EsiWelma TW1-M User manual

Type / N°
Rev.
Fw
Date
Page
Total pages
EW055.600D
D
4L
6th June 2018
1
43
EsiWelma®s.r.l.
TW1-M and TW1nA-M
Computer Head User Guide
CNG Version (Methane)
EsiWelma®s.r.l.
Via F.lli Canepa 134d-e
16010 Serra Riccò (Genoa)
ITALY
Tel: +39 010 754211
Fax: +39 010 7542178
email:[email protected]

Type / N°
Rev.
Fw
Date
Page
Total pages
EW055.600D
D
4L
6th June 2018
2
43
EsiWelma®s.r.l.
CONTENTS
1. TECHNICAL DESCRIPTION -----------------------------------------------------------------------------------------------4
1.1. Structural specifications -----------------------------------------------------------------------------------------------4
1.2. Technical data ------------------------------------------------------------------------------------------------------------- 4
2. FUNCTIONAL DESCRIPTION---------------------------------------------------------------------------------------------6
2.1. Data display ----------------------------------------------------------------------------------------------------------------6
2.2. Operating sequence description ------------------------------------------------------------------------------------6
2.2.1 Manual delivery ----------------------------------------------------------------------------------------------------8
2.2.2 Pre-set value delivery --------------------------------------------------------------------------------------------8
2.2.3 Programming by Host--------------------------------------------------------------------------------------------8
2.2.4 Programming by a 16-key keyboard ------------------------------------------------------------------------9
2.2.5 Automatic stop sequence--------------------------------------------------------------------------------------- 9
2.2.6 Supply voltage blackout management ------------------------------------------------------------------- 10
2.3. Connection to Host ---------------------------------------------------------------------------------------------------- 10
2.4. Euro €----------------------------------------------------------------------------------------------------------------------- 10
2.5. Delivery in Self-Service mode -------------------------------------------------------------------------------------- 10
2.5.1 Electrical devices involved----------------------------------------------------------------------------------- 11
2.5.2 Sequence of delivery------------------------------------------------------------------------------------------- 11
2.5.3 Warning light management----------------------------------------------------------------------------------- 12
3. TROUBLESHOOTING ----------------------------------------------------------------------------------------------------- 13
3.1. Fatal errors---------------------------------------------------------------------------------------------------------------- 13
3.2. Non fatal errors---------------------------------------------------------------------------------------------------------- 13
3.3. Error review table------------------------------------------------------------------------------------------------------- 14
3.4. Operating modes ------------------------------------------------------------------------------------------------------- 17
3.4.1 System adaptation ---------------------------------------------------------------------------------------------- 17
3.4.2 CNG dispenser adaptation ----------------------------------------------------------------------------------- 17
3.5. Types of refuelling ----------------------------------------------------------------------------------------------------- 17
4. PROCEDURES -------------------------------------------------------------------------------------------------------------- 18
4.1. Reading from the absolute totalizer ------------------------------------------------------------------------------ 18
4.2. Computing head set-up----------------------------------------------------------------------------------------------- 19
4.2.1 Simple parameters ---------------------------------------------------------------------------------------------- 26
4.2.2 Parameters for temperature compensation------------------------------------------------------------- 26
4.2.3 Complex parameters ------------------------------------------------------------------------------------------- 27
4.2.4 Password----------------------------------------------------------------------------------------------------------- 27
4.2.5 Price change ------------------------------------------------------------------------------------------------------ 29
4.3. Metrical check procedure-------------------------------------------------------------------------------------------- 30
5. HARDWARE PERSONALIZATION------------------------------------------------------------------------------------- 31
6. OPTIONALS ------------------------------------------------------------------------------------------------------------------ 33
6.1. External 4x4 keyboard ------------------------------------------------------------------------------------------------ 33
6.2. 16-digit-on-2-line Display--------------------------------------------------------------------------------------------- 33
6.3. Anomaly signalling device------------------------------------------------------------------------------------------- 34
6.4. I/O expansion device -------------------------------------------------------------------------------------------------- 34
7. ELECTRICAL CONNECTIONS------------------------------------------------------------------------------------------ 35
7.1. Low voltage connections -------------------------------------------------------------------------------------------- 35
7.2. High voltage connections-------------------------------------------------------------------------------------------- 39
8. IDENTIFICATION OF COMPUTING HEAD TW1 ------------------------------------------------------------------- 41
9. MECHANICAL CLAMPING----------------------------------------------------------------------------------------------- 42
10. LEGALIZING PROCEDURE OF THE COMPUTING HEAD TW1 ---------------------------------------------- 43
10.1.
Legalizing procedure of CPU
------------------------------------------------------------------------------------- 43
10.2.
Legalizing procedure of display
--------------------------------------------------------------------------------- 43

