Glasdon Beacon Installation and operation manual

Operating & Maintenance Manual
Glasdon Buildings
Operating & Maintenance Manual
Glasdon Buildings
Operating & Maintenance Manual
Glasdon Buildings
Operating & Maintenance Manual
Glasdon Buildings
Operating & Maintenance Manual
Glasdon Buildings
Glasdon U.K. Limited
Preston New Road
BLACKPOOL
Lancashire
FY4 4UL
Tel: (01253) 600410
Fax: (01253) 792558
e-mail: [email protected]
www.glasdon.com

2
Operating & Maintenance Manual
Thank you for purchasing a Glasdon product. This manual contains important
information for the installation and future care of your product.
Contents
Chapter 1 Installation
Chapter 2 Electrical Installations
Chapter 3 Base Fixing Guidelines
Chapter 4 Future Care of Your Product
Chapter 5 Handling & Moving Your Product
Should you require any further assistance please contact us on tel: 01253 600410,
2

3
We recommend that all Glasdon Buildings are permanently sited and fixed down to a prepared
concrete base at the time of delivery using the fixing bolts supplied.
Installation guidelines are contained in Chapter 3. To ensure satisfactory operation of door locks
after installation, it is very important to keep door frames square and level during base fixing.
If a panel form delivery option has been arranged for assembly by yourselves following agreement
with our Sales and Technical Department, you will find a comprehensive instruction booklet enclosed
with this manual.
If your Building has been manufactured to a customised design there should also be a CAD drawing
of the layout enclosed for your reference.
If your Building has been fitted with sanitaryware such as wash hand basins, sinks, WC’s and water
heaters, you may have opted for the relevant pipework and fittings to be pre-installed at our factory
rather than making your own arrangements with a local plumber. The final site connection to the
water supply and waste system should always be arranged locally by yourselves and all pre-installed
pipework and fittings thoroughly checked on site before use.
When external shelves and canopies are supplied it may not always be possible to fit these items at
our factory because of delivery width restrictions. In such cases the items will be supplied loose
within the Building ready for simple site fitting by yourselves using the instruction sheet enclosed.
In the event that installation of your Glasdon Building does not take place at the time of delivery,
suitable temporary storage arrangements must be made by yourselves to prevent damage being
sustained either by adverse weather conditions or other influences.
Glasdon Manufacturing Limited cannot accept responsibility for:
1. Damage to Glasdon Buildings which are not permanently sited and installed at the time
of delivery.
2. Damage caused by insecure storage or careless handling.
3. Re-delivery costs due to failure to install immediately or provide adequate storage.
For Buildings which are fitted with an electrical installation we usually issue the original factory test
certificate separately by post to your correspondence address. You will also find a copy of the
certificate enclosed with this manual.
General technical information and individual operating instructions are enclosed for your future
reference for the electrical components fitted within your Building, e.g. consumer units, electrical fan
convector heaters and lighting.
The final site connection to the electric mains supply, along with the earthing of any fitted
sanitaryware and pipework etc, should be arranged locally by yourselves.
We recommend that all electrical installations are inspected annually by a suitably qualified and
competent person.
1 Installation
2 Electrical Installations
3

4
4
3 Base Fixing Guidelines
Beacon
The overall size of a Beacon building is 192mm greater than the nominal internal size, e.g. a 3.66 x
2.44m building is 3.852 x 2.632m.
Base Requirements
The minimum base size required is equal to the overall building size. Assuming no suitable existing
surface, the base should be a minimum of 125mm concrete on to well consolidated hardcore.
The concrete should be of minimum C20/25 grade in accordance with BS8500 Concrete: The
Complementary British Standard to BS EN 206-1.
The base should be flat, level and square, and preferably be raised slightly above the surrounding
ground level.
Base Fixing Detail
82mm composite wall panel
Cover cap
Expanding anchor bolt
Flat, level and square
concrete base (by customer)
Treated softwood bearers
at 300mm spacing
Treated
softwood
plinth
Aluminium
framework
Mastic seal
(by others)
125
45
132 F.F.L.
2094
44
136
Composite insulated floor panel with
heavy-duty vinyl covering and vapour
barrier to underside
44
300
Treated softwood bearers
Base Fixing
Base fixing (by our customers) is accomplished using the expanding anchor bolts supplied. Refer to
the base fixing instructions supplied with the fixings for correct installation in accordance with the
manufacturer’s recommendations.
Finally, apply an external mastic seal to the perimeter of the building.

