Galvin Engineering CliniMix TMV 1500 Instruction sheet

© Galvin Engineering Pty Ltd
Product Installation
Guidelines
& Scope of Use
Version 1, 13 November 2023, Page 1 of 13
Document No: 001.00.10.32
CliniMix
®
TMV 1500 Lead Safe
™
½” Thermostatic Mixing Valve in SS
Cabinet
PRODUCT CODES
- 201.10.70.10
- 201.11.70.10
- 201.13.70.10
SPECIFICATIONS
CliniMix
®
Thermostatic Mixing Valve Cabinet assemblies are designed to protect users from scalding or cold
water shock by providing tempered water to the desired outlets.
This stainless steel hinged cabinet kit is a lockable cabinet with 20mm copper fittings which allows secure
installation and safe, simple maintenance of thermostatic mixing valve.
Flat faced connections allow removal of the valve without disturbing the pipework.
In the event of either hot or cold water supply failure the valve will shut down.
Units come complete with right angle isolating ball valve, non-return valve and strainer assemblies.
Can be installed in any configuration with the water outlet in the horizontal or vertical position, and inlet
connections can be rotated to suit inlet pipework.
Complies with the requirements of AS/NZS 4032.1 – Thermostatic Mixing Valves.
WARNINGS: Special attentions to be paid on notes, photos, images, or drawings of
assembly steps marked with the warning symbol.
TABLE OF CONTENTS
1.0 DESCRIPTION 2
2.0 TECHNICAL DATA 2
3.0 SAFETY 2
4.0 DIMENSIONS 3
5.0 FLOW SIZING GRAPH 4
6.0 WATER SUPPLY CONDITIONS 5
6.1 SCOPE OF USE 5
6.2 SUPPLY PRESSURE REQUIREMENTS 5
7.0 INSTALLATION 6
8.0 TROUBLESHOOTING 8
9.0 WARRANTY 9
10.0 APPENDIX 10

© Galvin Engineering Pty Ltd
Product Installation
Guidelines
& Scope of Use
Version 1, 13 November 2023, Page 2 of 13
1.0 DESCRIPTION
This manual covers the CliniMix
®
TMV 1500 Lead Safe
™
TMV SS Cabinet Assembly. This product is designed to
provide tempered water to the desired outlets. This mixing valve cabinet assembly is supplied with integral
isolating valves, strainers and check valves and is provided with a facility for thermal disinfecting of the cold inlet
side and mixed water outlet.
Avoid using heat for soldering near the mixer inlets to prevent damage to internal components.
2
.0
TECHNICAL DATA
MIXED OUTLET TEMPERATURE
Factory Preset Temperature
(°C)
43 +/- 2
Adjustable Temperature Range (°C) 35 – 50
INLET TEMPERATURES
Cold Supply (°C) Min 5
Max 30
Hot Supply (°C) Min 55
Max 90
Hot to Mix Temp Differential (°C) Min 10
Cold to Mix Temp Differential (°C) Min 5
Nominal Flow Rate (LPM) Min 4
DYNAMIC INLET PRESSURES
Hot and Cold Inlet Pressures Min 20
Max 600
STATIC INLET PRESSURE
Hot and Cold Inlet Pressures (kPa) Max 1600
INLET PRESSURE RATIO
Supply Pressure Loss Ratio
Max 10:1
Recommended Supply Pressure Variation (Hot:Cold or Cold:Hot) ±10%
Minimum Flow Rate to Ensure Stable Operation 4 L/min
NOTE 1: For optimum operation it is recommended that the hot and cold water supply pressure be balanced to within +/- 10%
NOTE 2: Notwithstanding the above, compliance with AS/NZS3500 must be maintained.
3.0 SAFETY
The CliniMix
®
TMV 1500 Lead Safe
™
TMV SS Cabinet Assembly is a high-performance valve designed to give
stable and dependable operation, provided it is installed, commissioned, operated and maintained as per the
recommendations outlined in this manual. It should be noted, however, that this valve should not be considered
as an alternative to adequate supervision and duty of care during its use and operation.
Note: The mixing valve, inlet controls, pipe work and the surrounding area may become hot when
installed which may cause burn injuries. Precautions should be taken to ensure that these
surfaces cannot cause such injuries.

