GF 2280 User manual

GF Piping Systems
Instruction manual
2280 Swing Fork
with relay output
Georg Fischer Piping Systems Ltd CH-8201 Schaffhausen
Phone +41 (0)52 631 30 26 / info.ps@georgfischer.com /
www.gfps.com
GFDO 6382_4 (08.14)
© Georg Fischer Rohrleitungssysteme AG
CH-8201 Schaffhausen / Switzerland,
2014 Printed in Switzerland
Observe instruction manual
The instruction manual is part of the product and an important element within the safety
concept.
Read and observe the instruction manual.
Always have the instruction manual available at the product.
Pass on the instruction manual to all subsequent users of the product.
1Intended use
The tuning fork switch is used for level measuring and for detecting the limit level of liquids.
2About this document
This document contains all necessary information for the installation, operation and
maintenance of the product.
3Safety and responsibility
Only use the product as intended, see intended use.
Do not use the product if it is damaged or faulty. Throw out the product immediately
if it is damaged.
Make sure that the piping system has been installed professionally and that it is
inspected regularly.
The product must only be installed by persons who have the required training,
knowledge and experience.
Regularly train personnel on all questions pertaining to the locally accepted
regulations on occupational safety and environmental protection, especially on
pressure-retaining pipelines.
The personnel is responsible for the following measures:
Know, understand and follow the instruction manual and the advices therein.
4Scope of delivery
2280 Tuning fork switch with relay output
Instruction manual
1 x gasket, 2 mm thick, made of KLINGER OILIT (for G1"process connection only)
2 x 3-pole connector plugs (3 x 3-pole connector plugs when 2 output relays)
2 x M20 x 1.5 cable entry
5Transport and storage
Protect the product against external force during transport (impact, stroke,
vibrations, etc.).
Transport and/or store the product in unopened, undamaged original packaging.
Protect the product from dust, dirt and moisture, as well as heat and ultraviolet
radiation.
Make sure that the product has not been damaged by either mechanical or thermal
influences.
Check the product for transport damage before assembly.
6Function
The tuning fork switch is used for level measuring and for detecting
the limit level of liquids. Example: overfill prevention, no-load
protection, pump control.
The product can be installed in several ways.
When mounting laterally the position of the fork needs to be
taken into account!
Can be used for the following liquids:
Low viscosity: Mounting in any position (horizontal, vertical,
diagonal).
High viscosity: Vertical mounting exclusively (from the top), as
otherwise the tuning fork frees up only with difficulty.
7Technical specifications
Data
Values
Model
2280-S-xxxT-X
Wetted parts
stainless steel 1,4571 (X6 CrNiMoTi 17122)
Data
Values
Housing material
Plastic: PBT fiberglass-reinforced, hardly
inflammable (DuPont®)
Medium temperature
-40 to +130 °C
Ambient temperature
-30 to +70 °C
Max. operating pressure
40 bar
Installation length
short version 69 mm
standard version 125 mm
Medium density
≥0.7 kg/dm3
Medium viscosity
≤10.000 mm2/s (cSt)
Delay time
upon covering
≤0.5 s
upon freeing up
≤1 s (see Delay time –Viscosity)
Switching status display
two-color LED
Setting min./max. safety
with switch selectable
Output
SPDT relay, 250 VAC, 8 A, AC 1
Electr. connection/wire cross-section
2 x M20 x 1.5, wire Ø6 –12 mm / 0.75 –2.5 mm2
Supply voltage
20 –255 VAC and 20 –60 VDC
Power input
1.2 –17 VAAC; <3 WDC
Protection against accidental contact
Class I
Protection rating
IP67 (NEMA 6)
Weight
0.95 kg + 1.2 kg/m
Storage conditions
Ambient temperature
-25 to +60 °C
Relative humidity
max. 98 %
8Dimensions
Short version
Standard version
1
2 x M20 x 1.5 (gland)
L1
89 mm
L4
125 mm
2
2 x NPT ½" (gland)
L2
111 mm
d1
BSP 1" / NPT 1"
3
Hexagonal collar SW41
L3
69 mm
d2
Ø28 mm
9Graphs
Temperature –Pressure
Delay time –Viscosity
Delay time upon freeing up depending on the viscosity of the medium:
1
Fully immersed
2
Semi-immersed
3
Only tip immersed
Switching point, switching hysteresis
The switching point and the witching hysteresis are subject to the density of the medium
and the mounting position.