Type / N°
Rev.
Fw
Date
Page
Total pages
EW055.600D
D
4L
6th June 2018
3
43
EsiWelma®s.r.l.
List of figures
Figure 1: Summary electric connections ......................................................................................................5
Figure 2: Max data display ...........................................................................................................................6
Figure 3: Refuelling start sequence; CNG metric counting version .............................................................7
Figure 4: Example of a 5.00€ .......................................................................................................................8
Figure 5: Example of a 10Kg........................................................................................................................8
Figure 6: 16-key Keyboard...........................................................................................................................9
Figure 7: Temporary amount conversion to Euro.......................................................................................10
Figure 8: “deadman’s break” push button ..................................................................................................11
Figure 9: Activation Key of Self-Service/Served mode ..............................................................................11
Figure 10: Visualization “waiting procedure selecting”...............................................................................18
Figure 11: Set-up buttons...........................................................................................................................18
Figure 12: Display absolute total counter Kg..............................................................................................19
Figure 13: Enter password .........................................................................................................................19
Figure 14: Notice insert jumper JP2...........................................................................................................19
Figure 15: Visualization of some set-up parameters..................................................................................26
Figure 16: Zeroing Massmeter procedure.................................................................................................26
Figure 17: Specific weight setting...............................................................................................................27
Figure 18: Visualization of the conversion rate Currency/Euro..................................................................27
Figura 19: Changing password request .....................................................................................................27
Figure 20: Visualization saving data...........................................................................................................27
Figure 21: Changing Password..................................................................................................................28
Figure 22: Inserting Password....................................................................................................................29
Figure 23: Password changing request......................................................................................................29
Figure 24: Visualization saving unit price...................................................................................................29
Figure 25: Entering Password....................................................................................................................30
Figure 26: Confirm of anomaly simulation procedure ................................................................................30
Figure 27: Passage from delivery to block during an “anomaly simulation” phase....................................30
Figura 28: TW1-M; “Standard” Identification plate .....................................................................................41
Figura 29: TW1nA-M; “Atex” Identification plate ........................................................................................41
Figure 30: Clamping of the CPU box..........................................................................................................42
Figure 31: Clamping of the display box......................................................................................................42
List of photos
Photo 1: CPU................................................................................................................................................4
Photo 2: Set-up / Price Changing.................................................................................................................4
Photo 3: Display ...........................................................................................................................................4
Photo 4: Set-up jumper on CPU.................................................................................................................31
Photo 5: Pre-set keyboard adjustement on customer’s demand ...............................................................33
Photo 6: Second Display............................................................................................................................33
Photo 7: Anomaly remote signalling device ...............................................................................................34
Photo 8: I/O expansion device ...................................................................................................................33
Photo 9: Identification plate of the electronic computing head TW1..........................................................41
Photo 10: Computing head TW1 CPU .......................................................................................................43
Photo 11: Computing Head TW1-M and TW1nA-M display front view......................................................43
Photo 12: Computing Head TW1-M and TW1nA-M display rear view.......................................................43
Photo 13: Computing Head TW1-M and TW1nA-M display rear view . Neon tube back-lighting version.43

Type / N°
Rev.
Fw
Date
Page
Total pages
EW055.600D
D
4L
6th June 2018
4
43
EsiWelma®s.r.l.
1. TECHNICAL DESCRIPTION
TW1 electronic computing head is designed to operate on one-nozzle fuel dispensers, using
one or two-sided display systems. It can communicate with a Host sending data concerning
the refuelling during the process and/or at the time of the device.
1.1. Structural specifications
The computing head is composed of:
One CPU board of a supplier and communication
interface. Each assembly is settled into a metallic
box to be protected both mechanically and against
EMI interferences;
One board for set-up/price changing settled into a Photo 1: CPU
plastic box. This assembly can be put by the
customer in the most comfortable place or inserted
by convenience;
One or two display boards, optionally settled
in a metallic box. Photo 2: Set-up / Price Changing
1.2. Technical data
Power supply: 230Vac 10%
Power consumption: 10VA
Temperature: min. –40°C max 70°C Photo 3: Display
Humidity (no dew): 95%
Max flow rate: 3.5Kg/s or 3.5Sm³/s (see Setup)
Measure: 1dag or 10dm³ (see Setup)
Solenoid valve control: N.O. max 270Vca/3A Standard /1A Atex (*)
Measuring device inlet:
Pulses →one channel: 1 pulse = 10g
Serial
→
ModBus: A-B channel
Protection grade IP20(**)
Total counter depending on version:
Electromechanical not resetable (7 numbers): 1 counting unit = 1Kg/Smc (see Setup)
Electronic not resetable (10 numbers): 1 counting unit = 1Kg/Smc (see Setup)
Computing Head CPU Dimensions: (230 x 154 x 66)mm
Computing Head CPU Weight: 1950g
Computing Head Display Dimensions: (225 x 250 x 50)mm
Computing Head Display Weight: 960g
(*) Outputs device depending:
Relays for TW1-M “Standard”, or Solid State relays for TW1nA-M “ATEX”.
(**) The declared protection degree is referred to the metallic box. The devices enclosed by
the dotted line in Figure 1 must be installed in a cabinet with at least protection degree IP54,
compliant to standard EN60079-15 of ATEX directive.

Type / N°
Rev.
Fw
Date
Page
Total pages
EW055.600D
D
4L
6th June 2018
5
43
EsiWelma®s.r.l.
Figure 1: Summary electric connections
to Display
Connector
J1
Display-1
Keyboard Interface
SET - UP
Keypad
Display-2
L
p.u./L
L
p.u./L
TB2
TB3
TB6
TB4
TB1
TB7TB8
Field Links
Power Links
Display Link
J1
TB1
5 not Used
4Tx
3Rx
1 Aut/Man
2 0V Field
TB2
Inputs available for
new applications
TR1
PT100
Temperature 2
(Optional)
Temperature 1
TR2
PT100
6 0VField
5 TR2-
2 TR1-
3 0VField
4 TR2+
1 TR1+
TB4
Computing Head
TW1 CPU Board
3 EV2 - 2 Level
1 Electrovalves Common
4 EV3 - 3 Level
TB6
2 EV1 - 1 Level
3 Green
1 Lamp Common
TB7
2 Red
Lamp Power Supply
230Vac o 24Vac
Electrovalves Power Supply
230Vac o 24Vac
3 Gnd
1 Phase
TB8
2 Neutral
Computer Head
Power Supply
230Vac
Impulsive
Mass
Flowmeter
7 not Used
6 0V Flow Meter
8Max Pressure
TB3
5 not Used
4 IN from IMF
3 not Used
1 Nozzle
2 0V Field
Pulse Version
ModBus Version
ModBus
- Mass +
Flowmeter
2 0V Field
1 Nozzle
3 +12Vcc Flow Meter
4 RS485 - A
5 RS485 - B
TB3
8Max Pressure
6 0V Flow Meter
7 not Used
2
1PT
ATMxi
0-400bar
VART286-5
Flow Pressure
2IN2 N.U. (4-20mA)
1IN1 PT (4-20mA)
3 0V Field
4 +24V Field
TB5
TB5
5 Low Flow
See NOTE
§ 7.1
See NOTE
§ 7.1
nd
rd
st
} {
or
Optional
Failure Output I/O Expansion
board
8
7
6
5
43
21
0V
Auto/Man (Auto=closed)
Reset (NO)
Dead-Man control (NO)
Self-Service
connections
0V
N.U.
N.U.
N.U.
Self-Service
Device
2
3
0V
Temp. N.O.
N.O.
1Aut
Reset
Man
4x4 Keyboard
8
7
6
5
4
3
2
1
9
0,
56
8
7
3
4
2
1Delete
Euro
Litres
Enter
C3
C2
C1
C0
R2
R1
R0
NC
R3
Not
Used
The box containing the devices
enclosed in the dotted line must
have protection degree IP54

