Permalert PAL-AT AT20C User manual


Notice
The information contained in this manual, including but not limited to any product specifications, is subject to
change without notice.
PERMALERT ESP, INC. (PERMALERT) PROVIDES NO WARRANTY WITH REGARD TO THIS MANUAL OR
ANY OTHER INFORMATION CONTAINED HEREIN AND HEREBY EXPRESSLY DISCLAIMS ANY IMPLIED
WARRANTIES OF MERCHANTABILITY OR FITNESS FOR ANY PARTICULAR PURPOSE WITH REGARD TO
ANY OF THE FOREGOING. PERMALERT ASSUMES NO LIABILITY FOR ANY DAMAGES INCURRED
DIRECTLY OR INDIRECTLY FROM ANY TECHNICAL OR TYPOGRAPHICAL ERRORS OR OMISSIONS
CONTAINED HEREIN OR FOR DISCREPANCIES BETWEEN THE PRODUCT AND THE MANUAL. IN NO
EVENT SHALL PERMALERT BE LIABLE FOR ANY INCIDENTAL, CONSEQUENTIAL, SPECIAL, OR
EXEMPLARY DAMAGES, WHETHER BASED ON TORT, CONTACT OR OTHERWISE, ARISING OUT OF OR
IN CONNECTION WITH THIS MANUAL OR ANY OTHER INFORMATION CONTAINED HEREIN OR THE USE
THEREOF.
Caution --This manual may not be up-to-date.
Please check the PermAlert website, www.permalert.com, for the latest revision of this manual.
The manual is typically revised at least once a year. The revision date is on the back cover.

PAL-AT Installation Manual
1
Table of Contents
1Introduction............................................................................................... 5
1.1 General Description......................................................................................................... 5
1.2 Applications ..................................................................................................................... 5
1.3 Receiving and Handling Precautions............................................................................... 5
1.4 Materials and Equipment Normally Supplied by PermAlert.............................................. 5
1.5 Materials and Equipment Normally Supplied by Installing Contractor.............................. 6
2PAL-AT Alarm/Locator Panel ................................................................... 7
2.1 Alarm/Locator Panel Installation ...................................................................................... 7
2.2 Internal Wiring.................................................................................................................. 9
2.3 Control Relays ................................................................................................................. 9
2.4 RS-232 Port................................................................................................................... 10
2.5 Intrinsically Safe - UL / FMRC........................................................................................ 10
2.6 FCC ............................................................................................................................... 10
3Jumper Cable and Junction Box Installation........................................ 13
3.1 Jumper Cable ................................................................................................................ 13
3.2 Calibration Points........................................................................................................... 13
3.3 Junction Boxes............................................................................................................... 14
4Cable Installation in Secondary Contained Piping ............................... 15
4.1 General.......................................................................................................................... 15
4.2 Pull Points...................................................................................................................... 16
4.3 Cable Splices................................................................................................................. 18
4.3.1 Factory Installed Fiber Pull Rope to Continuous Pull Wire Rope Splice.............. 18
4.3.2 Wire Rope to Wire Rope Splice........................................................................... 19
4.3.3 Wire Rope to Wire Rope Splice (alternate) ......................................................... 20
4.3.4 Wire Rope to Leak Detection Cables.................................................................. 21
4.4 Installation of the Continuous Pull Rope........................................................................ 23
4.5 Installing the Sensor and Jumper Cables ...................................................................... 25
4.6 Cathodic Protection........................................................................................................ 27
4.7 Air Testing...................................................................................................................... 28

