DAYLIGHT SOLUTIONS MIRcat-QT 2 Series User manual

D11-00028-02_A Page 1 of 54
MIRcat™
Ultra-Broadly Tunable
Mid-IR Laser
User Manual
©2017 DRS-Daylight Solutions, Inc. All Rights Rese ved.
D11-00028-02 Rev. A
1 5 3 7 8 A V E N U E O F S C I E N C E , S U I T E 2 0 0 , S A N D I E G O , C A 9 2 1 2 8
P H O N E : 8 5 8 . 3 2 . 7 5 0 0 F A X : 8 5 8 . 3 2 . 5 7 3 7
Models: MIRcat-QT-2xxxx
&
MIRcat-1xxxx

TABLE OF ONTENTS
D11-00028-02_A Page 2 of 54
I.
INTRODU TION & USER SAFETY .............................................................................................................................................. 4
1. LASER SAFETY WARNINGS ........................................................................................................................................................................................ 4
2. SAFETY WARNING LABELS ......................................................................................................................................................................................... 5
3. LASER EMISSION WARNING INDICATORS ................................................................................................................................................................ 7
4. EYE PROTECTION ......................................................................................................................................................................................................... 7
5. OPERATING CONDITIONS ............................................................................................................................................................................................ 8
5.1 Power Requirements ...................................................................................................................................................................................... 8
5.2 Cooling Requirements for CW or High-Duty-Cycle Pulsed peration ........................................................................................ 8
5.3 Cooling Lines – Preventive Maintenance ............................................................................................................................................... 9
5.4 Laser Safety Preventive Maintenance – Maintaining Regulatory Compliance. ...................................................................... 9
II. SYSTEM OVERVIEW .......................................................................................................................................................................... 10
2. SYSTEM FEATURES ................................................................................................................................................................................................... 10
3. MIRCAT LASER HEAD - PRECAUTIONS ................................................................................................................................................................ 13
4. COMPUTER CONTROL .............................................................................................................................................................................................. 14
5. POWER SUPPLY ........................................................................................................................................................................................................ 15
III. GETTING STARTED .......................................................................................................................................................................... 16
1. PACKING LIST ........................................................................................................................................................................................................... 16
2. SETTING UP ............................................................................................................................................................................................................... 17
IV. OPERATION ........................................................................................................................................................................................ 19
1. BACK PANEL INTERFACE ........................................................................................................................................................................................ 19
2. TRIGGERING AND ACQUISITION SIGNALS ON DB-9 CONNECTOR ..................................................................................................................... 20
PIN
SIGNAL DESCRIPTION .................................................................................................................................................................................. 20
PIN
SIGNAL DESCRIPTION (CONT.) ........................................................................................................................................................................ 21
3. USING THE SYSTEM INTERLOCK ............................................................................................................................................................................. 23
4. USING THE OPTIONAL VISIBLE AIMING BEAM ..................................................................................................................................................... 23
5. POWER THE SYSTEM ON/OFF ................................................................................................................................................................................ 23
6. TURN THE LASER OUTPUT ON/OFF ..................................................................................................................................................................... 24
7. GUI MENU FUNCTIONS ........................................................................................................................................................................................... 26
Menu Template ...................................................................................................................................................................................................... 27
Tune Menu ............................................................................................................................................................................................................... 27
P efe ed Tuning ......................................................................................................................................................................................................................... 31
Scan Menu ............................................................................................................................................................................................................... 32
Scan Settings: ................................................................................................................................................................................................................................ 32
Sweep Mode: ................................................................................................................................................................................................................................. 33
Settings Menu ......................................................................................................................................................................................................... 40
Favorites Menu ...................................................................................................................................................................................................... 43
Contact Us Menu ................................................................................................................................................................................................... 44

TABLE OF ONTENTS
D11-00028-02-A Page 3 of 54
About Menu ............................................................................................................................................................................................................. 45
8. WIDTH, FREQUENCY AND DUTY CYCLE ................................................................................................................................................................ 47
9. MODULATION FUNCTIONS (CW) .......................................................................................................................................................................... 48
V. OMPUTER ONTROL ..................................................................................................................................................................... 49
1. INTERFACES .............................................................................................................................................................................................................. 49
VI. SERVI E AND SUPPORT ................................................................................................................................................................. 50
1. WARRANTY ............................................................................................................................................................................................................... 50
2. SERVICE AND CALIBRATION ................................................................................................................................................................................... 50
Pe iodic Safety Checks Requi ed to Maintain CDRH Compliance ....................................................................................................................... 50
VII. SPE IFI ATIONS: MIR AT LASER SYSTEMS .......................................................................................................................... 52
APPENDIX A: DIMENSIONS .................................................................................................................................................................. 53
1.
MIR AT LASER HEAD (-QT & -1XXX MODELS) .................................................................................................................. 53
2. POWER MODULE ...................................................................................................................................................................................................... 54

