Econ T2-CAN-HS68D User manual

SHENZHEN ECON TECHNOLOGY CO.,LTD User Manual For CANopen Hybrid Servo Driv
T2-CAN-HS68D
CANopen Hybrid Servo Drive
© 2017 shenzhen ECON Technology Co.,Ltd. Version 2.0
Add: 2F,Building B,Jintai Industrial Park,Hangcheng Avenue,Gushu Village,Xixiang Street,Bao'an Area,Shenzhen
City,Guangdong Province,China
Tel: +86 136 2096 1024
E-mail:[email protected]
All rights reserved
[Please read this manual carefully before use to avoid damage the drive]

SHENZHEN ECON TECHNOLOGY CO.,LTD User Manual For CANopen Hybrid Servo Driv
Contents
1 Descriptions.............................................................................................................................................................. 4
2 Features.................................................................................................................................................................... 4
3 Applications.............................................................................................................................................................. 4
4 Specifications............................................................................................................................................................ 4
4.1 Electrical Specifications................................................................................................................................ 4
4.2 Operating Environment ................................................................................................................................. 5
5 Mechanical Specifications........................................................................................................................................ 5
6 Connectors and Pin Assignment............................................................................................................................... 6
6.1 Control signals connector.............................................................................................................................. 6
6.2 Encoder Feedback and hall signal Connector............................................................................................... 7
6.3 Power and Motor........................................................................................................................................... 7
6.4 CANopen Communication Port..................................................................................................................... 8
7 DIP Switch Settings .................................................................................................................................................. 9
7.1 T2-CAN ID Table........................................................................................................................................... 9
8 Hybrid servo Motors............................................................................................................................................... 10
8.1 Nema24 and Nema34motor......................................................................................................................... 10
8.2 Nema34motor .............................................................................................................................................. 10
9 Wiring Diagrams .....................................................................................................................................................11
9.1 Interface........................................................................................................................................................11
9.2 Diagram for CANopen communication........................................................................................................11
10 Protection Indications............................................................................................................................................11
11 CANopen protocol and parameters....................................................................................................................... 12
11.1 CANopen protocol...................................................................................................................................... 12
11.2 Common Object Table—factory parameters list........................................................................................ 12
11.3 Operation mode and control parameters list............................................................................................. 17
12 Frequently Asked Questions ................................................................................................................................. 17
Problem Symptoms and Possible Causes........................................................................................................... 18
13 Warranty ............................................................................................................................................................... 18
Exclusions.......................................................................................................................................................... 19
Obtaining Warranty Service .............................................................................................................................. 19
Warranty Limitations......................................................................................................................................... 19
Contact us:................................................................................................................................................................. 19

SHENZHEN ECON TECHNOLOGY CO.,LTD User Manual For CANopen Hybrid Servo Driv
Notice!
Read this manual carefully before any assembling and using. Incorrect handling of products in this manual can
result in injury and damage to persons and machinery. Strictly adhere to the technical information regarding
installation requirements.
This manual is not for use or disclosure outside of ECON technology except under permission. All rights are
reserved. No part of this manual shall be reproduced, stored in retrieval form, or transmitted by any means,
electronic, mechanical, photocopying, recording, or otherwise without approval from ECON technology. While
every precaution has been taken in the preparation of the book, ECON technology assumes no responsibility for
errors or omissions. Neither is any liability assumed for damages resulting from the use of the information
contained herein.
This document is proprietary information of ECON technology that is furnished for customer use ONLY.
Information in this document is subject to change without notice and does not represent a commitment on the part
of ECON technology. Therefore, information contained in this manual may be updated from time-to-time due to
product improvements, etc., and may not conform in every respect to former issues.
\/’

SHENZHEN ECON TECHNOLOGY CO.,LTD User Manual For CANopen Hybrid Servo Driv
1 Descriptions
T2-CAN HS68Dis our new CANopen network driver, which adopt the latest 32-bit DSP digital processing technology, the
advanced vector control technology drive the motor with low heating ,low noise and extra smoothly. The user can set any ID address
within 1-255 and any current value under the rated current, it can be matched with different of size motors(from Nema23-Nema34) to
applied for variable applications. the drive can auto-tuning for matching the motor when power up, which can automatically generate
optimal operating parameters for different motors to maximize the performance of the motor.
2 Features
Latest 32bit DSP Technology
Serial Port And Auto Tune Function
4 channel opto-coupler isolation OC output
1 channel analogy input(0~5V)
Advanced vector control technology
High torque at starting and low speed
5 channel opto-coupler isolation input,2 of them are high speed opto-coupler isolation input
Communication Frequency up to 1Mhz(default is 1Mhz)
Current setting range 0.1-8A
Smooth movement and extra low noise
Quick response, no delay and zero settling time
No loss of steps; no hunting; no overshooting
3 Applications
For a variety of small and medium-sized automation equipment and instruments, such as: AGV, speed pass door,
engraving machine, marking machine, cutting machine, laser Phototypesetting, router machine, plotter, CNC
machine tools, automatic assembly equipment. The users can get special effect from small noise, high speed
equipment application.
4 Specifications
4.1 Electrical Specifications
Description
T2-CAN- HS68D
Min
Typical
Max
Unit
Output Current(peak)
0.1
-
8.0
A
Input Voltage(DC)
15
36
50
VDC
Control Signal Input Current
6
10
16
mA
Control Signal Voltage
4.5
5
28
Vdc
OC output Pull-Up voltage
4.5
-
24
Vdc
CANopen communication
frequency
-
100
-
MHz
Insulation Resistance
100
MΩ
Analogy voltage input
0
5
Vdc

