DINGLI BA14J-AWD User manual

Operation & Maintenance Manual
Table of Contents
Dingli Machinery
i
Series 1

Operation & Maintenance Manual
Table of Contents
Dingli Machinery
ii
Table of Contents
Foreword
1
Section
1
Safety Precaution
1-1
1.1
General
1-1
1.2
Safety Alert Symbols and Safety Signal Word
1-1
1.3
Safety Precaution
1-2
Operator Training and Knowledge
1-2
Workplace Inspection
1-3
Machine Inspection
1-3
1.4
Operation
1-3
General
1-3
Trip and Fall Hazard
1-4
Electrocution Hazards
1-5
Tipping Hazards
1-6
Crushing and Collision Hazards
1-8
1.5
Towing, Lifting, and Hauling
1-9
1.6
Additional Hazards/Safety
1-9
Section
2
Specifications
2-1
2.1
Machine Specifications
2-1
2.2
Performance Specifications
2-2
2.3
Hydraulic Specifications
2-4
2.4
Kubota 2403-M Engine Specifications
2-5
2.5
Perkins 404D-22 Engine Specifications
2-6
2.6
Bolt Torque Specifications
2-6
Section
3
User responsibility, Machine Preparation,
and Inspection
3-1
3.1
Personal Training
3-1
Operator Training
3-1
Training Supervision
3-1
Operator Responsibility
3-1
3.2
Preparation, Inspection, and Maintenance
3-1

Operation & Maintenance Manual
Table of Contents
Dingli Machinery
iii
3.2.1
General
3-1
3.2.2
Preparation for Use
3-2
3.2.3
Delivery and Frequent Inspection
3-3
3.2.4
Daily Walk-around Inspection
3-5
3.2.5
Daily Function Check
3-9
3.3
Oscillation Axle Lockout Test(If Equipped)
3-10
Section
4
Machine Controls and Indicators
4-1
4.1
General
4-1
4.2
Controls and Indicators
4-1
4.2.1
Ground Control Station
4-1
Ground Control Indicator Panel
4-2
4.2.2
Platform Control Station
4-6
4.2.3
The Multi-Function Gauge
4-11
4.2.4
The Control Unit Display Panel
4-12
4.3
Tilt Alarm Warning
4-14
4.4
Footswitch/Enable Indicator
4-14
4.5
Placards and Decals
4-15
Section
5
Operation Instruction
5-1
5.1
Description
5-1
5.2
Operating Characteristics and Limitations
5-2
Capacities
5-2
Stability
5-2
5.3
Engine Operation
5-5
Staring Procedure
5-5
Shutdown Procedure
5-5
5.4
Traveling(Driving) Operation
5-6
Driving Forward and Reverse
5-6
5.5
Steering Operation
5-7
5.6
Platform Operation
5-7
Platform LevelAdjustment Operation
5-7
Platform Rotation
5-7

Operation & Maintenance Manual
Table of Contents
Dingli Machinery
iv
5.7
Turntable Swinging Operation
5-7
5.8
Boom Operation
5-8
Raising and Lowering the Lower and Mid Boom
5-8
Boom Synchronizing Procedure
5-8
Raising and Lowering the Main(Upper) Boom
5-9
Telescoping the Main Boom
5-9
Raising and Lowering the Jib Boom
5-9
5.9
Auxiliary Pump Operation
5-9
5.10
Oscillation Axle Lockout Test
5-10
5.11
Shut Down and Parking Operation
5-10
5.12
Lifting and Tie Down
5-10
Lifting Operation
5-10
Tie Down Operation
5-10
5.13
Towing Operation
5-14
Prior to Towing
5-14
Section
6
Emergency Procedures
6-1
6.1
General
6-1
6.2
Emergency Towing Procedures
6-2
6.3
Emergency Controls and Their Locations
6-2
Power/Emergency Stop Switches
6-2
Ground Control Station
6-2
Auxiliary Power
6-2
6.4
Emergency Operation
6-3
Use of Ground Controls
6-3
Operator Unable to Control Machine
6-3
Platform or Boom Caught Overhead
6-3
Post Incident Inspection and Repair
6-4
6.5
Incident Notification
6-4
Section
7
General Maintenance
7-1
7.1
General
7-1
7.2
Lubrication Specification
7-1

Operation & Maintenance Manual
Table of Contents
Dingli Machinery
v
7.3
Lubrication Diagram
7-1
7.4
Operator Maintenance
7-3
7.4.1
Wheel Bearings
7-3
7.4.2
Lubrication for the Swing Bearing and Worm Gear
7-3
7.4.3
Test and Replace the Hydraulic Oil
7-4
7.4.4
Replace the Hydraulic Filters
7-5
Replace the Charge Filter Procedure
7-5
Replace the Return Filter Procedure
7-6
Replace the Suction Filter Procedure
7-7
7.4.5
Replace the Engine Oil
7-7
7.4.6
Replace the Engine Fuel Filter
7-7
7.4.7
Replace the Water Separator
7-8
7.4.8
Tires & Wheels Maintenance
7-9
Tire Damage
7-9
Tire Replacement
7-9
Wheel Replacement
7-9
Wheel Installation
7-9
7.4.9
Battery Maintenance
7-10
Section
8
Troubleshooting and Schematics
8-1
8.1
General Introduction
8-1
8.2
Hydraulic System Schedule Drawing
8-2
8.3
Electric Circuit Principle Drawing
8-4

