ETNA Hydrokon User manual

Hydrokon
Pump & Booster Frequency Control Unit
User Manuel

2
Dear Customer,
Thanks for selecting our product. To use this product correctly, make sure that you
read this manual carefully and keep the manual safe together with the warranty card.
Warning - Specifications 03
Driver Terminal Connection 05
Control Connections 08
Setting Parameters 09
Troubleshooting Table 21
Building Automation System 22
Error Codes - Triphase Inverter 23
CONTENS

3www.etna.com.tr
Warnings
• Cut o the power supply before assembling the device.
NOTE: Standard power loss (Watt) = 3% of device power
∆T = Temperature dierence in the cabin (°C)
3.1 = Specific heat of air at sea level
Min. Operating Temperature = 0°C
Max. Operating Temperature = 50°C
• Wait for 5 minutes before opening the cover after the power is cut postoperation
(for the discharging of DC capacitors).
Attention!
If the device is not connected in line with the specified rules, there is always the risk of
mild and severe injury, death and material damage. Thus, all settings should be done by
expert personnel paying ultimate attention to the security warnings and precautions.
Warranty Conditions
• Do not drop the device, expose it to frequent shock.
• Operate the device in a non-vibrating environment.
• Do not assemble the device near an electromagnetic radiation source.
• Ensure the cable connections of the device are correct and complete.
• Prevent any arc on the connection cables.
• Ensure the grid frequency is 47Hz-63Hz.
• Take additional precautions against stroke of lightning on the grid.
• Prevent instantaneous voltage fluctuations on the grid.
• Keep the grid voltage in the given range.
Note: The device will be out of warranty in any failure that will arise due to the reasons
mentioned above.
Specifications
• Easy programming
• 120% loading for 60 seconds
• Operating temperature range between 0°C and 50°C
• Ability to set the output frequency (motor speed) using
/ buttons
• Output frequency can be set by 2 digital inputs
• Programmable start and stop ramps
• High and low voltage protection
• Short circuit protection on motor terminals
WARNING - SPECIFICATIONS

4
Protections
Low Voltage Protection: Low voltage fault appears on screen in case supply voltage is
lower than %20 of nominal value
High Voltage Protection: High voltage fault appears on screen in case supply voltage is
higher than %20 of nominal value
Overheating Protection: Overheating fault appears on screen in case the body temperature
of device is higher than 80 °C
Phase Protection: Phase fault appears in case there is a missing phase on three phase
version of device
Short circuit protection: Motor short circuit fault appears in case there is a short circuit
on motor connections.
Electrical Assembly
• Cable thickness and fuse capacities should be selected according to the device input
and output current values.
• Power supply line cables and cables that control inductive load such as relay windings
must be aparted from each other and located vertically not horizontally. Control cables
must be used isolated type.
• Earth connection of device should not be short-circuited with neutral line.
Mains Supply - Device Connection
• Ensure the power supply voltage and current are compatible with the device, and
there are compatible circuit breakers between the mains and the device.
• Cut o the power on the mains before connecting the device.
• Connect the device by tightening the connectors well without leaving any naked cable
or causing short circuits.
Caution! Never use the same cable conduit.
WARNING - SPECIFICATIONS

