Gaspardo PA2 User guide

Cod. G19503380 2016-07
IT
EN
DE
FR
ES
USO E MANUTENZIONE
USE AND MAINTENANCE
GEBRAUCH UND WARTUNG
EMPLOI ET ENTRETIEN
EMPLEO Y MANTENIMIENTO *)
*) Valido per Paesi UE
*) Valid for EU member countries
*) Valable dans les Pays UE
*) Gilt für EU-Mitgliedsländer
*) Válido para Países UE
MASCHIO GASPARDO S.p.A.
CONCIME
FERTILIZER
DÜNGEMITTELN
FERTILISANT
FERTILIZANTES
SEMENTI
SEEDS
SAATGUT
GRAINES
SEMILLAS
PA2-CENTAURO
PA2
CENTAURO

ITALIANO ENGLISH DEUTSCH
INDICE INDEX INHALT
-
2cod. G19503380
1.0 Premessa......................................... 5
1.1 Generalità ........................................... 5
1.2 Garanzia ............................................. 8
1.2.1 Scadenza garanzia ............................ 8
1.3 Identificazione dell'attrezzatura ......... 8
2.0 Indicazioni generali di sicurezza .. 9
2.1 Segnali di sicurezza e indicazione ..... 9
2.1.1 Segnali di avvertenza ......................... 9
2.1.2 Segnali di pericolo .............................. 9
2.1.3 Segnali di indicazione ......................... 9
2.2 Norme di sicurezza e prevenzione
infortuni ............................................. 10
3.0 Descrizione della macchina ....... 13
3.1 Dati tecnici ........................................ 14
3.2 Movimentazione ................................ 15
3.3 Disegno complessivo ....................... 16
3.4 Dosatore ........................................... 18
3.5 Azionamento oleodinamico della
soffiante ........................................... 22
3.5.1 Impiantodipendente .......................... 22
3.5.2 Impiantoindipendente ....................... 23
3.5.3 Regolazione del soffiaggio ............... 24
3.5.4 Raffreddamento olio ......................... 24
4.0 Norme d'uso .................................. 25
4.1 Applicazione al trattore .................... 25
4.1.1 Attrezzatura anteriore ...................... 25
4.1.2 Attrezzatura posteriore (CENTAURO) .. 26
4.1.3 Attrezzatura posteriore (PA2) ......... 27
4.1.4 Collegamento centrale ...................... 27
4.1.5 Completamentomacchina ................ 28
4.2 Verifica capacità di sollevamento e
stabilità della trattrice abbinata alla
macchina .......................................... 30
4.3 Chiusura ed apertura dell'attrezzatura
posterior ........................................... 30
4.4 Trasporto stradale ............................ 31
4.5 Assetto della seminatrice ................. 32
4.5.1 Regolazione della profondità di semina .. 32
4.6 Regolazione dischi marcafile ........... 33
4.6.1 Lunghezza braccio marcafile .......... 33
4.7 Erpice copriseme posteriore ............ 34
4.8 Prima di iniziare il lavoro ................... 35
4.9 Inizio del lavoro ................................. 35
4.9.1 Preparativi per la distribuzione ......... 35
4.9.2 Esclusione semina mezza macchina . 35
4.10 Durante il lavoro ............................... 36
4.11 Fine lavoro ........................................ 36
4.11.1 Scarico della tramoggia .................... 36
5.0 Manutenzione ............................... 37
5.1 Piano di manutenzione ...................... 38
5.2 Suggerimenti in caso d’inconvenienti . 39
5.3 Lubrificanti consigliati ......................... 39
6.0 Demolizione e smaltimento....... 39
Dichiarazione di conformità ......... 194-195
1.0 Introduction ................................... 43
1.1 General ............................................. 43
1.2 Guarantee ......................................... 46
1.2.1 Expiry of guarantee .......................... 46
1.3 Identification ...................................... 46
2.0 General safety rules .................... 47
2.1 Danger and indicator signals ........... 47
2.1.1 Warning signals ................................ 47
2.1.2 Warning signals ................................ 47
2.1.3 Indicator signals ............................... 47
2.2 Safety regulations and accident
prevention ......................................... 48
3.0 Description of the machine ........ 51
3.1 Technical data .................................. 52
3.2 Handling ............................................ 53
3.2 Assembly drawing ........................... 54
3.4 Doser ................................................ 56
3.5 Oleo-dynamic blower drive .............. 60
3.5.1 Dependent system ........................... 60
3.5.2 Independent system ......................... 61
3.5.3 Blower pump control ........................ 62
3.5.4 Oil cooling ......................................... 62
4.0 Rules of use ................................... 63
4.1 Attachment the tractor ..................... 63
4.1.1 Front equipment ................................ 63
4.1.2 Rearequipment(CENTAURO) .......... 64
4.1.3 Rear equipment (PA2) ...................... 65
4.1.4 Central connection ........................... 65
4.1.5 Completion of the machine ............... 66
4.2 Check the lifting capacity and stability
of the tractor to which the machine is
hitched .............................................. 68
4.3 Open and close the rear equipment 68
4.4 Transport .......................................... 69
4.5 Seeder position ................................. 70
4.5.1 Adjusting the seeding depth ............ 70
4.6 Row marker disk adjustment ............ 71
4.6.1 Row marking arm length................... 71
4.7 Rear spring harrow .......................... 72
4.8 Before starting work ........................ 73
4.9 Operation start .................................. 73
4.9.1 Preparations for distributing ............. 73
4.9.2 Half machine seeding exclusion
function ............................................. 73
4.10 During work ...................................... 74
4.11 The end of operation ........................ 74
4.11.1 Emptying the hopper ......................... 74
5.0 Maintenance .................................. 75
5.1 Maintenance plan - summary table .. 76
5.2 Suggestions in case of inconveniences . 77
5.3 Recommended lubricants ................. 77
6.0 Demolition and disposal ............. 77
Conformity declaration ................. 194-195
1.0 Vorwort .......................................... 81
1.1 Allgemeines ...................................... 81
1.2 Garantie ............................................ 84
1.2.1 Verfall des Garantieanspruchs ....... 84
1.3 Identifizierung ................................... 84
2.0 Allgemeine
Sicherheitsanweisungen .......... 85
2.1 Warnsignale und Anzeigesignale .... 85
2.1.1 Warnsignale ...................................... 85
2.1.2 Gefahrsignale ................................... 85
2.1.3 Anzeigesignale ................................. 85
2.2 Sicherheits- und Unfallverhütungs-
Bestimmungen .................................. 86
3.0 Beschreibung die Maschine ...... 89
3.1 Technische Daten ............................ 90
3.2 Fortbewegung .................................. 91
3.3 Zusammenfassend .......................... 92
3.4 Dosiervorrichtung ............................. 94
3.5 Hydraulischer Antrieb des Gebläses .. 98
3.5.1 Anschluss an die Schlepperhydraulik .. 98
3.5.2 Separate Hydraulikanlage ................ 99
3.5.3 Druckeinstellung ............................. 100
3.5.4 Ölkühlung ........................................ 100
4.0 Betriebs-Anleitungen ................ 101
4.1 Einbau am Schlepper ...................... 101
4.1.1 Frontanbaugerät ............................. 101
4.1.2 Hinteranbaugerät(CENTAURO) ..... 102
4.1.3 Hinteranbaugerät (PA2) ................. 103
4.1.4 Mittiges Verbindungsrohr ............... 103
4.1.5 Ergänzender ausbau der maschine . 104
4.2 Prüfung der Hubkraft und
Standsicherheit des mit der Maschine
verbundenen Traktors .................... 106
4.3 Schließen und öffnen des Hinteren
Maschine ........................................ 106
4.4 Transport ........................................ 107
4.5 Position der sämaschine ................ 108
4.5.1 Einstellung der Aussaattiefe ............ 108
4.6 Einstellung der Spurreisserscheiben .. 109
4.6.1 Länge des Spurreisserarmes ........ 109
4.7 Rückwärtige Egge mit Federung .... 110
4.8 Vor Arbeitsbeginn .......................... 111
4.9 Arbeitsbeginn ................................. 111
4.9.1 Vorbereitungen vor dem verteilung .. 111
4.9.2 Ausschluss der halben Maschine
beimSäen ........................................ 111
4.10 Während des Betriebs ................... 112
4.11 Am Ende der Verteiler .................... 112
4.11.1 Ablassen des Saatgutes aus dem
Trichter ........................................... 112
5.0 Wartung ........................................ 113
5.1 Wartungsplan - Übersichtstabelle .. 114
5.2 Ratschläge bei Störungen .............. 115
5.3 Empfohleneschmiermittel ............... 115
6.0 Zerlegen und entsorgen der
Maschine...................................... 115
Konformitätsenklärung ................ 194-195

