delta-mobrey VM Series Guide

www.delta-mobrey.com Page 1 of 7
IOM-VM-C: JUN 2022
Installation, Operation &
Maintenance Instructions
VM Series
Models VM2, VM4 (Pressure Switches)
Foreword
The unit is manufactured, checked and supplied in
accordance with our published specification. When
installed and used in normal or prescribed applications,
with the lid in place and within the parameters set for
mechanical and electrical performance, will not cause
danger or hazard to life or limb.
Warning: Units must be selected and installed by
suitably trained and qualified personnel in
accordance with appropriate codes of practice so
that the possibility of failure resulting in injury or
damage caused by misuse or misapplication is
avoided.
Warning: before installation check that the
instrument characteristics comply with process and
plant requirements
Warning: The users attention is drawn to the fact
that, when the unit is ‘live’ with respect to electrical or
pressure supplies, a hazard may exist if the unit is
opened or dismantled
Warning: Where any special conditions of the
product has been required as identified by the last 4
digits of the part number, follow the necessary safety
instructions for a correct installation.
If the equipment is likely to come into contact with
aggressive substances, suitable precautions should be
taken that prevent it from being adversely affected, thus
ensuring that the type of protection is not compromised.
Aggressive substances: e.g. acidic liquids or gases that
may attack metals or solvents that
may affect non-metallic materials. Suitable precautions:
e.g. regular checks as part of routine inspections or
establishing from the material’s data sheet that it is
resistant to specific chemicals.
SAFETY INSTRUCTIONS
Information ..points out useful tips,
recommendations and information
for efficient and trouble-free
operation.
CAUTION! ..indicates a potentially dangerous
situation that can result in light
injuries or damage to equipment or
the environment, if not avoided.
WARNING! ..indicates a potentially dangerous
situation that can result in serious
injury or death, if not avoided.
WARNING!..identifies hazards caused by
electric power. Should the safety
instructions not be observed, there
is a risk of serious or fatal injury.
WARNING! ..indicates a potentially dangerous
situation that can result in burns,
caused by hot surfaces or liquids, if
not avoided.
WARNING! ..indicates a potentially dangerous
situation in the hazardous area that
can result in serious injury or death,
if not avoided.
Ex applications..special instructions for Ex
applications.
Contents
Foreword
• Allowed over range
• Ambient Temperature
• Process Temperature
• Tools to be used for checking and calibrate the set point
Operating principle
Marking
List of standards to which the product conforms
Special conditions of use
Installation
• Mounting
• Electrical connections
• Wiring
• End of line resistors
• Earthing connections
Operation
• Adjustments
• Calibration
• Periodical calibration check
Commissioning
Inspection and maintenance
• Periodical visual inspection
• Periodical functional verification
Replacement parts
Warranty
Decommissioning
Disposal
Model code
Allowed over range
Pressure exceeding the adjustable range can be allowed
up to the max pressure stated on nameplate. The voltage
and current limits for the microswitch must not be
exceeded. (see fig. 2 & 3). Transitory electrical over
ranges can have a destructive effect on the microswitch.
Ambient Temperature
The surface temperature of the instrument is influenced
by the process temperature, electrical working conditions,
installation and environmental. Special attention must be
taken to avoid exceeding the limits specified on the table
below (i.e. remote mounting, valves, siphons, diaphragm
seals. See Mounting).
Process temperature
For the instrument model VM* the following table is
applicable.

IOM-VM-C: JUN 2022
www.delta-mobrey.com Page 2 of 7
Marking
Flameproof models carry the following label
Installation
Mounting
The instruments are designed to be mounted
vertically with the process connection
underneath. However, mounting up to 45°
vertically is acceptable, although a small
calibration shift may occur. They can be
mounted either directly, or to a wall or panel
using the mounting holes provided. Select the
mounting point to avoid excessive shock,
vibration or temperature fluctuation.
If sudden changes of pressure (pulsations)
are likely then we recommend that a snubber
is fitted between the process line and
instrument.
Operating principles
Pressure Switch models VM* are diaphragm
operated switches. These diaphragms
generate a force proportional to the applied
pressure and are balanced by a user
adjustable control spring. When the force
exceeds that created by the control spring, the
diaphragm moves causing a push rod to
actuate a snap-acting microswitch.