D1
~14 mm
D3
~13 mm
D2
~3 mm
D4
~4 mm

Georg Fischer Piping Systems Ltd CH-8201 Schaffhausen
Phone +41 (0)52 631 30 26 / info.ps@georgfischer.com /
www.gfps.com
GFDO 6382_4 (08.14)
© Georg Fischer Rohrleitungssysteme AG
CH-8201 Schaffhausen / Switzerland,
2014 Printed in Switzerland
10 Installation
Checking the installation conditions
Are the working pressure and temperature values being observed?
Checking the mounting position
The tuning fork switch can be mounted at almost any angle in the tank. The requirements
are as follows:
The liquid can flow out of the sensor gap.
Turbulence from around inlet/outlet valves or agitators must be avoided.
The distance between the sensor gap and tank
walls (other fittings in the tank) must be at least
x = 5 mm to ensure that no pockets of air or liquid
can form.
The threaded guide should stop as flush with the
wall of the tank as possible to ensure that no
pockets of air or liquid can form.
When mounting on pipes, the sensor gap must
always be aligned in parallel with the direction of
flow.
Mounting the tuning fork switch mechanically
Make sure that the thread in the tank is free of contamination.
If the tuning fork needs to be positioned, use PTFE tape or
an equivalent pipe sealing tape.
Otherwise install the gasket, supplied.
When mounting, protect the tuning fork switch against mechanical damage.
Carefully push the tuning fork switch into the opening and tighten on the hexagonal
collar (SW41) so that the gap is accurate. Use the marking (1) on the hexagonal collar
as a guide.
Check whether the connection is tight.
Carefully turn the housing by hand (max. 300°) so that the glands are pointing in the
direction desired.
Connecting the tuning fork switch electrically
2
Mode
5
LED status
8
M20 x 1.5 (glands)
3
Distribution
6
Output
9
Grounding screw
4
Connection to ground
7
½" NPT (glands)
Ensure that the voltage values for the tuning fork switch correspond to those for the
system.
Makesure that the connectioncable is de-energized.
Carefully screw the housing cover and the glands (7, 8) off and set them aside on a
clean surface.
Do not connect AC and DC voltages to a common cable.
Do not connect low potential and supply voltages to a common cable.
Thread the supply cable with outside diameter 8 –15 mm in.
Fasten the separate wires in the appropriate terminal sockets with screws.
For the connection to ground use the grounding screw (9) on the housing or the
internal ground connection (4).
Position the glands in place and carefully tighten so that protection rating IP67 is
assured.
Setting the mode
Voltage
Tuning fork
Switch
Mode
Output
Safety
LED
status
On
High
Alarm
Red
Released
Low
Alarm
Green
Operated
High
Alarm
Green
Operated
Low
Alarm
Red
Released
Interrupti
on
Free or covered
High or Low
Off
Released
Position the housing cover in place and carefully tighten so that protection rating IP67 is
assured.
Route the cables to the connection point and secure them at regular intervals using
cable ties or similar.
The tuning fork switch is operational once the supply voltage has been switched on.
The switching process can be tested as follows:
-Immerse the sensor in a beaker of water.
-The switching output is switched.
11 Ordering information
Item No.
Type
Length
Description
159 300 240
2280-S-5WBT-1
69 mm
Stainless steel
1 SPDT relay,
PBT housing, 1"
159 300 241
2280-S-5WBT-2
125 mm
159 300 242
2280-S-5WNT-1
69 mm
159 300 243
2280-S-5WNT-2
125 mm
12 Dismantling
Make sure that the connection cable is de-energized and can be freely rotated.
Make sure that the tank is depressurized and has been drained to a level that is at
least below that of the sensor mounting position.
VORSICHT
Leakage of media harmful to health and the environment possible!
Risk of personal injury and damage to the environment caused by these media.
Wear the protective clothing required.
Collect leaking media and dispose of them pursuant to local regulations. Consult
the safety data sheet.
13 Disposal
Before disposing of the different materials, separate them into recyclables, normal
waste and special waste.
Comply with local legal regulations and provisions when recycling or disposing of the
product, the individual components and the packaging.
Comply with national regulations, standards and guidelines.
VORSICHT
Parts of the product may be contaminated with media that are harmful to health and the
environment meaning that simple cleaning is not sufficient!
Risk of personal injury and damage to the environment caused by these media.
Prior to disposing of the product:
Collect leaking media and dispose of them pursuant to local regulations. Consult
the safety data sheet.
Neutralize any media residue that is present in the product.
Separate materials (plastics, metals, etc.) and dispose of them pursuant to local
regulations.
A product marked with this symbol must be sent for separate
collection of electrical and electronic devices.
If you have questions regarding the disposal of the product, please
contact your national GF Piping Systems representative.
14 Disclaimer
The technical data are not binding. They neither constitute expressly warranted
characteristics nor guaranteed properties nor a guaranteed durability. They are subject to
modification. Our General Terms of Sale apply.
