delta-mobrey GR Series Owner's manual

www.delta-mobrey.com
IOM-GR-B : SEPT 2019
Installation, Operation &
Maintenance Instructions
GR Series
Models GR2, GR4 (Pressure Switches)
Models GR3, GR6 (Differential Pressure Switches)
Model GR7 (Temperature Switches)
General
The unit is manufactured, checked and supplied in
accordance with our published specification, and
when installed and used in normal or prescribed
applications, with the lid in place and within the
parameters set for mechanical and electrical
performance, will not cause danger or hazard to life
or limb.
THE USERS ATTENTION IS DRAWN TO
THE FACT THAT, WHEN THE UNIT IS
‘LIVE’ WITH RESPECT TO ELECTRICAL
OR PRESSURE SUPPLIES, A HAZARD
MAY EXIST IF THE UNIT IS OPENED OR
DISMANTLED.
UNITS MUST BE SELECTED AND
INSTALLED BY SUITABLY TRAINED AND
QUALIFIED PERSONNEL IN
ACCORDANCE WITH APPROPRIATE
CODES OF PRACTICE SO THAT THE
POSSIBILITY OF FAILURE RESULTING IN
INJURY OR DAMAGE CAUSED BY
MISUSE OR MISAPPLICATION IS
AVOIDED.
THE MICROSWITCH ASSEMBLY WITH
FACTORY SEALED LEADS HAS BEEN
CAREFULLY POSITIONED AT THE
FACTORY. ANY DISTURBANCE MAY
RENDER THIS UNIT INOPERATIVE.
Operating principles
Pressure Switch models GR2, GR4 and Differential
Pressure Switch models GR3, GR6 are diaphragm
operated switches.
These diaphragms generate a force proportional to
the applied pressure and are balanced by a user
adjustable control spring. When the force exceeds
that created by the control spring, the diaphragm
moves causing a push rod to actuate a snap-acting
micros-witch.
Temperature model GR7 works in the same way as
the Pressure models with the exception that the
applied pressure comes from the expansion of a
vapour enclosed in either a rigid stem or semi-rigid
thermal system.
INSTALLATION
Mounting (All models)
The instruments are designed to be mounted
vertically with the process connection underneath.
However, mounting up to 45° from the vertical in any
plane is acceptable, although a small calibration shift
may occur. They can be mounted either direct to
process, or to a wall or panel using the back plate
provided. Select the mounting point so as to avoid
stresses, excessive shock, vibration or temperature
fluctuation being imparted to the switch during
operation. Instruments should be mounted to avoid
excessive heat transfer from the process lines or
adjacent plant. To avoid undue stresses being
imparted to the instrument when wall/panel
mounted, it is recommended that a short length of
flexible line be installed between the instrument and
process line. If sudden changes of pressure
(pulsations) are likely then we recommend that
snubbers are fitted between the process line and
instrument.
ALWAYS HOLD A WRENCH ON THE
PRESSURE ENTRY HEX WHEN MAKING
PRESSURE CONNECTION TO THE
SWITCH. DO NO TIGHTEN BY TURNING
THE ENCLOSURE.
CHECK THE CONNECTION THREAD SIZE
AND SPECIFICATION ON THE UNIT TO
AVOID MIS-MATCHING WITH THE
PROCESS CONNECTION ADAPTOR. SEE
DIGIT 11 OF PRODUCT CODE.
Mounting (Model GR7- Rigid Stem)
Assemble the unit via a thermowell, using the
spanner facility provided and ensuring that:
a) the sensing bulb is fully immersed in the
process temperature
b) the sensing bulb does not bottom out in the
thermowell which could cause damage
Mounting (Model GR7 - Capillary system)
Mount the sensing bulb so that the capillary end is
above the bulb and the bulb is level with, or no more
than 250mm below the base of the instrument. The
stem is fitted with a sliding compression gland to
accommodate different thermowells.

www.delta-mobrey.com
IOM-GR-B : SEPT 2019
Junction Boxes
Various optional junction boxes can be provided and
are defined by the 5th character of the model code.
Option include:
Code ‘C’: see fig 1
Code ‘D’: same dimensions as code ‘C’ but Exe
approved for use in Zone 1.
Code ‘V’ and ‘W’ same dimensions as code ‘C’
but Exia approved for use in Zone 0.
