CWT GFM A0A0161 User manual

GFM
Gas Flow Monitor
Operation / Installation Manual
Manual Part Number: A8M5028
Revised: 01/23/2017
Computer Weld Technology, Inc.
10702 Old Bammel N Houston Rd.
Houston, TX 77086
Phone: (713) 462
-2118
Fax: (713) 462
-2503
Email: cwt@cweldtech.com


SAFETY PRECAUTIONS – READ BEFORE USING
Welding is not particularly hazardous when certain safety practices are followed. Everyone using
this equipment should be thoroughly trained in safe welding practices. Failure to observe safe
practices may cause serious injury.
Handling welding torches presents no danger if the appropriate safety regulations are strictly
adhered to. For example:
•Starting procedures must be reserved for those fully conversant with processes relating to arc welding
equipment.
•Arc welding can prove damaging to eyes, skin, and hearing! It is therefore imperative that both
management and operators understand and follow the ANSI Standard Z49.1, SAFETY IN WELDING
ANDCUTTING. All Personal Protective Equipment (PPE) shall be in place in accordance with this
referenced specification and all other applicable and governing regulations.
•The operating data provided in the Specifications are maximum values. Overloading the welding torch
will inevitably damage the product and void any and all warranties.
•Before changing any parts on the torch or control box, disconnect the torch from the welding power
source and disconnect the control box input power source. Unplug the control box from the electrical
outlet.
•The operating instructions for all other welding components - e.g. power source, wire feed and cooling
unit must be followed per the manufacturer’s recommendations.
•Never pull the cable assembly across sharp edges or set down on a hot surface.
•Never move the torch by pulling or dragging by the welding torch or cable.
•Curtains or partitions shall be installed to protect other workers or observers from arc radiation.
•When handling gas cylinders, consult the instructions issued by the manufacturers and the suppliers of
the pressurized gas.
•Work pieces that have been degreased using chlorinated solvents must be sprayed down with clean
water before welding starts to avoid the risk of phosgene forming. For the same reason, no degreasing
baths containing chlorine must be placed close to the welding point.
•All vapors given off by metals can cause harm and a special warning is attached to lead, cadmium,
copper, zinc, and beryllium. Take appropriate precautions to ensure that the legal maximum levels of
toxic concentrations are not exceeded.
•Do not touch the welding torch with bare skin until it has had adequate time to cool down.
•Wait to adjust the rotation diameter until the torch has cooled to room temperature.
Fume and Gases
FUMES AND GASES can be hazardous. Welding and cutting
produces fumes and gases. Breathing these fumes and gases
can be hazardous to your health.
•Keep your head out of the fumes. Do not breathe the fumes.
•If inside, ventilate the area and/or use local forced ventilation at the arc to remove welding and cutting
fumes and gases. The recommended way to determine adequate ventilation is to sample for the
composition and quantity of fumes and gases to which personnel are exposed.
•If ventilation is poor, wear an approved air-supplied respirator.
•Read and understand the Safety Data Sheets (SDSs) and the manufacturer’s instructions for
adhesives, coatings, cleaners, consumables, coolants, degreasers, fluxes and metals.
•Work in a confined space only if it is well ventilated, or while wearing an air-supplied respirator. Always
have a trained watch-person nearby. Welding fumes and gases can displace air and lower the oxygen
level causing injury or death. Be sure the breathing air is safe.

•Do not weld or cut in locations near degreasing, cleaning, or spraying operations. The heat and rays of
the arc can react with vapors to form highly toxic and irritating gases.
•Do not weld or cut on coated metals, such as galvanized, lead, or cadmium plated steel, unless the
coating is removed from the weld area, the area is well ventilated, and while wearing an air supplied
respirator. The coatings and any metals containing these elements can give off toxic fumes if welded.
Arc Rays
ARC RAYS can burn eyes and skin. Arc rays from welding and cutting processes
produce intense visible and invisible (ultraviolet and infrared) rays that can burn eyes
and skin. Sparks fly off from the weld.
•Wear an approved welding helmet fitted with a proper shade of filter lenses to protect your face and
eyes from arc rays and sparks when welding, cutting, or watching (see ANSIZ49.1 and Z87.1 listed in
Safety Standards).
•Wear approved safety glasses with side shields under your helmet.
•Use protective screens or barriers to protect others from flash, glare and sparks; warn others not to
watch the arc.
•Wear body protection made from durable, flame resistant material (leather, heavy cotton, wool).
•Body protection includes oil-free clothing such as leather gloves, heavy shirt, cuff less trousers, high
shoes and a cap.
Welding and Cutting
Welding or cutting on closed containers such as tanks, drums or pipes, can cause
them to blow up. Sparks can fly off from the welding or cutting arc. The flying sparks,
hot work piece and hot equipment can cause fires and burns. Accidental contact of
electrode to metal objects can cause sparks, explosion, overheating or fire. Check
and be sure the area is safe before doing any welding or cutting.
•Remove all flammables within 35 ft. (10.7 m) of the welding or cutting arc. If this is not possible, tightly
cover them with approved covers.
•Do not weld or cut where flying sparks can strike flammable material.
•Protect yourself and others from flying sparks and hot metal.
•Be aware that welding sparks and hot materials from welding and cutting can easily go through small
cracks and openings to adjacent areas.
•Watch for fire, and keep a fire extinguisher nearby.
•Be aware that welding or cutting on a ceiling, floor, bulkhead or partition can cause fire on the hidden
side.
•Do not weld or cut on containers that have held combustibles, or on closed containers such as tanks,
drums, or pipes unless they are properly prepared according to AWS F4.1 and AWS A6.0 (see Safety
Standards).
•Do not weld or cut where the atmosphere may contain flammable dust, gas, or liquid vapors (such as
gasoline).
•Connect work cable to the work as close to the welding or cutting area as practical to prevent welding
or cutting current from traveling long, possibly unknown paths and causing electric shock, sparks and
fire hazards.
•Do not use welder to thaw frozen pipes.
•Remove stick electrode from holder or cut off welding wire at contact tip when not in use.
•Remove any combustibles, such as a butane lighter or match, from your person before doing any
welding or cutting.

