Haas Mill User manual

HAAS AUTOMATION INC. • 2800 STURGIS ROAD • OXNARD, CA 93030
TEL. 888-817-4227 FAX. 805-278-8561
www.HaasCNC.com
96-8000 revR
Mill
Operator’s
Manual
Mill Operator’s Manual
EC1600
EC 300
EC 500
JUNE 2007

I
TableOfContents
96-8000 rev R June 2007
LIMITEDWARRANTYCOVERAGE
All new Haas mills are warranted exclusively by the Haas Automation’s ("Manufacturer") limited warranty as follows:
Each Haas CNC machine ("Machine") and its components ("Components") (except those listed below under limits and
exclusions) is warranted against defects in material and workmanship for a period of one (1) year (except Tooroom Mills
and Mini-Mills, which are six (6) months) from the date of purchase, which is the date that a machine is installed at the
end user. The foregoing is a limited warranty and it is the only warranty by manufacturer. Manufacturer disclaims all other
warranties, express or implied, including but not limited to all warranties of merchantability and fitness for a particular
purpose.
REPAIRORREPLACEMENTONLY: MANUFACTURER'SLIABILITYUNDERTHISAGREEMENTSHALLBELIMITED TO
REPAIRINGOR REPLACING,ATTHEDISCRETIONOFMANUFACTURER,PARTS, OR COMPONENTS.
An additional warranty extension may be purchased from your authorized Haas distributor.
LIMITS and EXCLUSIONS of WARRANTY
Except as provided above, buyer agrees that all warranties express or implied, as to any matter whatsoever, including but
not limited to warranties of merchantability and fitness for a particular purpose are excluded.
Components subject to wear during normal use and over time such as paint, window finish and condition, light bulbs,
seals, chip removal system, etc., are excluded from this warranty.
Factory-specified maintenance procedures must be adhered to and recorded in order to maintain this warranty.
This warranty is void if the machine is subjected to mishandling, misuse, neglect, accident, improper installation, improper
maintenance, or improper operation or application, or if the machine was improperly repaired or serviced by the customer
or by an unauthorized service technician. Warranty service or repair service is available from the authorized Haas distributor.
Withoutlimitingthe generalityofanyoftheexclusionsor limitationsdescribedinotherparagraphs,manufacturer'swarranty doesnotincludeanywarrantythatthe machineorcomponentswillmeetbuyer's
productionspecificationsor otherrequirementsorthat operationofthemachine andcomponentswillbe uninterruptedorerror-free.Manufacturerassumesnoresponsibility withrespecttothe useofthe
MachineandComponents byBuyer,andmanufacturer shallnotincuranyliabilityorSeller toBuyerforany failureindesign, production,operation,performanceor otherwiseoftheMachine or
Componentsotherthan repairorreplacementofsameasset forthintheLimitedWarrantyabove.Manufacturer isnotresponsibleforanydamageto parts,machines,businesspremisesorotherproperty
ofBuyer,orfor anyotherincidental orconsequentialdamages thatmaybe causedbya malfunctionoftheMachineorComponents.
LIMITATION OFLIABILITYAND DAMAGES:MANUFACTURERISNOTLIABLETOBUYER,SELLER ORANYCUSTOMER OF
BUYER FOR LOSS OF PROFITS, LOST DATA, LOST PRODUCTS, LOSS OF REVENUE, LOSS OF USE, COSTOF DOWN
TIME,BUSINESSGOODWILL, ORANY OTHER INCIDENTALOR CONSEQUENTIALDAMAGE, WHETHER INANACTIONIN
CONTRACT OR TORT,ARISING OUT OF OR RELATEDTOTHE MACHINE OR COMPONENTS, OTHER PRODUCTS OR
SERVICESPROVIDED BY MANUFACTURER OR SELLER, ORTHEFAILUREOF PARTSOR PRODUCTS MADE BYUSING
THEMACHINEORCOMPONENTS, EVEN IF MANUFACTURER ORSELLERHASBEENADVISED OFTHE POSSIBILITYOF
SUCHDAMAGES.MANUFACTURER'SLIABILITYFORDAMAGESFORANYCAUSEWHATSOEVERSHALLBELIMITEDTO
REPAIROR REPLACEMENT,ATTHEDISCRETIONOFMANUFACTURER, OFTHEDEFECTIVEPARTS,COMPONENTSOR
MACHINE.
Buyer has accepted this restriction on its right to recover incidental or consequential damages as part of its bargain with
Seller. Buyer realizes and acknowledges that the price of the equipment would be higher if Seller or Manufacturer were
required to be responsible for incidental or consequential damages, or punitive damages.
ThisWarrantyCertificatesupersedes anyandallother agreements,eitheroralorin thiswriting,betweenthe partiesheretowithrespectto thewarranties,limitationsof liabilityand/ordamagesregarding
theMachineor Components,andcontainsallofthecovenants andagreementsbetween thepartieswithrespecttosuchwarranties, liabilitylimitationsand/or damages.EachpartytothisWarranty
Certificateacknowledgesthatnorepresentations, inducements,promises,oragreements,orally orotherwise,havebeenmadebyanyparty,oranyoneactingonbehalfofanyparty,whichare notembodied
hereinregardingsuchwarranties, liabilitylimitationsand/ordamages, andthatnoother agreement, statement,orpromisenot containedinthisWarranty Certificateshallbevalidor bindingregarding
suchwarranties,liability limitationsanddamages.
TRANSFERABILITY
This warranty is transferrable from the original end-user to another party if the machine is sold via private sale before the
end of the warranty period.
Warranty Certificate
CoveringHaasAutomation, Inc.,CNCEquipment
EffectiveJanuary1, 2003
HaasAutomation, Inc.2800Sturgis Road,Oxnard,CA93030-8933 Phone:(805) 278-1800 FAX:(805)278-8561