5www.etna.com.tr
DRIVER TERMINAL CONNECTIONS
Driver – Motor Connection
• Driver and motor current values must be checked if they are compatible
• Any kind of fuse must not be located between driver and motor.
• Motor driver connections must be four wired and shielded and connected to U,V,W
terminals of motor. In addition to this shield of cable must be connected to earth
terminal of motor and driver. Total cable length can not exceed 25 m.
NOTE : Please refer to the technical specifications section of user manual for cable
thickness.
Control Cables Connection
Shielded cable mut be used as control cables and shiled part must be grounded. (Please
do not connect to neutral)
ATTENTION: Control cables, power supply and motor cables must be separated. CAN
NOT BE LOCATED in the same cable channel.
Frequency Inverter Assembly
1Take out the inverter from the box.
2Check whether there is a physical damage.
3Locate the inverter as aluminium side up and balanced on the motor fan cover.
4Take out the assembly clamps of the inverter.
5Disassemble the upper cover by unbolting the 4 bolts located on the corner of the
cover.
6Locate M5 x 50 mm sized screws on the inverter aluminium body.
7Fix assembly clamps by screwing M5 x 50 mm screws.
8Fix assembly clamps to motor fan cover.
9Fix the inverter to the by screwing the assembly clamp screws. (M5 x 50 mm fixing
screw heads must be inside of the screw slots otherwise upper cover and gasket can
not be located properly and the parts can not be sealed.
10 Disassemble the sealing component inside the cable glands and locate cables inside
the glands.
11 Connect Transmitter, Floater and RS485 cables to spring terminals.
12 Connect motor cables including earth connection.
13 Connect power supply cables including earth connection.
14 Set MASTER-SLAVE operation micro-switches after whole cables are connected.
15 Assemble upper cover to aluminium bosy properly.
16 DO NOT switch on the power until upper cover located properly.
17 Make sure that upper cover is located properly.
18 Switch on the power supply .
19 Set the parameters according to the working condition.
20 The device will be on operation mode after leaving the set parameter mode.

6
DRIVER TERMINAL CONNECTIONS
MOTOR
CONNECTION
DIGITAL
CONNECTIONS
POWER
INPUT
MASTER - SLAVE
SELECTION SWITCH
T
W
V
U
S
R
12) BMS Connection (-)
11) BMS Connection (+)
2) Internal Communication (-)
3) Floater
4) Floater
5) Transmitter 1 (-)
9) Transmitter 2 (-)
6) Transmitter 1 (+)
10) Transmitter 2 (+)
7) Contact Switch
8) Contact Switch
1) Internal Communication (+)

7www.etna.com.tr
220 V AC (MONOPHASE) POWER-SUPPLIED
INVERTER CONNECTION CHART
V
U
MOTOR
CONNECTION
GROUNDING
INPUT
220 V
0 (NEUTRAL)
W

8
CONTROL CONNECTIONS
Connector No. 1 : RS485 communication (+) terminal
Connector No. 2 : RS485 communication (-) terminal
Connector No. 3 : 1. External contact tip (0v) GND.
Connector No. 4 : 1. External contact tip.
Connector No. 5 : 1. Pressure sensor (4-20 mA) (-)
Connector No. 6 : 1. Pressure sensor (4-20 mA) (+)
Connector No. 7 : 2. External contact tip (0v) GND.
Connector No. 8 : 2. External contact tip.
Connector No. 9 : 2. Pressure sensor (4-20 mA) (-)
Connector No. 10 : 2. Pressure sensor (4-20 mA) (+)
Connector No. 11 : BMS Communication (RS485) (+)
Connector No. 12 : BMS Communication (RS485) (-)
Connect External Contact 1 and floater, if any. Otherwise bridge the contact switch.
1. Connect the pressure sensor's (4-20 mA) (+) and (-) terminals correctly.
Master - Slave Selection Switch Positions
Master Slave 1 Slave 2 Slave 3
1 5 93 7 112 6 104 8 12

9www.etna.com.tr
SETTING PARAMETERS
Sample Parameter Setting
Setting Booster Parameters
NOTE: These settings are for the Master device.
Enter the motor current to the parameter P0007. Enter the operating pressure to the
parameter P0009 (Ex. 4.0 bar). Enter the maximum pressure of the pump to the parameter
P0015. Or set parameter P0018 and exit the program. (Note: After turning o the valve
in the delivery part (given that there are no expansion tanks between the valve and the
pump), set the autoset parameter.)
The device calculates this pressure automatically. There is no need to set the parameter
for Slave devices. It would be enough to correctly position the micro switches.
NOTE: Position the switches while there is no power in the device. The device will set itself
according to this position after connecting power.
Setting Circulating Pump Parameters
Enter the dierential pressure value of the system to the parameter P0009
(∆P, ex. 1bar). Enter the maximum pressure of the pump to the parameter
1. STEP
Press Pbutton and PASSWORD screen will be displayed.
2. STEP
Move indicator to the right using right arrow button (
).

