Eminox CRT System Manual

CRT® System
Operation & Maintenance Manual
E x h a u s t E n g i n e e r i n g E x c e l l e n c e
LITM002
©Eminox Ltd 2011: CRT® System is a Registered Trademark of Johnson Matthey plc


Contents
Section Title Page Nos.
Introduction 2
1. Technical Description & Identification of Parts 3
2. CRT® System Operation 4
3. Regular Maintenance Check 6
4. CRT® System Service Intervals 6
5. Electronic Service Indicator 8
6. CRT® System Service Records 9
7. Dismantling your CRT® System 10
8. Re-assembling your CRT® System 11
9. Servicing the CRT® System Filter 13
10. Catalyst Maintenance 14
11. Summary of Warnings 15
Glossary of Terms 16
1
CRT® System Operation & Maintenance Manual

Highly Active
Catalyst Module
Wall-Flow Filter Module
Inlet Module
Outlet
Module
© 2004 Eminox Ltd
Port to facilitate
smoke or back
pressure testing
CRT® System Operation & Maintenance Manual
2
Introduction
Your CRT® system is a Continuously Regenerating Trap using novel patented
technology which largely eliminates harmful pollutants from your diesel engine
exhaust, in addition to providing the normal functions of a silencer system such as
noise reduction. Typical reductions for some of the major pollutants are:
Particulate matter (PM) 75 to 95%
Hydrocarbons (HC) 75 to 95%
Carbon Monoxide (CO)75 to 95%
Nitrogen Oxides (NOx) up to 10%
Your CRT® system contains a specially formulated, highly active Catalyst and
a wall-flow ceramic filter housed in modular units. The patented chemical
technology promotes self cleaning of the soot or particulate matter trapped within
the ceramic wall flow filter. The efficiency of this process determines the service
frequency.
Your CRT® system is housed in high grade stainless steel which protects the
system from corrosion giving many years of useful service.

Section 1 - Technical Description & Identification of Parts
Your CRT® system is made up of four major parts illustrated in the diagram below:
1. Inlet Module
2. Catalyst Module
3. Filter Module
4. Outlet Module
Note:
1. In certain circumstances modules may be combined.
2. The Catalyst must always be positioned upstream of the Filter.
3
1. Inlet
Module
2. Catalyst
Module
3. Filter
Module
4. Outlet
Module
To TailpipeExhaust gas
from engine
Service Port
if fitted
3. Filter
Module
Plugged Cells
(“Chequer board”
structure ie:
Alternate cells
are plugged)
2. Catalyst
Module
Both made
from Ceramic
Substrate
Catalyst Filter
Open Cells
(“Honeycomb”
structure)

CRT® System Operation & Maintenance Manual
4
Section 2 - CRT® System Operation
CRT® System Operating Characteristics.
The essential characteristic of the CRT® system is to capture and oxidise the soot
or particulate matter contained in diesel exhaust, commonly observed as smoke.
The particulate matter is caught within the wall flow filter and then continuously
oxidised, at typical exhaust gas temperatures, into harmless gas by the novel
patented chemical technology.
Under normal operating conditions, with a properly maintained engine under
typical loading, the soot component of diesel exhaust is oxidised harmlessly
leaving only ash, mainly the incombustible residue of burnt engine oil. This
accumulates very gradually in the Filter and should be removed by regular
servicing.
In conditions of prolonged low engine loading however, for example when
vehicles travel at slow speeds in urban conurbations or engines are used in a static
utility role, the exhaust gas may not achieve a high enough temperature for the
full oxidation of the soot. In these cases the Service Interval of the CRT® system
must then be shortened in order to remove any accumulation of unburned soot
and ash.
In the exceptional case, when engine soot output exceeds that specified by the
manufacturer, faster soot (and ash) accumulation within the Filter can cause
exhaust gas flow restriction and a corresponding increase in Back Pressure. In
the extreme condition, when the Filter carries an undetected high concentration
of soot, a relatively short period of high engine work output can cause a rapid rise
of exhaust gas temperature. This can lead to spontaneous soot ignition and very
high temperatures which can result in irreparable damage to the filter and the
need for replacement.
The following conditions are essential for satisfactory CRT® system operation:
• Use only diesel fuel with sulphur content less than 50 ppm and conforming
to EN590
• Do not use fuel additives other than those already incorporated in general
commercial diesel fuel supplies
• Additionally the following biodiesel and water-diesel emulsion fuels are
approved for use with CRT® technology
• Biodiesel
30% Diester
Greenenergy Global Diesel, 5% biodiesel, 95% ULSD
Global Commodities UK Ltd, driveEco
Rix Biodiesel Ltd, Bioblend 5
Petroplus Marketing Ltd, Bio-plus
• Water-fuel emulsions
BP Aspira @ 10% demineralised water
Lubrizol PuriNOx™ @ 10% demineralised water