© Galvin Engineering Pty Ltd
Product Installation
Guidelines
& Scope of Use
Version 1, 13 November 2023, Page 3 of 13
4
.0
DIMENSIONS
Cabinet to suit rough-in wall opening area
360mm width x 360mm height x minimum 75mm
maximum 105mm depth.
Cabinet secured using back mount or side
mount.
Measure and mark the cabinet mounting hole
locations as per the dimensions shown in below
mounting details image.
Suitable fasteners will need to be sourced by the
installer.
201.10.70.10 – CliniMix
®
TMV 1500 Lead Safe
™
½” Thermostatic Mixing Valve in SS Cabinet
201.11.70.10 – CliniMix
®
TMV 1500 Lead Safe
™
½” Thermostatic Mixing Valve with Cold Bypass in SS Cabinet
360
360
27
0
57
Back Mount
Side
Mount
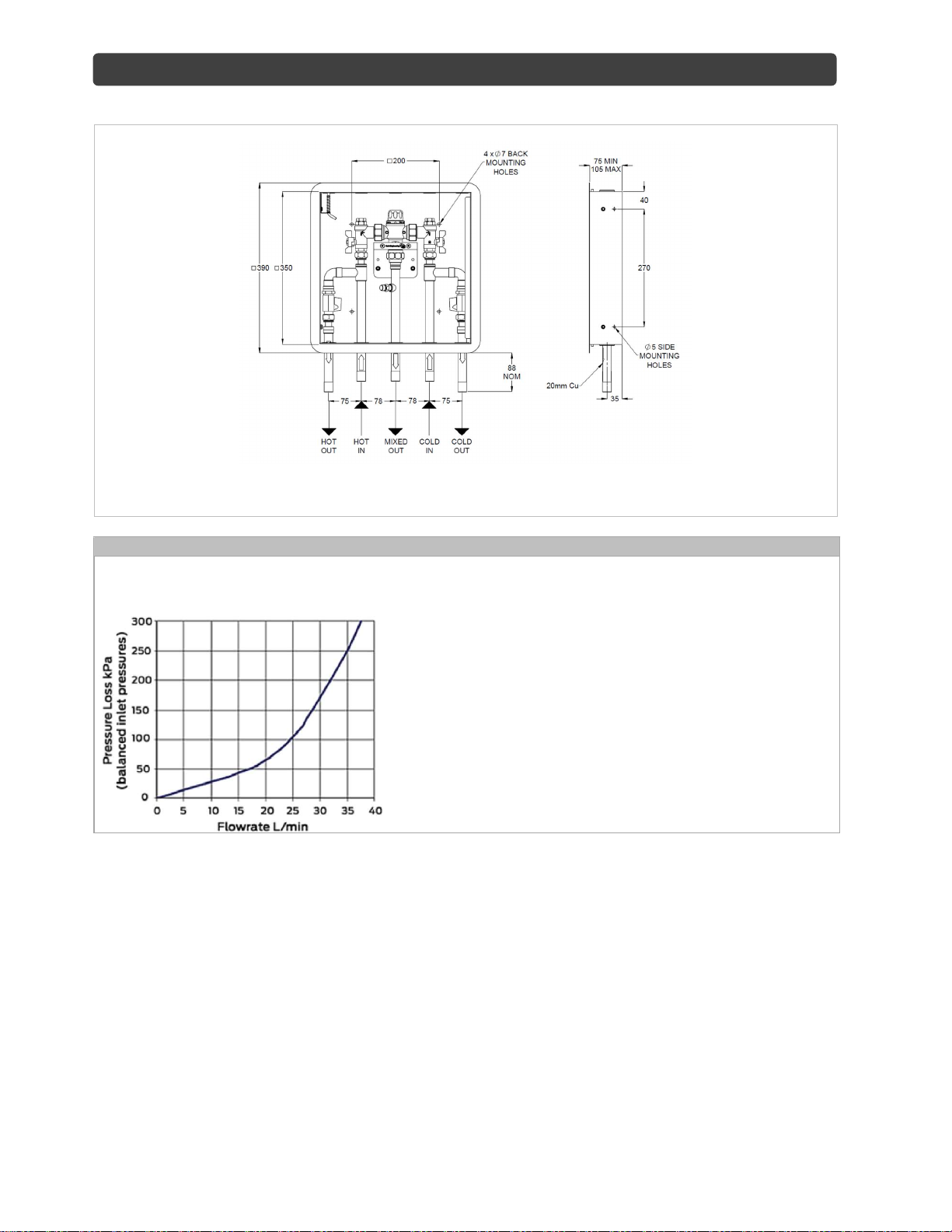
© Galvin Engineering Pty Ltd
Product Installation
Guidelines
& Scope of Use
Version 1, 13 November 2023, Page 4 of 13
5.0
FLOW SIZING GRAPH
The Galvin
Engineering
CliniMix
®
Thermostatic Mixing Valve is suitable for many applications. The Pressure Loss
Characteristic for Mixed Outlet Flow rate versus Balanced Inlet Pressure is shown in the graph below. It is important that
the valve is not oversized for its intended application.
