GE Ajax DPC 2804 LE Manual

GE Oil & Gas
Ajax
®
Compressor
Ajax DPC 2804 LE / Non-LE Operation & Maintenance Manual

GE Oil & Gas
GE Oil & Gas Compression Systems, LLC is the entity owning this Installation, Operating and
Maintenance Manual.
GE Oil & Gas Compression Systems, LLC can be contacted as follows:
Phone: +1-866-754-3562
Website: www.geoilandgas.com
Cameron is not affiliated with this manual, and any reference to Cameron or Cameron International
herein is unintentional.

GE Oil & Gas
Revision History
Rev
No.
Rev Description Date
Revised
By
0
Initial Release
11/09/2012
Prabhu
1
GE Cover Page Update
7/9/2014
Prabhu
2
GE – Contact Information & Lubrication System (Baffle) Update
09/03/2015
Prabhu
3
Content added in Sections, General Data, Fuel System & Power Cylinder
10/19/2015
Prabhu
4Sealing Compound Instructions added in Section : 6 03/22/2016Prabhu


Table of Contents
Table of Contents
Table of Contents 3
Section 1: Introduction 13
Message from GE Oil & Gas Compression Systems LLC 13
GE Oil & Gas Compression Systems LLC Policies 13
Standards 13
Our Quality Policy 13
Warranties To Original Purchaser (Non-Transferable) 14
Prerequisites 15
Additional Information 16
GE Oil & Gas Compression Systems LLC Contact Information 16
Section 2: Safety Information 17
Introduction 17
Danger, Caution and Note Symbols 17
DANGER SYMBOL 17
CAUTION SYMBOL 17
NOTE SYMBOL 17
Safety Decals 18
Danger, Caution and Note Decals 18
Figure 2-1 Safety Decals 19
Figure 2-2 Safety Decals 20
General Precautions 21
Engine Maintenance Precautions 21
Compressor Maintenance 22
Section 3: Warranty 25
Warranties to Original Purchaser (Non-Transferable) 25
Section 4: Basic Design and Application 27
Basic Design 27
Engine & Frame 27
Piston 27
Power Cylinder 27
AJAX®3

Table of Contents
Jet Cell 27
Compressor Cylinder 27
Lubrication System 27
Piston Rods 27
Fuel System 27
Figure 4-1: 2804 Engine Compressor 28
Basic Application 28
Two-Cycle Principle of Operation 28
Figure 4-2: Compression 29
Figure 4-3: Power 29
Figure 4-4: Scavenging 30
Section 5: General Data 31
General Data 31
Table 5-1 General 31
Table 5-2 Power and RPMs 31
Table 5-3 Basic Specifications - Engine 31
Table 5-4 Compressor 32
Table 5-5 Auxiliary Systems 32
Table 5-6 Estimated Weighs & Dimensions 32
Table 5-7 Engine Component Dimensional & Clearance Data 32
Table 5-8 Compressor Component Dimensional and Clearance Data 33
Table 5-9 Torque Table for Critical Ajax Fasteners 33
Table 5-10 General Torque Table for Fasteners (for use when a specific torque is not specified) 35
Clearance and Torque 37
Figure 5-1 Crankcase and Main Bearing Journal Group 37
Figure 5-2 Power Cylinder Group 38
Figure 5-3 Power Piston, Crosshead, and Connecting Rod Group 39
Figure 5-4 Compressor Crosshead and Connection Rod Group 40
Ajax Engine Compressor Noise Data 40
Table 5-11 Sound Pressure Levels 2804LE 40
Table 5-12 Sound Pressure Levels Vs. Frequencies - 2804LE 41
AJAX®4

Table of Contents
Special Tools 41
Figure 5-5: Special Tools 41
Section 6: Unit Installation 43
Installation Design for Permanent Ajax Compressor Packages 43
Foundation 43
Figure 6-1: Canister Bolt Detail 44
Preparation of the Foundation and Skid for Grouting 44
Setting the Engine Compressor 45
Sheave Alignment Procedure 46
Figure 6-2: Sheave Alignment Procedure 46
Grout 47
Table 6-1: Grout Compressive Strength Requirement Estimates (for reference only) 47
Final Grouting Instructions 47
Setting an Inertia-Base AJAX Compressor Unit 47
Figure 6-3: Typical Concrete-filled AJAX Inertia-base Skid 48
Figure 6-4: Typical Pit Dimensions for Inertia-base Units 49
Figure 6-5: Recommended Pit Depth and Sand Pad Specification 50
Setting Inertia-Base Compressor Unit and Cooler: 50
Figure 6-6: Recommended Sand Placement following Unit Placement 51
Fabricated Piping Assembly 51
Keyless Flywheel Installation and Ignition Timing 51
Installation 51
Figure 6-7: Flywheel Cross-Section 52
Finding TDC and Timing Degree Marks 53
Setting Timing of the Flywheel 54
Installation of Sheave and Flywheel 54
Installation 54
Table 6-2: Screw Tightening Torques, Sheave and Flywheel 55
Figure 6-8: Flywheel Tolerances 56
Removal 56
Re-Installation 56
AJAX®5

Table of Contents
Field Connections 56
Fuel Gas Piping 56
Figure 6-9: Typical 2804 Starter/Fuel Gas Piping 57
Air Starting System 57
General Information 58
Product Identification 58
Unit Specific Model # and Serial # 58
Table 6-5: Starter Motor Pressure Ratings and Part Numbers 58
Figure 6-10: Starter Motor Diagram 59
Air Starter Motor Precautions 59
Exhaust System 60
Exhaust Pipe and Mufflers 60
Exhaust Temperature Shutdown Settings 60
Sealing Electrical Fittings in Hazardous Locations using CHICO A Sealing Compound 61
Installation 61
Dam: 61
Use the EYS-TOOL-KIT to pack a proper fiber dam (do not use metal tools). Proceed as follows: 61
Compound: 61
Follow these instructions carefully: 61
For Applications Involving Groups C and D 62
For Group B Applications 62
Section 7: Unit Start-Up 63
General Information 63
Overview 63
Power Cylinder Pre-Start-up Servicing 63
Compressor Cylinder Pre-Start-up Servicing 64
Compressor Purging 65
Start-Up Procedure (with bypass) 66
Start-Up Procedure (without bypass) 68
Section 8: Lubrication Systems 71
General 71
AJAX®6