SHENZHEN ECON TECHNOLOGY CO.,LTD User Manual For CANopen Hybrid Servo Driv
4.2 Operating Environment
Cooling
Natural Cooling or Forced cooling
Environment
Condition
Far away from other heating device, Avoid dust, oil fog
and corrosive gases, heavy humidity and strong vibration
occasion, forbid flammable gases and conductive dust
Temperature
-10℃~+50℃
Humidity
40 ~90%RH
Vibration
5.9m/s2MAX
Storage Environment
-20℃~60℃
Altitude
Less than 1000m
Weight
about 0.2KG
5 Mechanical Specifications
※Recommend side installation, better cooling effect, when design installation dimension, consider the terminal
size and wiring!
Enhance Cooling method
A:The driver's reliable operating temperature is usually within 60 ℃, the motor operating temperature is within
80 ℃;
B: It is recommended to use the automatic half-flow mode, the current will be automatically reduced by half when
the motor stops, so as to reduce the heating of the motor and the drive;
C: When installing the driver, please use the vertical side installation, so that the cooling teeth form a strong air
convection; when necessary, install a fan where is close to the drive, forced cooling to ensure that the drive is in a
reliable working temperature range

SHENZHEN ECON TECHNOLOGY CO.,LTD User Manual For CANopen Hybrid Servo Driv
6 Connectors and Pin Assignment
The T2-CAN-HS68D has four connectors, connector for i/o connections, connector for Encoder Feedback and hall
signal, connector for power and motor connection, and the CAN Communication Port
6.1 Control signals connector
Pin Function
Details
pl+
Pulse signal: In Pulse+direction mode, this input represents pulse signal,active at each
rising or falling edge, In CW/CCW mode, this input represents clockwise (CW) pulse,
active both at each high level and low level. 4-28V for PUL-HIGH, 0-0.5V for
PUL-LOW. For reliable response,pulse width should be longer than 1.5μs
pl-
dr+
Dir signal: In Pulse+direction mode, this signal has low/high voltage levels representing
two directions of motor rotation; in CW/CCW mode (software configurable), this signal
is counter-clock (CCW) pulse,active both at high level and low level (software
configurable). For reliable motion response, DIR signal should be ahead of PUL signal
by 2.5μs at least. 4-28V when DIR-HIGH,0-0.5V when DIR-LOW. Please note that
rotation direction is also related to motor-Drive wiring match. Exchanging the
connection of two wires for a coil to the Drive will reverse motion direction. For
reliable response,pulse width should be longer than 1.5μs
dr-
in+
Low speed signal:in1,in2,in3 common postive input,5-28VDC
in1
Low speed in1 negative input
in2
Low speed in2 negative input
in3
Low speed in3 negative input
ot-
Common negative OC emitter output,ot1,ot2,ot3 emitter OC output common terminal
ot1
ot1 emitter output,the Max pull-up voltage 24Vdc,the pull-up resistance 2KΩ,the Max
output current 100mA
ot2
ot2 emitter output,the Max pull-up voltage 24Vdc,the pull-up resistance 2KΩ,the Max
output current 100mA
ot3
ot3 emitter output,the Max pull-up voltage 24Vdc,the pull-up resistance 2KΩ,the Max
output current 100mA
Ot4
Ot4 emitter output,the Max pull-up voltage 24Vdc,the pull-up resistance 2KΩ,the
Max output current 100mA
5V
Provide 5V voltage to analogy input, current 50mA
]I/O signal
Encoder
Motor
Power input

