Gruetzner Lubricus LUB-C-1 User manual

User Guide
Lubricus Controller
LUB-C-1, LUB-C-2,
LUB-C-3, LUB-C-4,
LUB-C-1-1
(24 VDC)
Lubricus Type C

page 2
Content
General Information, Scope of supply 3
Overview:Lubricus Controller & Lubricus Lubrication System, Type C 4
General safety details 5
- Intended use 5
- Extent of warranty 5
- General safety information 5-7
- Transport and storage 7
- Installation instruction, Start up 7
Function 9
- Adjustment Flow Chart 10
- Flow chart details –Overview adjustment option 11-12
- Activation of exits, Pump specific adjustment 10-12
- Inputting the generation of the Lubricus C devices used 13
- Table pause time adjustments 14
- Table quantity adjustment 14
Details: Activation (Start/Stop/Adjustment) 15-18
- Functional problems: error, message and problems 17-18
Extras: Quick check function and system control 19
Communication Interface 20
Service: Lubricus, Type C with cartridge 21
Technical data: Lubricus Controller & Lubricus, Type C 23
Mounting: Lubricus Controller & Lubricus Lubrication System 24
Recommended tube/hose length & Disposal 25

page 3
General Information
Thank you very much to have decided to use our Lubricus Lubrication System and Lubricus Controller. Make sure that you
familiarize yourself with the safety instructions of this unit and the accessories supplied with this unit. This manual contains
important safety information.
The Lubricus Lubrication System is a very compact lubrication pump for oil and grease up to NLGI 2. The types LUB-C-1,
LUB-C-2, LUB-C-3, LUB-C-4 and LUB-C-1-1 are designed for external control (Lubricus Controller) and a power supply of 24
VDC. The lubricant reservoir (400 cm³) is located in a cartridge.
- Lubricus Lubrication System (Type LUB-C-1, LUB-C-2, LUB-C-3, LUB-C-4, and LUB-C-1-1) will be installed near the
lubrication point
- Lubricus Controller (System Control) will be installed in a central location
Depending on the configuration of Lubricus Lubrication System, Type C is available with up to four outlets and therefore
suitable to lubricate several lubrication points.
Warning
Lubricus Lubrication System is designed for use in normal industrial environment indoor as well as outdoor but is not suitable
for mounting on moving equipment for example trucks. Only use original Lubricus cartridges and original spare parts. None
original spare parts can destroy the Lubricus Lubrication System or the Lubricus Controller.
Scope of supply
Standard delivery Lubricus Controller includes:
-Lubricus Controller
-Operating Instructions
Standard scope of supply Lubricus Lubrication System, Type C:
-Lubricus Lubrication System, (Type LUB-C-1, LUB-C-2, LUB-C-3, LUB-C-4, LUB-C-1-1)
-Tube connector attaches to the outlet, suitable for flexible tube 6 x 4
-Operating Instructions
Lubricus Lubrication System, Type C
LUB-C-1
LUB-C-2
LUB-C-3
LUB-C-4
LUB-C-1-1

page 4
Lubricus Lubrication System
Important remark: unused exits cannot be closed and must remain open to avoid damage to the Lubricus
Lubrication System!
Lubricus Controller
Connection Lubricus Controller
Ventilation Lock & programming key
(The programming key is conveniently stored on top of
the clear housing, to remove the key for Setup or
Adjustments of your Lubricus (Simply turn clockwise to
release key)
The point of the key is used for programming.
Please note: Always replace the key for safe keeping
as this also forms part of the cover.
Cover for cartridge
Display showing adjustment
values and error messages
Sensor for Activation and programming key
Connector pin M12 x 1 = connection to plc +
power supply 24 VDC
LED: Status indicator
4 Outlets for Lubricus,
Connector pin M8 x 1

page 5
Attention
!
General safety details
Everybody who is involved with the installation, start-up, maintenance and operation of the Lubricus Lubrication System
must read these instructions carefully!
Use in accordance with guide
Lubricus Lubrication System is only allowed for industrial use.
Lubricus Lubrication System may only be put into service, if it is integrated or attached to another
machine and will be operated together with that machine.
Lubricus Lubrication System may only be used according to the technical data (see chapter
“technical data”).
Unauthorized structural changes at the Lubricus Lubrication System are not permitted. We do
not assume liability for damages of persons or machines which result from that.
Other uses or uses beyond those described above cannot be considered to be in
accordance with the regulations.
Extent of warranty
Warranties concerning operating safety, reliability and capacity, are only granted under the following conditions:
Assembly, installation, maintenance and repair are only carried out through trained specialist. Hazardous hot or cold
machine parts must be shielded to prevent touching.
Lubricus Lubrication System must be used according to the instructions in the technical operating manual
- the rated technical data must not be exceeded in any case.
- Retrofitting and repair work on the Lubricus Lubrication System may only be done by manufacturer.
Liability and extent of guarantee
Proper functioning of the Lubricus Lubrication System can only be achieved through use of recommended lubricants from the
original Lubricus range of accessories, and by observation of all installation, operation and maintenance instructions.
Grützner GmbH excludes all liability if these instructions are not observed.
Grützner GmbH grants guarantees concerning operating safety, reliability and performance only under the following
conditions:
assembly, installation, maintenance and repairs are carried out by qualified staff only;
hazardous hot or cold machine parts must be shielded to prevent skin contact;
the Lubricus Lubrication System must be used according to the Technical Data and instructions;
the limit values stated in the Technical Data are under no circumstances to be exceeded;
retrofitting and repair work on the Lubricus Lubrication System may only be carried out by the manufacturer;
the lubrication system must be protected against damp and wet.
If a lubricant that has not yet been tested for compatibility with the Lubricus Lubrication System be supplied or requested for
use in the Lubricus Lubrication System by the purchaser/customer, the purchaser/customer undertakes the risk and
responsibility.
This product is subject to strict production controls and fulfils our company’s factory specifications. However, guarantee of
testing of each individual case cannot be given due to the numerous factors involved.
We therefore strongly recommend that test runs be carried out.
All liability is excluded.
The Lubricus Lubrication System lubricant cartridge has been constructed and produced for one-time use only. Multiple use
of the lubricant cartridge is not envisaged. After being used once, the lubricant cartridge is to be completely replaced; refilling
is not permitted. Noncompliance will lead to nullification of the guarantee.
For guarantee conditions see the sales and delivery conditions of Grützner GmbH
Attention
!