Table of Contents
Crankcase Lubrication System 71
Crankcase Oil Level Control 71
Figure 8-1: Oil Level at the center of the sight glass 71
Oil Control Baffle 72
Figure 8-2: Oil Control Baffle 72
Function and Design 72
Notes and Precautions: 72
Frame Oil Level 72
Baffle Maintenance 73
Figure 8-3: Cylinder 3 Shown, Typical Configuration at Cylinder Locations 1, 2, 4 73
Table 8-1: Baffle Fastener Torque table 73
Crankcase Oil Maintenance 74
Figure 8-4: Frame, Crosshead Guide, & Scavenging Chamber Drains 75
Figure 8-5: Lube Oil from Frame Mounted Supply Reservoir 76
Figure 8-6: Lube Oil from Frame Mounted Supply Reservoir 77
Lubrication System Components 77
SMX Divider Valve 77
Base 78
Table 8-2: Metering Elements 78
Table 8-3: SMX Divider Valve Specifications 78
DNFT - LED Digital No-Flow Timer 79
Table 8-4: DNFT-LED Specifications 79
DNFT-LED Operation 79
Power Cylinder Lubrication 80
Power Cylinder Lubrication Rates(for DPC-2800 Series Compressors) 80
Table 8-5: Lubrication Rates - DPC-2804 & LE 80
Lubricating Oil Recommendations for Ajax Engine-Compressors (Ajax ES-1006) 81
General 81
Quality and Performance 81
General Specification 81
Table 8-6:Physical Properties of Recommended Oil 81
AJAX®7

Table of Contents
Ash Level 81
Viscosity Requirements 81
Figure 8-7: Oil Selection for Ambient Temperature 82
Low Temperature Operation Procedures 82
Table 8-7: Low Overnight Temperature Starting Chart 83
Crossheads 83
Section 9: Fuel System 85
Operating Instructions for plunger type, spill-port gas injection systems 85
General Description 85
Figure 9-1: Fuel System 85
Operation of the system 86
Figure 9-2: Fuel Suction Stroke 86
Hydraulic Fluid 87
Fluid supply Tank 87
Pump Assembly 87
Flow Control Valve 87
Injection Valve Assembly 87
Bleeder Cock 87
Bleeding of Air Before Starting 88
Gas Pressure 88
Adjusting Fuel Injection Valves 88
Figure 9-3 Fuel Injection Valve adjustments 88
Gas Injection Timing Instructions 89
Checking the gas injection timing on the DPC-2804LE engine 89
Figure 9-4: 2804LE Crankshaft with Straight Edge and Level Vial 89
Figure 9-5: View Looking from Flywheel Towards Control Box 90
Figure 9-6: Marked Keyway Locations 90
Ajax Jet Cell Operation and Maintenance 91
Jet Cell Operation 91
Ignition Timing 91
Maintenance 92
AJAX®8

Table of Contents
Spark Plugs 92
Fuel Admission Check Valves 93
Section 10: Cooling System 95
Cooling System 95
Figure 10-1 Engine Coolant Temperature 95
Compressor Cylinder Cooling 96
Precautions 96
Figure 10-2: Package Coolant Piping 97
Precautions 97
Belt Tensioning Procedure - Goulds Pump 98
Figure 10-3: Belt Tensioning Procedure - Goulds Pump 98
Figure 10-4: Belt Tensioning Procedure - Goulds Pump 99
Belt Tensioning Procedure 99
Belt Tensioning Procedure - Peerless Pump 100
Figure 10-5: Belt Tensioning Procedure - Peerless Pump 100
Figure 10-6: Belt Tensioning Procedure - Peerless Pump 100
Belt Tensioning Procedure 100
Cooler 101
Cooler Operation and Maintenance 101
Fan and Drive 101
Lubrication 101
Tube Cleaning 102
Plug Leaks 102
Tube Leaks 102
Section 11: Power Cylinder Assembly 103
Power Cylinder 103
Power Cylinder Wear 103
Air Intake Check Valves 103
Piston and Piston Rings, Power End 103
Figure 11-1: Engine Piston Ring Tapered Face 105
Figure 11-2: Engine Piston Ring Installation 105
AJAX®9

Table of Contents
Power Piston Striking Clearance (Non-LE) 105
Engine Piston Rod Stuffing Box 106
Packing ring installation 106
Figure 11-3: Packing ring installation 106
Compressor piston rod stuffing box 107
Packing ring installation 107
Figure 11-4: Packing ring installation 107
Ajax Power Cylinder Balancing 107
Ajax Low Emissions Retrofit Conversions 108
Ajax Low Emissions Retrofit Conversions, 13-1/4 inch and 15 inch Bores - Assembly Procedure 108
Figure 11-5: Clearance Between the Piston and Head 109
Gas Cam Timing 109
Figure 11-6: Control Box and Cams 110
Ignition Timing 110
Igniter Assembly Installation 110
Figure 11-7: Igniter Assembly 111
Accessories 111
Spark plugs 111
Air intake filter 111
Breather cap 112
Main Bearing & Crankshaft Installation 112
Main Bearing Installation 112
Figure 11-8: DPC-2804 Series Main Bearing Installation 112
Crankshaft Installation 113
Figure 11-9: DPC-2804 Series Crankshaft Installation and Orientation 113
Figure 11-10: Lowering the Crankshaft into the Frame 114
Main/Thrust Bearing Installation 114
Bearing Clearances 114
Figure 11-11: Plastigage® Measurement 115
Crankshaft Web Deflection 115
Figure 11-12: Compressor Pins, Center Main, for 3- and 4-Throw Crankshafts 116
AJAX®10

Table of Contents
Gas Injection Valves 117
Preventive Maintenance 117
Section 12: Compressor Cylinder Assembly 119
Performance 119
Clearance Adjustment - Compressor 119
Performance Curves - Compressor 119
Single Acting Operation 119
Hydrogen Sulfide Gas 120
Compressor Cylinder Maintenance 120
Compressor Cylinder Bodies 120
Cylinder Groups 120
Slip Liners 120
Shrink Liners 120
Compressor Pistons 120
Compressor Piston Rings 121
Table 12-1: Piston Ring Clearance 121
Compressor Piston Rods 121
Compressor Pressure Packing 121
Compressor Valves 122
Compressor Cylinder and Pressure Packing Lubrication 123
Compressor Lubrication 123
Packing Lubrication Quantities 124
Fire Resistant Lubricants 124
Section 13: Ignition 127
Altronic III Ignition - DPC-2804LE 127
Installation instructions 127
Engine 127
Rotation 127
Flange-Mount Unit 127
Primary Wiring 128
Table 13-1: Primary Wiring 128
AJAX®11

