl
.
v
shown
in
f
iguire
3.4
.
Short
Time
Level
SS
1
-
SS
4
TRIP
TIME
(
SEC
)
_
Sv
V
0.40
Short
Time
Deloy
SS
5
-
SS
7
1
'
0.15
I
I
l
l
>
1
.
I
f
10
i
:
2.5
V
-
CURRENT
(
Multiples
of
CT
Rotio
)
?
Fig
.
3.3
SHORT
TIME
SWITCH
SETTINGS
-
f
.
'
f
•
SHORT
TIME
DELAY
'
.
SWITCH
*
-
.
SETTINGS
5
T
.
SWITCHES
SS
1
2
3
4
5
6
7
8
FUNCTION
LEVEL
.
t
--
i
>
-
:
•
•
Short
Time
Pickup
2.5
x
CT
Rating
3
.
x
CT
Rating
3.5
x
CT
Rating
x
CT
Rating
4.5
x
CT
Rating
x
CT
Rating
5.5
x
CT
Rating
x
CT
Rating
6.5
x
CT
Rating
x
CT
Rating
7.5
x
CT
Rating
x
CT
Rating
8.5
x
CT
Rating
x
CT
Rating
9.5
x
CT
Rating
10
x
CT
Rating
1111
0
111
.
1 0
1 1
0
0
1 1
110
1
0
1 0
1
1 0
0
1
000
1
1110
0
110
1 0
1 0
0
0
1 0
110
0
0
1 0
0
1 0
00
0
0
0
0
1
1
1
1
4
1
1
—
5
1
1
-
^
6
1
)
1
7
1
1
8
1
1
9
1
1
1 0
0
1
Short
Time
Delay
0.15
sec
.
@
>
150
%
pickup
level
0.25
sec
.
@
>
150
%
pickup
level
sec
.
@
>
150
%
.
pickup
level
0
1 0
1
0
0
1 1
-
0.4
'
V
'
0
Short
Disable
0
=
off
1
=
on
no
effect
0
o
o
|
oio
15
Courtesy of NationalSwitchgear.com

3.4
LONG
TIME
SETTINGS
To
allow
a
breaker
to
protect
system
components
such
as
transformers
,
motors
,
conductors
,
etc
.
that
fail
due
to
resistive
heating
,
a
set
of
time
overcurrent
curves
that
follow
a
current
squared
characteristic
is
provided
.
When
an
overcurrent
condition
persists
for
a
specified
length
of
time
the
breaker
trips
and
breaks
the
load
.
Trip
times
for
various
levels
of
current
and
curve
settings
are
listed
in
figure
3.5
for
testing
convenience
.
These
curves
are
shown
on
the
time
/
overcurrent
graph
of
figure
3.10
for
coordination
purposes
.
f
A
Fig
3.5
LONG
TIME
OVERLOAD
TRIP
TIMES
FB
600
E
LONG
TIME
PICKUP
DELAYS
(
SECONDS
)
CURRENT
IN
MULTIPLES
OF
LONG
TIME
PICKUP
SL
5
-
7
12
1.5
1.25
CURVE
ERROR
10
8
7
6
5
3
•
2
1.1
1
4
-
20
%
0.50
0.63
0.76
0.72
0.90
1.08
1.13
1.41
1.69
2.88
3.60
4.32
4.50
5.63
6.76
8.00
10.00
12.00
18.00
22.50
27.00
46.08
57.60
69.12
59.50
74.38
89.26
72.00
90.00
108.00
1.47
1.84
2.21
2.00
2.50
3.00
32.00
40.00
48.00
1
0
111
+
20
%
-
20
%
1.01
1.26
1.51
1.44
1.80
2.16
5.76
7.20
8.64
16.00
20.00
24.00
36.00
4
5.00
54.00
92.16
115.20
138.24
119.01
148.76
178.51
144.00
180.00
216.00
2.26
2.82
3.38
2.94
3.68
4.42
4.00
5.00
6.00
9.01
11.26
13.51
64.00
80.00
96.00
2
0
Oil
+
20
%
1.51
1.89
2.27
-
20
%
2.16
2.70
3.24
13.51
16.89
20.27
24.00
30.00
36.00
138.24
172.80
207.36
178.51
223.14
267.77
216.00
270.00
324.00
3.38
4.23
5.08
4.42
5.52
6.62
6.00
7.50
9.00
8.64
10.80
12.96
54.00
67.50
81.00
96.00
120.00
144.00
.
