ELKHART BRASS APEX-S Assembly instructions

98607000 REV-rel
Valve Controller
Installation, Operating, & Maintenance Instructions
1-574-295-8330
www.elkhartbrass.com

2
CONTENTS
INTRODUCTION ......................................................................................4
Overview ...........................................................................................4
Specications .......................................................................................5
Control Module ......................................................................................5
GENERAL DESCRIPTION ..............................................................................6
Components.........................................................................................6
Controls and Indicators...............................................................................7
INSTALLATION.......................................................................................8
Install Valve Controller ...............................................................................8
ELECTRICAL CONNECTIONS ..........................................................................10
Wiring the Valve Controller ...........................................................................12
MAINTENANCE/CALIBRATION........................................................................17
Automatic Valve Position Calibration for APEX-S .......................................................17
OPERATION ..........................................................................................19
Button Functions ....................................................................................19
PROGRAMMING MODE ...............................................................................20
Customizing Default Settings .........................................................................20

3
List of Figures
Figure 1. Controls and Indicators .......................................................................7
Figure 2. Valve Controller Mounting Dimensions ........................................................9
Figure 3. Valve Controller Wiring.......................................................................10
Figure 4. Valve Actuator Wiring ........................................................................11
Figure 5. Wiring (Cables and Connectors) ...............................................................13
Figure 6. Wiring (Cables and Connectors) ...............................................................14
Figure 7. APEX-S 1:1 Wiring Connections ...............................................................15
Figure 8. APEX-S 2:1 Wiring Connections ...............................................................16
List of Tables
Error/Warning Codes Troubleshooting Table ............................................................22

4
INTRODUCTION
Overview
The APEX-S electric valve controller is designed with precision and ease of use in mind.
Rugged design withstands the demands of outdoor apparatus use. Monitor the valve position
with ultra-bright LEDs.Tactile buttons provide enhanced user experience with intuitive and
familiar operation. Use keypad buttons to open, close and adjust valve position. All controls
and indicators are located on the front of the controller. Controls are simple push button style
controls.The controller is compatible with E14X and E16X (EB6D) electric valve actuators.
Features
. 10 Green LEDs Indicate Open Valve Position
. Red LED Indicates Valve is Closed
. Keypad–rubberized, large, embossed and color-coded Tactile Buttons (glove friendly)
. Button actions–Full Open, Full Close
. Automatic valve position calibration
. Auto-travel open and close
. Programmable LED intensity
. Automatic adjusting day/night LED intensity
. Enclosure– Molded Glass-filled Polymer for Rigidity, Surface Hardness and Strength
. Sealed to IP67 Ingress Protection on All Sides
. Visor–Color-coded in 12 Colors to Match Discharges to Valve Controller
. Datalink interface simplifies wiring between controller & valve
. Connector– Sealed Connectors (Power & CAN data/bus)
. CAN communication to Unibody valve using E14X/E16X
. Power Requirements–9 to 30 VDC; Less than 1 Watt Power Consumption

5
Specications
APEX-S Valve Controller
Supply Voltage: 9—30VDC
Current: 0.5 A - Display Module only.
Fuse Rating: 1 A (12V) & & 0.5 AMPS (24V)
Dimensions:
Height 3 31/32"
Width 3 5/8"
Depth 2 5/16"
Datalink Interface: CAN Bus

6
GENERAL DESCRIPTION
Components
The Electric Valve System consists of the following components:
. Valve Controller
. Valve with Actuator
. Cables
Valve Controller
The valve control and LED is sealed to an IP67 rating, and has dimensions of 3 31/32 inches
high by 3 5/8 inches wide by 2 5/16 inches deep. All controls and indicators are located on the
front of the module. (Refer to Controls and Indicators.)
Valve with Actuator
An Elkhart Unibody valve with an E14X (E16X for EB6D) actuator must be installed in the
apparatus plumbing and connected to the valve controller.
Cables
Interconnecting cables are provided. Refer to Electrical Connections (Wiring) section.

