GE WSXH208A Series How to use

g
g
PUB # 31-9060 08/00
MODEL SERIES:
TECHNICAL SERVICE GUIDE
GE Consumer Home ServicesTraining
Front-Load Washer
WSXH208A

IMPORTANT SAFETY NOTICE
The information in this service guide is intended for use by
individuals possessing adequate backgrounds of electrical,
electronic, and mechanical experience. Any attempt to repair a
major appliance may result in personal injury and property
damage. The manufacturer or seller cannot be responsible for the
interpretation of this information, nor can it assume any liability in
connection with its use.
WARNING
To avoid personal injury, disconnect power before servicing this
product. If electrical power is required for diagnosis or test
purposes, disconnect the power immediately after performing the
necessary checks.
RECONNECT ALL GROUNDING DEVICES
If grounding wires, screws, straps, clips, nuts, or washers used
to complete a path to ground are removed for service, they must
be returned to their original position and properly fastened.
!
GE Consumer Home Services Training
Technical Service Guide
Copyright © 2000
All rights reserved.This service guide may not be reproduced in whole or in part
in any form without written permission from the General Electric Company.

– 1 –
Table of Contents
Table of Contents
Introduction . . . . . . . . . . . . . . . . . . . . . . . . . . . . . . . . . . . . . . . . . . . . . . . . . . . . . 2
Functional Part Changes . . . . . . . . . . . . . . . . . . . . . . . . . . . . . . . . . . . . . . . . . . 3
Door Lock Assembly . . . . . . . . . . . . . . . . . . . . . . . . . . . . . . . . . . . . . . . . . . . . . . 6
Automatic Dispenser . . . . . . . . . . . . . . . . . . . . . . . . . . . . . . . . . . . . . . . . . . . . . 7
Motor Speed Control . . . . . . . . . . . . . . . . . . . . . . . . . . . . . . . . . . . . . . . . . . . . . 8
Timer . . . . . . . . . . . . . . . . . . . . . . . . . . . . . . . . . . . . . . . . . . . . . . . . . . . . . . . . . . 9
Drive Motor . . . . . . . . . . . . . . . . . . . . . . . . . . . . . . . . . . . . . . . . . . . . . . . . . . . . . 9
Resistance Chart . . . . . . . . . . . . . . . . . . . . . . . . . . . . . . . . . . . . . . . . . . . . . . . 10
Troubleshooting . . . . . . . . . . . . . . . . . . . . . . . . . . . . . . . . . . . . . . . . . . . . . . . . 11
Timer Flowchart Example. . . . . . . . . . . . . . . . . . . . . . . . . . . . . . . . . . . . . . . . . 15
Special Troubleshooting and Access Tips . . . . . . . . . . . . . . . . . . . . . . . . . . 16
Wiring Diagram . . . . . . . . . . . . . . . . . . . . . . . . . . . . . . . . . . . . . . . . . . . . . . . . . 18
Motor Movement .. . . . . . . . . . . . . . . . . . . . . . . . . . . . . . . . . . . . . . . . . . . . . . . 19
Timer Flowchart . . . . . . . . . . . . . . . . . . . . . . . . . . . . . . . . . . . . . . . . . . . . . . . . 20
Schematic . . . . . . . . . . . . . . . . . . . . . . . . . . . . . . . . . . . . . . . . . . . . . . . . . . . . . 21
Diagnostics Flowcharts . . . . . . . . . . . . . . . . . . . . . . . . . . . . . . . . . . . . . . . . . . 22
Parts Catalog . . . . . . . . . . . . . . . . . . . . . . . . . . . . . . . . . . . . . . . . . . . . . . . . . . . 27
Warranty Information. . . . . . . . . . . . . . . . . . . . . . . . . . . . . . . . . . . . . . . . . . . . . 28
Quiz. . . . . . . . . . . . . . . . . . . . . . . . . . . . . . . . . . . . . . . . . . . . . . . . . . . . . . . . . . . 29

–2 –
Introduction
GE introduced its Horizontial Axis Front-Load
Washer in 1998. The manual, Pub #31-9005,
provided service information for that product. The
2000 version of the front-load washer has several
significant changes that are shown in this manual.
This Technical Service Guide is a supplement for
that manual, and highlights and illustrates product
changes and service methods to successfully
service the updated washer. The significant
changes are listed below and covered in this
supplement. A detailed method for servicing the
bellows is also included to assist you.
• Door lock assembly and strike
• Automatic dispenser
• Motor Speed Control
• Timer
• Drive Motor

–3 –
1998 Model
Door Lock Assembly and Strike
Automatic Dispenser
Functional Part Changes
NEW Model
New Door Lock Assembly and Strike
New Automatic Dispenser
Motor Speed Control New Motor Speed Control

–4 –
Drive Motor New Drive Motor
1998 Model
Timer
NEW Model
NewTimer

–5 –
Notes

–6 –
Door Lock Assembly
The new door lock assembly consists of a coil,
door switch, switch actuator, locking fork, wax
motor, and spin lock arm.When the timer line
switch is closed, electrical power is applied to the
coil and the door lock switch.The magnetic field of
the coil pulls the locking fork down and tries to pull
the contacts of the door lock switch closed.If the
washer door is open, a tab on the switch actuator
prevents the contacts from closing.The locking
fork will not allow the door to be closed until the
timer line switch is opened.When the washer door
is closed, the door strike pivots the switch actuator
out of the way.This allows the magnetic field of
the coil to close the contacts of the door lock
switch and the locking fork locks the door. The
wax motor and spin lock arm are used to prevent
the door from being opened while the drum is still
spinning. The wax motor is electrically in parallel
with the drain pump. Power is applied to the wax
motor when the washer is in spin.When power is
applied to the wax motor, it expands its piston (40
to 65 seconds), driving the spin lock arm between
the locking fork and the switch actuator holding the
locking fork down.When power is removed from
the wax motor, it takes about 130 seconds for the
wax motor to cool down and retract the piston,
pulling the spin lock arm back and releasing the
locking fork. This allows time for the drum to coast
to a stop before the door can be opened.

–7 –
Automatic Dispenser
The Automatic Dispenser has been changed from
a mechanical to an electrical operation.When the
water valve is activated, all the water entering the
washer must pass through the tube at the rear of
the dispenser.The tube at the end of the dis-
penser has four possible outlets.The outlet that
allows water to go into the tub and the outlet that
allows water to go into the soap section of the
dispenser are constantly open.The outlet that
allows water into the bleach section of the dis-
penser and the outlet that allows water into the
softner section of the dispenser are controlled by
solenoids.When water enters the washer, water
flows through the tube directing water into the tub
and through the soap section to the dispenser.
When it is time for either the bleach or the softener
to be released, the timer will activate the soleniod
that controls water to that section.The addition of
water to either the bleach or softener cavity starts
the flow out of that cavity into the tub. As in the
earlier model, the tubes in the inserts and the
tubes in the cavities form a siphon that empties
the cavity once the flow has started.

–8 –
Motor Speed Control
The motor speed control now provides all func-
tional control to the washer.
The board controls:
1. Electrical power to the timer motor by con-
necting and disconnecting neutral to the timer
motor.Timer contacts 6C to 6T are electrically in
parallel with the switch in the speed control board
and are used as a backup or to sequence the
timer when the knob is turned.
2.The timing of each function and the speed
and direction of the drive motor. In the previous
front-load washer, the timer used a slip disc inside
the timer to extend the increments (e.g., the
13-minute fill and agitate increment). Contacts of
the timer were also used to reverse the polarity on
the motor armature of the drive motor to reverse
the drive motor.These functions have been
removed from the timer and added to the new
speed control board.The new speed control board
has six terminals marked A, B, C, D, E, and F that
receive inputs or codes from the contacts of the
timer. Each terminal receives an input of either
line to neutral voltage (120 VAC) or zero for each
function. For example, if the code received by the
speed control board is 120 VAC on terminals A, B,
and D and zero on terminals C, E, and F, this tells
the board to allow the washer to fill, tumble at
52 RPM for 107 seconds, then close the contact
that connects the neutral side of the timer motor
so it advancesand gives the next code.
3.The speed of the drive motor by converting
input line to neutral, single-phase 60-Hz voltage,
to varying frequency, three-phase output voltage
from 0 to 300 VAC. By varying the amount, fre-
quency, and polarity of the voltage, and comparing
the input from the tachogenerator on the drive
motor, the control board can operate the drive
motor at a preprogrammed speed and direction.
The motor PC board produces three phases from
a single phase by rectifying the line voltage to DC
voltage.The digital signal processor (DSP) gener-
ates the three-phase sine waves by switching ON/
OFF the six drivers. The DSP varies the voltage,
current, and frequency of the sine waves to vary
the speed of the motor.
4. Determines if the load in the washer is out of
balance by converting the sine wave from the
tachogenerator to square waves and comparing
the distance between the square waves.

