Earthworks CMK4 CloseMic Kit User manual

Made in U.S.A.
Earthworks, Inc.
37 Wilton Rd.
Milford, NH 03055
603-654-6427, ext. 14
www.earthworksaudio.com
Printed in U.S.A.
DP30/C
Frequency response
Polar Pattern
Cardioid
Sensitivity
1
0mV/Pa (-40dBV/Pa)
Power requirements 48V Phantom,
1
0mA
Peak acoustic input
1
45dB SPL
Output XLR (PIN 2+)
Minimum output load
600Ω, balanced
between pins 2&3
Noise
22dB SPL (A weighted)
Dimensions L x D
Weight
30Hz to 30kHz +2dB@1’
1
0.75 x .860 inches
(275mm x 22mm)
.22lb (
1
00g)
DP30/C


Congratulations on your purchase of an Earthworks CMK4 or CMK5
CloseMic™ Kit System. You will be thrilled with the results you will be
able to obtain using the CloseMic™ Kit System. After reading this manu-
al, if you have any unanswered questions, please email or phone us using
the contact information on the back page of this manual.
Happy Drumming!
First, identify the exact product you have purchased from the list below.
Then verify that you have received each of the items listed below the product
model/name.
Items Enclosed with:
CMK4 CloseMic™ Kit
4 – DP30/C Drum Periscope™ Microphones
4 - LP1530 LevelPads™
4 – RM1 RimMount™
4 – PW1 Foam Windscreens
1 – CMK-C High Impact Carrying Case
with custom foam insert
1 – CMK4/CMK5 User’s Manual
CMK5 CloseMic™ Kit
5 – DP30/C Drum Periscope™ Microphones
5 - LP1530 LevelPads™
5 – RM1 RimMount™
5 – PW1 Foam Windscreens
1 – CMK-C High Impact Carrying Case
with custom foam insert
1 – CMK4/CMK5 User’s Manual
Version 5, June 1, 2012 2
NOTES
13

Figure 8-A and 8-B Miking the Top Head of a Tom
The DP30/C High Denition Drum Periscope Microphones™ have been used
successfully by drummers with major recording artists in both recording ses-
sions and for live performance. The Drum Periscope Microphones™ will pro-
vide you with years of exceptional and reliable results and will withstand the
rigors of the road. We welcome you to the ever-growing number of drummers
and sound engineers using Earthworks High Denition Microphones™.
We know that when you use the Earthworks High Denition Drum Periscope
Microphones for your recording and live performances you will be thrilled with
the results. We are pleased to welcome you to the ever-growing family of
professionals using Earthworks High Denition Microphones™.
We hope the suggestions in this manual have been benecial to you. Don’t
be afraid to experiment with mic placement. You can be as creative with your
mic placement as you are with your music. You are the judge of what works
best and sounds best.
If you have any questions, or require any additional information, please
do not hesitate to contact Earthworks using the contact information on
the back cover of this manual.
FIFTEEN-YEAR WARRANTY
All Earthworks
®
products (excluding accessories) carry a fifteen-year limited
warranty (parts and labor). If you have any problems with your Earthworks
products, please contact our warranty/repair department by email at:
12
A. B.
IMPORTANT NOTICE - Please Read This:
Use of the LevelPad™ - DP30/C microphones have a high output level,
which may overload the preamps of some mixers or consoles. Many out-
board microphone preampliers and preampliers in mixing consoles will
handle as much as +24dbv at the microphone input, without distortion. We
suggest that you check the “maximum preamp input level” specications
of your mixer or preamplier to see if it will accommodate signal levels
this high. Some mixers and preamps will not handle levels this high at the
microphone input. To prevent overload, please use a LevelPad™ in the
microphone cable feeding each DP30/C Microphones.
Some mixer or outboard preampliers have a pad that can be switched in or
out. However, some of these pads are not attenuators that precede the pre-
amplier input, instead they only reduce the gain of the preamplier. These
(so called) pads will provide no input overload protection from high level
microphone signals (see Fig. 1-A). In contrast, other outboard or mixer pre-
ampliers have actual pads that precede the preamplier. These types of
pads will provide the input overload protection that is needed (see Fig. 1-B).
Such pads will typically provide –10dB or –20dB attenuation. However, due
to the very high output level of the Drum Periscope™ microphones, -10 dB
or even –20dB may not be enough attenuation when close miking snares or
toms with DP30/C Microphones.
In any case where the pad does not precede the preamplifier, or the pad
does not provide enough attenuation, the Earthworks LP1530 LevelPad™
can be used and will provide either –15dB or –30dB of attenuation. The
LevelPad™ comes housed in a stainless steel tube with gold-plated XLR
connectors on each end. As the LevelPad™ is inserted in the mic line,
it will always precede the preamplifier input. It makes no difference if the
LevelPad™ is inserted at the microphone, or somewhere in the middle
3
Figure 1-A and 1-B Preamp Input Pads
A.
B.

