Fullwood Packo FullClean Plus User manual

Fullwood Packo FullClean Plus
Instructions for Use
Document Number:
006614
Revision Number:
D
Date of Issue:
14/08/2020

Copyright © 2020, Fullwood Packo. The contents of this document are the copyright of
the publisher and may not be reproduced (even extracts) unless permission is granted.
Fullwood Packo has taken every precaution to avoid errors and omissions of the
information contained in this document but does not accept any responsibility or liability
for damage of any kind arising from the use of the information contained herein. Fullwood
Packo reserves the right to make changes to the manual at any time and without prior
notice.
Original language of the manual is British English.

Doc No:
006614
Fullwood Packo FullClean Plus
Revision:
D
Date:
14/08/2020
Page 1of 58
Revision Control
Revision
Date
Details of Change
A
04/2011
Pages 31
B
09/2011
Pages 45, Writer: GIK.
Completely revised.
Removed references to the Fusion UPS, since this is no
longer an option; there is now a lithium back-up battery on
the PCB itself.
C
10/2015
Pages 57, Writer: BC/Checked: MvdD.
New template + corrections
D
03/07/2020
Document rebranded.
Based upon the newest PCB version 181.104.06/E Based upon the following firmware
versions:
•FCC –GB/CS/P 1.04
•FCC –NL/F/D 1.04
•FTT –1.05

Doc No:
006614
Fullwood Packo FullClean Plus
Revision:
D
Date:
14/08/2020
Page 2of 58
Contents
1. Introduction.........................................................................................................5
2. Scope .................................................................................................................5
3. Glossary .............................................................................................................5
4. Icons Used in this Manual...................................................................................6
5. Safety.................................................................................................................7
6. General and Features.........................................................................................9
6.1. FullClean Plus Feature Listing............................................................................9
6.2. The FullClean Plus Operational Modes.............................................................10
6.2.1. Operation Mode................................................................................................10
6.2.2. Adjust Mode......................................................................................................10
6.3. The FullClean Plus Cleaning Possibilities.........................................................10
6.3.1. Circulation Cleaning..........................................................................................10
6.3.2. Heat Based Cleaning........................................................................................10
7. Firmware Versions............................................................................................11
7.1. Firmware for the FullClean Plus, covered by this Manual..................................11
7.2. Firmware NOT covered by this Manual.............................................................11
8. Hardware description........................................................................................12
8.1. The User Interface............................................................................................12
8.2. The FullClean Plus Circuit Board......................................................................13
8.2.1. Connectors.......................................................................................................13
8.2.1.1. (X1A t/m X1D) I1...I4.........................................................................................13
8.2.1.2. (X2) 4-20 mA ....................................................................................................13
8.2.1.3. (X3) PT 100......................................................................................................13
8.2.1.4. (X4 a/b).............................................................................................................13
8.2.1.5. (X5) Expansion.................................................................................................14
8.2.1.6. (X6) FTT...........................................................................................................14
8.2.1.7. (X7) 01-04.........................................................................................................14
8.2.1.8. (X8...X15) 05...012............................................................................................14
8.2.1.9. (X17) Alarm ......................................................................................................14
8.2.1.10. (X18 A/B) 24 V..................................................................................................14
8.2.1.11. (X19) Mains (not applicable for 24 V powered models!)....................................15
8.2.1.12. (X20) 1-4 CMN..................................................................................................15
8.2.2. Fuses................................................................................................................15
8.2.3. Switches...........................................................................................................15
8.2.4. Jumpers............................................................................................................15

Doc No:
006614
Fullwood Packo FullClean Plus
Revision:
D
Date:
14/08/2020
Page 3of 58
8.2.5. LEDs.................................................................................................................15
8.2.6. Important ICs....................................................................................................16
9. Hardware Installation and Wiring......................................................................16
9.1. General Installation Information ........................................................................16
9.2. Relay Contact Protection..................................................................................17
9.3. Circulation Cleaning Installation........................................................................18
9.4. Boiling Water Cleaning Installation....................................................................19
9.5. Closed Water-Circuit Cleaning Installation........................................................21
10. User Operation .................................................................................................24
10.1. The Operation Modes.......................................................................................24
10.1.1. Standby Mode...................................................................................................25
10.1.2. Milk Mode.........................................................................................................26
10.1.3. Automatic Cleaning Mode.................................................................................26
10.1.3.1. Errors................................................................................................................27
10.1.3.2. Power failure.....................................................................................................27
10.1.3.3. Alarm notifications ............................................................................................27
10.1.4. Manual Clean Mode..........................................................................................28
10.1.5. Info Mode..........................................................................................................29
10.1.6. User Setting Mode............................................................................................31
11. User Trouble Shooting......................................................................................33
12. Technical Operation..........................................................................................34
12.1. Adjust Mode......................................................................................................34
12.1.1. How to Enter Adjust Mode ................................................................................35
12.1.2. First Time Settings - Full Reset.........................................................................35
12.1.3. Handling Main Menu Items ...............................................................................36
12.1.4. Handling Sub Menu Items.................................................................................38
12.1.5. Options and Settings of the Heat Based Cleaning System................................40
12.1.6. Options and Settings of the Circulation Based Cleaning System.......................45
12.2. Internal Diagnostics ..........................................................................................55
13. Technical Trouble Shooting ..............................................................................56
14. Disclaimers.......................................................................................................57
Tables
Table 1 Glossary of Terms ..............................................................................................5
Table 2 Icons...................................................................................................................6
Table 3 Operation modes..............................................................................................24

