Cylinda 4VI515 Series User manual

SERVICE MANUAL
INDUCTION HOB
THIS SERVICE MANUAL IS INTENDED FOR SERVICE TECHNICIANS IS-EN-0097/6
(10.2018)
*4VI515* / *4VI517* / *set 10132.3* / set 10142.3*

- 2 -
CONTENTS
1. HOB FEATURES AND COMPONENTS 3
2 . CHARACTERISTICS OF HOB 4
3. ERROR CODES 5
3.1. ERROR E7 5
3.2. ERROR E6 6
3.3. ERROR E4 7
3.4. ERROR E 8
3.5. ERROR EE 9
3.6. ERROR E5 9
3.7. DAMAGED FAN 9
4. CHECK THE CONNECTION 10
4.1. CONNECT THE POWER SUPPLY 10
4.2. MEASURE THE L1 PHASE SUPPLY VOLTAGE 10
4.3. MEASURE THE L3 PHASE SUPPLY VOLTAGE 11
5. CHECK FOR WHICH COOKING ZONES THE E7 MESSAGE IS SHOWN 11
5.1. PROCEDURE 11
6. CHECK THE COIL TYPE 12
7. TEST THE INSULATED-GATE BIPOLAR TRANSISTOR (IGBT) 14
8. CHECK THE CORRECT OPERATION OF THE HOB 15
8.1. CHECK THE CORRECT OPERATION OF THE CONTROL PANEL 15
8.2. CHECK THE CORRECT ASSIGNMENT OF THE COOKING ZONE 16
9. CONNECTION FILTER PCB WITH THE MODULE 17
9.1. CHECK IF NEUTRAL CONDUCTOR FOR L2 PHASE IS CONNECTED CORRECTLY 17
9.2. CHECK IF NEUTRAL CONDUCTOR FOR L1 PHASE IS CONNECTED CORRECTLY 18
9.3. CHECK IF L1 PHASE IS CONNECTED CORRECTLY 19
9.4. CHECK IF L2 PHASE IS CONNECTED CORRECTLY 20
9.5. CHECK IF COILS ARE CONNECTED CORRECTLY 21
9.6. CHECK THE VARISTORS 22
10. CONTROL PANEL - MODULE COMMUNICATION HARNESS 23
11. SWAP THE COILS 25
12. POTS 26

- 3 -
1. HOB FEATURES AND
COMPONENTS

- 4 -
1.1 Induction module PCB
1.2 Insulated-gate bipolar transistor T1
1.3 Insulated-gate bipolar transistor T2
1.4 Insulated-gate bipolar transistor T3
1.5 Insulated-gate bipolar transistor T4
1.6 Control panel module communication harness connector
1.7 Filter PCB
1.8 Varistors
1.9 Fan
1.10 FL (front left) cooking zone coil
1.11 FL cooking zone temperature sensor
1.12 RL (rear left) cooking zone coil
1.13 RL cooking zone temperature sensor
1.14 RR (rear right) cooking zone coil
1.15 RR cooking zone temperature sensor
1.16 FR (front right) cooking zone coil
1.17 FR cooking zone temperature sensor
1.18 Control Panel
2 . CHARACTERISTICS OF
HOB
• induction hob with GECO module
• two heating zones 210mm / 3,0kW
• two heating zones 160mm / 1,4kW
• sensor control panel / GECO

