HANSA-FLEX HK S TKV User manual

USER MANUAL
HK S TKV Analogue Power Meter
Stainless steel design
Pressures up to 350 bar
Volume flow up to 190 l/min
Temperature display up to 120°
Internal overpressure protection
an be used with all mineral oils
Power supply not required
ompact design

Valid from: 15.02.2021 / Source: VAM-UM-00551-EN-04
Despite careful checking, we cannot exclude the possibility of errors in this document and we accept no liability for the information it
contains.
Page 1
TABLE OF CONTENTS
INTRODU TION 2
UNPA KING AND HE KING THE PRODU T 3
FUN TIONAL PRIN IPLE 4
INSTALLATION 5
Important information 5
Installing the volume flow meter 7
Installing the power meter 9
OPERATION 11
Information about the power meter 11
ONDU TING THE POWER MEASUREMENT 12
General information 12
Standard test condition 12
Pump test 13
Test sequence 13
Pressure relief valve test 14
Test sequence 15
MAINTENAN E 16
Pressure release 16
Dismantling and cleaning the volume flow meter 16
Removing the dust protection casing 17
Reconnecting the magnetic coupling 18
Maintaining the pressure loading unit 18
Loading valve 18
Volume flow meter 18
Replacing the safety disc 18
TE HNI AL DATA 20
Temperature range 20
Nominal pressure (safety factor 3:1) 20
Drop in pressure 20
Accuracy 21
Repeatability 21
Thread 21
Pressure display 21
Temperature display 21
Loading valve 21
Medium 21
DIMENSIONS 22

Valid from: 15.02.2021 / Source: VAM-UM-00551-EN-04
Despite careful checking, we cannot exclude the possibility of errors in this document and we accept no liability for the information it
contains.
Page 2
INTRODUCTION
This volume flow meter is a robust industrial-grade inline gear flow meter that is available in an
aluminium, brass or stainless steel design for the purpose of monitoring many different fluids.
Available in seven connection sizes from 1/4... 3 inches for flow ranges from (0.02...0.20 gal/min)
0.1...0.75 l/min to (20...300 gal/min) 100...1100 l/min. The devices are calibrated to a specific
weight of 0.876 for oil or other oil-based fluids, 1.0 for water or other water-based fluids or 1.18
for phosphate ester fluids.
The volume flow meter is equipped with a 360° rotatable protective case/scale that allows it to
be installed in any position without needing to consider the scale direction. As soon as the
volume flow meter is permanently installed, the protective case/scale can be rotated 360° to
make it easier to read.
In addition, the unique spring-loaded design of this volume flow meter reduces its sensitivity to
viscosity and allows it to be installed in any position, including inverted, without losing any
precision. An optional inverted scale is available for such applications.
The standard volume flow meter only works in one direction. If required, a bypass option with
inverted flow is available for the mineral oil, phosphate ester and water-based fluids models.
Please note that the volume flow is only measured in the direction of the arrow.
Aluminium models are offered as robust, low-cost volume flow meters for
monitoring non-corrosive, water-based or oil-based fluids. Oil-based fluids for
operating pressures of up to 250 bar (3500 psi).
Brass models are recommended for water monitoring applications or other systems
where there are no corrosion inhibitors.
Stainless steel models are used for monitoring hydraulic systems with operating
pressures of up to 350 bar (6000 psi) or other corrosive, caustic fluids such as acetic
acid. You can obtain further information from your technical consultant.

Valid from: 15.02.2021 / Source: VAM-UM-00551-EN-04
Despite careful checking, we cannot exclude the possibility of errors in this document and we accept no liability for the information it
contains.
Page 3
UNPACKING AND CHECKING THE
PRODUCT
Perform the following steps once you receive the product:
If the product packaging is damaged, ask the shipping agent to be present when the product is
unpacked. If the product is damaged and the shipping agent is not present, ask for an
inspection by the representative of the shipping agent within 48 hours of delivery and lodge a
complaint with the shipping agent. The purchaser has sole responsibility for lodging a
complaint about any damage to the device caused during transport.
Open the shipping packaging carefully and follow all the instructions specified on the outside.
Remove all the packaging materials and carefully remove the product from the packaging.
Retain the undamaged packaging and all the packaging materials for possible onward shipment
or storage. heck the product and the relevant accessories visually for any physical damage
such as scratches, loose or broken parts or other signs of damage that might have occurred
during transport.

