gMFC GGC V3 Operator's manual

GGC V3 documentation
V3.00 - 16/10/2020
The GGC V3 adapter is an intelligent USB converter for driving a step
motor interface. The GGC drives most step/dir compatible motor
interfaces, such as the MM2001, and the MDLCNC bipolar motor controller.
1. Functionalities
The functionalities of the GGC V3 adapter are:
Generation of a unique GMFC license key, independent of the PC and
disk formatting.
Works under any Windows version that supports USB from Win98 to
Windows 10.
10, 20, or 50 KHz internal timer for implementing smooth
accelerations. The internal timer supports motor interfaces that
don’t have a timer.
Compatible with most existing step/dir unipolar and bipolar motor
interfaces. Fully configurable Dir/Step outputs. Motor Enable on
parallel port pin 1 or 17, with High/Low active level.
Internal wire heat circuits.
Optional LCD display. The GGC V3 support LCDs with 1 or 2 lines of
16 characters and the RepRap LCD with 4 lines of 20 characters.
Automated recognition of the GGC parameters by GMFC (from version
3.89.14).
Full compatibility with the former MMUSB interface.
Programming of the MM2001 PIC firmware. The V5.1 or MM2001_GGC
versions of the MM2001 firmware are mandatory to work with the
GGCV3 interface.

Configuration through the ggc_utility V3 software on the PC. The
utility also allows the programming of the MM2001 PIC firmware.
Several internal parameters can be set by using ggc_utility: the
configuration of the parallel port pinout, the timings of the motor
pulse commands and the frequency of the internal timer.
The GGC adapter possesses two functioning modes: MMUSB and GGC.
2. MMUSB Mode
In the MMUSB mode, the GGC adapter is legacy compatible with the former
MMUSB adapter and supports only the MM2001 motor interface. The LCD
display is optional. The wire heat is managed by the MM2001 interface.
No switch or LED is necessary for the GGC to work in this mode. When
using a MM2001 with the GGC in MMUSB mode, the MM2001 must be programmed
with the V5.1 firmware.
In the MMUSB mode, the GGC internal parameters can’t be changed and are
set to the following values:
Timer frequency: 100 microseconds (10 KHz)
Motor step duration: 50 microseconds
Time for data before step: 14 microseconds
If a LCD display is used, it successively displays after reset:
"GGC V3.00 ", where 3.00 is the GGC firmware version.
"Dir 14,Stp 50,T0", this screen gives the value of internal parameters.
Dir is the time for the data to be set before the motor pluse command.
Stp is the duration of the motor pulse command. T is the timer value: 0
means 10Khz.
"MMUSB Mode ", this screen indicates that the GGC is operating in
MMUSB mode.
"WAITING USB ", this screen is shown until the GGC is recognized by
Windows and ready to be used.
"MMUSB H50% MAN M", this screen is displayed during normal functioning.
H50% shows the current heat (here, 50%), MAN (or PC) shows the position
of the PC/MAN switch of MM2001 interface. M (if displayed) shows that
the motors are powered on by GMFC.

3. GGC Mode
In GGC mode, two different command panels are supported: the BP button
and the RepRap panel.
3.1. The BP Button panel
The BP panel must be made by the user. The BP panel relies on three push
buttons BP+, BP-, Reset, the led LEDHeat and 3 switches HeatOn, PC/MAN
and MotorOn.
The LEDHeat is mandatory for the heat circuit to work. Buttons and
switches are optional. When used, buttons and switches are connected
through the J3 connector. The LCD is connected to J2. Both 1 line et 2
line 16 character LCDs can be used.

