ETL MC68HC912 User manual

Engineering Technical Laboratory Rev. 6
MC68HC912/9S12 FLASH/EEPROM Programmer
User’s Guide
© ETL 2004-2006 Microcontroller Development Tool

TABLE OF CONTENTS
1. PREFACE...................................................................................................................................... 3
2. CHECKLIST AND REQUIREMENTS........................................................................................ 3
3. INSTALLATION AND USE ........................................................................................................ 4
3.1 PROGRAMMER CHECK AND CONNECTION TO PC...................................................... 5
3.2 PROGRAMMER FIRMWARE UPDATE.............................................................................. 5
4. INTERFACE TYPES .................................................................................................................... 6
4.1 IN-CIRCUIT PROGRAMMING ............................................................................................ 6
4.2 ON-BOARD PROGRAMMING............................................................................................. 6
5. WORKING WITH TARGET MCU.............................................................................................. 7
5.1 MC68 HC912 Devices............................................................................................................. 7
5.1.1 In-Circuit EEPROM/FLASH reading example ................................................................ 7
5.1.2 In-Circuit EEPROM/FLASH programming example....................................................... 7
5.1.3 On-Board EEPROM/FLASH reading example................................................................ 8
5.1.4 On-Board EEPROM/FLASH programming example ...................................................... 8
5.2 MC 9S12 Devices.................................................................................................................... 9
5.2.1 Features of MC9S12xx128 Devices with 0L85D/1L85D masksets................................. 9
6. FILE OPERATIONS................................................................................................................... 11
6.1 LOAD FILE INTO BUFFER ................................................................................................ 11
6.2 SAVE FILE FROM BUFFER............................................................................................... 11
7. ERRORS AND TROUBLESHOOTING .................................................................................... 12
8. WARRANTY STATEMENT...................................................................................................... 14
9. APPENDIX.................................................................................................................................. 15
Figure 2. In-Circuit programming schematic diagram for HC912/9S12 MCU............................... 15
Figure 3. In-Circuit wiring diagram for MC68HC912B32, 80-PIN QFP Package......................... 16
Figure 4. In-Circuit wiring diagram for MC68HC912D60/DG128, 112-PIN TQFP Package........ 17
Figure 5. In-Circuit wiring diagram for MC68HC912D60A/DG128A, 112-PIN LQFP Package.. 18
Figure 6. In-Circuit wiring diagram for MC68HC(9)12D60, 80-PIN QFP Package ...................... 19
Figure 7. In-Circuit wiring diagram for MC68HC912D60A, 80-PIN QFP Package...................... 20
Figure 8. In-Circuit wiring diagram for MC9S12Dx64/Dx128/Dx256, 80-PIN QFP Package ...... 21
Figure 9. In-Circuit wiring diagram for MC9S12Dx64/Dx128/Dx256, 112-PIN LQFP Package.. 22
Figure 10. In-Circuit wiring diagram for MC9S12H-Family 112-PIN LQFP Package.................. 23
Figure 11. In-Circuit wiring diagram for MC9S12H-Family 144-PIN LQFP Package.................. 24
©ETL 2004-2006 MC68HC912/9S12 Programmer User’s Guide 2

1. PREFACE
This manual will guide you through the installation and operation of the ETL
MC68HC912/9S12 Programmer, referenced hereafter as the HC912-Programmer.
The HC912-Programmer has been designed for Reading, Programming of FLASH,
EEPROM contents of the next Motorola Microcontroller Unit (MCU):
9MC68HC912 DC128A (3K91D) 9MC9S12 DG128B (0L85D)
9MC68HC912 DC128 (0K50E) 9MC9S12 DT128B (0L85D)
9MC68HC912 DG128 (5H55W) 9MC9S12 A128B (0L85D)
9MC68HC912 DG128A (3K91D) 9MC9S12 DB128B (0L85D)
9MC68HC912 D60A (2K38K) 9MC9S12 DT128B (1L85D)
9MC68HC912 D60 (0K75F) 9MC9S12 DG256C (2K79X)
9MC68HC912 D60 (0K13J) 9MC9S12 DT256C (2K79X)
9MC68HC912 D60 (4F73K) 9MC9S12 DP256C (2K79X)
9MC68HC912 B32 (4J54E) 9MC9S12 DP512 (1L00M)
9MC68HC912 B32 (9H91F) 9MC9S12 D64 (2L86D)
9MC9S12 DT128B (3L40K)
9MC9S12 H128 (1K78X)
9MC9S12 H256 (1K78X)
&Note: Most number of devices can be programmed in two operating modes In-
.
ove in list can’t be guaranteed of correct
grammer.
Circuit and On-Board.
&Note: On-Board programming must be used when device secured or BDM
module disabled only. See Section 4.2 for details
&Note: Devices that not mentioned ab
reading, programming by HC912-Pro
2. CHECKLIST AND REQUIREMENTS
The d with the HC912-Programmer and the
system
– Optional Extra
following describes what items are supplie
requirements if used by a PC.
9HC912-Programmer – supplied
9Two HC912 QFP112 Adaptors – supplied
9Two MC9S12 112QFP Adaptors– supplied
le - supplied9Cable -A DB9 “straight-thru” cab
9HC912-Programmer PC software on CD-ROM
..8)
Power supply 12 Volt/500 mA linear power supply source
OS -MS-Windows (Win98, Win2000/XP/2003)
Desktop PC and a free Serial Communication Port (COM1.
Memory - Minimum 32 Mbytes
Display - Color SVGA display recommended
©ETL 2004-2006 MC68HC912/9S12 Programmer User’s Guide 3

3. INSTALLATION AND USE
The HC912-Programmer includes two LED’s and mode jumper (Figure 1).
Color LED’s indicates programmer state and external power supply voltage (Table 1, 2).
GREEN HC912-Programmer is ready.
GREEN Flashing HC912-Programmer is busy.
RED Error occurred while operation.
DARK Voltage applied to HC912-Programmer lower than 6 Volt.
Table 1. LED D1 color meaning
GREEN Motorola device powered on.
DARK Motorola device powered off.
Table 2. LED D4 color meaning
Jumper-1 (JP1) is intended for HC912-Programmer mode selection (see Table 3).
JP1 Shorted Normal operation. Motorola device EEPROM/FLASH
Reading/Programming.
JP1 Opened Service mode. HC912-Programmer firmware update.
Table 3. HC912-Programmer operation modes
&Note: When Service mode sele ted LED D1 will be RED.c
12V
Power
Connector
SerialPortConnector
COM1...8
BDMICP
Motorola Device Socket for
On-BoardProgramming
D4 D1
JP1 1-Pin Key
BKGD GND
RES
VDD
P5
Figure 1. The HC912-Programmer board layout
©ETL 2004-2006 MC68HC912/9S12 Programmer User’s Guide 4

3.1 PROGRAMMER CHECK AND CONNECTION TO PC
Connect the power supply source to HC912-Programmer (an external 12 V DC power
supply source is required).
Attach a COM port cable to the 9-pin connector on the programmer and to a COM port
on the PC.
Insert jumper JP1 (see Figure 1).
Remove any adaptor from Motorola device socket.
Turn On power supply source and make sure that LED D1 appear green.
Start HC912-Programmer software.
After few seconds you should see on display message: “MC68HC912 Programmer Ver-
X.X detected”.
In case when you should see message: “MC68HC912 Programmer Ver-X.X not
found”, change COM port number. To do that select “Tools” menu item and than select
“Comm Port Options”. Select new COM port number. After pressing “OK” button the
new setting will be applied and software reattempts connection with programmer.
Now HC912-Programmer ready to operate.
&Note: To speed up connection between HC912-Programmer and PC
re if required (see Section 3.2).
communication port baud rate must be set to maximum value.
&Note: Update HC912-Programmer firmwa
3.2 PROGRAMMER FIRMWARE UPDATE
This section describes how to update firmware (ATMEGA and XILINX) of HC912-
Program er
Cdetected” and version
sp
ssage box “Firmware Update” appeared, press “OK” button.
are update completed, turn Off power supply, close HC912-Programmer
so
1 appear green.
Start HC912-Programmer software on PC. New firmware version “MC68HC912
Programmer Ver-X.X detected” will appear.
m .
Remove JP1 (see Figure 1).
Turn On power supply; make sure that LED D1 appears red.
Start HC912-Programmer software.
ompare firmware version “MC68HC912 Programmer Ver-X.X
ecified in “Help>About” menu item.
If versions not coincide, follow next steps to update firmware.
Select menu item “Tools>Firmware Update”.
After me
After firmw
ftware.
Insert JP1.
Turn On power supply. Make sure that LED
©ETL 2004-2006 MC68HC912/9S12 Programmer User’s Guide 5