FRANÇAIS
TABLES DE MATIERES
ESPAÑOL
INDICE
-3
cod. G19503380
1.0 Introduction ................................. 119
1.1 Généralités ..................................... 119
1.2 Garantie .......................................... 122
1.2.1 Expiration de la garantie ................ 122
1.3 Identification .................................... 122
2.0 Indications générales de
sécurité ........................................ 123
2.1 Signaux de securite d'indication .... 123
2.1.1 Signaux de recommandation .......... 123
2.1.2 Signaux de danger ......................... 123
2.1.3 Signaux de indication ..................... 123
2.2 Normes de securite et de prevention
des accidents ................................. 124
3.0 Description de la machine ........ 127
3.1 Donnees techniques ...................... 128
3.2 Movimentation ................................. 129
3.3 Dessin global .................................. 130
3.4 Doseur ............................................ 132
3.5 Installation d'actionnement de la
soufflante ....................................... 136
3.5.1 Installation dependante ................... 136
3.5.2 Installation independante ................ 137
3.5.3 Réglage de la pression ................... 138
3.5.4 Refroidissement huile ..................... 138
4.0 Normes d'emploi........................ 139
4.1 Attelage au tracteur ....................... 139
4.1.1 Equipement anterieur ...................... 139
4.1.2 Configuration graines (CENTAURO) .. 140
4.1.3 Configuration engrais (PA2) .......... 141
4.1.4 Raccordement central .................... 141
4.1.5 Montage de la machine ................... 142
4.2 Stabilite pendant le transport
machine-tracteur ............................ 144
4.3 Fermeture et l'ouverture de
l'equipement arriere ........................ 144
4.4 Transport ........................................ 145
4.5 Position du semoir .......................... 146
4.5.1 Reglage de la profondeur de
l’ensemencement ............................... 146
4.6 Reglage des disques a tracer ........ 147
4.6.1 Longueur du bras traceur
de rangees ..................................... 147
4.7 Herse arriere a ressorts ................ 148
4.8 Avant de commencer le travail ...... 149
4.9 Debut du travail ............................... 149
4.9.1 Preparation pour le distribution ...... 149
4.9.2 Exclusion du semis sur une moitié
de la machine .................................. 149
4.10 Durant le travail............................... 150
4.11 Fin de travail ................................... 150
4.11.1 Rideau de vidange .......................... 150
5.0 Entretien ....................................... 151
5.1 Plan d'entretien - tableau
récapitulatif ..................................... 152
5.2 Conseils en cas d'inconvenients ... 153
5.3 Lubrifiants conseilles ..................... 153
6.0 Demantelement et elimination. 153
Confotmity declaratione ............... 194-195
1.0 Premisa ........................................ 157
1.1 Generalidades ................................ 157
1.2 Garantía .......................................... 160
1.2.1 Vencimiento de la garantía ............. 160
1.3 Identificación ................................... 160
2.0 Indicaciones generales de
seguridad ...................................... 161
2.1 Señales de seguridad y de indicación 161
2.1.1 Señales de advertencia ................. 161
2.1.2 Señales de peligro .......................... 161
2.1.3 Señales de peligro .......................... 161
2.2 Normas de seguridad y prevención
contra los accidentes ..................... 162
3.0 Descripción de la màquina ...... 165
3.1 Datos tecnicos ................................ 166
3.2 Manipulación ................................... 167
3.3 Diseño general ................................ 168
3.4 Dosificador ..................................... 170
3.5 Accionamiento hidráulico del soplador . 174
3.5.1 Instalación dependiente .................. 174
3.5.2 Instalación independiente ............... 175
3.5.3 Regolación de la presion ................ 176
3.5.4 Refrigeración del aceite ................. 176
4.0 Normas de uso ........................... 177
4.1 Aplicación al tractor ....................... 177
4.1.1 Equipo delantero ............................. 177
4.1.2 Equipamientoparasemilla(CENTAURO) 178
4.1.3 Equipamiento para abono (PA2) .... 179
4.1.4 Conexión central ............................ 179
4.1.5 Ensamblaje de la màquina .............. 180
4.2 Estabilidad durante el transporte
de la màquina -tractor .................... 182
4.3 Cierre y la apertura del equipo
posterior ......................................... 182
4.4 Transporte ...................................... 183
4.5 Ajuste de la sembradora ................ 184
4.5.1 Graduación de la profundidad del
siembra ........................................... 184
4.6 Regulacion de los discos
marcadores de hileras ................... 185
4.6.1 Longitud del brazo marcador de
hileras ............................................. 185
4.7 Grada posterior de muelle .............. 186
4.8 Antes de iniciar el trabajo .............. 187
4.9 Inicio del trabajo .............................. 187
4.9.1 Preparativos para el trabajo ........... 187
4.9.2 Exclusión siembra media máquina . 187
4.10 Durante el trabajo ........................... 188
4.11 Final del trabajo............................... 188
4.11.1 Descarga de las semillas desde
la tolva ............................................ 188
5.0 Mantenimiento ............................ 189
5.1 Plan de mantenimiento - tabla de
resumen .......................................... 190
5.2 Sugerencias en caso de
inconvenientes ............................... 191
5.3 Lubricantes aconsejados .............. 191
6.0 Desguace y eliminación ............ 191
Declaración de conformidad ........ 194-195

ENGLISH
-43
cod. G19503380
1.0 INTRODUCTION
This Instruction Manual for Operation (hereafter called "the Manual") provides the operator with useful information on how to simplify
EQUIPMENT use by operating it correctly and in safe conditions.
The sections below must not be considered as a long and burdensome list of warnings: they must be regarded as a number of
instructions that improve machine performance and prevent damage to persons, objects or animals originating from incorrect
machine operation and use.
It is essential that each operator in charge of transporting, installing, commissioning, operating, maintaining, repairing and dismantling
the machine consults this manual and read it carefully before carrying out any operation. This will help him avoid incorrect manoeuvres
and prevent inconveniences that may jeopardise the machine integrity and eventually result in risks for operators' safety.
If you are still in doubt or have points to clear on machine operation after reading this manual, do not hesitate to contact the
Manufacturer who will be ready to assist you promptly and carefully for better and most efficient machine operation.
Finally, we would like to point out that existing regulations on safety, hygiene at work and environmental protection must always be
adhered to during all the phases of machine operation. The operator must therefore check that the machine be operated
exclusively in optimised safety conditions for both persons and objects.
This manual is to be considered as an integral part of the product. Therefore, along with the Declaration of Conformity, it must be
stored in a safe place where it can be consulted during the entire machine life and passed on to the new owner.
This manual was drawn up according to the regulations existing at the time when it was printed.
The Manufacturer reserves the right to change the machine without having to promptly update this manual. In the event of
disputes, the valid version is the Italian text.
Some of the pictures in this manual show details or accessories which may be different from those fitted in your machine. Components
or guards may have been removed to make images more useful.
1.1 GENERAL
Conventional symbols:
To identify and make different danger types recognisable, the following symbols are used in the manual:
WARNING!
DANGER FOR OPERATORS'
HEALTHAND SAFETY.
WARNING!
RISK OF DAMAGE TO MACHINE OR
DRILL PRODUCT.
In the text, symbols are accompanied by safety warning messages: these are short sentences to further exemplify the type of risk/
danger. Warning texts guarantee the safety of operators and prevent damage to the machine or drill product.
The drawings, pictures and diagrams in this manual are not scaled. They exemplify the information provided in the text and are an
addition to it: they are not meant to illustrate the supplied machine in details. For a more comprehensive overview of the machine,
drawings, pictures and diagrams represent the machine, or parts of it, without the protections or guards in most cases.
Finally, a few words on annexes. As they are photocopies of catalogues, drawings, etc., they have the original ID and page numbers
(when provided with it). If they are not originally provided with a numbering, they are not given one.