Operation & Maintenance Manual
Foreword
Dingli Machinery
1
Foreword
We are very appreciated for your interesting with Dingli machine and choosing it for your
application. Our priority above all is you can use the machine safely for your application and
you can benefit from the Dingli machine mostly. For these reason we hope you can:
1.Comply with employer, job site and local governmental rules.
2.The manual provides very important information about the machine. It is essential to the
owner or the operator who use the machine. So we strongly recommend that you should
read the manual thoroughly before attempting to do anything with the machine, so as to
understand and follow the instruction or other information in the manual, especially the
safety information.
3.Dingli cannot anticipate every possible circumstance that might involve a potential
hazard. The warnings in this publication and on the product are, therefore, not all
inclusive. If a tool, procedure, work method or operating technique that is not specifically
recommended by Dingli is used, you must satisfy yourself that it is safe for you and for
others. You should also ensure that the product will not be damaged or be made unsafe by
the operation, lubrication, maintenance or repair procedure that you choose.
4.The information, specifications, and illustrations in this publication are on the basis of
information that was available at the time that the publication was written. Due to the
continuous improvements, Dingli reserve the rights to make the specifications changes
without prior notification. Please contact with Dingli dealers or Dingli distributors to
obtain the complete and most current information.
5.Any one who read the manual or used the machine, is encouraged to notify Dingli
Machinery Co, Ltd of any errors or send in suggestions for improvement. All
communications will be carefully considered for future printings of this and other
manuals, certainly if you have any question about the machine, please contact with our
team by dialing technical support phone, sending email, or any methods you want, etc.
Our contact information as bellow:
If you are in China Mainland, Please contact with:
Zhejiang Dingli Machinery Co.,Ltd Domestic Office:
Phone: 0086-572-8681685
Fax: 0086-572-8681687
Email: [email protected]
If you are out of the China Mainland, Please contact with :
Zhejiang Dingli Machinery Co.,Ltd International Office
Phone: 0086-572-8681688
Fax: 0086-572-8681690
Email: [email protected]

Operation & Maintenance Manual
Section1-Safety Precaution
Dingli Machinery
1-1
Safety Precaution
1.1 General
This section prescribes the proper and safe practices for major areas of machine usage. In
order to promote proper usage of the machine, it is mandatory that a daily routine be
established based on instructions given in this section. A maintenance program must also be
established by a qualified person and must be followed to ensure that the machine is safe to
operate.
The owner/user/operator of the machine should not accept operating responsibility until this
manual has been read and understood, and operation of the machine, under the supervision of
an experienced and qualified person, has been completed. If there is a question on application
and/or operation, Dingli Machinery Co,Ltd, should be consulted.
Most accidents that involve product operation, maintenance and repair are caused by failure to
observe basic safety rules or precautions. An accident can often be avoided by recognizing
potentially hazardous situations before an accident occurs. A person must be alerted to
potential hazards. This person should also have the necessary training, skills, and tools to
perform these functions properly.
Improper operation, lubrication, maintenance or repair of this product can be dangerous and
could result in injury or death. Do not operate or perform any lubrication, maintenance or
repair on this product, until you have read and understood the operation, lubrication, and
maintenance & repair information.
1.2 Safety Alert Symbols and Safety Signal Words
This Safety Alert Symbol is used to call attention to POTENTIAL HAZARDS,if these hazard
warnings are not heeded, bodily injury or death could occur to you or to other persons. The
hazards are identified by the “Safety Alert Symbol” and followed by a “Signal Word” such as
DANGER, WARNING” or CAUTION, which have been inserted throughout this manual to
emphasize these areas. They are defined as follows:
Section
1

Operation & Maintenance Manual
Section1-Safety Precaution
Dingli Machinery
1-2
Indicate an IMMINENTLY HAZARDOUS SITUATION, which if not avoided, WILL
RESULT IN SERIOUS INJURY or DEATH. This decal will have a red background
Indicate a potentially HAZARDOUS SITUATION, which if not been avoided, COULD
RESULT IN SERIOUS INJURY OR DEATH. This decal will have an orange background.
Indicate a potentially HAZARDOUS SITUATION, which if not avoided, may RESULT IN
minor or moderate INJURY. This decal will have a yellow background.
Indicate a potentially hazardous situation, which if not avoided, could result in property
damage, this decal have a blue background.
1.3 Safety Precaution
FAILURE TO COMPLY WITH THE SAFETY
PRECAUTIONS LISTED IN THIS MANUAL COULD
RESULT IN MACHINE DAMAGE, PROPERTY DAMAGE,
PERSONAL INJURY OR DEATH.
Operator Training and Knowledge
Read and understand this manual before operating the machine.
Read, understand, and obey all DANGERS, WARNINGS, CAUTIONS, and operating
instructions on the machine and in this manual.
Do not operate this machine until complete training is performed by authorized persons.
Only authorized and qualified personnel can operate the machine.
Use the machine in a manner which is within the scope of its intended application.
All operating personnel must be familiar with the emergency controls and emergency
operation of the machine as specified in this manual.
Read, understand, and obey all applicable employer, local, and governmental regulations
as they pertain to operation of the machine.

Operation & Maintenance Manual
Section1-Safety Precaution
Dingli Machinery
1-3
Workplace Inspection
The operator is to take safety measures to avoid all hazards in the work area prior to
machine operation.
Do not operate or raise the platform while on trucks, trailers, railway cars, floating
vessels, scaffolds or other equipment.
Do not operate the machine in hazardous environments unless approved for that purpose
by Dingli.
Be sure that the ground conditions are able to support the maximum load shown on the
decals located on the machine.
This machine can be operated in temperatures of -20℃to 40℃. Consult Dingli for
operation outside this range.
Machine Inspection
Before machine operation, perform inspections and functional checks. Refer to Section 3
of this manual for detailed instructions.
Do not operate this machine until it has been serviced and maintained according to
requirements specified by the manufacture.
Be sure the footswitch and all other safety devices are operating properly. Modification of
these devices is a safety violation.
MODIFICATION OR ALTERATION OF AN
AERIAL WORK PLATFORM SHALL BE MADE
ONLY WITH WRITTEN PERMISSION FROM
THE MANUFACTURER
Do not operate any machine on which safety or
instruction placards or decals are missing or illegible.
Avoid any buildup of debris on the platform floor.
Keep mud, oil, grease, and other slippery substances
from footwear and platform floor.
1.4 OPERATION
General
Do not use the machine for any purpose other than positioning personnel, their tools, and
equipment.
Never operate a machine that is not working properly. If a malfunction occurs, shut down
the machine for troubleshooting.
Never slam a control switch or lever through neutral to an opposite direction. Always
return switch to neutral and stop before moving the switch to the next function. Operate