5
• The engine is properly maintained so that the level of smoke produced
by the engine does not exceed the maximum limits set by the engine
manufacturer. If this is not available then Eminox recommend:-
• Eminox approve the use of E4 and E6 oil. Eminox recommend the use
of E6 rated engine oils ahead of E4, because of their potential to extend
catalyst life and the advantages of extended filter service intervals. Which
ever oil is used, it is important to ensure that it is a low ash engine oil with
a sulphur content of less than 7,000 ppm.
• Eminox recommend that oil consumption is monitored closely. It
is important that oil consumption rates should not exceed engine
manufacturer’s limits, typically less than 1 litre per 1,000km
• The vehicle must be serviced according to manufacturer’s recommendations
in order to maintain the optimal engine performance, which the CRT®
system is designed to be compatible with
• Repeated long periods of engine idling should be avoided. This can lower
the engine temperature below that required for filter regeneration, causing
soot to accumulate and block the filter
Warning.
The factors described in this Section have an effect on the life of the Catalyst.
Under normal operating conditions where the engine is well maintained and the
correct oil is used your Catalyst has been designed to last for the operating life of
a vehicle. If these conditions have not been met it is possible that the Catalyst
will require earlier replacement.
The activity level of the catalyst, contained in many diesel particulate filter
systems, can also affect the frequency of filter servicing. We recommend that
catalysts are checked after 5-6 years to ensure optimum system performance. We
offer a catalyst testing service to check the activity level of the catalyst and advise
on whether this could be affecting your system performance and servicing costs.
Aim of the Manual. The aim of the following Sections of this Manual is to set out
CRT® service requirements which should avoid the extreme condition that leads
to filter damage
Note: A Health and Safety risk assessment should be done before attempting to
carry out work described in the following Sections of this Manual. To help with
your Risk Assessment, material safety data sheets (MSDS) for both ash and soot
are available from the Eminox Ltd website www.eminox.com.
E1 + E0 E2 E3
Pass Fail Pass Fail Pass Fail
K < 1.25 >= 1.25 < 1.0 >= 1.0 < 0.8 >= 0.8

CRT® System Operation & Maintenance Manual
6
Section 3 – Regular Maintenance Check
Caution: Before checking your CRT® system you should observe the requirements
of your Health & Safety Risk Assessment.
Back Pressure. Exhaust Back Pressure (BP) rises as a CRT® system Filter
accumulates ash and soot. BP checks at regular intervals can indicate the extent
of this accumulation, and the point at which the Filter needs to be serviced, see
Section 4.
BP should be measured when the:
• vehicle is stationary
• engine is as close to operating temperature as possible
• engine is run at max static rpm (the condition reached when the
accelerator pedal is fully depressed with the transmission in neutral).
Care must be taken if a Limiter is fitted to make allowance for an rpm
that is lower than the standard set by the manufacturer see Section 4.
Record BP using:
• an Electronic Service Indicator (ESI) if this is fitted, see Section 5
• Eminox hand held Digital Pressure Gauge (Part Number QM1466) connected
by a tube to the BP tapping point fitted to your system. This could be
to a Schrader valve output located
within the engine bay or at some
other easily accessible position, or
to the CRT® system Service Port (by
removing the Allen screw).
Section 4 - CRT® System Service Intervals
Engine Duty Cycle. The efficiency of soot oxidation within the CRT® system
increases with exhaust gas temperature. It follows that, if an engine has a low
work output or idles for long periods, this may reduce effective regeneration and
lead to soot accumulation and an earlier service requirement. Eminox therefore
strongly recommends that a regular check of BP is maintained in order to guard
against excess ash and soot accumulation due to operation in adverse conditions
and/or deterioration in engine performance leading to high engine out smoke.
Alternatively it is possible to identify categories of engine duty cycle which are
listed below and can be used a guide.