10
3. STEP
Enter correct password by using up (
) and down ( ) buttons. Approve password
by using Left arrow button (
). You can proceed to parameter settings if password is
correct .
If the password is not correct, wrong password will be displayed on screen. Repeat the
steps from the beginning of step 2 until enter the correct password
4. STEP
P 1 Display Select ............................. 0 – 3 Display selection:
[ 0 ] 0 = Output Frequency ( Hz )
1 = Motor current ( A )
2 = DC bar voltage ( V Dc )
3 = Device temperature ( °C )
Press P button and enter correct password. Afterwards change P0000_ value to P0001_
by pressing up and down buttons. Move the cursor to right by pressing Right button. You
can set the parameter while device is in operating mode by using up and down buttons
and set by pressing left button. After completing parameter set, you can leave parameter
set mode by pressing Pbutton.
P 2 Ramp Up Time ........................... 0–10,0
( Seconds ) [2,0]
This duration shows the time from total stop to maximum frequency set by parameter 6.
SETTING PARAMETERS
f(Hz)
Ramp Up Time t (sn)

11 www.etna.com.tr
Press P button and enter the correct password. Change P0000_ value to P0002_ by
using Up and Down buttons. Move the cursor to right by using right button and increase or
decrease the parameter value by using Up and Down buttons, set the parameter by using
left button and leave parameter set mode by pressing Pbutton
P 3 Ramp Down Time ..................... 0–10,0
[2,0]
This time represents the duration from maximum frequency set by parameter 6 to total
stop.
Press P button and enter the correct password. Change P0000_ value to P0003_ by
using Up and Down buttons. Move the cursor to right by using right button and increase
or decrease the parameter value by using Up and Down buttons, set the parameter by
using left button and leave parameter set mode by pressing Pbutton.
SETTING PARAMETERS
f(Hz)
Ramp Down Time t (sn)
Press P button and enter the correct password. Change P0000_ value to P0004_ by
using Up and Down buttons. Move the cursor to right by using right button and increase
or decrease the parameter value by using Up and Down buttons, set the parameter by
using left button and leave parameter set mode by pressing Pbutton.
P 4 Manual Operation ………................. 15,0 – 50,0
Start frequency (Hz) [15,0]
Manual Operation start frequency value

12
P 5 Operation Mode …..................... 0 – 1
0 = Manual operation
1 = Automatic operation
Press P button and enter the correct password. Change P0000_ value to P0005_ by using
Up and Down buttons. Move the cursor to right by using right button and set operation
mode Manual / Automatic by using up and down buttons. set the parameter by using left
button and leave parameter set mode by pressing P button.
P6 Motor frequency (Hz) .................. 50.0 – 60.0
[50.0]
Enter the frequency value written on the motor label (Hz)
P 7 Motor Current …............................ 0 – 8
When the inverter works with a smaller capacity motor, this parameter should be set to
motor label value.On other conditions, not necessary.
Press P button and enter the correct password. Change P0000_ value to P0006_ by
using Up and Down buttons. Move the cursor to right by using right button and increase
or decrease frequency value to the same value written on motor label by using Up and
Down buttons, set the parameter by using left button and leave parameter set mode by
pressing P button.
Press P button and enter the correct password. Change P0000_ value to P0007_ by
using Up and Down buttons. Move the cursor to right by using right button and increase
or decrease current value to the same value written on motor label by using Up and Down
buttons , set the parameter by using left button and leave parameter set mode by pressing
P button.
SETTING PARAMETERS