3.1.1 Buttons and switches
BP+, BP- are used to set the heat value when the heat value is
controlled by the GGC. A short press on BP+ increases the heat; a short
press on BP- decreases the heat.
Pressing on BP- and BP+ simultaneously enters a menu for setting the
maximum possible heat value. The maximum heat prevents breaking the wire
if it does not support a heat value of 100%. Pressing on BP- and BP+
again will exit this menu. Note, that with versions of GMFC above 4.0,
the maximum heat value is specified in the table configuration dialog of
GMFC and overrides the maximum value in the GGC.
The optional PC/GGC switch controls the source heat value that is set
either by the PC or the GGC interface. Even in the GGC position, the
heat is only activated when GMFC sends a heat command.
The optional HeatON switch enables the heat. This switch is useful only
for providing additional security in the addition of the GMFC heat
command.
The optional MotorOn switch enables the motors. This switch is useful
only for providing additional security. It can be used as an emergency
stop switch.
The optional Reset button is used to reset the GGC interface.
3.1.2 LEDs
LEDHeat: this LED indicates that the heating circuit is functioning.
Because control of the wire heat goes through the LED, it MUST be
connected for the heat circuit to work.
LEDMotor: this optional LED indicates that there is power to the motors.
LEDOn: this optional LED indicates that there is power to the GGC.

3.2. The RepRap panel
The RepRap panel contains a 4 line LCD, a rotary selector with a press
button, and a reset button.
The RepRap panel must be connected to the GGC through the GGC LCD
adapter which has to be bought in addition to the GGC. The adapter
provides the LEDHeat, and is ready to use. Soldering is only required
for the optional switches.

3.2.1 Buttons and switches
The rotary selector is used to set the heat value when the heat value is
controlled by the GGC.
Pressing on the selector enters a menu for setting the maximum possible
heat value. The maximum heat prevents breaking the wire if it does not
support a heat value of 100%. Pressing on the selector again will exit
this menu. Note, that with versions of GMFC above 4.0, the maximum heat
value is specified in the table configuration dialog of GMFC and
overrides the maximum value in the GGC.
The optional PC/GGC switch controls the source heat value that is set
either by the PC or the GGC interface. Even in the GGC position, the
heat is only activated when GMFC sends a heat command.
The optional HeatON switch enables the heat. This switch is useful only
for providing additional security in the addition of the GMFC heat
command.
The optional MotorOn switch enables the motors. This switch is useful
only for providing additional security. It can be used as an emergency
stop switch.
3.3. Motor interface parameters
The control of the motor interface can be adjusted by several
parameters:
- Parallel port pinout of the step/dir signals.
-Timer frequency: 50KHz (20microseconds), 20KHz (50
microseconds) or 10KHz (100 microseconds).
-Step pulse duration: the step pulse is active low. Its value
can be chosen with 2 microseconds increments.
-Direction available before the step pulse: value can be
chosen with 2 microseconds increments.
- Motor enable signal on pin 17 (MM2001 compatible) or pin 1
(Chinese motor interfaces).
- Motor enable active low or high.
When using a MM2001 with the GGC in GGC mode, you must program the
MM2001 with the MM2001_GGC firmware which is compatible with a 50 Khz
Dir
Step Step duration
Dir before step

timer. Using the MM2001_GGC firmware, the MM2001 internal timer and heat
functionalities are disabled.
3.4. LCD screens
3.4.1 Initialisation
If the LCD display is used, it successively displays after reset:
"GGC V3.00 ", where 3.00 is the GGC firmware version.
"Dir 2,Stp 2,T1", this message displays the value of internal
parameters. Dir is the time for the data to be set before the motor
pluse command. Stp is the duration of the motor pulse command. T is the
timer value: 0 means 10KHz, 1 means 20KHz, 2 means 50KHz.
"HMAX SECURE:99%", this screen indicates the maximum allowable heat
value to suit the type of cutting wire being used.
"WAITING USB", this message is displayed until the GGC is recognized by
Windows on the PC and ready to be used.
3.4.2 Main menu
If using a one or two line LCD display:
"H:050% PC M* H*", this message is displayed during normal functioning.
H050% shows the current heat value (here, 50%),
PC/GGC tells that the heat value is given by the GGC or by the PC
(GMFC). In GCC heat mode, the value can be adjusted by the BP+ and BP-
buttons.
M* shows that the motors are powered on. This means that GMFC is running
a heat command. M (without *) is shown when motors are off.
H* shows that the heat is on. The LEDHeat is also on. H (without *) is
shown when the heat is off.
If using a four line RepRap LCD display:
"Heat: 50% Max: 100%"
"PC Motor* Heat*"
Heat: 80% shows the current heat value (here 50%). Max: 100% shows the
maximum heat value (here 100%),
PC/GGC tells that the heat value is given by the GGC or by the PC
(GMFC). In GCC heat mode, the value can be adjusted by the rotary
button.
Mot* shows that the motors are powered on. This means that GMFC is
running a heat command. Mot (without *) is shown when motors are off.
Heat* shows that the heat is on. The LEDHeat is also on. Heat (without
*) is shown when the heat is off.
3.4.2 Maximum Heat Menu
If using a one or two line LCD display:
"Heat Max: 100%"
This is the value of the maximum heat value. It is adjusted by the BP+
and BP- buttons. Pressing both buttons simultaneously will return to
the main menu.
If using a four line RepRap LCD display:
"Max Heat Setting"
"Max: 100%"