page 6
Remark
Attention
!
General safety information
Basic information, which must be followed during service, operation and maintenance, are listed as follows.
It is absolutely essential to read the operator’s manual / user guide by respective technical staff / technical operator before
installation and start up.
In addition to this, it must be permanently available at the site.
IMPORTANT
Please pay attention, not only to the safety instructions under this main point, but also to those special security cautions that
are mentioned on the other pages.
This symbol warns of electrical voltage.
Safety instructions which, if not complied with, may endanger persons, are marked specifically with
the general hazard symbol.
This heading is used if inaccurate compliance or non-compliance with the operating Instructions or
specified work procedures etc. may result in damage.
Points out special information.
Notes attached directly on the machine, must be strictly followed and maintained in completely readable
condition!
Qualification and training of the personnel
The operation, maintenance, service and installation personnel must have appropriate qualifications for this
work. Responsibility and supervision of the personnel must be clearly defined by the end user / operator. If
the personnel do not have the necessary knowledge, they must be trained and instructed. The operator must
ensure that the personnel have completely understood the contents of the user information.
Non-observance of the safety information can be dangerous
Not observing the safety information can lead to danger for people, environment and machines.
Not observing the safety information can mean the loss of any or all damage claims. In special cases, non-
observance can, for example, lead to the following dangers:
Failure of important plant functions.
Failure of prescribed methods of maintenance and preventive maintenance.
Endangering people due to electrical, mechanical and chemical effects.
Endangering the environment due to leaks of dangerous materials.

page 7
Safety information for operators/operating staff
Hot or cold machine parts are hazardous and must be protected from touching. The protection on
"moving or rotating parts" must not be removed.
In case of leakages of dangerous media proper disposal not endangering environment and people must
be ensured.
Legal Regulation must be observed and complied.
Eliminate any danger due to electrical power.
Safety information for maintenance, inspection and assembly work
All maintenance, inspection and installation work may only be carried out by trained specialists who
have been informed appropriately by studying the user information closely.
All work must only be carried out when machine is shut down and while wearing appropriate protective
clothing. Always comply with the procedures for shutting the machine down that are described in the
operating manual. All the safety and protective equipment must be replaced immediately after completing
work. Environmentally hazardous substances that endanger the environment must be disposed in
accordance with local regulations. Secure the system during maintenance and repair work, against
intentional or unintentional operation. Dispose of used lubricants in accordance with the safety data sheets of
the lubricant manufacturer.
Alterations and manufacture of spare parts without authority
Rebuilding or altering the Lubricus Lubrication System is only allowed after consultation with the
manufacturer. Original spare parts and accessories authorized by the manufacturer are for safety
purposes. Using other parts results in loss of liability for claims resulting out of this. For components,
retrofitted by the operator, the manufacturer does not assume guarantee nor claims for damages.
Prohibited methods of operation
Operational security of the Lubricus Lubrication System is only guaranteed if it is operated in accordance with the
operating instructions. The limit values stated in the technical data must not be exceeded under any circumstances.
General risk reference
All components of the system are designed in accordance with the prevailing regulations of the construction
of technical machines, in regards to operational safety and accident prevention. Operation outside of these
constraints can lead to dangers for the user respectively third persons or other technical facilities. The
Lubricus Lubrication System therefore may fulfil only in technically fault-free condition its intended use.
This may only be carried out under compliance of the safety regulations and the attention of the operator's
manual.
Therefore please regularly inspect the pump and its attachments for possible damage or leaks.
Transport and storage
Use suitable lifting gear for transport.
Do not throw or expose the Lubricus Lubrication System to strong shock loads.
Store the Lubricus Lubrication System in a cool and dry place to avoid corrosion of the system’s individual parts.
Pay attention to the current safety- and accident prevention instructions during the transport. Wear suitable
protection equipment if necessary!