•After completion of work, inspect area to ensure it is free of sparks, glowing embers, and flames.
•Use only correct fuses or circuit breakers. Do not oversize or by-pass them.
•Follow requirements in OSHA 1910.252 (a) (2) (iv) and NFPA 51B for hot work and have a fire watcher
and extinguisher nearby.
•Read and understand the Safety Data Sheets (SDSs) and the manufacturer’s instructions for
adhesives, coatings, cleaners, consumables, coolants, degreasers, fluxes and metals.
Electric Shock
Touching live electrical parts can cause fatal shocks or severe burns. The electrode
and work circuit is electrically live whenever the output is on. The input power circuit
and machine internal circuits are also live when power is on. In gas metal arc welding
(GMAW), the wire, wire reel, drive roll housing and all metal parts touching the
welding wire are electrically live. Incorrectly installed or improperly grounded
equipment is a hazard.
•Do not use AC output in damp areas, if movement is confined, or if there is danger of falling.
•Use AC output ONLY if required for the welding or cutting process.
•If AC output is required; use remote output control if present on unit. Additional safety precautions are
required when any of the following electrically hazardous conditions are present: in damp locations or
while wearing wet clothing; on metal structures such as floors, gratings or scaffolds; when in cramped
positions such as sitting, kneeling or lying; or when there is a high risk of unavoidable or accidental
contact with the workpiece or ground. For these conditions, use the following equipment in order
presented: 1) a GMAW DC constant voltage (wire) welder, 2) a DC manual (stick) welder or 3) an AC
welder with reduced open circuit voltage. In most situations, use of a DC, constant voltage wire welder
is recommended. And, do not work alone!
•Disconnect input power or stop engine before installing or servicing equipment. Lockout/tagout input
power according to OSHA 29 CFR 1910.147 (see Safety Standards).
•Properly install, ground, and operate this equipment according to its Owner’s Manual and national,
state/provincial and local codes.
•Always verify the supply ground – check and be sure that input power cord ground wire is properly
connected to ground terminal in disconnect box or that cord plug is connected to a properly grounded
receptacle outlet.
•When making input connections attach proper grounding conductor first and double-check
connections.
•Keep cords dry, free of oil and greases and protected from hot metal and sparks.
•Frequently inspect power cord for damage or bare wiring. Replace cord immediately if damaged. Bare
wiring can kill.
•Turn off all equipment when not in use.
•Do not use worn, damaged, undersized or poorly spliced cables.
•Do not drape cables over your body.
•If earth grounding of the workpiece is required; ground it directly with a separate cable.
•Do not touch electrode if you are in contact with the work, ground or another electrode from a different
machine.
•Do not touch electrode holders connected to two welding machines at the same time since double
open circuit voltage will be present.
•Use only well-maintained equipment. Repair or replace damaged parts at once. Maintain unit according
to manual.
•Wear a safety harness if working above floor level.
•Keep all panels and covers securely in place.
•Clamp work cable with good metal-to-metal contact to workpiece or worktable as near the weld as
practical.

•Insulate work clamp when not connected to workpiece to prevent contact with any metal object.
•Do not connect more than one electrode or work cable to any single weld output terminal. Disconnect
cable for process when not in use.
Cylinders
Compressed gas cylinders contain gas under high pressure. If damaged, a cylinder
can explode. Since gas cylinders are normally part of the welding process, be sure to
treat them carefully.
•Protect compressed gas cylinders from excessive heat, mechanical shocks, physical damage, slag,
open flames, sparks and arcs.
•Install cylinders in an upright position by securing to a stationary support or cylinder rack to prevent
falling or tipping.
•Keep cylinders away from any welding, cutting or other electrical circuits.
•Never drape a welding electrode or cutting torch over a gas cylinder.
•Never allow a welding electrode or cutting torch to touch any cylinder.
•Never weld on a pressurized cylinder – explosion will result.
•Use only the correct compressed gas cylinders, regulators, hoses and fittings designed for the specific
application; maintain them and associated parts in good condition.
•Turn face away from valve outlet when opening cylinder valve. Do not stand in front of or behind the
regulator when opening the valve.
•Keep protective cap in place over valve except when cylinder is in use or connected for use.
•Use the right equipment, correct procedures and sufficient number of persons to lift and move
cylinders.
•Read and follow instructions on compressed gas cylinders, associated equipment, and Compressed
Gas Association (CGA) publication P-1 listed in Safety Standards.