Doc No:
006614
Fullwood Packo FullClean Plus
Revision:
D
Date:
14/08/2020
Page 4of 58
Table 4 Available User Settings.....................................................................................31
Table 5 FullClean 1.04 GB/CZ/P Heat Based Cleaning System ....................................40
Table 6 Heat Based Cleaning System...........................................................................44
Table 7 Diagnostic Codes..............................................................................................55
Table 8 Service list........................................................................................................56
Figures
Figure 1 The Control Panel of the FullClean Plus Enclosure...........................................12
Figure 2 The FullClean Plus Main PCB with its Main Components.................................13
Figure 3 General Wiring and Settings of the FullClean Plus Controller ...........................16
Figure 4 Examples of Relay Contact Protection..............................................................17
Figure 5 Circulation Cleaning System Flow Diagram......................................................18
Figure 6 Circulation Cleaning System Wiring Schedule ..................................................19
Figure 7 Boiling Water Cleaning System Flow Diagram..................................................20
Figure 8 Boiling Water Cleaning System Wiring Schedule..............................................21
Figure 9 Closed Circuit Washing System Flow Diagram.................................................22
Figure 10 Closed Circuit Washing System Wiring Schedule .............................................23
Figure 11 Legend; Example of LEDs and Display Readings.............................................24
Figure 12 Display & LEDs in Standby Mode .....................................................................25
Figure 13 Arrangement of the Keys on the Front ..............................................................25
Figure 14 Display & LEDs in Milking Mode .......................................................................26
Figure 15 Display & LEDs during the Cleaning Mode .......................................................27
Figure 16 Alarm Warning; Display & LEDs within 5 Minutes after the Occurrence of an
Error During Cleaning .........................................................................................................28
Figure 17 Display & LEDs after finishing a “Special Cleaning Phase” (manual- or
emergency).........................................................................................................................28
Figure 18 Display & LEDs during the Manual Cleaning Mode...........................................28
Figure 19 Display & LEDs during the Manual Cleaning Mode...........................................30
Figure 20 Display & LEDs during the User Setting Mode..................................................31
Figure 21 Position of Function Switch 8............................................................................35
Figure 22 Simplified Menu Structure; Main Menu “General” shown with Sub Menu and
Parameter Items Extended..................................................................................................36
Figure 23 Main Menu........................................................................................................36
Figure 24 Sub Menu.........................................................................................................38
Figure 25 Fullclean Display in Diagnostics Mode..............................................................55

Doc No:
006614
Fullwood Packo FullClean Plus
Revision:
D
Date:
14/08/2020
Page 5of 58
1. Introduction
Fullwood Packo thanks you for choosing one of our smart milking and cooling solutions.
The farmer and their herd are at the heart of everything we do. That is why we are constantly
pushing the boundaries of what is possible, to deliver cutting-edge technologies that will
significantly improvethe lives of our farmers, health of their herds and provide maximumsafety
and efficiency on farm.
Whilst Fullwood Packo equipment will comply with all relevant directives, customers are
reminded that all equipment into which Fullwood Packo equipment is to be incorporated must
comply with all applicable European directives.
2. Scope
This document provides an overview of the Fullwood Packo FullClean Plus system.
It covers the safety aspects; including system safety and operational safety, technical
information regarding the equipment, descriptive information on the firmware and hardware
within the system, operation of the system (user and technical) and additional information
regarding trouble shooting.
3. Glossary
Table 1 Glossary of Terms
Acronym / Abbreviation
or Term
Definition
A
Amps
AC
Alternating Current
CZ
Czech
DC
Direct Current
DC
German
EEPROM
Electrically Erasable Programmable Read-Only Memory
EN
English
F
French
FCC
FullClean Controller
FTT
Fusion Tiny Terminal
LCD
Liquid Crystal Display
LED
Light Emitting Diode
mA
Milliampere
min
Minute(s)
NL
Dutch
PCB
Printed Circuit Board
PL
Polish
PPE
Personal Protective Equipment

Doc No:
006614
Fullwood Packo FullClean Plus
Revision:
D
Date:
14/08/2020
Page 6of 58
Acronym / Abbreviation
or Term
Definition
RAM
Random Access Memory
RTC
Real Clock Time
TVS
Transient Voltage Suppressor
UK
United Kingdom
V
Volts
VDR
Voltage Dependent Resistor
Ω
Ohm
4. Icons Used in this Manual
A number of icons are used in this manual, to draw your attention to, for example, safety
information. Table 2 provides an overview of the icons used and what they mean.
Table 2 Icons
Icon
Meaning
Description
Warning
A warning draws your attention to a
possible danger or risk of personal
injury.
Caution
If you do not follow the directions
precisely, then:
The system can be damaged (in this
case, damage is not covered by the
warranty). The quality of the milk can be
affected.
Note
A remark provides additional information
about a certain topic. The information in
a remark is not invaluable, but can be
useful.