This is the value of the maximum heat value. It is adjusted by the
rotary buttons. Pressing the button will return to the main menu.

4. GGC Connections
The GGC connects to the motor interface via the parallel port, and to
the PC via a ‘B’ type USB cable as used for printers.
On board connectors -
J1 – 14 pin connector - Home and Limit switches
J2 - 14 pin connector - LCD display
J3 - 14 pin connector – LED, buttons and switches
J4 - 20 pin connector – Optional temperature sensor daughter board.
The pinout of J1, J2, J3 from top is:
2 4 6 8 10 12 14
1 3 5 7 9 11 13
Pin 1 is marked on the board.
Powering the heat wire
The wire power supply is connected to the GGC via the PowBow connector.
The maximum voltage is 50V DC. Beware of polarities; wrong connection
will damage the GGC. The bow must be connected to the Bow connector.
J3 - LEDs and switches wiring
Buttons and switches are connected to GND through J3.14. Do not connect
J3.14 to power supply ground.

J2 - LCD wiring
J2 is used to connect the one or two lines 16 character LCD Display
Panel via a short length of ribbon cable wired as detailed below. All 16
character LCDs should be compatible.
Connector
Pin
Function LCD Pin
J2.1 PD7 LCD14
J2.2 PD6 LCD13
J2.3 PD5 LCD12
J2.4 PD4 LCD11
J2.5 Non connected
J2.6 Non connected
J2.7 Non connected
J2.8 Non connected
J2.9 E LCD6
J2.10 R/W LCD5
J2.11 RS LCD4
J2.12 GND LCD3
J2.13 Vcc LCD2
J2.14 GND LCD1
Here is a picture of the J2 connecting cable:
Note that the red wire is connected to pin J2.1

J1 – Home & Limit Switch Wiring
The Home switches and Limit switches are used to prevent accidental
over-run beyond the physical limits of the X and Y axes. The Home and
Limit switch options are only functioning when running the GMFC EXPert
software. They do not function under any other version of GMFC. Home and
Limit Switches must be of type "Normally Open".
Important: Limit switches are internally connected to the input signals
of the parallel port (10 timer, 11 Heat acquisition, 12 Man/Auto heat).
If you want to use Limit switches, the GGC must be used in GGC mode, and
you must be sure that these input signals are left open or not used by
the motor interface. This can be done by cutting the parallel cable. If
you are using an MM2001 motor interface, the MM2001_GGC firmware is
mandatory.

5. Configuration utility, ggc_utilityV3
The ggc_utilityV3 program allows the PC configuration of the GGC
interface, testing and moving motors without GMFC. It also permits to
program the PIC firmware of the MM2001.
The program ggc_utilityV3 is available from https://gmfcsoft.fr/shop/en/
usb-support-for-gmfc-with-the-ggc-adapter/ .
5.1. Internal parameter configuration
Download the file ggcV3.zip, then uncompress it; run the executable file
ggcV3.exe. If the GGC adaptor is not yet connected, the ggc_utility will
ask you to connect it.
Press the “Read Configuration” button so that the ggc_utilityV3 displays
the configuration of the GGC adaptor.