4
of the mic line, or by plugging the LevelPad directly into the preamplifier
input. The most popular practice is to plug the LevelPad™ into the pre-
amplifier input, which makes it more accessible to switch the attenuation
settings (-15dB or –30dB) if needed. Figures 2-A, 2-B and 2-C show how
the LevelPad can be inserted into the microphone line in one of three
ways as indicated below:
Figure 2-A LevelPad™ inserted at the microphone base
Figure 2-B LevelPad™ inserted in the microphone cable.
Figure 2-C LevelPad™ inserted into mixer mic input
CAUTION: Plugging the LevelPad into the mic input
of a mixer can cause damage to the mixer input con-
nector if the LevelPad receives a hard push to the
side. However, if your are careful, placing the Level-
Pad at the mixer mic input will provide greater ease
of use in changing the LevelPad attenuation switch.
suggested that the microphone head be positioned between 1.5 inches and
3 inches above the drumhead.
All of the previous information in this manual applies to both toms and
snares when using a Drum Periscope Microphone.
The DP30/C SnareMic has been optimized for miking snare drums and toms
and has a low frequency response down to 30Hz. If the DP30/C sounds a
little “tubby” on your snare drum, then use a high-pass lter set somewhere
between 60Hz and 100Hz to reduce the low frequency response or a low
frequency equalizer (EQ) to accomplish the same thing by attenuating/cut-
ting a few dB in the area of 60Hz to 100Hz for the desired results.
The DP30/C SnareMic™ can be used on either the top drumhead, bottom
drumhead or both. Figure 7-A shows a snare drum with a DP30/C micro-
phone placed over the top drumhead, while Figure 7-B shows a share drum
with both the top and bottom heads miked.
Figure 7-A and 7-B Miking the Top or Top & Bottom of a Snare
Close Miking Toms with the DP30/C
This extended low frequency response and the crisp transient response of
the DP30/C will provide a rich and full tom sound. You can mike either the
top head of a tom with the DP30/C TomMic™ as indicated in Figure 8 or you
can also mike the bottom, or top and bottom of a tom in a similar fashion as
shown on a snare in Figure 7-B. You will notice in Figure 8-A the microphone
head is placed closer to the drum rim, while in Figure 8-B the microphone
head is moved closer to the center of the drumhead by changing the posi-
tion of the mini-ex gooseneck.
11
A. B.

