Genesis LiveDrive LDD 1800 Series User manual

LiveDrive® Direct Drive
User Manual
LiveDrive
LDD 1800 Series
®
Motion Redefined
105678-C
LDD 1800 Series


LDD 1800 Series User Manual 3
105678-C
Copyright
Copyright 2022. Genesis Motion Solutions, LP. All rights reserved.
Printed in Canada.
Trademarks
LiveDrive, MOTION REDEFINED, and the G logo design are trademarks owned by Genesis Motion Solutions, LP in the United
States, and may be registered in certain jurisdictions.
All other trademarks that appear are the property of their respective owners.
Permissions and Restrictions
Information in this publication is subject to change without notice. No part of this document may be reproduced or transmitted in
any form, by photocopy, microfilm, xerography, or any other means, or incorporated into any information retrieval system, elec-
tronic or mechanical, for any purpose, without the express permission of Genesis Motion Solutions, LP.
Published By
Genesis Motion Solutions Canada, LP
6279 202 St Langley, BC Canada V2Y 1N1
genesismotion.com
+1 604 800 1907
Certifications
UL file #E515181
Revision Release Date History
A May 5, 2022 Production release.
B July 20, 2022 Minor edits, post technical review.
C March 1, 2023 Removed specifications (datasheet and web only), updated cabling information, comany name and logo.
Document Control
Document number: 105678

LDD 1800 Series User Manual 4
105678-C
Table of Contents
1. About This Manual ............................................................................................................................................................................... 6
2. Safety Instructions ...............................................................................................................................................................................7
2.1 Safety Symbols.................................................................................................................................................................................................... 7
2.2 Operating Precautions .....................................................................................................................................................................................9
2.3 Operating Environment ....................................................................................................................................................................................9
3. Product Overview ...............................................................................................................................................................................10
3.1 Front View ........................................................................................................................................................................................................... 10
3.2 Rear View............................................................................................................................................................................................................ 11
3.3 Product Nomenclature ....................................................................................................................................................................................12
3.4 Selection and Sizing ........................................................................................................................................................................................12
4. Permissible Shaft Loads...................................................................................................................................................................14
5. Intergrated Features.......................................................................................................................................................................... 15
5.1 Holding Brake .................................................................................................................................................................................................... 15
5.2 Temperature Sensors..................................................................................................................................................................................... 15
6. Housing Materials ..............................................................................................................................................................................16
7. Interfaces .............................................................................................................................................................................................. 17
7.1 Connector Block .................................................................................................................................................................................................17
7.2 Pinouts .................................................................................................................................................................................................................17
7.3 Cabling ................................................................................................................................................................................................................ 18
8. Handling and Transportation..........................................................................................................................................................20
8.1 State on Delivery.............................................................................................................................................................................................. 20
8.2 Handling and Transportation ....................................................................................................................................................................... 20
8.3 Storage.............................................................................................................................................................................................................. 20
9. Installation and Commissioning ..................................................................................................................................................... 21
9.1 Safety Precautions.............................................................................................................................................................................................21
9.2 Design and Installation Positions..................................................................................................................................................................21
9.3 Mechanical Mounting and Assembly..........................................................................................................................................................22
9.4 Sealing Output Interface................................................................................................................................................................................23
9.5 Electrical Connections ...................................................................................................................................................................................24
9.6 Drive Setup and Configuration .....................................................................................................................................................................24

LDD 1800 Series User Manual 5
105678-C
10. Operation........................................................................................................................................................................................... 25
10.1 Commissioning................................................................................................................................................................................................25
10.2 Braking..............................................................................................................................................................................................................25
10.3 Cleaning ...........................................................................................................................................................................................................25
10.4 Deactivation ....................................................................................................................................................................................................26
10.5 Disposal............................................................................................................................................................................................................26
11. Maintenance...................................................................................................................................................................................... 27
11.1 Maintenance .....................................................................................................................................................................................................27
12. Troubleshooting ............................................................................................................................................................................... 29
13. Service and Support .......................................................................................................................................................................30
13.1 Service and Support...................................................................................................................................................................................... 30
14. Certification and Compliance........................................................................................................................................................ 31
14.1 List of Standards ..............................................................................................................................................................................................31
14.2 Declaration of UL Rated Performance......................................................................................................................................................32

