Halyard Exhaust Alert Mk3 Manual

Exhaust Alert Mk3
Installation & Operating Instructions
THE SCIENCE OF SILENCE
© Halyard 2020. All Rights Reserved.

Exhaust Alert Operating & Fitting Instructions
Contents
Safety and General Precautions: ....................................................................................... 1
Section 1 Introduction..................................................................................... 2
1.1 About these instructions......................................................................................................... 2
1.2 System Description ................................................................................................................. 2
1.3 Exhaust Alert Operation.......................................................................................................... 2
1.4 Pre-Installation Checks............................................................................................................3
1.5 Tools & Fasteners....................................................................................................................3
Section 2 Components & Accessories .............................................................. 3
2.1 Single Engine, Single Helm Station.......................................................................................... 3
2.2 Twin Engines, Single Helm Station..........................................................................................3
2.3 Twin Engines, Dual Helm Stations........................................................................................... 3
2.4 Accessories.............................................................................................................................. 4
Section 3 Installing the Components ............................................................... 4
3.1 Fitting the sensor ....................................................................................................................4
3.2 Fitting the Connection Block...................................................................................................5
3.3 Fitting the Master Gauge ........................................................................................................ 5
Section 4 Wiring & Connections ...................................................................... 7
4.1 Connection Block .................................................................................................................... 7
4.2 Wiring Master Gauge ..............................................................................................................7
4.3 Circuit Diagrams......................................................................................................................8
4.4 Wiring Repeater Gauge......................................................................................................... 12
4.5 Sensor Wiring for Single Engine Installations .......................................................................12
4.6 Sensor Wiring for Twin Engine Installations .........................................................................12
4.7 Optional Night Mode Gauge Illumination.............................................................................12
4.8 Optional 120dB Siren ............................................................................................................13
4.9 Connecting to a Power Supply ..............................................................................................13
Section 5 Post Installation Checks ................................................................. 13
5.1 Electrical Checks....................................................................................................................13
5.2 Pre-Engine Start checks ........................................................................................................13
5.3 Post-Engine Start checks.......................................................................................................14
5.4 Fault Diagnosis. .....................................................................................................................14
Section 6 Exhaust Alert Components ............................................................. 15

Exhaust Alert Operating & Fitting Instructions
1
HMI 201/01
Warning
Halyard Exhaust Alert reduces the risk of exhaust system failure when
compared to operator due diligence alone, it does not prevent it. Fitting
a Halyard Exhaust Alert does not negate the need for a correctly designed
exhaust system, routine maintenance and operator due diligence.
Safety and General Precautions:
All personnel working on the equipment should employ safe practices.
Halyard (M&I) Limited will not be responsible for personal injury or
damage to property resulting from careless use of hand tools, lifting
equipment, power tools, or unaccepted maintenance or working
practices.
Because of the possible danger to persons or property from accidents
that may result from the use of machinery, proper installation,
maintenance and operating procedures must be followed. Halyard (M&I)
Limited will not be responsible for personal injury resulting from careless
working practices.
All personnel working on the equipment should inspect as necessary to
assure safe operations under prevailing conditions. The appropriate
Personal Protective Equipment (PPE), proper guards and other devices
that may be specified in safety codes should be used. This equipment is
neither provided by nor is it the responsibility of Halyard (M&I) Limited.