The GGC is shipped configured in MMUSB mode. If you want to switch to
the GGC mode, you must uncheck the ‘MMUSB mode’ box. Then you can modify
the appropriate internal timer frequency and motor timing parameters.
Additionally, to avoid rewiring motor cables, you can simply reconfigure
the motor outputs. Finally, you can set the pinout for the “Motor On”
signal (1 or 17) and also the active state (“Low” or “High”).
The ggc_utilityV2 provides a list of predefined settings for well-known
interfaces. Just select the interface in the list to set the predefined
parameters. Caution: this drop box is only for settings parameters, it
does not display the type of the interface currently connected.
To program the settings into the GGC V2, you have to press the ‘Program
GGC’ button. Wait until “done” is printed in the message window.
Note for the Gecko G540 controller - Choose setting for the MDLCNC
interface. Then set the "step duration" to 2 and "Delay for Dir before
Step" to 0. Set the Timer to 50Khz. You have to disable the charge pump
on the Gecko since the GGC does not provide the required signal. There
is no Motor ON signal for the Gecko, by disabling the charge pump,
motors are always ON.
5.2. Moving motors with the ggc_utilityV3
To move the motors, you must first press the ‘Motor On’ button to power
the motors. Then, you have to set several parameters:
First, you must specify which motors to move using the field ‘Motors’
and the following table:
X Left X Right Y left Y Right
12 192 3 48
204 51
Sum up values to move motors simultaneously. The value 255 will move all
motors.
#Step: This is the number of steps performed by a move command. The
maximum value is 128.
When starting to move the motors, a good value would be to use the
number of steps required to rotate the shaft a half or one full
revolution.
Step rate: This sets the interval between motor steps. The value is
given in hundreds of microseconds. The default value of 20 (i.e., 2
milliseconds) should work with all motors. You should decrease the value
for testing a higher speed. Still, precise speed calibration should be
done within GMFC.
Cut Repeat: This is the number of times that the motor move will be
executed when pressing the Cut button.
For example: if #Step equals the number of steps for rotating 1
revolution, and Cut Repeat equals 10, the motors will turn 10
revolutions each time Cut is pressed.

