GRAUPNER ASW 28 User manual

GRAUPNER GmbH & Co. KG D-73230 KIRCHHEIM/TECK GERMANY
Modifications reserved. No liability for printing errors. Ident. # 0062067 4/2010
1
Order No. 9451
Instructions
ASW 28
Model glider
for
slope-soaring and aero-tow
This model requires at least a five-function radio control system.

GRAUPNER GmbH & Co. KG D-73230 KIRCHHEIM/TECK GERMANY
Modifications reserved. No liability for printing errors. Ident. # 0062067 4/2010
2
Specification
Wingspan approx. 4000 mm
Overall length approx. 1750 mm
Wing section HQ/W 3/11
Tailplane section NACA 009
Total surface area approx. 75.5 dm²
All-up weight according to
fittings, min. approx. 5500 g
Centre of Gravity approx. 85 - 90 mm back from the wing root
leading edge, measured on both sides
Longitudinal dihedral approx. 1 - 1.5°
Caution: This model is not a toy!
If you are a beginner to this type of model, please ask an experienced model flyer for
help and support. If you attempt to operate the model without knowing what you are
doing, you could easily injure yourself or somebody else. Please keep your safety
and well-being in mind at all times.
Important: before you start construction
Even if you have already built a large number of RC models please read right through
these instructions and check that all the kit components are actually present. We
have taken great trouble to keep construction as simple as possible, without making
any compromises in the area of safety.
Notes on building the model
It is essential to read right through the building instructions before starting work on
the model. Bear in mind the hazards involved in the use of tools.
Before making any glued joints, be sure to clean the surfaces and remove all traces
of grease. We recommend sanding lightly, before wiping with a non-greasy cleaning
agent. Before gluing parts to the fuselage it is essential to roughen the surfaces with
fine abrasive paper and de-grease them with acetone or similar solvent, otherwise
you will not obtain strong, durable joints. This applies in particular to moulded GRP
fuselages.
RC system components and the control surface linkages must be installed at the ap-
propriate stage of construction, as it may be very difficult or even impossible to fit
them later.
When you are buying a radio control system it is important to ensure that the trans-
mitter and receiving system are designed for use with model aircraft, and are ap-
proved by your national Post Office approvals authority. All RC units should possess
an FTZ series approval number.
Please remember that other radio systems and radio-frequency apparatus are also
permitted to operate in the frequency ranges used by model radio control equipment,
and there is no guarantee that your system will not suffer interference caused by
such apparatus.
If you are not sure whether this applies to you, contact your nearest Post Office Tele-
communications office. Your local model shop will also have this information.

GRAUPNER GmbH & Co. KG D-73230 KIRCHHEIM/TECK GERMANY
Modifications reserved. No liability for printing errors. Ident. # 0062067 4/2010
3
During construction
When handling adhesives and solvent-based materials it is important to observe the
safety notes and instructions supplied by the manufacturer. Many glues and solvents
are capable of causing injury and damage to materials if they are not used com-
petently. Take waste glue and paint to your local model shop or toxic waste collection
centre.
Note that balsa knives, pins, etc. have sharp points and edges, and should be hand-
led carefully to avoid injury.
Take care to keep tools, adhesives and paints out of the reach of children.
A large, unobstructed working surface is a great advantage for all types of model-
making.
If you are a relative beginner and are not sure of any process, ask an ex-
perienced modeller for help.
Tools required to build the ASW 28
Pencil (HB lead), felt-tip pen, setsquare, tape measure or metre rule, household scis-
sors, sharp narrow-bladed knife, e.g. balsa knife, Order No. 980, small electric drill,
set of twist drills, allen keys, syringe, Order No. 739.3.
Gluing different materials
The following table gives examples of some typical joints, but it makes no claim to be
comprehensive.
Material Typical joint Adhesive
Order No.
GRP to Fuselage to UHU plus endfest 300
plywood formers Order No. 950.43
GRP to Camber-changing UHU plus endfest 300
aluminium flap to flap horn Order No. 950.43
Areas of the fuselage which are to be glued should be rubbed down with fine-grit
abrasive paper to remove any lingering traces of mould release agent. Carefully re-
move all sanding dust. Aim at reducing the glossy surface to a matt finish, otherwise
there is no chance of a durable glued joint between the fuselage and other parts.
When using adhesives it is important to observe the instructions supplied by the glue
manufacturer. The main Graupner FS catalogue includes many other types of ad-
hesive.
When you are using solvent-based adhesives be sure to provide good ventilation in
your workroom.
Read the manufacturer’s instructions.