Exhaust Alert Operating & Fitting Instructions
2
HMI 201/01
Section 1 Introduction
1.1 About these instructions
Information boxes alongside sections will draw attention to SAFETY
CONSIDERATIONS of the text in accordance with the conventions of the
Recreational Craft Directive.
•DANGER: Indicates a hazard that could EASILY result in death or serious
injury if proper precautions are not taken. If you have any doubts about what
precautions to take, you should seek expert advice.
•WARNING: Indicates a hazard that could result in serious injury or damage to
your boat or its equipment if proper precautions are not taken. If you have
any doubts about what precautions to take, you should seek expert advice.
•CAUTION: Indicates a hazard that could result in personal injury or damage
to your boat or its equipment if suitable care is not taken.
•NOTE: Contains additional information that may be of help.
1.2 System Description
The Halyard Exhaust Alert system provides a class leading exhaust overheat
alert system housed in a 52mm diameter, waterproof (IP67 rated) gauge.
The system incorporates self-test functionality and is supplied as a dual
voltage (12V or 24V) unit.
•The Exhaust Alert monitors the exhaust temperature of inboard marine
engines with a ‘wet’ exhaust, i.e. those engines in which cooling water from
outside (also referred to as raw water) is injected into the exhaust system
immediately after the engine exhaust outlet. The cooling water reduces the
temperature of the exhaust system and reduces exhaust noise.
•Should the cooling water flow be blocked or substantially reduced, the boat’s
exhaust system can overheat and suffer significant thermal damage.
•Raw water is also used to cool the engine. A rapid rise in exhaust
temperature often signals a problem in the raw water cooling system.
Common causes are a blocked skin fitting, blocked inlet strainer, or failed
raw water pump.
•By monitoring the exhaust temperature directly, Exhaust Alert gives early
audible and visual indication of potential raw water cooling problems and
offers protection against exhaust system overheat and possible thermal
damage.
1.3 Exhaust Alert Operation
On power-up the Exhaust Alert unit will cycle through a self-test, lighting
each warning light in turn and sounding the buzzer and siren if fitted.
On detecting a fault on an active engine, the system will display a visual
flashing warning LED and sound an alert with the internal buzzer and the
optional siren if fitted. If the fault is rectified within 15 seconds the system
will automatically reset. After this time the system will latch on and needs
to be acknowledged before it is reset. Touching the units face will
acknowledge an alert and silences the buzzer and siren. When an alert is
acknowledged, the warning LED changes to be constantly lit, and will remain
lit until the fault is rectified.
WARNING:
The Exhaust Alert
should only be fitted to
water cooled exhausts.
WARNING:
DANGER:
CAUTION:
NOTE:

Exhaust Alert Operating & Fitting Instructions
3
HMI 201/01
1.4 Pre-Installation Checks
Before commencing the installation please read through these instructions
carefully. Fitting the Halyard Exhaust Alert involves:
•Removing and replacing the section of flexible exhaust hose connected to
the exhaust sprayhead / injection elbow.
•Drilling into the exhaust hose and clamping the temperature sensor in place
with nuts, washers and silicone sealant.
•Drilling a hole and mounting the Master gauge.
•Mounting the connection block in a suitable dry location.
•Running and connecting the system wiring
1.5 Tools & Fasteners
The Halyard Exhaust Alert can be installed with basic DIY tools. The only
special equipment you might need is a wire-stripping tool. You will also need:
•A hand or electric drill with 10mm drill bit.
•A tool to trim the edges of the hole in the flexible exhaust pipe.
•A 52mm hole cutter for mounting the Master gauge
•A pair of side cutters - if you wish to shorten the overall cable lengths.
•Electrical tie-wraps or cable clips to secure the wiring to suitable supports.
•A small electrical screwdriver to fit the terminals on the connection block.
•Spanners to fix the sensors to the flexible exhaust pipe.
•Any tools required to remove and refit the section of exhaust hose.
•Tape measure
•Extra cable for the optional siren(s) if fitted.
Section 2 Components & Accessories
2.1 Single Engine, Single Helm Station
•1 x Exhaust Alert Master Gauge [Part No:H020170].
•1 x Exhaust Alert sensor with 16 metre cable [Part Nos: H021235 or
H000450]. This sensor kit contains a tube of silicone sealant and smaller
bags of minor components.
•1 x Exhaust Alert connection Block.
2.2 Twin Engines, Single Helm Station
•As for Single Engine, Single Helm system but with two Exhaust Alert sensors.
[Part Nos: H021235 or H000450]
2.3 Twin Engines, Dual Helm Stations
•As for Twin Engines, Single Helm system but with the addition of an Exhaust
Alert Repeater Gauge [Part No:H020171].
CAUTION:
If you have any
doubts at any time
about installing this
equipment, please
contact Halyard or
consult a qualified
engineer.
WARNING:
Suitable PPE such as
eye protection and
gloves should be
worn during the
installation of the
system.

