CustomCrimp D165NP Series User manual

1Page
D165NP SERIES HYDRAULIC HOSE
CRIMPER OPERATORS MANUAL

2Page
SAFETY PRECAUTIONS
READ INSTRUCTIONS AND IDENTIFY ALL
COMPONENT PARTS BEFORE USING CRIMPER
CRIMPER CAN PRODUCE 60 TONS OF FORCE
KEEP HANDS AWAY FROM PINCH POINTS
CONSULT CRIMP SPECIFICATIONS FOR CORRECT
MACHINE SETTINGS AND CRIMP MEASUREMENTS
ALWAYS WEAR EYE PROTECTION
Rev 11/01/2005
For Parts and Service, Contact:
Custom Machining Services, Inc.
Valparaiso, In 46383
(219) 462-6128

3Page
SPECIFICATIONS
Die Series-----------------------------------------------------------------------CC020/NP60 Series
Maximum Cylinder Force---------------------------------------------------------------------60 Ton
Maximum Hose Diameter (2 Wire)-----------------------------------------------------1 1/4 Inch
Maximum Hose Diameter (4 Wire)-----------------------------------------------------1 1/4 Inch
Maximum Hose Diameter (6 Wire)----------------------------------------------------------1 Inch
Crimper Depth ---------------------------------------------------------------------------------------22”
Crimper Width--------------------------------------------------------------------------------------12.5”
Crimper Height------------------------------------------------------------------------------------22.25”
Weight----------------------------------------------------------------------------------------------140 Lb
Pump-----------------------------------------------------------------------------------------------Electric
Pump HP-------------------------------------------------------------------------------------1 HP(110V)
Reservoir Capacity--------------------------------------------------------------------------------1 Gal
Oil Type----------------------------------------------------------------------ISO Viscosity Grade 46
Electric Power Requirement---------------------------------------------------------------------110V

4Page
COMPONENT IDENTIFICATION
Oil Fill &
Vent CapVent
Plug
Cylinder/Top
Pusher
Hydraulic Pump
Calibration
Adjustment
Screw
Micrometer
Micro-Stop
Switch
Power
Switch
&Circuit
Breaker
Retraction
Stop
Die Set
Pusher Plate
Start/Stop Switch Die Storage Shelf

5Page
CALIBRATION CHECK PROCEDURE
QUICK START GUIDE
STANDARD
MICROMETER
• Remove reservoir plug and replace with Oil Fill and Vent
Cap. The Oil Fill and Vent cap and the work light bulb are found in
the accessories box.
• Place the crimper on a sturdy bench in a well lit area, and
plug the crimper directly into a 115 V 15 Amp wall outlet. Do not
run the crimper on an extension cord as low voltage can damage
the motor.
• The oil level in the pump should be approximately
1-1/2 inches below the fill plug. If necessary,
replenish with ISO Viscosity Grade 46 hydraulic
oil.
Note: The crimper is calibrated prior to shipment, but
a calibration check is recommended prior to using
the crimper for the first time.
• Lubricate all contact surfaces and place
the Cone Insert, any Small Series die set and
the Standard Pusher in the crimper in the order
shown. Note that a hose and fitting are not required for
an initial calibration check. Note: failure to lubricate all
contact surfaces can cause the Cone Insert and/or the dies
to seize in the cone base.
• Slide the Pusher onto the stud on the hydraulic ram.
• Set the Micro-Crimp adjuster at “95”
• Press and hold the start switch bulb.
• If the ram extends and the crimper shuts off approximately
1 second after the dies are completely closed and the pump starts
to build pressure, the crimper is correctly calibrated.
• If the time to shut off is not approximately 1 second, the
crimper must be recalibrated. Recalibrate per instructions in this
manual
FOLLOW THESE STEPS BEFORE USING THE CRIMPER FOR THE FIRST TIME

6Page
CRIMPING INSTRUCTIONS
Lubrication of the cone
must be done prior using
for the first time.
.
Lubricate die fingers, all
contact surfaces and die
cones.
Use care to be certain
that the die halves do not
overlap.
Place the die set and hose
and fitting loosely in the
cone insert.
Place the Pusher Plate on
top of the die set.
Correct alignment of the
hose and fitting in the die
set is shown. Reference
crimp specifications for fit-
ting locations.
Slide the Pusher onto the stud
on the hydraulic ram and press
and hold the start switch until
the motor shuts off.
Check the finished crimp
diameter to be certain that it is
within the crimp specification
limits.
Adjust Micrometer
per hose and fitting
specification.

