Emotron EMX-B User manual

Emotron EMX-B
Drive system
for rotary heat exchangers
Instruction manual
English


Emotron EMX-B
Drive system
Instruction manual
Valid from software version 3.0
Document number: 01-6048-01
Edition: r3
Date of release: 2019-03-27
© Copyright CG Drives & Automation Sweden AB 2015-2019
CG Drives & Automation retain the right to change
specifications and illustrations in the text, without prior
notification. The contents of this document may not be copied
without the explicit permission of CG Drives & Automation
Sweden AB.

The product is protected as follows:
Patents: US 6 628 100; SE 9902821-9
SE 0100814-3; SE 0100814-3; EP 1 366 346; US 7 083 544
Registered design: US 462 937; DE 400 05 393.4; SE 66 630
Patent pending for UltraRotoSenseTM: EP17171733.3

CG Drives & Automation 01-6048-01r3 1
Safety instructions
Instruction manual
Read this instruction manual before installing and running the drive system.
The following symbols can appear in this manual. Always read these first before
continuing:
Users
This instruction manual is intended for:
• installation engineers
• maintenance engineers
•operators
• service engineers
Handling the drive system
Installation, commissioning, demounting, taking
measurements, etc, of or on the drive system may only be carried out by
personnel technically qualified for the task. The installation must be carried out
in accordance with local standards.
NOTE: Additional information as an aid to avoid problems.
CAUTION! Failure to follow these instructions can result in malfunction
or damage to the drive system.
WARNING! Failure to follow these instructions can result in serious
injury to the user in addition to serious damage to the drive system.
!

2CG Drives & Automation 01-6048-01r3
Opening the control unit
Always take adequate precautions before opening the control unit. Although the
connections for the control signals and the switches are isolated from the mains
voltage, do not touch the control board when the drive system is switched on.
Precautions to be taken with a connected motor
If work must be carried out on a connected motor or on the driven machine,
the mains voltage must always be disconnected from the drive system first.
Earthing
The control unit must always be earthed via the mains safety earth connection.
EMC Regulations
In order to comply with the EMC Directive, it is absolutely necessary to follow
the installation instructions. All installation descriptions in this manual follow
the EMC Directive.
Voltage tests (Megger)
Do not carry out voltage tests (Megger) on the motor, before all the motor
cables have been disconnected from the drive system.
Condensation
If the control unit is moved from a cold (storage) room to a room where it will
be installed, condensation can occur. This can result in sensitive components
becoming damp. Do not connect the mains voltage until all visible dampness
has evaporated.
Incorrect connection
The control unit is not protected against incorrect connection of the mains
voltage, and in particular against connection of the mains voltage to the motor
outlets R, Y and B. The control unit can be damaged in this way.
WARNING! Always switch off the mains voltage before opening
the control unit.
Wait at least 5 minutes before starting work.

CG Drives & Automation 01-6048-01r3 3
Transport
To avoid damage, keep the drive system in its original packaging during
transport. This packaging is specially designed to absorb shocks during
transport.

4CG Drives & Automation 01-6048-01r3

CG Drives & Automation 01-6048-01r3 5
Contents
Safety instructions................................................................... 1
Contents ................................................................................ 5
1. Description ............................................................................ 7
1.1 Introduction................................................................................................. 7
1.2 Delivery and unpacking.............................................................................. 8
1.3 Warranty ...................................................................................................... 8
1.4 General description .................................................................................... 9
1.5 Operating indicators ............................................................................... 10
2. Mounting and installation ..................................................... 13
2.1 Basic mounting ........................................................................................ 13
2.2 External sensor for rotation monitor (optional) ..................................... 14
2.3 Cable connections ................................................................................... 15
2.4 Control board ........................................................................................... 16
2.5 Select type of control signal.................................................................... 22
3. Built-in functions .................................................................. 23
3.1 Holding torque ......................................................................................... 23
3.2 Automatic purging.................................................................................... 23
3.3 Rotation monitor (DIP switch 6).............................................................. 24
3.4 Protection of the control unit .................................................................. 26
3.5 Defrosting................................................................................................. 27
3.6 Manual control using a 10 kOhm potentiometer .................................. 27
3.7 Test Switch ............................................................................................... 27
3.8 Cooling recovery....................................................................................... 27
3.9 DIP switches............................................................................................. 28
3.10 Communication through Modbus........................................................... 32
3.11 Built-in configurable non-linearity........................................................... 39
4. Troubleshooting ................................................................... 41
4.1 Trip conditions, causes and remedial action......................................... 41