4. INTERFACE TYPES
This section describes two interfaces, In-Circuit Programming (ICP) and On-Board
Programming (OBP) of HC912-Programmer.
4.1 IN-CIRCUIT PROGRAMMING
In-Circuit programming interface is basic for HC912-Programmer. With this interface HC912-
Programmer automatically detects target MCU bus speed. Ceramic resonator connected to target
MCU must be in range from 2 MHz to 16 MHz. If target MCU secured (9S12 devices) or BDM
module disabled (912 devices) there is no way to establish connection between MCU and HC912-
Programmer.
&Note: ECLK Pin on target MCU must be connected to circuit via resistor
&Note: When using In-Circuit programming interface remove adaptor from
gure 1).
1Kohm or higher to avoid damaging of this pin.
Motorola device socket (see Fi
4.2 ON-BOARD PROGRAMMING
On-board programming interface designed for establishing connection with target device when
MCU secured (9S12 devices) or BDM module disabled (912 devices). This interface allows
Read/Program EE
must be mounted -Programmer.
can be damaged!
&Note: When On-board programming interface used, remove cable from BDM
ICP connector (see Figure 1).
PROM/FLASH without any restrictions. To work with this interface type MCU
to the corresponding QFP adaptor supplied with HC912
&Note: When target adaptor with MCU mounted, check contacts careful to avoid
short circuit. Otherwise target MCU
©ETL 2004-2006 MC68HC912/9S12 Programmer User’s Guide 6

5. WORKING WITH TARGET MCU
This section contains overall information about Motorola MCUs supported by HC912-
Programmer. When HC912-Programmer successfully installed (see Section 3) target devices can
be read, program and verify.
5.1 MC68 HC912 Devices
This section describes basic rules working with next devices:
9MC68HC912 DC128A (3K91D)
9MC68HC912 DC128 (0K50E)
9MC68HC912 DG128 (5H55W)
9MC68HC912 DG128A (3K91D)
9MC68HC912 B32 (4J54E)
9MC68HC912 D60A (2K38K)
FLASH/EEPROM memory for these devices can be read, program in both OBP and ICP
interfaces.
&Note: On-Board programming interface not implemented for MC68HC912B32
device.
er
ed MCU is mount MCU on corresponding
aptor and use On-Board programming interface.
gure 2).
).
evice” button).
912-Programmer software.
SH” button.
hat means that +5 voltage
-Programmer became permanent green, reading completed.
ccessfully completed it is necessarily to save memory dump to
If some errors appeared during reading process refer to Section 7.
gure 2).
).
Extra care must be taken when working with EEPROM Shadow Word/Byte in ICP interface.
If BDM Lockout bit (NOBDML) programmed to zero, further access to MCU will be blocked aft
next reset. The only one way to grant access to lock
ad
5.1.1 In-Circuit EEPROM/FLASH reading example
Connect required pins to board with target MCU (see Appendix Fi
Remove any adaptor from Motorola device socket (see Figure 1).
Apply power to HC912-Programmer. LED D1 became to green light (see Table 1
Select corresponding device in HC912-Programmer software (“D
Select “Read Sequence” panel in HC
Press “EEPROM/FLA
Press “Start” button.
LED D4 on HC912-Programmer became to green light. T
regulator switched on and VCC applied to target MCU.
Now HC912-Programmer automatically detects MCU bus speed.
When LED D1 on HC912
Target MCU powered off.
After read sequence su
file (see Section 6.2).
5.1.2 In-Circuit EEPROM/FLASH programming example
Connect required pins to board with target MCU (see Appendix Fi
Remove any adaptor from Motorola device socket (see Figure 1).
Apply power to HC912-Programmer. LED D1 became to green light (see Table 1
Select corresponding device in HC912-Programmer software (“Device” Button).
©ETL 2004-2006 MC68HC912/9S12 Programmer User’s Guide 7

Load EEPROM/FLASH data from file (see Section 6.1) or enter data to Hex Editor.
HC912-Programmer software.
SH” button.
hat means that +5 voltage
mer became permanent green, programming
If some
SH programming, for a first
file.
ket on HC912-Programmer in according to 1 pin-
r.
2-Programmer software (“Device” Button).
HC912-Programmer became to green light. That means that +5 voltage
HC912-Programmer became permanent green light, reading
When read sequence successfully completed it is necessarily to save memory dump to
file (se
If some 7.
&t MCU HC912-Programmer must
in-
r.
Select “Program Sequence” panel in
Press “EEPROM/FLA
Press “Start” button.
LED D4 on HC912-Programmer became to green light. T
regulator switched on and VCC applied to target MCU.
Now HC912-Programmer automatically detects MCU bus speed.
When LED D1 on HC912-Program
completed. Target MCU powered off.
errors appeared during programming process refer to Section 7.
&Note: Extra care must be taken when programming the EEPROM Shadow
Word/Byte.
&Note: Strongly recommended before EEPROM/FLA
time, read EEPROM/FLASH contents and save it to
5.1.3 On-Board EEPROM/FLASH reading example
Mount target MCU on corresponding QFP adaptor.
Insert adaptor to Motorola Device Soc
key (see Figure 1).
Remove cable from BDM ICP connector (see Figure 1).
Apply power to HC912-Programme
Select device in HC91
Select “Read Sequence” panel in HC912-Programmer software.
Press “EEPROM/FLASH” button.
Press “Start” button.
LED D4 on
regulator switched on and VCC applied to target MCU.
When LED D1 on
completed.
e Section 6.2).
errors appeared during reading process refer to Section
&Note: When target MCU mounted on adaptor check contacts careful to avoid
short circuit. Otherwise target MCU can be damaged!
Note: During removing the adaptor with targe
be powered off to avoid damaging of programmer and target MCU!
5.1 ample.4 On-Board EEPROM/FLASH programming ex
Mount target MCU on corresponding QFP adaptor.
Insert adaptor to Motorola Device Socket on HC912-Programmer in according to 1 p
key (see Figure 1). ector (see Figure 1).Remove cable from BDM ICP conn
2-ProgrammeApply power to HC91
Select device in HC912-Programmer software (“Device” Button).
Load EEPROM/FLASH data from file (see Section 6.1) or enter data to Hex Editor.
©ETL 2004-2006 MC68HC912/9S12 Programmer User’s Guide 8

Select “Program Sequence” panel in HC912-Programmer software.
Press “EEPROM/FLASH” button.
LED D
regulat
When
comple
If some
g removing the adaptor with target MCU HC912-Programmer must
off to avoid damaging of programmer and target MCU!
amming the EEPROM Shadow
&ended before EEPROM/FLASH programming, for a first
LASH contents and save it to file.
Press “Start” button.
4 on HC912-Programmer became to green light. That means that +5 voltage
or switched on and VCC applied to target MCU.
LED D1 on HC912-Programmer became permanent green light, programming
ted.
errors appeared during programming process refer to Section 7.
&Note: When target MCU mounted on adaptor check contacts careful to avoid
short circuit. Otherwise target MCU can be damaged!
&Note: Durin
be powered
&must be taken when progrNote: Extra care
Word/Byte.
Note: Strongly recomm
time, read EEPROM/F
5.2 MC 9S12 Devices
This king with next devices:
MC9S
MC9S
&
MC
hi hen In-
Circuit es there
section describes basic rules wor
9MC9S12 D64 (2L86D)
MC9S12 DG128B (0L85D)9
9MC9S12 DT128B (0L85D)
9MC9S12 A128B (0L85D)
912 DB128B (0L85D)
912 DT128B (1L85D)
9MC9S12 DG256C (2K79X)
9MC9S12 DT256C (2K79X)
9MC9S12 DP256C (2K79X)
9MC9S12 DP512 (1L00M)
FLASH/EEPROM memory for these devices can be read, program in both OBP and ICP
interfaces.
Note: Use On-Board programming interface only if target MCU secured.
Extra care must be taken when working with FLASH Option/Security byte in ICP interface. If
U not erased (all EEPROM and FLASH bytes not equal to $FF) and FLASH Security byte not
equal to XXXXXX10B, further access to MCU will be blocked after next reset. To grant access to
MCU device must be mounted on corresponding adaptor and On-Board programming interface
must be used.
In all other respects EEPROM/FLASH programming technique similar to MC68HC912
devices (See sections 5.1.1-5.1.4)
T
5.2.1 Features of MC9S12xx128 Devices with 0L85D/1L85D masksets
s section describes specific behavior of MC9S12xx128 (0L85D/1L85D) devices w
programming interface is used. In according to Motorola errata relative to this devic
©ETL 2004-2006 MC68HC912/9S12 Programmer User’s Guide 9

