DIGIWAY PTY SW50-2S User manual

- 1 -
SW50-2 Dual Swing Gate Motor
INSTRUCTION MANUAL
DIGIWAY PTY LTD

- 2 -
Electricity and power motors associated accessories could be fatal or at
least cause seriously injury. Digiway suggested some safety device to be
used so as to prevent personnel from being injured by motorized device
being controlled. All main voltage wiring must be installed by a licensed
electrician.
Recommended install PE beams or loop detectors for additional
safety.
Do not operate gate unless gate is in full view and free from objects.
Remote control must be kept away from children.
IMPORTANT SAFETY WARNING

- 3 -

- 4 -
1. General Descriptions and features
1.1 General descriptions
It is recommended reading and understanding this manual before start to install the control board.
Some features and idea are new. So, take some time to read through the manual to get better
understanding of the board. That will save your time during installation and get the best benefit
from the control board.
1.2 General features
SW50 is designed for most of domestic swing gate. It can be mounted on brick wall/pier or steel
post. The arm supplied can be met most of application situations. If special need, customer can
modify arm or ask supplier/dealer to contact manufacturer for different arm.
Before installation must check:
A) Gate moves freely by hand without any difficulty in either open and closing directions.
B) The post or pier must be strong enough.
C) Gate must have open and closed stopper
D) 240V 10A power point must be available within one metre of the post/pier
E) If there is not enough side room, minimum side room requirement see following drawing.
2. Motor installation
Two arms are the exactly same. For different gate or different application, can cut the arm to the
required length to suit the gate.
MAIN FEATURES

- 5 -
Standard installation for brick post
Gate Swing in
GATE MOTOR MOUNTING
Opened position
Opened position
Closed Position
Closed Position

- 6 -
Gate swing in
Opened position
Opened position
Closed Position
Closed Position

- 7 -
Brick Post, Gate Swing Out
Steel Post, swing out application
Opened position
Closed Position
Closed Position
Opened position

- 8 -
Steel Post, small side room, swing in with special parts
Special limited side room, cut the arm to suit the application
Closed Position
Opened position
Opened position

- 9 -
1 2 3 4 5
1) Anticlockwise push handle. 2) push handle to the position. 3) Push motor up and left
direction. NOW GATE IS FREE TO MOVE. 4) Push motor down and right direction.
Make sure gears engaged. 5) push manual release handle clockwise and clock the gear.
Manual Release

- 10 -
3. Control board
The SW50-2 swing gate motor controlled by DC2 control board, which has following features:
•Control one or two 12 or 24V DC motors. For Swing gates, Sliding Gates, Roller shutter
doors etc.
•Limit switch inputs, N/C or N/O
•Lock or lights relay output.
•Adjustable timers: auto close time and PE trig auto close time.
•Pedestrian cycle
•Safety control inputs.
•Self-learn soft start and soft stop.
View of Control board
Fig. 9 DC2 PCB
1
2
1
4
3
5
6
8
9
12
13
14
15
10
11
7
GATE MOTOR CONTROLLER

- 11 -
1. OPN open push button
2. CLS close push button
3. PED pedestrian open push button
4. OSC Open, Stop, Close push button
5. Gate status display, open green, close red
6. Mode selection DIP switch
7. Close motor force (reverse power)
8. Control inputs terminals.
9. Limit switch input
10. Lock output relay
11. M1 output
12. M2 output
13. Accessories power 14VDC or 26VDC depending the transformer voltage
14. Battery terminals
15. Power supply 12 V or 24V AC.
3.1 Control inputs
GATE MOTOR CONTROLLER