6CG Drives & Automation 01-6048-01r3
5. Maintenance........................................................................ 46
5.1 Motor diagnosis........................................................................................ 46
6. Technical Data..................................................................... 47
6.1 Dimensions ............................................................................................... 48
6.2 Part numbers ............................................................................................ 51
7. Appendix ............................................................................. 53
7.1 Connection label....................................................................................... 53
7.2 Front label................................................................................................. 54

CG Drives & Automation 01-6048-01r3 Description 7
1. Description
1.1 Introduction
Emotron EMX-B is a speed controlled drive system specially designed for
driving rotary heat exchangers. The drive system consists of a motor and its
associated control unit with a wide speed range from 4 to 500 rpm.
Emotron EMX-B motor is based on permanent magnet brush-less DC (PM
BLDC) motor technology. These motors make it possible to drive heat
exchanger rotors without gears, making the system very silent.
The system can be controlled either via terminals/analogue and digital inputs or
via RS485/Modbus RTU communication protocol.
Emotron EMX-B drive system completely replaces Emotron EMX-R drive
systems.
Fig. 1 EMX-B motor and control unit mounted on rotary heat exchanger

8Description CG Drives & Automation 01-6048-01r3
1.2 Delivery and unpacking
Check for any visible signs of damage. Inform your supplier immediately of any
damage found. Do not install the equipment if damaged.
The shipment of a complete drive system consists of two boxes containing:
Box 1:
• Emotron EMX-B Control unit
•OneFerritecore
Box 2:
Emotron EMX-B motor with connected cables
1.3 Warranty
The warranty applies when the equipment is installed, operated and maintained
according to instructions in this instruction manual.

CG Drives & Automation 01-6048-01r3 Description 9
1.4 General description
Emotron EMX-B is a silent speed-controlled drive system specially designed for
driving rotary heat-exchangers. Emotron EMX-B is available in different sizes
suitable for different sizes of rotors. The system supports a wide speed range
from 4 up to 500 rpm. The drive system consists of a motor and its associated
control unit which are linked by two cables. The control unit is connected to
single-phase power supply, 230 VAC, 50/60 Hz.
Built-in functions:
• Automatic purging operation/Continuous purging operation
• Rotation monitor - integrated UltraRotoSenseTM or with external rotation
sensor
• Active holding torque
• Alarm relay
•Defrosting
• Cooling recovery
• Full speed Test switch
• Short circuit/earth fault protection
• Under voltage, over voltage and over current/overload protection
• Sixteen (16) speed selections through DIP switches
• Direction of rotation through DIP switch
• Soft start/soft stop
• Non-linearity function that gives a non-linear relationship between the con-
trol signal and the efficiency
• RS485 interface with industrial Modbus RTU communication protocol

10 Description CG Drives & Automation 01-6048-01r3
1.5 Operating indicators
Fig. 2 Control unit with LED´s for operation indication
Three LEDs, one red, one green and one yellow, are used for indication
purpose, which are as follows:
*)Exception Belt test, see page 44
All possible combinations of LED indication is described in detail in Table 13,
page 43.
Table 1 Operating indication
Green *
Slow flashing (1 time/s) – Purging mode/Low control signal
Rapid flashing (10 times/s) – Operation, the motor rotates
continuously.
Lit 1 second - External rotosense magnet passes sensor
Red * Constantly Lit or flashing LED indicates alarm, see also in
chapter “Troubleshooting” on page 41.
Yellow
Flashing – Modbus incoming message addressed to unit active
and CRC correct.
Constantly Lit - Modbus timeout
LED window