A Guide to Service Interval Prediction.
* or as indicated by the Electronic Service Indicator (ESI), whichever occurs
first
Warning.
• Long periods of idle should be avoided. In a workshop environment this
should be limited to 15 minutes per day.
The Interpretation of Back Pressure. BP varies with the maximum static rpm
(which may have an rpm limiter fitted or reset as a matter of Fleet operating
policy), and with engine temperature (where it is not possible to reach a normal
operating level during a service). The BP Limit is the conservative figure that
Eminox Ltd will provide for your engine configuration which can help to take
account of these uncertainties. Best practice is to record BP readings under similar
measurement conditions (see Section 2) at intervals of not more than 4 weeks.
Interpretation may be assisted by plotting a graph of BP against time. When the
BP Limit is reached the Filter must be serviced but a graph may assist with the
detection of a rapid rise in BP which is a stronger indication that damage is likely
to occur.
7
Duty Cycle Typical Example Typical Service
Interval
High and sustained
workload
Long haul truck
Intercity train or coach
Upto 1 year*
Variable engine
work rate
All purpose delivery truck
Bus operating in a mix of city
and rural areas
Upto 1 year*
Low engine
work rate
Bus operating in heavy traffic
and congested city centres
Waste refuse vehicles
Upto 6 months*
Monitor back
pressure at least
once every 6 weeks

Warning.
• If the BP limit is reached within the CRT® system Service Interval it is
likely that engine smoke has increased. (A condition that will be masked
by the CRT® system). You must then check engine smoke output. If
corrective action is not taken you will risk catastrophic failure of the
Filter, and invalidation of any warranty cover. You may also experience a
deterioration in engine performance.
• The measurement of engine out smoke is a gauge of engine performance,
not an indication of the state of a CRT® system. Ideally, smoke readings
should be taken with the CRT® system disconnected, with appropriate
safeguards against fumes and noise.
• If you do not know what the manufacturer’s smoke limits are for your
engine then you should consult your engine supplier. Alternatively Eminox
Ltd Recommends:-
• If black smoke emerges from the tailpipe of the CRT this is a clear indication
that the system is not working and should be thoroughly investigated.
Section 5 – Electronic Service Indicator (when fitted).
Operation. The Eminox Ltd Electronic Service
Indicator (ESI) is a robust Back Pressure (BP)
recording device normally fitted within an engine
bay, or adjacent to it. It has two key elements; a
pressure sensor connected by heat resistant tube
to the CRT® system inlet (or upstream of the CRT®
system), and a central processor unit (CPU) which
continuously measures dynamic BP.
ESI Warning System. The ESI warning system
consists of 3 coloured lights. Limits are set
within the micro-processor by Eminox Ltd for a
particular engine configuration and duty cycle. The ESI triggers the appropriate
light illumination when a preset BP has been exceeded:
Green. System on, BP at acceptable levels
Amber. BP above acceptable levels. Filter will require servicing shortly.
Check by recording BP at max static rpm.
Red. Filter requires an immediate service. The display also shows the
BP in the format Cxxx and Mxxx where C = current value of BP, M =
the maximum BP since the unit was last re-set and xxx = numerical
value of BP in mbar. The display alternates between these two
formats automatically whilst the unit is turned on.
CRT® System Operation & Maintenance Manual
8
E1 + E0 E2 E3
Pass Fail Pass Fail Pass Fail
K < 1.25 >= 1.25 < 1.0 >= 1.0 < 0.8 >= 0.8

9
CRT® System Operation & Maintenance Manual
BP Measurement at Max Static rpm. The ESI digital display may also be used to
read a maximum BP when the vehicle is stationary (when the highest BP reading
remains on display). It is possible therefore for one man to run the engine to max
static rpm, allow the vehicle to return to idle (or stop the engine), then walk back to
read max BP. This should be
used as an independent check
on the Amber and Red lights on
the Warning System.
The CPU retains the BP trace
history of the vehicle. This
can be downloaded for analysis.
Resetting the unit to carry out a
max static rpm pressure reading
does not erase this memory.
Section 6 - CRT® System Service Records.
The following information should be recorded on your vehicle check sheet at each
service:
• Back Pressure before and after service (note that the engine must be warm
at the time of measurement)
• Vehicle mileage
• Filter and Catalyst Serial Numbers
• Filter cleaning, method and date
Note: Eminox Ltd will require service records in order to investigate any warranty
claim. Failure to provide service records will invalidate your warranty cover. A
typical CRT® system Service Record Sheet can be obtained from the Eminox Ltd
website www.eminox.com