MIRcat OPERATION
•
D11-00028-02-A Page 4 of 54
I. INTRODU TION & USER SAFETY
The safe and effective use of ou p oducts is of the utmost impo tance to Daylight Solutions. This manual
desc ibes the safe installation, use, and maintenance of the ‘MIRcat™ family of widely tunable mid-IR lase
systems. This p oduct family includes MIRcat-QT-2xxx (tuning slew ates to >5,000 cm
-1
/s) and MIRcat-
1xxx (slew ates up to 100 cm
-1
/s) systems. All info mation in this manual applies inte changeably to
MIRcat-QT and MIRcat-1xxx p oduct models unless stated othe wise. Please ead this manual, including
Lase Safety Wa nings section, befo e attempting to ope ate the lase . A basic knowledge of lase safety is
assumed. Consult the elevant po tions of Lase Institute of Ame ica’s (LIA) document 21 CFR Pa t 1040
Section 1040.10 fo Class IIIB lase s (o Class IV lase s, if you system p ovides Class IV output).
This symbol is intended to ale t the use of this equipment to the p esence of exposu e to
haza dous invisible o , depending on options selected at time of o de *, visible lase adiation.
This symbol is intended to ale t the use to the p esence of dange ous voltages associated with
the p oduct that may be of sufficient magnitude to constitute a isk of elect ical shock.
This symbol is intended to ale t the use of this equipment of the potential inju y haza ds. Obey
all safety messages that follow this symbol to avoid possible inju y o death.
AUTION: Caution used with the safety ale t symbol indicates a potentially haza dous situation
which, if not avoided, may esult in p ope ty damage.
WARNING: Wa ning indicates a potentially haza dous situation which, if not avoided, may esult
in mino o mode ate inju y.
DANGER: Dange indicates an imminent haza dous situation which, if not avoided, will esult in
death o se ious inju y.
NOTE: To shut-off powe to the unit completely, disconnect AC powe .
1. Laser Safety Warnings
AUTION: UNDER NO CIRCUMSTANCES SHALL THE USER ATTEMPT TO OPEN THE LASER
HEAD. Opening the lase head will void the wa anty, and may esult in and/o i epa able
damage to inte nal components. The lase head is also pu ged with a d y ine t gas befo e sealing
to minimize moistu e. B eaking this seal will also void the wa anty.
AUTION: The lase adiation emitted f om MIRcat lase systems is invisible to the naked eye
and may be ha mful if the beam makes di ect and p olonged contact with the eye. In some units,
depending on options selected at time of o de *, the lase may also emit visible lase adiation. In
all cases, avoid di ect exposu e to the beam o looking di ectly towa ds the lase beam. These
lase s emit light in the wavelength ange f om 3µm to 14 µm, depending on the wavelength
ange options selected at the time of o de . If the visible aiming beam option was selected at time
of o de , these lase s will also emit in the ange ~0.6 to 0.7 µm. The specific ange of each lase is
listed on the safety label affixed to each MIRcat. An example of the safety labels is shown below.
*Fo mo e info mation, please contact Daylight Solutions o you autho ized dist ibuto .

MIRcat OPERATION
•
D11-00028-02-A Page 5 of 54
2. Safety Warning Labels
1a
2a
1b
2b
1c
2c
1d
2d
Figure 1. MIRcat safety warning labels. (1) Aperture warning label: (1a) invisible output only; (1b) invisible &
visible output; (1c) invisible output only, French text; (1d) invisible and visible output, French text.
(2) ombination warning/certification/identification label stating emitted wavelengths and
maximum emitted average power: (2a) invisible output only, (2b) invisible & visible output;
(2c) invisible output only, French text; (2d) invisible and visible output, French text.

MIRcat OPERATION
•
D11-00028-02-A Page 6 of 54
DANGER – non-inte locked housing label. Wa ns of invisible lase
adiation when housing is open. AVOID DIRECT EXPOSURE TO
BEAM(S). NOTE: MIRcat housing must neve be opened by use s.
Wa anty is void if housing is opened by use .
DANGER – non-inte locked housing label. Wa ns of invisible and
visible lase adiation when housing is open. AVOID DIRECT
EXPOSURE TO BEAM(S). NOTE: MIRcat housing must neve be
opened by use s. Wa anty is void if housing is opened by use .
DANGER: The lase adiation emitted f om this unit is invisible to
the naked eye and may be ha mful if the beam makes di ect and
p olonged contact with the eye. Avoid di ect exposu e to the beam
o looking di ectly towa ds the lase beam.
DANGER: The lase adiation emitted f om this unit is visible and
invisible to the naked eye and may be ha mful if the beam makes
di ect and p olonged contact with the eye. Avoid di ect exposu e
to the beam o looking di ectly towa ds the lase beam.
Figure 2. Radiation control diagram - position and type of laser safety warning labels used on
MIRcat-QT / MIRcat laser heads.
Lase emission ape tu e
wa ning label
Combination
lase
wa ning/
ce tification/identification label,
stating emitted wavelengths &
maximum ave age powe
Non-inte locked
housing label