II 96-8000 rev R June 2007
Table OfContents
Warranty Registration
Certificate
LIMITED WARRANTY COVERAGE
Allnew Haasmills arewarranted exclusivelyby theHaasAutomation’s("Manufacturer") limited warrantyas follows:
Each Haas CNC machine ("Machine") and its components ("Components") (except those listed below under limits
andexclusions) iswarranted againstdefects inmaterial and workmanshipfor aperiod ofone (1)year (except
Tooroom Mills and Mini-Mills, which are six (6) months) from the date of purchase, which is the date that a machine
is installed at the end user.The foregoing is a limited warranty and it is the only warranty by manufacturer. Manufac-
turer disclaims all other warranties, express or implied, including but not limited to all warranties of merchantability
andfitness fora particular purpose.
REPAIR OR REPLACEMENT ONLY:MANUFACTURER'SLIABILITYUNDERTHISAGREEMENTSHALL
BELIMITEDTOREPAIRINGORREPLACING,ATTHE DISCRETIONOFMANUFACTURER,PARTS,OR
COMPONENTS.
Anadditional warrantyextension maybepurchased fromyour authorizedHaasdistributor.
LIMITS and EXCLUSIONS of WARRANTY
Exceptas providedabove, buyeragrees thatallwarranties expressor implied,as toany matterwhatsoever,includ-
ingbut not limited to warrantiesof merchantabilityand fitnessfor aparticular purposeare excluded.
Componentssubject to wearduring normaluse andover time such as paint,window finishand condition,light bulbs,
seals, chip removal system, etc., are excluded from this warranty.
Factory-specifiedmaintenance proceduresmust beadheredto andre corded inorderto maintain thiswarranty.
This warranty is void if the machine is subjected to mishandling, misuse, neglect, accident, improper installation,
impropermaintenance, orimproperoperation orapplication, or ifthe machinewasimproperly repairedorserviced by
thecustomer orby anunauthorizedservice technician.Warranty serviceorrepair serviceis availablefromthe
authorizedHaas distributor.
Withoutlimiting thegenerality ofany ofthe exclusionsor limitationsdescribed inother paragraphs,manufacturer's
warrantydoes notinclude any warranty that the machine orcomponents willmeet buyer'sproduction specifications
orother requirementsorthat operationofthe machineandcomponents willbeuninterrupted orerror-free.Manufac-
turer assumes no responsibility with respect to the use of the Machine and Components by Buyer, and manufacturer
shallnot incurany liabilityor Sellerto Buyerfor anyfailure indesign, production,operation, performanceor other-
wise of the Machine or Components other than repair or replacement of same as set forth in the Limited Warranty
above.Manufacturer isnot responsiblefor anydamageto parts,machines, businesspremises orotherproperty of
Buyer, or for any other incidental or consequential damages that may be caused by a malfunction of the Machine or
Components.
LIMITATION OF LIABILITYAND DAMAGES:MANUFACTURERIS NOTLIABLETOBUYER,SELLER
ORANYCUSTOMER OFBUYER FOR LOSSOF PROFITS,LOSTDATA,LOSTPRODUCTS,LOSS OFREV-
ENUE,LOSS OFUSE, COSTOF DOWNTIME, BUSINESSGOOD WILL,ORANYOTHER INCIDENTALOR
CONSEQUENTIALDAMAGE, WHETHERINANACTION INCONTRACTORTORT,ARISINGOUTOFORRE-
LATEDTOTHE MACHINEORCOMPONENTS,OTHER PRODUCTS ORSERVICESPROVIDEDBYMANUFAC-
TUREROR SELLER,ORTHEFAILUREOF PARTSORPRODUCTS MADEBYUSINGTHE MACHINEOR COM-
PONENTS,EVEN IFMANUFACTUREROR SELLERHASBEENADVISED OF THEPOSSIBILITYOF SUCH
DAMAGES.MANUFACTURER'S LIABILITYFOR DAMAGESFORANYCAUSEWHATSOEVERSHALLBE
LIMITEDTO REPAIRORREPLACEMENT,ATTHE DISCRETIONOFMANUFACTURER,OFTHEDEFECTIVE
PARTS,COMPONENTS OR MACHINE.