List of standard to which the product is
conformed
This product complies with the following standards:
IECEx ATEX UKEx
IEC 60079-0: Ed.7 EN IEC 60079-
0:2018
BS EN IEC 60079-0:2018
IEC 60079-1: Ed 7 EN 60079-1:2014 BS EN 60079-1:2014
IEC 60079-31: Ed.2 IEC 60079-31:2014 BS EN 60079-31:2014
Tools to be used for checking and
calibrate the set point.
• Hex Socket Key 1.5 mm
• Open ended spanner A/F 13mm
• Screwdriver Pozidriv size 1
The following calibration circuit is to be used
for the calibration of the set point or periodical
functional verification. The test gauge should
have a range similar to the instrument under
verification with an accuracy consistent with
the accuracy required to calibrate the set
point.
Temperature
Class
Ambient
temperature
range
Max process
temperature
at the process
connection
Max electrical
loads
(resistive loads)
T6
-20°C to +65°C
or
-30°C to +65°C
or
-55°C to +65°C
65°C
5 A @
110/250 V
a.c. or 2 A @
30V d.c.
T5 .. T1
-20°C to +80°C
or
-30°C to +80°C
or
-55°C to +80°C
80°C
Special conditions of use
Warning: The VM Pressure Switch must not
be installed in a location where moving dust
flow can generate an electrostatic charge on
the equipment.
Warning: if the equipment is likely to come
into contact with aggressive substances, e.g.
acidic liquids or gases that may attack metals
or solvents that may affect polymeric
materials, then it is the responsibility of the
user to take suitable precautions that prevent
it from being adversely affected, ensuring that
the type of protection is not compromised .
Warning: The flamepaths are not to be
repaired.
Warning: Before open the lid de-energise the
instrument and wait 5 minutes.
Fig. 1 - Calibration Circuit
Fig. 2 - Flameproof nameplate
Instrument equipped with End of Line
Fig. 3 - Nameplate of instrument equipped with
End of Line resistors
Instrument equipped with End of Line resistor
carry the following label markings:

IOM-VM-C: JUN 2022
www.delta-mobrey.com Page 3 of 7
Insert bare wires fully into the terminal block
and tighten securely. Keep wiring tails to a
minimum and check that wires do not
interfere with the operating mechanism. The
instrument may be equipped with a
microswitch single pole, double throw or two
independent switches settled at the same set
point.
Before closing the lid:
- Ensure the wire is clear of all moving parts.
- Ensure that wires do not touch the lid as it
is closed.
Close the lid, being careful not to trap any
wires in doing so. Securely tighten the M3 lid
locking screw set provided using a 1.5mm
hex key.
Caution: Check the connection thread size
and specification on the unit to avoid
mismatching with the process connection
adaptor. See no. 11 of product code.
Electrical Connections
One electrical entry is provided, into which
cable glands can be assembled. The thread
type and size is marked on the enclosure, just
below the connection.
Warning: Cable gland/adaptor used for the
electrical connection of the flameproof
instruments shall be certified according to IEC
or EN standards and shall guarantee
instrument degree of protection (IP66).
Furthermore, in order to guarantee the degree
of protection IP66 and the non-loosening of
cable gland/adaptor, it is recommended to
seal the threads of connection with an
anaerobic sealant. For instance, a sealant like
Loctite ® 542 can be applied on the thread
before screwing it into the enclosure entry.
The three switch terminals are clearly marked
“NC - NORMALLY CLOSED”, “NO -
NORMALLY OPEN” and “C - COMMON”.
The following diagram can be used as a
guide for wiring.
Fig. 5 - Direct Installation
Wiring
Disconnect all supply circuits before wiring.
Wire in accordance with local and national
codes. Use cables no larger than 2.5 mm2 (14
AWG)
Warning: Do not exceed electrical ratings
stated in literature and on nameplates.
Warning: If the ambient temperature exceeds
60 °C it is recommended to use cables suita-
ble for operating temperatures no less than
105 °C.
End of line resistors
Some products may be supplied to order,
fitted with end of line resistors. Resistors in
use may generate heat. The type, quantity,
configuration, fitment method and allowable
electrical loads are limited by the scope of the
certification.
Warning: Never fit the end of line resistors or
modify without contacting Delta-Mobrey.
For wiring see the figure on the last page.
Warning: Do not exceed electrical ratings
stated in literature and on nameplates.