Type / N°
Rev.
Fw
Date
Page
Total pages
EW055.600D
D
4L
6th June 2018
6
43
EsiWelma®s.r.l.
2. FUNCTIONAL DESCRIPTION
2.1. Data display
TW1 computing head can be combined with one-nozzle fuel dispensers, data are always
visualised on a 6-digit display for the amount to be paid, a 5-digit display for delivered fuel
and a 4-digit display for unit price.
TOTAL AMOUNT
DELIVERED FUEL
UNIT PRICE
Figure 2: Max data display
25mm high back lighted LCDs made up the display bars. The backlighting system is made up
of a printed circuit with a led matrix welded on. It is settled on the backside of the metal box
and gives out a green light. As an alternative it is possible to use the dispenser’s own light.
2.2. Operating sequence description
Once initialised, the computing head carries out some checks:
EPROM - it checks the EPROM CRC and compares it to the data reported
on the program.
RAM - it checks the writing and reading ability of data RAM.
EEROM - it checks the congruence of the data reported in EEROM.
DISPLAY - it checks the connection status of the display.
RX-TX - presence of active connection with Host.
DATA COMPLIANCE - compliance of the data used by RAM with the originals in
E2ROM.
UNIT PRICE - it checks that the unit price is not zeroed.
ANALOG INPUTS - it checks the presence of pressure and temperature transmitters.
MEASUREMENT - it checks that the mass flow meter (in case of MODBUS system)
is present and communicating.
MAX. PRESSURE - it checks that pressure does not exceed the maximum
functioning pressure of the plant.
If the above mentioned checks give a positive result, display temporarily shows the program
code and the data about the last delivery, then it switches-off. In case of anomalies display
shows the relevant error code (See further, “Anomalies management” §3).
When the dispenser is in stop-mode , the computing head performs continuously the
same controls described above.
p.u.
Kg

Type / N°
Rev.
Fw
Date
Page
Total pages
EW055.600D
D
4L
6th June 2018
7
43
EsiWelma®s.r.l.
The refuelling operation begins by turning the switch to START
If the dispenser is available and nozzle is connected to the refuelling receptacle on the
vehicle, it’s possible to actuate the “START” switch, activating the delivering sequence of the
computing head, which will perform the following controls:
The same as described above - see §2.2
PULSER - in case of a pulse measuring device, the presence of
pulses is verified in time compliance.
TOTAL COUNTER - verifies the presence of the electromechanical total
counter
HF - verifies that the compressed natural gas flow does
not exceed the set value, so that in case of a gas
loss due to the cut of a nozzle connected to the
vehicle, flow can be immediately stopped.
If the above mentioned checks give a positive result, the refuelling procedure can start with a
visual control by display and a subsequent activation of the solenoid valves.
Display - All digits show 8, then blank and at last 0.00 Euro
and 0.00 kg. Each phase takes about 1 second: in
this way user can verify immediately the good
working of each step.
Figure 3: Refuelling start sequence; CNG metric counting version
During the refuelling process the computing head executes the following functions:
Activation of the command modules of the following devices: solenoid valves and
operating lights.
As defined during the set-up: Pulse acquisition coming from the transducer
Every pulse is equivalent to 10g.
Acquisition of the delivered quantity through
communication with the mass flow meter.
Calculation and visualization of the delivered quantity and the relevant amount.
Control of the validity of the visualized data (implicit with the control of Ram and Eprom).
Functional control of the single or both displays.
Presence control of the electro mechanical total counter and managing of both electro
mechanical and/or electronic total counter.
p.u.
Kg
p.u.
Kg
p.u.
Kg
p.u.
Kg

Type / N°
Rev.
Fw
Date
Page
Total pages
EW055.600D
D
4L
6th June 2018
8
43
EsiWelma®s.r.l.
Delivery ends because of:
Opening of the “start” switch.
Reaching of a pressure in the vehicle cylinder that makes the flow tend to zero.
Reaching of the maximum allowed pressure value in the vehicle cylinder.
Reaching of the maximum amount or of the maximum delivered quantity.
Anomalies (see §3).
Blocking order by Host.
…If delivery is stops due to anomalies:
display shows, if possible, the relevant error code. (see troubleshooting §3.).
2.2.1 Manual delivery
Operator decides the beginning of the delivering process, acting on the “START” switch and
ends the refuelling by acting on the “START” switch again, when the desired quantity is
reached or when the tank in completely filled.
2.2.2 Pre-set value delivery
The computing head provides to stop delivery once the pre-set value is reached, both in case
of programming by pre-set buttons and in case of Host programming.
The requested quantity is shown as follows:
Unit price display - always active
Amount display - if pre-setting is in Euro, display shows the requested
value, otherwise it is shaded.
Quantity delivered display - if pre-setting is in litres, display shows the requested
value, otherwise it is shaded.
Figure 4: Example of a 5.00€ Figure 5: Example of a 10Kg
Amount pre-setting delivered quantity pre-setting
2.2.3 Programming by Host
Every time the computing head is connected to a Host with Post-pay function, it can receive
an order of price change, by sending a new unit price, or an order of delivering stop.
Metrological parameter settings cannot be modified by Host.
Unit price cannot be modified during the delivery.
p.u.
Kg
p.u.
Kg