–9 –
Timer
Drive Motor
The timer functions have been reduced to a line
switch that turns electrical power ON and OFF to
the washer, applying codes to the speed control
board.The line switch also applies electrical power
to the dispenser valves, the water valve, the drain
pump, the wax motor, and the end-of-cycle buzzer
at the proper time.
The new motor is a permanent magnet,
three-phase AC motor that varies speeds when
the voltage from the speed control board varies in
frequency and amount. The motor still has a
tachogenerator that inputs the speed of the motor
to the speed control board.

–10 –
Resistance Chart
Drain Pump Motor 15 Ohms +/- 7%
DispenserValves Solenoids 1100 Ohms +/- 7%
Drive Motor Windings
Terminals 1 to 2 2.6 Ohms +/- 7%
Terminals 1 to 3 2.6 Ohms +/- 7%
Terminals 2 to 3 2.6 Ohms +/- 7%
Drive MotorTachogenerator 184 Ohms +/- 7%
Timer Motor 2425 Ohms +/- 6%
Water Valve Solenoids 880 Ohms +/- 10%
Wax Motor 380 Ohms +/- 10%

–11 –
is the first step in the timer, that timer contacts 0C
to 0T, 1C to 1B, 5C to 5B, and 12C to 12B are
closed, and the speed board will not advance the
timer for 479 minutes.
With the transfer of the timing, the motor speed,
and the motor reversing functions from the timer
to the speed control board, it is important to
understand the coding system to the speed
control board. By using different combinations of
five inputs, the timer can input hundreds of codes.
The speed control board recognizes a code of
line-to-neutral voltage (120 VAC), or 0 at each of
the five input pins.This code would tell the board
to count down for 479 minutes then advance the
timer one step.
Two major differences between the previous front-
load washer and the 2000 front-load washer are:
1.The door lock and switch assembly can be
replaced through the top of the washer. Discon-
nect the two wire plugs by reaching down from the
top, opening the door, and removing the mounting
screws and lifting the door lock out through the
top.
2.The timer can be replaced through the top by
removing the knob and dial, removing the two
screws holding the timer to control panel, and
lifting the timer out through the top of the washer
(see figure above).
Troubleshooting
Attached to the inside of the service panel is the
Tech Sheet with a timer flowchart and a wiring
schematic, which is invaluable when troubleshoot-
ing the washer.The timer flowchart shows which
timer contacts are closed at each step.The sche-
matic shows the electrical connection of the
components.
Using the example of the
Timer Flowchart Sample
on page 15 and the
Schematic
on page 21, we
can review how the two work together.On the
timer flowchart at the top of the first column is
CAM, and the numbers below it go from 00 to 14.
These numbers indicate the timer cams. (When
you look at the schematic, each timer contact is
numbered; this is the timer cam number.) On the
timer flowchart at the top of the fourth column is
CONTACT. Below CONTACT are the letters T and
B (Top & Bottom) for each cam number.
On the schematic, each set of timer contacts is
labeled with the cam number and a letter C (Cen-
ter contact), T, or B. On some schematics, the
letter C may be omitted and the contact is labeled
by just the cam number (the C is understood to be
there).
On the flowchart at the top of the fifth column is
CIRCUIT. Below it are different electric circuits
controlled by the timer. Above the rest of the
columns on the flowchart are the washer func-
tions.The column(s) for each function will either
be shaded or blank in line with each circuit.For
example, look at the first column below the 8-hour
delay function. Looking down the column, we see
the block for machine power is shaded, indicating
that timer contacts 0C to 0T are closed.The block
for code C is shaded, indicating that timer contacts
5C to 5B are closed.The block for pressure switch
bypass is shaded, indicating that timer contacts
12C to 12T are closed.
At the bottom of the flowchart is the step time in
minutes and the step number. If we look under the
8-hour delay column, we see 479 in the step time
block and 1 in the step number block. From the
timer flowchart we now know that the 8-hour delay
TIMER
DOOR LOCK/SWITCH
GEA00516

–12 –
WATER Possible Causes What To Do
Water leaks
Fill hoses or drain hose is •Make sure hose connections are tight at washer and
improperly connected faucets and make sure end of drain hose is correctly
inserted in and secured to drain facility.
Household drain may •Check household plumbing. You may need to call
be clogged a plumber.
Constant water pressure •Tighten hoses at the faucets and turn the water off after
to the fill hoses at the each use.
water source •Check condition of the fill hoses; they may need
replacement after 5 years.
Oversudsing •Use less detergent or low sudsing detergent.
Too many suds
Type of detergent •Switch to a low sudsing detergent and follow
instructions on package.
Very soft water •Try less detergent.
Water won’t drain
Drain hose is kinked or •Straighten drain hose and make sure washer is not sitting
improperly connected on it.
•Top of drain outlet should be less than 8 ft. (2.5 m)
above floor.
Water temperature
Control is not set properly •Check water temperature control and adjust.
is incorrect
Water supply is improperly •Make sure hoses are connected to correct faucets.
connected
Water valve screens are •
Turn off the water source and remove the water connection
stopped up
hoses from the upper back of the washer. Use a brush or
toothpick to clean the screens in the machine. Reconnect
the hoses and turn the water back on.
House water heater is •Make sure house water heater is delivering water
not set properly at 120°F.–140°F.(48°C.–60°C.).
Water does not enter
Water supply is turned off •Turn on both hot and cold faucets fully.
washer or enters slowly
Troubleshooting

–13 –
NOISE Possible Causes What To Do
Washer is noisy
Washer is uneven •Make sure washer is level and rests firmly on the floor.
Washer load is unbalanced •Push the Cycle knob in to stop the washer, open the
door and redistribute the load evenly. Close the door
and restart.
High pitch jet engine sound •This is normal during the spin cycle.
Squealing sound or hot •Washer is overloaded. Stop washer and reduce load.
rubber odor
Shipping bolts and foam block •See Installation Instructions for directions to remove
have not been removed shipping bolts and foam block.
Washer is overloaded, •Stop washer and reduce load size.
causing squealing sound or
hot rubber odor
Rattling and clanking caused •Check drum for foreign objects. Turn items with
by foreign objects in tub metal fasteners inside out. Call authorized servicer to
or pump or metal fasteners inspect pump.
hitting tub
PERFORMANCE Possible Causes What To Do
Lint or residue on
Incorrect sorting •Separate lint producers from lint collectors.
Washing too long •Excess wash time may create lint.
Detergent not dissolving •Try a liquid detergent.
•Use warmer water temperature.
Overloading •Wash drum may be fully loaded with loosely added items.
Incorrect use of fabric softener •Check fabric softener package for instructions and follow
directions for using dispenser.
clothes
OPERATION Possible Causes What To Do
Washer pauses in cycle
The washer normally pauses
between washing steps
Washer won’t operate
Washer is unplugged •Make sure cord is plugged securely into a working outlet.
Water supply is turned off •Turn both hot and cold faucets fully on.
Controls are not set •Check controls and make sure Cycle knob is pulled out.
properly
Door is open •Close door and pull Cycle knob out.
Dispenser drawer is open •Close drawer.
Circuit breaker/fuse is •Check house circuit breakers/fuses. Replace fuses or
tripped/blown reset breaker. Washer should have separate outlet.
Motor is overheated •Washer motor will stop if it becomes overheated. It
will automatically restart after a cool down period of
up to 30 minutes (if washer has not been manually
turned off).
Washer won’t spin
Washer door open •Make sure door is closed.
Dispenser drawer open •Close drawer.
Load is too small •Add one or two similar items to help balance the load.
Troubleshooting