Table of Contents
Secondary Wiring 128
Dual Coils 128
Section 14: IGTB Governor 131
General 131
IGTB Governor 131
Figure 14-1 IGTB Governor 131
Table 14-1: RPM, Voltage, Pressure 131
Problem Diagnostics 132
Table 14-2: Problem Diagnostics 132
Section 15: Servicing for Extended Periods of Storage 135
Preparing For Extended Usage 135
Servicing After Extended Periods In Storage 136
Section 16: Preventive Maintenance Program 139
Preventive Maintenance 139
Section 17: Engineering Standards 143
Contents 143
ES 1002: LUBRICATION RECOMMENDATIONS FOR SUPERIOR® RECIPROCATING
COMPRESSORS. 143
ES 1006: LUBRICATING OIL RECOMMENDATIONS FOR AJAX ENGINES - COMPRESSORS. 143
ES 4025: CRANKSHAFT WEB DEFLECTIONS FOR THREE AND FOUR CYLINDER AJAX
ENGINES 143
Section 18: Technical Documentation 161
Contents 161
1. TIB 061013 Catalytic Converter Installation and Maintenance instructions 161
2. TIB-AJ-1003: Ajax Non-LE, setting power piston crown height "striking clearance". 161
AJAX®12

Section 1: Introduction
Section 1: Introduction
Message from GE Oil & Gas Compression Systems LLC
Thank you, for purchasing GE Oil & Gas Compression Systems LLC equipment! This Service Manual con-
tains safety, operating and basic maintenance instructions for the AJAX series compressor frames.
GE Oil & Gas Compression Systems LLC is committed to continuous improvements and design advancements.
Because of this commitment, changes may occur in your compressor frame that may not appear in this instruction
manual. Photographs or illustrations in this manual show details or options may not appear on your compressor frame.
Guards, covers or other protective mechanisms may have been removed for explanatory purposes. Any time a
question arises concerning your compressor or this instruction manual, please contact GE Oil & Gas Compression
Systems LLC for the latest available information.
It is very important that personnel associated with operation maintenance of the AJAX series compressor read this
manual and support documentation. Keep this manual with related literature and compressor information. Store it so it
is easily found by maintenance or service personnel. It is also important that users carefully study the safety
information provided in Section 2. Always use good safety practices at all times to prevent injury to personnel or
damage to equipment.
THIS MANUAL CONTAINS CONFIDENTIAL AND PROPRIETARY INFORMATION FROM GE OIL & GAS
COMPRESSION SYSTEMS LLC. THIS MANUAL IS GIVEN TO USERS FOR THE PURPOSE OF PROVIDING
INFORMATION TO FACILITATE USE AND MAINTENANCE OF AJAX SERIES COMPRESSOR FRAMES
PURCHASED FROM GE OIL & GAS COMPRESSION SYSTEMS LLC. BY RECEIVING THIS DOCUMENT,
YOU AGREE NOT TO USE SUCH CONFIDENTIAL INFORMATION FOR ANY PURPOSE OTHER THAN
PURPOSE STATED HEREIN AND FUTHER AGREE NOT TO DISCLOSE SUCH INFORMATION TO
OTHERS EXCEPT IN ACCORDANCE WITH THE PURPOSE STATED HEREIN.
All specifications and ratings are subject to change without notice. AJAX is a trademark of GE Oil & Gas Compression
Systems LLC.
GE Oil & Gas Compression Systems LLC Policies
Standards
GE Oil & Gas Compression Systems LLC has developed several standards for our compressor addressing cooling
water quality, lubrication, and packaging. GE Oil & Gas Compression Systems LLC recommends that users of AJAX
compressors understand and follow these standards to get the best performance possible from the equipment. GE Oil
& Gas Compression Systems LLC also recommends that oil and gas production service packagers follow the
guidelines for prime movers described in the American Petroleum Institute’s Specification for Packaged Reciprocating
Compressors for Oil and Gas Production Services (ISO13631). American Petroleum Institute web address;
http://www.api.org will default you to http://www.global.ihs.com. You can call 1-800-854-7179 ext. 7969 for copies of
ISO 13631.
Our Quality Policy
All GE Oil & Gas Compression Systems LLC employees will work to understand and to meet or exceed our
customer’s expectations. Customers include purchasers of goods and services, co-workers, other departments and
suppliers. All employees will correctly and efficiently perform their respective functions in accordance with established
AJAX®13