Exhaust Alert Operating & Fitting Instructions
4
HMI 201/01
2.4 Accessories
Please check you have the accessories you need in addition to the standard
kit. If these have not been ordered at the time of purchase, they can be
added at a later date. Further accessories include:
•Optional additional 120db siren(s) 12 Volt [Part No: H000447]
•Optional additional 120db siren(s) 24 Volt [Part No: H021451]
•Additional Sensor for use with single engine system when connecting
generator or additional engine. [Part Nos: H021235; H000450]
•Repeater Gauge [Part No:H020171].
Section 3 Installing the Components
3.1 Fitting the sensor
•With a cold engine release the retaining clamps and remove the exhaust
hose from the engine and outlet.
•Drill a 10mm diameter hole through the hose (Fig. 2), in the top section as
close to either the 10 o’clock or 2 o’clock positions as possible and
approximately 75-100mm downstream of the end of the exhaust elbow as
detailed in Fig. 2.
•Tidy up the edges of the hole as necessary.
•Identify the correct components from the sensor kit as per Fig. 1.
•Fit rubber grommet G into the centre of one of the large penny washers D.
(A smear of silicone sealant may assist)
•Smear both sides of the washer/grommet with silicone sealant and screw the
combination onto the thread of the sensor until the grommet fits snugly
against the underside of the sensor base.
•Clean the area of the hose around the drilled hole to remove any dirt and
grease
•Apply silicone sealant to the hose immediately around the drilled hole, both
inside and out, using the silicone sealant supplied.
•Insert the sensor probe through the hole in the exhaust hose.
CAUTION:
If the exhaust hose
retaining clamps are in
poor condition or are
damaged during the
removal, they MUST be
replaced otherwise
exhaust gases may escape
and water leaks occur.
Before removing the hose
ensure that the outlet and
inlet are well above the
waterline.
NOTE:
Please contact Halyard
for replacement
exhaust clamps, hoses
and other exhaust
system components.
www.halyard.eu.com

Exhaust Alert Operating & Fitting Instructions
5
HMI 201/01
•If the exhaust hose internal diameter is less than 76mm place small rubber
washer B over the end of the probe, followed by the small stainless steel
washer C and stainless locking nut N.
•If the hose internal diameter is 76mm or larger, place the large rubber washer
F over the end, followed by the large stainless steel washer E and stainless
locking nut N.
•Tighten the self-locking nut, taking care not to displace or unduly distort the
inner rubber washer.
Note:
Very thin wall hose requires the use of the larger rubber and steel washers
irrespective of diameter.
3.2 Fitting the Connection Block
•Position the Connection block in a protected dry environment within reach of
the Master Gauge wiring loom
•Identify 12V/24V dc power source. Typically, this is the ignition circuit of each
engine to be monitored but it can be from an independent switch power
source.
•Secure the Connection block to a bulkhead or other resilient surface with self-
tapping screws or other suitable fasteners. Make sure it is not distorted or put
under stress by the fixing arrangement.
•DO NOT connect the power supply at this time.
3.3 Fitting the Master Gauge
•The Master Gauge is fitted with a 3 metre loom. If you need to shorten this
cable you can do so, alternatively you can simply coil up any excess and
secure it in a convenient place.
•Identify the mounting position for the Master Gauge on a flat panel where it
is readily visible and within easy reach.
NOTE:
Do not connect the
power supply cable to
the source that is live
when the engines are
switched off or the
unit may malfunction.
CAUTION:
Do not attempt to
open the Display Head
or you will destroy its
water tightness and
void the warranty.

