GEM 1240 User manual

GEMÜ 1240
Electrical position indicator
Operating instructions
EN
further information
webcode: GW-1240

All rights including copyrights or industrial property rights are expressly reserved.
Keep the document for future reference.
© GEMÜ Gebr. Müller Apparatebau GmbH & Co. KG
24.05.2022
www.gemu-group.com2 / 18GEMÜ 1240

Contents
1 General information ............................................. 4
1.1 Information .................................................... 4
1.2 Symbols used ................................................ 4
1.3 Warning notes ............................................... 4
2 Safety information ............................................... 4
3 Product description ............................................. 5
3.1 Construction .................................................. 5
3.2 Description ..................................................... 5
3.3 Function ......................................................... 5
3.4 Product label ................................................. 5
4 GEMÜ CONEXO .................................................... 5
5 Correct use .......................................................... 6
6 Order data ........................................................... 7
6.1 Order codes ................................................... 7
6.2 Order example ............................................... 7
7 Technical data ..................................................... 8
8 Dimensions .......................................................... 9
9 Manufacturer's information .................................. 10
9.1 Delivery .......................................................... 10
9.2 Packaging ...................................................... 10
9.3 Transport ....................................................... 10
9.4 Storage ........................................................... 10
10 Assembly and installation .................................... 10
11 Electrical connection ........................................... 14
12 Troubleshooting .................................................. 15
13 Inspection and maintenance ................................ 15
14 Disassembly ........................................................ 15
15 Disposal .............................................................. 15
16 Returns ................................................................ 15
17 Declaration of Incorporation according to
2006/42/EC (Machinery Directive) ....................... 16
18 Declaration of conformity according to 2014/30/
EU (EMC Directive) ............................................... 17
GEMÜ 1240www.gemu-group.com 3 / 18

www.gemu-group.com4 / 18GEMÜ 1240
1 General information
1 General information
1.1 Information
- The descriptions and instructions apply to the standard ver-
sions. For special versions not described in this document
the basic information contained herein applies in combina-
tion with any additional special documentation.
- Correct installation, operation, maintenance and repair work
ensure faultless operation of the product.
- Should there be any doubts or misunderstandings, the Ger-
man version is the authoritative document.
- Contact us at the address on the last page for staff training
information.
1.2 Symbols used
The following symbols are used in this document:
Symbol Meaning
Tasks to be performed
Response(s) to tasks
– Lists
1.3 Warning notes
Wherever possible, warning notes are organised according to
the following scheme:
SIGNAL WORD
Type and source of the danger
Possible
symbol for the
specific
danger
Possible consequences of non-observance.
Measures for avoiding danger.
Warning notes are always marked with a signal word and
sometimes also with a symbol for the specific danger.
The following signal words and danger levels are used:
DANGER
Imminent danger!
▶Non-observance can cause death or
severe injury.
WARNING
Potentially dangerous situation!
▶Non-observance can cause death or
severe injury.
CAUTION
Potentially dangerous situation!
▶Non-observance can cause moderate
to light injury.
NOTICE
Potentially dangerous situation!
▶Non-observance can cause damage to
property.
The following symbols for the specific dangers can be used
within a warning note:
Symbol Meaning
Danger of explosion
Electric shock by high voltage
2 Safety information
The safety information in this document refers only to an indi-
vidual product. Potentially dangerous conditions can arise in
combination with other plant components, which need to be
considered on the basis of a risk analysis. The operator is re-
sponsible for the production of the risk analysis and for com-
pliance with the resulting precautionary measures and re-
gional safety regulations.
The document contains fundamental safety information that
must be observed during commissioning, operation and main-
tenance. Non-compliance with these instructions may cause:
- Personal hazard due to electrical, mechanical and chemical
effects.
- Hazard to nearby equipment.
- Failure of important functions.
- Hazard to the environment due to the leakage of dangerous
materials.
The safety information does not take into account:
- Unexpected incidents and events, which may occur during
installation, operation and maintenance.
- Local safety regulations which must be adhered to by the
operator and by any additional installation personnel.
Prior to commissioning:
1. Transport and store the product correctly.
2. Do not paint the bolts and plastic parts of the product.
3. Carry out installation and commissioning using trained
personnel.
4. Provide adequate training for installation and operating
personnel.
5. Ensure that the contents of the document have been fully
understood by the responsible personnel.
6. Define the areas of responsibility.
7. Observe the safety data sheets.
8. Observe the safety regulations for the media used.