Doc No:
006614
Fullwood Packo FullClean Plus
Revision:
D
Date:
14/08/2020
Page 7of 58
5. Safety
A risk assessment is an important step in protecting your workers and your business, as well
as complying with the law. It helps you focus on the risks that really matter in your
workplace - the ones with the potential to cause real harm. In many instances, straightforward
measures can readily control risks, for example ensuring spillages are cleaned up promptly
so people do not slip, or cupboard drawers are kept closed to ensure people do not trip. For
most, that means simple, cheap and effective measures to ensure your most valuable asset -
your workforce - is protected.
The law does not expect you to eliminate all risk, but you are required to protect people as far
as “reasonably practicable”.
•There are many work situations which add to the hazards of welding. Each must be
assessed carefully, since there may be added hazards such as falls or asphyxiation
•The employer should make a critical assessment of the work to be done, and how it
may be carried out safely
•Lifting and manual handling is one of the highest risks in work environments. It is
essential to inform your staff about safe lifting and manual handling basics
•Some form of dust extraction is also beneficial as exposure to airborne particles can
cause respiratory complaints
•The main requirement of the PPE at Work Regulations 2002 is that personal
protective equipment is to be supplied and used at work wherever there are risks to
health and safety that cannot be adequately controlled in other ways
•Power tools can be extremely dangerous if not used correctly. The correct techniques
and personal protective equipment must be worn at all times
The following information must be read before operating the equipment:
•Before placing the Fullwood Packo FullClean Plus system in operation, this manual
and the appropriate operating instructions must be read carefully. A proper handling
of the equipment is the basis for correct functioning
•The equipment must be used only for the application described
•It is the responsibility of the farmer to check his animals and the performance of the
equipment. If, for any reason, the Fullwood Packo FullClean Plus system is not
operational or individual animals refuse to use the system, it is the responsibility of
the farmer to feed and milk the animals with alternative methods
•Check that no pipes or anything similar are protruding in the barn or in the parlour on
which the (transponder) neck bands or leg bands can get caught
•Calibration of Milk Meters and feed dispensers is of most importance to obtain proper
milking and feeding results. If calibration for some reason is wrong, or wrong values
have been programmed, the milking results and feed distribution will be bad until
correct calibration has been done and proper values have been entered
•Never remove cover(s) or parts of the system before the electrical power cable(s)
is/are disconnected
•Do not flush the electronic equipment with (high) pressure hoses
•Installation of the equipment must becarried out by skilled and authorised technicians
only

Doc No:
006614
Fullwood Packo FullClean Plus
Revision:
D
Date:
14/08/2020
Page 8of 58
•False or incorrect operation of the system may seriously affect the animals. It is
therefore necessary to double check all input and output of the system
•The manufacturers guarantee does not cover damage that has been caused by
incorrect installation, incorrect usage, improper treatment, inadequate cleaning and
servicing or wrong input. Neither does it cover further damage resulting from the
above
•To the full extent allowed by law, Fusion Electronics also excludes itself and its
suppliers any liability, whether based in contract or not (including negligence), for
incidental, consequential, indirect, special, or punitive damages of any kind, or for
loss of revenue or profits, loss of business, loss of information or data, or other
financial loss arising out of or in connection with the sale, installation, maintenance,
use, performance, failure, or interruption of its products, even if Fusion Electronics or
its authorised reseller has been advised of the possibility of such damages, and limits
its liability to repair, replacement, or refund of the purchase price paid, at Fusion
Electronics' option. This disclaimer of liability for damages will not be affected if any
remedy provided herein shall fail of its essential purpose
•Some countries, states, or provinces do not allow the exclusion or limitation of implied
warranties or the limitation of incidental or consequential damages for certain
products supplied to consumers or the limitation of liability for personal injury, so the
above limitations and exclusions may be limited in their application to you. When the
implied warranties are not allowed to be excluded in their entirety, they will be limited
to the duration of the applicable written warranty. This warranty gives you specific
legal rights which may vary depending on local law

Doc No:
006614
Fullwood Packo FullClean Plus
Revision:
D
Date:
14/08/2020
Page 9of 58
6. General and Features
The FullClean Plus cleaning controller is a micro-processor-based system which is able to
control all kindof washing systems formilking equipment, suchas Circulation cleaning, Boiling
water cleaning and Closed-circuit washing.
The system has a large number of outputs to control a vacuum pump, a milk pump, water
supply valves, vacuum or compressed air valves, detergent pumps etc. The FullClean Plus
controls these outputs on adjustable time bases or by reading a number of inputs such as
different water levels, temperature sensors etc. The interaction between inputs and outputs is
software controlled and can be configured by a technical engineer using the FullClean Plus
terminal. Many features such as water recuperation, automatic chemical dosing etc. can be
set in this way.
6.1. FullClean Plus Feature Listing
The features are as follows:
•User interface with:
oA two-line 20 character display on the front side of the terminal to monitor all kind
of information about the cleaning cycle status, time in cleaning, water
temperature etc. It navigates the user or technician through the menu structure
of the software and can support different languages
oFive keys on the front side of the FullClean Plus terminal, for user control of the
system, for editing and entering all settings
oFive indication LEDs, indicating the status of the Operation Mode
oBuzzer indicating each key pressed or warning for several errors during
operation
•Large number of different inputs. Available by default is:
oFour digital inputs to detect water levels, milk delivery line position, etc
oTwo analogue inputs for temperature sensors
oOne Input for a pH or conductivity sensor for future applications
•Large number of different outputs. Standard available:
oEight Galvanic isolated relays contacts max. 8 A/230 V, for vacuum pump, milk
pump, Milk Meter power supply, air injector, cluster tube clamps, etc
oFour Galvanic isolated relay contacts with common power for max. 5 A/230 V
AC
oOne Low capacity normally closed relay contact for an alarm (max. 1 A/24 V
AC/DC)
•Enclosure IP66 rated
•Standard expansion connector to connect one 4-IN/OUT board (4 extra in- and
outputs)
•Standard hardware on-board of the controller:
oBattery backed RAM
oReal Time Clock (RTC)
oEEPROM to store all cleaning parameters
•Power supply (two models available):
o24 V AC/DC