Additional Safety Warnings for Installation, Operation and Maintenance
READ INSTRUCTIONS
•Read and follow all labels and the Owner’s Manual carefully before installing,
operating, or servicing the unit.
•Read the safety information at the beginning of the manual and each section.
•Use only genuine replacement parts from the manufacturer.
•Perform maintenance and service according to the Owner’s Manual, industry
standards and national, state/provincial and local codes.
ELECTRIC AND MAGNETIC FIELDS (EMF) can affect implanted Medical Devices
•Wearers of Pacemakers and other Implanted Medical Devices should keep
away.
•Implanted Medical Device wearers should consult their doctor and the device
manufacturer before going near arc welding, spot welding,
gouging, plasma arc cutting or induction.
H.F. RADIATION can cause interference
•High-frequency (H.F.) can interfere with radio navigation, safety services,
computers and communications equipment.
•Have only qualified persons familiar with electronic equipment perform this
installation. The user is responsible for having a qualified electrician promptly
correct any interference problem resulting from the installation.
•Have the installation regularly checked and maintained.
•If notified by the FCC about interference, stop using the equipment at once.
•Keep high-frequency source doors and panels tightly shut, keep spark gaps at correct setting and use
grounding and shielding to minimize the possibility of interference.
California Proposition 65 Warnings
Welding or cutting equipment produces fumes or gases that contain chemicals known to the State
of California to cause birth defects and in some cases, cancer. (California Health & Safety Code
Section 25249.5 et seq.) This product contains chemicals known to the State of California to cause
cancer and birth defects or other reproductive harm. Wash your hands after using.
EMF Information
Electric current flowing through any conductor causes localized electric and magnetic fields (EMF).
The current from arc welding (and allied processes including spot welding, gouging, plasma arc
cutting, and induction heating operations) creates an EMF field around the welding circuit. EMF
fields may interfere with some medical implants, e.g. Pacemakers. Protective measures for
persons wearing medical implants have to be taken. For example, restrict access for passersby or
conduct individual risk assessment for welders. All welders should use the following procedures in
order to minimize exposure to EMF fields from the welding circuit:
1. Keep cables close together by twisting or taping them, or using a cable cover.
2. Do not place your body between welding cables. Arrange cables to one side and away from the
operator.
3. Do not coil or drape cables around your body.
4. Keep head and trunk as far away from the equipment in the welding circuit as possible.

5. Connect work clamp to workpiece as close to the weld as possible.
6. Do not work next to, sit or lean on the welding power source.
7. Do not weld while carrying the welding power source wire feeder.
About Implanted Medical Devices:
Implanted Medical Device wearers should consult their doctor and the device manufacturer before
performing or going near arc welding, spot welding, gouging, plasma arc cutting, or induction
heating operations. If cleared by your doctor, then following the above procedures is
recommended.
Safety Standards
•ANSI Standard Z49.1, SAFETY IN WELDING AND CUTTING, American Welding Society, 2501 N.W.
7th St., Miami, FL 33125. Free download at http://www.aws.org/technical/AWS_Z49.pdf
•ANSI Standard Z41.1, STANDARD FOR MEN’S SAFETY - TOE FOOTWEAR obtainable from the
American National Standards Institute, 1430 Broadway, New York, NY 10018.
•ANSI Standard Z49.2, FIRE PREVENTION IN THE USE OF CUTTING AND WELDING
PROCESSES obtainable from the American National Standards Institute, 1430 Broadway, New York,
NY 10018.
•OSHA, SAFETY AND HEALTH STANDARDS, 29CRF 1910, obtainable from the U.S. Government
Printing Office, Washington, D.C. 20402.
•OSHA, PERSONAL PROTECTIVE EQUIPMENT, OSH 3151-12R 2003. Free download at
https://www.osha.gov/Publications/osha3151.pdf

Table of Contents
1.0 OVERVIEW..................................................................................................................... 1
1.1 SYSTEM REQUIREMENTS........................................................................................................................1
1.2 BENEFITS ....................................................................................................................................................1
1.3 FEATURES...................................................................................................................................................1
1.4 MECHANICAL SPECIFICATIONS.............................................................................................................1
1.5 SENSOR SPECIFICATIONS......................................................................................................................2
1.6 MODELS.......................................................................................................................................................2
2.0 INSTALLATION.............................................................................................................. 3
2.1 OPTIONS......................................................................................................................................................3
2.2 GAS LINE HOOKUP....................................................................................................................................3
2.3 CABLE HOOKUP.........................................................................................................................................3
2.4 GAS FLOW LIMITS......................................................................................................................................4
2.5 GAS FLOW VOLUME..................................................................................................................................4
3.0 OPERATION................................................................................................................... 5
3.1 FIRMWARE VERSION................................................................................................................................5
3.2 PROGRAM LIMITS......................................................................................................................................5
3.3 PARAMETERS.............................................................................................................................................6
4.0 SETTING GAS FLOW CONTROL LIMITS................................................................... 9
4.1 DESCRIPTION.............................................................................................................................................9
4.2 SETUP ..........................................................................................................................................................9
5.0 GAS FLOW SURGE “PEAK” MEASUREMENT....................................................... 10
5.1 DESCRIPTION.......................................................................................................................................... 10
5.2 SETUP ....................................................................................................................................................... 10
6.0 GAS FLOW USAGE LOG ........................................................................................... 11
6.1 DESCRIPTION.......................................................................................................................................... 11
6.2 SETUP ....................................................................................................................................................... 11
6.3 RESET LOG MODE CLOCK.................................................................................................................... 11
6.4 RESET LOG MODE VOLUME................................................................................................................. 12
7.0 GFM CONNECTOR PIN ASSIGNMENT .................................................................... 13
7.1 AUX CONNECTOR................................................................................................................................... 13
8.0 POWER OPTIONS AND BATTERY SPECIFICATION/CHANGING ........................ 14
8.1 POWER OPTIONS................................................................................................................................... 14
8.2 BATTERY SPECIFICATIONS.................................................................................................................. 16
8.3 CHANGING THE BATTERY.................................................................................................................... 16
9.0 MODEL SPECIFICATIONS......................................................................................... 18
9.1 120/240 VAC PORTABLE GFMSYSTEM P/N: A0A0161.................................................................. 18
9.2 120/240 VAC IN-LINE GFMSYSTEM P/N: A0A0162 ........................................................................ 19
9.3 ADM IIIGFMSYSTEM P/N: A0A0163 ............................................................................................. 20
9.4 ADM IVGFMSYSTEM P/N: A0A0164............................................................................................. 21
9.5 WDL IIGFMSYSTEM P/N: A0A0165 .............................................................................................. 22

