Curtis Dyna-Fog TYPHOON 2 3 Series User manual

DYNA-FOG
®
TYPHOON™2
MANUAL
MODEL 2985 SERIES 3
ULV APPLICATOR
MANUFACTURED BY:
CURTIS DYNA-FOG, Ltd.
17335 U.S. Highway 31 North
WESTFIELD, INDIANA, U.S.A.
www.dynafog.com
INNOVATORS OF SPRAYING AND FOGGING DEVICES

OPERATION AND MAINTENANCE MANUAL
FOR
DYNA-FOG TYPHOON 2
®
ULV AEROSOL APPLICATOR
(UNITED STATES AND FOREIGN PATENTS PENDING)
Copyright 2006
Dyna-Fog, Typhoon 2 and Syncroflow are trademarks or registered trademarks of
Curtis Dyna-Fog, Ltd.
CURTIS DYNA-FOG Ltd.
17335 U.S. HWY. 31 north
P.O. BOX 297
WESTFIELD, IN 46074-0297 USA
2

TABLE OF CONTENTS
INTRODUCTION…………………………………………………………………………………………........ 4
1.0 SPECIFICATIONS……………………………………………………………………………………….. 5
2.0 FOREWORD……………………………………………………………………………………………… 6
2.1 DESCRIPTION………………………………………………………………………………………….. 6
2.2 WORKING PRINCIPLES………………………………………………………………………………. 7
2.3 FLUID PUMPING SYSTEMS AVAILABLE…………………………………………………………… 7
MAJOR COMPONENTS DIAGRAM…………………………………………………………………………. 8
3.0 ASSEMBLY INSTRUCTIONS…………………………………………………………………………… 9
3.1 CHARGING THE BATTERY…………………………………………………………………………… 9
3.2 MACHINE INSTALLATION…………………………………………………………………………….. 11
4.0 SAFETY PRECAUTIONS………………………………………………………………………………… 13
5.0 MACHINE OPERATION………………………………………………………………………………….. 15
5.1 PRE-SPRAY CHECKLIST………………………………………………………………………………. 16
5.2 BLOWER PREPARATION………………………………………………………………………………. 17
5.3 ENGINE PREPARATION………………………………………………………………………………... 17
5.4 STARTING THE ENGINE………………………………………………………………………………... 18
6.0 MEASURING LIQUID VISCOSITY……………………………………………………………………….. 18
7.0 DROPLET SIZE VS. FLOW RATE AND BOOM PRESSURE…………………………………………. 21
TABLE 1 (SCOURGE) RESMETHRIN (1-6.5)-ADULTICIDE……………………………………………… 21
TABLE 2 (CYTHION) MALATHION-ADULTICIDE………………………………………………………….. 21
TABLE 2A (TECKNAR) BTI-LARVACIDE……………………………………………………………………. 21
8.0 PREVENTATIVE MAINTENANCE………………………………………………………………………... 22
BLOWER INTAKE FILTER……………………………………………………………………………………... 23
FORMULATION FILTER MAINTENANCE……………………………………………………………………. 24
TABLE 3 PREVENTATIVE MAINTENANCE SCHEDULE………………………………………………….. 25
8.1 FLUSHING THE SYSTEM…………………………………………………………………………………. 26
8.2 NOZZLE……………………………………………………………………………………………………… 27
8.3 DRIVE COUPLING…………………………………………………………………………………………. 28
8.4 STORAGE AND SHIPMENT………………………………………………………………………………. 31
9.0 SYSTEMS FLOW DIAGRAM………………………………………………………………………………… 33
10.0 ELECTRICAL SCHEMATIC (EXCLUDING PUMPING SYSTEM)……………………………………… 34
ENGINE ASSEMBLY…………………………………………………………………………………………….. 35
TACHOMETER/HOURMETER………………………………………………………………………………….. 36
11.0 PARTS IDENTIFICATION…………………………………………………………………………………… 37-41
11.1 MACHINE DIAGRAM……………………………………………………………………………………….. 37, 38
PARTS LIST………………………………………………………………………………………....................... 42
11.2 NOZZLE ASSEMBLY........................................................................................................................ 43
11.3 FLEXIBLE COUPLING……………………………………………………………………………………… 44
11.4 3-WAY VALVE ASSEMBLY………………………………………………………………………………... 45
11.5 FORMULATION TANK ASSEMBLY………………………………………………………………………. 46
11.6 FLUSH TANK ASSEMBLY…………………………………………………………………………………. 47
11.7 STEEL AND PLASTIC GRIPPER NUTS……………………………………......................................... 48
12.0 TROUBLE SHOOTING GUIDE……………………………………………………………………………… 49-51
13.0 CONVERSION TABLES……………………………………………………………………………………... 52
3