Valid from: 15.02.2021 / Source: VAM-UM-00551-EN-04
Despite careful checking, we cannot exclude the possibility of errors in this document and we accept no liability for the information it
contains.
Page 4
FUNCTIONAL PRINCIPLE
The volume flow meter is a float-type measuring device. A sharp-edged baffle (1) located in the
piston assembly (2) forms an annular opening with the contoured measuring cone (3).
The piston assembly features a cylindrical PPS/ceramic magnet (4) that is coupled magnetically
to an external display magnet (5) which moves in direct response to the movement of the
piston. A calibrated spring (6) counteracts the flow in the forward direction.
These volume flow meters are the most readable products in their class. Vivid coloured
indicators move across the linear display scale (7), which contains numbers and markings in
bold that are easy to read. The improved resolution virtually eliminates any parallax issues
(reading errors caused by viewing from a different angle).
1
Baffle
9
rossplate
2
Piston assembly
10
Locking spring washer
3
Measuring cone
11
O
-
ring seal (pressure seal)
4
Internal magnet (piston magnet)
12
Threaded
connector
5
External magnet (display ring
-
13
End cap
6
Spring
14
High
-
pressure casing (pressure
7
Display scale
15
Protective casing (scale protection)
8
Locking ring
16
Rubber protective seal (bumper)
Table 1: Volume flow meter components

Valid from: 15.02.2021 / Source: VAM-UM-00551-EN-04
Despite careful checking, we cannot exclude the possibility of errors in this document and we accept no liability for the information it
contains.
Page 5
INSTALLATION
I portant infor ation
AUTION!
This product should be installed and maintained by technically qualified
personnel who have been trained on this specific product.
AUTION!
Read through the instructions before you install the device.
If you have any questions about installation or maintenance, call your local
supplier to obtain further information.
AUTION!
Volume flow meters for mineral oil are not recommended for water
applications.
If the measuring device is to be used for both mineral oil and water, brass water
meters are recommended. Please contact the manufacturer for customer-specific
details.
AUTION!
The volume flow meter may contain residual quantities of testing fluid when it
is delivered. This fluid should be removed before installation as this fluid may
be incompatible with some fluids or gases or dangerous.
Failure to follow this instruction may cause the device to be damaged!
AUTION!
This volume flow meter is unidirectional. The volume only flows in one
direction!
Any attempt to make fluids flow in the opposite direction to the flow arrow will
cause the measuring device to act as a non-return valve. The flow will be
stopped. The resulting increase in pressure will cause damage to the
components inside the measuring device!

Valid from: 15.02.2021 / Source: VAM-UM-00551-EN-04
Despite careful checking, we cannot exclude the possibility of errors in this document and we accept no liability for the information it
contains.
Page 6
The volume flow meter is a device that is easy to install. However, the following
measures are recommended to ensure it can be operated safely and without any faults:
Align the pipeline precisely. The piping should be aligned precisely and be of the
correct length. The high-pressure casing of the volume flow meter is able to
withstand impacts and flow/pressure pulsations. However, the pipeline should be
securely supported by external mounting brackets both before and after the
measuring device in order to prevent the pipeline from any sagging that might
shorten the useful life of the measuring device.
Use a rigid form of mounting. If the inlet or outlet of the volume flow meter is to
have a rigid mounting and the opposite connector is to be connected with a flexible
hose, the opposite end of the flexible hose must be mounted with a rigid fixing.
Use Teflon® tape to seal up the NPT threaded fitting.
Fit screw connections. Fit a screw connection close to the inlet or outlet of the
volume flow meter. This will make it quick and easy to remove or carry out an
inspection during the regular maintenance work.
Mount the volume flow meter either horizontally or vertically (flow arrow pointing
upwards or to the side). If the volume flow meter needs to be mounted inverted,
special inverted scales are available from the manufacturer.
Make sure that the fluid flows in the direction of the flow arrow (Figure 1 / p. 7).
Use at least one 74 µm filter. The measuring device will let through particles that
would block most valves and flow meters. Systems that do not have any filtering
should be equipped at least with a 74 µm filter.
Most hydraulic systems already have much finer filtering.
Dirt, iron filings or sealants, such as Teflon tape, may clog up the system and cause
malfunctions. If the measuring device has jammed in one position, follow the
cleaning and maintenance instructions.
Do not use any thread lock agent as a thread seal!
Do not install the volume flow meter near to any fittings that create turbulence, for
example elbows, reducer parts, short-cut valves, etc. The volume flow meter does not
require any flow straighteners or special lengths of straight inlet/outlet pipes to
stabilise turbulent flow patterns. However, in order to guarantee maximum
operational reliability, avoid fitting any elbows, valves and/or reducer parts in the
immediate vicinity of the device.
Do not install the volume flow meter in the vicinity of quick-acting valves. Quick-
acting valves may generate high hydraulic pressure peaks. These pressure peaks may
damage the internal components, which can cause inaccuracies or malfunctions.