Type / N°
Rev.
Fw
Date
Page
Total pages
EW055.600D
D
4L
6th June 2018
9
43
EsiWelma®s.r.l.
2.2.4 Programming by a 16-key keyboard
When computing head switches on, it makes a presence control of the keyboard. If this test is
positive, the computing head manages the keyboard to pre-set a quantity or an amount to be
delivered.
1
2
3
DELETE
4
5
6
ENTER
7
8
9
Euro
Not
Used
0
,
Kg/Smc
Figure 6: 16-key Keyboard
With nozzles in place, keyboard works and can be used as follows:
1. Choose Euro or Liter pre-set by pressing the corresponding button.
2. Press number buttons (with comma, if necessary) to pre-set value.
3. Press « ENTER». Now the display of the computing head shows on the LCD the amount
(upper line) or the quantity delivered (central line).
4. If the value is correct, delivery can start. If an error occurs, press «DELETE» and repeat
steps 1÷3.
During the delivery, keyboard doesn’t work.
When operator puts the nozzle back in place another operation is possible.
2.2.5 Automatic stop sequence
Automatic stop occurs in two phases:
Flow rate reduction by controlling an optional solenoid valve. The point of intervention
can be varied by set-up (bP parameter) following the procedure described below.
Motor and solenoid valve stop.

Type / N°
Rev.
Fw
Date
Page
Total pages
EW055.600D
D
4L
6th June 2018
10
43
EsiWelma®s.r.l.
2.2.6 Supply voltage blackout management
If during normal operation a supply voltage black out or even a blackout occurs, both when
nozzle is inserted and during delivery, the computing head enters a procedure called PWF
which allows to memorise: amount, quantity delivered and absolute totalizer. The data
display is maintained for about 30 minutes from the moment the network shortage occurred.
The power supply lack is visualized writing “OFF” on the unit price display. The network
shortage state is displayed by writing OFF on the unit price bar. When power supply is
restored, data related to interrupted delivery are read by the memory and visualised on the
display and send to the Host, if present.
2.3. Connection to Host
This computing head as its standard can be connected by “Pumalan” 3 wire current loop TX,
RX, Gnd. Different connections are possible by adding an adapter. To use and implement
different protocols, a license released by manufacturer is needed.
Pumalan is a registered mark of GILBARCO (LOGITRON).
2.4. Euro €
The standard computing head connection is foreseen with three cables, TX, RX, Gnd.
The computing head, by its set-up, can work with different foreign currencies: operator can
set the decimal digits in the unit price and in the amount. In any case operator can choose
quickly the Euro set by setting jumper J3: while starting, the computer head will set the
correct decimal digits. Further, as requested from the
standard, in those countries,
which are approaching to the
Euro, after the refuelling
process shown in local
currency, it’s possible to
visualize the amount converted
in Euro by temporarily pushing
an appropriate button.
Figure 7: Temporary amount conversion to Euro
The standard rate DGII-C-4(99) is used as conversion factor.
By pushing the button for a second time, the visualization will switch back to the local
currency value. If another refuelling process should be started, the computing head switches
in any case to the normal visualization.
2.5. Delivery in Self-Service mode
In accordance with the Decree dated 11 September 2008, amendments and supplements to
Decree of Minister dated 24th May 2002 about the rules for fire prevention and planning,
construction and operation of distribution systems of natural gas for vehicles. (GU n. 232 del
3-10-2008)
Ps
Ps/Kg
Kg
p.u.
p.u.
Ps
Ps/Kg
Kg

Type / N°
Rev.
Fw
Date
Page
Total pages
EW055.600D
D
4L
6th June 2018
11
43
EsiWelma®s.r.l.
The computing head can work in Self Service mode following the procedures required and
described below:
2.5.1 Electrical devices involved
In addition to the lights (red and green) the
following devices will be installed on board of the
dispenser: a “deadman’s break” push button
(mushroom head, no block, normally open) , an
emergency push button (with block interrupting the
power supply to distributor) and a 3-position key
selector (1 unstable and 2 stable). Figure 8: “deadman’s break” push button
Aloof (safe zone), a button (normally closed) to disable the delivery to the user by the
operator (connected in series with the dead man's button).
The computing head manages these devices by the following digital inputs.
1 Input « deadman’s break » temporary voltage free contact, normally open
2 Input «Reset deadman’s break » temporary contact of the 3-position key selector
3 Input selector «Self (AUT) / Served (MAN)» bistable contact of the 3-position key
selector, contact closed in position Served.
2.5.2 Sequence of delivery
The 3-position key selector allows the operator to choose the operating mode of the
dispenser: Manual (SERVED) or Automatic (SELF-SERVICE).
The positions of the selector are:
1 Deadman’s break Reset (counterclockwise
rotation) temporary, return to central position
2 Automatic Self-Service (central position)
close stable contact.
3 Manual Served (clockwise rotation),
open stable contact.
The key can be removed only in positions 2 and 3 Figure 9: Activation Key of
Self-Service/Served mode
Manual (Served) mode works as described in §2.2.
In addition to what already explained, operator can stop and restart the flow of gas without
resetting the current delivery. By the “deadman’s break” push button in the manual mode, the
delivery starts and stops alternately every time it is pushed.
This function can be repeated several times consecutively without resetting the counting. The
delivery definitely finishes when the user puts the nozze back in place or when the condition
of low flow (full bottle) is reached.
Comune
Deadman's break (NO)
2
3
Common
Temporary N.O.
N.O.
1Aut
Reset