7
Figure 1. Controls and Indicators
Controls and Indicators
The display and pushbuttons controls are accessible on the front of the unit.
(Refer to Figure 1.)
Valve Position Indicator LEDs
Closed Indicator will be red when the valve is fully closed. As the valve moves from the closed
to fully open position the red closed LED will go out and the green LEDs will turn on one at a
time from left to right until all 10 of the green LEDs light up indicating the valve is fully open.
Valve Control Buttons
Two buttons open and close the valve.The third button (Preset) will move the valve to a
programmed position.
Color-Coded Visor
The Visor helps prevent water and dirt from running down the display. It can also be used to
color code the valve controller to match the corresponding discharge.
Valve Closed
Indicator
Visor
Valve Open position LEDs
(10% increments)
Valve Control
Buttons
APEX-S
Light
Sensor

8
INSTALLATION
The APEX valve controller is compatible with unibody valves used in 1.5 to 8 inch piping.
Install Valve Controller
1.Measure and mark mounting location for controller panel cutout and mounting screw holes.
Make sure there is clearance behind the panel for the display and cables before cutting
holes. Refer to Figure 2 for layout and dimensions.
2.Cut out a mounting hole according to the cutout diagram in Figure 2, and drill three holes
(clearance or tapped) for #10 mounting screws.
3.Connect the cables and wires. (Refer to Wiring section.)
4.*Place control module into position and secure with three screws.
Use #10 size, Phillips pan head type screws with a minimum length of 1.25 inch.
*NOTE: The Visor must be placed onto the valve controller housing prior to inserting
mounting screws and attaching to your apparatus.

9
Figure 2. Valve Controller Mounting Dimensions
2 5/16"
29 3/32"
Recommended Panel Cutout
#10 clear
(thru-bolt with nut)
or tapped for #10
fasteners, 3x
2 3/32"
2 3/32"
1 3/64"
2 9/16"
1 9/32"
3 1/16"
R 1/2"
1 17/32"
3 5/8"
3 31/32"

10
ELECTRICAL CONNECTIONS
Figure 3. Valve Controller Wiring
Valve Controller 6-Pin Connector
Pin Signal Description
1 Power 12/24 VDC
2 Ground Supply
3 NC
4 Datalink Shield
5 Datalink CAN Low
6 Datalink CAN High
Pin 1
6-Pin
Connector

11
Figure 4. Valve Actuator Wiring
Actuator 12-Pin Connector
Pin Signal Description
1 Power 12/24 VDC
2 Ground
3 Valve Position 5 VDC
4 Valve Position Ground
5 Valve Position Signal
6 Valve Control (–)
7 Valve Control (+)
8 CLOSE
9 PRESET
10 OPEN
11 Datalink CAN High
12 Datalink CAN Low
12-Pin
Connector
Pin 1
6-Pin
Connector
Pin 1
NOTE: 6-Pin Connector is not used with the
APEX-S. Leave sealed plug in place.

12
Wiring the Valve Controller
For a single APEX-S controlling one valve, see diagram on page 15:
1. Connect power and ground to the controller. Use 1 amp fuse for 12v (0.5 amp for 24v)
on positive controller leads.
2. Connect CAN wiring from the APEX-S to the valve. See Wiring Diagrams on the
following page for pin positions and wire colors for wiring a APEX-S.
3. When done there should be continuity between the CAN LOW contacts (Yellow wires
in connector position A), CAN HIGH contacts (Green wires in connector position B),
and CAN SHIELD contacts (Black wires in connector position C) throughout the entire
CAN communication wiring harness.**
For two APEX-S controllers to be controlling one valve, see diagram on
page 16:
1. Connect power and ground to the controllers. Use 1 amp fuse for 12v (0.5 amp for
24v) positive controller leads.
2. Connect CAN wiring from the first APEX-S to a CAN splitter at the valve and then onto
the second APEX-S.
3. Replace the terminated CAN leads going to positions 11 &12 in valves 12 pin connector
with the non-terminated version - Cable D. Plug the triangular connector into the CAN
splitter as shown.The wire length from one APEX-S to the other should not exceed 131 ft.
(40 m) when added together.
4. When done there should be continuity between all CAN LOW contacts (Yellow wires
in connector position A), CAN HIGH contacts (Green wires in connector position B),
and CAN SHIELD contacts (Black wires in connector position C) throughout the entire
CAN communication wiring harness.**
NOTE: ** CAN Shield (black wire connector position C) stops at valve connector

13
6-Pin Plug
Connector
3-Pin Receptacle
Connector
Butt Splice
Connectors
Terminating
Resistor
To APEX-S
Valve
Controller
+12 VDC
GND
Red
Black
Cable A–Display Cables withTerminating Resistor
(P/N 37542000)
12-Pin Plug
Connector
2-Pin
Connector
Butt Splice
Connectors
To APEX-S
Valve
Controller
+12 VDC
GND
Red
Black
Cable C–Valve Controller Cables
(P/N 37544000)
Terminating
Resistor 3-Pin Receptacle
Connector
Figure 5. Wiring (Cables and Connectors)