Valid from: 15.02.2021 / Source: VAM-UM-00551-EN-04
Despite careful checking, we cannot exclude the possibility of errors in this document and we accept no liability for the information it
contains.
Page 7
Unidirectional devices (such as this volume flow meter) must not be operated in the
direction opposite to the one shown by the flow arrow. The piston acts like a non-
return valve and blocks the flow in the opposite direction. This causes an excessive
difference in pressure that may damage the internal components. The volume flow
meter is also available in a modified version that offers a bypass function for the
return flow in order to enable bidirectional flow.
Please note:
Volume flow meters are also available with a bypass function to allow reverse flow. lease
contact the manufacturer’s plant or the regional supplier for more details.
Installing the volu e flow eter
1. Mount the volume flow meter so that the fluid flows in the direction of the flow arrow.
Figure 1: Flow direction arrow
Flow direction

Valid from: 15.02.2021 / Source: VAM-UM-00551-EN-04
Despite careful checking, we cannot exclude the possibility of errors in this document and we accept no liability for the information it
contains.
Page 8
2. hoose an installation location that is suitable for inspection and product maintenance. To
connect the volume flow meter to the pipeline system, place a flat spanner on the wrench
flats of the volume flow meter next to the pipe connection that is to be installed.
Do not screw on the opposite end of the volume flow meter as this may cause leaks.
Attach the flat spanner on the same
side on which the pipelines are
tightened.
Never attach the flat spanner on the
opposite side of the pipeline that is to be
screwed on.
Figure 2: Installing the volume flow meter
Turn the volume flow meter by hand so
that you can see the flow scale.
Never use a flat spanner to turn the
protective casing in order to view the flow
scale.
Figure 3: Turning the volume flow meter

Valid from: 15.02.2021 / Source: VAM-UM-00551-EN-04
Despite careful checking, we cannot exclude the possibility of errors in this document and we accept no liability for the information it contains.
Page 9
Installing the power eter
1. Mount the power meter so that the fluid flows in the direction of the flow arrow. (
See Figure
1. Page 7
)
2. Install the power meter at any point in the hydraulic circuit, so that the volume flow,
pressure and temperature displays can be read easily. To connect the power meter to the
piping system, place a wrench on the valve block (wrench flat) on the inlet side.
Do not screw on the opposite end of the power meter as this may cause leaks.
(See
Figure 4).
Attach the wrench on the same side on
the valve body on which the pipeline is
tightened.
Never attach the wrench on the opposite
side of the pipelines that are to be
screwed on.
Figure 4 (schematic diagram): Mounting the power meter
3. Use the plastic caps that are also supplied to seal off the power meter after use and keep it
clean. Store it in a transport case.
Alternatively, use quick release couplings as a simple connection and to protect
against any contamination when the power meter is not in use.
You will find schematic diagrams illustrating the mounting position during typical
test procedures with the power meter under
(" onducting the power measurement”
on page 11
).

Valid from: 15.02.2021 / Source: VAM-UM-00551-EN-04
Despite careful checking, we cannot exclude the possibility of errors in this document and we accept no liability for the information it contains.
Page 10
Figure 5: ower meter in the transport case
4. Turn the premounted volume flow meter by hand after installation so that you can see the
flow scale.
Turn the volume flow meter by hand so
that you can see the display scale.
Never use a flat spanner to turn the
volume flow meter when you want to see
the display scale.
Figure 6 (schematic diagram): Turning the power meter