Type / N°
Rev.
Fw
Date
Page
Total pages
EW055.600D
D
4L
6th June 2018
12
43
EsiWelma®s.r.l.
Automatic mode (Self-Service) is almost the same but during the delivery the “deadman’s
break” push button must be always pushed. If this push button is released before the
refuelling finishes, delivery stops and has to be locally rehabilitated by operator using the key
selector in reset position, then the user can re-start the delivery by pushing (and keeping) the
“deadman’s break” push button.
In remote, by the button "Single Block" (Normally Closed), located in series with the "
deadman’s break" device, the operator may at any time stop the current delivery , which can
be rehabilitated only locally using the key selector in reset position.
According to the standard or the Self-Service mode, the cumputing head works
automatically, detecting the presence of the I / O Expansion switch board.
The card connection on the flat I²C Bus, is described and shown below. See wiring B.T. § 7.1
2.5.3 Warning light management
To allow operators to follow in remote the operations, each possibile status of the dispenser
is coupled with a unique code as shown in the table below:
Status of the dispenser
Green Light
Red Light
Dispenser off
Off
Off
Dispenser Ready
On
Off
Nozzle off
Flashing
Off
In delivery
Off
On
End of delivery (for low flow or Stop by HOST in Auto)
Off
Flashing
End of delivery (Nozzle in) ≡Dispenser Ready
On
Off
Deadman’s break (push button released)
Flashing
Flashing
Computing head error (Dispenser not available)
On
On
Computing head set-up (Dispenser not available)
On
On

Type / N°
Rev.
Fw
Date
Page
Total pages
EW055.600D
D
4L
6th June 2018
13
43
EsiWelma®s.r.l.
3. TROUBLESHOOTING
During its normal working the computing head controls the internal data flow and the
correspondence of data coming from outside. Possible anomalies are managed in different
ways according to the damage they may cause to data.
The recognized errors can be subdivided in fatal and non fatal errors as described as follows.
In any case the computing head stops the current refuelling, visualizes the memorized
recognized error code and, if connected to a Host, communicates the state of error using a
proper error code.
3.1. Fatal errors
Fatal errors are normally due to malfunctioning which may cause data loss. In such a case
the computing head stops the delivery, displays the relevant code and does not re-start. To
start again it must be reset by switching off power supply for some second.
Data congruence
EPROM Error
RAM Error
EEROM Error
Presence of totalizer Error
Presence of optional I/O (Self-Service)
Pulser or communication with mass flow
meter
3.2. Non fatal errors
Belong to such a category all blocks due to an anomalous status of the field, and all
temporary blocks occurring due to an anomalous working process, caused by a secondary
situation such as the lack of unit price, or occasionally, for example because of an incorrect
data due to a disturbance. In that case the error will be automatically deleted as soon as the
anomalous status that created it ends.
The computing head tries three times to restart; at the fourth unsuccessful attempt, the error
turns into fatal.
Display 1 and 2
Communication with Host
Set-up data loss
Maximum system pressure
Maximum delivering flow
Temperature transducer presence
Pressure transducer presence
Pulser disconnection

Type / N°
Rev.
Fw
Date
Page
Total pages
EW055.600D
D
4L
6th June 2018
14
43
EsiWelma®s.r.l.
3.3. Error review table
Errors review table
Fatal errors
Description
Data congruence
EPROM error
Ram error
Eerom error
Totalizer Error
Spare Inputs
Mass flow meter control
(also for impulsive type)
Display 1 after 3 errors NF
Display 2 after 3 errors NF
Maximum pressure error after
3 errors NF
High flow rate error after 3 NF
errors
Temperature sensor. after 3
NF errors
Pressure sensor after 3 NF
errors
Pulser Output not connected
after 3 NF errors
Protocol Code
[E+][E-]
Ascii
[3][0]
[1][1]
[1][0]
[1][5]
[2][2]
[4][7]
[4][2]
[G][0]
[G][0]
[D][4]
[G][7]
[D][6]
[D][5]
[G][1]
Hex
[0x33][ 0x30]
[0x31][ 0x31]
[0x31][ 0x30]
[0x31][ 0x35]
[0x32][ 0x32]
[0x34][ 0x37]
[0x34][ 0x32]
[0x47][ 0x30]
[0x47][ 0x30]
[0x44][ 0x34]
[0x47][ 0x37]
[0x44][ 0x36]
[0x44][ 0x35]
[0x47][ 0x31]
Display
Code
FECd
FEEP
FErA
FEEE
FEto
FEin
FEMF
FEPd
FEPd
FEHP
FEHF
FESt
FESP
FEPU
Non fatal errors
Description
Display 1
Display 2
Communication
Set-up data missing
Maximum pressure
High flow rate
Presence Temperature sensor
Presence Pressure sensor
Pulser Output not connected
Protocol Code
[E+][E-]
Ascii
[7][0]
[7][0]
[8][0]
[4][1]
[4][4]
[7][7]
[4][6]
[4][5]
[7][1]
Hex
[0x37][ 0x30]
[0x37][ 0x30]
[0x38][ 0x30]
[0x34][ 0x31]
[0x34][ 0x34]
[0x37][ 0x37]
[0x34][ 0x36]
[0x34][ 0x35]
[0x37][ 0x31]
Display
Code
Erd1
Erd2
ErLn
ErSU
ErHP
ErHF
ErSt
ErSP
ErPU