–14 –
Troubleshooting
(cont.) PERFORMANCE Possible Causes What To Do
Clothes too wet
Load is too small •Add one to two similar items.
Load is out of balance •Redistribute load.
Pilling
Result of normal wear on •While this is not caused by the washer, you can slow the
poly-cotton blends and pilling process by washing garments inside out.
fuzzy fabrics
Grayed or yellowed
Not enough detergent •Use correct amount of detergent.
Hard water •Use hottest water safe for fabric.
•Use a water conditioner like Calgon brand or install
a water softener.
Water is not hot enough •Make sure water heater is delivering water at
120°F.–140°F. (48°C.–60°C.).
Detergent is not •Try a liquid detergent.
dissolving
Dye transfer •Sort clothes by color. If fabric label states
wash separately,
unstable dyes may be indicated.
Colored spots
Incorrect use of fabric •Check fabric softener package for instructions and follow
softener directions for using dispenser.
Dye transfer •Sort whites or lightly colored items from dark colors.
•Promptly remove wash load from washer.
Wrinkling
Improper sorting •Avoid mixing heavy items (like work clothes) with
light items (like blouses).
Overloading •Load your washer so clothes have enough room
to move freely.
Incorrect wash cycle •Match Cycle selection to the type of fabric you are
washing (especially for easy care loads).
Repeated washing in •Wash in warm or cold water.
water that is too hot
Snags, holes, tears, rips
Pins, snaps, hooks, sharp •Fasten snaps, hooks, buttons, and zippers.
•Remove loose items like pins, objects in pockets
and sharp buttons.
•Turn knits (which snag easily) inside out.
Undiluted chlorine bleach •Never add undiluted bleach to wash or allow clothes
to come in contact with undiluted bleach.
Chemicals like hair bleach •Rinse items that may have chemicals on them before
or dye, permanent wave washing.
solution
or excessive wear
buttons, belt buckles,
zippers, and sharp objects
left in pockets
clothes

–15 –
Timer Flowchart Example
C
A
M
A
C
T
I
V
E
F
I
X
E
D
TERM. C
O
N
T
A
C
T
T
B
T
B
T
B
T
B
T
B
T
B
T
B
T
B
T
B
T
B
T
B
T
B
T
B
RINSE WATER TEMP
CIRCUIT
DETENT
0/0
MACHINE POWER
0
1
2
3
4
5
6
7
8
10
12
14
2
23
1
22
24
54
6DISPENSER V2
23 19
21 CODE B
CODE A
57
9
CODE E
DISPENSER V1
23 16
18
11 10
12
23 13
15
CODE C
TM DIRECT
CODE D
14 17
15
17
WASH WATER MAIN
RINSE WATER MAIN
16
18 WASH WATER TEMP
20 19
21
19 22
24
4
7
9
PRESS SW. BYPASS
BUZZER
DRAIN PUMP
DRAIN PUMP
STEP TIME (MIN)
STEP NO
ELECTRONIC - DELAY TO START
8 HR 6 HR 4 HR 2HR 1HR
HEAVY
WASH NORMAL WASH
1
1111
1
3
5
9
2
3
9
5
1
1
9
5
9
1
0
31
.
8
6
.
7
5
.
9
0
.
8
1
5
QUICK
WASH

–16 –
Special Troubleshooting and AccessTips
The front panel can be removed to give you
access to the motor and motor connectors for
resistance readings.This prevents moving the
washer from its installations.
With the front panel removed, and the motor
connector exposed, you can check the motor
windings.They are color coded in the schematic
as black, blue, and red.
Black is #1 Winding, Blue is #2 Winding, Red is #3 Winding
Note: Resistance is 2.8 ohms which is within
approximate range for winding resistance.Check 1
to 3, 1 to 2, and 2 to 3.
The tachogenerator resistance is also read from
the front.The leads are located on the right upper
and center of the block.
With volt/ohmmeter probes attached to the right
and center leads, the reading should approximate
the one in the picture.With a required resistance
of 184 ohms, this reading is within the acceptable
range.The information is provided in the sche-
matic. Remember to access the tachoenerator
leads from the front.
To check for magnetic properties of the magnet
on the dispenser door, hold an ordinary metal
paper clip to the magnet with the door open (see
photo below). If the magnet in the dispenser door
will not hold the paper clip, replace the magnet.

–17 –
The reed switch connector can be accessed, with
the top removed. Separate the connector and the
reed switch pins.The dispenser door open is NO
continuity.The dispenser door closed is continuity.
As a follow-up to “the timer won’t advance after
checking timer motor resistance,”rotate the timer
until contacts 10 and 11 close intermittently. If they
have continuity, the problem is the speed control
board, and it should be replaced.
To remove the timer knob, push in and turn coun-
terclockwise.The timer dial is D-shaped and will
pull straight out.
Timer motor resistance is approximately 2.4K
ohms +/- 7%. (See Resistance Chart or Sche-
matic for resistance values.)
To remove the timer, first remove the knob and the
dial indicator.Then, while supporting the timer
from the back, remove two screws and pull the
timer straight out.You may find wire ties; if so, cut
them. Replace and redress the harness when
reinstalling the timer.
All other selector knobs are D-shaped and can be
removed by pulling straight out.
To remove the temperature switch, remove the
top, turn the switch counterclockwise until the
locking ears align, and pull straight out.
The rinse and speed switches are removed by
inserting a small screwdriver to depress tab, then
rotating counterclockwise to remove.

