GROCO SSA-3 Series User manual

For service assistance/information call 410.712.4242 and ask for Strainers Service Department. After hours go to www.groco.net.
InstallationandOperatingInstructionsfor
GROCOSSA-3andSSA-4Series(TOUCHPADVERSION)
US Patent No. 7491320
InfoSheetSSA-3and 4Series, 1of5
110816
1999 GROSS MECHANICAL LABORATORIES, INC. ALL RIGHTS RESERVED.
The Concept: GROCO®SSA-4 continuously
monitors raw water flow to as many as four devices
(engines, generators, air conditioners, refrigeration,
R/O systems, pumps, etc). Through calibration the
patented process considers unique individual
plumbing and flow parameters, and learns “normal”
flow for each connected device. Audible and visual
alerts are provided within 7 seconds of a dangerous
reduction of raw water flow to any of the devices.
Components: An SSA system includes these components
(Refer to Figure-1):
*Processor
*Flow sensors, sized for each plumbing system
*Flow signal cables (blue)
*Power cable (red)
*Touchpad
*JPCB enclosure and helm data cable (black)
*"On" Signal cables:
Switched AC (yellow)
Switched DC (green)
Engine Speed (orange)
Processor
Signal Cable
Flow Sensor
JPCB
Touchpad
Ribbon

For service assistance/information call 410.712.4242 and ask for Strainers Service Department. After hours go to www.groco.net.
InstallationandOperatingInstructionsfor
GROCOSSA-3andSSA-4Series(TOUCHPADVERSION)
US Patent No. 7491320
InfoSheet SSA-3and 4Series, 2of5
110816
Processor Installation: Install the Processor in the engine room
above the highest bilge water level. The enclosure is water resistant,
but is not water tight; water damage to the processor is not covered
by the warranty. Secure the Processor to a smooth and flat surface
with the hook & loop tape provided. Optionally, the Processor can
be mounted with #8 screws through the four corner holes in the
enclosure, accessible with cover removed. Install the Processor
with the fuse holder and power connections facing up.
The Processor enclosure is labeled to identify correct cable connec-
tions, and some locations may not be used. Protect unused
locations with the dust caps provided.
Flow Sensors Installation: Bronze flow sensor housings should be
installed with their pull-ring facing down.
Each sensor is sized to fit the hose ID of the connected plumbing
system. Insert the bronze barbs fully into the hose and double-
clamp each side. For best results install the housing with at least
12” (more of possible) of straight plumbing before and after the sen-
sor to assure maximum “quiet” water. Paddlewheel assemblies are
interchangeable. Install the paddlewheel assembly into the bronze
housing so its directional arrow (on top opposite the cable exit)
points in the direction of flow.
Cables: Two cable connections to the Processor are required from
each device (flow and "on"). Cables are color-coded and their
connector pins allow connection to any same-color connector on the
Processor. There are multiple same-color bulkhead connectors on
the enclosure, so be sure to connect each cable to the Processor
location that matches the device you are connecting. Refer to Fig. 2
schematic. Verify color match and align the index pin before
pushing the connector halves together - do not force. Screw the
cable nut onto the bulkhead connector 1/4 turn until it locks into
place. Excess cable length may be coiled or may be removed from
the end without the connector. Before cutting off excess cable
length, verify adequate length for routing and securing cables.
Note: Connecting a blue GEN flow cable to the AIRCON flow location
will not cause damage, but will result in calibration errors, improper
system operation and the incorrect display of alerts.
Labels are provided to mark each “on” signal cable to identify the
device (Gen, Aircon, etc.) to which it is connected. Apply the
identification label to the cable at the end that connects to the
Processor.
Flow Signal Cables: See Figure-2 and connect to Processor Jack 1
through 4. Flow signal cables are marked BLUE. Connect one end
to the flow sensor and run the cable to the Processor. Extension
flow cables are available in 30-ft lengths (#11-1028-30).
“On” Signal Cables: There are three types of “on” signals:
Switched DC, Switched AC, and Engine. The signal type is
determined by the device you are connecting.
CONNECTING 'ON' SIGNAL CABLES FROM
GENERATORS AND CIRCULATOR PUMPS
See Figure-2 and connect to Processor Jack 10 or 11. Generators
and circulator pumps are constant speed devices that provide a
switched DC “on” signal. Cables are marked GREEN.
A generator “on” signal comes from a normally open switched
source such as a fuel pump or oil pressure sender – the switch
closes when the generator is operating, notifying the Processor that
the generator is "on".
A DC powered circulator pump “on” signal comes from the pump’s
power switch or breaker. The Processor detects that the device is
operating when the normally open switch becomes closed.