10.0 GFM ENCLOSURE SPECIFICATIONS.................................................................. 23
10.1 GFMENCLOSURE PARTS LIST......................................................................................................... 23
10.2 GFMMOUNTING DIMENSIONS......................................................................................................... 24
11.0 CABLE SPECIFCATIONS....................................................................................... 26
11.1 GFMAUX CABLE P/N: A3W0352........................................................................................................ 26
11.2 ADM IIIGFMSENSOR CABLE P/N: A3W0356 .............................................................................. 27
11.3 ADM IVGFMSENSOR CABLE P/N: A3W0350.............................................................................. 28
11.4 WDL IIGFMSENSOR CABLE P/N: A3W0351 ............................................................................... 29
12.0 MODBUS SCPECIFICATIONS ................................................................................ 30
12.1 GFM MODBUS REGISTER DATA.......................................................................................................... 30
12.2 MODBUS COILS CR [1..16]..................................................................................................................... 30
12.3 MODBUS REGISTER REG [1..10].......................................................................................................... 31
12.4 MODBUS SERIAL PORT CONNECTIONS............................................................................................ 31

1
1.0 OVERVIEW
1.1 Description
The Gas Flow Monitor (GFM) is designed to precisely measure the flow rates of
welding shielding gases. WARNING – DO NOT USE WITH ANY FLAMMABLE
GASES. The unit comes in both "portable" and "in-line" models and is software
configurable for English or Metric units of measure. The portable version can be
used to check the gas flow rates directly at the welding torch. The unit is battery
powered (and rechargeable) which allows it to be carried throughout the shop. This
version is ideal for use by maintenance personnel to correctly set and verify shielding
gas flow rates at the welding torch. The GFM
has 6 selectable gas settings,
ARGON, Argon/ CO2(90/10), Argon/ CO2(80/20), Argon/ CO2(75/25), Helium,
and CO2. The GFM
can be custom ordered and configured for additional gas
mixtures.
1.2 Benefits
The "in-line" version is designed to be permanently installed in a welding fixture to
continuously monitor the gas flow rate. When used in this manner the GFMcan
provide "sure-flow" gas testing by setting upper and lower control limits for the user
defined gas flow rates. An internal fault relay can be used to warn or interrupt the
welding process if an out-of-limits condition is detected.
1.3 Features
Some of the features contained in the unit are the capability to limit test, provide an
accumulated gas usage and peak flow rates as well as displaying on-going gas flow
rates. The unit also provides an analog output voltage representing measured gas
flow rates. The GFMalso has a Modbus® RS-485 serial port. The sensor can
communicate with third party controllers via the Modbus® protocol. The sensor
defines 16 coils and 10 Registers for use with the Modbus® serial port. See the serial
communications section for further descriptions of the feature. The GFMuses an
OLED graphic display panel to display the gas flow rates, to provide programming
menus and user defined optional parameter display.
1.4 Mechanical Specifications
Dimensions
2-13/16"W x 3-1/2"H x 2-13/16”L (71.4 mm W x 88.9 mm H x 71.4 mm L)
Weight
19 oz. (539 gm)
Pipe Fittings
3/8" NPT with 3/8" hose barb fittings recommended max torque 15 in. lbs.

2
1.5 Sensor Specifications
Measurement Range
5 - 255 CFH (2 - 120 LPM)
Display Resolution
±1 CFH (± 1 LPM)
Accuracy
±3 % of full-scale ±1 digit
Operating Pressure
50-PSI maximum (344 KPA)
Fault Relay Output
Opto-Isolated Solid State Relay (N.O. Contacts)
Relay Rating
48 vac @ 0.5 amps non-inductive
48 vdc @ 1.0 amps non-inductive
Analog Sensor Output
0 - 2.55 vdc @ 10 ma.
Analog Scaling
0.01 vdc = 1 CFH (0.01 V = 1 LPM)
Power Requirement
12 - 28 vdc @ 100 ma.
Operating Temperature
20° to 140° F (-7° to 60° C)
Battery Charger
120 vac 60 hz @ 300 ma (220 VAC 50 hz @ 300 ma)
Battery Life
Approximately 24 hours with full charge
(User configurable English / Metric units of measurement)
Note: Specifications subject to change without notification.
1.6 Models
The following models are covered in this document:
Part No.
Description
A0A0161
120/240 VAC Portable GFMSystem
A0A0162
120/240 VAC In-Line GFMSystem
A0A0163
ADM III™ GFM™ System
A0A0164
ADM IV™ GFM™ System
A0A0165
WDL II™ GFMSystem

3
2.0 INSTALLATION
2.1 Options
The GFMcan be used as a portable or in-line gas flow monitor. If the unit was
purchased as a portable monitor, it will be equipped with a rubber gas cone. When
installing the rubber hose and gas cone on the GFMmake sure the hose is
installed on the side of the GFMmarked gas inlet. The cone is designed to fit
standard torch gas cups and allows the GFMto measure the actual gas flow at the
torch. To install, simply press the GFMgas cone onto the welding torch gas cup.
Make sure that the cone is fitted snugly to the gas cup. The GFMuses a custom
MEM sensor that is calibrated to measure Air. The GFM
has 6 selectable gas
settings, ARGON, Argon/ CO2(90/10), Argon/ CO2(80/20), Argon/ CO2(75/25),
Helium, and CO2. The GFM
can be custom ordered and configured for
additional gas mixtures.By default the Argon gas type is enabled. To change the
gas type, refer to the Section 3: Operations.
2.2 Gas Line Hookup
The GFM may also be installed into the gas line and used to permanently monitor the
gas-flow rate. This model is supplied with barbed 3/8 ID hose fittings. The sensor will
accept any 3/8” NPT pipefitting. The user may hard plumb the sensor if desired. DO
NOT USE PIPE DOPE OR TEFLON TAPE ON THE PIPE FITTINGS. The sensor
should be located between the welding-gas solenoid and the torch. DO NOT
INSTALL THE SENSOR ON THE INLET SIDE OF THE GAS SOLENOID. If the
sensor is installed on the inlet pressure side of the gas solenoid, the maximum
operating pressure (50 psi) of the transducer may be exceeded.
WARNING: Do not over tighten fittings as it may damage the sensor. The maximum
recommended torque for fittings is 15 in. lbs or 1.7 newton meters
2.3 Cable Hookup
The GFM provides an analog voltage, which will represent gas flow. This analog
voltage can be monitored by using the Auxiliary cable and connecting the plug to the
"AUX" connector on the bottom panel. The output voltage will have the following
relationship:
2.55 volts = 255 scfh
or
0.01 volt/scfh