–18 –
Wiring Diagram
Wiring Diagram
WARNING: POWER MUST BE DISCONNECTED
BEFORE SERVICING THE APPLIANCE.
Table of contents
Other GE Washer manuals
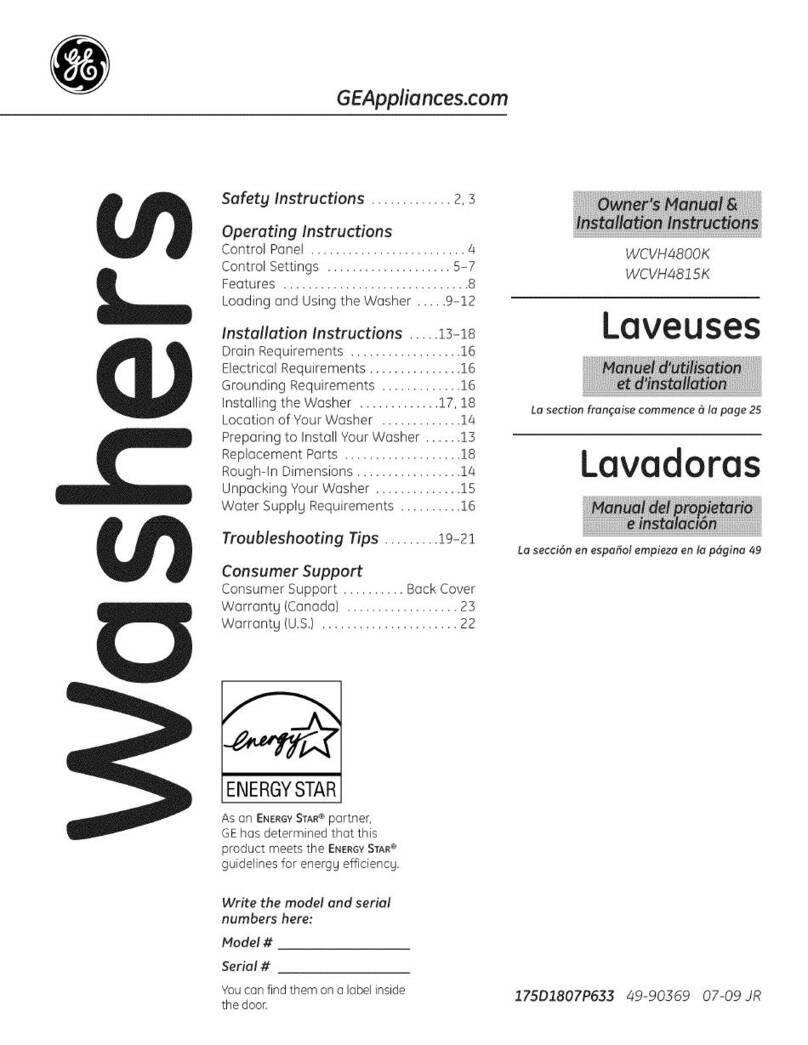
GE
GE WCVH4800K Safety guide
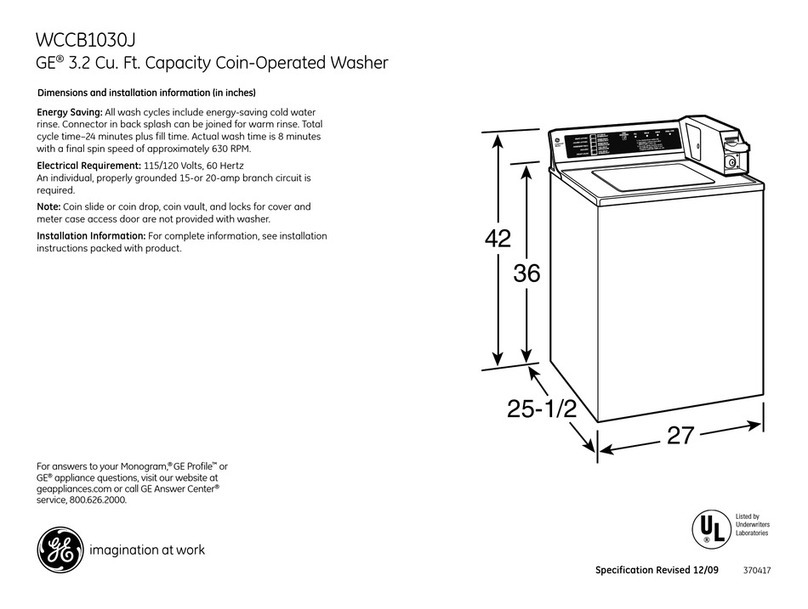
GE
GE GE Profile WCCB1030J Manual
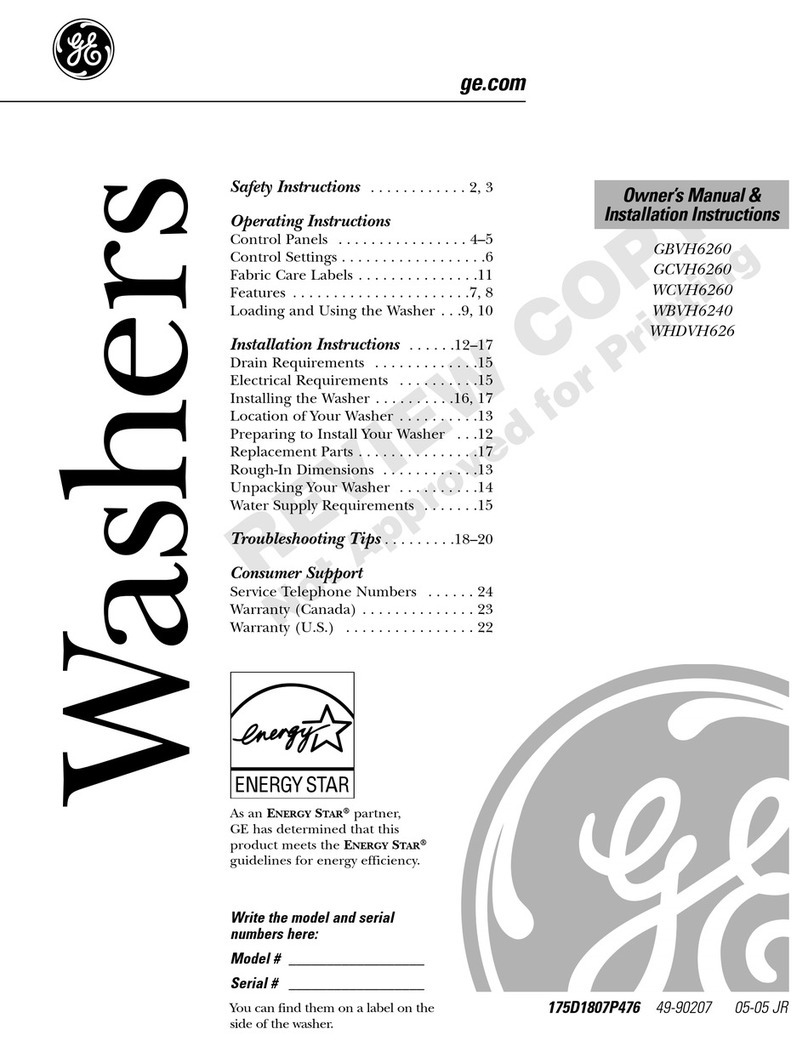
GE
GE GBVH6260 Original instructions
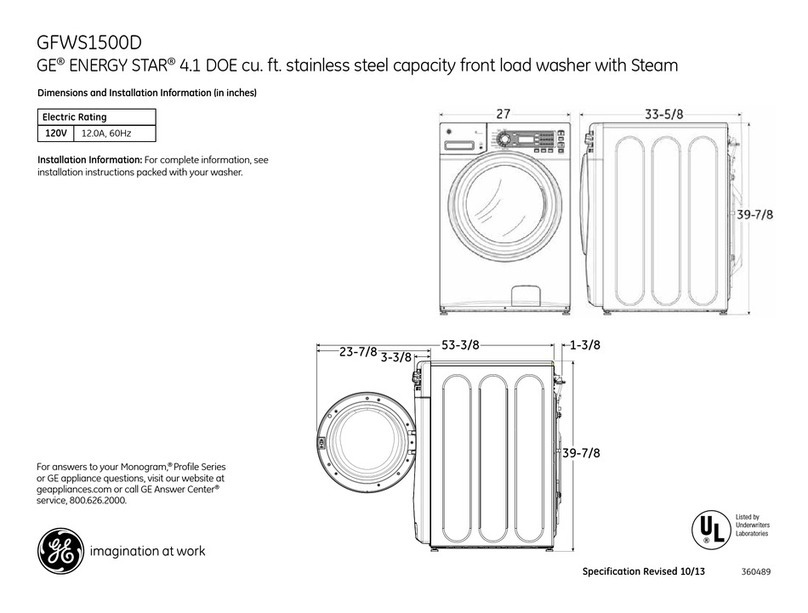
GE
GE GFWS1500D Manual
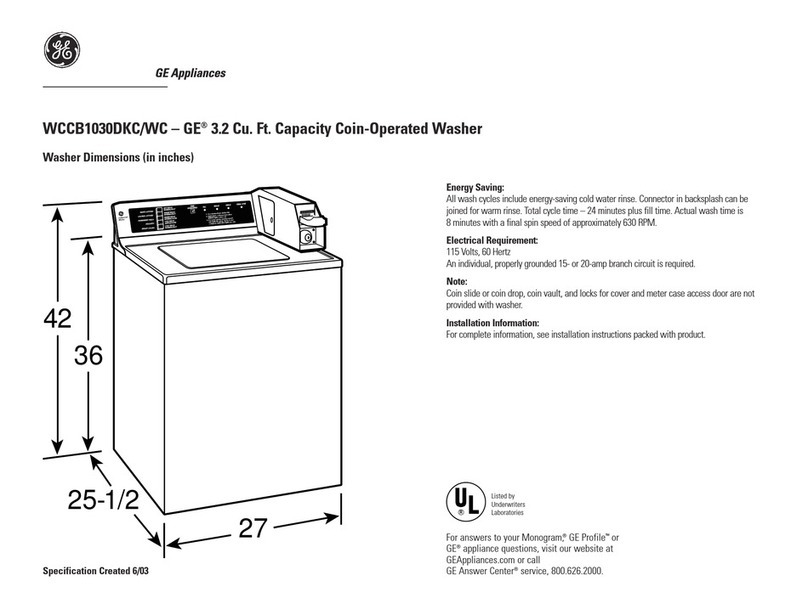
GE
GE GE Profile WCCB1030DKC User manual