Fig. 4 - Remote installation
Fig. 6 - Electrical Connections
SPDT version DPDT version
Instruments should be mounted to avoid excessive
heat transfer from the process lines or adjacent
plant. The process fluid could crystallise/solidify, so
it is recommended to use of adequate chemical
seals and capillary.
Use a spanner to support the process connection
when fitting the instrument. The following figures
show the essential installation tips.

IOM-VM-C: JUN 2022
www.delta-mobrey.com Page 4 of 7
Operation
Adjustments
Pressure Switches are supplied to a midscale
falling, unless otherwise specified.
If the instrument has been ordered with a
specific calibration value the adhesive label
shows the set point value.
It is a good rule to check the calibration values
are marked on the relevant adhesive label,
prior to installation.
Earthing connections
Warning: The instrument is supplied with two
protective grounding connections, one inside
and one outside the enclosure. The two
connections provide effective connection to a
conductor with a cross-sectional area of at
least 4 mm2.
Warning: In order to protect the instrument
against extreme environmental conditions, a
coating thicker than 0.2 mm should be
applied. The grounding connection has to be
adequately realised to prevent an
electrostatic surcharge on the instrument
surface. CLEAN ONLY with a damp cloth
Calibration
Please follow the below suggested steps to
calibrate the set point of the instrument:
Connect the instrument to the pneumatic tools
in the normal installation position (see Fig.1).
Loosen the lid lock screw and unscrew the lid.
Connect the warning lamp appropriately.
Caution: Do not attempt to set the switch
outside the scale limits.
Though the unit may be set anywhere within
its range, for optimum performance, it is good
practice to have a set point value between
25% and 75% of span.
Connection C-NO terminal
- The circuit is open at the normal operating
pressure, the switch closes the circuit as the
pressure increase when the desired value is
reached.
- The circuit is closed at the normal operating
pressure, the switch opens the circuit as the
pressure decreases when the desired value
is reached
Connection C-NC terminal
- The circuit is closed at the normal operating
pressure, the switch opens the circuit as the
pressure increases when the desired value is
reached.
- The circuit is open at the normal operating
pressure, the switch closes the circuit as the
pressure decreases when the desired value
is reached
Pressurise the circuit and slowly increase the
pressure up to the set point. Using a suitable
spanner (Ch 13), rotate the range adjuster
clockwise to increase the set point and counter
clockwise to decrease the set point up to the
relative lamp turn ON (or OFF).
Go to the normal operating pressure and
increase (or decrease) the pressure up the
relative lamp turn ON (or OFF). Read the
pressure on the test gauge. Eventually adjust
the range adjuster and re-check again using
the lamp until the set point is achieved with the
required accuracy.
Close the instrument lid and tighten lid lock
screw.
Write the set point on the adhesive label
Caution: The microswitch is factory set and
should not be adjusted. Should these parts be
accidentally loosened, please contact Delta
Mobrey for assistance.
Periodical calibration check
Connect the instrument to the pneumatic tools
in the normal installation position (see Fig.1).
Loosen the lid lock screw and unscrew the lid.
Connect the warning lamp according to the
desired function.
Set point calibrated with increasing
pressure
On atmospheric pressure, pressurise the
circuit and slowly increase the pressure up to
the set point (the warning lamp turns ON).
Record the pressure read out on the test
gauge. Return to atmospheric pressure.
Repeat the above operation twice.
Set point calibrated with decreasing
pressure
On atmospheric pressure, pressurise the
circuit up to the upper range value.
Decrease the pressure slowly up to the set
point (the warning lamp turns ON).
Record the pressure read on the test gauge.
Return to upper range pressure value.
Repeat the above operation twice.
Evaluation of set point value and
repeatability
With all the above values detected, calculate:
- Average set point value
- Repeatability find the maximum difference
of the detected set point values
If the average set point is different from the
expected setpoint, the instrument must be
recalibrated.
If the repeatability is higher than the value in
the Technical Data Sheet of the product,
replace the instrument with a new one and
contact the factory.
End of verification
Remove the instrument from the pneumatic
tool and disconnect the warning lamp
Close the instrument lid and tighten the lid lock
screw.

IOM-VM-C: JUN 2022
www.delta-mobrey.com Page 5 of 7
Warranty
See Standard Conditions of Sale.