- 5 -
3. ERROR CODES
3.1. Error E7
Incorrect power connection
Incorrect supply voltage: ……V
Wrong coil for the cooking zone: FL RL RR FR
NO YES Cooking zone coil connected incorrectly: FL RL RR FR
Cooking zone sensor connected incorrectly: FL RL RR FR
Damaged IGBT: 1 2 3 4
Damaged varistor
No connection of filter PCB with the module
Replaced induction coil
Replaced induction module
NO YES
NO YES
NO
YES
YES
NO
YES
NO
NO
YES
YES
NO
NO YES
Are correct coils used?
Check whether the E7 error is indicated when
left or right cooking zones are activated (note
the result). Point 5.2.
Check the connection and the voltage on L1 and L2 power
conductors. Point 5.1.
Technician should note all defects found in the following
list:
Are the connections and
voltage correct?
Inform the client of an incorrect
cooking zone connection or
overvoltage — note the
recommendations according to
the service procedure Check if the correct type induction coils are
used. Point 7
Is the E7 error
indicated when you
turn on the same
cooking zones?
Replace the induction module while paying
special attention to the correct connection of
induction coils and temperature sensors
Replace with correct coils.
Check the connection of cooking zone
induction coils and temperature sensors.
Point 10.5.
Is the connection
correct?
Check if the four IGBTs are operational. Point
8
Check if varistors are operational Point 10.6.
Are IGBTs
operational?
Replace the induction module while paying
special attention to the correct connection of
induction coils and temperature sensors
Check the connection between filter PCB and
induction module PCB. Point 10.1.
Swap the induction coils. Point 12
Check if the E7 error is
indicated.
Check if the E7 error is indicated. Point 5.2.
Check the correct operation of the hob Point
9.2.
Replace the induction coils on the side which
indicates the E7 error
Damage to the varistor is due to
the miswiring of power
conductors or electrical network
overvoltage. - Add the
recommendations consistent with
the service procedure
Check the correct operation of the hob Point
9.2.
Is the connection
correct?
Assemble the hob paying special attention to
the correct connection of induction coils and
temperature sensors
Replace the induction module while paying
special attention to the correct connection of
induction coils and temperature sensors
Check whether the E7 error is indicated when
left or right cooking zones are activated.
Point 6.1.
Are varistors
operational?
Check the correct operation of
the hob Point 9.2.
Check the correct operation of the hob Point
9.2.
Check the correct operation of the hob Point
9.2.
Does the hob operate
correctly?
Replace the induction module while paying
special attention to the correct connection of
induction coils and temperature sensors
End of repair
Compare whether the E7 error is indicated
when you turn on the same cooking zones
(left or right) as before the coils are swapped.

- 6 -
3.2. Error E6
Incorrect power connection
Incorrect supply voltage: ……V
Wrong coil for the cooking zone: FL RL RR FR
Cooking zone coil connected incorrectly: FL RL RR FR
NO YES Cooking zone sensor connected incorrectly: FL RL RR FR
Damaged IGBT: 1 2 3 4
Damaged varistor
No connection of filter PCB with the module
Replaced induction module
NO
YES
NO
YES
NO
YES
YES NO
YES NO
NO YES
Check the connection and the voltage on L1 and L2 power
conductors. Point 3.1.
Technician should note all defects found in the
following list:
Are the connections and
voltage correct?
Check varistors. Point 10.6.
Are varistors
operational?
Damage to the varistor is due to
the miswiring of power
conductors or electrical network
overvoltage. - Add the
recommendations consistent
with the service procedure
Check if the four IGBTs are operational. Point
8.
Are IGBTs
operational?
Replace the induction module while paying
special attention to the correct connection of
induction coils and temperature sensors
Inform the client of an incorrect
cooking zone connection or
overvoltage — note the
recommendations according to
the service procedure
Is the connection
correct?
Check the connection between filter PCB and
induction module PCB. Point 10.
Is the connection
correct?
Check if the correct type induction coils are
used. Point 7.
Are correct coils used?
Replace with correct coils.
Check the connection of cooking zone
induction coils and temperature sensors.
Point 10.5.
Replace the module while paying special
attention to the correct connection of
induction coils and temperature sensors
End of repair
Check the correct operation of the hob Point
9.2.
Check the correct operation of the hob Point
9.2.
Check the correct operation of the hob Point
9.2.
Replace the induction module while paying
special attention to the correct connection of
induction coils and temperature sensors
Assemble the hob paying special attention to
the correct connection of induction coils and
temperature sensors
Does the hob operate
correctly?

- 7 -
3.3. Error E4
The control panel - module harness installed incorrectly
Faulty control panel - module harness
Replaces control panel
Replaced induction module
NO YES
NO
YES NO YES
YES NO
Check the correct operation of the hob Point
9.2.
Check if the control panel - module harness is installed correctly:
1. Are plugs correctly inserted into sockets?
2. Is the harness routed according to specification?
Point 11
Check the correct operation of the hob Point
9.2.
Replace the control panel.
Does the hob operate
correctly?
End of repair
Check the correct operation of the hob Point
9.2.
Check the correct operation of the hob Point
9.2.
Does the hob operate
correctly?
Does the hob operate
correctly?
End of repair
Replace the induction module while paying
special attention to the correct connection of
induction coils and temperature sensors
End of repair
Technician should note all defects found in the
following list:
Is the harness
installed correctly?
Check if there is an aluminium sticker "Amica Service Centre" — if so,
carefully peel it off!
Install the control panel - module harness
according to specification. Point 11
Replace the control panel - module harness.
Make sure the installation is consistent with
the specification.