GRAUPNER GmbH & Co. KG D-73230 KIRCHHEIM/TECK GERMANY
Modifications reserved. No liability for printing errors. Ident. # 0062067 4/2010
4
Radio control system
We particularly recommend computer radio control systems ranging from the mc-19
to the mc-24
or
Recommended servos:
Rudder DES 657 BB MG Order No. 7923 1 reqd.
Elevator DES 587 BB MG Order No. 7932 1 reqd.
Ailerons DS 3068 Order No. 5188 2 reqd.
Camber-changing flaps DS 3068 Order No. 5188 2 reqd.
Airbrakes C 351 Order No. 5123.lose 2 reqd.
Aero-tow mechanism DS 8077 Order No. 5149 1 reqd.
Retractable wheel C 713 Order No. 3887 1 reqd.
Select a suitable receiver on the 35 MHz or 2.4 GHz band to suit your system.

GRAUPNER GmbH & Co. KG D-73230 KIRCHHEIM/TECK GERMANY
Modifications reserved. No liability for printing errors. Ident. # 0062067 4/2010
5
Order No. 4135 PRX 3A stabilised receiver power supply 1 reqd.
Servo extension leads required
Order No. 3935.50 for permanent connection to receiver 6 reqd.
Order No. 3935.105 for elevator 1 reqd.
Order No. 3935.105 for ailerons 2 reqd.
Order No. 3935.32 for airbrakes 2 reqd.
Order No. 3935.32 for camber-changing flaps 2 reqd.
Order No. 98516.1 folding ferrite ring for aileron,
flap and airbrake servos 2 reqd.
Order No. 1587 Velcro (hook-and-loop) tape 1 pack
We recommend a receiver battery of at least 3 Ah capacity, which should be properly
prepared before use and maintained during its life, i.e. the pack must be charged and
discharged (cycled) several times before it reaches its full stated capacity.
We deliberately recommend the use of rechargeable batteries for the receiver and
transmitter, as they offer the widest margin of safety in use.
Please see the main GRAUPNER FS catalogue for details of suitable chargers.
Use foam rubber to pack round the receiver.
Assembling the ASW 28
Please don’t start work on the model until you have read through the instructions and
have a clear understanding of the purpose of the various components and the in-
dividual stages of construction. If you are not satisfied with the quality of any part,
take it back to your model shop for replacement before modifying it in any way.
These instructions describe the construction of the model including the installation of
the retractable motor, Order No. 6097. If you do not intend to fit a power system, i.e.
you prefer to build the model as a pure glider, you should simply ignore these stages.
The fuselage
Thoroughly sand all the joint areas inside the fuselage until they have a matt ap-
pearance (see the note following the Adhesives table).
Before you start construction you have to decide whether to install a retractable
wheel or not. If you are fitting a retractable motor, a retractable wheel is essential.
If you intend to complete the ASW 28 as a pure glider, cut the wheel doors out of the
fuselage using a fine-blade piercing saw; the outline of the opening is marked on the
underside of the fuselage.
However, if the model is to be fitted with a retractable motor, the wheel doors need to
be moved forward by about 60 mm, and should be about 110 mm long overall.
Before cutting out the wheel doors, drill four 1 mm Ø holes on the marked transverse
lines at both ends, spaced about 22 mm from the fuselage centreline. Fit short steel
pins through these holes, projecting on the inside, and place the aluminium tubes

GRAUPNER GmbH & Co. KG D-73230 KIRCHHEIM/TECK GERMANY
Modifications reserved. No liability for printing errors. Ident. # 0062067 4/2010
6
(the wheel door pivot bushes) against them, so that the distance between the tubes
is around 22 mm.
Position the aluminium tubes against the pins on the inside of the fuselage, projecting
by about 15 mm front and rear, and tack them to the floor of the fuselage with a few
drops of cyano. The steel pins can now be withdrawn, and the aluminium tubes fixed
permanently to the fuselage using EPOXY resin and glass cloth. When the resin has
cured, the wheel doors can be sawn out as shown in the photo below.
Lightly sand the edges of the wheel doors. The doors are attached to the fuselage by
means of two 1.5 mm Ø steel rods which are slipped through the aluminium tubes
from the front. Check that the wheel doors open and close smoothly; you may need
to sand back the edges slightly to avoid them fouling the opening.
At this stage the two formers which support the retractable wheel unit can be glued
into the fuselage. Use the outer former shape if you are installing a retractable motor;
the inner former shape is for the glider version. Carefully remove the formers from the
plywood sheets and fit them onto the support lugs of the retract unit at front and rear.
Place this assembly in the fuselage, and align it with the opening in the underside.
With the wheel up, check that the retract unit is central in the fuselage opening. It is
also essential to check that the wheel can extend and retract without fouling the rear
edge of the fuselage opening. When you are confident that all is well, tack the two
formers in the fuselage using a few drops of cyano. Check the system once more,
then glue both formers in the fuselage permanently using epoxy resin and glass
cloth.

