Diablo DSP-10 User manual

DSP10_MAN_C 07/27/18 Page 1of 26 Pros Who Know Trust Diablo
User
Manual
DSP-10
Vehicle Detector

DSP-10 User Manual Page 2 of 26 DSP10_MAN_C
1. Contents
Figures ....................................................................................................................................................................3
2. Introduction ...........................................................................................................................................4
3. Technical Data........................................................................................................................................5
Functional Data.......................................................................................................................................................5
Electrical Data.........................................................................................................................................................5
Environmental Data................................................................................................................................................6
Mechanical Data.....................................................................................................................................................6
4. Features and Functions...........................................................................................................................7
Detector Reset........................................................................................................................................................7
Presence Detection.................................................................................................................................................7
Pulse Detection.......................................................................................................................................................7
Fail-Safe vs Fail-Secure ...........................................................................................................................................8
Sensitivity................................................................................................................................................................8
Frequency (DIP Switches 9 and 10) ........................................................................................................................8
Fail Memory (DIP Switch 8) ....................................................................................................................................9
Extended Presence (DIP Switch 7)..........................................................................................................................9
Output B Selection (DIP Switches 5 and 6).............................................................................................................9
Sensitivity Boost (DIP Switch 4) ............................................................................................................................11
Extension (DIP Switches 2 and 3) .........................................................................................................................12
Delay (DIP Switch 1)..............................................................................................................................................12
Indicators..............................................................................................................................................................12
5. Installation ...........................................................................................................................................16
General Rules and Best Practices for Inductive Loops .........................................................................................16
Detector Installation.............................................................................................................................................17
Loop Installation ...................................................................................................................................................18
6. Configuration .......................................................................................................................................22
Wiring ...................................................................................................................................................................22
Internal Settings ...................................................................................................................................................22
7. Troubleshooting ...................................................................................................................................23
No Power LED .......................................................................................................................................................23
Power LED Flashes On Once Every 2 Seconds ......................................................................................................23
Power LED Flashes Slowly (1 Hz) ..........................................................................................................................23
Power LED Flashes Quickly (5 Hz).........................................................................................................................24
Power LED Shows Two Quick Flashes Once Every Two Seconds..........................................................................24
Detect LED Intermittently Comes On / Stays On Without a Vehicle Present.......................................................25
Detect LED Will Not Come On With a Vehicle Present.........................................................................................26

DSP-10 User Manual Page 3 of 26 DSP10_MAN_C
Figures
Figure 1: Product Views..............................................................................................................................................4
Figure 2: Physical Dimensions ....................................................................................................................................6
Figure 3: Outputs with No Delay or Extension ........................................................................................................ 10
Figure 4: Outputs with Delay................................................................................................................................... 10
Figure 5: Outputs with Extension ............................................................................................................................ 11
Figure 6: Outputs with Delay and Extension ........................................................................................................... 11
Figure 7: Power LED States...................................................................................................................................... 14
Figure 8: Detect LED States ..................................................................................................................................... 15
Figure 9: Loop Installation ....................................................................................................................................... 20
Figure 10: Saw Cut for Home Run Exit and Chiseled Corner for Home Run Exit..................................................... 20
Figure 11: Fail-Safe and Fail-Secure Internal Jumpers ............................................................................................ 22

DSP-10 User Manual Page 4 of 26 DSP10_MAN_C
2. Introduction
The DSP-10 Detector is intended to be a top of the line single channel detector. Many features have been
included which are normally found only on more expensive models. The small package is powered by a high-
performance 16-bit microcontroller that does not skimp on performance. The DSP-10 Detector was designed to
retrofit into existing locations that may require a detector upgrade. This allows maintenance personnel to carry
only one detector to meet most, if not all, of their vehicle detection needs.
The detector uses an 11-pin relay socket for connections.
Figure 1: Product Views

DSP-10 User Manual Page 5 of 26 DSP10_MAN_C
3. Technical Data
Functional Data
Sensitivity: Ten sensitivities are user selectable.
Setting
Sensitivity
Setting
Sensitivity
0
.48% ΔL/L
5
.08% ΔL/L
1
.32% ΔL/L
6
.06% ΔL/L
2
.24% ΔL/L
7
.04% ΔL/L
3
.16% ΔL/L
8
.03% ΔL/L
4
.12% ΔL/L
9
.02% ΔL/L
Frequency Settings: There are four frequency settings available. The actual loop frequency is
dependent on loop circuit inductance.
DIP Switch
Frequency
9
10
OFF
OFF
High
OFF
ON
Medium High
ON
OFF
Medium Low
ON
ON
Low
B Pulse Output: 250ms ±15ms.
Response Time: Response time is dependent on the sensitivity selected.
Setting
Response Time
Setting
Response Time
0
70ms ±10ms
5
70
ms ±10ms
1
70ms ±10ms
6
140ms ±20ms
2
70ms ±10ms
7
140ms ±20ms
3
70ms ±10ms
8
140ms ±20ms
4
70ms ±10ms
9
140ms ±20ms
Vehicle Hold Time: In Normal Presence Mode: Approximately 1 hour for a detection of 1% ΔL/L.
In Extended Presence Mode: Approximately 19 hours for a detection of 1% ΔL/L.
Electrical Data
Loop Inductance: 20 microhenries to 1500 microhenries (including lead-in inductance). Not all
frequency settings are available at inductances below 30 microhenries.
Operating Voltages: Three power versions:
10.5 volts to 30 volts AC or DC with over voltage protection
100 volts to 135 volts AC
200 volts to 270 volts AC
Output Relay Rating: 3 amps @ 125 volts