USEAND MAINTENANCE
ENGLISH
-
44 cod. G19503380
Definitions:
Below is a list of definitions of the main terminology used in this Manual. Read these definitions carefully before consulting the
Manual.
•OPERATOR: ................................................. The person/s charged with installing, starting up, adjusting, carrying out maintenance,
cleaning, repairing or transporting a machine.
•DANGER ZONE: ........................................... any area inside a/o near a machine in which the presence of an exposed person
constitutes a risk for the safety and health of that person.
•DANGER CONDITION: .................................. Any condition in which an operator is exposed to one or several risks.
•RISK: ............................................................ A combination of likelihood and seriousness of possible injuries or damage to the
operator's health in a danger condition.
•PROTECTIONS ............................................ Safety measures consisting in installation of specific technical systems (guards and
safety devices) to protect operators against dangers.
•GUARD: ........................................................ An element on the machine which is used in a specific way to protect the operator by
means of a physical barrier. Depending on its construction, it can be a shroud, a cover,
a shield, a door, a fence, a guard, a segregation unit, etc.
•EXPOSED PERSON: .................................... Any person who happens to be completely or partially in a danger zone.
•USER: .......................................................... The user is the person or the organization or the firm which has purchased or rented
the machine and intends to use it for the purposes it was conceived for.
•QUALIFIED PERSONNEL: ............................ Those persons who have been specially trained and qualified to carry out interventions
of maintenance or repair requiring a particular knowledge of the machine, its functioning,
safety measures, methods of intervention - and who are in a position to recognize the
potential dangers when using the machine and are able to avoid them.
•TRAINED PERSONNEL: ............................... These are operators that have been informed or trained on the operating tasks and
relating risks.
•AUTHORIZED SERVICE CENTER: ................ The authorized Service Center is a structure legally authorized by the manufacturer
which disposes of personnel specialized and qualified to carry out all the operations of
assistance, maintenance and repair - even of a certain complexity - found necessary to
keep the machine in perfect working order.
Responsibility
The Manufacturer declines any direct or indirect responsibility in the following cases:
- incorrect machine operation for non-intended uses;
- machine operation by unauthorised operators who have not been trained and do not have a driving license;
- non-performance of scheduled maintenance;
- unauthorised changes or work;
- installation of non-genuine and specific spare parts;
- non-observance, either total or partial, of the instructions provided in this manual;
- non-observance, either total or partial, of the instructions provided in this manual;
- failure to apply regulations on safety, hygiene and health at work;
- unscheduled and unpredictable events.
ATTENTION
• Minors, illiterates and persons under altered physical or psychological conditions must not be allowed to operate the machine.
• Operators who do not have a suitable driving license, or who are not properly informed and trained, must not be allowed to operate
the machine.
• The operator must check that the machine operates correctly, and must replace and repair parts subject to wear that may cause
damage.
• The customer should instruct personnel on accident risks, on the operator safety devices provided, on noise emission risks and on
general accident prevention regulations provided for by the international directives and by the law in the country in which the
machines are used.
• In any case, the machine should be used exclusively by skilled operators who will be held to follow scrupulously the technical and
accident-prevention instructions in this manual.
• The Customer is responsible for finding and selecting the category of suitable PPE (Personal Protection Equipment).
• The machine features pictograms which the operator must keep in perfect readable conditions. When no more readable, they must
be replaced as instructed by European regulations.
• It is the user's responsibility to check that the machine is operated only in optimum conditions of safety for people, animals and property.
• Any change made on the machine without authorisation relieves the Manufacturer from any and all responsibility for damage to
objects or injuries to operators or third partiesi.
The Manufacturer declines any and all responsibility for possible incorrect information in this manual if it is due to printing, translation
or transcription errors. If the Manufacturer deems it necessary to provide the Customer with any additional information to the
instruction provided in this instruction manual for operation must be stored with the manual which it is an integral part of.

USEAND MAINTENANCE ENGLISH
-45
cod. G19503380
List of personal protection equipment (PPE) to be used during all the phases of the machine life
Table 1 summarises the PPE (Personal Protection Equipment) to be used during the different phases of machine life (each phase
requires mandatory use of and/or availability of PPE.
The Customer is responsible for finding and selecting the type and category of suitable PPE.
Table 1
Trasportation
Handling
Removal from packaging
Assembly
Routine operation
Adjustments
Cleaning
Maintenance
Disassembly
Demolition
PPE required PPE available or to be used if required PPE not required
The utilised PPE must be CE-marked and be compliant with Directive 89/686/EEC.
The machine life phases (ref. to Table 1) are listed in the table below.
•Transportation:............... Machine transfer from one location to a new one on a suitable vehicle.
•Handling .......................... Machine transfer from and on the transportation vehicle and movements inside the plant.
•Removal from packaging . Removal of all the packaging materials.
•Assembly ........................ All the assembly operations to initially prepare the machine for setup.
•Routine operation .......... The machine intended (or usual) use according to its design, construction and function.
•Adjustments ................... Adjustment, setup and calibration of all those devices that need to be adapted to normal machine
operation.
•Cleaning .......................... Removal of dust, oil and work process residues which may jeopardise correct machine operation and
use as well as the health/safety of operators.
•Maintenance .................. Periodic checking of machine parts which are subject to wear or require replacement.
•Disassembly .................. Complete or partial disassembly of the machine for any reason whatsoever.
•Demolition ...................... Permanent removal of all the machine parts for final machine dismantling in order to enable recycling or
differentiated collection of components according to the methods envisaged by the existing regulations.
ATTENTION
Do not wear protective gloves which may get entangled in the machine moving parts.
Protection
equipment
Safety
footwear
Gloves Goggles Ear
defenders
Mask Hardhat
or helmet
Phase

USEAND MAINTENANCE
ENGLISH
-
46 cod. G19503380
fig. 1
(1)
(2)
(3)
(5)
(7)
(4)
(6)
1.2 GUARANTEE
On delivery, check that the equipment has not been damaged during transport and that the accessories are integral and complete.
POSSIBLE CLAIMS MUST BE PRESENTED IN WRITING WITHIN EIGHT DAYS OF RECEIPT.
The purchaser will enforce his rights on the guarantee only when he has respected the conditions concerning the benefit of the
guarantee, set out in the supply contract.
1.2.1 EXPIRY OF GUARANTEE
Besides what has already been set out in the supply contract, the guarantee expires:
- If the limits set out in the technical data table are overshot.
- If the instructions set out in this booklet have not been carefully followed.
- If the equipment is used badly, defective maintenance or other errors by the client.
- If modifications have been carried out without written authorization of the manufacturer and if non original spare parts have been
used.
1.3 IDENTIFICATION
Each individual machine has an identification plate (Fig. 1)
indicating the following details:
1) Mark and address of the Manufacturer;
2) Type and model of machine;
3) Total unladen mass, in kilograms;
4) Maximum working load capacity, in kilograms (front hopper);
5) Registration of the machine;
6) Year of manufacture;
7) CE mark.
You are advised to note down your data on the form below, along
with the date of purchase (8) and the dealer’s name (9).
8) ____________________
9) ____________________
This information must always be quoted whenever assistance
or spare parts are needed.
ATTENTION
Do not remove, tamper with or make the CE mark affixed on
the machine illegible.
Refer to the information provided on the CE mark for the
manufacturer's contact details (e.g. for requesting spare
parts, etc.).
When the machine is demolished, destroy the CE marking.

USEAND MAINTENANCE ENGLISH
-47
cod. G19503380
2.0 GENERAL SAFETY RULES
7) When using fungicidal chemicals, use suitable means of per-
sonal protection.
8) Danger of getting trapped. Keep away from moving parts.
9) Danger of crushing of the upper limbs while handling mobile
parts.
10)Risk of inhaling harmful sub- stances. Wear a dust mask.
11) Danger of becoming entangled in the fan. Do not remove the
guards and do not come close to the moving parts.
12)Danger of getting squashed. Keep well away from the machine
while it operates.
2.1.3 INDICATOR SIGNALS
13)Wear safety clothing.
14)Greasing point.
15)Coupling point for lifting.
The Manufacturer declines any and all responsibility in the event that the safety pictograms supplied with the
machine are missing, illegible or moved from their original position.
2.1 DANGER AND INDICATOR SIGNALS
The signs described are reproduced on the machine (Fig. 2).
Keep them clean and replace them if they should come off or
become illegible. Carefully read each description and learn their
meanings by heart.
2.1.1 WARNING SIGNALS
1) Before operating, carefully read the instruction booklet.
2) Before carrying out maintenance, stop the machine and
consult the instruction booklet.
2.1.2 WARNING SIGNALS
3) Pipes with high pressure fluids. Take care if flexible pipes break
as oil could spurt. Read the instruction manual.
4) Danger of getting squashed during closure. Keep at a safe
distance from the machine.
5) Danger of falling. Do not climb onto the machine.
6) High noise level. Use suitable ear defenders.
fig. 2
1310
3
47
8
5
611
9
2
1
14
8
14
8
14
15
15
14
14
14
12
12
CENTAURO
CENTAURO / PA2