page 8
Installation instruction
The following conditions have to be satisfied during the installation of this Lubricus Lubrication System, thus it
can be assembled, with other parts, to a complete machine without affecting the safety and health of
humans.
The housing of the Lubricus and/or Lubricus Controller should not be exposed to direct sunlight
and/or radiant heat preventing the formation of condensation.
Electrical connection
Have the electric power supply connected only by a trained electrician!
Connection and wiring of the electric components should be done by an expert trained in this field.
Check the voltage details with the existing power supply voltage!
Maintenance /repair
Disconnect the voltage feed, before starting with maintenance or repair.
Maintenance and repair work may only be done with the system shut down.
Check the surface temperature of Lubricus Lubrication System, due to danger of burning by radiant heat.
Always wear heat-resistance gloves! Protect the system from activation during maintenance and repair work!

page 9
Function/Principle
When activating the Lubricus Lubrication System the piston pump starts to work and pumps the lubricant in small quantities
to the outlets. The integrated microprocessor controls the delivery rates and the operating time, which can be individually set.
Lubricus Controller Installation: Lubricus Controller settings:
- Observe the safety instructions - The programming mode enables:
- Lubricus will be installed near the lubrication point => Entering the quantity of exits per Lubricus
- Install Lubricus Controller in a central location (page 12 and page 13-14, specific settings)
- Connect cable => Entering pause time (=Time between 2
- Switch on lubrication intervals, page 12: table pause time
adjustment)
=> Finished => Entering the lubrication quantity per interval
(page 12, table quantity adjustment)

page 10
Adjustment Flow chart

page 11
Flow chart details –overview adjustment
Lubricus Controller can be adjusted without any Lubricus unit attached. Settings will stay in memory. The Controller controls
the Lubricus units in sequence starting at exit 1.
.
1.
1) 1.1. For every Lubricus connected the number of outlets must be programmed.
Divided into left half (green LED) and to right (orange LED) half of the Lubricus body.
The display shows following: Base setting: A00 = no exit activated A01 = 1 exit activated
A02 = 2 exits activated
Settings for every specific Lubricus Models
Type LUB-C-1 adjustment at green LED / left Lubricus body: 1 exit = A01
adjustment at orange LED / right Lubricus body no exit = A00
Type LUB-C-2 adjustment at green LED / left Lubricus body 2 exits = A02
adjustment at orange LED / right Lubricus body no exit = A00
Left side of Lubricus body: dispensing equal quantity from both exits/outlets.
green LED: Function left side of Lubricus body
orange LED: Function right side of Lubricus body
Normal Status Indication: F: red LED –constant light –failure, fault, error report
OK: green LED –constant light –OK

page 12
Typ LUB-C-3 adjustment at green LED / left Lubricus body 1 exit = A01
adjustment at orange LED / right Lubricus body: 2 exits = A02
Left exit individual controlled
Right side of Lubricus body (2 outlets) is dispensing equal quantity.
OR
Typ LUB-C-3 adjustment at green LED / left Lubricus body: 2 exits = A02
adjustment at orange LED / right Lubricus body: 1 exit = A01
Right exit individual controlled.
Left side of Lubricus body (2 outlets) is dispensing equal quantity.
Typ LUB-C-4 adjustment at green LED / left Lubricus body: 2 exits = A02
adjustment at orange LED / right Lubricus body: 2 exits = A02
Left and right side of Lubricus body is individual controlled.
Mix of 2x different dispensing quantities.
Right side of Lubricus body (2 outlets) is dispensing equal quantity.
Left side of Lubricus body (2 outlets) is dispensing equal quantity .
Typ LUB-C-1-1 adjustment at green LED / left Lubricus body 1 exit = A01
adjustment at orange LED / right Lubricus body: 1 exit = A01
Left and right side of Lubricus body is individual controlled

page 13
1.2. Inputting the generation of the Lubricus C devices used
For all Lubricus controllers => identified by
A) the release number n01 r03 for the software used indicated
on the LCD display when switching on the Lubricus controller
for the first time,
B) a serial number, SN, greater than 1601919,
C) the inscription SW: N01R03 on the name plate,
D) an illuminated LCD display,
the generation of the Lubricus C lubrication systems used is entered via the parameters Pu1 and Pu2 after entering the
number of outlets!
If your Lubricus controller does not have any of these features, please continue inputting the settings
by selecting the pause time, H, as described under point 2.
All of the latest generation of Lubricus C lubrication systems, which can be identified by a serial number, SN,
greater than 1601909, belong to the Pu2 generation!
If the Lubricus C lubrication system connected to the Lubricus controller belongs to the latest generation, Pu2, no changes
need to be made to the Pu parameter on the controller, as all Lubricus controllers with n01 r03 software are set to the PU2
generation on delivery. In accordance with this, Pu2 is shown on the display. After approx. 4 seconds, the display
automatically jumps to the next menu item, setting the pause time, H, as described further under point 2.
All Lubricus controllers with the n01 r03 software are set to the PU2 generation on delivery.
If the Lubricus C lubrication system connected to the Lubricus controller belongs to the Pu1 generation (serial number, SN,
smaller than 1601909), the parameter on the Lubricus controller must be modified as follows:
to change the parameter from Pu2 to Pu1, touch the sensor area on the Lubricus controller with the activation key within
approx. 4 seconds of the PU2 indicator on the LCD display lighting up. The indicator on the display will change to Pu1 and
will then automatically jump to the next menu item (setting the pause time, H) after approx. 4 seconds.
This parameter must be changed from Pu2 to Pu1 on the Lubricus controller for all Pu1 generation Lubricus C devices and
for all existing pump units (left side of the housing / green LED; right side of the housing / orange LED).