SHENZHEN ECON TECHNOLOGY CO.,LTD User Manual For CANopen Hybrid Servo Driv
Ain
Analogy input, input range 0-5V
gnd
Analogy input reference terminal negative
6.2 Encoder Feedback and hall signal Connector
Pin Function
Details
ea+
Encoder channel A input
ea-
eb+
Encoder channel B input
eb-
ez+
Encoder channel Z input(if there is Z signal in encoder ,no connection needed )
ez-
eu+
Hall U channel U input, special for dc brushless servo, open loop/hybrid servo no
connection needed
eu-
ev+
Hall V channel U input, special for dc brushless servo, open loop/hybrid servo no
connection needed
ev-
ew+
Hall W channel U input, special for dc brushless servo, open loop/hybrid servo no
connection needed
ew-
5V
Provide 5V+ dc power to motor encoder and Hall components, current 100mA
gnd
5V-
6.3 Power and Motor
Pin
Definition
I/O
Description
1
A+
O
Motor Phase A+
2
A-/U
O
Motor Phase A- (U for dc brushless servo motor)
3
B+ /V
O
Motor Phase B+ (V for dc brushless servo motor)
4
B- /W
O
Motor Phase B- (W for dc brushless servo motor)
5
+VDC
I
15-50VDC,36VDC is recommended, leaving rooms for voltage fluctuation
and back-EMF.
6
GND
GND
Power supply voltage between the provisions of the normal work, E5-CAT driver is best to use non-regulated DC
power supply, can also use the transformer step-down + bridge rectifier + capacitor filter. However, take care that
the peak value of the rectified voltage ripple does not exceed its maximum specified voltage. It is recommended
that users use DC voltage lower than the maximum voltage to supply power and avoid the fluctuation of power grid
beyond the working range of driver voltage.
If you are using a regulated switching power supply, be aware that the output current range of the switching power

SHENZHEN ECON TECHNOLOGY CO.,LTD User Manual For CANopen Hybrid Servo Driv
supply needs to be maximized.
Please note!
A: When wiring, pay attention to the positive and negative poles of the power supply.
B: Better use non-regulated power supply;
C: When use a non-regulated power supply, the power supply current output capacity should be greater than 60%
of the drive setting current;
D:The use of regulated switching power supply, the output current of the power supply should be greater than or
equal to the working current of the driver;
E:To reduce costs, two or three drives can share a power supply, but should ensure that the power supply is large
enough.
6.4 CANopen Communication Port
Two RJ45 terminals
PIN
Signal
Function Description
1
CANH
CANopen signal input
CAN IN
2
CANL
CANopen signal low input
3
NC
No wiring,reserve
4
EGNG
CANopen signal ground
5
EGNG
CANopen signal ground
6
NC
Reserved
7
EGNG
CANopen signal ground for shield ,used for
strong interference condition
8
EGNG
CANopen signal ground for shield ,used for
strong interference condition
9
CANH
CANopen signal high level output
CAN OUT
10
CANL
CANopen signal low level output
11
RS232-RXD
RS232 serial port,TTL -3.3V, for debugging
12
EGNG
CAN OPEN signal ground
13
EGNG
CAN OPEN signal ground
14
RS232-TX
RS232 serial port,TTL-3.3V,for debugging
CAN IN
]CAN OUT

SHENZHEN ECON TECHNOLOGY CO.,LTD User Manual For CANopen Hybrid Servo Driv
15
EGNG
CANopen signal ground for shield ,used for
strong interference condition
16
E5V
RS232 serial port 5V
Note: The cable connecting T2-CAN-HS68D to PC must be a dedicated cable. Please check before use to avoid
damage.
7 DIP Switch Settings
7.1 T2-CAN ID Table
ID
S1
S2
S3
S4
S5
Reserved
(Default)
On
On
On
On
On
1
Off
On
On
On
On
2
On
Off
On
On
On
3
Off
Off
On
On
On
4
On
On
Off
On
On
5
Off
On
Off
On
On
……
……
……
……
……
……
30
On
Off
Off
Off
Off
31
Off
Off
Off
Off
Off
Note: lower 5 ID set by DIP switches ,and higher 2 ID set by master.
The calculation formula of the ID as follows: ID=1*S1+2*S2+4*S3+8*S4+16*S5. The default ID value is 0,
0 indicates the broadcast address, you can set other addresses or higher address through the master or other
software.
CAN communication Baud-Rate Table
Baud Rate
SW6
SW7
100KHz(can be set by master)
On
On
DIP switch

SHENZHEN ECON TECHNOLOGY CO.,LTD User Manual For CANopen Hybrid Servo Driv
200KHz
Off
On
500KHz
On
Off
1MHz(Default)
Off
Off
CAN communication cable terminal resistor selection SW8:OFF=CAN R OFF,the default setting is OFF;
ON=CAN R ON
Note! The SW8 must be set ON
8 Hybrid servo Motors
T2-CAN-HS68D can work with the following ECON technology’s hybrid servo motors:
8.1 Nema24 and Nema34motor
TC60-30
TC86-45
Step Angle (Degree)
1.8
1.8
Holding Torque (N.m)
3.6
4.5
Phase Current (A)
6.0
6.0
Phase Resistance (Ohm)
0.7
0.325
Phase Inductance (mH)
1.9
3
Inertia (g.cm2)
2
)
0.91
1.4
Weight (Kg)
1.4
2.3
Encoder (lines / Rev.)
1000
1000
8.2 Nema34motor
TC86-85
TC86-120
Step Angle (Degree)
1.8
1.8
Holding Torque (N.m)
8.5
12
Phase Current (A)
6.0
6.0
Phase Resistance (Ohm)
0.5
0.73
Phase Inductance (mH)
6.0
8.68
Inertia (g.cm2)
2
)
2.7
4000
Weight (Kg)
3.8
5.3
Encoder (lines / Rev.)
1000
1000

SHENZHEN ECON TECHNOLOGY CO.,LTD User Manual For CANopen Hybrid Servo Driv
9 Wiring Diagrams
9.1 Interface
9.2 Diagram for CANopen communication
10 Protection Indications
The green indicator turns on when power-up. When drive protection is activated, the red LED blinks periodicity to
indicate the error type.