is some
Only Bulk
solved by
this key a Backdoor Access Key disabled there is no
possibilities to disable security. To solve this problem the second method of security disabling
must b
Chip mode below:
when link with MCU completed it is necessarily to read all FLASH and
ore information see sections 5.1.3 On-
ave EEPROM and
ce panel. Also, press
rmanent green light, erasing
solder it back to board.
Figure 2).
rom Motorola device socket (see Figure 1).
are (“Device” Button).
e, $7BF0F Address to $FE in Hex Editor. That
e changes in
EEPROM and FLASH areas are possible.
If furth
Press “
Press “
LED D
regulat
When
comple
If some errors appeared during programming process refer to Section 7.
&Note: There is no way to restore EEPROM and FLASH contents after erasing.
That is strongly recommended read EEPROM and FLASH contents and save it
to file before erasing.
&Note: When target MCU mounted on adaptor check contacts careful to avoid
short circuit. Otherwise target MCU can be damaged!
&Note: During removing the adaptor with target MCU HC912-Programmer must
be powered off to avoid damaging of programmer and target MCU!
problem exists with running of Sector Erase and Program Commands when MCU secured.
Erase of FLASH and EEPROM command possible. In many cases this problem can be
disabling of security via Backdoor Access Key. HC912-Programmer automatically read
nd passes the security sequence. But if
e used. After erasing FLASH and EEPROM, target MCU can be accessed in Special Single
(HC912-Programmer In-Circuit interface). Follow instructions
Read full EEPROM and FLASH contents in On-Board programming interface.
First of all,
EEPROM contents and save it to File. For m
Board EEPROM/FLASH reading example. It is obligatory to s
FLASH contents to file (see Section 6.2).
Erase EEPROM and FLASH.
Press Erase FLASH and EEPROM buttons on Program Sequen
Verify EEPROM and FLASH buttons to perform erase check.
Press Start button.
When LED D1 on HC912-Programmer became pe
completed.
Disconnect power from HC912-Programmer.
Remove target MCU from programmer and
Prepare target MCU for In-Circuit Programming.
Connect required pins to board with target MCU (see Appendix
Remove any adaptor f
Apply power to HC912-Programmer. LED D1 became to green light (see Table 1).
Select corresponding device in HC912-Programmer softw
Load EEPROM/FLASH data from previous saved file.
Change value of FLASH Security byt
mean that device will be unsecured after programming. Also, som
er access to MCU is not required, FLASH Security byte not need to be changed.
EEPROM/FLASH” button on Program Sequence Panel.
Start” button.
4 on HC912-Programmer became to green light. That means that +5 voltage
or switched on and VCC applied to target MCU.
LED D1 on HC912-Programmer became permanent green, programming
ted. Target MCU powered off.
©ETL 2004-2006 MC68HC912/9S12 Programmer User’s Guide 10

6. FILE OPERATIONS
This section describes basic rules working with files. Memory dump from Hex Editor (Buffer)
can be load/save from/to hard disk. Also short descriptions such as project name, MCU type and
memory cell assignment can be done for future fast remind. HC912-Programmer accepts tree types
of file formats:
9BIN (Binary format)
9Motorola S-Record (4 byte address)
9Motorola S-Record (6 byte address)
9EEF (Extended ETL Format)
6.1 LOAD FILE INTO BUFFER
Select “File>Open” menu item.
Press “Browse” button.
In File Open Dialog window, select file witch need to be open.
Press “Open” button.
Than opposite “Auto Format Detected:” text, select correct file format. Note that software
try automatically detects file format, but unknown records in file will fail this detection.
“Load Entire file” check box must be checked if automatically loading procedures
required.
Than press “OK” button.
Sometimes load data from file to specific buffer allocations required. For Example if required
load buffer from $0400 address from binary file beginning from $0000 address follow next steps:
Select “File>Open” menu item.
Press “Browse” button.
In File Open Dialog window, select file which need to be open.
Press “Open” button.
Than, opposite “Auto Format Detected:” select Binary format.
Uncheck “Load Entire File” check box.
In field “Offset Value to Place Data to Buffer:” enter 0x0400.
Than press “OK” button.
Now data placed to Hex Editor Buffer from the beginning of 0x0400 address.
If more complicated operations with files required, for example load Hex Editor Buffer from
many files “Lowest Address From File To Load”, “Highest Address From File To Load” and
“Clear Buffer Before Loading File” options are available.
6.2 SAVE FILE FROM BUFFER
Select “File>Save” menu item.
Press “Browse” button.
Select directory in which file will be saved.
Type file name, for example “test1”
Press “Save” button.
Than select format in which file will be saved*.
Press “OK” button.
&Note: Use EEF Format for future “Load File Into Buffer” automatically
processing. Also, only in EEF Format
Project Description, Device Name and
&Note: Use Motorola S-Record (6 byte address) Format to save all FLASH
memory contents.
Memory Cells attributes can be saved.
©ETL 2004-2006 MC68HC912/9S12 Programmer User’s Guide 11

7. ERRORS AND TROUBLESHOOTING
This section describes most recently encountered problems, errors and fixing solutions.
Problem: LED D1 (see Figure 1) Dark.
Causes: This problem can accrue when external power supply connected to HC912-
Programmer is damaged or connected in wrong polarity.
Solutions: Check voltage on HC912-Programmer power clamps. It must be 12 V +/- 1V.
Problem: LED D1 (see Figure 1) Red.
Causes: These problem can appear in two cases: if HC912-Programmer is in the service
mode (JP1 removed) and if some error accrue while operation of HC912-
Programmer.
Solutions: Insert jumper JP1 (see Figure 1), remove adaptors from Motorola device socket
and cable from ICP connector, turn-off and than turn-on power supply connected
to HC912-Programmer. If LED D1 still red contact ETL technical support.
Error Message: MC68HC912 Programmer not found
Causes: This message can appear when HC912-Programmer software couldn’t
establish connection with HC912-Programmer board.
Solutions: Check connection of COM port cable from PC to HC912-Programmer
board.Apply power from external power supply to HC912-Programmer. In
menu item “Tools>Comm Port Options” select correct COM port number.
Error Message: Communication Error
Causes: This message can appear when Communication between HC912-
Programmer and PC is broken.
Solutions: Try to decrease communication baud rate in “Tools>Comm Port Options”
dialog window. Also this message can appear when COM port cable has
poor contact with DB-9 connectors.
Error Message: RESET Line must be in 'high' state
Causes: This message can appear when MCU Reset pin connected to ground through
external components or no oscillation on EXTAL, XTAL pins.
Solutions: Check MCU reset pin resistance relatively to VSS pin, and if it too low
check passive and active components connected. Or check integrity of
ceramic resonator and passive components connected to EXTAL, XTAL
pins.
Error Message: BKGD Line must be in 'high' state
Causes: This message can appear when MCU BKGD pin connected to ground
through external components.
Solutions: Cut any component from pin.
Error Message: Pin Tester Errors:
Causes: This message can appear in On-Board programming interface when some
pins has poor contact with QFP adaptor, or pins are damaged.
Solutions: Clean pins from colophony. Check contacts between adaptor and target
MCU pins. Check short circuits between pins to pins, pins to GND and pins
to VCC.
©ETL 2004-2006 MC68HC912/9S12 Programmer User’s Guide 12