14
Figure 6. Wiring (Cables and Connectors)
Cable D–Valve Controller Cable withoutTerminating Resistor
P/N 375440NT
Connectors
3-Pin Plug
Connector
Cable E–APEX Extension Cable
P/N 37543002 - 2'
P/N 37543010 - 10'
P/N 37543015 - 15'
P/N 37543020 - 20'
P/N 37543030 - 30'
P/N 37543040 - 40'
To APEX
Valve
Controller
3-Pin Plug
Connector
3-Pin Plug
Connector
CAN Network
Y Splitter
F–Splitter
P/N 24196000

15
APEX-S Wiring 1:1 Connections
Figure 7. APEX-S 1:1 Wiring Connections
A
C
E

16
APEX-S Wiring 2:1 Connections
Figure 8. APEX-S 2:1 Wiring Connections
A
A
E
E
F
D
Replaces CAN Lead
with termination

17
MAINTENANCE/CALIBRATION
!
Important: All valves must have the position calibrated after installation.
NOTE: If using an EB_J or EB_S butterfly valve refer to ”Valve Polarity“ in the Programming Mode
section on page 21. This programming must be done before performing the automatic valve position
calibration.
Automatic Valve Position Calibration for APEX-S
The valve position calibration determines the point where the valve is fully open or fully
closed.This process will automatically determine these points by running the valve to the fully
closed position then the fully open position, and then back to the fully closed position.This
calibration must be done after installation, when the actuator has been replaced, or in any
case when valve does not fully close or fully open.
NOTE: These routines must be utilized so the position of the valve will be displayed accurately.
Valve Calibration (CODE 1113)
1.Turn on power to the valve and controller(s).
Enter Code 1113
2.Press and hold the CLOSE button; then press and hold the OPEN button. After 5 seconds, the red
CLOSE LED will flash. Code 1113 can now be entered.
3.Use the OPEN button to set the first digit of the code 1113. Press the OPEN button once, one
green LED on.
4.Press the CLOSE button to move the cursor to the next digit for the second digit to be entered.
Press the OPEN button once, one green LED on.
5.Press the CLOSE button to move the cursor to the next digit for the third digit to be entered.
6.Press the CLOSE button to move the cursor to the next digit for the fourth digit to be entered.
Press the OPEN button three times. Valve calibration begins approximately 4 to 5 seconds after
the last digit is entered for Code 1113.
7.The valve will move to the closed position, calibrate to the closed position, then move to the open
position, calibrate that position and then return back to the closed position and stop. While the
valve is calibrating the LEDs on the controller will turn on and off on at a time from left to right.
When calibration is complete all 11 LEDs will flash several times and then the red closed LED will
stay on solid. The valve is now position calibrated.

18
Maintenance Instructions
Preventive Maintenance
The control system should be inspected during each apparatus check. Inspect the valve
controller, wiring, and valve for damage.
• Operate all possible functions to ensure that each works normally
• Fully open and fully close valve to check for full range operation
• During valve check, inspect rotation for smoothness and seats/seals for leaks
• Inspect all exposed wiring for signs of damage

19
OPERATION
On power-up the valve controller will be in the normal operating mode.The green OPEN, red
CLOSE, and yellow PRESET buttons will control valve position.The yellow PRESET button will set
the valve to a programmed position. Once a preset position has been programmed, pressing the
PRESET button will move the valve to that position.
The red LED will be on when the valve is in the fully closed position. The 10 green LED indicators
will show the valve position. Each LED indicator signifies 10 percent of the valve position.When
the valve is in the fully open position, all 10 of the green LEDs will be lit.
All information is supplied to the controller from the E14X or E16X electric actuator on the CAN bus.
Button Functions
Button Operations
Green OPEN button: Press and hold to drive a valve toward the Open position. Valve
will stop when the button is released, or when it is fully open.
Red CLOSE button: Press and hold to drive a valve toward the Closed position. Valve
will stop when the button is released, or when it is fully closed.
Yellow PRESET button: Press and release once; upon release the LED for programmed
preset position will flash and the valve will travel to that position and stop there.
To program a preset position move the valve to the desired position (full closed of full open or
anywhere in between) then press and hold the preset button until the valve position LED starts
flashing. Let up on the preset button and wait for the position LED to stop flashing.The new
preset position is now set.
AutoTravel OPEN and AutoTravel CLOSE
The auto travel OPEN method will fully open the valve when initiated.
1.Press and hold the OPEN button
2.While holding the OPEN button, press and release the CLOSE button
3.Release the OPEN button and the valve will automatically travel to the fully open position
The auto travel CLOSE routine will fully close the valve when initiated.
1.Press and hold the CLOSE button
2.While holding the CLOSE button, press and release the OPEN button
3.Release the CLOSE button and the valve will automatically travel to the fully closed position.
Setting the PRESET Position
To set or change the preset position:
1.Use the OPEN or CLOSE buttons to move the valve to the desired position.
(This can be fully closed, fully open, or somewhere in between.)
2.Press and hold the PRESET button for until the LED(s) flash.
3.Release the PRESET button and do not operate the valve until the LED(s)
stop flashing.
Once the LED(s) stop flashing the new preset position will be saved.