LDD 1800 Series User Manual 6
105678-C
1. About This Manual
The purpose of this manual is to provide clear information on the wide range of application options when using the LiveDrive®
LDD 1800 series motors from Genesis Motion Solutions.
It contains information for robot and machinery designers responsible for selecting, operating, and maintaining the motor.
This manual also contains an overview of the various features, specifications of the product, as well as information on the setup,
installation and commissioning, operation and maintenance of the LDD 1800 series motors.
Unless otherwise specified, all measurements within this guide are in metric units.
Scope
The information in this user manual is intended for qualified technicians or operators who are tasked with installing, commission-
ing, operating, troubleshooting or maintaining a system.
Knowledge and Permissions
We assume that any personnel working with this product have a good working knowledge of servomotor applications, and access
to any and all tools or safety equipment required.
Important
This manual is limited to the motor alone and does not include the robot or system in which it is used.

LDD 1800 Series User Manual 7
105678-C
2. Safety Instructions
This section summarizes the safety precautions, hazards and mitigation actions associated with handling, installing, and
operating LiveDrive® LDD 1800 series motors. Tasks such as installing, commissioning, tuning, and operating electric motors
should only be done by qualified personnel.
If the content in this document is unclear, please contact Genesis Motion Solutions prior to installation or operation. Non-compli-
ance with the safety and technical recommendations may lead to injury or damage to property and environment.
2.1 Safety Symbols
Electric Shock
Electric shock may result in serious injury or death. The motor operates at high voltages and may become energized under
certain circumstances.
Sparking or Arcing Hazard
Sparking or arcing may be present in the event of a motor failure.
No Pacemakers
The motor is a high current electrical device and may present EMI levels dangerous to those with pacemakers or other sensi-
tive medically necessary equipment.
High Temperature
The motor operates at high internal temperatures. The motor, in addition to the mounting equipment, cables, and control
panel may become hot during operation.
Fire
The motor may create a fire hazard in the event of an equipment failure.
Crushing, Impacting, Pinching
The motor is designed to rotate at high speeds. Depending on the equipment setup, risk of crushing, impact or pinching may
be present.
Entanglement
The motor is designed to rotate at high speeds. Depending on the equipment setup, risk of entanglement may be present.
Warning
Death or severe bodily injury can occur.
!

LDD 1800 Series User Manual 8
105678-C
2.1.1 Shock Hazard
• The motor operates at hazardous voltages. Electric shock may result in serious injury or death.
• Do not touch the motor, shaft or connected conductive components (the load on the shaft) while the motor is enabled.
• Do not conduct work on live (energized) equipment. Prior to connecting or disconnecting cables, ensure that the system
power is off and locked out.
• Do not disassemble the motor. Only qualified personnel may work on the motor and must use insulated tools
(as per IEC 60900).
• Avoid contact with power connector pins, since back-driving the motor can create hazardous voltages (Back EMF) on the
power wires.
• Do not operate the motor with any exposed leads. Terminate or insulate and protect any unused leads on the drive end of
the cables.
• The motor drive (provided by customer) must include fault detection that will disconnect power to the motor in the event of
a short circuit (for example, line-to-line and line-to-ground), or other fault (for example, over-speed, over-voltage and over-
current).
• The motor drive (provided by customer) must include a main disconnect and circuit breaker on the main power for overload
protection.
• Branch circuit power-surge protection shall be provided by customer in accordance with National/ International electrical
code and regulations. It must include a main disconnect, circuit breaker and surge protection device (SPD) on the main
power for overvoltage and overcurrent protection.
2.1.2 Sparking/Arcing Hazard
Motor or component overheating may result in sparking/arcing and motor failure.
• Verify that system grounding is in place. For information on motor grounding through the power cable, see section "7.3
Cabling".
• Ensure the internal motor temperature sensor is connected to a thermal shutdown circuit.
• Do not allow the motor to remain in a stall condition. A stall condition is defined as when the motor is generating torque but
prevented from rotating.
Removing connectors while power is enabled may result in sparking/arcing or unexpected motion. Excessive bending of cables
may result in internal cable damage.
• Disable all power to the motor before disconnecting any cables or terminals.
• Ensure there is enough space around the motor to safely bend the cables.
2.1.3 Electromagnetic and Magnetic Interference
Electromagnetic interference may affect performance of personal medical equipment and implants. Personnel with personal
electric medical equipment or a ferromagnetic prosthesis must not operate the motor.