DSP-10 User Manual Page 6 of 26 DSP10_MAN_C
Current Draw: 10.5 volts to 30 volts AC or DC 75 milliamps maximum.
100 volts to 135 volts AC 7.5 milliamps maximum.
200 volts to 270 volts AC 3.75 milliamps maximum.
Environmental Data
Operating Temperature: -35°F to 165°F (-37°C to 74°C)
Storage Temperature: -40°F to 176°F (-40°C to 80°C)
Humidity: Up to 95% relative humidity non-condensing
Mechanical Data
Mounting Position: Any
Housing Material: Lexan
Housing Size: 2.36 inches (High) x 1.75 inches (Wide) x 4.06 inches (Deep)
59.94 mm (High) x 44.45 mm (Wide) x 103.12 mm (Deep)
Figure 2: Physical Dimensions

DSP-10 User Manual Page 7 of 26 DSP10_MAN_C
4. Features and Functions
Detector Reset
When any of the 10-position DIP switches or the 10-position rotary switch is changed, the detector will perform
a detector wide reset. Both LEDs will turn off for 500 milliseconds at the start of the reset event, then on for 500
milliseconds, and then it will indicate if the internal setting is for Fail-Safe or Fail-Secure configuration of the
detector. For Fail-Safe the LEDs will be on for another 500 milliseconds then off for 500 milliseconds before
returning to their normal states. For Fail-Secure the LEDs will flash at 50 milliseconds on and 50 milliseconds off
rate for another 1000 milliseconds before returning to their normal states. The detector will not output any
detections during this two second reset period. If a prior loop fault is being displayed it will be cleared. If a
vehicle is over the loop during the reset period it will not be detected.
Presence Detection
The A output will always operate in the presence detection mode. The Delay and Extend features may modify
the output behavior. Once activated, the output will remain activated as long as a vehicle is detected over the
loop. After four minutes of continuous detection, the detector will begin to slowly retune the detector with the
goal of tuning out the vehicle that stalled or parked on the loop over a relatively long time. The retuning process
takes about an hour to complete in the Normal Presence mode and about 19 hours in the Extended Presence
mode with a vehicle detection of 1% ΔL/L. When the retuning process is complete, any loop area that vehicles
can still travel over will still detect the vehicle as expected. Once the vehicle leaves, the detector will recover
from the retuning process within 1 second.
The B output can be set to operate in the True Presence mode. In this mode the B output activates as soon as a
vehicle enters the loop and drops as soon as the loop is no longer occupied. The output will ignore any Delay or
Extend features that are currently active.
Pulse Detection
The B output can be configured for Pulse on Entry or Pulse on Exit operation. The pulse generated by the output
will be 250 milliseconds long. The B output will follow any Delay or Extend features that are currently active.
Pulse operation is not available on the A output.
In Pulse on Entry mode, the B output will pulse when the A output activates. If the delay feature is enabled, the
pulse will not occur until the delay has timed out and the loop is still occupied. The output will not pulse again
until the loop has been unoccupied and any enabled extension has timed out.
In Pulse on Exit mode, the B output will pulse when the A output deactivates. If one of the extension features is
enabled, the pulse will not occur until the extension has timed out and the loop is still vacant. The output will
not pulse again until the loop has been reoccupied and any enabled delay has timed out.

DSP-10 User Manual Page 8 of 26 DSP10_MAN_C
Fail-Safe vs Fail-Secure
Here’s a little note on fail-safe versus fail-secure operation. On the DSP-10, the option for fail-safe or fail-secure
only applies to the A output. In general, a fail-safe detector will activate the output when the loop circuit is
failed. This is useful on a safety loop to prevent accidental closure of a gate arm on a vehicle. On the free exit
loop this will keep the gate open until the situation is fixed. Fail-safe is used in applications where it is important
to allow traffic flow to continue. A fail-secure detector will not activate the output when the loop circuit is
failed. This will keep the gate closed. This is useful in high-security areas or installations where containment is
needed.
The B output is always fail-secure when not in the fail output mode.
The DSP-10 is one of the few vehicle detectors that honors fail-safe and fail-secure even in the absence of
power. Inside the unit, on the main PC board, are three jumpers that set the failure mode. When placed in the
fail-safe position, the A output relay will be fail-safe in the absence of adequate voltage. If placed in the fail-
secure position, the reverse is true. The jumpers are factory set to be fail-safe. All three jumpers must be set to
the same setting. Not doing this will cause incorrect operation of the A output.
Sensitivity
The detector has ten user selectable sensitivity levels. In most situations the medium sensitivity 5 setting will
work effectively. For those situations where setting 5 is not sensitive enough, raise the sensitivity one level at a
time until the desired performance is obtained. For those situations where the detector is oversensitive, lower
the sensitivity one level at a time until the desired performance is obtained. The sensitivity is factory set to 5.
Like most inductive loop vehicle detectors, the DSP-10 directly measures the change in frequency of the loop
and from there, calculates the change in inductance when a vehicle interacts with it. The change in inductance
is measured as %ΔL/L (reads as “percent delta L over L”).
For the ten sensitivities, the thresholds are:
Setting
Sensitivit
y
Setting
Sensitivity
0
.48% ΔL/L
5
.08% ΔL/L
1
.32% ΔL/L
6
.06% ΔL/L
2
.24% ΔL/L
7
.04% ΔL/L
3
.16% ΔL/L
8
.03% ΔL/L
4
.12% ΔL/L
9
.02% ΔL/L
Frequency (DIP Switches 9 and 10)
Another important variable is loop frequency. When loops are installed sufficiently far apart, any two loops will
not interfere with each other. However, if two loops are fairly close together, say two to four feet apart, the
inductive fields may couple together and may interact causing intermittent false detections. The two main
variables for inductive coupling are distance and frequency separation. To aid in avoiding inductive coupling,
each DSP-10 unit comes with two frequency switches. They are binary coded allowing up to four different

