EVAPCO CPA Technical specifications

1
C
CP
PA
A
MAINTENANCE INSTRUCTIONS
NOTE – Failure to follow recommended maintenance procedures could void unit
warranties.
Interior Sanitization:
The interior of the unit should be cleaned and sanitized periodically. The frequency of
cleaning will be dependent upon the application and the HACCP procedures outlined
for the air-handling unit. It is extremely critical that the chemicals used to clean the unit
are compatible with the interior materials and components. It is recommended the
supplier of cleaners and sanitizers for the plant be consulted so they can make
recommendations on proper cleaning procedures and processes for the unit.
When cleaning the unit:
1. Make sure the unit is locked and tagged out per plant procedures.
2. Cleaning personnel should make sure to have proper protective clothing, as per
their standard operating procedures.
3. Make sure all of the filters have been removed from the unit.
4. Protect any control devices inside the unit with waterproof covering.
5. If the unit is supplied with UVC lights, protect both the light and the fixture from
the cleaning process.
6. Make sure that all of the drain connections are open.
7. Do not aggressively spray/wash the motor bearings. Aggressive washing can
damage the seal and wash out the grease. This can cause premature failure of
the bearing.
8. The coils can be cleaned however do not spray with high pressure system,
especially at an angle toward the fins. This can bend the leading edge of the
fins over. If the coil has aluminum fins do not use caustic cleaners.
9. Do not aggressively spray the gasketing on the filters. This can damage the
gasketing.
10. Do not aggressively spray the caulked seams in the unit. This can damage or
dislodge the sealing caulk.
Prior to putting the unit back in operation:
1. Make sure the interior of unit is as dry as possible. Operating before the unit is dry
can cause water to be airborne and damage the electrical components or get
the filters wet and damage them.
2. Make sure any drain caps that have been removed for cleaning, are replaced
and sealed.
3. Remove all protective coverings used during the cleaning process.
4. Check all the caulked seams in the unit for integrity. Caulking is a routine
maintenance item.
5. Check the gasketing on the filter frames. Replace if necessary.
6. Replace all filters and remove all protective material from interior components.

2
Pre-filter Service:
The prefilters in the CPA unit are a pleated synthetic media filter with a moisture resistant
frame, each held in place with two holding clips.
The frequency of changing of the prefilters is
determined by the cleanliness of the air passing
through them and the proper operation of the
unit during the cleanup cycle. Most prefilter
systems are changed on a preventative
maintenance schedule and not purely by the
appearance of the filter. Visible dirt on the
surface is not a true indication of full loading of
the filter. However, it can be an initial indicator. If
the CPA unit is supplied with a filter gauge, the
filters should be changed at a 0.8” to 1.0” w.g.
reading. Typical life of the filter should be
anywhere from 30 days to 90 days, depending
upon the application and operation of the unit.
Please call Evapco at 507-446-8005 for availability of pre-filters.
Use the following procedure to change the prefilters.
1) Stop the fan motor and lockout using the disconnect switch.
2) Remove each filter from their individual holding frame.
3) Inspect the filter frame gasketing, caulking between the frames and holding clips
and replace if necessary.
4) Clean and sanitize the prefilter section.
5) Install the new prefilters. The prefilters should have the pleats in the vertical
position if possible.
6) Start the fan motor.
7) It is suggested that the prefilters be checked after approximately 8 hours of
operation to ensure that they have been installed properly.
8) Make note in the maintenance schedule for the unit.
Final Filter Service:
CPA units can be supplied with two types of final filters, MERV 14 or 15 and HEPA filters.
These filters are typically located at the discharge of the unit. The following is the
servicing procedures for the two types of filters.
MERV 14 and 15 Final Filters
The MERV 14 and 15 filters are a cartridge type filter each held with four spring holding
clips. The filter media is glass microfiber media (with an optional synthetic media filter).
The MERV 14 and 15 filters should be changed when the reading on the final filter
gauge indicates approximately 1.1” to 1.2” pressure drop across the filters. The pressure