Operation & Maintenance Manual
Section1-Safety Precaution
Dingli Machinery
1-4
controls with slow and even pressure. Hydraulic cylinders should never be left fully
extended or fully retracted before shutdown or for long periods of time.
Do not allow personnel to tamper with or operate the machine from the ground with
personnel in the platform, except in an emergency.
Do not carry materials directly on platform railing.
When two or more persons are in the platform, the operator shall be responsible for all
machine operations.
Always ensure that power tools are properly stowed and never left hanging by their cord
from the platform work area.
Supplies or tools which extend outside the platform are prohibited unless approved.
When driving, always position boom over rear axle in line with the direction of travel.
Remember, if boom is over the front axle, steer and drive functions will be reversed.
Do not assist a stuck or disabled machine by pushing, pulling, or by using boom functions.
Only pull the unit from the tie-down lugs on the chassis.
Do not place boom or platform against any structure to steady the platform or to support
the structure.
Stow boom and shut off all power before leaving machine.
Trip and Fall Hazards
During operation, occupants in the platform must
wear a full body harness with a lanyard attached
to an authorized lanyard anchorage point. Attach
only one (1) lanyard per lanyard anchorage point.
Before operating the machine, make sure all gates are closed and fastened in their proper
position.

Operation & Maintenance Manual
Section1-Safety Precaution
Dingli Machinery
1-5
Keep both feet firmly positioned on the platform floor at all times. Never use ladders,
boxes, steps, planks, or similar items on platform to provide additional reach.
Never use the boom assembly to enter or leave the platform.
Use extreme caution when entering or leaving platform. Be sure that the boom is fully
lowered. It may be necessary to telescope out to position the platform closer to the
ground for entry/exit. Face the machine, maintain “three point contact” with the machine,
using two hands and one foot or two feet and one hand during entry and exit.
Electrocution Hazards
This machine is not insulated and does not provide protection from contact or proximity
to electrical current.

Operation & Maintenance Manual
Section1-Safety Precaution
Dingli Machinery
1-6
Maintain distance from electrical lines, apparatus, or any energized (exposed or insulated)
parts according to the Minimum Approach Distance (MAD) as shown in Table 1.1
Table 1-1. MinimumApproach Distances (M.A.D.)
Voltage Range (Phase to Phase)
MINIMUM APPROACH DISTANCE in Feet
(Meters)
0 to 50 KV
10 (3)
Over 50KV to 200 KV
15 (5)
Over 200 KV to 350 KV
20 (6)
Over 350 KV to 500 KV
25 (8)
Over 500 KV to 750 KV
35 (11)
Over 750 KV to 1000 KV
45 (14)
NOTE: This requirement shall apply except where employer, local or governmental
regulations are more stringent.
Allow for machine movement and electrical line swaying.
Maintain a clearance of at least 10 ft. (3m) between any part of the machine and its
occupants, their tools, and their equipment from any electrical line or apparatus carrying
up to 50,000 volts. One foot additional clearance is required for every additional 30,000
volts or less.
The minimum approach distance may be reduced if insulating barriers are installed to
prevent contact, and the barriers are rated for the voltage of the line being guarded. These
barriers shall not be part of (or attached to) the machine. The minimum approach distance
shall be reduced to a distance within the designed working dimensions of the insulating
barrier. This determination shall be made by a qualified person in accordance with the
employer, local, or governmental requirements for work practices near energized
equipment
DO NOT MANEUVER MACHINE OR PERSONNEL INSIDE
PROHIBITED ZONE (MAD). ASSUME ALL ELECTRICAL PARTS AND
WIRINGARE ENERGIZED UNLESS KNOWN OTHERWISE.
Tipping Hazards
The user should be familiar with the surface before driving. Do not exceed the allowable
sideslope and grade while driving.
Do not elevate platform or drive with platform elevated while on a sloping, uneven, or
soft surface.

Operation & Maintenance Manual
Section1-Safety Precaution
Dingli Machinery
1-7
Before driving on floors, bridges, trucks, and other surfaces, check allowable capacity of
the surfaces.
Never exceed the maximum platform capacity. Distribute loads evenly on platform floor.
Do not raise the platform or drive from an elevated position unless the machine is on firm,
level and smooth surfaces.
Keep the chassis of the machine at least 2 ft. (0.6m) from holes, bumps, drop-offs,
obstructions, debris, concealed holes, and other potential hazards on the floor/surface.
Do not push or pull any object with the boom.
Never attempt to use the machine as a crane.
Do not tie off machine to any adjacent structure.
Do not operate the machine when wind conditions exceed 28 mph (12.5 m/s).

Operation & Maintenance Manual
Section1-Safety Precaution
Dingli Machinery
1-8
Do not increase the platform size with unauthorized deck extensions or attachments.
If boom assembly or platform is in a position that one or more wheels are off the ground,
all persons must be removed before attempting to stabilize the machine. Use cranes,
forklift trucks, or other appropriate equipment to stabilize machine and remove personnel.
Crushing and Collision Hazards
Approved head gear must be worn by all operating and ground personnel.
Check work area for clearances overhead, on sides, and bottom of platform when lifting
or lowering platform, and driving.
During operation, keep all body parts inside platform railing.
Use the boom functions, not the drive function, to position the platform close to
obstacles.
Always post a lookout when driving in areas where vision is obstructed.
Keep non-operating personnel at least 6 ft. (1.8m) away from machine during all driving
and swing operations.
Limit travel speed according to conditions of ground surface, congestion, visibility, slope,
location of personnel, and other factors which may cause collision or injury to personnel.
Be aware of stopping distances in all drive speeds. When driving in high speed, switch to
low speed before stopping.
Travel grades in low speed only.
Do not use high speed drive in restricted or close quarters or when driving in reverse.