CG Drives & Automation 01-6048-01r3 Description 11
1.5.1 Dismantling and scrapping
The enclosures of the drives are made from recyclable material. Each drive
contains a number of components demanding special treatment, for example
capacitors. The circuit boards contain small amounts of tin and lead. Any local
or national regulations in force for the disposal and recycling of these materials
must be complied with.
Disposal of old electrical and electronic equipment
The product is designed to comply with the RoHS and REACH directives, and
shall be handled and recycled in accordance with local legislations.
This symbol on the product or on its packaging indicates that this
product shall be taken to the applicable collection point for the
recycling of electrical and electronic equipment. By ensuring this
product is disposed of correctly, you will help prevent potentially
negative consequences for the environment and human health,
which could otherwise be caused by inappropriate waste handling
of this product. The recycling of materials will help to conserve natural
resources. For more detailed information about recycling this product, please
contact the local distributor of the product or visit our home page
www.cgglobal.com/www.emotron.com.

12 Description CG Drives & Automation 01-6048-01r3

CG Drives & Automation 01-6048-01r3 Mounting and installation 13
2. Mounting and installation
2.1 Basic mounting
Both the motor and the control unit are usually mounted in the heat exchanger
housing. In this way, they do not occupy any space outside of the heat
exchanger housing and are well protected during transport. Furthermore, it is
often advantageous from the point of view of interference (EMC) to place the
motor and control unit in the rotor housing.
Larger motors are usually mounted on a sprung motor support when a V-belt is
used. In this way, problems arising if non-circular rotors are used can be
prevented.
Vibration dampers should be mounted between the motor and the motor
support so that any vibration from the motor is not transmitted to the rotor
housing.
Fig. 3 Emotron motor and Control unit for rotary heat exchangers
Heat exchanger rotor
Control unit
Motor

14 Mounting and installation CG Drives & Automation 01-6048-01r3
2.2 External sensor for rotation monitor
(optional)
Fig. 4 Rotation monitor
Two different rotation monitors can be selected. The first, which is an
integrated UltraRotoSenseTM rotation monitor, and secondly a rotation
monitor using an external rotation sensor (optional) see also further info in
chapter 3.3 page 24.
The magnet for the external rotation monitor is mounted tight on the periphery
or in the body of the heat-exchanger. It is recommended to place the sensor
magnet close to the axis of the rotary heat exchanger. If the housing around the
rotor is magnetic itself then the sensor magnet must be isolated from the
housing. The rotation sensor is mounted to ensure that the magnet passes over
it at a distance of 5-8 mm, see Fig. 4.
Rotation sensor
Magnet
5-8 mm
Heat exchanger rotor

CG Drives & Automation 01-6048-01r3 Mounting and installation 15
2.3 Cable connections
2.3.1 Motor
The motor is delivered with fixed connected motor cables to simplify
installation of the drive system. The length of the cables is 2.5m.
In order to secure the function of the drive system, do not change the length of
the motor cables.
2.3.2 Mains supply
An external slow-blow fuse rated at <6 A must always be installed on mains
supply. The drive system does not contain a fuse. Electronic motor protection is
built into the control unit, and monitors the motor at all times. The control
unit is protected from short circuit within the motor.
Connect the mains cables according to Fig. 7 and Table 4.
2.3.3 Communication connections
For communication signals, the used RS485 cable type should preferably be
screened and of twisted pair type to avoid EMI. The cable should be placed at
least 20 cm away from any power cables. Drop cables shall be avoided to the
extent possible. It is recommended to connect the screen of the cable to chassis/
mounting plate near to the EMX-B gland.
WARNING! Do not install a switch between the motor and the
control unit.