Code ‘J’ :see fig 2. Exe approved for use in Zone
1.
Cert Baseefa03ATEX0089X (EN 60079-0: 2006,
EN 60079-7: 2006)
Certified II2G Exe II T6
When used at 11A , cabling to be 12AWG.
ATEX
ATEX
Installation of electrical adaptors and
cable glands to the electrical entry -
when Junction Box is fitted
The standard entry is a single 1/2” NPT - M thread.
Other non-ISO and tapered threads will have their
size and type stamped on the enclosure next to the
entry.
TAKE CARE TO SELECT AND INSTALL
ADAPTORS THAT DO NOT REDUCE
THE ENCLOSURE’S DEGREE OF PRO-
TECTION WHEN IN USE IN ZONE 1
HAZARDOUS AREAS.
IT IS A SAFETY REQUIREMENT THAT
AT LEAST 5 FULL THREADS ARE EN-
GAGED BETWEEN THE ADAPTER, CA-
BLE GLAND OR STOPPING PLUG, AND
THE ELECTRICAL ENTRY WHEN THE
UNIT IS IN OPERATION. NEVER OPER-
ATE THE UNIT UNLESS THIS CONDI-
TION IS MET.
Wiring
DISCONNECT ALL SUPPLY CIRCUITS
BEFORE WIRING
DO NOT EXCEED ELECTRICAL RAT-
INGS STATED IN LITERATURE AND ON
NAMEPLATES.
The leads are factory sealed so it is unnecessary
to seal the conduit to the conduit nipple. However,
the leads must be suitably protected against me-
chanical damage and terminated in a suitable junc-
tion box or terminal facility in accordance with local
and national codes. Each conductor is provided
with an identity tag. If these become detached refer
to the colour code in the wiring diagram (Fig 2).
Fig 1
Fig 3
Fig 2

www.delta-mobrey.com
IOM-GR-B : SEPT 2019
End of line resistors
Some products may be supplied to order fitted with
end of line resistors. Resistors in use may generate
a heat source. The type, quantity, configuration,
fitment method and allowable electrical loads are
limited by the scope of the certification.
NEVER FIT END OF LINE RESISTORS OR
MODIFY WITHOUT REFERENCE TO
DELTA MOBREY
Replacing cover on Flameproof
enclosures
Before connecting to electrical power, screw on
cover hand tight making sure that mating surfaces of
the lid and enclosure are in contact. Use the locking
screws provided to prevent casual and unauthorised
removal of the cover.
DO NOT USE GREASES OR
LUBRICANTS NOT COMPATIBLE WITH
THE ENVIROMENT, PROCESS OR
ALUMINIUM.
IT IS A SAFETY REQUIREMENT THAT AT
LEAST 5 FULL THREADS ARE ENGAGED
BETWEEN THE COVER / LID AND THE
ENCLOSURE WHEN THE UNIT IS IN
OPERATION. NEVER OPERATE THE
UNIT UNLESS THIS CONDITION IS MET.
Note: For accurate setting of Pressure and
Differential Pressure models, a suitable pressure
gauge must be used in conjunction with the above
procedure. Do not attempt to set the switch outside
the scale limits. For Temperature models a suitable
calibrated temperature source should be used.
Though the unit may be set anywhere within its
range, for optimum performance, it is good practice
to have a set point value between 25% and 75% of
span.
ATEX
OPERATION
Adjustments
Pressure and Temperature Switches are supplied
calibrated at the midpoint of their range and to a
falling pressure or temperature unless otherwise
specified.
Set point adjustments (All Models):
(See fig. 4)
1. Isolate the instrument from process and power
(Adjustment may be carried out with the unit live)
2. Loosen both cover screws
3. Rotate cover anti-clockwise to allow access.
4. Using a screwdriver, rotate the range adjuster to
obtain the desire setting. Turn right to left to
increase the setting. An appropriate setting is
shown by pointer against reference scale.
5. Rotate cover clockwise to close and tighten
screws.
As a guide, one complete revolution of the adjuster
will alter the set point by approximately 15% of the
range.
Wiring - when Junction Box is fitted
(See Fig. 3)
Some models may be provided with an integral
weatherproof or Ex junction box.
WIRE IN ACCORDANCE WITH LOCAL
AND NATIONAL CODES. USE CABLES
NO LARGER THAN 2.5 MM 2 (14 AWG)
Insert bare wires fully into the terminal block and
tighten securely. Keep wiring tails to a minimum.