- 12 -
DC2 PCB dimensions and mounting holes
Control Terminals
OPN ----- N/O open input.
PED ------ N/O pedestrian open push button, only open motor-1
PEB ------ N/C photo electrical beams
OSC------ N/O Open –Stop –Close--Open
OL1 ------ Motor 1 open limit switch, N/C or N/O selected by DIP4
CL1 ------ Motor 1 close limit switch, N/C or N/O selected by DIP4
OL2 ------ Motor 2 open limit switch, N/C or N/O selected by DIP4
CL2 ------ Motor 2 close limit switch, N/C or N/O selected by DIP4
Buttons
OPN button ---- Full (M1&M2) open gate and used for settings
PED button ----- Ped (M1) open gate and used for settings
CLS button ----- CLS gate and used for settings
OSC button ----- Open –Stop –Close—Open and for setting
3.2 DIP Switch Settings
DIP1---- SET ON—set, OFF –Run
DIP2---- SYNC ON—SYNC mode, OFF –No Sync mode
DIP3---- DIP3 Spare for V4.2 and before
DIP4---- CODE ON—Encoder control M1 only, OFF –limit control
DIP5---- LKPS ON—Lock Pulse Output, OFF –Lock Presence Output
DIP6---- NOLS ON—N/O limit switch, OFF –N/C limit switch
DIP7---- PECL ON—PE trig Auto Close, OFF –No PE trig Auto close
DIP8---- AUCL ON—Auto Close Mode, OFF –No Auto close
3.3 Motor Force
If any motor current over current setting, both motors will stop in opening cycle or reopen in
closing.
If gate(motor) already in low-speed section and nearly closed or opened, controller will not
response the overload
3.4 Power input
12 or 24V AC power input. 12VAC for 12VDC motor, 24VAC for 24V DC motor
3.5 Battery Backup
12V battery --- 12VDC motor, 12VAC input.
24V battery --- 24VDC motor, 24VAC input.
Solar regulator output can be direct connected to this terminal if in case of solar application.
3.6 Motor output
M1: Motor 1 output. M2: Motor 2 output
3.7 Power output
Power out for accessaries. About 14V----- 12VAC supply, about 26V------24VAC supply
3.8 Timers setting
Push Buttons functions
Button
SET ON---Setting
SET OFF---Running
Note
OPN
Sync Delay Time
Open gate
PED
Lock Pulse Time
Lock pulse Time
CLS
PE Trig Close Time
PE Trig Close Time
CONTROLLER SETTINGS

- 13 -
STP
Auto Close Time
Auto Close Time
Set time settings
Turn SET on, red and green LED flashes a little fast alternatively.
Push and hold on OPN for Sync Delay Time
Push and hold on PED for Lock Pulse Time
Push and hold on CLS for PE Trig Close Time
Push and hold on STP for Auto Close Time
Factory setting
Timer
F/Setting
Step
Setting Method
Range
Sync Delay Time
2 sec.
0.1 sec.
SET on + OPN Button
0-25 sec.
Lock Pulse Time
2 sec.
0.1 sec.
SET on +PED Button
0-25 sec.
PE Auto close Time
2 sec.
0.1 sec
SEC on + CLS Button
0-25 sec
Auto Close Time
30 sec.
0.1 sec.
SET on + PRO Button
0-6553 sec
To restore factory setting, turn power off and set DIP1 (SET) on, push and hold
CLS button, then power on. While hold CLS button, set SET1 off and then release
the CLS button. Now controller restored factory setting from memory.
Special settings
To get into Special Setting: Turn power off and set DIP1 (SET) on, push and hold CLS button, then
power on. then release the CLS button. Now controller get into special setting mode
DIP1 On + Special setting.
OPN button---Motor Close Delay Time (Default same to Open Delay Time)
PED button---Spare, CLS button---Spare
OSC button---Spare
Then turn DIP1 off, setting finished
Special setting at the moment only uses OPN bottom to set Close Delay Time. Sometimes Motor
Close Delay Time need to be different to Motor Open Delay Time. Reset Motor Open Delay
Time will reset Motor Close Delay Time, but reset Motor Close Delay Time will not change
Motor Open Delay Tine.
Controller Setting

- 14 -
4 Motor Connections
4.1 Two wires motor without limit switch
4.2 Five wires motor with N/C limit switch
MOTOR CONNECTION

- 15 -
4.3 Sample of five wires with N/C limit
4.4 Step by step set up motor.
a) Mounting and connect motor
b) Disengage cutch and push two gates in middle position, then engage clutch. Power up,
push OPN button, gate should open, if any gate goes close direction, switch motor two
wires.
c) Adjust limit switch (make sure DIP4 limit switch selection is matched to limit switch).
(1) If 5 wires system, turn power off and disengage clutch and setting limits switch.
Move gate to closed potion and adjust closed limit stop to touch the limit switch
and this limit should connect to closed limit switch in put on control board. Open
gate to opened position do the same things for opened limit switch.
(2) If 2 wires system with limit switch with diode, need keep power on, push remote,
while gate is running (either open or close), using screw driver touch limit switch,
so can find out which limit is for open or close. Turn power off, then disengage
clutch, push gate and set up limit switch.
(3) If two wires system without limit switch, in this case, opened and closed
mechanical stopper must be installed. Adjust motor force pot to suit actual gate
power requirement.
d) Power up, use remote or push button to operate gate. Controller will automatically learn
soft stop positions. After two fully close and open cycles, auto-learn procedure finish.