Valid from: 15.02.2021 / Source: VAM-UM-00551-EN-04
Despite careful checking, we cannot exclude the possibility of errors in this document and we accept no liability for the information it contains.
Page 11
OPERATION
Infor ation about the power eter
WARNING!
Always start with the load valve open.
Power meters are supplied with a closed load valve (1).
The load valve must be fully opened before the test in the hydraulic circuit is initiated.
Turn the load valve handle anticlockwise to open the load valve fully. If the load valve is
not opened fully, this may cause injuries to people and/or damage to the equipment.
Figure 7: Stainless steel power meter, 350 bar Type: HK S TKV Stainless steel
1
Loading valve (load valve)
2
Volume flow meter
3
Thermometer
4
Pressure gauge
5
Burst pressure protection
1
2
5
4
3
Pressure loading unit
Open the load valve
(free flow)
lose the load valve

Valid from: 15.02.2021 / Source: VAM-UM-00551-EN-04
Despite careful checking, we cannot exclude the possibility of errors in this document and we accept no liability for the information it contains.
Page 12
CONDUCTING THE POWER
MEASUREMENT
AUTION!
The information in this user manual is intended for general application only. All the
information that is provided by the manufacturer and/or constructor of the hydraulic
components of the machine, the hydraulic system, should be followed. Special systems
may require special test procedures. This is why the documentation for the
machine/hydraulic system should be consulted before conducting any measurements.
General infor ation
The power meter is designed for measuring volume flow Q [l/min] and pressure p [bar].
The result of the power measurement is calculated from the product of the volume flow and
pressure. When you use the power meter, the power P [kW] can be calculated using the
following practical formula:
∗
Standard test condition
1. Install the power meter as described in one of the following test procedures.
2. Open the load valve fully by turning the handle anticlockwise.
3. Start the pump and set it to the nominal speed.
4. Use the load valve to regulate the pressure in accordance with the test procedure you want
to carry out.
5. The power meter shows the flow rate, the set load pressure and the oil temperature.
AUTION!
Be aware of the maximum permissible pressure of the hydraulic components in the
hydraulic system!

Valid from: 15.02.2021 / Source: VAM-UM-00551-EN-04
Despite careful checking, we cannot exclude the possibility of errors in this document and we accept no liability for the information it contains.
Page 13
Pu p test
Figure 8: Schematic diagram of pump test
Figure 9: Hydraulic diagram of pump test
Test sequence
1. The power meter (4) is connected on the input side (IN) to the pressure line of the pump (1),
which is preferably safeguarded by means of a pressure relief valve (3).
2. With a fully opened loading valve (4.3), the hydraulic oil is returned to the tank on the
output side (OUT). Slowly closing the loading valve generates a steadily rising load pressure
p that is displayed on the pressure gauge (4.1) in [bar].
3. The oil temperature T can be read off the thermometer (4.2) in [° ].
Syste PRV
IN OUT
4.1
3
2
1
Syste
pressure
gauge
4.3
4.4
4.2
Tank
4.0

Valid from: 15.02.2021 / Source: VAM-UM-00551-EN-04
Despite careful checking, we cannot exclude the possibility of errors in this document and we accept no liability for the information it contains.
Page 14
4. The volume flow Q of the pump is now displayed as a function of the load pressure (4.1) on
the scale of the volume flow meter (4.4) in [l/min] (LPM).
5. The values that are read on the power meter (pressure, volume flow, temperature) can then
be compared with the p/Q characteristic curve
(pump specification)
in the data sheet from
the pump manufacturer and evaluated.
6. The power formula
(see page 11)
can then be used to calculate the hydraulic power P [kW]
of the pump and demonstrate the current level of efficiency.
Please note:
The pressure relief valve (3) must be set to the maximum permissible value, greater than the
load pressure (see page 14-15). The documentation from the manufacturer of the hydraulic
system/component should be noted here.
Pressure relief valve test
Pressure relief valves (PRV) (3)
(see
Figure 10)
often begin to open before the pump reaches its
full power.
The oil that flows away via a PRV is lost power and heats up the hydraulic oil in the system
unnecessarily.
Figure 10: Schematic diagram of pressure relief valve test
3
3.1
1
Syste PRV
IN OUT
Syste
pressure
gauge
4.1
Tank
4.3
4.4

