EZG FORK-N-HOG User manual

FNH
FORK-N-HOG
FORKLIFT
Owner’s Manual
EZG MANUFACTURING
1-800-417-9272
FORK-N-HOG FORKLIFT
EZG Manufacturing
405 Watertown Road
Waterford, Ohio 45786
(740) 749-3512 or 1-800-417-9272
Fax (740) 962-2037 www.ezgmfg.com
Before using this FORK-N-HOG FORKLIFT,
study and understand the entire Owner’s
Manual.
Serial Number _____________

1-800-417-9272 www.ezgmfg.com
Revision Number-001 01-01-2020 - Present
2
INTRODUCTION.................................................................................................................................3
ABOUT THIS MANUAL.......................................................................................................................3
GENERAL INFORMATION..................................................................................................................3
SAFETY INFORMATION.....................................................................................................................3
SAFETY PRECAUTIONS.....................................................................................................................4
CALIFORNIA PROPOSITION 65WARNING......................................................................................5
MACHINE DESCRIPTION.....................................................................................................................5
SPECIFICATIONS.......................................................................................................................6
OPERATING SAFETY............................................................................................................................................7
PRE-STARTCHECKS /ADJUSTMENTS.......................................................................................................................8
START / STOP PROCEDURE............................................................................................9-12
SERVICE & MAINTENANCE................................................................................................13-22
MAIN COMPONTENTS............................................................................................................................23-25
DRIVE WHEEL................................................................................................................................26-27
WARRANTY......................................................................................................................................43
TABLE OF CONTENTS
STEERING SYSTEM....................................................................................................................28-30
BRAKE SYSTEM..........................................................................................................................31-32
HOISTING SYSTEM.....................................................................................................................33-36
ELECTRICAL SYSTEM.................................................................................................................37-39
HYDRAULIC SYSTEM..................................................................................................................40-41
NOTES / SERVICES RECORDS......................................................................................................42
WARRANTY REGISTRATION...........................................................................................................44

3
Revision Number-001 01-01-2020 - Present
EZG Manufacturing 1-800-417-9272 www.ezgmfg.com
This symbol, either used alone or with a signal word, is used to call your attention
to instructions involving your safety and/or the safety of others. Failure to follow
these instructions will likely result in personal injury or death.
DANGER This signal word is used to identify a hazard which, if not avoided, will result in
death or serious injury.
WARNING This signal word is used to identify a hazard which, if not avoided, could result in
death or serious injury.
CAUTION This signal word is used to identify a hazard which, if not avoided, could result in
minor or moderate injury.
NOTICE
This signal word is used to identify a hazard which, if not avoided, could result in
property or equipment damage. It also may be used for special instructions
related to performance, maintenance or general items.
INTRODUCTION
Congratulations on purchasing one of the nest pieces of construction equipment on the market today!
If this is your rst EZG Manufacturing product, you will not be disappointed. If you have previously
owned an EZG Manufacturing product, you will nd the same high quality and dependability that you
have come to expect from EZG Manufacturing.
The purpose of this manual is to inform the owner/employer/and the operator, how to safely operate
this piece of equipment, and make them aware of any hazards. It also contains important information
regarding assembly, set up, operation, and maintenance. It is the Owner/Employer’s responsibility
to make sure that anyone who operates this machine understands all safety warnings. If you do not
understand any items in this manual, please contact the dealer where this product was purchased, or
the manufacturer at the number listed throughout this manual. If you have any suggestions about how
to make this manual easier to understand, contact the manufacturer. Keep this manual available for
reference wherever this piece of equipment is being used and make it available to any operators.
Illustrations in this manual may show details or components that may not be the same as your
machine. Continuing improvements to the design of this machine may have caused changes that are
not included in this manual. The information in this document is subject to change without notice.
The following safety symbols and signal words will be used throughout this manual and on the
product, for your safety and the safety of others, please become familiar with their meaning and heed
their warnings.
ABOUT THIS MANUAL
GENERAL INFORMATION
SAFETY INFORMATION

1-800-417-9272 www.ezgmfg.com
Revision Number-001 01-01-2020 - Present
4
WARNING
Failure to obey the following safety instructions could result in DEATH or
SERIOUS INJURY.
Read and understand this entire manual before operating the Fork-N-Hog Forklift.
For your safety and the safety of others, replace any missing or damaged warning decals by contact-
ing the manufacturer at 1-800-417-9272.
Make sure anyone operating the Fork-N-Hog Forklift is thoroughly familiar with its operation. Keep all
unauthorized and untrained personnel, especially children, away from operating the Fork-N-Hog.
Improper maintenance can be hazardous. Read and understand this section before you perform
any maintenance, service or repairs.
General Safety
•The Fork-N-Hog should only be lifted by qualified personnel.
•DO NOT lift the machine by the ROPS.
•DO NOT lift the machine from the bottom side using forks. Mechanical and electrical components
can be damaged from this lifting position.
•Never exceed the rated capacity of the piece of lifting equipment being used to lift the Fork-N-Hog.
•All rigging should be inspected per OSHA requirement.
•Never stand under a suspended load
SAFETY PRECAUTIONS