CONNECTING 'ON' SIGNAL CABLES FROM AIR CONDITIONERS,
R/O SYSTEMS, OR REFRIGERATION SYSTEMS
See Figure-2 and connect to Processor Jack 8 or 9. Air
Conditioners, refrigeration pumps, and R/O systems are constant
speed devices that provide a switched AC signal; their cables are
marked YELLOW. The Processor detects that the device is
operating when its control circuit turns the pump motor on. DO
NOT obtain the Air Conditioner “on” signal from the circuit breaker
that provides power to the device - False Alerts will result. Consult
system manufacturer's schematics.
CONNECTING 'ON' SIGNAL CABLES FROM ENGINES
For engines the “on” signal is a tachometer input that provides
engine speed data to the Processor.
Engine Speed Signals for SSA models with suffix “1”:
A tachometer signal is obtained directly from a helm-mounted
tachometer. Make the connection with yellow (port) and violet
(starboard) wires provided. Run wires from the tachometer (+)
terminal through the compression fitting on JPCB, and to J2
locations 7 and 8 (see Figure-2).
Engine Speed Signals for SSA models with suffix “2”:
See Figure-2 and connect the orange cable to Processor Jack 12 or
13 (use Jack 12 only if there is a 2nd engine). A tach signal is
obtained from the tach signal generator on each engine. Cut off the
3-pin Deutsch™ connector and connect black and blue wires to the
tach signal generator. Connection points are polarity sensitive -
improper tach operation may result if polarity is incorrect.
Engine Speed Signals for SSA models with suffix “3”:
See Figure-2 and connect the orange cable to Processor Jack 12 or
13 (use Jack 12 only if there is a 2nd engine). A tach signal is
obtained from a J1939 connection. Tach signal cables are
terminated with a 3-pin Deutsch™ connector. Consult the engine
electrical schematic to identify the J1939 connector, usually a large
70-pin (approximately) connector that terminates at the Engine
Control Unit (ECU) for each engine. On each ECU there is commonly
an unused jack (marked CAN hi and CAN low) to which the tach
signal cable can be connected. If this connection requires a 2-pin,
4-pin or 6-pin connector, an adaptor may be ordered from GROCO:
3-pin to 2-pin = 11-1033-02
3-pin to 4-pin = 11-1033-04
3-pin to 6-pin = 11-1033-06
Touchpad Installation: When choosing a location for the touchpad,
consider the following:
*The touchpad is water resistant, but not waterproof. Choose a
location that is protected against direct exposure to water.
*LED’s on the touchpad will be more visible if installation is not in
direct sunlight.
*The vessel operator will need access to the touchpad for
calibration and to acknowledge an alert.
*12” ribbon extensions are available (#11-0023-12).
*The touchpad should be located at the helm station that is most
often used during vessel operation.
First, determine how you will route the touchpad ribbon. Trial-fit the
touchpad before peeling off the adhesive backing. Then, peel off
half the backing paper, insert the ribbon through the slot (1/4" X
1-1/4"), align the touchpad carefully and press lightly against the
chosen surface. Last, peel off the other half of the backing paper
and press the touchpad firmly into place.

For service assistance/information call 410.712.4242 and ask for Strainers Service Department. After hours go to www.groco.net.
InstallationandOperatingInstructionsfor
GROCOSSA-3andSSA-4Series(TOUCHPADVERSION)
US Patent No. 7491320
InfoSheet SSA-3and 4Series, 3of5
110816
CAUTION: Be careful not to crease or pinch the ribbon.
CAUTION: Carefully align the male tab on the ribbon with the
female slot on the pcb. You will hear a “click” when the two are
properly connected.
JPCB Enclosure Installation:
JPCB is the black box with the
touchpad and 50-foot cable
attached. Connections are
made at the factory for system
testing and do not have to be
broken if you can run the
large connector at the end of
the cable to the Processor
(1-1/4” hole required).
If you cannot route the large connector to the Processor you must
route the cable from the processor to JPCB. Open JPCB enclosure
and cut all wires about 1/2” from the terminal block leaving the
wires connected and the colors visible. This will aid with
re-connection of the wires. Connect the large connector to the
Processor, and run the cable to JPCB. Figure-2 Schematic shows
proper wire connections.
The touchpad communciates with and/is connected to JPCB
through a flat ribbon. If you open JPCB enclosure to complete the
installation you may have to disconnect the ribbon from the circuit
board. Press the ribbon release from the black connector at the
end of the ribbon and gently pull the connector (do not pull the
ribbon). When reassembling, gently push the connector halves
together until they lock - you will hear a click.
CAUTION: The pins inside the connector halves are delicate and
can easily be bent.
When replacing JPCB enclosure cover, place the ribbon in the
notch between top and bottom enclosure halves. Use the hook
& loop tape provided to attach JPCB to a flat smooth surface
behind the instrument panel.
