Hansen P4 User manual

nNieuwe
instructies
zijn met een grijze
balk in de marge
aangeduid.
ansen
M
E
M
B
E
R
O
F
An Invensys company
405 EFDNd
ISO 9001
Standardized Réducteurs de Normzahnrad- Standaard
gear units vitesse standard getriebe tandwielkasten
Service Manuel Betriebs- Bedrijfs-
manual d'entretien anleitung handboek
nNew
instructions
are indicated by
a grey bar in the
margin.
Nouvelles
instructions
sont marquées
d'une barre verti-
cale grise dans la
marge.
Neue
Vorschriften
sind mittels eines
grauen Balkens
in der Marge
markiert.
!
SHIPPED
WITHOUT
OIL !
LIVRE
SANS
HUILE !
GELIEFERT
OHNE
ÖL
GELEVERD
ZONDER
OLIE
!
n n

!
n
M
!
n
M
MANUFACTURING OR ASSEMBLY IN
Australia Germany The Netherlands
Belgium Italy United Kingdom
Canada Japan USA
China South Africa
France Sweden
CONTENTS Page
1 GENERAL 4
2 SHIPPING 4
3 STORAGE 4
4 HANDLING 4
5 INSTALLATION 5-6-7-8
6 LUBRICATION 8-9
7 COOLING 9-10
8 BACKSTOPS 10
9 STARTING-UP 10
10 MAINTENANCE 11
LUBRICANTS 36
INDEX Page
1 GENERALITES 12
2 LIVRAISON 12
3 ENTREPOSAGE 12
4 MANUTENTION 12
5 INSTALLATION 13-14-15-16
6 LUBRIFICATION 16-17
7 REFROIDISSEMENT 17-18
8 ANTIDEVIREURS 18
9 MISE EN MARCHE 18
10 ENTRETIEN 19
LUBRIFIANTS 36
ENGLISH : see pages 4...11
: DANGER
: WARNING
: MAINTENANCE
: NEW INSTRUCTIONS
WORLDWIDE TRANSMISSION SERVICE ORGANISATION INTERNATIONALE DE VENTE
FRANCAIS : voir pages 12...19
: DANGER
: AVERTISSEMENT
: ENTRETIEN
: NOUVELLES INSTRUCTIONS
ansen
2
AUSTRALIA
• Melbourne Tel. : (3) 9729 3300
Head Office Fax: (3) 9729 7626
• Brisbane Tel. : (7) 3279 1399
Fax: (7) 3279 1366
• Perth Tel. : (8) 9451 8777
Fax: (8) 9451 4389
• Sydney Tel. : (2) 9792 2355
Fax: (2) 9792 2663
• Newcastle Tel. : (24) 9528 131
Fax: (24) 9561 935
AUSTRIA
• Wien Tel. : (1) 774 5759
(Vienna) Fax: (1) 774 5758
BELGIUM
• Antwerp Tel. : (3) 450 12 11
(export sales) Fax: (3) 450 12 20
• Brussels Tel. : (2) 255 42 11
Fax: (2) 252 52 82
CANADA
• Montreal - Quebec Tel. : (514) 735 1521
Fax: (514) 342 2877
• Vancouver - British Columbia
Tel. : (604) 533 1580
Fax: (604) 533 0759
• Toronto - Ontario Tel. : (416) 675 3844
Fax: (416) 675 6885
CHINA
• Changzhou Tel. : (519) 648 3076
Fax: (519) 648 3026
DENMARK
• Herlev Tel. : (45) 44 50 13 70
Fax: (45) 44 50 13 79
FRANCE
• Raon l'Etape Tel. : 3 29 52 62 72
(Nancy) Fax: 3 29 41 80 40
• Paris Tel. : 1 47 60 19 60
Fax: 1 47 81 29 29
• Lyon Tel. : 4 72 60 02 40
Fax: 4 78 95 15 44
GERMANY
• Hameln Tel. : (5151) 780-0
Fax: (5151) 780 356
• Castrop-Rauxel Tel. : (2305) 921 300
Fax: (2305) 921 3030
TRANSMISSIONS
ansen
®
Every care has been taken to ensure the accuracy of the information contained
in this publication, but, due to a policy of continuous development and improve-
ment the right is reserved to supply products which may differ slightly from
those illustrated and described in this publication.
Please contact one of the worldwide sales centres for information on any
aspects of storage, installation, operating, lubrication and maintenance that
need clarifying.