Exhaust Alert Operating & Fitting Instructions
6
HMI 201/01
•Ensure there is adequatespace behind mounting position for the gauge body
and cable. There needs to be a minimum of 75mm clearance from the
mounting panel face to accommodate the unit correctly.
•Mark the centre of the gauge desired position and drill the mounting hole with
a 53mm hole cutter. It is recommended that a pilot hole is drilled first, and
its location is checked before proceeding with cutting the hole.
•Clean up the hole edges as necessary removing any sharp edges.
•Ensure the gauge seal is in place against the bezel and pass the gauge cable
through the hole and then through the gauge backing nut on the inside of the
panel.
•Locate Display unit into hole and slide backing nut up the cable, around the
units’ body and tighten sufficiently by hand to seal and hold the unit in place
as shown in Fig 3.
•Run the cable to the connection block.
Fig. 3. Through Panel Gauge Mounting

Exhaust Alert Operating & Fitting Instructions
7
HMI 201/01
Section 4 Wiring & Connections
Refer to appropriate wiring diagram.
4.1 Connection Block
•Connection 1 is the common negative (-ve) for the unit, sensors, controls and
sirens.
•Connections 2 (engine 1) and 3 (engine 2) are positive (+ve) supply (12/24V)
to the unit from engine 1 and 2 ignition circuits. The unit uses this supply to
identify which engine is running. These feeds must be protected using the
fuse holders and 1A fuses supplied.
•Connection 7 is for the Repeater guage or the optional 120db siren positive
(+ve).
•The Repeater Gauge connects to 8,9,10,11 and 1
•Connections 4,5 & 1 are for exhaust sensors for two engines, each with one
pair of wires. For a single sensor system then the connection for the second
sensor (connection 5) should be connected directly to earth (connection 1),
•Connection 12 activates the unit’s night mode, dimming LEDs to preserve
night vision (+ve to dim).
4.2 Wiring Master Gauge
•Remove approximately 80mm of the outer sheathing from the Master gauge
loom.
•Remove 8mm of insulation of each core wire.
•Lightly twist the strands of each core and insert into the appropriate
connection block position.
•Connect the wires from the gauge unit to the connector block as follows and
tighten the clamping screws:
Connection
Block
Number
Wire Colour
Description
Required
Wire size
1
Black
Common -ve
0.75mm2
2
Green
Engine 1 +ve
0.75mm2
3
Turquoise
Engine 2 +ve
0.75mm2
4
Orange
Engine 1 Sensor +ve
Halyard
Supplied
5
Red
Engine 2 Sensor +ve
Halyard
Supplied
6
Yellow
No connection
7
Slate Grey
Repeater gauge buzzer or
Optional 120 dB siren +ve
0.75mm2
8
White
Optional repeater gauge
0.75mm2
9
Blue
Optional repeater gauge
0.75mm2
10
Brown
Optional repeater gauge
0.75mm2
11
Purple
Optional repeater gauge
0.75mm2
12
Pink
Night Mode input (+ve to
dim)
0.75mm2
CAUTION:
Follow the wiring
instructions carefully
and check the
connections against
the correct wiring
diagram on page 7
before connecting the
power. Incorrect
connections could
damage the unit.
CAUTION:
When removing the
outer sheathing take
care not to damage
the insulation of the
individual core wires
underneath.