III
Table OfContents
96-8000 rev R June 2007
Buyer has accepted this restriction on its right to recover incidental or consequential damages as part of its
bargainwith Seller.Buyer realizesand acknowledgesthat theprice oftheequipment wouldbe higherif Selleror
Manufacturerwere requiredtobe responsible forincidentalor consequentialdamages,or punitivedamages.
ThisWarranty Certificatesupersedes anyand allother agreements,either oralor inthis writing,between the
partieshereto withrespect tothe warranties,limitations ofliability and/ordamages regardingthe Machineor
Components,and containsall ofthe covenantsand agreementsbetween theparties withrespect tosuch
warranties, liability limitations and/or damages. Each party to this Warranty Certificate acknowledges that no
representations,inducements,promises,or agreements,orally or otherwise,have beenmade byany party,or
anyoneacting onbehalf ofany party,which arenot embodiedherein regardingsuch warranties,liabilitylimita-
tions and/or damages, and that no other agreement, statement, or promise not contained in this Warranty
Certificateshall bevalid orbindingregarding suchwarranties, liabilitylimitations and damages.
TRANSFERABILITY
Thiswarranty istransferrable fromtheoriginal end-userto anotherparty ifthemachine issold viaprivate sale
beforethe endofthe warrantyperiod.
Shouldyou have aproblem withyour machine,please consultyour operator'smanual first. If this doesnot
resolve the problem, call your authorized Haas distributor.As a final solution, call Haas directly at the number
indicatedbelow.
HaasAutomation, Inc.
2800 Sturgis Road
Oxnard, California 93030-8933 USA
Phone: (805) 278-1800
FAX: (805) 278-8561
In order to record the end-user of this machine for updates and for product safety notices, we must have the
machineregistrationreturned immediately. Please filloutcompletelyand mailtotheabove addresstoATTENTION
(VF-1,GR-510, VF-6,etc.—whichever isapplicable)REGISTRATIONS.Please include a copy of your invoice
tovalidate yourwarranty dateandto coverany additionaloptionsyou mayhave purchased.
Company Name:Company Name:
Company Name:Company Name:
Company Name: __________________________________________________________
__________________________________________________________
_____________________________ Contact Name:Contact Name:
Contact Name:Contact Name:
Contact Name: ________________________________________________
________________________________________________
________________________
Address:Address:
Address:Address:
Address:__________________________________________________________________________________________________________________________________________________________________
__________________________________________________________________________________________________________________________________________________________________
_________________________________________________________________________________
______________________________________________________________________________________________________________________________________________________________________________________
______________________________________________________________________________________________________________________________________________________________________________________
___________________________________________________________________________________________
______________________________________________________________________________________________________________________________________________________________________________________
______________________________________________________________________________________________________________________________________________________________________________________
___________________________________________________________________________________________
Dealer:Dealer:
Dealer:Dealer:
Dealer:________________________________________________________________________________
________________________________________________________________________________
________________________________________ Date Installed:Date Installed:
Date Installed:Date Installed:
Date Installed: ________________________________________________
________________________________________________
________________________
Model No.Model No.
Model No.Model No.
Model No.
::
::
:________________________________________________________________________
________________________________________________________________________
____________________________________ Serial Number:Serial Number:
Serial Number:Serial Number:
Serial Number: ________________________________________________
________________________________________________
________________________
Telephone: (Telephone: (
Telephone: (Telephone: (
Telephone: ( ______
______
___ ))
))
) ______________________________________________________
______________________________________________________
___________________________ FAX: (FAX: (
FAX: (FAX: (
FAX: ( __________
__________
_____))
))
)______________________________________________________
______________________________________________________
___________________________
IMPORIMPOR
IMPORIMPOR
IMPORTT
TT
TANT NOANT NO
ANT NOANT NO
ANT NOTICE!!! PLEASE READ IMMEDIATICE!!! PLEASE READ IMMEDIA
TICE!!! PLEASE READ IMMEDIATICE!!! PLEASE READ IMMEDIA
TICE!!! PLEASE READ IMMEDIATELTEL
TELTEL
TELY!!!Y!!!
Y!!!Y!!!
Y!!!
This machine is equipped with an electronically-recorded serial number that cannot be altered. This is done to
protectyou in caseoftheftand totrackmachineswhen soldtoother owners.Afterapproximately800 hoursofuse,
the machine will automatically shut down if it has not been electronically unlocked by the Haas Factory Outlet. To
unlockthemachine, wemusthavetheabove registrationwiththeserial number.You willreceiveanumber fromthe
Haas Factory Outlet that you will write in over the serial number on the setting page (#26). If, for any reason, the
serial number of the machine is erased in memory, the machine will revert back to a 200 hour limit for your
protection.

IV 96-8000 rev R June 2007
Table OfContents
CustomerSatisfactionProcedure
Dear Haas customer,
Your complete satisfaction and goodwill are of the utmost importance to both Haas Automation, Inc.,
and the Haas distributor where you purchased your equipment. Normally, any concerns you may have
about the sales transaction or the operation of your equipment will be rapidly resolved by your
distributor.
However, if your concerns are not resolved to your complete satisfaction, and you have discussed your
concerns with a member of the dealership’s management, the General Manager or the dealership’s owner
directly, please do the following:
Contact Haas Automation’s Customer Service Center by calling 800-331-6746 and ask for the Customer
Service Department. So that we may resolve your concerns as quickly as possible, please have the
followinginformation availablewhenyou call:
• Your name, company name, address and phone number
• The machine model and serial number
• The dealership name, and the name of your latest contact at the dealership
• The nature of your concern
If you wish to write Haas Automation, please use this address:
Haas Automation, Inc.
2800Sturgis Road
Oxnard,CA93030
Att: Customer Satisfaction Manager
e-mail:[email protected]
Once you contact the Haas Automation Customer Service Center, we will make every effort to work
directly with you and your distributor to quickly resolve your concerns. At Haas Automation, we know
that a good Customer-Distributor-Manufacturer relationship will help ensure continued success for all
concerned.
Customer Feedback
If you have any concerns or questions in regards to the Haas Operator’s manual, please contact us via our
AllHaas CNCmachine toolscarry theETL Listed
mark,certifying thatthey conform to the NFPA79
Electrical Standard for Industrial Machinery and
theCanadianequivalent, CAN/CSA C22.2No.73.
TheETLListedandcETLListedmarksareawarded
to products that have successfully undergone
testing by Intertek Testing Services (ITS), an
alternativeto Underwriters’Laboratories.
The ISO 9001:2000 certification from TUV
ManagementService (anISO registrar)serves as
animpartialappraisalof HaasAutomation’squality
management system. This achievement affirms
HaasAutomation’sconformancewiththestandards
set forth by the International Organization for
Standardization, and acknowledges the Haas
commitmenttomeetingtheneedsandrequirements
of its customers in the global marketplace.
Certification

