Curtis 1356 User manual

Manual
Models 1356 &1356P
CAN Expansion Modules
Read Instructions Carefully!
Specifications are subject to change without notice.
© 2015 Curtis Instruments, Inc. ® Curtis is a registered trademark of Curtis Instruments, Inc.
© The design and appearance of the products depicted herein are the copyright of Curtis Instruments, Inc. 53221, Rev A 10/2015
Curtis Instruments, Inc.
200 Kisco Avenue
Mt. Kisco, NY 10549
www.curtisinstruments.com


Curtis 1356 /1356P CAN Expansion Module Manual, Rev. A iii
CONTENTS
1. OVERVIEW ............................................................................ 1
2. INSTALLATION AND WIRING .......................................... 4
Mounting the Module ........................................................ 4
Connections and Wiring Guidelines................................... 6
Wiring: Basic Configuration .............................................. 8
Wiring: Application Example........................................... 10
Input/Output Specifications.............................................. 11
3. CANopen COMMUNICATIONS ........................................ 16
Minimum State Machine .................................................. 16
NMT Messages ................................................................ 18
Emergency Messages ........................................................ 19
Heartbeat ......................................................................... 19
4 PDO COMMUNICATIONS ............................................... 20
5. SDO COMMUNICATIONS ............................................... 23
SDO Master Request (SDO-MOSI) ................................ 23
SDO 1356 /1356P Response (SDO-MISO) .................... 24
Using an SDO to Map a PDO ........................................ 25
Types of SDO Objects ..................................................... 26
Communication Prole Objects ....................................... 26
Parameter Prole Objects ................................................. 33
Monitor Prole Objects ................................................... 38
6. DIAGNOSTICS & TROUBLESHOOTING ...................... 39
Troubleshooting ................................................................ 40
Fault Log........................................................................... 41
7. SERIAL COMMUNICATIONS & PROGRAMMING ...... 42
Program Menus ............................................................... 42
Monitor Menus ................................................................ 48
Fault Menu ...................................................................... 50
appendix aVehicle Design Considerations
appendix bProgramming Devices
appendix cSpecifications, 1356 /1356P CAN Expansion Module
CONTENTS

iv Curtis 1356 /1356P CAN Expansion Module Manual, Rev. A
FIGURES
. 1: Curtis 1356/1356P CAN expansion module .......................... 1
. 2: Mounting dimensions, Curtis 1356/1356P ............................ 4
. 3: Basic wiring diagram ............................................................... 8
. 4: Application example .............................................................. 10
TABLES
1: Connector pinout .................................................................. 6
2: Communication prole object dictionary ............................ 26
2a: Manufacturer’s status registers .................................... 31
2b: Store parameter object ............................................... 31
2c: Restore default parameters object ............................... 32
3: Parameter prole object dictionary ....................................... 33
4: Monitor object dictionary .................................................... 38
5: Troubleshooting chart .......................................................... 40
6: Programmer: program menus ............................................... 42
7: Programmer: monitor menus ............................................... 48
C-1: Specifications, Curtis 1356/1356P ..................................... C-1
FIGURES / TABLES

Curtis 1356/1356P CAN Expansion Module Manual, Rev. A 1
OVERVIEW
e Curtis 1356 and 1356P are CAN expansion modules that provide simple,
exible, and low-cost control of up to 18 I/O, two high-frequency driver out-
puts, one encoder input, and ve analog inputs. ese modules can be used
on electric vehicles and internal combustion engines.
e 1356/1356P can extend the I/O capabilities of any Curtis VCL-driven
system and enhance systems that use Curtis AC controllers by providing ad-
ditional I/O. ese expansion modules have the exibility to be used in many
applications, such as Mobile Elevating Work Platforms (MEWPs), electric
forklifts, aerial lifts, etc.
Two versions of the module are available. e 1356 is a PCBA, for which
customers develop their own case to provide environmental protection. e
1356P comes potted with a plastic tray that provides IP65 water and dust
immunity for its electronics.
1
1 — OVERVIEW
Fig. 1 Curtis 1356 and
1356P CAN expansion
modules.
More Features +
Features include:
311 active-high digital inputs
32 high-frequency driver outputs (1 amp and 3 amps), which can also be used
as active-high digital inputs
3Closed loop constant current, constant voltage, or direct PWM control on each
output
35 analog inputs (0–15V), which can also be used as virtual digital inputs
with programmable thresholds

2Curtis 1356/1356P CAN Expansion Module Manual, Rev. A
3Analog inputs are selectable for resistive sensors (0–5kΩ)
31 quadrature encoder input
3Serial port for Curtis programmer or fault code display
3CANopen communication port controlled by dynamic mapping
3Regulated 5V and unregulated 12V current-limited power supplies
3The output voltage and current of the 5V and 12V supplies can be monitored
3Software and hardware watchdog circuits ensure proper software operation
3IP65-rated protection for 1356P (exclusive of connectors)
3Red and yellow status LEDs provide external monitoring.
DESCRIPTIONS OF KEY FEATURES
Active-High Digital Inputs
e 1356 /1356P has eleven digital inputs. Each input is digitally ltered to
eliminate switch “bounce” or noise in the signal. A power resistor pull-down
to B- at each input provides active high to B+.
High Frequency Driver Outputs
e 1356 /1356P contains two driver outputs. One can sink up to 1 amp
through an inductive or a resistive load; the other can sink up to 3amps through
an inductive or a resistive load. Internal yback diodes to B+ prevent voltage
spikes. High frequency PWM (16kHz) provides smooth current to the load.
Constant Current or Voltage Outputs
e two driver outputs can work in Constant Current mode or in Constant
Voltage mode.
In Constant Current mode, the software runs a closed loop PI controller
to provide an average constant current. is current is commanded over PDO
as a 0–100% command based on the maximum current setting (set through a
Curtis programmer or an SDO).
Each output can also be programmed for Constant Voltage mode. In this
mode, the battery voltage is monitored and the PWM command is corrected
by a feed-forward controller to provide a constant average voltage commanded
over the PDO (a 0–100% command based on the maximum voltage setting).
In addition, each output can also be programmed to provide a directly
commanded PWM% output (Direct PWM mode) or shut o to be used as
an input (Active-High Digital Input Only mode).
Programmable Dither for Hydraulic Valves
Dither is a small variation in the command that keeps the seals of a proportional
valve oiled. is lubrication allows the valve to move freely for accurate PV
control. Dither is only active on drivers in Constant Current mode.
1 — OVERVIEW