PAL-AT Installation Manual
2
5Installation of Direct Buried Sensor Cable.............................................29
5.1 General.......................................................................................................................... 29
5.2 Installing the Sensor Cable ............................................................................................ 30
5.3 Above Ground Storage Tanks........................................................................................ 33
6Cable Installation for Raised Floor Areas ..............................................35
6.1 General.......................................................................................................................... 35
6.2 Install the Sensor Cable................................................................................................. 35
6.3 Locator Chart ................................................................................................................. 36
7Cable Connectors ....................................................................................37
7.1 General.......................................................................................................................... 37
7.2 Cable Connector Installation.......................................................................................... 37
7.2.1 CAGOLD and CATFHG Connectors for Sensor Cable Types AGW-Gold, AGT-
Gold and TFH...................................................................................................... 37
7.2.2 CAGOLD / CAJPL Connector for Jumper Cable Types JMP-U/-UD, JPL-U/-UD,
JPP and JMP.......................................................................................................40
7.2.3 CASTD Connector for Jumper Cable Types JMP-U and JMP-UD - Alternate.....42
7.2.4 Butt Splice Connector for TFH Cable .................................................................. 44
7.2.5 CAGOLD Connector for ATP Cable.................................................................... 46
7.3 Shrink Tubing................................................................................................................. 48
7.3.1 Cable Type TFH..................................................................................................48
7.3.2 Cable Types AGT-Gold and AGW-Gold.............................................................. 49
7.4 Cable and Connector Testing Procedures..................................................................... 50
7.4.1 General................................................................................................................ 50
7.4.2 Continuity Test .................................................................................................... 50
7.4.3 Insulation Test..................................................................................................... 50
7.4.4 Alternative System Test....................................................................................... 50
8Probes.......................................................................................................51
8.1 UL and FMRC Requirements......................................................................................... 51
8.2 Probe Integrator Selection ............................................................................................. 51
8.3 Probe Installation ........................................................................................................... 51
8.4 PHLR Hydrocarbon Probe ............................................................................................. 53
8.4.1 Cleaning Sensor Elements Procedure ................................................................ 54
8.4.2 Testing the Probe................................................................................................ 55
8.4.3 Troubleshooting................................................................................................... 55
8.5 Typical Installations........................................................................................................56
8.6 Probe Tests.................................................................................................................... 61

PAL-AT Installation Manual
3
9ATP Cable in Polyurethane Foam Insulation......................................... 63
9.1 General.......................................................................................................................... 63
9.2 System Configuration..................................................................................................... 63
9.3 Calibration Points........................................................................................................... 63
9.4 ATP Cable Tests............................................................................................................ 63
9.4.1 Insulation Test..................................................................................................... 63
9.4.2 Continuity Test.................................................................................................... 64
9.5 Start of Run.................................................................................................................... 64
9.6 Connection of ATP Cable .............................................................................................. 65
9.7 ATP Cable at Tee Connections...................................................................................... 66
9.8 End of Run Termination................................................................................................. 67
WARRANTY .................................................................................................... 69