MIRcat OPERATION
•
D11-00028-02-A Page 7 of 54
3. Laser Emission Warning Indicators
Figure 3. Position of laser emission warning indicator (white LED)
on MIRcat laser heads.
AUTION: Lase emission may be p esent wheneve the lase emission wa ning indicato light is
on (white LED is lit). This includes cases whe e the lase may be ope ating in ‘Exte nal Pulse’
mode, but the use has disconnected the ‘Exte nal Pulse’ t igge signal f om the lase . Always
obse ve all lase safety p ecautions and p ocedu es and assume lase emission is p esent
wheneve the emission wa ning indicato is lit.
A white-light LED emission wa ning indicato on MIRcat lase heads flashes fo 3-5 seconds wheneve the
lase is fi st A med and eadied fo lase emission. The lase is A med and eady fo mid-inf a ed lase
emission when the white light on the top of the unit is lit, and the button on the ight side of the Cont ol
Panel GUI next to “Disa m Lase ” o “Stop Scan” has a g een light. Fo those units fitted with an optional
visible lase aiming beam, the white-light emission wa ning indicato tu ns on immediately, as soon as the
v beam is activated via the GUI. (Unlike the mid-inf a ed output, the e is no 3-5s wa ning delay befo e the
visible aiming beam output is activated). The e is also an optional acoustic beeping sound that can be
selected to wa n use s of mid-inf a ed lase emission.
4. Eye Protection
The lase adiation emitted f om this unit is invisible to the naked eye and may be ha mful if the beam
makes di ect and p olonged contact with the eye. In some units, depending on options selected at time of
o de , the lase may also emit visible lase adiation. The use must eview this safety label and/o the final
test data sheet included with you system to dete mine lase safety glasses that will p ovide suitable
p otection fo the ange of wavelengths and output powe emitted. As gene al guidelines, howeve : a)
ecommended Optical Density (OD) fo safety glasses is at least 5 fo wavelengths in the ange 3µm to
14µm; b) p ovided di ect o p olonged viewing of the visible aiming beam (if included in you system) is
avoided, safety glasses that p otect against this visible wavelength should not be necessa y. Rega dless of
gene al guidelines given he e, use s should consult with lase p otective eyewea vendo s fo help
selecting lase safety glasses, and to confi m that selected eyewea will p ovide sufficient eye p otection.
Emission wa ning
light. Indicates lase
emission when lit

MIRcat OPERATION
•
D11-00028-02-A Page 8 of 54
5. Operating onditions
MIRcat lase s a e designed to ope ate in an indoo labo ato y envi onment. A no mal ope ating
envi onment is defined as: within a tempe atu e ange of 15°C to 30°C; Relative Humidity in the ange 10%
- 80% (non-condensing), and altitude f om sea level up to 6500 ft (2000m). MIRcat lase s must be ope ated
in a well-ventilated a ea that allows ai flow a ound the unit. Do not position MIRcat lase s such that the
Lase On/Off button is not easily accessible, o the back panel is not easily accessible.
AUTION: If the ope ation of this lase system is in a manne not specified by the manufactu e ,
the p otection p ovided by the equipment may be impai ed. Do not ope ate this lase system if its
panels a e emoved o if any of the inte io ci cuit y is exposed.
AUTION: Do not ope ate this lase system in wet o damp conditions, o in an explosive
envi onment.
AUTION: Back eflections can cause damage to the quantum cascade gain media and could void
you wa anty. Ca e must be taken to minimize all back eflections into the lase cavity. Ensu e
that no optical su face is no mal to the p opagating beam. Linea o non-linea amplification
systems o pa amet ic f equency conve sion devices (fo example ‘OPOs’ o ‘OPAs’) can cause
intense back eflections. These amplified back eflections can cause immediate and i epa able
damage to the ECqcL™ and should sc upulously be p evented f om eente ing the ECqcL™ cavity.
5.1 Power Requirements
MIRcat lase s a e ated to ope ate with 90VAC to 264VAC single-phase AC input powe . The input AC
f equency must be in the ange f om 47Hz to 63Hz. Plug the unit into an ea th g ounded eceptacle.
Ve ification of p ope g ounding is ecommended. A powe co d with the p ope configu ation f om the
wall to the powe supply input may be substituted fo the supplied cable.
AUTION: Ope ate this lase system only within the specified voltage ange and with p ope
g ounding. Elect ical shock haza d can occu if the equipment is not p ope ly g ounded.
5.2 ooling Requirements for W or High-Duty- ycle Pulsed
Operation
When ope ating a MIRcat in CW o high duty cycle (>10%) pulsed mode, wate cooling of the lase head is
equi ed to emove the highe heat load p oduced by these modes. A wate chille with a cooling capacity
of up to 150W should be used. Suitable compact, closed-loop chille s a e available f om Daylight Solutions –
please inqui e. The chille should be connected to the MIRcat lase head via cooling lines (clea vinyl tubing
with 3/8” OD and ¼” ID) connected to the two quick-disconnect coolant po ts located at the ea of the
MIRcat lase head. MIRcat-QT uses 2 male quick-disconnect plugs with 7/16” OD, such as McMaste -Ca
pa t# 51545K69. MIRcat 1xxx uses 5/16” OD plugs, such as McMaste -Ca pa t# 51545K68. Refe to
chille manufactu e manual fo coolant specification. No mally, only distilled wate should be equi ed as
the coolant fo sho t pe iod of time. The chille should be set to keep the tempe atu e of the MIRcat lase
housing at eithe 20°C, o the tempe atu e stated in the final test epo t that shipped with you MIRcat.

MIRcat OPERATION
•
D11-00028-02-A Page 9 of 54
5.3 ooling Lines – Preventive Maintenance
Pe iodically, and afte moving the lase system, inspect the system fo contamination and ve ify that
cooling po ts a e clea and all cable connections a e visibly secu e. If liquid cooling is employed, ve ify the
cooling connections a e secu e. Fo cleaning and decontamination of the lase system, use only mild
dete gent and moist pape towel. Do not subme se in wate o cleaning solvent.
5.4 Laser Safety Preventive Maintenance – Maintaining Regulatory
ompliance.
It is ecommended that all lase safety featu es and safety inte locks included in you system a e tested and
thei p ope function ve ified eve y 6 months to ensu e they a e still ope ating co ectly. If any safety
featu e o inte lock fails to pe fo m as desc ibed in Section VI of this manual, stop use of the lase system
immediately, p event othe s f om using it (by emoving the key, fo example), and contact Daylight
Solutions o you autho ized ep esentative fo fu the inst uctions.