4
The output impedance of this signal is 100 ohms and can source 10 milliamps of
current. The analog-interface cable can also be used to supply power to the GFM.
The power requirement is (12 - 28) vdc @ 100 ma. This cable also has the
connections for the Fault Relay and Modbus® RS-485 serial port.
The following is the pin out for the GFMAUX Cable (P/N: A3W0352).
Pin No.
Function
1 (WHT)
Modbus RS-485 D+ serial port
2 (BRN)
User supplied Power Input VIN+ (12-28 VDC @100 ma)
3 (GRN)
CR-A -Will be active when gas flow is within programmed limits.
4 (YEL)
CR-B –Will be active when gas flow is within programmed limits.
5 (GRY)
User supply power common VCOM
6 (PNK)
Modbus RS485 and Vout analog common
7 (BLU)
Modbus RS-485 D- serial port
8 (RED)
Gas Flow Analog output VOUT+ (0.00 – 2.55 vdc)
2.4 Gas Flow Limits
The GFMcan be used to test for High/Low gas flow limits. An internal fault relay
will be set (CLOSED) when the gas flow is within the programmed limits. The fault
relay can be interfaced to an external weld fixture controller.
2.5 Gas Flow Volume
The GFMcan also be used to monitor accumulated gas flow and to provide an
indication when the volume in a gas cylinder has reached a programmed minimum
limit. The GFMwill calculate the volume of gas used based on the measure flow
rate. If the user programs the minimum volume for safe operation, the GFMwill
indicate when the estimate minimum volume has been reached. The GFMwill set
a fault relay when the estimated volume has decreased below the programmed
minimum. Setting the starting volume “V” to 0 disables the function.
NOTE: THE LOW GAS VOLUME FAULT WILL NOT ACTIVATE THE FAULT RELAY BUT
WILL INDICATE THE FAULT CONDITION BY SETTING A MODBUS® COIL
CR15.

5
3.0 OPERATION
3.1 Firmware Version
The GFMis supplied with a plug-in the wall transformer, which powers the GFM
and will also charge the optional internal battery. Plug the transformer into a suitable
ac receptacle, and connect the power cable into the "POWER" jack located on the
bottom panel of the GFM. Press the power switch on the front panel "ON".The
“POWER” LED will light and the following power up message will be displayed:
**** GFM ****
P/N A5Z0044 Ver #.##
Copyright (c) 2011
Computer Weld
Technology Inc.
All Rights Reserved
Where: #.# is the firmware version number
Followed by the run time display:
0 CFH
Note: CFH will be replaced with LPH in metric mode
Activate the gas solenoid for the welding torch. The GFMwill now display the gas
flow rate in CFH (Cubic Feet per Hour) or LPM (Liters per Minute).
3.2 Program Limits
To program the High/Low limits and test parameters press both “▼” and "▲" switch
simultaneously to enter the “Select Para INC/DEC”mode. The first programmable
parameter will appear on the display. To increment through the program menus
press the “▲” button. To decrement through the menus press the “▼” button. To
edit a menu option press both “▼” and "▲" switch simultaneously to enter the “Edit
Para INC/DEC” mode. To increment the parameter press the “▲” button. To
decrement the parameter press the “▼” button. To end the “Edit Para INC/DEC”
press both “▼” and "▲" switch simultaneously to exit and return to the normal display
mode. The user can edit only one parameter at a time. To edit other parameters
repeat the above sequence.

6
3.3 Parameters
The following is the list of the parameters and system configurations that can be
modified by the user:
•Max Limit= ###- Maximum gas flow Limits. This value is used to set the high
fault alarm and disable the output alarm. This value is also used to trigger the
Peak Flow detector. The Peak flow value is updated and the peak flow time is
incremented when the flow rate is greater then this limit. (Value range 5 – 255)
•MIN Limit= ### -Minimum gas flow rate limits. This limit in conjunction with
the test delay time is used to set the Low Fault alarm and to disable the output
alarm. When the flow is detected the Test delay timer is decremented and
when the user defined delay time is reached the Low limit is tested and the
output relay will be disabled if the flow rate is below this limit. (Value range 5 to
100)
•Test Delay= ##.# - This is the time in seconds that the GFM will wait before
testing for a Low or High limit fault following an initial detection of gas flow.
(Value range 0.5 to 10.0 seconds)
•Enable Alarms? - Allows the user to enable or disable the High Low limit
testing. Setting this option to “No” will disable the alarm relay output. Setting
this option to “Yes” will enable the alarm relay output. (Status Yes or No)
•Enable Peak? – Setting this parameter to yes will enable the Peak Flow
display. When enabled an additional “Peak= ### *.** sec” display will be
active. Where ### is the last peak flow rate measured and “*.**” is the Total
time at peak flow. The time at peak is the total time measured above the High
limit value. The Peak is the peak flow measured above the High Limit. The
peak value and time is reset at the start of the next detected gas flow period.
This peak display will remain on the display until the peak is set to “No”.
•Log Mode? – Setting this parameter to yes will enable the flow volume
accumulator and it will enable the “Tot Volume= ##.#”and the “Total Time=
HR:MN:SS” display. Where ##.# is the total accumulated volume and
HR:MN:SS is the total time of gas flow since the last user reset. When
disabled the volume display will be inactive and the gas flow accumulator will
be disabled.
•Metric Units? – This parameter is used to select the units of measure for the
gas flow rate. When set to “Yes” the units of measure is in Liters per Minute
(LPM). When set to no, the units of measure are standard Cubic Feet per Hour
(CFH).