www.gemu-group.com 5 / 18 GEMÜ 1240
During operation:
9. Keep this document available at the place of use.
10. Observe the safety information.
11. Operate the product in accordance with this document.
12. Operate the product in accordance with the specifications.
13. Maintain the product correctly.
14. Do not carry out any maintenance work and repairs not de-
scribed in this document without consulting the manufac-
turer first.
In cases of uncertainty:
15. Consult the nearest GEMÜ sales office.
3 Product description
3.1 Construction
1
2
5
3
4
Item Name Materials
1 Housing cover PC
2 Housing base PPS
3 Electrical connection SS, PP
4 Adapter piece SS
5 Mounting kit, valve spe-
cific
SS, PP
Seals NBR
3.2 Description
The GEMÜ 1240 electrical position indicator is suitable for
mounting to pneumatically operated linear actuators. The po-
sition of the valve spindle is reliably detected electronically
and fed back via microswitches or proximity switches, using
play-free and non-positive mounting. The product has been
designed specially for valves with a stroke of 5 to 75 mm.
3.3 Function
The GEMÜ 1240 electrical position indicator is used to feed
back and verify the position of valves operated with pneu-
matic linear actuators. The spindle of the electrical position
indicator is connected to the valve spindle of the linear actu-
ator through play-free and non-positive mounting and is
moved along with the linear movement of the actuator. The
cam attached to the spindle then actuates the built-in mi-
croswitches or proximity switches, which are used for elec-
tronic signal transmission. Depending on the version, the elec-
trical position indicator is equipped with one to two mi-
croswitches or proximity switches.
3.4 Product label
Design in accordance with order data
Item number
Device-specific data
Year of manufacture
XXXXXXX | XXXX
Traceability number Serial number
The month of manufacture is encoded in the traceability num-
ber and can be obtained from GEMÜ. The product was manu-
factured in Germany.
The manufacturing month is coded under the traceability
number and can be requested from GEMÜ. The product was
manufactured in Germany.
4 GEMÜ CONEXO
Order variant
In the corresponding design with CONEXO, this product has
an RFID chip (1) for electronic identification purposes. The po-
sition of the RFID chip can be seen below. The CONEXO pen
helps read out information stored in the RFID chips. The CON-
EXO app or CONEXO portal is required to view this informa-
tion.
1
For further information please read the operating instructions
for CONEXO products or the CONEXO datasheet.
Products such as the CONEXO app, the CONEXO portal and
the CONEXO pen are not included in the scope of delivery and
need to be ordered separately.
4 GEMÜ CONEXO

www.gemu-group.com6 / 18GEMÜ 1240
5 Correct use
5 Correct use
DANGER
Danger of explosion
▶Risk of death or severe injury.
●Do not use the product in potentially
explosive zones.
WARNING
Improper use of the product
▶Risk of severe injury or death.
▶Manufacturer liability and guarantee will be void.
●Only use the product in accordance with the operating
conditions specified in the contract documentation and in
this document.
The product is not intended for use in potentially explosive
areas.
The product is designed for fitting to a GEMÜ valve in order to
detect the position of linear actuators electrically. It is non-
positively connected with the actuator spindle by means of a
mounting kit (spring, operating bush). The valve end positions
and the integrated travel sensor can be controlled via the elec-
trical connections.
●Use the product in accordance with the technical data.