1-800-417-9272 www.ezgmfg.com
Revision Number-001 01-01-2020 - Present
4
WARNING
Failure to obey the following instructions could result in DEATH or
SERIOUS INJURY.
Use the nylon lifting strap and the three (3) rigging points provided with the Fork-N-Hog.
•Inspect lifting strap prior to use.
•Slide the seat forward prior to positioning the lifting strap.
•Rig one end of the strap through the cage (Figure 1) and hook to rigging point on the top of the
mast (Figure 2).
MACHINE LIFTING INSTRUCTIONS
Figure 1 Figure 2
•Loop the center point of the strap into the pin opening and replace the pin (Figure 3).
•Position the forks of the lifting machine above the cage and below the straps (Figure 4).
•Ensure that the sleeve is over top of the forks to prevent unnecessary wear to the strap when
lifted.
Figure 3 Figure 4

1-800-417-9272 www.ezgmfg.com
Revision Number-001 01-01-2020 - Present
4
WARNING
Failure to obey the following instructions could result in DEATH or
SERIOUS INJURY.
MACHINE LIFTING INSTRUCTIONS
Figure 5 Figure 6
•Begin to lift the machine until the straps have a slight amount of tension (Figure 5).
oStop and double check the correct positioning of the hook ends and the counterweight pin.
•Continue to lift the machine to the desired elevation (Figure 6).

1-800-417-9272 www.ezgmfg.com
Revision Number-001 01-01-2020 - Present
5 EZG Manufacturing
California - Proposition 65 Warning
Engine exhaust and some of its constituents, and some dust created by power sanding,
sawing, grinding, drilling, and other construction activities contains chemicals known to the
State of California to cause cancer, birth defects and other reproductive harm. Some examples
of these chemicals are:
Lead from lead based paints - Crystalline silica from bricks -Cement and other masonry
products -Arsenic and chromium from chemically treated lumber
Your risk from these exposures varies, depending on how often you do this type of work. To
reduce your exposure to these chemicals: ALWAYS work in a well ventilated area, and work
with approved safety equipment, such as dust masks that are specially designed to lter out
microscopic particles.
MACHINE DESCRIPTION
The 24-volt battery powered EZG Fork-N-Hog Forklift is unique in its shape, heavy-duty yet compact
carriage and ergonomic, comfortable operation. Designed for narrow passages and small operating
areas, the Fork-N-Hog can easily transport over one US ton of goods in small freight elevators, cargo
containers and enclosed trailers. With the special three-point drive designed framework, variable
wheelbase and the rear drive unit, the mini Fork-N-Hog has excellent stability and a 90 degree turning
angle capability.
Mast
Tilt / Lift Cylinders
Emergency Stop (Color Red)
Load Backrest
Brake Pedal
Accelerator Pedal Forks
Front Wheels
Chassis
Motor/Battery
Compartment
Drive & Steer Wheel
Counter Weight
Control Panel Console
Operator Cab
Hand Brake
Lights
Overhead Guard
Mast Control

6
Revision Number-001 01-01-2020 - Present
EZG Manufacturing 1-800-417-9272 www.ezgmfg.com
SPECIFICATIONS
Type Unit
Capacity of lift loading Q lb (kg)
Distance of load center C in (mm)
Lifting high h3 in (mm)
Free lifting high* h2 in (mm)
Length of the fork b3 in (mm)
Displacement to side of the fork* b2 in (mm)
Type of lifting
Lifting speed m/min
Lowering speed
Tilt of lift mast ~ forward/backward <
Height of mast h1 in (mm)
Height of mast extended h4 in (mm)
Height of overhead guard h5 in (mm)
Height of seat from floor h6 in (mm)
Length of the fork back to truck rear L2 in (mm)
Width of carriage B in (mm)
Distance between wheel bases
Distance between wheels
Height of truck body from floor Yin (mm)
Turning radius Wa in (mm)
Type of steering
Type of drive
Driving speeds (with load/without) mile(km)/h
Speed control
Gradeability %
Driving brake
Stopping brake
Battery 24V
Weight of battery
Weight of truck (include battery) lb (kg)
Driving motor - Compound wound dynamo
Lifting motor - Shunt wound dynamo kw
Wheels (front/rear)
Dimensions of front wheels (2) mm
Dimensions of driving wheels (rear) (1) mm
Table 1 The Main Technical Parameters
Note: 1. The type of the items with * can be chosen according to the demand of the customer.
2. The producer reserves the right to modify the above parameter.
FNH9
2,200 (1000)
16[20*] (400{500*])
126 (3,200)
63 (1,600)
32[39*] (800[1000*])
Left/right 4 (100)
Hydraulic-electronically controlled
>5
m
Adjustable type
2°/5°
75 (1,900)
142 (3,600)
75 (1,900)
33 (850)
50 (1,260)
32 (800)
35~41 (900~1,030)
26 (660)
4 (90)
49 (1,240)
Steering wheel mechanical
Wheel electronically controlled
4.3 (7.0) /6.0
Stepless adjustable system
8
The drum brakes in the
front wheel hubs
The hand brake Mechanical
D-385
858 (390)
3,410 (1,550)
2
2.8
Solid tires
φ267×127×165
φ267×127×165
in (mm)
in (mm)
kw