Doc No:
006614
Fullwood Packo FullClean Plus
Revision:
D
Date:
14/08/2020
Page 10 of 58
o115/230 V AC
•Features related to the software:
oAdjustable times for each cleaning phase
oAutomatic selection of chemicals for pre-determined wash cycle
oManually step through the cleaning cycle to check the cleaning process
oManually start a specific cleaning phase
oAutomatic disinfection can be performed before milking
oRecording of cleaning parameters and errors occurred during cleaning process
oInternal diagnostics to test the PCB
6.2. The FullClean Plus Operational Modes
The FullClean Plus user interface software is divided into two parts:
6.2.1. Operation Mode
This mode is the normal function mode of the controller. The keys on the terminal allow the
user to start or stop the milking and the cleaning, view the cleaning status, confirm warnings,
and change some user settings, for instance the start time of the automatic disinfection before
milking. More information about this mode is provided in Section 10; User operation.
6.2.2. Adjust Mode
This mode is used by a technician to set all technical settings of the controller. This mode is
protected by an on-board dipswitch setting. More information about this mode is provided in
Section 12; Technical operation.
6.3. The FullClean Plus Cleaning Possibilities
The firmware mentioned above, for the FullClean Plus controller, supports two types of
cleaning.
6.3.1. Circulation Cleaning
This cleaning procedure is based on washing the milking equipment in three or four phases
where basically cleaning water with detergent is circulated through the system for a certain
period.
6.3.2. Heat Based Cleaning
This is a simple cleaning procedure, based on washing the equipment with boiling water which
runs through the system only once.
In Section 9: hardware installation and wiring of the FullClean Plus controller, information is
provided according to the type of cleaning desired.

Doc No:
006614
Fullwood Packo FullClean Plus
Revision:
D
Date:
14/08/2020
Page 11 of 58
7. Firmware Versions
Because of the availability of two, quite different firmware branches,these are mentioned here.
7.1. Firmware for the FullClean Plus, covered by this Manual
This manual covers the following firmware:
•FCC GB/CZ/P 1.04. Contains the English (GB), the Czech (CZ) and the Polish (P)
language
•FCC NL/F/D 1.04. Contains the Dutch (NL) French (F) and the German (D) language
The difference between these two is only the available languages.
7.2. Firmware NOT covered by this Manual
This firmware version was developed for the UK FC+ Closed Circuit Washing system, the
software programs and output assignments are not covered in this manual.
For information about a FullClean Plus controller with this firmware, contact Fullwood Packo
Ltd.

Doc No:
006614
Fullwood Packo FullClean Plus
Revision:
D
Date:
14/08/2020
Page 12 of 58
8. Hardware description
This section gives a description of the hardware of the FullClean Plus.
8.1. The User Interface
The FullClean Plus controller cabinet is divided into two interconnected sections.
The top section with the blue front label, houses the user interface of the controller. It has five
keys, five indication LEDs and an LCD display. This section is a hinged lid which can be
opened like a door. This is the "electrically safe" section of the controller and does not carry
the dangerous mains voltage.
Figure 1 The Control Panel of the FullClean Plus Enclosure
The bottom section contains all the connectors for the FullClean Plus (in and outputs) and can
only be opened using a screwdriver.
WARNING
THE BOTTOM SECTION OF THE FULLCLEAN PLUS CAN
HAVE HIGH VOLTAGES INSIDE, EVEN AFTER THE UNIT
HAS BEEN SWITCHED OFF! ACCESS TO THE UNIT IS ONLY
ALLOWED FOR QUALIFIED SERVICE ENGINEERS AND
AFTER ALL POWER SUPPLIES HAVE BEEN SWITCHED
OFF.
Depending on the type used, the FullClean Plus controller can be powered by 24 V AC/DC or
115/230 V AC.
At the back side of the terminal’s top section (the lid), two small PCBs are mounted. One
controls the LCD display and the other reads the keys of the front. These two PCBs are
connected to the main board of the controller with a ribbon cable.

Doc No:
006614
Fullwood Packo FullClean Plus
Revision:
D
Date:
14/08/2020
Page 13 of 58
8.2. The FullClean Plus Circuit Board
Figure 2 The FullClean Plus Main PCB with its Main Components
The following components are located on the FullClean Plus PCB:
8.2.1. Connectors
8.2.1.1. (X1A t/m X1D) I1...I4
Four 2-terminal digital 12-24 V AC/DC inputs, used to connect digital inputs such as water
level detectors and the delivery line switch. These inputs are read through an optocoupler,
which means that these inputs are electrically isolated from the PCB.
8.2.1.2. (X2) 4-20 mA
3-terminal connector, not used.
8.2.1.3. (X3) PT 100
4-terminal analogue input for two PT100 temperature sensors. Temperature sensor 1 is
connected between the terminals 1 and 3 and the second PT100 sensor isconnected between
the terminals 2 and 3. Terminal 4 can be used for connecting the shield of the cable.
8.2.1.4. (X4 a/b)
Two 3-terminal connectors, not used.