Section 7 - Dismantling your CRT® System
Caution: Before dismantling your CRT® system you should observe the
requirements of your Health & Safety Risk Assessment.
Note: Unless the Filter is already marked with the exhaust gas flow direction
through the Filter, this should be marked on the outside of the casing before
removal, unless it is to be returned to be reconditioned as an Eminox Ltd Service
Exchange Filter.
Your CRT® system may be removed as a complete unit by slackening Inlet Module
and Outlet Module pipe retaining Band Clamps and dismantling the supporting
brackets as necessary. Some installations like twin systems may require that one
or more Modules be released first, in which case disconnect the V-Clamps and
remove the CRT® system units individually.
When the Filter Module is to be removed for servicing or exchange it may be
possible to release it as a single unit by disconnecting its V-Clamps and easing
away the adjacent Modules and pipe work.
When the CRT® system is dismantled always inspect all parts for obvious external
damage, particularly the flared end of all units which form together with the
gaskets the gas tight joint beneath the V-Clamps. A significant dent in a Catalyst or
Filter Module may well have damaged the ceramic substrate. Check for obvious
signs of damage on the surfaces of the ceramic substrate. Any damaged Module
must be replaced.
CRT® System Operation & Maintenance Manual
10

11
Joint ring
V-Clamp
Gasket
Section 8 - Re-assembling your CRT® System
Caution: Before re-assembling your CRT® system you should observe the
requirements of your Health & Safety Risk Assessment.
Re-assemble your CRT® system in the reverse sequence using new gaskets and,
if needed, new V-clamps. The Catalyst Module may be re-assembled in either
direction and must be fitted upstream of the Filter. The Filter should be replaced
so as to maintain the marked previous exhaust gas flow direction.
Note: It is recommended that the Filter Module is refitted with the CRT® system
Serial No and ID No easily visible to the Vehicle and Operations Services Agency
(VOSA) for the purposes of their Reduced Pollution Certificate (RPC) inspections.
Serial No.
Part No.
ID No.

CRT® System Operation & Maintenance Manual
12
The following torque settings should be applied. Note that it is essential not to
over-tighten the clamps that provide the structural rigidity of the CRT® system as
this can lead to in service failure which could have serious results.
• CRT® system Band Clamps (pipe work) 14 Nm
• CRT® system V-Clamps 14 Nm
• Hi-Torque Clamps (heat shields) 11 Nm
• Service Port Plug (if fitted) 68 Nm
• Allen Screws 20 Nm
Following the replacement of the CRT® system and all exhaust pipes:
• Connect the garage exhaust extractor and start the engine.
• Allow the engine to reach normal operating temperature.
• Run at idle for five minutes, then gradually increase to full rpm. Then
leave on tick over for 5 minutes before shutting off the engine. Remove
the exhaust extractor unit and check the security of CRT® system and pipe
work fixings making sure there are no leaks in the system.
• Check that any insulation fitted to the pipe-work is replaced and properly
secured with a tight fitting to the pipe.
Please quote the CRT® system Serial Numbers when ordering spare parts.

Section 9 - Servicing the CRT® System Filter
Caution: Before servicing your Filter you should observe the requirements of your
Health & Safety Risk Assessment.
The unique design of the Eminox CRT® and SCRT® systems mean that the filters
are continuously regenerating, however, incombustible residues can still build up
on the filter. Similarly FBC and FBC Active systems are designed to regenerate
during use. For optimal performance, the filter needs periodic cleaning to remove
incombustible ash and any excess soot. Failure to clean the filter can result in filter
blockage, causing build up of soot and ultimately an exothermic reaction which
will damage the filter.
Eminox has developed a specialist cleaning process which rejuvenates the filter
for the best possible performance. Filters are professionally reconditioned and
their performance tested. This is backed by a 12 month warranty for reconditioned
filters. The cleaning process helps maintain the service interval and improves the
longevity of the filter.
A range of filter servicing packages are available, for details please visit
www.eminox.com or contact us on +44(0)1427 810088
The environmental benefits of fitting an Eminox Systems are well established
CRT® Systems significantly reduce exhaust emissions, including Carbon
Monoxide, Hydrocarbons and Particulate Matter, FBC systems also reduce
particulate matter, the SCRT® system additionally reduces Nitrogen Oxides
The environmental benefits have encouraged many operators to run green
vehicles. A clean filter will ensure that the CRT® and SCRT® systems will
continue to offer trouble free performance and carry on reducing harmful
emissions.
13
Normal Appearance Local Internal Damage Extensive internal damage

CRT® System Operation & Maintenance Manual
14
Section 10 - Catalyst Maintenance
Caution: Before maintaining your Catalyst you should observe the requirements
of your Health & Safety Risk Assessment.
When operating under Normal Conditions the Catalyst should not become clogged
by soot. However, during a Filter service it is advisable to check the condition of
the Catalyst and to dislodge any accumulated soot by using a soft brush. Inspect
those visible surfaces of the Catalyst that are accessible (not always possible on
the upstream side) to ensure that there is no surface cracking or pitting and that
the ceramic substrate is secure within the high grade stainless steel housing.
Should any defect be found, replace the Catalyst Module.