Curtis 1356/1356P CAN Expansion Module Manual, Rev. A 3
Voltage Analog Inputs
e 1356 /1356P has ve analog inputs that are scaled to read 0–15 volts. e
analog channels are read by a 12-bit ADC, resulting in about 3.66 millivolt
resolution. Independently adjustable lters ensure a smooth signal.
Resistive Sensor Inputs
Each analog input can be used with resistive sensors, such as RTDs (Resistive
Temperature Devices).
Virtual Digital Inputs
e ve analog inputs are also sensed and decoded as if they were digital inputs.
A unique feature of these digital inputs is that the active high/low thresholds are
completely programmable. us, these inputs can be used with analog sensors
to detect conditions like over/under pressure, high/low level points, etc.
Encoder Interface
e 1356 /1356P has one quadrature encoder input, which shares with the
Analog 4–5 pins. e 1356 /1356P can detect an open fault on the encoder
input wire.
CAN Interface
e 1356 /1356P is CANopen compliant, responding to the standard NMT,
PDO, and SDO communications as well as the DS301-required identity and
standard objects. e Curtis CANopen extensions allow additional features,
such as OEM and User default congurations and time-stamped fault logging.
PDO Dynamic Mapping
e 1356 /1356P can receive two PDOs and respond with two PDOs. ese
PDOs use dynamic mapping. All programmable parameters and viewable values
within the 1356 /1356P are accessible by SDOs or with a Curtis programmer.
Online Update
e 1356 /1356P has the ability to update its software through the serial port
(with Curtis 1309USB) or through the CANopen interface (with Peak-CAN
tools), using existing Curtis PC software tools.
Status LEDs
e 1356 has two fault LEDs (red and yellow) to clearly ash the fault code.
Both the 1356 and the 1356P can drive a single remote LED via the serial
port, to ash the fault code.
Familiarity with your Curtis 1356 /1356P module will help you install and operate
it properly. We encourage you to read this manual carefully. If you have questions,
please contact the Curtis office nearest you.
1 — OVERVIEW

4Curtis 1356/1356P CAN Expansion Module Manual, Rev. A
2 — INSTALLATION & WIRING
2
Fig. 2 Mounting
dimensions, Curtis 1356
and 1356P expansion
modules.
Dimensions in millimeters.
INSTALLATION AND WIRING
MOUNTING THE MODULE
e outline and mounting hole dimensions for the modules are shown in Fig. 2.
e 1356P module should be mounted using two M4 screws.
e 1356 module requires the OEM to develop an appropriate case to
provide environmental protection. Mounting for the 1356 depends on the case.
Care should be taken to prevent contaminating the PCBA (1356) or
connector (1356P). In order to prevent external corrosion and leakage paths
from developing, the mounting location should be carefully chosen to keep
the module as clean and dry as possible.
+
CAUTION
100.0
92.4
3.8
3.8
62.4
70.0
60.7 5X Ø3.50
4XR3
J1 CONNECTOR J2 CONNECTOR
1 12
13 24
1 2
43
14.4 ±1.5
1.60
16.3
STATUS
LEDs
110.0
116.0
126.0
2x Ø4.50
4xR8
25.0
32.0
80.0
J1 CONNECTOR J2 CONNECTOR
121
2413
1
3
2
4
5.0
25.0
17.0
1356
1356P

Curtis 1356/1356P CAN Expansion Module Manual, Rev. A 5
If the outputs will be used at or near their maximum ratings, it is rec-
ommended that the module be mounted to a good heatsinking surface, such
as an aluminum plate.
You will need to take steps during the design and development of your
end product to ensure that its EMC performance complies with applicable
regulations; suggestions are presented in Appendix A.
e 1356 /1356P contains ESD-sensitive components. Use appropriate
precautions in connecting, disconnecting, and handling the module. See instal-
lation suggestions in Appendix A for protecting the module from ESD damage.
2 — INSTALLATION & WIRING
Working on electrical systems is potentially dangerous. You should
protect yourself against uncontrolled operation, high current arcs, and
outgassing from lead acid batteries:
UNCONTROLLED OPERATION — Some conditions could cause the motor to
run out of control. Disconnect the motor or jack up the vehicle and get
the drive wheels o the ground before attempting any work on the motor
control circuitry.
HIGH CURRENT ARCS — Batteries can supply very high power, and arcing can
occur if they are short circuited. Always open the battery circuit before
working on the motor control circuit. Wear safety glasses, and use properly
insulated tools to prevent shorts.
LEAD ACID BATTERIES — Charging or discharging generates hydrogen gas,
which can build up in and around the batteries. Follow the battery man-
ufacturer’s safety recommendations. Wear safety glasses.
+
CAUTION