MIRcat OPERATION
•
D11-00028-02-A Page 10 of 54
II. SYSTEM OVERVIEW
Figure 1. MIRcat system a chitectu e.
NOTE: This manual desc ibes the safe installation, use, and maintenance of Daylight Solutions’
MIRcat™ family of widely tunable mid-IR lase systems. This p oduct family includes MIRcat-QT
(tuning slew ates to >5,000 cm
-1
/s) and MIRcat-1xxx (slew ates up to 100 cm
-1
/s) systems. All
info mation in this manual applies inte changeably to MIRcat-QT and MIRcat-1xxx p oduct
models unless stated othe wise.
As shown in Figu e 4, MIRcat™ lase systems comp ise the following majo system components:
• Sealed, maintenance-f ee MIRcat™ lase head with integ ated cont olle
• AC-DC powe supply
• Compute unning cont ol softwa e
• Optional wate chille fo CW and/o high duty cycle ope ation
The key featu es and main components of the MIRcat™ system a e explained in mo e detail below.
2. System Features
MIRcat’s modula design p ovides use s with g eat flexibility to select a MIRcat configu ation optimized fo
thei applications. The modula design allows use s to facto y-configu e thei system fo one, two, th ee o
fou pulsed o CW/pulsed modules, add a visible aiming beam*, o facto y-upg ade thei configu ation
(type and numbe of modules) late . The lase modules in each MIRcat can be add essed and ope ated
individually, o multiplexed togethe (automatically, via the included cont ol softwa e) to c eate a
collectively ult a-wide tuning ange. Each MIRcat lase module inco po ates a mid-IR Quantum Cascade
Lase (QCL) chip as the gain medium. By using advanced packaging and miniatu ization technology,
Daylight is able to p ovide oom-tempe atu e ope ation of all its QCLs, and a wide selection of QCL chip
Cont ol
compute
(use -
supplied)
USB 2.0
MIRcat
lase
Wate cooling (CW o >10% duty cycle)
Chille
Powe supply
AC
AC
-
DC

MIRcat OPERATION
•
D11-00028-02-A Page 11 of 54
options with cente wavelength spanning ~3 to >13 µm. (We continue to expand the pe fo mance envelope
of ou QCLs – please inqui e.)
Each QCL is built into a p op ieta y Exte nal Cavity QCL (ECqcL™) optical configu ation, in which one end
of the lase cavity is fo med by the QCL and the othe by a diff action g ating that can be otated. By using
an ECqcL design, the emission wavelength and linewidth can be ca efully cont olled. All MIRcat lase
modules can p ovide tunable mid-IR pulsed output. If a CW-capable QCL has been selected fo a lase
module, that module will also be capable of Continuous Wave (CW) ope ation (wate cooling is equi ed).
Unlike many othe lase sou ce types, changing between pulsed and CW ope ation in Daylight’s QCL-based
lase s is effo tless and instantaneous, and equi es only a simple change of ope ating mode (change in
d ive cu ent p ofile) via the GUI o SDK. Compa ed to pulsed ope ation, CW ope ation p ovides na owe
linewidth, highe ave age powe , and fine amplitude and wavelength modulation via MIRcat’s standa d
exte nal cu ent modulation input.
NOTE: The linewidth of a pulsed MIRcat lase module is typically about 0.5 cm
-1
(FWHM). In CW
ope ation, linewidths can be as low as <0.01 cm
-1
(less than a few 100MHz) if MIRcat is tuned to a
single longitudinal mode.
Typical tuning cu ves (output powe ve sus wavelength) a e shown below fo a Daylight Solutions’ pulsed
(Figu e 5) and CW (Figu e 6) ECqcL™. The plots show the high peak (Figu e 5) and ave age (Figu e 6)
powe and wide tuning anges attainable with the ECqcL design. Figu e 7 also shows the ext emely
b oad—and gapless—tuning ac oss the impo tant mid-IR ‘spect al finge p int’ ange that can be achieved
with a MIRcat configu ed with fou pulsed QCL’s selected fo maximum wavelength cove age.
Figure 5. Typical peak power versus wavelength curves for pulsed operation of a Daylight external cavity
quantum cascade laser (E qcL™) at different Q L drive currents. Data recorded at: 500 ns pulse
width and 5 % duty cycle at 15° .

MIRcat OPERATION
•
D11-00028-02-A Page 12 of 54
Figure 6. Typical W (average) power output versus Q L drive current recorded at three different
wavelengths for W operation of a Daylight external cavity quantum cascade laser (E qcL).
Figure 7. Typical tuning curve for an example MIRcat configuration of four pulsed Q L lasers.
Use cont ol of the MIRcat lase system is via a use -supplied compute unning a GUI o SDK command set,
both of which a e included as standa d with each MIRcat system. Using these inte faces, MIRcat use s can
cont ol: wavelength set-points; scans; powe ; t igge ing (and pulse width, duty cycle, and epetition ate in
pulsed ope ation). Info mation sto ed in an EEPROM in the MIRcat lase head p events the use f om
attempting to tune the module beyond the lase ’s ange, o applying inco ect d ive cu ents to the QCLs in