Warranties To Original Purchaser (Non-Transferable)
requirements, and identify needed changes. Providing goods, services and communications with ever-increasing
quality and value for our customers is a continuous business process in our company.
Warranties To Original Purchaser (Non-Transferable)
a. "Material and Workmanship Warranty": The Seller warrants to the Purchaser that the Equipment of Seller's own
manufacture to be supplied hereunder will be complete in all its parts, and, for the *Warranty Period - The
warranty period shall extend for 12 months from date of start-up, but shall not exceed 18 months from date of
shipment from factory. Warranty Period specified will be free from defects in material or workmanship caused
by the Seller and arising under normal and proper operating conditions; and that such Equipment will be
delivered free from any lawful security interest or other lien or encumbrance known to the Seller, except
security interests or other liens or encumbrances arising hereunder. The obligation of the Seller and the
Purchaser's sole and exclusive remedy hereunder shall be limited at the Seller's option:
1. To replacement or repair of any Equipment or parts thereof which are returned to the Seller's works
within the Warranty Period, transportation charges prepaid.
2. Should the Equipment or parts thereof be determined by the Seller to be so defective, however, as to
preclude the remedying of warranty defects by replacement or repair, the Purchaser's sole and exclusive
remedy shall then be a refund of the purchase price, less a reasonable charge for any utilization of the
Equipment by Purchaser.
3. Notwithstanding the foregoing, the Seller shall have no obligation as a result of improper storage,
installation, repairs or modifications not made by the Seller, or as a result of removal, improper use, or
misapplication of the Equipment after it has been delivered to the Purchaser.
4. Purchaser shall pay freight charges in connection with the return or replacement of the defective Equip-
ment or parts.
b. "Performance Warranty": The Seller warrants that the Equipment of its own manufacture, when shipped and/or
installed, will operate within any performance characteristics which are expressly specified herein as a
performance guarantee. Any performance characteristics indicated herein which are not expressly stated as
guarantees are expected, "but not guaranteed". When factory testing is conducted for measuring and
performance guarantee of the Equipment purchased, then certified test results verifying any such guarantees
shall be considered both by the Purchaser and the Seller as conclusive. The Purchaser may have a
representative present when such factory tests are conducted, if requested at the time an order is placed.
Should Purchaser desire to conduct a field performance test to verify any performance guarantee, such test
must be conducted by Purchaser, at his expense, within thirty (30) days from the date of initial start-up of the
Equipment, and in accordance with the appropriate ASME Power Test Code, except as otherwise agreed in
writing by Seller. Seller shall be entitled to have a representative or representatives present to witness such
test and Purchaser shall reimburse Seller for the time and expense of such representatives at the Seller's
service rates then in effect at the time of the test. Purchaser shall give Seller fifteen (15) days written notice
prior to the date Purchaser intends to commence such test. If the field performance test is not conducted within
the aforesaid period all performance guarantees shall be deemed to have been met. In the event any Equipment
performance guarantee which is to be verified by the field performance test is not successfully demonstrated
within thirty (30) days from the commencement of such test, the obligation of the Seller and the Purchaser's
sole and exclusive remedy hereunder shall be that set forth in paragraph (a) above.
AJAX®14

Prerequisites
c. "OSHA" Warranty": The Seller warrants for installations within the United States that Equipment of its own
manufacture, when shipped, will be in compliance with the Occupational Safety and Health Act, and any and all
amendments thereto and regulations promulgated thereunder that may be in effect as of the date of the Seller's
quotation insofar as said law and regulations may pertain to the physical characteristics of the Equipment
"provided however", the Seller does not warrant such compliance with respect to the circumstances of use of
said Equipment and "provided further", the Seller makes no warranty with respect to the noise level of said
Equipment, when put into operation, since such noise levels will be influenced by and dependent upon the
environment into which the Equipment may be placed. The Seller's obligation and the Purchaser's sole remedy
with respect to this warranty shall be providing notice of any such non-compliance is given within one year from
the date of delivery of said Equipment to Purchaser, to repair or replace any part of said Equipment that is
proven to Seller's satisfaction not to have been in compliance with the Act as amended and regulations thereto
in effect as of the date of quotation or, if it be determined by Seller that the Equipment or parts thereof cannot be
repaired or replaced in such a manner as to put the Equipment in compliance, Purchaser's sole and exclusive
remedy shall then be a refund of the purchase price less a reasonable charge for any utilization of the
Equipment by Purchaser. Purchaser shall pay freight charges in connection with the return or replacement of
any Equipment or parts that are found not to be in compliance.Notwithstanding the foregoing, the Seller shall
have no obligation under this warranty as a result of installation, repairs or modifications not made by the Seller,
or as a result of removal, improper use, improper operation, or mis-application of the Equipment after it has been
delivered to the Purchaser.
d. "Warranty As To Equipment Not Made By The Seller": Equipment parts and accessories made by other
manufacturers and supplied hereunder by the Seller are warranted only to the extent of the original
manufacturer's warranty to the Seller.
e. "EXCEPT AS SET FORTH HEREIN, AND EXCEPT AS TO TITLE IT IS EXPRESSLY AGREED":
"THAT THERE IS NO IMPLIED WARRANTY OF MERCHANTABILITY, NOT OTHER WARRANTY,
EXPRESS, IMPLIED, OR STATUTORY, NOR ANY AFFIRMATION OF FACT, OR PROMISE BY THE
SELLER WITH REFERENCE TO THE EQUIPMENT OR PARTS THEREOF, OR OTHERWISE, WHICH
EXTENDS BEYOND THE DESCRIPTION OF THE EQUIPMENT AS SET FORTH HEREIN, AND (2) THAT
THE PURCHASER ACKNOWLEDGES THAT IT IS PURCHASING THE EQUIPMENT SOLELY ON THE
BASIS OF THE COMMITMENTS OF THE SELLER EXPRESSLY SET FORTH HEREIN".
DAMAGES. "IN NO EVENT SHALL SELLER BE LIABLE FOR SPECIAL, CONSEQUENTIAL OR
INCIDENTAL DAMAGES, NOR FOR LOSS OF ANTICIPATED PROFITS NOR FOR LOSS OF USE OF
ANY EQUIPMENT, INSTALLATION SYSTEM, OPERATION OR SERVICE INTO WHICH THE GOODS
OR PARTS MAY BE PUT, OR WITH RESPECT TO WHICH ANY SERVICES MAY BE PERFORMED BY
SELLER". "THIS LIMITATION ON SELLER'S LIABILITY SHALL APPLY TO ANY LIABILITY FOR DEFAULT
UNDER OR IN CONNECTION WITH THE GOODS, PARTS OF UNIT SALES OR SERVICES DELIVERED
HEREUNDER, WHETHER BASED ON WARRANTY, FAILURE OF OR DELAY IN DELIVERY OR
OTHERWISE". "ANY ACTION FOR BREACH OF CONTRACT HEREUNDER MUST BE COMMENCED
WITHIN ONE YEAR AFTER THE CAUSE OF ACTION HAS ACCRUED".
Prerequisites
Personnel using this manual should be familiar with compressor systems, standard mechanical service tools, and
compressor terminology. Service personnel should have adequate experience in good maintenance and
troubleshooting techniques. GE Oil & Gas Compression Systems LLC recommends that all personnel using this
manual should complete GE Oil & Gas Compression Systems LLC’s AJAX Reciprocating Compressor
Training. Training includes the following:
AJAX®15