7Page
CALIBRATION AND FEATURES
CALIBRATION INSTRUCTIONS
CRIMPER FEATURES
The easily removable Coupling Stop makes
repetitive crimps faster by not having to visu-
ally align the fitting before each crimp.
• After proper lubrication, place any standard die set in the
compression cone and the pusher plate on top.
• Set the Micro-Crimp adjuster at “95”
• Press and hold the start switch bulb.
• If the ram extends and the crimper shuts off
approximately 1 second after the dies are complete-
ly closed and the pump starts to build pressure, the
crimper is correctly calibrated.
• If the time to shut off is not approximately
1 second, the crimper must be recalibrated. Reca- li-
brate as follows:
• Hold the micrometer barrel with a 5/16 inch open end wrench and
rotate the stem either in or out with a 5/32 inch hex key wrench.
• If the motor shuts off too quickly or before the dies are complete-
ly closed, rotate the stem in.
• If the motor does not shut off or shuts off in substantially more
than 1 second, rotate the stem out.
The adjustable retraction stop limits the
retraction of the ram to only the amount
required to easily remove the hose and fit-
ting. This feature saves time when doing
multiple crimps.

8Page
TROUBLESHOOTING
PROBLEM: CRIMPER WILL NOT RUN AT ALL
The white rocker switch is also a circuit breaker. Check to see that the circuit breaker has not been
tripped
Check the wall outlet. The crimper comes from the factory wired for a 115 volt single phase circuit.
Use of extension cords or outlets with inadequate power can damage the motor . Do not run the crimper
from a portable power source.
Check the stop switch mounted to the switch bracket under the Micro-Crimp Adjuster. This is a nor-
mally closed switch and if it does not close the crimper will not operate.
CAUTION: Do not operate the crimper with this switch jumpered as the pump will not shut off and the
brackets can be damaged.
Check the pneumatically actuated switch in the electrical box mounted on the motor. This switch
controls power to the motor and is actuated with air pressure from the pendant switch bulb.
PROBLEM: CRIMP DIAMETER TOO LARGE
Incorrect setting of the Micro-Crimp Adjuster. Check crimp specifications.
(NOTE: All published machine settings are approximate. To correct for slight variances, the gauge settings
may be adjusted for the specific hose, fitting and size combination.)
Incorrect die being used. Each die has a range of approximately 3mm (.120 in) above the closed
diameter of the die. The closed diameter is the die size stamped on the die ring.
Check crimper calibration and re-calibrate if required.
Inadequate pump pressure. Check oil level in the pump. It should be 1-1/2 to 2 inches below the fill
plug. Replenish with ISO Viscosity Grade 46 hydraulic oil.
Inadequate lubrication of the dies and compression ring causing the pump to work harder than normal
to reach the required diameter. Use only the grease shipped with the machine or equivalent.
Inadequate pressure being generated by the pump. This is most likely if the crimper can crimp the
smaller size hoses and not the larger hoses. When correctly adjusted, the pump should generate ap-
proximately 10,000 psi.
Do Not adjust pump to produce in excess of 10,000 psi as damage to components or personal injury may
result.
No pressure being generated by the pump. There should be a definite change in pitch of the pump
as it cycles into high pressure mode and begins to “work” harder.
PROBLEM: CRIMP DIAMETER TOO SMALL
Incorrect setting of the Micro-Crimp Adjuster. Check crimp specifications.
( NOTE: All published machine settings are approximate. To correct for slight variances, the gauge set-
tings may be adjusted for the specific hose, fitting and size combination.)
Incorrect die being used (See die range under Crimp Diameter too Large)
Check crimp diameter and re-calibrate if necessary
PROBLEM: DIES STICKING IN COMPRESSION CONE
Inadequate lubrication of the compression cone and die surfaces. Use only the grease shipped with
the machine or equivalent.