GE
GE WWA8330V User manual
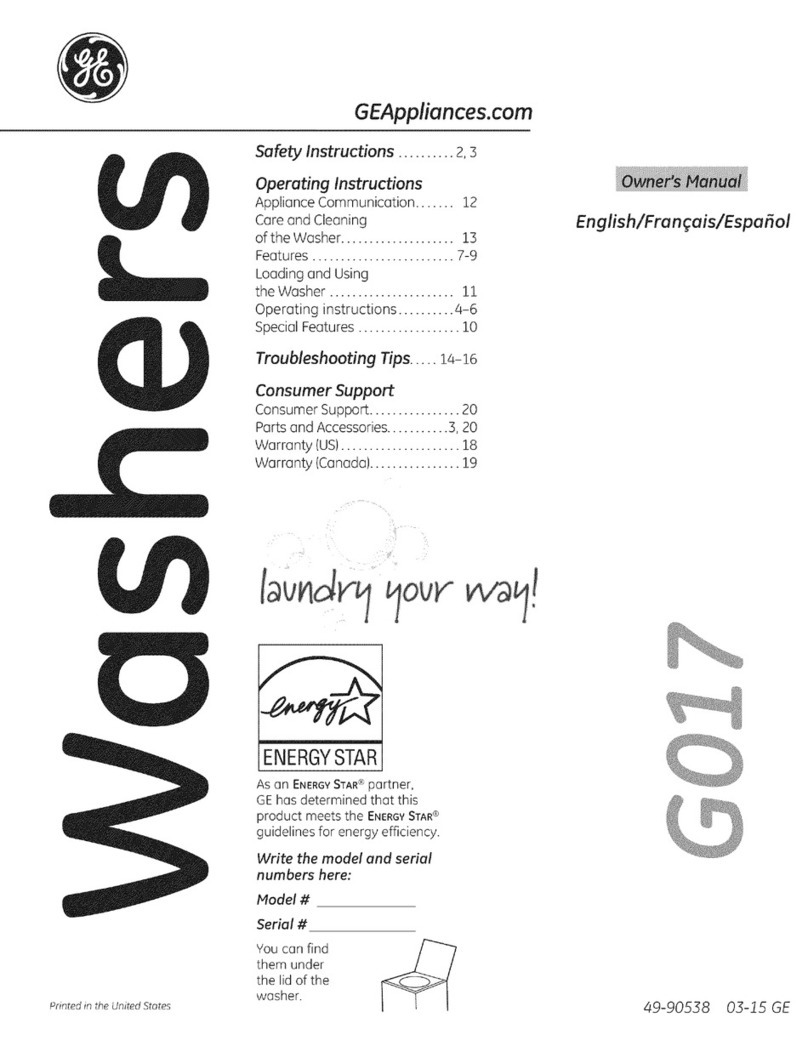
GE
GE G017 User manual
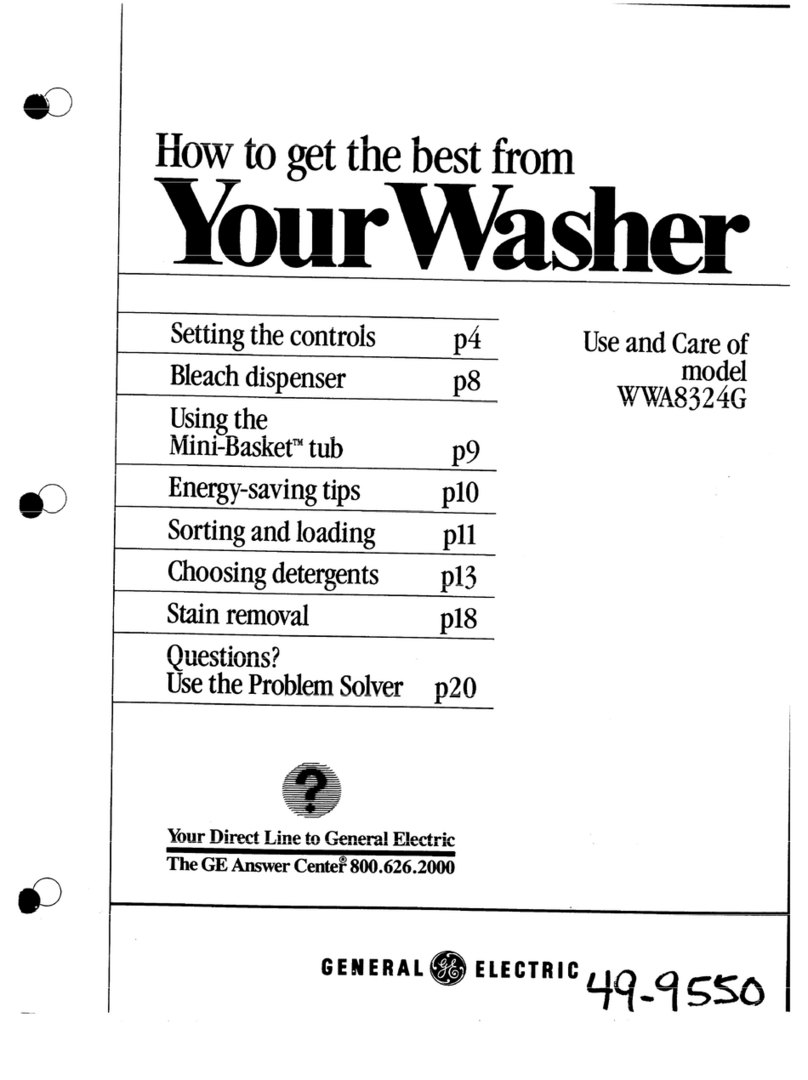
GE
GE WWA8324G Installation instructions
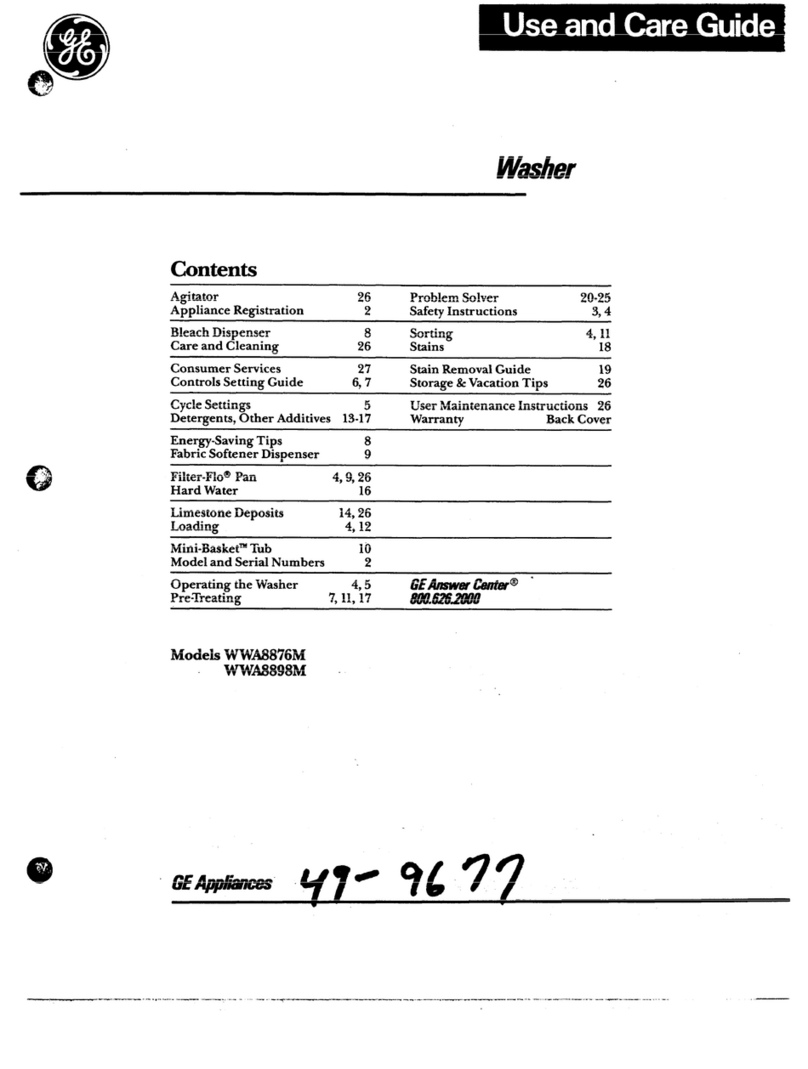
GE
GE 113D5497P183 User manual
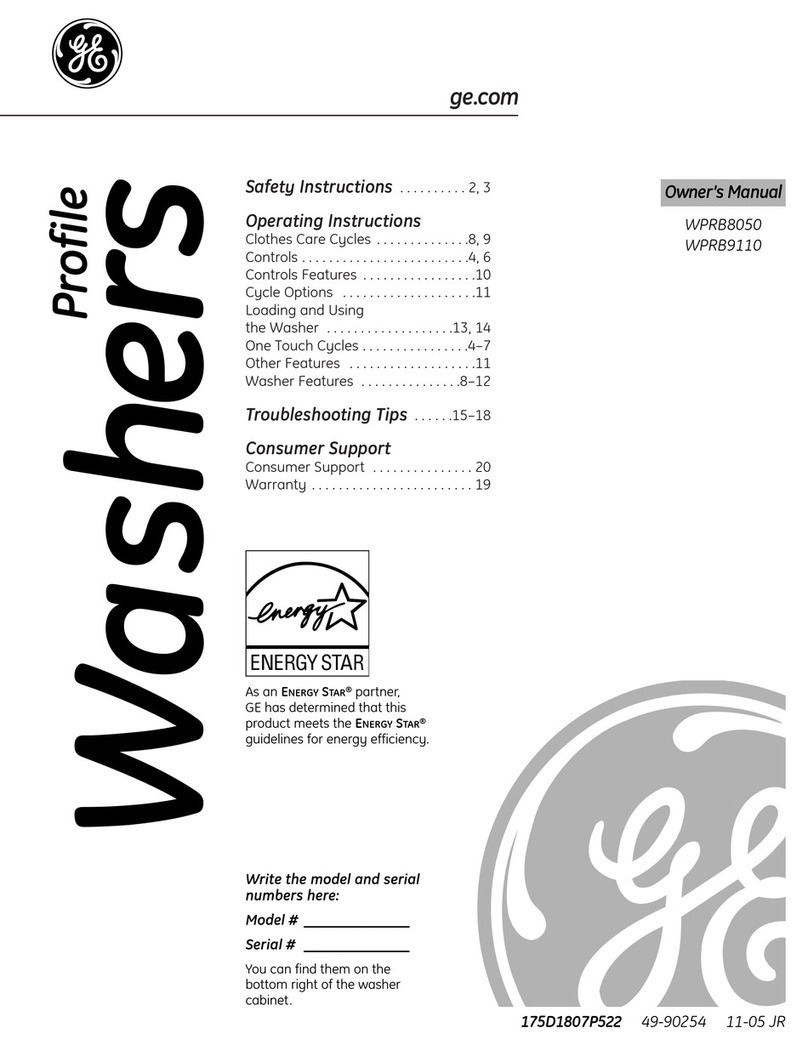