LDD 1800 Series User Manual 9
105678-C
2.1.4 Handling and Installation Safety
LiveDrive® motors can weigh upwards of 16 kg. Carrying or lifting the motor without adequate protection (such as safety footwear),
assistance, or safe lifting practices, may result in equipment damage and personal harm.
• Wear adequate personal protection equipment and follow safe lifting practices.
2.2 Operating Precautions
The motor can impart significant mechanical energy:
• Unexpected movements of the motor (and attached components) may occur due to control instability, wiring damage or
internal motor damage.
• During a sudden power-shutdown event, the motor may continue to move.
• Components attached to the motor housing and shaft may loosen over time (this could occur if inappropriate bolted joints
are not correctly torqued or if there is excessive vibration) and may be ejected as projectiles.
Establish an appropriate boundary around the motor during operation or troubleshooting. Appropriate shielding and/or working
boundaries are especially important when working with eccentric loads.
• Ensure the e-stop (emergency stop button) is wired correctly and nearby the operator.
• Perform regular verifications of critical mechanical connections.
• Monitor for unusual vibration and noise. Cease operation and resolve issue(s) if unusual vibration or noise are detected.
2.2.1 High Temperatures
The motor, frame, and components attached to the shaft, connectors and cables may become hot during operation.
• Be aware of hot surfaces on the motor. Internal temperatures of 110°C are possible during operation.
• Always ensure parts have had sufficient time to cool prior to touching the motor.
• Ensure the internal motor temperature sensor is connected to a thermal shutdown circuit. Please refer to the motor
datasheet for maximum operating temperature.
2.2.2 Equipment Damage
Inspect the motor for damages prior to installation, commissioning, and operation. Contact Genesis Motion Solutions for addi-
tional
guidance if the motor is damaged.
2.3 Operating Environment
LiveDrive® motors must not be used in applications requiring special environmental considerations; examples include vacuum or
clean room applications, or those with atmospheres that are potentially explosive or radioactive. Contact Genesis Motion Solu-
tions for further information.

LDD 1800 Series User Manual 10
105678-C
3. Product Overview
Genesis Motion Solutions LiveDrive® LDD 1800 series are high torque density, direct-drive motors developed for robotics and
automation machinery. The motors are brushless, permanent-magnet, 3-phase synchronous motors. Loads can be directly
coupled to the output without the need for additional transmission components (i.e. belts or gears). The simple construction of
machines using LDD 1800 series motors allows higher system reliability and cleanliness through the elimination of lubricated
gearboxes.
Compared with other servo motor technology, our LiveDrive® technology delivers much higher torque at comparatively lower
speed. The LDD 1800 series motors are well suited to the following types of applications:
• If factory floor space is at a premium, our reduced motor size means a smaller footprint enabling space efficient designs
• In demanding and highly dynamic applications that require a high torque and low inertia/high stiffness, and instant response
• In highly dynamic packaging or assembly line environments that require higher speed, backlash-free positioning
• In hygienic environments requiring IP67 washdown and no contamination by lubricants
3.1 Front View
Figure 1 — Front view
Output Shaft
Stator
Rotor
Shaft Seal
Front End Cover
End Cap
(Mounting Surface)
Connector Block
Bearing
Frame

LDD 1800 Series User Manual 11
105678-C
3.2 Rear View
Figure 2 — Rear view, two cable connector
Figure 3 — Rear view, one cable power/encoder connector
Power/Temperature Connector
Rear End Cover
Connector Block
Encoder Connector
Rear End Cover
Power/Encoder/Temperature Connector
Connector Block