If you want to display SSA information at more than one location,
order an additional station kit for each location. The suffix number
defines the touchpad.
JPCB-31
JPCB-41
Power Connection: See Figure 2 and connect DC power to
Processor Jack 7. SSA will operate with any input voltage from
12VDC to 32VDC. The Processor is protected by the 2-amp fuse
on the enclosure. The cable marked red is for DC power.
Connect the wire end (red +, black -) to the DC Main buss to
assure uninterrupted DC power. When power is applied the
processor will conduct a self-test, and the touchpad will rapidly
cycle three times through its LEDs. When all "on" signal cables
and flow signal cables are connected you are ready to calibrate.
Operation
Definitions:
* Grace Period – The first 30-seconds of operation of any
connected device is considered the “Grace Period” during which
pumps prime, purge air, and achieve stabilized flow.
* Horn – In the context of these instructions the term “horn” is
used to mean the high-pitch audible alarm mounted on the
JPCB enclosure. We are not referring to the vessel’s main horn.
* Alert – During operation (not during calibration or the grace
period) a flashing LED and simultaneous horn
* Alert Acknowledge – When an alert is indicated, pressing the
acknowledge (red bell) button will silence the horn; the LED
status will change from flashing to steady.
* Alert Clear – After an alert occurs, if flow returns to “normal”
the alert LED will clear.
* Auto-clear – An alert that clears itself (ie: a plastic bag covers
the air conditioner inlet, and then floats away). Audible and
visual alerts will be displayed, and will automatically cease 5
seconds after the flow restriction clears.
Notes:
*SSA will continuously monitor flow rate to connected and
calibrated devices and alert you visually and audibly if flow to
any device is significantly reduced.
*Under normal operating conditions, no alerts will be displayed
*Each 60-seconds a brief LED flash will occur for each device that
is running.
*SSA will "self-clear" (audible and visual alerts will turn off) if a
temporary flow reduction occurs, and then clears itself.
*During the Grace Period, or until stable flow is achieved, the
display of a solid LED is normal.
Sensitivity Adjustments:
Near the center of the Processor PCB is a set of dipswitches.
Switches 1 and 2 adjust system sensitivity. Factory settings
provide mid-range sensitivity to flow reduction. We suggest that
you operate with the factory setting for a period of time before
making sensitivity adjustments. Switch settings may be changed
to increase or decrease tolerance.
*Switch-3 is factory-set to “off”. DO NOT alter Switch-3.
*Switch-4 is factory-set to “off”. DO NOT alter Switch-4.
Switch-1 Switch-2 Restriction Tolerance
OFF OFF Low (alert will trigger sooner)
OFF ON Mid-range (factory setting)
ON OFF High
ON ON Very high (not recommended)
The photo shows one possible installation where the touchpad
ribbon runs through an existing hole behind the autopilot control.
Touchpad
Autopilot
control
on your boat

For service assistance/information call 410.712.4242 and ask for Strainers Service Department. After hours go to www.groco.net.
InstallationandOperatingInstructionsfor
GROCOSSA-3andSSA-4Series(TOUCHPADVERSION)
US Patent No. 7491320
InfoSheet SSA-3and 4Series, 4of5
110816
Calibration Overview: Calibration teaches the Processor the
unique plumbing and flow characteristics of each connected
device, and enables SSA to distinguish between normal and
below normal flow over the full range of operating conditions.
Air conditioners, generators, circulator pumps, refrigeration
pumps, and R/O systems operate at a constant speed, so one
calibration flow rate is required. Propulsion engines operate at
variable speed, determined by throttle setting, so calibration is
required at multiple throttle settings.
Calibration takes place at the helm (or at any location if multiple
stations are installed) and can be conducted by one person, but
we suggest calibrating with two persons - one to operate the
vessel and one to perform the calibration.
The touchpad has two buttons – an “acknowledge” (bell) button
and a hidden button located next to the bell button. Lightly
pass your finger over the hidden button location to detect a
slight bump. Both buttons will be used during calibration.
You may calibrate constant speed devices (generators, air
conditioners and pumps) while at berth, but engines must be
calibrated in open water where full throttle operation is safe.
Calibration notes:
*Before calibrating any device check these maintenance items
that will affect flow rate:
-The raw water strainer filter basket is clean
-Pumps impellers have no broken or missing blades
-The seacock is fully open and clear
-Plumbing connections are tight and free of leaks
-There are no hose kinks
*Calibration mode will automatically end if no buttons are
pressed for five minutes. You will not lose calibrations already
successfully completed.
*If a calibration attempt is not successful you will hear 2 short
beeps and the corresponding LED will return to a solid light.
Refer to the Troubleshooting Section.
