GESTRA SPECTORcontrol II User manual

1
EN
English
Control, Display & Operating Panel
SPECTORcontrol II
Original Installation Instructions
819410-01

2
Contents
Page
Important notes
About this user manual ...........................................................................................................................4
Additional documents..............................................................................................................................4
Usage for the intended purpose...............................................................................................................4
Terms and definitions..............................................................................................................................4
Function..................................................................................................................................................7
Safety note..............................................................................................................................................8
Directives and Standards
LV (Low Voltage) Directive and EMC (Electromagnetic Compatibility)........................................................9
ATEX (Atmosphère Explosible) .................................................................................................................9
UL/cUL (CSA) Approval ...........................................................................................................................9
Note on the Declaration of Conformity / Manufacturer's Declaration ...................................................9
In control cabinet: Installing SPECTORcontrol
Dimensions Spectorcontrol....................................................................................................................10
Installation in control cabinet.................................................................................................................11
In control cabinet: Connecting SPECTORcontrol
Wiring diagram for Spectorcontrol .........................................................................................................12
Key .......................................................................................................................................................12
Connecting the power supply ................................................................................................................13
Connecting the power supply for Spectorcontrol....................................................................................13
WAGO-I/O system 750 power supply....................................................................................................14
Connecting the COM1 interface for burner control Modbus ...................................................................14
CAN interface .......................................................................................................................................15
Connecting the Ethernet ......................................................................................................................16
Connecting the Profibus (optional).........................................................................................................16
Factory setting
Spectorcontrol.......................................................................................................................................17
Commissioning procedure
Applying supply voltage.........................................................................................................................17

3
Contents
Page
- continued -
Commissioning procedure
Startup pages .......................................................................................................................................18
Operating SPECTORcontrol
Buttons and their description.................................................................................................................19
Menu structure .....................................................................................................................................20
System Malfunctions
Indication, diagnosis and remedy ..........................................................................................................24
Further Notes
Action against high frequency interference............................................................................................25
Decommissioning / replacing the SPECTORcontrol ................................................................................25
Disposal................................................................................................................................................25

4
Important notes
About this user manual
This user manual is a short operating manual containing important information on the installation, func-
tion, electrical connection and commissioning of the equipment.
Additional documents
The Equipment Description EP-370 (SPECTORcontrol) is part of this user manual. This Description -
among other documents - is stored in the equipment. In addition you can find all pertinent documents
on the supplied documentation CD "SPECTORcontrol“.
Terms and definitions
3-element controller
Large, momentary spikes in steam consumption cause the water in the steam boiler to boil up and ef-
fervesce, resulting in abnormally high readings of the level electrode.
To correct this error not only the liquid level but also the amount of steam and feedwater are measured
and their difference is used to determine an appropriate weighing factor. This factor evaluates the influ-
ence of the difference (steam flowrate - feedwater flowrate) on the level reading.
Creep flow
Very low flowrates due to creep flow do not affect flowrate measurements. Creep flow is caused by
thermal convection and occurs even if the valve is completely closed (and the output flow should be
zero).
Switch-off threshold
If the manipulated variable (i. e. the output signal) of the pump control falls below the switch-off
threshold the associated pump is switched off. This prevents the pump from constantly being turned on
and off.
Usage for the intended purpose
SPECTORcontrol is used for controlling, viewing and parameterizing GESTRA CANopen equipment.
However, it is not only designed for GESTRA CANopen equipment but can also be used for third-party
devices approved by GESTRA and connected to the plant system.