Error Message: BDM Speed Auto Detection failed
Causes: This message can appear in In-Circuit programming interface if target MCU
not connected correctly to HC912-Programmer or MCU secured.
Solutions: Check contacts between HC912-Programmer and MCU pins. If this error
not disappeared, place MCU on corresponding QFP adaptor and use On-
Board programming interface.
Error Message: BDM Activation Error
Causes: This message can appear when wrong Device selected.
Solutions: Select correct device type; take attention on MCU maskset.
Error Message: No clock on ECLK pin
Causes: This message can appear in On-Board programming interface when wrong
Device selected.
Solutions: Select correct device type; take attention on MCU maskset.
Error Message: Parallel Boot Failed
Causes: This message can appear in On-Board programming interface when wrong
Device selected.
Solutions: Select correct device type; take attention on MCU maskset.
Error Message: Monitor Loader time-out Error
Causes: This message can appear when wrong Device selected.
Solutions: Select correct device type; take attention on MCU maskset.
Error Message: Monitor Check-sum Error
Causes: This message can appear after monitor firmware loaded into target MCU
with errors.
Solutions: Try to reconnect to target MCU. If this error not disappeared, possible target
MCU has damaged RAM.
Error Message: Monitor Heap Check-sum Error
Causes: This message can appear after monitor firmware transferred data into target
MCU RAM with errors.
Solutions: Try to reconnect to target MCU. If this error not disappeared, possible target
MCU has damaged RAM.
Error Message: BDM active status or monitor firmware time-out Error
Causes: This message can appear if target MCU “hangs up”.
Solutions: Try to reconnect to target MCU. If this error not disappeared, check contacts
between HC912-Programmer and MCU pins, power supply voltage on VCC
pins.
Error Message: Parallel Bus active status or monitor firmware time-out Error
Causes: This message can appear if target MCU “hangs up”.
Solutions: Try to reconnect to target MCU. If this error not disappeared, check contacts
between HC912-Programmer and MCU pins, power supply voltage on VCC
pins.
©ETL 2004-2006 MC68HC912/9S12 Programmer User’s Guide 13

Error Message: Device still locked
Causes: This message can appear in On-Board programming interface when target
MCU secured.
Solutions: Check accuracy of device type selected; take attention on MCU maskset.
Try to reconnect to target MCU.
Error Message: Device can't be unsecured
Causes: This message can appear in In-Circuit programming interface when MCU
EEPROM/FLASH erased (all data equal to $FF) and accordingly device
still secured.
Solutions: Check voltage on VCC pins. Try to reconnect to target MCU.
Error Message: Voltage on VFP pin is below normal programming voltage level
Causes: This message can appear when no or low voltage applied to VFP pin.
Solutions: Apply specified by Motorola voltage to VFP pin.
Error Message: On-Board Programming Interface not supported for the Device
Causes: This message can appear when wrong Device selected.
Solutions: Select correct device type; take attention on MCU maskset.
Error Message: External power supply must be disconnected from BDM ICP connector
Causes: This message can appear in On-Board programming interface when
external voltage applied to BDM ICP connector (see Figure 1).
Solutions: Disconnect cable from BDM ICP connector.
Error Message: Vreg Overcurrent Protection
Causes: This message can appear when current consumption from built-in power
supply grater than 500 mA.
Solutions: Check target MCU power pins on short circuit.
Error Message: Vreg Output Voltage out of range
CYPRESS IIC BUS Busy
CYPRESS IIC Protocol Failed
CYPRESS Frequency out of range
Wrong Subroutine call
Causes: These messages can appear when fatal problems with HC912-Programmer
hardware accrued.
Solutions: Contact ETL technical support.
&Note: HC912-Programmer has Log Window which can be stored to file. To
perform this operation right clicks on Log Window. Than click on “Sav
hc912prog.log file“ menu item. Now this file can be found in the same
directory as HC912-Programmer software. Log File can be se
e to
nd by E-mail to
form to applicable. Report any defects for a 45
days period, from the applicable data on invoice.
ETL warrants that Product delivered shall con
8. WARRANTY STATEMENT
©ETL 2004-2006 MC68HC912/9S12 Programmer User’s Guide 14

9. APPENDIX
HC912/9S12 MC
U
RESET
BKGD
V
SS
MODA
MODB
V
DD
Gnd
ECLK
EXTAL
XTAL
2...16 MHz
Logic level on this pin must be “LOW”
HC912 Programmer
P5
1
2
4
6
BKGD
Gnd
RESET
Logic level on this pin must be “LOW”
External circuit *
1 K
1 K
Gnd
>1 K
Note: To avoid damaging of ECLK pin
it must be connected to external circuit
via resistor equal or grater than 1 Kohm.
V
DD
Figure 2. In-Circuit programming schematic diagram for HC912/9S12 MCU
©ETL 2004-2006 MC68HC912/9S12 Programmer User’s Guide 15

1
2
3
4
5
6
7
8
9
10
11
12
13
14
15
16
17
18
19
20
80
79
78
77
76
75
74
73
72
71
70
69
68
67
66
65
64
63
62
61
21
22
23
24
25
26
27
28
29
30
31
32
33
34
35
36
37
38
39
40
MC68HC912B32
80 QFP
60
59
58
57
56
55
54
53
52
51
50
49
48
47
46
45
44
43
42
41
BKGD
RESET
GND
VDD
PP5
PP4
PW3 / PP3
PW2 / PP2
PW1/ PP1
PA2 / DATA10 /ADDR10
PA3 / DATA11 / ADDR11
PA4 / DATA12 /ADDR12
PA5 / DATA13 /ADDR13
PA6 / DATA14 /ADDR14
PA7 / DATA15 /ADDR15
PP6
PP7
ADDR0 / DATA0 / PB0
ADDR1 / DATA1 / PB1
ADDR2 / DATA2 / PB2
SMODN / TAGHI/ BKGD
PAI / IOC7 / PT7
IOC6 / PT6
IOC5 / PT5
IOC4 / PT4
IOC3 / PT3
IOC2 / PT2
IOC1 / PT1
IOC0 / PT0
ADDR9 / DATA9 / PA1
XIRQ
/ PE0
IRQ/ PE1
R/W
/ PE2
LSTRB/ TAGLO / PE3
XTAL
EXTAL
RESET
V
DDX
V
SSX
ECLK / PE4
MODA/ IPIPE0 / PE5
MODB / IPIPE1 / PE6
DBE/ PE7
ADDR7 / DATA7 / PB7
ADDR6 / DATA6 / PB6
ADDR5 / DATA5 / PB5
ADDR4 / DATA4 / PB4
ADDR3 / DATA3 / PB3
V
DD
V
SS
PW0/ PP0
V
SSA
V
DDA
PAD7 / AN7
PAD6 / AN6
PAD5 / AN5
PAD4 / AN4
PAD3 / AN3
PAD2 / AN2
PAD1 / AN1
PAD0 / AN0
V
RL
V
RH
V
SS
V
DD
PS0/ RxD
PS1 / TxD
PS2
PS3
PS4 / SDI/MISO
PS5 / SDO/MOSI
PS6 /SCK
PS7 / CS/SS
V
FP
PDLC6
PDLC5
PDLC4
PDLC3
PDLC2
PDLC1 /DLCTx
PDLC0 /DLCRx
V
SSX
V
DDX
ADDR8 / DATA8 / PA0
Figure 3. In-Circuit wiring diagram for MC68HC912B32, 80-PIN QFP Package
©ETL 2004-2006 MC68HC912/9S12 Programmer User’s Guide 16