Type / N°
Rev.
Fw
Date
Page
Total pages
EW055.600D
D
4L
6th June 2018
15
43
EsiWelma®s.r.l.
Description of anomalies:
Display
Communication with Host
Set-up data missing
Maximum system pressure error
High flow rate error
Presence of temperature sensor
Presence of pressure sensor
Pulser output not connected
LCD single bar presence control, with
identification of the absent line
Error Code: Erd1 o Erd2
The computing head verifies the existence
of polling from Host every 5 seconds at
least. If there is no polling, it stops the
delivery
Error Code: ErLn
If there are no Set-up data or they are not
conformable, the computing head does not
deliver and operator must input these data
Error Code: ErSU
Verifies the status of the pressure sensor (or
pressure sensor switch) and in case of
exceeded pressure delivering procedure will
be blocked.
Error Code: ErHP
Verifies the outgoing flow rate and if the
maximum value is exceeded, delivering
procedure will be stopped.
Error Code: ErHF
Verifies that the signal coming from the
temperature sensor Pt100, respects the
functioning range (-60°C ÷ +60°C)
Error Code: ErSt
Verifies that the signal coming from the
pressure sensor respects the functioning
range (4÷ 20mA)
Error Code: ErSP
Verifies that, from the beginning of the
delivering process (solenoid valve start), the
relevant pulses arrive within 6s.
Error Code: ErPU

Type / N°
Rev.
Fw
Date
Page
Total pages
EW055.600D
D
4L
6th June 2018
16
43
EsiWelma®s.r.l.
Data congruence
EPROM error
RAM Error
EEROM Error
Totalizer Error
Optional Inputs/Outputs
Mass flow meter control
Data correspondence control. The computing
head checks, even during the delivery, both
EPROM and RAM data. In case an error
occurs, it finally stops the delivery.
Error Code: FECd
When nozzle hangs on, the computing head
checks the EPROM checksum. If something
is wrong, it doesn’t allow the delivery.
Error Code: FEEP
When nozzle hangs on, the computing head
checks RAM. If something is wrong, it
doesn’t allow the delivery.
Error Code: FErA
When nozzle hangs on, the computing head
checks the E²rom checksum. If something is
wrong, it doesn’t allow the delivery.
Error Code: FEEE
The computing head checks the totalizer
presence. In case an error occurs, it finally
stops the delivery.
Error Code: Feto
The computing head verifies the presence of
device dedicated to Self Service and other
applications.
Error Code: FEin
The computing head verifies the communi-
cation and/or of the reset procedure of the
mass flow meter; In case an error occurs it
finally stops the delivery.
Error Code: FEMF
(also in the case of impulsive type mass flow)

Type / N°
Rev.
Fw
Date
Page
Total pages
EW055.600D
D
4L
6th June 2018
17
43
EsiWelma®s.r.l.
3.4. Operating modes
For fitting different field operating modes, the computing head can work in different ways, that
can be subdivided in two principal categories:
1. system adaptation (to implant)
2. dispenser adaptation
3.4.1 System adaptation
The management of the solenoid valves is adaptable to the type of system where the
dispenser is installed:
Single level for the implants that have only one compression system installed
Cascade 2 levels for the implants that have a 2-level compression system installed
Cascade 3 levels for the implants that have a 3-level compression system installed
3.4.2 CNG dispenser adaptation
The management of the solenoid valves is adaptable on the type of dispenser installed:
EV1 active only during the first level phase
EV1 always active until the end of refuelling
High pressure control determinate with a pressure switch
High pressure control determinate with a pressure transmitter
3.5. Types of refuelling
The computing head can be adapted to different national standards, allowing to modify the
way of refuelling as follows:
No control:
–Free delivery up to the maximum available pressure.
Compensated:
–It modifies the end of the refuelling in function of the pressure value related to
the ambient temperature (so that at 25°C the pressure can not exceed the
specific value inserted during the set-up by PCON parameter).

Type / N°
Rev.
Fw
Date
Page
Total pages
EW055.600D
D
4L
6th June 2018
18
43
EsiWelma®s.r.l.
4. PROCEDURES
Further the normal refuelling, there are three different possible procedures:
Reading from the absolute total counter
Computing head set-up (changing the configuration parameters), price change
Metrical office (anomaly simulation)
To start a procedure, operator has to push one of the push-buttons on the set-up board;
display will show the following notice:
Push on one of the set-up buttons, to activate the relevant
procedure; push-buttons are available on the printed circuit
connected to the same cable of the display:
Figure 10: Visualization “waiting procedure selecting”
Procedureblack «t» reading absolute totalizer
Procedurered «S» Set-up computing head: Para-
meters changing
Proceduregreen «U»Metrical office: anomaly simulation t S U
Figure 11: Set-up buttons
4.1. Reading from the absolute totalizer
The absolute totalizer is a counter which cannot be reset (to zero) and allows to store and
display the quantity delivered in Kg or Smc on 10 digits. Since it is not possible to dispose of
such an extended display, digits are subdivided into groups and visualised as follows:
1st group 1digit 2nd group 3 digits 3rd group 3 digits 4th group 3 digits
0000 000 000
most significant digit less significant digit
0.000.000.000
p.u.
Kg