1-800-417-9272 www.ezgmfg.com
Revision Number-001 01-01-2020 - Present
7
Before starting work, check the brakes, steering wheel, tires, horn, hydraulic system, battery
capacity, etc. to ensure proper that they are working properly.
•Never use the forklift if you have not been specifically trained and authorized to do so.
•Read the data carefully about the Forklift capacity, the load weight, and the load curve.
Never exceed the load capacities specified on the data plate.
•Never drive the Forklift with wet or greasy hands or shoes.
• Do not install other implements around the head guards or the carriage that restrict
operation or visibility.
•Buckle seat belt prior to operating forklift.
•Never activate control levers if you do not know their purpose. Activate controls only
correctly seated in the driver seat and facing straight and level.
•Never drive over electric cables or hoses unless they are appropriately protected.
•Never drive over soft surfaces, uneven ground, any openings above 2” (5cm). Also never
drive over platforms or scaffolds that are not sufficiently safe considering the total weight
of the Forklift and the payload.
•While driving the Forklift, you should always maintain the correct driving position. Never
stick your legs outside the Forklift and never put your hands and feet between the moving
parts of the lift.
•While loading goods, be sure to check the quality of the pallets, never put the goods on
damaged pallets.
•Avoid starting suddenly, sharp braking, reversing, and changing direction suddenly as the
Forklift may tip over to the front or the side.
•If the Forklift tips over, remain seated, grasp the steering wheel tightly, keep your body in
the center of the Forklift as much as possible to avoid being trapped under the machine.
•Keep battery charged, periodically checking to ensure the level of the electrolyte and the
density of the electrolyte match. Never add liquid.
•Keep each part of your Forklift lubricated and the external appearance of your Forklift
clean.
•Check that wheel nuts and all other connecting hardware is properly secured.
•Check that the brake system is in good operational condition.
•Do not turn the steering wheel when the Forklift is stopped and unloaded to avoid excess
stress on the steering system.
•Park the Forklift on firm, flat ground and set the hand brake on when the Forklift is
stopped.
OPERATING SAFETY

8
Revision Number-001 01-01-2020 - Present
EZG Manufacturing 1-800-417-9272 www.ezgmfg.com
PRE-START CHECKS / ADJUSTMENTS
Adjustment of the Seat
The driver seat can be adjusted to several positions in front or back for optimal driving comfort. To adjust
seat position, press the adjustment lever under the seat (not shown), pull the seat to the appropriate posi-
tion, forward or back, and when adjusted to the appropriate position, release the lever and attempt to
physically push the seat forward and backward to ensure that it is locked in place. The adjustment of the
seat is complete.
NOTE: Adjust the seat only when the the Forklift is turned off. Ensure the seat is locked in place
Warning: Before adjusting the rake of the steering wheel, you should park the Forklift and apply the
hand brake.
Adjustment of the Vertical Tilt of the Steering Wheel
The rake of the steering wheel can be adjusted to personal operation habit. To adjust the rake of the steering
wheel, use the method described below:
Loosen the locknut connecting the carriage under the steering column with the wrench and push the steering
column forward or pull the steering column backward lightly. Position the steering wheel as required and
then re-tighten locknut.
Fig 2
1. The hand brake
2. The steering column locknut
1 The steering column locknut.
2 The brake pedal.
3 The accelerator pedal