- 16 -
5 Trouble shooting guide
5.1 General checking
Normally if installation is done properly, there would be trouble free. If in case of malfunction,
please checking as following steps.
1) Check the DIP setting limit switch selection is right.
2) Gate status LED green (open) and red (close), one or both should be flashing depending on the
gate position. If not flashing, please check the power supply and 12V DC output circuits if there is
a short circuit.
5.2 Gate not open
1) Check the limits switch type selection if it is right.
2) Push button on the control board, if gate status green LED flashing and red LED off, please
check motor fuse and motor.
5.3 Gate not close
1) Check the limits switch type selection if it is right
2) Check the DIP switches auto close mode selection if it is right.
3) Check control input. If one or more of OPN, PED, PEB input LED are on, which means access
control system hold gate open.
5.4 Control board display right, but motor not run
1) Mot like is the motor protect fuse burnt. 5x20mm, 10A. that is caused motor jammed or wrong
connection. Please check motor mechanism.
TROUBLE SHOOTING GUIDE
Table of contents
Popular Gate Opener manuals by other brands
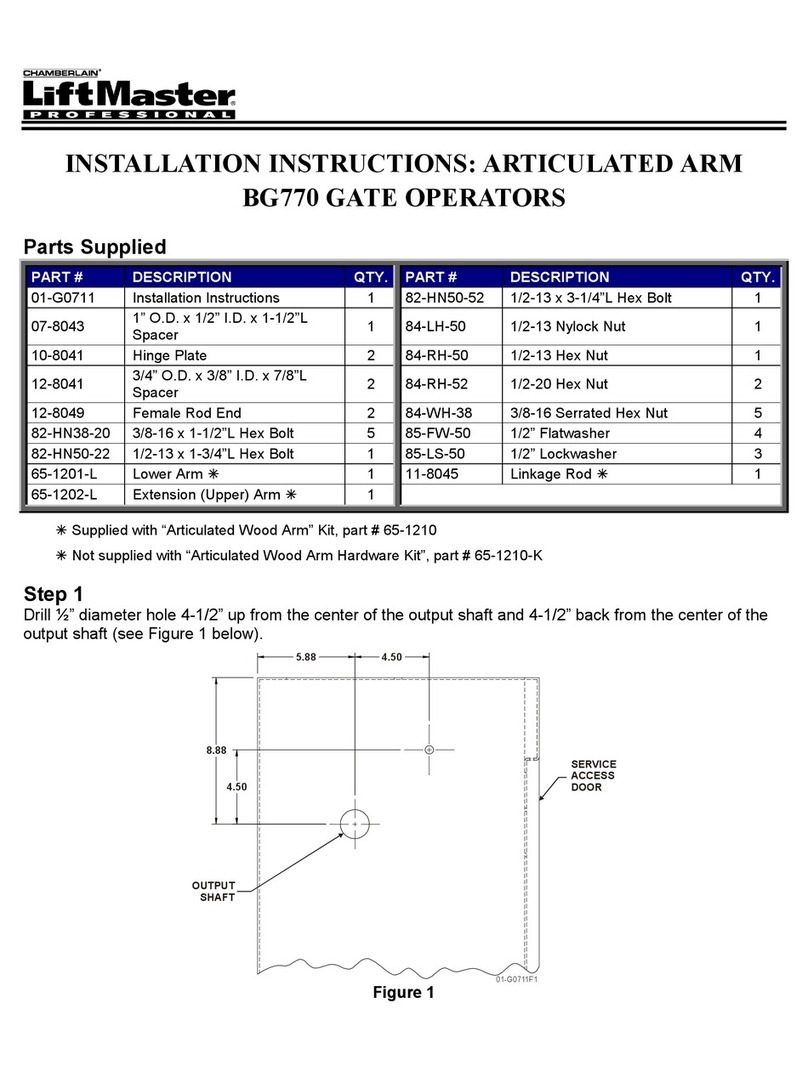
Chamberlain
Chamberlain LiftMaster Professional BG770 installation instructions
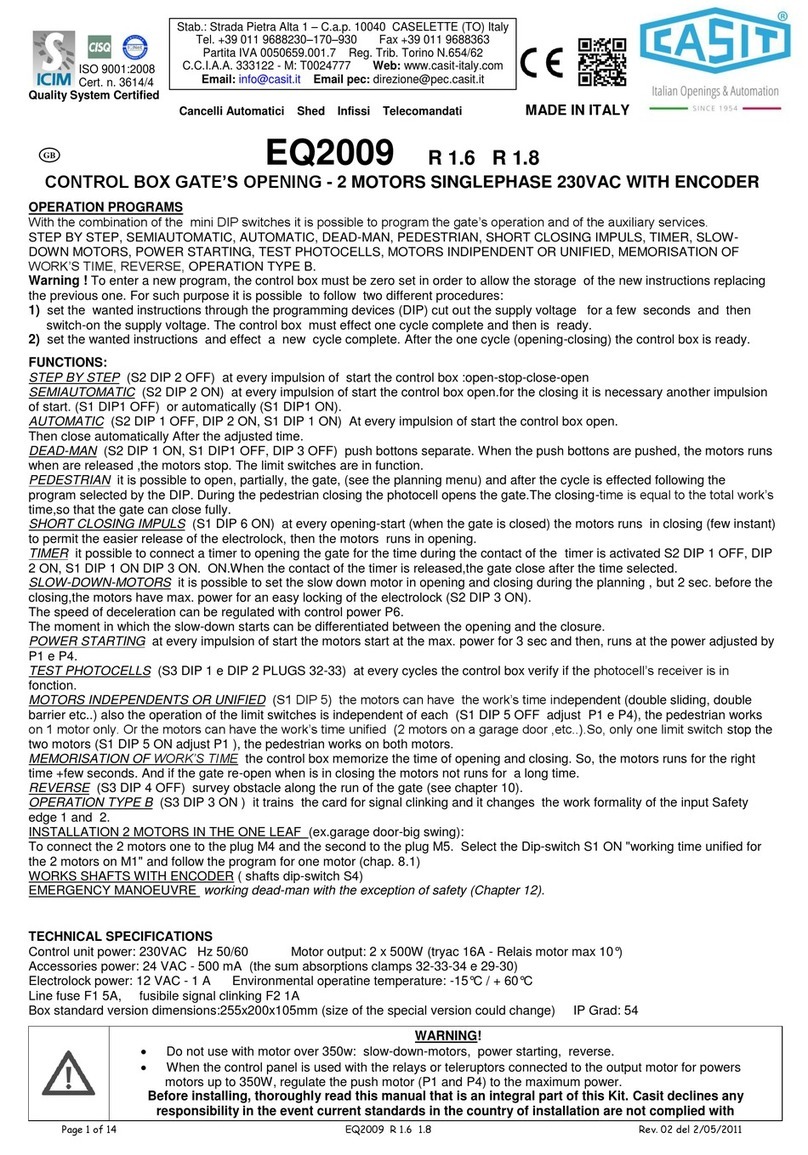
Casit
Casit EQ2009 manual
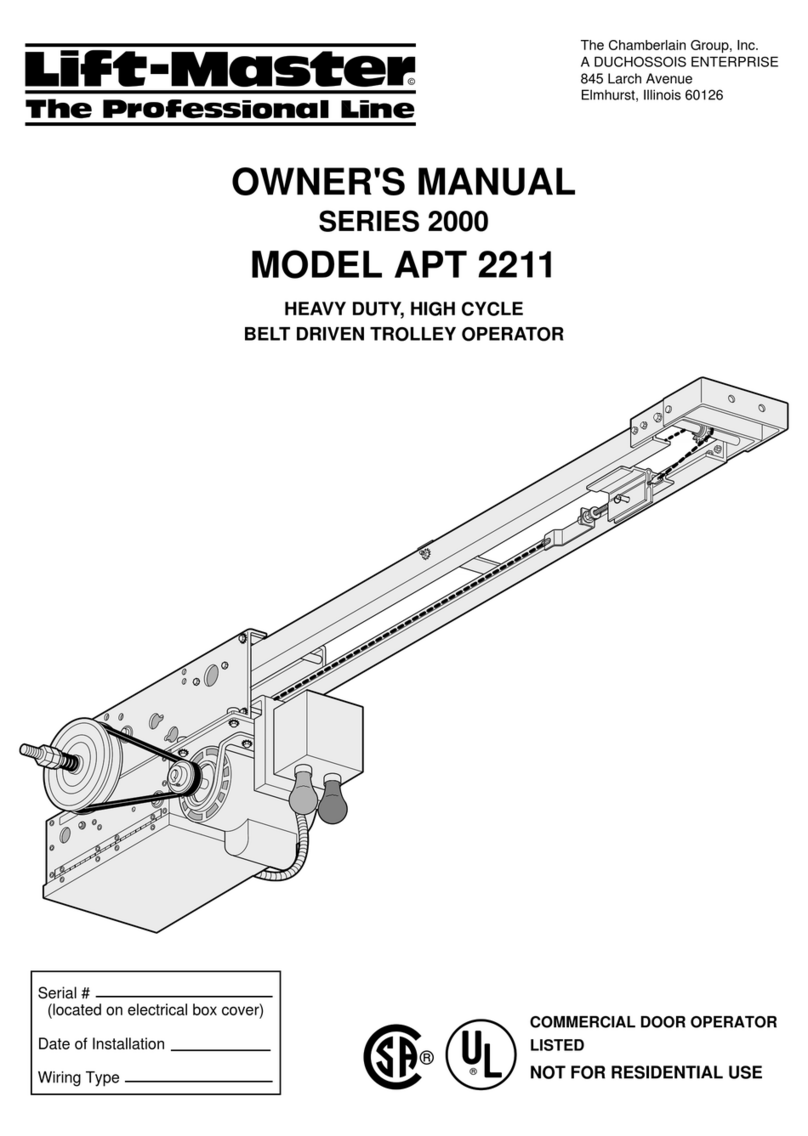
Chamberlain
Chamberlain 2000 Series owner's manual
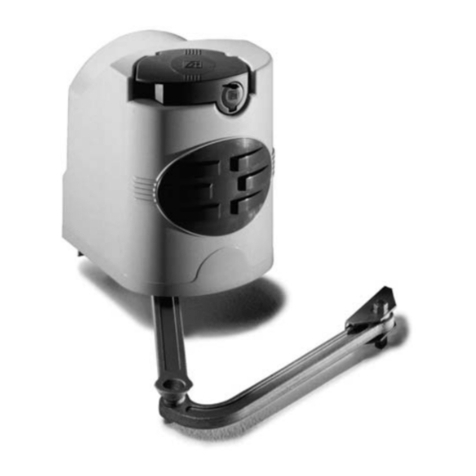
CAME
CAME F7024E instruction manual