Doc No:
006614
Fullwood Packo FullClean Plus
Revision:
D
Date:
14/08/2020
Page 14 of 58
8.2.1.5. (X5) Expansion
20-terminal ribbon cable connector used to connect optional 4-IN/OUT board. Four holes in
the FullClean Plus PCB can be used to mount the 4-IN/OUT board. In that case an extra
extension ring must be mounted between the top lid and the back part of the enclosure.
8.2.1.6. (X6) FTT
One 16-terminal- and one 10-terminal ribbon cable connector for the Fusion Tiny Terminal
(FTT) PCB, mounted inthe lid of the FullClean Plus. The 16-terminal connector is for the older,
previous type FTT and the 10-terminal connector for the current type FTT.
8.2.1.7. (X7) 01-04
5-terminal connector, from 4 electrically isolated relay outputs, capable to control four loads
up to a maximum of 5 A/230 V AC in total. These outputs can be used to activate water valves,
vacuum valves or water circulation valves and share a common power supply. The contacts
are open if the FullClean Plus is powered (normally open).
Connector X20 should be used to connect the power supply for these four outputs.
These output relay contacts are by default not protected against arcing. Upon installation,
suitable contact-protection must be implemented, see Section 9.2 for information about
relay-contact protection.
8.2.1.8. (X8...X15) 05...012
Eight 2-terminal connectors, from 8 electrically isolated relay outputs, capable to control eight
loads up to a maximum of 8 A and 230 V AC each. These connectors are used, for instance,
to control a vacuum pump, a milk pump, the Milk Meter power supply. The contacts are open
if the FullClean Plus is unpowered (normally open). These output relay contacts are by default
not protected against arcing. Upon installation, suitable contact protection must be
implemented. See Section 9.2 for information about relay-contact protection.
8.2.1.9. (X17) Alarm
One 2-terminal, low capacity relay contact (1 A, 24 V AC/DC). This relay contact is normally
closed (contact closed when FullClean Plus unpowered) and can be used to connect an alarm
device such as a lamp or buzzer.
8.2.1.10. (X18 A/B) 24 V
Two 2-terminal connectors for 24 V power- input/ output:
The + and - is only a reference for the internal electrical connection between these terminals.
•FullClean Plus 24 V: This is the input for a 24 V AC/DC power supply. Either one of
the two connectors can be used for powering the FullClean Plus. The other can be
used to provide power along the terminals of the controller, which needs 24 V
•FullClean Plus 115/230 V: The connectors X18 A/B carry the 24 V AC of the internal
transformer, and can be used as a power source to supply a maximum of 500 mA. It
can be used to provide power along the terminals of the controller, which need 24 V.
This connector X18 A/B is protected by the 500 mA fuse F15

Doc No:
006614
Fullwood Packo FullClean Plus
Revision:
D
Date:
14/08/2020
Page 15 of 58
8.2.1.11. (X19) Mains (not applicable for 24 V powered models!)
3-terminal connector for a 115/230 V AC mains power supply. The middle terminal of this
connector can be used to connect an earth wire, but the terminal itself it is not connected to
anything on the PCB. Selection of 115 or 230 V AC is done with switch S3 just above this
connector. This connector X19 together with fuse F14, switch F3 and the transformer are not
present in the 24 V AC/DC version of the FullClean Plus controller.
8.2.1.12. (X20) 1-4 CMN
2-terminal connector used to connect the power supply (230 V/5 A maximum) for devices
connected to X7.
8.2.2. Fuses
F14: Microfuse T 200 mA to protect 115/230 V AC mains connector X19. (115/230 V AC
version only)
F15: Microfuse T3.15 A to protect 24 V AC/DC connector X18.
8.2.3. Switches
S1: Set of 8 dipswitches labelled address, used to set the address of the controller. Always
set to address 1; (only dipswitch 1 “on”). Other addresses are not implemented.
S2: Set of 8 dipswitches labelled Function, used to enter special functions of the FullClean
Plus controller. All switches OFF = normal function mode. If the controller is powered up with
only dipswitch 8 set to “on”, it will enter the technical Adjust Mode. Other functions are not
implemented in S2.
S3: Switch to select 115 V or 230 V AC mains power supply (only for mains powered models).
8.2.4. Jumpers
(J1) Reset: Reset jumper, if these pins are closed, the FullClean Plus controller will be reset;
the saved settings will not be lost.
(J3) No label: To enable the lithium backup battery; the FullClean Plus controller will not
function without this jumper.
8.2.5. LEDs
H201: Yellow LED lights up depending on the function of the FullClean Plus controller.
H202: Red LED flickering indicates activity of the microprocessor.
H203: Green LED, should light up continuously if the controller is powered and the program is
running properly. If this LED blinks then the program is not running properly. If the LED does
not light at all, there is no power (switched off, or fuse(s) blown).
H401-413: Yellow LEDs. These LEDs indicate the status of the corresponding output relays
K401 up to K413. Each relay has a yellow led connected to the coil of the relay. LED “on”
indicates a powered relay. Output X17 is the only output from which the normally closed
contacts are used. This means that the corresponding LED H413 lights up when the controller
is powered up, meaning this output and thus the alarm is not activated.
NOTE
LED H413 lights up when the controller is powered up; meaning this output,
and thus the alarm, is not activated.

Doc No:
006614
Fullwood Packo FullClean Plus
Revision:
D
Date:
14/08/2020
Page 16 of 58
8.2.6. Important ICs
U203: This is the EPROM of the controller, containing the firmware (built-in software).
9. Hardware Installation and Wiring
9.1. General Installation Information
This section gives all information to install the FullClean Plus controller and all its wirings to
peripheral equipment. This manual is specific tothe installation ofthe FullClean Plus and does
not cover the installation of any peripheral cleaning equipment or cleaning routines and
procedures.
The FullClean Plus controller can be mounted to a wall at a central place in the milk room. It
has to be connected to a large amount of other equipment. Although the enclosure has an
IP66 rating protected, it is advised to install the controller in a dry place which can easily be
reached by the operator and service technician.
Figure 3 shows general wiring and settings which are valid for FullClean Plus controllers used
in every type of cleaning method.
Figure 3 General Wiring and Settings of the FullClean Plus Controller
Some remarks related to Figure 3:
•All peripheral equipment shown in Figure 3 is used in every type of cleaning system.
Inputs which are only used for a certain type of cleaning are shown in the next
sections