page 14
2) If exits are activated (A01 or A02), each side of Lubricus body half can be adjusted:
H = Pause Time => Time interval between 2 lubrication intervals (1 to 96 h possible)
than
C = Lubrication quantity per interval => (1x 0,15 cm³to 30 x 0,15 cm³= 4,5 cm³possible)
H = Pause Time
H: Adjustment for
Lubricus –1 side of body
H (Pause Time) adjustment = Time between 2 lubrication intervals
(1 to 96 h possible)
H: Pause Time (hours)
1
12
24
48
96
Result: Lubrication cycles per exit per
month
720
60
30
15
7,5
Intermediate steps are possible.
C = Lubrication quantity per interval
C: Adjustment for
Lubricus –1 side of body
C (number of strokes) adjustment
= delivery rate of one period
Number of strokes
1
5
10
20
30
Delivery rate
of one period
0,15cm³
0,75cm³
1,5cm³
3,0cm³
4,5cm³
Intermediate steps are possible.

page 15
Start up (Switch on / Switch off / Change)
Lubricus Controller can be adjusted without any Lubricus unit attached. Settings will stay in memory. Lubricus Controller
controls the connected Lubricus in sequence one after the other. This ensures no Lubricus unit is operating parallel
preventing higher energy usage. During pump operation no further changes and functions are possible.
(1) Connect Lubricus Controller with M12x1 Plug to 24 VDC (e.g. via PLC), power consumption max. 300 mA (more
details in communication interface, page 18) after connection 24 VDC -> green LED illuminated (constant light)
(2) Lubricus Controller displays ON, the display will show all values in the display associated with the assigned LED
light. Lubricus unit 1: green LED, than orange LED; Lubricus unit 2: green LED, than orange LED; Lubricus unit 3
green LED, than orange LED ; Lubricus unit 4: green LED, than orange LED.
Basic settings: all Controller- exits are not activated.
(3) After displaying all adjustments, ON is blinking for approx. 3 sec in the display : Now you can adjust the basic
settings.
Open the ventilation lock (turn clockwise to OPEN) and remove the cover. The nose of the cover is your Operating /
programming key.
green LED: Function left side of Lubricus body
orange LED: Function right side of Lubricus body
All adjustments and changes will be executed by touching
the sensor area on the Controller with the activation and
programming key.
Normal Status Indication: F: red LED –constant light –failure, fault, error report
OK: green LED –constant light –everything OK
If no further action the
Controller will continue in the
operating mode. Place
activation and programming
key in ventilation hole and
turn it from OPEN -> CLOSE

page 16
(4) Basic adjustment will be changed when display blinks “ON”: touch the sensor area with the activation and
programming key, approx. 2-3 sec and hold until the display “On” disappears (red LED), then remove programming
key:
Should you have missed the time when „On“ was blinking, place programming key on sensor and hold until
you see a 3 x red blinking signal (red LED) OFF in display. To switch Unit ON place programming key on sensor
and hold until you see a 3 x red blink signal (red LED) ON in display.
Programming for each Controller exit:
The programming mode enables:
1. Entering the quantity of exits per Lubricus unit, page 10-11, specific settings (if no exit is
activated = A00 -> 2. and 3. are not available!)
2. Entering H: Pause Time (= Time between 2 lubrication intervals, page 12: table pause time
adjustment)
3. Entering C: the lubrication quantity per interval, (page 12, table quantity adjustment)
a) Lubricus Controller Exit 1, green LED is blinking (-> left side of Lubricus body)
- Display shows A00: Enter required pump exits as per your attached Lubricus Model, page 10-11
Example: Lubricus LUB-C-2: Adjustment at green LED / left side of Lubricus body: 2 Exits= A02
Touch sensor shortly with programming key until required information is displayed. If there is no change the
displayed value will be used.
- After the exit activation the parameters H and C need to be adjusted:
H: Pause time between 2 lubrication cycles, Input options: 1 to 96 (Values in h, Table page 12)
Short touch of the programming key on the sensor changes the value (1-96 are possible); Constant contact
will let the display fast forward; short contact will advance values by 1. No activity for 2 sec through touching
the sensor pad the displayed value will then be used and placed in memory. After a short time the unit will
switch automatically to C.
C:Number of cycles (Number of cycle’s x 0,15cm³ = lubrication quantity): Input options: 1 to 30 (table page
12).
Short touch of the programming key on the sensor changes the value (1-30 are possible); Constant contact
will let the display fast forward; short contact will advance values by 1, no activity for 2 sec by touching the
sensor pad the displayed value will then be placed in memory and will be used. This will finish the basic
settings of Lubricus Controller Exit 1, left Lubricus body side, green LED.
- Automatic change to next Lubricus body half, on the same Lubricus Controller Exit