NOTE: To ensure optimum performance the minimum outlet flow of the
TMV during operation should be at least 4 litres/minute.
It is important that the valve is sized such that the flow rates from the
outlets are not less than those listed AS/NZS 3500.1
The pipe-work between the TMV and the system must be sized in
accordance with AS/NZS 3500.1 to ensure the water velocity in the pipe-
work is within the allowed limit.
If the TMV is to be installed and operated under unequal inlet pressures,
the lower inlet pressure determines the outlet flow rate. However, for
optimum performance and stability it is recommended that the TMV be
installed with balanced dynamic inlet pressures (+/- 10%).
201.13.70.10 – CliniMix
®
TMV 1500 Lead Safe
™
½” Thermostatic Mixing Valve w/ Cold & Hot Bypass in SS
Cabinet
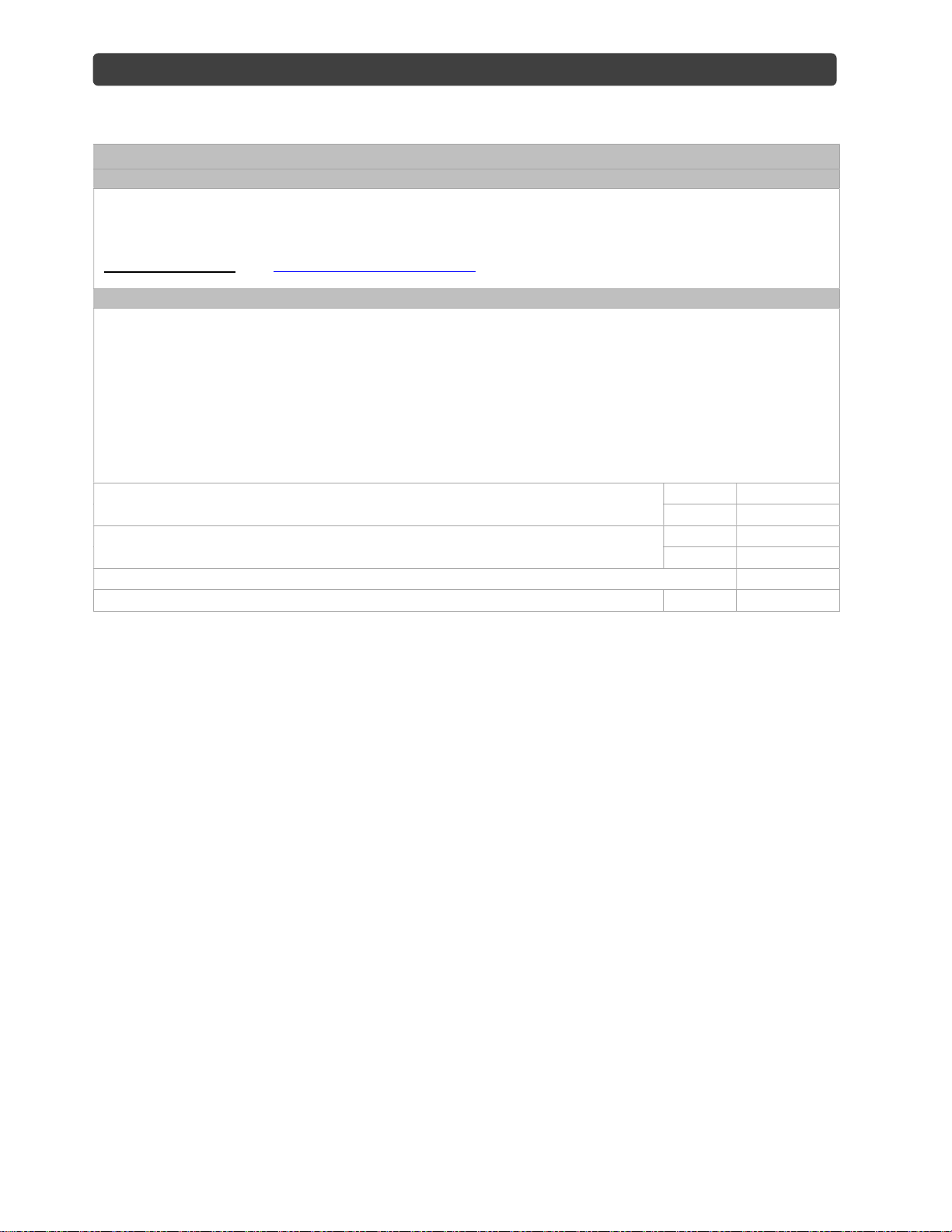
© Galvin Engineering Pty Ltd
Product Installation
Guidelines
& Scope of Use
Version 1, 13 November 2023, Page 5 of 13
6.0 WATER SUPPLY CONDITIONS
6
.1
SCOPE OF USE
This mixing valve cabinet assembly is manufactured to the highest standards and has approval to AS4032.1
which permits it to be installed in healthcare establishments such as hospitals, nursing homes and residential
care homes. When installed in healthcare establishments the supply conditions detailed below must be
observed and commissioning, maintenance, temperature adjustment, and on-going servicing provided in
201.70.11.09 Install from www.galvinengineering.com.au must be followed.
6
.2
SUPPLY PRESSURE REQUIREMENTS
This mixer is designed to be installed on all types of plumbing systems.
For optimum operation it is recommended that the hot and cold water supply pressure be balanced to within +/-
10%.
The mixer has integral isolating valves which permit servicing of the strainer, check valve and thermostatic
cartridge. They are also used for thermal disinfection.
If there is a risk that the dynamic inlet pressures exceed 600 kPa, a suitable pressure reducing valve must be
fitted upstream of the inlet fitting.
If there is a risk that the hot water supply temperature exceeds 90°C, a suitable temperature limiting valve must