Type / N°
Rev.
Fw
Date
Page
Total pages
EW055.600D
D
4L
6th June 2018
19
43
EsiWelma®s.r.l.
By pushing the black button «t», the computing head shows the first group of digits; to
visualize the second, third and fourth group, advance by pushing the green button «U» once
each time.
Figure 12: Display absolute total counter Kg
Further, a non annullable electro mechanical total counter that can show 7 digits can be
installed on the display. This counter is electronically controlled and in case of failure, the
computing head stops the occurring refuelling process and visualizes the error code: FEto.
4.2. Computing head set-up
After entering in set-up mode by pushing the red button «S», the computing head requires a
password; if nothing has been previously changed, the default password is “20000”. To insert
the correct code follow this procedure:
To enter the SETUP procedure, operator has to set JP2 Jumper “closed”.
SETUP can’t be done if JP2 Jumper is “open”.
Set Jumper J2
Push the black button «t» until the value of the first digit has
been reached
Push the red button «S» to switch to the next digit
Once the correct value has been inserted also for the last digit,
push the red «S» button again to enter the set-up.
Figure 13: Enter password
If the password is not correct, the computing head immediately
breaks down the set-up procedure and turns.
If the password is correct, it’s possible to proceed with the upgrade
of the values of the parameters.
If jumper J2 has not been inserted already, the computing head
indicates that it is required for the set-up to insert the jumper now
with the shown message: Set JP2
Figure 14: Notice insert jumper JP2
p.u.
Kg
p.u.
Kg
p.u.
Kg
p.u.
Kg
p.u.
Kg
p.u.
Kg

Type / N°
Rev.
Fw
Date
Page
Total pages
EW055.600D
D
4L
6th June 2018
20
43
EsiWelma®s.r.l.
The following table shows all the available parameters:
Computing head set-up parameters
Code
Imprint
Signification
Range
Step
Default
Units
01
LF
Functioning level
1-3
1
2
----
02
St
Functionality Electro valve 1
0-3
1
0
----
03
Mt
Meter type
0-3
1
3
----
04
Sb
ModBus communication baud rate
0-3
1
0
----
05
L0
Low flow rate 1st...2nd level (stop for mono-level)
1-16
1
2
10g
06
t0
Acquisition delay for L0
0-15
1
8
s
07
L1
Low flow rate 2nd…3rd level (stop for bi-level)
1-16
1
1
10g
08
t1
Acquisition delay for L1
0-15
1
12
s
09
L2
Low flow rate 3rd level (stop delivery)
1-16
1
1
10g
10
t2
Acquisition delay for L2
0-15
1
12
s
11
AL
LAN address
1-32
1
1
----
12
HF
High flow rate
1-299
1
150
10g/s
13
AP
Enables the pressure switch
0-15
1
12
----
14
AC
Enables the pressure compensation
0-1
1
0
----
15
HP
Pressure switch intervening values
200-299
1
235
barg
16
Pcon
Compensation pressure
150-250
1
207
barg
17
tC
Compesation temperature
0 –50
1
21
°C
18
Ot
Temperature offset
± 20
1
10
°C
19
tF
Duration of the first puff
2-60
1
4
s
20
tS
Duration of the second puff
1-30
1
10
s
21
dr
Awaiting reading
1-40
1
10
s
22
Po
POS option
0-2
1
0
----
23
Pr
Kind of preset
0-2
1
0
----
24
bP
Slowdown (low flow)
0-90
10
50
10g
25
cA
Early closure of the solenid valve
0-11
1
6
10g
26
cM
Hose compensation in preset mode
0-10
1
5
10g
27
tP
Nozzle switch acquisition time
0-10
1
1
s
28
FC
Holding time of the count beyond the stop
0-40
5
30
0.1s
29
PL
Protocol Level
1-4
1
4
----
30
PC
Pressure switch contact polarity
0-1
1
0
----
31
Ar
Amount approximation
0-3
1
3
----
32
DP
Unit price decimal digits
0-3
1
3
----
33
DI
Amount decimal digits
0-3
1
2
----
34
Ct
Passage to round digit
1-3
1
1
----
35
nd
Number of connected displays
1-2
1
1
----
36
CE
Number of delivered display digits
5-6
1
5
----
37
bL
Delivery stop for LAN error
0-1
1
0
----
38
MC
Flow meter zero setting procedure
0-1
1
0
----
39
PS
Specific weight
255-9999
1
7000
----
40
P1
Preset value push button 1
0-9/dig
1
10
€
41
P2
Preset value push button 2
0-9/dig
1
5
€
42
CF
Conversion factor currency / €
0.1-9.99999
1
6.55957
----
This manual suits for next models
1
Table of contents
Popular Computer Hardware manuals by other brands
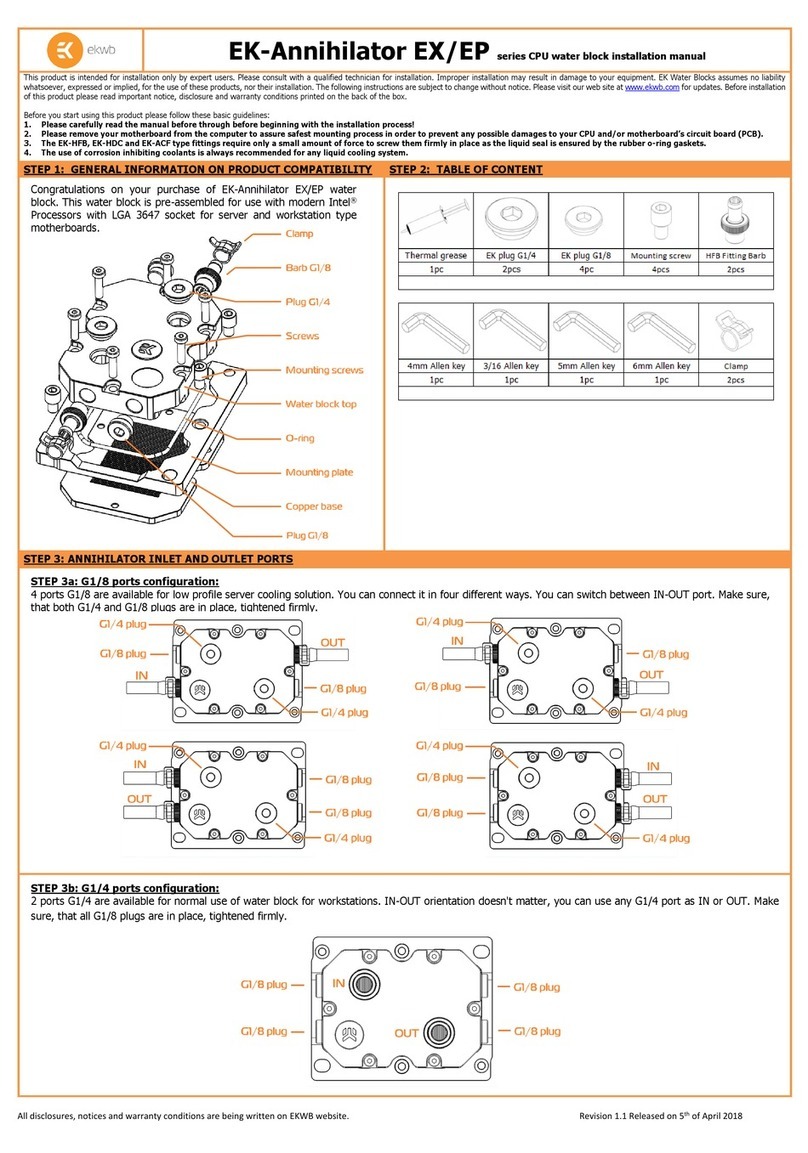
ekwb
ekwb EK-Annihilator EX/EP Series installation manual