DSP-10 User Manual Page 9 of 26 DSP10_MAN_C
frequencies to operate within. If there are suspicions that one of the two loops are interacting, simply change
one of the two unit’s frequency settings.
DIP Switch
Frequency
9
10
OFF
OFF
High
OFF
ON
Medium High
ON
OFF
Medium Low
ON
ON
Low
Fail Memory (DIP Switch 8)
Normal operation is that during a loop failure, the green Power LED will indicate what type of loop failure (open,
short, or large ΔL/L). During the loop failure the red Detect LED and output A will be active for fail-safe
operation or inactive for fail-secure operation. If the loop recovers from its failure, the red and green LEDs,
along with its two relay outputs, will operate normally again. However, when Fail Memory is enabled, the green
LED will continue to indicate a previous failure by blinking 1850 milliseconds on, 50 milliseconds off, 50
milliseconds on again, and then 50 milliseconds off. This blinking sequence will repeat until a reset or power
cycle occurs. Note that the red LED and relay outputs will continue to work normally.
Extended Presence (DIP Switch 7)
Under normal conditions, the DSP-10 will hold a vehicle presence for a reasonable amount of time. If a vehicle
parks over the loop and the detector measures a 1% ΔL/L, it will slowly tune that vehicle out over a period of
about one hour. For those instances where a longer period is desired, extended presence will hold that same
vehicle for about 19 or 20 hours. This is quite a long time, but it isn’t infinite. The DSP-10 does not have infinite
presence.
Output B Selection (DIP Switches 5 and 6)
Output B can be programmed to operate in one of four different modes that are selected using DIP switches 5
and 6. The following table identifies these four modes:
DIP Switch
Output B Mode
of Operation
5
6
OFF
OFF
True Presence
OFF
ON
Pulse
o
n Entry
ON
OFF
Pulse
o
n Exit
ON
ON
Fail
True Presence: The B output will be energized whenever a vehicle is present over the loop detection area. The
A output can be modified by the delay and/or extension timing settings. The B output will not use these timing
settings. For example, if 2 seconds of delay is set, output B will energize as soon as the vehicle is detected, while
output A will wait for two seconds of continuous presence prior to energizing.
Pulse on Entry: Every time the loop is occupied, a single 250 milliseconds pulse will be output on the B output.

DSP-10 User Manual Page 10 of 26 DSP10_MAN_C
Pulse on Exit: Every time the loop becomes vacant or a vehicle is tuned out, a single 250 milliseconds pulse will
be output on the B output.
Fail: If the DSP-10 recognizes some type of loop failure, a continuous output on the B output will be given. The B
output will remain activated until the failure is corrected.
The following figures show the effects of delay and extension on the A & B outputs. The numbers between
edges are the number of seconds in that period.
Figure 3: Outputs with No Delay or Extension
Figure 4: Outputs with Delay

DSP-10 User Manual Page 11 of 26 DSP10_MAN_C
Figure 5: Outputs with Extension
Figure 6: Outputs with Delay and Extension
Sensitivity Boost (DIP Switch 4)
The detector has a user selectable feature that increases the sensitivity of a channel after initial detection. This
feature is most often used to allow a detector to have a lower starting sensitivity and then increase it after a
vehicle has been detected. This is useful in situations where high-bed tractor-trailer vehicles will be passing over
the loop. With this feature the detector may be able to detect the high-bed portion of the vehicle without
having to be overly sensitive and susceptible to false detections. NOTE: If detection of high-bed tractor-trailers
is required, correctly sized loops must be used.