Dear Valued Customer,
Congratulations on your purchase of one of the most advanced Ultra-Low-
Volume applicators available.
The TYPHOON 2 ULV aerosol applicator was developed to provide a more
efficient, low cost method of insect control without sacrificing quality. Technology the
Typhoon 2 employs enables you to dispense concentrated formulations at accurately
low flowrates. This results in a significant chemical savings and an invaluable benefit to
the environment. This machines ability to reliably produce consistent droplets are
unsurpassed in the industry making it a favorite choice among professional users.
Properly maintained, the TYPHOON 2 will provide years of trouble free service.
We trust you will agree, the Typhoon 2 will be a great asset to any spraying program.
Thank you for choosing DYNA-FOG.
4

1.0
MACHINE SPECIFICATIONS
FOR
TYPHOON 2, MODEL 2985
TYPE: ULV, NON-THERMAL AEROSOL APPLICATOR
ENGINE: 11 HP HONDA, 4-CYCLE, OVERHEAD VALVE,
GASOLINE POWERED, ELECTRIC START WITH RECOIL
BACKUP STARTER, HEAVY-DUTY CHARGING SYSTEM.
FUEL CONSUMPTION: .51 lb/hph (313 g/kWh)
FUEL CAPACITY: 6.9QTS. (6.5 LTRS.)
OIL CAPACITY: 1.16QTS. (1.1LTRS.)
BLOWER: HIGH VOLUME, POSITIVE DISPLACEMENT, ROTARY TYPE,
MAXIMUM OUTPUT: 12 PSI (.82 BAR), 205 CFM (5.8 CU.M/MIN)
FORMULATION 3-TYPES AVAILABLE:
PUMP: 1) HIGH VOLUME, CORROSION RESISTANT DIAPHRAM PUMP
2) STAINLESS STEEL GEAR PUMP WITH OPTIONAL RADAR
SYNCROFLOW CONTROL.
3) FMI CERAMIC PISTON PUMP WITH CARBON CYLINDER.
SPRAY NOZZLE: HIGH EFFICIENCY DUAL NOZZLE; ADJUSTABLE AND
REMOVABLE FOR CLEANING.
LIQUID TANKS: BOTH FORMULATION AND FLUSH TANKS ARE CORROSION
RESISTANT, HIGH DENSITY POLYETHYLENE.
CAPACITIES: FORMULATION- 15 U.S. GAL. (57 LITERS)
FLUSH- 1.0 U.S. GAL. (3.8 LITERS)
BATTERY: 250 COLD CRANKING AMPS
PARTICLE SIZE: MEETS ALL CURRENTLY AVAILABLE CHEMICAL
MANUFACTURERS LABEL REQUIREMENTS WITH AT LEAST
95% OF DROPLETS PRODUCED UNDER 20 MICRONS
VOLUME-MEDIAN-DIAMETER.
WEIGHT: EMPTY: 297 LBS. (135 KG.)
FILLED: 412 LBS. (187 KG.)
DIMENSIONS: SHIPPING DIMENSIONS (CRATED):
LENGTH: 41.5 in. (105 cm) 48.0 in. (122 cm)
WIDTH: 29.0 in. (74 cm) 40.0 in. (102 cm)
HEIGHT: 32.0 in. (81 cm) 39.0 in. (99 cm)
BASE FRAME: 26 x 36 in. (66 x 91 cm)
SHIPPING WEIGHT: 415 LBS. (188 KG)
SHIPPING VOLUME: 43.3 cu.ft. (1.23 cu.m.)
5