CAUTION
CAUTION
Other GF Switch manuals
Popular Switch manuals by other brands
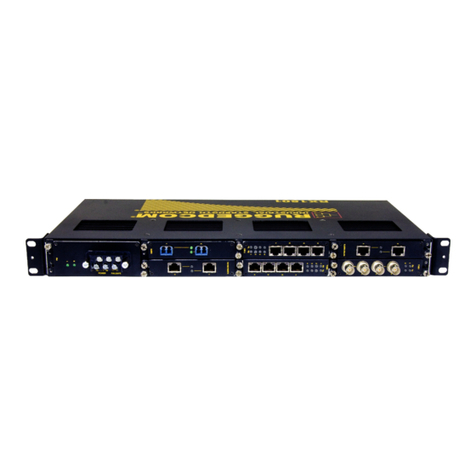
RuggedCom
RuggedCom RUGGEDBACKBONE RX1501 Hardware installation guide
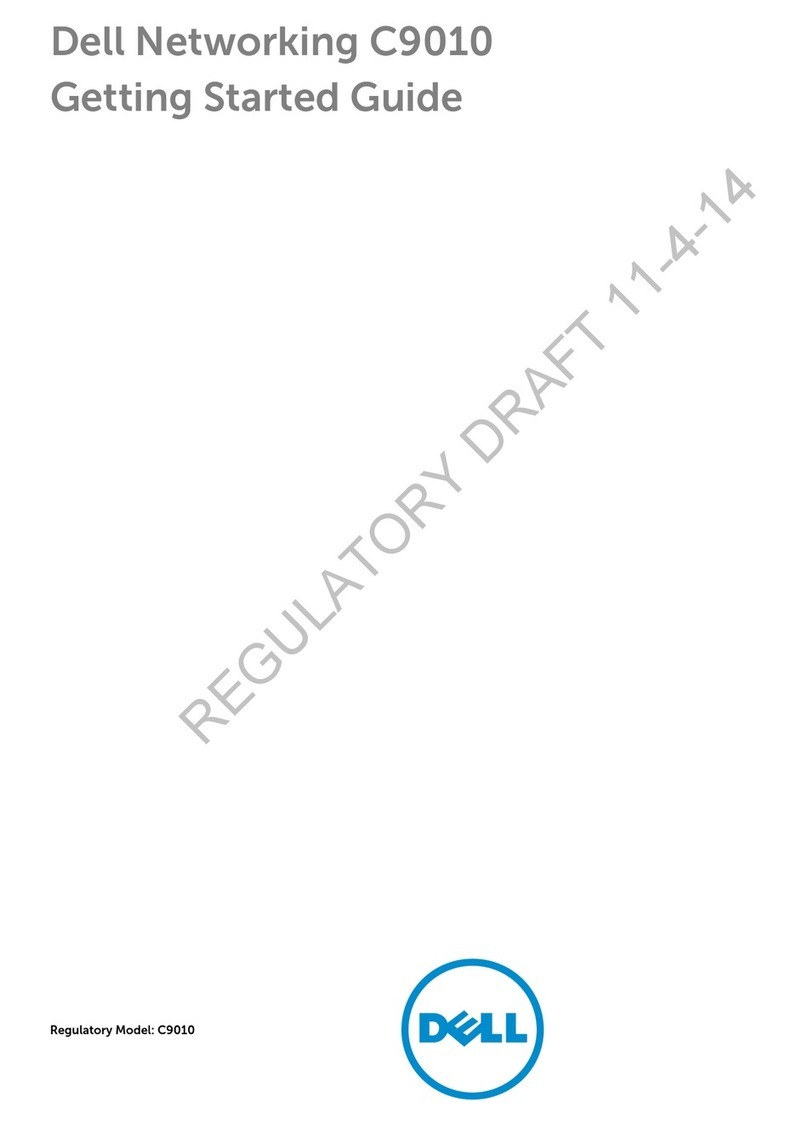
Dell
Dell Networking C9010 Getting started guide
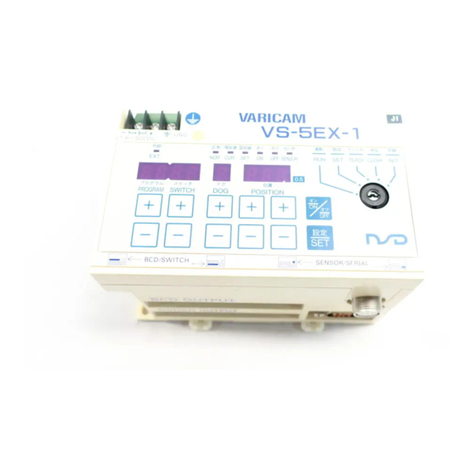
NSD