3
101
0
+
20
%
2.02
2.52
3.02
-
20
%
2.88
3.60
4.32
5.89
7.36
8.83
18.02
22.52
27.02
32.00
40.00
48.00
72.00
90.00
108.00
288.00
360.00
432.00
4.51
5.64
6.77
8.00
10.00
12.00
11.52
14.40
17.28
128.00
160.00
192.00
184.32
230.40
276.48
238.02
297.52
357.02
4
m
0
+
20
%
-
>
2.52
3.15
3.78
3.60
4.50
5.40
297.52
371.90
446.28
360.00
450.00
540.00
-
20
%
5.64
7.05
8.46
7.36
9.20
11.04
10.00
12.50
15.00
22.52
28.15
33.78
40.00
50.00
60.00
230.40
288.00
345.60
14.40
18.00
21.60
90.00
112.50
135.00
160.00
200.00
240.00
5
110
0
+
20
%
-
3.02
3.78
4.54
4.32
5.40
6.48
6.77
8.46
10.15
357.02
446.28
535.54
432.00
540.00
648.00
-
20
%
8.83
11.04
13.25
12.00
15.00
18.00
17.28
21.60
25.92
27.02
33.78
40.54
48.00
60.00
72.00
108.00
135.00
162.00
276.48
345.60
414.72
192.00
240.00
288.00
6
010
0
+
20
%
3.53
4.41
5.29
5.04
6.30
7.56
416.53
520.66
624.79
-
20
%
7.90
9.87
11.84
10.30
12.88
15.46
14.00
17.50
21.00
56.00
70.00
84.00
126.00
157.50
189.00
322.56
403.20
483.84
504.00
630.00
756.00
20.16
25.20
3
C
.
24
31.53
39.41
47.29
224.00
280.00
336.00
7
100
0
+
20
%
4.03
5.04
6.05
5.76
7.20
8.64
-
20
%
9.02
11.28
13.54
64.00
80.00
96.00
476.03
595.04
714.05
576.00
720.00
864.00
11.78
14.27
17.66
16.00
20.00
24.00
23.04
28.80
34.56
36.03
45.04
54.05
144.00
180.00
216.00
256.00
320.00
384.00
386.64
460.80
552.96
000
!
8
0
+
20
%
16
Courtesy of NationalSwitchgear.com

Switches
SL
1
to
.
SL
8
are
used
to
select
pickup
current
levels
of
0.5
-
1.25
times
the
CT
rating
and
time
delays
of
2.5
-
20
seconds
(
at
6
times
the
CT
rating
)
as
shown
in
figure
3.6
.
The
short
time
delay
and
instantaneous
trip
settings
should
be
selected
to
ensure
that
the
breaker
trips
without
allowing
a
continuous
current
to
flow
that
is
greater
than
400
%
of
the
CT
rating
(
see
Maximum
Inputs
section
2.5
)
.
The
effect
of
switches
SL
1
to
SL
7
on
the
time
/
current
curves
is
shown
in
figure
3.7
.
Fig
.
3.6
LONG
TIME
DELAY
SWITCH
SETTINGS
.