1
2
3
4
5
6
7
8
9
10
11
12
13
14
15
16
17
18
19
20
21
22
23
24
25
26
27
28
112
111
110
109
108
107
106
105
104
103
102
101
100
99
98
97
96
95
94
93
92
91
90
89
88
87
86
85
29
30
31
32
33
34
35
36
37
38
39
40
41
42
43
44
45
46
47
48
49
50
51
52
53
54
55
56
MC68HC912 D60/DG128
112TQFP
PAD17/AN17
PAD07/AN07
PAD16/AN16
PAD06/AN06
PAD15/AN15
PAD05/AN05
PAD14/AN14
PAD04/AN04
PAD13/AN13
PAD03/AN03
PAD12/AN12
PAD02/AN02
PAD11/AN11
PAD01/AN01
PAD10/AN10
PAD00/AN00
V
RL0
V
RH0
V
SS
V
DD
PA7/ADDR15/DATA15/DATA
7
PA6/ADDR14/DATA14/DATA
6
PA5/ADDR13/DATA13/DATA
5
PA4/ADDR12/DATA12/DATA
4
PA3/ADDR11/DATA11/DATA3
PA2/ADDR10/DATA10/DATA
2
PA1/ADDR9/DATA9/DATA1
PA0/ADDR8/DATA8/DATA0
PP3/PW3
PK0/PIX0
PK1/PIX1
PK2/PIX2
PK7/ECS
V
DDX
V
SSX
RxCAN0
TxCAN0
RxCAN1
TxCAN1
PIB4
PIB5
PIB6/SDA
PIB7/SCL
V
FP
*
PS7/SS
PS6/SCK
PS5/SDO/MOSI
PS4/SDI/MISO
PS3/TxD1
PS2/RxD1
PS1/TxD0
PS0/RxD0
V
SSA
V
RL1
V
RH1
V
DDA
PW2/PP2
PW1/PP1
PW0/PP0
IOC0/PT0
IOC1/PT1
IOC2/PT2
IOC3/PT3
KWJ7/PJ7
KWJ6/PJ6
KWJ5/PJ5
KWJ4/PJ4
V
DD
PK3
V
SS
IOC4/PT4
IOC5/PT5
IOC6/PT6
IOC7/PT7
KWJ3/PJ3
KWJ2/PJ2
KWJ1/PJ1
KWJ0/PJ0
SMODN/TAGHI/BKGD
ADDR0/DATA0/PB0
ADDR1/DATA1/PB1
ADDR2/DATA2/PB2
ADDR3/DATA3/PB3
ADDR4/DATA4/PB4
ADDR5/DATA5/PB5
ADDR6/DATA6/PB6
ADDR7/DATA7/PB7
KWH7/PH7
KWH6/PH6
KWH5/PH5
KWH4/PH4
DBE/CAL/PE7
MODB/IPIPE1/PE6
MODA/IPIPE0/PE5
ECLK/PE4
V
SSX
VSTBY
V
DDX
V
DDPLL
XFC
V
SSPLL
RESET
EXTAL
XTAL
KWH3/PH3
KWH2/PH2
KWH1/PH1
KWH0/PH0
LSTRB/TAGLO/PE3
R/W/PE2
IRQ/PE1
XIRQ/PE0
84
83
82
81
80
79
78
77
76
75
74
73
72
71
70
69
68
67
66
65
64
63
62
61
60
59
58
57
RESET
GND
VDD
BKGD
External +12V for FLASH Programming
Figure 4. In-Circuit wiring diagram for MC68HC912D60/DG128, 112-PIN TQFP Package
©ETL 2004-2006 MC68HC912/9S12 Programmer User’s Guide 17

1
2
3
4
5
6
7
8
9
10
11
12
13
14
15
16
17
18
19
20
21
22
23
24
25
26
27
28
112
111
110
109
108
107
106
105
104
103
102
101
100
99
98
97
96
95
94
93
92
91
90
89
88
87
86
85
29
30
31
32
33
34
35
36
37
38
39
40
41
42
43
44
45
46
47
48
49
50
51
52
53
54
55
56
MC68HC912 D60A/DG128A
112 LQFP
84
83
82
81
80
79
78
77
76
75
74
73
72
71
70
69
68
67
66
65
64
63
62
61
60
59
58
57
PAD17/AN17
PAD07/AN07
PAD16/AN16
PAD06/AN06
PAD15/AN15
PAD05/AN05
PAD14/AN14
PAD04/AN04
PAD13/AN13
PAD03/AN03
PAD12/AN12
PAD02/AN02
PAD11/AN11
PAD01/AN01
PAD10/AN10
PAD00/AN00
VRL0
VRH0
VSS
VDD
PA7/ADDR15/DATA15/DATA7
PA6/ADDR14/DATA14/DATA6
PA5/ADDR13/DATA13/DATA5
PA4/ADDR12/DATA12/DATA4
PA3/ADDR11/DATA11/DATA3
PA2/ADDR10/DATA10/DATA2
PA1/ADDR9/DATA9/DATA1
PA0/ADDR8/DATA8/DATA0
PP3/PW3
PK0/PIX0
PK1/PIX1
PK2/PIX2
PK7/ECS
VDDX
VSSX
RxCAN0
TxCAN0
RxCAN1
TxCAN1
PIB4
PIB5
PIB6/SDA
PIB7/SCL
TEST
PS7/SS
PS6/SCK
PS5/SDO/MOSI
PS4/SDI/MISO
PS3/TxD1
PS2/RxD1
PS1/TxD0
PS0/RxD0
VSSA
VRL1
VRH1
VDDA
PW2/PP2
PW1/PP1
PW0/PP0
IOC0/PT0
IOC1/PT1
IOC2/PT2
IOC3/PT3
KWJ7/PJ7
KWJ6/PJ6
KWJ5/PJ5
KWJ4/PJ4
VDD
PK3
VSS
IOC4/PT4
IOC5/PT5
IOC6/PT6
IOC7/PT7
KWJ3/PJ3
KWJ2/PJ2
KWJ1/PJ1
KWJ0/PJ0
SMODN/TAGHI/ BKGD
ADDR0/DATA0/PB0
ADDR1/DATA1/PB1
ADDR2/DATA2/PB2
ADDR3/DATA3/PB3
ADDR4/DATA4/PB4
ADDR5/DATA5/PB5
ADDR6/DATA6/PB6
ADDR7/DATA7/PB7
KWH7/PH7
KWH6/PH6
KWH5/PH5
KWH4/PH4
ECLK/DBE/CAL/PE7
CGMTST/MODB/IPIPE1/PE6
MODA/IPIPE0/PE5
ECLK/PE4
VSSX
VSTBY
VDDX
VDDPLL
XFC
VSSPLL
RESET
EXTAL
XTAL
KWH3/PH3
KWH2/PH2
KWH1/PH1
KWH0/PH0
LSTRB/TAGLO/PE3
R/W /PE2
IRQ /PE1
XIRQ/PE0
RESET
GND
VDD
BKGD
Figure 5. In-Circuit wiring diagram for MC68HC912D60A/DG128A, 112-PIN LQFP Package
©ETL 2004-2006 MC68HC912/9S12 Programmer User’s Guide 18