PAL-AT Installation Manual
4

PAL-AT Installation Manual
5
1 Introduction
1.1 General Description
This PAL-AT®Installation Manual is intended for use as a general installation guide for PAL-AT
alarm/locator panels, sensor cable, cable connectors, and probes. Users (installers) should
independently evaluate the suitability of this information and PermAlert's products for their application
and specific installation. If you receive a PermAlert product that is not described in this manual, contact
PermAlert for the appropriate instructions. Refer to the website, permalert.com (permapipe.com), for the
latest revision of manuals and product data sheets.
1.2 Applications
The PAL-AT system consists of an electronic microprocessor-based alarm/locator panel that monitors
sensor cables and/or probes. The sensor cable may be installed in many applications including:
secondary contained piping, directly in the ground adjacent to pipes or tanks; computer room subfloors;
cleanroom subfloors, or any area where liquids need to be detected. There are several PAL-AT models
available including:
AT20C: Monitors 1 cable up to 2,000 feet.
AT50C: Monitors 1 cable up to 5,000 feet.
AT20K: Monitors up to 2 cables each up to 7,500 feet.
AT40K: Monitors up to 8 cables each up to 5,000 feet.
AT80K: Monitors up to 8 cables each up to 7,500 feet.
1.3 Receiving and Handling Precautions
The following general precautions should be observed:
1. Read this manual carefully before beginning any work. Do not use substitute materials or
short cut recommended procedures. Understanding and following this guide is essential to
avoid installation problems.
2. Collect the needed quantities of all materials well in advance of scheduled work.
3. Check the packing list against received items. Report immediately any shortages or
damaged materials to PermAlert's delivering carrier.
4. All cable must be tested immediately upon receipt following the cable test procedures contained
in this manual. Report immediately to PermAlert any cables that fail this quality control test.
Failure to report within ten workdays of receipt of goods shall waive the purchaser's right to file a
warranty claim.
5. Care must be taken to store all PAL-AT components in a dry and protected area at all times.
Electronic alarm/locator units and sensor cable should be wrapped and sealed with plastic.
6. System drawings, provided by the designer, should indicate the extent, general location, and
arrangement of leak detection equipment, cable, and probes. The contractor (installer) should
become familiar with all details of the installation before proceeding.
7. Electrical work should be performed by a qualified electrician.
1.4 Materials and Equipment Normally Supplied by PermAlert
Each system may include the following items as quoted:
1. Leak detection/location alarm panel
2. Leak sensor cable
3. Jumper cable
4. Cable connector assemblies
5. Adhesive backed cable mounts (CMA) furnished for attachment of sensor cable to flat surfaces

1 Introduction
6
6. Probe assembly, including a PT10 Probe Integrator installed in a NEMA 4X junction box with 60'
of jumper cable and one cable connector assembly
7. Watertight junction boxes conforming to NEMA 4X
Maximum No. of
Cable Connectors
in Enclosure
Enclosure Dimensions
1
6" x 6" x 4"
2
8" x 6" x 4"
4
10" x 8" x 4"
8. Watertight cord grips
9. Shrink tubing for cable connectors
10. RTV adhesive/sealant for cable connectors
1.5 Materials and Equipment Normally Supplied by Installing Contractor
Each system may require the installing contractor to supply the following items:
1. Pull rope, 1/8" diameter, 7 strands, steel wire rope aircraft cable. For installation of cable in
DOUBLE QUIK®, fiberglass, or other plastic piping systems use plastic coated (non-vinyl) wire rope.
Provide pull rope in quantities equal to 120% of system length. (Included with PermAlert piping
systems)
2. Cable spool rack or stand
3. PVC electrical tape
4. Miscellaneous pipe nipples, unions, and fittings, as required to provide watertight jumper cable
connections to sensor cable.
5. 1" rigid or liquid-tight flexible electrical conduit, as required, for installation of jumper cable within
manholes, pits, and buildings. Use 1" conduit hub, OZ Gedney CH-100, connection to junction
boxes.
6. Electrical conduit, junction boxes, and wiring, as required.
7. Ohmmeter for testing jumper cables and sensor cables.
8. 500 volt megger for testing ATP cable only.
9. Hole saw
10. Construction adhesive mastic for attachment of cable mounts to unsealed concrete surfaces
11. Hot air gun for shrink tube application on cable connector assemblies