Additional Information
• Frame, crosshead guide, and lubrication systems
• Compressor details including: rings, rider bands, pressure packings, valves, and unloaders
• Support systems to include: Coolers, water pumps, and control systems
• Description of installation, inspection, and set up procedures for rod run out, web deflection, coupling alignment
• Description of recommended operational procedures include: startup, normal & emergency shutdown and
compressor performance control
• Description and application of recommended maintenance: maintenance, critical repairs, and troubleshooting
For training, contact the GE Oil & Gas Compression Systems LLC’s Learning Center by phone: 713-354-1296 or
by email: recip.tlc@ge.com.
Additional Information
Unrestricted copies of Service Bulletins are available at the GE Oil & Gas Compression Systems LLC web site. You
must have Adobe® Acrobat® Reader (version 6.0 or later) to view the bulletins.
GE Oil & Gas Compression Systems LLC Contact Information
For parts and customer service, contact by phone: 1-877-300-2550.
AJAX®16

Section 2: Safety Information
Section 2: Safety Information
Introduction
These safety instructions and procedures are intended to help prevent injury in the operation and maintenance of Ajax
engines, compressors, and auxiliary equipment. These safety procedures should not be considered as the only
precautions to be taken. Good judgment and careful safety practices should always be used.
Do not operate or attempt to repair this equipment unless you have had the proper training approved by
Ajax Division, GE Oil & Gas Compression Systems LLC. For training information, contact GE Oil & Gas
Compression Systems LLC’s Learning Center by phone: 713-354-1296 or by email: recip.tlc@ge.com.
Danger, Caution and Note Symbols
DANGER SYMBOL
A DANGER Symbol, indicates that if the specified precaution is not heeded, there is a substantial risk of serious injury
or death along with damage to property. A DANGER may appear as follows:
CAUTION SYMBOL
A CAUTION Symbol, indicates that if the specified precaution is not heeded, damage to equipment and/or personal
injury may result. A CAUTION may appear as follows:
NOTE SYMBOL
A NOTE Symbol, indicates an essential operating procedure or condition which must be highlighted. A NOTICE may
appear as follows:
Some general precautions are listed in the following pages. Make sure that all personnel read these precautions and
adhere to them.
AJAX®17