GE
GE Profile WPRB8050 User manual
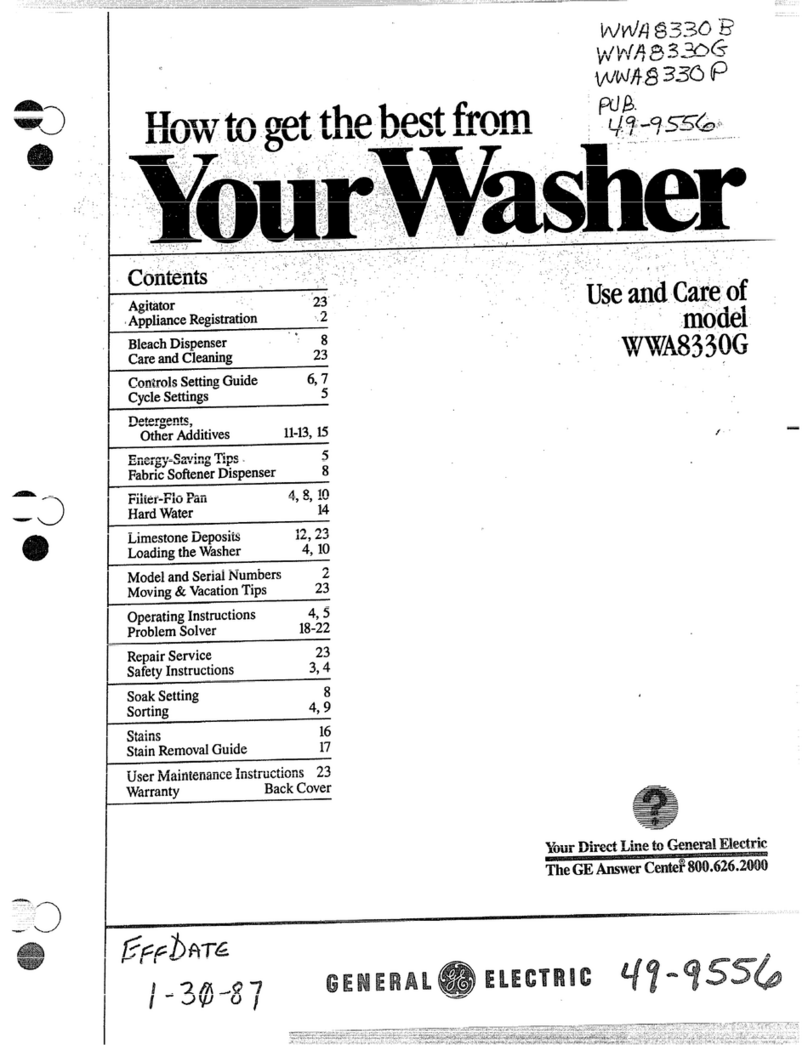
GE
GE WWA8330G Installation instructions
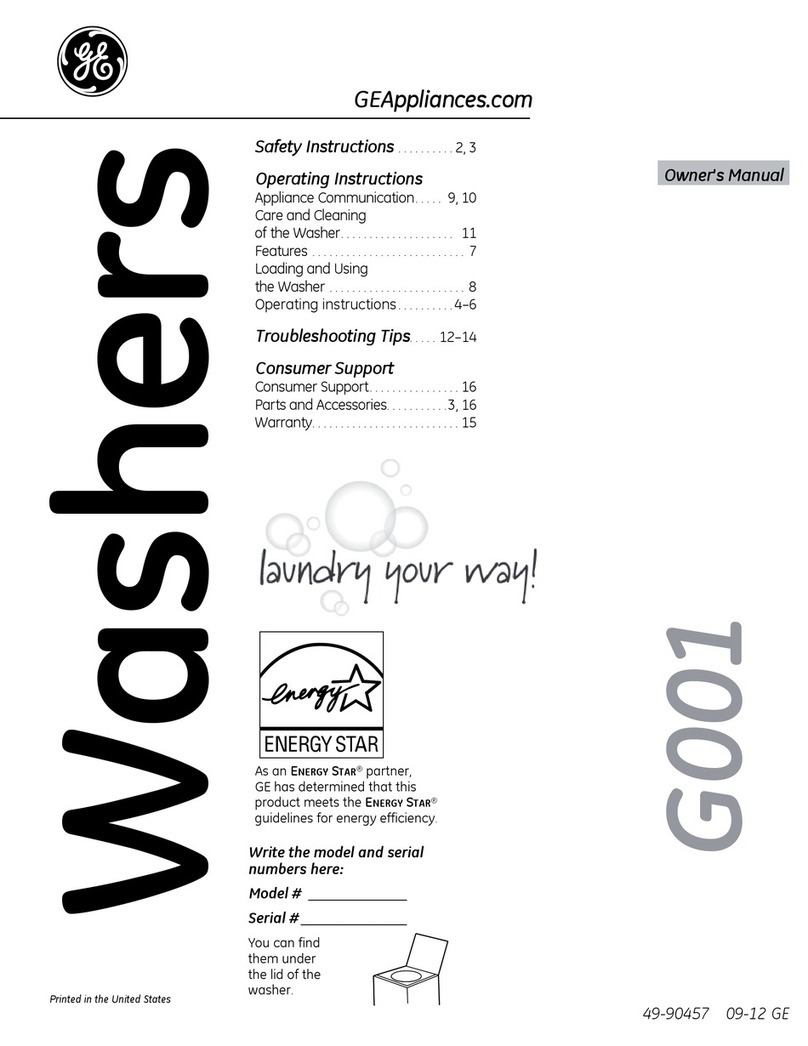
GE
GE GTWN7450DWW User manual
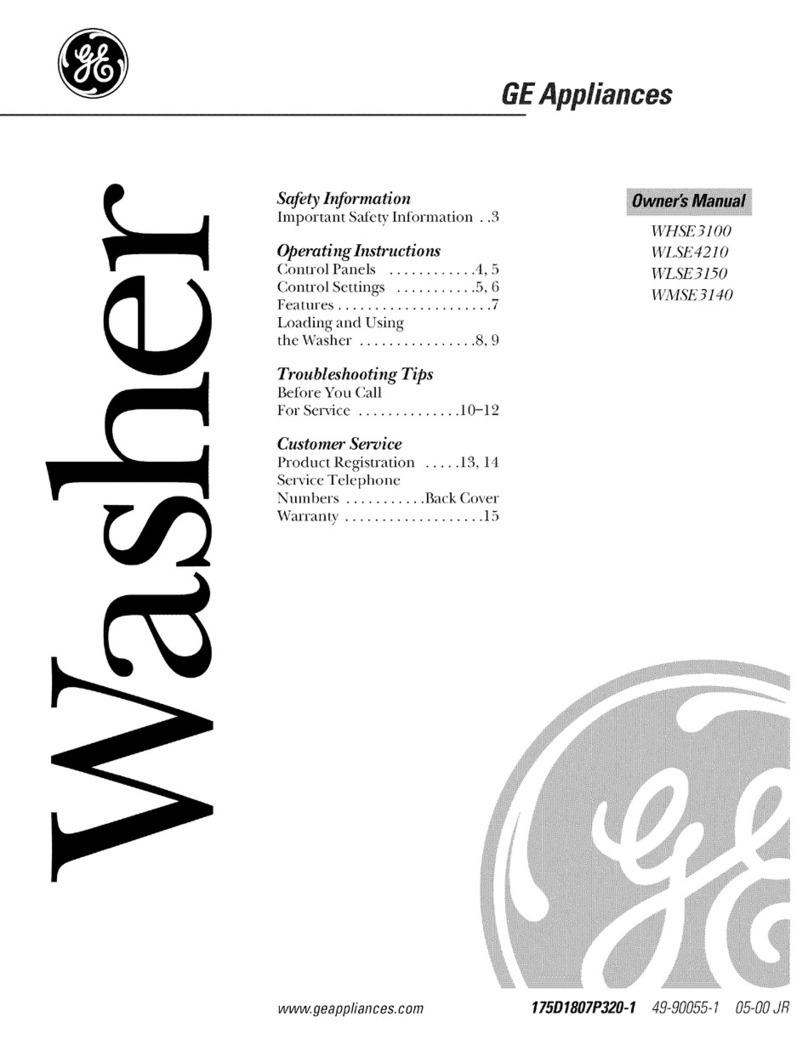
GE
GE WLSE4210 User manual