2.0
FOREWORD
The application of insecticides is the predominate method by which man attempts
to control the size of insect populations. Due to environmental and economical reasons,
it is desirable to treat a given area with the least amount of insecticide that can be made
to be effective. The most efficient method is to break up the liquids into aerosols and
distribute these fine droplets over the target area. The small droplets stay suspended
for longer periods of time due to their size and are distributed more evenly, remaining
effective longer.
The term ULV is an abbreviation for Ultra-Low-Volume, the technology used to
treat areas with small amounts of chemical in an aerosol form. These chemicals are
usually in a more concentrated state than chemicals used in other methods of
application.
For best results, the Dyna-Fog ULV aerosol generator model 2985 should be
operated and maintained in compliance with this manual.
WARNING
Read and thoroughly understand all information, cautions and warnings on the
formulation label which may affect personal safety. Know any dangers of the
solution used and know what to do in case of an accident involving the solution.
Always use the appropriate safety equipment and dress accordingly to the
chemical formulation which is being used.
2.1
DESCRIPTION
The Dyna-Fog model 2985 ULV Aerosol Generator is designed to disperse
concentrated formulations at flow rates in the range of .5-20 oz./min. (15-590 ml/min)
with droplet sizes less than 20 microns VMD (volume-median-diameter). When
equipped with the Diaphragm Pumping System, flow rates of up to 120 oz./min. (3560
ml/min.) and larger droplet sizes are possible.
This machine is to be vehicle or trailer mounted and is designed to be operated
by a person in the cab of the vehicle using the remote control box.
6

2.2
WORKING PRINCIPLES
An 11 horsepower, four-cycle gasoline engine is used to drive a positive
displacement rotary-blower to generate 125 cfm (3.5 cu.m./min) of air at 8.5 psi. The air
entering the blower is first filtered through a large stainless steel filtering element. The
speed of the engine (approximately 2750 rpm maximum) moves this large air mass
through the boom assembly at a pressure of up to 8.5 psi. Attached to the boom
assembly are two nozzles. The nozzles have six stationary fins that create a swirling
effect of the air mass as it leaves the nozzles. In the center of this swirling air mass is a
liquid supply spray tube. The spray tube directs the formulation into the air mass where
it is sheared into billions of tiny droplets and dispersed into the atmosphere. The
formulation is delivered into the spray tube by means of a 12 volt DC pump that draws
the formulation from the tank, through a filter and 3-way valve, and then pumps it into
the nozzle spray tube.
This unit is also equipped with a flushing system. The flushing system is
activated manually. The flushing liquid is conveyed to the nozzles in the same manner
as the formulation. The system must be flushed after each use.
2.3
FLUID PUMPING SYSTEMS
There are three types of pumping systems available for the TYPHOON 1 ULV:
1) (MODEL 2985-1) FMI (SET-FLOW) Ceramic Piston-Pump: This highly accurate
pumping system utilizes a 12 volt DC motor to drive a ceramic, rotary piston-pump.
Once the liquid flow rate has been set, this is the flow rate that will be obtained when
the operator activates the SPRAY ON/OFF switch.
2) (MODEL 2985-2) Diaphragm Pump: This high volume pumping system utilizes a
diaphragm type pump with a needle valve on its outlet port to regulate liquid flow. Once
the liquid flow rate has been set, this is the flow rate that will be obtained when the
operator activates the SPRAY ON/OFF switch.
3) (MODEL 2985-3) Rotary Gear-Pump: This pump is driven by a variable speed
electric motor. All functions are controlled from the remote control box. Once the pump
has been set to the desired flow rate, that flow rate will be obtained when the operator
activates the SPRAY ON/OFF switch. When adapted with the Dyna-Fog Radar
Syncroflow feature, the flow rate of the pump will automatically vary with vehicle speed.
7

8
BATTERY BOX

3.0
ASSEMBLY INSTRUCTIONS
1) Uncrate the unit and remove all packing materials.
NOTE:
It is a good idea to retain the original machine-shipping carton for storage.
2) Place the remote control unit where it will not be damaged while the machine is
being installed.
3) Remove the machine from the shipping skid by removing the three lag screws that
retain the shipping brackets. Keep the brackets for mounting the machine to your
vehicle or trailer bed.
4) Check the lubricating oil level in both the engine and blower. Refer the engine and
blower sections of this manual and to the engine and blower manuals for the correct
filling procedure and add oil if necessary.
5) The battery, if supplied complies to SAEJ537 (SAE #24LO). Activate the dry charge
storage battery according to the following instructions:
3.1
CHARGING THE BATTERY
DANGER POISON
Batteries produce explosive gases. Keep sparks, flame and cigarettes away!
Ventilate when charging or using in an enclosed space.
The battery contains Sulfuric Acid, which causes severe burns. If acid contacts eyes,
skin or clothing, flush well with water. For contact with eyes, get immediate medical
attention.
Keep battery and acid away from children and other persons who may not be aware of
dangers involved.
A. Remove battery from its mounting and place on a stable workbench.
B. Remove vent caps from battery. Remove or destroy any sealing device, which may
have been used to close or restrict the vent openings in the vent caps.
C. Fill each cell of the battery to the top of the separators with approved battery
electrolyte of 1.265 specific gravity.
NOTE:
The temperature of the battery and electrolyte at time of filling should not exceed 60 oF
(15 oC).
CAUTION:
Never fill battery in machine as spills will damage finish and cause premature
corrosion and/or damage to components.
9

