EYC P064 Series User manual

www.eyc-tech.com
1
P064 SERIAL
DIGITAL INTELLIGENT
PRESSURE TRANSMITTER /
DIFFERENTIAL PRESSURE TRANSMITTER
INSTRUCTION MANUAL

www.eyc-tech.com
2
Warning
1. Place the transmitter horizontally before adjusting.
2. Adjust the zero point of the transmitter after it is installed on
site.
3. The process connection should be well installed and tightened
before the transmitter is pressurized.
4. The transmitter should be installed in a dry environment
preventing from getting wet by rain. In harsh environments,
protection box for the transmitter should be used.
5. It is forbidden for the user to disassemble the transmitter by
self.
6. Do not disassemble the transmitter cover in an
explosive/flammable environment when power is on.
7. Please check if the transmitter power supply voltage meets the
power supply voltage requirements in the manual.
8. The external grounding screw of the transmitter should be
connected to the ground securely.
9. The installation of the transmitter in an explosive environment
must comply with international, national and local standards,
specifications and guidelines. Please refer to the restrictions on
safe installation listed in the Explosion-proof section of the
manual.
10. Installation and use of the intrinsically safe transmitter with
safety barrier shall be carried out according to the specific
instruction manual.
11. When doing transmitter calibration and temperature
compensation using HART communication, use the
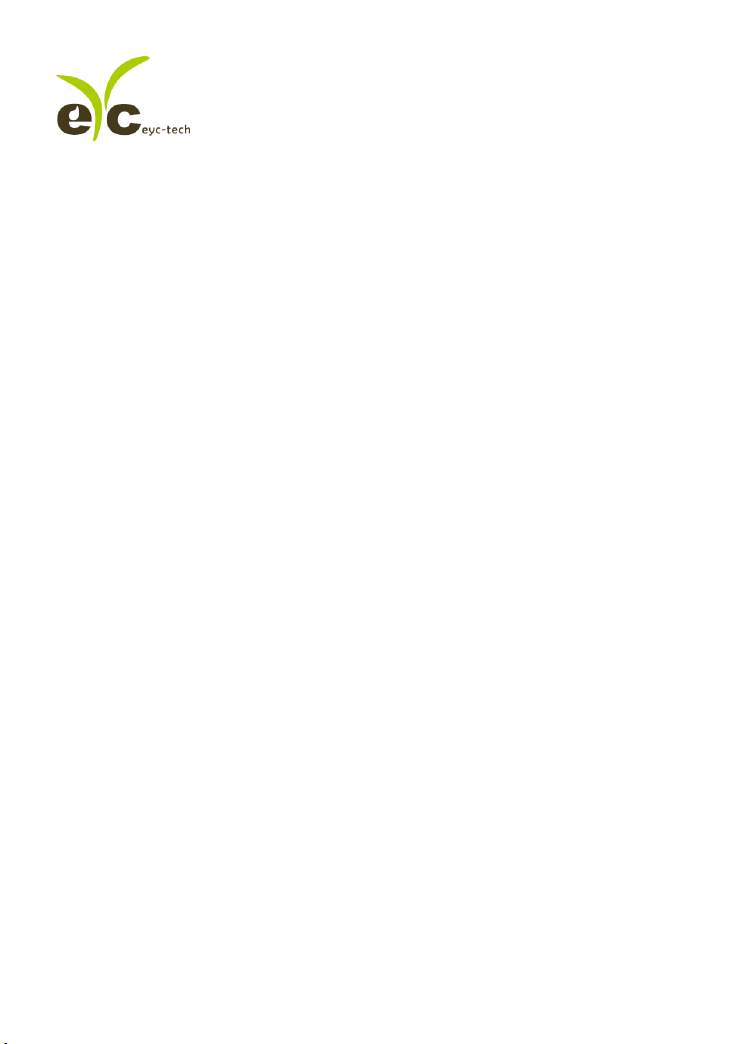
www.eyc-tech.com
3
communication equipment and software provided by the
manufacturer.