7
•DEVICE ID= -This parameter sets the Modbus address ID number for the
GFM. This address is used to identify the Device when using the Modbus®
serial communications protocol. Each sensor connected to the Modbus®
network must have a unique ID number assigned. (Value Range 1 to 247)
•Clear Log Timer? – This Option is used to reset the accumulated gas flow
timer used when the log option is enabled. When set to “Yes” the timer will be
reset to 00:00:00.
•Reset Volume? – This option is used to reset the gas volume accumulator to
zero. The accumulator is used when the Log mode is set to yes. Setting this
option to “Yes” will clear the accumulated volume of gas to zero.
•Filter TC = ## -The parameter sets the filter time constant for the displayed
gas flow. Increasing this value will decrease the fluctuation in the gas flow
reading. This filter does not impact the peak readings or accumulated flow
parameters. (Value Range from 1 to 255).
•Argon Gas? - Allows the user to enable or disable Argon Gas conversion
factor. Setting this option to “No” will disable the Argon Gas conversion factor.
Setting this option to “Yes” will enable the Argon Gas conversion factor. (Status
Yes or No) Note: Disabling all Gas types (set to NO) will enable the Air
conversion factor.
•CO2Gas? - Allows the user to enable or disable CO2Gas conversion factor.
Setting this option to “No” will disable the CO2Gas conversion factor. Setting
this option to “Yes” will enable the CO2Gas conversion factor. (Status Yes or
No) Note: Disabling All Gas types (set to NO) will enable the Air conversion
factor.
•Helium Gas? - Allows the user to enable or disable Helium Gas conversion
factor. Setting this option to “No” will disable the Helium Gas conversion factor.
Setting this option to “Yes” will enable the Helium Gas conversion factor.
(Status Yes or No) Note: Disabling All Gas types (set to NO) will enable the
Air conversion factor.
•75/25 Argon/ CO2Gas? - Allows the user to enable or disable 75/25 Argon/
CO2Gas conversion factor. Setting this option to “No” will disable the 75/25
Argon/ CO2Gas conversion factor. Setting this option to “Yes” will enable the
75/25 Argon/ CO2Gas conversion factor. (Status Yes or No) Note: Disabling
All Gas types (set to NO) will enable the Air conversion factor.
•80/20 Argon/ CO2Gas? - Allows the user to enable or disable 80/20 Argon/
CO2Gas conversion factor. Setting this option to “No” will disable the 80/20
Argon/ CO2Gas conversion factor. Setting this option to “Yes” will enable the

8
80/20 Argon/ CO2Gas conversion factor. (Status Yes or No) Note: Disabling
All Gas types (set to NO) will enable the Air conversion factor.
•90/10 Argon/ CO2Gas? - Allows the user to enable or disable 90/10 Argon/
CO2Gas conversion factor. Setting this option to “No” will disable the 90/10
Argon/ CO2Gas conversion factor. Setting this option to “Yes” will enable the
90/10 Argon/ CO2Gas conversion factor. (Status Yes or No) Note: Disabling
All Gas types (set to NO) will enable the Air conversion factor.

9
4.0 SETTING GAS FLOW CONTROL LIMITS
4.1 Description
To use the GFM as a Sure-Flow gas switch, the user can set the “Max Limit” and
“Min Limit”.
The GFM will activate the internal fault relay as long as the gas flow remains above
the lower limit and below the upper limit. If the gas flow rate moves outside of the
control limits the fault relay will be deactivated. The "Test Delay"parameter is used
to delay the start of high limit testing. The value of this parameter will determine
when the GFM will begin testing for the upper control limit after the gas flow is
initiated. The lower limit is always being checked during the gas flow period. A high
gas flow fault will only occur after this time period has expired.
4.2 Setup
To program the High/Low limits and test parameters press both “▼” and "▲" switch
simultaneously to enter the “Select Para INC/DEC”mode. The first programmable
parameter will appear on the display. To increment through the program menus
press the “▲” button. To decrement through the menus press the “▼” button. To
edit a menu option press both “▼” and "▲" switch simultaneously to enter the “Edit
Para INC/DEC” mode. To increment the parameter press the “▲” button. To
decrement the parameter press the “▼” button. To end the “Edit Para INC/DEC”
press both “▼” and "▲" switch simultaneously to exit and return to the normal display
mode.

