Han's Robot Elfin Series User manual

Collaborative Robot Elfin Series
Electrical installation
(E03/E05/E10)
V1

2
Introduction
How to Use This Manual
This manual is intended for operators of Elfin robots, who should have some
electrical and programming knowledge. The manual will provide instructions for Elfin
operators from the following ways:
Safety: The operator should keep all safety instructions in mind.
Mechanical Installation: The operator should follow the instructions
when installing the robot.
Electrical interface: Open ports of Elfin are introduced for the
convenience of secondary development.
Software Control: It can guide the operator to install software and run
the robot.
Security Configuration: It introduces the basic safety settings.
Technical Support
Shenzhen Han's Robot Co., Ltd will provide you with long-term technical services. If
you have any technical problems or other needs during using our robot, you are welcome
to visit our company website: www.hansrobot.com, or directly contact our technical
engineers.
Contact Information
Company Address: 5F, Block B, Han's Innovation Mansions, No. 9018 Beihuan
Boulevard, High-tech Park, Nanshan District, Shenzhen, China
Factory Address: 4F, Building 4, Han's Laser Industrial Park, No.128 Chongqing Road,
Fuyong Town, Baoan District, Shenzhen, China
Mobile: +86 75526983668 Fax: +86 7552698278
www.hansrobots.eu

I
INDEX
CHAPTER 1 ELECTRICAL INTERFACES...................................................................... 1
PRECAUTIONS..................................................................................................................1
1.1 CONNECTING CABLE.................................................................................................2
1.2 EXTERNAL INTERFACE AND CONNECTION INSTRUCTIONS...............................................3
1.3 INTRODUCTION TO CONTROLLER I/O......................................................................... 5
1.4 GENERAL SPECIFICATION FOR ALL DIGITAL I/O............................................................6
SAFETY I/O..............................................................................................................7
DEFAULT SECURITY CONFIGURATION........................................................................... 8
CONNECT THE E-STOP BUTTON................................................................................... 9
EMERGENCY STOP RESET FUNCTION............................................................................ 9
SAFE EMERGENCY STOP WITH OTHER MACHINES.........................................................10
SAFETY PROTECTION STOP....................................................................................... 10
PROTECTIVE STOP WITH RESET.................................................................................. 11
1.5 BUILD A GENERAL DIGITAL I/O.............................................................................. 12
1.6 GENERAL ANALOG I/O..........................................................................................13
USING ANALOG OUTPUT..........................................................................................14
USING ANALOG INPUT.............................................................................................14
REMOTE SWITCH CONTROL....................................................................................... 15
1.7 SAFETY GUARDRAIL...............................................................................................15
1.8 ROBOT TERMINAL IO INTERFACE DESCRIPTION.........................................................16
CHAPTER 2 TEACH PENDANT.................................................................................20
CHAPTER 3 THE PROCESS OF STARTING THE ROBOT.......................................... 21
www.hansrobots.eu

1
Chapter 1 Electrical Interfaces
This chapter describes all the electrical interfaces of the robot arm and the control
box. These interfaces are divided into five categories, each of which has different uses and
attributes:
Controller I/O
Tool I/O
Ethernet
Power connection
Robot connection
“I/O”The term refers to the digital and analog control signals coming in and out of
the interface.
These five types of interfaces are described below, and most types of I/O provide
examples.
Precautions
Please read the Elfin electric control box interface instructions before
installing the electric control box.
The location of electric control box and distribution cable should be
away from the noise source as much as possible. If it is too close to the
noise source, there may be position deviation or misoperation.
Don’t apply excessive force to the connector or overbend the cable.
Otherwise, it may lead to bad contact or broken line.
Please make sure that the equipment is well grounded.
Please use the accessory nylon clip to fix the cable after connecting
the cable.
Don’t disassemble the electric control box, otherwise it may cause
electricity leakage and electric shock.
The electric control box is equipped with fans at both ends. Don’t block
them when installing, and keep it well ventilated.
www.hansrobots.eu