Doc No:
006614
Fullwood Packo FullClean Plus
Revision:
D
Date:
14/08/2020
Page 17 of 58
•The FullClean Plus controller can be powered by 115/230 V AC or 24 V AC/DC,
depending on the PCB
•The outputs of the FullClean Plus controller that control high power devices like
vacuum pumps, should in their turn, control (be connected to) the high-power motor-
switch in the control box of those devices
•Inputs I1...I4, outputs 05...012 and alarm output are free contacts, which means that
power must be provided
•If some inputs like the delivery line are not used, in the software these should be set
to "neither"
9.2. Relay Contact Protection
Any relay contact that switches a load, especially an inductive load, will gradually wear, and
eventually fail. The relay contacts of the FullClean Plus are not protected by default. To reduce
wear to the relay contacts of the FullClean Plus, relay contact protection tailored to the
connected load is recommended.
Depending on the type of the connected devices (solenoid valves, pulsators, motors, AC or
DC powered) a different contact protection method is required. Consult the manufacturer of
the connected device for the best relay contact protection. If the load is non-inductive, such
as light bulbs or (heating)-resistors, no additional protection is needed. The operating voltage
of the connected device should never exceed 230 V (Alarm contact max. 24 V).
Some suggestions of contact protection methods are provided here. The most effective
solution is a shunt protection over the device itself, as close to the device as possible.
Figure 4 Examples of Relay Contact Protection
For DC loads, the most effective contact protection is a suitable diode placed in the right
direction parallel to the load. The right diode direction is the non-conducting direction: with the
cathode connected to the ‘+’ and the anode connected to the ‘-‘terminal of the load. A
transzorb or varistor of the right voltage can also be used for DC loads, but it is slightly less
protective.
For AC loads, a regular diode cannot be used. Instead, a transzorb = Transient Voltage
Suppressor (TVS) should preferably be used. A varistor = Voltage Dependent Resistor (VDR)
can also be used.
Both should be of the right voltage and power rating. Recommended minimum TVR/VDR
voltage (VDR):
•DC –Maximum load voltage multiplied by 1.1
•AC –Maximum load voltage multiplied by 1.5