be fitted upstream of the inlet fitting.
Working Temperature Range (°C) Min 5
Max 90
Working Pressure Range (kPa) Min 20
Max 600
Maximum Static Pressure (kPa) 1600
Permitted Supply Pressure Variation Max 10:1
Note: Tapware must be installed in accordance with the provisions of AS/NZS 3500. Installations not complying with
AS/NZS 3500 may void the product and performance warranty provisions.

© Galvin Engineering Pty Ltd
Product Installation
Guidelines
& Scope of Use
Version 1, 13 November 2023, Page 6 of 13
7.0 INSTALLATION
INSTALLATION COMPLIANCE: Galvin Engineering products must be installed in accordance with these
installation instructions and in accordance with AS/NZS 3500, the PCA and your local regulatory requirements.
Water and/or electrical supply conditions must also comply to the applicable national and/or state standards.
Failing to comply with these provisions shall void the product warranty and may affect the performance of the
product.
1. Remove cabinet door
1. Open the cabinet door
2. Pull hinge down to allow removal of the
door. Remove the door from cabinet.
2. Secure the cabinet
Insert cabinet into wall opening.
Mount cabinet in wall using four fasteners, only securing
hand tight.
If side mounting, make sure door frame has clearance and
can slide after fastening the cabinet.
Note: The cabinet must be mounted with four
fasteners for stability and strength. This is critical,
failure to do this may void the warranty.
Back Mount Side Mount

© Galvin Engineering Pty Ltd
Product Installation
Guidelines
& Scope of Use
Version 1, 13 November 2023, Page 7 of 13
For commissioning, maintenance, temperature adjustment, spare parts and on-going servicing information refer to
201.70.11.09 Install from www.galvinengineering.com.au.
3. Connect water lines
Before connecting to water lines, all lines must
be flushed
Remove protective vinyl cap from copper
tubes.
Join each copper tube to the correct main
water line, taking note of flow direction
arrows. Use suitable copper joining methods,
ensuring no flash sits inside the pipeline, this
will cause damage to the valves.