5
Important notes
Terms and definitions - continued -
Continuous boiler blowdown
As the boiler water evaporates, the concentration of non-volatile dissolved solids (TDS) left behind in
the boiler increases over time as a function of steam consumption. If the TDS (= total dissolved solids)
concentration exceeds the limit defined by the boiler manufacturer, foaming and priming occurs as the
density of the boiler water increases, resulting in a carry-over of solids with vapour into steam lines and
superheaters.
As a consequence, the operational safety is impaired and severe damage to boiler and tubes may
occur. To keep the TDS concentration within admissible limits, a certain portion of boiler water must be
removed continuously or periodically (by means of a blowdown valve) and fresh make-up water must
be added to the boiler feed to compensate for the water lost through blowdown.
Electrical conductivity - here as a result of the TDS content of boiler water - is measured in
microSiemens/cm (μS/cm). However, in some countries ppm (parts per million) is used for conductivity
readings. Conversion: 1µS/cm = 0.5 ppm.
Intermittent boiler blowdown
During the evaporation process fine sludge deposits settle on heating surfaces and in the lowest part
of the steam boiler. Boiler sludge is caused e. g. by oxygen-scavenging agents. Sludge deposits can
form an insulating layer that retards the flow of heat and cause the boiler walls to become dangerously
overheated.
To perform a bottom blowdown the intermittent blowdown valve must be opened abruptly.
The resulting suction effect occurs only at the moment when the valve is being opened, the opening
time should therefore not exceed 3 seconds. Longer blowdown periods will merely waste boiler water.
The timed pulse/interval control of the intermittent blowdown valve optimises sludge removal while
minimising loss of boiler water. The interval between the intermittent blowdown pulses and the duration
of the boiler blowdown can be set accordingly.
Large boilers often require more frequent boiler blowdowns. In this mode the frequency and the interval
between the pulses can be adjusted.
Operating position of the continuous blowdown valve
To keep the TDS concentration within certain limits a small quantity of boiler water is discharged con-
tinuously via the top blowdown valve. To ensure continuous blow-off the valve is always slightly open
(= operating position).
This operating position can be adjusted accordingly. For the corresponding amount of boiler blowdown
refer to the capacity charts of the continuous blowdown valve.
Compensation for steam bubbles (conductivity control)
The presence of steam bubbles can lead to greatly fluctuating conductivity readings. An attenuator will
damp the oscillations in the measurements.
Switching hysteresis (conductivity control)
If the controller is configured as 2-position controller, the valve will OPEN if there is a positive deviation
(X > w). The conductivity must then decrease until a new value that is lower than the setpoint minus the
adjusted hysteresis is reached. Once this value is reached the valve will be motored into the operating
position.
- continued -

6
Important notes
Terms and definitions
Stand-by mode (conductivity control)
To avoid loss of water, the continuous blowdown control and the programme-controlled intermittent
boiler blowdown (if activated) can be de-activated during stand-by operation or when the burner is
switched off. An external control command will be triggered and, as a result, the continuous blow-
down valve will be closed. During stand-by operation the MIN/MAX limits and the monitoring function
remain active.
After the equipment switches back to normal operation the continuous blowdown valve is motored
into the OPERATING potion or the control position. In addition an intermittent blowdown pulse is trig-
gered off (provided that automatic intermittent boiler blowdown has been activated and an interval
period and pulse duration has been set).
Temperature compensation (conductivity control)
The electrical conductivity changes as the temperature falls or rises. To obtain meaningful readings it
is therefore necessary that the measurements are based on the reference temperature of 25°C and
that the measured conductivity values are corrected by the temperature coefficient factor.
For automatic temperature compensation the following three settings are available: TK Linear, TK
Norm or TK Auto.
TK (Linear)
To ensure that the readings are based on 2 5°C set the TK value between 0 and 3.0 %/°C (default
setting 2.1 %/°C. This setting permits the linear temperature compensation of the measured value
over the whole measuring range. This method is usually applied for steam boilers operating at
constant service pressure. After the TK is set and the service pressure is reached use a calibrated
conductivity meter to measure the conductivity of the boiler water and compare the reading with
the indicated conductivity value. If the reading differs from the indicated conductivity change the TK
setting until they tally.
TK (Norm)
Since conductivity is not a linear function of temperature over a larger temperature range, various
conditioning agents and different basic conductivities were used in order to ascertain empirical
conductivity/temperature curves. These curves are stored as standard curves and can be used for
temperature compensation. TK (NORM) is suitable for boilers operating with variable pressure, which
means that the boiler does not have a fixed working pressure (e. g. low load 10 bar, full load 15 bar).
TK (Auto)
For this method a characteristic conductivity/ temperature curve of the plant is used for temperature
compensation. The installation specific readings are recorded during the heat-up phase and stored
as Auto curve. TK (AUTO) is particularly suitable for steam boilers operating with variable pressures.
Cell constant and correction factor (conductivity control)
The cell constant is a geometric quantity characteristic of the conductivity electrode and is taken into
account when calculating the conductivity. However, in the course of time this constant may chance,
e. g. due to dirt deposits accumulated on the measuring electrode. Deviations can be compensated
by changing the correction factor.
Purging of the continuous blowdown valve
To prevent the continuous blowdown valve from getting stuck the valve can be rinsed automatically.
At regular intervals the continuous blowdown valve is motored into the open position. When the
purging time is over, the valve is motored into the OPERATING position or into the required control
position.
- continued -
- continued -