16 Mounting and installation CG Drives & Automation 01-6048-01r3
2.4 Control board
Fig. 5 and Fig. 6 shows the layout of the control board and where the parts most
important to the user are located.
For safety reasons do not make changes while the mains supply is on, see also
“Safety instructions” on page 1.
Fig. 5 Control board layout EMX-B15.
Table 2 Location of terminals and components EMX-B15.
No. Designation
1Three LED operation indicators
2DIP switches
3Test switch
4Jumper SW2 to select signal type, voltage or current (K/I)
5Control signal terminals and RS485 interface (31-40)
6Alarm terminals (41-43)
7Hall sensor terminals (1-5)
8Motor terminals ( -R-Y-B)
9Mains supply terminals (L-N- )
10 PE connector
1
2
3
4
98765
10
Table of contents
Other Emotron Control Unit manuals
Popular Control Unit manuals by other brands

Philio
Philio PAN03 manual
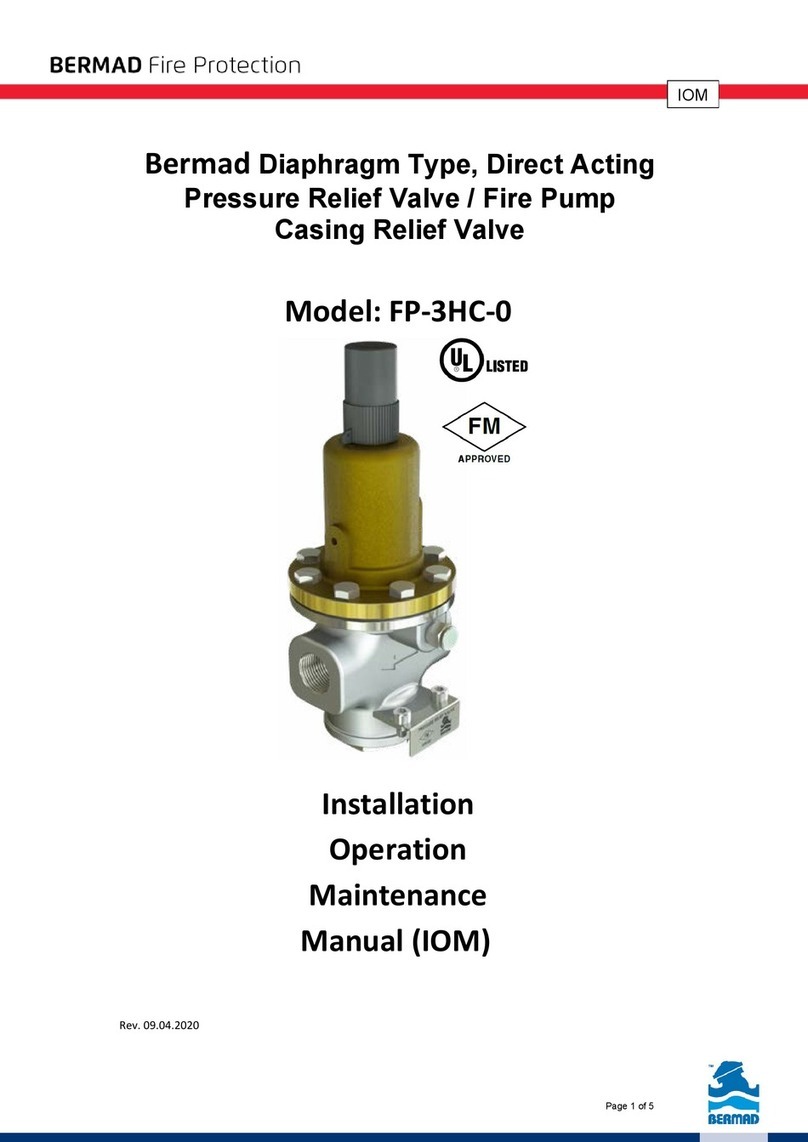
BERMAD
BERMAD FP-3HC-0 Installation, operation & maintenance manual