V
Table OfContents
96-8000 rev R June 2007
The Information contained in this manual is constantly being updated.
The latest updates, and other helpful information is available online as a
free download in .pdf format (go to www.HaasCNC.com and click on
“Manual Updates” under the “Customer Services” drop-down menu in
the navigation bar).
Table of Contents
SAFETY ................................................................................................................................................................... 4
OPERATION ............................................................................................................................................................ 9
PENDANT KEYBOARD INTRODUCTION ............................................................................................................. 11
FUNCTION KEYS ........................................................................................................................................ 12
JOG KEYS ................................................................................................................................................ 12
OVERRIDE KEYS ....................................................................................................................................... 13
DISPLAY KEYS ........................................................................................................................................... 14
CURSOR KEYS .......................................................................................................................................... 15
ALPHA KEYS ............................................................................................................................................. 15
MODE KEYS ............................................................................................................................................. 16
NUMERIC KEYS ......................................................................................................................................... 17
POSITION DISPLAYS .................................................................................................................................... 17
OFFSETS DISPLAY ...................................................................................................................................... 18
CURRENT COMMANDS DISPLAY ..................................................................................................................... 18
ALARMS / MESSAGES DISPLAY ...................................................................................................................... 19
SETTING / GRAPHIC DISPLAY FUNCTION ......................................................................................................... 20
DATE AND TIME ......................................................................................................................................... 21
SCREEN SAVER......................................................................................................................................... 21
HELP / CALCULATOR FUNCTION .................................................................................................................... 21
SPINDLE WARM-UPPROGRAM ..................................................................................................................... 24
RUN-STOP-JOG-CONTINUE .......................................................................................................................... 24
COOLANT LEVEL GAUGE ............................................................................................................................. 25
OPTIONS .................................................................................................................................................. 25
RJH-ESCREENS ...................................................................................................................................... 28
PROGRAMMING ................................................................................................................................................... 31
MACHINE POWER-UP................................................................................................................................. 31
PROGRAMMING INTRODUCTION ..................................................................................................................... 31
ALPHABETICAL ADDRESS CODES .................................................................................................................. 38
PART SETUP............................................................................................................................................. 38
TOOLING ................................................................................................................................................. 39
TOOL CHANGER ........................................................................................................................................ 40
JOG MODE .............................................................................................................................................. 48
PALLET CHANGER (EC-SERIES AND MDC-500) ............................................................................................. 56
TIPS AND TRICKS ...................................................................................................................................... 62

VI 96-8000 rev R June 2007
Table OfContents
This manual and all of its contents are copyright protected 2007, and may not be reproduced without written
permissionfrom HaasAutomation, Inc.
INTUITIVE PROGRAMMING SYSTEM (IPS) ......................................................................................................... 65
INTRODUCTION .......................................................................................................................................... 65
AUTOMATIC MODE ...................................................................................................................................... 65
SYSTEM MODE .......................................................................................................................................... 65
SUBROUTINES ..................................................................................................................................................... 68
LOCAL SUBROUTINES ................................................................................................................................68
SUBROUTINE CANNED CYCLE EXAMPLE ......................................................................................................... 69
SUBROUTINES WITH MULTIPLE FIXTURES ...................................................................................................... 69
ADVANCED EDITOR ............................................................................................................................................. 70
THE PROGRAM MENU ................................................................................................................................70
THE EDIT MENU ....................................................................................................................................... 71
THE SEARCH MENU .................................................................................................................................. 71
THE MODIFY MENU ................................................................................................................................... 71
THE I/O MENU......................................................................................................................................... 72
THE F1: HELP MENU ................................................................................................................................72
ADVANCED EDITOR SHORTCUTS ................................................................................................................... 73
QUICKCODE ........................................................................................................................................................ 74
VISUAL QUICK CODE ................................................................................................................................. 79
CUTTERCOMPENSATION.................................................................................................................................... 80
ENTRY AND EXIT FROM CUTTER COMPENSATION ............................................................................................... 81
FEED ADJUSTMENTS IN CUTTER COMPENSATION .............................................................................................. 81
MACROS ............................................................................................................................................................... 83
INTRODUCTION .......................................................................................................................................... 83
OPERATION NOTES ..................................................................................................................................... 84
SYSTEM VARIABLES IN-DEPTH ...................................................................................................................... 89
VARIABLE USAGE ....................................................................................................................................... 93
ADDRESS SUBSTITUTION ............................................................................................................................ 94
G65 MACRO SUBROUTINE CALL ................................................................................................................101
COMMUNICATION WITH EXTERNAL DEVICES - DPRNT[ ] .................................................................................102
FANUC-STYLE MACRO FEATURES NOT INCLUDED INHAAS CNC CONTROL .........................................................104
4TH AND 5TH AXIS PROGRAMMING .................................................................................................................105
CREATING FIVE-AXIS PROGRAMS .................................................................................................................105
INSTALLING AN OPTIONAL FOURTH AXIS........................................................................................................107
INSTALLING AN OPTIONAL FIFTH AXIS ...........................................................................................................108
AUXILIARY AXIS .......................................................................................................................................108
DISABLEING THE AXES ..............................................................................................................................109
GCODES(PREPARATORYFUNCTIONS)............................................................................................................ 111
MCODES(MISCELLANEOUSFUNCTIONS) .......................................................................................................167
SETTINGS............................................................................................................................................................175
MAINTENANCE ....................................................................................................................................................193
INDEX...................................................................................................................................................................207