7
Important notes
Function
SPECTORcontrol (SC) is a control, display and operating panel with integrated programmable logic con-
troller (PLC) for CANopen equipment.
Apart from GESTRA equipment such as level electrodes for conductivity and capacitance readings,
temperature limiters and conductivity electrodes, you can also connect equipment produced by other
manufacturers such as Jumo CANTransP/T and incorporate it into the system.
Data are exchanged between CANopen equipment and SPECTORcontrol via CAN bus to ISO 11898,
using the CANopen protocol.
SPECTORcontrol determines cyclically the current parameter settings and values of CANopen devices.
These readings are shown on the display as soon as a node ID has been allocated to the respective
equipment. It is then possible to adjust and allocate connected equipment directly via SPECTORcontrol.
The individual inputs can be flexibly allocated to the various CAN nodes. However, the allocation of the
IO terminal is dictated by the selected arrangement and cannot be changed. After a restart the equip-
ment is in the initializing phase for approx. 10 seconds. Then it shows up-to-the-minute readings of
the associated CAN bus devices.
The system can process digital signals and analog values and allows you to establish alarm and
switching limits for them. These signals can be assigned directly to the control units or processed
further by using the functions Logic and Calculations. After that the signals are outputted via a digital
or analog output (IPO model). These signals can be used to accomplish various switching tasks.
Clear unambiguous signal designations allow quick allocations within the system. Any cryptic desig-
nations can be replaced by the name of the equipment or the place of installation. Example: Instead
of "LRG 16-41" "Boiler feedwater conductivity". Note that at most 30 characters can be entered.
This designation is then used universally as key identifier. This is particularly advantageous in large
installations where not only boiler data but also liquid levels in feedwater and condensate vessels are
registered.
- continued -

8
Danger
The parameter settings of the level electrodes NRG 1..-40 (LW), NRG 1..-41, NRG 1..-41.1
(HW) and the temperature transmitter TRV 5-40 can be viewed and monitored.
However, SPECTORcontrol does not replace the switching controllers for the low-water
level limiter, the high-water level limiter or the safety temperature limiter
(NRS 1-40, NRS 1-41, NRS 1-40.1 and NRS 1-40.2).
Data can only be exchanged safely with equipment tested and approved by GESTRA.
Important notes
Safety note
The equipment must only be installed and commissioned by qualified and competent staff.
Retrofitting and maintenance work must only be performed by qualified staff who - through adequate
training - have achieved a recognised level of competence.
The Equipment Description EP-370 (SPECTORcontrol) is part of this user manual. This Description -
among other documents - is stored in the equipment. In addition you can find all pertinent documents
on the supplied documentation CD "SPECTORcontrol“
Please observe the safety instructions stated in these documents!
- continued -

9
Directives and Standards
ATEX (Atmosphère Explosible)
According to the European Directive 2014/34/EU the equipment must not be used in explosion risk
areas.
LV (Low Voltage) Directive and EMC (Electromagnetic Compatibility)
The equipment meets the requirements of the Low Voltage Directive 2014/35/EC and the
EMC Directive 2014/30/EC.
Note on the Declaration of Conformity / Manufacturer's Declaration
For details on the conformity of our equipment according to the European Directives see our Declaration
of Conformity or our Declaration of Manufacturer.
The current Declaration of Conformity / Declaration of Manufacturer are available in the Internet under
www.gestra.de Documents or can be requested from us.
The equipment complies with the requirements of the following standards: UL 60950-1 and CSA C22.2
No. 60950-1-07, Information Technology Equipment - Safety - Part 1: General Requirements.
File E176557.
UL/cUL (CSA) Approval