ATEX
ATEX
ATEX
Fig 4
Fig 5

www.delta-mobrey.com
IOM-GR-B : SEPT 2019
SPECIAL CONDITIONS FOR SAFE USE
For certificate number
Baseefa02ATEX0214X:
The permanently attached leads shall be suitably
protected against mechanical damage and
terminated in a suitable junction box or terminal
facility suitable for the conditions of use.
For certificate number
Baseefa06ATEX0091X:
1) The apparatus must be installed such that the
risk of impact or abrasion is negligible.
2) The permanently attached leads shall be suitably
protected against mechanical damage and
terminated in a suitable junction box or terminal
facility suitable with a minimum degree of
protection of at least IP6x.
3) The installation of external connections to models
of the apparatus with terminal enclosures must
be carried out using appropriate conduit or cable
gland with a degree of protection of at least IP6x,
Component Certified by an EU approved
Certification Body
For certificate number
Baseefa03ATEX0089X:
1) Not more than 1 single or multiple lead shall be
connected into either side of any terminal
2) Leads to be insulated for the appropriate
voltage. Insulation to extend to within 1mm of the
terminal throat.
3) All terminal screws used and unused to be
tightened down
4) Circuits to be protected by excess current
protection which shall operate within 4 hours a t
1.5 X the designed load current.
5) Al cable entries shall maintain IP66 minimum
6) Kwikstik 3507 inseal gasket must be fitted
between GR series adaptor and enclosure to
ensure IP66 ingress protection.
Note: When weatherproof junction box code ‘C’ is
fitted the unit must not be used in hazardous areas
unless the circuit or system to which it is connected
is Intrinsically Safe.
REPLACEMENT PARTS:
Use only factory authorised parts and the fitting
instructions that are supplied.
Process configurations
(Models GR3, GR6 - range BC)
For normal pressure difference operation, the con-
nections are made to the High Pressure (HP) and
Low Pressure (LP) ports as appropriate. For single-
ended positive pressure operation, the HP only is
used and the LP is left open to atmosphere. The
single-ended negative pressure operation, the LP
only is used and the HP is left open to atmosphere.
Use a breather / filter in the vacant port of single-
ended operation.
Compound range eg –12.5 to +12.5 mbar
(Models GR3, GR6 - range BC)
For normal operation, negative pressure may be
applied to the LP port, whereby the HP port is left
open to atmosphere and the set point is between 0
and +12.5 mbar.
For reverse operation, negative pressure may be
applied to the HP port, whereby the LP port is left
open to atmosphere and the set point is between 0
and –12.5 mbar.
For positive pressures the opposite applies.
It is recommended that the minimum setting is to be
not less than 5% of FS either side approaching zero.
MAINTENANCE
Inspections should be carried out at quarterly to
yearly intervals depending upon operating condi-
tions.
Where a terminal enclosure is fitted, isolate the unit
from process and power and remove the lid. Check
all terminals for tightness. Check that cable tails are
not fouled or chafed. Check for internal condensa-
tion. Rectify as necessary.
It is recommended that instruments used to provide
an alarm are operated periodically to ensure they
are functioning correctly.
If further maintenance is required, seek advice from
DELTA MOBREY before attempting repair or re-
placement of parts.
Should the diaphragm fail the process will vent to
atmosphere via a control orifice without pressurising
the switch enclosure. Periodically ensure the vent
area does not become blocked and vent plug has
not degraded. Ensure that the vent area is not ob-
structed.