3.1
CHARGING THE BATTERY (CONT'D)
D. Charge 12 volt battery at 30-40amps until the acid temperature is above 80 oF (26
oC), and the hydrometer readi ng is 1.250or higher. Acid temperature must never
exceed 125 oF while charging.
NOTE:
Both temperature and hydrometer readings must be met.
E. After charging the battery, check acid levels in all cells and fill each cell with acid to
the proper level.
F. Re-install vented caps.
G. Re-install the battery onto the machine. Po sition battery in the battery box so that
the terminal side of the battery is facing the engine.
H. Connect the RED positive (+)cable to the positive terminal of the battery and fasten
it securely with the hardware provided.
I. Connect the BLACKnegative (-)cable to the negative terminal of the battery and
fasten it securely with the hardware provided.
CAUTION
When installing the battery, connect the negative (-) cable last to prevent sparking
and shorting. When disconnecting is required, remove the negative (-) cable first.
Reverse polarity can cause damage to the starting and charging system.
10

3.2
MACHINE INSTALLATION
1. Remove the machine from the skid and lift the machine onto the vehicle with the
discharge end of the machine toward the rear of the vehicle.
2. Securely mount the machine to the bed of the vehicle using ½” (12mm) diameter
bolts as shown in the diagram on page 12.
3. Pass the remote control unit through an open window and locate it within reach of
the person operating the machine. If permanent vehicle installation is desired, the
remote control cable can be fed through a clearance hole in the vehicle chassis and
then reconnected. When drilling clearance holes, ensure that all sharp edges are
removed and covered to prevent premature wearing of the remote cable. When
routing the cable to the vehicle cab, do not allow the cable to be exposed to any
sharp edges. Avoid sharp bends when routing the cable.
4. Once the cable has been routed to the cab, reseal all drilled openings to prevent
moisture and/or exhaust gases from entering the cab.
11

12

4.0
SAFETY PRECAUTIONS
WARNING
READ AND UNDERSTAND THESE SAFETY PRECAUTIONS
BEFORE OPERATING MACHINE
1. ENGINE AND FUEL: This machine uses gasoline as the fuel for the internal
combustion engine and all precautions commonly applying to this volatile fuel should be
observed. Exercise extreme caution to avoid spilling of gasoline. If spillage occurs,
wipe it off and allow evaporation time before starting the engine. DO NOT attempt to
put fuel in tank while the machine is still running. Avoid smoking or open flame in area
when handling gasoline. Never run the unit indoors unless exhaust is vented to outside.
These fumes contain carbon monoxide which is colorless and odorless and can be fatal.
CAUTION
Do not operate engine without muffler
NOTE:
The engine is equipped with a muffler that has a U.S. Forestry Service approved spark
arrestor which is required by law in some states.
DO NOT TOUCH HOT MUFFLER, CYLINDERS OR FINS AS CONTACT MAY
CAUSE BURNS.
EXCEPT FOR ADJUSTMENT, DO NOT OPERATE THE ENGINE IF AIR
CLEANER OR COVER DIRECTLY OVER THE CARBURETOR AIR INTAKE IS
REMOVED.
DO NOT RUN THE UNIT IF THE COUPLING GUARD IS REMOVED.
DO NOT TAMPER WITH GOVERNOR SPRINGS, GOVERNOR LINKS OR OTHER
PARTS WHICH MAY INCREASE OR DECREASE THE GOVERNED ENGINE
SPEED.
2. THE ENGINE SPEED (RPM) should be checked periodically to insure that it is
operating correctly as engine speed affects the rate of the air flow through the nozzle
system which controls droplet particle size. Should be approximately 2700 RPM @ 8.0
PSI boom pressure.
3. MACHINE DAMAGE: Never operate a machine after it has been damaged. A
damaged machine can be very hazardous.
13