GE
GE WWA3650R User manual
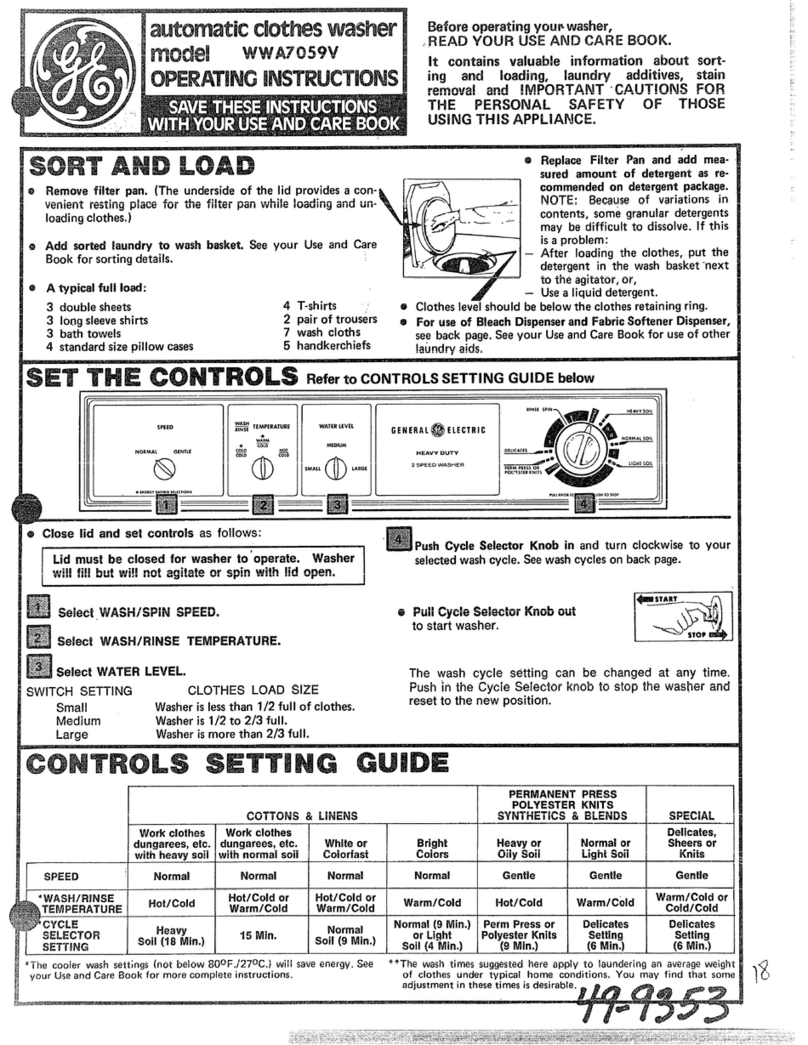
GE
GE WWA7Q59V User manual
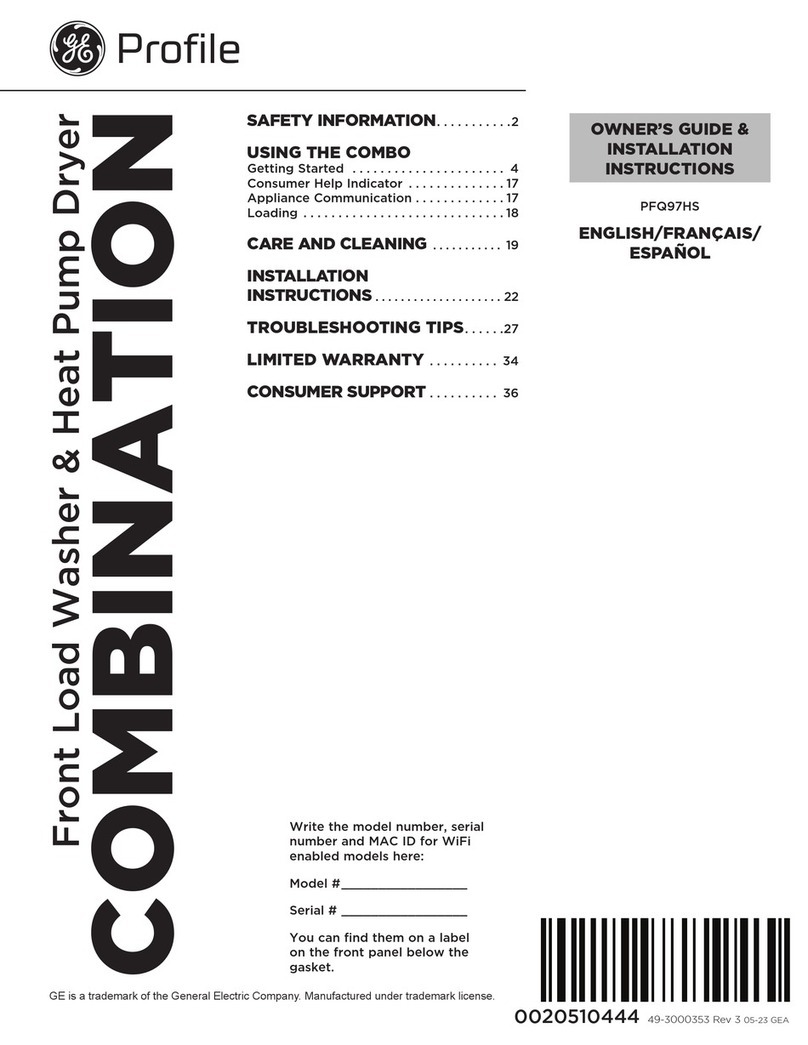
GE
GE Profile PFQ97HS Technical Document
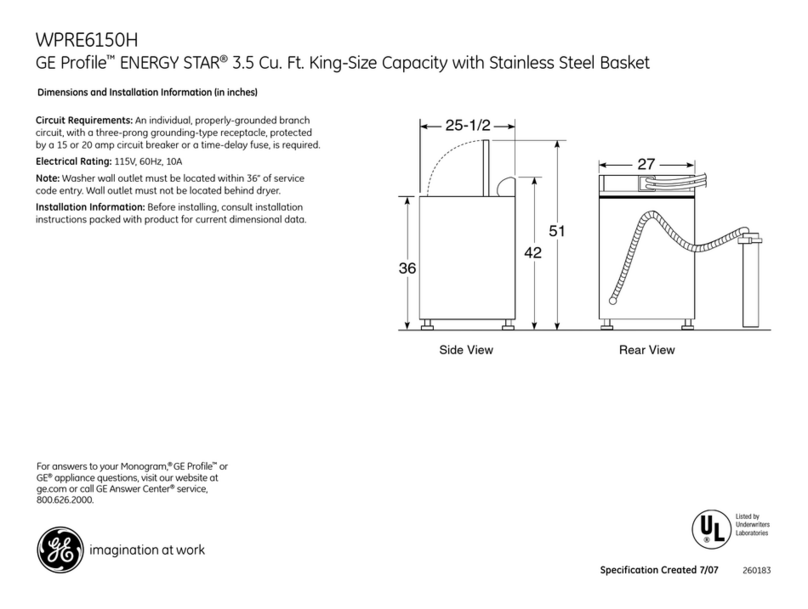