- 8 -
3.4. Error E
Cooking zone coil connected incorrectly: FL RL RR FR
Cooking zone sensor connected incorrectly: FL RL RR FR
Faulty cooking zone temperature sensor: FL RL RR FR
Replaced induction module
NO YES
NO
YES NO YES
Check the correct operation of the hob Point
9.2.
Does the hob operate
correctly?
Technician should note all defects found in the
following list:
Connect induction coils and temperature
sensors correctly. Point 10.7.
Check the correct operation of the hob Point
9.2.
Replace the induction module while paying
special attention to the correct connection
of induction coils and temperature sensors
Check the connection of cooking zone induction coils and
temperature sensors. Point 10.7.
Is the connection correct?
Replace the temperature sensor for the
cooking zone, which indicates "E” symbol
End of repair
Before the repair, make sure that the hob has cooled down. The "E"
message when the hob is hot is not a fault but only information
about the overheated cooking zone!
Does the hob operate
correctly?
End of repair
Check the correct operation of the hob Point
9.2.

- 9 -
3.5. Error EE
1. If error displays intermittently, one-time – disruption in temperature
sensor circuit.
Repair: Unplug and plug in.
2. If error displays after 2-4 minutes of switching on cooking zone -
possible damage of sensor or faulty connection.
Repair: Check and verify cooking zones temperature sensors con-
nections (as shown in diagram), if it’s done correctly, replace the
sensor of cooking zone where error displayed.
3.6. Error E5
1. Communication error between control panel and hab module
HG361.01 - 8065761
Solution:
Check the connection. If errror still exist, replace the hab module
8065761
3.7. Damaged fan
Symptoms:Autoswitchingothehobafterfewsecondsofwork.
Earlier all symbol will light.
Solution: Replace the fan- 1038010

- 10 -
4. CHECK THE CONNECTION
4.1. Connect the power supply
1N 2N
4.2. Measure the L1 phase supply voltage
Perform the measurement using a multimeter, applying multimeter
probes to terminals L1 and N.
In accordance with the current regulations the supply voltagemust be
inthespeciedrange,dependingonthecountry:
Country Tolerance Minimum voltage [V] Maximum voltage [V]
PL 230V (-15/+10%) 195 253
DE / CS / SK / ES /
LT / RO / BG / MD /
UA / RU
230V (-10/+10%) 207 253
RU 230V (-10/+10%)*
220V (-10/+10%)*
207
198
253
242
UK / IE 230V (-6/+10%) 216,2 253
DK / NO / FI / SE 230V (-10/+10V) 220 240
AM 220V (-10/+10V) 210 230
KK / GE / 230V (-10 /+10V) 210 230
AZ 220V (-10/+10%) 198 242
*According to the region
Jumper bar

- 11 -
Voltage lower or higher than listed in the table may cause damage
to the electronic components. In order to protect against damage,
detection of incorrect voltage will result in disabling of the cooking
zones and displaying an error message E6 “low voltage” or E7 “high
voltage.”
4.3. Measure the L3 phase supply voltage
Perform the measurement using a multimeter by applying multimeter
probes to terminals L2 and N.
5. CHECK FOR WHICH
COOKING ZONES THE E7
MESSAGE IS SHOWN
5.1. Procedure
• Turn on the hob with the ON/OFF sensor
• TurnothehobwiththeON/OFFsensor
• Wait at least 60 seconds
• Turn on the hob with the ON/OFF sensor
• Put a pan of water on the left front FL cooking zone
• Set FL cooking zone heat setting to 9
• Wait 20 seconds for the E7 error to be displayed
• If the error message is shown — note that the error occurs when
using the FL cooking zone