Operation & Maintenance Manual
Section1-Safety Precaution
Dingli Machinery
1-9
Exercise extreme caution at all times to prevent obstacles from striking or interfering with
operating controls and persons in the platform.
Be sure that operators of other overhead and floor level machines are aware of the aerial
work platform’s presence. Disconnect power to overhead cranes.
Warn personnel not to work, stand, or walk under a raised boom or platform. Position
barricades on floor if necessary.
1.5 TOWING, LIFTING, AND HAULING
Never allow personnel in platform while towing, lifting, or hauling.
This machine should not be towed, except in the event of emergency, malfunction, power
failure, or loading/unloading. Refer to the Emergency Procedures section of this manual
for emergency towing procedures.
Ensure boom is in the stowed position and the turntable locked prior to towing, lifting or
hauling. The platform must be completely empty of tools.
When lifting machine, lift only at designated areas of the machine. Lift the unit with
equipment of adequate capacity.
Refer to the Machine Operation section of this manual for lifting information.
1.6 ADDITIONAL HAZARDS / SAFETY

Operation & Maintenance Manual
Section1-Safety Precaution
Dingli Machinery
1-10
Do not use machine as a ground for welding.
When performing welding or metal cutting operations, precautions must be taken to
protect the chassis from direct exposure to weld and metal cutting spatter.
Do not refuel the machine with the engine running.
Battery fluid is highly corrosive. Avoid contact with skin and clothing at all times.
Charge batteries only in a well ventilated area.

Operation & Maintenance Manual
Section3-User Responsibility, Machine
Preparation, and Inspection
Dingli Machinery
2-1
Specification
2.1Machine Specification
Stowed Dimension
Length
5.15m
Width
2.3m
Height
2.4m
Machine Gross Weight
7500kg
Ground Clearance
0.30m
Operation Dimension
Maximum Platform Height
14m
Maximum Platform Working Height
16m
Maximum Up and Over Height
7.67m
Maximum Horizontal Reach
7.47
Main Boom Up Angle
75
Main Boom Down Angle
-24
Maximum Turntable Tailswing
0
Wheelbase
2.2m
Minimum Turning Circle Inside
2.22m
Maximum Turning Circle Outside
5.10m
Turntable Rotation
357 non-continuous
Platform Rotation
160
Tire and Wheels
Section
2

Operation & Maintenance Manual
Section3-User Responsibility, Machine
Preparation, and Inspection
Dingli Machinery
2-2
Solid Tire and Wheel
Size
33*12-20
Outer Diameter
838mm
Width
287
Weight
194 kg
Foam Filled Tire
Size
12*16.5
Outer Diameter
818mm
Width
305
Weight
227 kg
2.2 Performance Specification
Driving Speed
Boom Stowed, high range
6km/h
Boom Raised or Extended
1.1km/h
Gradeability (Stowed)
40% for 4*4 drive
30% for 4*2 drive
Main Lift Up
24-28 sec
Main Lift Down
20-24 sec
Swing Right & Left
80-90 sec
Telescope Extent Out
15-20 sec
Telescope Retract In
9-15 sec
Platform Rotate R & L
25-32 sec
Jib Up
20-31 sec
Jib Down
19-25 sec

Operation & Maintenance Manual
Section3-User Responsibility, Machine
Preparation, and Inspection
Dingli Machinery
2-3
Lower and Mid Boom Up
30-38 sec
Lower and Mid Boom Down
22-28 sec
Machine Orientation When Doing Speed Tests
Lift: Boom Retracted. Telescope Retracted. Lift Up, Record Time, Lift Down, Record Time.
Swing: Boom at Full Elevation. Telescope Retracted. Swing the Turntable to the end stop.
Swing the Opposite Direction, Record Time.
Telescope: Boom at Full Elevation; Telescope Retracted; Telescope Out, Record Time.
Telescope In, Record Time.
Drive: Test to be done on a smooth level surface. Drive Select Switch should be set at 2WD
High Engine. Start approximately 25 ft. (7.62 m) from starting point so that the unit is at
maximum speed when starting the test. Results should be recorded for a 200 ft. (60.96 m)
course. Drive Forward, record time. Drive Reverse, Record Time.
Drive (Above Horizontal): Test should be done on a smooth level surface. Drive Select
Switch should be set to 2WD High Engine. The Platform Speed Knob should be selected out
of the creep speed. This verifies that the switches are working when the boom is above
horizontal. Results should be recorded for a 50 ft. course. Drive Forward, Record Time. Drive
Reverse, Record Time.
Platform Rotate: Platform level and completely rotated one direction. Rotate the opposite
direction, Record Time. Rotate the other direction, Record Time.
Articulating Jib: Platform level and centered with the boom. Start with the Jib down. Jib Up,
Record Time. Jib Down, Record Time.
Lower Lift: Upper Boom horizontal. Telescoped In. Lower Lift Up, Record Time. Lower Lift
Down, Record Time.
Test Notes
1. Stop watch should be started with the function, not with the controller or switch.
2. Drive test results reflect 12x16.5 tires.
3. All speed tests are run from the platform. These speeds do not reflect the ground control
operation.
4. The platform speed knob control must be at full speed (turned clockwise completely).
5. Function speeds may vary due to cold, thick hydraulic oil. Test should be run with the oil
temperature above 100° F (38° C).