SHENZHEN ECON TECHNOLOGY CO.,LTD User Manual For CANopen Hybrid Servo Driv
Flashes Times
Red LED flash wave
Fault Description
1
over-current or phase short-circuit fault
2
over-voltage fault
3
under-voltage fault
7
over-error alarm
A:Over current or phase Short circuit protection
When a short circuit occurs or the internal drive over-current, the drive RED Led flashes 1 time, and repeat flashing
within 3 seconds. At this point must discharge fault, re-power and reset.
B: Over-voltage protection
When input voltage is higher than 55V, the driver RED Led flashes twice, and flashes repeatedly within 3 seconds.
At this point must discharge fault, re-power and reset.
△Note! Since the drive does not have the power supply reverse polarity protection function, therefore,
before power on, make sure the positive and negative power supply wiring is correct. Reverse polarity will
lead to burn the fuse in the drive!
11 CANopen protocol and parameters
T2-CAN HS68D hybrid servo drive is a standard CAN slave device that follows the standard CiA 301 and 402
sub-protocol stacks and any host controller(computer) that supports this protocol can communicate with it.
Currently, the PLC supports CANopen master function can modify the object dictionary (OD) of T2-CAN driver
through SDO communication to modify the status of the drive, operation mode and control parameters which
includes enable status, PP or PV mode, PI parameters of current loop & position loop, operating current proportion,
function of external IO port, alarm threshold and so on. Object Dictionaries can take OD Builder software to set the
properties of each object (read/write, read-only, write-only, and storable), defaults, and data types, and EDS files
are generated as master connection slaves identification documents.
11.1 CANopen protocol
T2-CAN-HS68D follows the CAN protocol as below
Follow CAN 2.0A standard
Follow CANopen standard protocol CiA 301 V4.02
Follow CANopen standard protocol CiA 402 V2.01
11.2 Common Object Table—factory parameters list
CANopen
address
Definition
Property
Default
value
Range
Description
2000+00
Peak Current
R/W/S
3200
1—Max
current
Max current set by drive
software(mA)。

SHENZHEN ECON TECHNOLOGY CO.,LTD User Manual For CANopen Hybrid Servo Driv
2001+00
Pulse/Resolution
R/W/S
50000
200—51200
pulse needed for one round
2002+00
Standby time
R/W/S
500
100—10000
Unit:ms
2005+00
Output 1
Function setting
R/W/S
1
1—4
bit0:alarm output
bit1:ready output
Bit2: PEND output
2006+00
Enable valid
level
R/W/S
1
0/1
0:high level
1:low level
2007+00
Disable mode
R/W/S
0
0/1
0:no response to pulse, motor unlock
1:no response to pulse, motor locked
2008+00
level setting for
Output 1
R/W/S
0
0/1
0:low level
1:high level
2009+00
Pulse filter
enable
R/W/S
0
0/1
0:Disable
1:Enable
2010+02
Filter time
R/W/S
1000
50—25600
Unit:us
2013+00
Current loop
auto-tuning
enable
R/W/S
1
0/1
0:Disable
1:enable
2015+00
Current loop Kp
R/W/S
1000
200—32767
Auto-tuning enable, only for read;
disable, user can write
2016+00
Current loop Ki
R/W/S
200
0—32767
Auto-tuning enable, only for read;
disable, user can write
2017+00
Current loop Kc
R/W/S
100
80—300
Auto-obtain, do not allow to modify
2020+00
Motor resistor
R/W/S
1000
1—20000
unit:m Ohms
2021+00
Motor
inductance
R/W/S
1
1—6000
Unit:uH
2024+00
open/closed
loop control
mode
R/W/S
2
0~2
1:open loop mode
2:close loop control mode
2025+00
Closed loop
control mode
R/W/S
5
0—10
0:DIPs selection 1:Lead 2:PM
3:FOC 4:Self-test 5:CL
2026+00
holding current
R/W/S
50
0—100
Unit:%,for open loop mode only
2029+00
Encoder
revolution
R/W/S
1000
200—60000
p/r
2030+00
Following error
R/W/S
1000
1—60000
p
2039+00
External
position sum H
R
0
0~65535
Receiving position command
accumulated value higher than 16bit
2040+00
External
position sum L
R/W
0
0~65535
Receiving position command
accumulated value lower than 16bit
Write:write 1 to clear counter
2041+00
Encoder
feedback sum H
R
0
0~65535
Encoder feedback sum higher than
16bit
2042+00
Encoder
feedback sum L
R/W
0
0~65535
Encoder feedback sum lower than
16bit