Valid from: 15.02.2021 / Source: VAM-UM-00551-EN-04
Despite careful checking, we cannot exclude the possibility of errors in this document and we accept no liability for the information it contains.
Page 15
Test sequence
1. The power meter (4) is connected on the input side (IN) to the pressure line of the pump (1),
which is safeguarded by means of a pressure relief valve (PRV) (3).
2. With a fully opened loading valve (4.3), the hydraulic oil is returned to the tank on the
output side (OUT). Please note the value displayed on the scale (4.4) of the volume flow
meter [l/min] (LPM). Observe the pressure [bar] on the pressure gauge (4.1).
3. Slowly closing the loading valve (4.3) generates a steadily rising load pressure p that is
displayed on the pressure gauge (4.1) / ((3.1) if present) in [bar].
4. The volume flow Q of the pump is now displayed as a function of the load pressure (4.1) on
the scale of the volume flow meter (4.4) in [l/min] (LPM).
5. As the load pressure (4.1) starts to get close to the pressure that is currently set for the PRV
(3), some of the volume flow from the pump starts to flow into the tank via the PRV (3).
6. The value displayed on the scale (4.4) of the volume flow meter reduces.
7. Increase the set value for the PRV (3). Keep an eye on the scale (4.4), the value displayed on
the volume flow meter will increase roughly up to the value noted in step 2.
8. Repeat steps 3-6 above until the volume flow that is noted under step 2 is achieved as a
function of the max. desired system pressure (3.1) / (4.1).
Please note:
Note the specifications of the pump (slipping/leakage) and the performance of the pressure
relief valve (early opening, p/Q characteristic curves).
In practice, the system RV is generally set approx. 10-20 bar higher than the max. load
pressure. The documentation from the manufacturer of the hydraulic system/component
should be noted.

Valid from: 15.02.2021 / Source: VAM-UM-00551-EN-04
Despite careful checking, we cannot exclude the possibility of errors in this document and we accept no liability for the information it contains.
Page 16
MAINTENANCE
WARNING!
Before you remove the power meter from the line, check that the hydraulic system has
been depressurised. Failure to follow this instruction may cause serious physical injuries
or death and/or material damage.
Pressure release
Before starting work:
mobile hydraulic systems must be depressurised,
vehicle drives must be shut down,
hydraulic systems must be shut off,
hydraulic accumulators must be shut off and relieved on the pressure side.
Please note:
Be careful of any residual pressures caused by trapped volumes of fluid, e.g. between
valves and cylinders. They should be released by operating an adjusting lever or valve.
The pressure release should be checked, e.g. using a pressure gauge.
Dis antling and cleaning the volu e flow eter
1. Remove the power meter from the line. Remove any excess pipelines/screw connections
from the power meter.
Please note! It is not necessary to remove the transparent dust protection casing (15)
(see Table
1, page 4)
from the power meter in order to remove the meter from the line. If you wish to
remove the dust protection assembly from the volume flow meter, see "Removing the dust
protection” on
page 17
.
2. Wipe down the whole of the surface of the volume flow meter thoroughly with a mild
cleaning agent or isopropyl alcohol.
AUTION!
Do not use any aromatic hydrocarbons, halogenated hydrocarbons, ketones or ester-based
liquids to clean polycarbonate surfaces. Failure to follow this instruction may cause the
power meter to be damaged.

Valid from: 15.02.2021 / Source: VAM-UM-00551-EN-04
Despite careful checking, we cannot exclude the possibility of errors in this document and we accept no liability for the information it contains.
Page 17
3. Disconnect the volume flow meter (2) from the “
pressure loading unit
“, see
(
Figure 7 page 11)
4. Remove the end caps (13)
(see Table 1, page 4
) from the volume flow meter and note down
the order in which you dismantle things as a reference for when you reassemble them later
on.
5. The internal parts are secured with a locking ring. Remove the locking ring and the internal
parts that come into contact with media from the volume flow meter.
Please note:
If the internal parts do not slide freely out of the volume flow meter, use a wooden stick that
is inserted into the outlet opening of the volume flow meter to slide out the parts.
6. Place all parts on a clean work surface. lean and check all parts. Replace any parts that
appear worn or damaged. heck the O-ring seal (11)
(see Table 1, page 4
) of the inlet
connector for any damage and replace it if necessary.
AUTION!
Replacing the spring, measuring cone and/or piston/magnet assembly may cause changes
to the calibration of the volume flow meter.
7. Reinsert the spring, then the piston/magnet assembly and the locking ring in the volume
flow meter.
8. Install the dosing cone/star plate assembly and the locking spring. omplete the installation
by mounting the end cap.
9. Mount the volume flow meter back on the pressure loading unit.
Re oving the dust protection casing
To remove the dust protection to clean or replace it, use a suitable tool to loosen the screw
connection on the side of the measuring device and slide the end cap, the rubber protection
bumper and the dust protection casing off the measuring device.
Make sure that the O-ring seal between the end cap and the pressure body is not damaged.