LDD 1800 Series User Manual 12
105678-C
3.3 Product Nomenclature
The LDD 1800 series motors can be identified using the following nomenclature. Custom models may use additional codes.
3.4 Selection and Sizing
Use the procedure below to size an LDD 1800 series motor to your application. If you need application and sizing help, please
contact the Applications Engineering team.
Product Family
LDD: LDD
Configuration
A: Standard product
X: Custom feature
Sealing
7: IP67
X: Custom feature
Stack Length
30: Short stack
41: Medium stack
50: Intermediate stack
60: Long stack
Other: Application specified
Winding
A: 400-480 VAC
B: 200-230 VAC
X: Custom feature
LDD 1800B-D17-NA
Brake
B: Holding brake
N: No brake
X: Custom feature
Feedback
R1: Rockwell Automation compatible, HIPERFACE DSL®, single turn, absolute *
E1: EnDat 2.2, single turn, absolute
H1: HIPERFACE®, single turn, absolute
D1: HIPERFACE DSL®, single turn, absolute
B1: BiSS-C®, single turn, absolute
XX: Custom feature
Product Series
18: 180mm OD
NOTE: Custom features available on all models.
* R1 feedback compatible with Rockwell Automation under technology license agreement, 202201028

LDD 1800 Series User Manual 13
105678-C
3.4.1 Basic Sizing From Motion Profile
Follow these steps to size an LDD 1800 series motor for your application:
1. Determine the desired motion profile for the application.
2. Compute torque (Nm) vs. time (s) and speed (rpm) vs. time (s).
3. Calculate the RMS (root mean square) torque and speed for the motion profile.
4. Calculate the maximum torque and maximum speed for the motion profile.
5. Confirm that the RMS torque (Nm) and RMS speed (rpm) are within continuous operating range (see torque vs. speed curve)
of the motor, assuming a 100% duty cycle.
6. Confirm that the maximum torque (Nm), maximum speed (rpm) are within the peak operating range of the motor.
7. Ambient temperatures >20°C require derating of the continuous operating range. Ambient temperatures <20°C allow
increased performance. Refer to datasheet for details on the size of the radiation plate. Contact our Applications Engineering
team for performance curves with adjusted temperature.
8. Continuous operating range based on passive cooling with a radiation plate to represent a typical machine installation. Field
performance may vary depending on cooling condition. Contact our Applications Engineering team for more information.
3.4.2 Drive Selection and Sizing
LDD 1800 series motors are controlled by standard 3-phase servo drives. It is important to check compatibility with the servo
drive to realize optimal system performance. Follow the general steps below.
1. Select a drive based on the rated voltage, rated current, and peak current of the motor. The drive must be able to supply the
rated and peak current in order to achieve the rated performance.
2. Determine the appropriate encoder protocol (EnDat 2.2, HIPERFACE®, HIPERFACE DSL®, BiSS-C®) that is compatible with
the selected servo drive.
3. Use a servo drive with PWM frequencies greater than or equal to 8kHz.
4. Refer to the LDD 1800 Series datasheet for motor specifications that will be needed for drive commissioning.
5. For motor assembly questions, contact Genesis Motion Solutions.
For servo drive commissioning questions, please contact the drive manufacturer.
CHECK
• Some industrial servo drives are compatible only with encoders including a proprietary digital nameplate. Check with the
drive manufacturer for encoder compatibility information.

LDD 1800 Series User Manual 14
105678-C
4. Permissible Shaft Loads
The following diagram shows the maximum permissible continuous loads which can be applied to the LDD 1800 series motors.
These loads can be applied individually in any direction. For simultaneous axial, radial, or moment loads please consult with an
Applications Engineering team member.
Figure 4 — Shaft load, all models
F
A
F
R
M
B
• Maximum permissible radial force (FR)
• Maximum permissible axial force (FA)
• Maximum permissible bending moment (MB)
Model 1830x-xxx-xx 1841x-xxx-xx 1850x-xxx-xx 1860x-xxx-xx
Allowable Radial Load N± 1300 ± 1400 ± 1500 ± 1650
Allowable Thrust Load N+250 / -800 +250 / -800 +250 / -800 +250 / -800
Allowable Moment Load Nm ± 75 ± 120 ± 160 ± 200

LDD 1800 Series User Manual 15
105678-C
5. Integrated Features
5.1 Holding Brake
The following table outlines the brake specifications on selected models of the LDD 1800 series.
Brake Information
Holding Torque
18 Nm (20° C)
Supply Voltage
24 VDC
Rated Power
24 W
Nominal Current
1 A
Engaging Delay (after disconnecting current)
3 ms
Engaging Time (after disconnecting current)
10 ms
Release Delay (after connecting current, until 90 %* holding torque is attained)
50 ms
5.2 Temperature Sensors
The following table outlines temperature sensor information on all LDD 1800 series models.
Note: During operation, one temperature sensor must be connected to and monitoring a thermal shutdown at all times.
Type
PT1000 RTD
Operating Temperature
-70 to 260°C
Resistance at 0°C
1000 Ω