MIRcat OPERATION
•
D11-00028-02-A Page 13 of 54
MIRcat lase head. Daylight’s p op ieta y HFQD™ (High-Fidelity QCL D ive) ci cuit y also ensu es MIRcat’s
QCL chips a e p otected elect onically.
MIRcat p ovides th ee diffe ent wavelength tuning modes: Sweep Mode, Step and Measu e Mode, o Multi-
Spect al Mode. These a e selectable via eithe the GUI o SDK. MIRcat’s Sweep Scan p ovides apid
scanning of the QCL ac oss its p og ammed gain p ofile, eithe uni- o bi-di ectionally. In this mode, use s
can select scanning pa amete s such as sta t/stop wavelengths, step size, tuning ate, numbe of scans and
time between steps (Dwell). MIRcat-1xxx can pe fo m sweep scans at up to 100cm-1/s, while MIRcat-QT
systems p ovide tuning slew ates as high as 5,000 cm
-1
/s. Multi-Spect al Mode allows jumping to up to 20
diffe ent fixed wavelengths ac oss the tuning ange. In this mode, the ope ato can select scanning
pa amete s such as sta t/stop wavelengths, step size, tuning ate, numbe of scans and time between steps.
With this wide ange of options, MIRcat delive s uncomp omised pe fo mance in application-c itical a eas.
Depending on lase modules and configu ation selected, MIRcat can p ovide; tuning anges to >900 cm
-1
;
CW RIN as low as -145dBc/Hz; peak powe output up to 1W; ave age powe output up to 0.5W, and
wavelength epeatability as high as <0.1cm
-1
. All MIRcats also p ovide a single TEM
00
output beam,
ega dless of the numbe of modules selected, which ensu es high on-ta get beam intensities and enables
high-efficiency fibe coupling. In addition, the new MIRcat-QT also adds faste wavelength tuning and
scanning (to >5000 cm
-1
/s) and highe spect al epeatability to the field-p oven MIRcat-1xxx design.
*MIRcat’s optional integ ated visible lase aiming beam p ovides a high-quality, low-dive gence visible
aiming beam that is bo e-sighted accu ately to the path of the mid-inf a ed output. It can be used fo
st aightfo wa d visual p e-alignment of the MIRcat output beam path p io to switching to the mid-
inf a ed output. The visible beam is activated by an ‘Enable Aiming Lase ’ command on the GUI. Activating
the visible beam switches the MIRcat f om mid-inf a ed out to the visible beam output, and vice ve sa.
(Simultaneous mid-inf a ed and visible lase output is not possible.)
3. MIRcat Laser Head - Precautions
The MIRcat lase head is a sealed, alignment-f ee design that neithe equi es no allows inte nal
maintenance. Pulsed and CW ope ation (with wate cooling) is suppo ted by the same lase head. The e a e
no inte nal adjustments available to the use . NEVER attempt to emove the cove o open the optical head
in any way, o the wa anty will be voided.
AUTION: UNDER NO IR UMSTAN ES SHALL THE USER ATTEMPT TO OPEN THE MIRcat
LASER HEAD. Opening the MIRcat lase head will void the wa anty, esulting in misalignment
of the lase cavity, and/o cause i epa able damage to the inte nal components. The MIRcat
lase head is pu ged with a d y ine t gas befo e sealing to minimize moistu e. B eaking this seal
will also void the wa anty.
AUTION: The lase adiation emitted f om this unit is invisible to the naked eye and may be
ha mful if the beam makes di ect and p olonged contact with the eye. Avoid di ect exposu e to
the beam o looking in the di ection of the lase beam di ectly. The safety labels shown in
Section I-2 a e attached to this p oduct.
The optical output po t of the lase is cove ed by a manual shutte , should use s want to block the lase
output beam. The base of the MIRcat lase head has th ee holes, aligned to match up with standa d hole

MIRcat OPERATION
•
D11-00028-02-A Page 14 of 54
patte ns found on met ic of English optical benches. If the MIRcat lase head is mounted di ectly onto an
optical table o b eadboa d, the height of the beam is 4.0 inches (10.61cm).
AUTION: Back eflections can cause damage to the quantum cascade gain media and could
void you wa anty. Ca e must be taken to minimize all back eflections into the lase cavity.
Ensu e that no optical su face is no mal to the p opagating beam. Linea o non-linea
amplification systems o pa amet ic f equency conve sion devices can cause intense back
eflections. These amplified back eflections can cause immediate and i epa able damage to
the ECqcL™ and should sc upulously be p evented f om eente ing the ECqcL™ cavity.
4. omputer ontrol
Figure 8. Back panel for computer control
The MIRcat cont ol GUI offe s a simple inte face that allows manual tuning of the lase , as well as manual
cont ol ove lase d ive cu ent (lase output powe ), tempe atu e, pulsed pa amete s, scanning modes,
and communications po ts.
Compute cont ol of the lase is available th ough the USB 2.0 (o Ethe net - not yet suppo ted but please
inqui e). This allows the use to automatically synch onize tuning of the lase ’s wavelength to a detection
scheme fo applications that include spect oscopy, as well as adjusting the cu ent, pulse pa amete s,
tuning, and tempe atu e of the MIRcat. The back panel of the MIRcat also p ovides TTL signals to help
synch onize the MIRcat to a data acquisition unit. See Section IV-2 fo signals and timing diag ams.
The Cont ol Panel GUI is necessa y to ope ate the MIRcat lase . A Softwa e Development Kit (SDK) is
available and has examples fo LabView VI’s with example sc ipts. A 64-bit ve sion is also available upon
equest.
See Section IV. Manual Ope ation fo fu the details on back panel functionality.