PAL-AT Installation Manual
7
2 PAL-AT Alarm/Locator Panel
2.1 Alarm/Locator Panel Installation
1. The standard PAL-AT alarm panel must be permanently mounted indoors in a dry area. If the alarm
panel is located outside, it must be installed in a NEMA 3R or 4X enclosure. If PAL-AT is installed
inside another enclosure, a fan is usually required inside the enclosure. The enclosure must not be
located in direct sunlight to prevent excessive heat buildup. In all installations the ambient
temperature must not be less than 0°F and not exceed 120°F
2. A hole is provided for the power conduit entrance (½" conduit) into the alarm unit's enclosure. Use a
knockout punch if larger conduit is required. Inspect and clean the interior of the enclosure before
continuing. Connect all electrical conduits.
3. Wire the unit to an isolated (circuit breaker protected) 120/240 VAC 50/60 Hz circuit. Refer to
Figures 1, 2 or 3 for PAL-AT alarm units wiring diagrams.
4. The PAL-AT alarm unit is connected to the sensor cable using jumper cable (Type JMP-U, JMP-UD,
JPL, or JPP). At least 50' of jumper cable (65' if JPP) must be strung or coiled between the
alarm unit and the connection to the sensor cable. It is recommended to run jumper cable in a
separate conduit for protection of the cable.
5. Remove the partition (cover) over the BNC connector on the PAL-AT panel by removing the 3
mounting screws.
6. Install a standard connector on the jumper cable using the instructions in this manual. A BNC/UHF
adapter is supplied to connect the jumper cable to the BNC connector located under the metal
partition in the PAL-AT panel. The cable must exit the enclosure through the ½" conduit opening
provided. (Use a knockout punch if a larger conduit is required.) Cut the jumper cable to the
required length (minimum 50'), and install a standard coaxial connector as described above.
Replace the partition over the jumper cable connector (see Figures 1, 2 or 3).

2 PAL-AT Alarm/Locator Panel
8
Figure 1
Wiring Diagram for PAL-AT Model AT40K & AT80K
Figure 2
Wiring Diagram for PAL-AT Model AT20C & AT50C

PAL-AT Installation Manual
9
Figure 3
Wiring Diagram for PAL-AT Model AT20K
2.2 Internal Wiring
PAL-AT is shipped with a green LED (power), and a red LED (alarm), on the door of the panel. An
optional horn (90dB or chime) is available. The wiring for the lights and horn is a 5-wire cable connected
to a connector on the processor card. The green LED is illuminated when the panel is powered. The
green LED flashes slowly when the system is not monitoring and is continuously on when it is
monitoring. The red LED is illuminated when any cable is in alarm.
2.3 Control Relays
When PAL-AT detects a fault condition, it switches two SPDT output relays rated for 250VAC, 10A. On
the AT40K and AT80K, they are labeled "alarm” relay and "cable” relay for the appropriate cable number
(see Figure 1). The AT20C, AT50C, and the AT20K relays are labeled "1A", "1B”, and "2B" (AT20K
only) (see Figures 2 and 3). PAL-AT is shipped with the relays configured to operate in a normally
energized mode, so they de-energize in the alarm state (see Section 2.9.1 of the "PAL-AT Operating
Manual" for setting relay configuration).
When PAL-AT is in alarm, the # key can be pressed to return the alarm relay to its normal state. If an
audible alarm or other device is connected to these contacts it is deactivated. When an optional audible
alarm is ordered with PAL-AT it will be prewired to the processor card. All panels must have cable
card 1 installed for the alarm relay to operate, but the cable card does not have to be on-line.
The cable relay remains switched until the fault is cleared or a new reference map is taken and the
system is monitoring the cable again. Control devices or auxiliary equipment should be connected
to the cable relay so they will not be reactivated when the alarm is silenced.