5
5
Warrior
The overall size of a Warrior building is 112mm greater than the nominal internal size, e.g. a 3.66 x
2.44m building is 3.772 x 2.552m.
Base Requirements
The minimum base size required is equal to the overall building size. Assuming no suitable existing
surface, the base should be a minimum of 125mm concrete on to well consolidated hardcore.
The concrete should be of minimum C20/25 grade in accordance with BS8500 Concrete: The
Complementary British Standard to BS EN 206-1.
The base should be flat, level and square, and preferably be raised slightly above the surrounding
ground level.
Base Fixing Detail
42mm composite wall panel
Cover cap
Expanding anchor bolt
Flat, level and square
concrete base (by customer)
Treated softwood bearers
at 300mm spacing
Treated
softwood
plinth
Aluminium
framework
Mastic seal
(by others)
45
20
94
90
Floor panel with heavy duty vinyl
covering and insulation/vapour
barrier to underside
44
300
Treated softwood bearers
Base Fixing
Base fixing (by our customers) is accomplished using the expanding anchor bolts supplied. Refer to
the base fixing instructions supplied with the fixings for correct installation in accordance with the
manufacturer’s recommendations.
Finally, apply an external mastic seal to the perimeter of the building.
125 79 F.F.L

6
6
Boxer
Base Requirements
The minimum base size required is equal to the overall building size. Assuming no suitable existing
surface, the base should be a minimum of 125mm concrete on to well consolidated hardcore.
The concrete should be of minimum C20/25 grade in accordance with BS8500 Concrete: The
Complementary British Standard to BS EN 206-1.
The base should be flat, level and square, and preferably be raised slightly above the surrounding
ground level.
Base Fixing
Base fixing (by our customers) is accomplished using the expanding anchor bolts supplied. Refer to
the base fixing instructions supplied with the fixings for correct installation in accordance with the
manufacturer’s recommendations.
Finally, apply an external mastic seal to the perimeter of the building.
63
45125
35
97
9530045
Plastic cover cap
Flat, level and square
concrete base (by customer)
95 x 45mm treated
softwood plinth
Mastic seal
(by others)
2mm vinyl floor covering on 15mm
exterior grade plywood with vapour
barrier to underside.
45 x 45mm treated
softwood bearers
25mm insulation to underside of
plywood in between bearers.
Expanding anchor bolt
Base Fixing Detail

7
7
Olympic
The length of an Olympic building is always 200mm longer than the side panels used, e.g. a building
having 2 no. 1m panels in each side and 1 no. 1.5m panel at each end has the dimensions
2200mm x 1500mm
Base Requirements
The minimum base size required is equal to the overall building size. Assuming no suitable existing
surface, the base should be a minimum of 125mm concrete on to well consolidated hardcore.
The concrete should be of minimum C20/25 grade in accordance with BS8500 Concrete: The
Complementary British Standard to BS EN 206-1.
The base should be flat, level and square, and preferably be raised slightly above the surrounding
ground level.
Base Fixing
Base fixing (by our customers) is accomplished using the expanding anchor bolts supplied. Refer to
the base fixing instructions supplied with the fixings for correct installation in accordance with the
manufacturer’s recommendations.
Finally, apply an external mastic seal to the perimeter of the building.
Mastic seal
(by others)
m.s. reinforcement
87
10
115
8042
Vapour barrier
on 3mm plywood
25mm treated
softwood bearers
Flat, level and square
concrete base (by customer)
Black floor seal
Black cover caps
2mm vinyl floor covering on 12mm plywood
44mm foam
80
x
Expanding
anchor bolt
Base Fixing Detail

8
GENESIS BASE FIXING DETAIL
(SCALE 1:2)
Sleeve type M8 heavy duty high
load BZP anchor bolt Gr 8.8 size
12/10 - anchor length 80mm
122 28
C
L
galvanised mild
steel subframe
100 x 5mm welded
base !"#$% plate
Flat, level concrete
base (by others)
18mm Anti-slip plywood
GRP wall panel with !&'
retardent foam and resin
chipboard reinforcement
Genesis
Base Requirements
The minimum base size required is 100mm less than the overall building size. Assuming no suitable existing
surface, the base should be a minimum of 125mm concrete on to well consolidated hardcore.
The concrete should be of minimum C20/25 grade in accordance with BS8500 Concrete: The Complementary
British Standard to BS EN 206-1.
The base should be flat, level and square, and preferably be raised slightly above the surrounding ground
level.
Base Fixing Detail
Base Fixing
Base fixing is recommended for all installations, permanent and non-permanent.
Base fixing (by our customers) is accomplished using the expanding anchor bolts supplied. Refer to the base
fixing instructions supplied with the fixings for correct installation in accordance with the manufacturer’s
recommendations.