6 Order data
The order data provide an overview of standard configurations.
Please check the availability before ordering. Other configurations available on request.
Note: A valve specific mounting kit is required for assembly. For designing the mounting kit, the valve type, nominal size, control
function and actuator size must be stated.
Order codes
1 Type Code
Electrical position indicator 1240
2 Fieldbus Code
Without 000
3 Accessory Code
Accessory Z
4 Housing material Code
PPS base, PC cover 01
5 Device version Code
Open A0
Open/Closed AZ
Closed Z0
6 Electrical connection Code
M16 Skintop cable gland 03
7 Option Code
Without 00
8 Switch Code
Change-over contact, microswitch, 24 V DC, 250 V AC
Crouzet, V4S, SPDT
M1
Proximity switch, 2-wire, NAMUR
P+F, HJ1,5-6,5-15-N-Y180094
N1
Proximity switch, 3-wire, normally open contact, PNP,
10–30 V DC
Balluff, BES 516-371-SA 16
P1
9 Connection diagram Code
Microswitch, change-over contact, SPDT M1
Terminals, NAMUR N1
3-wire P1
10 Travel sensor version Code
Potentiometer, 75 mm length 075
11 CONEXO Code
Without
Integrated RFID chip for electronic identification and
traceability
C
Order example
Ordering option Code Description
1 Type 1240 Electrical position indicator
2 Fieldbus 000 Without
3 Accessory Z Accessory
4 Housing material 01 PPS base, PC cover
5 Device version A0 Open
6 Electrical connection 03 M16 Skintop cable gland
7 Option 00 Without
8 Switch M1 Change-over contact, microswitch, 24 V DC, 250 V AC
Crouzet, V4S, SPDT
9 Connection diagram M1 Microswitch, change-over contact, SPDT
10 Travel sensor version 075 Potentiometer, 75 mm length
11 CONEXO Without
6 Order data
www.gemu-group.com 7 / 18 GEMÜ 1240

7 Technical data
7.1 Temperature
Ambient temperature: 0 — 60 °C
Storage temperature: -10 — 70 °C
7.2 Product conformity
EMC Directive: 2014/30/EU
Low Voltage
Directive:
2014/35/EU
7.3 Mechanical data
Installation position: Optional
Weight: 420 g
Protection class: IP 67
Travel sensor: 5 — 75 mm
7.4 Electrical data
Electrical connection
type:
Connection thread: M16 x 1.5, WAF 19
Cable diameter: 4.5 to 10mm
Recommended wire cross section: 0.75 mm² x 8 cables
Switch type: Code M1 Code N1 Code P1
Microswitch, change-over con-
tact, SPDT
2-wire NAMUR 3-wire, normally open contact,
PNP
Supply voltage: Switch
Code M1 Code N1 Code P1
24 V DC, 250 V AC 8 V DC 10 to 30 V DC
Current consumption: Switch
Code M1 Code N1 Code P1
for DC: 5 mA to 5 A
for AC: 100 mA to 6 A
≥ 3 mA (undamped)
≤ 1 mA (damped)
0–200 mA
www.gemu-group.com8 / 18GEMÜ 1240
7 Technical data

8 Dimensions
Square
142
Ø 90
14,5
86,5 26
11
SW 24
Dimensions in mm
GEMÜ 1240www.gemu-group.com 9 / 18
8 Dimensions

www.gemu-group.com10 / 18GEMÜ 1240
9 Manufacturer's information
9 Manufacturer's information
9.1 Delivery
●Check that all parts are present and check for any damage
immediately upon receipt.
The product's performance is tested at the factory. The scope
of delivery is apparent from the dispatch documents and the
design from the order number.
9.2 Packaging
The product is packaged in a cardboard box which can be re-
cycled as paper.
9.3 Transport
1. Only transport the product by suitable means. Do not drop.
Handle carefully.
2. After the installation dispose of transport packaging ma-
terial according to relevant local or national disposal regu-
lations / environmental protection laws.
9.4 Storage
1. Store the product free from dust and moisture in its ori-
ginal packaging.
2. Avoid UV rays and direct sunlight.
3. Do not exceed the maximum storage temperature (see
chapter "Technical data").
4. Do not store solvents, chemicals, acids, fuels or similar
fluids in the same room as GEMÜ products and their spare
parts.
10 Assembly and installation
1. Observe the national regulations and provisions.
2. Observe the installer provisions.
3. Lay cables securely and protect them from damage.
4. Connect open wire ends in a junction box with protection
class IP20 and higher or outside the EX area
10.1 Preparations for installing the valve (linear
actuator)
1. Move the actuator A into zero position (actuator vented).
2. Remove optical position indicator 2 and / or protective cap
1 from the actuator top.
A
12
10.2 Information on use in damp conditions
1
The following information is intended to help when installing
and operating the product in damp conditions.
1. Lay cables and pipework so that no condensate or rain
water that remains on the pipework / cables can enter the
cable glands or plugs of the product.
2. Check that all cable glands or plugs are positioned cor-
rectly
3. Check the sealing ring 1 for any damage and correct posi-
tioning before tightening the cover.
10.3 Mounting kit assembly
Item Name Item Name
1 Spindle 7 Flange plate
2 Spring 8 Screws
3 Operating bush 9 Pressure disc*
4 Distance piece 10 O-ring*
5 O-ring 11 O-ring*
6 Adapter
* Included depending on version.
CAUTION
Pretensioned spring!
▶Damage to the device.
●Slowly release the tension in the spring.
CAUTION
Do not scratch the spindle!
▶A damaged spindle surface may cause failure of the
travel sensor.