6Curtis 1356/1356P CAN Expansion Module Manual, Rev. A
2 — INSTALLATION & WIRING: Low Current Connections
pin name description
J1-1 B+ Battery positive.
Active High Digital Input1 &
J1-2 Input/Output 1 High Power PWM Active Low
Output1.
J1-3 Input 3 Active High Digital Input3.
J1-4 Input 5 Active High Digital Input5.
J1-5 Input 7 Active High Digital Input7.
J1-6 Input 9 Active High Digital Input9.
J1-7 Input 11 Active High Digital Input11.
J1-8 Input 13 Active High Digital Input13.
J1-9 Analog Input 2 Voltage or Resistive Input2.
Voltage or Resistive Input4 &
J1-10 Analog Input 4 /
Quadrature Encoder Input
Encoder A Phase A.
J1-11 CAN H CAN Bus High
Communication Line.
J1-12 +5V Regulated Low Power +5V
Output.
Table 1 24-Pin Molex Connector Pin Assignment
pin name description
J1-13 B- Battery negative.
Active High Digital Input2 &
J1-14 Input/Output 2 High Power PWM Active Low
Output2.
J1-15 Input 4 Active High Digital Input4.
J1-16 Input 6 Active High Digital Input6.
J1-17 Input 8 Active High Digital Input8.
J1-18 Input 10 Active High Digital Input10.
J1-19 Input 12 Active High Digital Input12.
J1-20 Analog Input 1 Voltage or Resistive Input1.
J1-21 Analog Input 3 Voltage or Resistive Input3.
Voltage or Resistive Input5 &
J1-22 Analog Input 5 /
Quadrature Encoder Input
Encoder B Phase B.
J1-23 CAN L CAN Bus Low
Communication Line.
J1-24 I/O GND Input and Output Ground
Reference.
Table 2 4-Pin Molex Connector Pin Assignment
pin name description
J2-1 Serial Rx /LED Enable Serial Receive /Status LED Enable.
J2-2 I/O GND Input and Output Ground Reference.
J2-3 Serial Tx / LED Output Serial Transmit / Status LED Output.
J2-4 +12V Unregulated Low Power +12V Output.
CONNECTIONS
e 1356 /1356P connections are made through 24-pin and 4-pin Molex
connectors. e mating plugs are Molex #39-01-2245 and #39-01-2045, and
the contact pins are #39-00-0059.
e individual pins are characterized in Tables 1 and 2.
24 23 22 21 20 19 18 17 16 15 14 13
121110987654321
J1 J2
12
34

Curtis 1356/1356P CAN Expansion Module Manual, Rev. A 7
2 — INSTALLATION & WIRING: Low Current Connections
Wiring recommendations
Power (Pins J1-1 and J1-13)
e B+ and B- cables should be run close to each other between the module
and the battery. For best noise immunity the cables should not run across the
center section of the module.To prevent overheating these pins, the wire gauge
must be sucient to carry the continuous and maximum loads that will be
seen at each pin.
Driver outputs (Pins J1-2 and J1-14)
e driver outputs produce high frequency (16 kHz) pulse waves that can
radiate RFI noise. e wire from the module to the load should be kept short
and routed with the return wire back to the module.
CAN bus (Pins J1-11 and J1-23)
It is recommended that the CAN wires be run as a twisted pair. However, many
successful applications at 125 kbit/s are run without twisting, simply using two
lines bundled in with the rest of the low current wiring. CAN wiring should
be kept away from the high current cables and cross it at right angles when
necessary. If the 1356 /1356P is at the end of the CAN bus, the bus needs to
be terminated by externally wiring a 120Ω½W resistor across CAN High and
CAN Low (for those models that do not have a 120Ωterminal resistor between
CAN H and CAN L).
All other low current wiring
e remaining low current wiring should be run according to standard practices.
Running low current wiring next to the high current wiring should always be
avoided.

8Curtis 1356/1356P CAN Expansion Module Manual, Rev. A
Fig. 3 Basic wiring diagram, Curtis 1356/1356P CAN expansion module.
2 — INSTALLATION & WIRING: Standard Wiring Diagram
WIRING: BASIC CONFIGURATION
A basic wiring diagram is shown in Fig. 3, and described below. e diagram
shows the standard power and battery connections, as well as some basic uses
for the inputs and outputs.
Power Connection
e battery is connected to the module’s B+ pin though a fuse, a diode, and a
keyswitch. e fuse protects the wiring in the event of a short or failure. e
return path of the coils is also brought back to the B+ pin to utilize the yback
diodes connected inside the module between B+ and each driver output.
e keyswitch is used to turn on the system. When the keyswitch is closed,
B+ goes high and the 1356 /1356P’s power supply brings up the module.
J1-11
J1-23
J1-13
J1-1
J1-2
J1-14
J1-3
J1-15
J1-4
J1-16
J1-5
J1-17
J1-6
J1-12
KEYSWITCH
SWITCH
BATTERY
(12–80V)
REVERSE
POLARITY
PROTECTION
PROPORTIONAL
VALVE
CONTACTOR
CAN PORT
1356 / 1356P
ENCODER A
ENCODER B
ANALOG INPUT 1
ANALOG INPUT 2
ANALOG INPUT 3
OUTPUT 1
OUTPUT 2
INPUT 3
INPUT 4
INPUT 5
INPUT 6
INPUT 7
INPUT 8
INPUT 9
CAN H
CAN L
+5V
ENCODER
J1-10
J1-22
J1-20
J1-9
J1-21
0–15V IN
RESISTIVE THROTTLE,
RTD, etc.
J2-4
J2-3
J2-1
SERIAL PORT
(4-pin Molex)
4
3
1
2
840
DISPLAY
8
6
5
+12V
RX
TX
J1-18
J1-7
J1-19
J1-8
INPUT 10
INPUT 11
INPUT 12
INPUT 13
J2-2
I/O GND
I/O GND J1-24