GRAUPNER GmbH & Co. KG D-73230 KIRCHHEIM/TECK GERMANY
Modifications reserved. No liability for printing errors. Ident. # 0062067 4/2010
7
To ensure that the two wheel doors close flush with the outside of the fuselage, glue
a small piece of plywood to the inside of the fuselage front and rear, as shown in the
photo above.
Check that the wheel doors still open and close smoothly.
Take care not to glue the wheel doors to the fuselage.
When the glue has set hard, the wheel door closing springs can be installed:
Bend two torsion springs to the shape shown in the photo: one right and one left
(handed pair).
The torsion springs should be about 15 mm shorter than the wheel doors, and the
short ends should be around 15 mm long. Both ends of the torsion springs are fitted
in pieces of plastic tube which are glued to the wheel doors and fuselage as shown.
Do not glue the springs in the plastic sleeves, as you may need to replace them and /
or the wheel doors at some time.
Install the torsion springs as shown in the photo below. Once again, take great care
to avoid gluing the wheel doors to the fuselage accidentally.

GRAUPNER GmbH & Co. KG D-73230 KIRCHHEIM/TECK GERMANY
Modifications reserved. No liability for printing errors. Ident. # 0062067 4/2010
8
The next step is to mount the rudder servo and the retract servo on the retract unit,
as shown in the photos below.
The retract pushrod is assembled and installed as shown in the photo.
Adjust the retract linkage so that the wheel locks reliably in the extended and retrac-
ted states.
Now place the undercarriage unit in the slots in the rear former, and secure it by
screwing the plywood plate in place at the front.

GRAUPNER GmbH & Co. KG D-73230 KIRCHHEIM/TECK GERMANY
Modifications reserved. No liability for printing errors. Ident. # 0062067 4/2010
9
The next step is to install the rudder linkage: the rudder has first to be fitted to the fin
in order to mark the correct position of the horn. Fit the rudder onto the hinge lugs
and slip the 2 mm Ø steel pivot rod into place from the underside. Check that the rud-
der moves freely to both sides of centre. Mark the position of the hole for the rudder
horn as shown in the photo, centred on the pushrod shrouds.
The exact position of the hole through the rudder is dictated by the horn lugs: the
linkage point of the horn lugs must line up exactly with the rudder hinge axis, so the
through-hole in the rudder must be positioned further aft to take this into account.
Cut a piece about 45 mm long from the length of M3 studding (threaded rod) included
in the kit. Push the studding through the hole and screw a horn lug on each end.
Attach the two pull-cables to the horn lugs as shown in the photo. After crimping the
sleeves, solder the joints for additional security.

GRAUPNER GmbH & Co. KG D-73230 KIRCHHEIM/TECK GERMANY
Modifications reserved. No liability for printing errors. Ident. # 0062067 4/2010
10
Now thread the two pull-cables forward into the fuselage, so that they can be con-
nected to the double-ended servo output arm using ring-screws, nuts and clevises.
Connect an extension lead, Order No. 3935.180, to the elevator servo lead, and fit a
heat-shrink sleeve round the connector to prevent it working loose.
Thread the extension lead through the fin and allow it to fall forward into the fuselage
nose. The elevator servo can now be mounted in the plate inside the top of the fin,
using the screws supplied in the servo accessory pack.

GRAUPNER GmbH & Co. KG D-73230 KIRCHHEIM/TECK GERMANY
Modifications reserved. No liability for printing errors. Ident. # 0062067 4/2010
11
Assemble the elevator pushrod from the threaded pushrod, nut and clevis, as shown
in the photo below. Bend the plain end of the rod at right-angles as shown.
An opening now has to be cut in the trailing edge of the fin to accommodate the ele-
vator pushrod. Drill and file it to shape as shown in the photo below. Note that the
pushrod should rest lightly against the inside of the fin, as this eliminates the pos-
sibility of the pushrod slipping out of the elevator horn.
Drill and file out a slot in the elevator for the horn, referring to the dimensions in the
photo below. The slot should extend as far as the top skin of the elevator, but not
pass right through it.