Valid from: 15.02.2021 / Source: VAM-UM-00551-EN-04
Despite careful checking, we cannot exclude the possibility of errors in this document and we accept no liability for the information it contains.
Page 18
Reconnecting the agnetic coupling
This piston-type volume flow meter is less sensitive to impacts and vibrations than other float-
type designs.
The magnetic coupling dispenses with the need for a mechanical connection, which may
become worn or loose over the lifespan of the measuring device.
However, a pressure spike or sudden increase in volume flow may cause the piston magnet to
move at such a high velocity that the piston magnet (4) and the external display ring (5)
(see
Table 1, page 4)
become detached.
If this happens, use one of the following methods to reconnect the piston magnet and the
external display ring:
aution! The manufacturer’s documentation for the hydraulic system must be
followed.
If the system allows it, change the volume flow from "min. to no flow rate" to "max.
flow rate" so that the moving piston magnet (4) reconnects with the display ring (5)
magnetically.
In the case of heavily cyclical applications in which frequent decoupling can occur,
please contact one of the technical service staff for further recommendations.
Maintaining the pressure loading unit
Loading valve
If the loading valve (1)
(see Figure 7, page 11)
does not build up any load pressure in the
system, remove the load valve from the pressure loading unit. heck it for any foreign bodies
and worn parts or seals. heck the burst pressure protection (5)
(see Figure 7, page 11).
Replace
the defective burst pressure protection, see the “Replacing the safety disc” section on page 19
Volu e flow eter
If no volume flow is displayed on the volume flow meter (2) (
see Figure 7, page 11
), this may
indicate a clogged piston assembly (2) (
see Table 1, page 4
). Remove any material that might
prevent the piston from sliding. Note the “
Reconnecting the magnetic coupling”
section on
page 18.
Note the “
Dismantling and cleaning the volume flow meter”
section on
page 1.
If the volume flow meter still does not show any flow, return the measuring device to the
factory for inspection.
Replacing the safety disc
Power meters of the type:
HK 7xx Sxx TKV
made from stainless steel are equipped with overload
protection. This overpressure protection is located in the pressure loading unit. (
Burst pressure
protection
(5), see
Figure 7, page 11)

Valid from: 15.02.2021 / Source: VAM-UM-00551-EN-04
Despite careful checking, we cannot exclude the possibility of errors in this document and we accept no liability for the information it contains.
Page 19
The burst pressure protection breaks at a pressure of over 400 bar. Stainless steel volume flow
meters are designed for an operating pressure of up to 350 bar and a safety factor of 3:1.
Burst pressure protection HANSA-FLEX article number:
K-MEP2470
Figure 11: ower meter with burst pressure protection
Figure 12: Locking screw
Figure 13: (Hex nut) screw-in part with safety disc
1. Remove the locking screw from the power meter (
see Figure 11/ 12)
2. Remove the screw-in part from the locking screw
3. The safety disc is located in the bottom section of the screw-in part
(see Figure 13)
Undo
the hex nut and replace the defective safety disc (P2470) Art. No. K-MEP2470. The safety
disc deforms when the hex nut is tightened.
Make sure that the high-pressure seal fits correctly when it is remounted!
Table of contents
Popular Measuring Instrument manuals by other brands
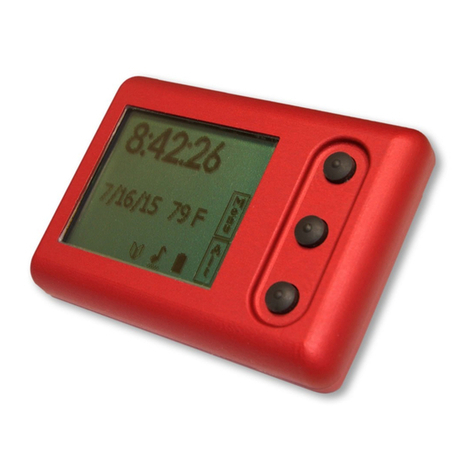
Alti-2
Alti-2 Altimaster Atlas quick start guide