SHENZHEN ECON TECHNOLOGY CO.,LTD User Manual For CANopen Hybrid Servo Driv
Write:write 1,clear counter
2051+00
Motor running
direction
R/W/S
0
0/1
0:motor running direction unchanged
1:motor running direction reversed
2053+00
PEND output
level
R/W/S
0
0~1
0:low level 1:high level
2056+00
Fault detecting
selection
R/W/S
0xc3
0—0xffff
check the relevant documents
2057+00
Allow enable
signal to clear
fault?
R/W/S
0
0/1
0:not allowed
1:allow
2058+00
current soft start
time after motor
enable
R/W/S
1
0—10000
To reduce the rotor vibration when
motor power on and enable. Unit:
50us
2060+00
Frist
anti-vibration
amplitude
R/W/S
0
0—100
The first low-speed resonance
suppresses the amplitude
2061+00
First
anti-vibration
phase A
R/W/S
0
0—255
The first low-speed resonance
suppresses the phase A
2062+00
First
anti-vibration
phase B
R/W/S
0
0—255
The first low-speed resonance
suppresses the phase B
2063+00
Second
anti-vibration
amplitude
R/W/S
0
0—100
The second low-speed resonance
suppresses the amplitude
2064+00
Second
anti-vibration
phase A
R/W/S
0
0—255
The second low-speed resonance
suppresses the phase A
2065+00
Second
anti-vibration
phase B
R/W/S
0
0—255
The second low-speed resonance
suppresses the phase B
2066+00
Third
anti-vibration
amplitude
R/W/S
0
0—100
The third low-speed resonance
suppresses the amplitude
2067+00
Third
anti-vibration
phase A
R/W/S
0
0—255
The third low-speed resonance
suppresses the phase A
2068+00
Third
anti-vibration
phase B
R/W/S
0
0—255
The third low-speed resonance
suppresses the phase B
2069+00
The fourth
anti-vibration
amplitude
R/W/S
0
0—100
The fourth low-speed resonance
suppresses the amplitude
2070+00
The fourth
anti-vibration
phase A
R/W/S
0
0—255
The fourth low-speed resonance
suppresses the phase A

SHENZHEN ECON TECHNOLOGY CO.,LTD User Manual For CANopen Hybrid Servo Driv
2071+00
The fourth
anti-vibration
phase B
R/W/S
0
0—255
The fourth low-speed resonance
suppresses the phase B
2072+00
Z axis
anti-vibration
phase
R/W/S
0
0—255
Z axis low speed resonance
suppresses the phase
2083+00
Whether motor
shaft left and
right swing after
power on
R/W/S
0
0/1
0:no movement
1:left and right swing
2137+00
Position loop
KP
R/W/S
120
0~150
No
2138+00
Position loop KI
R/W/S
50
0~150
No
2139+00
Position loop
KVFF
R/W/S
70
0~150
No
2140+00
Speed loop KP
R/W/S
60
0~150
No
2150+00
CANopen slave
device address
the higher 2
R/W/S
0
0—3
Slave device address
2151+00
CANopen Baud
Rate
R/W/S
0—7
kBdi1MBaud 0 // 1 MBit/sec
kBdi800kBaud 1 // 800 kBit/sec
kBdi500kBaud 2 // 500 kBit/sec
kBdi250kBaud 3 // 250 kBit/sec
kBdi125kBaud 4 // 125 kBit/sec
kBdi100kBaud 5 // 100 kBit/sec
kBdi50kBaud 6 // 50 kBit/sec
kBdi20kBaud 7 // 20 kBit/sec
2152+01
Digital input 1
function
selection
R/W/S
1
0—32768
1:home signal 2:left limit
4:right limit 8:external enable
(coordinate AIO analogy input)16:
motor direction(coordinate AIO
analogy input)
2152+02
Digital input 2
function
selection
R/W/S
2
0—32768
1:home signal 2:left limit
4:right limit 8:external enable
(coordinate AIO analogy input)16:
motor direction(coordinate AIO
analogy input)
2152+03
Digital input 3
function
selection
R/W/S
4
0—32768
1:home signal 2:left limit
4:right limit 8:external enable
(matched with AIO analogy input)
16:motor direction(matched with
AIO analogy input)
2153+01
Digital input
1filter time
R/W/S
1000
50—60000
unit:us
2153+02
Digital input 2
R/W/S
1000
50—60000
unit:us