Safety Decals
Safety Decals
Danger, Caution and Note Decals
Danger, Caution, and Notice decals will be placed so that they are visible to the operator while the engine is running.
The Ajax 2804LE units have the following decals:
AJAX®18
This manual suits for next models
1
Table of contents
Other GE Air Compressor manuals
Popular Air Compressor manuals by other brands
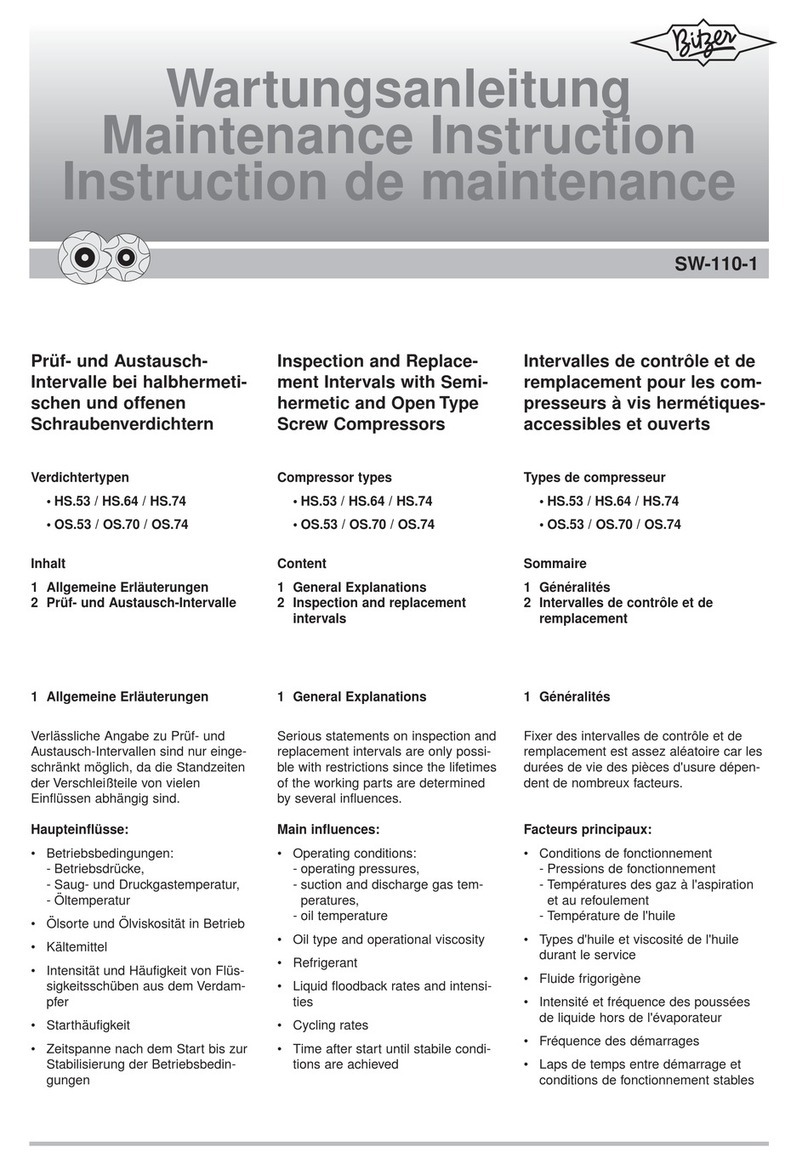
Bitzer
Bitzer SW-110-1 Maintenance Instruction
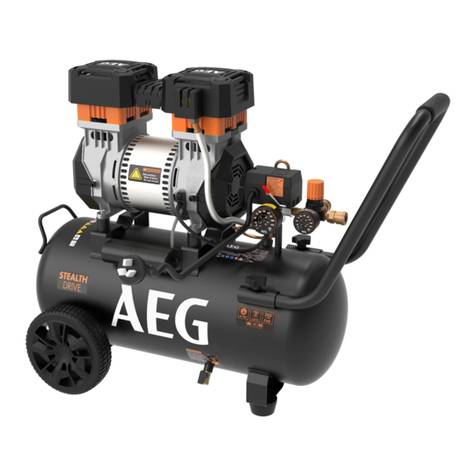
AEG
AEG AC1030S Original instructions