2
1.1 Connecting cable
As shown in the below figure, the line is the power cable of the electric control box.
The cable line is 5m long. The control box must be connected to the power supply. This
process must be completed using the corresponding IEC C13 wire connected to the
standard IEC C14 plug on the bottom of the control box.
Note:
The power supply shall be equipped with at least the following accessories:
Grounding;
Fuse of electric supply;
Residual current circuit breaker;
It is recommended that all the devices in the robot application should have a power
supply switch, so as to lock and hang up a sign during the maintenance.
As shown in the following figure, the line is a cable that connects the robot body and
electric control box, with a length of 5m. It connects the machine hand and the electric
control box. The gray end connects the plug of robot base, and the black end connects the
electric control box’s aviation plug.
www.hansrobots.eu

3
1.2 External Interface and Connection Instructions
Front:
Bottom::
No.
Name
1
Carrying handle
2
Exhaust vent
3
Air inlet
4
Cabinet keyhole
5
Screw
6
fixed foot rack
7
fixed plate of teaching pad
No.
Name
1
Robot connector
2
Teach pendant connector
3
Controller power switch
4
AC power socket
5
grommet
www.hansrobots.eu

4
The controller connects the teach pendant:
The controller connects the robot:
Fasten the controller:
www.hansrobots.eu

5
1.3 Introduction to Controller I/O
The controller provides a series of external interfaces, for connecting controller I/O
with various devices such as external relays, PLC, sensors and emergency stop device.
The port layout of the controller panel I/O is shown below:
www.hansrobots.eu

6
1.4 General specification for all digital I/O
This section describes the electrical specifications of 24V digital I/O provided by the
controller.
General I/O (Type:PNP)
Safety I/O (Type:PNP)
Configurable I/O (Type:PNP)
The digital I/O power supply is provided internally by the controller, and can be
supplied externally when needed. The current is limited to 2A when using
internal/external power supply. The digital I/O can connect the external power according
to the following diagram. The configurable I/O can be configured into general I/O.
The electrical specifications for internal and external power supply are as follows:
Terminal
Parameter
Minimum
Value
Typical
Value
Maximum
Value
Unit
Internal 24V Power Supply
INT_24 - INT_GND
Voltage
23
24
25
V
INT_24 - INT_GND
Current
0
-
2
A
External 24V Power Supply
24D - GND
Voltage
20
24
29
V
24D - GND
Current
0
-
2
A
www.hansrobots.eu

7
The digital I/O follows the requirements of IEC61131-2. The electrical specifications
are as follows.
Terminal
parameter
minimum
value
Typical
value
Maximum
value
unit
Digital output
COx / DOx
Current
0
-
1
A
COx / DOx
Voltage drop
0
-
0.5
V
COx / DOx
Leakage current
0
-
0.1
mA
COx / DOx
Function
-
PNP
-
Type
COx / DOx
IEC 61131-2
-
1A
-
Type
Digital input
SIx /DIx
Voltage
-3
-
30
V
SIx /DIx
OFF area
-3
-
5
V
SIx/ DIx
ON area
11
-
30
V
SIx/ DIx
Current(11-30V)
2
-
15
mA
SIx/ DIx
Function
-
PNP
-
Type
SIx/ DIx
IEC 61131-2
-
3
-
Type
Safety I/O
This section introduces special safety input (red text font), please follow the 24V
digital I/O general specification when using.
The safety inputs include emergency stop and safety protection stop. Emergency stop
input is used only for stopping equipment under emergency. The safety protection stop
input is used for all types of safety protection devices. Their functional differences are
shown in the following table.
Terminal
Emergency Stop
Safety Protection Stop
Robot stops moving
Yes
Yes
Run program
Stop
Suspend
Robot power supply
Close
open
Initialization
Manual
Automatic or manual
Frequency of use
Low
Ordinary
Need to be re-initialized
Only release the brake
No
Shutdown category (IEC 60204)
1
2
Performance rate (ISO 13849-1)
PLd
PLd
www.hansrobots.eu

8
Danger:
Don’t connect the safety signal with non-safe PLC. Failure to comply
with this warning may lead to casualty accidents due to failure of safety
functions. Be sure to separate safety signals from the normal I/O port
signal.
All the Safety I/O are redundant (two independent channels). Keep two
channels independent to ensure that the safety function will not fail
when one channel fails.
The robot’s safety functions must be checked before using, and safety
functions must be tested regularly.
Default Security Configuration
The robot is in default security configuration when it is delivered, and is not
connected with other safety devices. Its configuration is as follows:
www.hansrobots.eu

9
Connect the e-stop button
The external connection diagram of one or more e-stops is shown below:
Emergency stop reset function
www.hansrobots.eu