20
PROGRAMMING MODE
Customizing Default Settings
Programming mode allows the user to customize some default settings on the controller.
When in programming mode, the position of the LEDs is used to program the valve controller
to the desired settings.
NOTE: The valve must be closed and the red CLOSED LED must be on to enter program mode.
Entering Program Mode
Press and hold the CLOSE button, then press and hold the OPEN button. After 5 seconds the
red CLOSED LED will flash. A program code can now be entered.
Daytime LED Intensity (CODE 318)
NOTE: Operator must be in programming mode with the red CLOSED LED flashing to make changes.
1.Use the OPEN button to set the first digit of the code 318, three green LEDs on. Each time the OPEN
button is pressed the next LED will illuminate.
2.Press the CLOSE button to move the cursor to the next digit. Now all LEDs will be off and ready for the
second digit to be entered. Press the OPEN button once, one green LED on.
3.Press the CLOSE button to move the cursor to the next digit. All LEDs will be off. Press the OPEN
button eight times, eight green LEDs on.
4.After 3 seconds all the LEDs will turn on at the current brightness level. Use the OPEN and CLOSE
buttons to scroll through the intensity levels.
5.Once the desired brightness level has been reached, press and hold the PRESET button for 3 seconds
to accept the setting. The valve controller will resume normal operation.
Nighttime LED Intensity (CODE 317)
Follow the instructions from the Daytime LED Intensity setup to set a Nighttime LED Intensity
level. Only press the button seven times in step three to enter the code 317, instead of 318.
Table of contents
Other ELKHART BRASS Controllers manuals
Popular Controllers manuals by other brands
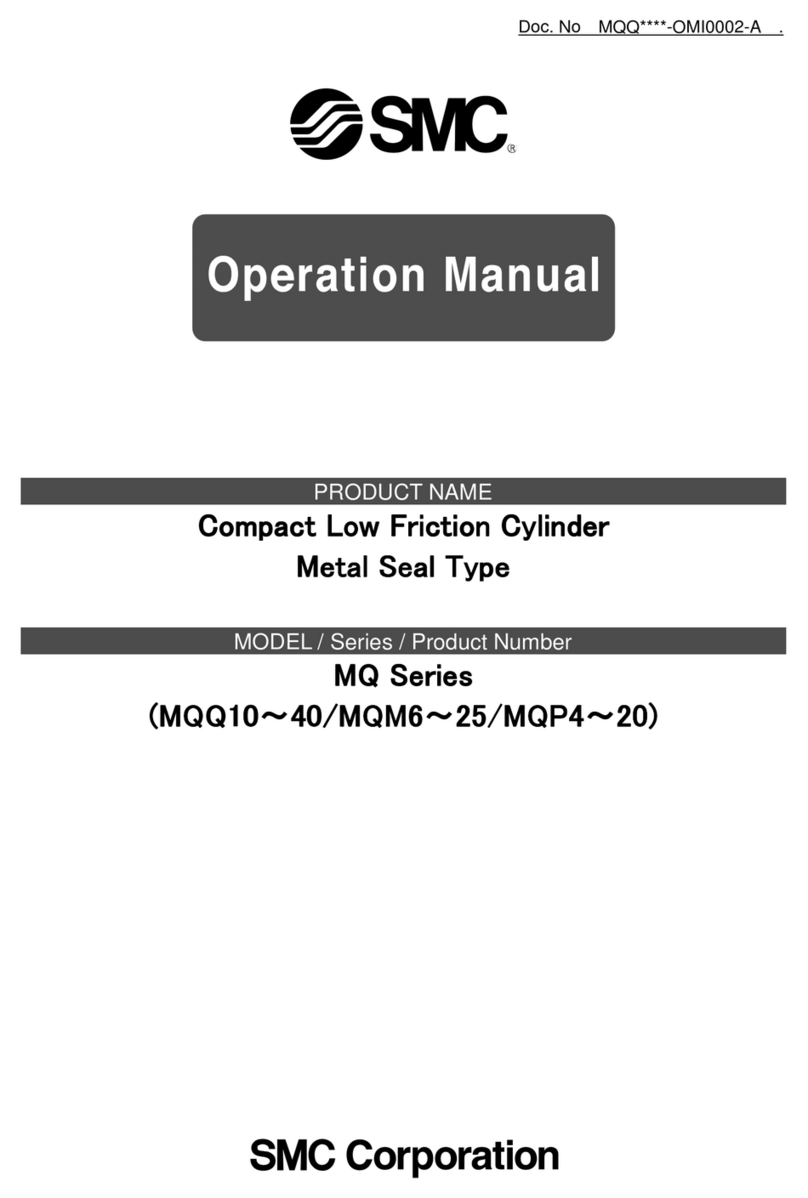
SMC Networks