Exhaust Alert Operating & Fitting Instructions
8
HMI 201/01
4.3 Circuit Diagrams
Fig. 4. Single Engine, Single Helm Station Wiring Diagram

Exhaust Alert Operating & Fitting Instructions
9
HMI 201/01
Fig. 5. Twin Engines, Single Helm Station Wiring Diagram

Exhaust Alert Operating & Fitting Instructions
10
HMI 201/01
Fig. 6. Single Engine, Dual Helm Station Wiring Diagram
(No 120dB siren)

Exhaust Alert Operating & Fitting Instructions
11
HMI 201/01
Fig. 7. Twin Engines, Dual Helm Station Wiring Diagram
(No 120dB siren)

Exhaust Alert Operating & Fitting Instructions
12
HMI 201/01
4.4 Wiring Repeater Gauge
•Remove approximately 80mm of the outer sheathing from the Master gauge
loom.
•Remove 8mm of insulation of each core wire.
•Lightly twist the strands of each core and insert into the appropriate
connection block position.
•Connect the wires from the gauge unit to the connector block as follows and
tighten the clamping screws:
** Do not connect if using a separate 120 dB sire.
4.5 Sensor Wiring for Single Engine Installations
•Remove approximately 35mm of the outer insulation from the sensor cable.
•Cut back the exposed wire and foil shielding that lies between the outer
insulation and the twin inner wires.
•Remove 8mm of the red and black insulation of the two wires.
•Lightly twist the strands of each inner wire and insert into the appropriate
connection block terminals and tighten the clamping screws.
•Connect the wires from the sensors to connection block terminals 4 and 1
and tighten the clamping screws.
•Connect terminals 5 and 1 of the connection block and tighten the clamping
screws.
4.6 Sensor Wiring for Twin Engine Installations
•Prepare the wiring for both sensors as in the Single Engine instructions
above.
•Connect the wires from the Port engine sensor to terminal 4 and 1 and tighten
the clamping screws.
•Connect the wires from the Starboard engine sensor to terminal 5 and 1 and
tighten the clamping screws.
4.7 Optional Night Mode Gauge Illumination
For night mode operation supply main gauge connector 12 with a +ve supply
e.g. From navigation lights.
Connection
Block
Number
Wire Colour
Description
Main Gauge
Connection
Block Number
1
Purple
Repeater Power LED
11
2
Brown
Repeater Silence O/P
10
3
Blue
Repeater Eng 2 LED
9
4
White
Repeater Eng 1 LED
8
5
Slate Grey
Repeater gauge buzzer**
7
6
Turquoise
Engine 2 +ve
3
7
Green
Engine 1 +ve
2
8
Black
Common -ve
1
NOTE:
The ferrules make for
a neat and sound
connection. The wires
are not crimped or
soldered to the
ferrules; the silver
tubular part is
crushed onto the core
when the terminal
screws are fully
tightened.
CAUTION:
When removing the
outer sheathing be
careful not to damage
the insulation of the
individual cores
underneath.
CAUTION:
When removing the
outer sheathing take
care not to damage
the insulation of the
individual core wires
underneath.

Exhaust Alert Operating & Fitting Instructions
13
HMI 201/01
4.8 Optional 120dB Siren
•Identify suitable dry and protected location and securely mount the siren.
•Remove approximately 25mm of the outer sheathing from the siren cable(s).
Extend the cable as required with wiring of the same gauge.
•Lightly twist the strands of each inner wire and insert into terminals 7 and 1
of the connection block and tighten the clamping screws.
4.9 Connecting to a Power Supply
System -ve connection
•The Master gauge requires a common -ve from each engine ignition gauge
circuit connected to terminal 1 of the connection block.
System +ve connection
•The Master gauge requires a +ve supply from each engine ignition gauge
circuit connected to terminal 2 only for a single engine and 2 & 3 for a twin
engine installation.
Note: Twin engine installations must operate at the same voltage. Exhaust
Alert cannot accept a supply from one engine at 12V and the second engine
at 24V.
Section 5 Post Installation Checks
5.1 Electrical Checks
•Double-check all your connections and compare them with the appropriate
wiring diagram.
•Switch ON the engine(s) ignition (power supply).
•Both red and green lights should flash momentarily on the Master gauge and
the internal buzzer sounds.
•If fitted the optional 120dB siren also sounds.
•Switch OFF the engine(s) ignition (power supply).
•Validate the system function by unscrewing the connecting plug on the
sensor and remove plug.
•Switch ON the relevant engine ignition (power supply), for twin engine
installation do one engine at a time.
•The self-test the buzzer should sound and the relevant Exhaust Alert red
warning light flash.
•Acknowledge the alert (see Section1.3) and switch OFF the engine(s)
ignition (power supply).
•Reconnect the sensor plug and tighten the screw, ensuring the pins are
correctly aligned and the rubber gasket is in place.
5.2 Pre-Engine Start checks
•Verify all connections and cable runs are correct and secure.
WARNING:
Ensure there is no
power on the DC
circuit when the wires
are being connected.
NOTE:
A supply voltage drop
may cause the
Exhaust Alert to
restart and go
through its self-test
function. This may
occur when there is a
heavy power draw on
the batteries such as;
starting the engine,
using a bow thruster
or anchor winch.