3
drops should be read with the unit operating, all service doors closed and new prefilters
in place.
Typically the final filters should last 6 months to 15 months, depending upon the
cleanliness of the application, the frequency of prefilter changes, and if the unit
cleanup cycle is operated properly. The filter gauge will ensure the final filters have
reached their full life, and are not changed prematurely. Please contact EVAPCO at
507-446-8005 for availability of filters.
Use the following procedure to change the filters.
1) Stop the fan motor and lockout using
disconnect switch.
2) Remove the fully loaded final filters.
(NOTE: Maintenance personnel may
want to use protective clothing and
facemasks while changing.) Be careful
not to dislodge any of the particles
collected in the filter.
3) Inspect the final filter frame gasketing
(in some applications the gasketing is
on the filter and not the frame) and
the retaining clips.
4) Check the caulking seal between the
final filter frames. If any cracks are
observed, caulk with a USDA/FDA
approved sealant.
5) Install the new MERV 14 or 15 final filters. The pleats should be in the vertical
position if possible.
6) Clean and sanitize the final filter section.
7) Start the fan motor.
8) Make note in the maintenance schedule for the unit that the final filters have
been changed.
9) Check filter gauge for proper operation. Recalibrate if necessary.
HEPA Final Filters
The HEPA filters are a cartridge type filter each held with four holding clips. The filter
media is glass microfiber material.
The HEPA filters should be changed when the reading on the final filter gauge indicates
approximately 2.0” pressure drop across the filters. The pressure drops should be read
with the unit operating, all service doors closed and the prefilters in their clean position.
Typically the final filters should last 6 months to 15 months, depending upon the
cleanliness of the application, the frequency of prefilter changes, and if the unit
cleanup cycle is operated properly. The filter gauge will ensure the final filters have
reached their full life, and are not changed prematurely. Please contact EVAPCO at
507-446-8005 for availability of filters.

4
Use the following procedure to change the HEPA filters.
1) Stop the fan motor and lockout using disconnect switch.
2) Remove the fully loaded final filters. (NOTE: Maintenance personnel may want to
use protective clothing and facemasks while changing.) Be careful not to
dislodge any of the particles collected in the filter.
3) Inspect the final filter frame gasketing and the retaining clips.
4) Check the caulking seal between the final filter frames. If any cracks are
observed, caulk with a USDA/FDA sealant.
5) Install the new HEPA final filters. The pleats should be in the vertical position.
6) Clean and sanitize the final filter section.
7) Start the fan motor.
8) Make note in the maintenance schedule for the unit that the final filters have
been changed.
9) Check filter gauge for proper operation.
Recalibrate if necessary.
The HEPA filters are installed using the following
procedure:
•Carefully open the box. Touch only
the frame of the filter, never the
white media.
•Slide in the filter into the frame,
centering on the filter frame.
•Install four spring bolts to a
compression of approximately 30-
50%.

5
Some applications will have a three filter system, a pre, an intermediate and a
final filter. The pre and intermediate filters are held in the same filter frame at
the inlet of the unit using a special “P” clip. The intermediate filter “pushes
through” the frame and the pre filters sits in front. The following shows the
installation of the “P” clip.
Blower, Motor and Drive Assembly:
1) Every 6 months the fastening bolts for the blower, motor and drive should be
checked for tightness. Also, check the bearing set screws and the blower hub
set screws. Check alignment of the sheaves.
2) A periodic maintenance schedule should be set up for checking the belts. At
minimum, the belts should be checked every 6 to 9 months for wear and proper
tightness and alignment.
3) The blower bearings should be lubricated per the lubrication instructions and
schedule in the service manual.
4) Motors that do not have re-grease capability are factory lubricated for the
normal life of the bearings. For motors with re-grease capability, they should be
lubricated at these intervals:
Motor
Horsepower
Rated Speed (RPM)
3600
1800
1200
900
2
5500
12000
18000
22000
10
3600
9500
15000
18000
40
2200
7400
12000
15000
50 and above
2200
3500
7400
10500
Baldor motors should normally be greased with Exxon Mobil Polyrex EM grease
and U.S. motors either a Chevron SRI#2 or a Shell Dolium R.