60
59
57
56
55
54
53
52
51
50
49
48
47
46
45
58
1
2
4
5
6
7
8
9
10
11
12
13
14
15
16
3
44
43
42
41
18
20
19
17
80
79
77
76
75
74
73
72
71
70
69
68
67
66
65
78
64
63
62
61
21
22
24
25
26
27
28
29
30
31
32
33
34
35
36
23
38
40
39
37
MC68HC(9)12D60
80 QFP
PP3/PW3
PP4
PP5
PP6
PP7
VDDX
VSSX
PCAN0/RxCAN
PCAN1/TxCAN
PS7/SS
PS6/SCK
PS5/SDO/MOSI
PS4/SDI/MISO
PS3/TxD1
PS2/RxD1
PS1/TxD0
PS0/RxD0
VSSAD
VDDAD
PAD07/AN07
PAD06/AN06
PAD05/AN05
PAD04/AN04
PAD03/AN03
PAD02/AN02
PAD01/AN01
PAD00/AN00
VRL0
VRH0
VSS
VDD
PA7/ADDR15/DATA15/DATA7
PA6/ADDR14/DATA14/DATA6
PA5/ADDR13/DATA13/DATA5
PA4/ADDR12/DATA12/DATA4
PA3/ADDR11/DATA11/DATA3
PA2/ADDR10/DATA10/DATA2
PA1/ADDR9/DATA9/DATA1
PA0/ADDR8/DATA8/DATA0
ADDR5/DATA5/PB5
ADDR6/DATA6/PB6
ADDR7/DATA7/PB7
KWH4/PH4
ECLK/DBE/CAL/PE7
CGMTST/MODB/IPIPE1/PE6
MODA/IPIPE0/PE5
ECLK/PE4
VSSX
VDDX
VDDPLL
XFC
VSSPLL
RESET
EXTAL
XTAL
LSTRB/TAGLO/PE3
R/W/PE2
IRQ/PE1
XIRQ/PE0
PW2/PP2
PW1/PP1
PW0/PP0
IOC0/PT0
IOC1/PT1
IOC2/PT2
IOC3/PT3
KWG4/PG4
VDD
VSS
IOC4/PT4
IOC5/PT5
IOC6/PT6
IOC7/PT7
SMODN/TAGHI/BKGD
ADDR0/DATA0/PB0
ADDR1/DATA1/PB1
ADDR2/DATA2/PB2
ADDR3/DATA3/PB3
ADDR4/DATA4/PB4
RESET
GND
VDD
BKGD
V
FP
*
External +12V for FLASH Programmin
g
Figure 6. In-Circuit wiring diagram for MC68HC(9)12D60, 80-PIN QFP Package
©ETL 2004-2006 MC68HC912/9S12 Programmer User’s Guide 19

60
59
57
56
55
54
53
52
51
50
49
48
47
46
45
58
1
2
4
5
6
7
8
9
10
11
12
13
14
15
16
3
44
43
42
41
18
20
19
17
80
79
77
76
75
74
73
72
71
70
69
68
67
66
65
78
64
63
62
61
21
22
24
25
26
27
28
29
30
31
32
33
34
35
36
23
38
40
39
37
MC68HC912D60A
80 QFP
PP3/PW3
PP4
PP5
PP6
PP7
V
DDX
V
SSX
PCAN0/RxCAN
PCAN1/TxCAN
TEST
PS7/SS
PS6/SCK
PS5/SDO/MOSI
PS4/SDI/MISO
PS3/TxD1
PS2/RxD1
PS1/TxD0
PS0/RxD0
V
SSAD
V
DDAD
PAD07/AN07
PAD06/AN06
PAD05/AN05
PAD04/AN04
PAD03/AN03
PAD02/AN02
PAD01/AN01
PAD00/AN00
V
RL0
V
RH0
V
SS
V
DD
PA7/ADDR15/DATA15/DATA7
PA6/ADDR14/DATA14/DATA6
PA5/ADDR13/DATA13/DATA5
PA4/ADDR12/DATA12/DATA4
PA3/ADDR11/DATA11/DATA3
PA2/ADDR10/DATA10/DATA2
PA1/ADDR9/DATA9/DATA1
PA0/ADDR8/DATA8/DATA0
ADDR5/DATA5/PB5
ADDR6/DATA6/PB6
ADDR7/DATA7/PB7
KWH4/PH4
ECLK/DBE/CAL/PE7
CGMTST/MODB/IPIPE1/PE6
MODA/IPIPE0/PE5
ECLK/PE4
V
SSX
V
DDX
V
DDPLL
XFC
V
SSPLL
RESET
EXTAL
XTAL
LSTRB/TAGLO/PE3
R/W/PE2
IRQ/PE1
XIRQ/PE0
PW2/PP2
PW1/PP1
PW0/PP0
IOC0/PT0
IOC1/PT1
IOC2/PT2
IOC3/PT3
KWG4/PG4
V
DD
V
SS
IOC4/PT4
IOC5/PT5
IOC6/PT6
IOC7/PT7
SMODN/TAGHI/BKGD
ADDR0/DATA0/PB0
ADDR1/DATA1/PB1
ADDR2/DATA2/PB2
ADDR3/DATA3/PB3
ADDR4/DATA4/PB4
RESET
GND
VDD
BKGD
Figure 7. In-Circuit wiring diagram for MC68HC912D60A, 80-PIN QFP Package
©ETL 2004-2006 MC68HC912/9S12 Programmer User’s Guide 20
This manual suits for next models
1
Table of contents
Other ETL Network Hardware manuals
Popular Network Hardware manuals by other brands

ProfiTap
ProfiTap PROFISHARK 1G+ Installation and configuration manual
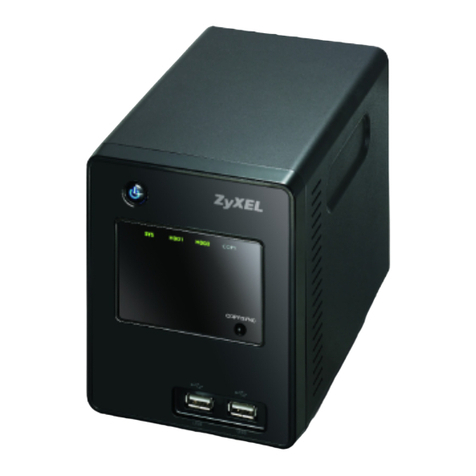
ZyXEL Communications
ZyXEL Communications Network Storage Appliance NSA-220 user guide