2 PAL-AT Alarm/Locator Panel
10
2.4 RS-232 Port
PAL-AT is provided with an RS-232 communications port. Refer to Figures 1, 2 and 3 for the terminal
strip location and connector pin designation. There is a 40-pin ribbon cable connected to the processor
card. A 10-pin ribbon section branches off the main cable and must be connected to the socket on the
motherboard next to the terminal strip.
2.5 Intrinsically Safe - UL / FMRC
The PAL-AT is listed by Underwriters Laboratories, Inc. and approved by Factory Mutual Research
Company. PAL-AT provides intrinsically safe output circuits for use in Class 1, Division 1 Groups C and
D hazardous locations when used with PAL-AT sensor cables and probes, and installed in accordance
with the instructions in this manual. The sensor cables include AGW-Gold, AGT-Gold, and TFH. Refer
to Section 8, "Probes" for specific probe UL and FMRC requirements. Also, refer to PAL-AT control
drawing, Figure 4, for intrinsic safety requirements.
THE MAXIMUM OPERATING VOLTAGE ALLOWED IN THE PAL-AT PANEL IS 250VAC. IN
ADDITION, THE VOLTAGE ON ANY WIRES TO THE CONTROL RELAYS MUST BE LIMITED TO
250VAC.
The partition (cage) must be installed over the jumper cable BNC connector(s) before operating
the system.
2.6 FCC
The user is cautioned that any changes or modifications, not expressly approved by the party
responsible for FCC compliance, could void the user’s authority to operate the equipment.
NOTE: This equipment has been tested and found to comply with the limits for a Class A digital device,
pursuant to Part 15 of the FCC Rules. These limits are designed to provide reasonable protection
against harmful interference when the equipment is operated in a commercial environment. This
equipment generates, uses and can radiate radio frequency energy and, if not installed and used in
accordance with this instruction manual, may cause harmful interference to radio communications.
Operation of this equipment in a residential area is likely to cause harmful interference in which case the
user will be required to correct the interference at his own expense.
Each Model AT40K and AT80K is supplied with 2 "ferrite blocks" (PermAlert part # 8058205) to comply
with FCC regulations. The jumper cable must pass thru the block in the enclosure. Each block may
have up to 4 cables (see Figure 5).

PAL-AT Installation Manual
11
Figure 4
PAL-AT Control Drawing
Figure 5
Ferrite Block Assembly

2 PAL-AT Alarm/Locator Panel
12
Models AT20C, AT50C and AT20K
Models AT40K and AT80K
Figure 6
Metal Enclosure Dimensions

PAL-AT Installation Manual
13
3 Jumper Cable and Junction Box Installation
3.1 Jumper Cable
1. Jumper cable (types JMP-U, JMP-UD, JPL-U, JPL-UD, or JPP) is used to connect sensor cable
segments and probes in series to form the sensing circuit (string). Jumper cable is not affected by
occasional contact with water and can be installed in building and vaults. In underground locations
and areas where damage may occur to the jumper cable, it is recommended that electrical conduit
be used to provide protection. In wet environments or areas subject to flooding, cable connectors on
jumper cable should be located in watertight electrical junction boxes (NEMA 4 or 4X).
2. At least 50' of jumper cable (65' for type JPP) must be installed from the PAL-AT alarm panel before
the first connection to sensor cable. Table 1 lists the length of jumper that should be installed at the
very end of a sensing string. A cable connector must be installed to terminate the end of the last
jumper cable section and a threaded plastic cap is supplied to cover that connector. Refer to Table 2
for additional jumper cable required in a probe section.
3. Where possible, jumper cable connections to sensor cable should be made within the monitored
area. PermAlert recommends the use of OZ Gedney cord grips installed as shown in Figure 7. Cord
grips must clamp only jumper cable or TFH cable. The outer braid on TFH cable must be pulled
back so the cord grip is located on the smooth outer jacket.
4. Check the assembly with an ohmmeter following the cable testing procedures contained in this
manual.
Figure 7
Typical Cable Connection in Monitored Areas with Junction Boxes
3.2 Calibration Points
1. During the initial setup and calibration of the alarm/locator unit, connectors at selected locations
(calibration points) are temporarily disconnected. Therefore, it is imperative to have accessibility
to connectors at calibration points at all times until the system is brought on-line.
2. Reported fault location accuracy of the first leak is dependent upon the use of and distance between
calibration points. Calibration points are required at changes of cable types unless connected to
short lengths of jumper cable (15' or less). Additional calibration intervals of 500' or less will result in
location accuracy of within +/- 5'. Systems installed with calibration intervals exceeding 500' will
result in location accuracy of less than +/- 1% of the cable length from the previous calibration point.