fadini
fadini Bart 350 instruction manual
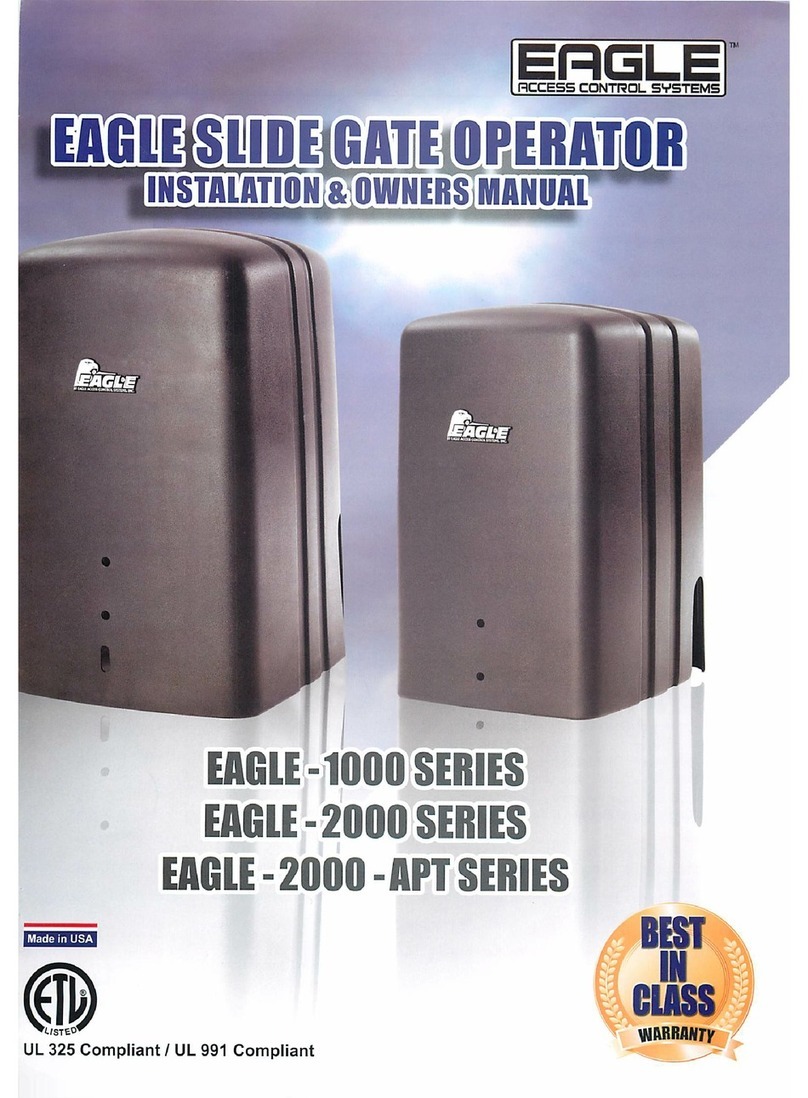
Eagle Access Control Systems
Eagle Access Control Systems 1000 series owner's manual