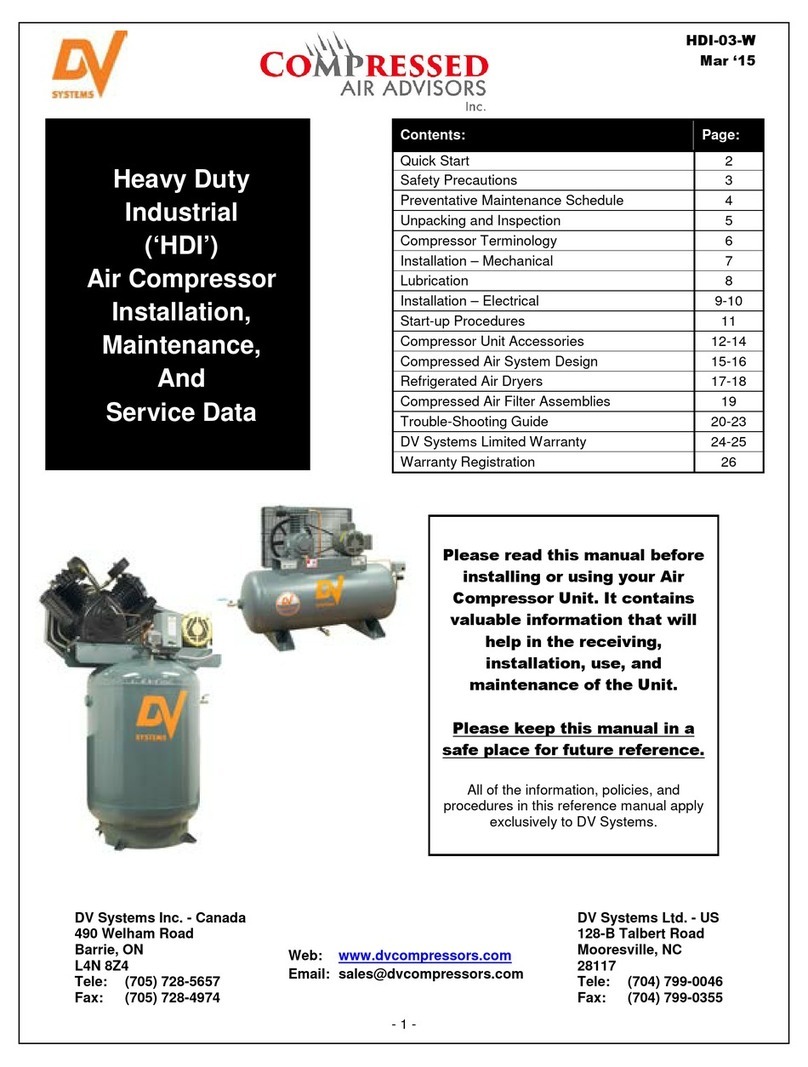
DV Systems
DV Systems HDI Installation maintenance and service manual
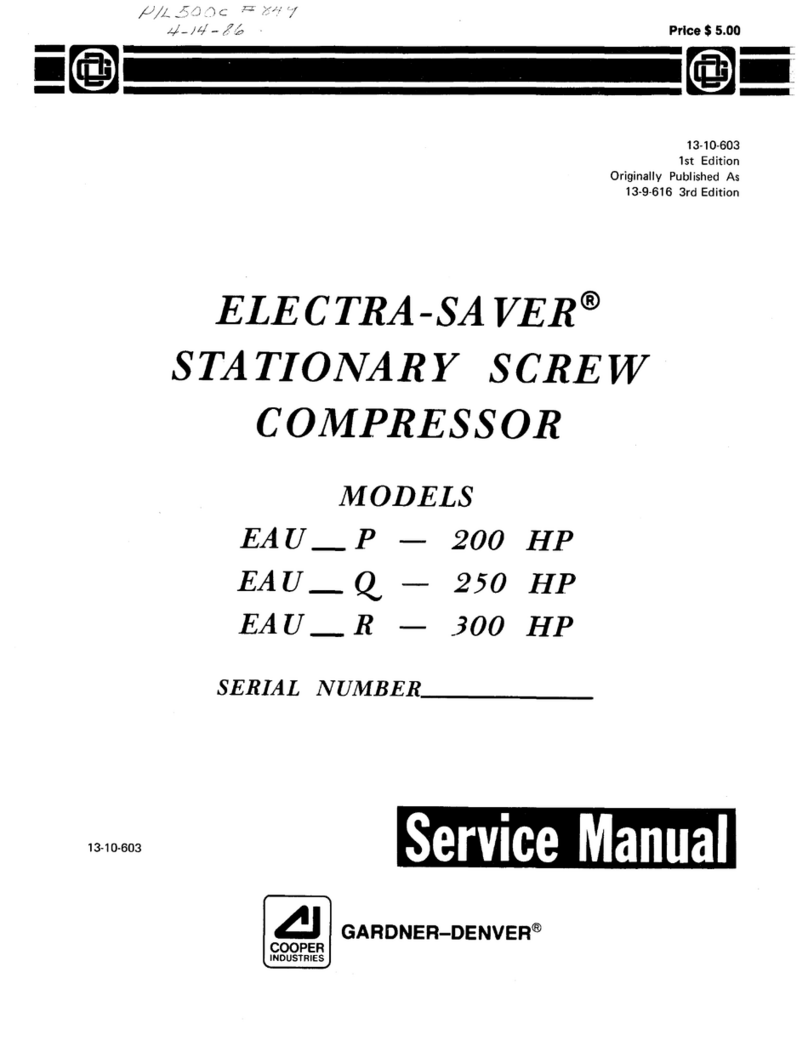
Gardener Denver
Gardener Denver Electra-Saver EAU P Series Service manual
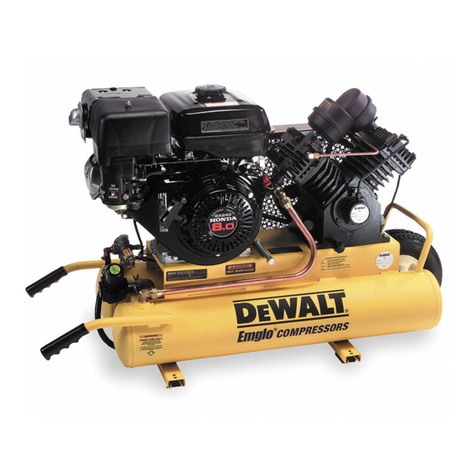
DeWalt
DeWalt D55270-1 instruction manual
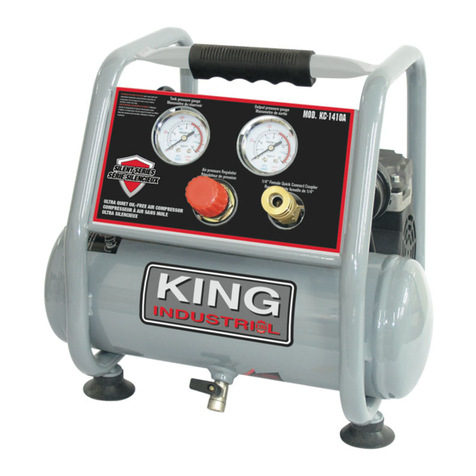
King Industrial
King Industrial KC-1410A instruction manual
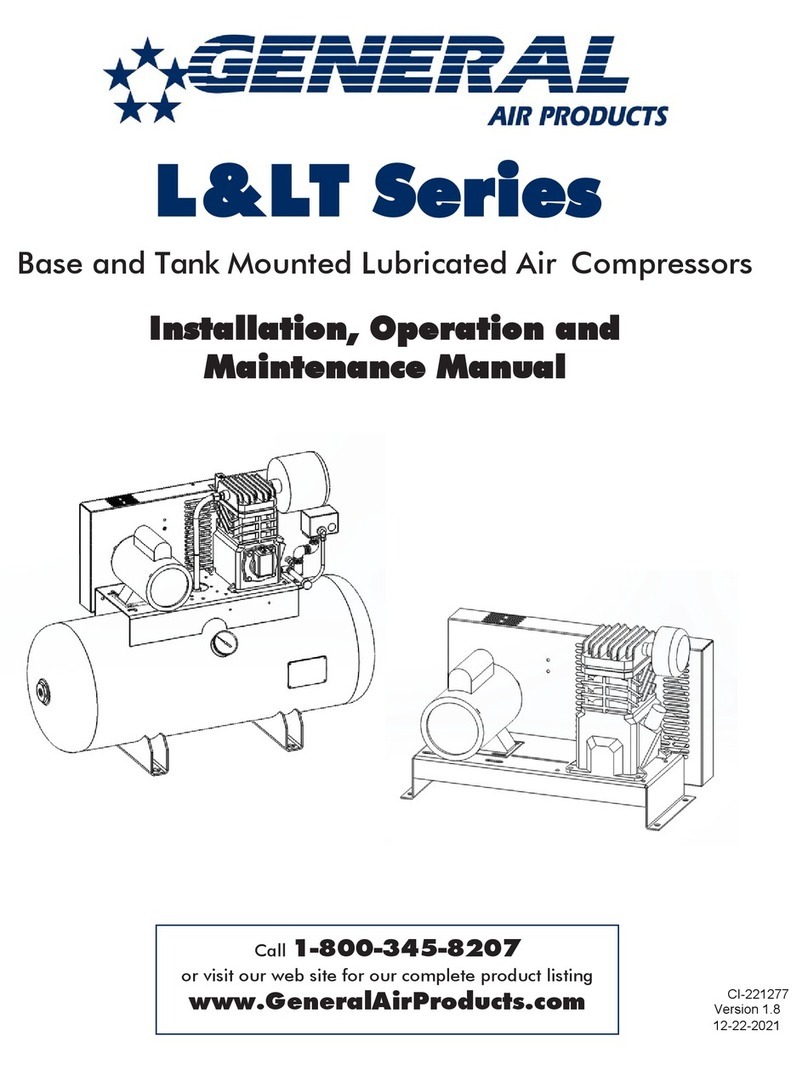
General Air Products
General Air Products L Series Installation, operation and maintenance manual