Doc No:
006614
Fullwood Packo FullClean Plus
Revision:
D
Date:
14/08/2020
Page 18 of 58
NOTE
Not protecting the relay contacts can shorten relay contact life and can have
an effect on the performance of the FullClean Plus in certain conditions.
When using ac valves, diodes cannot be used for relay contact protection.
Use varistors instead.
9.3. Circulation Cleaning Installation
Figure 5 shows a flow diagram of the Circulation Cleaning system. The principle of this
cleaning system is to wash the milking equipment in three or four phases:
•Pre-rinse phase: Lukewarm water is flushed through the system once, to remove milk
residues
•Primary cleaning phase: Hot water with some kind of detergent is circulated through
the system for a certain time to remove fat and protein residues
•After-rinse phase: Cold water is flushed through the system to remove detergent
residues
•Second after-rinse phase: Double procedure, the same as after-rinse
Figure 5 Circulation Cleaning System Flow Diagram
Labels and output numbers used in this diagram are also used in the wiring schedule for this
system in Figure 6.
Table of contents
Popular Controllers manuals by other brands
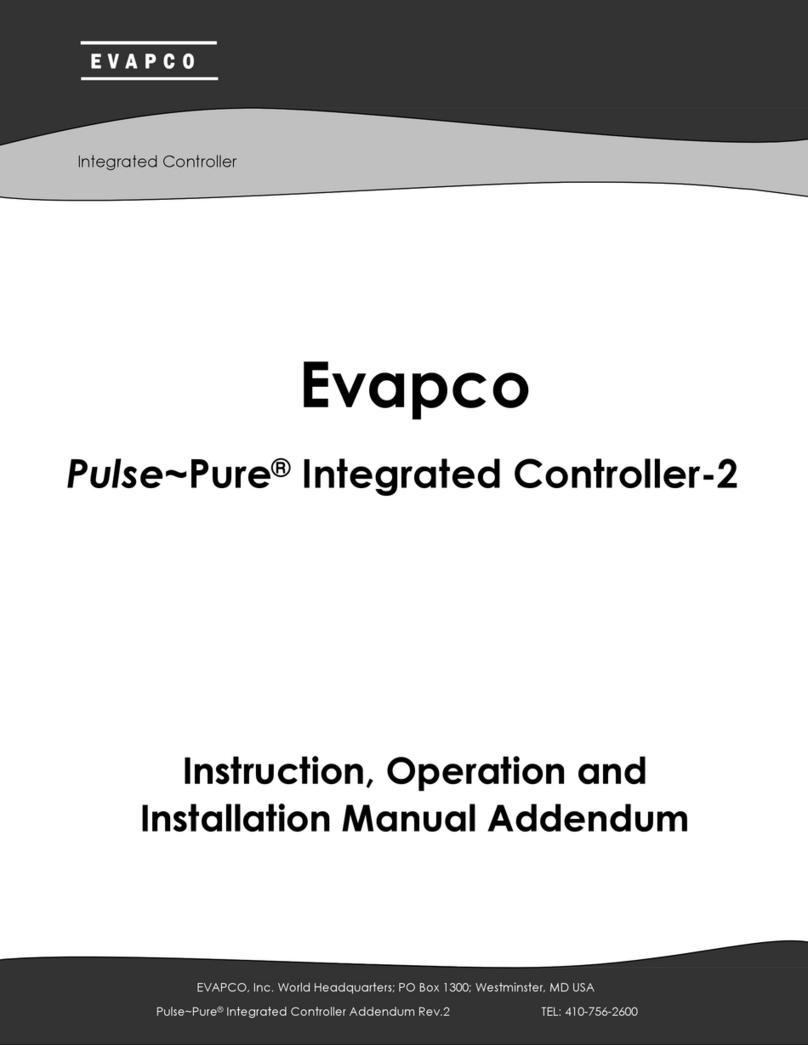
EVAPCO
EVAPCO PulsePure Integrated Controller-2 Instruction, Operation and Installation Manual Addendum
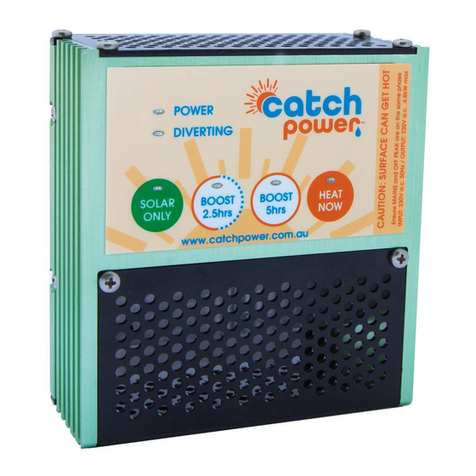
Catch Power
Catch Power GREEN user guide
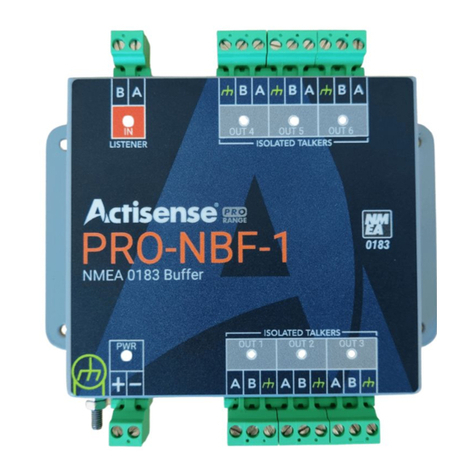
Actisense
Actisense PRO-NBF-1 quick start guide
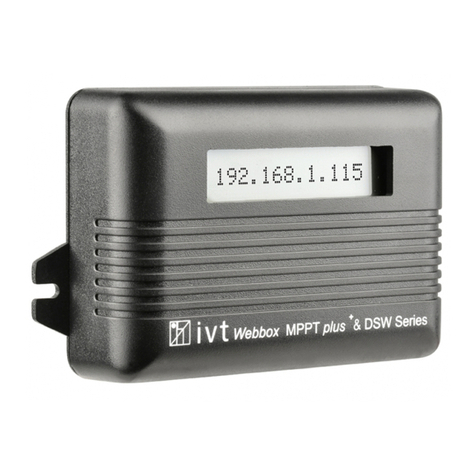
IVT
IVT Webbox LCD operating instructions
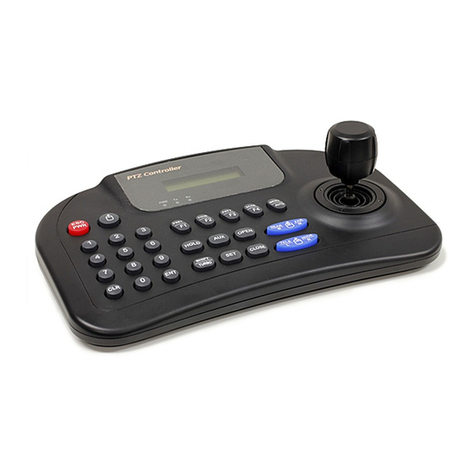
Marshall Electronics
Marshall Electronics VS?TKC?100 Provisional Instructions
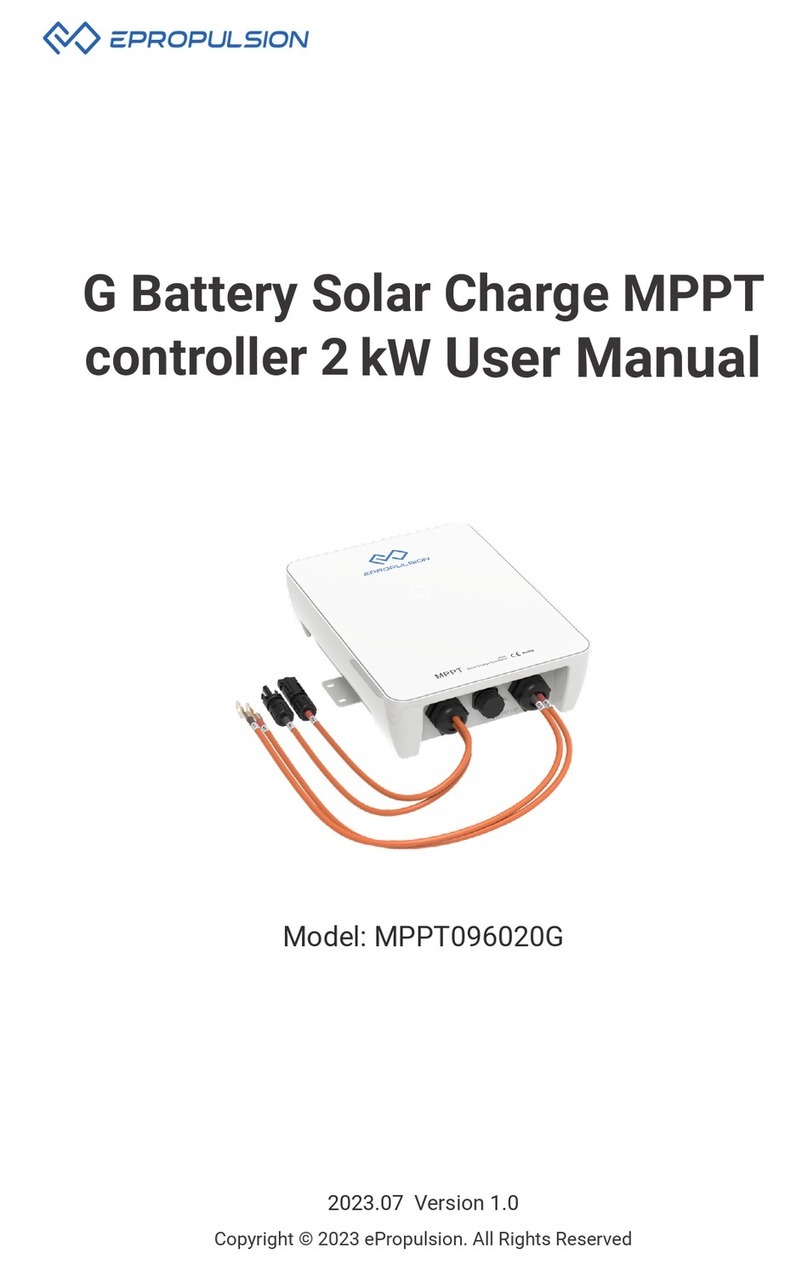
ePropulsion
ePropulsion MPPT096020G user manual
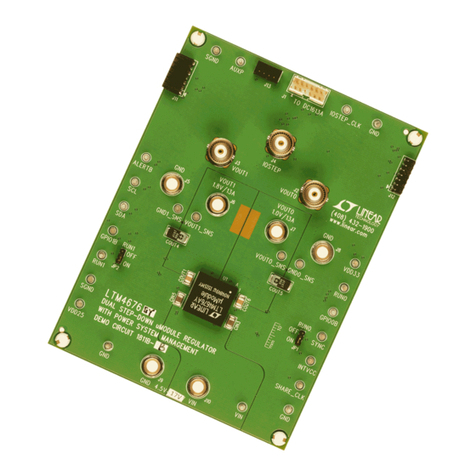
Linear Technology
Linear Technology Analog Devices LTM4676A Demo Manual
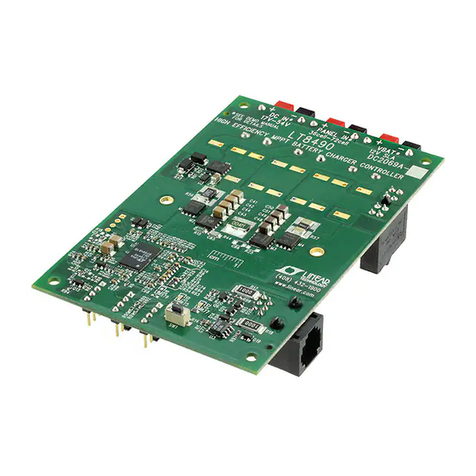
Linear Technology
Linear Technology DC2069A Demo Manual