6
Greasing procedure:
Clean the grease fitting (or the area around the hole, if equipped with slotted
grease screws. If motor has a purge plug, remove it. Apply grease gun fitting.
Too much grease or injecting grease too quickly can cause premature bearing
failure. Slowly apply the recommended amount of grease, taking 1 minute or
more to apply. Operate motor for 20 minutes, the reinstall purge plug if
previously removed. Caution: Mixing dissimilar grease is not recommended.
Amount of Grease to Add
5) If the unit is supplied with spring isolation, check spring bolts/nuts for tightness.
Also, check the flexible duct for wear.
Electrical Connections:
The control system for the unit should be checked at least twice a year for proper
operation of the system. Also check all terminals to ensure they are tight. It is
suggested that the units be checked in the fall, prior to the heating season and in the
spring, prior to the summer cooling season. Make sure that all settings are per the
operation manual.
Smoke Detector (Optional Feature)
IMPORTANT: The smoke detector must be tested and maintained regularly following
NFPA 72 requirements. The detector should be cleaned and tested at least once a
year. Detailed information on maintenance and service is contained within the service
manual for this unit.
WARNING: WITHOUT PROPER SERVICE AND MAINTENANCE, THE SMOKE DETECTOR COULD
INITIATE FALSE ALARMS OR FAIL TO FUNCTION PROPERLY IN THE CASE OF A FIRE. STRICT
SERVICE AND MAINTENANCE SCHEDULES MUST BE FOLLOWED AND COMPLETE SERVICE
RECORDS KEPT.
Ammonia Detector (Optional Feature)
For proper operation it is essential that the test and calibration schedule be adhered to.
The supplier recommends the following maintenance schedule.
1) Response test once per month. Expose sensor to ammonia/water solution to
verify proper sensor response and alarm functions. Test more frequently in highly
critical applications.
Motor Horsepower
Amount of Grease to
Add
Weight in
Volume in
Ounces
Teaspoons
2
0.3
2.0
10
0.61
3.9
40
0.81
5.2
50 and above
2.12
13.4

7
2) Calibration should be performed with certified calibration gas every six months.
All tests and calibrations must be logged. Note – the sensor must have a 12 hour
warm up before it can be calibrated.
Sensor Life: These electrochemical cells are extremely reliable, but several things can
cause the cell chemicals to become depleted including:
1) A period of time.
2) Exposure to high temperatures.
3) Exposure to varying concentrations of the target gas.
4) Exposure to high moisture for extended periods without proper sensor enclosure
When the cell becomes depleted, the unit will give no indication of failure other than
that the sensor will not respond. For this reason it is absolutely essential that these units
be exercised with a gas sample on a regular and timely basis.
Typical sensor life in a refrigerated area will be two to three years. Typical life in a non-
refrigerated area will be one to two years. Exposure to high levels of ammonia will
shorten these times. In addition to timely response checks, a preventative
maintenance program of periodic cell replacement should be implemented.
When the cell becomes depleted, a replacement cell can be obtained from Evapco,
507-446-8005. Simply unplug the ribbon cable from the transmitter, pull the old cell from
the spring clip, discard the old cell and replace it with a new one.
The sensor should be calibrated after a 12 hour warm-up period.
WARNING: WITHOUT PROPER SERVICE AND MAINTENANCE, THE AMMONIA DETECTOR
COULD INITIATE FALSE ALARMS OR FAIL TO FUNCTION PROPERLY IN THE CASE OF AN
AMMONIA LEAK. STRICT SERVICE AND MAINTENANCE SCHEDULES MUST BE FOLLOWED
AND COMPLETE SERVICE RECORDS KEPT.
ESS UVC Lights (Optional feature)
1) CAUTION! NEVER EXPOSE EYES OR SKIN TO UVC LIGHT. ALWAYS TURN
POWER OFF, OR WEAR GLOVES, FACE SHIELDS AND COVER ANY EXPOSED SKIN,
BEFORE SERVICING THE UNIT.
2) CAUTION! IMPROPER SERVICE AND MAINTENANCE CAN CAUSE FIRE, ELECTRICAL
SHOCK OR OTHER CONDITIONS THAT MAY CAUSE PERSONAL INJURY OR PROPERTY
DAMAGE.
3) The bulbs should be replaced every 12 – 18 months and should need no
maintenance between replacements. Carefully remove the old bulb(s) and
check all wiring and connections to the bulbs. Carefully inspect the watertight
assembly and replace if necessary.
4) Test all circuits. Leave the unit, close the access door, and then turn the
lights on. A “blue hue” will glow from the light indicating the fixture is
working. Remember – only view the lights through the service door
window, or while wearing the protective gear as described above.
5) Mark your preventative maintenance calendar to replace the bulbs 12-18
months from the replacement date.