page 17
b) Lubricus Controller Exit 1, orange LED is blinking (-> right side of Lubricus body)
Same procedure like a) …
-Automatic change to next Lubricus Controller exit 2, 3 and 4 see Adjustment Flow chart, page 9
c) If no further action the unit will continue in the operating mode. Place activation and programming key in
ventilation hole and turn it from OPEN -> CLOSE
d) Lubricus Controller will initiate all activated exits. The display will change to “ON”. An extra lubrication cycle of
0.15 cc per exit with back pressure measurement (Quick check) will be performed. A value that represents the
pressure required to pump the lubricant to the lubrication point will be displayed. After the pump cycle is
finished the max pressure is shown in bar, e.g. 015 represents 15 bar. The unit can only provide approximate
values from + / - 15 %. This is accurate enough to establish the condition of the lubrication point.
(5) Additional functions: QuickCheck = extra dispensing cycle (= pumping of small amounts of lubricant for
testing purposes): Touch contact sensor of Lubricus Controller with programming key and count 2 x red blinking
signal (central LED in the display)
(6) Additional functions: Switch „OFF“:
Touch contact sensor of Lubricus Controller with programming key and count 3 x red blinking signal (central
LED in the display) and remove programming key. Display changes to “OFF”. Adjustment stays in Memory. A
longer contact of the programming key with the sensor does not switch the unit off preventing accidental stopping
when a strong magnet is near the of Lubricus Controller.
(7) Additional functions: Switch „ON“: To switch the unit “ON” Touch contact sensor of Lubricus Controller with
programming key and count 3 x red blinking signal (central LED in the display) and remove programming key.
Display changes to “ON”. Adjustment stays in Memory

page 18
Malfunction (error shown on LCD / LED)
“Normal“ operating mode: Lubricus Controller display „ON” each LED for activated pumps blink shortly one after each
other in 1 second intervals. Not activated Lubricus Controller exits will not blink
Example:
Lubricus Controller exit 1: Lubricus LUB-C-2: Adjustment green LED / left Lubricus body: 2 exits = A02
Adjustment orange LED / right Lubricus body: 0 exits = A00
Lubricus Controller exit 2: Lubricus LUB-C1-1: Adjustment green LED / left Lubricus body: 1 exit = A01
Adjustment orange LED / right Lubricus body: 1 exit = A01
Green LED for normal operating mode is always illuminated, LED’s of Lubricus Controller exit 1 and 2 blink shortly one after
each (green, green ,orange , and starting again from the beginning …)
Error messages / faults: The dedicated error message for each connected Lubricus unit is displayed.
E1: Empty lubricant reservoir: red LED lights constantly + Display will show error for Lubricus unit connected to Lubricus
Controller exit + E1, when the sequence of the connected pump with the error is reached. If the sequence reaches the units
without error the display will show “ON”, the red LED will still light to signal that an error message exists.
Root cause: The lubricant cartridge is empty. The unit continues to be active and will pump!
Corrective action: replace cartridge. Lubricus will continue to run as per active program.
Example: exit 1, Lubricus LUB-C-2, all OK exit 2, Lubricus LUB-C-1-1, cartridge empty
E2: Back pressure too high: red LED lights constantly + Display will show error for Lubricus unit connected to Lubricus
Controller exit + E2; the error message is related to the Lubricus body half respectively to the Lubricus exit.
Root cause: Back pressure was measured 3 x too high. The lubrication point could be clocked, the tube length could
be too long or the grease is too stiff or has hardened. Lubricus will stop!
Corrective action: Trace reason for high back pressure >70bar and correct it.
Switch unit „OFF“ and „On“ again. The error message will be reset to 0. Lubricus will start again as per
program in memory.
Example: Exit 2, Lubricus LUB-C-1-1, Error 2E2 at exit 2 + orange LED / right Lubricus body half: exit1

page 19
E4: Lubricus-feedback: Exit was activated, but no feedback from connected Lubricus unit: red LED lights constantly +
Display will show error for unit connected to Lubricus Controller exit + E4; the red LED will light additionally to the green and
orange LED when the sequence of the connected unit with the error is reached. If the sequence reaches the Lubricus units
without error the display will show “ON”, the red LED will still light to signal that an error message exists.
Root cause: The connection cable between Controller and Lubricus unit is broken, disconnected or missing. Lubricus
Controller unit stays active and other connected units will dispense as per program in memory.
Corrective action: Change or connect cable (broken, missing or disconnected connection cable), Switch unit „OFF“ and
„On“ again. The error message will be reset to 0. Lubricus will start again as per program in memory
Example: Exit 1, Lubricus LUB-C-2, all OK Exit 2, Lubricus LUB-C-1-1, cable defect
System error: Switch unit „OFF“ and „On“ again, Memory will not be erased.
Extras:
”Quick check” back pressure measurement
For testing purposes the Lubricus Controller is equipped with the “Quick Check” back pressure measuring function. Quick
Check back pressure measurement uses the extra lubrication cycle. A simple touching of the programming key to the
sensor pad will measure the existing pressure between the lubrication point and the pump unit exit. The value in bar will be
shown in the display.