10
5.0 GAS FLOW SURGE “PEAK” MEASUREMENT
5.1 Description
The GFM has a peak value "sample and hold" feature. This allows the user to
measure the maximum gas flow rate, which occurred during the welding cycle. The
maximum value is the result of a gas surge, which occurs when the gas solenoid is
activated. The trigger used to determine the time at peak is the “Max Limit” value.
The time above this level is measured and displayed. Whenever the Flow rate
exceeds this value the time is accumulated. When the flow stops the GFM will
display the Peak flow and the accumulated time above the max limit. When the flow
starts again the values are cleared and new values are displayed.
5.2 Setup
To enable the Peak flow and set the High limits and test parameters press both “▼”
and "▲" switch simultaneously to enter the “Select Para INC/DEC”mode. The
first programmable parameter will appear on the display. To increment through the
program menus press the “▲” button. To decrement through the menus press the
“▼” button. Until the “Enable Peak?” option is displayed. To edit a menu option
press both “▼” and "▲" switch simultaneously to enter the “Edit Para INC/DEC”
mode. To toggle the option to “YES” press the “▲” button. To end the “Edit Para
INC/DEC” press both “▼” and "▲" switch simultaneously to exit and return to the
normal display mode. The “Peak= ### ##.# sec” window will be displayed and the
Peak function will be enabled.
This manual suits for next models
4
Table of contents
Popular Measuring Instrument manuals by other brands
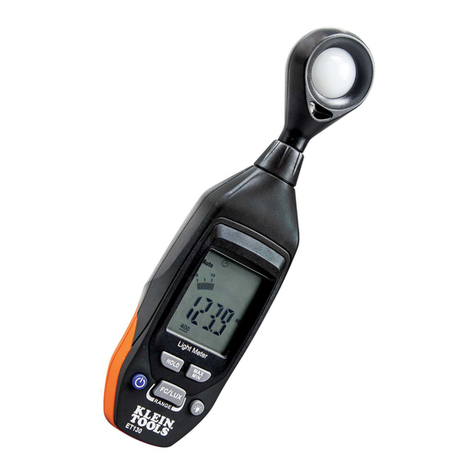
Klein Tools
Klein Tools ET130 instruction manual
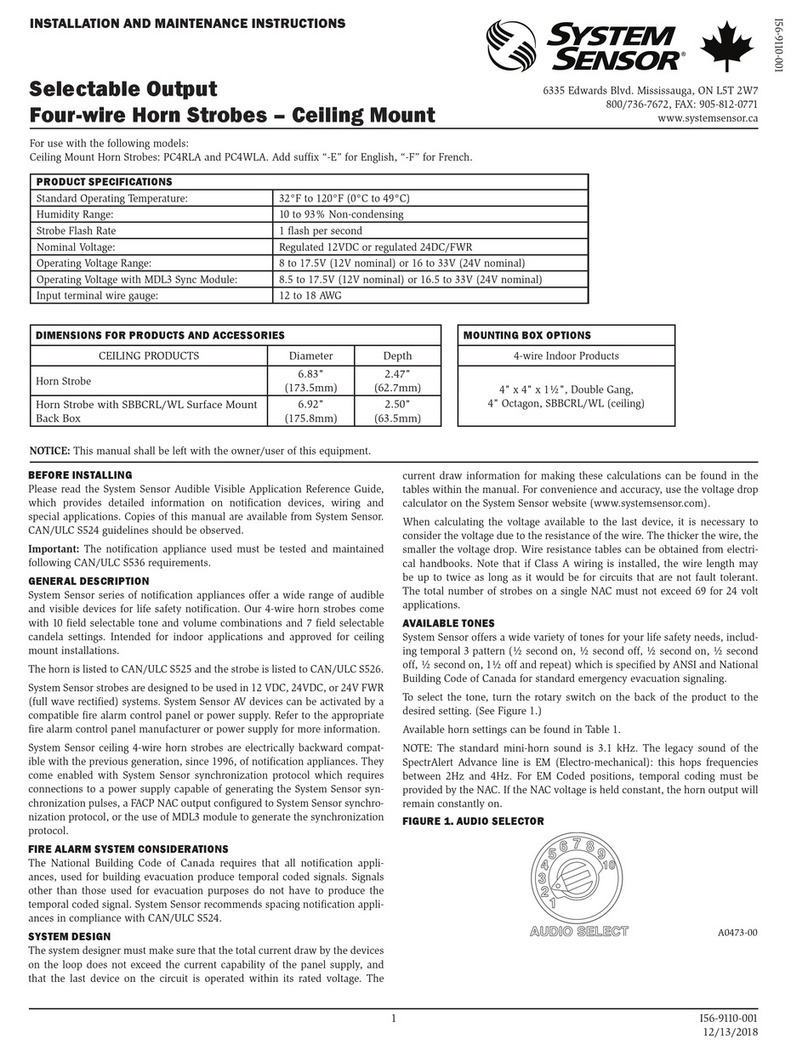
System Sensor
System Sensor PC4RLA Installation and maintenance instructions