www.delta-mobrey.com
IOM-GR-B : SEPT 2019
DIMENSIONS
Enclosures Styles
Sensors
This manual suits for next models
5
Table of contents
Other delta-mobrey Switch manuals
Popular Switch manuals by other brands

NETGEAR
NETGEAR GSM7224R - ProSafe Switch datasheet
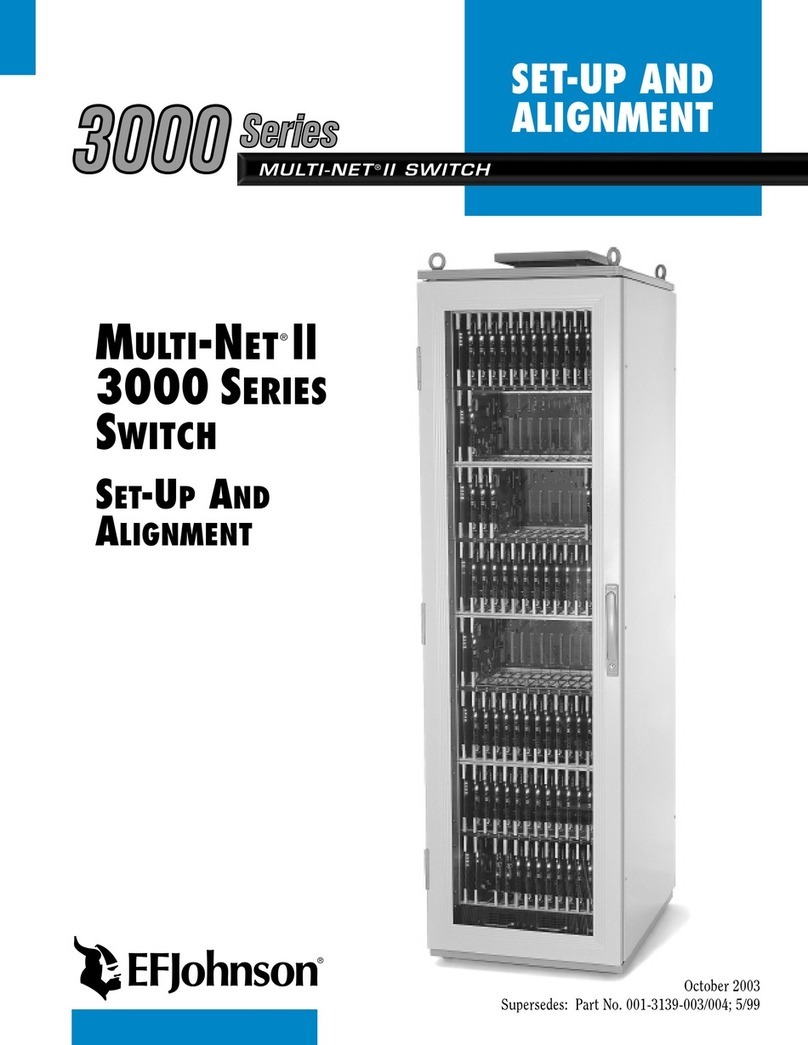
E.F. Johnson Company
E.F. Johnson Company 3000 SERIES Setup and alignment manual