TO CALIBRATE CONSTANT SPEED DEVICES:
1. Turn on the pump, air conditioner or generator and observe
that raw water flow is present.
2. To enter calibration mode – press and hold both buttons for
3 seconds. All LEDs will flash 3 times to confirm Calibration
Mode. Release both buttons. A solid LED identifies which
device is offered for calibration. If this is not the device you
want to calibrate press the hidden button to advance to other
devices. When the device you want to calibrate is indicated by
a solid LED press the bell button to accept this device; the LED
will flash at a one second interval.
3. To calibrate the device - press the bell button. Rapid beeping
indicates that the Processor is collecting data. When data
collection is complete the LED will automatically advance to
the next device.
4. When the device you want to calibrate is indicated by a solid
LED press the bell button to accept this device; the LED will
flash at a one second interval.
5. Repeat step 3 for each constant speed device.
6. To exit calibration mode - press and hold both buttons for
3 seconds. All LEDs will blink three times, the horn will beep
simultaneously, and the LED’s will cycle to indicate that the
calibration mode has been exited.
TO CALIBRATE ENGINES:
Engine Calibration Note: Engines with 3/4" to 1-1/2" plumbing
will collect flow data quickly (in about 2 seconds). Engines with
2" and larger plumbing may take up to 10 seconds to collect flow
data.
The data collection process is indicated by rapid beeping. Do not
change throttle setting or make touchpad selections during data
collection.
1. Run the engine(s) at idle speed and confirm that water flow is
present. Proceed to open water (you will have to operate at
idle speed and at full throttle to complete the calibration
process for each engine).
2. To enter calibration mode - press and hold both buttons. All
LEDs will flash 3 times to confirm Calibration Mode. Release
both buttons. A solid LED identifies which device is offered
for calibration. If this is not the engine you want to calibrate,
press the hidden button to advance to the next engine. Press
the bell button to accept the engine for calibration.
3. To calibrate this engine at idle speed - press the bell button
again; rapid beeping indicates the collection of flow data.
When beeping stops, idle speed data collection is complete.
4. The LED flashing rate will increase – accelerate to full throttle
WHEN SAFE TO DO SO. After the vessel has reached plane
and is running at stable speed wait 15-seconds to allow raw
water flow to stabilize.
5. To calibrate this engine at full throttle press the bell button –
rapid beeping indicates the collection of flow data. When
beeping stops, data collection at full throttle for this engine is
complete; the LED will automatically advance to the next
device.
6. Repeat steps 3, 4 and 5 for each engine.
7. To exit calibration mode - press and hold both buttons. All
LEDs will blink three times, the horn will beep simultaneously,
and the LED’s will cycle to indicate that the calibration mode
has been exited.

For service assistance/information call 410.712.4242 and ask for Strainers Service Department. After hours go to www.groco.net.
InstallationandOperatingInstructionsfor
GROCOSSA-3andSSA-4Series(TOUCHPADVERSION)
US Patent No. 7491320
InfoSheet SSA-3and 4Series, 5of5
110816
Maintenance
Marine growth and debris will impede paddlewheel
operation and may trigger false alerts. Clean all flow
sensor paddlewheels monthly. First, close the seacock.
The sensor can be removed by grasping the pull-ring and
turning it 90-degrees counter-clockwise – then pull straight
out. Lubricate the O-Rings (GROCO #2-120) with silicon or
Teflon® based grease. DO NOT use petroleum based grease.