Leica
Leica NA320 user manual
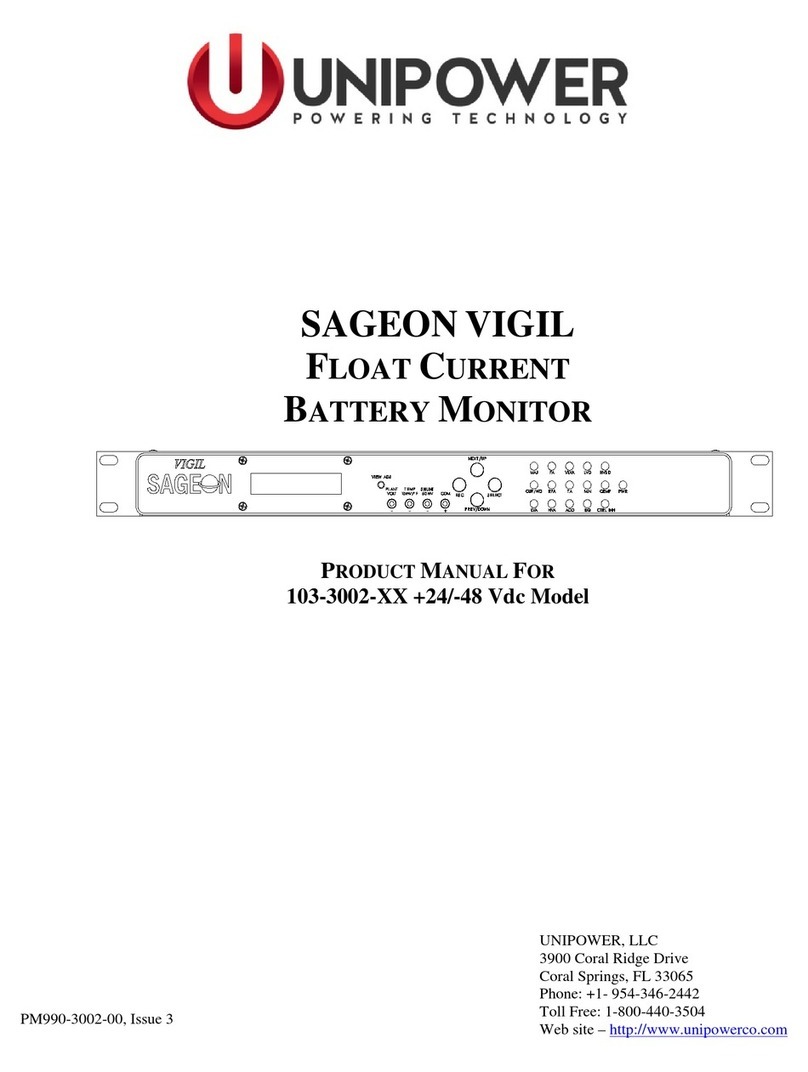
Unipower
Unipower 103-3002 Series User's product manual
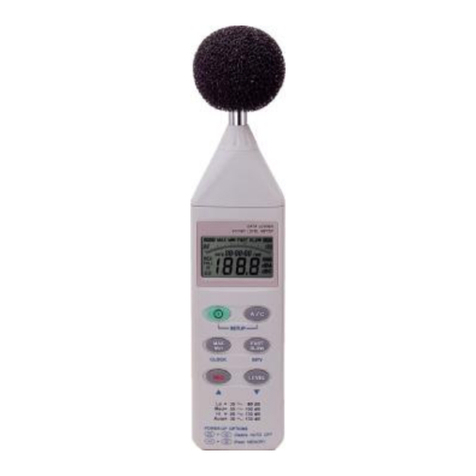
Dostmann Electronic
Dostmann Electronic 5020-0322 instruction manual

Sper scientific
Sper scientific 300058 instruction manual
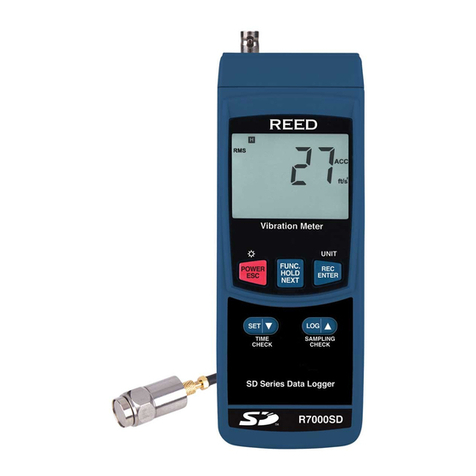
Reed Instruments
Reed Instruments R7000SD instruction manual