USEAND MAINTENANCE
ENGLISH
-
48 cod. G19503380
2.2 SAFETY REGULATIONS AND ACCIDENT
PREVENTION
Pay attention to danger signs, where shown, in this booklet.
There are three levels of danger signs:
•DANGER: This sign warns that the operations described cause
serious lesions, death or long term health risks, if they are not
carried out correctly.
•ATTENTION: This sign warns that the operations described
could cause serious lesions, death or long term health risks, if
they are not carried out correctly.
•CAUTION: This sign warns that the operations described could
cause serious damage to the machine. if they are not carried
out correctly.
In order to complete the various levels of danger, the following
describe situations and specific definitions that may directly
involve the machine or persons.
•DANGER ZONE: any area inside a/o near a machine in which
the presence of an exposed person constitutes a risk for the
safety and health of that person.
•EXPOSED PERSON: Any person who happens to be completely
or partially in a danger zone.
•OPERATOR: The person/s charged with installing, starting up,
adjusting, carrying out maintenance, cleaning, repairing or
transporting a machine.
•USER: The user is the person or the organization or the firm
which has purchased or rented the machine and intends to
use it for the purposes it was conceived for.
•SPECIALIZED PERSONNEL: Those persons who have been
specially trained and qualified to carry out interventions of
maintenance or repair requiring a particular knowledge of the
machine, its functioning, safety measures, methods of
intervention - and who are in a position to recognize the potential
dangers when using the machine and are able to avoid them.
•AUTHORIZED SERVICE CENTER: The authorized Service Center
is a structure legally authorized by the manufacturer which
disposes of personnel specialized and qualified to carry out all
the operations of assistance, maintenance and repair - even of
a certain complexity - found necessary to keep the machine in
perfect working order.
Carefully read all the instructions before using the machine; if
in doubt, contact the technicians of the Manufacturer’s dealer.
The manufacturer declines all responsibility for the non-
observance of the safety and accident prevention regulations
described below.
General norms
1) During machine operation, maintenance, repair, handling
and storage, wear suitable personal protection equipment.
2) Maintenance, adjustment and cleaning operations must be
carried out after positioning the machine on the ground (in
stable conditions); the PTO must be disconnected, the motor
of the tractor must be off, the parking brake engaged and the
ignition key disengaged.
3) When operating the machine during the night time or in
reduced visibility conditions, turn on the lighting system of
the tractor.
4) The machine must be operated by one operator only. Any
use other than that intended is considered as incorrect.
5) Pay close attention to the danger signs in this manual and
on the machine.
6) The labels with the instructions attached to the machine give
abbreviated advice for avoiding accidents.
7) Scrupulously observe, with the help of the instructions, the
safety and accident prevention regulations.
8) Avoid touching the moving parts in any way whatsoever.
9) Any work on and adjustment to the machine must always be
done with the engine switched off and the tractor blocked.
10) People or animals must not, under any circumstances be
transported on the equipment.
11) It is strictly prohibited to drive the tractor, or allow it to be
driven, with the equipment attached by persons not in
possession of a driver’s license, inexpert or in poor conditions
of health.
12) Before starting the tractor and the equipment, check that all
safety devices for transport and use are in perfect working
order.
13) Before starting up the equipment, check the area surrounding
the machine to ensure that there are no people, especially
children or pets, nearby, and ensure that you have excellent
visibility.
14) Use suitable clothing. Avoid loose clothing or garments with
parts that could in any way get caught in the rotating or moving
parts of the machine.
15) Before operating the machine, make sure that all the safety
devices are in perfect operating condition and installed
properly. Replace them if they are malfunctioning or are
damaged. Replace it immediately if it presents signs of
deterioration.
16) Before starting work, familiarize yourself with the control
devices and their functions.
17) Only start working with the equipment if all the protective
devices are in perfect condition, installed and in the safe
position.
18) It is absolutely prohibited to stand within the machine’s radius
of action where there are moving parts.
19) It is absolutely forbidden to use the equipment without the
guards and container covers.
20) During operation, the machine may cause excessive dust.
We recommend working with tractors featuring a cabin with
a ventilation system equipped with filters; alternatively, protect
the airways with dust-proof masks or masks equipped with
a filter.
21) Make sure that the machine has not been damaged during
transportation. If this is the case, immediately report the
damage to the Manufacturer.
22) Clean the machine from foreign matter (deposits, tools, misc.
objects) which may jeopardise machine operation or damage
the operator
23) Before leaving the tractor,lower the equipment hooked to the
lifting unit, stop the engine, pull the hand brake and remove
the key from the dashboard, make sure that the chemical
substances safely out of reach.
24) The driver’s seat must never be left when the tractor engine
is running.

USEAND MAINTENANCE ENGLISH
-49
cod. G19503380
25) Before starting the equipment, check that the supporting feet
have been removed from under the machine; check that the
machine has been correctly assembled and regulated; check
that the machine is in perfect working order, and that all the
parts subject to wear and tear are in good condition.
26) Before releasing the equipment from the third point
attachment, put the hoist command lever into the locked
position and lower the support feet.
27) Only operate when visibility is good.
28) All operations must be carried out by expert personnel,
equipped with protective gloves, in a clean and dust-free
environment.
Tractor hitch
1) Hook the equipment to a suitable, sufficiently-powered tractor
by means of the appropriate device (lifter), in conformity with
applicable standards.
2) The class of the equipment attachment pins must be the
same as that of the lifter attachment.
3) Take care when working within the range of the lifting arms
as this is a very dangerous area.
4) Be very careful when hooking and unhooking the equipment.
5) It is absolutely forbidden to stand between the tractor and
linkage for manoeuvring the lifting controls from the outside
(Fig. 3).
6) It is absolutely forbidden to stand in the space between the
tractor and the equipment (Fig. 3) with the engine running.
It is possible to work between the tractor and the equipment
only after the parking brake has been applied and a suitably
sized blocking wedge or stone has been placed under the
wheels.
7) The attaching of additional equipment onto the tractor brings
about a different distribution of weight on the axles. Check
the compatibility of the tractor performance with the weight
that the machine transfers onto the three-point linkage. If in
doubt consult the tractor Manufacturer.
8) Comply with the maximum admissible weight for the axle,
the total mobile weight, transport regulations and the highway
code.
Transport on Road
1) When driving on public roads, be sure to follow the highway
code of the country involved.
2) Any transport accessories must be provided with suitable
signs and guards.
3) It is very important to remember that road holding capacity as
well as direction and braking capacity can be influenced,
sometimes con-siderably, by equipment being either carried
or towed.
4) To work in safety the instructions given in the highway code
should be followed; these prescribe that at least 20% of the
weight of the tractor alone should be borne by the front axle
and that the weight on the arms of the hoist should not be
more than 30% of the weight of the tractor itself.
5) When negotiating curves, be aware of the variation in
centrifugal force exerted in a position other than that of the
center of gravity, with and without the equipment in tow. Also
pay greater attention on sloping roads or ground.
6) For transport, adjust and fasten the lateral lifting arm chains
of the tractor; check that the seed and fertilizer hopper covers
are closed properly; lock the hydraulic lifting control lever.
7) All road transport must only be carried out with the tanks and
tanks empty and at max speed of 25 km/h. For the transport
on the road it must be assured the cover with the appropriate
one pulling of coupling (A, Fig. 4). Periodically, it is necessary
to verify the degree of deterioration of pulling and to the
occurrence to replace it.
8) For displacements beyond the work area, the equipment
must be placed in the transportation position.
9) Upon request the Manufacturer will supply supports and
tables for signaling of dimensions.
10) When the dimensions of carried or partially-carried equipment
conceal the tractor’s signalling and lighting devices, these
must also be installed on the equipment itself, in conformity
with regulations of the highway code of the country involved.
When in operation make sure that the lighting system is in
perfect working order. The transport on the road must be
done with light (B, Fig. 4) turned off. The orientation of the
light (C, Fig. 4) must be done in conformity with regulations
of the highway code of the country involved.
fig. 3
fig. 4 CENTAURO
400/450
A
A
B
C
B
C
CENTAURO
500/600
PA2

USEAND MAINTENANCE
ENGLISH
-
50 cod. G19503380
Safety measures concerning the hydraulics
1) At the moment of connecting the hydraulic tubes to the
hydraulic system of the tractor, make sure that the hydraulic
systems of the operating machine and the tractor are not
under pressure.
2) For the operative hydraulic connections between tractor and
operating machine, the sockets and plugs should be marked
with colours to distinguish them, to avoid them being used
wrongly. There would be a danger of accident if the
connections were to be swapped round.
3) The hydraulic system is under high pressure; because of
the accident risk, when searching for leakage points special
auxiliary instruments should be used.
4) Not to never carry out the search losses with the fingers or
the hands. The liquids that exit from the holes can be nearly
not visible.
5) During transport by road the hydraulic connections between
tractor and operating machine should be disconnected and
secured to the support provided.
6) Do not use vegetable oils under any circumstance. These
could cause a risk of damage to the cylinder gaskets.
7) The operating pressures of the hydraulic system should be
between 100 bars and 180 bars.
8) Never exceed the indicated hydraulic system pressure levels.
9) Check that the quick hook-ups are coupled correctly; parts of
the system could get damaged if they are not.
10) Oil escaping at high pressure can cause skin injury with the
risk of serious wounds and infection. Call a doctor
immediately if such an incident occurs. If the oil with surgical
means is not removed quickly, can take place serious
allergies and/or infections. Therefore, the installation of
hydraulic components in the tractor driver's cab is strictly
forbidden. All the components of the system should be
positioned carefully to avoid parts being damage during use
of the equipment.
11) In case of participation on the hydraulic system, to unload
the hydraulic pressure carrying all the hydraulic commandos
in all the positions some times after to have extinguished the
motor.
Maintenance in safety
During work and maintenance operations, use suitable perso-
nal protection gear:
Overalls Gloves Shoes Goggles Hardhat
1) Do not proceed with maintenance and cleaning if the power
take-off has not been disconnected first, the engine power
off, the hand brake pulled and the tractor blocked with a
wooden block or stone of the right size under the wheels.
2) Periodically check that the bolts and nuts are tight, and if
necessary tighten them again. For this it would be advisable
to use a torque wrench, respecting the values of 53 Nm for
M10 bolts, resistance class 8.8, and 150 Nm for M14 bolts
resistance class 8.8 (Table 2).
3) During assembling, main-tenance, cleaning, fitting, etc., with
the machine raised, place adequate supports under the
equipment as a precaution.
4) The spare parts must correspond to the manufacturer’s
specifications. Use only original spares.
Table 2