13 www.etna.com.tr
P 8 Transmitter Pressure .................. 0,1 – 100,0
(Bar) [16,0]
Transmiitter in the system pressure value (bar)
P 9 Operating Pressure .................... 0,1 – 100,0
(Bar) [3,0]
Press P button and enter the correct password. Change P0000_ value to P0008_ by
using Up and Down buttons. Move the cursor to right by using right button and adjust the
maximum transmitter value same as the transmitter available on the system by using Up
and Down buttons set the parameter by using left button and leave parameter set mode
by pressing P button.
P 10 Di. Pressure ……………............. 0,1 – 3,0
(Bar) [0,5]
Hysteresis value of set pressure for operation and stop
System operating pressure value (bar) in Automatic Mode, Dierential pressure (∆p) in
Circulation Systems. Press P button and enter the correct password. Change P0000_
value to P0009_ by using Up and Down buttons. Move the cursor to right by using right
button and adjust the operating pressure value by using Up and Down buttons set the
parameter by using left button and leave parameter set mode by pressing Pbutton.
Press P button and enter the correct password. Change P0000_ value to P0010_ by
using Up and Down buttons. Move the cursor to right by using right button and adjust the
hysteresis value by using Up and Down buttons set the parameter by using left button and
leave parameter set mode by pressing Pbutton.
SETTING PARAMETERS

14
P 11 Stop Delay ................................. 0,1 - 30,0
Sec) [30,0]
Time delay to stop when the system reaches set pressure
Press P button and enter the correct password. Change P0000_ value to P0011_ by using
Up and Down buttons. Move the cursor to right by using right button and adjust the stop
delay value by using Up and Down buttons set the parameter by using left button and
leave parameter set mode by pressing Pbutton.
P 12 Minimum motor ........................ 0 – 60,0
frequency (Hz) [15,0]
Indicates minimum motor frequency value (Hz).
P 13 Maximum motor .......................... 0 – 60,0
frequency (Hz) [50,0]
Indicates maximum frequency output of the inverter (Hz)
Press P button and enter the correct password. Change P0000_ value to P0012_ by using
Up and Down buttons. Move the cursor to right by using right button and adjust the motor
minimum frequency value by using Up and Down buttons set the parameter by using left
button and leave parameter set mode by pressing Pbutton. (This frequency is calculated
automatically in automatic operation mode.)
Press P button and enter the correct password. Change P0000_ value to P0013_ by using
Up and Down buttons. Move the cursor to right by using right button and adjust maximum
frequency value by using Up and Down buttons set the parameter by using left button and
leave parameter set mode by pressing Pbutton.
SETTING PARAMETERS

15 www.etna.com.tr
P 14 Factory Settings …………........…… 0 – 1
P 15 Automatic Pump Pressure …....... 0 – 1
Maximum pump pressure is entered manually or inverter calculates this value in automatic
mode by itself and saves.
Press P button and enter the correct password. Change P0000_ value to P0014_ by
using Up and Down buttons. Move the cursor to right by using right button and adjust the
parameter by using Up and Down buttons (Y). Set the parameter by using left button and
leave parameter set mode by pressing Pbutton.
P 16 Operation according to motor. 1 – 2
[2]
1) Normal operation
2) Pump operation
Press P button and enter the correct password. Change P0000_ value to P0015_ by
using Up and Down buttons. Move the cursor to right by using right button and adjust
maximum pump pressure value by using Up and Down buttons set the parameter by using
left button and leave parameter set mode by pressing Pbutton or you can activate P0018
parameter and inverter calculates this parameter automatically.
Press P button and enter the correct password. Change P0000_ value to P0016_ by
using Up and Down buttons. Move the cursor to right by using right button and adjust the
parameter by using Up and Down buttons (Pump). Set the parameter by using left button
and leave parameter set mode by pressing Pbutton.
SETTING PARAMETERS