Exhaust Alert Operating & Fitting Instructions
14
HMI 201/01
•Check that the system cables and components are not able to contact any
heat sources or subject to abrasion, stress etc.
•The clamps securing the exhaust pipes and hoses are securely tightened.
•Any other components disturbed or removed during the fitting process have
been refitted correctly.
•The raw water seacocks are OPEN and all other systems are correctly set.
5.3 Post-Engine Start checks
With the engine running and from a safe position observe to verify the
following:
•Ensure there are no gas or water leaks around the sensors
•Ensure there are no gas or water leaks around the hose connections and the
clamps are secure.
Note: any rectification works must only be completed once the engine has
been shut down and cooled sufficiently.
5.4 Fault Diagnosis.
Halyards Exhaust Alert is designed to detect open sensor circuit faults. For
example, if there is a lose/broken wire on the sensing circuit or within the
sensor the system will signal a visual and audible alert. If there is an alert
present with a cold engine exhaust, then the following should be checked
with the electrical power and engine isolated:
•Sensor and wiring circuit connections.
•Correct engine is being powered for the active sensor.
•The continuity of the sensor wires, i.e. a broken wire.
DANGER:
Do not work on a live
system, isolate power
first.
DANGER:
Moving machinery,
rotating components
and hot surfaces!!
Open hatches!!

Exhaust Alert Operating & Fitting Instructions
15
HMI 201/01
Section 6 Exhaust Alert Components
Part No.
Reference
Exhaust Alert System
H020170
AS701
Master gauge with IP67 gland and hard wired
3 metre harness.
H020171
AS702
Repeater Gauge with IP67 gland and hard
wired 3 metre harness
H021247
AS115
Single engine single station gauge with
through hose sensor with 16 metre cable
H021248
AS125
Single engine single station gauge with
removable through hose sensor with 16 metre
cable
H021249
AS135
Single engine dual station gauge with through
hose sensors with 16 metre cable
H021250
AS145
Single engine dual station gauge with
removable through hose sensors with 16
metre cable
H021251
AS215
Twin engine single station gauge with through
hose sensor with 16 metre cable
H021252
AS225
Twin engine single station gauge with
removable through hose sensors with 16
metre cable
H021253
AS235
Twin engine dual station gauge with through
hose sensors with 16 metre cable
H021254
AS245
Twin engine dual station gauge with
removable through hose sensors with 16
metre cable
H000447
AS777
Optional additional siren

Exhaust Alert Operating & Fitting Instructions
16
HMI 201/01
Installation Notes
Installation Date: ………………………..