3 Installing Jumper Cable
14
3.3 Junction Boxes
1. Locate and install all junction boxes before installing any cable. Locate junction boxes as indicated
on system drawings or as required. These locations include calibration points, the start and end of
cable runs, manholes, probes, etc. Care must be taken to prevent water from contaminating these
areas.
2. Securely mount the junction boxes to a vertical wall. In manholes or pits that might collect and hold
water, mount junction boxes as high as possible. Use NEMA 4X junction boxes at all locations.
3. Use a hole saw to cut the junction box as needed for conduit.
4. When jumper cable is installed in electrical conduit, use watertight conduit hubs and cord grips at
junction boxes. Discard the male bushing supplied with the hub and use the cord grip supplied in its
place. Depending upon the specific products used, a lock nut may be required on the cord grip's
threads to pull the hub tight to the wall of the junction box.
Caution: Always keep junction boxes and electrical conduits capped to prevent water from
entering.
Table 1
End of System Jumper Cable Length
System Length
ft/(m)
JMP-U/UD
End Jumper Length
ft/(m)
JPP
End Jumper Length
ft/(m)
0–2500/(0-750)
20/(6)
25/(8)
2500-5000/(750-1500)
50/(15)
65/(20)
5000-7500/(1500-2300)
100/(30)
125/(40)
Table 2
Additional Jumper Cable after Probe
Probe Location
on Sensing String
ft/(m)
Additional JMP-U/-UD
At End of Probe
ft/(m)
Additional JPP
At End of Probe
ft/(m)
Twin Lead Length
Twin Lead Length
20/(6)
15/(4.5)
10/(3)
20/(6)
15/(4.5)
10/(3)
0-3000/(0-900)
0/(0)
0/(0)
0/(0)
0/(0)
0/(0)
0/(0)
3001-4000/(900-1200)
20/(6)
0/(0)
0/(0)
25/(8)
0/(0)
0/(0)
4001-5000/(1200-1500)
60/(18)
25/(8)
20/(6)
80/(25)
35/(11)
25/(8)
Over 5000/(over 1500)
Contact Factory

PAL-AT Installation Manual
15
4 Cable Installation in Secondary Contained Piping
4.1 General
In secondary contained pipe applications, the sensor cable is installed in the bottom (6 o’clock position)
of the air space between the product pipe(s) and secondary containment (outer casing or conduit). The
leak detection cable is a sensitive sensor, capable of detecting small amounts of liquid. Therefore,
every effort must be made to keep the cable dry and prevent water from entering the air space.
Also, long term accumulations of water, corrosive liquids, or hydrocarbon liquids in the
containment pipe may degrade the containment or the leak detection system components. The
piping system must remain sealed during installation to prevent moisture entering the system. The
installing contractor must install caps on the open ends of pipe installed in a trench to prevent liquids
from entering the conduit or containment pipe. If the system becomes wet, if must be completely dried.
Drying methods can consist of: pulling a vacuum on the interstitial space; using compressors; using
desiccant dryers or other methods. Obtain guidance from your piping supplier on proper techniques to
be used with your system.
This section is intended to cover installation methods typically employed with any fabricated secondary
contained pipe systems. Typically, these manufactured products are custom fabricated with product
pipes positioned by specially designed supports within the secondary containment. All pipe supports
and changes in direction that will have leak detection installed must have guides constructed out
of stainless steel, minimum ¾" ID tubing, with flared ends. Plastic supports must be avoided
when the carrier pipe is metal. Consult with the piping system manufacturer before installation
to ensure that all provisions are being made for the cable installation. Because the sensor cable
installation is dependent upon the design provisions employed by the pipe manufacturer, it is
recommended that the secondary pipe manufacturer supply the leak detection/location products. This
sole source responsibility will greatly facilitate proper installation with lower cost.
The following charts are general references for installing a sensor cable into field-constructed secondary
contained pipe system built with piping components. Typically, these systems are constructed using
standard lengths of pipe and fittings for the product and secondary containment structures. Components
of the piping system should be designed, manufactured, and installed to facilitate sensor cable
installation. Because the sensor cable is placed on the bottom of the air space, there must be a
continuous unobstructed passage for the cable(s) being pulled into the system. PermAlert
recommends a 1" air space. Pipe support design and alignment is critical. Pipe supports and
other surfaces that the cable may come in contact with during “pulling” operations must be
smooth to prevent snagging or damaging the cable. Flexible piping systems must include a
perforated tube to install the sensor cable to prevent crushing.
Field joint designs and procedures employed in the installation of the piping system must prevent
damage to the pull rope and/or sensor cable.
Pull ropes must be installed as the pipe system is assembled together to facilitate the installation.
Special stainless steel ¾" ID guide tubes must be installed in the air space of the containment straight,
elbows, tees and wyes (lateral) at the factory. Pull points must be designed and provided at specific
locations to facilitate the installation of the pull cable and leak detection cable.