Inspections and maintenance
The instrument is maintenance-free but it is a
good practice to proceed with periodical
inspections (visual and functional).
Inspections should be carried out at list once
a year depending upon operational and,
environmental conditions and customer
planning.
Caution: It is recommended that instruments
used to provide an alarm or shutdown safety
are operated on periodically to ensure they
are functioning correctly. If further
maintenance is required seek advice from
Delta Mobrey before attempting to repair or
replacement parts.
Decommissioning
Warning: Verify that the loop is in a safe
configuration before acting on the valves and
instrument. Power off the instrument.
Warning: before removing the lid or the cable
glands de-energise the instrument and wait 5
minutes.
Do not dispose the process fluid into the
environment if this cause pollution or personal
injury.
Warning: In the case of flameproof
instruments, it is recommended to follow the
standard IEC 60079-17 and for the withdrawal
from service of electrical apparatus.
- Isolate the instrument from the process and
depressurise acting on the valves.
- Loosen the lid lock screw and unscrew the lid.
- Disconnect all the live terminals and insulate
the cables.
- Disconnect the grounding.
- Remove the cable gland.
- Dismount the instrument from the process
connection.
Warning: Verify that loop is in a safe
configuration before acting on the valves and
instrument. Do not dispose the process fluid
into the environment if this causes pollution or
personal injury.
Periodical visual inspection
Isolate the unit from the power supply and
operational location.
Warning: Flameproof instruments installed in
the explosive atmospheres of combustible
dust, must be periodically cleaned externally
in order to remove any accumulation of dust.
Verify the integrity of the electrical unit using
IEC 60079-17 as guide.
Verify if the device for natural ventilation is in
place and is free from obstructions such as
fungi, molds and insects.
Verify the leakage of the process externally.
Loosen the lid lock screw and unscrew the lid
Warning: Before removing the lid or the cable
gland, de-energise the instrument and wait 5
minutes.
- Check all terminals for tightness.
- Check the cable tails are not fouled or
chaffed.
- Check for internal condensation.
- Check that the gasket is seated properly in
the lid recess and is not worn.
- Check that the vent area does not become
blocked or obstructed and vent plug has not
degraded.
Commissioning
Warning: Ensure the enclosure is sealed and
the cover locking set screw is tightened fully
before the switch is energised.
The instrument starts operating as soon as it is
energised and the root valve is opened.
Fig. 7 - Set point adjusting
Replacement parts
Only the microswitch and terminals can be
replaced. Use factory authorised parts only.
IMPORTANT NOTE: Operations involving
the replacement of essential components
must be carried out at our workshop, espe-
cially for instruments with flameproof certifi-
cation; this is to guarantee the user accurate
restoration of the products original settings.
Warning: The flame paths (cable entry &
cover threads, range adjuster) are not to be
repaired.
Periodical functional verification
The verification consists of checking the set
point. This verification is done, usually,
removing the instrument from the plant and
perform the verification in a test room (see
periodical calibration check paragraph).
Warning: Before removing the lid or the cable
gland, de-energise the instrument and wait 5
minutes.
If the verification is done on-site the preferred
procedure is the verification of the entire loop
without removing the lid or the cable gland.
Warning: The flameproof instruments may be
checked on site only if the apparatus suitable
for explosive atmospheres are used.

IOM-VM-C: JUN 2022
www.delta-mobrey.com Page 6 of 7
Model code
Enclosure
Model
Electrical Entry
Material of Wetted Part
Range
Switch
Process Connection
Options & Treatments
Special Engineering
Warning: The process fluid can be hot or
corrosive.
- Plug the process pipe.
- Re-assemble the lid.
- Remove the mounting screws to the wall/panel.
Disposal
The instrument is mainly made of aluminium
and stainless steel. Remove the microswitch
and clean the wetted parts before disposing
the instrument.