LDD 1800 Series User Manual 16
105678-C
6. Housing Materials
The LDD 1800 series consists of parts with several main exterior materials. All finishes are compatible with many standard clean-
ing products and chemicals and are designed to operate in a washdown environment. All exterior gaskets are silicone. For more
information on specific compatibility in the end-user environment, contact Genesis Motion Solutions.
Figure 5 — Housing materials
2
1
1Anodized Aluminum
2Nitrided Steel
3Stainless Steel Fasteners
4Food Grade PTFE Seal
5Silicone Gasket
5
4
3
5

LDD 1800 Series User Manual 17
105678-C
7. 2 Pinouts
Note: PE mechanically fastened to the housing of the motor. N/C = not connected.
*Note: HIPERFACE DSL®configurations have temperature data routed through the encoder data stream.
7. Interfaces
7.1 Connector Block
The LDD 1800 series motors feature a connector block with two straight head connectors or one single connector for
HIPERFACE DSL®models.
Figure 6 — Connector block
Figure 7 — Pinouts
Encoder, temperature
connector (male)
LDD models with one
cable technology
Power, brake
temperature connector (male)
LDD Series
Pin 18xxx-E17-BA 18xxx-D17-BA 18xxx-H17-BA 18xxx-B17-BA 18xxx-E17-NA 18xxx-D17-NA 18xxx-H17-NA 18xxx--B17-NA
1
L1 L1 L1 L1 L1 L1 L1 L1
2
PE PE PE PE PE PE PE PE
3
L2 L2 L2 L2 L2 L2 L2 L2
4
L3 L3 L3 L3 L3 L3 L3 L3
A
BR+ BR+ BR+ BR+ N/CN/CN/CN/C
B
BR- BR- BR- BR- N/CN/CN/CN/C
C
TH- DSL+ *TH- TH- TH- DSL+ *TH- TH-
D
TH+ DSL- *TH+ TH+ TH+ DSL- *TH+ TH+
LDD Series
Pin 18xxx-E17-BA 18xxx-D17-BA 18xxx-H17-BA 18xxx-B17-BA 18xxx-E17-NA 18xxx-D17-NA 18xxx-H17-NA 18xxx-B17-NA
1
SENSOR 0V - DATA- N/CSENSOR 0V - DATA- N/C
2
SENSOR Up - DATA+ N/CSENSOR Up - DATA+ N/C
3
DATA+ - REFCOS DATA+ DATA+ - REFCOS DATA+
4
DATA- - COS+ DATA- DATA- - COS+ DATA-
5
0V - GND 0V 0V - GND 0V
6
CLK- - REFSIN CLK- CLK- - REFSIN CLK-
7
CLK+ - SIN+ CLK+ CLK+ - SIN+ CLK+
8
UP- U UPUP- UsUP
C
D
4
3
2
1
A
B
7
8
1
2
3
4
5
6

LDD 1800 Series User Manual 18
105678-C
7. 3 Cabling
7.3.1 Field Cables
Attention: The LDD 1800 series should be operated using the field cables supplied by Genesis (M23 power cable / M12 encoder
cable).
Ensure complete installation prior to operation. Both the power and encoder cables must be fully mated to ensure IP67 sealing.
The motor end of each cable comes with the appropriate connectors to mate with the connector block. The drive end of each
cable is flying leads and should be terminated upon installation with the appropriate connector block to mate with the drive.
7.3. 2 Power Cables
Figure 8 — Power cables
Cable Part Numbers
Straight Connector
3m
102750
5m
102751
10m
102752
90°Connector
3m
102753
5m
102754
10m
102755
Cable Specifications
Connector M23 8-Pole, Power and Control
Cable Type Shielded Servo Cable, PVC Jacket
Conductors Power – 16 AWG (1.5mm)
Control – 18AWG (0.75mm)
Colour Orange
Cable Diameter 13.5mm
Minimum Bend Radius
67.5mm
Current Rating
21 A
SHIELD-TO-GROUND
CONNECTOR
HOUSING PINS
CABLE ELECTRICAL DIAGRAM
D
C
B
A
3
2
C
3
D
2
CONNECTOR PIN ASSIGNMENT
A
B
STRAIGHT CONNECTOR
A
A