ELTEX
ELTEX Terrabox TCB030 operating instructions
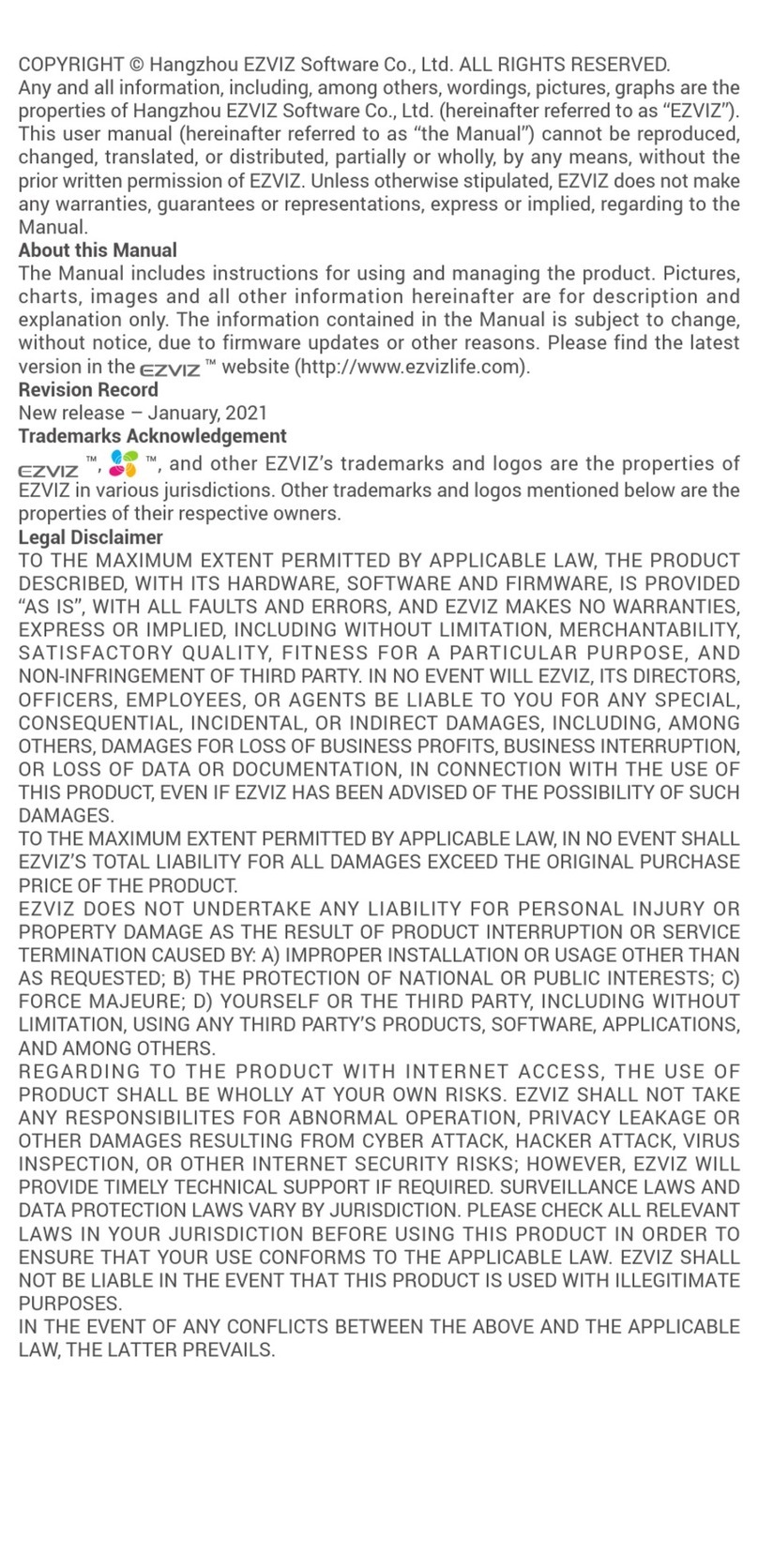
Ezviz
Ezviz CST3C manual
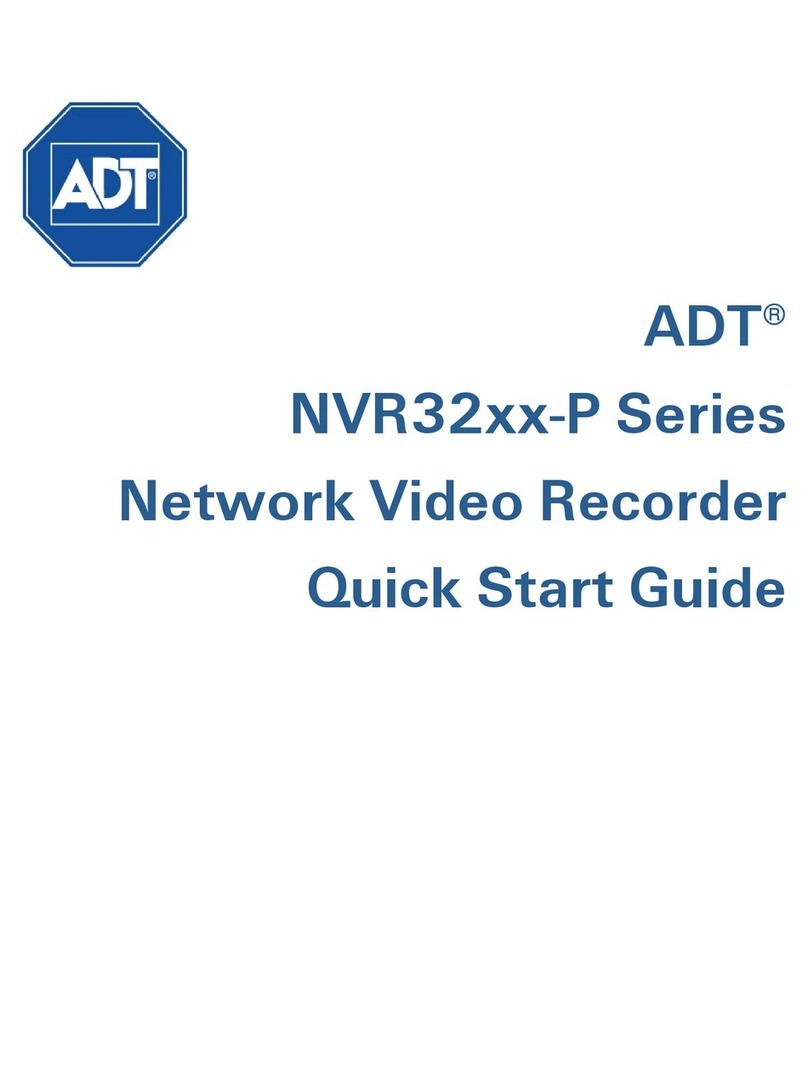
ADT
ADT NVR32xx-P Series quick start guide
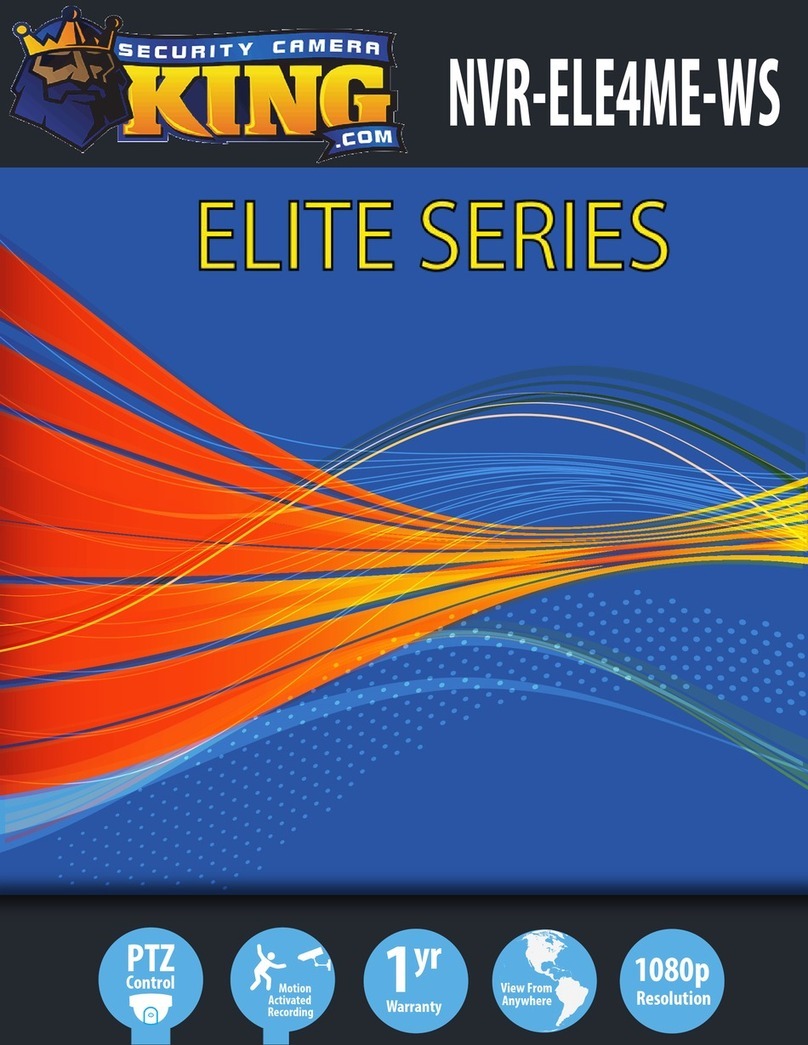
Security Camera King
Security Camera King NVR-ELE4ME-WS user manual
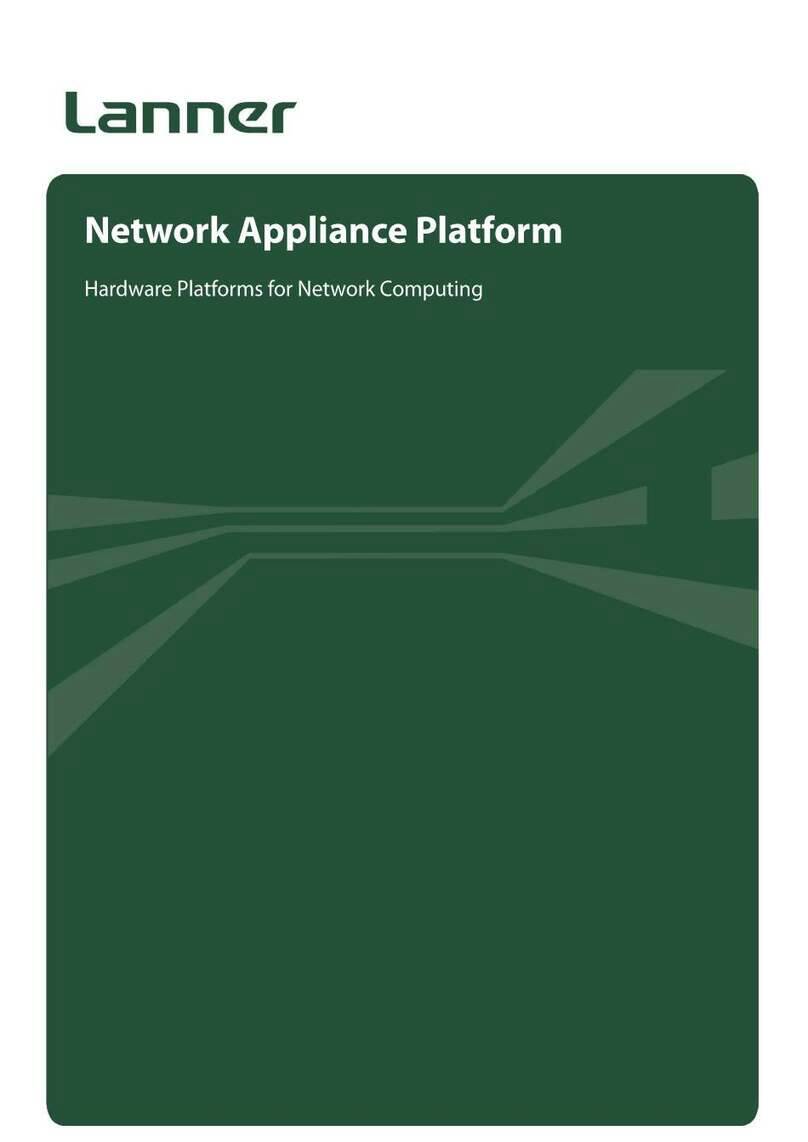
Lanner
Lanner NCA-4210 user manual