9
All Glasdon products are manufactured using only the highest quality materials and are designed to
provide the very best value for money with years of trouble-free service. To help preserve the life of
your Glasdon Building and keep it in pristine condition, we recommend that regular cleaning is
arranged as part of your routine site cleaning programme.
The frequency of cleaning will depend on the prevailing site conditions, e.g. industrial and marine
environments are likely to need more frequent cleaning than rural environments.
Standard Construction Materials
Routine Cleaning for Standard Materials
a) EXTERNAL SURFACES
D 78.3</.8;!8@./;8+=/.5>6373>6;+6/@8;4
Wash using a soft sponge mop and plenty of warm water containing a mild soapy detergent and
then rinse immediately with clean water. Anodised or powder-coated surfaces can be further
enhanced with the application of a proprietary wax-free polish.
D "!
Wash using a soft sponge mop and plenty of warm water containing a mild soapy detergent (or
car body shampoo) and then rinse immediately with clean water, preferably using a hose pipe
without power-washing. To further enhance the appearance of GRP we recommend the annual
application of a coat of wax polish, e.g. a proprietary car body wax.
Any minor GRP surface blemishes can be restored using a proprietary cutting compound prior to
applying a coat of polish.
D !5+<=3-8+=371<
Wash using a soft sponge mop and plenty of warm water containing a mild soapy detergent and
then rinse immediately with clean water, preferably using a hose pipe without power-washing.
b) INTERNAL SURFACES
D 8==87&37B58;+637+=/+-/.'+55<
Clean using a sponge and warm water containing a mild soapy detergent. For stubborn marks
a soft bristle brush may be used.
D 5/-4/.!+37='+55<
Clean using a sponge and warm water containing a mild soapy detergent.
D &37B5588;<
Always clean in accordance with the manufacturer’s instructions enclosed.
- *
D $8>12/7/.5+<<$2/;6895+<=3-
Clean with a sponge and warm water containing a mild soapy detergent and rinse immediately
with clean water. Dry toughened glass using a chamois leather. Thermoplastic is very susceptible
to scratching and marking, therefore, please clean with extreme care.
>=>;/+;/ 0)8>;!;8.>-=
8
!" %$# $"($"#%"# *
5>6373>6
;+6/@8;4
"!'+55<
or Roof
!5+<=3-8+=/.
'+55<8;"880
8==87&37B58;
+637+=/
7=/;7+5'+55<
5/-4/.!+37=
7=/;7+5'+55<
$8>12/7/.
5+<<8;
$2/;6895+<=3-
Beacon
Warrior
Boxer
Olympic
PRODUCTS INTERNAL & EXTERNAL SURFACES GLAZING
Aluminium
Framework
External
GRP Walls
or Roof
Plastic-Coated
Walls or Roof
Cotton Vinyl or
Laminate
Internal Walls
Flecked Paint
Internal
Walls
GRP Internal
Walls &
Ceiling
Toughened
Glass or
Thermoplastic
Beacon t t t t
Warrior t t t t t
Boxer t t t
Olympic t t t
Genesis t t t
a) EXTERNAL SURFACES
t Anodised or Powder-Coated Aluminium Framework
Wash using a soft sponge mop and plenty of warm water containing a mild soapy detergent and then
rinse immediately with clean water. Anodised or powder-coated surfaces can be further enhanced with
the application of a proprietary wax-free polish.
t GRP
Wash using a soft sponge mop and plenty of warm water containing a mild soapy detergent (or car body
shampoo) and then rinse immediately with clean water, preferably using a hose pipe without power-
washing. To further enhance the appearance of GRP we recommend the annual application of a coat of
wax polish, e.g. a proprietary car body wax.
Any minor GRP surface blemishes can be restored using a proprietary cutting compound prior to applying
a coat of polish.
t Plastic-Coatings
Wash using a soft sponge mop and plenty of warm water containing a mild soapy detergent and then
rinse immediately with clean water, preferably using a hose pipe without power-washing.
b) INTERNAL SURFACES
t Cotton Vinyl or Laminate-Faced Walls
Clean using a sponge and warm water containing a mild soapy detergent. For stubborn marks a soft
bristle brush may be used.
t Flecked Paint Walls
Clean using a sponge and warm water containing a mild soapy detergent.
t GRP Internal Wall & Ceiling
Simply wipe down with sponge and warm water. then dry with soft cloth.
Any minor GRP surface blemishes can be restored using a proprietary cutting compound prior to applying
a coat of polish.
t Vinyl Floors
Always clean in accordance with the manufacturer’s instructions enclosed.
c) GLAZING
t Toughened Glass & Thermoplastic
Clean with a sponge and warm water containing a mild soapy detergent and rinse immediately with clean
water. Dry toughened glass using a chamois leather. Thermoplastic is very susceptible to scratching and
marking, therefore, please clean with extreme care.
Standard Construction Materials