page 20
Connector PIN assignment, connection Lubricus Controller to Lubricus Lubrication System, Type C
Connection Lubricus Controller - Exit M8x1, 4–pol - to Lubricus, Typ C –Exit
a) M12x1, 4-pol. All special cables are available on stock in our catalogue
b) If customer is managing all the necessary cabling, required to keep the system functional:
Lubricus Controller M8: PIN 1 to Lubricus unit, Typ C, M12: PIN 1
Lubricus Controller M8: PIN 2 to Lubricus unit, Typ C, M12: PIN 2
Lubricus Controller M8: PIN 3 to Lubricus unit, Typ C, M12: PIN 3
Lubricus Controller M8: PIN 4 to Lubricus unit, Typ C, M12: PIN 4
Mit dieser Kombination an Informationen wird sowohl eine von der
Maschinenlaufzeit abhängige Versorgung der Schmierstellen an der
Maschine, also auch eine lokal zeitnahe Schmiersystemkontrolle
realisiert.
Connector PIN assignment Lubricus Controller M 12 x 1
PIN 1: input voltage +20...30 VDC, color brown
PIN 2: no assignment, color white
PIN 3: Ground (GND), color blue
PIN 4: Output Signal, color black
Details:
PIN 1: Peak current (24 VDC): Imax, approx. 350 mA (during pump
operation), typically < 200 mA, Standby current (standby mode)
< 20 mA
Input Signal can switches ON and OFF
PIN 2: no assignment
PIN 3: Ground (GND)
PIN 4: High = operating mode (=OK) = input voltage, Low = 0 V = error
(type of error shown in display of Lubricus Controller), the outlet
signal, PIN4, can be charged with maximal 300mA. Warning: the
exit is not short-circuit proof
A time delay fuse 1A is normally required.
The Lubricus Controller is equipped with a 4- pol M12x1 connector to connect to the controller of your machine for
example a PLC. This connector supplies power to the Lubricus units and communicates with the controller. The voltage
to operate and to switch unit “ON” and “OFF” is +20...+30 VDC (PIN 1). The Controller will be in operating mode when
voltage is present. The green LED is illuminated. The supply voltage will be switched to exit (PIN4) if there are no errors
(Unit OK). The Controller will save the current operating parameters in memory if the supply voltage is disconnected or
unit is switched “OFF”. The unit will start again using the last parameters saved in memory. The operating status will be
communicated via PIN 4 and will be displayed in the integrated display of the Lubricus Controller.
This manual suits for next models
4
Table of contents
Popular Controllers manuals by other brands

Life
Life RG1 24DL Installation, use and maintenance
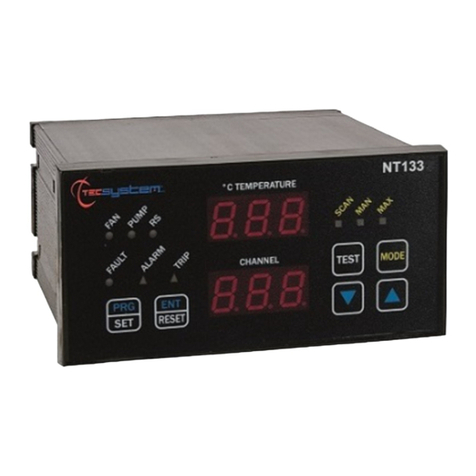
TECSYSTEM
TECSYSTEM MULTIMODULE 133 instruction manual