- 12 -
Repeat the procedure for all the cooking zones in sequence — note the
results in the table.
E7 error table
Left cooking zones Right cooking zones
FL – front left
210mm
RL – rear left
160mm
RR – rear right
210mm
FR – front right
160mm
6. CHECK THE COIL TYPE
210 mm induction coils (large cooking zones) with a suitable number of
turns are used in the P**4VI515FTB4P3 induction hob. Adjacent coils
withadieringnumberofturnsareusedininductionhobsofdierent
specication.Ifyouinstallacoilwiththewrongnumberofturnsinthe
hob, this will lead to malfunction or damage to the induction module.
Induction coil

- 13 -
2 single coils 6 dual coils 5 single coils

- 14 -
7. TEST THE INSULATED-GATE
BIPOLAR TRANSISTOR (IGBT)
In order to test the IGBT, set the multimeter to circuit continuity func-
tion (a beep is heard when the circuit is continuous) and then check
whether there is an electrical connection between the IGBT terminals.
Repeat the same procedure for all four IGBTs.
If there is an electrical connection (the meter beeps) between any IGBT
terminals, the IGBT is faulty.

- 15 -
8. CHECK THE CORRECT
OPERATION OF THE HOB
8.1. Check the correct operation of the control panel
Check if each of the touch sensors responds to touching and if it acti-
vates the desired function.
• TheON/OFFsensor–turnsthehobon/o
• Child lock sensor – touch and hold for 3 s to lock/unlock the control
panel
• FL cooking zone selection sensor – selects the FL cooking zones to
allow setting the heat setting
• RL cooking zone selection sensor – selects the RL cooking zones to
allow setting the heat setting
• RR cooking zone selection sensor – selects the RR cooking zones to
allow setting the heat setting
• FR cooking zone selection sensor – selects the FR cooking zones to
allow setting the heat setting
• Higher setting sensor – allows you to increase the power and timer
settings
• Lower setting sensor – allows you to decrease the power and timer
settings
• Timer sensor – activates the timer
• When touching a sensors a beep is sounded.
• Check if the displays correctly show the heat and timer settings.

- 16 -
8.2. Check the correct assignment of the cooking zone
Check the correct assignment of the cooking zone to control panel
touch sensor and temperature sensor of induction coils.
Set the maximum power (P-booster) of the front left (FL) induction
cooking zone and then place a pot of water on it. Check whether the
pot was detected and the water begins to heat up. Wait for the water to
boil.Turnothecookingzone,the"H"or"h”symbolshouldbedis-
played. If the symbol does not appear, place the pot with water on the
cooking zone and activate it again.
Repeat the procedure for each cooking zone individually. Pay particular
attentionifthe"H"or"h"symbolcomesonforthecookingzonewhere
water was boiled. The symbol displayed for the wrong cooking zone
indicates incorrect connection of the sensor, which may leading to unit
damage.
11 432
5 876 9
1 — FL cooking zone selection sensor
2 — lower setting sensor
3 — higher setting sensor
4 — FR cooking zone selection sensor
5 — Child lock sensor
6 — RL cooking zone selection sensor
7 — Timer sensor
8 — RR cooking zone selection sensor
9 — ON/OFF sensor

- 17 -
9. CONNECTION FILTER PCB
WITH THE MODULE
In order to test the connections, set the multimeter to circuit continu-
ity function (a beep is heard when the circuit is continuous) and then
check whether there is an electrical connection between the individual
terminalsoflterPCBandinductionmodule.
9.1. Check if neutral conductor for L2 phase is connected
correctly