Intel
Intel DC3217BY user guide

ASRock Industrial
ASRock Industrial iBOX 250 Series user manual

Pickering
Pickering 50-297 user manual
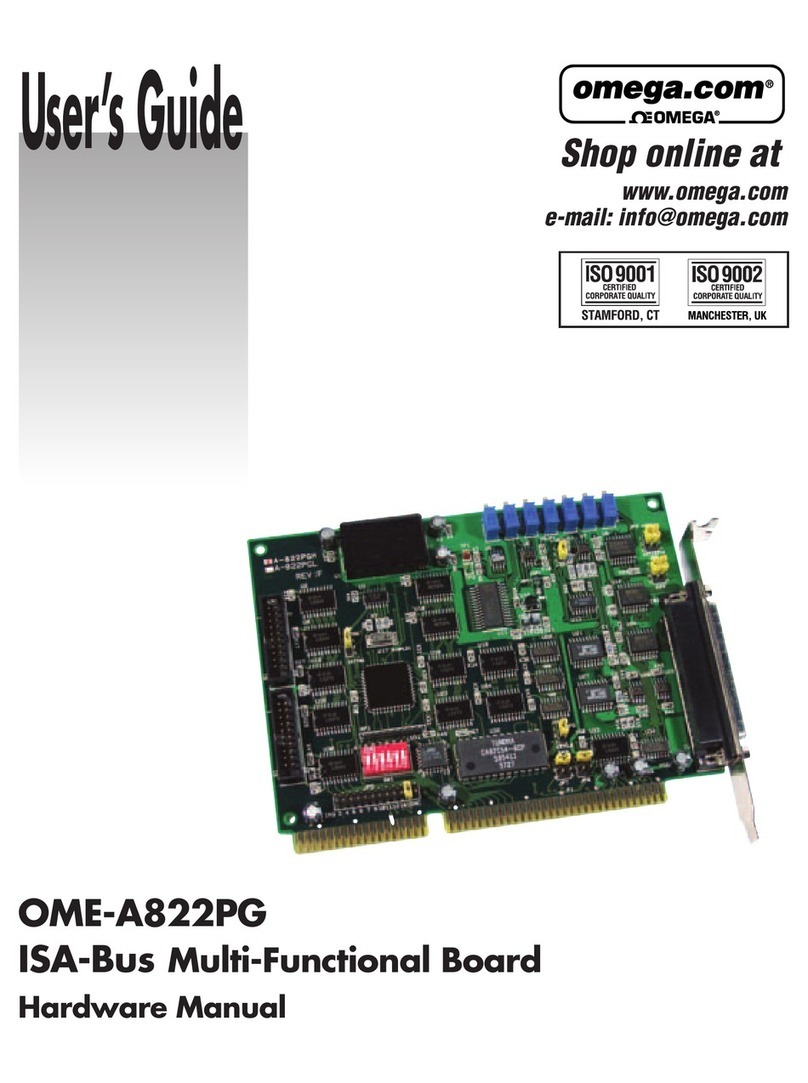
Omega
Omega ISA- BUS MULTI-FUNCTIONAL BOARD OME-A822PG Hardware manual
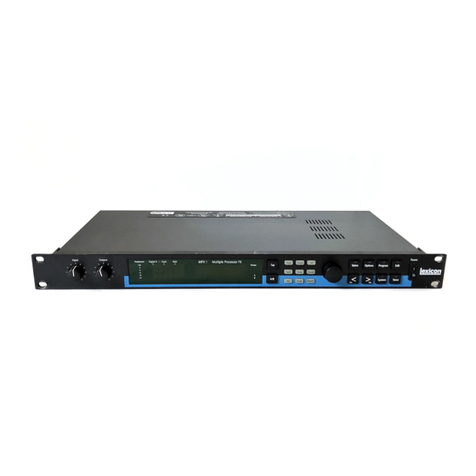
Lexicon
Lexicon MPX - ADDENDUM REV 1 Quick reference guide