www.gemu-group.com 11 / 18 GEMÜ 1240
1
4
1
2
3
1. Pull out the
spindle 1.
2. Align the indentation of the dis-
tance piece 4 to the spring and push
it over the spindle 1 using the spring
2 and fix it in place using the operat-
ing bush 3.
5
6
3. Tighten the oper-
ating bush 3 by turn-
ing it
clockwise.
4. Affix the O-ring 5 and the adapter
6.
7
8
5. Attach the flange
plate 7
6. Screw the flange plate on tight us-
ing screws 8 (1 – 1.5 Nm).
- Push in the spindle until it pushes against the spring and
then slowly release the pressure on the spring.
NOTICE
▶For some valves (e.g. GEMÜ 650 and GEMÜ 687) it is ne-
cessary to fit a pressure disc between the threaded ad-
apter and the actuator head. This is included in the re-
quired mounting kits, sometimes with an additional O-ring
(only GEMÜ 650 with normally open and double-acting
control function – code 2+3).
▶If the pressure disc does not have a groove for a seal, this
will already be inserted in the groove provided at the ad-
apter opening of the actuator head (e.g. GEMÜ 687 with
normally open control function – code 2).
9
6
11
10
Insert the O-ring 11 (if in-
cluded) into the correspond-
ing groove on the adapter 6.
If included: Push the pres-
sure disc 9 over the adapter
6 and insert the O-ring 10 in
the intended groove of the
pressure disc.
10.4 Assembling the adapter (linear actuator)
With some mounting kits it is necessary to install an adapter
as well. This adapter is enclosed with the required mounting
kits. Valves with a normally open and double acting control
function (code 2+3) also include additional O-rings (1+2).
1
3
2
1. Move the actuator to the closed position.
2. Place O-rings 1 and 2 into adapter 3.
3. Screw adapter 3 into the actuator opening as far as it will
go and tighten.
10 Assembly and installation

www.gemu-group.com12 / 18GEMÜ 1240
10 Assembly and installation
10.5 Assembling the stroke limiter (linear actuator)
5
5
4
3
2
1
6
8
9
7.1
7.2
Option1 Option2
1. Screw distance piece 5 onto/
into actuator spindle 6.
2. Move the actuator to the
closed position.
3. Insert the O-ring 7.1 in the
stroke limiter 1.
4. Insert the O-ring 7.2 in the
washer 4.
5. Screw stroke limiter 1 with
nut 2, seal 3 and washer 4
into the actuator opening.
6. Set stroke limiter 1 to the re-
quired stroke.
7. Make sure that the minimum
stroke is reached.
8. Secure stroke limiter 1 with
nut 2.
Key
1 Stroke limiter 7.1 1)
7.2 1)
O-ring
2 Nut 8 Protective cap
3 1) Seal 9 Position indicator
4 1) Washer 10 Operating bush
5 2) Distance piece 11 Spindle
6 Actuator spindle 12 Travel sensor
1) Only available for valves with the NO and DA control functions.
2) Only included in required mounting kits. The design depends on
the valve.
10.6 Assembling and installing the electrical position
indicator
DANGER
Danger of explosion
▶Risk of death or severe injury.
●Do not use the product as a step or
foothold.
●Prior to commissioning, ensure that
the cover is fully closed and that the
housing and the O-ring are not dam-
aged.
1. Move the actuator into the OPEN position.
2. Place the product as far as it will go into the actuator
opening, insert adapter 3 (see chapter 9.3) or stroke lim-
iter 1 (see chapter 9.4) and screw in clockwise against the
initial spring tension.
3. Use the spanner flat of the travel sensor to tighten the
product.
4. Turn the housing clockwise to align the pneumatic or elec-
trical connections.
5. Set the switch on the product.
CAUTION
Incorrect installation of the product.
▶Damage to the housing.
●Only tighten the product using the spanner flats provided
for this purpose.