GRAUPNER GmbH & Co. KG D-73230 KIRCHHEIM/TECK GERMANY
Modifications reserved. No liability for printing errors. Ident. # 0062067 4/2010
12
Glue the horn in the slot in the elevator using EPOXY. Leave the resin to cure for at
least 24 hours.
The tailplane is mounted on the fin using the two socket-head cap screws supplied in
the kit. At the same time slip the elevator pushrod through the hole in the horn.
If you intend to fly the ASW 28 as a pure glider, all you need to do is paint the tail-
wheel fairing black. If you are fitting a retractable power unit, a tailwheel needs to be
installed.
If you are fitting a tailwheel, drill a 2 mm Ø hole in both sides of the fairing, positioned
as stated in the photo below.
The tailwheel is installed using a steel rod axle cut to the correct length, with a collet
on either side to centre the wheel. File one face of each collet at an angle, as shown
in the photo below.
Slip the steel axle through the hole in one side of the fairing, fit a collet on it, then the
wheel and finally the second collet, before pushing it through the opposite hole. Note
that the angled face of the collets must face the outside. The steel axle should project
on either side by about 1 - 1.5 mm. Apply a drop of UHU thread-lock fluid to the grub-
screws before tightening them.

GRAUPNER GmbH & Co. KG D-73230 KIRCHHEIM/TECK GERMANY
Modifications reserved. No liability for printing errors. Ident. # 0062067 4/2010
13
The canopy
Whether you are building the ASW 28 with or without a retractable motor, you need
to drill a 10 mm Ø hole in the point of the fuselage nose.
The hole is required for gluing the front canopy locating peg to the fuselage.
Glue is applied to the correct point in the fuselage through this hole in order to fix the
front locating peg in place.
Drill a 2 mm Ø hole in the front of the fuselage canopy flange, as shown in the photo.
Place the canopy in its recess, and check that it is a snug fit all round. Now slip a
length of 2 mm Ø steel rod through the front 10 mm Ø hole in order to mark the posi-
tion of the hole on the canopy frame. Remove the canopy and bore a 2 mm Ø hole in
the frame at the marked point, drilling to a depth of about 4 mm. Slip a length of 2
mm Ø steel rod through the 10 mm Ø hole in the fuselage nose and through the hole
in the fuselage flange, so that it engages in the 4 mm deep hole in the canopy frame.
Tape the canopy to the fuselage in this position, so that it cannot shift on the fuse-
lage. Working through the hole in the nose, apply glue to the steel rod where it meets
the fuselage; this is best accomplished using a syringe with a length of aluminium
tube as an extension. Allow the glue to set hard, then remove the canopy from the
fuselage once more. The next step is to install the canopy latch, but the method dif-
fers according to the version of the model you are building: glider or powered version.
For the glider version drill a 3 mm Ø hole below the wing root fair-ing on one side,
and another in the rear canopy flange, as shown in the photo. Fit a 3.2 mm Ø plastic
sleeve through these two holes, projecting at the front by at least 5 mm. The plastic
sleeve can now be glued to the inside of the fuselage. When the glue has set hard,
trim the sleeve off flush with the fuselage.

GRAUPNER GmbH & Co. KG D-73230 KIRCHHEIM/TECK GERMANY
Modifications reserved. No liability for printing errors. Ident. # 0062067 4/2010
14
Now place the canopy on the fuselage
again, with the front locating peg engaged
in the hole, and resting snugly on the fuse-
lage flange at the rear. Slip a length of 0.8
mm Ø steel rod into the thin plastic sleeve,
slide this into the fixed sleeve, working
from the hole under the wing root fairing,
and push it against the rear of the canopy
frame to make a mark. Remove the canopy
from the fuselage once more, and drill the
hole for the latch to a depth of about 5 mm.
If you now place the canopy on the fuse-
lage, you can push the wire / plastic sleeve latch into the rear hole to secure it. Be
sure to push the latch into the canopy frame as far as it will go. The latch now needs
a “handle”, so that it can be withdrawn easily: bend the end at right-angles just aft of
the rear opening, and snip off excess length, leaving the bent end about 5 mm long.
If your model is to be fitted with a retractable motor, the canopy latch must be in-
stalled in such a way that it can be operated through the opening for the motor. This
is accomplished by bending and cutting the latch pin to the appropriate shape, and
sliding it into a guide sleeve which is glued in the fuselage. This alternative form of
latch pin must also engage in the canopy frame to a depth of around 5 mm.
If you have installed a retractable wheel, you will need to shorten the front end of the
seat shell to provide clearance. Fix the seat shell to the canopy frame using a pair of
pan-head self-tapping screws.
If you wish, you can fit a full-length quarter-scale pilot (not included in the kit) in the
cockpit to improve the model’s scale appearance.
Installing the retractable power system
Please refer to the instructions provided with the retractable motor unit.
You will need to cut or saw out a rectangular opening in the top of the fuselage.