Note: The Galvin Engineering CliniMix
Thermostatic Mixing Valve must be
installed by a licensed plumber. If the
valve is not installed correctly then it
will not function correctly and may
put the user in danger. It may also
void the warranty of the valve.
4. Testing and operation
Adjust the door door frame until it sits flush with the wall.
Completely tighten mounting fasteners and apply sealant if
necessary.
Turn on hot and cold water supply.
Check for any leaks
Carry out commissioning procedure as per 201.70.11.09
installation instructions.
Check temperature of water is correct. If not, see
temperature adjustment in 201.70.11.09 installation
instructions available from www.galvinengineering.com.au.
Fit hinged door back into cabinet and lock with supplied key.
Ensure instructions are placed in the cabinet for future
service and maintenance record.
Apply sealant

© Galvin Engineering Pty Ltd
Product Installation
Guidelines
& Scope of Use
Version 1, 13 November 2023, Page 8 of 13
8.0 TROUBLESHOOTING
PROBLEM CAUSE RECTIFICATION
The desired mixed
water temperature
cannot be obtained.
Hot and cold supplies are fitted to
the wrong connections
Valve contains debris.
Strainers contain debris.
Ensure the valve has the Hot/Cold supplies
fitted to the correct connections.
Clean valve ensuring debris is removed and
components are not damaged.
Clean strainers ensuring debris is removed.
Check non return device is not jammed. Clean
if necessary.
The valve will
not shut down
during testing.
The hot to mix temperature
differential is not high enough.
Sealing seat is damaged or
fouled by debris
Raise hot water temperature.
Replace piston O-rings
Clean seat.
Replace element assembly
Mix temperature
unstable.
Debris is fouling valve.
Flow rate below 4 L/min.
Strainers are fouled.
Systems may be fluctuating
outside valve parameters
Clean the valve ensuring that all debris is
removed and components are not damaged.
Rectify any pressure deterioration.
Clean strainers
Check system pressure; install pressure
control valves to ensure inlet conditions are
within limit
Mix temperature
changing over
time.
Inlet conditions (pressures or
temperatures) are fluctuating,
Strainers contain debris.
Install suitable pressure control valves to
ensure inlet conditions are within range.
Clean strainers ensuring debris is removed.
Either full hot or cold
flowing from the
outlet fixture.
Valve is incorrectly set.
Hot/Cold water has migrated to
other inlet.
Adjust mix temperature between 35 – 48
Degrees Celsius as required.
Replace faulty non-return valves
No flow from the
valve outlet.
Hot or cold water failure.
Strainers are fouled
Valve functioning correctly. Restore inlet
supplies and check mix temperature.
Clean strainer.
Flow rate reduced or
fluctuating
Valve or inlet fittings fouled by
debris.
Dynamic inlet pressures are not
within those recommended limits.
Check valve and inlet fittings for blockages.
Ensure the dynamic inlet pressures are
nominally balanced to within +/- 10%
Mixed water
temperature too
hot or cold.
Valve has been tampered with.
Valve incorrectly set.
Inlet temperatures are not within
specified limits.
Readjust valve to required set temperature.
Readjust valve to required set temperature.
Ensure inlet temperatures are within the
specified limits.
Valve is noisy.
Water velocity above velocity
requirements of AS3500.1.
Reduce water velocity.

© Galvin Engineering Pty Ltd
Product Installation
Guidelines
& Scope of Use
Version 1, 13 November 2023, Page 9 of 13
9.0 WARRANTY
Galvin Engineering products are covered under our Manufacturer's Warranty. Galvin Engineering products
must be installed in accordance with the installation instructions and in accordance with AS 3500 and NCC
Volume Three, relevant Australian Standards and local authorities applicable to product being installed. Water
and electrical supply conditions must also comply to the applicable national and/or state standards, failing to
comply with these provisions may void the product warranty and affect performance of the product.
Please visit www.galvinengineering.com.au to view the full warranty, our Installation Compliance and
Maintenance & Cleaning information as well as any other additional information.