Curtis 1356/1356P CAN Expansion Module Manual, Rev. A 9
Driver Outputs
Each of the two driver outputs (Output 1, 2) is capable of driving a closed-loop
current-controlled proportional valve or a voltage-controlled contactor. Each
driver has independent mode, max, and dither settings.
ese are high-power drivers. e internal impedance to ground will cause
leakage current to ow through the output even when the output driver is o.
is leakage current can be enough (>2 mA) to light high-eciency LEDs.
In the wiring diagram, the output at J1-2 is shown driving a proportional
valve coil. is driver is programmed for Constant Current mode and would
have some Dither applied.
e second output, at J1-12, is driving a basic contactor coil. is output
is in the Constant Voltage mode and can be set to run at a lower voltage than
the nominal battery voltage.
Switch Inputs
All the inputs are used as Active High inputs (“On” when connected to B+).
In the wiring diagram, Input 13 (J1-8) is shown as an Active High input
switching to B+.
(Note that when Input/Output 1 or 2 is used as a switch input, its Op-
eration Mode must be set to 0; see pages 33 and 45.)
Analog Inputs
Analog Input 3, at J1-21, is shown being used with an RTD. is requires
setting Analog Input 3’s Input Type parameter to 1 = Resistive input (see pag-
es34 and 43).
CAN Bus
e 1356 /1356P has an internal 1 kΩbus termination resistor. is internal
impedance matches the system requirements for a mid-line connection or
short stub connection. e 1356 /1356P can communicate up to 1 Mbit/s on
a properly terminated/wired bus.
2 — INSTALLATION & WIRING: Standard Wiring Diagram

10 Curtis 1356/1356P CAN Expansion Module Manual, Rev. A
2 — INSTALLATION & WIRING: Application Example
WIRING: Application Example
e wiring diagram in Fig. 4 provides an example of a ngertip joystick appli-
cation for an electric forklift.
Fig. 4 Application example, Curtis 1356 /1356P CAN expansion module.
J1-11
J1-1
J1-12
KEYSWITCH
FINGERTIP JOYSTICKS
REVERSE
POLARITY
PROTECTION
CAN
PORT
1356 / 1356P
OUTPUT 2
+5V
CAN H
CAN L
OUTPUT 1
J1-14
CURTIS AC
CONTROLLER
J2-4
J2-3
J2-1
4
3
1
2
+12V
RX
TX
J1-24 I/O GND
INPUT 9
J2-2
I/O GND
INPUT 13 J1-8
2
1
6
5
4
3
J1-6
J1-10
J1-18
ANALOG INPUT 4
INPUT 10 1353
WARNING LIGHT
HORN PUSHBUTTON
INPUT 7
2
1
6
5
4
3
J1-5
J1-21
J1-17
ANALOG INPUT 3
INPUT 8
INPUT 5
2
1
6
5
4
3
J1-4
J1-9
J1-16
ANALOG INPUT 2
INPUT 6
INPUT 3
2
1
6
5
4
3
J1-3
J1-20
J1-15
ANALOG INPUT 1
INPUT 4
Reach FW/BW
Shift Left/Right
Tilt Up/Down
Lift Up / Lowering
PROGRAMMER
ANALOG INPUT 5 J1-22
INPUT 11
INPUT 12 J1-19
BUZZER
BATTERY
(12–80V)
FW
BW
J1-23
J1-7
J1-2
J1-13

Curtis 1356/1356P CAN Expansion Module Manual, Rev. A 11
INPUT/OUTPUT SIGNAL SPECIFICATIONS
e input/output signals wired to the 24-pin connector can be grouped by type
as follows; their electrical characteristics are discussed below.
— digital inputs
— driver outputs
— analog inputs with virtual digital input
— encoder inputs
— serial port
— CAN Bus interface
— auxiliary power supplies.
Digital Inputs
e 1356 /1356P has eleven digital inputs. In addition, the two driver outputs
(Input/Output 1 and Input/Output 2) can be programmed as digital inputs (as
long as the drivers are o: i.e., no current, voltage, or PWM output). Each of
these digital inputs has a pull-down resistor to B-. is provides an active high
input (“On” when connected to B+). e side eect of this pull-down resistor is
that there is a small leakage current in the two driver outputs when the output
driver is O. is leakage can be enough (>2mA) to light high-eciency LEDs.
2 — INSTALLATION & WIRING: I/O Signal Specifications
1
13
12
24
Because Input/Output 1 and Input/Output 2 can also be used as driver
outputs, it is important to ensure that Operation Mode is set appropriately.
When they will be used as digital inputs, the Operation Mode parameter must
be set to 0 = Active High Digital Input (see pages 33 and 45). Otherwise, a
direct short from the battery through the internal driver FET will occur when
the input is switched high and the FET is turned on.
DIGITAL INPUT SPECIFICATIONS
signal name pin logic threshold input impedance
Input/Output 1 J1-2 All models: 12 – 36V models:
Input/Output 2 J1-14 Low = 1.6 V about10kΩ
Input 3 J1-3 High = 4.0 V 36 – 80V models:
Input4 J1-15 about47kΩ
Input 5 J1-4
Input 6 J1-16
Input 7 J1-5
Input 8 J1-17
Input 9 J1-6
Input 10 J1-18
Input 11 J1-7