1-800-417-9272 www.ezgmfg.com
Revision Number-001 01-01-2020 - Present
9
START/STOP PROCEDURE
1
2
3
4
5
6
7
Speed Selection Switch
Direction (Reverse/Forward) Lever
Emergency Stop Switch
Battery Capacity Meter
Horn Button
Light switch
Starting switch
Console “A”
Starting & Stopping the Machine
To start the FNH, insert the key in the Starting Switch (7) switch and turn it to the
right. Turn the Emergency Stop Switch (3) in a clockwise direction to reset (out
position). This activates the control system. (Consoles “A” and “B” are shown as
references)
To stop the Forklift, take your right foot o the accelerator pedal. Press the brake
pedal until the Forklift has come to a complete stop. Completely lower the forks and
apply the parking brake (hand brake) and remove the key from the switch.
Battery Capacity Display
The Battery Capacity Meter can indicate the battery capacity level and shows the total operating time
(total hours) on the battery. Check to see that the battery has sufficient capacity for operation.
FNH Forklift Operation
Once the FNH is started:
• Lift the Forks about 4 inches (10 cm) from the oor.
• Release the Hand Brake (Figure 4 – 1).
• Place the Direction Lever (Figure 1 - 2) in the required direction (forward/reverse).
• Use the Speed Selection Switch (Figure 1 - 1) to select the desired operating speed of Slow
(tortoise) or Fast (rabbit).
• Press the Accelerator Pedal (Figure 2 – 3) slowly until the required speed is reached,
Fig.1 - The Fork-N-Hog Forklift Console “B”
Important notice:
If you lose control of the Forklift during any kind of maneuver, press the red Emergency Stop (3
button on the right-hand side of the seat immediately to stop all operating power.
When turning the Forklift, you should slow down as turning at fast speeds is dangerous.
The power gradeability of the electric FNH is 8%. When starting on an uphill slope, place the Speed
Selection Switch in the slow (tortoise) position and fully engage the accelerator pedal of the Forklift to
acquire the maximal gradeability.

10
Revision Number-001 01-01-2020 - Present
EZG Manufacturing 1-800-417-9272 www.ezgmfg.com
In the case of downhill slope, release the accelerator pedal to obtain reverse current braking. If reverse
current braking cannot control the speed of downhill slope (the downhill slope speed is too fast), the brake
pedal should be pressed at this time to slow the Forklift.
Warning: Never leave the Forklift before applying the parking brake (hand brake.
Directional Lever (Forward / Reverse
To change direction, use the Direction Lever on the console (as shown in the fig.1 - 2). Push the lever
forward so the Forklift moves forward and pull the lever back to move the Forklift backward. Allow the Forklift
to stop between shifting.
Accelerator Pedal
Be aware of the Forward/Reverse selection. Press the accelerator pedal (fig. 2 - 3) slowly with your right
foot for the Forklift to move forward or backward.
Warning: Never press the accelerator pedal with excess force to avoid the Forklift getting out of
control resulting in an accident.
The Foot Brake Pedal
To stop the Forklift, take your right foot off the accelerator pedal, and press the brake pedal (fig. 2)
until the Forklift has completely stopped.
Do not press the accelerator pedal and the brake pedal at the same time as that will burn out the
electric component.
The Emergency Stop Switch Button
If the Forklift suddenly gets out of control, you smell/see any fumes or any other potentially dangerous
conditions, immediately press the red Emergency Stop Switch on the console to immediately cut off the power.
Only after examining and correcting the unsafe condition should you turn on the Forklift. To turn on the
Forklift rotate the red Safety Switch in a clockwise direction lightly until the button springs up and resets.
Warning: Never turn on the power if you have not found the cause of the problem.
Do not use excess force on the red Emergency Switch to avoid possible damage.
The Horn and the Reversing Buzzer
For driving the Forklift safely, the Forklift is equipped with a horn (Fig. 1 – 5) and a backup alarm
reversing buzzer. The Horn Button on the console. Press it lightly to sound the horn. The Backup Alarm
Buzzer is actuated when the Direction Lever is moved into the reverse direction.
START/STOP PROCEDURE

1-800-417-9272 www.ezgmfg.com
Revision Number-001 01-01-2020 - Present
11
START/STOP PROCEDURE
Forklifting Operation
A three-lever single-body hydraulic value controls the hydraulic system to activate the related parts. The
functions of the hydraulic control distributor levers are:
b) Stop fork c) Lowering fork forwards
c) Tilt forwards
1) Lifting lever:
a) Lift fork
2) Tilting lever:
a) Tilt backwards b) Stop position
3) Side shift lever:
a) Move forks left b) Stop position c) Move forks right
Fig.3 - The Hydraulic Control Levers Hydraulic Control Levers
3-directional Systems 2-Directional Systems
HANDLING THE LOAD
Adjust the tilt fork position to level the forks before lifting a load. Place the forks as far under the load as
possible. Center the weight of the load between the forks. You can adjust the fork width as needed. Tilt the
mast back to stabilize the load.
Off-center loads, overloading, and loading damaged or loose loads, and driving at excess speeds are
the primary causes of unsafe, unstable loads that lead to accidents. Here are the steps you need to
take to ensure a stable load and safe forklift load capacity for any forklift task
•Secure the load so it is stable and can’t move around. Don’t try to pick up damaged loads unless it has
been secured by wrapping or banding.
•Ensure the load is as centered as possible on the forklift. When it is impossible to avoid carrying an off-
center load, arrange it so the heaviest part is nearest to the front wheels. For more informa-tion on safe,
centered loads, consult OSHA’s online forklift load calculator. This forklift load capac-ity resource
should only be used whenever the manufacturer’s recommended max load figures aren’t available. Always
consult with your safety supervisor for unusual heavy load forklift transport.
•Do not exceed the capacity of your forklift.
Approaching a Load
•Approach the load carefully and slowly. Tip-overs often occur when the driver is moving too fast.
•Ensure the forklift is directly in front of the load and is centered to it, so the forks are at the correct
height.
• Set the direction control to neutral.
•Only raise the forks if the forklift is stopped and the brake is set.
•Before picking up the load, ensure your overhead is clear.