Exhaust Alert Operating & Fitting Instructions
17
HMI 201/01

HMI 201/01
Halyard (M&I) Ltd
86 Cobham Rd,
Ferndown Ind. Estate,
Wimborne
BH21 7PQ
T: +44 (1722) 710922
E: technical@halyard.eu.com
W: www.halyard.eu.com
Table of contents
Popular Security System manuals by other brands
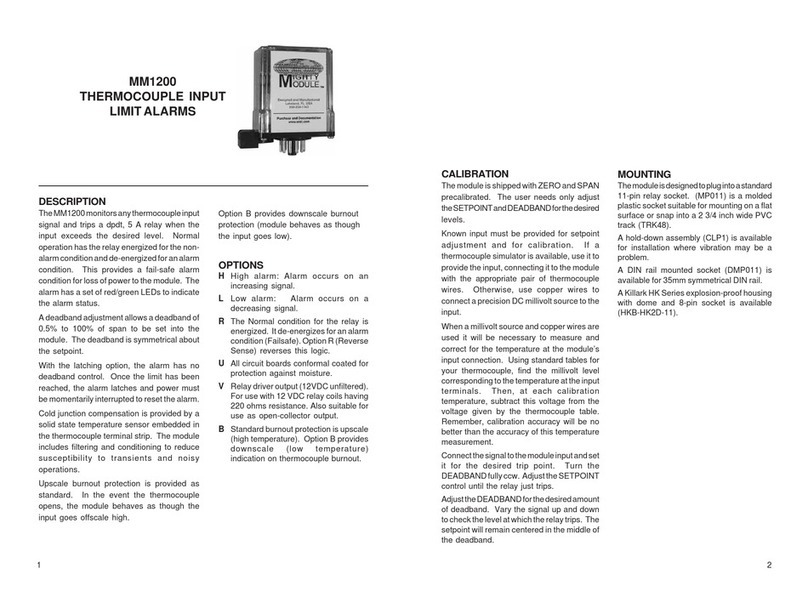
Mighty Module
Mighty Module MM1200 manual
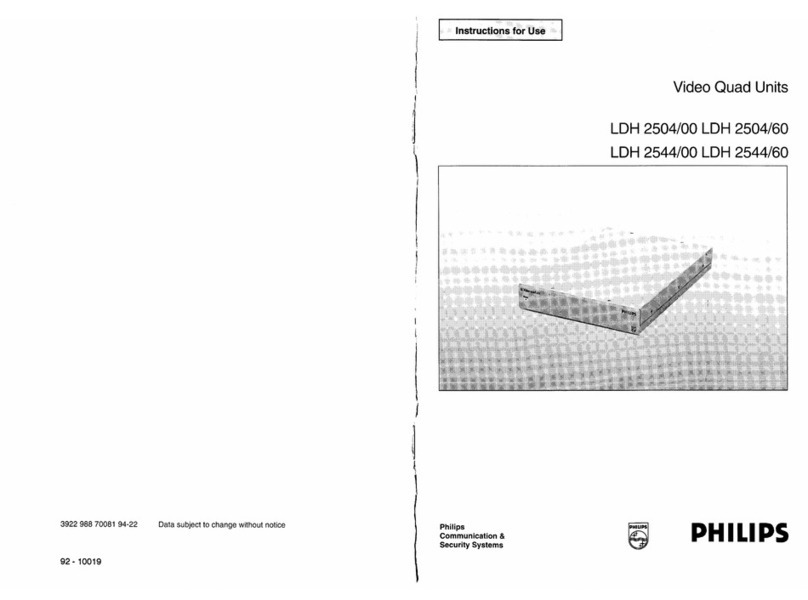
Philips
Philips LDH2544/10 Instructions for use