LDD 1800 Series User Manual 19
105678-C
7.3.3 Encoder Cables
Encoder Cable Part Numbers
Straight Connector
3m
102744
5m
102745
10m
102746
90°Connector
3 m
102747
5m
102748
10m
102749
Cable Specifications
Connector M12 8-Pole A-Coded
Cable Type Shielded Cat5e, PVC Jacket
Conductors 24AWG (0.25mm)
Colour Teal
Cable Diameter 7mm
Minimum Bend Radius
58.5mm
Current Rating
2 A
Figure 9 — Encoder cables
7.3.4 90°Connector Alignment
Figure 10 indicates correct 90° connector cable alignment
relative to the LDD 1800 Series actuator.
Ensure that the cable connector is properly clocked relative
to the connector block prior to mating the connectors.
Improper alignment could damage the pins in the connector.
Figure 10 — Connector Alignment
SHIELD-TO-GROUND
CONNECTOR
CABLE ELECTRICAL DIAGRAM
2
1
BROWN
BLUE
GREEN
ORANGE
21
SECTION A
STRAIGHT CONNECTOR
A
A

LDD 1800 Series User Manual 20
105678-C
8. Handling and Transportation
This section details the approved handling, transport, and storage requirements.
8.1 State on Delivery
An LDD 1800 series motor is delivered from the factory fully tested and packaged. For a list of electrical and mechanical tests
performed at the factory before shipping, contact Genesis Motion Solutions.
When you receive the shipment, inspect the packaging for damage, and compare the order form with the physical goods
received. If the packaging is damaged or the actuator itself appears damaged, follow these guidelines
• Retain the original packaging if possible
• Record the device model and serial number listed on the name plate, see section "13.1 Service and Support" for additional
information
• Notify the carrier and contact Genesis Motion Solutions customer service immediately (see section "13. Service and
Support")
8.2 Handling and Transportation
To avoid equipment damage, injuries, and invalidation of the warranty due to improper handling, transport the motor securely and
in its original packaging which is designed to protect against vibration and shock. In the event of a drop or excessive vibration
when not secured in its packaging, the motor may be damaged.