12
Revision Number-001 01-01-2020 - Present
EZG Manufacturing 1-800-417-9272 www.ezgmfg.com
Adjusting the Mast Position to Ensure a Stable Load
•Do not tilt forward with a load with the forks elevated except when picking up a load. When stacking a
load, tilt the mast backward just enough to stabilize it.
•When working with a maximum capacity load, tilt the mast backward and position the load so the heaviest
part is against the carriage.
•Move the forklift with the mast tilted back.
•When you are ready to stack the load, tilt the mast forward very slowly, and never travel with the mast
tilted forward.
Adjusting the Fork Positions
•Level the forks before lifting a load.
•Place the forks as far under the load as possible.
•Center the weight of the load between the forks. Adjust forks manually or with a fork positioner.
•Tilt the mast back to stabilize the load.
Lifting the Load
•Ensure there is adequate overhead clearance before lifting the load.
•Slowly lift the load and tilt the mast backward slightly to stabilize it.
• Slowly return the lift control to the neutral position.
Lowering the Load
• Ensure the load is secure.
•Tilt the mast back carefully to stabilize the load.
•Slowly move the forklift away from the stack.
•Stop the truck and return the mast to the vertical position before lowering the load.
•Lower the load so that the lowest point is 6-8 inches (15-20 cm) from the floor.
START/STOP PROCEDURE

1-800-417-9272 www.ezgmfg.com
Revision Number-001 01-01-2020 - Present
13
SERVICE & MAINTENANCE
Note: Before carrying out any repair, inspection, or maintenance operations, check that you have applied the
parking brake, lowered the forks to floor level and removed the key from the switch. Always pull the plug out
of the battery before carrying out any operations on the electrical system.
For general cleaning of the Forklift, use dry air and damp rags; never use pressure washing, solvents, or
gasoline to avoid damage to Forklift components equipment.
Maintenance and inspection should be carried every 10 hours. If the Forklift is used frequently, the interval of
maintenance must be shortened.
Warning: The inspection, maintenance, adjustment and repair operations must be carried out by
qualified and authorized personnel only.
Connect the battery only when necessary for testing.
Take all the necessary precautions and other measures when carrying out any maintenance, adjustment,
repair & inspection and when the drive wheel is raised o the ground.
The Usage and Maintain of the Storage Battery
The safety rules of the battery
Remember that the battery generates gases that may cause it to explode on contact with ames or sparks.
(1) Connections must be coated with anti-acid grease or neutral Vaseline.
(2) Do not tap current from the battery with plugs or clips for makeshift contacts.
(3) Check whether the plastic protections of the connections are positioned correctly.
(4) No smoking should be allowed when repairing a battery or while it is charging.
(5) Never rest tools or metal parts on the battery.
(6) Keep the metal cowling of the batteries clean and dry.
Checking the electrolyte in the battery
The most important thing to be carried out on the battery is measurement of the density of the electrolyte as this indi-
cates the state of the charge.
The density of the electrolyte is measured with a density meter by inserting this in the element to be measured and
tapping a sucient quantity of electrolyte to bring the oat to the surface. Read the value from the specic weight piece
in the density meter. The density of a completely charged element is around 1:1.27~1:1.28 at 20~25°C. Density drops
as the battery runs down. Running down of the battery must be interrupted when the density of the electrolyte reaches
1:1.25. If the temperature of the electrolyte is other than 25°C when the check is made, the value drops by approx. 7g/l
for an increase of 10°C.
Top up the electrolyte
The electrolyte used in lead batteries is a solution of sulfuric acid in distilled or demineralized water.
A drop in the level of the solution in the elements is normal. This is caused partly by evaporation and partly by the elec-
trolysis that occurs during the nal charging phase. One of the most important maintenance operations on the battery is
therefore topping up of the water to keep the level of the solution required. Follow the rules indicated below:
• Always use distilled or demineralized water.
• Keep the level approx. 10mm slightly above the element.
• Do not use tap water or pure water.
• Do not overll, avoid spilling of the acid that causes reduction of element capacity.