96-8000 rev R June 2007 Safety 1
HAAS SAFETY PROCEDURES
THINK SAFETY!
DON’TGET CAUGHT UP
INYOUR WORK
Allmilling machines containhazards fromrotating
parts, belts and pulleys, high voltage electricity,
noise, and compressed air. When using CNC
machines and their components, basic safety
precautionsmust alwaysbe followedto reducethe
riskof personalinjury andmechanicaldamage.
Important – This machine to be operated only
by trained personnel in accordance with the
Operator’s manual, safety decals, safety
procedures and instructions for safe machine
operation.
SafSaf
SafSaf
Safety Contentsety Contents
ety Contentsety Contents
ety Contents
USESAND GUIDELINES FORPROPER MACHINE OPERATION ........................................................................... 4
MODIFICATIONSTOTHEMACHINE ....................................................................................................................... 4
SAFETYPLACARDS............................................................................................................................................... 4
MILLWARNINGDECALS ........................................................................................................................................ 6
DECLARATIONOF WARNINGS, CAUTIONS,ANDNOTES ..................................................................................... 6
LATHEWARNING DECALS..................................................................................................................................... 7

2Safety 96-8000 rev R June 2007
READ BEFORE OPERATING THIS MACHINE:
♦Only authorized personnel should work on this machine. Untrained personnel present a hazard to
themselves and the machine, and improper operation will void the warranty.
♦Check for damaged parts and tools before operating the machine. Any part or tool that is damaged should be
properlyrepaired orreplaced byauthorized personnel. Do notoperate themachine ifany component doesnot
appearto befunctioning correctly. Contactyour shopsupervisor.
♦Useappropriate eyeandear protectionwhileoperating themachine. ANSI-approved impactsafetygogglesand
OSHA-approvedear protectionarerecommended toreduce therisksof sightdamage and hearingloss.
♦Donot operatethe machineunless thedoors areclosed andthe doorinterlocks arefunctioning properly.
Rotating cutting tools can cause severe injury. When a program is running, the mill table and spindle head can
move rapidly at any time in any direction.
♦The Emergency Stop button (also known as an Emergency Power Off button) is the large, circular red switch
located on the Control Panel. Pressing the Emergency Stop button will instantly stop all motion of the machine, the
servo motors, the tool changer, and the coolant pump. Use the Emergency Stop button only in emergencies to avoid
crashingthe machine.
♦The electrical panel should be closed and the three latches on the control cabinet should be secured at all times
except during installation and service. At those times, only qualified electricians should have access to the panel.
When the main circuit breaker is on, there is high voltage throughout the electrical panel (including the circuit boards
andlogic circuits)and somecomponentsoperate athigh temperatures.Therefore, extremecautionis required.
Once the machine is installed, the control cabinet must be locked and the key available only to qualified service
personnel.
♦♦
♦♦
♦DO NOT modify or alter this equipment in any way. If modifications are necessary, all such requests must be
handled by HaasAutomation, Inc. Any modification or alteration of any Haas Milling orTurning Center could lead to
personalinjury and/ormechanicaldamage andwillvoid yourwarranty.
♦Itis theshop owner’sresponsibility to make sure that everyone who is involvedin installingand operatingthe
machineis thoroughlyacquainted withthe installation,operation,and safetyinstructions providedwith themachine
BEFORE they perform any actual work. The ultimate responsibility for safety rests with the shop owner and the
individualswho workwiththe machine.
♦♦
♦♦
♦Thismachine isautomaticallycontrolled andmay startat anytime.
♦♦
♦♦
♦Thismachine cancause severebodilyinjury.
♦♦
♦♦
♦Do not operate with the doors open.

96-8000 rev R June 2007 Safety 3
♦♦
♦♦
♦Avoidentering themachineenclosure.
♦♦
♦♦
♦Do not operate without proper training.
♦♦
♦♦
♦Alwayswearsafetygoggles.
♦♦
♦♦
♦Never place your hand on the tool in the spindle and pressATC FWD,ATC REV,
NEXT TOOL, or cause a tool change cycle. The tool changer will move in and
crushyourhand.
♦♦
♦♦
♦To avoidtool changer damage, ensurethat tools areproperlyaligned with the
spindledrive lugswhen loadingtools.
♦♦
♦♦
♦Theelectrical power mustmeet thespecifications in thismanual. Attempting to
runthe machine fromanyother sourcecancause severe damageand will voidthe
warranty.
♦♦
♦♦
♦DO NOT press POWER UP/RESTART on the control panel until after the
installationiscomplete.
♦♦
♦♦
♦DONOTattempt tooperatethe machine beforeall of theinstallation instructions
havebeencompleted.
♦♦
♦♦
♦NEVER service the machine withthe power connected.
♦♦
♦♦
♦Improperlyclamped partsmachined athighspeeds/feedsmaybeejectedand
puncturethe safety door. Machining oversized ormarginally clamped partsisnot
safe.
♦♦
♦♦
♦Windowsmust bereplacedif damagedor severelyscratched -Replacedamaged
windowsimmediately.
♦♦
♦♦
♦Donot process toxicor flammablematerial. Deadly fumescan bepresent. Consult
materialmanufacturer forsafe handlingof materialby-products beforeprocessing.
OBSERVE ALL OF THE WARNINGS AND CAUTIONS BELOW:

4Safety 96-8000 rev R June 2007
USESAND GUIDELINESFOR PROPERMACHINE OPERATION
All milling machines contain hazards from rotating cutting tools, belts and pulleys, high voltage electricity,
noise, and compressed air. When using milling machines and their components, basic safety precautions
should always be followed to reduce the risk of personal injury and mechanical damage. READ ALL APPRO-
PRIATE WARNINGS, CAUTIONS,AND INSTRUCTIONS BEFORE OPERATING THIS MACHINE.
MODIFICATIONS TO THE M ACHINE
DO NOT modify or alter this equipment in any way. If modifications are necessary, all such requests must be
handled by HaasAutomation, Inc. Any modification or alteration of any Haas machining center could lead to
personalinjury and/ormechanicaldamage andwillvoid yourwarranty.
SAFETY P LACARDS
Tohelp ensurethat CNCtool dangers arequickly communicatedand understood,hazard symboldecals areplaced on
HaasMachines inlocations wherehazards exist.If decalsbecome damagedorworn, orif additionaldecals areneeded
to emphasize a particular safety point, contact your dealer or the Haas factory. Never allow anyone to alter or
remove any safety decal or symbol.
Each hazard is defined and explained on the general safety decal, located at the front of the machine. Particular loca-
tionsof hazardsare markedwithwarning symbols.Review andunderstand thefourparts ofeach safetywarning, ex-
plainedbelow, andfamiliarize yourselfwith thesymbols on thefollowing pages.

96-8000 rev R June 2007 Safety 5

6Safety 96-8000 rev R June 2007
DECLARATION OF W ARNINGS, CAUTIONS, AND N OTES
Throughoutthis manual,importantand criticalinformationis prefacedwith the word“Warning”, “Caution”and“Note”
Warnings are used when there is an extreme danger to the operator and/or to the machine. Take all steps neces-
sary to heed the warning given. Do not continue if you cannot follow the warning instructions.An example warning is:
WARNING!
NEVER PUT HANDS BETWEEN TOOL CHANGER AND SPINDLE HEAD.
Cautions areused whenthere isthe potential forminor personalinjury ormechanical damage, forexample:
CAUTION!Powerdown themachinebefore performinganymaintenance tasks.
Notes giveadditional informationtothe operatorabouta particularstep or procedure.This informationshouldbe
taken into consideration by the operator as the step is performed to ensure there is no confusion, for example:
NOTE: If machine is equipped with the optional extended Z-clearance table, follow
these guidelines:
• Avoid extreme loads on the center of table or far end of table. The weight
of the part should be distributed evenly over the table or one pad.
• Flatness of part should be within 0.002".
MILL W ARNING D ECALS

96-8000 rev R June 2007 Safety 7
LATHE W ARNING D ECALS

8Safety 96-8000 rev R June 2007

9
Introduction
96-8000 rev R June 2007
OPERATION
The following is a visual introduction to a HAAS mill. Some of the features shown will be highlighted in their
appropriatesections.
5
6
8
9
11
14
7
10
12
13
15
16
17
19
18
20HP
GEAR DRIVE
2-SPEED
10,000
RPM
Floppy Disk Drive
Air Gun
Clip Board
Key Memory Lock
Work Light Switch
(GFI Protected)
G & M Code
Reference List
Work Beacon
Run/Setup Mode Key
Switch
USB Memory Device
(See
Detail A)
Vise Handle
Holder
Tool Tray
Tool Changer
(Umbrella Type)
Side Mount
Tool Changer
(SMTC)
Window
Work Light (2)
Spindle
Control Pendant
Tool Crib
Table
Operator Door (2)
Tool Holding Vise
Chip Chute
Coolant Tank
Assembly
Chip Basket
Optional
P-Cool
Assembly
Coolant Nozzles
SMTC
Double Arm
Optional
Second
Home
Switch
Window
Closed
Position
Window
Open
Position
Push in
Pull up
Pull down
to Lock in
Place
1
2
3
Beeper
View Rotated 90 CW8
Tool Release Button
Operator
Manual &
Assembly
Data
Remote Jog Control
O
I
USB
MEMORY
WORK LIGHT
GFI
PROTECTED
LOCK
RUN
RUN
HOLD TO
SETUP
MODE MODE
Detail A
Hold to Run Button
(Some Features are Optional)