LONG
TIME
DELAY
SWITCH
SETTINGS
FUNCTION
SWITCHES
SL
-
12345678
LEVEL
Long
Time
Pickup
0.5
x
CT
Rating
0.55
x
CT
Rating
0.60
x
CT
Rating
0.65
x
CT
Rating
0.70
x
CT
Rating
0.75
x
CT
Rating
0.80
x
CT
Rating
0.85
x
CT
Rating
0.90
x
CT
Rating
0.95
x
CT
Rating
1.00
x
CT
Rating
1.05
x
CT
Rating
1.10
x
CT
Rating
1.15
x
CT
Rating
1.20
x
CT
Rating
1.25
x
CT
Rating
1111
0
111
10
11
0
0
1 1
110
1
0
1 0
1
1 0
0
1
0
0
0
1
1110
0
110
i
o
i
o
0
0
1 0
110
0
0
1 0
0
1 0
00
0
0
0
0
1
1
1
1
1
1
1
1
3
1
1
1
1
1
1
1
1
Long
Time
Delay
sec
.
@
6
x
Pickup
Level
sec
.
@
6
x
Pickup
Level
sec
.
@
6
x
Pickup
Level
sec
.
@
6
x
Pickup
Level
12.5
sec
.
@
6
x
Pickup
Level
sec
.
@
6
x
Pickup
Level
17.5
sec
.
@
6
x
Pickup
Level
sec
.
@
6
x
Pickup
Level
2.5
1111
0
111
1 0
1 1
0
0
1 1
110