GE
GE Profile ENERGY STAR WPRE6150H Manual
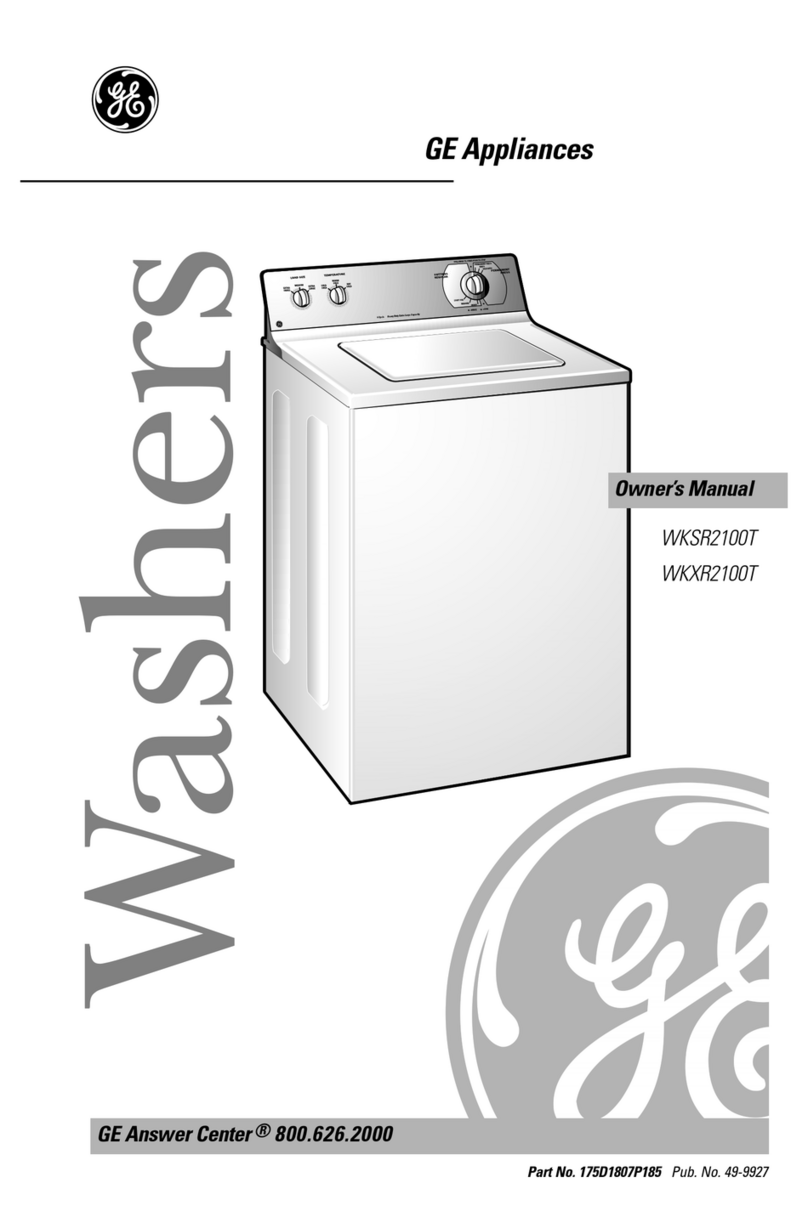
GE
GE WKSR2100T User manual
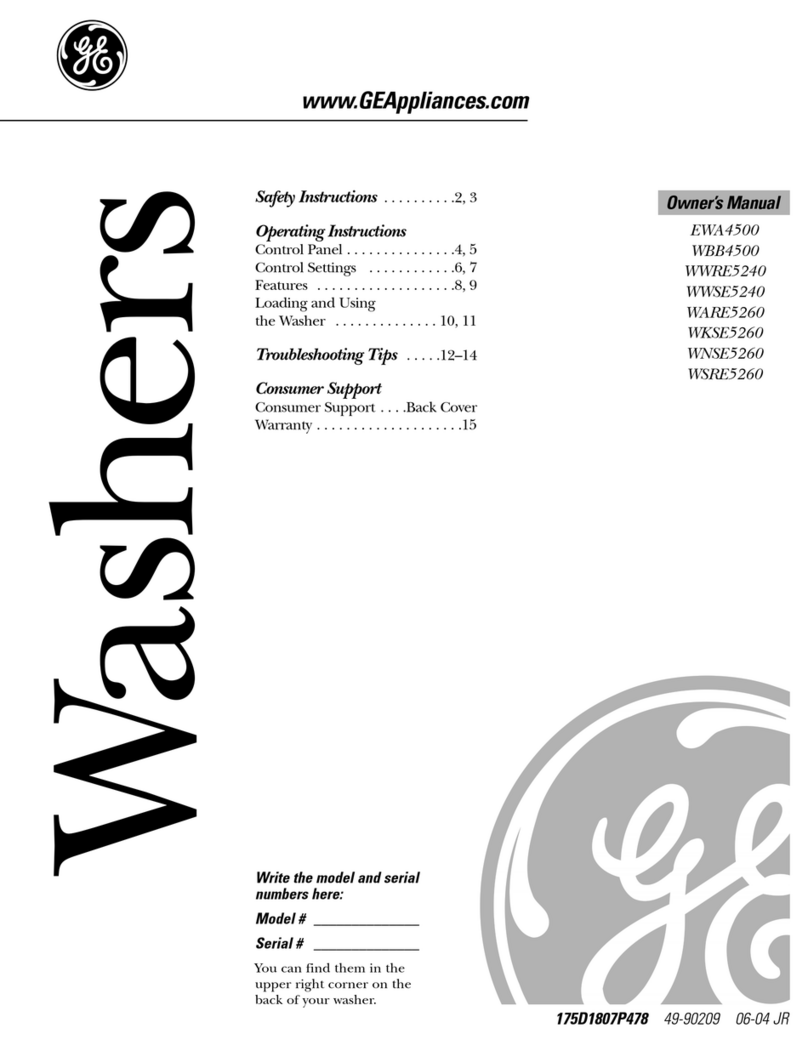
GE
GE EWA4500 User manual

GE
GE WCVH6800JBB User manual