Earthworks Drum Periscope™Microphones
The Earthworks DrumKit™ High Denition Three-Microphone Systems
have had great success because they pick up drum sounds with far more de-
tail and accuracy than conventional microphones. This improved sound qual-
ity is due to proprietary advanced technologies utilized in Earthworks High
Denition Microphones.
Many drummers such as Je Campitelli with Joe Satriani, Keith Carlock
with Steely Dan, and FOH engineers such as Randy Lane with Dream The-
ater, were using Earthworks High Denition Microphones™ for overheads
and kickdrum with exceptional results. They then wanted the same excep-
tional sound quality from their snare and tom mics. With the introduction of
the DP30/C microphone, they were able to get the same pristine, detailed
sound from their toms and snares as they were from their Earthworks High
Denition drum overhead mics.
We worked with major artists for nearly two years developing and eld
testing the DP30/C High Denition tom and snare mic. During the develop-
ment phase, we miked a set of drums with nine Earthworks High Denition
Microphones (including our new DP30/C tom and snare mics) and also nine
industry favored mics. When veteran engineers heard the dierence be-
tween these two recordings, they made the comment that the improvement
was so dramatic, it didn’t even sound like the same set of drums. They all
agreed, “the increase in detail and sound quality was astounding.”
The DP30/C was designed specifically for snare and toms that features a
flexible mini-gooseneck for easy positioning in addition to a high acoustic
input level that can handle up to 145 dB SPL. The Earthworks patented
polar technology provides excellent rear rejection and a uniformity of fre-
quency response out to 90 degrees off-axis. This vastly reduces phase
cancellation or other phasing issues, and minimizes cymbal leakage as
well as acoustic feedback problems in “live sound” applications.
Earthworks High Definition Microphones™
the New Science in Microphones
David Blackmer, the brilliant engineer who invented the unique technolo-
gies of dbx, is also the inventor and founder of Earthworks. In the last few
years of his life, David developed a number of revolutionary technologies
that dramatically improve the quality and performance of microphones.
In short, Earthworks High Definition Microphones™ will pick up sounds
and detail that other microphones cannot. These technological improve-
5
The flexible mini-gooseneck will allow you to move the microphone head
either up or down above the drumhead as well as in and out from the
drum rim. In addition, you can change the angle of the microphone head
for your desired results. Figure 6-A shows how the microphone head can
be rotated while Figure 6-B shows how the microphone head can be
moved more toward the center of the drum by changing the positioning
of the mini-gooseneck.
Figure 6-A and 6-B Positioning the Microphone Head
Plug in the LevelPad, if necessary
In close miking drums, one should keep in mind that the peak sound
level at the microphone head is extremely loud. Microphones used for
close miking drums should have a sound pressure handling capability of
at least 140dB SPL to prevent audible distortion. The Drum Periscope™
microphones will handle up to 145dB SPL without distortion. However,
as mentioned earlier, with this kind of high sound pressure level, it is
possible for the microphone output to be as much as +24dBV which may
overload some microphone preamplifiers. The use of the Earthworks Lev-
elPad in the microphone line will prevent any such distortion or overload.
So, to be safe, we suggest that you first plug a LevelPad into the mic
line feeding the Drum Periscope microphone. For full information refer to
pages 3 and 4 of this manual.
Close Miking Snare Drums with the DP30/C
As previously mentioned, when close miking drums with a DP30/C micro-
phone, never position the microphone head parallel to the drumhead. Al-
ways position the microphone head at an angle to the drumhead. It is also
10
A. B.