14
Revision Number-001 01-01-2020 - Present
EZG Manufacturing 1-800-417-9272 www.ezgmfg.com
SERVICE & MAINTENANCE
Charging the Battery
• Open the plug of each element.
• Check the level of the electrolyte. If the level is under the standard value, you must charge the battery.
• Insert the plug of the battery into the battery charger socket. Do not insert the plug of the charger into
the electric appliances control plank socket.
• Start charging the battery.
• After recharging, check the level of the electrolyte.
• After 250 hours of usage of the battery, check the tightness of the terminals and protect with anti-acid
grease or neutral Vaseline.
Replace the Battery
Because the battery installed in the Forklift is welded, when replacing the battery, you should use the hook to lift out the
battery and the metal box. Insert the new battery and connect the electrical wire. The battery is ready to be used.
The method above can also be used in the enterprise for continuous work. The spare battery and the battery within the
Forklift can be used alternatively, charging the spare battery outside while the Forklift battery is being used.
The Motor
The driving motor and the lifting motor are all direct current dynamos that make up of stator and rotor. The
commutators on rotor conduct electricity by friction with the carbon brash, so carbon or copper powders
are produced when used for a long time. Suggest that you blow clean compressed air onto the commutator
to remove any dust and the carbon or copper powder after a period of time. At the same time, inspect and
check the roughness of the commutators and the protrusions between the blades.
If there are any spots of rust on the commutator, clean the armature with ne grain emery paper. If there
are obvious signs of abrasion or scratches on the commutator and the mica between the blades have come
to the surface, rotor must be taken out and re-machined on the lathe and scrape its entire surface to lower
the mica. This process needs to be done by an expert personnel with appropriate tools to lower the mica, to
deburr the corners of the blades and smooth the commutator.
Inspect and check periodically to ensure they are evenly worn out without any signs of abrasion or scratch-
es and the brushes are free inside their housing. When replacing the brushes, follow the instructions of the
“Parts Catalog”. After replacement, attach the brushes so that they adhere completely to the commutator.
Inspect and check periodically to ensure they are evenly worn out without any signs of abrasion or scratch-
es and the brushes are free inside their housing. When replacing the brushes, follow the instructions of the
“Parts Catalog”. After replacement, attach the brushes so that they adhere completely to the commutator.
After attaching new brushes, remove any carbon dust between the blades of the commutator with dry com-
pressed air.
If the motor of the Forklift makes an unusual noise when operating, you should inspect and replace the
bearings.
Typical Electrical Motor

1-800-417-9272 www.ezgmfg.com
Revision Number-001 01-01-2020 - Present
15
SERVICE & MAINTENANCE
ELECTRIC SYSTEM PRINCIPLE DIAGRAM
M1 model 1 low speed m1 Compound wound dynamo motor
M2 model 2 high speed m2 oil pump motor
A forward V1 inching switch for liing
B reverse V2 inching switch for tilt
5KΩ regulating speed potentiometer V3 inching switch for sideshi
K1 key switch W horn
K2 locking for the other circuits N1 horn button
A1,A2 the armature T1 big pilot light in front
S1,S2 magnetic eld P1 fuse (100A)
Z1 main contactor P2 fuse (20A)
ZS1 main contactor coil P3 fuse (20A)
Z2 pump motor contactor J1 relay for the pilot light in front and back
ZS2 pump motor contactor coil Js relay coil