10
Routine Inspection of Moving Parts
During the routine cleaning process we recommend inspection and cleaning of all moving parts such
as external security shutters, sliding windows, door handles, locks and hinges. The application of a
proprietary light oil to items such as security shutters, door lock mechanisms and hinges will also help
to maintain their efficient operation.
Regular cleaning and lubrication where appropriate is essential to prevent an accumulation of
dirt and debris which can be detrimental to most moving parts and cause irreversible damage if
left unattended.
Rainwater Management Systems
Beacon and Warrior Buildings which are supplied for external use have an integral rainwater
management system with fascia guttering and a corner post downspout arrangement. To prevent
any possible blockage and the build up of rainwater on the roof, we recommend periodic inspection
and cleaning of the guttering and the ‘leafguard’ located at the top of each downspout.
Window Glazing Film
Upon delivery of your Building you may find that any tinted and mirror finish glazing film has a
slightly cloudy appearance and contains small surface water bubbles. This is a normal part of the
curing process and it usually clears up within a few weeks of delivery, but may take longer in
colder weather.
Please allow a minimum of 28 days from delivery before cleaning the glazing film and do not
attempt to ‘push out’ any surface defects during this curing period.
Wash with a sponge and warm water containing a mild soapy detergent and rinse immediately with
clean water.
Air Conditioning Systems
If an Air Conditioning System is installed in your Building, the commissioning together with a 12
month maintenance and service agreement (via a third party provider) are normally included as
standard. To ensure the safe and efficient operation of this equipment beyond the initial 12 month
period, we strongly recommend that you make your own arrangements for an ongoing maintenance
and service agreement directly with the existing provider or with an alternative qualified and
competent source.
Warranty
Our standard warranty period is 12 months from the date of delivery and this covers the cost of any
parts and labour required to rectify defects in materials and workmanship supplied by Glasdon. This
warranty does not extend to defects caused by abuse, exceptional usage and modifications or work
undertaken by others.
Spares & Repairs
For replacement and spare parts and repair work etc please contact our Service Department.
CAUTION!
1. For mild soapy detergents we recommend using proprietary household cleaners (or a car body
shampoo for GRP) to the concentration as detailed on the manufacturer’s instructions.
2. Do not use organic solvents or abrasive cleaners which may cause surface damage or
colour fading.
3. Always clean from top to bottom and avoid overcleaning or scrubbing which can do more
harm than good.
9

11
DO NOT sling across the door threshold.
BEACON & WARRIOR
Position the slings at each end of the Building
approximately 250mm from the corners.
Cut-outs
Tie-back
rope with
protective
packing
Timber spreader beams
5 Handling and Moving Your Product
10
To prevent damaging your Glasdon Building whilst moving and handling, please follow these
guidelines. If you are unsure about any aspect please contact our Transport Department and we will
be delighted to assist.
General Principles
E 6A,C=?=016,>-06>8C698=6482=
E 6A,C=60>>30=6482=>,50>3069,/
E '=0:<9>0.>4@0:,.5482-0>A008>30=6482=,8/
product, where appropriate, to prevent damage.
E 6A,C=>40-,.5>30=6482=A4>3.,<0
E 6A,C=:,/>30>40-,.5<9:0=>9:<0@08>
damaging your product.
E 6A,C=641>=69A6C.,<01?66C,8/=,106C
EDO NOT USE CHAINS OR ROPES TO LIFT.
EDO NOT RUSH ANY PART OF THE LIFT.
EIF IN DOUBT PLEASE ASK.
Building sizes of 3.66 x 2.44m and aboveBuilding sizes up to 3.66 x 2.44m
Position the slings at each corner of the
Building on the underside of the panel base
perimeter radius.
Position the slings at each corner of the Building
on the underside of the panel base perimeter.
Position the slings in the cut-outs provided
in the timber base plinth.
OLYMPIC
Timber spreader beams
BOXER
RIGHT WRONG
Tie-back ropes
around end
elevations to
prevent slings
slipping inwards
250
Tie-back rope
around side
elevation to
prevent slings
slipping
outwards
Sling
Sling
Protective
packer
Protective
packer
Tie-back rope
around side
elevation to
prevent slings
slipping outwards
Sling
Protective
packer
To allow slings to be released easily
after the lift, always lower the
Building on to temporary wedges.
Temporary
wedge
/ GENESIS