10
In control cabinet: Installing SPECTORcontrol
Dimensions Spectorcontrol
Fig. 1
Front panel
345
260
Fig. 2
Rear panel Fixing frame

11
In control cabinet: Installing SPECTORcontrol
Dimensions Spectorcontrol
Installation in control cabinet
SPECTORcontrol is designed to be installed in the control cabinet
by means of the fixing frame and
the integrated stud bolts at the rear panel.
SPECTORcontrol
can be used with ambient temperatures
up to max. 50°C. Note that direct sun light (UV light) reduces the lifespan of the LCD display. Install the
SPECTORcontrol as follows:
nUnscrew the fixing nuts and remove the fixing frame.
nInsert the supplied seal into the front panel slot.
nPush the SPECTORcontrol equipment from the front into the front panel cut-out.
nPush the fixing frame back onto the stud bolts. To secure the equipment in place use the four fixing
nuts. Make sure the nuts are tightened evenly from the rear until the front frame is flush with the front
panel all round
.
Fig. 3
Front panel cut-out
287,0
321,0
329,0
196,0
229,8
238,0
5,5
135.0°
The thickness of the front panel
must not exceed 5 mm.
- continued -
- continued -

12
In control cabinet: Installing SPECTORcontrol
Attention
nAvoid a location where direct sunlight falls on the flat screen.
nThe mounting angle must not exceed ± 35° from the vertical.
nEnsure that the seal is fitted correctly on the front panel. For devices with a round seal
the two ends must be at the lower side of the device and should fit together without a
gap.
nAvoid tightening torques of greater than 0.5 Nm as this could otherwise damage the
device.
nThe thickness of the front panel must not exceed 5 mm.
In control cabinet: Connecting SPECTORcontrol
Wiring diagram for Spectorcontrol
1Functional earth terminal
2Power supply
3COM1
4CAN
54x USB
Key
6Network adapter 1: Maintenance / Service
7Network adapter 2: Ethernet + Ethernet Field-
bus
8SDCARD slot
9Battery
0PC/104 slot (optional Profibus)
Fig. 5
24 VDC
reserved
2
0 VDC
Fig. 4
5
7
1
4
6
3
2
0
89
- continued -

13
Connecting the power supply for Spectorcontrol
SPECTORcontrol
belongs to protection class 3. The system power supply must be provided with 24VDC
SELV (safety extra-low voltage). The max. disconnection capacity of the fuse must be taken into consider-
ation. The power supply is NOT isolated. The 0 V connection is directly connected to the housing potential.
The voltage supply is protected with a melting fuse. A reverse polarity protective device is used to protect
the equipment in the event of reversed poles. Operation, however, is only possible if the connection was
made correctly.
The connection must be made as follows:
nThe cross section of the power supply cable must be at least 0.75 mm² and a maximum of 2.5 mm².
nA flexible lead or wire can be used for the connection.
nThe current consumption must be taken into account when implementing the power supply.
nThe functional earth can help to avoid disturbance caused by potential differences.
The cross section must not be less than 2.5mm2.
nThe GND connection is directly connected to the housing potential.
For safety reasons the wires should be fixed together near by the connector.
The plug connector (socket connector with screw terminals) for the power supply connection is supplied
with the equipment. (WAGO 1757022).
In control cabinet: Connecting SPECTORcontrol
Connecting the power supply
SPECTORcontrol, all CANopen devices and the WAGO IO terminal block are supplied with 24 V DC /
≥ 5 A. 5 A is the sum current of all CAN bus nodes. Please use a safety power supply unit with safe
electrical isolation.
The power supply unit must be electrically isolated from dangerous contact voltages and must meet at
least the requirements on double or reinforced isolation according to one of the following standards:
DIN EN 50178, DIN EN 61010-1, DIN EN 60730-1 or DIN EN 60950.
Attention
nDo NOT use the power supply of GESTRA control devices for the power supply of
SPECTORcontrol and connected equipment.
Attention
nIn the event of reverse connection and simultaneous connection
of a further 0 connection, e. g. GND connection of the COM1
interface, the fault current flows via this 0 V connection. If the
housing is not lying well set on the 0 V potential, the result can
be destruction of the equipment or of external components!
nFor safety reasons the wires should be fixed together near by the
connector.
- continued -