DSP-10 User Manual Page 12 of 26 DSP10_MAN_C
Extension (DIP Switches 2 and 3)
Extension is the time added after a vehicle leaves the detection area. During this interval, the A output will
remain activated, with the intent of allowing the vehicle to fully exit the detection area before the gate begins to
close. If another vehicle arrives during this extension interval, the remainder of the extension time is canceled
and the detector returns to the normal presence state. This interval is indicated by the red Detect LED blinking
fast at 50 milliseconds on followed by 50 milliseconds off repeated until the interval is complete. There are four
intervals to choose from: No extension, 2 seconds of extension, 5 seconds of extension, and 10 seconds of
extension. The choices are summarized in the table below.
DIP Switch
Output A
Extension Time
2
3
OFF
OFF
0 seconds
O
N
O
FF
2 seconds
O
FF
ON
5 seconds
ON
ON
10 seconds
Delay (DIP Switch 1)
Delay is the time added after a vehicle arrives in the detection area but before the A output is activated. During
the delay interval the A output relay will remain de-activated, requiring that the vehicle stay in the detection
area for a full 2 seconds before activating the A output. This is useful at sites where vehicles traveling
perpendicular to the gate may travel across the detection zone. This interval is indicated by the red Detect LED
blinking slowly at 200 milliseconds on followed by 200 milliseconds off repeatedly until the interval is complete.
The delay interval is fixed at 2 seconds.
Indicators
The DSP-10 is equipped with two LED indicators: Power (Green) and Detect (Red).
Power LED – The green power LED indicates these possible states:
Off The voltage applied to the detector is less than the minimum display
voltage of approximately 7.75 volts. The LED will be off.
Low Voltage The voltage applied to the detector is less than the minimum voltage for
proper operation of approximately 10.25 volts. The LED will blink on for
50 milliseconds once every 2 seconds.
Reset in Fail-safe At the start of a reset event (a DIP switch change, sensitivity change, or
power cycle) the LED will turn off for 500 milliseconds, on for 500
milliseconds, off for 500 milliseconds, off for 500 milliseconds, and then
display its normal state.
Reset in Fail-secure At the start of a reset event (a DIP switch change, sensitivity change, or
power cycle) the LED will turn off for 500 milliseconds, on for 500

DSP-10 User Manual Page 13 of 26 DSP10_MAN_C
milliseconds, blink repeatedly with 50 milliseconds on followed by 50
milliseconds off for one second, and then display its normal state.
Open Loop When the detector senses that the loop is open or the inductance is too
high, the LED will turn on for 500 milliseconds then off for 500
milliseconds repeatedly, for the duration of the fault.
If the fault is corrected and the Fail Memory feature is enabled, the LED
will display the Prior Fault indication.
Shorted Loop When the detector senses that a loop is shorted or the inductance is too
low, the LED will turn on for 100 milliseconds then off for 100
milliseconds repeatedly, for the duration of the fault.
If the fault is corrected and the Fail Memory feature is enabled, the LED
will display the Prior Fault indication.
Large Change Fault When the detector senses that a loop is experiencing a large inductance
change (greater than 30%), the LED will turn off for 100 milliseconds
then on for 100 milliseconds for 500 milliseconds then stay on for 500
milliseconds and repeat the sequence for the duration of the fault.
If the fault is corrected and the Fail Memory feature is enabled, the LED
will display the Prior Fault indication.
Prior Fault The detector is equipped with the ability to remember prior faults that
have occurred since the last power interruption or reset (changing a DIP
switch or the sensitivity). The LED will turn on for 1850 milliseconds, off
for 50 milliseconds, on for 50 milliseconds, off for 50 milliseconds and
then repeat the sequence until power is cycled or the detector reset.
Normal The LED is always on when the detector is in its normal state of
operation.

DSP-10 User Manual Page 14 of 26 DSP10_MAN_C
Figure 7: Power LED States
Detect LED – The red detect LED is used to display the status of the A output. There are several
different statuses that can be displayed on this LED:
Off No vehicle present in the detection area.
Reset in Fail-safe At the start of a reset event (a DIP switch change, sensitivity change, or
power cycle) the LED will turn off for 500 milliseconds, on for 500
milliseconds, off for 500 milliseconds, on for 500 milliseconds, and then
finally display its normal state.
Reset in Fail-secure At the start of a reset event (a DIP switch change, sensitivity change, or
power cycle) the LED will turn off for 500 milliseconds, on for 500
milliseconds, blink repeatedly with 50 milliseconds on followed by 50
milliseconds off for one second, and then display its normal state.
Delay Interval A vehicle has been detected but the A output is not activated due to the
2 second delay feature being active. The LED will turn on for 200
milliseconds and then off for two hundred milliseconds. If the vehicle
leaves the detection area before the two second delay interval expires,
the LED will return to the off state. If the vehicle is still present after 2
seconds, the LED will become solid and the A output will be activated.

DSP-10 User Manual Page 15 of 26 DSP10_MAN_C
Extension Interval A vehicle was detected but the detection zone is now empty and an
extension interval is being timed. The extension interval can be
programmed for no extension, 2 seconds, 5 seconds, or 10 seconds.
When the detection area becomes vacant, the extension timer will start
and the A output will continue to be activated. During this interval, the
LED will blink quickly at 50 milliseconds on and 50 milliseconds off. If
another vehicle enters the detection area during this interval, the
extension time is cancelled and the LED will return to the solid state.
Note: There is no delay interval for any newly arriving vehicle if a vehicle
is already in the detection area or the detector is in the extension
interval.
Detect The LED will be on solid when a vehicle is being detected and the delay
interval (if activated) has finished timing.
Figure 8: Detect LED States