ATTO Technology
ATTO Technology iPBridge 2500C Specifications
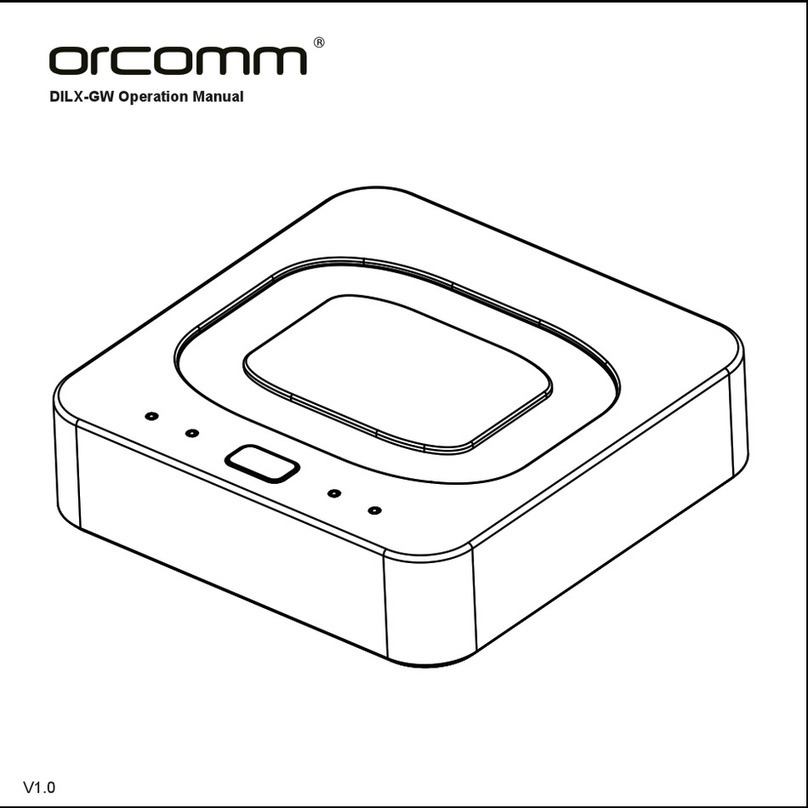
Orcomm
Orcomm DILX-GW Operation manual
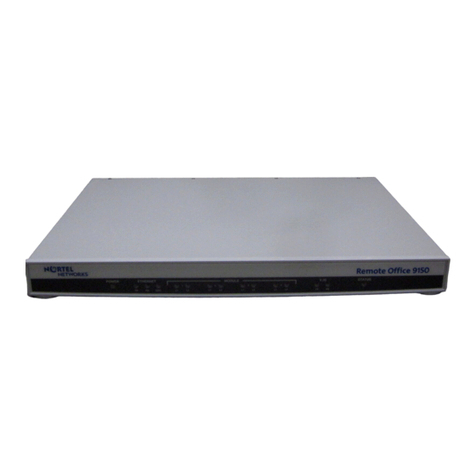
Nortel
Nortel Remote Office 9150 Installation and administration guide
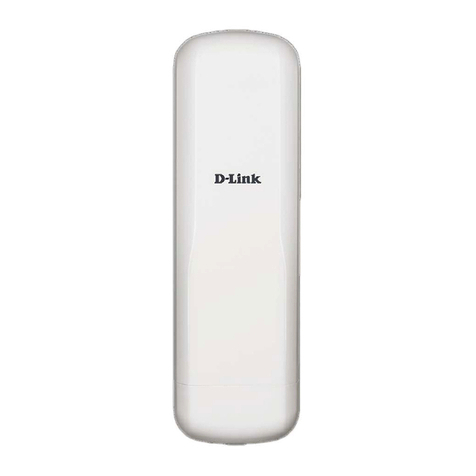
D-Link
D-Link DAP-3711 Quick installation guide
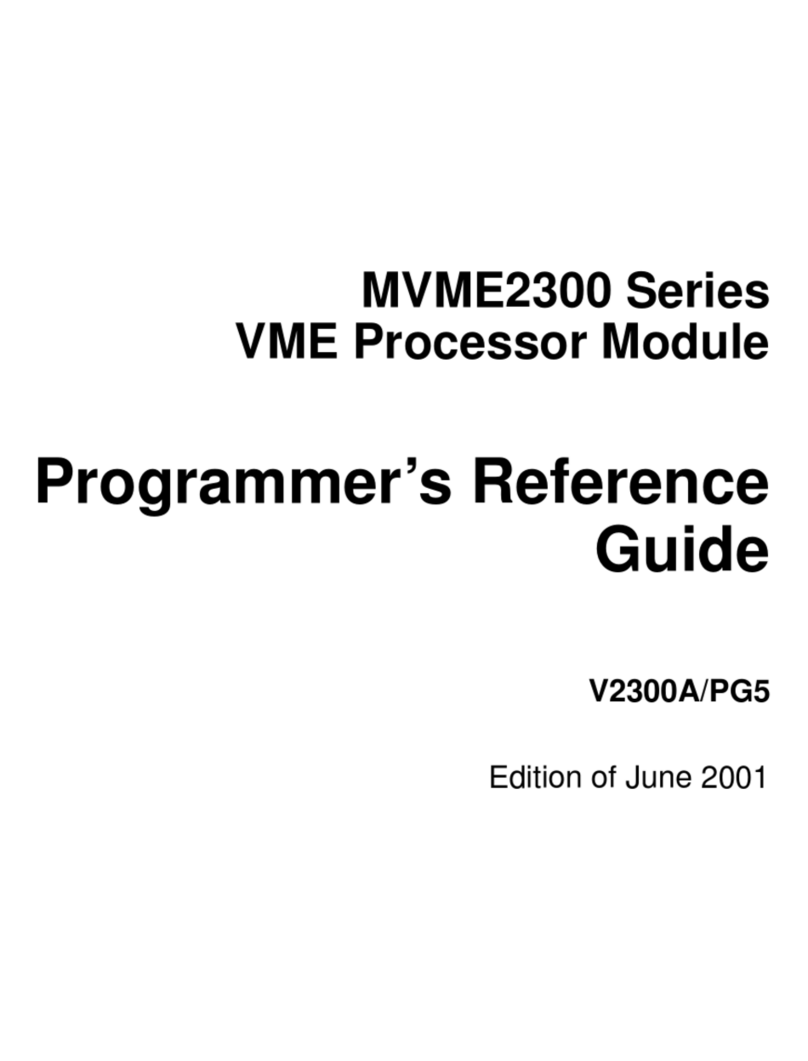
Motorola
Motorola MVME2300 Series Programmer's reference