ments are in the areas of impulse response, diaphragm settling time and
polar technologies. Those who have heard Earthworks High Definition
Microphones™, say that they hear more of the attack, and more subtle
details with a more pristine quality in the sound than with any other mi-
crophones, regardless of price.
Miking Drums
There are many ways to mic drums and it seems that most every recording
or live sound engineer has their own way of doing so. Our objective is not
to indicate which drum miking approach is better, but to make suggestions
and look at advantages and disadvantages of each. Every engineer or pro-
ducer uses their own methods to obtain the results they desire, and that’s
what matters.
Multi-microphone Method
The objective in multi-microphone drum miking is to place a separate
microphone on either most or all the elements of a drum set. Typically,
separate mics are used on snare, toms, high-hat and kick drum with one
or two overhead microphones. The overhead mics pick up the overall
sound of the drums including cymbals, which are typically not miked
separately. With this method, the mixing engineer can control the level,
and signal processing (limiting, EQ, etc.) for each element of the drum set
(toms, snare, hi-hat, etc.). This provides a great deal of control over the
sound of the entire drum set and allows bringing out certain patterns on
sock cymbal, snare, etc. Multi-miked drums may be desirable when you
are recording in a large room with high ambient sound as it will reduce the
amount of unwanted room sound. Multi-miking is also a popular practice
for miking drums in “live sound” applications such as concerts, as it will
provide more gain before feedback in addition to greater control of the
drum mix.
No Phase Cancellation Issues
with Earthworks™Microphones
One of the typical disadvantages in the multi-microphone approach, when
using conventional microphones, is the interactive microphone phasing
problems that result in the cancellation of certain frequencies. These
phasing problems are a result of the poor polar response of conventional
microphones. Conventional microphones have a drastically different fre-
quency response between the front and sides of the microphone. It is
common for conventional microphones to have a loss of 10 to 20 dB at
high frequencies on the sides of the microphone. This is why you can
6
The various types of metal drum rims may have the bottom flange of the
rim either closer to the shell or further from the shell. Depending upon
the type of metal drum rim, one of the previously described three posi-
tions will allow the RimMount bracket to be mounted parallel to the drum
shell. The soft protective Polyolefin® coating on the RimMount bracket
will prevent the possibility of scratching the drum shell finish. Position the
rim-guide so the bottom edge “flange” of the drum rim fits comfortably
into one of the rim-guide grooves. This will insure that the cushioned rim-
guide remains securely in place as you tighten the thumbscrew to firmly
secure the RimMount to the drum rim.
Adjusting the Microphone Height
Once the RimMount is mounted securely on the drum rim with the DP30/C
microphone housed in the rubber holder, the microphone body can be
moved either up or down in the rubber holder to adjust the desired height.
Then the mini-gooseneck will provide a good amount of latitude in posi-
tioning the microphone head from any pre-set microphone body height.
Adjusting the height of the Drum Periscope microphone body is shown in
Figure 5-A and 5-B.
Figure 5-A and 5-B Adjusting DP30/C Microphone Height
Positioning the Microphone Head
Once the Drum Periscope microphone height has been set, then the mi-
crophone head can be positioned where you desire. However, you should
never place the microphone head “parallel” to the drumhead. The micro-
phone head should always be at “an angle” to the drumhead. This will
prevent any possibility of the diaphragm being forced to the microphone
back plate which could cause an unwanted pop or thump in the sound or
recording system.
9
A. B.