4 Cable Installation
16
Leak Detection Sizing Chart
Polypropylene / Polyethylene Piping SDR Sizes
Pipe Size
Casing Size
SDR11/SDR11
SDR11/SDR32.5
1.5
4
OK
OK
2
6
OK
OK
3
6
OK
OK
4
8
OK
OK
6
10
OK
OK
8
12
OK
OK
10
14
NO
OK
12
16
N/A
OK
14
18
N/A
OK
16
20
N/A
OK
Leak Detection Sizing Chart
For Standard Weight Steel and Fiberglass Pipe
(w/o insulation, 10 gauge steel or fiberglass containment)
Pipe Size
Casing Size
2
6
3
6
4
8
6
10
8
12
10
14
12
16
Note:
1. Not all pipe types or sizes are shown in the above charts. For different systems
contact PermAlert.
2. Chart is based on smooth pulling surfaces and installation of guide tubes.
3. Multi pipe system will require factory sizing.
4.2 Pull Points
1. Sensor cable must be “pulled” into the monitored areas using a continuous pull rope free of splices
between pull points. Surfaces in which the cable may come in contact with during “pulling”
operations must be smooth to prevent hanging up or damaging of the cable.
2. Generally, pull points can be located at 500' intervals for straight runs. Each 90° fitting on the run
reduces the interval by 150'. For example, a run of 50' with 3 elbows is allowable (500' - (3' x 150') =
50').
3. Pull point designs should be selected not only on the basis of accessibility during installation, but
potential future cable replacement. When future cable replacement is a consideration, it is
recommended that underground installations have watertight junction boxes or secondary contained
access points installed at grade or in vaults (see Figure 8). Caution: Pulling points often become

PAL-AT Installation Manual
17
calibration locations. When this occurs, accessibility to the cable connectors is necessary
during the initial commissioning of the alarm panel and the system’s setup procedures.
Figure 8
Detail of Pulling Point