DSP-10 User Manual Page 16 of 26 DSP10_MAN_C
5. Installation
General Rules and Best Practices for Inductive Loops
Before beginning the installation, it is important to make that the loop you are about to use is appropriate for
this installation. Here are some general rules and best practices that will help you ensure that the loop you use
will have the desired performance and a long life.
1. The preferred insulation material for loop wire is cross-linked polyethylene (XHHN or XHHW are types of
this wire). Wire with PVC insulation should never be used. This includes THHN. The cross-linked
polyethylene is a much more durable insulation and, more importantly, has a much lower moisture
absorption rate. Moisture absorption can affect loop stability.
2. Wire gauge of the loop wire has little to no impact on the sensitivity of the loop. A larger wire gauge
may help extend the life of the loop, especially in asphalt installations where heavy truck traffic is
expected.
3. Wire nuts should never be used in loop connections. At a minimum wire to wire connections should be
crimped or use a screw terminal. Ideally, solder the connections.
4. Loop saw cuts should be mitered to reduce the loop wire bend angle to not exceed 45 degrees at any
location.
5. Use backer rod to hold the loop wire at the bottom of the saw cut before sealing the loop. The backer
rod should be cut into 1-inch pieces and one placed every foot or so, as needed.
6. If a loop installation will cross an expansion joint in the roadway surface some method of leaving some
slack wire at the joint should be implemented. This can be done by core drilling a 1” or larger hole
where the saw cut crosses the expansion joint and leaving a loop of wire in the hole each time you go
through it when installing the loop wire. The other option is to dip the saw at the expansion joint to
make the saw slot at least two inches deeper at the joint. Then when installing the loop wire, ensure
that the wire lays all the way at the bottom of the saw slot at the expansion joint.
7. Useable detection height of a loop is 2/3rds of the shortest leg of the loop. Therefore, if you need to
detect semi-truck trailers, no side of the loop can be shorter than 6’.
8. The approximate inductance of the loops can be calculated using the formula:
L = (P / 4) x (N + N2)
Where: L = Loop Inductance in microhenries (µH)
P = Perimeter of the loop in feet
N = Number of turns (wraps) in the loop
For example, a 6’ by 14’ loop with 2 turns would be:
L = ( (6 + 14 + 6 + 14) / 4) x (2 + 22)
L = (40 / 4) x (2 + 4)
L = 10 x 6
Loop Inductance is approximately 60µH.

DSP-10 User Manual Page 17 of 26 DSP10_MAN_C
9. The approximate inductance of the lead-in cable can be calculated using a value of .22 µH per foot for
lead-in cable.
100’ x .22 µH = 22 µH of inductance in 100’ of lead-in cable.
10. The ratio of loop inductance to lead-in inductance should be 2 to 1 for a well-designed installation.
Since the vehicle to be detected can only influence the loop inductance, letting the lead-in inductance
get close to the loop inductance will effectively lower the sensitivity of the loop. This is usually only an
issue when the loop is 50’ or more away from the detector. If you do have a long lead-in, additional
turns should be added to the loop until the 2 to 1 ratio is satisfied.
11. The ideal loop inductance is 50 to 500 µH. Although the detector will tune to loops in the range of 20 to
1000 µH, the 20 to 50 range should be avoided to provide a more stable loop and loss of sensitivity due
to lead-in inductance. It is always better to have too much inductance than too little.
12. Lead-in wires must be twisted. Ideally, 3 to 6 twists per foot should be maintained. It is also important
that the twists are tight. An air gap between the two wires should not exist as this can cause loop
stability issues. The lead-in wires should be kept twisted until right before connection to the detector.
13. A figure 8 loop can be used in locations where electrical interference is expected or seen. This is a
standard loop with an extra saw cut down the middle of the loop. This extra saw cut should point
toward the source of the interference as much as practical. If the source is overhead or below ground
(power lines) the saw cut should be parallel to the short side of the loop. The loop wire is placed in the
saw cuts using a figure 8 motion. A figure 8 loop will have more inductance that a similar sized
conventional loop.
14. If multiple loops are to be connected to the same detector there are several things to be aware of:
a. Always connect multiple loops in series. This increases the inductance and insures that a loop
failure will cause a loop fault at the detector.
b. The loops connected together must be the same size and the same number of turns. Failure to
do this will lead to the loops having different sensitivities that cannot be compensated for. This
difference in sensitivity can very large.
c. Connecting two loops together will reduce the sensitivity of each loop by half.
d. If the two loops are within 6’ of each other, the phasing of the loops should be considered. If
the loops are on the same side of a gate and are being used to increase the size of the detection
zone, the two edges closest to each other should have opposite phasing (North to South). This
will increase the sensitivity in the area between the two loops. If the loops are on opposite
sides of a gate, the loops should have the same phasing (North to North). This will decrease the
sensitivity in the area between the two loops. Especially at the middle point between the two
loops, it may be impossible to detect any object in this area. So, this phenomenon can be very
useful in sliding gate and lift gate installations.
Detector Installation
Location: The detector should be plugged in to the appropriate connector on the DoorKing operator.
Mounting: The detector will function when mounted in any orientation. Using the two holes in the detector,
secure the detector in place.