16
Revision Number-001 01-01-2020 - Present
EZG Manufacturing 1-800-417-9272 www.ezgmfg.com
SERVICE & MAINTENANCE
The electrical control system
The electrical control system adopts the Compound Wound Dynamo mainboard of 1243 type that the
American CURTIS produces. All control functions are carried out logically by the microprocessor. According to MOS
technology at high frequency and the valid control of the microprocessors, the system has the following
characteristics:
•Snuer of the coils of the contactors inside the logic, assuring absence of arcs on the contacts of these.
•A microprocessor supports the EEPROM that makes it possible to modify, within a prexed range, some of the
adjustment parameters using an external console.
•Have the protective function when open circuit and short circuit happens.
•Diagnostics with output of the type of fault by means of the external console. Logging of the last 5 alarms with
related electric current value and temperature that can be displayed from the console.
•Programming of the controller can improve response at low speeds.
• A tight container is also mounted to assure optimal protection against splashing and against dust, chip, or small
objects.
Warning: Do not connect the anode and the cathode of the battery to the wrong conjunction bolt of controller,
and do not insert the plug of the charger into the electric appliances control plank socket that will burn out
the controller.
The Meter for Examining Malfunction (table 2
The state LED has been installed on controllers 1243 and can be seen from the window of the label on top of the-
controller. When the controller or the input of the controllers is out of order, the state LED will show the malfunction
code. When the operation process is in order, the state LED will be stable. If the controller has encounted a fault,
the two-digital indication code of the fault will ash continuously until the fault is corrected. For example, the fault
code”3,2” indicates that the main conductor is in touch with other. Show as:
Table 2 The state LED and the malfunction code
LED Code Explain
All light o ■■■■■■■■■ The source or controllers are bad
All light on ¤ ¤ ¤ ¤ ¤ ¤ ¤ ¤ ¤ Controller or microprocessor breakdown
0,1 ■ ¤ The controller work; No breakdown
1,1 ¤ ¤ The sensor of the electric current break- down
1,2 ¤ ¤ ¤ The hardware breakdown
1,3 ¤ ¤ ¤ ¤ the breakdown in the M- or electrical engineering output
1,4 ¤ ¤ ¤ ¤ ¤ The SRO break down
2,1 ¤ ¤ ¤ The accelerator breakdown
2,2 ¤ ¤ ¤ ¤ The breakdown in the emergent reverse check electro circuit
2,3 ¤ ¤ ¤ ¤¤ The high pedal (HPD) breakdown
2,4 ¤ ¤ ¤ ¤ ¤ ¤ The breakdown in the low import of the accelerator
3,1 ¤ ¤ ¤ ¤ The overflow in the driver of the contactor or the short circuit of excitation coil
3,2 ¤ ¤ ¤ ¤ ¤ The adhesive connection of the main contact
3,3 ¤ ¤ ¤ ¤ ¤ ¤ The open circuit of the coil circuit
3,4 ¤ ¤ ¤ ¤ ¤ ¤ ¤ No contact for the contactor
4,1 ¤ ¤ ¤ ¤ ¤ The battery electric voltage is low
4,2 ¤ ¤ ¤ ¤ ¤ ¤ Over press
4,3 ¤ ¤ ¤ ¤ ¤ ¤ ¤ Cutting off owing to the overheat/ overcool
4,4 ¤ ¤ ¤ ¤ ¤ ¤ ¤ ¤ The breakdown in anti-moor

1-800-417-9272 www.ezgmfg.com
Revision Number-001 01-01-2020 - Present
17
SERVICE & MAINTENANCE
THE HYDRAULIC LIFTING SYSTEM
Each lever controls one hydraulic system only. The position of the control lever, distribution of hydraulic line
will control the dierent speeds. With the manipulating lever activated, the supplementary dynamoelectric
switch activates the oil pump motor which starts to turn synchronously, to export the hydraulic oil, and allows
movement of the related hydraulic parts. In order to ensure the pressure safety of the hydraulic system, the
pressure overow device is installed on the hydraulic valve. Once the pressure exceeds the safety value, the
pressure overow valve will overow to unload automatically
Notice: Do not adjust the pressure unit on the hydraulic valve at your discretion.
The Lifting System
The lifting unit consists of a xed upright and a mobile upright for the dynamoelectric counterweight Forklift
of series of CPD-F type. The mobile upright can move up and down by means of stretching and shrinking the
cylinder. The high strength forged steel forks slides on the mobile upright by means of the traction of the high
tensile strength chain to load and unload the goods safely. (Fig.4)
The Hydraulic Cylinders
The dynamoelectric counterweight Forklift of series of CPD-F type has common type and standard type. The
common type is tted with two lift cylinders outside the xed upright while the standard type is additionally
equipped with a third central cylinder that can be used inside the container. All cylinders are plunger type
cylinders.
There is a double acting plunger type cylinders that is used to tilt the uprights in the bottom of the uprights.
The Forklift is also equipped with a safety valve in the hydraulic circuit of the lift cylinder to slow the downward
speed of the mobile upright that ensures the safety downward movement.
There is a one-way throttle valve at the rear of oil exit of the tilt cylinder. With the appropriate regulating it can
choose the tilt speed.
Fig.4 - The Hydraulic Lifting System
1. The fixed upright
2. The mobile upright
3. The forks holder plate
4. The lift cylinders
5. The central cylinder
6. The lifting chains