SMC Networks MQ Series Operation manual
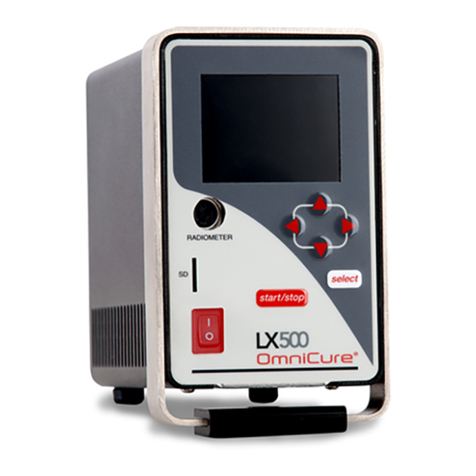
Excelitas Technologies
Excelitas Technologies OmniCure LX500 Installation reference guide
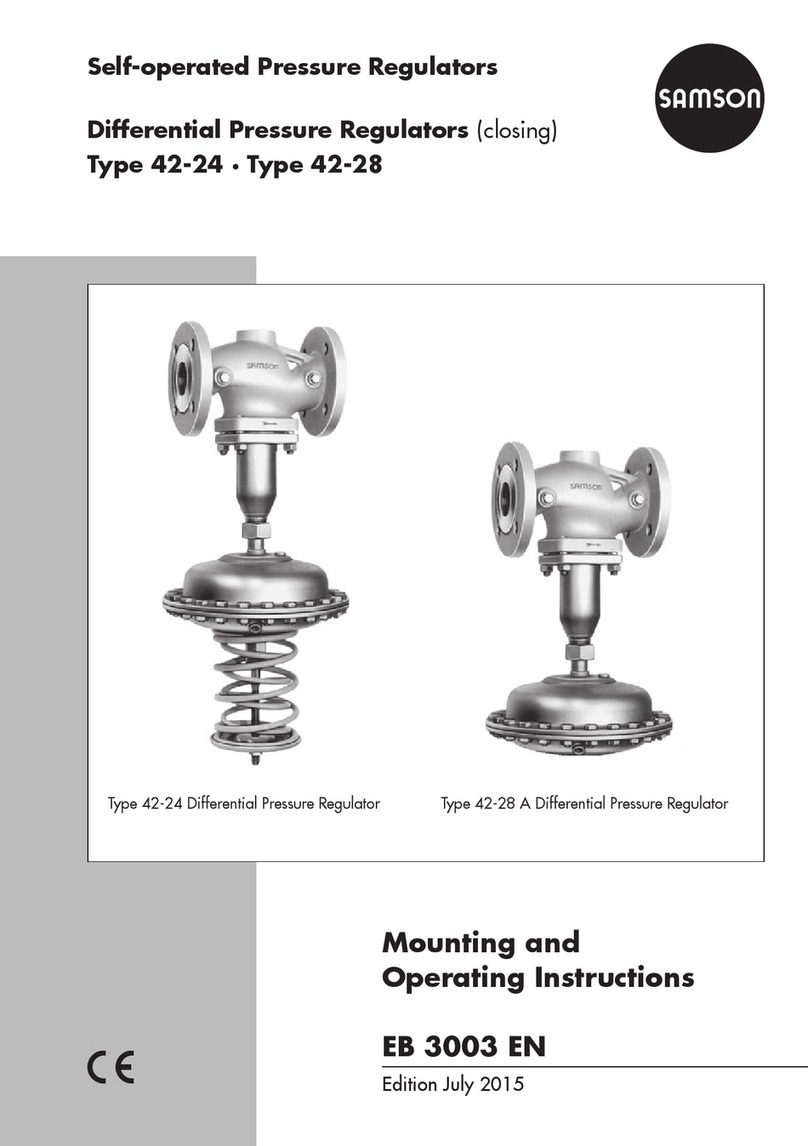
Samson
Samson 42-24 Mounting and operating instructions
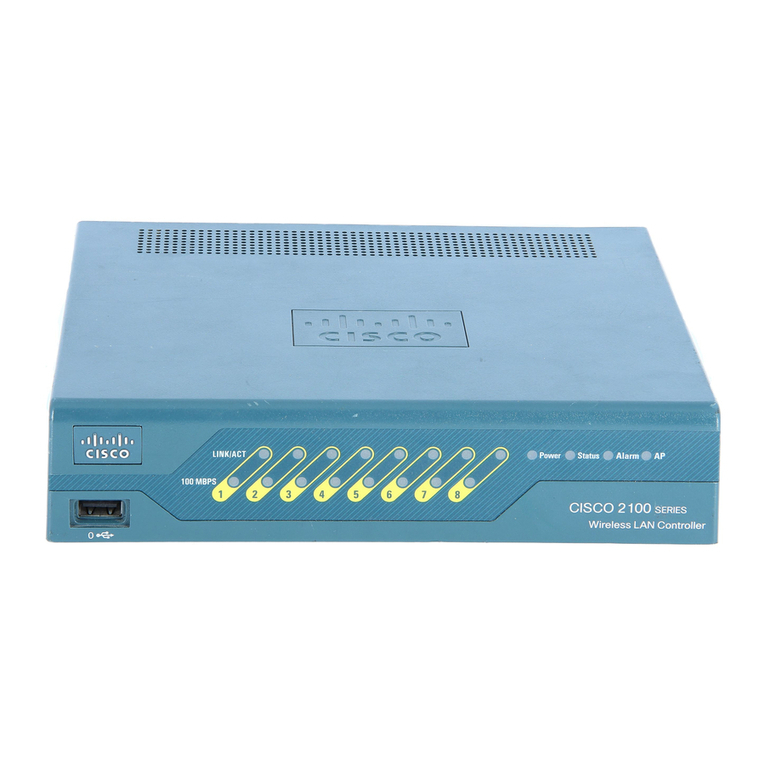
Cisco
Cisco 2100 Series Configuration guide
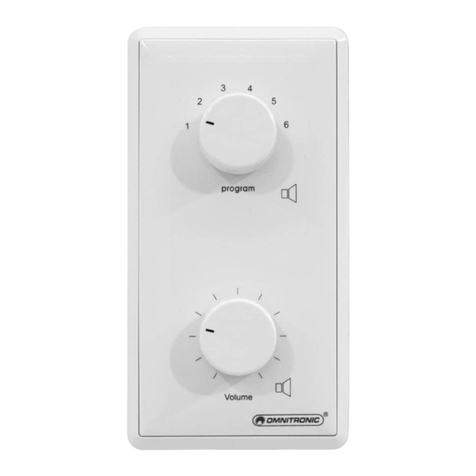
Omnitronic
Omnitronic 80711081 user manual
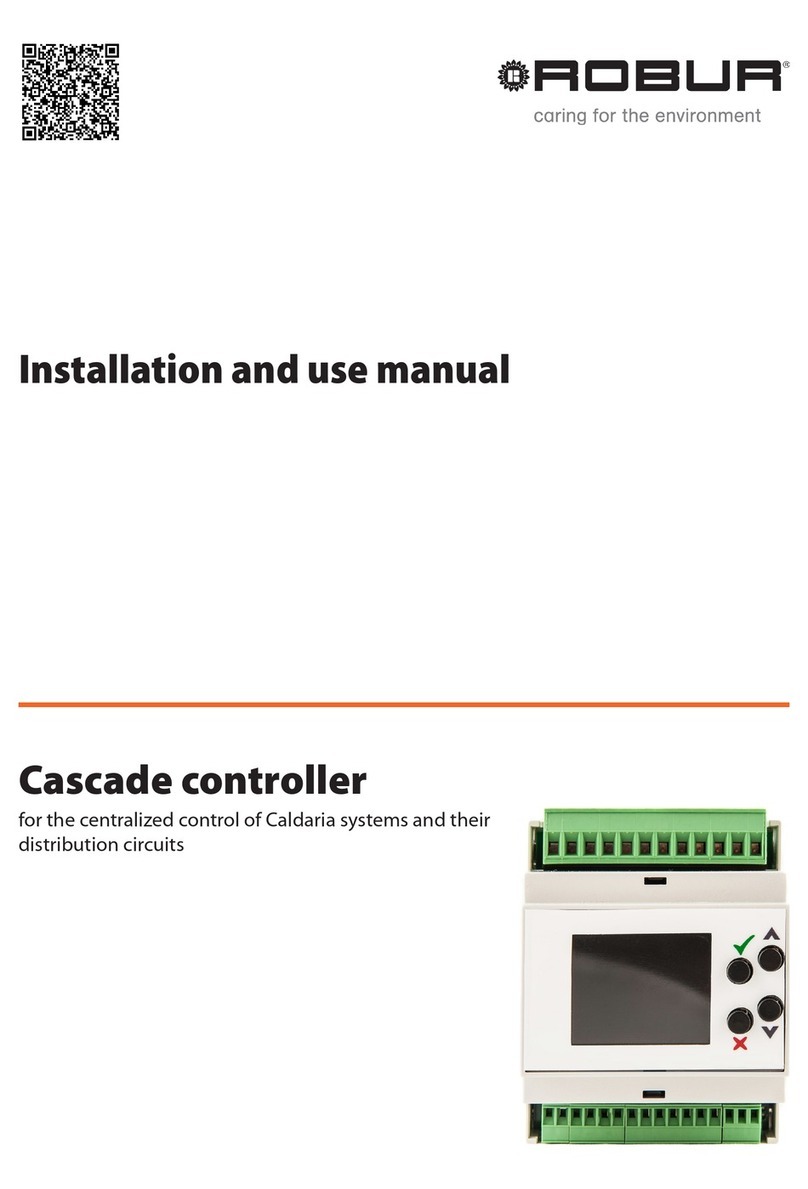
Robur
Robur Cascade controller Installation and use manual
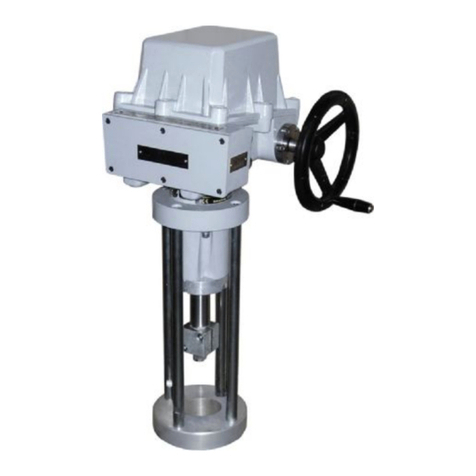
Regada