SHENZHEN ECON TECHNOLOGY CO.,LTD User Manual For CANopen Hybrid Servo Driv
filter time
2153+03
Digital input 3
filter time
R/W/S
1000
50—60000
unit:us
2154+01
Digital input 1
level polarity
configuration
R/W/S
0
0/1
0:constant
1:inversion
2154+02
Digital input
2level polarity
configuration
R/W/S
0
0/1
0:constant
1:inversion
2154+03
Digital input 3
level polarity
configuration
R/W/S
0
0/1
0:constant
1:inversion
2155+01
Digital input 1
level
R
0
0/1
0:low level
1:high level
2155+02
Digital input 2
level
R
0
0/1
0:low level
1:high level
2155+03
Digital input 3
level
R
0
0/1
0:low level
1:high level
2156+00
Analog AI port
function
selection
R/W/S
0
0/1
0:invalid
1:speed control
2157+00
Analog AI port
filter time
R/W/S
1000
50—60000
unit:us
2158+00
Analog AI port
dead zone
voltage
R/W/S
0
0—1000
unit:0.01V
2159+00
Analog AI port
bias voltage
R/W/S
0
0—1000
unit:0.01V
2160+01
Analog AI port
10V correspond
speed
R/W/S
500
0—2000
unit:0.1*R/S
2160+01
Analog AI port
ACC/DEC
speed
R/W/S
1
0—65535
unit:R/S/S
2161
Analogy or
CANopen
control mode
selection
R/W/S
0
0/1
0:CANopen mode
1:analog mode
2090+00
Save parameters
R/W
2091+00
Reset to default
value
R/W
2093+00
Clear alarm
record
R/W

SHENZHEN ECON TECHNOLOGY CO.,LTD User Manual For CANopen Hybrid Servo Driv
11.3 Operation mode and control parameters list
CANopen ID
Parameter
Property
Description
6040+00
Control word
R/W
0x06:motor power off
0x0F:motor power on
0x0B:fast stop, load stop-voltage off
0x2F-3F: absolute positioning
0x4F-5F:relative positioning
0x103F:enter the absolute positioning immediately according to
the target position changes
0x0F-1F:home positioning
0x80:clear internal fault
6041+00
Status word
R
display drive status
6060+00
Mode setting
RW
Operation mode:
1—PP mode
3—PV mode
6—Home mode
6061+00
Mode display
R
display drive operation status
607A+00
Target position
R/W
The target position of PP mode,if control word set as start
movement, turn to effective command position
6063+00
Actual position
R
display motor actual position
6081+00
Trapezoid
Velocity
R/W
The Max Trapezoid Velocity curve of PP mode
60FF+00
Target Velocity
R/W
The Max Velocity at home mode
606C+00
Actual speed
R/W
Display motor actual speed, unit:RPM
6083+00
Trapezoid
acceleration
R/W
Ladder curve acceleration
6084+00
Trapezoid
deceleration
R/W
Ladder curve deceleration
6098+00
Home mode
R/W
Find home mode
6099+01
Home mode speed
R/W
Find limit switch speed
6099+02
Home mode speed
R/W
Find home signal speed
609A+00
Home mode speed
R/W
Find home acceleration
607C+00
Home offset
R/W
Home offset
T2-CAN HS68D supports :PP(position mode)、 PV(speed mode)and Homing mode
12 Frequently Asked Questions
In the event that your drive doesn’t operate properly, the first step is to identify whether the problem is electrical or
mechanical in nature. The next step is to isolate the system component that is causing the problem.As part of this
process you may have to disconnect the individual components that make up your system and verify that they
operate independently. It is important to document each step in the troubleshooting process. You may need this

SHENZHEN ECON TECHNOLOGY CO.,LTD User Manual For CANopen Hybrid Servo Driv
documentation to refer back to at a later date, and these details will greatly assist our Technical Support staff in
determining the problem should you need assistance.
Many of the problems that affect motion control systems can be traced to electrical noise, controller software errors,
or mistake in wiring.
Problem Symptoms and Possible Causes
Problem
Possible Reason
Solution
Motor is not rotating
Power supply light is off
check power supply line, keep power supply
normal
motor shaft disabled
Pulse signal weak, increase signal current to
7-16mA
Micro-step too small
select the suitable micro-step
current setting is too small
Select the correct current
drive protected
Reboot
Enable signal too low
Pull up enable signal or disconnect
no action to control signal
Check the power supply input
Wrong motor motion
Motor cable incorrect
connect
Change any two cables of same phase(such as
A+/A- change)
Motor cable has breakage
Check and correct wiring connection
The drive In alarm
motor cable incorrect
connect
Check wiring
over-voltage or
under-voltage
Check power supply
motor or drive damaged
Replace a motor or drive
Position inaccurated
signal is interfered
Exclude interference
Shield ground disconnect or
bad connect
Reliable ground connection
Motor cable has breakage
Check and correct wiring connection
Wrong micro-step
Set correct micro-step
Current small
Increase current
Motor stall when
speed increase
Acceleration time is too
short
Increase acceleration time
Motor torque is too small
Select big torque motor
Voltage is low or current is
small
Suitable increase voltage and current
13 Warranty
Shenzhen ECON Technology Co., Ltd. warrants its products against defects in materials and workmanship for a
period of 12 months from shipment out of factory. During the warranty period, ECON technology will either, at its
option, repair or replace products which proved to be defective.