NSD Varicam VS-5E Series Specifications & Instruction Manual
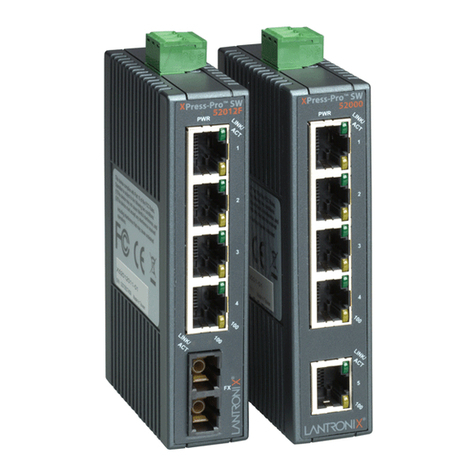
Lantronix
Lantronix Xpress-Pro SW 52000 user guide
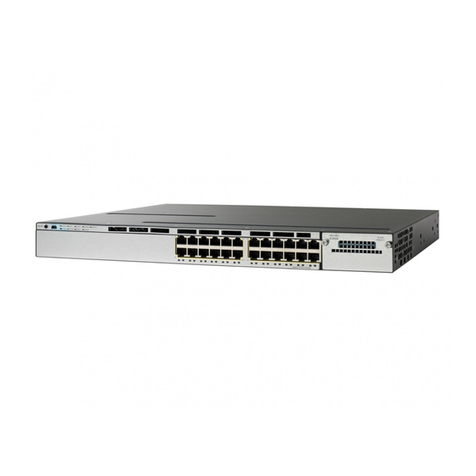
Cisco
Cisco Catalyst 3850 series Configuration guide
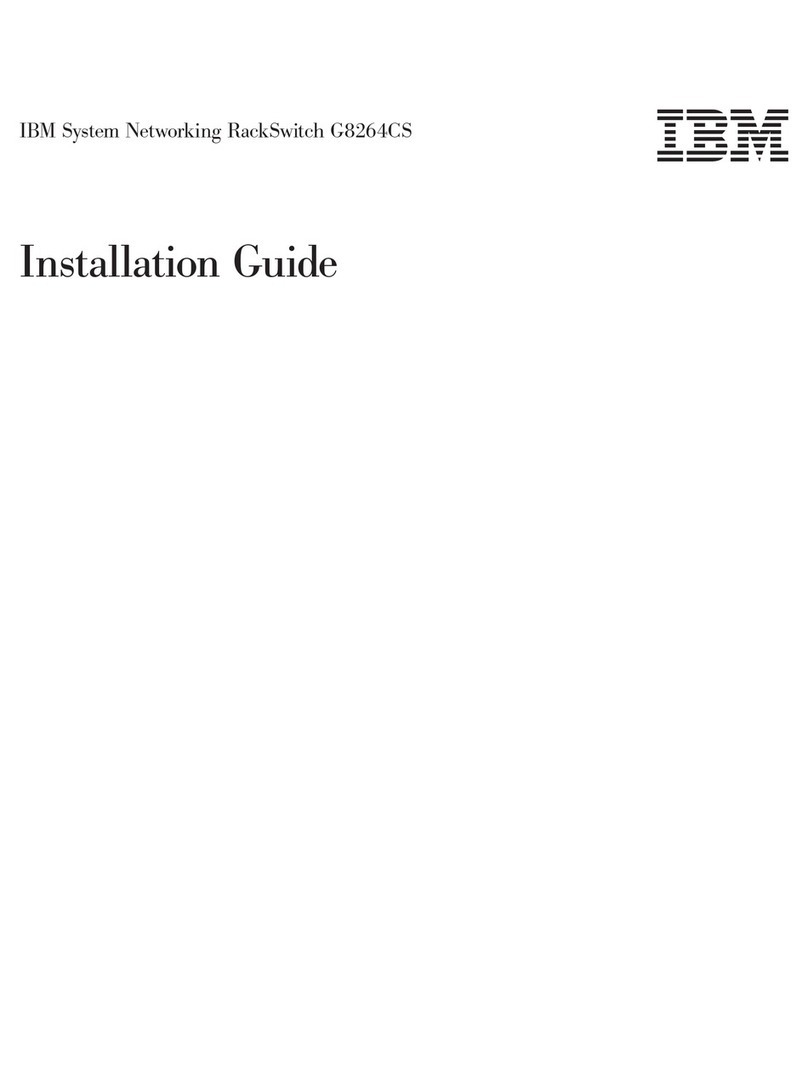
IBM
IBM RackSwitch G8264CS installation guide