4.0
SAFETY PRECAUTIONS (CON’T)
4. WIND: Spraying during windy conditions is not usually practical because the
formulation will drift out of the intended area. However, under NO circumstances should
spraying into the wind be attempted. This may cause hazardous accumulations on the
machine or carrying vehicle.
5. SAFETY EQUIPMENT: In addition to any safety equipment that may be required by
the type of formulation which is being used, the following items should be mandatory for
each vehicle which carries this machine during fogging operations.
a. Fire Extinguisher, chemical-type rated for fuel fires.
b. First Aid Kit.
c. Eye Wash Solution.
d. Safety Glasses.
e. Container of Oil Dry Compound.
f. Gloves Rated for High Temperature.
g. Respirator Adequate for Formulation being used.
6. CHILDREN: Many spraying operations are performed in residential areas,
commonly at dusk. This presents the operator with the problem of children who are
attracted to the noise and/or mist being created. Children have been observed running
into and riding bicycles through the mist. The possible hazard lies in the toxic effect of
some formulations, the severity of which depends upon the chemical used, mist density
and the length of time of direct exposure.
IT IS THE OPERATOR'S RESPONSIBILITY TO DISCOURAGE ANYONE FROM
PLAYING IN THE MIST OR BEING NEAR THE MOVING VEHICLE.
7. FORMULATIONS: Ensure that formulations are applied only in strict compliance
with the formulation label as well as local, state and federal regulations and that these
formulations are dispersed only by trained personnel of public health organizations,
mosquito abatement districts, pest control operators or other qualified personnel.
a. Always comply with any requirements for protective clothing, goggles, gloves,
Facial masks or respirators required on the formulation label.
b. Do not exceed the dosage set forth on the registration label of the insecticide to
be used.
c. Always store formulation in its original labeled container.
14

5.0
MACHINE OPERATION
CAUTION
Read this complete operation section and the section on safety precautions
before starting the machine for the first time.
For first time operation, the sections on MACHINE INSTALLATION and MACHNE
OPERATION must be performed before proceeding with this section.
When operating this machine for the first ti me, move to an uncongested and well-vented
work area away from flammable materials.
WARNING
READ THE SECTION ON SAFETY PRECAUTIONS BEFORE PREPARING TO
DISPENSE FORMULATION.
READ AND THOROUGHLY UNDERSTAND ALL INFORMATION, CAUTIONS AND
WARNINGS ON THE FORMULATION LABEL WHICH MAY AFFECT PERSONAL
SAFETY. KNOW ANY DANGERS OF THE SOLUTION USED AND KNOW WHAT TO
DO IN CASE OF AN ACCIDENT INVOLVING THE SOLUTION.
ALWAYS USE THE APPROPRIATE SAFETY EQUIPMENT AND DRESS
ACCORDING TO THE CHEMICAL FORMULATION WHICH IS BEING USED.
WARNING
DO NOT USE ANY SUBSTANCES FROM UNMARKED CONTAINERS OR FROM
CONTAINERS WITH OBVIOUSLY ALTERED LABELS.
READ AND FOLLOW THE INSTRUCTIONS ON THE CHEMICAL SOLUTION LABEL
FOR ULV SPRAYING OF THE SOLUTION.
DO NOT SPRAY NEAR AN OPEN FLAME OR HOT MATERIALS.
DO NOT LEAVE THE MACHINE UNATTENDED.
15

5.1
PRE-SPRAY CHECK LIST
1. Verity that the formulation pump has been calibrated and is dispensing formulation in
accordance with the manufacturers label requirements.
2. Verify that the adjustable nozzle boom is in the correct position as required for the
spraying operation to be accomplished, and that the ring clamp which allows this
positioning is tight.
3. Verify that the engine has sufficient fuel and is properly lubricated.
4. Verify that the blower has been serviced.
5. Inspect all hoses for abnormal conditions.
6. Verify that no foreign objects or tools have been left in or about the machine.
7. Verify that the sufficient amount of formulation is in the tank and that the tank filling
cap is tight and its air vent hole is not clogged.
8. Verify that the battery is mounted securely and cable connections are proper.
9. Verify that all safety equipment is in place and is in proper working order.
10. Verify that the remote control box is within easy reach of the operator.
CAUTION
Before proceeding with any spraying operation, the operator should be
thoroughly familiar with starting and stopping the machine and with all the
operating controls. If you are operating the machine for the first time, exercise
the machine through its full operational sequences from a position of full
visibility of the machine before operating the machine fully remote. This is also a
good idea for experienced operators who may be operating a new machine or
who may be reactivating a machine after repairs or a period of inactivity. Refer to
the engine manual for starting and stopping the engine.
16