kincrome
kincrome K13090 user guide

ABB
ABB HT606743 Operation manual
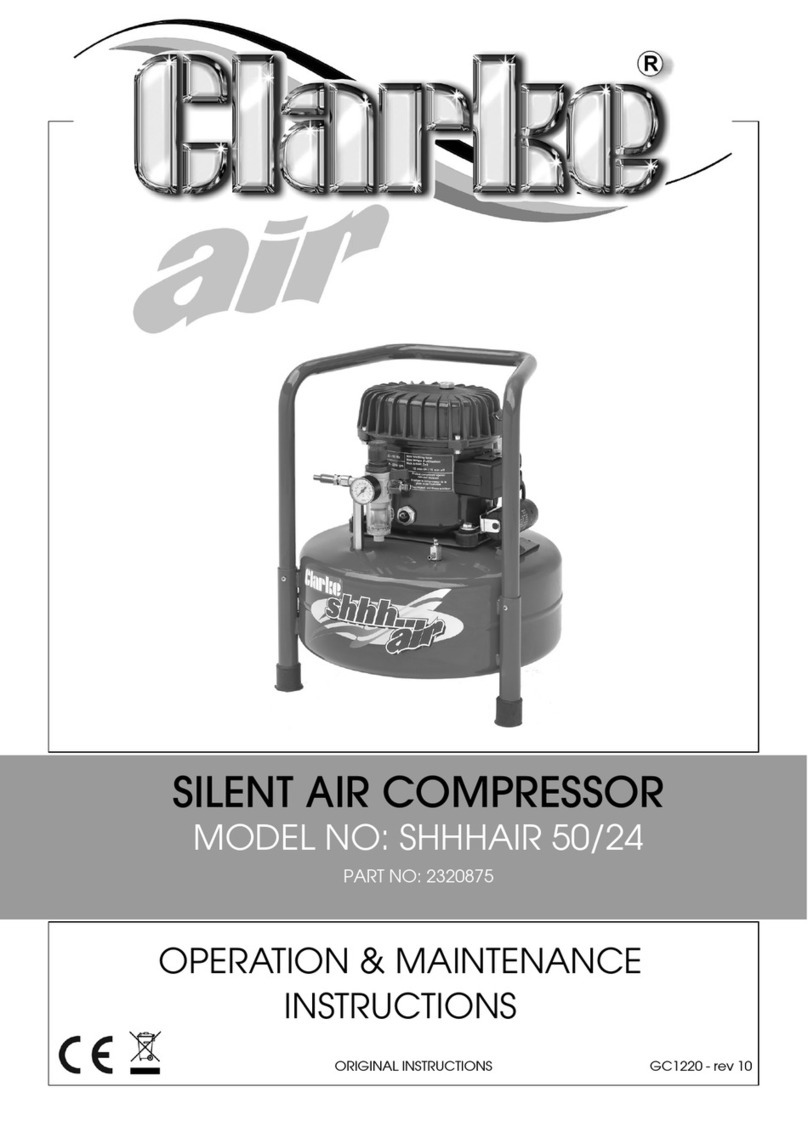
Clarke
Clarke SHHHAIR 50/24 Operation & maintenance instructions
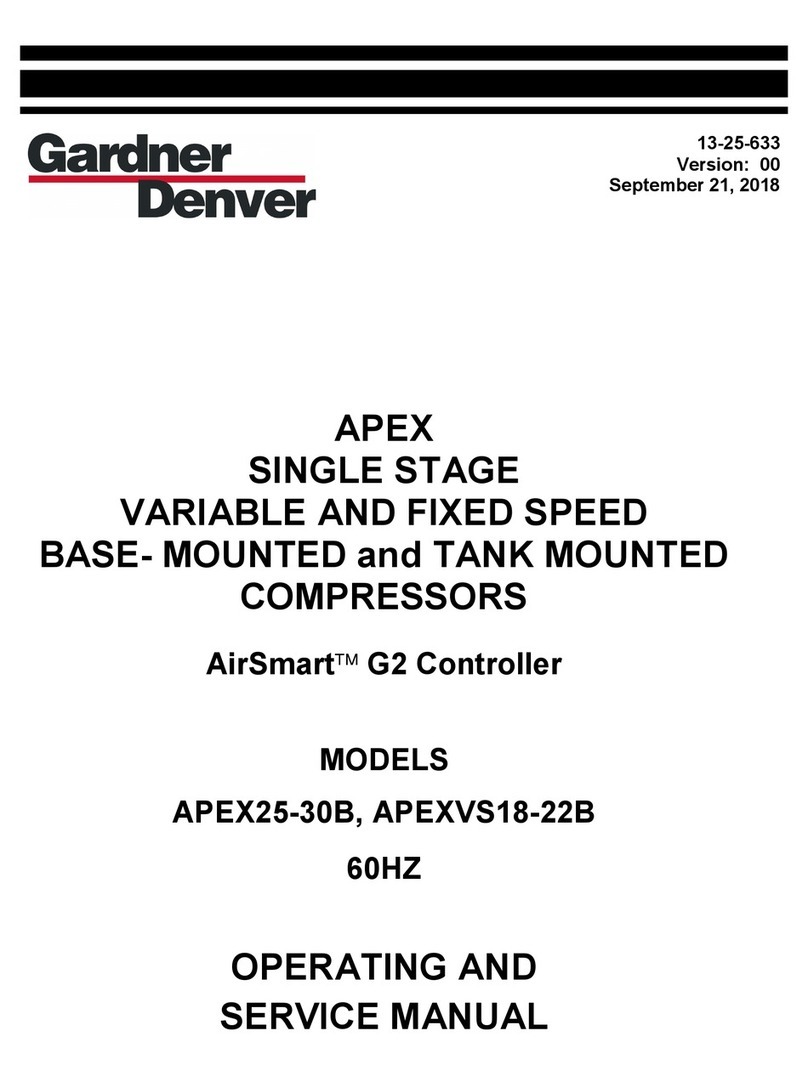
Gardner Denver
Gardner Denver APEX25-30B Operating and service manual
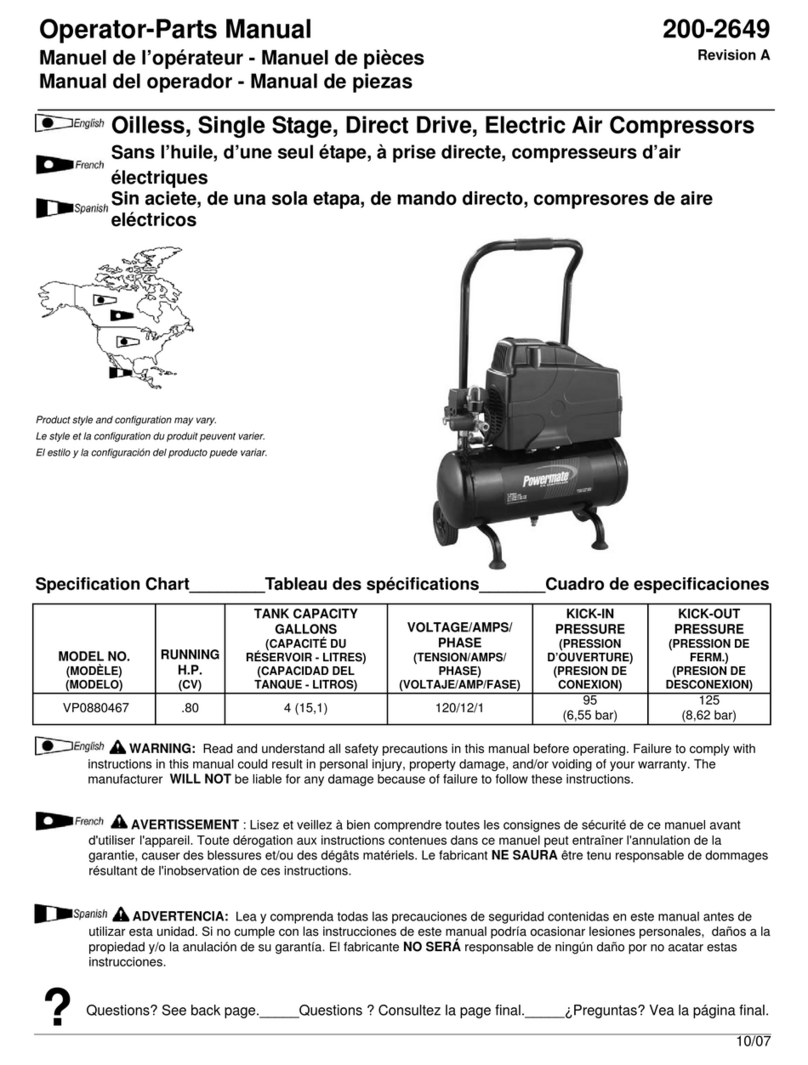
Powermate
Powermate 200-2649 Operator's & parts manual