18
Revision Number-001 01-01-2020 - Present
EZG Manufacturing 1-800-417-9272 www.ezgmfg.com
SERVICE & MAINTENANCE
9.4 Hydraulic pump station
The hydraulic pump station is made up of a motor, pump, oil tank and so on. After the Forklift is used for one year,
the oil should be replaced. Replacement could be done as follows:
•Park the Forklift on a at surface.
•Bring the forks to the lowest position in order for the oil to circulate back to the tank.
•Loosen the lock screws of the footrest and remove the footrest.
•Put the oil dish in the bottom of the oil tank and loosen the sucking oil pipeline to let o the oil.
•Take out the mesh lter from the oil tank and clean it with kerosene.
•Fit the mesh lter on the oil tank and connect the sucking oil pipeline.
•Using the funnel with a mesh lter, pour in oil to about 80% of the oil tank height.
•Reconnect the ller plug and footrest.
9.5 Forks and Forks holder plate
The forks holder plate slide on the holder plate to make the forks move up and down. The lift forks holder plate
should be checked to inspect if the limit screws on the two sides are operating appropriately. If the limit screws
are too tight, the forks holder plate cannot slide freely. If too loose, the forks holder plate will shake. The forks
should be checked after 500 hours of usage. Any faulty forks must be taken out of service immediately and
cannot be used again until they have been repaired or replaced.
The fence must be xed after the forks are tted on the lift forks holder plate. If not, the forks that slide from
the two sides of the forks holder plate can lead to malfunctioning.
If the fork thickness has been reduced to 90% of the original thickness due to wear, you must stop using them
and need to be replaced immediately.
9.6 The Lifting Chain
As there are no xed rules as regards to the frequency and checking of the chains. If there is a lot of dusts on
the chains, the chain should be cleaned and re-lubricated. In the normal case, after having worked for 1000
hours, the chains should be removed and washed, check wear & tear of the chain and measure elongation. If
the chains have a lot of wear and elongation exceeds 2%, the chains must be replaced. Replace coupling pin,
coupling screw together with their respective nuts when replacing the chains. The chains should be
re-lubricated after cleaning and replacing the chains.
This manual suits for next models
1
Table of contents
Other EZG Forklift manuals
Popular Forklift manuals by other brands

Hyster
Hyster A1.3XNT Service manual

LoadSurfer
LoadSurfer WH20L-65 Operate manual & Parts manual

AUSA
AUSA CH 200 Operator's manual

SWEDMACH
SWEDMACH Liftwell 22 Instruction manual & Spare parts catalogue
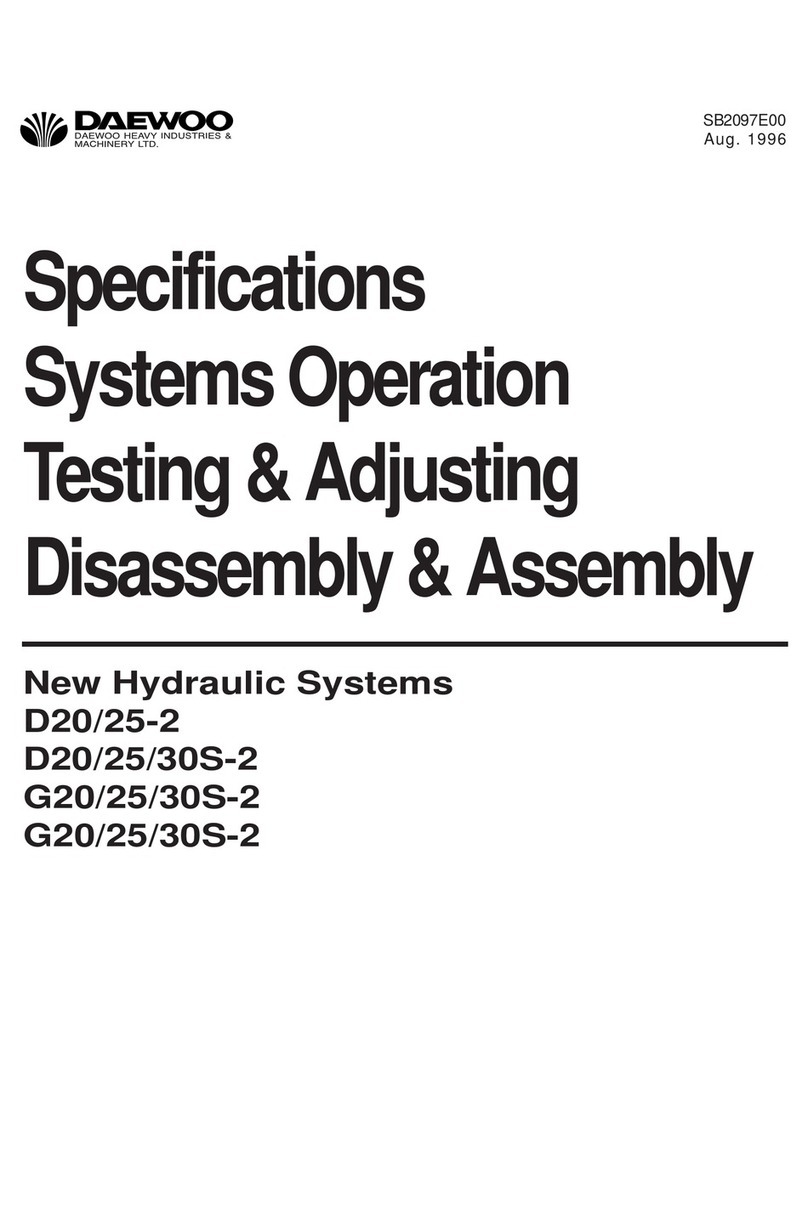
Daewoo
Daewoo D20S-2 Specifications Systems Operation Testing & Adjusting Disassembly & Assembly

Gradall
Gradall XL4000 manual