Caution: When handling the equipment, always wear adequate personal protective equipment and follow safe lifting practices.
8.3 Storage
Upon delivery, store the motor in its original packaging in a dry location that is free of vibration, dust, and corrosive materials.
Storage Temperature 0°C to 40°C
Storage Humidity 20% to 80% RH (no condensation)
Caution: Incorrect storage of the motor can result in damage to the equipment and invalidate the warranty.
Table of contents
Popular Robotics manuals by other brands
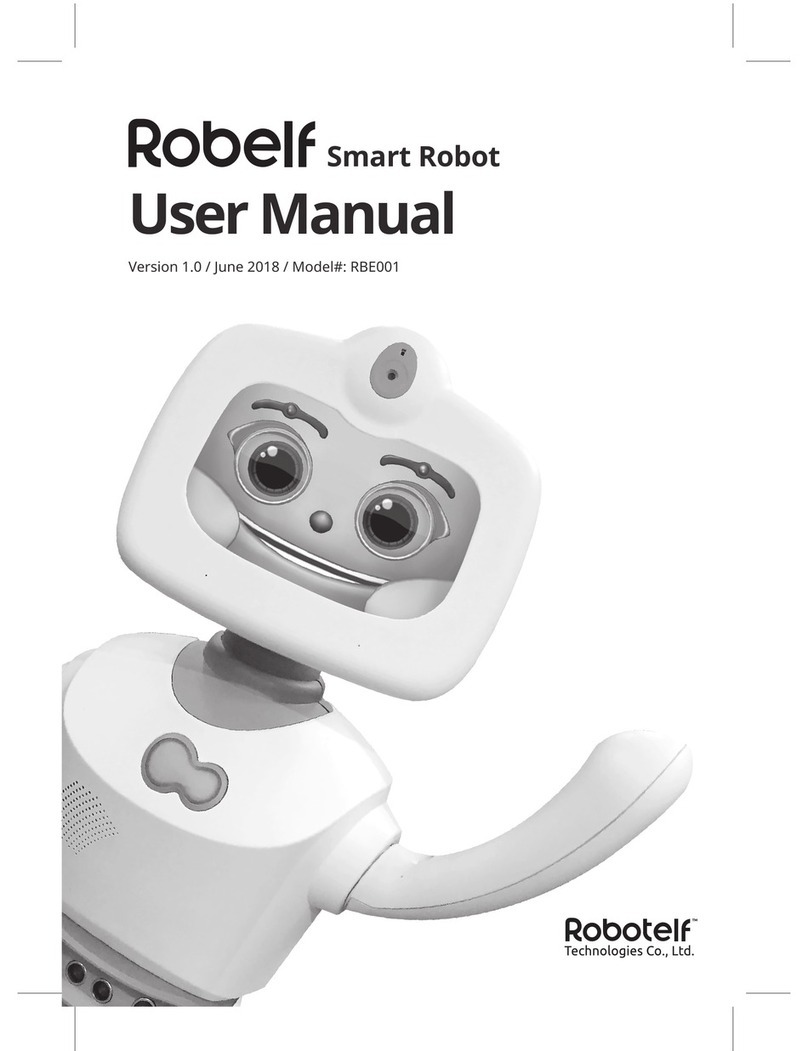
Robotelf Technologies Co., Ltd.
Robotelf Technologies Co., Ltd. Robelf RBE001 user manual
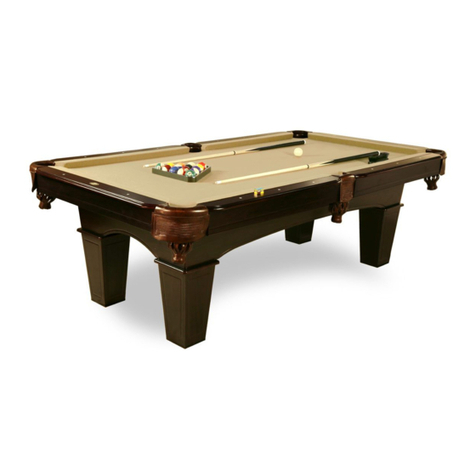
Sportcraft
Sportcraft WRIGHTWOOD 96IN BILLIARD TABLE WITH TABLE TENNIS... Assembly instructions
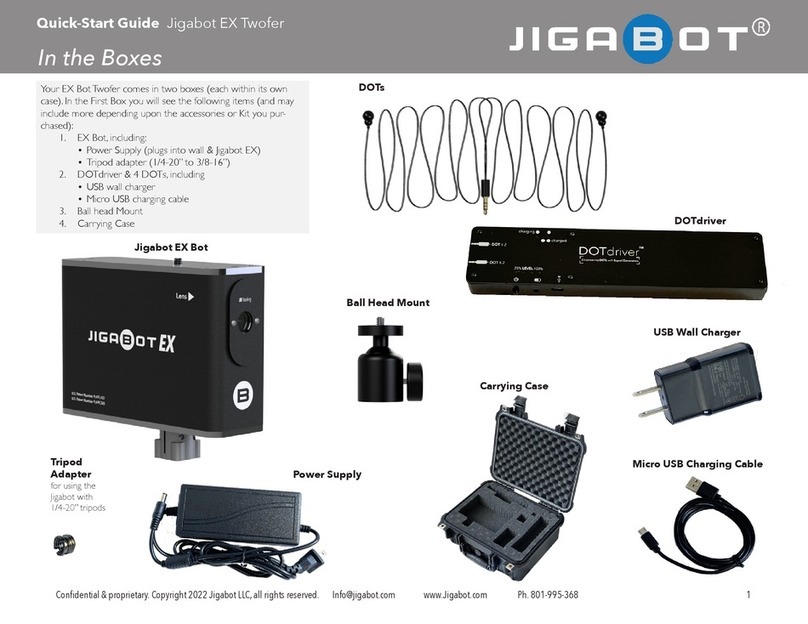
Jigabot
Jigabot EX Twofer quick start guide
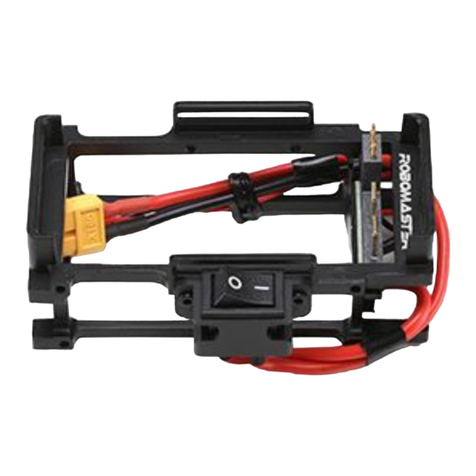
dji
dji ROBOMASTER user guide
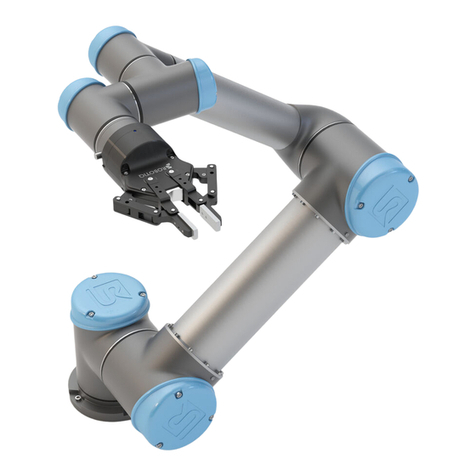
ROBOTIQ
ROBOTIQ UR3 quick start guide
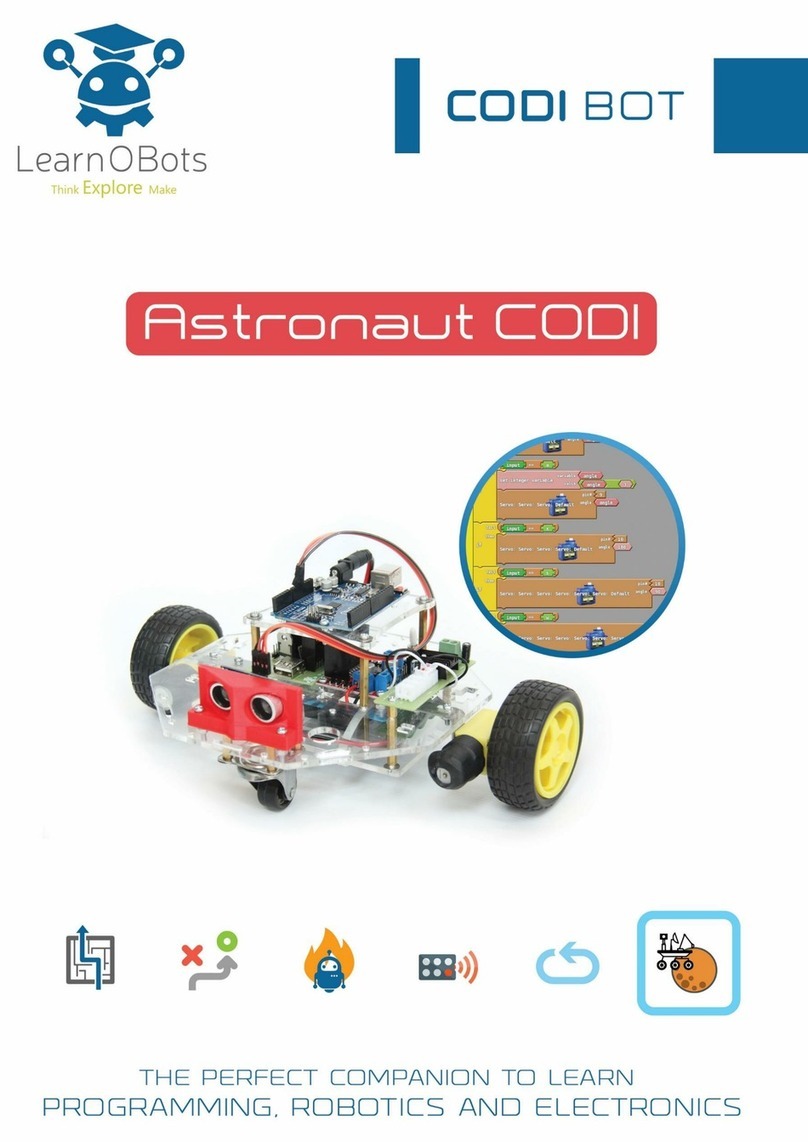
LearnOBots
LearnOBots CODIBOT manual