BFT
BFT MOOVI 30 Installation and user manual
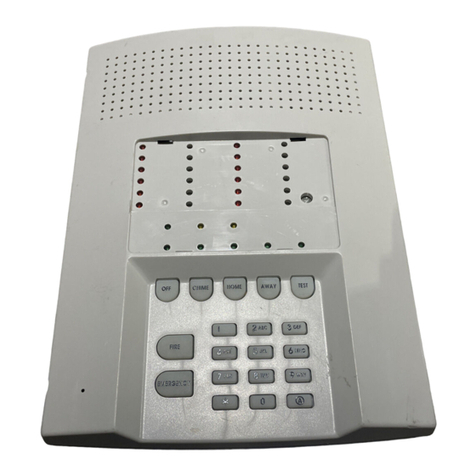
Linear
Linear REMOTE ACCESS SOFTWARE DVS-1200 installation instructions
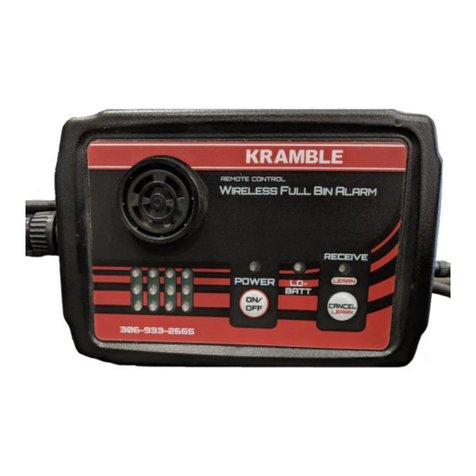
KRAMBLE INDUSTRIES
KRAMBLE INDUSTRIES 6 Series Installation and operating manual
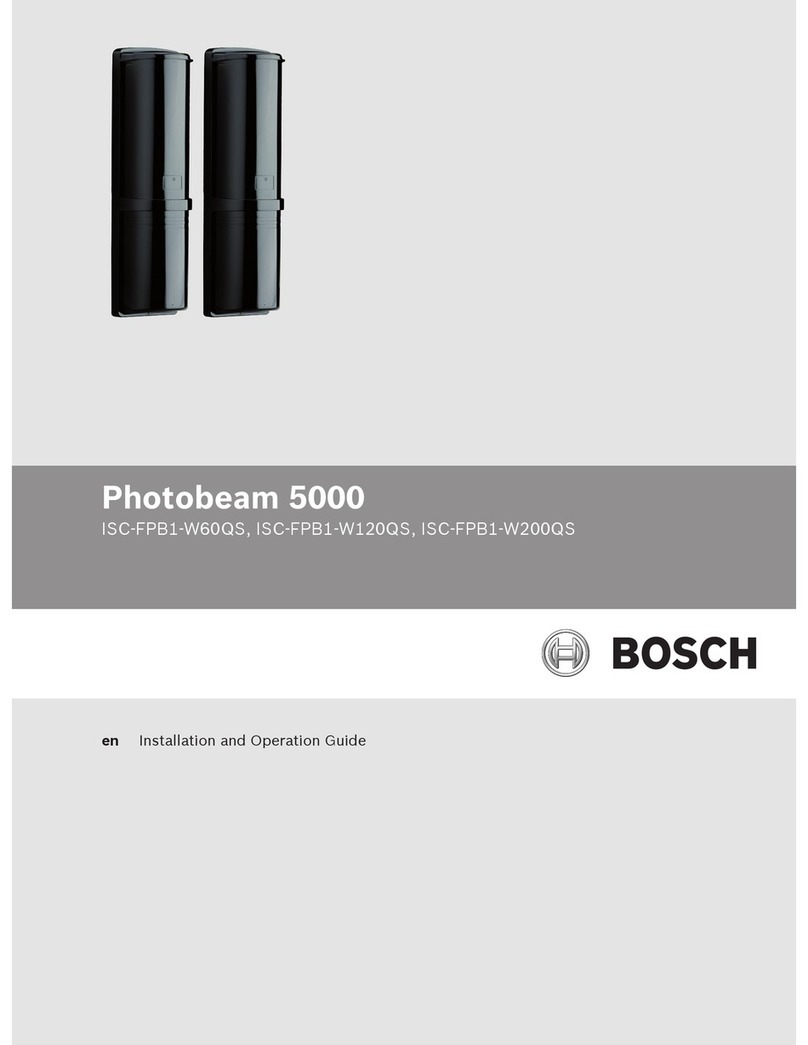
Bosch
Bosch ISC-FPB1-W60QS Installation and operation guide