USEAND MAINTENANCE ENGLISH
-51
cod. G19503380
3.0 DESCRIPTION OF THE MACHINE
Pneumatic drillmachine for cereals, rape, soya, lucerne and other forage crops to be fitted on folding power harrow and seeding on
minimum tilled soils. The forward placed hopper may be used for spreading fertilizer combining it with a vacuum precision planters.
Cost reduction by time and energy saving and optimisation of the environment health by reducing soil compaction, are always more
considered and appreciated from the farmers by using power harrow/drill combinations:
• Speeds up the job; • Energy saving;
• Money savings; • Soil packed down to a lesser degree;
• Simplified cultivation work; • Soil preparation and planting at the same time;
• Speedier planting work;
• Blends the soil to an optimum degree with the plant residues and stubble.
It is suitable for sowing cereal: wheat, barley, rye, oats, rice.
For minute and forage seeds: rape, clover, alfalfa, rye-grass.
For coarse seeds: soya, peas.
Seeds (fertilizer) are laid down on the ground by means of ploughing devices, planter shoe, and they are distributed continuously.
The quantities to be distributed are controlled by a dosing device driven by an electric motor connected to the tractor speed sensor
(See the Electrical Distribution Control Operation and Maintenance Manual). The arms of the furrowing tools, independent of each
other, dispose of a wide margin of oscillation to adapt to the surface of the ground.
ATTENTION
The machine is suitable only for the uses indicated. The recommended working speed is 6÷8 km/h. The machine must only be
transported by road with the tanks and hoppers empty and at max speed of 25 km/h. Any other use different from that described
in these instructions could cause damage to the machine and represent a serious hazard for the user. The machine must be
operated by qualified operators of the Customer. The operator must wear suitable personal protection equipment (safety
footwear, overalls and gloves, etc.). This machine has been intended for professional use: it must be operated exclusively by
preliminarily educated, trained and authorised operators who hold a regular driving license.
Operating instructions
• The machine was manufactured for dosing and distributing commercial seeds (fertilizer) of standard quality.
• It must be fitted with a soil tilling equipment (rotating harrow), connected to the three-point hook-up of a tractor and operated by an operator.
• The machine is intended for professional users: operation must be allowed to skilled operators only.
• The machine must be operated by one operator only.
• The machine is not intended for purposes other than farming applications.
Conforming machine operation also includes:
• compliance with all the instructions provided in this manual;
• performance of inspection and maintenance operations described in
this manual;
• exclusive use of genuine GASPARDO spare parts.
The machine can to sow on a gradient up to 10%.
The machine’s correct operation is not guaranteed if having to plant on a slope that is more than 10% steep.
We recommend doing the following:
• reduce advancement speed;
• increase the blower’s rotation speed up to maximum power (see table herein);
• frequently check that pipes are not clogged by seeds;
• check the amount of used seeds per planted Ha, corresponds to that set;
• available on request to install the special doser for steep slopes, more information to contact our Technical servicing;
• do not, in any case, work on slopes that jeopardise the machine’s stability.
Additional checks before operation
Below is a list of additional checks required before operating the machine:
• ensure that there are no remarkably big stones or rocks (diameter superior to 8 to 12 cm) on the soil;
• ensure that there are no protruding sections of trees (over 10 cm) having a diameter superior to 8 to 12 cm on the soil;
• ensure that there are no metal elements of any type whatsoever, but especially nets, cables, wire ropes, chains, pipes, etc. on the soil.
The Customer must ensure that Qualified Operators for routine machine operation are suitably trained and prove competent in
carrying out the tasks assigned to them, taking care of their safety and that of third parties. Depending on the qualification level and
tasks assigned, qualified operators must be duly instructed on the machine functions so as to operate and manage it correctly and
guarantee good machine efficiency. Regular operation depends on the correct use and adequate maintenance of the equipment. It
is advisable therefore to observe scrupulously what is described in order to prevent any inconveniences that could prejudicate proper
operation and duration. It is just as important to keep to what is described in this booklet since the Manufacturer declines all
responsibility due to negligence and non-observance of these rules. At any rate the Manufacturer is available to assure immediate
and accurate technical assistance and all that may be necessary for the improved operation and better performance of the equipment.
The machine user shall be liable for damage caused by non-compliance with the instructions hereby.
Max. 10% Max. 10% Max. 10% Max. 10%

USEAND MAINTENANCE
ENGLISH
-
52 cod. G19503380
3.1 TECHNICAL DATA
FRONT TANK U.M. Seed Seed Fertilizant
Load capacity of the hopper [l] (kg) 1260 (1500) 1600 (1920) 1600 (1920)
Transport width [m] 2,38 2,45 2,45
Distribution Electrical Electrical Electrical
Dosers [nr.] 1 2 2
Weight [kg] 530 580 580
Three- point universal joint [nr.] II II II
Dimensions Height [m] 1,54 1,68 1,68
Width [m] 2,38 2,45 2,45
Length [m] 1,30 1,27 1,27
CENTAURO (Power Harrow + Front Tank + Bar of seeds) U.M. mod. 400 mod. 450 mod. 500 mod. 600 -
Transport width [m] 2,45 2,45 2,55 2,55 -
Working width [m] 4,00 4,50 5,00 6,00 -
Weight (Version with shares) [kg] 4780 5170 -
Weight (Version with Corex disc) [kg] 4930 5330 -
Working speed [Km/h] 8 (max)
Acoustic pressure level LpAm (A) (*) [dB] 84,2
BAR OF SEEDS POSTERIOR U.M. mod. 400 mod. 450 mod. 500 mod. 600 -
Transport width [m] 2,45 2,45 2,55 2,55 -
Working width [m] 4,00 4,50 5,00 6,00 -
Row number [nr.] 32 36 40 48 -
Row distance [cm] 12,5 12,5 12,5 12,5 -
Distributors [nr.] 1 1 2 2 -
Weight (Version with shares) [kg] 830 880 -
Weight (Version with disc) [kg] 980 1040 -
HYDRAULICALLY OPERATED FAN - TRACTOR DEPENDENT
Tractor oil delivery [l/min] 32
The pressure of return circuit [bar] 0 (max. 10)
Max. working pressure (hydraulic blower system) [bar] 170
HYDRAULICALLY OPERATED FAN - TRACTOR INDEPENDENT
PTO (rpm) [r.p.m.] 1000
Power take-off [nr.] 1 (front)
Oil hopper capacity [l] 55
Max. working pressure (hydraulic blower system) [bar] 170
TRACTOR SPECIFICATIONS U.M. mod. 400 mod. 450 mod. 500 mod. 600 PA2
Power required [kw] 120÷150 135÷165 135÷185 150÷225 -
Three- point universal joint [nr.] II - III III III III II
Battery voltage [V] 12 12 12 12 12
Tractor pump pressure (max) [bar] 180 180 180 180 180
Tractor hydraulic connections Row marker: nr. 1 double-acting;
Furrower pressure regulation: nr. 1 double-acting;
Hydraulic blower drive: nr. 1 double-acting +
nr. 1 exhaust (without pressure - max 10bar).
12 V electrical connections Lights kit 7-pole connector;
(*) LpA = Continuous equivalent acoustic radiation pressure level (Weighed A) in the “worker’s position”.
The technical data and the models provided must be considered as non binding. We reserve the right to change them without notice.