12
For small Buildings only
RIGHT WRONG
Always use fork extensions to lift across the
full width of the Building.
Short forks will damage the floor (if fitted) or
will not support a Building without a floor.
Always ensure a high
apex to the crane hook.
DO NOT use a low
apex to the crane hook
as it places a crushing
effect upon the roof of
the Building.
Always use spreaders on all large Buildings.
The spreaders should be larger than the span
of the Building.
By not using spreaders the load on the slings
produces a crushing effect upon the roof of
the Building.
Slings must be seated at
each end of the Building
and positioned approx.
250mm from the corners for
maximum stability.
Always tension the slings
before tying back and place
the tie-back ropes at low
level to prevent the slings
from slipping inwards or
outwards as indicated on
page 6.
Small Buildings may require
tighter roping.
Too much tension on the
tie-back rope may cause it
to snap or the Building to
topple due to the lower
centre of balance.
Slings positioned too close
to the centre of the
Building will be unstable.
CRANAGE
Hook Height
Sling Security
FORK LIFT TRUCK
11
Spreader Beams
Tie-back
rope with
protective
packing

Enclosed Documents for your Glasdon Building
Customer ................................................................. Glasdon Ref No. .............................
Product Description .............................................................................................................
Additional Items:
........................................................................
........................................................................
........................................................................
........................................................................
........................................................................
Documents prepared by
........................................................................
Date ...............................................................
Product Brochure
CAD Layout Drawing
Electrical Test Certificate
Certificate of Compliance
On Site Assembly Instructions
Canopy & Shelf Installation Sheet
Technical documentation for:
Vinyl Floor Covering
Consumer Unit
Lighting
Heating
Air Conditioning System
Should you require any further assistance please contact us on
In accordance with our policy of continuous development and improvement, we reserve the right
to make changes in design and specification without notice.
Glasdon UK Limited products are manufactured under license worldwide and
various components of the models are patented and design registered.
Glasdon U.K. Limited
Preston New Road
BLACKPOOL
Lancashire
FY4 4UL
Tel: (01253) 600410
Fax: (01253) 792558
e-mail: [email protected]
www.glasdon.com
C000/0001
© Copyright Glasdon AUG2008
© Copyright Glasdon May 2015
C999/0001
12B088-12 Issue 1
This manual suits for next models
4
Other Glasdon Trash Compactor manuals
Popular Trash Compactor manuals by other brands