14
In control cabinet: Connecting SPECTORcontrol
WAGO-I/O system 750 power supply
If the sum of the internal power consumption exceeds the sum current for bus modules, then an internal
system supply module (750-613) must be placed before the module where the permissible residual
current was exceeded.
Example:
In a node with a CANbus coupler 750-337 10 relay modules (750-513) will be used. Current consump-
tion: 18 x 100 mA = 1800 mA. The coupler can provide 1650 mA for the bus modules. Consequently,
an internal system supply module (750-613, max. 2 A output current) must be added from the sixteenth
module 750-513 of the node. In this case an error message will inform you about this when you are
setting the parameters for the module.
For more information go to the download centre of www.wago.com and then download the PDF file
"Design Notes WAGO I/O System 750" and other relevant technical documents and tools.
Connecting the COM1 interface for burner control Modbus 3
PIN no. Signal
1
2 RXD
3 TXD
4
5 GND
6
7
8
9
Connector 9poles
SubD
Connector
The serial interface COM1 is PC-compatible.
Attention
nFor the connection use screened multi-core data cable.
nData cable(s) connected to other equipment must be laid separately from high-voltage
cables.
nConnect the screen only once to the central earthing point (CEP) in the control cabinet.
1
6
2
73
84
95
1 2 3 4 5 .
6 7 8 9 .
- continued -

15
PIN no. Signal Description
1 - -
2 CAN LOW Negative data signal
3 GND Signal Ground
4 -
5 -
6 GND Signal Ground
7 CAN HIGH Positive data signal
8 -
9 -
Housing Case Cable screen
CAN interface 4
In control cabinet: Connecting SPECTORcontrol
The connection to the CANopen equipment is implemented via the CAN interface.
A D-Subminiature plug connector in accordance with DIN 41652 must be used for the connection.
Use a multi-core flexible control cable as supply line.
Note that screened multi-cored twisted-pair control cable is required as Bus line, e. g. UNITRONIC®BUS
CAN 2 x 2 x...mm2or RE-2YCYV-fl 2 x 2 x...mm2.
Cable length Number of pairs and conductor size [mm2]
125 m 2 x 2 x 0.34
250 m 2 x 2 x 0.5
335 m 2 x 2 x 0.75
Other lengths available on request.
Note
The design and preparation of the data cable is an important factor for the electromag-
netic compatibility (EMC) of SPECTORcontrol. Wiring should therefore be carried out with
special care.
nWire equipment in series. Star-type wiring is not permitted!
nData cable(s) must be laid separately from high-voltage cables.
nLink screen of the data cable such that electrical continuity is ensured and connect
it once to the central earthing point (CEP). If equipotential bonding currents are to be
expected, for instance in outdoor installations, make sure that the screen is separated
from the central earthing point (CEP).
nIf two or more system components are connected in a CAN bus system, provide the
first and the last device with a terminating resistor of 120 Ω (terminal CAN LOW/CAN
HIGH).
1 2 3 4 5 .
6 7 8 9 .
- continued -

16
1
62
73
84
95
Connecting the Ethernet
ACT LINK PIN no. Signal
1 TXD
2 TXD+
3 RXD+
4 -
5 -
6 RXD-
7
8
Socket, 8pole
RJ45
RJ45 connector
6 +7
In control cabinet: Connecting SPECTORcontrol
The Ethernet interface complies with the requirements of standard IEEE 802.3
(10/100/1000BASE-T).
The network connection is implemented via a screened Cat-5e cable with RJ45 connectors. The maxi-
mum cable length and transfer speed is limited by the cable quality defined in EIA/TIA 568 TSB-36.
Cable lengths up to 100 m are possible.
Two diagnosis LEDs are available:
Orange: LINK (connection to HUB or to another device)
Green: ACT (sending or receiving)
Attention
nFor the connection use screened multi-core data cable.
nData cable(s) connected to other equipment must be laid separately from high-voltage
cables.
nConnect the screen only once to the central earthing point (CEP) in the control cabinet
Connecting the Profibus (optional) 0
PIN no. Signal
1
2
3 Line B
4
5
6
7
8Line A
9
Connector 9poles
SubD
Connector
- continued -