USEAND MAINTENANCE ENGLISH
-53
cod. G19503380
3.2 HANDLING
If the equipment is to be moved, it is necessary to raise each part and hook it onto the respective mountings shown in (Fig. 5) with
hoisting apparatus of suitable lifting capacity. As this operation is dangerous, it must be carried out by trained, responsible personnel.
The machine weight is shown on the identification label (Fig. 1). The mass of the equipment is shown in the Technical Data table of the
user and maintenance booklet and is determined by the sum of the weight and the load shown in the table.
Stretch the cable to level the machine. The hooking points are shown by the graphic "hook" symbol (14, Fig. 2).
ATTENTION
• Packaging materials (pallets, cartons, etc.) must be disposed of as prescribed by the existing regulations through authorised disposal
companies.
• Parts making up the machine must not be lifted by hooking them up from moving or weak parts such as guards, electrical runways,
pneumatic parts, etc.
• Standing under suspended loads is not allowed; unauthorised personnel are not allowed access to the work sites; it is mandatory to
wear overalls, safety footwear, gloves and a hardhat.
B
A
C
B
AC
fig. 5
CENTAURO
CENTAURO / PA2

USEAND MAINTENANCE
ENGLISH
-
54 cod. G19503380
3.3 ASSEMBLY DRAWING (Fig. 6)
1) Seed hopper;
2) Load bearing structure;
3) Covering hopper;
4) Distributor;
5) Tube for conveying seed;
6) Inspection footboard;
7) Blower pump;
8) Seed covering harrow;
9) Lighting kit;
10) Warning boards;
11) Identification plate;
12) Monitor GENIUS;
13) Electrical motor;
14) Doser;
15) Dosing roller:
> G1000 NORMAL seeds distribution over 200 Kg/Ha;
> N500 NORMAL seeds distribution up to 200 Kg/Ha;
> F25-125 SMALL (fine) seeds distribution;
> G1002 FERTILIZER distribution;
16) Shoe coulter;
17) Disc coulter: A-Single Disc; B-Corex Disc;
18) Depth gauge wheel for disc coulter;
19) Oleodynamic blower drive;
20) Three-way regulator with manometer;
21) Supports feet (bar of seeds posterior).
5
3
4
7
8
fig. 6 10
1
2
9
6
11
mod.CENTAURO400/450
mod. CENTAURO 500/600 - PA2

USEAND MAINTENANCE ENGLISH
-55
cod. G19503380
14
21
12
17 1816
A
B
15
13
G1000 N500 F25-125 G1002
2019

USEAND MAINTENANCE
ENGLISH
-
56 cod. G19503380
3.4 DOSER
The doser (Fig. 7) the most important part for distribution, is
located underneath the seed (fertilizer) hopper.
It is driven by an electric motor connected to the tractor speed
sensor.
In that event, for the metering operation and the metering
adjustment, checking and tests, please refer to the relevant User
and Maintenance Booklet.
The volumetric distributing device, is essentially composed of
four elements for seeds distribution:
A) aluminium monobloc frame;
B) agitator element;
C) dosing rollers;
D) feeler pin.
MONOBLOC FRAME
The monobloc frame is made of aluminium and offers the
following main advantages:
- realization of very high precision and high quality over time;
- resistance to the effects of UV rays or to the problems of harsh
autside temperatures;
- high resistance to corrosion;
- quick simple maintenance: in a few minutes we can completely
remove the components of the doser without fully unscrewing
the screws, using just one spanner.
AGITATOR ELEMENT
Guarantee of continuous feeding to the dosing rollers. The
agitator can be disabled by simply removing the drive belt. To
disable the agitator, lift the round belt above the edge of the drive
pulley (Fig. 8) and, on the opposite side, rotate the dosing roller
in the driving direction. The belt will come off (Fig. 11).
(To fit the belt, see chapter on dosing roller)
DOSING ROLLERS (Fig. 9)
- Large diameter to reduce the number of revolutions and avoid
seed load losses;
- High number of cells arranged in a steggered pattern to
guarantee uninterrupted delivery;
Assembling and disassembling the dosing roller
All the dosing rollers are compact units constructed in a single
block (except for the fine seeds dosing roller, yellow).
Never fit dosing rollers with screws loosening the handwheel!
The radial precision of the wheels, which are calibrated after
assembly, could be damaged!
WARNING
Always use gloves: after calibration, the new dosing rollers
could have sharp edges that might injure the operator!
There are various types of wheels for a wide range of applications,
in 4 different product families (Fig. 9):
C1) 5 wheels, 8 chambers per wheel, (mod. G1000 - red).
Normal seeds distribution over 200 Kg/Ha.
C2) 5 wheels, 16 chambers per wheel (mod. N500 - green).
Normal seeds distribution up to 200 Kg/Ha.
C3) 5 wheels, 32 chambers per wheel, (mod. F25-125 - yellow)
Fine seeds distribution.
C4) 2 wheels, 8 chambers per wheel, (mod. G1002 - red).
Fertilizer distribution.
Use a suitable metering roller with the type of distributed seeds.
fig. 9
C1
C3
C2
fig. 8
C4
fig. 7
C
B
A
B
D
P

USEAND MAINTENANCE ENGLISH
-57
cod. G19503380
Replacing the DOSING ROLLER
Perform this operation while the dosing chamber is empty:
A) Empty hopper;
B) Hopper with product: use the movable panel (P, Fig. 7) to
exclude feeding from the hopper to the doser. Then empty
the dosing chamber.
1) Remove the belt from the agitator and fully disconnect the
metering roller transmission (Fig. 8).
2) Take out the bearing support of the metering roller (G, Fig.
10);
3) Take the metering roller out sideways (H, Fig. 10) ...
To re-assemble, follow the steps in reverse order.
IMPORTANT: before starting seeding, open the panel (P, Fig. 7)
to feed the doser.
FEELER PIN
The feeler unit may also be easily disassembled in a single block in a matter of minutes for cleaning purposes. It consists of 5 single
hatches that are spring-loaded to ensure tight closing. The hatches do not touch the seeding wheel while it is in operation! Thanks
to the separators fixed between one hatch and the next, it is possible to activate each element independently of the others. Moreover,
the separators are shaped in such as way as to act as a shield against foreign bodies that could damage the dosing roller. The
hatches are adjustable, and their shape has been specifically designed to adapt to the seeds.
WARNING
Always use gloves. The new parts especially might have sharp edges that could injure the operator!
1) In order to disassemble the feeler unit, loosen the four nuts of the axles (front and back) (Fig. 11), using a 13 mm spanner ...
2) until it is becomes possible to push out the discs fitted inside, remove them from their seats (Fig. 12) and move the axles.
3) Remove the back part (Fig. 13) of the feeler pin unit, first, followed by the front part.
When the hatch is disassembled, it is also possible to remove the emptying hatch, by
sliding it out from below.
On completion of cleaning, re-assemble the unit by following the above mentioned
steps in reverse order, taking care to position the flat parts of the axles correctly! Put the
feeler pin unit in place. Then slide the washers back in their housing and finally tighten
the nuts by hand.
Once the hatch has been mounted, the elements must be mobile. To check that they
are, simply push them with your fingers (Fig. 14). If they do not move, it is advisable to
disassemble them and clean them.
During re-assembly, before tightening the various parts, ensure that the rear part of
the hatch (on the spring side) is not too high. Install the dosing roller in order to
ensure that the height is correct.
fig. 10
G
H
fig. 11
fig. 13
fig. 12
fig. 14

USEAND MAINTENANCE
ENGLISH
-
58 cod. G19503380
CLEANING SPRING ELEMENTS (SEEDS)
Cleaning spring elements (A, Fig. 15) are used during the
distribution of oily seeds by means of the yellow seeding roller,
mod. F25-125.
The main action of these spring elements is keeping the
chambers of the seeding roller clear so that seed distribution is
regular and constant.
The shaft of the cleaning spring elements is positioned outside
the seed dosing chamber.
When other types of seeds are being distributed, disengage the
cleaning spring elements to avoid undesired wear:
… loosen the knob (B, Fig. 15), remove the levers (C) from their
housing and move them in the direction shown by the arrow.
Wear
When the oil layer is thick, spring elements wear out quite quickly
and they are no longer efficient.
Wear can be easily checked from the outside.
Replacing the spring elements
1) Loosen and remove the knob (B, Fig. 15). Then, move the
lever (C) in the direction shown by the arrow.
2) Extract the seeding roller (Fig. 16) as shown and described
previously.
3) Loosen the M8 nuts (Fig. 17) using the supplied multi-purpose
wrench.
4) Extract the shaft of the spring elements from its housing (Fig.
18).
5) Use the supplied multi-purpose wrench and an Allen wrench
(no. 3) to loosen the fastening screws of the spring elements
as shown in Figure 19.
6) Replace the spring element using genuine spare parts. Then,
assemble the unit back repeating the procedure above in a
reversed sequence.
fig. 18
fig. 19
fig. 15
fig. 17
fig. 16
A
C
B