10
Safe emergency stop with other machines
Safety Protection Stop
Taking the door switch as an example, the following diagram introduces the
construction of basic protection stop function, when the door is opened, robot stops.
www.hansrobots.eu

11
Protective stop with reset
When the protective stop is triggered, the following double channel buttons can be
reset or reset through the trainer software.
The corresponding construction method is as follows.
www.hansrobots.eu

12
1.5 Build a General Digital I/O
The general digital I/O must follow the general configuration of digital I/O. The
flexible I/O, which is not used for safety functions, can be used as general digital I/O.
The use of digital output:
Control digital input with button:
www.hansrobots.eu

13
1.6 General Analog I/O
Used to set or measure voltage (0-10v) or current (4-20ma) between devices.
To achieve high precision, please follow the following rules in use:
Use the closest GND to I/O.
The measuring equipment and the controller use the same ground (GND),
and the analog I/O is not isolated from the controller.
Use shield wire or twisted pair. Connect the shield to the "GND" on the
common I/O terminal.
The current signal is not sensitive to noise. It is preferred to use the
equipment in current mode.
The corresponding I/O configuration is as follows:
Voltage mode input
AIx - AG
voltage
0
-
10
V
AIx - AG
resistance
-
12
-
Kohm
AIx - AG
dissociation
energy
-
12
-
Bit
Current mode output
AOx - AG
current
4
-
20
mA
AOx - AG
voltage
0
-
10
V
AOx - AG
dissociation
energy
-
16
-
Bit
Voltage mode output
AOx - AG
voltage
0
-
10
V
AOx - AG
electricity
0
-
20
mA
AOx - AG
resistance
-
43
-
ohm
AOx - AG
Dissociation energy
-
16
-
Bit
www.hansrobots.eu

14
Using analog output
The following example shows how to use analog output to control the speed of
conveyor belt.
Using analog input
The diagram below shows how to connect the analog sensors.
www.hansrobots.eu

15
Remote switch control
With Power IO, the control box can be turned on and off without going through the
teach pendant. The construction method is as followed:
Power on: contact trigger;
Power off: keep the short connection at 2.5s-3 S
1.7 Safety Guardrail
Users should conduct a risk assessment for specific robot applications to determine
whether to install security guardrails in the actual operating environment. If a safety
guardrail needs to be installed, you should carefully calculate the space of the safety
guardrail.
Suggestions: The circle radius of guardrail space> the length of mechanical arm + the
length of mechanical arm’s end clamp.
www.hansrobots.eu

16
1.8 Robot Terminal IO Interface Description
1、IO external wiring harness is defined as follows:
Connector plug
PIN
Line color
definition
signal description
1
INPUT_0
Brown
Digital input 0
2
INPUT_1
blue
Digital input 1
3
INPUT_2
White
Digital input 2
4
OUTPUT_0
green
Digital output 0
5
OUTPUT_1
powder
Digital output 1
6
OUTPUT_2
yellow
Digital output 2
7
485_A
black
484 communication A pin
8
485_B
gray
484 communication B pin
9
AIO
red
Analog input 0
10
AI1
purple
Analog input 1
11
24V
Ash powder
Power supply (24V)
12
GND
Red and blue
Ground (0V)
www.hansrobots.eu