12 Curtis 1356/1356P CAN Expansion Module Manual, Rev. A
Driver Outputs
e 1356 /1356P contains two driver outputs. ese outputs have all the
features necessary to drive proportional valves as well as many other inductive
and non-inductive loads. A variable amount of dither (xed frequency com-
mand “jitter”) can be added to the PWM to prevent proportional valves from
sticking in place.
2 — INSTALLATION & WIRING: I/O Signal Specifications
DIGITAL OUTPUT SPECIFICATIONS
signal name pin max current impedance frequency
Input/Output 1 J1-2 3A 12 – 36V models: All models:
10kΩpulldowntoB- 16 kHz
Input/Output 2 J1-14 1A 36 – 80V models: 0–100% duty cycle
47kΩpulldowntoB-
e drivers can be set for Constant Current, Constant Voltage, or Direct PWM
control mode.
In Constant Current mode, the driver command of 0 to 100%
is interpreted as a current from 0 to the Max Output setting.
Internal current shunts are measured and fed back to a closed
loop PI controller to provide a steady current over changing
loads and supply voltages.
In Constant Voltage mode, the driver command of 0 to 100%
is interpreted as a voltage from 0 to Max Output. e battery
voltage is constantly monitored and fed back to a closed loop
PI controller to provide a steady voltage, compensating for
battery droop and discharge. If the command is higher than
the driver can output, the PWM will max out at 100%.
In Direct PWM mode, the driver command of 0 to 100% is
directly output on the driver.
Each driver is monitored and will detect a short in the load, a failed internal
driver FET, and/or an open in the load wiring. At near 0% and 100% PWM,
it is not possible to discern each fault and some faults will not be detected.
If the driver outputs are connected to inductive loads, the coil should
have a return line to the B+ pin of the 1356/1356P. is connection provides
a path for the internal freewheel diodes to clamp the turn-o spike. Failure
to make this connection with inductive loads can cause permanent damage to
the 1356 /1356P as well as propagate failures of other electronics in the system
due to the high voltage spike caused when an inductive load turns o without
a freewheel path.
1
13
12
24

Curtis 1356/1356P CAN Expansion Module Manual, Rev. A 13
2 — INSTALLATION & WIRING: I/O Signal Specifications
Analog Inputs
e 1356 /1356P has ve 0– 15V analog inputs. ese inputs are scaled down
by 5.76, clamped to 3.3V, and read by a 12-bit ADC internal to the MCU.
ANALOG INPUT SPECIFICATIONS
protected
voltage
signal name pin voltage input impedance range
Analog Input 1 J1-20 Nominal input voltage: Voltage Input Type:
Analog Input 2 J1-9 0–15V about21kΩ
Analog Input 3 J1-21 Input maximum Resistance Input Type: -1 V to B+
Analog Input 4 J1-10 reverse voltage:-1.7V about1kΩ
Analog Input 5 J1-22
e maximum resistive input on each analog input is 7.5 kΩ. e resistive or
voltage type of analog input can be selected by a Curtis programmer (1313/1314)
or CAN SDO message.
ese ve analog inputs can also be used as digital inputs. A unique fea-
ture of these digital inputs is that the active high/low thresholds are completely
programmable. us, these inputs can be used with analog sensors to detect
conditions like over/under pressure, high/low level points, etc.
Encoder Inputs
Analog Inputs 4 and 5 can be congured as a quadrature encoder input (En-
coder A and B). is standard quadrature encoder input accepts open collector
encoders with pull-up resistors in the 1356/1356P module. e encoder can be
powered from the +5V supply (J1-12) or the +12V supply (J2-4) while using
the I/O GND (J1-24) as a common.
ENCODER INPUT SPECIFICATIONS
protected
encoder frequency input voltage
phase pin vth lo vth hi max iimpedance range
A J1-10 1 kΩ
B J1-22 1.0 V 2.2 V 15 kHz (internal pull-up -1 V to B+
to +4.4 V)
1
13
12
24
1
13
12
24

14 Curtis 1356/1356P CAN Expansion Module Manual, Rev. A
Serial Port
e Curtis 1313/1314 programmer or the Curtis Model 840 can be connected
to the 1356 /1356P’s serial port, J2.
Power is provided through J2-4 (+12V) and J2-2 provides the I/O ground
reference.
When the 840 is connected to the serial port, it will alternately show
BDI, hour meter, and fault information.
e serial port can also be used as an external Status LED fault code display.
When the serial port is used for fault code display, a jumper must be added
between J2-1 and J2-4, and an LED is connected between J2-2 and J2-3.
SERIAL PORT SPECIFICATIONS
protected
supported voltage
signal name pin protocol /devices data rate range
TX J2-3 1313 Handheld Programmer, As required,
RX J2-1
1314 PC Programming Station, 9.6 to 56 kbit/s -0.3 V to 12 V
Curtis 840 Display
CAN Bus Interface
e CAN bus interface will comply with CAN2.0B, active from 50 kbit/s to
1Mbit/s communication rate.
e 1356 /1356P will be terminated by an internal 1kΩ resistor across
the CAN High and Low communication pins. is assumes a mid-truck con-
nection (not end-of-line).
If a 1356/1356P without terminal resistance (models ending in -4101
or -6101) is at the end of the CAN bus, the bus needs to be terminated by
externally wiring a 120 Ω, ½W resistor across CAN High and CAN Low.
2 — INSTALLATION & WIRING: I/O Signal Specifications
1
13
12
24
1
3
2
4
1
2
3
4

Curtis 1356/1356P CAN Expansion Module Manual, Rev. A 15
2 — INSTALLATION & WIRING: I/O Signal Specifications
Auxiliary Power Supplies
e 1356 /1356P provides +12V and +5V auxiliary output power for low pow-
er circuits such as ngertip joysticks, electronic throttle, Curtis programmer,
Curtis 840 display, or remote I/O boards. e return line for these low power
circuits is I/O GND. e maximum total combined output current is 200 mA.
1
13
12
24
1
3
2
4
Power
e power pins are each capable of carrying up to 9 A. Every application must
use B+ (J1-1) and B- (J1-13).
1
13
12
24
AUXILIARY POWER SUPPLY SPECIFICATIONS
signal name pin vout vout tolerance iout (max) ripple/noise
+12V J2-4 12 V 10 % 100 mA 2 %
+5V J1-12 5 V 5 % 100 mA 2 %