Regada ST 1-Ex Installation, service and maintenance instructions
![MOBILUS MOTOR mob.iq [RHM] user manual MOBILUS MOTOR mob.iq [RHM] user manual](/data/manuals/1h/m/1hmgl/sources/mobilus-motor-mob-iq-rhm-controller-manual.jpg)
MOBILUS MOTOR
MOBILUS MOTOR mob.iq [RHM] user manual
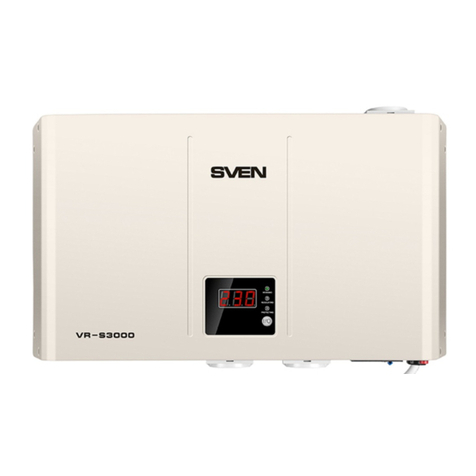
Sven
Sven VR-S3000 Operation manual
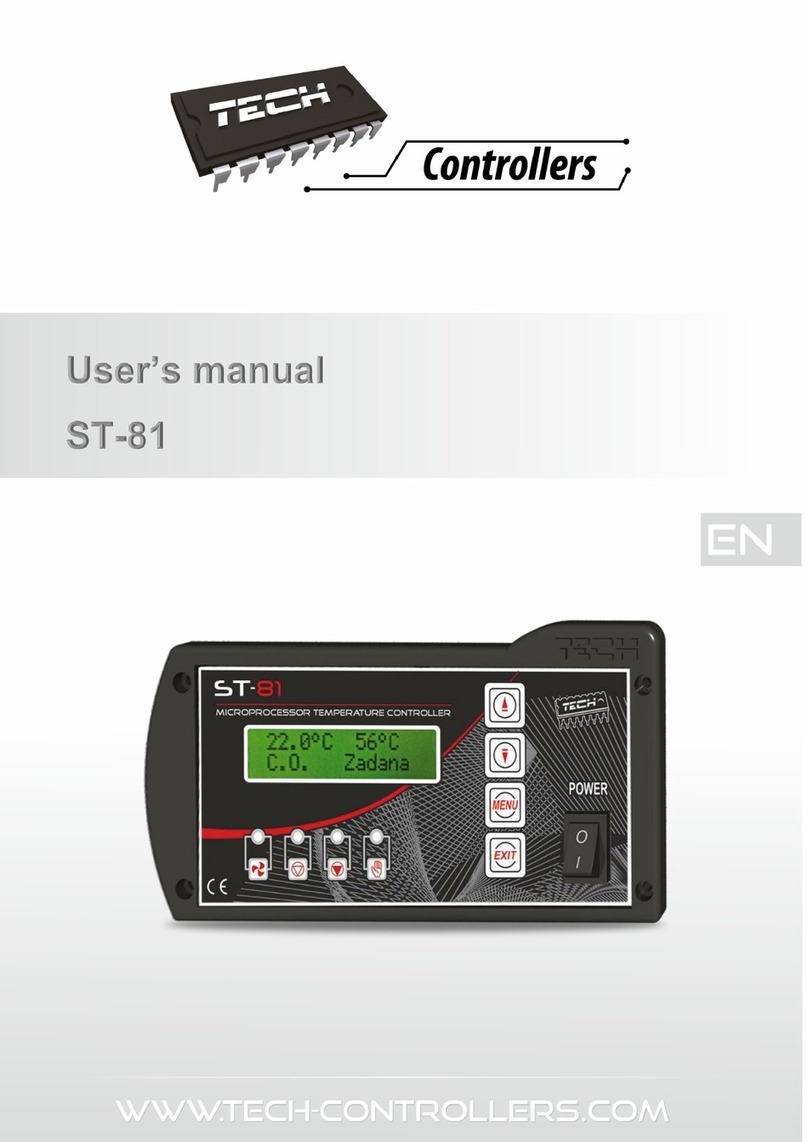
Tech Controllers
Tech Controllers ST-81 user manual
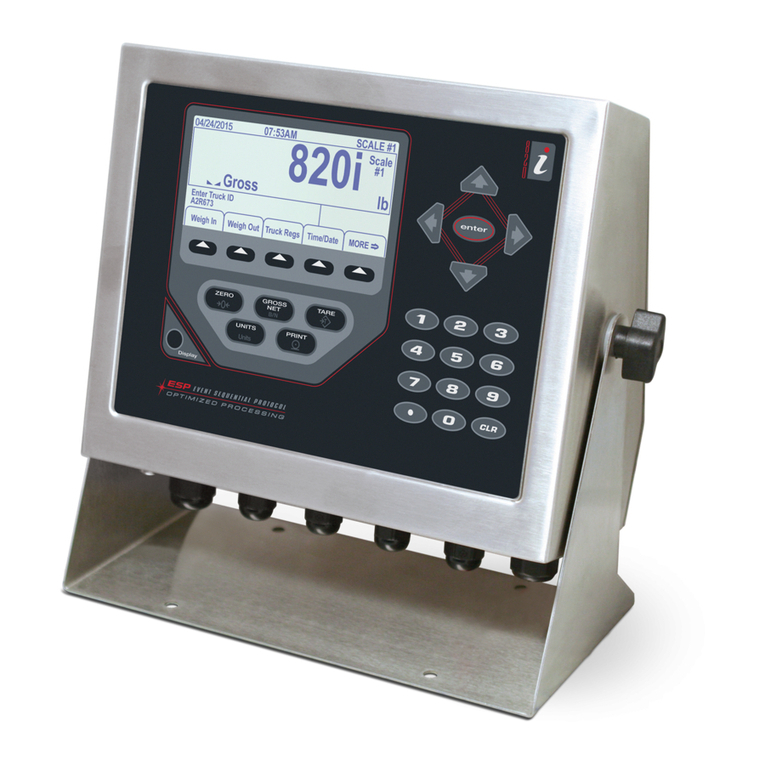
Rice Lake
Rice Lake iRite 920i installation manual
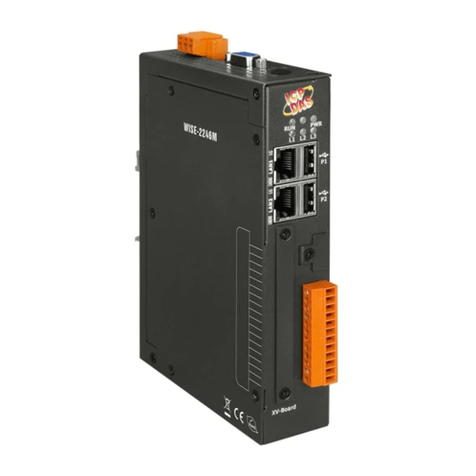
ICP DAS USA
ICP DAS USA WISE-224 Series quick start