15
Section 11 – Warnings
The performance of your CRT® system and engine are linked. If the condition of
either is allowed to deteriorate it will have a harmful effect upon the other. This
can be avoided if the instructions in this Manual are followed. In particular, the
following measures will minimise the chances of poor performance:
Never:
• Use jointing compound, gasket cement or such like on upstream exhaust
connections. These may contain silicon (a catalyst poison) which can
destroy your CRT® system
• Exceed the CRT® system Service Interval,
• Run the vehicle when the engine is generating excessively high smoke
levels,
• Allow the engine oil consumption to exceed engine manufacturers limits,
• Overfill the engine with oil,
• Allow the engine to idle for long periods, and in a Workshop not more than
15 minutes continuously
• Allow any insulation material to become dislodged.
Always:
• Service the filter when a Back Pressure limit is reached or when a BP graph
indicates a rapid rise
• Re-assemble a filter correctly with the marked or previous gas flow
direction
• Use fuel with a sulphur content less than 50 ppm,
• Use fuels, fuel additives or alternative fuels which conform to EN590, or
which are specifically approved by Eminox Ltd
• Use E4 or E6 oil. Eminox recommend the use of E6 rated engine oils ahead
of E4, because of their potential to extend catalyst life and the advantages
of extended filter service intervals. Which ever oil is used, it is important
to ensure that it is a low ash engine oil with a sulphur content of less than
7,000 ppm.

CRT® System Operation & Maintenance Manual
16
Glossary of Terms
Term Meaning
Ash The incombustible particulate matter in the exhaust gas,
mainly residues of components of the lubricating oil.
Back Pressure The pressure above atmospheric within an exhaust
system caused by flow resistance.
Band Clamps Flat metal clamps which are used to connect your
CRT® System to the exhaust pipes.
Catalyst A ceramic substrate coated with precious metals to oxidise
pollutants in the exhaust gas.
Catalyst Module The metal housing containing the Catalyst.
Ceramic Substrate A ceramic extrusion usually in the form of a cylinder with
channels running its full length, used as the basis of both
the Catalyst and Filter. The channels in the Catalyst are
open at both ends. In the filter every other channel is
blocked forming a chequer board effect. This forces the
gas to flow through tiny pores in the walls of the channels
preventing the passage of soot.
CRT® System Continuously Regenerating Trap. A unique patented
process which uses a Catalyst to convert some NOx into
NO2. This oxidises or burns any soot which is collected on
the walls of the filter at temperatures in excess of 250°C so
cleaning the filter.
Filter A extruded ceramic substrate used to trap Soot and Ash.
Filter Module The metal housing containing the Filter.
Inlet Module The metal housing into which the exhaust down pipe from
the engine enters the CRT® System.
Maximum Static rpm The rpm reached by the engine when the accelerator pedal
is fully depressed with the vehicle stationary and the
transmission in neutral (sometimes called ‘max.static’).
Outlet Module The metal housing from which the exhaust exits your
CRT® System.
Particulate Matter (PM) PM is the solid content of Soot and Ash in the exhaust gas
normally observed as dark or black smoke.
ppm ‘Parts per million’. A measurement used to quantify very small
amounts of a trace element within a larger overall substance.
Serial Number A unique number etched onto a plate welded onto the outside
of the Catalyst Module and the Filter Module used to record
when either module was manufactured and fitted.
Service Port An access port may be built into the Inlet Module of your
CRT® System which contains a smaller threaded orifice to allow
the connection of a tube to a Back Pressure gauge.
Smoke Reading The visible and measurable opacity (blockage of light) of the
exhaust gas. This is related to the amount of particulate matter
emitted by the engine.
Soot The combustible particulate matter in the exhaust gas created
as part of the normal engine combustion process typically
observed as smoke.
V-Clamps The metal clamps with a V shaped cross section which are
used to hold the four modules of your CRT® System together.
They are also often used to connect the turbo charger to the
engine and exhaust pipes.