16 Curtis 1356/1356P CAN Expansion Module Manual, Rev. A
3 — CANopen COMMUNICATIONS
3CANopen COMMUNICATIONS
e 1356 /1356P adheres to the industry standard CANopen communication
protocol and thus will easily connect into many CAN systems, including those
using the Curtis AC and Vehicle System controllers. Any CANopen-compatible
master can be programmed to control the 1356/1356P.
e 1356 /1356P receives two incoming (MOSI) PDOs and responds with
two outgoing (MISO) PDOs. Dynamic mapping is available for the PDOs. All
programmable parameters and monitor parameters are accessible by standard
SDO transfer.
e time between incoming PDOs is monitored and if excessive, will
ag a fault. is allows the 1356 /1356P to know that the system is still under
master control. e 1356 /1356P also produces Heartbeat and Error messages,
which is the CiA-preferred safety and security method.
MINIMUM STATE MACHINE
e 1356 /1356P will run the CANopen minimum state machine as dened
by CiA. e CANopen minimum state machine has four dened states: Ini-
tialization, Pre-Operational, Operational, and Stopped.
When the 1356 /1356P powers up, it goes to the Initialization state; this is
also known as the Boot-up state. No CAN communications from the 1356/1356P
are transmitted in this state although the 1356 /1356P listens to the CAN bus.
When the 1356 /1356P has completed its startup and self-tests, it issues an ini-
tialization heartbeat message and automatically goes to the Pre-Operational state.
In the Pre-Operational state, the 1356 /1356P can receive and respond to
SDOs and NMT commands, and will send its heartbeat. It will not receive or
send PDOs (unless PDO-MISO cyclic transmitting is enabled). After receiving
an Operational State NMT command, the 1356 /1356P will enter the Opera-
tional state (full normal operation).
In the Operational state, the 1356 /1356P will start receiving and respond-
ing to PDOs and process all other necessary CANopen messages.
Transmit Boot-up
Initialization
Pre-Operational
Operational
Stopped
Power-On
Reset
Reset
Module
Reset
Communication
This manual suits for next models
1
Table of contents
Popular Computer Hardware manuals by other brands
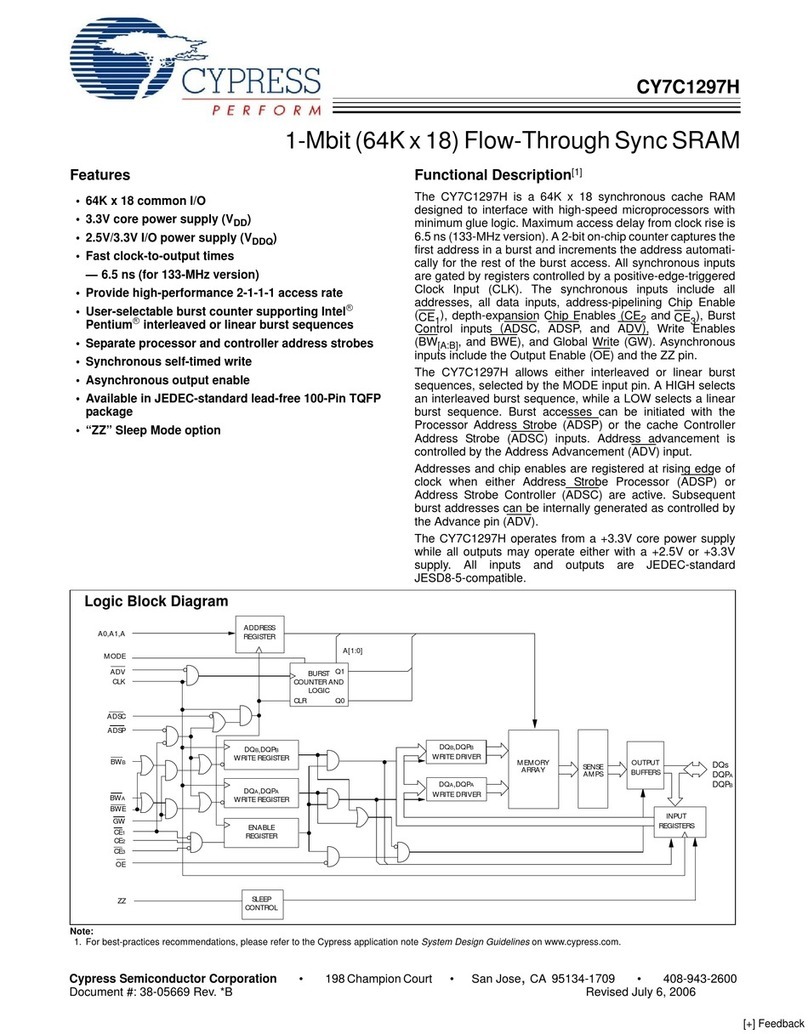
Cypress Semiconductor
Cypress Semiconductor CY7C1297H Specification sheet