GRAUPNER GmbH & Co. KG D-73230 KIRCHHEIM/TECK GERMANY
Modifications reserved. No liability for printing errors. Ident. # 0062067 4/2010
15
Saw out the panel, referring to the dimensions in the photo above, then clean up the
edges and cut it exactly in half lengthways to form two doors. The motor unit is in-
stalled in the fuselage using a pair of aluminium brackets which are screwed to two
half-formers; this procedure is also described in the motor unit instructions.
The first step is to attach the two aluminium brackets and the half-formers to the mo-
tor unit inside the fuselage. Position the motor assembly accurately, and tack the two
half-formers to the fuselage. The additional support for the motor unit is screwed to
the rear retract unit former. When the motor is retracted, the two doors are closed
again by means of two torsion springs. End-stops for the doors have to be glued to
the inside of the fuselage at both ends of the motor opening, as already described for
the retractable wheel.
The wings
Work on the wing panels is limited to installing the servos and the control surface
horns. Heat-shrink sleeves should be shrunk round the servos before they are glued
in the wings. Thoroughly roughen (sand) the gluing surface of the servos and the in-
side of the wing panels to ensure that the glue adheres well. The position of the ai-
leron horns is shown in the photo: they should line up with the pushrod fairings. Mark
the position of the horn slots on the ailerons in line with the centre of the pushrod fair-
ings, and cut the slots out accurately. Note that the horn linkage point should line up
exactly with the aileron hinge pivot axis.

GRAUPNER GmbH & Co. KG D-73230 KIRCHHEIM/TECK GERMANY
Modifications reserved. No liability for printing errors. Ident. # 0062067 4/2010
16
Glue the horns in the ailerons and allow the epoxy to set hard. The aileron servos
can now be glued in the servo wells. Ensure that the servo output arms line up ac-
curately with the aileron horns; this can be checked by connecting the pushrods. The
rods need to be bent slightly in order to obtain sufficient up-aileron travel; this is
shown in the photo below.
Each pushrod consists of a length of M2.5 studding (threaded rod), two M2.5 nuts
and two M2.5 clevises.
The airbrake servos and camber-changing flaps are glued into the wing as shown in
the photos below. When fitting the airbrake servos, ensure that they line up with the
actuating levers of the airbrake units. We recommend connecting the pushrod to the
hole in the actuating arm using a simple double bend (Z-bend).
Mount the swivel pushrod connector on the servo output arm using a lever length of
11 mm, as shown in the photo. Fit the pushrod through the cross-hole in the connec-
tor barrel in order to determine the exact position of the servo. Apply glue to the
servo, position it carefully, then weight it down lightly to prevent it shifting while the
glue hardens.

GRAUPNER GmbH & Co. KG D-73230 KIRCHHEIM/TECK GERMANY
Modifications reserved. No liability for printing errors. Ident. # 0062067 4/2010
17
When the epoxy has cured, mark the position of the horns on the camber-changing
flaps: place the servo in the opening in the wing, as shown in the photo below. Posi-
tion the horn in such a way that the flap pushrod forms a right-angle with the leading
edge of the control surface.
Drill a 4 mm Ø hole in each camber-changing flap at the appropriate point for the
aluminium flap horn. Take care not to drill right through the control surface; remem-
ber that the flap is quite thin at this point.
You will need to relieve the sealing lip of the camber-changing flap slightly to allow
the clevis to be connected, as shown in the photo.
Allow the epoxy to set hard, then glue the two incidence pegs in the wing roots. They
should project about 10 mm out of the wing root ribs, as shown in the photo below.
The final work on the two wing panels is to install the wing retainer system. Apply
glue to the wing retainer plugs before screwing them into the holes in the wing roots
as far as they will go. Screw the two aluminium threaded sleeves onto the studding,
and adjust the length so that the wings are held securely against the fuselage, with
no gaps at the root fairings, but without distorting the moulding. The approximate
length of the retainer system is about 158 mm.

GRAUPNER GmbH & Co. KG D-73230 KIRCHHEIM/TECK GERMANY
Modifications reserved. No liability for printing errors. Ident. # 0062067 4/2010
18
Assemble the model, fine-tune the length of the retainer unit as accurately as pos-
sible, then apply UHU thread-lock fluid to the threads to secure the system.
One option for connecting the wing-mounted servos to the receiver when assem-
bling the model is to solder the servo leads to a single G 6 plug; see photo.
In this case the positive wires from each servo lead are bundled together and sol-
dered to one outer contact of the plug or socket. Repeat the procedure with all the
negative wires and a second contact. The individual signal wires are then soldered to
the remaining vacant contacts.
If you don’t enjoy soldering, simply connect the extension leads individually when you
assemble the model.
The wings are completed by plugging the winglets into the tips of the wings using the
GRP tongues supplied. The winglets must be taped in place before the model is
flown. Push the GRP tongue into the winglet first, and then into the socket in the wing
tip.