Eminox Ltd
North Warren Road,
Gainsborough,
Lincolnshire,
DN21 2TU.
Tel: +44 (0) 1427 810088
Fax: +44 (0) 1427 810061
www.eminox.com
©Eminox Ltd 2011: CRT® System is a Registered Trademark of Johnson Matthey plc
Table of contents
Popular Water Filtration System manuals by other brands
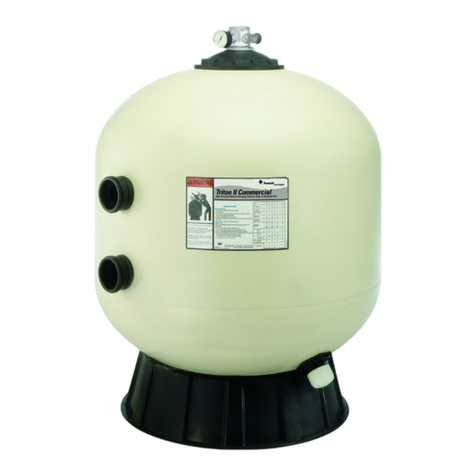
Pentair
Pentair TRITON II TR 40 Installation and user guide
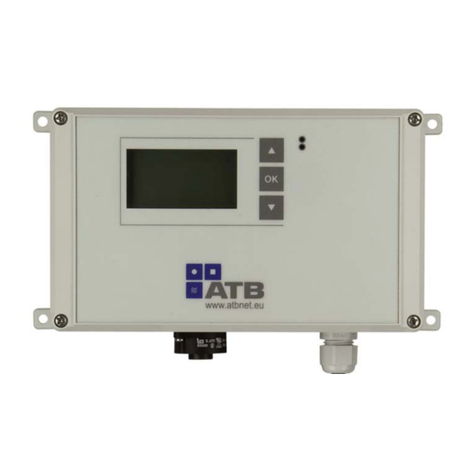
ATB
ATB AQUAmax BASIC series Operation and maintenance manual