5.2
BLOWER PREPARATION
The blower on your machine has already been filled with a non-detergent, SAE 40 grade
oil. It should not be necessary for you to use a different grade of oil unless the machine
will be operated in climates with a temperature above 90 F (32 C). In applications where
the machine will be operated for extended periods above 90 F (32 C), use SAE-50 grade
oil. (See pages 7 and 8 of the "Blower Instructions" manual for lubrication schedules and
oil capacities, etc...).
5.3
ENGINE PREPARATION
Change and add oil according to chart below. Do not overfill. Use high quality
detergent oil API classified “For service SE, SF, SG” . If oil remains in the engine, oil
viscosity must be suitable for the lowest temperature at which the engine will be operated
in service. Use no special additives with recommended oils.
(*) Air cooled engines run
hotter than automotive
engines. Use of
multi-viscosity oils
(10W-30, etc.) Above 40 °F
(4°C) will result in high oil
consumption and possible
engine damage. Check oil
level more frequently if
using these types of oil.
(**) SAE 30 oil, if used
below 40 °F (4 °C), will
result in hard starting and possible engine bore damage due to inadequate lubrication.
Check oil level before starting engine. Add oil (If required).
Start and run the engine at idle for 30 seconds. Shut engine off. Wait 30 seconds and
check oil level. Add oil to bring level to Full mark on dipstick, if required.
Note :Engine is shipped from factory without oil. Before starting it, check oil level.
Fuel Recommendations
The engine will operate satisfactorily using any automobile gasoline. Use clean, fresh,
lead-free gasoline with a minimum of 85 octane for overhead valve engines. Leaded
gasoline may be used if it is commercially available, and if lead-free is not available. Use
of lead-free gasoline results in fewer combustion deposits and longer valve life. Purchase
fuel in quantity that can be used within 30 days. This will assure fuel freshness and
volatility tailored to the season. DO NOT MIX OIL WITH GASOLINE.
B&S do not recommend using gasoline which contains alcohol, such a gasohol. If
gasoline with alcohol is used, it must contain less than 10% Ethanol and must be
removed from engine during storage. Do not use gasoline which contains Methanol.
Fuel Level : Do not overfill. Allow space in fuel tank for fuel expansion.
17

5.4
STARTING THE ENGINE
1. OPEN THE FUEL VALVE: Slide the fuel ON/OFF valve to ON.
2. CHOKE ENGINE: Move engine or remote choke control to position lever in "choke"
position.
3. TURN ENGINE "ON": Position key switch on engine to "ON" and place the machine
on/off switch on the remote control box to "ON". When the remote box switch is "ON",
the green L.E.D. on the remote box should glow indicating power to the remote
box.
4. TURN SPRAY OUTPUT "OFF": Verify that the spray on/off switch on the remote
control box is in the "OFF" position.
5. START ENGINE: Activate the spring-loaded start switch on the remote box, or use
the key switch to start the engine.
NOTE:
To prevent overheating the engine starter motor, do not activate the motor longer than
15 seconds at a time.
6. SET ENGINE SPEED: Allow the engine to warm-up and gradually move the choke
lever to the "unchoked" position. Adjust the engine throttle control to achieve the
desired BOOM PRESSURE. (See Tables 1 and 2, Section 7.0)
DO NOT EXCEED 8.5 PSI BOOM PRESSURE
6.0
MEASURING LIQUID VISCOSITY
In order to achieve consistent results in generating aerosols with the required volume
median diameter (VMD), several variables must be kept under control at the same time.
The ability of an aerosol generator to consistently break up a liquid into appropriate
sized droplets depends on (3) key elements:
1. The available energy flow (air flow) through the nozzle is governed by the blower
speed. As the air mass and its velocity through the nozzle decreases, the droplet
size (VMD) will increase assuming that the liquids viscosity and flow rate remains
constant.
2. The flow rate of the liquid governed by the speed of the liquid pump.
18