- 18 -
9.2. Check if neutral conductor for L1 phase is connected
correctly

- 19 -
9.3. Check if L1 phase is connected correctly

- 20 -
9.4. Check if L2 phase is connected correctly
This manual suits for next models
1
Table of contents
Other Cylinda Hob manuals
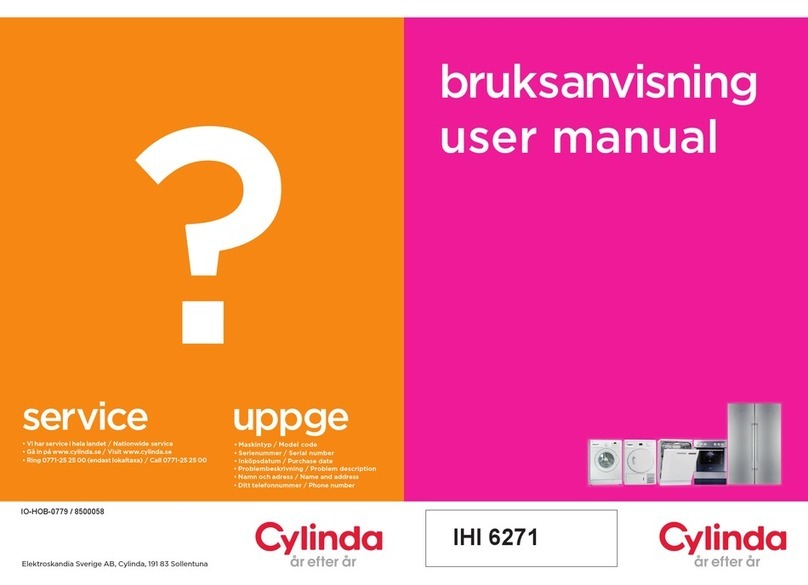
Cylinda
Cylinda IHI 6271 User manual
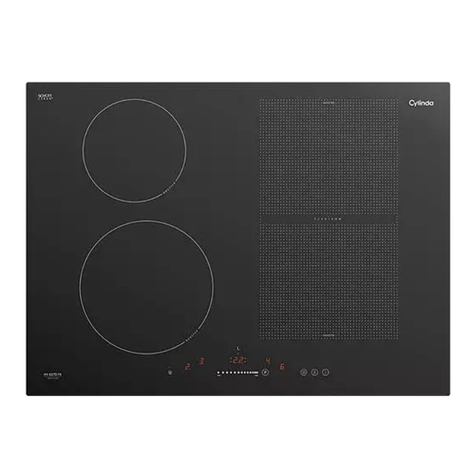
Cylinda
Cylinda IHI 6170 FX User manual

Cylinda
Cylinda IHI7260 User manual
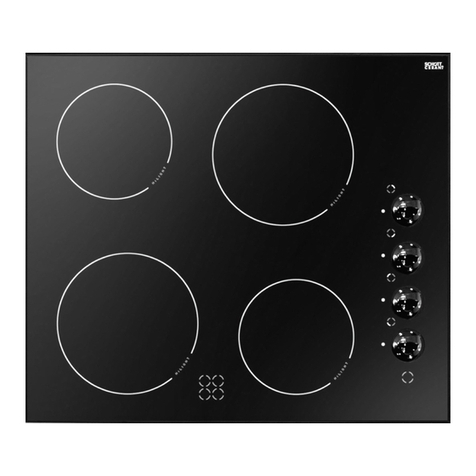
Cylinda
Cylinda IH 660-A User manual