IOM-VM-C: JUN 2022
www.delta-mobrey.com Page 7 of 7
DIMENSIONS (in mm) AND WEIGHT (in kg)
END OF LINE RESISTOR TYPICAL WIRING
Dimensions
Weight: 1.5 kg
SCHEME A - DUAL
RESISTORS
SCHEME B - DUAL
RESISTORS
SCHEME C - SINGLE
RESISTOR
SCHEME D - DUAL
RESISTORS
SCHEME E - DUAL
RESISTORS
SCHEME F - SINGLE
RESISTOR
This manual suits for next models
2
Other delta-mobrey Switch manuals
Popular Switch manuals by other brands

ZyXEL Communications
ZyXEL Communications GS1900 Series user guide
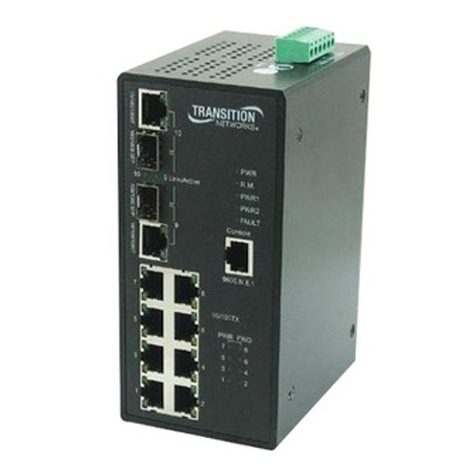
Transition Networks
Transition Networks SISPM1040-382-LRT quick start guide
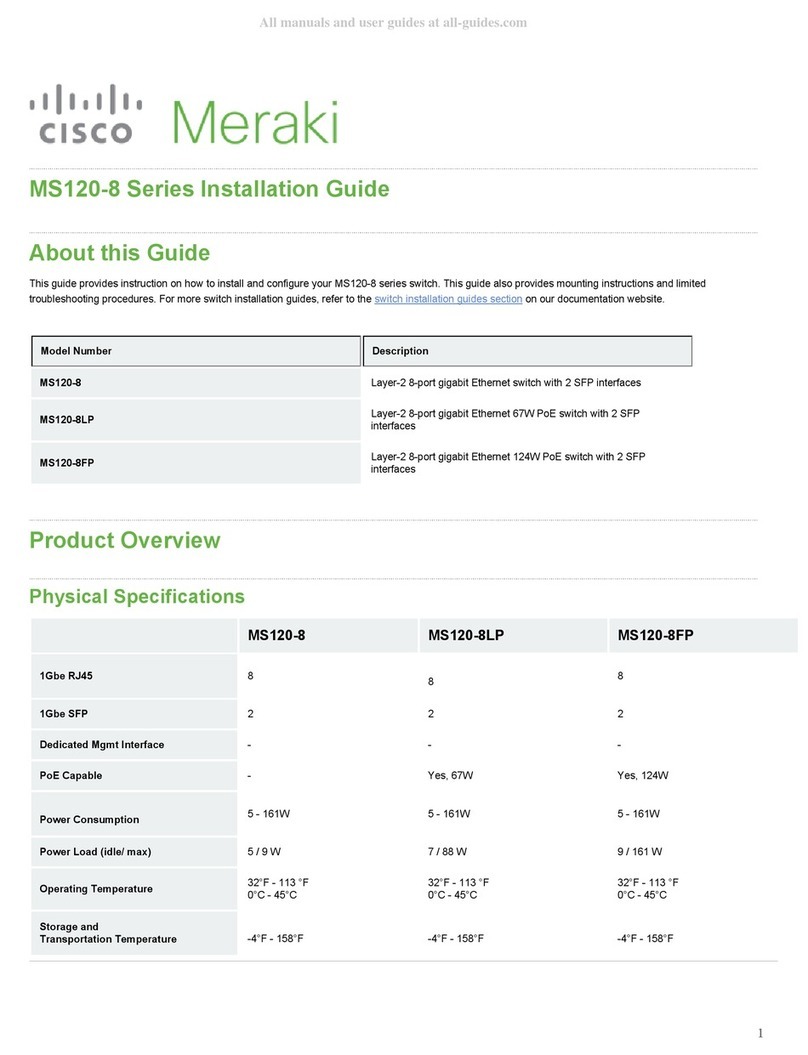
Cisco
Cisco Meraki MS120-8 Series installation guide
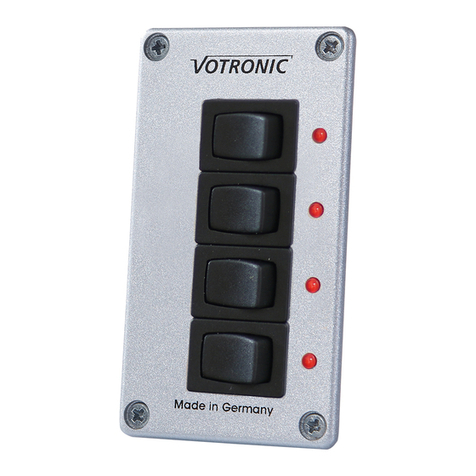
Votronic
Votronic 4 S 12/24 Installation and operating manual
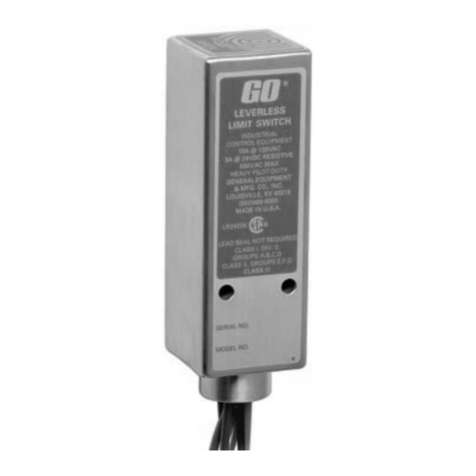
Emerson
Emerson 80 Series GO Switch Handbook
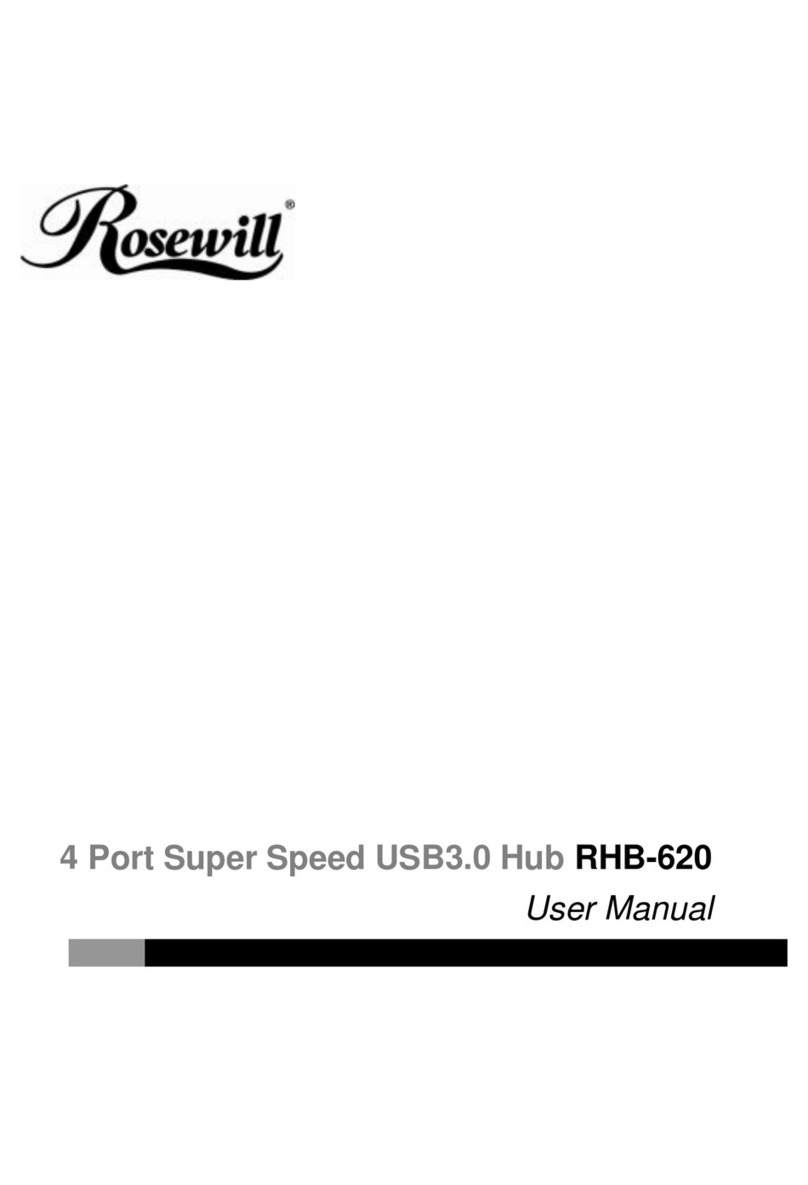
Rosewill
Rosewill RHB-620 user manual