4 Cable Installation
18
4.3 Cable Splices
Continuous pull rope and sensor cable are "pulled" into the secondary containment during certain stages
of installation. Several splices are used to provide secure attachments to pull ropes and cable during
this procedure. The following methods are recommended for splicing.
Note: When using tape to seal the splices, use only PVC electrical tape. PVC tape minimizes drag on
the cable and reduces snags.
4.3.1 Factory Installed Fiber Pull Rope to Continuous Pull Wire Rope Splice
Step A Extend 12" to 18" of fiber rope and 14" to 20" of wire rope.
Step B Wrap a small amount of electrical tape around the fiber rope's end to prevent unraveling. Using
a small pointed object (such as a nail), slightly separate the fiber rope braid and weave the wire
rope into each opening of the braid as you go.
Step C Pull the wire rope tight, as it is woven into the braid.
Step D Using electrical tape, wrap the entire length of the splice area. The tape should extend
approximately 2" over each end of the splice.
This manual suits for next models
4
Table of contents
Other Permalert Measuring Instrument manuals
Popular Measuring Instrument manuals by other brands
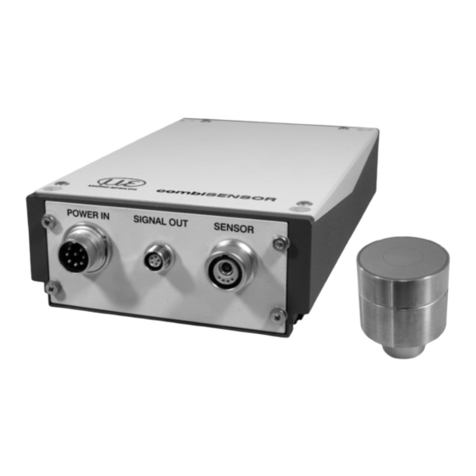
MICRO-EPSILON
MICRO-EPSILON combiSensor KSH5 instruction manual
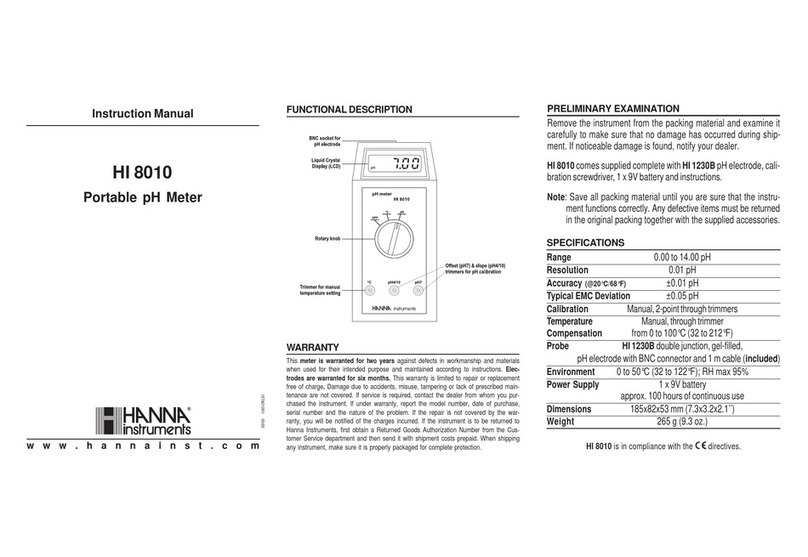
Hanna Instruments
Hanna Instruments HI 8010 instruction manual

ENDA
ENDA EPA942 manual
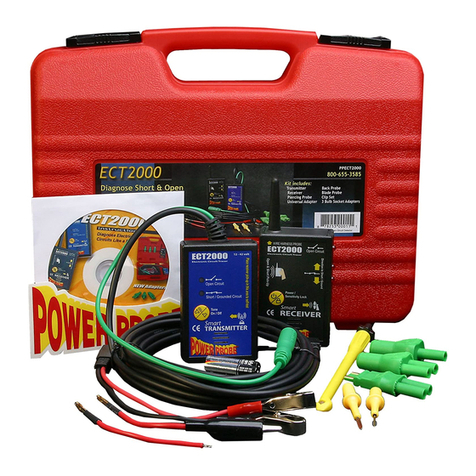
Power Probe
Power Probe power probe III ECT-2000 instruction manual

GREISINGER
GREISINGER GMH 5150 operating manual
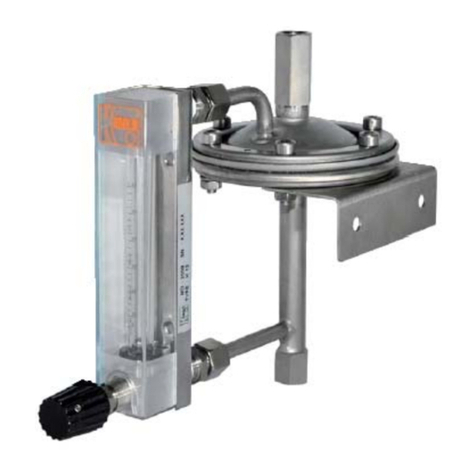
Kobold
Kobold KDF-2 Series operating instructions