www.gemu-group.com 13 / 18 GEMÜ 1240
10.7 Setting the switching positions
2
1. Turn the cover anticlock-
wise to open the bayonet
fitting.
2. Remove cover 2.
3
4
5
6
Setting the upper switching
position:
Setting the lower switching
position:
3. Move the valve to the
OPEN position.
4. Squeeze and hold red
levers 3.
5. Push switch 4 on the
toothed bar into the de-
sired position.
6. Release red levers 3.
ðSwitch 4 engages.
ðThe upper switching
position is set.
7. Move the valve to the
CLOSED position.
8. Squeeze and hold red
levers 5.
9. Push switch 6 on the
toothed bar into the de-
sired position.
10. Release red levers 5.
ðSwitch 6 engages.
ðThe lower switching po-
sition is set.
11. Make the electrical connection.
2
12. After completing the electrical connection, carefully pull
the connection cable taut.
13. Make sure that seal 1 is fitted correctly and is not dam-
aged.
14. Put on cover 2 so that the bayonet fitting is inserted cor-
rectly and turn cover 2 clockwise.
15. Restore the power supply.
16. To check that everything is working correctly, open and
close the valve and observe the signalling.
17. If the settings need to be readjusted, switch off power to
the product again and repeat the steps in "Setting the
switching positions".
10 Assembly and installation

11 Electrical connection
CAUTION
Electric shock by high voltage
▶Danger of injury or death caused by electric shock.
●Power supply varies depending on version.
●Switch off power to the product when working on the product.
●Work on electrical connections only by qualified trained personnel.
11.1 Microswitch, ordering option Connection diagram code M1
11.1.1 Connection diagram
1
4
2 1
4
2
1
2
3
S1
4
5
6
S2
CLOSED
OPEN
11.2 2-wire NAMUR proximity switch, ordering option Connection diagram code N1
11.2.1 Connection diagram
OPEN
S1
L+
L-
L+
L-
1
2
3
4
5
6
S2
CLOSED
11.3 3-wire proximity switch, ordering option Connection diagram code P1
11.3.1 Connection diagram
S2
L+L+
L- L-
1
2
3
4
5
6
S1
CLOSED
OPEN
www.gemu-group.com14 / 18GEMÜ 1240
11 Electrical connection

www.gemu-group.com 15 / 18 GEMÜ 1240
12 Troubleshooting
Error Error cause Troubleshooting
No stroke No mounting kit
available
Check mounting kit
Process valve
faulty
Replace process
valve
Wrong mounting kit
installed
Replace mounting
kit
No feedback Incorrect assembly Check assembly,
wiring and connec-
tion
Switch not set Set switch
Wrong mounting kit
installed
Replace mounting
kit
Voltage is not con-
nected
Connect voltage
Cover cannot be at-
tached
Sealing ring inser-
ted incorrectly
Insert sealing ring
correctly
Sealing ring dam-
aged
Replace sealing
ring
Cables protruding
over the edge of the
base
Check the cable
routing and shorten
the cables if neces-
sary
13 Inspection and maintenance
NOTICE
Exceptional maintenance work!
▶Damage to the GEMÜ product.
●Any maintenance work and repairs not described in these
operating instructions must not be performed without
consulting the manufacturer first.
The operator must carry out regular visual examination of the
products depending on the operating conditions and the po-
tential danger in order to prevent leakage and damage.
1. Have servicing and maintenance work performed by
trained personnel.
2. Wear appropriate protective gear as specified in plant op-
erator's guidelines.
3. Shut off plant or plant component.
4. Secure plant or plant component against recommission-
ing.
5. Depressurize the plant or plant component.
6. Actuate products which are always in the same position
four times a year.
7. Carry out inspection and maintenance for products in the
potentially explosive area to DIN EN 60079-17.
13.1 Spare parts
No spare parts are available for this product. If it is faulty,
please return it to GEMÜ for repair.
13.2 Cleaning the product
- Do not clean the product with a high pressure cleaning
device.
14 Disassembly
1. Disassemble in reverse order to assembly.
2. Unscrew the electrical wiring.
3. Disassemble the product. Observe warning notes and
safety information.
15 Disposal
1. Pay attention to adhered residual material and gas diffu-
sion from penetrated media.
2. Dispose of all parts in accordance with the disposal regu-
lations/environmental protection laws.
3. Dispose of electronic components separately.
16 Returns
Legal regulations for the protection of the environment and
personnel require that the completed and signed return deliv-
ery note is included with the dispatch documents. Returned
goods can be processed only when this note is completed. If
no return delivery note is included with the product, GEMÜ
cannot process credits or repair work but will dispose of the
goods at the operator's expense.
1. Clean the product.
2. Request a return delivery note from GEMÜ.
3. Complete the return delivery note.
4. Send the product with a completed return delivery note to
GEMÜ.
16 Returns