USEAND MAINTENANCE ENGLISH
-59
cod. G19503380
DISTRIBUTION OF FINE SEEDS
Distribution of quantities lower than 3 kg/ha.
During the dosing test the number of gearbox revolutions is low
because the quantity of product to be distributed is small. This
can result in irregular distribution of the product. If the operator
notes this, he should follow the instructions below.
Considering that every section (A, Fig. 20) of the dosing roller
distributes 20% of the product contained in roller itself, the number
of operating sections can be increase and the gearbox rotation
speed to reduce to obtain more homogeneous distribution.
First, take the dosing roller off the machine. Then, unscrew the
knob (B, Fig. 20) using the supplied wrench and remove the lock
nut (C). Extract the section(s) to be activated and put them back in
their positions (1-2-3-4-5, Fig. 20) turning them by 180°.
When re-assembling the sections, make sure that during
operation the dosing grooves of the active sections are staggered
from one another (D, Fig. 20). This will give continuity to
distribution.
Re-position the lock nut, tighten the knob using the supplied
wrench and assemble the roller back on the machine.
Block the cleaning element in the operating position and make
sure that the springs hook the previously excluded sections (E,
Fig. 20) preventing their rotation and consequently distribution.
Carrying out the dosing test. To rotate the dosing devices, follow
the instructions provided in the Operation and Maintenance
Manual of the Electrical Distribution Control, and make sure that
the real number of operating sections is coherent with the 1
section roller.
To start distribution again using some of the sections or all of
them disassemble the roller and its parts and put them back in
their original position.
1
2
3
4
5
A
C
B
DE
fig. 20
Other manuals for PA2
1
This manual suits for next models
1
Table of contents
Popular Spreader manuals by other brands
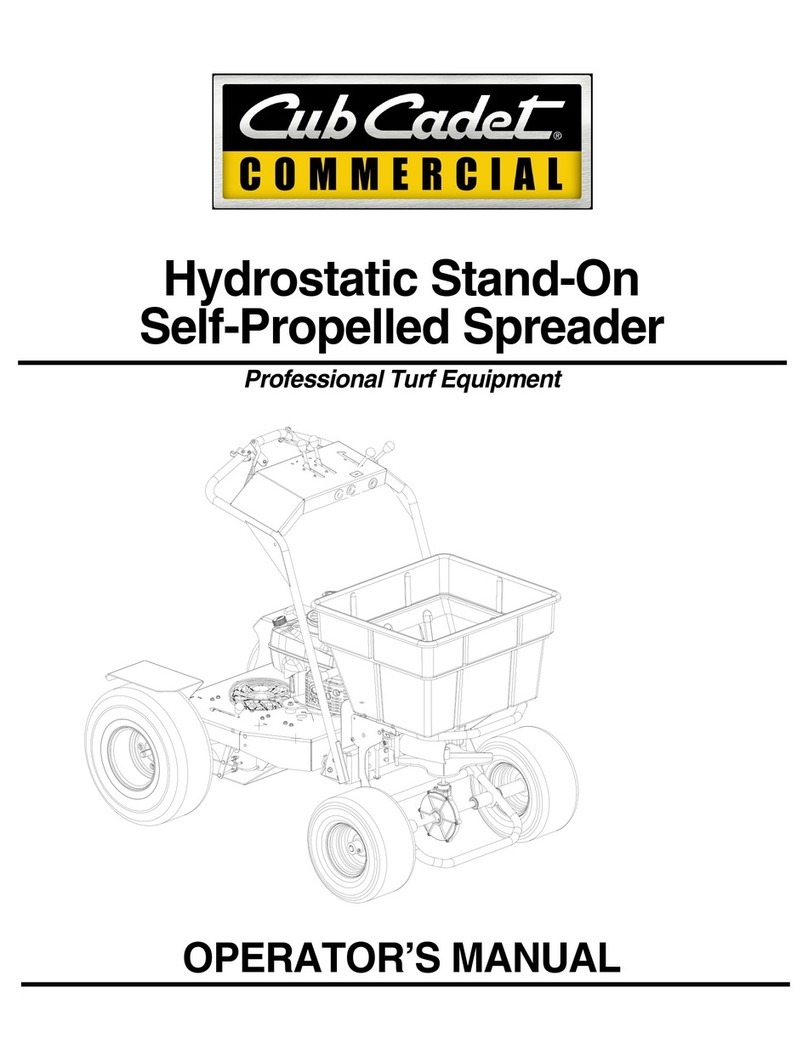
Cub Cadet
Cub Cadet Hydrostatic Stand-On Self-Propelled Spreader Operator's manual
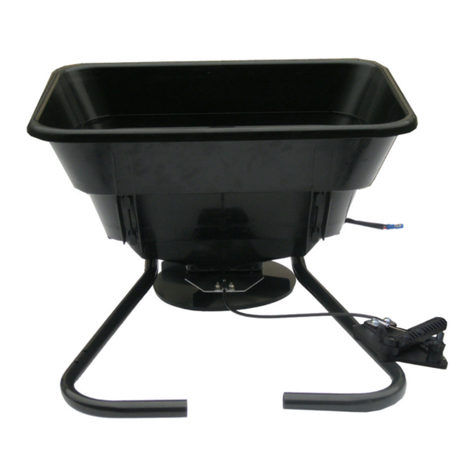
Kellfri
Kellfri 33-JM40 manual
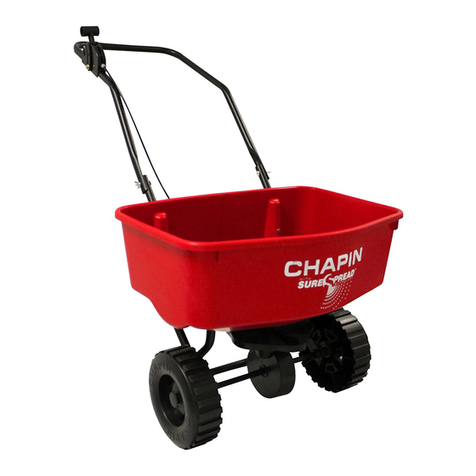
Chapin
Chapin SureSpread 80000 Assembly / operation instructions / parts
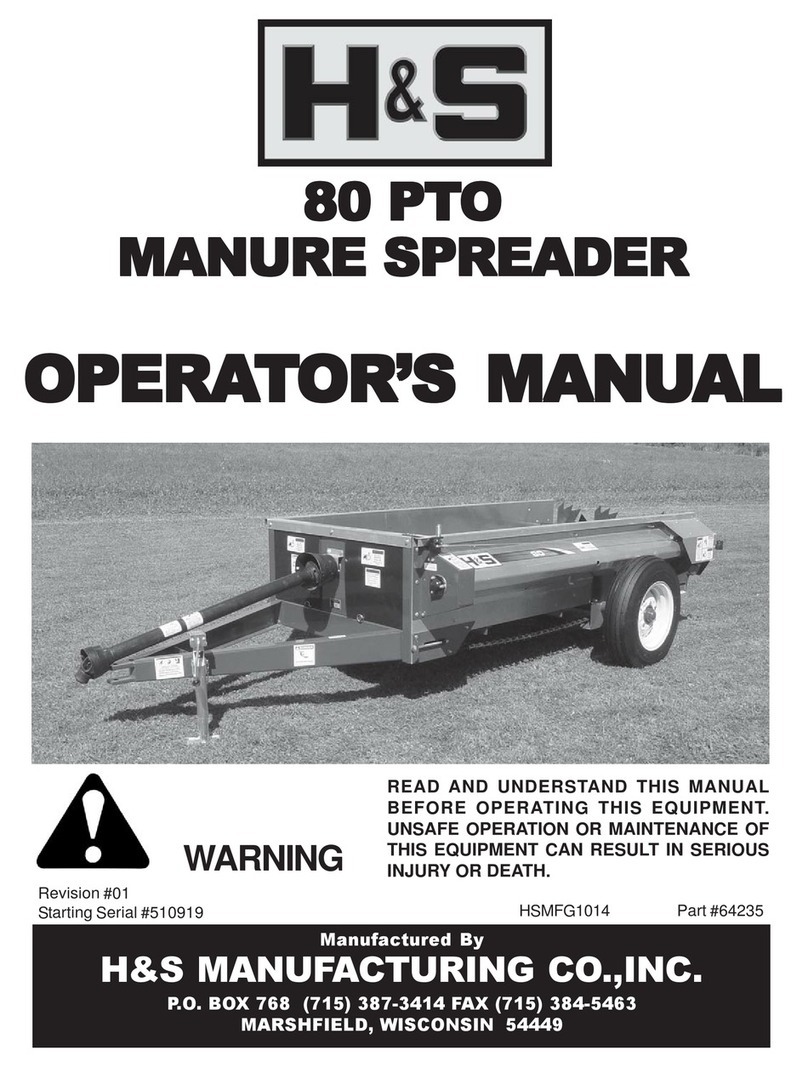
H&S
H&S MS80 Operator's manual
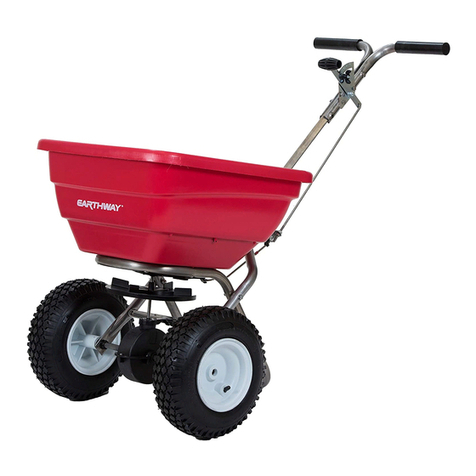
Earth Way
Earth Way FLEX-SELECT F80 Series Assembly and operating instructions