17
Factory setting
Spectorcontrol
All adjustable masks are completely available, no matter whether the indicated instruments are part of
the bus system or not.
Subsequent expansion or modification is therefore possible at any time.
You can find the SPECTORcontrol Runtime Licence at the rear of the equipment. Should it be necessary
to re-enter this licence number and the sticker is no longer attached to the equipment please contact
GESTRA Bremen (for more information on contact details see last page of this installation & operating
manual).
The inputs/outputs of the WAGO IO module can only be defined after having entered the number of
modules in [SPECTORcontrol]/System/IO-Module.
The system adjustments for the first commissioning are stored on the CompactFlash card. When
SPECTORcontrol is operating, data of the CompactFlash card, too, will be stored in the directory /Data.
The equipment features the following default settings:
nDate / Time Current date and time (Daylight saving time DST: de-activated)
nStartup page Startup page1 (1..4 freely definable)
nLanguage English
nIP address 1 (Ether 1) 192.168.0.99
nIP address 2 (Ether 2) can be freely allocated
nPassword Level 1: aaa
Level 2: bbb
nNode ID SC 127
nNode ID Wago IO 126
nBaudrate 250 kB
nProfibus station address 10 (Slave) – other arrangements possible on request
Note
After commissioning we recommend that you use a new password.
Make sure that the same password is not used twice.
Max. length of password: 8 characters.
Commissioning procedure
Applying supply voltage
Apply mains voltage to SPECTORcontrol. The startup page 1 appears.
Attention
nPlease follow the installation and operating instructions of all connected devices.

18
Commissioning procedure
Startup pages

19
Operating SPECTORcontrol
Note
To operate the SPECTORcontrol press on the respective buttons or use swipe gestures.
Buttons and their description
Button Description
Home: Press this button to go to one of the startup pages (1..4).
To define the startup page go to: System/Backlight - Startup Page…/ . If there
is no user response within 60 minutes the system returns automatically to the
startup page.
Alarm: The symbol is flashing if an alarm has been triggered. Press this button
to view the alarm list. If the alarm has stopped but has not been reset the button
remains highlighted. To sort the list entries press the yellow title bar. To view the
signal name shown at the bottom press one of the lines.
Back: Press this button to leave or close this page.
Delete: Press this button to delete signals, lists etc. You will receive a confirma-
tion message on which you need to press “OK”.
Save: Press this button to save the lists (e. g. flowrate or alarm) stored on the CF
card in the equipment under [StorageCard]/Data..
Setup: Press this button to customize values, signals and page settings.
Displays: Press this button and leave it depressed for more than 1 sec. to view
the content of a detailed operating manual.