1
0
1 0
1
1 0
0
1
0
0
0
1
5
7.5
10
1 5
20
Long
Time
Disable
0
0
=
off
1
on
no
effect
[
O
[
D
c
>
o o
1
17
Courtesy of NationalSwitchgear.com

Switches
SL
1
to
SL
4
determine
the
current
pickup
level
required
for
the
breaker
to
trip
.
The
time
to
trip
will
be
determined
by
the
amount
that
the
current
exceeds
the
overload
level
and
the
curve
selected
(
SL
5
to
SL
7
)
.
Long
time
delay
trip
can
be
defeated
for
test
purposes
by
setting
switch
SL
8
off
.
Fig
.
3.7
LONG
TIME
DELAY
CURVES
A
LeveI
SL
1
-
SL
4
TRIP
TIME
C
SEC
}
0
Minimum
pickup
(
0.5
x
CT
rating
)
Minimum
time
(
2.5
sec
.
@
6
x
CT
pick
-
up
)
curve
ABCDE
SL
8
to
SL
1
:
11111111
Minimum
pickup
(
0.5
x
CT
rating
)
Maximum
time
(
20
sec
.
@
6
x
CT
pick
-
up
)
curve
ABGH
SL
8
to
SL
1
:
10001111
Maximum
pickup
(
1.25
x
CT
rating
)
Minimum
time
delay
(
2.5
sec
.
@
6
x
CT
pick
-
up
)
curve
FGDE
SL
8
to
SL
1
:
11110000
Maximum
pickup
(
1.25
x
CT
rating
)
Maximum
time
delay
(
20
sec
.
@
6
x
CT
pick
-
up
)
curve
FGH
SL
8
to
SL
1
:
10000000
.
18
Courtesy of NationalSwitchgear.com
Popular Relay manuals by other brands

ABB
ABB C576 operating instructions

ABB
ABB CA-26 Instruction leaflet
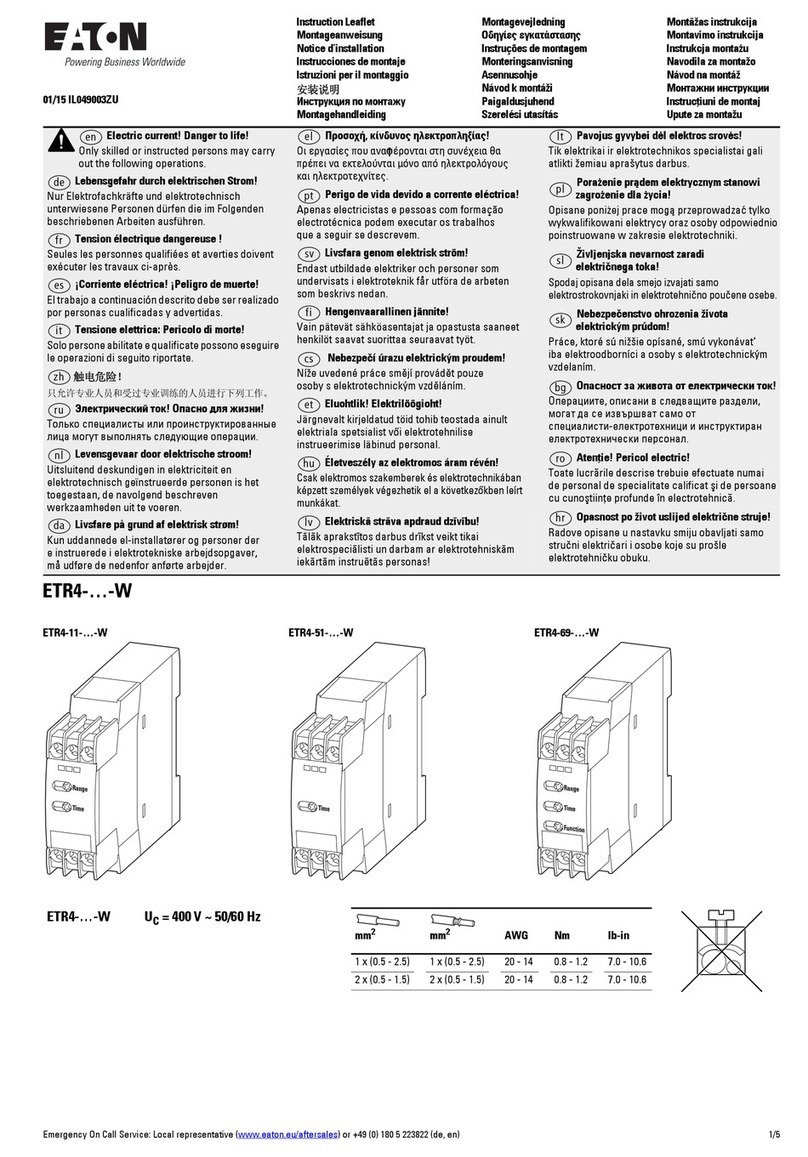
Eaton
Eaton ETR4 W Series Instruction leaflet

Pilz
Pilz PNOZ X2.4V Technical instructions
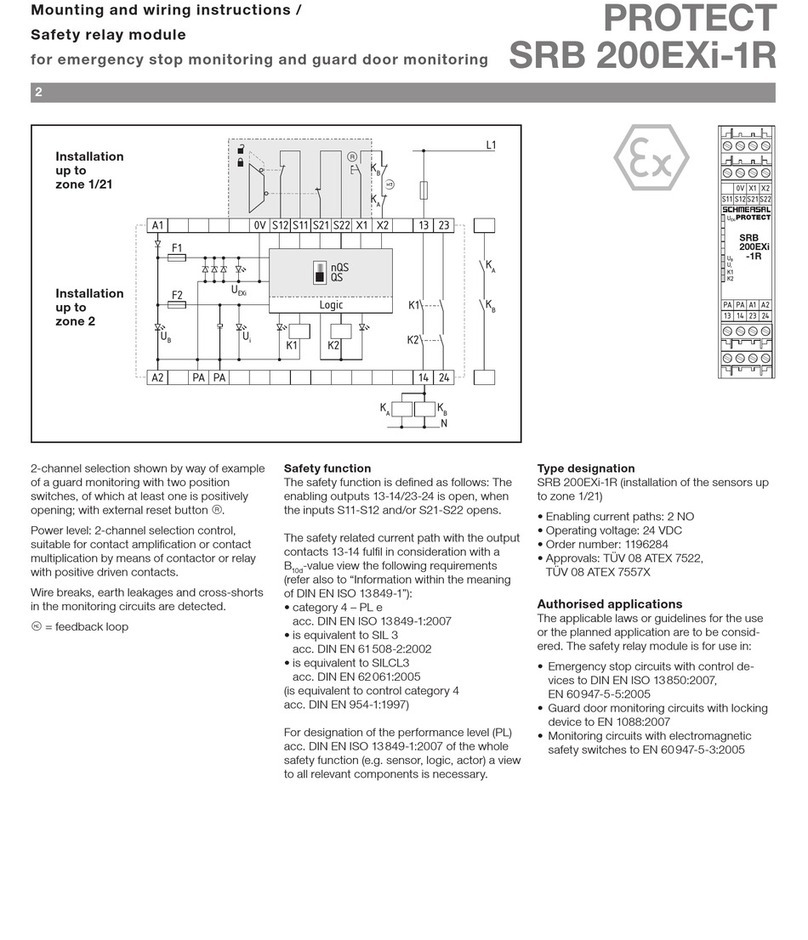
schmersal
schmersal PROTECT SRB 200EXi-1R Mounting and wiring instructions
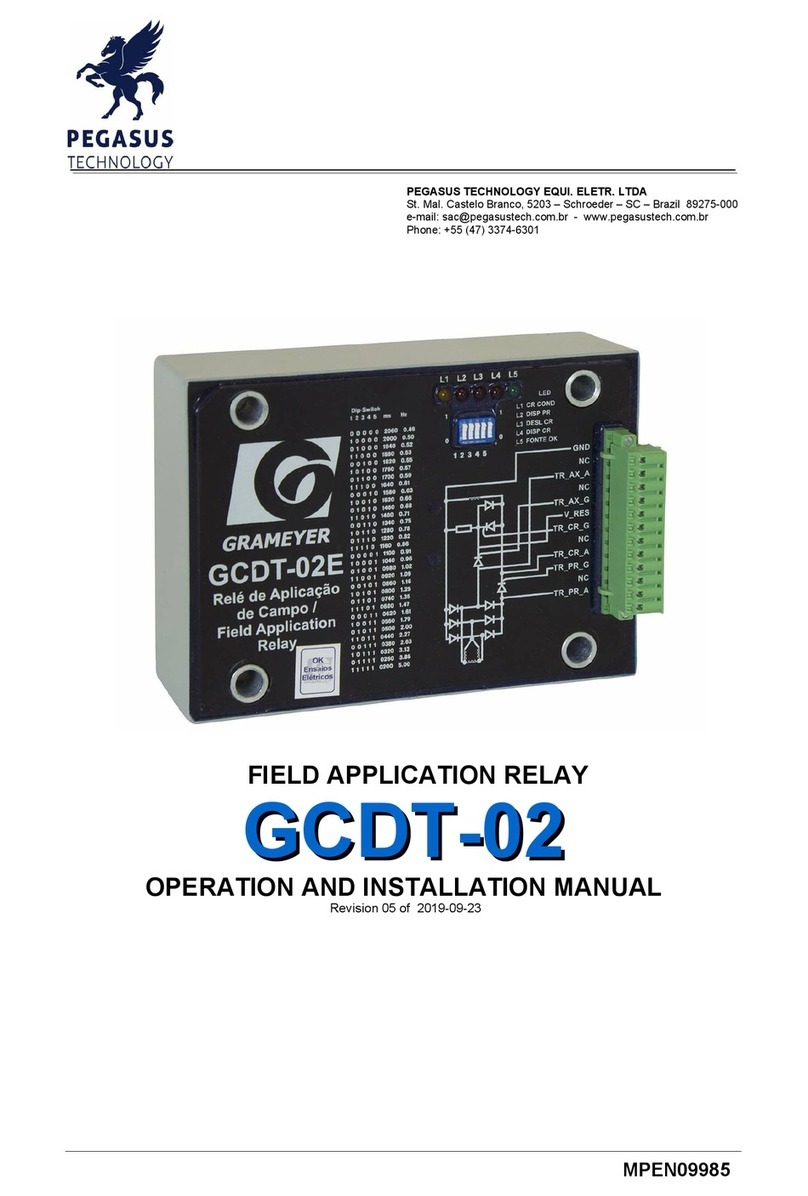
PEGASUS TECHNOLOGY
PEGASUS TECHNOLOGY GRAMEYER GCDT-02 Operation and installation manual