DSP-10 User Manual Page 18 of 26 DSP10_MAN_C
Wiring: Attach the loops to the appropriate loop screw terminals. Wire nuts should never be used at any point
in the loop circuit itself. All loop connections should be crimped or use screw terminals at a minimum and
soldered for best long-term reliability. Special attention should be paid to ensure that the loop wires remain
tightly twisted together. An air gap between the two wires for a loop may cause the detector to lock up if the
wires are disturbed.
If connecting two loops to one channel of a detector, there are certain rules you should follow:
1. Always connect multiple loops in series, not parallel. A failure of one loop may not be identified if the
loops are connected in parallel.
2. The loops should be the same size, shape, and have the same number of turns. If any of these items are
different, the loops will have different sensitivities that cannot be adjusted for. The difference in
sensitivity could be very significant.
3. Do not use a wire nut to connect the wire from each loop together. Wire nuts have a spring in them and
will expand and contract with temperature. Even the slightest change in resistance can cause detector
lock-ups.
Loop Installation
The reliability and overall performance of the detector are greatly dependent on the loop itself. Several factors
go into a good loop installation: type of wire used, loop configuration, and installation practices.
Type of Wire Used: The wire used for wiring the loop should have a jacket of cross-linked polyethylene or
similar material that has very low moisture absorption properties. This would be a wire with an XLP jacket such
as XHHW. THHN or similar wire types should never be used for loop wire.
The gauge of the wire to use depends on two factors: Distance in cable feet from the loop to the detector and
stresses the wire may see. The gauge of the wire can be 20 AWG as long as the detector is within 50 feet of the
loop in cable distance. For 50 to 100 feet, use at least 18 AWG wire. At greater than 100 feet, use a 16 AWG
wire at a minimum. If the loop is installed in asphalt and there will be heavy vehicles or stopping and starting
vehicles in the loop area, a 14 AWG or 12 AWG should be used to provide additional strength to the loop. This
helps increase the life of the loop in areas where the asphalt may slowly move and/or deform due to wear
and/or temperature.
Loop Configuration: The size and shape of the loop will determine what type of vehicles it can reliably detect.
There are many variables that come into play including loop dimensions, percent of coverage, length of lead-in
wire, number of turns in the loop area, and detection height to name just a few of them. One common rule is
that the useable field height of a loop is 2/3 of the shortest leg of the loop. So, if you plan on using a 2.5’ x 6’
loop, the expected useable detection height would be 20” (The shortest leg is 2.5’ or 30”, 30” x 2 = 60”, 60” / 3 =
20”). If the installation requires the detection of motorcycles as well as vehicles, the loop should go to within
one foot of the curb or roadway edge, whichever is present. If only motor vehicle detection is required, within
three feet of the curb or roadway edge is all that is required.
The number of turns to use in a loop is dependent on the size of the loop and length of the lead-in. Rather than
dive into all of the calculations to arrive at a value, we will just give you a table of safe values based on the

DSP-10 User Manual Page 19 of 26 DSP10_MAN_C
number of square feet in the loop (length times width in feet). If you are unsure about your particular
installation, call tech support for guidance.
Loop Size in Square Feet
Recommended
Turns
for <100’ of Lead-in
Recommended
Turns for
100’ to 199’ of Lead-in
Recommended
Turns for
200’ to 299’ of Lead-in
5
to
6
square feet
7
8
10
7 to 9 square feet
6
7
9
1
0
to
1
5
square feet
5
6
8
1
6
to
23
square feet
4
5
6
24
to
5
4
square feet
3
4
5
5
5
to
1
50 square feet
2
3
3
Installation Practices: Permanent loops should be installed into the road surface by cutting slots into the road
surface using a saw with an appropriate cutting disk for the road surface.
The slot cut should be wide enough that the wire being used will easily fit into the slot. This is needed so that
the loop sealant used can fully encapsulate the wire. When the wire fits tightly in the slot, the sealant may not
be able to get below the wire, leaving air pockets in the saw slot. If water finds its way in to these air pockets,
over time, freeze thaw cycles can slowly jack the loop out of the saw slot causing loop failure.
The saw slot should be deep enough that the loop wire will have a minimum of ½” of sealant over the top wire
in the slot. More is better. Going too deep with the saw cut is also a concern. Deep cuts in a road surface may
impact the structural strength of the roadway, especially if any reinforcement material is cut. Using a smaller
gauge of wire will allow for shallower saw cuts.
The corners of the loop should be crosscut at a 45°to help prevent damage to the wire insulation during
installation and temperature cycling. The angled cuts should be at least 9” back from where the corner would
be. The saw cuts should not go any further than necessary to ensure that the saw slots are at full depth where
they meet.
Special consideration should be given to where the home run saw cut meets the loop saw cuts. Here either an
additional saw cut should be made as shown in Detail A or the inside of the sharp corner should be removed
with a chisel as shown in Detail B.
Once the saw slot has been cut, the slot should be cleaned of all loose material. High-pressure air should be
directed in to the saw slot to remove all debris. This will also help remove dust from the saw cutting operation
from the sides of the saw slot. This will allow better adhesion of the loop sealant to the saw slot.