16
P 17 Language Selection ……………….. 0 – 1
[0]
1)Turkish
2)English
Press P button and enter the correct password. Change P0000_ value to P0017_ by
using Up and Down buttons. Move the cursor to right by using right button and adjust the
language setting by using Up and Down buttons. Set the parameter by using left button
and leave parameter set mode by pressing P button.
P 18 Automatic test ............................. 0 – 1
[0]
Inverter runs motor and saves parameters automatically when this parameter is set to 1.
P 19 Slave inverter ...…………...........…. 0 – 60,0
Start delay time (Sec) [ 5,0 ]
Start delay time for slave pumps on multiple inverter applications.
Press P button and enter the correct password. Change P0000_ value to P0018_ by
using Up and Down buttons. Move the cursor to right by using right button and adjust
parameter to 1 Set the parameter by using left button and leave parameter set mode by
pressing Pbutton. Inverter runs motor and sets pump parameters automatically.
Attention: Please set this parameter after closing the valve on discharge line (Expansion
tank must not be available between valve and pump).
Press P button and enter the correct password. Change P0000_ value to P0019_ by
using Up and Down buttons. Move the cursor to right by using right button and adjust
parameter by using Up and Down buttons Set the parameter by using left button and
leave parameter set mode by pressing Pbutton.
SETTING PARAMETERS

17 www.etna.com.tr
Press P button and enter the correct password. Change P0000_ value to P0020_ by
using Up and Down buttons. Move the cursor to right by using right button and adjust
parameter by using Up and Down buttons Set the parameter by using left button and
leave parameter set mode by pressing Pbutton.
P 20 Slave inverter ...…………...........…. 0 – 60,0
Stop delay time (Sec) [ 5,0 ]
Stop delay time for slave pumps on multiple inverter applications.
P 21 Min frequency hysteresis .........…... 0-10,0
Frequency [1,0]
Inverter minimum frequency value when the system reaches set pressure. Min frequency +
Hysteresis
P 22 Pump Type ..........………………….... 1 - 2
[2]
1) Booster
2) Circulation
Press P button and enter the correct password. Change P0000_ value to P0021_ by using
Up and Down buttons. Move the cursor to right by using right button and adjust hysteresis
parameter by using Up and Down buttons Set the parameter by using left button and
leave parameter set mode by pressing Pbutton.
Press P button and enter the correct password. Change P0000_ value to P0022_ by
using Up and Down buttons. Move the cursor to right by using right button and adjust
pump type parameter by using Up and Down buttons Set the parameter by using left
button and leave parameter set mode by pressing Pbutton.
SETTING PARAMETERS

18
P 23 BMS Communication Address ..... 1 - 255
[1]
Master inverter address is set by this parameter in Building Management Systems
Press P button and enter the correct password. Change P0000_ value to P0023_ by
using Up and Down buttons. Move the cursor to right by using right button and adjust
building management system communication address parameter by using Up and Down
buttons. Set the parameter by using left button and leave parameter set mode by pressing
Pbutton.
P 24 Phase fault …………............………. 0 - 1
[1]
Phase protection is ON, in case there is phase loss on input, the inverter protects itself and
motor and phase fault written on display
P 25 Operating Hours (h)
Indicates inverter total operating hours information (just readable)
Press P button and enter the correct password. Change P0000_ value to P0024_ by
using Up and Down buttons. Move the cursor to right by using right button and adjust
phase protection parameter by using Up and Down buttons. Set the parameter by using
left button and leave parameter set mode by pressing Pbutton. Inverter can not protect
itself and motor in case this protection is inactive.
SETTING PARAMETERS

19 www.etna.com.tr
P 27 Total duration on power (h)
Indicates inverter total duration on power (just readable)
P 29 Number of Start
Indicates inverter total number of start-up information (just readable)
P 31 Inverter Operation Condition
Indicates inverter operation condition (Master- Slave)
Inverter Operation Condition Indicator on Internal Communication Line
SETTING PARAMETERS

20
INDICATOR CODE EXPLANATION
111 All inverters are set as Master, ( Faulty parameter set, only one inverter
can be set as Master)
100 Only Slave1 Enabled
020 Only Slave2 Enabled
004 Only Slave3 Enabled
120 Slave1 and Slave2 Enabled
104 Slave1 and Slave3 Enabled
024 Slave2 and Slave3 Enabled
124 Slave1, Slave2 and Slave3 Enabled
000 Only MASTER Enabled
SETTING PARAMETERS
These display codes can only be seen on Master inverter
Table of contents
Popular Control Unit manuals by other brands