Salt Dogg
Salt Dogg TGS01B installation instructions
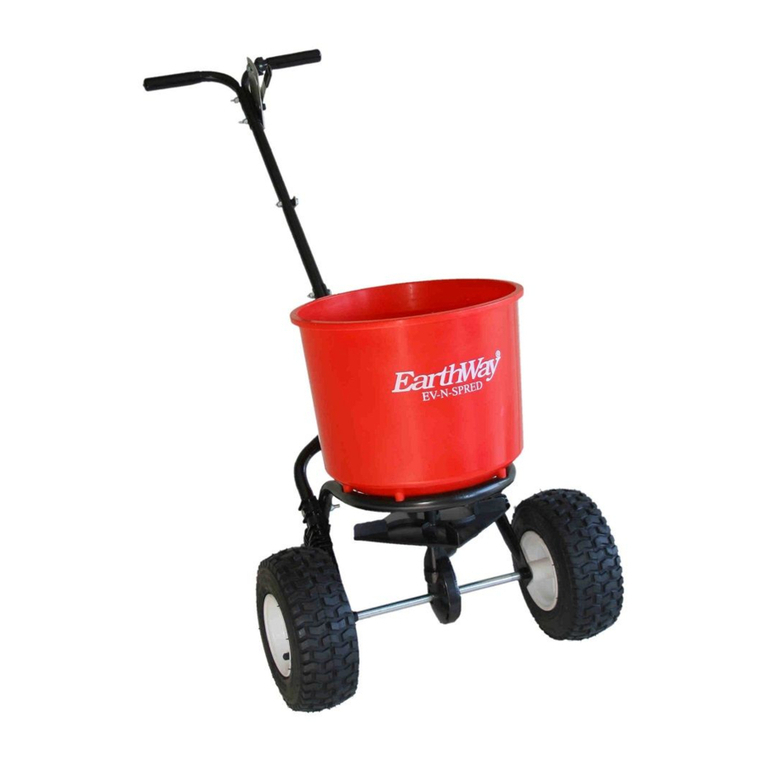
Earth Way
Earth Way 2600A-Plus Estate Assembly and operating instructions
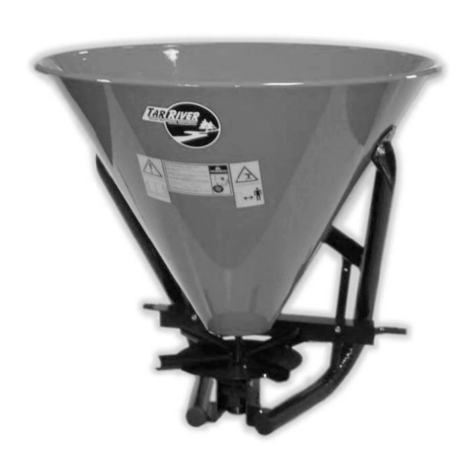
Tar River
Tar River SSC-100 Operator's manual
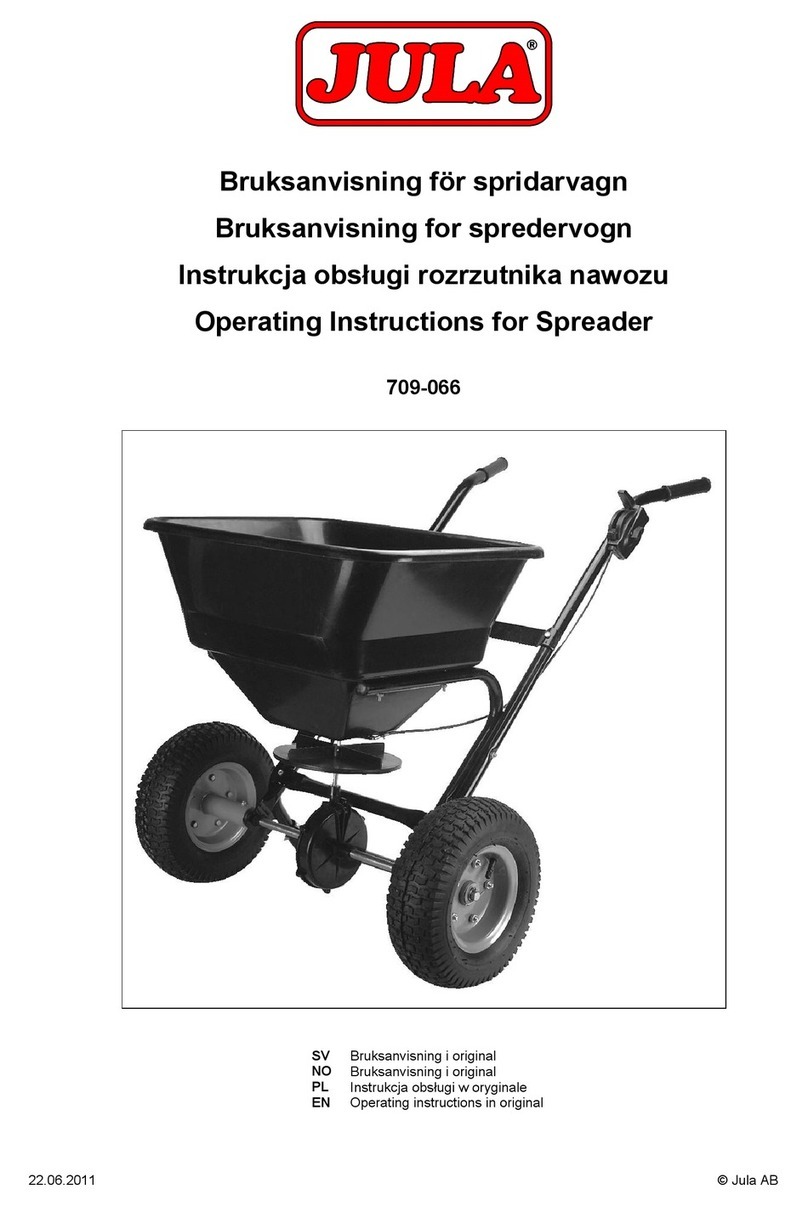
Jula
Jula 709-066 operating instructions
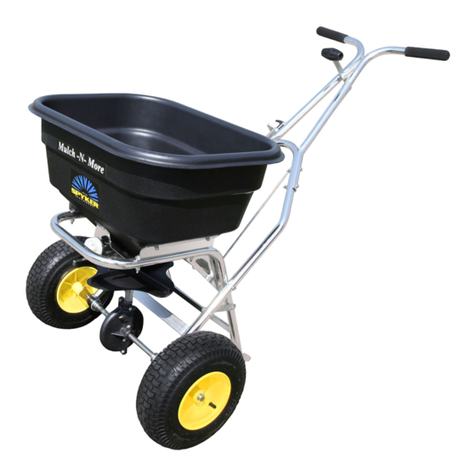
SPYKER
SPYKER PRO Series Operator's manual
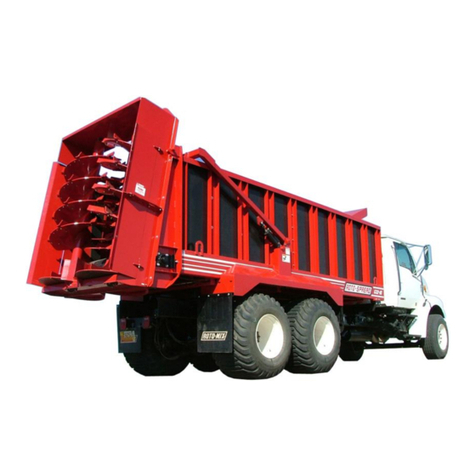
Roto-Spread
Roto-Spread 532-16 Operation and parts manual
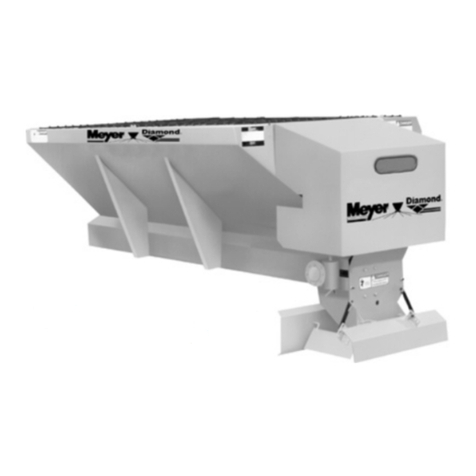
Meyer
Meyer Diamond 62209 Installation and operating instruction manual