www.eyc-tech.com
4
Contents
Introduction.......................................................................................5
1.Introductio......................................................................................6
1.1 Overall appearance ............................................................6
1.2 Intelligent transmitter working principle ..............................6
2. Installation....................................................................................8
2.1 On-site installation..............................................................8
2.2 Relevant Issues of measurement methods......................11
2.3 Electrical Installation.........................................................15
2.4 Intrinsic Safety Explosion-proof Type Transmitter System
Wiring Diagram.......................................................................17
2.5 Isolation Explosion-proof Type Transmitter Instruction ....18
3.Debugging and Operation...........................................................19
3.1 Overview...........................................................................19
3.2 Button Operation for the Transmitter without the LCD
Display ....................................................................................20
3.3 Button Operation for the Transmitter with the LCD Display21
4.The flange transmitter installation & operation instructions........26
4.1 Overview...........................................................................26
4.2 Installation site..................................................................27
4.3 Calibration instrument.......................................................28

www.EYC.com
5
The intelligent transmitter produced by our company is a
multi-functional digital instrument. It is designed with advanced,
mature and reliable silicon sensor or capacitive sensor technology
combined with advanced single-chip technology and sensor digital
conversion technology.
The powerful functions and high-speed computing capabilities
of MCU, the core component, ensure the excellent quality of the
transmitter. The entire design framework focuses on reliability,
stability, high-precision and intelligence.
The transmitter has powerful interface operation function. The
digital header can display pressure, percentage, current, and
0~100% analog indication. By key operation, zero point shift, range
setting and damping setting can be easily completed without
standard pressure source. The setting of basic parameters is very
convenient for on-site comissioning.
Signal conversion, signal acquisition and processing, and
current output control use the application-specific integrated circuit
(ASICS) to make the transmitter stable, reliable, and
vibration-resistant, with good interchangeability.
Introduction

www.eyc-tech.com
6
1.1 Overall appearance
1.2 Intelligent transmitter working principle
1.2.1 Working principle
Figure 1-1 is an electrical block diagram of the basic working principle of an
intelligent transmitter. The working principle and functions of the various
components will be described below.
1.Introduction

www.eyc-tech.com
7
Figure 1-1 block diagram of Transmitter principle
1.2.2 Intelligent circuit board
1) A/D conversion
The A/D conversion circuit uses a dedicated low-power integrated circuit
to convert the analog current output into a digital quantity by the demodulator
with an accuracy of up to 18 bits, which is supplied to the microprocessor as an
input signal.
2) Microprocessor
The microprocessor of the intelligent transmitter controls the A/D and D/A
conversion work, and can also complete self-diagnosis and realize digital
communication. During work, a digital pressure value is processed by the
microprocessor and stored as a digital to ensure precise correction and
engineering unit conversion. In addition, the microprocessor can also perform
sensor linearization, turndown ratio, damping time, and other functional
settings.
3) EEPROM memory
The EEPROM stores all configuration, characterization and digital
trimming parameters. This memory is non-volatile, so even if the power is
turned off, the stored data can be kept intact, so that intelligent communication
can be realized at any time.
4) D/A conversion
The D/A conversion converts the corrected digital signal sent from the
microprocessor into a 4-20 mA analog signal and outputs it to the loop.
5) Digital communication
Transmitters with the HART protocol can test and configure intelligent
transmitters via a single communicator. Or complete communication through
any host system host that supports HART communication protocol. The HART

www.eyc-tech.com
8
protocol uses the industry standard BELL202 frequency phase shift keying
(FSK) technology to superimpose the digital signal of 1200Hz or 2000Hz on
the 4~20mA signal to realize communication. When communicating, the
frequency signal does not cause any interference to the 4~20mA process.
Intelligent transmitters can be tested and configured with dedicated adapters
and software without HART protocol transmitters.
6) Display and buttons
The Intelligent transmitter with liquid crystal display can display the
pressure value, current value, 0%-100% ratio display and temperature value of
the sensor measured by the transmitter, and the transmitter can be configured
through the buttons on the LCD panel.
Intelligent transmitters without display can also be used to clear, actively
calibrate the transmitter through the S and Z buttons on the line panel.
2.1 On-site installation
2.1.1 Installation method
Our pressure transmitters can be mounted directly on 2" pipes
Or mount directly on the wall and on the dashboard. (as shown in Figure 2-1
and Figure 2-2)
2. Installation

www.eyc-tech.com
9
Figure 2-1 Capacitive transmitter installation
Figure 2-2 Piezoresistive transmitter installation
After loosening the locking screw, the electronic compartment can be
rotated 90°left and right. As shown in Figure 2-3.
Warning: Do not rotate more than 90°! So as not to break the internal
cable!
Figure 2-3 Housing rotation