Keithley
Keithley 6514 quick guide
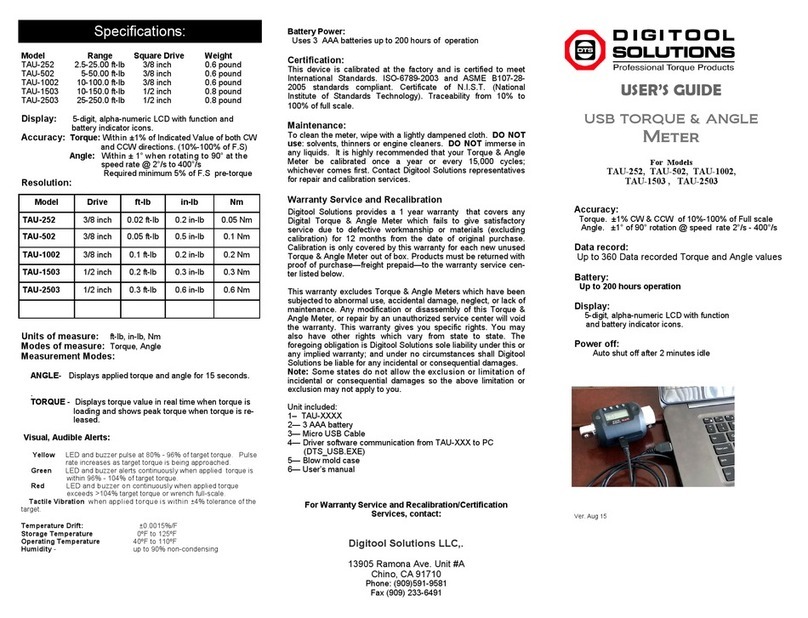
Digitool Solutions
Digitool Solutions TAU-252 user guide
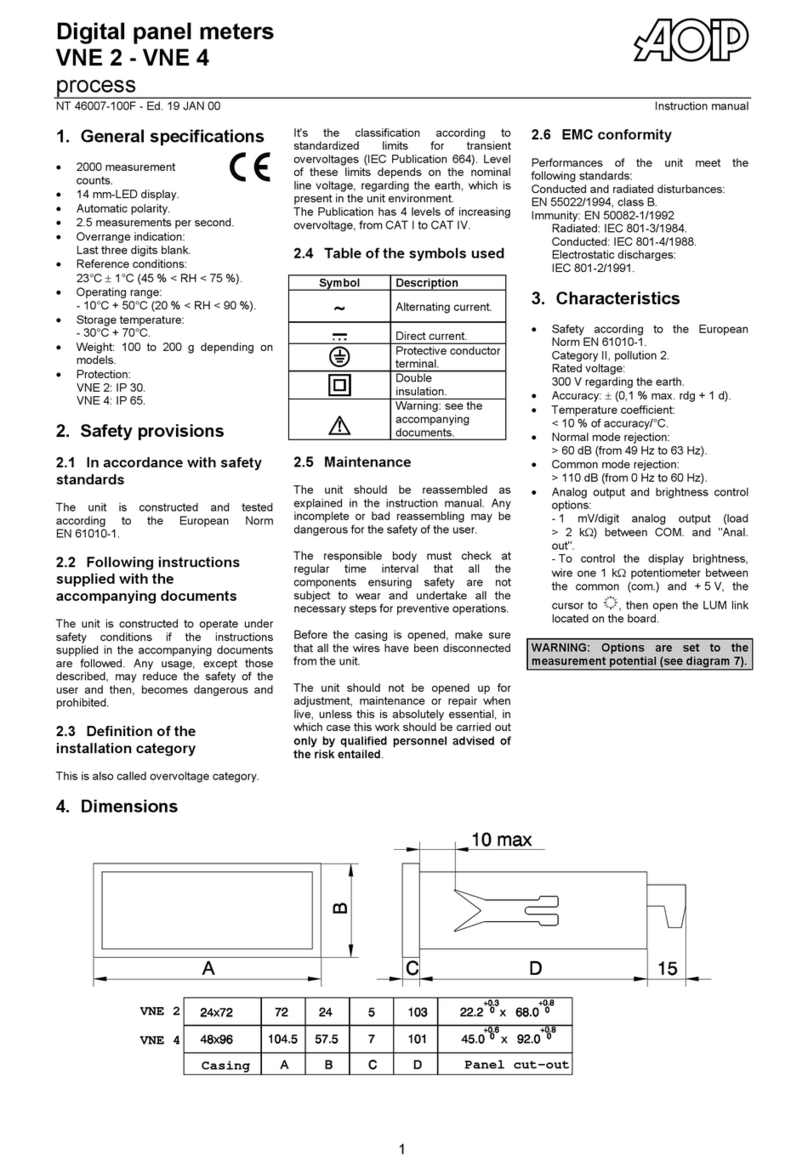
AOIP
AOIP VNE 2 quick start guide
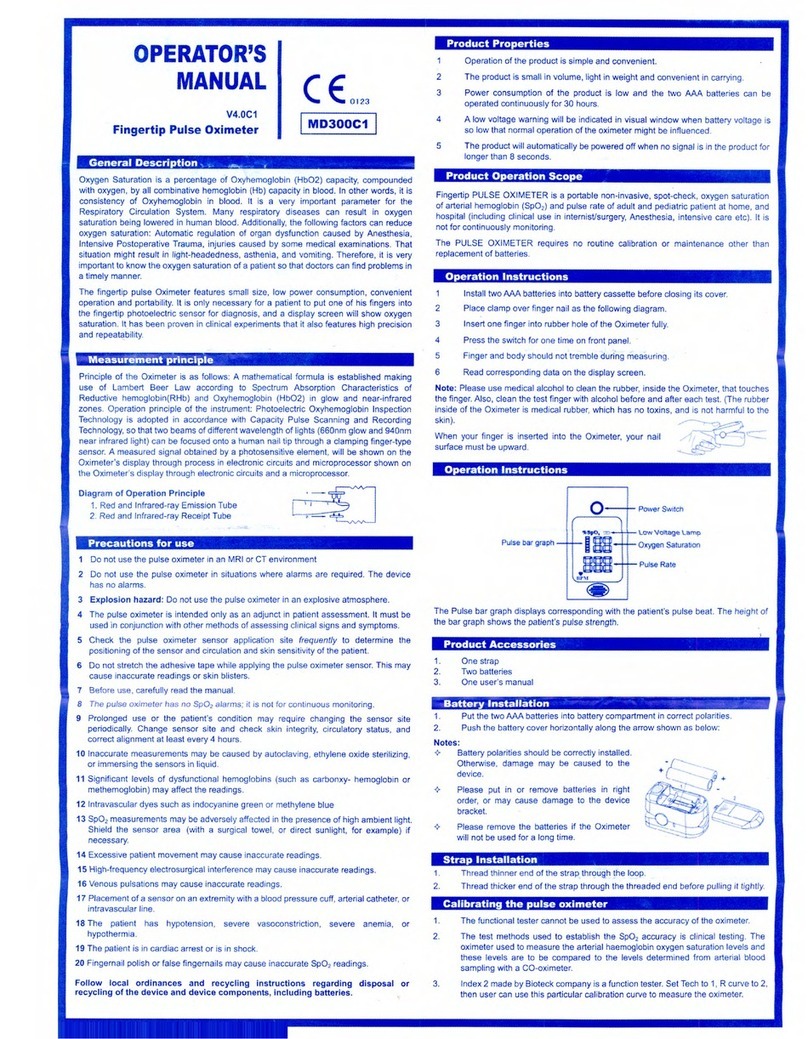
Beijing Choice Electronic Technology
Beijing Choice Electronic Technology Fingertip Pulse Oximeter Operator's manual