DSP-10 User Manual Page 20 of 26 DSP10_MAN_C
Figure 9: Loop Installation
Figure 10: Saw Cut for Home Run Exit and Chiseled Corner for Home Run Exit
BACKER ROD
LOOP WIRE
SAW
DETAIL A
DETAIL B
This manual suits for next models
3
Table of contents
Other Diablo Security Sensor manuals
Popular Security Sensor manuals by other brands
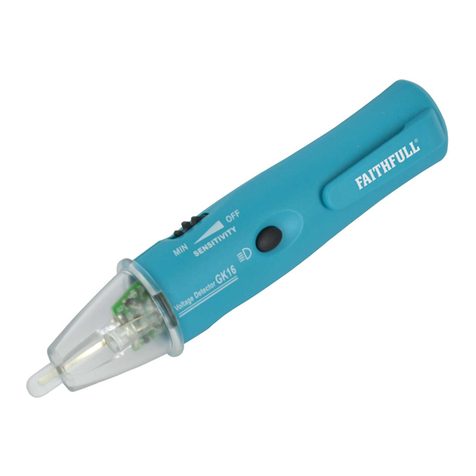
Faithfull
Faithfull FAIDETVOLT2 instructions
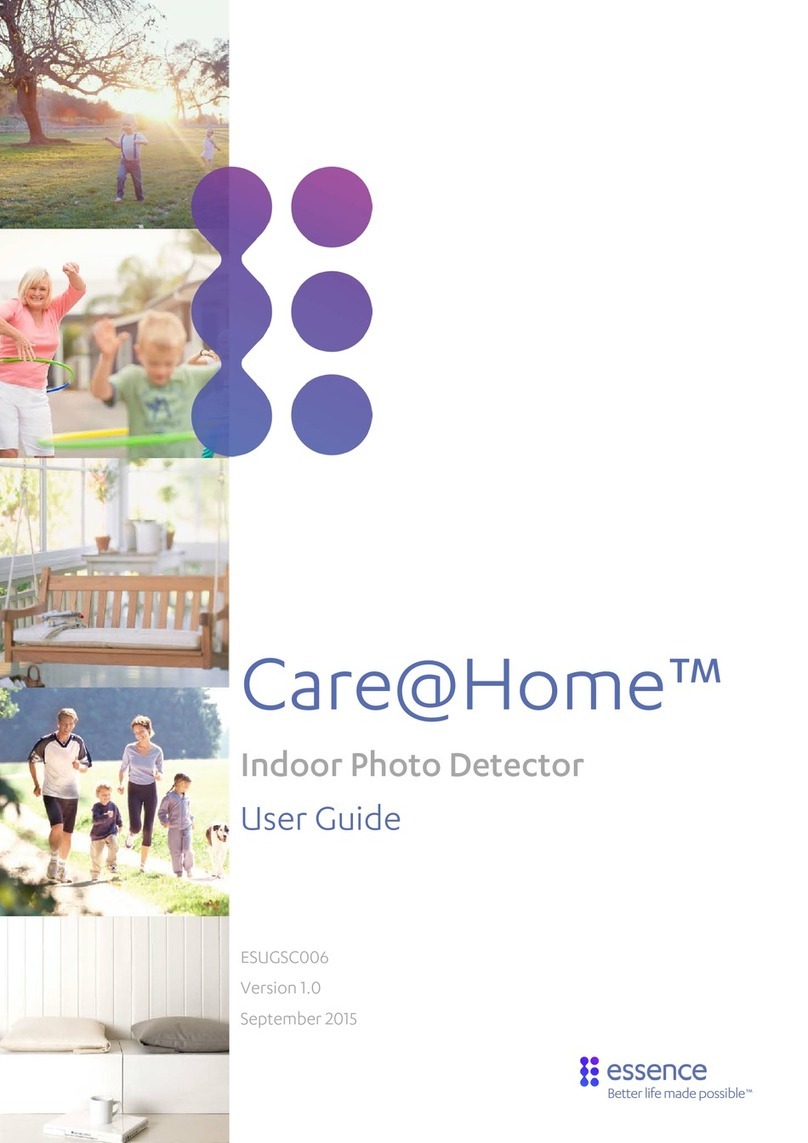
Essence Smartcare
Essence Smartcare Care@Home ES700IPD user guide
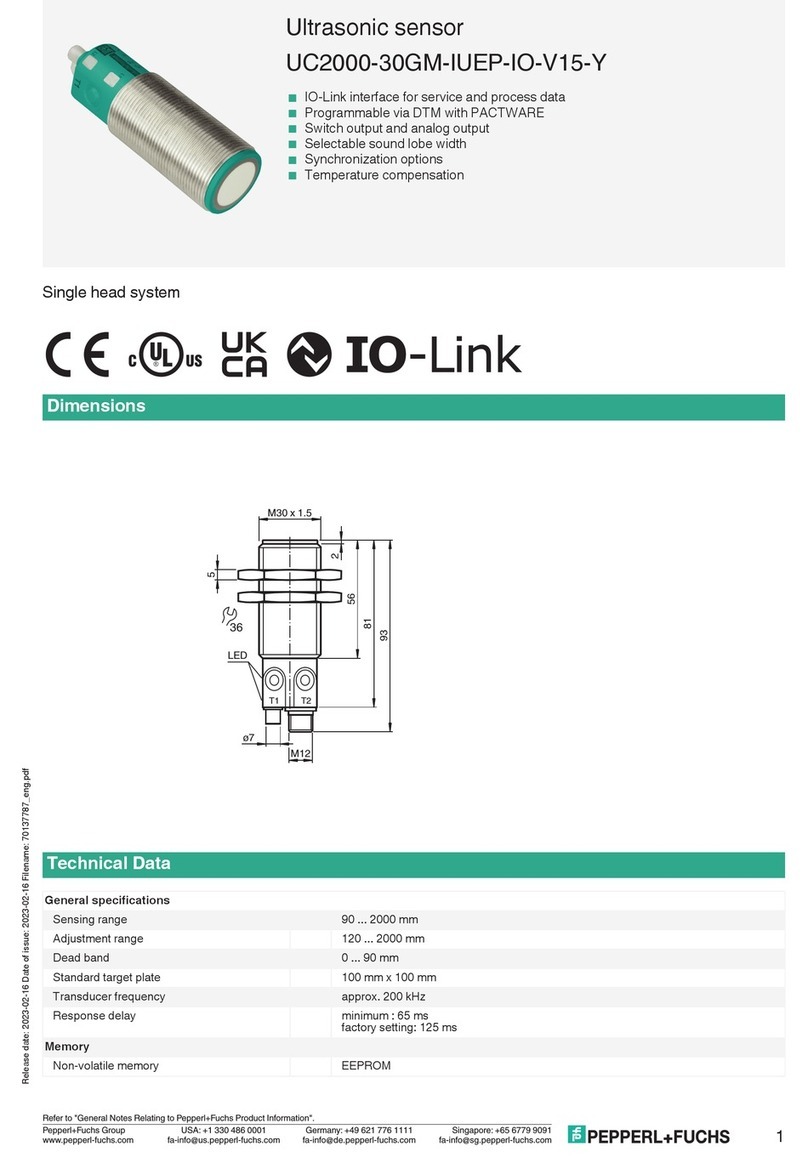
Pepperl+Fuchs
Pepperl+Fuchs UC2000-30GM-IUEP-IO-V15-Y manual
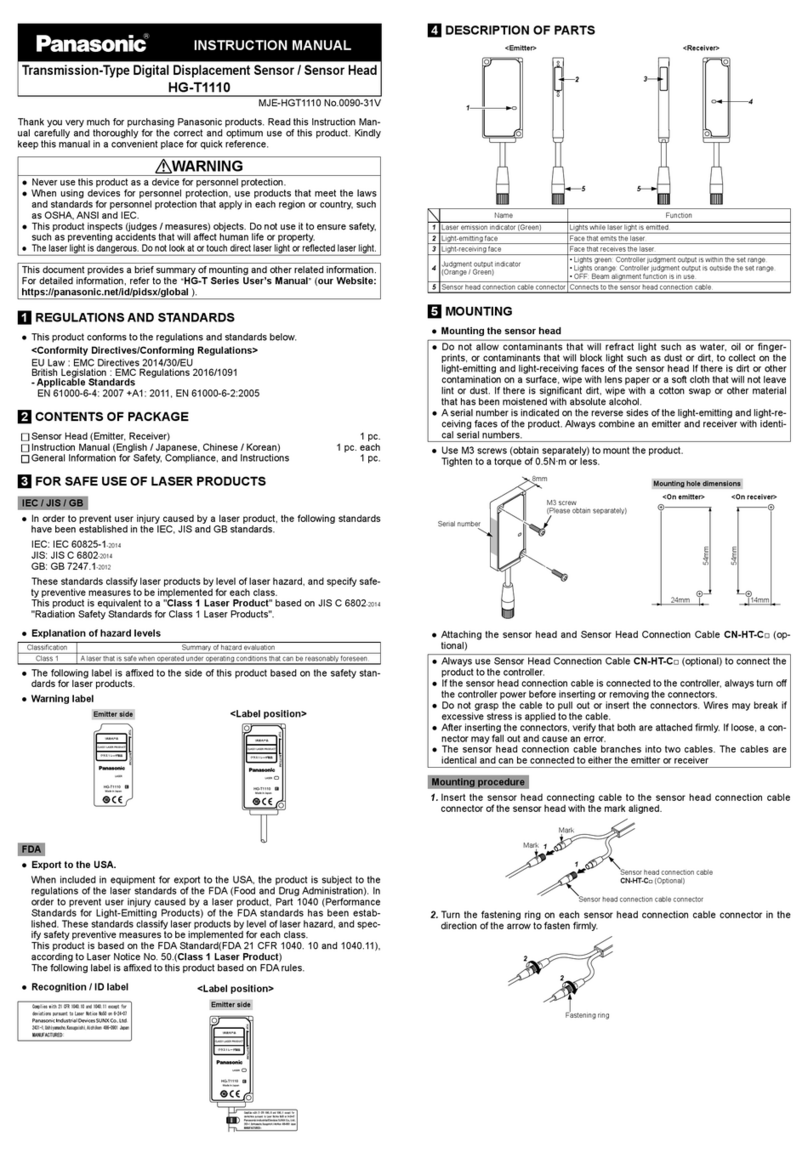
Panasonic
Panasonic HG-T1110 instruction manual

Ilmvac
Ilmvac biovac 106 Operation manual
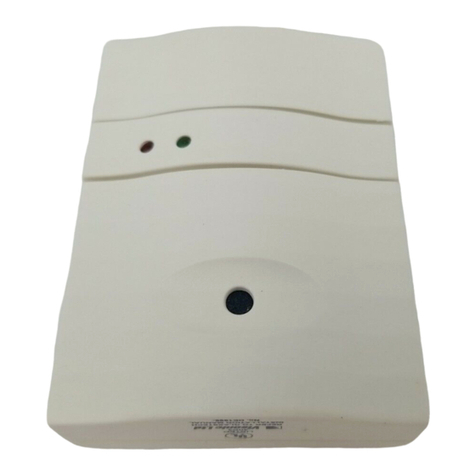
Visonic
Visonic GLASSTECH installation instructions