Roland
Roland SRX-98 owner's manual
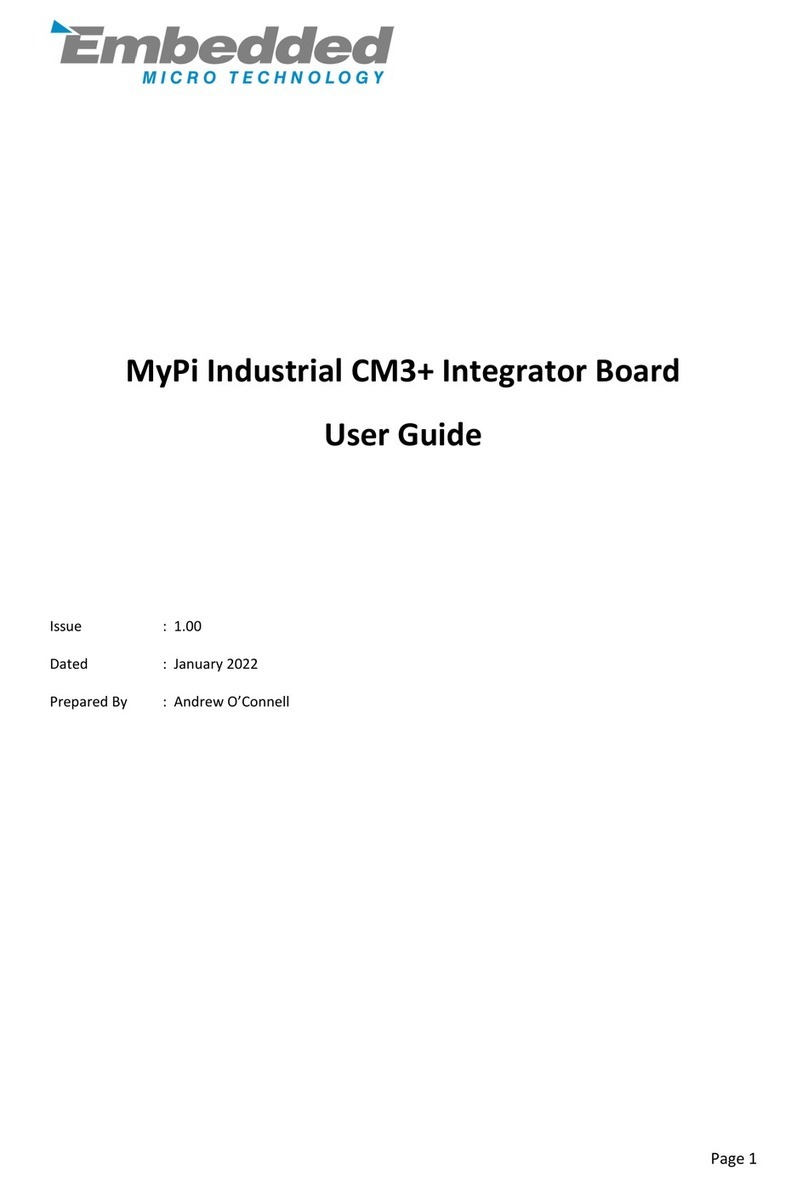
Embedded Micro Technology
Embedded Micro Technology MyPi user guide
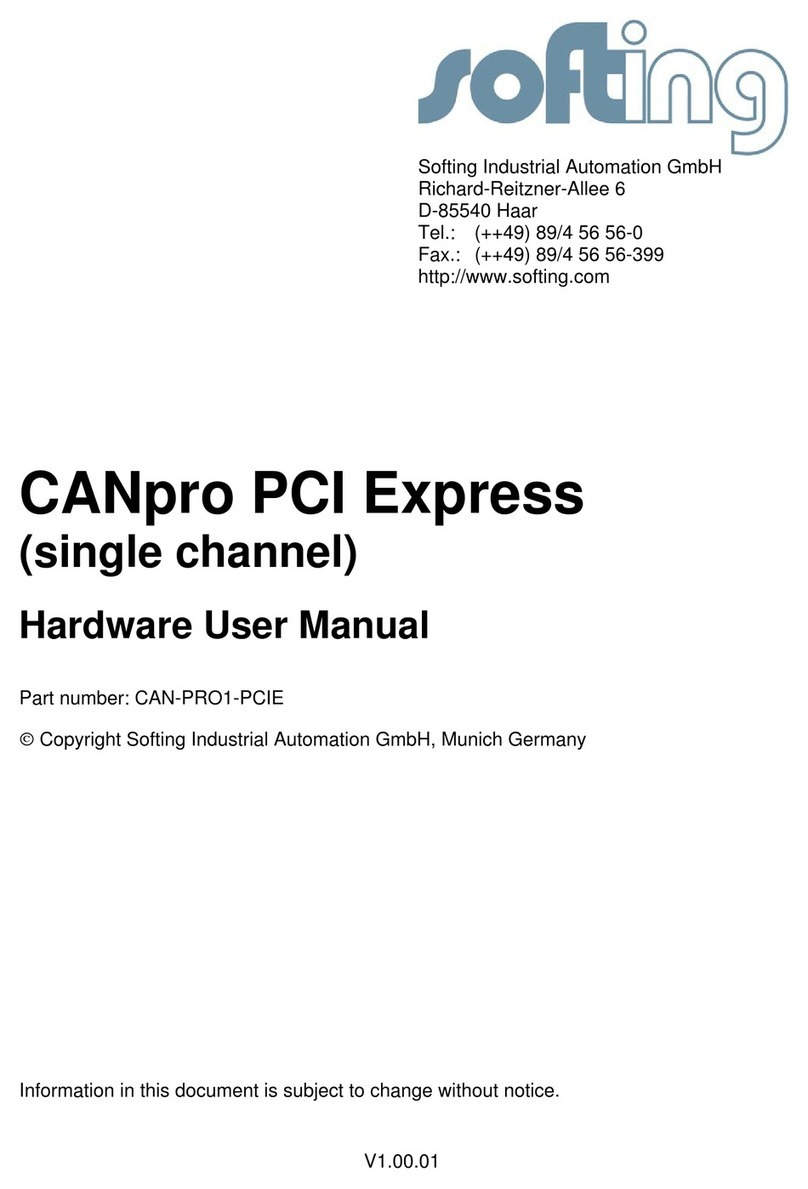
Softing