MIRcat OPERATION
•
D11-00028-02-A Page 15 of 54
5. Power Supply
Figure 9. MIRcat Power Supply (A -D converter)
The powe supply connects to the back panel of the MIRcat lase head. It conve ts the local AC powe to the
DC voltage and cu ent equi ed fo safe ope ation of MIRcat. It accepts AC input voltages in the ange 90-
264 VAC, and 47-63 Hz. Ensu e the cable is fi mly seated and secu ed on the back panel befo e tu ning on
the unit. The powe co d can be changed to match local eceptacles.
AUTION: Neve unplug the Powe Supply connecto while the lase is ope ating and the
compute is communicating to the system. Damage to the lase can occu if powe is emoved
du ing ope ation o tuning.

MIRcat OPERATION
•
D11-00028-02-A Page 16 of 54
III. GETTING STARTED
This section outlines the basic p ocedu es fo installing you MIRcat. See Section V - Compute Cont ol fo
details on compute cont ol of the MIRcat and its associated inst uction list.
AUTION: The lase system was shipped in a custom shipping containe . This containe was
custom-designed and tested to ensu e p otection of the MIRcat du ing t anspo tation. Save this
container in a safe place. Should you lase equi e epai o upg ade, you will need to ship the
unit back to the facto y in this same containe . Failu e to do so could void you wa anty. If you
need to etu n the lase to Daylight Solutions but can no longe locate the o iginal shipping
containe , please contact Daylight Solutions’ Custome Se vice using contact info mation listed in
Section VI ‘Se vice and Suppo t’ o visit the web site.
1. Packing List
Each MIRcat ships with the following components:
Power Supply Lase system powe supply (AC-DC conve te )
MIRcat laser head MIRcat lase head
Power cable Powe cable fo 110VAC, 60 Hz
Laser enable key Enable/disable lase powe (key inte lock)
Hose connectors (Qty 2) Fo wate chille connection ( equi ed fo CW o high duty
cycle ope ation)
User Manual (on D or USB
memory stick)
Contains: int oduction and copies of use manual, GUI, and
SDK
To mount the MIRcat on an optical bench, you will need (not included):
Optical bench or table Metal optical bench to mount MIRcat lase head assembly.
3 hex head bolts,
2” (50mm) length
(¼-20 fo English, o M6 fo Met ic).
Used fo mounting MIRcat lase head to optical bench.
Hex (Allen) Key (3/16 fo English, o M5 fo Met ic)
Used fo mounting MIRcat lase head to optical bench.
3 Mount pedestals
(optional)
3 pedestal adapto s to aise beam height to desi ed height
Example: Fo a 4.5” beam height, use 0.5 inch (M6) New
Focus pedestals, #9910, with ¼-20 counte bo e.
3 Pedestal clamping forks
(optional)
Used to clamp down the 3 pedestals above. Example: New
Focus 9909 (1 inch).
Tubing for connecting
liquid cooling
Clea vinyl tubing with 3/8” OD, and ¼” ID, (CW o high duty
cycle ope ation).

MIRcat OPERATION
•
D11-00028-02-A Page 17 of 54
2. Setting Up
1
If the desi ed beam height is g eate than the 4.0
in. beam height specified fo you lase , attach 3
pedestals to the base of the MIRcat lase head
with the additional beam height. Fo example, if
the desi ed beam height is 4.5 inches and the
lase beam height is 4.0 inches, use New Focus
3” pedestals, model# 9910 and optical holding
fo ks #9909 fo a final beam height of 4.5
inches.
2
Mount MIRcat lase head on an optical bench
using th ee (3) sc ews and/o 3 holding fo ks
listed above (o simila device). Beam height is
fixed at 4.0 inches if not using any pedestals. See
Section VII-Specifications fo mo e details on
beam height fo MIRcat lase heads.
3
Connect USB cable to MIRcat lase head and
Compute :
• Connect the USB cable to a compute USB
po t
• Connect USB connecto to the MIRcat lase
head
AUTION: Use caution when
connecting the USB cable if the unit is
plugged in and unning. Neve unplug
the USB cable du ing lase ope ation.