9Page
COMPONENT IDENTIFICATION

10Page
COMPONENT IDENTIFICATION

11Page
1102158 60 Ton Body / Top Flange 1
2100651 60 Ton Piston 1
3227-9250 227 Disogrin O-Ring 1
4101106 Piston End Cap 1
591251A424 3/8-24 x 1 SHCS 6
6100760_12 60 Ton Spring 1
7100653 Spring Plug 1
8F1-POM-3.75X4.00X0.375 3.75 x 4.00 x 0.375 Wear Ring 2
93500-4000-0375 POLYPAK 3.50 x 4.00 x 0.375 Polypak 1
10 93744A160 3/8 Copper Flat Washer 1
11 91251A633 3/8-16 x 2 1/4 SHCS 1
12 SH940-35 375 Ram Wiper 1
13 102169 60 Ton Retaining Ring 1
60 Ton Cylinder / Top Flange Assembly (102219)
Item Part Number Description Qty
12
13
8
5
4
3
2
9
8
6
7
111
10
1
5
4
2
3
1102214 Micrometer Suspension Flange 1
2102217 Micrometer Brace 1
3102215 Micrometer Base Bracket 1
491253A194 8-32 x 1/2 HSFHCS 4
598296A245 3/16 Dia. x 1/2 Spring Pin 1
D165 Micrometer Mount Assembly (102220)
Item Part Number Description Qty
COMPONENT IDENTIFICATION
Table of contents
Popular Tools manuals by other brands

Komshine
Komshine KOC-125 instructions
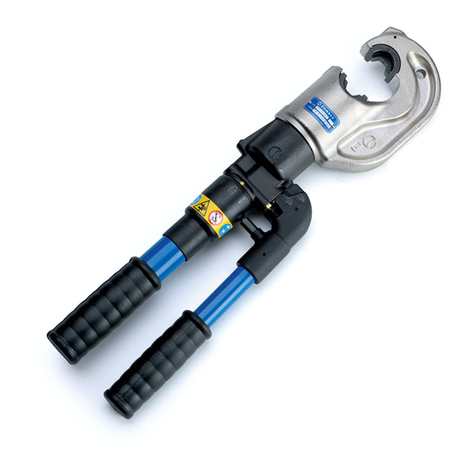
Cembre
Cembre HT131LN-C Operation and maintenance manual
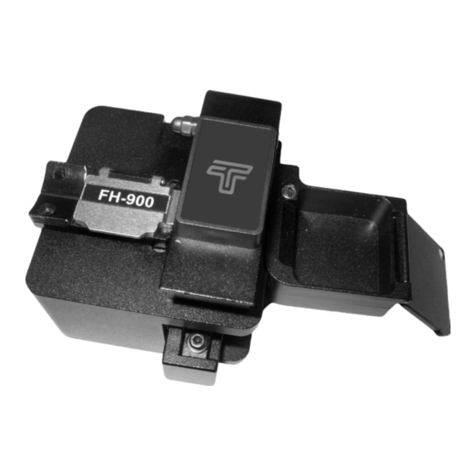
Tempo Communications
Tempo Communications 915CL instruction manual
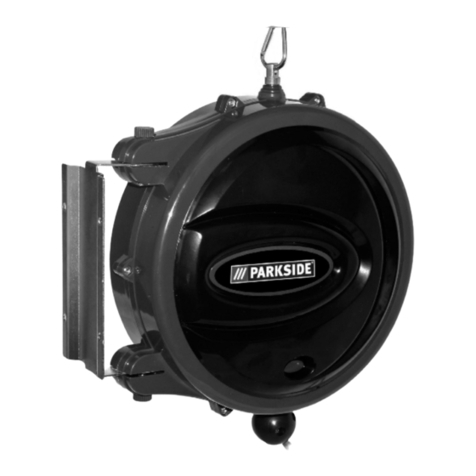
Parkside
Parkside PDST 10 A1 Operation and safety notes translation of the original instructions

Hilti
Hilti SD 4500 operating instructions

wto
wto 4201 Operating instruction