Pressing the ‘Cut Forward’ button will move the motors forward and up,
if the motors are correctly connected (X to the end of the table, and Y
up).
Pressing the `Cut Back’ button will move the motors backward and down.
The `Motors OFF’ button switches the motors off. When the motors are
off, pressing any of the Cut buttons will have no effect.
5.3. Programming the MM2001 PIC firmware
This section is only for the users of the MM2001 interface. It does not
apply to other motor interfaces.
You must carefully follow instructions related to the programming jumper
and the RESET button of the MM2001 interface.
If you have a PIC type 16F874A or 16F877A, check the box `PIC “A”
Revision’. If you forget to do so, the PIC may be blocked and further
programming disabled.
Press the `Write PIC’ button and follow the instructions carefully...
Use the file MM2001-V51.HEX or later for correct operation of the MM2001
with the GGC interface. Programming the PIC with older firmware is
possible, but the MM2001 will not run properly because the GGC interface
requires a faster response time.
When programming a PIC type "A", it is necessary to erase it first using
the `Erase PIC’ button. If the programming fails, it is necessary to
perform a further erase before each attempt to program the device.
For standard (none "A") PIC, erasing is not necessary.
Popular Adapter manuals by other brands
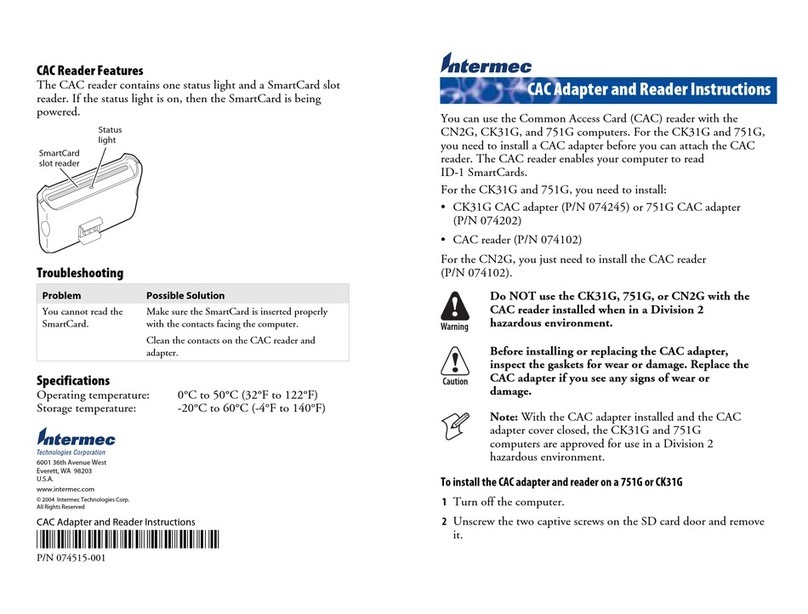
Intermec
Intermec 751G instructions
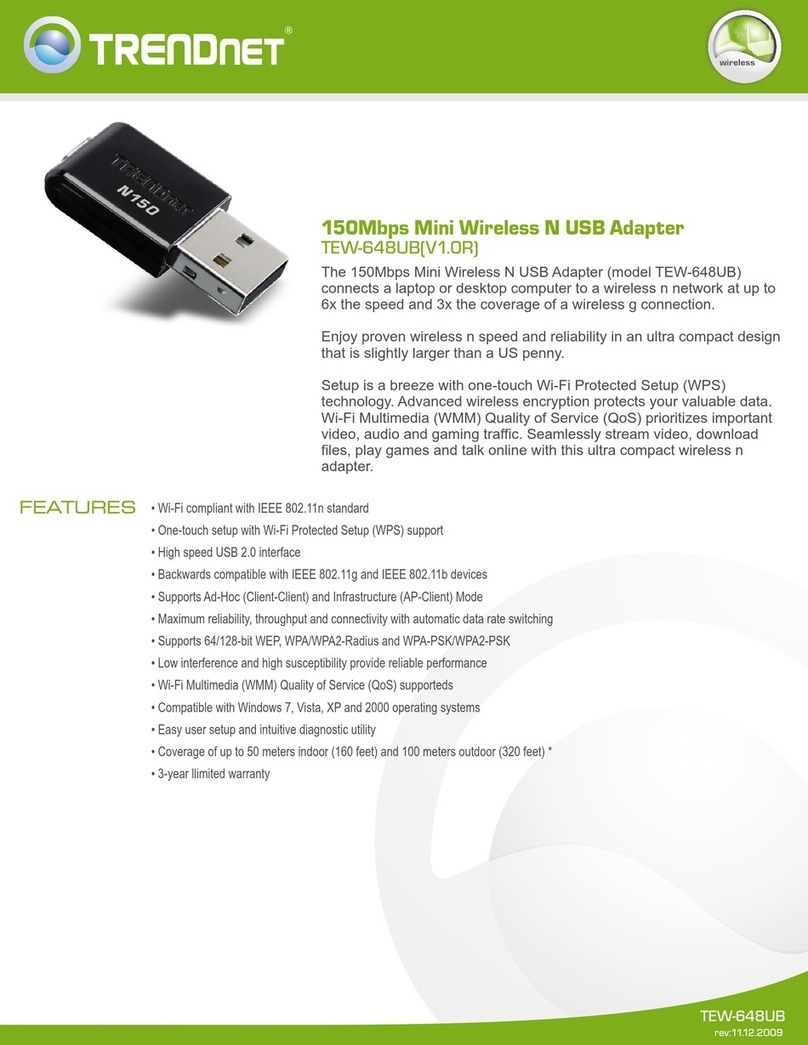
TRENDnet
TRENDnet TEW-648UB - 150Mbps Mini Wireless N USB 2.0... Specifications
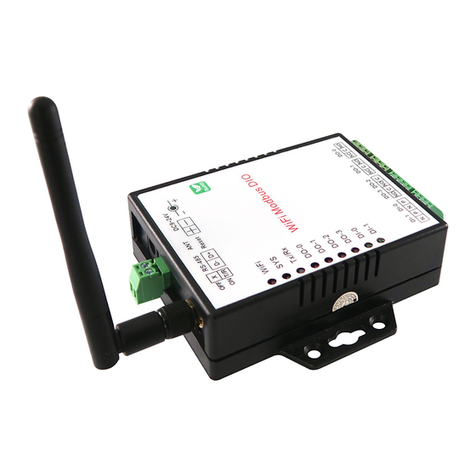
Quatech
Quatech RS-485 Operation manual
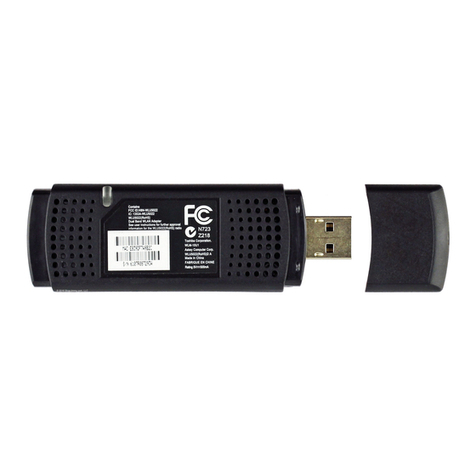
Toshiba
Toshiba WLM-10UB1 owner's manual
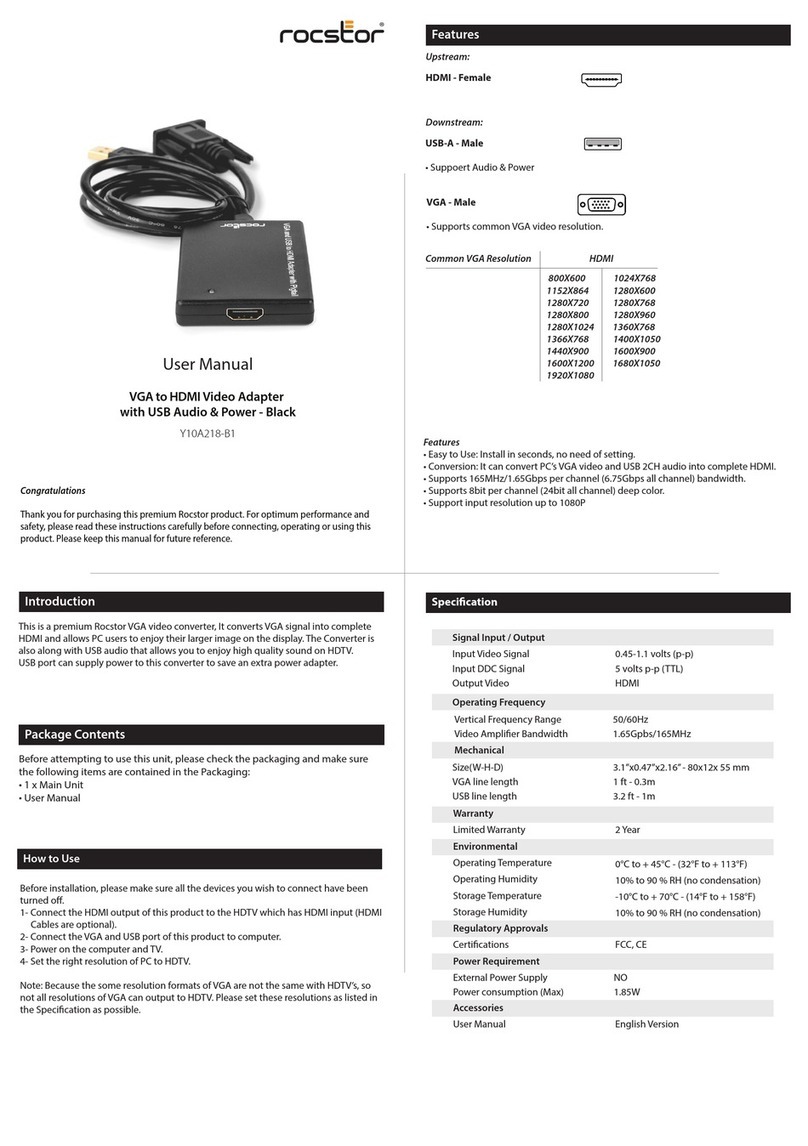
Rocstor
Rocstor Y10A218-B1 user manual
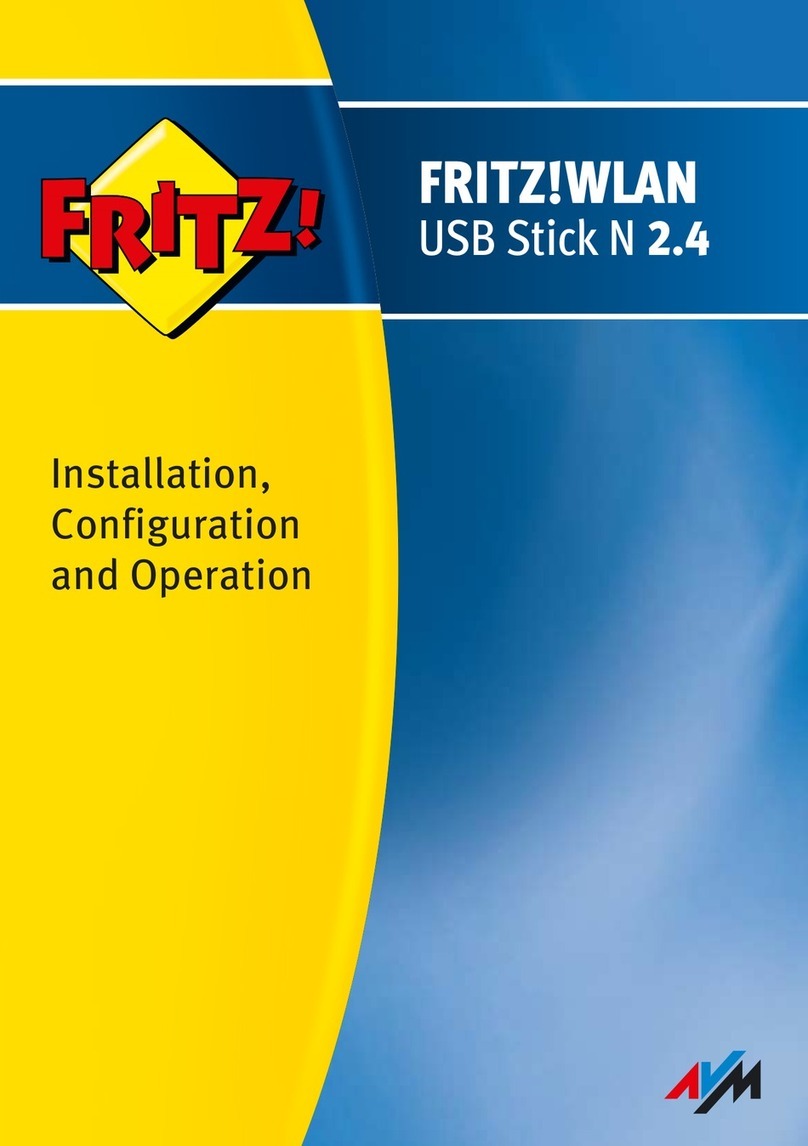
AVM
AVM FRITZ!WLAN USB Stick N 2.4 Installation, configuration and operation