not place three singers on a conventional microphone, the one in front of
the mic sounds great, but the two on the sides have a dramatic loss of
quality. These drastic changes in high frequency response on the sides of
the microphone cause phase differences, and these are the root cause of
phase cancellations with conventional microphones.
In contrast, Earthworks has a patented polar technology that provides
our microphones with the same frequency response on the sides of the mi-
crophone as it does at the front (no more than a 3dB loss at any frequency
out to 90º off-axis). This very uniform frequency response at the front and
sides of the microphone will nearly eliminate any phasing issues when
using Earthworks microphones. In addition, Earthworks cardioid micro-
phones have a very high rejection of sounds at the rear (back) of the mi-
crophone. This feature will greatly reduce the leakage of cymbals or
other sounds at the rear of Earthworks microphones.
Close Miking Toms and Snares with the
DP30/C Drum Periscope Microphones
Inserting the DP30/C into the RM1 RimMount
It is suggested that you insert the Drum Periscope microphone into the
RM1 RimMount™ prior to attaching the RimMount to the drum.
To insert the Drum Periscope microphone into the RM1 RimMount™ just
place the mic head and the mini-gooseneck into the rubber holder from
the bottom of the RimMount. Then push the body of the microphone from
the bottom (XLR connector end) to move the microphone up inside the
rubber holder. The fit will be firm, so you will need to apply a little pres-
sure to move the microphone body up into the rubber holder. The sug-
gested procedure is illustrated in Figure 3.
Figure 3. Inserting the Drum Periscope™ Mic into the RimMount™
78
Mounting the RM1 RimMount to the Drum
The RM1 RimMount is designed for metal drum rims, and will not work on
wooden drum rims. While reading this section, please refer to Figure 4-A,
which refers to the various elements of the RimMount™. Mounting the
RimMount to the drum rim is quite easy. First, unscrew the thumbscrew
so there is more than enough space for the Delrin® cushioned rim-guide
to clear the bottom of the drum rim. Then determine where on the drum
rim you want to place the microphone and place the top “hook portion”
of the RimMount bracket over the top edge of the drum rim.
Figure 4-A. Elements of the RM1 RimMount™
Referring to Figure 4-B, notice that on the cushioned rim-guide there are
two sets of grooves. One set of grooves is in the “center” of the rim-guide,
while the other set of grooves is “off center” (or closer to the edge of the
rim-guide). These two sets of grooves provide you with “three” mounting
options: (1) placing the “off center” rim-guide grooves close to the drum
shell, (2) or rotating the “off center” grooves 180 degrees will place the
rim-guide further away from the drum shell, and (3) the “center” grooves
will allow placement in-between the positions described in 1 and 2.
Figure 4-B Positioning the Cushioned Rim-guide
Soft Polyolefin® Coated
Metal Bracket
Rubber
Holder
Delrin®
Cushioned Rim-guide
Hook Portion
of Bracket
Thumbscrew
Offset Groove
Positioned
on Left
Offset Groove
Positioned
on Right
Centered
Grooves
NOTES
13
Other manuals for CMK4 CloseMic Kit
1
This manual suits for next models
1
Other Earthworks Microphone System manuals
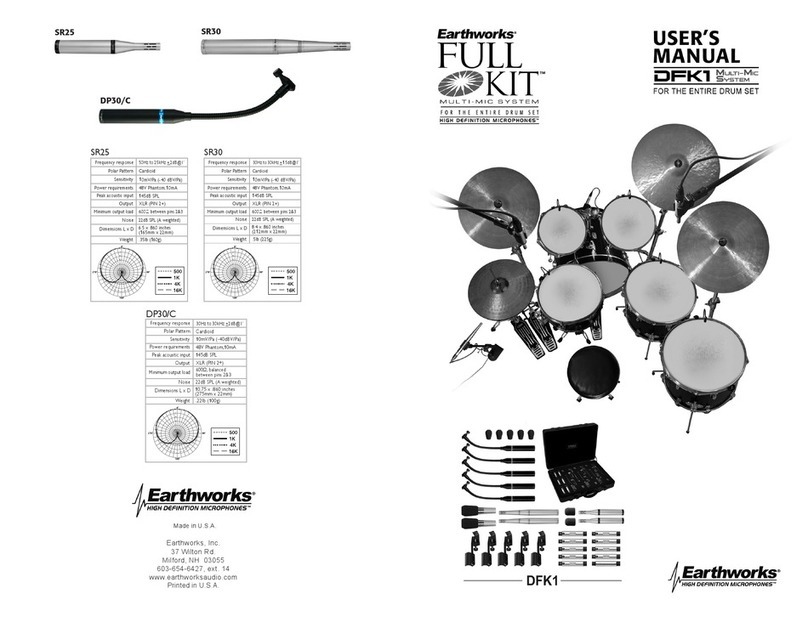
Earthworks
Earthworks SR25 User manual