TROUBLESHOOTING
INDICATION PROBLEM POSSIBLE CAUSE CORRECTIVE ACTION
During calibration, Calibration There is no flow Check pump, strainer
2 beeps, then solid LED not successful seacock, and hoses
Cables in wrong jack Check Figure-2
Audible Alert and Blinking Flow reduction Debris on sensor Clean Sensor
LED during operation Clogged Strainer Clean Strainer
Damaged Pump Impeller Replace Impeller
Failed Pump Motor Replace Motor
Partially Closed Seacock Open Seacock
Kinked Hose Replace Hose
Alerts flashing and beeping SSA not calibrated Calibrate system
No LED flash when consumer No power Blown fuse Replace fuse
is on Power cord disconnected Connect power cord
No self-test routine No power Blown fuse Replace fuse
Power cord disconnected Connect power cord
This manual suits for next models
1
Table of contents
Popular Measuring Instrument manuals by other brands
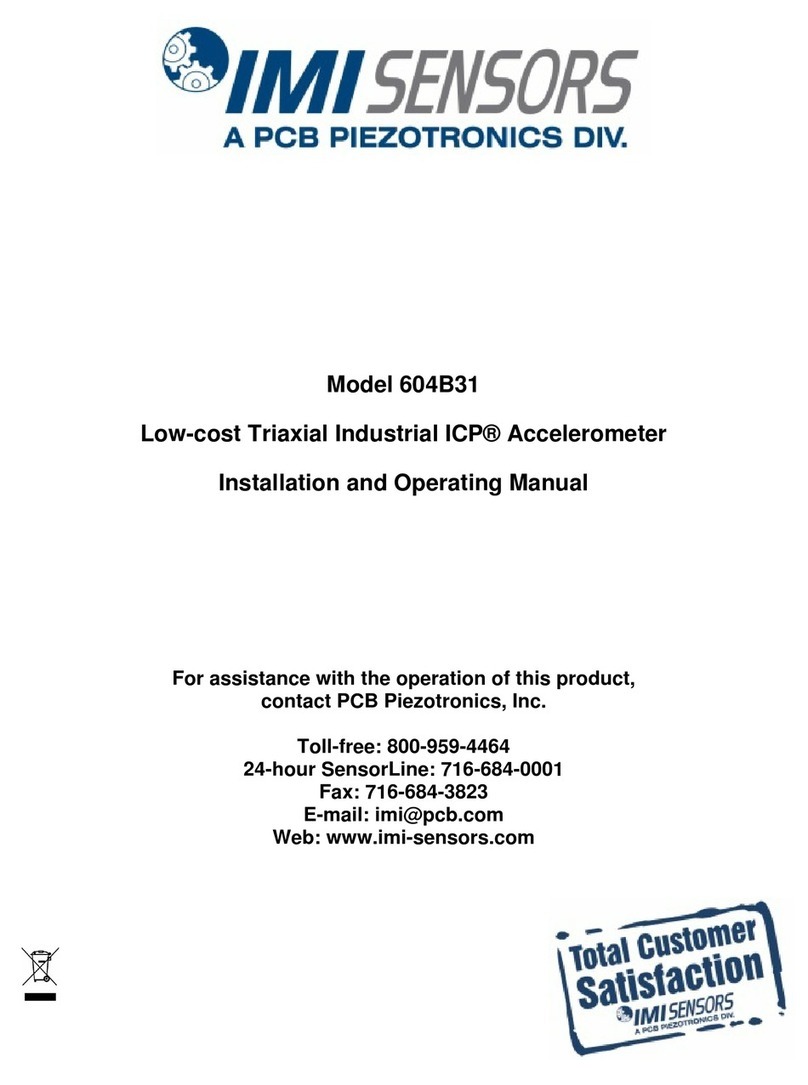
PCB Piezotronics
PCB Piezotronics IMI SENSORS 604B31 Installation and operating manual