www.eyc-tech.com
10
2.1.2 Pressure method
There are three types of capacitive transmitters, as shown in Figure 2-4:
·
Figure 2-4 Capacitor transmitter pressure map
The pressure-receiving type of the piezoresistive transmitter is mainly a
screw connection method, and the user can provide a pressure-welded joint
according to the specific thread specification.
2.1.3 The process connection hole distance adjustment of
differential pressure transmitter
The process connection holes on the pressure chamber are 1/4-18 NPT.
These process connection holes require a thread seal. When using a waist
flange joint, the transmitter can be easily removed from the production unit by
simply removing the upper and lower bolts of the joint. The center distance
between the two process connection holes is 54 mm. Rotating the waist flange
joint, the center distance can be changed to 50.8 mm, 54 mm, 57.2 mm
Waist flange type
Welding pipe joint type
Integration of the
three valve type

www.eyc-tech.com
11
as shown in the figure 2-5:
Figure 2-5 Connection hole distance of differential pressure transmitter
2.1.4 Installation Precautions
1. Prevent the transmitter from coming in contact with the measured
medium with corrosivity or high temperature (≥ 90 °C).
2. Prevent the dross from depositing in the pressure tube.
3. Get the pressure tube shortened as possible as it can.
4. Keep balance between the liquid heads in the pressure tubes on both
sides of the differential pressure transmitter.
5. Install the pressure tube in a place with small temperature gradient and
temperature fluctuation.
6. Prevent from the crystallization or low-temperature freeze in the
pressure tube.
2.2 Relevant Issues of measurement methods
Liquid measurement:
When measuring the flow rate of the liquid, the pressure tap should be
opened on the side of the process piping to avoid sedimentation of the dross.
At the same time, the transmitter should be installed beside or below the
pressure tap to allow air bubbles to be discharged into the process piping.

www.eyc-tech.com
12
Gas measurement:
When measuring the gas flow, the pressure tap should be opened on the
top or side of the process piping. And the transmitter should be mounted
beside or above the process piping so that the accumulated liquid can easily
flow into the process piping.
Steam measurement:
When measuring the steam flow, the pressure tap should be opened on
the side of the process piping and the transmitter is installed below the
pressure tap so that the pressure tube can be filled with the collected cold
liquid. It should be noted that when measuring steam or other high temperature
media, the temperature should not be higher than the limiting operating
temperature of the transmitter. When the measured medium is steam, the
pressure tube should be filled with water to prevent the steam from directly
contacting the transmitter so that the volume change of the transmitter is
negligible when the transmitter is working, and there is no need to install a
condensing tank.
Level measurement:
The differential pressure transmitter used to measure the liquid level is
actually the static head that measures the liquid column. This pressure is
determined by the level and the specific gravity of the liquid, and it’s equal to
the liquid level above the pressure tap multiply by the specific gravity of the
liquid, regardless of the volume or shape of the container.
●Liquid level measurement of open containers
When measuring the liquid level of the open container, the transmitter is
mounted close to the bottom of the container to measure the pressure
corresponding to the liquid level above the transmitter. The pressure of liquid
level in the container acts on the high-pressure side of the transmitter while the

www.eyc-tech.com
13
low-pressure side is connected with the atmosphere. If the lowest level of the
measured level changes is above the place where the transmitter is mounted,
the transmitter must make the positive transfer.
●Level measurement of closed containers
In the closed container, the pressure P0 of the container above the liquid
affects the measured pressure at the bottom of the container. Therefore, the
pressure at the bottom of the vessel is equal to the liquid level multiply by the
specific gravity of the liquid plus the pressure P0 of the closed container. In
order to measure the actual level, the pressure P0 of container should be
subtracted from the measured pressure at the bottom of container. For this
reason, open a pressure tap on the top of the container and get it connected to
the low-pressure side of the transmitter. Thus, the pressure in the container
acts on both the high and the low pressure sides of the transmitter at the same
time. As a result, the differential pressure obtained is proportional to the
product of the liquid level and the specific gravity of the liquid.
●Pressure connections
1) Dry pressure connection
If the gas above the liquid does not condense, the connecting tube on the
low-pressure side of the transmitter will remain dry. This condition is called the
dry pressure connection. The method of determining the measurement range
of the transmitter is the same as the method of determining the measuring
liquid level of opening container.
2) Wet pressure connection
If the gas above the liquid condenses, the liquid will gradually accumulate
in the pressure tube on the low-pressure side of the transmitter so that the
measurement error is caused. In order to eliminate this error, a certain liquid is
previously filled in the pressure tube on the low-pressure side of the transmitter,