Earthworks
Earthworks FlexWand FW730 User manual

Earthworks
Earthworks DP25C User manual
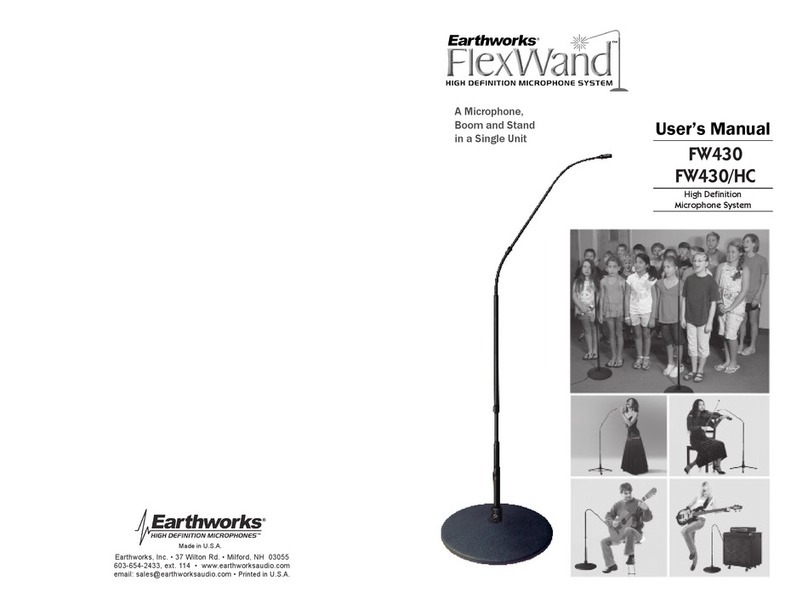
Earthworks
Earthworks FlexWand FW430 User manual

Earthworks
Earthworks PM40T User manual

Earthworks
Earthworks PM40T User manual

Earthworks
Earthworks PM40T User manual

Earthworks
Earthworks PianoMic PM40 User manual
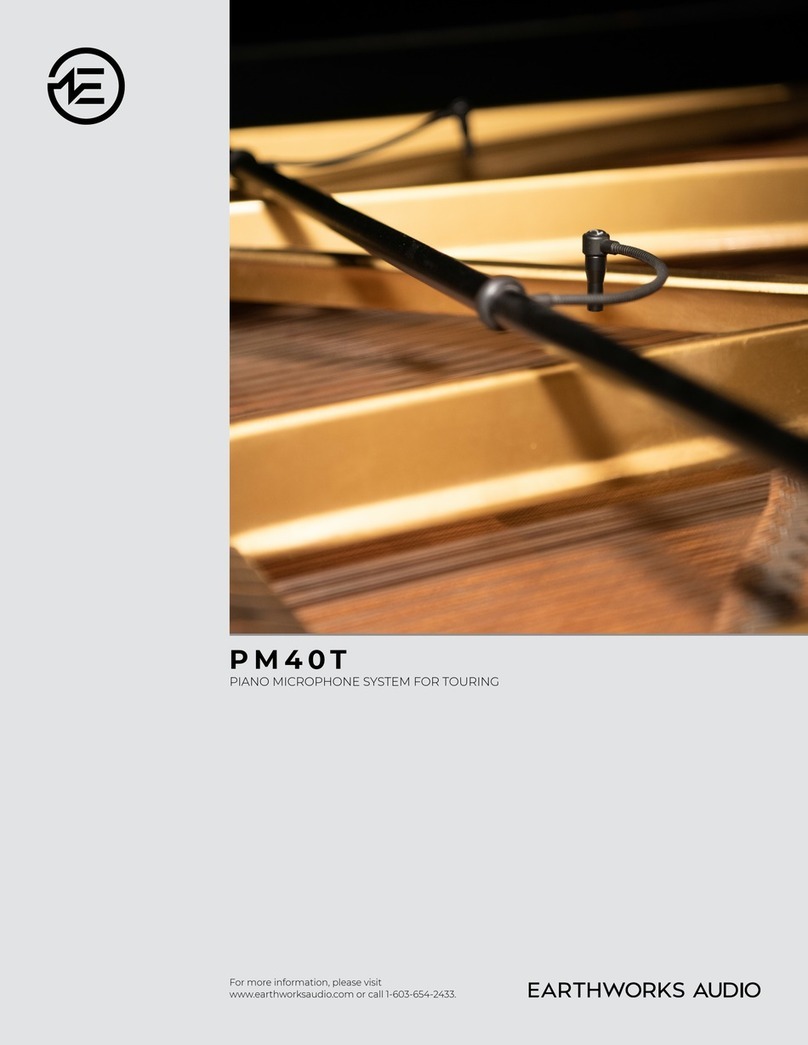
Earthworks
Earthworks PM40T Operator's manual

Earthworks
Earthworks FlexWand FW730 User manual