20
Operating SPECTORcontrol
Menu structure
START Swipe left or right to navigate between startup
pages 1 ... 4 and swipe upwards for configura-
tion.
Press to view the time, press
and hold down for 1 sec. to ac-
cess the operating instructions
Alarm 1.. 1024 First value message 1 .. 8,
For configuration go to Digital Inputs
Alarm Help
For viewing
external alarm
text
Remains stored
Alarm Info
For viewing the
triggering signal
Alarm Help
For viewing the
alarm text
Alarm History Alarm Info
For viewing the
triggering signal
Alarm
Confirmation
Alarm Filter
Alarm Setup
For acoustic and optical
alarm settings and
accessing the alarm window
Datalog 1 .. 5 3 signals
5 sec. / 10
days
- continued -
Other manuals for SPECTORcontrol II
1
Table of contents
Other GESTRA Control Panel manuals
Popular Control Panel manuals by other brands
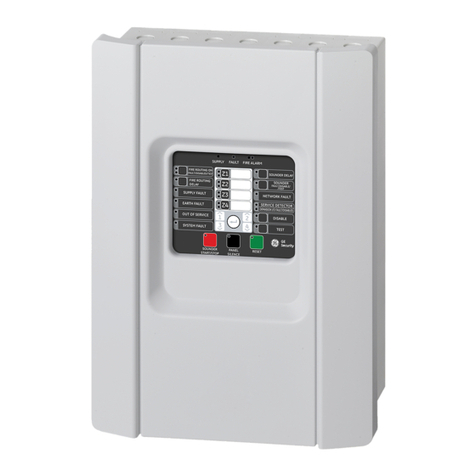
Aritech
Aritech 1X-F Series Operation manual
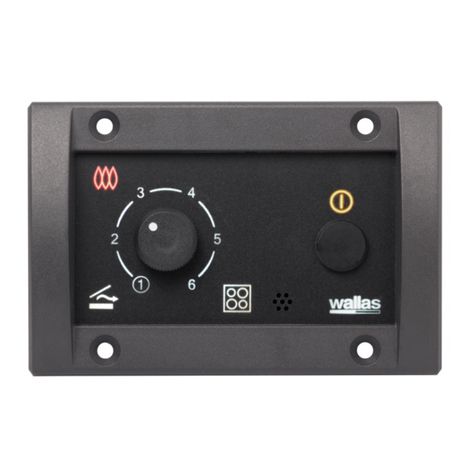
wallas
wallas 85 DT Operation guide
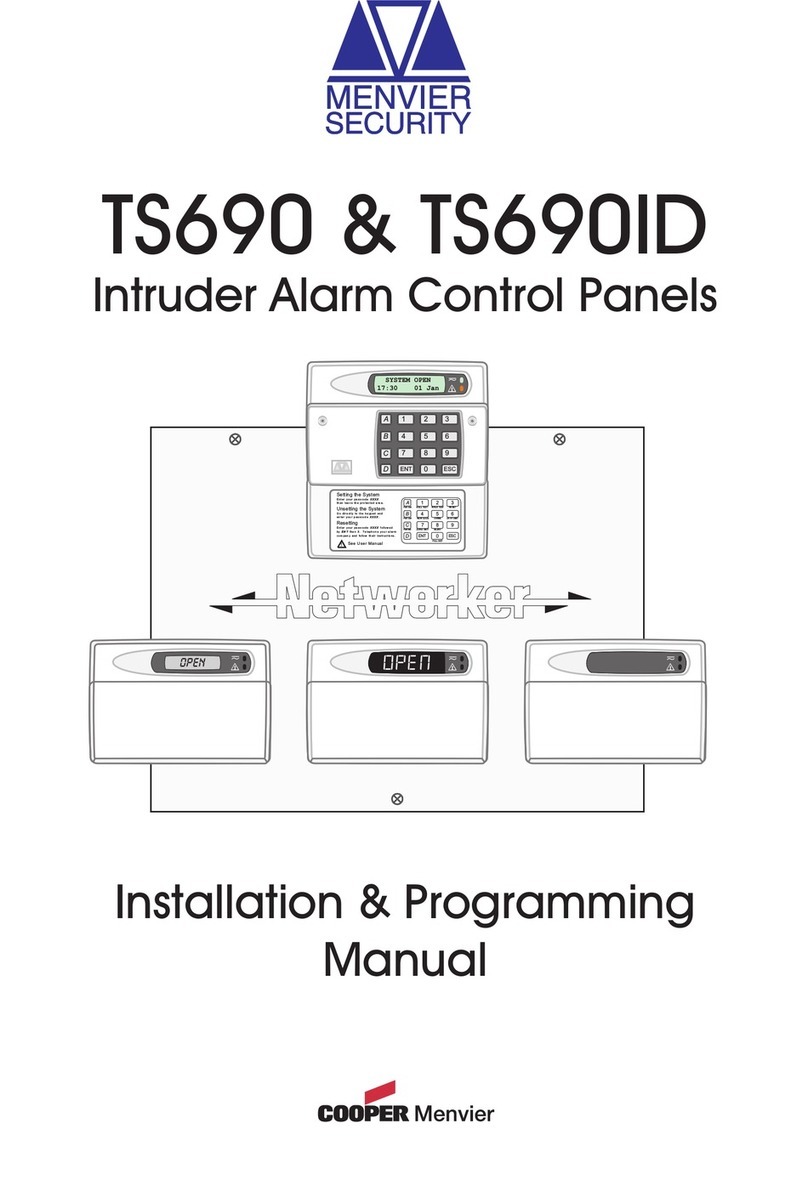
Menvier Security
Menvier Security TS690 Installation & programming manual