MIRcat OPERATION
•
D11-00028-02-A Page 18 of 54
4
For W Operation:
Connect liquid cooling to the inlet and outlet po ts on the base of the MIRcat lase head.
Use the 7/16” plug with 1/4” hose ba bs p ovided to attach clea vinyl tubing, with 3/8”
OD and 1/4” ID, to the cooling po t quick disconnects, and the othe ends to a chille . Set
the chille tempe atu e to 20°C fo no mal CW ope ation.
NOTE: To ensu e p ope cooling and longe lifetime fo the QCL, CW ope ation
equi es wate cooling of the MIRcat lase head. Since the the mal load in the
MIRcat lase head is small, a minimum of 50W the mal cooling capacity should
be sufficient fo most labo ato y use conditions. P og am the chille to keep
the MIRcat baseplate at 20°C (o the tempe atu e listed on you final test
sheet).
5
Plug the MIRcat Powe Supply into a standa d 3-p ong, single-phase, AC outlet that
p ovides AC powe within the following ange: 90-264VAC, 47 to 63 kHz. A diffe ent AC
powe co d may be equi ed, depending on count y of use.
6
With the Rea Panel Enable Key Switch in the ve tical “OFF” position, tu n the MIRcat
lase head on with the ea Powe switch by momenta ily p essing the black button. The
white LED on top of the MIRcat will come on. Afte initial powe up, the MIRcat Lase will
pe fo m a self-test. The system is eady to use afte an audio beep is hea d, usually 30-45
sec.
7
Launch the MIRcat Cont ol Panel p og am on the compute and it will automatically
connect. Allow app oximately 15 minutes fo the MIRcat lase head to each the mal
equilib ium befo e taking any p ecision measu ements.
8
Tu n on the lase light:
a. When a safe path fo the beam has been p epa ed, open the manual shutte on the
output of the MIRcat lase head.
b. Make su e the p ope Safety Inte lock is connected on the back panel of the
MIRcat lase head fo you lab configu ation in o de to safely tu n on the lase .
(Note: the lase is shipped with a BNC sho ting plug).
c. Tu n the ea panel Lase Enable key to the ho izontal “ON” position. Click the
A m Lase button on the Tuning tab on the GUI. Afte a 5 sec delay, the white light
on top of the MIRcat Lase unit will illuminate to indicate the lase is a med.
d. On the Tuning menu, click on the “tune to wavelength” button and click the TURN
EMISSION ON button. The button label will change to Turn Emission Off and an
optional audible chi p will sound to indicate the lase is emitting light.
e. The lase beam is now p opagating pa allel to the optical table.

MIRcat OPERATION
•
D11-00028-02-A Page 19 of 54
9
For W-Pulsed Operation: See Section IV-9 on Cu ent Modulation.
IV. OPERATION
AUTION: Use of cont ols o adjustments o pe fo mance of p ocedu es othe than those
specified he ein may esult in haza dous adiation exposu e.
This section desc ibes the ope ation of the MIRcat using the Cont ol Panel GUI (i.e., with exte nal compute
cont ol). The lase can be tu ned on and off via the Lase Powe button, and all lase pa amete s can be
adjusted using the menu on the Cont ol Panel p og am. The menu ope ation and complete command set
a e desc ibed below unde Menu Functions.
The back panel offe s access to a safety inte lock, TTL inputs and output synch onous with the lase output,
and othe featu es desc ibed below.
1. Back Panel Interface
Figure 10. MIRcat Back Panel
Power
On/OFF
Button
and
D Power ord
O
N
/
O
FF
switch and powe plug connecto
f om block powe supply
.
Accepts eithe 110VAC, 60Hz o 220VAC, 50Hz.
Interlock
(Safety Interlock)
BNC connecto : Tu ns off the lase when connection is opened. Each
unit is shipped with a sho ting cap fo immediate ope ation. Replace
this cap with an inte lock f om you lab doo o othe device to p ovide
a safe lase ope ating envi onment.
Water hiller (2) Used to connect a flow th u wate chille fo exte nal cooling. Requi ed
Laser Armed
Status LED
DC Power
Trigger In/Out
Laser Safety
Interlock
Modulation Input
(CW Only)
Key Switch
DB-9
USB
Water Chiller (2)
Power On/Off
Button

MIRcat OPERATION
•
D11-00028-02-A Page 20 of 54
fo CW mode o Pulsed >10% Duty Cycle only.
Ethernet RJ-45 connecto . Not yet suppo ted.
DB
-
9
Used to connect the
MIRcat
to an exte nal Data Acquisition System. See
next section fo pin out and signal desc iption.
Continued f om last page.
USB
connector
Used to connect the
MIRcat
to an exte nal compute . Uses HID
inte face. See USB communication late in manual.
Key Switch Used to Enable Lase A ming. Key cannot be emoved in A med
(ho izontal) position.
Trigger In/Out
BNC connecto
s
: A TTL in
put
/output pulse into 50Ω load is p ovided fo
synch onizing exte nal inst uments and data acquisition equipment
with the ising edge of the lase t igge pulse. See timing diag ams in
section 3 on T igge ing and Acquisition Signals.
Modulation Input
( W only)
Allows an exte nal signal to be applied to the QC cu ent bias fo
exte nal modulation. CW only, not yet suppo ted.
Laser Armed Status LED
Lase is A med when illuminated. Key switch must be ho izontal, and
A m lase selected in Cont ol Panel GUI.
2. Triggering and Acquisition Signals on DB-9 onnector
The DB9 connecto on the back of the MIRcat has the following TTL signals fo timing and cont ol with a
Data Acquisition System (DAQ):
Pin Signal description
1 Scan direction:
Active HI output. It is always HI when going f om a lowe to highe wavelength/wave numbe , and LO
when going in the opposite di ection. Fo example, if scan units a e cm
-1
, going f om 1200 to 1400 cm
-1
will
cause the signal to go HI, and LO in the othe di ection. If scan units a e in um, going f om 7 to 10 µm will
cause the signal to go HI, and LO in the othe di ection. This signal is dependent on scan units.
2 Tuned: HI when the laser has scanned to a step wavelength
Active HI output. This signal goes HI when the lase is tuned to a co ect wavelength and is
emitting light. When scanning it will go HI while the lase is emitting light and LO when lase is off.
3 Wavelength trigger: HI when laser has scanned to wavelength
Active HI output. This signal is only used when Wavelength T igge is selected in the
Settings. When in this mode, the lase will emit a single lase pulse using the pulse width specified in the
settings at the specified inte val. Fo example, if scanning f om 7 to 10 µm, and the WL t igge sta t and
stop a e set to 7.5 µm and 9.5 µm, espectively, and the WL t igge inte val is eve y 0.1 µm, this signal will
go HI when the scan c osses 7.5 µm, 7.6 µm, 7.7 µm, etc. The du ation of the HI pulse on the WL t igge
This manual suits for next models
1
Table of contents
Popular Measuring Instrument manuals by other brands
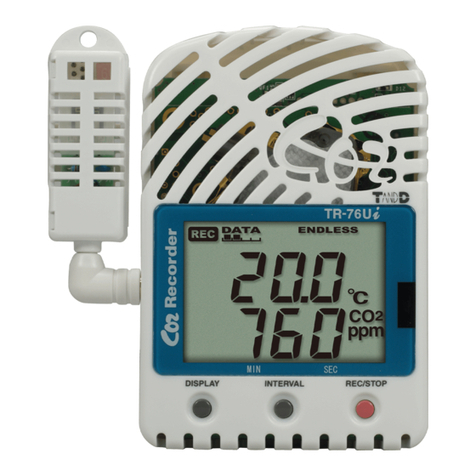
T&D
T&D TR-76Ui Getting started guide