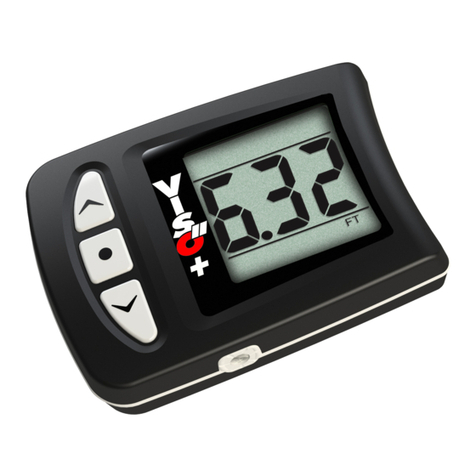
Larsen & Brusgaard
Larsen & Brusgaard VISO user manual

Weidmüller
Weidmüller 525 manual
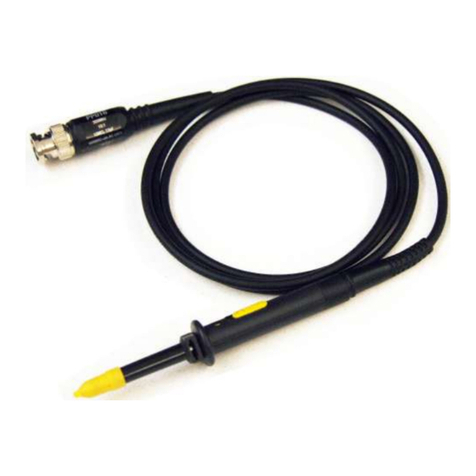
Teledyne Lecroy
Teledyne Lecroy PP016 Operator's manual
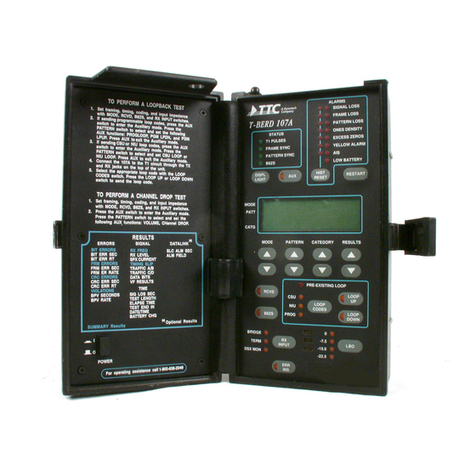
TTC
TTC T-BERD 107A Reference manual
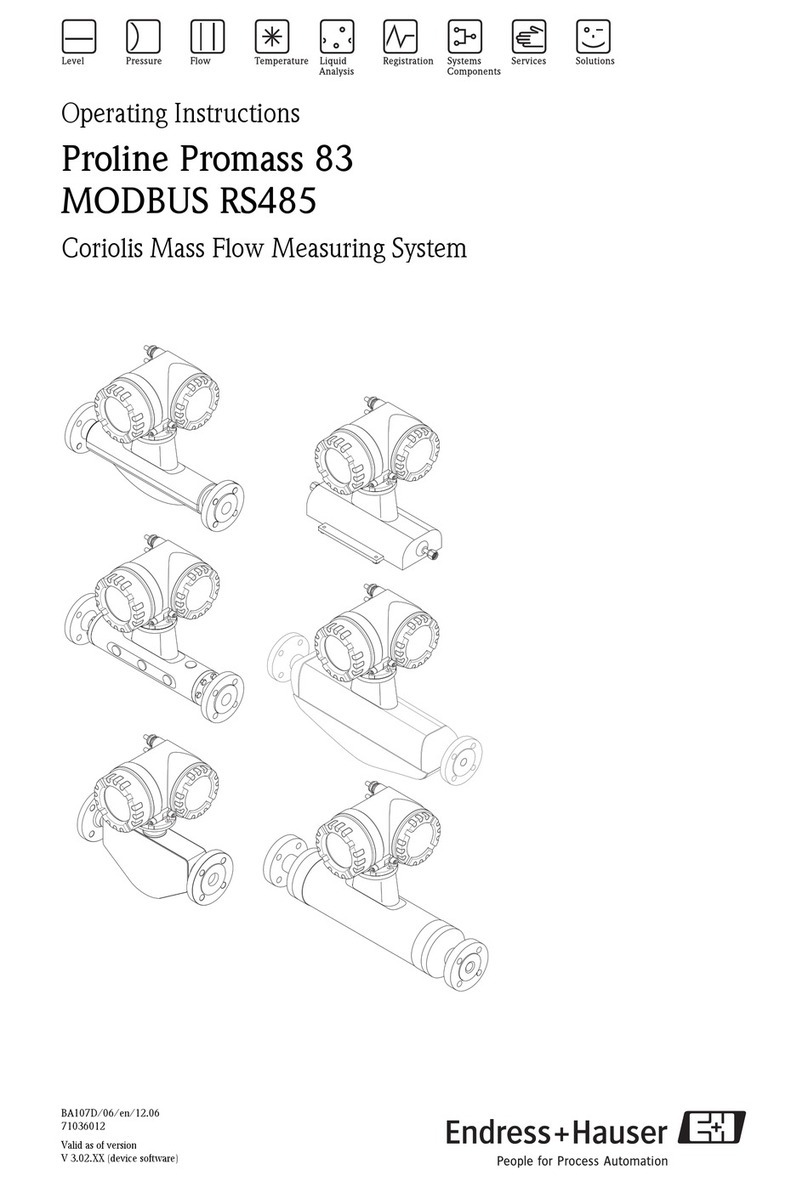
Endress+Hauser
Endress+Hauser Proline Promass 83 operating instructions
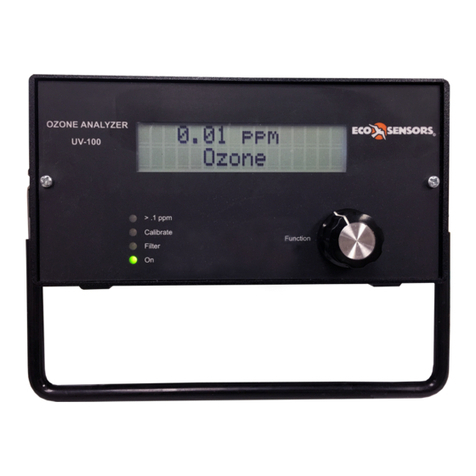
ECO Sensors