Riello
Riello CBD 35 Instruction booklet
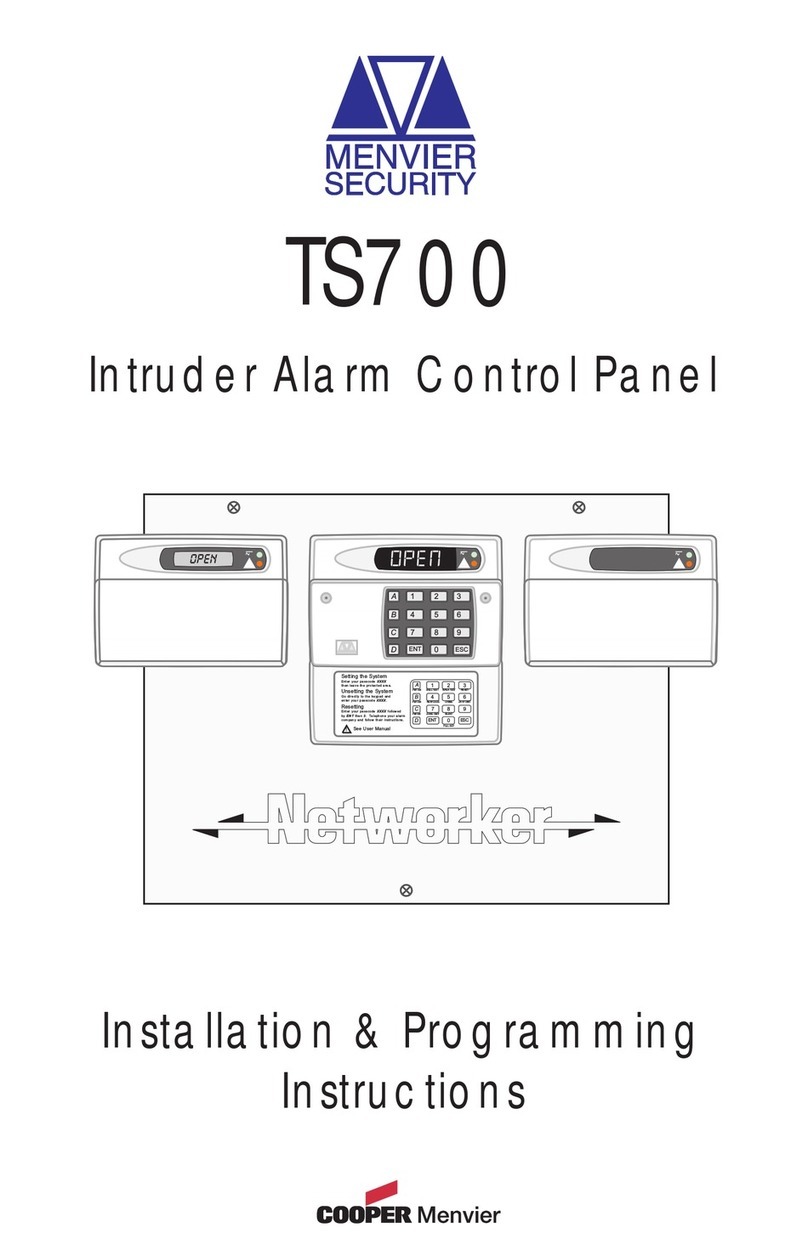
Menvier Security
Menvier Security TS700 Installation & programming instructions

urmet domus
urmet domus 1061/006A Installation and programming manual