www.gemu-group.com16 / 18GEMÜ 1240
17 Declaration of Incorporation according to 2006/42/EC (Machinery Directive)
17 Declaration of Incorporation according to 2006/42/EC (Machinery Directive)

www.gemu-group.com 17 / 18 GEMÜ 1240
18 Declaration of conformity according to 2014/30/EU (EMC Directive)
18 Declaration of conformity according to 2014/30/EU (EMC Directive)

GEMÜ Gebr. Müller Apparatebau GmbH & Co. KG
Fritz-Müller-Straße 6-8, 74653 Ingelfingen-Criesbach, Germany
Phone +49 (0) 7940 1230 · [email protected]
www.gemu-group.com
Subject to alteration
05.2022 | 88729239
Table of contents
Other GEM Measuring Instrument manuals
Popular Measuring Instrument manuals by other brands
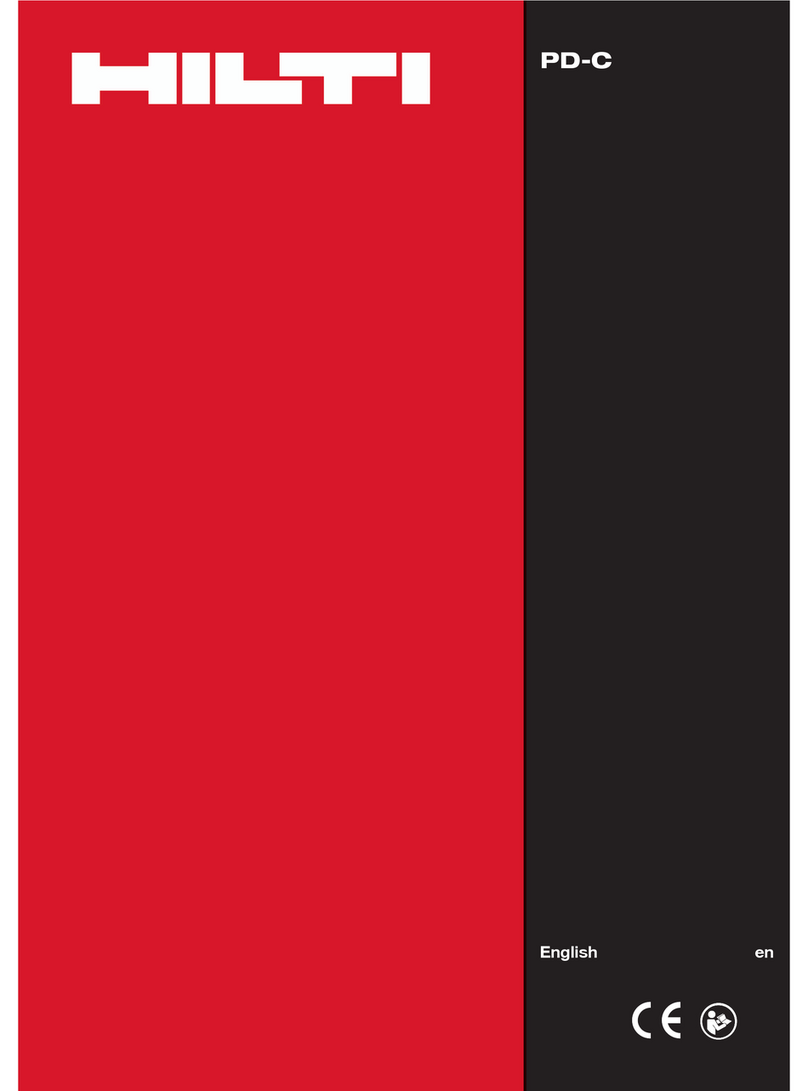
Hilti
Hilti HILTI PD-C operating instructions
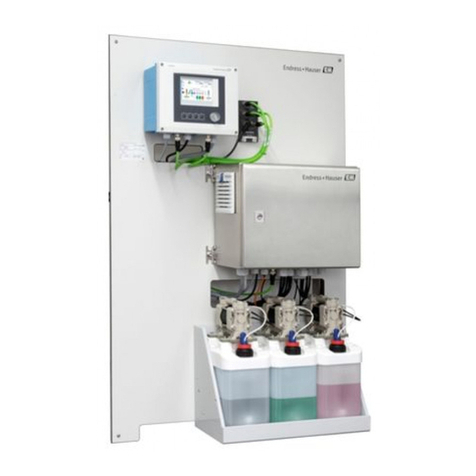
Endress+Hauser
Endress+Hauser Liquiline Control CDC90 operating instructions
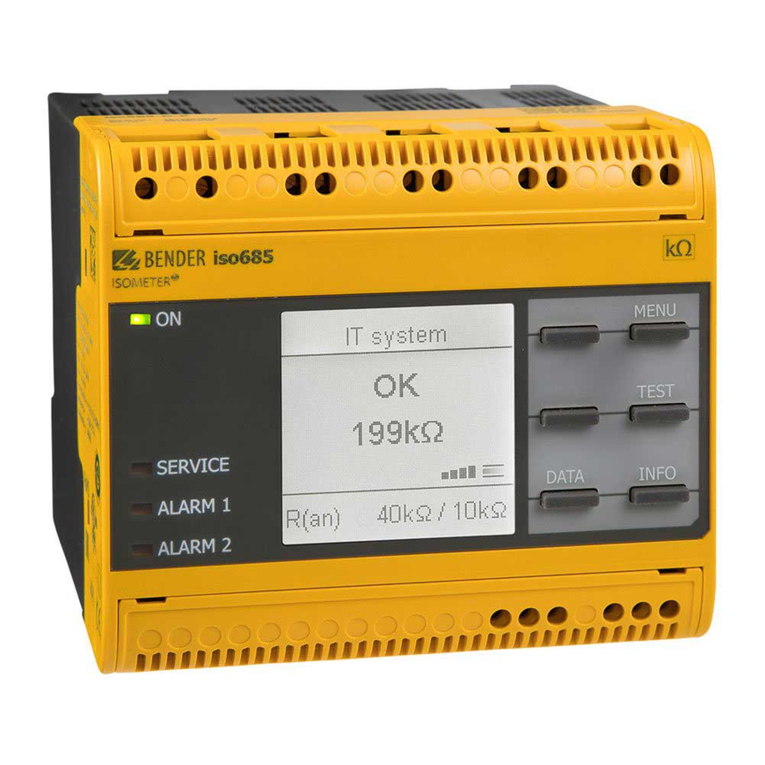
Bender
Bender ISOMETER isoRW685W-D manual
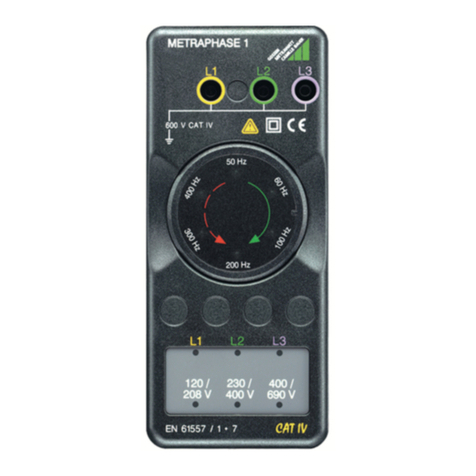
Gossen MetraWatt
Gossen MetraWatt METRAPHASE 1 operating instructions

AEG
AEG LMG 50 Original instructions
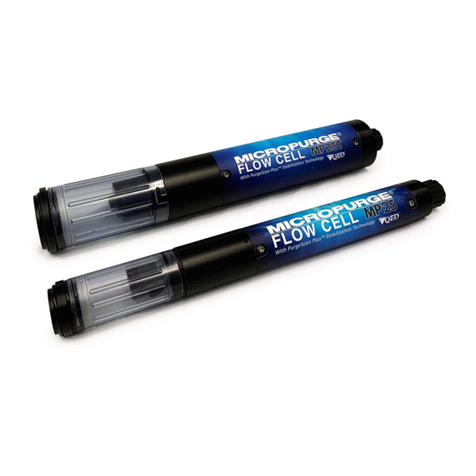
QED
QED MicroPurge MP25 Operation manual