www.eyc-tech.com
14
which is called the wet pressure connection.
In the above case, there is a pressure head on the low-pressure side of the
transmitter, so the negative transfer must be performed.
Reduce the error
The pressure tube connects the transmitter to the process piping, and
transfers the pressure at the pressure tap on the process line to the transmitter.
The causes of errors in the pressure transfer process are as follows:
1) Leakage;
2) Wear loss (especially when the detergent is used)
3) There is the gas in the liquid pipeline (causing the pressure head error).
4) Accumulated liquid in gas pipeline (causing the pressure head error)
5) Density difference between the pressure tubes on both sides due to
the temperature difference (causing pressure head error)
The methods of reducing the errors are as follows:
1) The pressure tube should be as short as possible.
2) The pressure tube should be connected upward to the process pipeline
and its slope should be less than 1/12 When measuring liquid or
steam.
3) For the gas measurement, the pressure pipe should be connected
downward to the process pipeline, and its slope should be not less than
1/12.
4) The layout of the liquid pressure pipeline should avoid the occurrence
of high points in the middle, and the layout of the gas pressure tube
should avoid the occurrence of low points in the middle.
5) The two pressure should maintain the same temperature.
6) In order to avoid the influence of friction, the diameter of the pressure
tube should be large enough.

www.eyc-tech.com
15
7) There should be no gas in the pressure tube filled with liquid.
8) When using the spacer liquid, the liquid in the pressure tubes
on both sides should be the same.
9) When using the cleaning agent, the connection of the cleaning agent
should be close to the pressure tapping of the process pipeline. The
length and diameter of the pipes through which the cleaning agent
passes should be the same. The cleaning agent should be prevented
from passing through the transmitter.
2.3 Electrical Installation
Wiring diagram of system:
Figure 2-6
(Note 1: Please refer to the usage methods of distributor and safety barrier
if the users require the distributor or safety barrier according to the site and
design requirements.)
It is recommended to wire the explosion-proof cable to the terminal, the

www.eyc-tech.com
16
cable diameter is φ8~ φ12. The terminal of the cable is designed with the test
end to facilitate the operator to test online. The signal terminals are located in a
separate cabinet of the electrical box. Unscrew the cover of indicator to make
the wire connection. The upper terminal is the signal terminal and the lower
terminal is for the test meter. Figure 2-11 shows the terminal position. The test
terminal is used to connect with the optional indicator or for testing. The power
is sent to the transmitter through the signal line, no additional wires are
required.
If the diode is damaged unfortunately, the direct connected (not through
the shield plate) test terminal can make the transmitter keep working, but it will
not be able to connect to the local indicator.
The signal line does not need to be shielded, but the effect will be better if
the stranded wire is used. The signal line should not be arranged together with
other power lines, or near the heavy current installation.
The threading hole of the transmitter housing should be sealed or inserted
with a plug coated with the sealant, so as to prevent the moisture accumulation
in the housing. If there is no sealing for the wiring, during the transmitter
installation, the threading hole should face downward to discharge water.
The signal line can be un-grounded (floating) or the ground connection
can be on the arbitrary point of the signal loop line. The transmitter housing
can be grounded or un-grounded; there is no voltage stabilization requirement
for the power supply, and even if the peak-peak value of the power ripple
reaches 1V, the transmitter output ripple can still be ignored. Because the
ground connection of the transmitter is through capacity coupling, please don't
! Pay special attention:
Do not connect the signal line with power to the test terminal,
otherwise the diode inside the test terminal will be destroyed.