6.0
MEASURING LIQUID VISCOSITY (CONT'D)
3. The viscosity of the liquid. Various liqui ds have different viscosities. Viscosity is
defined as a fluids resistance to flow commonly measured in units of a centipoise (CP).
Generally, the thicker the liqui d, the greater the viscosity and the higher the CP number.
Examples of some liquid viscosities are:
LIQUID VISCOSITY (CP)
WATER 1
DIBROM 3-4
DOW MFC 3-4
PYRETHRIN, RESMETHRIN 6-7
DURSBAN 1.5ULV 12-14
TECHNICAL MALATHION 28
To measure the flow ability (vi scosity)of your formulation:
1. Place a sample of the formulation liquid to be dispensed in the relative flow ability
meter provided with the machine such that the liquid level is above the top line.
2. Hold the meter vertical and allow the liqui d to flow through the brass orifice at the
outlet end of the meter into an appropriate container.
3. Using a stopwatch or a watch with a sweep second hand, determine the flow ability
time in seconds that it takes for the liquid level to fall from the top line to the bottom
line.
19

6.0
MEASURING LIQUID VISCOSITY (CONT'D)
Once the flowability of the liquid has been measured, tables 1 and 2 can be used as an
approximate guide for setting the pump flow rate and nozzle boom pressure for your
spray application.
NOTE:
Periodically calibrate the flowability meter using plain water. Water should flow through
the orifice such that the time between the top line and the bottom line is 32 + 2 seconds.
FLOWABILITY TEST METER
LINE N0. 1
COUNT SECONDS IT TAKES
FLUID TO DRAIN FROM
LINE NO. 1 TO LINE NO. 2
(FLOWABILITY TIME)
LINE NO. 2
CURTIS DYNA-FOG Ltd.
20
This manual suits for next models
1
Table of contents
Popular Portable Generator manuals by other brands