GRAUPNER GmbH & Co. KG D-73230 KIRCHHEIM/TECK GERMANY
Modifications reserved. No liability for printing errors. Ident. # 0062067 4/2010
19
Install the ON / OFF switch and the batteries on the RC installation plate, as shown in
the photo below.
The picture shows the radio installation of the powered version of the model. If you
have built the glider version, naturally the battery for the drive motor and the retract /
extend motor is not required.
Assembling the ASW 28
Plug the wing panels into the fuselage using the wing joiner rod, engaging the in-
cidence pegs in the holes in the wing root fairings at the same time. Connect the ai-
leron, airbrake and flap servo leads to the short extension leads which are per-
manently plugged into the receiver.
Fit the angled end of the elevator pushrod in the hole in the elevator horn, then attach
the tailplane to the fin using the two M4 socket-head cap screws supplied. Tighten
the screws just to the point where the tailplane rests squarely on the saddle, with no
movement - don’t overtighten them! Engage the wing retainer system to clamp the
wings against the fuselage. Insert the front canopy locating peg, then push the latch
pin forward to hold the canopy on the fuselage.
Balancing the ASW 28
Assemble the model completely, ready to fly, and support it at a point about 80 mm
aft of the wing root leading edge on both sides of the fuselage. The model should
now balance level, ideally with the nose inclined slightly down. Adjust the position of
the batteries to achieve the correct CG. If lead ballast is required, fix it securely, so
that it cannot possibly shift. Check that all the control surfaces are exactly at centre
(neutral position) when the transmitter sticks and trims are at centre.
Control surface travels:
Ailerons 23 mm up, 10 mm down
Elevator 13 mm up, 8 mm down
Rudder 40 mm right and left
Camber-changing flaps 2 mm up
Camber-changing flaps 3 mm down
Aileron - flap mixer 10 mm up, 6 mm down
For an even more pronounced braking effect the ailerons and camber-changing flaps
can be set up to deflect in what is known as the “butterfly” or “crow” configuration:
Ailerons 15 mm up

GRAUPNER GmbH & Co. KG D-73230 KIRCHHEIM/TECK GERMANY
Modifications reserved. No liability for printing errors. Ident. # 0062067 4/2010
20
Camber-changing flaps 10 mm down
During out test-flights with the ASW 28 using the retractable power system, we found
that it was advisable to mix in 3 mm of up-elevator and 3 mm of down-flap when
power was applied for take-off and climb.
The stated control surface travels are only a recommendation, and you will probably
want to adjust them to suit your personal flying style.
Important:
When installing and setting up the control surface linkages it is vital to ensure that
they work smoothly, are able to carry out their full movement - including trim travel -
without being impeded, and are not mechanically obstructed at any point.
When you move the rudder stick to the right, the rudder should also deflect to the
right (left stick: left rudder). If you pull the elevator stick back towards you, the eleva-
tor should deflect up (stick forward: elevator down).
Move the aileron stick to the right, and the right-hand aileron should deflect up, the
left-hand aileron down. The airbrakes should extend out of the wings when the throt-
tle stick (ratchet action) is moved back towards you, and close at the opposite end-
point.
For “thermal” and “speed” flying we recommend that you assign the wing flap settings
to a three-position toggle switch: “switch forward” equates to “speed”, “switch centre”
means “normal flying”, while “switch back” selects the “thermal” setting.
Do not extend the airbrakes too far too quickly, as they are extremely effective. For a
normal landing approach they only need to be extended by around 5 mm.
Now all that remains is for all of us to wish you many hours of pleasure flying your
new ASW 28.
Yours - the team !
Be sure to read right through the instructions covering assembly and operation
of your model before you attempt to operate it for the first time. You alone are
responsible for the safe operation of your radio-controlled model. Young peo-
ple should only be permitted to build and fly this model under the instruction
and supervision of an adult who is aware of the hazards involved in this activ-
ity.
If you have questions regarding the safe operation of your RC model aircraft,
please turn to your local model shop in the first instance, as the staff will be
pleased to help you.
Radio-controlled model aircraft are very demanding and potentially dangerous
machines, and call for a high level of technical knowledge and skill from the
operator, together with a responsible attitude.
In legal terms our models are classed as aircraft, and as such are subject to
statutory regulations and restrictions which must be observed. Our brochure
“Modellflugrecht, Paragrafen und mehr” (Model Aviation Law, Legal Require-
Table of contents
Other GRAUPNER Tools manuals
Popular Tools manuals by other brands
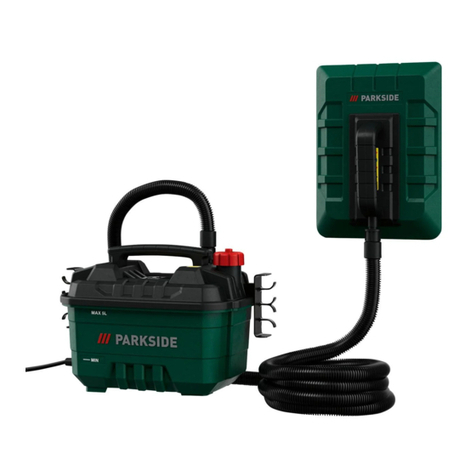
Parkside
Parkside PDTA 5 A1 Translation of the original instructions