Asutec
Asutec ASMEL-120 operating manual
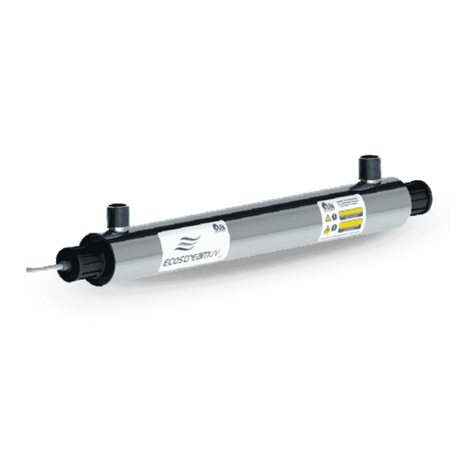
Alfaa
Alfaa EcoStream Lite Operation and maintenance manual
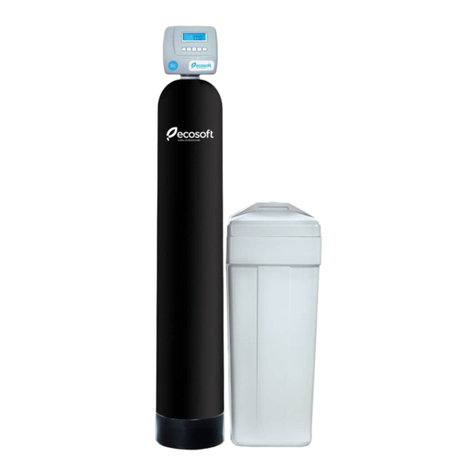
Ecosoft
Ecosoft FK Series instruction manual
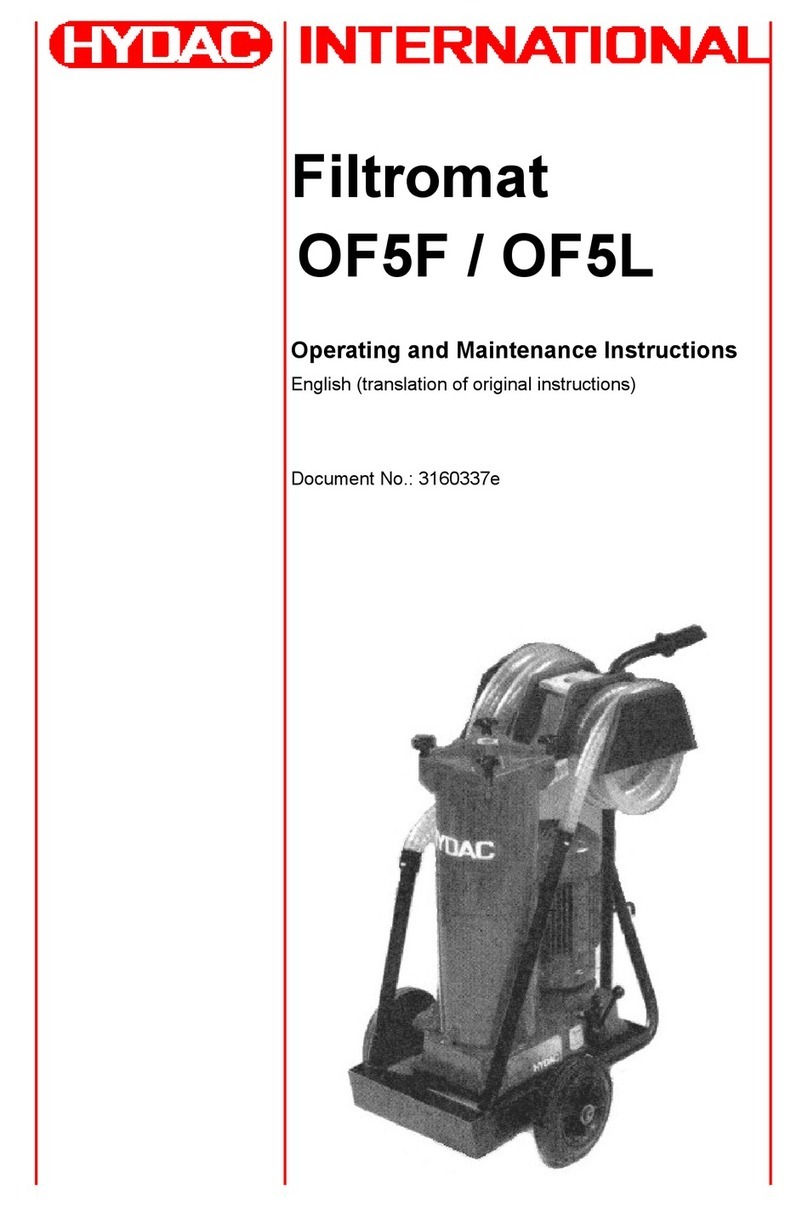
Hydac
Hydac Filtromat OF5F Operating and maintenance instructions
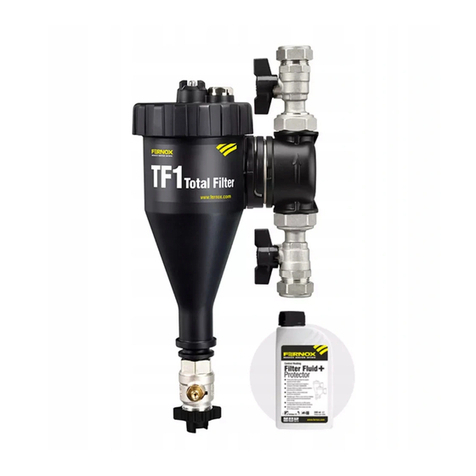
Fernox
Fernox Total Filter TF1 instructions