ECO Sensors UV-100 user manual
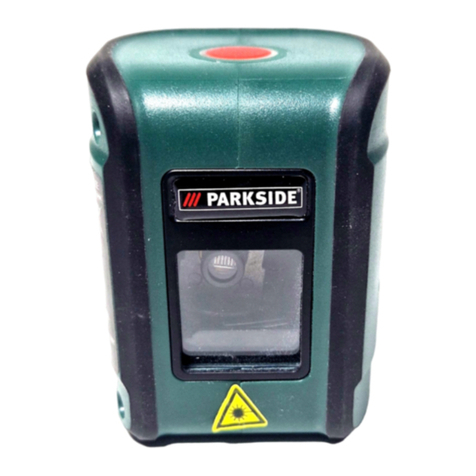
Parkside
Parkside PKLL 7 A1 operating instructions

Caleffi solar
Caleffi solar iSolar WMZ manual
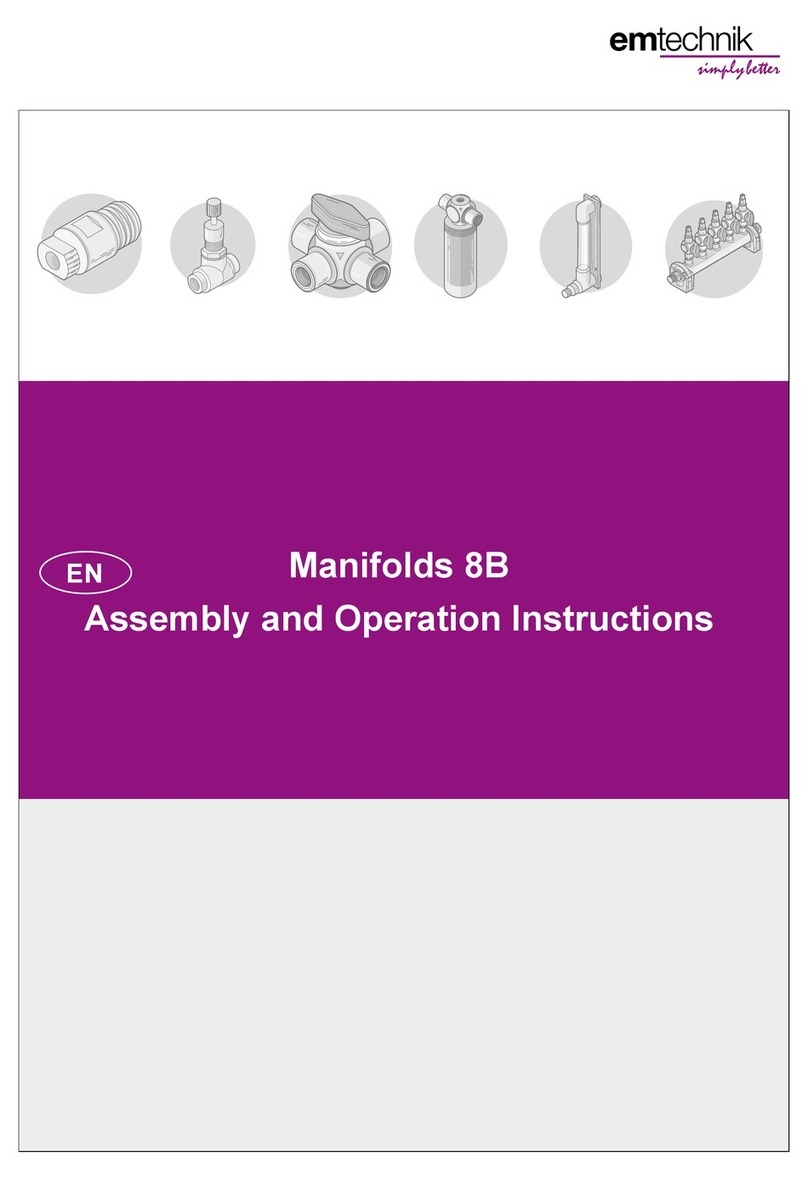
EM-Technik
EM-Technik 8B Series Assembly and operation instructions
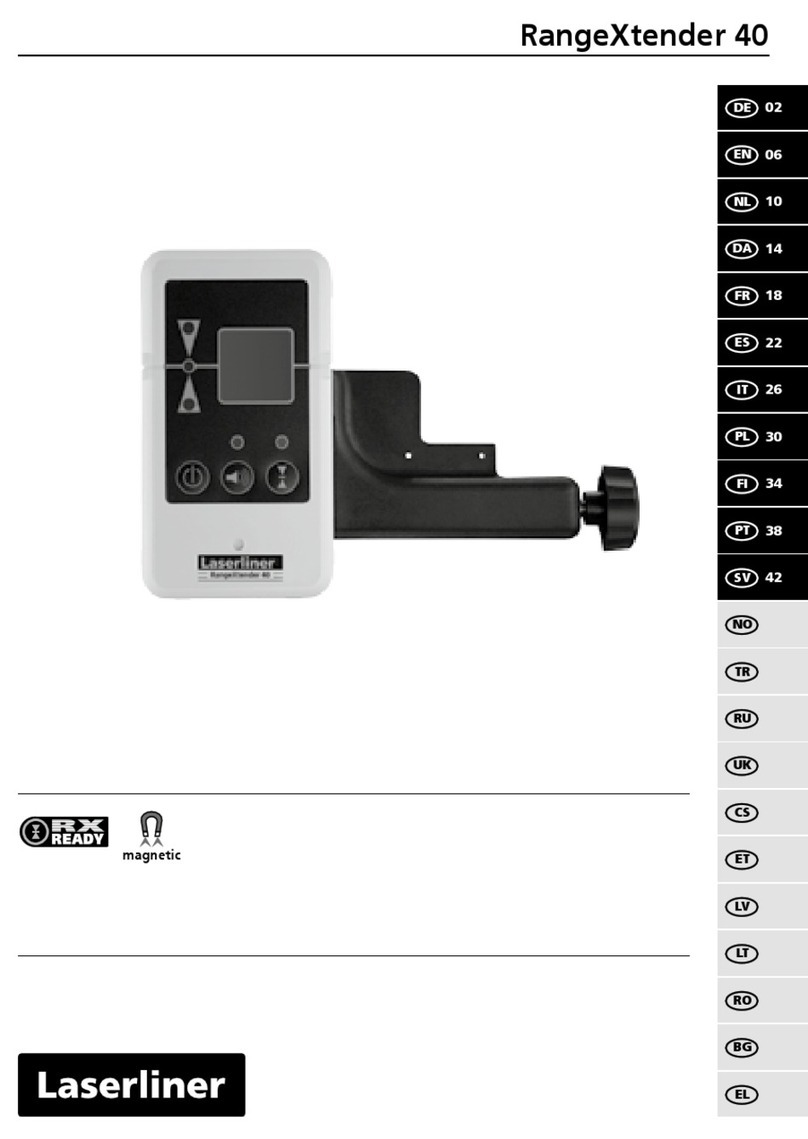
LaserLiner
LaserLiner RangeXtender 40 quick start guide
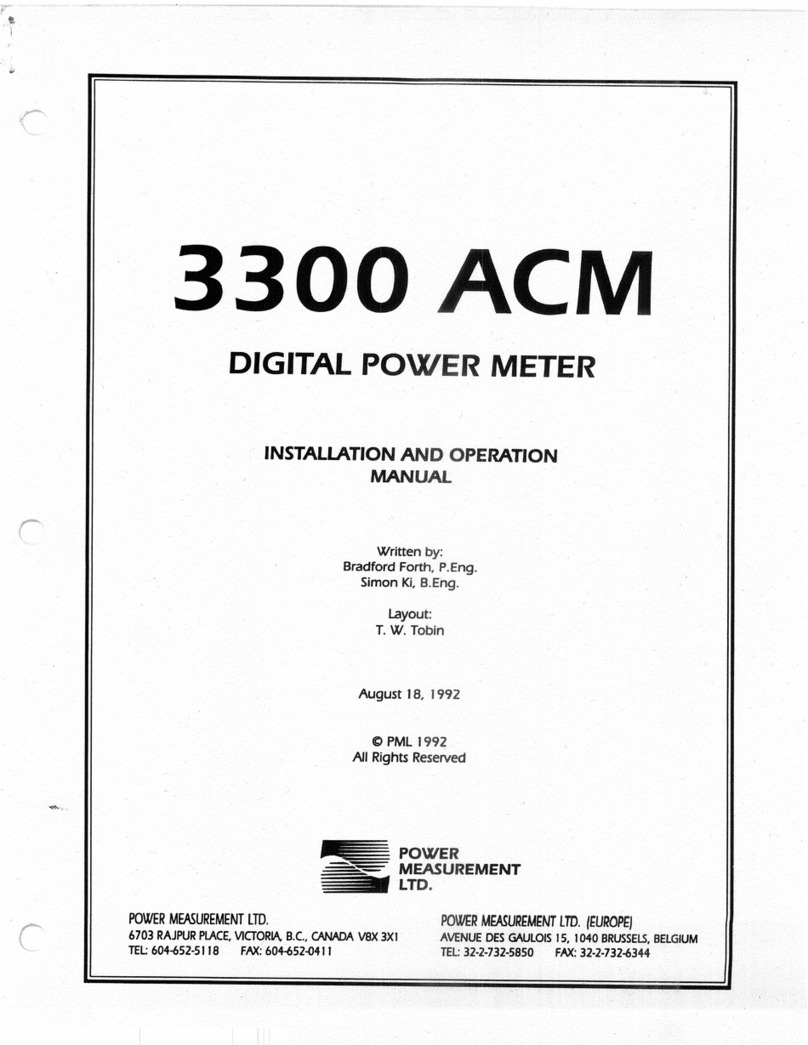
Power Measurement
Power Measurement 3300 ACM Installation and operation manual