Rapid
Rapid ESN114 instructions
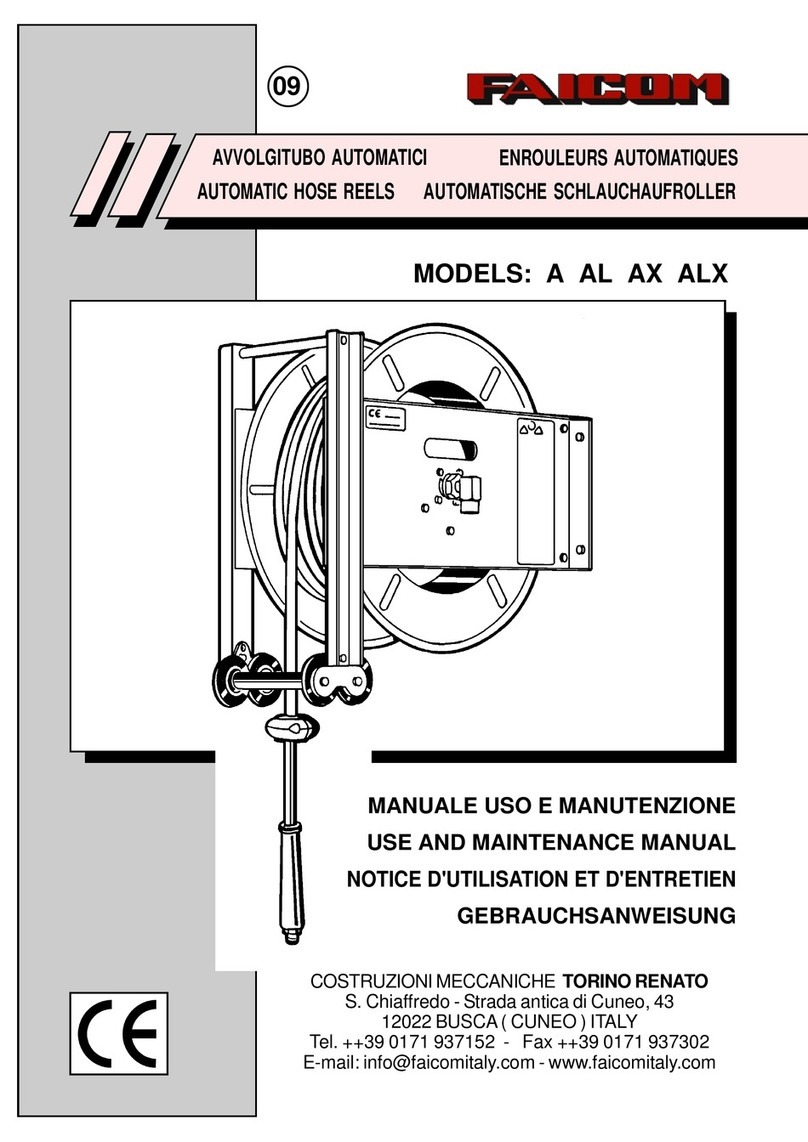
Faicom
Faicom A Series Use and maintenance manual
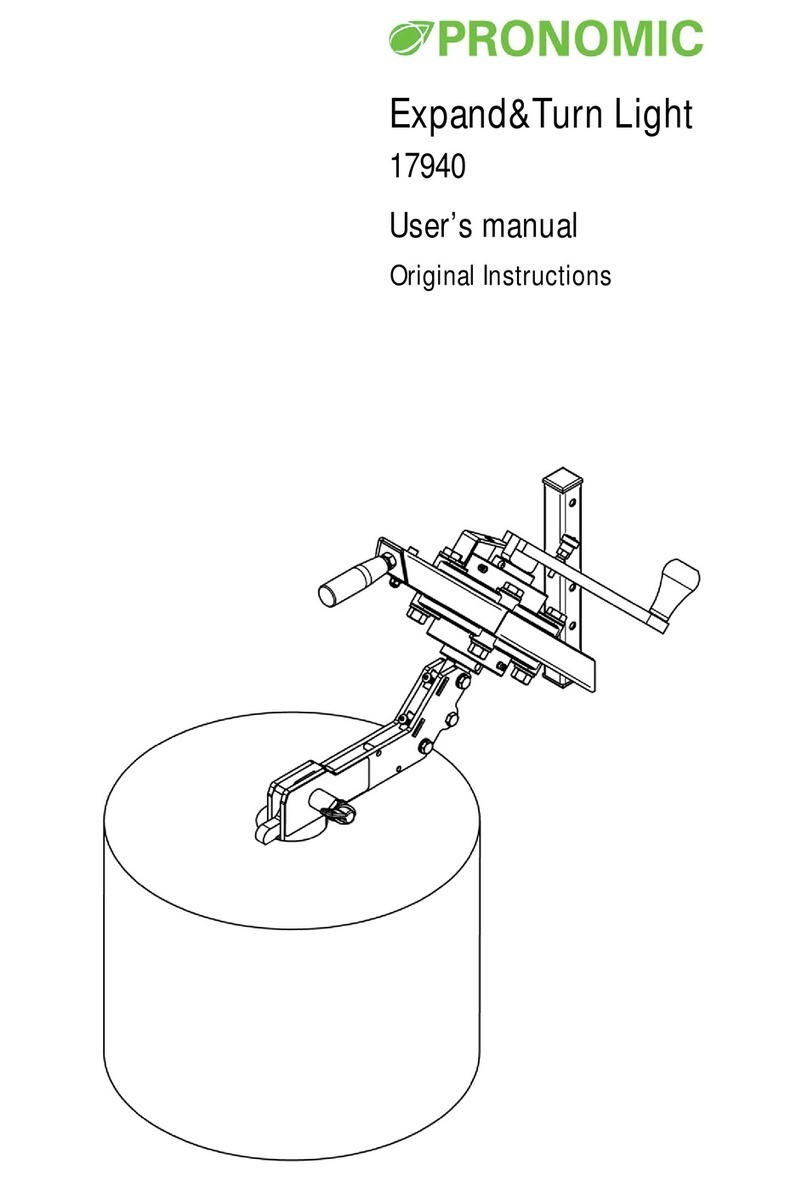
Pronomic
Pronomic Expand&Turn Light user manual