SHENZHEN ECON TECHNOLOGY CO.,LTD User Manual For CANopen Hybrid Servo Driv
Exclusions
The above warranty does not extend to any product damaged by reasons of improper or inadequate handlings by
customer, improper or inadequate customer wirings, unauthorized modification or misuse, or operation beyond the
electrical specifications of the product and/or operation beyond environmental specifications for the product.
Obtaining Warranty Service
To obtain warranty service, a returned material authorization number (RMA) must be obtained from customer
shipping charges for products returned to ECON technology for warranty service, and ECON technology shall pay
for return of products to customer.
Warranty Limitations
ECON technology makes no other warranty, either expressed or implied, with respect to the product. ECON
technology specifically disclaims the implied warranties of merchantability and fitness for a particular purpose.
Some jurisdictions do not allow limitations on how long and implied warranty lasts, so the above limitation or
exclusion may not apply to you. However, any implied warranty of merchantability or fitness is limited to the
12-month duration of this written warranty.
Contact us:
Shenzhen ECON Technology Co.,Ltd
Add: 2F,Building B,Jintai Industrial Park,Hangcheng Avenue,Gushu Village,Xixiang Street,Bao'an
Area,Shenzhen City,Guangdong Province,China
Tel: +86 136 2096 1024
Sales: [email protected]
Technical support: [email protected]
Table of contents
Popular DC Drive manuals by other brands
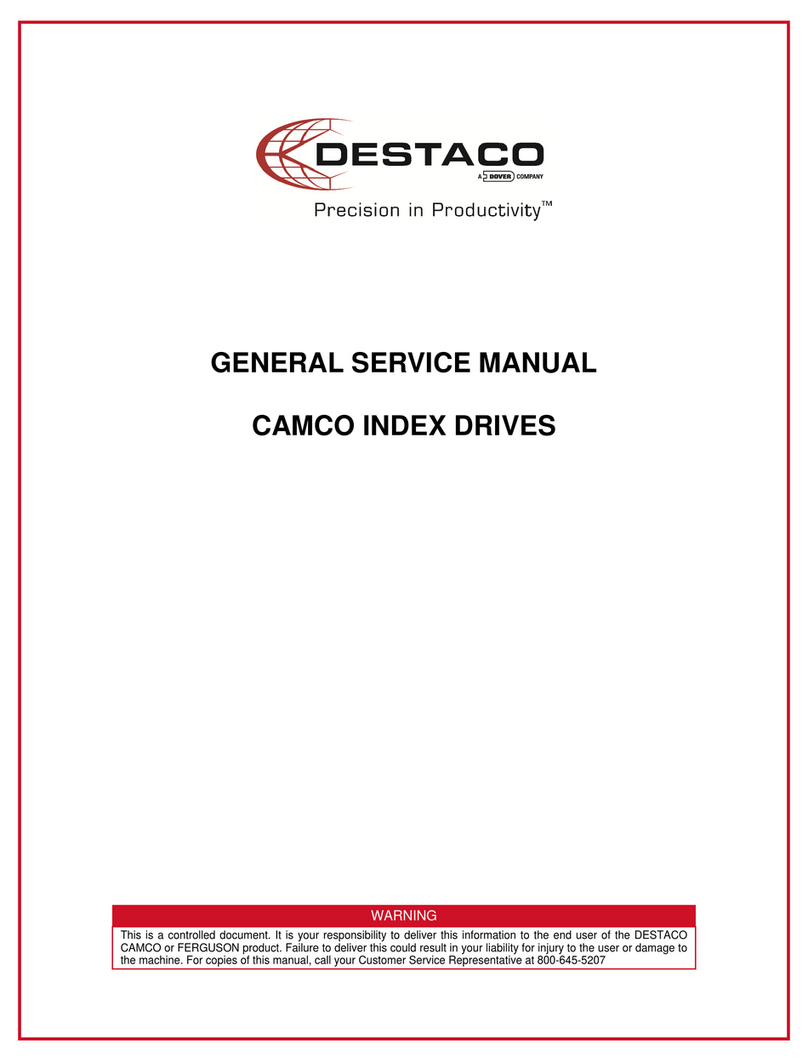
Dover
Dover DESTACO CAMCO 900P General service manual
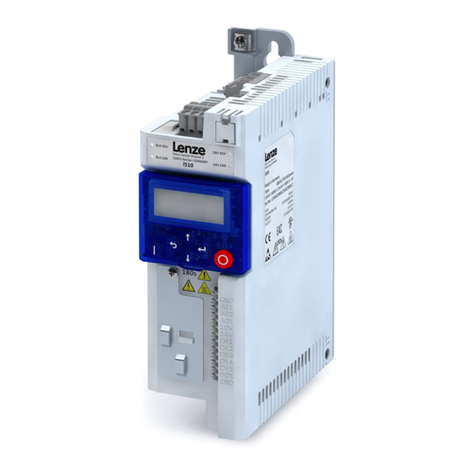
Lenze
Lenze i510 Series Mounting and switch-on instructions