KitchenAid
KitchenAid compactor installation instructions

Marathon
Marathon RJ-88SC user manual
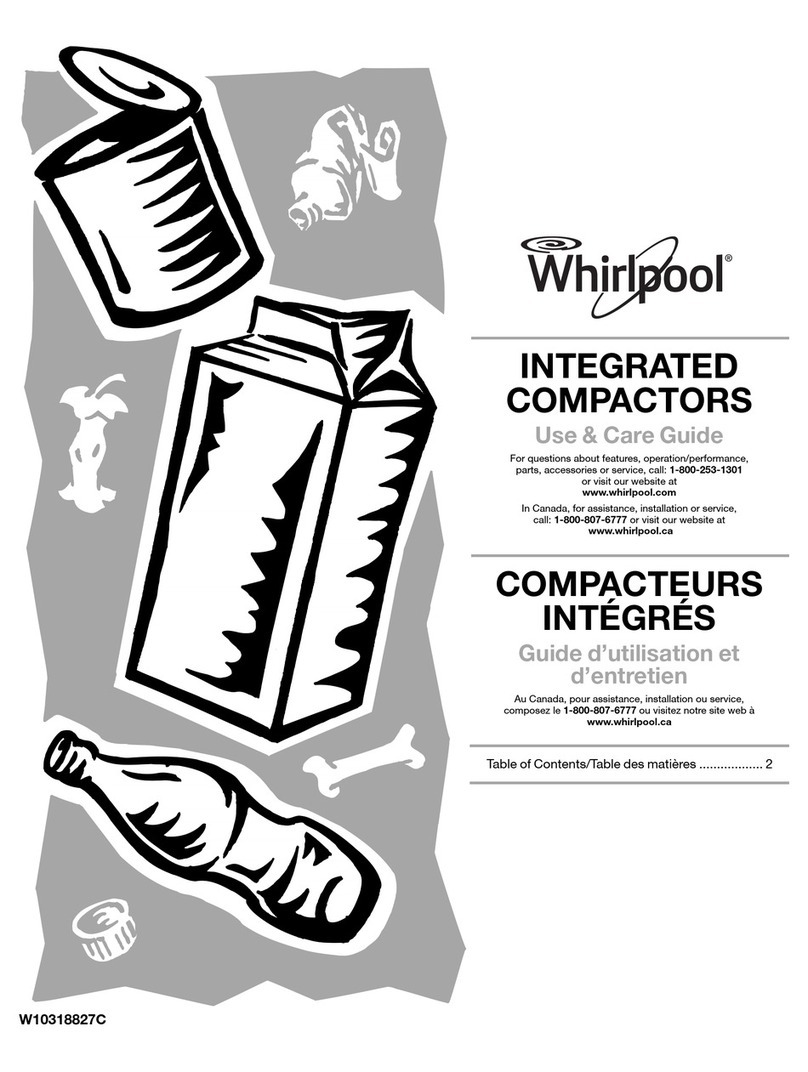
Whirlpool
Whirlpool W10318827C Use & care guide
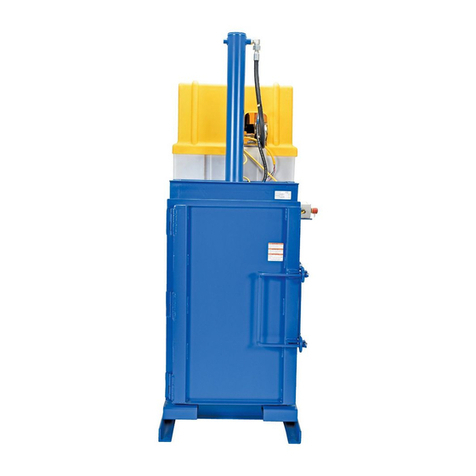
Vestil
Vestil HDC-905 Series instruction manual
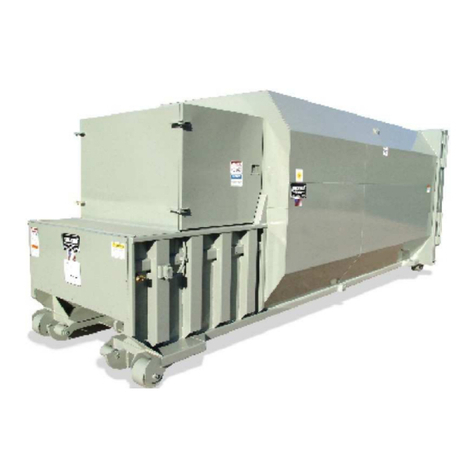
Dover
Dover Marathon RAMJET Signature Series Operation, maintenance and installation manual
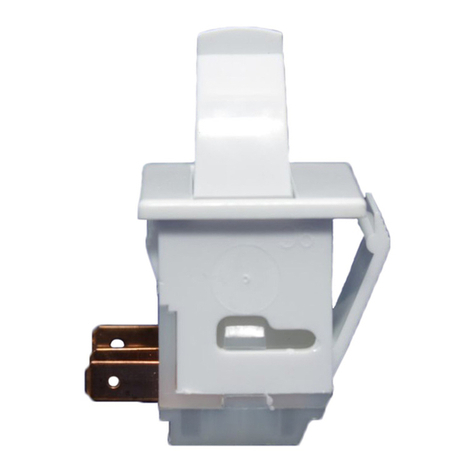
KitchenAid
KitchenAid KFCK03ITWH0 parts list