10 Introduction 96-8000 rev R June 2007

11
Introduction
96-8000 rev R June 2007
PENDANT K EYBOARD I NTRODUCTION
The keyboard is broken up into eight sections: Function Keys, Jog Keys, Override Keys, Display Keys, Cursor
Keys,Alpha Keys, Mode Keys and Number Keys. In addition there are miscellaneous keys and features
locatedon the pendant and keyboard which aredescribed briefly.
PARAM SETNG
GRAPH
HELP
CALC
NEXT
TOOL
RELEASE
TOOL
PART
ZERO
SET
TOOL
OFFSET
MEASURE
MESGS
ALARM
DGNOS
POSIT
OFFSET
COMDS
PRGRM
CONVRS
DISPLAY
CURNT
OVERRIDES
PAGE
AUX
CLNT
CLNT
CHIP
CHIP
CHIP
FWD
STOP
REV
DOWN
UP
CLNT
789
4
1
-
CANCEL
5
2
0
SPACE
6
3
WRITE
ENTER
JOG
LOCK
+B
SHIFT
SHIFT EDCBA
K
Q
W
)
J
P
V
(
I
O
U
EOB
H
N
T
Z
G
M
S
Y
F
L
R
X
100% +10
HAND
CW
STOP
CCW
SPINDLE
CNTRL
FEED
FEED RATE
FEED RATE
FEED RATE
-10 100% +10
SPINDLE
HAND
CNTRL
SPIN
SPINDLE SPINDLE
RAPID
5%
RAPID RAPID RAPID
25% 50% 100%
INSERT ALTER
DELETE
UNDO
SINGLE DRY
OPTION
BLOCK
BLOCK RUN
STOP
DELETE
COOLNT
ORIENT
SPINDLE
ATC
ATC
FWD
REV
.0001 .001
.01
.1
.1 1.
10.
100.
ALL
ORIGIN
SINGL
HOME
G28
SELECT SEND
RECV
ERASE
PROG PROG
EDIT
MEM
MDI
DNC
HAND
ZERO
LIST
JOG
RET
PROG
F1 F2 F3 F4
POWER
UP
RESTART
RECOVER
+A
-A
-B
-Z
+Y
+Z -Y
+X -X
&
@:
%
*
+
/
$
,
=
[
!
?
#
]
-10
UP
HOME
END
DOWN
PAGE
SHIFT
&
@:
%
*
+
/
$
,
=
[
!
?
#
]
CURSOR
RESET
Power On- Turns the machine on.
Power Off-Turns themachine off.
Spindle Load Meter - Displays the spindle load, in percent.
Emergency Stop - This stops all axes motion, stops the spindle and tool changer, and turns off the coolant
pump.
Jog Handle - This is used to jog all axes. Can also be used to scroll through program code or menu items
whileediting.
Cycle Start - Starts a program. This button is also used to start a program in Graphics mode.
Feed Hold - Will stop all axis motion. Note: Spindle will continue to turn during cutting.
Reset - Will stop the machine (axes, spindle, coolant pump, and tool changer are stopped). This is not a
recommended method to stop the machine, as it may be difficult to continue from that point.
Power Up / Restart - When this key is pressed, the axes will return to the machine zero position and a tool
change may occur. See Setting 81 in the Settings chapter for more information.
Recover - This button aids the operator in recovering the tool changer from an abnormal stop. See the tool
changersection formore information.

12 Introduction 96-8000 rev R June 2007
Memory Lock Key Switch - This switch prevent the operator from editing programs and from altering settings
when turned to the locked position. The following describes the hierarchy of locks:
Key switch locks Settings and all programs.
Setting 7 locks parameters.
Setting 8 locks all programs.
Setting 23 locks 9xxx programs.
Setting 119 locks offsets.
Setting120 locks macrovariables.
Second Home Button - This button will rapid all axes to the coordinates specified in work Offset G129. The
sequence is as follows: First, the Z axis is returned to machine zero, then the X and Y axes are moved, then
the Z axis is moved to its second home position. This feature will work in any mode except DNC.
Work Light Switch - This switch will turn on the work light inside of the machine.
Keyboard Beeper - Located at the top of the parts tray. The volume can be adjusted by turning the cover.
FUNCTION K EYS
F1- F4 Keys - Thesebuttons havedifferent functionsdepending uponwhich modeof operationyou arein. For
example, F1-F4 will cause a different action in Editing mode, than Program mode, than Offset mode. See the
specific mode section for further descriptions and examples.
Tool Offset Meas (Tool Offset Measure) - Used to record tool length offsets during part setup.
Next Tool - Used to select the next tool from the tool changer (usually used during part setup).
Tool Release - Releases the tool from the spindle when in MDI mode, zero return mode, or handle jog mode.
Part Zero Set - Used to automatically set work coordinate offsets during part setup (see Setting Offsets in the
Operationsection).
JOG K EYS
Chip FWD (ChipAuger Forward)- Starts optional chipauger inthe “Forward”direction, moving chips outof the
machine.
Chip Stop (ChipAuger Stop) - Stops augermovement.
Chip REV (ChipAuger Reverse) - Starts the optional chip auger in the “Reverse” direction, which is useful in
clearing jams and debrisfrom auger.
X/-X,Y/-Y,Z/-Z,A/-A andB/-B (axis keys)-Allows the operator to manually jog axis by holding down the
individual button or pressing the desired axes and using the jog handle.
Jog Lock - Works with the axes buttons. Press jog lock and then an axis button and the axis will move to
maximum travel or until jog lock is pressed again.
CLNT Up (CoolantUp) -Moves theoptional ProgrammableCoolant (P-Cool)nozzle up.
CLNT Down (Coolant Down) - Moves the optionalP-Cool nozzledown.
AUX CLNT (Auxiliary Coolant) - Pressing this key while in MDI mode will turn on the optional Through the
Spindle Coolant (TSC) system; pressing it a second time will turn off TSC.