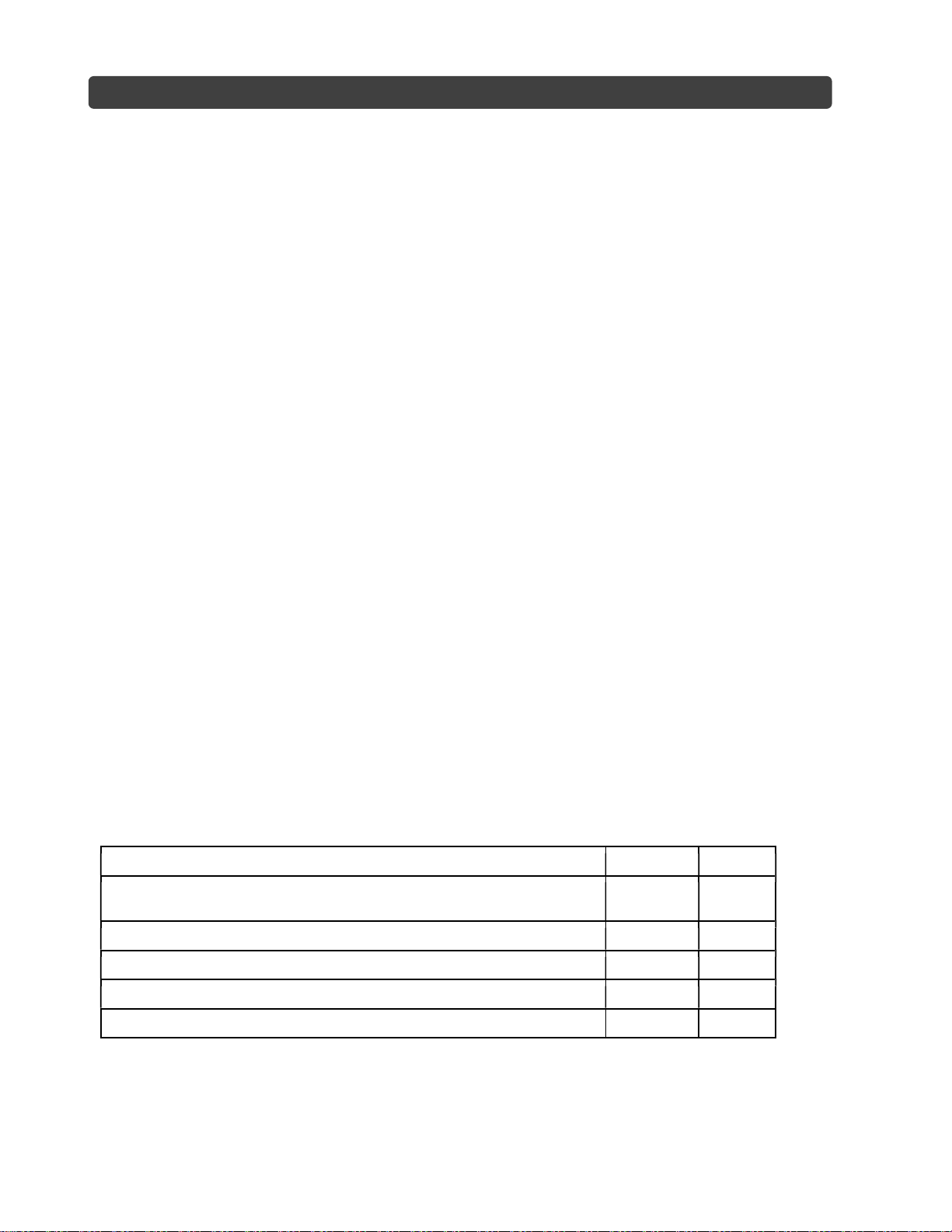
10
Product Installation
Guidelines
Version 1, 13 November 2023, Page 10 of 13
Version 1, 13 November 2023, Page 10 of 13
10.0 APPENDIX
Galvin
Engineering
Thermostatic Mixing Valve or
Tempering Valve Commissioning Report and/or
Maintenance Report
Note:
1. Please use a separate form for each valve.
2. The original copy of the report is to be given to the owner/occupier and retained on site for a minimum of 7 years.
Cross off appropriate box □
Thermostatic Mixing Valve □ Tempering Valve □
Commissioning Report □ Maintenance Report □
Name of Establishment: ____________________________________________________________________
Address of Establishment: ______________________________________________________________________
Phone Number: _____________________________ Date: _____________________ Work Order #: _______
Contact Person: _______________________ Make & Model of Hot Water System: ________________ ______
Temperature of Hot Water to the Valve: ____________ Temperature of Cold Water to the Valve: ______________
Hot Water Pressure: ________kPa Cold Water Pressure: _______kPa
Make of Mixing Valve: _______________________ Model No: ________________________ Size: _________
Valve Location/Building: _____________________________________________________________________
Valve Identification No: ______________________________________________________________________
Total No of Valves on the Site/Building: _________________________________________________________
No of Outlets Serviced by this Valve: Baths ( ) Basins ( ) Showers ( )
Other Outlets - Details ______________________________________________________________________
Valves Installed to the requirements of:
The NSW Code of Practice Plumbing and Drainage
Yes
No
The HOSPLAN Code of Practice for Thermostatic Mixing Valves in Health Care
Facilities
Yes No
The Valves manufacturers requirements
Yes
No
AS4032.3
Yes
No
The specifications and drawings for the project
Yes
No
The Local Water Supply or Authority
Yes
No
If No, give details and actions taken:
___________________________________________________________________________________________
___________________________________________________________________________________________
___________________________________________________________________________________________

11
Product Installation
Guidelines
Version 1, 13 November 2023, Page 11 of 13
Version 1, 13 November 2023, Page 11 of 13
Galvin
Engineering
Thermostatic Mixing Valve or
Tempering Valve Commissioning Report and/or
Maintenance Report
Test Results
Valve considered satisfactory for use: Yes □ No □
If No, state the reason and action taken:
___________________________________________________________________________________________
___________________________________________________________________________________________
___________________________________________________________________________________________
Commissioning Work
It is hereby certified that all the commissioning work has been carried out by the undersigned in accordance with
the requirements of the Codes of Practice indicated prior.
Date of Valve Commissioned: _________________________________________________________________
Name of Licensed Plumber: _______________________________ License/Cert No: _____________________
License Plumbers Signature: __________________________________________________________________
Telephone No. _____________________________________________________________________________
Owner/occupiers signature: ________________________________________________Date: ______________
Date of Initial Service Due: ___________________________________________________________________

12
Product Installation
Guidelines
Version 1, 13 November 2023, Page 12 of 13
Version 1, 13 November 2023, Page 12 of 13
Galvin Engineering Thermostatic Mixing Valve or