Horiba Scientific
Horiba Scientific LAQUAtwin-K-11 instruction manual
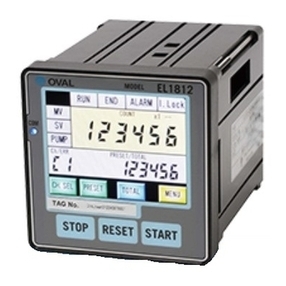
Oval
Oval EL1812 instructions
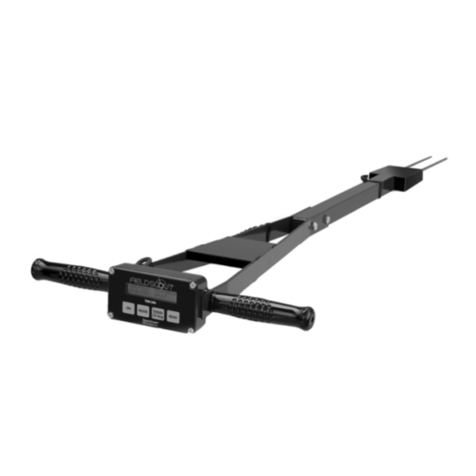
Spectrum
Spectrum fieldscout TDR 300 product manual
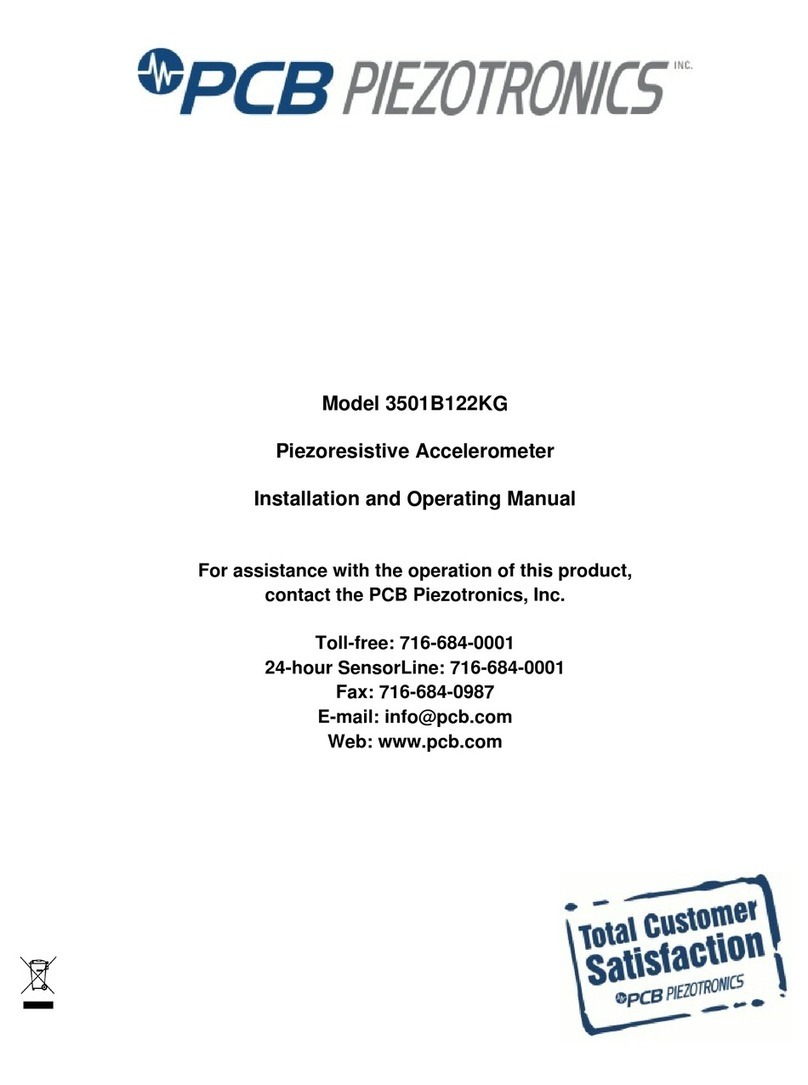
PCB Piezotronics
PCB Piezotronics 3501B122KG Installation and operating manual

Cablescan
Cablescan 90 Series Reference manual