13
Introduction
96-8000 rev R June 2007
OVERRIDE K EYS
Thesekeys give the user theability tooverride thespeed ofnon-cutting (rapid)axes motion,programmed feeds
andspindle speeds.
-10 -Decreases currentfeedrate by 10%.
100% -Setsoverridden feedratetoprogrammed feedrate.
+10 -Increases current feedrateby 10%.
-10 - Decreases current spindle speed by 10%.
100% -Sets overriddenspindlespeed toprogrammed speed.
+10 - Increases current spindle speed by 10%.
Hand Cntrl Feed (Handle Control Feedrate) - Pressing this button allows the jog handle to be used to control
thefeedrate in ±1% increments.
Hand Cntrl Spin (Handle Control Spindle) - Pressing this button allows the jog handle to be used to control
spindle speed in ±1% increments.
CW - Starts the spindle in the clockwise direction.This button is disabled on CE (export) machines.
CCW - Starts the spindle in the counterclockwise direction. This button is disabled on CE (export) machines.
The spindle can be started or stopped with the CW or CCW buttons any time the machine is at a Single Block
stop or the Feed Hold button has been pressed. When the program is restarted with Cycle Start, the spindle
will be turned back on to the previously defined speed.
STOP - Stops the spindle.
5% / 25% / 50% / 100% Rapid - Limits machine rapids to the value on the key. The 100% Rapid button allows
maximumrapid.
Override Usage
Thefeedrate canbe varied from 0% to999% ofthe programmedvalue whilein operation.This isdone withthe
feedrate+10%, -10%and 100%buttons. The feedrateoverride isineffective duringG74 andG84tapping
cycles.Feedrate override doesnot changethe speedof anyauxiliary axes.During manual jogging,the feedrate
override will adjust the rates selected from the keypad. This allows for fine control of the jog speed.
The spindle speed can also be varied, from 0% to 999%, using the spindle overrides. It is also ineffective for
G74 and G84. In the Single Block mode, the spindle may be stopped. It will automatically start up upon
continuingthe program (pressing Cycle Start).
By pressing the Handle Control Feedrate key, the jog handle can be used to control feedrate from 0% to 999%
in ±1% increments. By pressing the Handle Control Spindle key, the jog handle can be used to control spindle
speed in ±1% increments (from 0% to 999%).
Rapid moves (G00) may be limited to 5%, 25%, or 50% of maximum using the keypad. If the 100% rapid is too
fast, it may be set to 50% of maximum by Setting 10.
In the Settings page, it is possible to disable the override keys so that the operator cannot select them. These
are Settings 19, 20 and 21.
Table of contents
Other Haas Power Tools manuals
Popular Power Tools manuals by other brands

jcb
jcb 21-18JS Instructions & user's manual

Würth
Würth 1952 006 735 Translation of the original operating instructions

Ryobi
Ryobi R18ST50 Original instructions
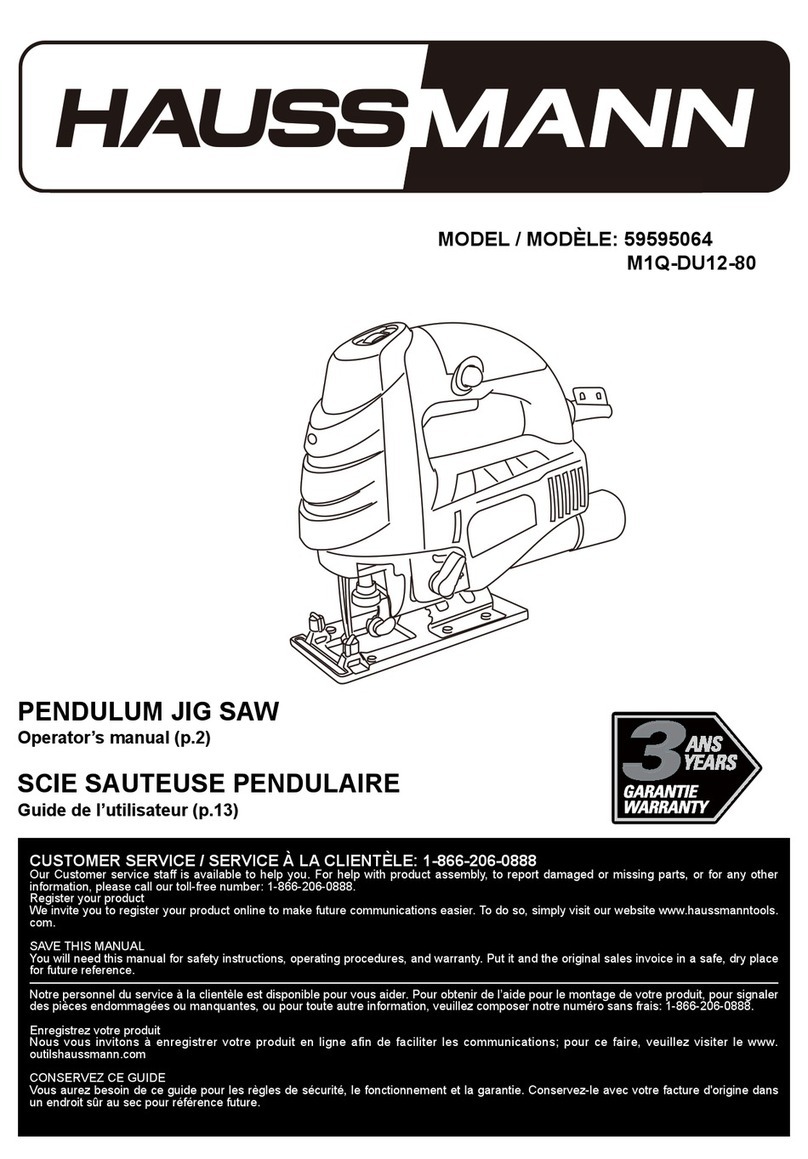
Haussmann
Haussmann 59595064 Operator's manual
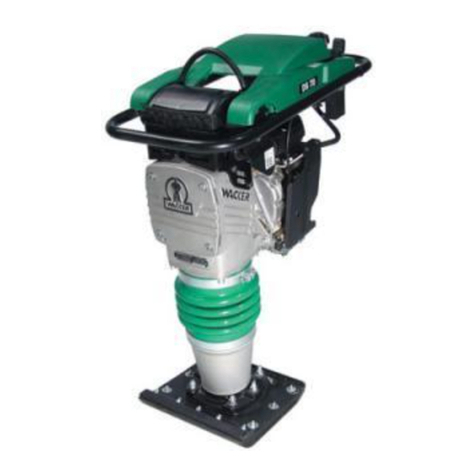
Wacker Neuson
Wacker Neuson DS720 Operator's manual / parts book

Evolution
Evolution 005-0001 Original instructions