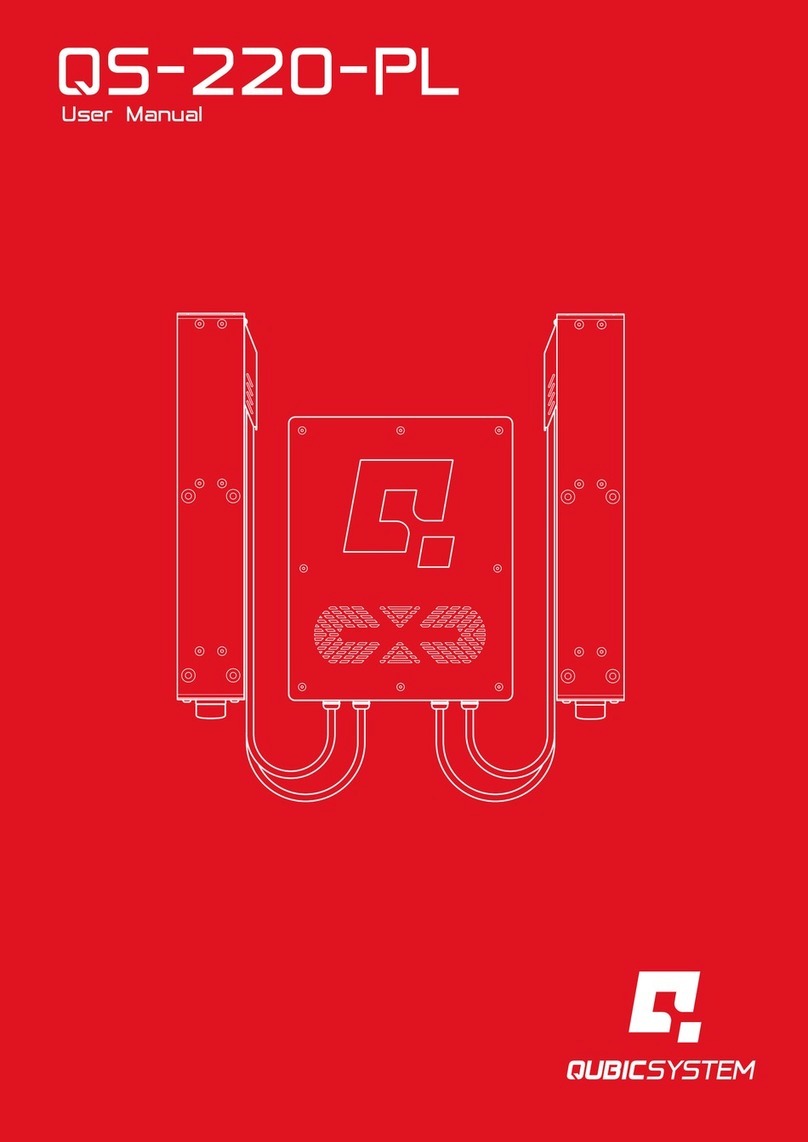
Qubic System
Qubic System QS-220-PL user manual
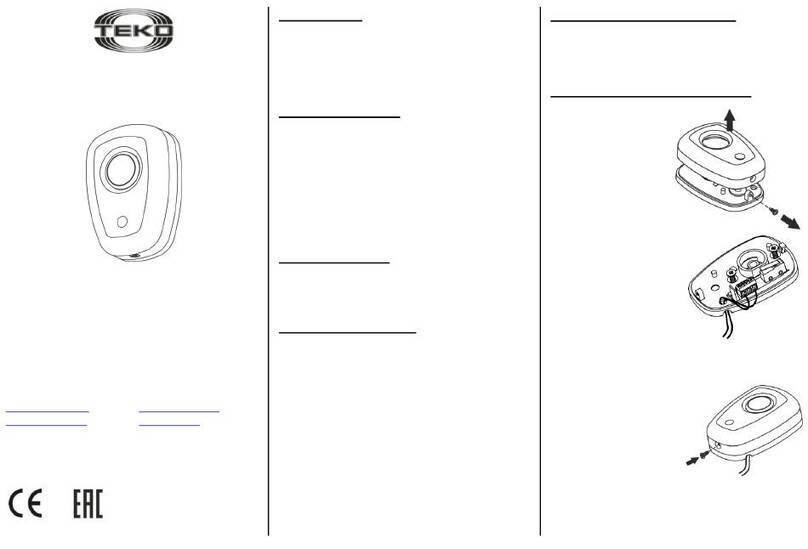
teko
teko Astra-321 M User instruction
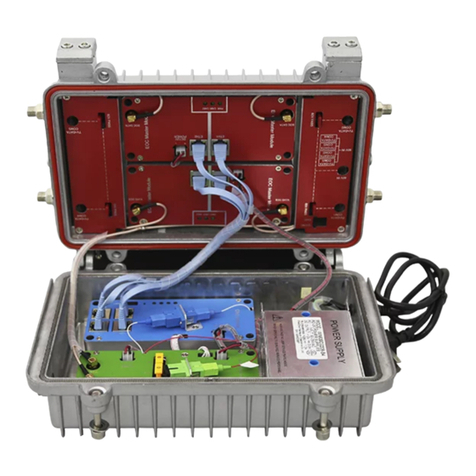
Data
Data EOC Master CD7944N Product user manual
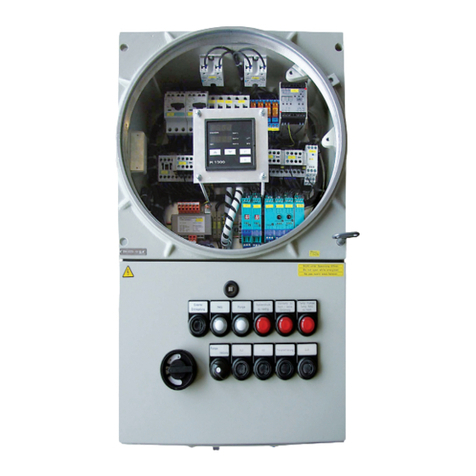
Bartec
Bartec Ex d 07-4 Series operating instructions