8
6) Check local codes for proper disposal of the used bulbs.
Desiccant Dehumidification (Optional feature)
1) CAUTION! The desiccant wheel is constructed of a fragile composite material.
DO NOT clean with water, chemicals, solvents, or high pressure sprays.
2) See the separate section in the maintenance manual for proper cleaning and
maintenance of the desiccant wheel and system.
VFD Drive Systems (Optional feature)
1) The control panel enclosing the VFD may contain an ambient air
cooling/ventilation system. This cooling system is used to control the interior
control panel temperatures for the VFD. The cooling system contains a filter
which must be periodically cleaned. It is recommended it be cleaned as least
as often as the pre-filters in the unit and more frequently if the atmosphere
around the unit is very dirty and dusty. Failure to keep the panel cooling filter
clean can cause reduced cooling air flow to the control panel. This can result in
overheating of the VFD which can then cause faults and or failure of the drive
and possible damage to the unit motor.
PLC Control Systems (Optional feature)
1) The control panel enclosing the PLC controls may contain an ambient air
cooling/ventilation system. This cooling system is used to control the interior
control panel temperatures for the PLC. The cooling system contains a filter
which must be periodically cleaned. It is recommended it be cleaned as
least as often as the pre-filters in the unit and more frequently if the
atmosphere around the unit is very dirty and dusty. Failure to keep the panel
cooling filter clean can cause reduced cooling air flow to the control panel.
This can result in overheating of the PLC which can then cause faults and or
failure of the control system.
Unit Motor Removal Rail (option):
Some units include motor removal rail/trolley system to facilitate easier and safer
removal of the unit motor. Please refer to the trolley installation instructions for
proper mounting of the trolley. Prior to every use, make sure the fasteners and
hardware are tight and aligned. Do not “swing” the motor when on the trolley

9
since this may stress the beam or trolley and cause an unsafe condition. Check
trolley before each use and at regular intervals per the O&M manual.
Unit Roof Fall Protection Anchor(s) (option):
As an option, CPA units can be
supplied with roof mounted fall
protection anchor(s). The system
includes a heavy backing plate,
installed at the factory, with an anchor
fastened to the heavy plate.
WARNING – this anchor is part of a
personal fall arrest or fall restraint
system. The instructions in this
document and the information in the O&M manual must be read and
understood before using the anchor. Alterations or misuse of the anchor or
failure to follow instructions may result in serious injury or death.
The end user or contractor using the anchor must use OSHA approved full body
harness and lifelines and selected for the application. Do not hang, lift or
support tools or equipment from the anchor, or attach guy lines to the anchor.
It is the responsibility of the users to assure they are familiar with the instructions,
trained in the correct care and use of, and are aware of the operating
characteristics, application limitations, and consequences of improper use of
the anchor.
The anchor is designed for use by one person with a combined weight (clothing,
tools, etc.) of nor more than 310 lbs (141 kg). Only one person shall be attached
to the anchor at any one time.
The anchor should be inspected before each use and, additionally, by a
competent person other than the user at intervals of no more than one year.
Follow the inspection procedures outlined in the O&M manual. Results of the
Competent Person inspection should be recorded in the maintenance log.
The anchor is not repairable. If the anchor is subject to a fall force or inspection
reveals an unsafe or defective condition, remove the anchor from service