Cylinda
Cylinda IHI7160RF User manual
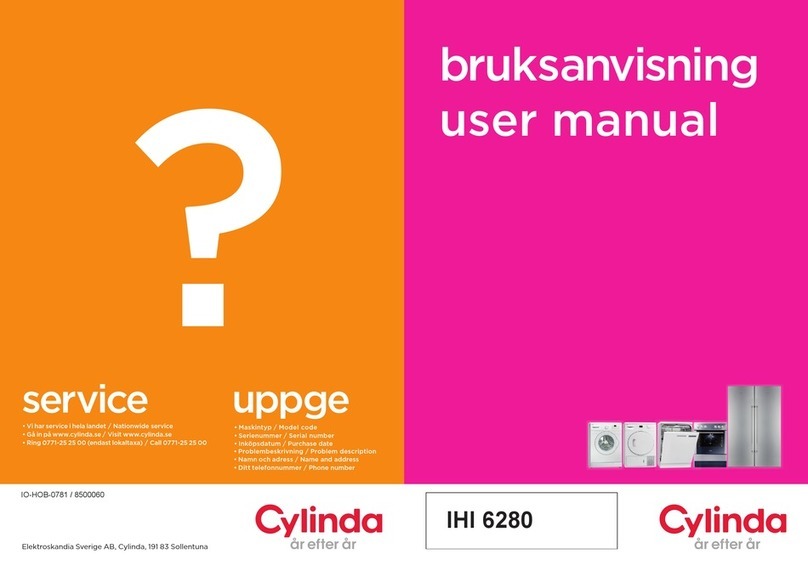
Cylinda
Cylinda IHI 6280 User manual
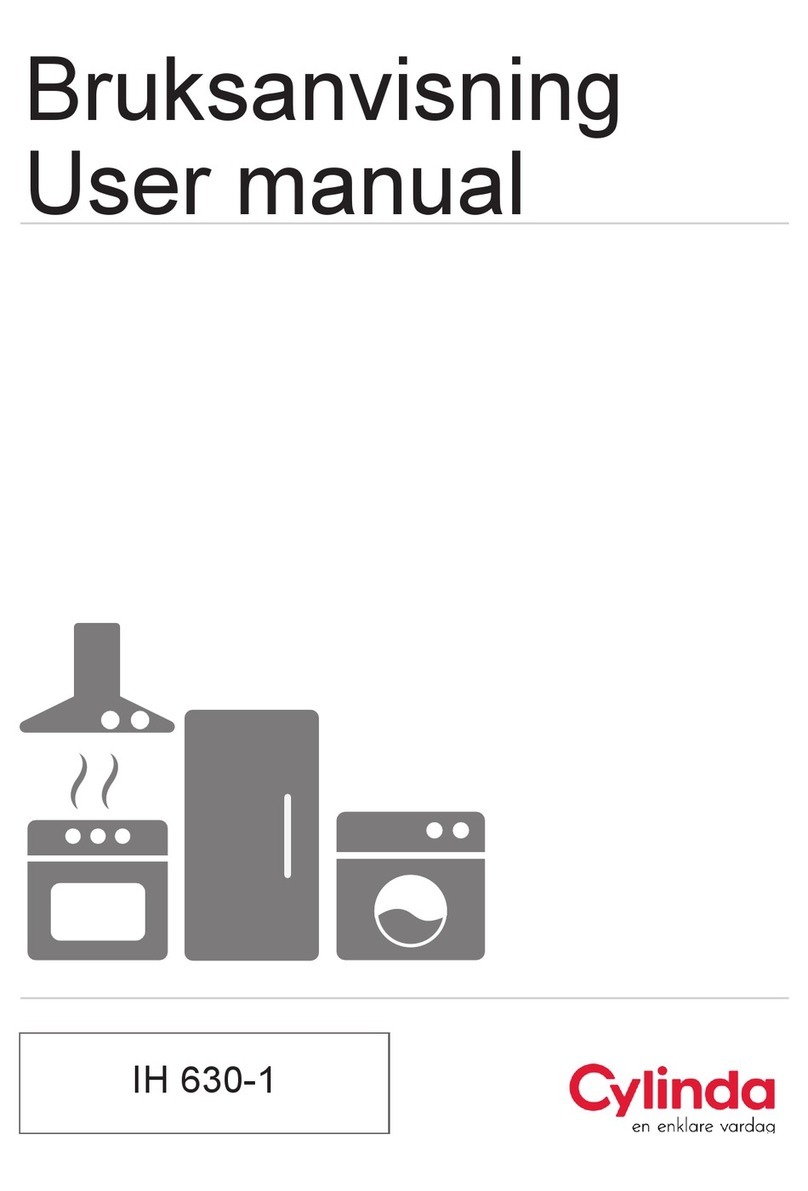
Cylinda
Cylinda IH 630-1 User manual

Cylinda
Cylinda IH 10.30 User manual

Cylinda
Cylinda IHI 6272 User manual
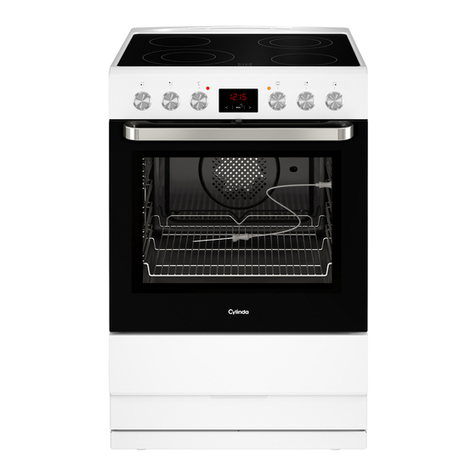
Cylinda
Cylinda S 6264 KVEP User manual