Operation & Maintenance Manual
Section3-User Responsibility, Machine
Preparation, and Inspection
Dingli Machinery
2-4
6. Some flow control functions may not work with the speed knob clicked into the creep
position
2.3Hydraulic System Specification
Drive Pump
Type
Bi-directional Variable Displacement
piston pump, EDC control
Displacement per revolution
28cc for 4*2 drive
46cc for 4*4 drive
Maximum Peak Pressure
340 bar
Maximum Continuous Working Pressure
250 bar
Hydraulic Filter
10um,
Drive Motor
Type
Two Speed Variable Displacement
Motor
Rated Working Pressure
340 bar
Function Pump
Type
Gear Pump
Rated Working Pressure
250 bar
Displacement per revolution
14cc
Hydraulic Tank Return Filter
10um
Dive Manifold
Motor Shift/Brake Release Pressure
20 bar
4WD Front Motor Flow Regulation
4WD Rear Motor Flow Regulation
2WD Rear Motor Flow Regulation
Function Manifold
Function Main Relief Pressure, used for Lower &
Mid Boom Up and Down; Main Boom Up and
Down
210 bar
Turntable Swing Pressure Setting
70 bar
Main Boom Telescopic Extent and Retract Pressure
Setting
180 bar
Jib Up and Down Pressure Setting
Platform Rotate R&L Pressure Setting
124 bar
Platform Level Up Pressure Setting
190 bar
Platform Level Down Pressure Setting
124 bar
Steering Pressure Setting