American Control Electronics
American Control Electronics LGC410 Series Installation
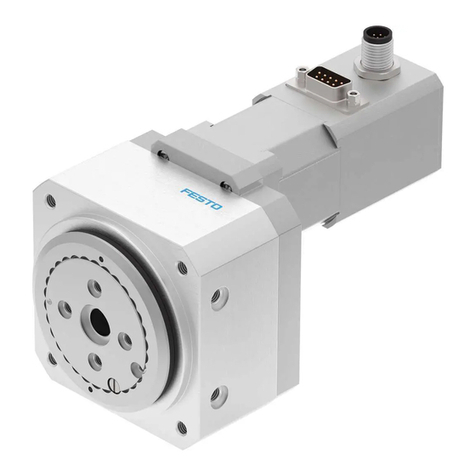
Festo
Festo ERMO operating instructions
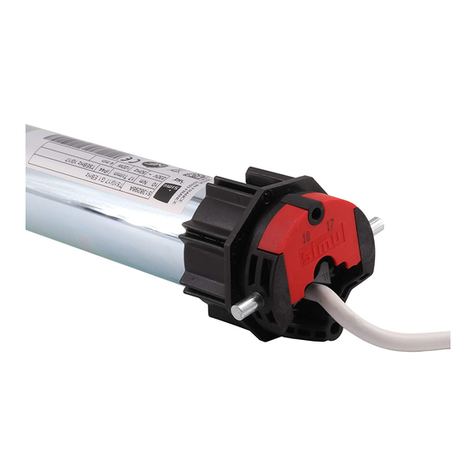
Simu
Simu T3.5EBHz Original instructions
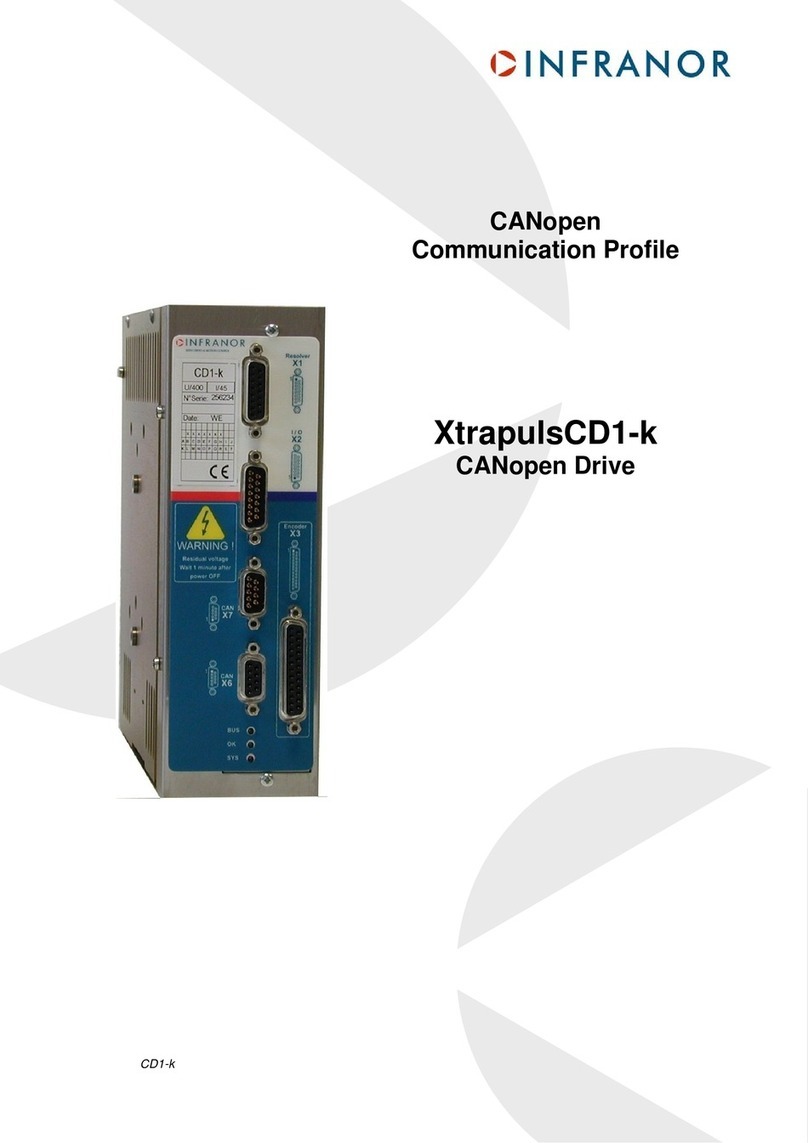
Infranor
Infranor XtrapulsCD1-k manual