Tempering Valve Commissioning Report
Valve Location/Building : ____________________________________________________________________
Room or Area: ____________________________________________________________________________
Work Order No.: ___________________________________________________________________________
Warm
Water
Outlet
Fixture
No.
*Name/Type/Size and location
of Outlet Fixture (Bath, Shower,
Basin, Other)
Flow rate of Design Water (LPS) Temp of Warm Water (C)
One Outlet
in Use
**All Req‘d
Outlets in Use
One Outlet
in Use
**All Req’d
Outlets in
Use
1.
2.
3.
4.
5.
6.
7.
8.
9.
10.
11.
*Give details of brand and model designation.
** Commensurate with the design flow rate for the mixing valve.
Note: An accurate digital thermometer is necessary for the temperature measurements
Prescribed temperature range for warm water ______________ C to _________________C
Thermal shutdown at both minimum and maximum design flow rates
(Passed/Failed) Yes □ No □ Name of Plumber: ___________________________________________
License/Cert No. ____________________________________________________________________________
Licensee’s Signature: _______________________________ Date: ___________________________________
Telephone Number: _________________________________________________________________________
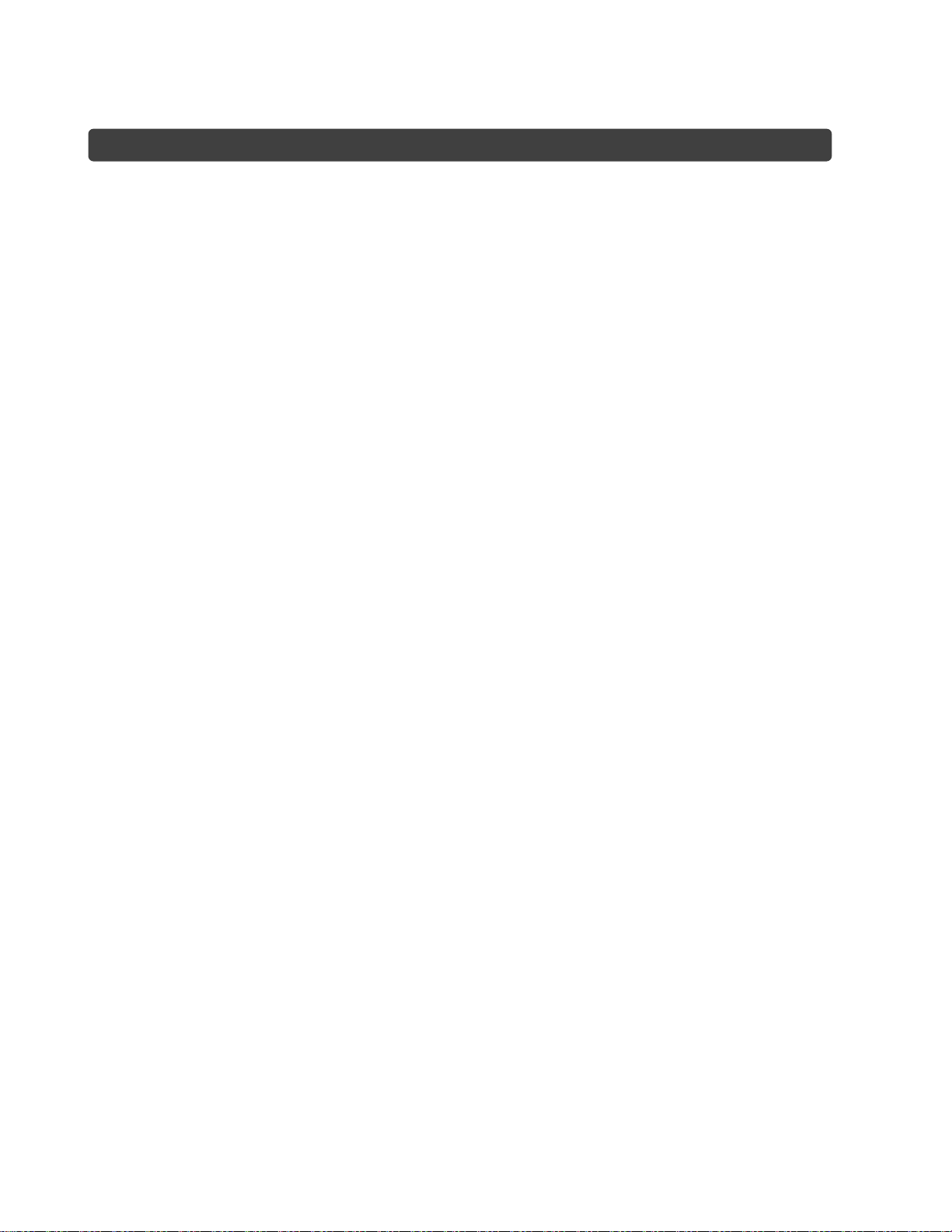
Product Installation
Guidelines
Version 1, 13 November 2023, Page 13 of 13
Version 1, 13 November 2023, Page 13 of 13
Galvin Engineering Thermostatic Mixing Valve or
Tempering Valve Commissioning/Maintenance Report
The following information is to be provided by the site manager/owner/occupier.
Valve size and installation recommended by : ______________________________________________________
Valves supplied by: ___________________________________________________________________________
Date of Installation: _________________________________ Drawing No. _______________________________
Service Manual on Site: Yes □ No □
Commissioning Tests for new installation or valve replacement. Yes □
This set of testing procedures and report received and witnessed by (Print Name): _________________________
___________________________________________________________________________________________
Temperature setting at completion of commissioning _______________ C
Position: ________________________________Signature: ______________________
Date:_______________________
Maintenance Tests. Yes □
Date of Previous Service: ______________________________________________________________________
Previous Service carried out by: _________________________________________________________________
Reason for Maintenance Tests: _________________________________________________________________
This Test and report Witnessed by: _______________________________________________________________
The valve has been operating/performing satisfactorily for the previous 12 months: Yes □ No □
Comment on monthly Temperature Tests carried out by the owner______________________________________
___________________________________________________________________________________________
Temperature setting at time of completion: _________C
Current Report received and witnessed by:
Name: _____________________________________________________________________________________
Position: ____________________________________________________________________________________
Signature: _____________________________ Date: _______________________________________________
This manual suits for next models
3
Table of contents
Other Galvin Engineering Control Unit manuals