www.eyc-tech.com
17
use the high voltage tramegger to check the insulation resistance. The voltage
to be used to check the lines should not be more than 100V.
The transmitter circuit design is the intrinsic safety circuit, and the output
current is limited below 24mA DC (24mA DC under the condition of high
temperature or high supply voltage).
2.4 Intrinsic Safety Explosion-proof Type Transmitter
System Wiring Diagram
Ui:28v DC Um ≥ 250V AC/DC
Ii:30mA Uo ≤ 28V DC
Pi:0.84W Io ≤ 30mA
Notes: ①Please refer to GB3836, 4-2000 standards for the definitions of
Vm, Vo, Io, Po, Vi, Ii and Pi.
②The maximum allowable distributed capacitance CP for the wire or
cable connection between the guard grating and the transmitter is not greater
than 0.02uF, and the maximum allowable distributed inductance LP is not
greater than 2.0mH.

www.eyc-tech.com
18
2.5 Isolation Explosion-proof Type Transmitter
Instruction
■ During the installation for the isolation explosion-proof type transmitter,
attention should be paid to the protection for the explosion-proof joint face and
the explosion-proof measures; the end cover must be screwed tightly and the
locking device must be locked tightly; the housing should be grounded; during
the loading and unloading for the parts of the plane gap, please prevent the
gap from becoming bigger caused by plane collision and scratch; please
prevent the housing from falling, crash or damage, so as not to reduce the
strength; after the completion of the instrument maintenance inspection, all the
bolts, housings and wirings must be fastened, and cannot be damaged, or else
the explosion-proof performance will be lost.
■ For the isolation explosion-proof type transmitter, it is forbidden to open
or loosen the end cover or housing under the energized condition on site.
■ The isolation explosion-proof type transmitter has two outlet ports, and
one of them is adopted for leading in cable connection, and its cable connector
should adopt the dedicated compression nut type explosion-proof leading-in
device. The tightly screwed hollow bolt, gasket, sealing rubber ring are set
along the external diameter of the cable, put into the port and screwed tightly;
the sealing ring must be ensured to be tightly packed along the external
diameter of the cable, and the hollow bolt must be screwed in for over 6 screw
threads. The other outlet port must be equipped with the sealing rubber ring,
gasket, solid bolt as well, and the solid must be screwed tightly; it must be
screwed in for over 6 screw threads, too. In order to meet the explosion-proof
requirements, the cable with the model KVVR with the diameter of 1.5*4 and
the outside core diameter of 10mm(10.5mmMAX) should be selected.
■ The structure and parts of the isolation explosion-proof type transmitter has

www.eyc-tech.com
19
passed the strict inspections and tests according to the isolation
explosion-proof type standard, conforming to the regulation of the national
standard GB3836.2—2000 Explosion-proof Electrical Equipment and Isolation
Explosion-proof Type Electrical Equipment “d” Applied in the Explosive
Environment, and its symbol is EXdsⅡBT5.
3.1 Overview
Panel Figure for the Circuit Board without Display
Figure 3-1
3.Debugging and Operation