10
Indirect Fired Heating Section:
The heat exchanger and stack should be inspected before the start of each
heating season. Make sure the stack is intact and has not deteriorated or the
roof cap leaking. Check the drain to ensure it is open and free flowing. Check
the heat exchanger for cracks or other deterioration.
Completely check the gas train for leaks. Check the complete control system
and all safeties for proper operation.
CAUTION! INDIRECT FIRED HEAT CHANGERS AND FLUE VENT STACKS ARE SUPPLIED WITH
CONDENSATE DRAIN CONNECTIONS PIPED TO THE OUTSIDE OF THE UNIT. THIS
CONDENSATE CAN BE CORROSIVE AND EXTREME CARE SHOULD BE EXCERCISED WHEN
SELECTING A LOCATION FOR DISCHARGE OF THE CONDENSATE. CONDENSATE SHOULD
NOT BE DISCHARGED ON TO A ROOF. FOLLOW ALL STATE AND LOCAL CODES.
SEMI-ANNUALLY CHECK THE DRAINS AND DRAIN PIPING/TRAPS TO ENSURE THEY ARE FREE
FLOWING. FAILURE TO EFFECTIVLY DRAIN CONDENSATE FORMED IN THE HEAT
EXCHANGER CAN RESULT IN PREMATURE CATASTROPHIC FAILURE OF THE HEAT
EXCHANGER.
Miscellaneous Items:
1) Check the operation of the dampers every time the electrical controls are
checked. Make sure that all of the linkage operates freely and the dampers
function correctly.
2) Check the seal between the sections on the units. Make sure the section split
seals remain water and air tight.
3) Check all drain traps to make sure that they are not plugged and have an
adequate water seal. Make sure that the other drain pans do not have standing
water in them.
4) Check all door gasketing yearly to make sure there is an airtight seal.
5) If the unit is supplied with a control panel cooling system, clean or replace the
filter regularly.
12-4-15
EVAPCO, Inc. 215 1st Street NE, P.O. Box 88 Medford, MN 55049
Phone: (507) 446-8005 Fax: (507) 446-8239
Popular Fan manuals by other brands

Munters
Munters TU600 Manual for use and maintenance
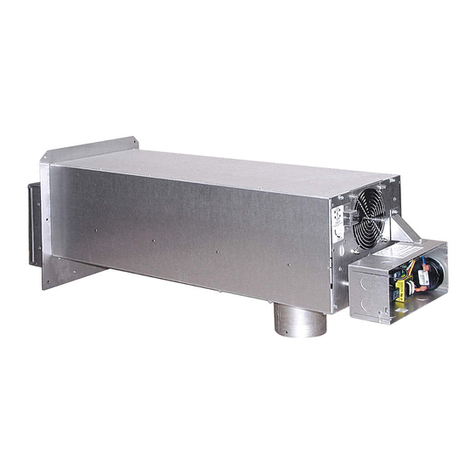
TJERNLUND
TJERNLUND SS2 SIDESHOT WITH UC1 UNIVERSAL CONTROL (VERSION X.02) 8504105 REV... installation instructions

Casablanca
Casablanca PANAMA owner's manual
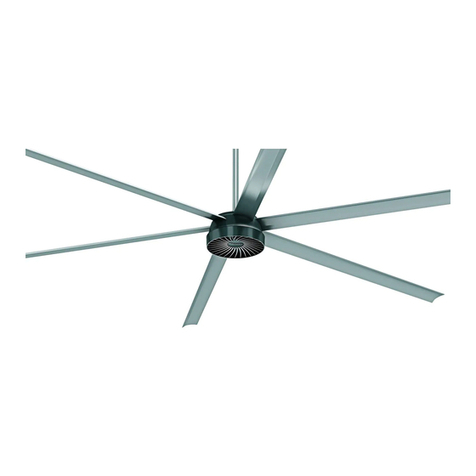
MacroAir Technologies
MacroAir Technologies AirVolution-D 370 installation manual
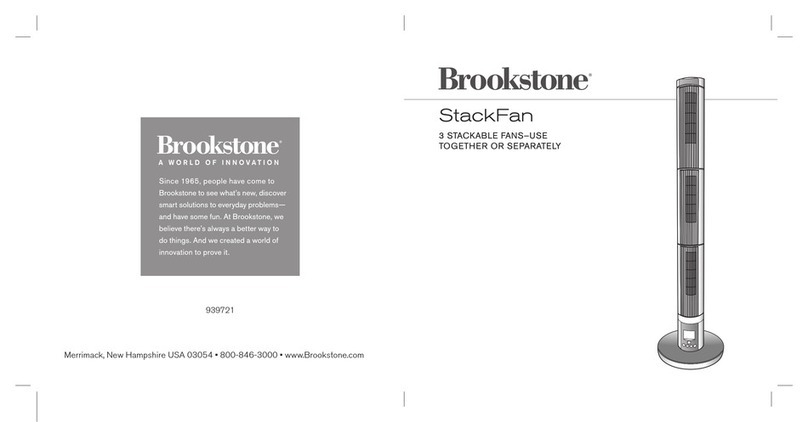
Brookstone
Brookstone STACKFAN manual

Broan
Broan SOLITAIRE Series installation instructions