Softing CAN-PRO1-PCIE Hardware user manual
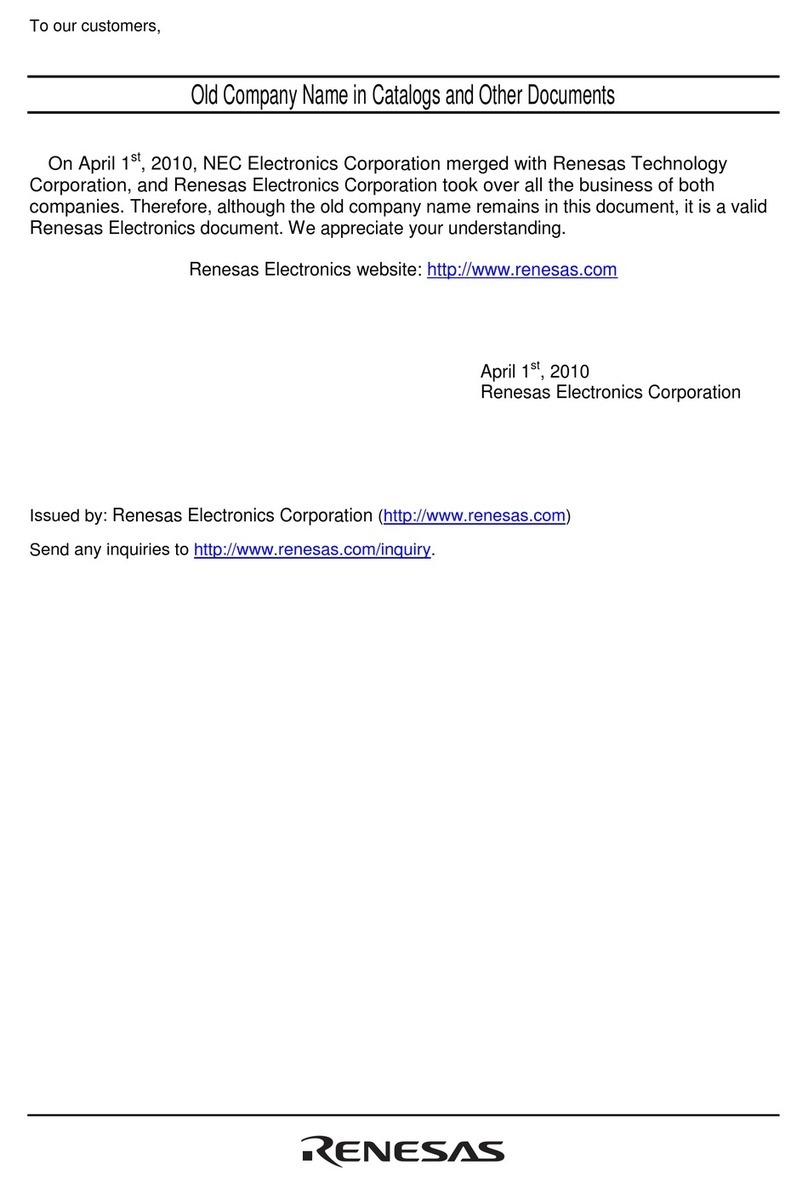
Renesas
Renesas MCU Board for PC4504 Emulator System... user manual
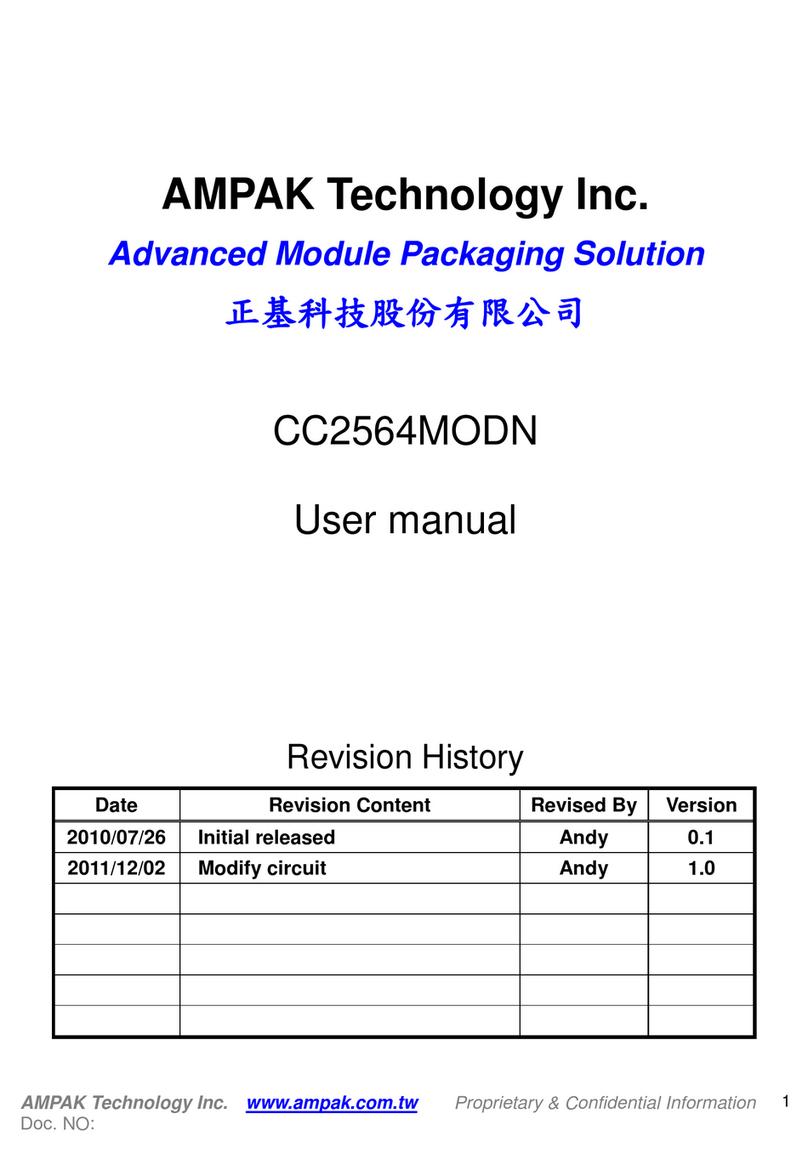
Ampak
Ampak CC2564MODN user manual