Sturtevant Richmont
Sturtevant Richmont Global 400mp user manual
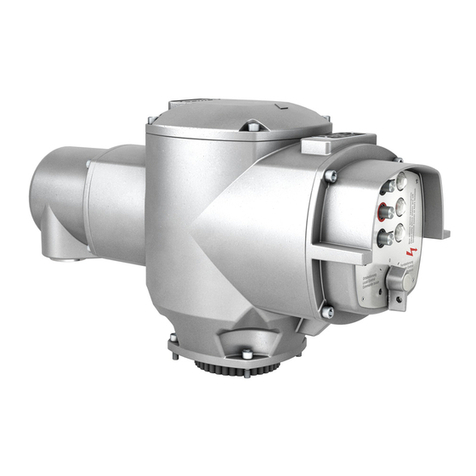
AUMA
AUMA AM 01.1 Operation instructions
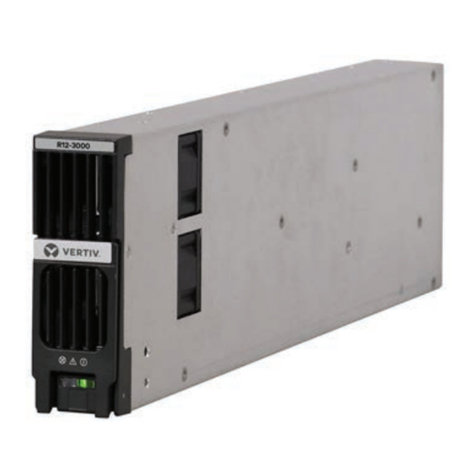
Vertiv
Vertiv NetSure SCC user manual
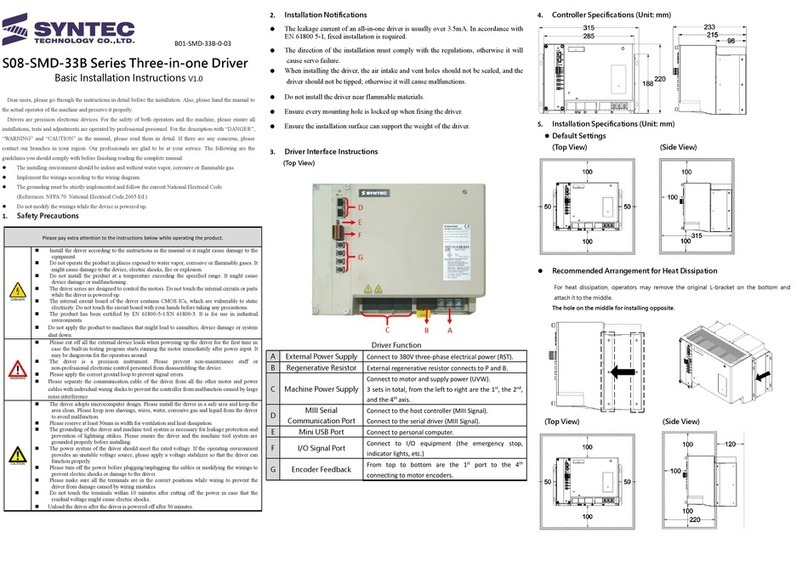
Syntec
Syntec S08-SMD-33B Series installation instructions