SEW-Eurodrive
SEW-Eurodrive MOVIPRO manual
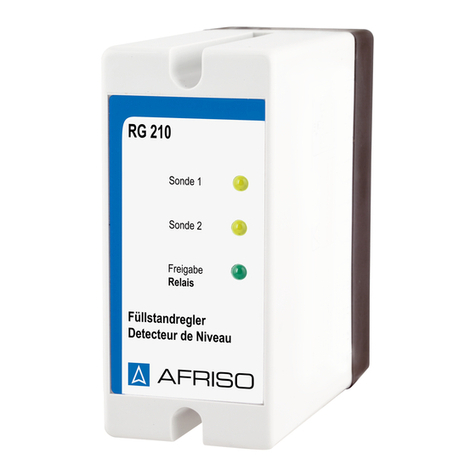
AFRISO
AFRISO RG 210 operating instructions
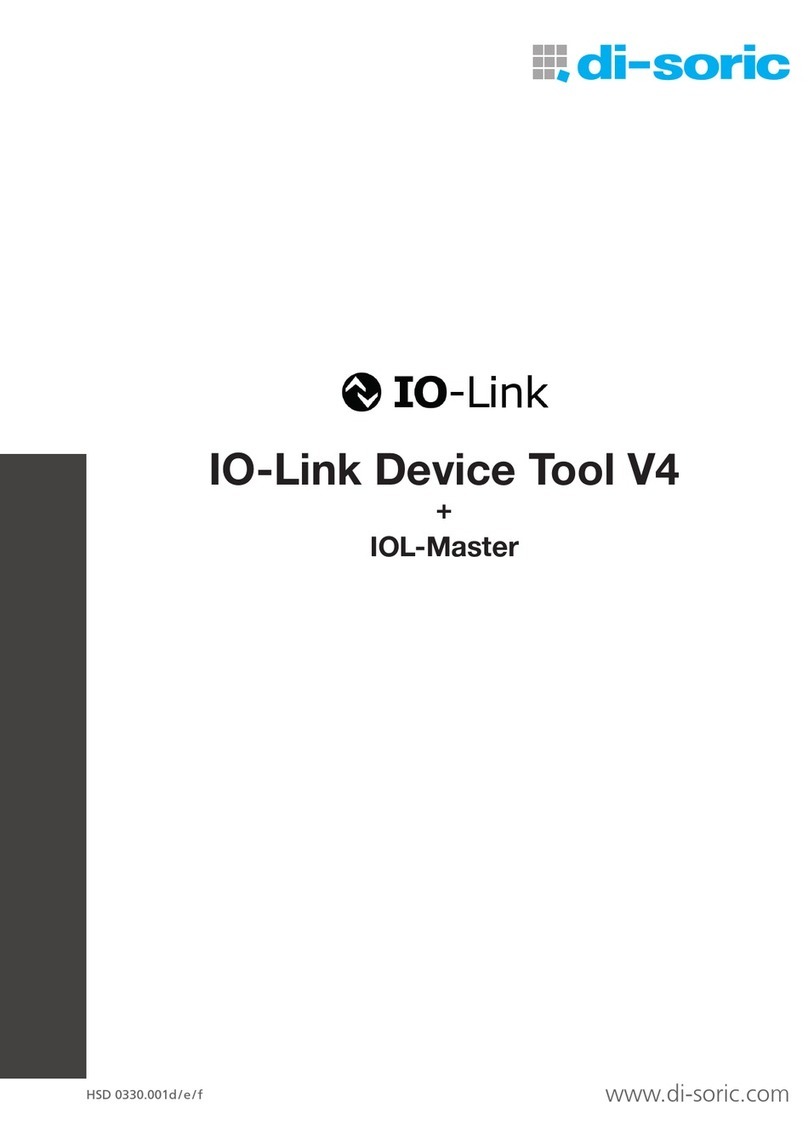
Di-soric
Di-soric IO-Link Device Tool V 4.0 instruction manual
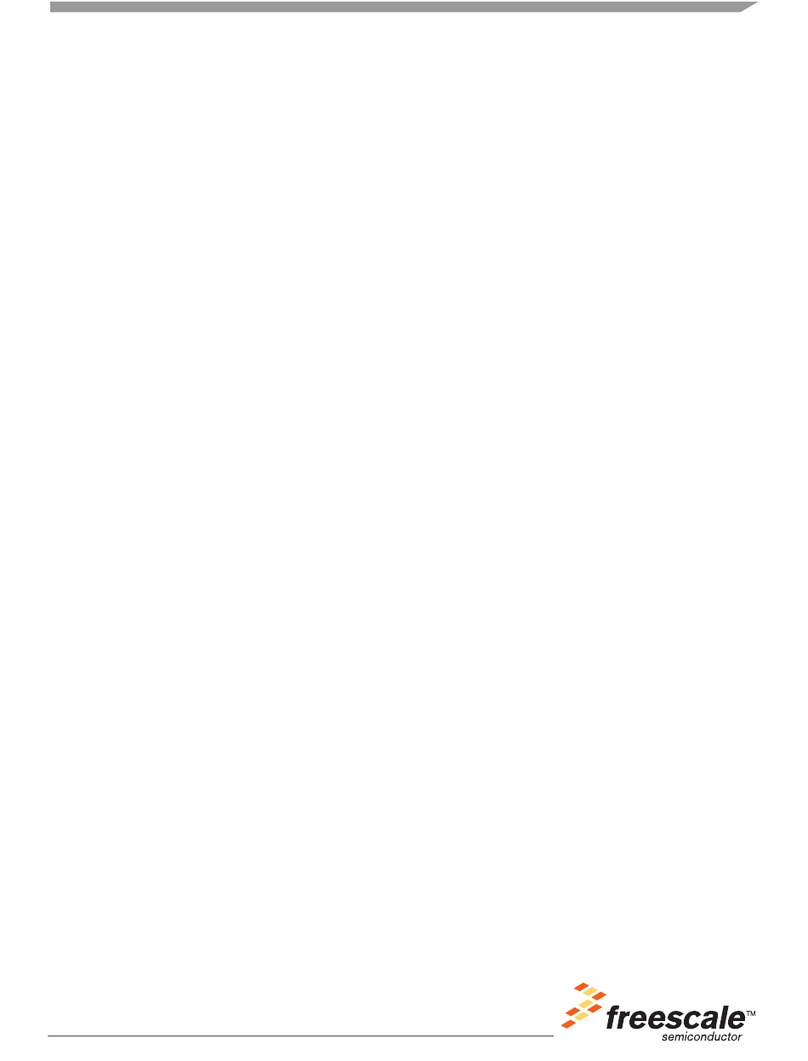
Freescale Semiconductor
Freescale Semiconductor MC33794 Setup instructions
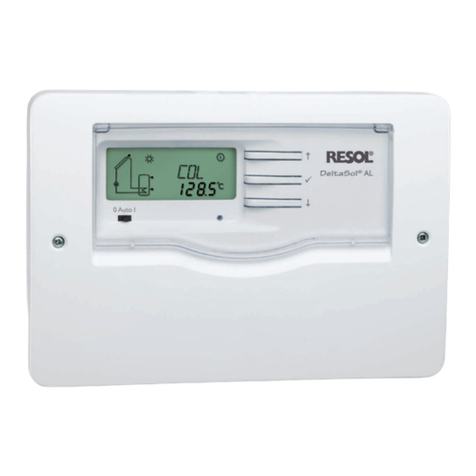
Resol
Resol DeltaSol AL Installation instructions manual