CALEFFI
CALEFFI 5495 SEP4 Installation, commissioning and servicing instructions

Microline
Microline T.F.C. - 435 Installation, operation & service manual
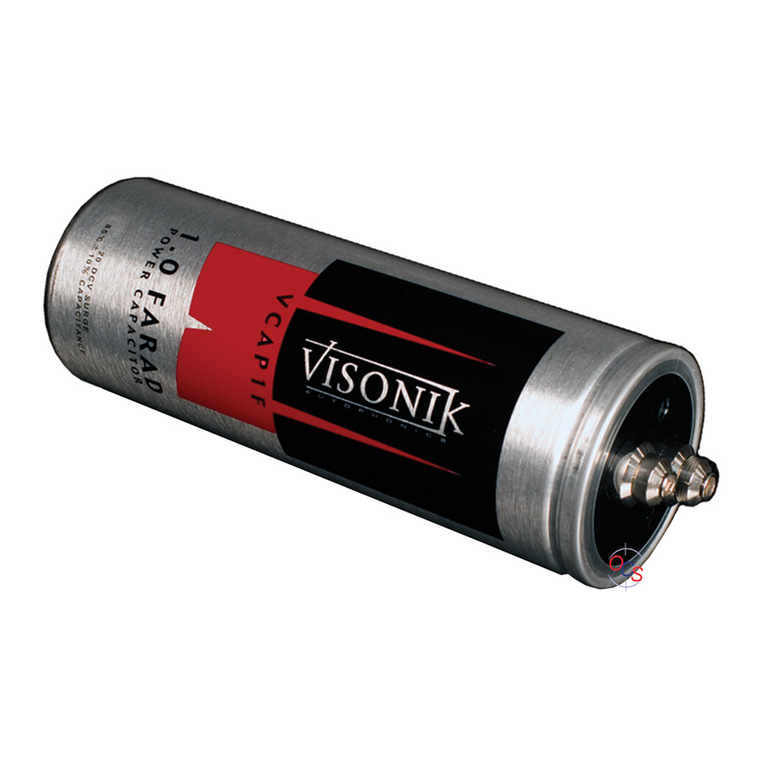
Visonik
Visonik VCAP1F instructions
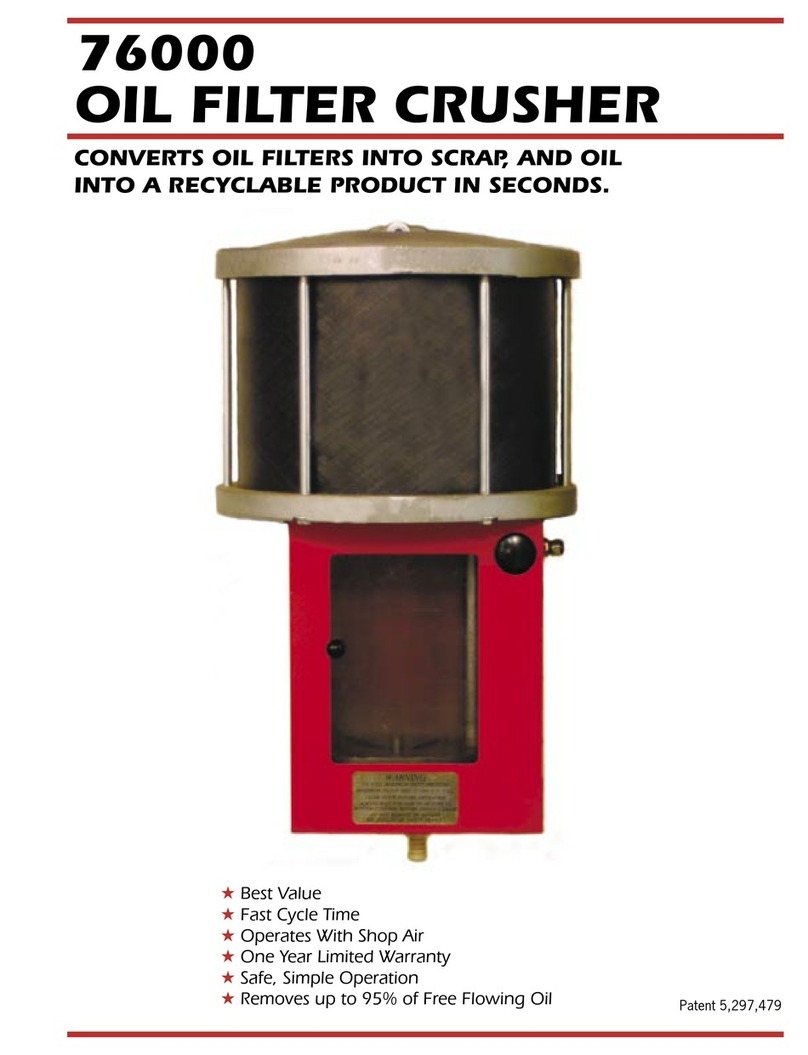
Lisle
Lisle 76000 quick start guide
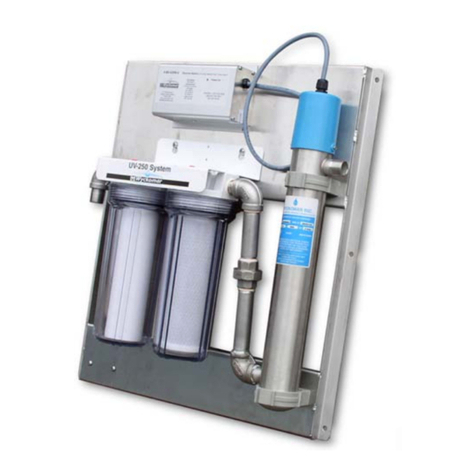
Wyckomar
Wyckomar UV-1 Installation and maintenance manual