124 bar
Table of contents
Other DINGLI Lifting System manuals
Popular Lifting System manuals by other brands
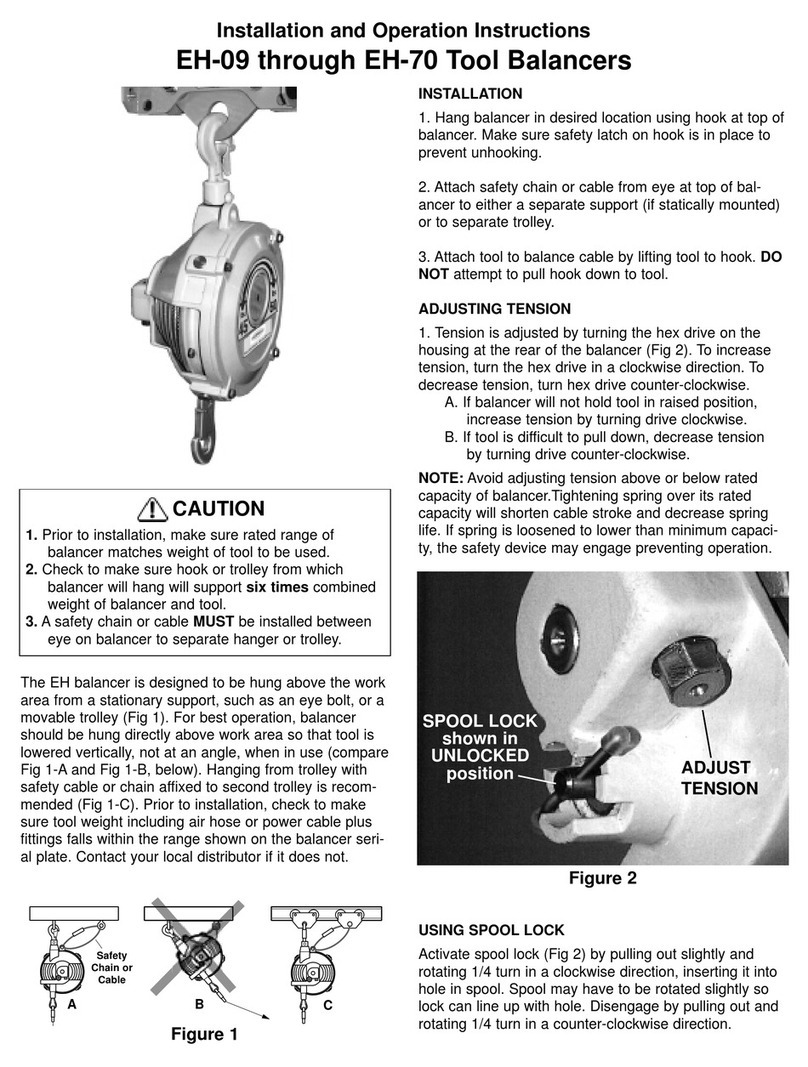
Hubbell
Hubbell EH-09 Installation and operation instructions
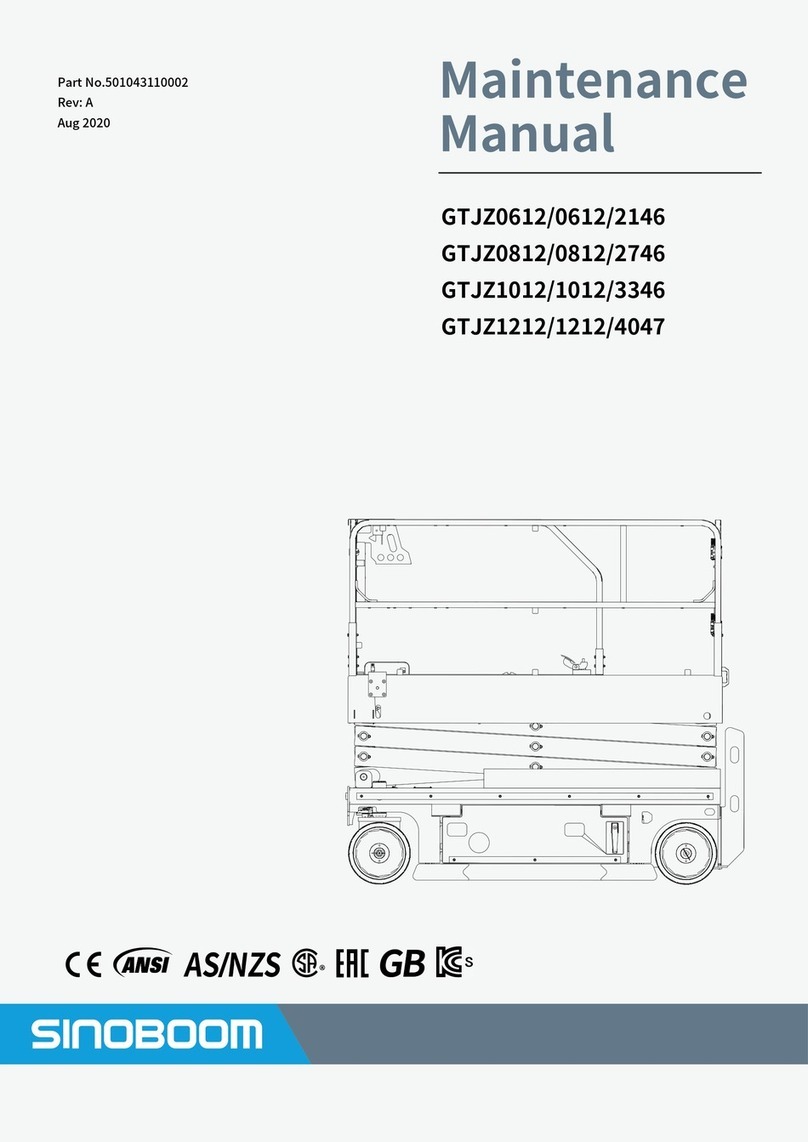
Sinoboom
Sinoboom GTJZ2146 Maintenance manual
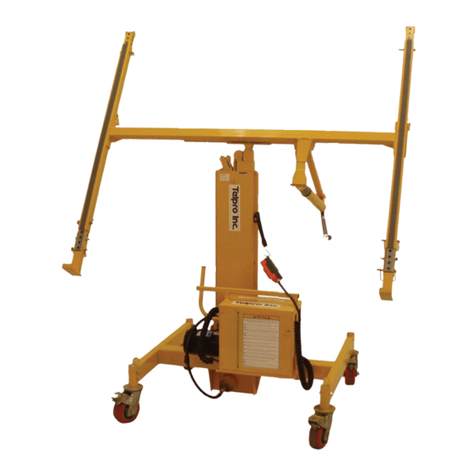
Paragon Pro
Paragon Pro Telpro 294 Assembly & Use Guide
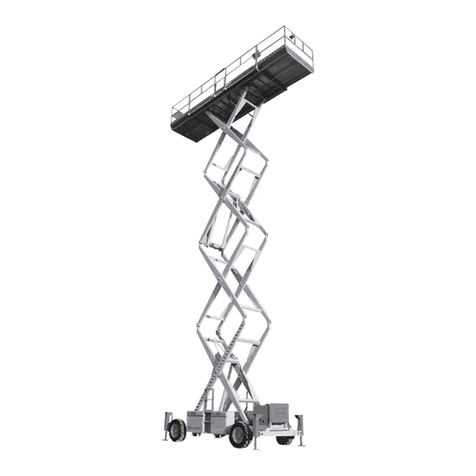
Skyjack
Skyjack SJ-600 Series operating manual
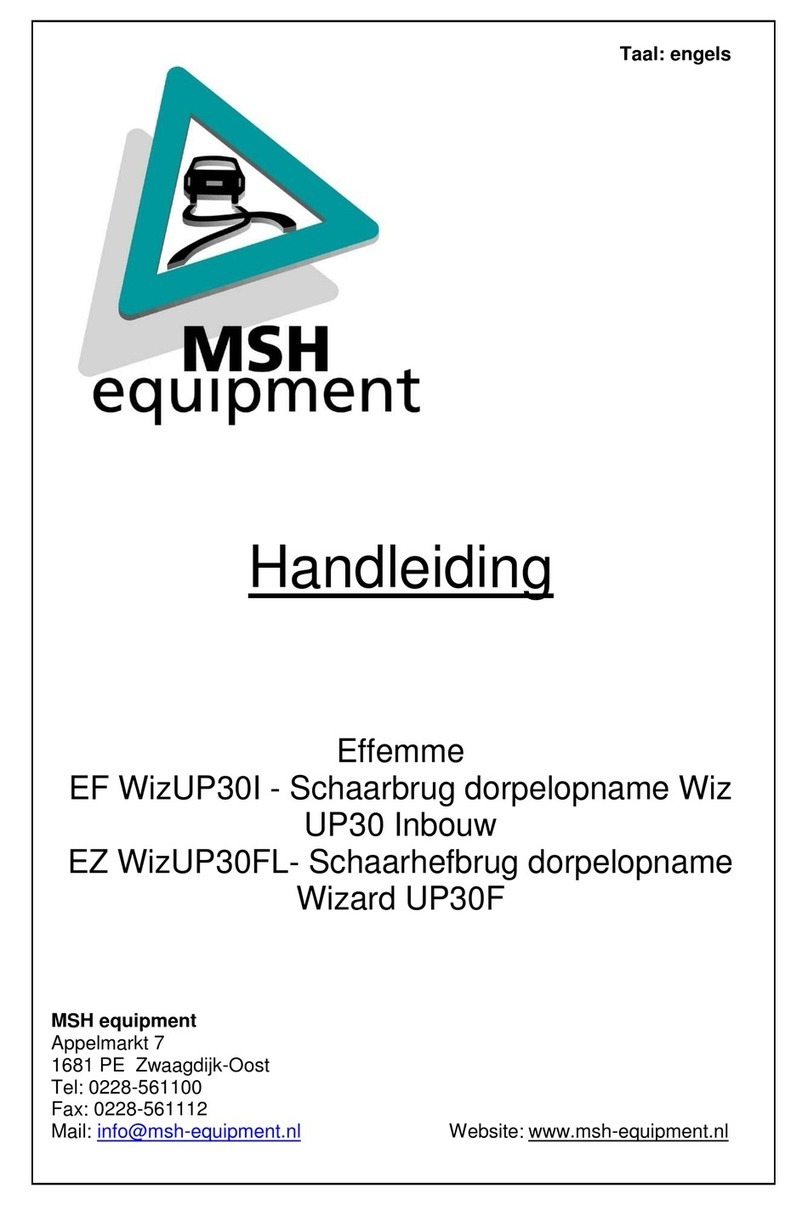
MSH equipment
MSH equipment WIZARD UP 30 operating instructions
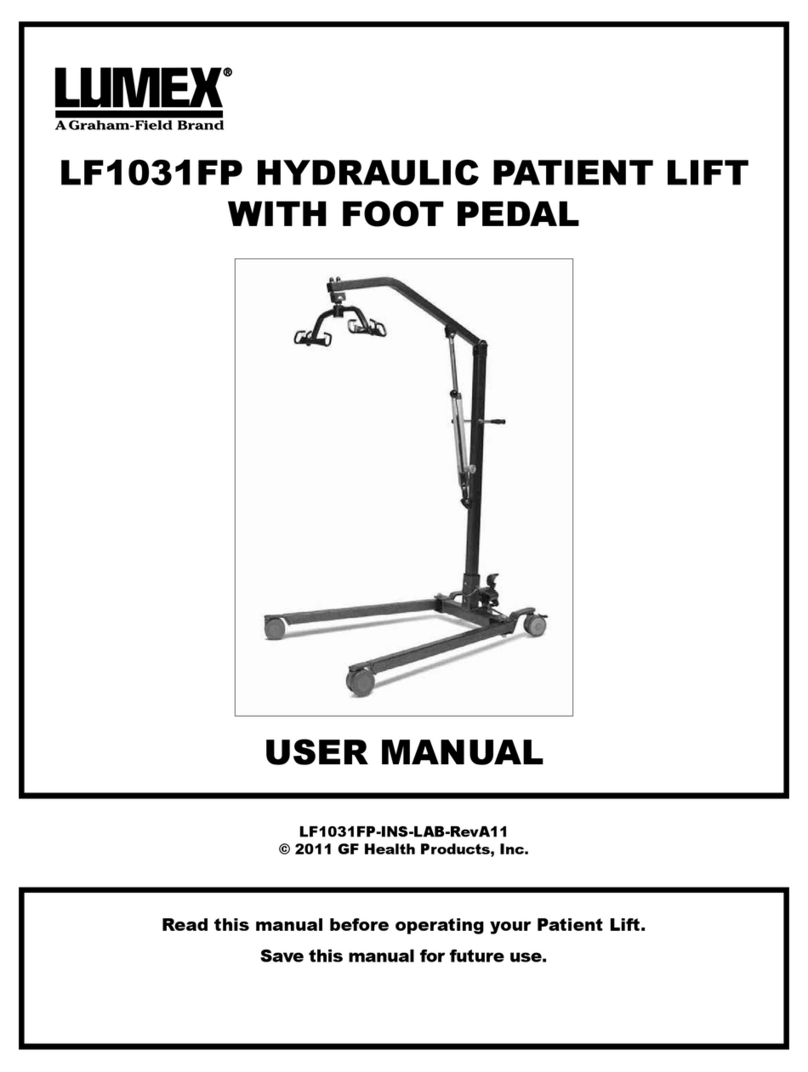