17
2. Internal power supply specifications:
parameter
Min
Typical value
Max
unit
24V power supply voltage
24
V
24V power supply current
1
1.5
A
If the current exceeds its limit, the software will protect and shut down the output,
and the internal control system will generate an error message and display it in the robot
log; the power output of these two ports is the output of the same power supply.
3. Digital output (type: PNP)
Digital output
terminal
parameter
Min
Typical value
Max
Unit
DOx
Current
0
-
0.4
A
DOx
Voltage drop
0
-
0.5
V
DOx
Leakage current
0
-
0.5
MA
DOx
Features
-
PNP
-
Type
DOx
IEC 61131-2
-
0.4A
-
Type
The digital output is implemented by sinking current only to GND (0V) instead of
sinking current. When the digital output is activated, the corresponding connector will be
driven to GND. When the digital output is disabled, the corresponding connector will be
open (open/open).
Note: There is no current limit on the digital outputs in the tool. If the specified data
is exceeded, it may cause permanent damage.
Example of using a digital output:
This example illustrates the use of an IO board power supply to power external
devices. If an external system is to be used to supply power to the external system, it
requires common processing.
DO
GND
www.hansrobots.eu
Other manuals for Elfin Series
1
Table of contents
Other Han's Robot Robotics manuals
Popular Robotics manuals by other brands
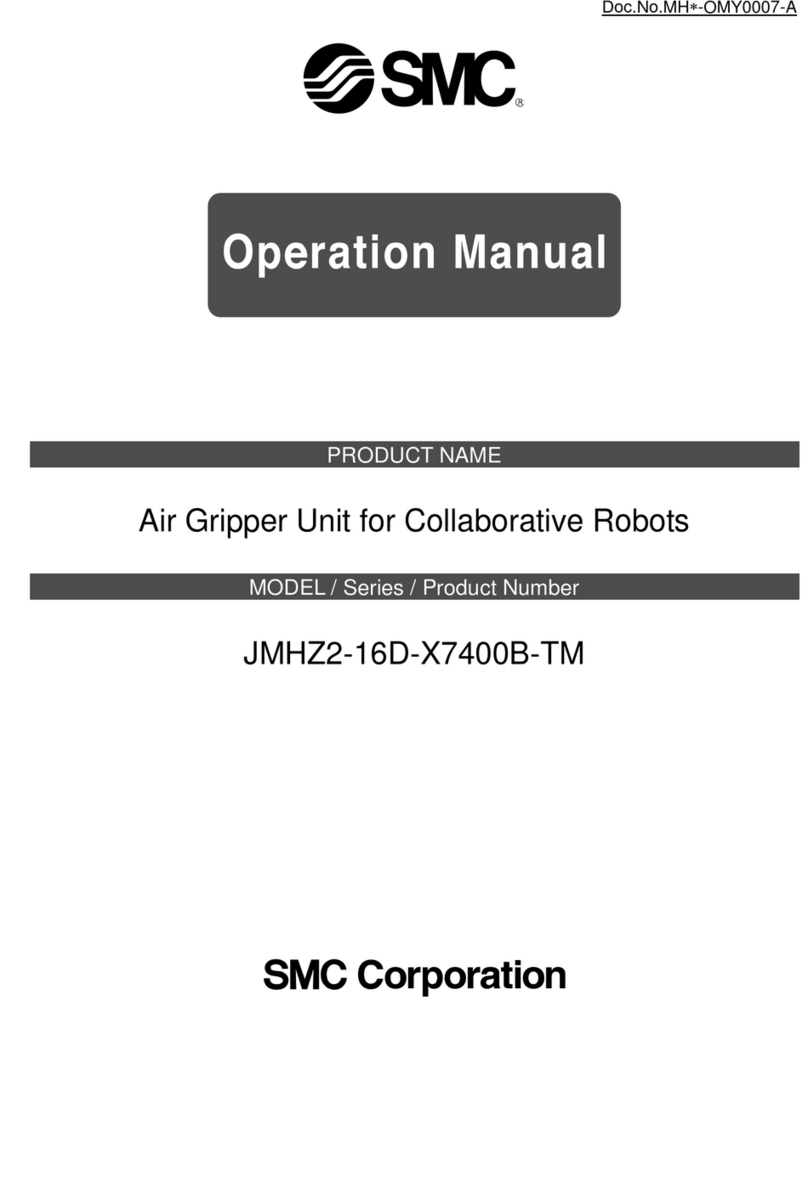
SMC Networks
SMC Networks JMHZ2-16D-X7400B-TM Operation manual
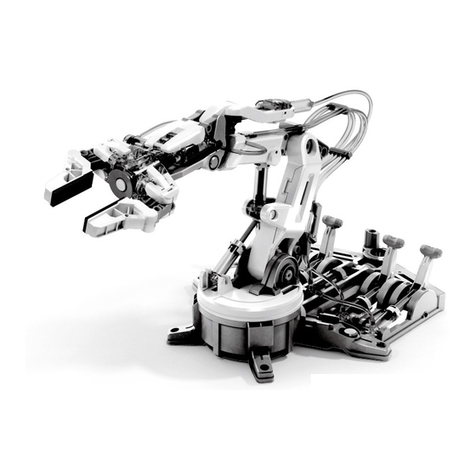
Pro's Kit
Pro's Kit GE-632 Assembly & instruction manual
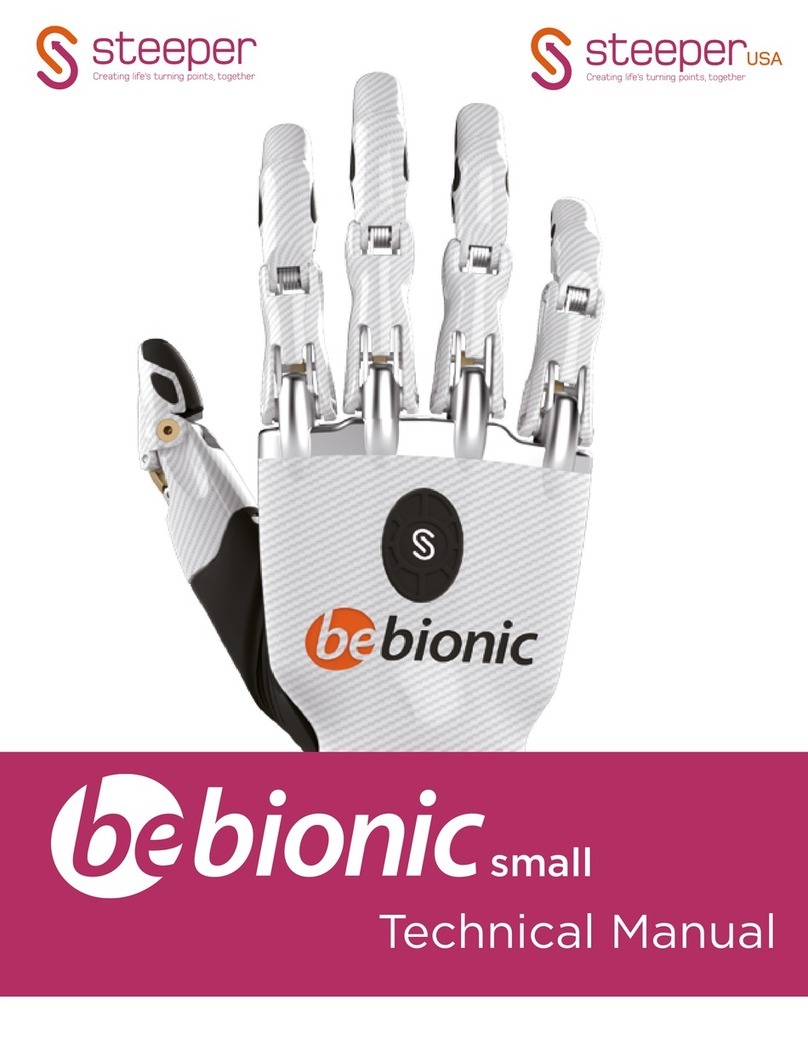
be bionic
be bionic steeper Technical manual
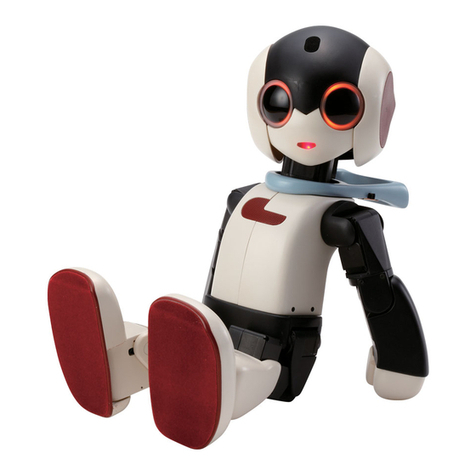
De Agostini
De Agostini MODEL SPACE Robi manual
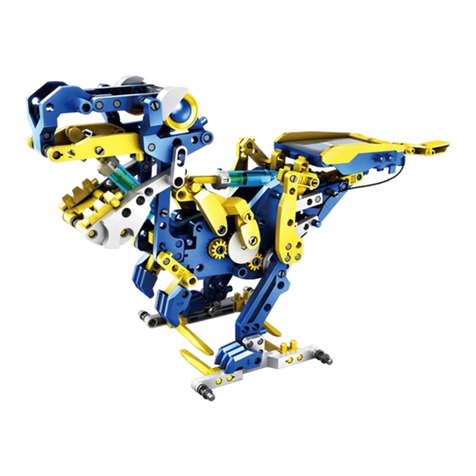
Pro's Kit
Pro's Kit GE-618 Assembly & instruction manual

MD SPORTS
MD SPORTS 18405 Assembly instructions