Fibocom
Fibocom FM160 Series Hardware guide

Seneca
Seneca Z-8AI installation manual

Beko
Beko BEKOMAT 13 Instructions for installation and operation
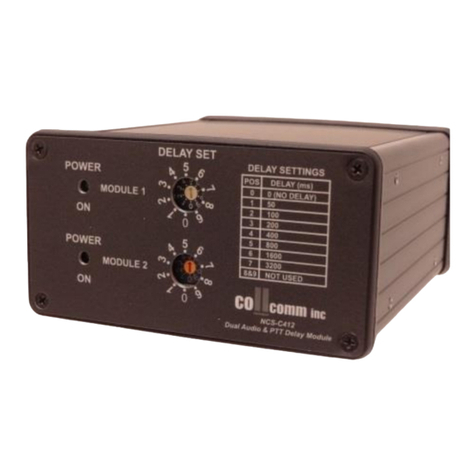
Collcomm
Collcomm NCS-C412 instruction sheet
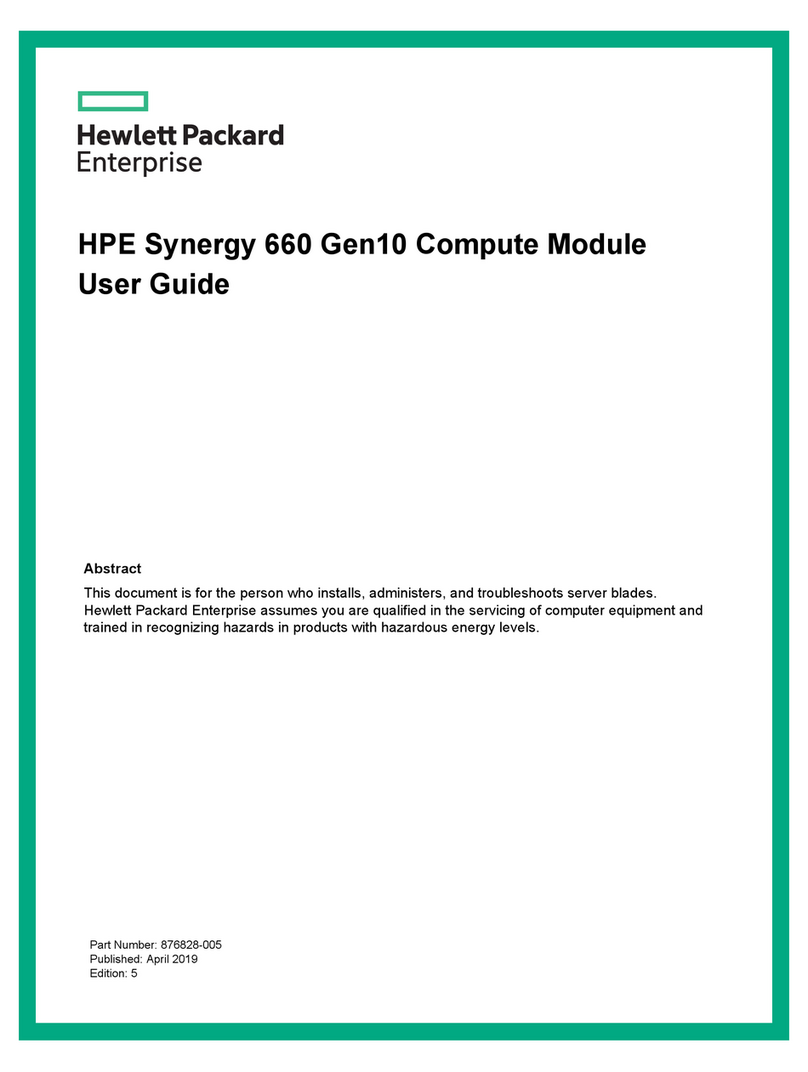
Hewlett Packard Enterprise
Hewlett Packard Enterprise Synergy 660 Gen10 user guide

Vag
Vag EKN AWWA Operation and maintenance instructions