www.eyc-tech.com
20
Panel Figure for the LCD Display Gauge Head
Figure 3-2
3.2 Button Operation for the Transmitter without the
LCD Display
When the transmitter has no display gauge head, the following operations
can be performed by using the buttons S and Z (as shown in Figure 3-1)
originally equipped on the circuit board.
3.2.1 Resetting
Please make sure the transmitter is in the “power on” status and in the
status of zero pressure compression, press and hold both S button and Z
button for more than 5 seconds, then release the two buttons at the same time,
press and hold the two buttons again for about 2 seconds, and the transmitter
will be reset according to the current pressure value.
3.2.2 Lower limit calibration (Zero point active transfer)
Please make sure the transmitter is in the “power on” status and in the
status of lower limit pressure range compression, press and hold both S button
and Z button for more than 5 seconds, then release the two buttons at the
Table of contents
Other EYC Transmitter manuals
Popular Transmitter manuals by other brands
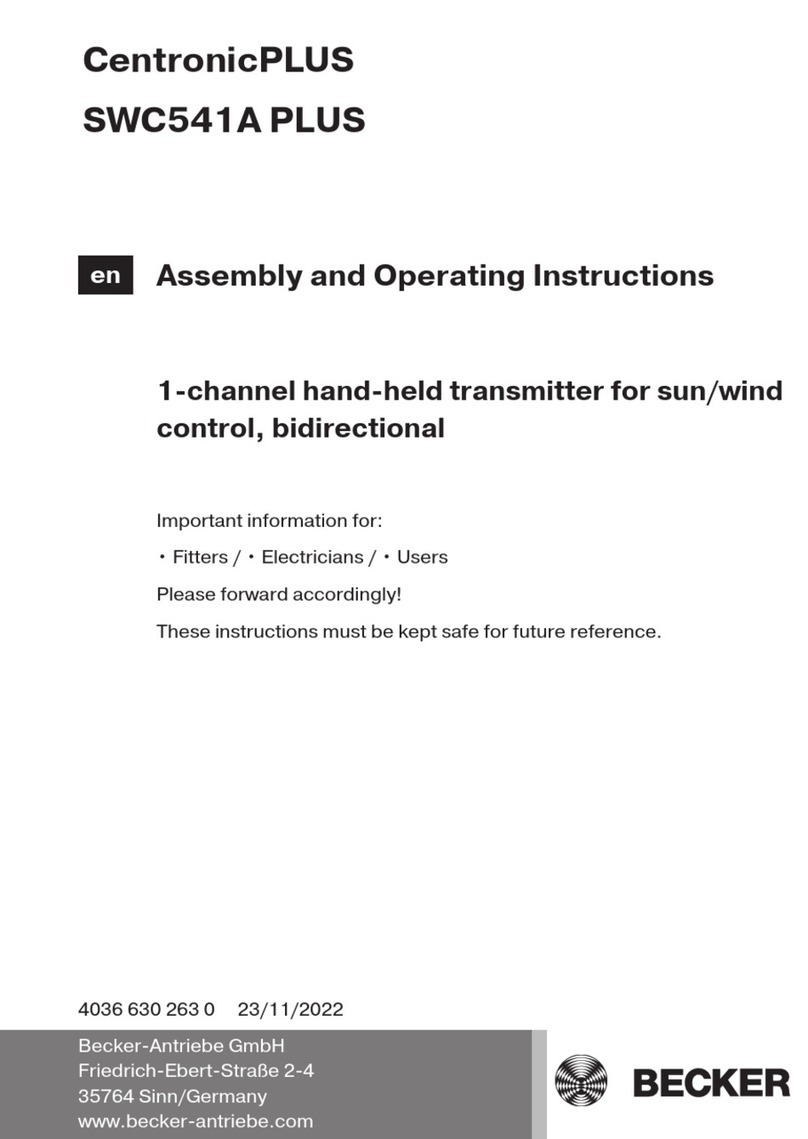
Becker
Becker CentronicPLUS SWC541A PLUS Assembly and operating instructions

Emerson
Emerson Rosemount 708 quick start guide

TAG Heuer
TAG Heuer HL 675 user manual
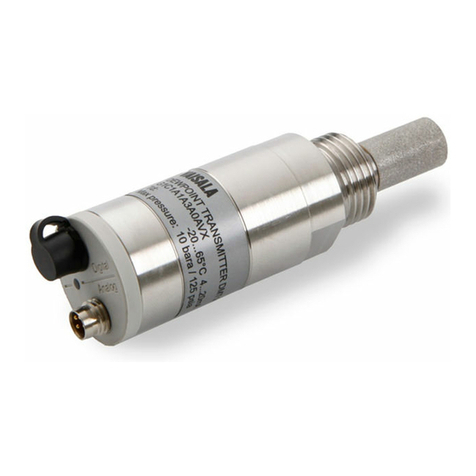
Vaisala
Vaisala DRYCAP DMT143 manual

Emerson
Emerson MICRO MOTION 1500 Configuration and user manual
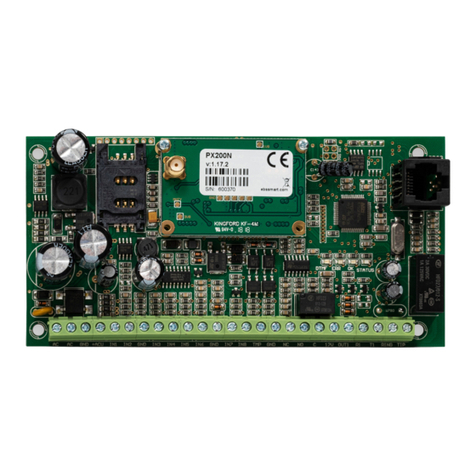
EBS
EBS PX200N Installation and programming manual