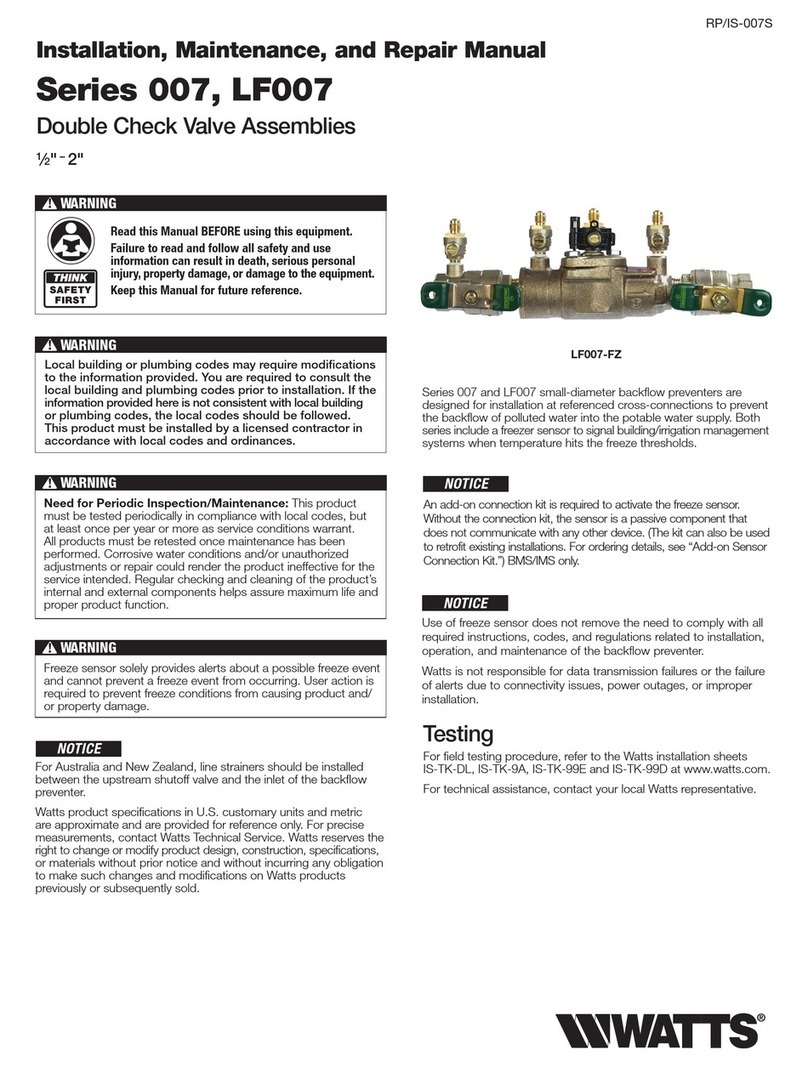
Watts
Watts 007 Series INSTRUCTION, INSTALLATION, MAINTENANCE AND REPAIR MANUAL
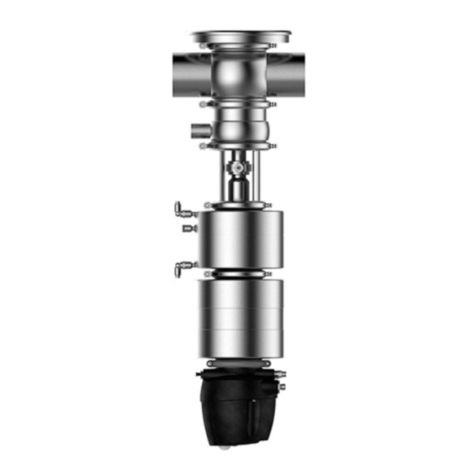
GEA
GEA VARIVENT Mixproof T R Series operating instructions
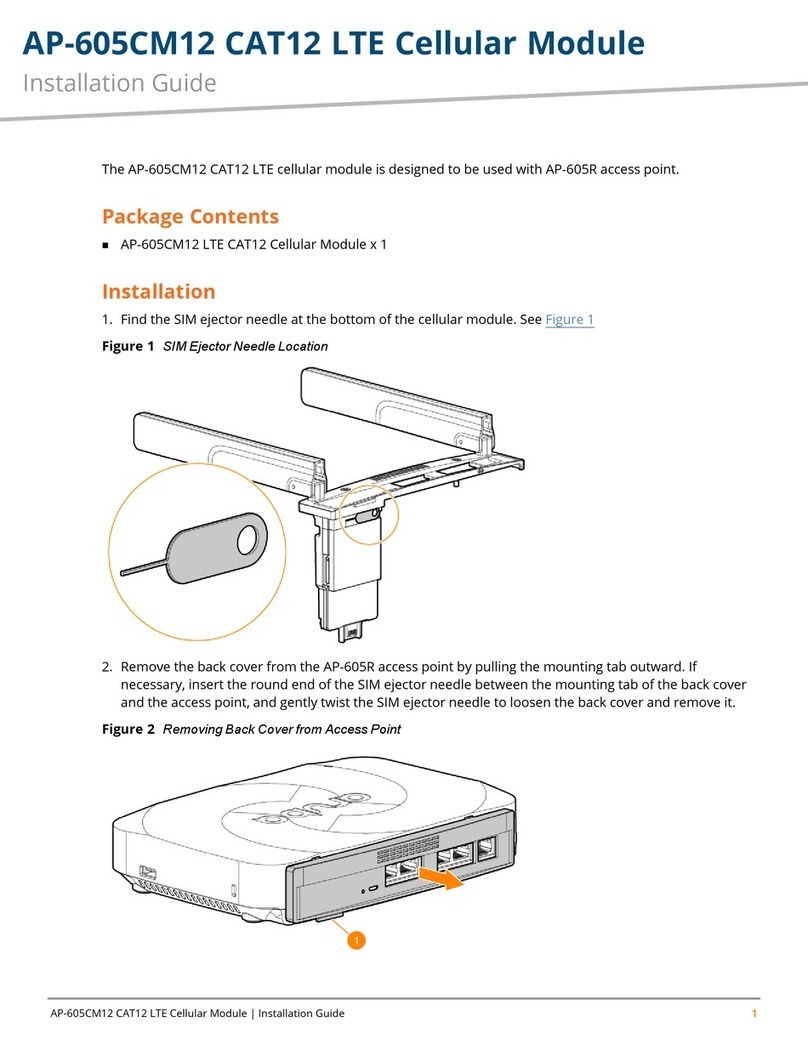
Aruba Networks
Aruba Networks AP-605CM12 CAT12 installation guide
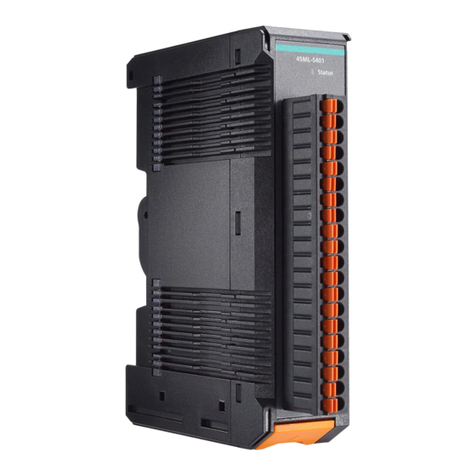
Moxa Technologies
Moxa Technologies ioThinx 4500 45ML-5401 user manual