Graham Field
Graham Field Lumex LF1031FP user manual
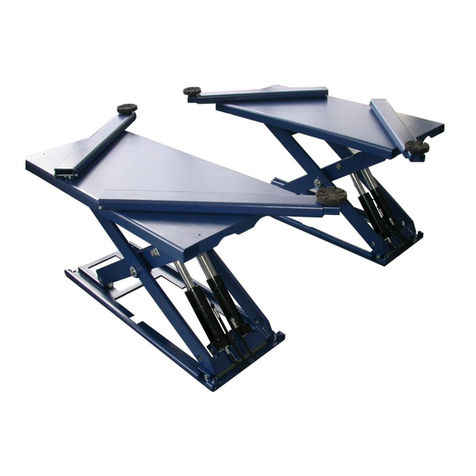
Nussbaum
Nussbaum Quick Lube HF Owners & installation manual
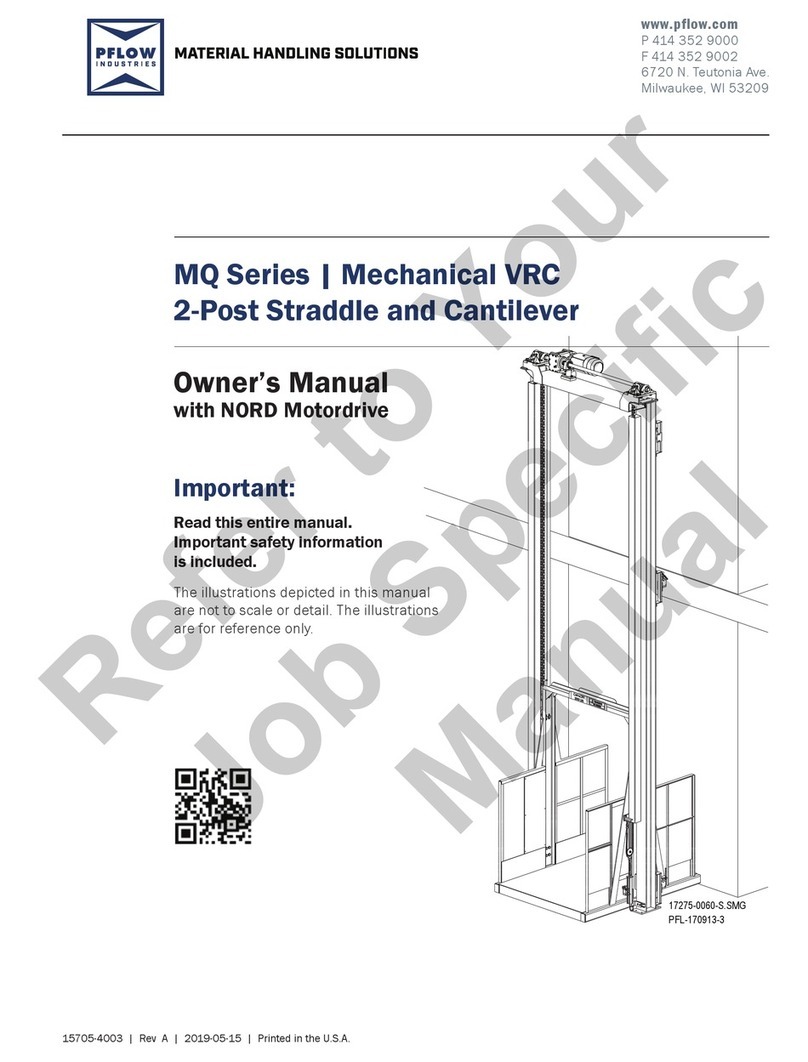
PFlow Industries
PFlow Industries MQ Series owner's manual
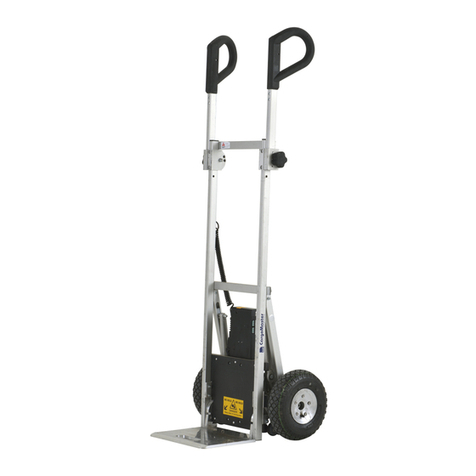
AAT
AAT CargoMaster C141 V Translation of the original user manual
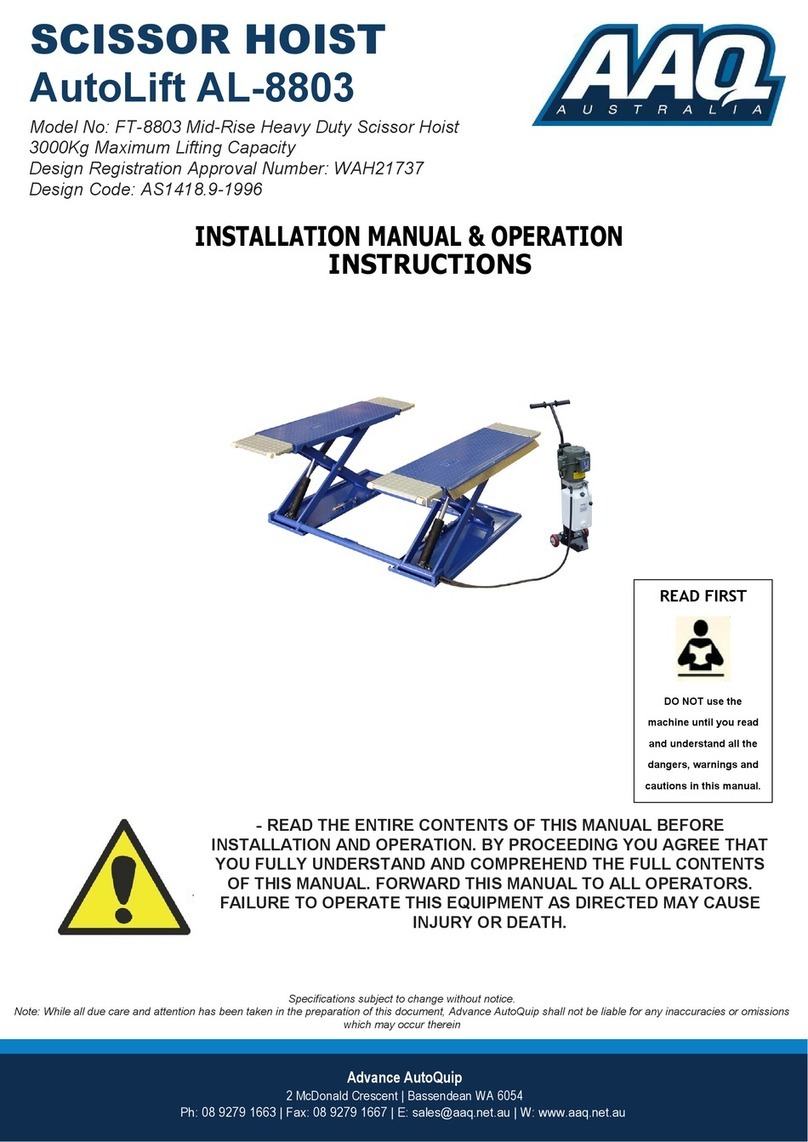
AAQ
AAQ AutoLift AL-8803 Installation manual & operation instructions
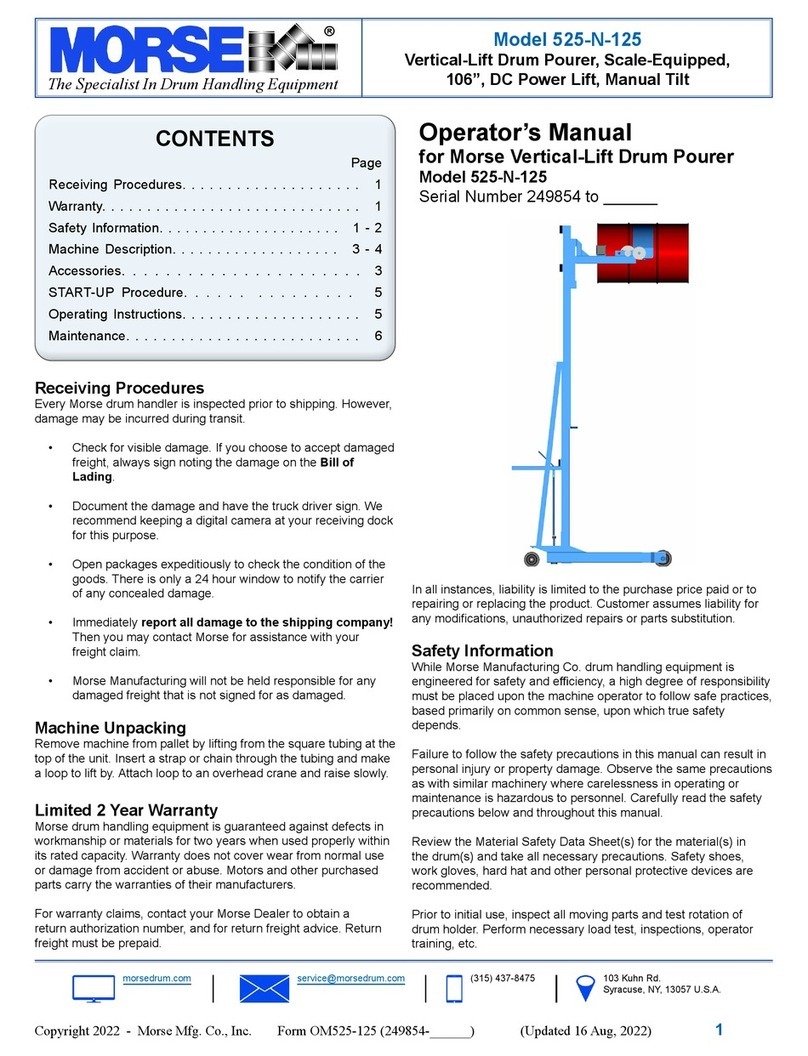
morse
morse 525-N-125 Operator's manual
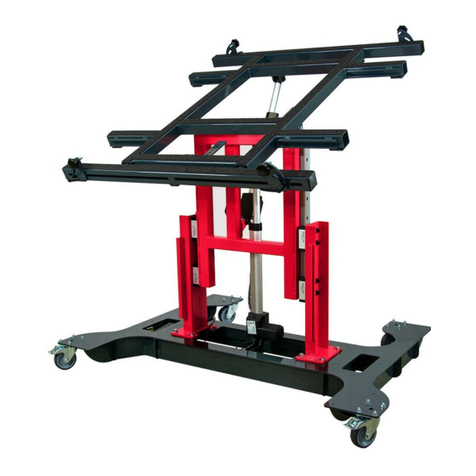
ALFRA
ALFRA AMTE 400 user manual