Lumisys
Lumisys LRP user guide

Mitsubishi Electric
Mitsubishi Electric FX3U-J1939 installation manual
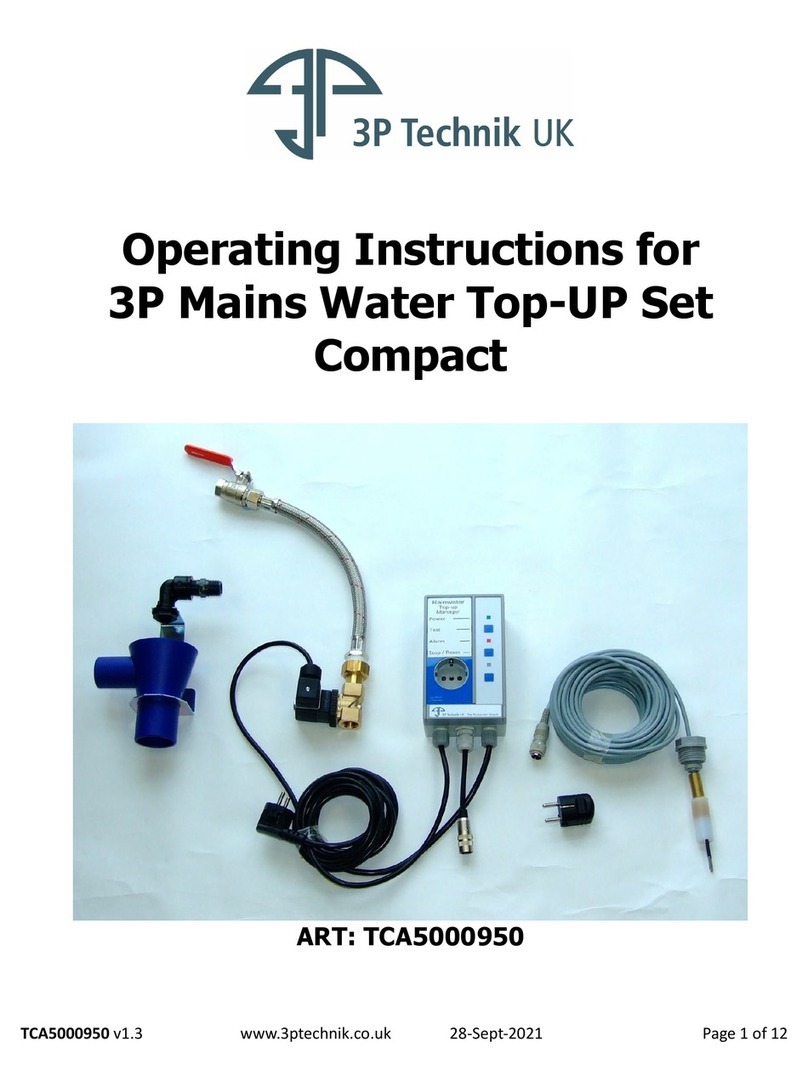
3P Technik
3P Technik TCA5000950 operating instructions
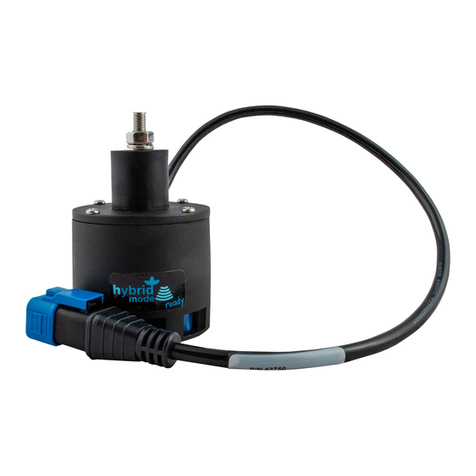
Norac
Norac UC5 Topcon X30 installation manual
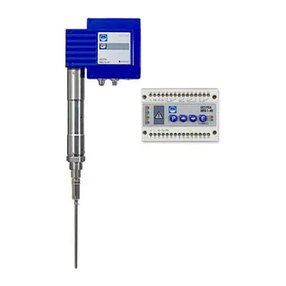
GESTRA
GESTRA NRS 1-40 Original installation manual