Parkside
Parkside PDST 10 B3 Translation of the original instructions
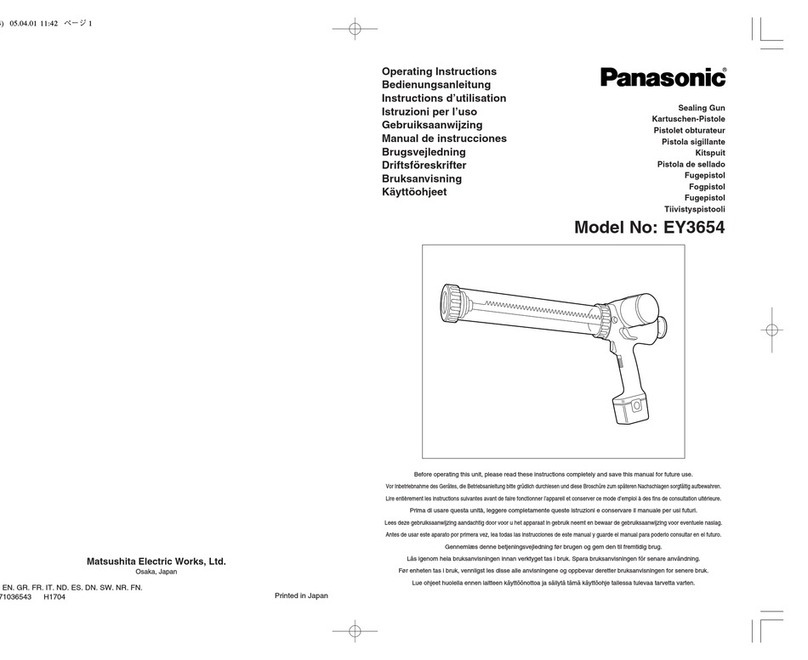
Panasonic
Panasonic EY3654 - 7.2V CAULKING GUN operating instructions