enraf
enraf 1200-5-10 CM instruction manual

Titan
Titan TG 8500M owner's manual

SIGLENT
SIGLENT SDG1000X Series Service manual
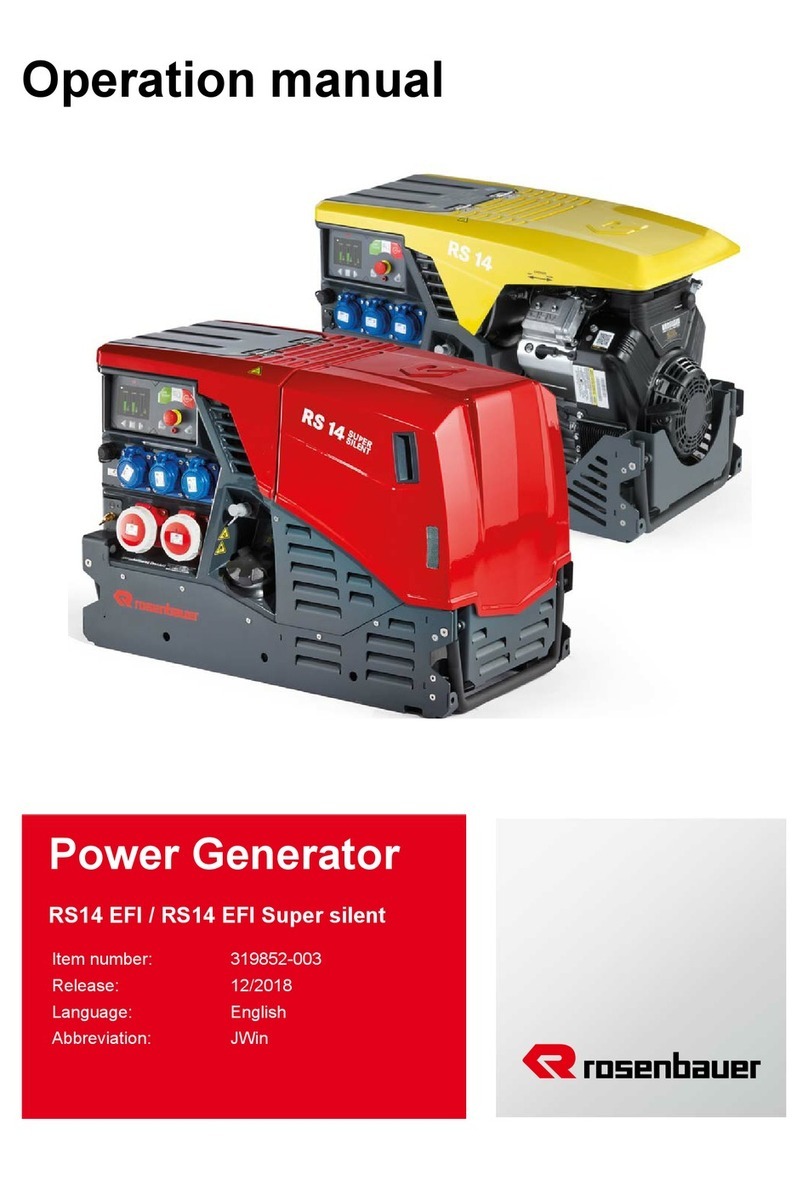
Rosenbauer
Rosenbauer RS 14 EFI SUPER SILENT EFI Operation manual
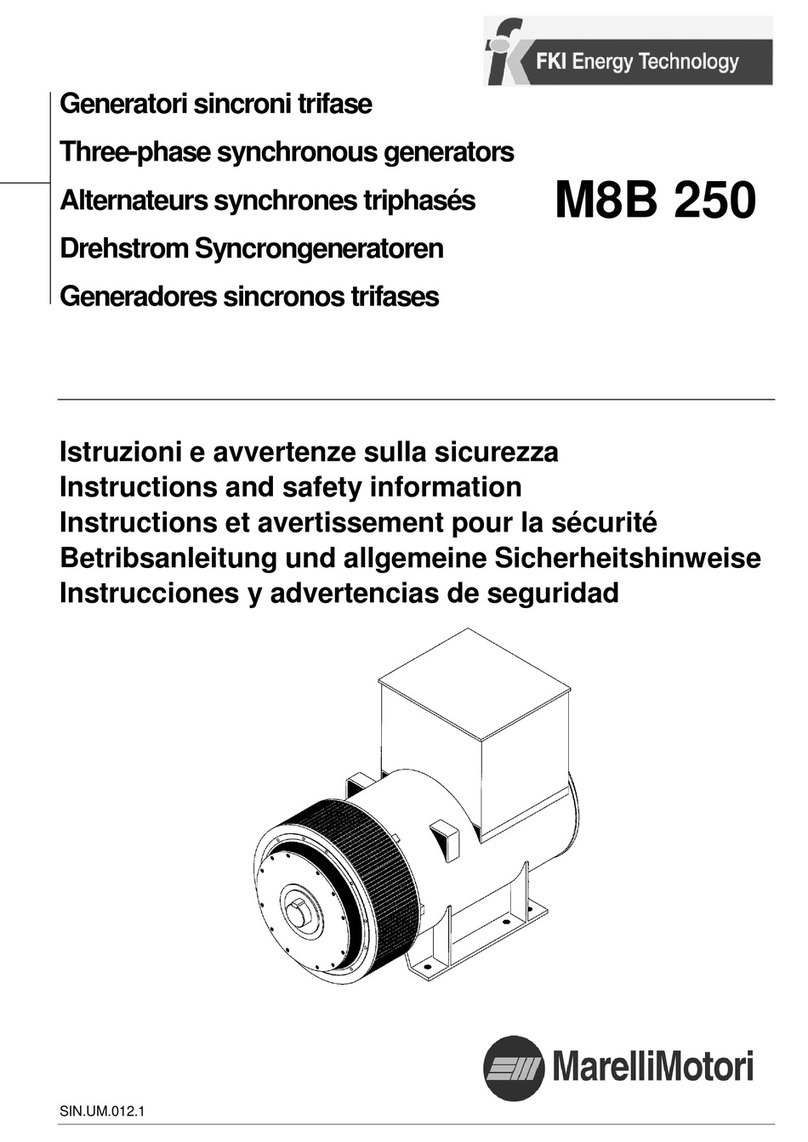
MarelliMotori
MarelliMotori M8B 250 Instructions and Safety Information
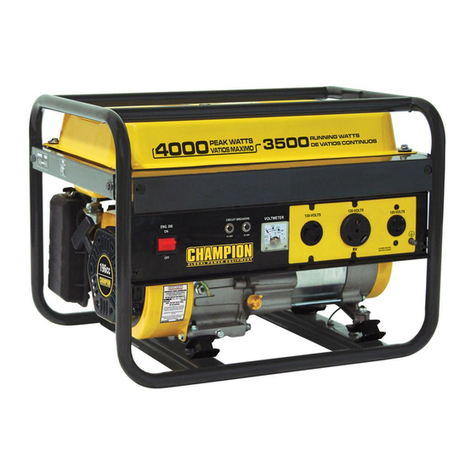
Champion
Champion 46515 Owner's Manual and Operating Instructions