SOUTH AFRICA
• Boksburg Tel. : (11) 397 2495
Fax: (11) 397 2585
SWEDEN
• Spånga Tel. : (8) 445 71 20
(Stockholm) Fax: (8) 445 71 30
• Sundsvall Tel. : (60) 318 10
Fax: (60) 318 05
• Hven Tel. : (418) 720 06
Fax: (418) 725 77
• Väräbacka Tel. : (340) 66 06 60
Fax: (340) 66 06 45
THE NETHERLANDS
• Almelo Tel. : (546) 488 500
Fax: (546) 872 035
TRANSMISSIONS
ansen
®
INHALTSVERZEICHNIS Seite
1 ALLGEMEINES 20
2 LIEFERUNG 20
3 LAGERUNG 20
4 TRANSPORT 20
5 AUFSTELLUNG 21-22-23-24
6 SCHMIERUNG 24-25
7 KÜHLUNG 25-26
8 RÜCKLAUFSPERREN 26
9 INBETRIEBNAHME 26
10 WARTUNG 27
SCHMIERSTOFFE 36
INHOUD blz.
1 ALGEMEEN 28
2 LEVERING 28
3 OPBERGING 28
4 BEHANDELING 28
5 INSTALLATIE 29-30-31-32
6 SMERING 32-33
7 KOELING 33-34
8 TERUGLOOPBLOKKERING 34
9 INBEDRIJFSTELLING 34
10 ONDERHOUD 35
SMEERMIDDELEN 36
INTERNATIONALE VERKAUFSORGANISATION INTERNATIONALE VERKOOPSORGANISATIE
ansen
3
ITALY
• Milano Tel. : (2) 2720 2171
Fax: (2) 2565 559
JAPAN
• Tokyo Tel. : (3)5224 3305
Fax: (3)5224 3300
NORWAY
• Langhus Tel. : (64) 86 08 00
(Oslo) Fax: (64) 86 76 70
SINGAPORE Tel. : (65) 332 0534
Fax: (65) 337 8786
UNITED KINGDOM
• Huddersfield Tel. : (1484) 431414
Fax: (1484) 431426
U.S.A.
• Colombus Tel. : (614) 675 3000
(OH) Fax: (614) 675 3001
• New Orleans Tel. : (504) 524 2363
(LA) Fax: (504) 528 9074
• Horsham Tel. : (215) 682 0400
(PA) Fax: (215) 773 4463
• Stuarts Draft Tel. : (540) 337 3510
(VA) Fax: (540) 337 1317
• Milwaukee Tel. : (414) 643 2576
(WI) Fax: (414) 643 2597
MANUFACTURING OR ASSEMBLY IN
Australia Germany The Netherlands
Belgium Italy United Kingdom
Canada Japan USA
China South Africa
France Sweden
!
n
M
!
n
M
DEUTSCH : siehe Seiten 20...27
: GEFAHR
: ACHTUNG
: WARTUNG
: NEUE VORSCHRIFTEN
NEDERLANDS : ZIE BLZ. 28...35
: GEVAAR
: OPGELET
: ONDERHOUD
: NIEUWE INSTRUCTIES
Every care has been taken to ensure the accuracy of the information contained
in this publication, but, due to a policy of continuous development and improve-
ment the right is reserved to supply products which may differ slightly from
those illustrated and described in this publication.
Please contact one of the worldwide sales centres for information on any
aspects of storage, installation, operating, lubrication and maintenance that
need clarifying.

n
!
!
SCOPE
This service manual contains the installation, operating, lubrication and main-
tenance instructions relative to the Hansen P4 standardized gear units.
Additional information can be obtained by contacting one of the HANSEN
sales centres worldwide (p. 2-3)
All handling, storage, installation, start-up,
inspection and maintenance of the equipment
shall be done by personnel qualified in matters
of industrial mechanical and - where applicable -
electrical equipment.
1. GENERAL
1.1. GENERAL INSTRUCTIONS
Carefully read this manual before installing the gear unit.
Compliance with the instructions will assure long and troublefree operation of
the gear unit.
The equipment should be checked against shipping papers and inspected for
apparent damage sustained during transport. Any shortage, discrepancy or
damage must immediately be reported to HANSEN.
1.1.1. Warranty
The warranty clause of the "General Conditions of Sale" applies to gear units
installed and maintained as per instructions contained in this manual and in
any additional instruction leaflets supplied with the gear unit insofar as the
gear unit operates within the service and rating conditions put forward in the
"Order Acknowledgement" and on the certified drawings.
Non compliance with these instructions, injudicious choice of lubricant or a
lack of maintenance will render warranty agreement invalid.
This warranty clause applies to all parts of the gear unit with the exception of
these parts which are subject to wear.
1.1.2. Safety
It is not allowed to use the gear unit for other
applications or in other operating conditions than
the one for which it is ordered.
The user shall be responsible for the proper in-
stallation of the complete equipment and the
supply of protection guards and other safety
equipment in accordance with local safety regu-
lations.
Heaters, coolers, electrical alarms and other safety or monitoring devices
supplied by HANSEN with the equipment must be installed and connected by
the user as indicated on the relative document.
1.2. GENERAL SPECIFICATIONS
For general specifications such as dimensions, weight, connecting diagrams,
refer to certified drawing of the gear unit and/or to the Hansen P4 standard-
ized gear unit catalogues.
1.3. IDENTIFICATION
Inquiries concerning a gear unit should always specify the unit's complete
type code and manufacturing number, which can be found on the name-
plate.
The nameplate, which is fitted on each gear unit, also contains ratings
and/or torque, speed and lubrication instructions.
This information is essential to identify positively the unit supplied by
HANSEN.
2. SHIPPING
Prior to shipment each unit has been inspected and accepted by the QUALITY
CONTROL DEPARTMENT according to order specifications, and after no
load test of several hours in its normal operating position and at speed
indicated on the nameplate.
2.1. SHIPPING CONDITIONS
Unless otherwise specified, gear units are shipped in unpacked condition
and depending on necessity, fixed on wooden pallets with open crating
protection. Sometimes parts, such as spare filter elements, are separately
packed. In such events, the end-user must take care of the assembly (see
chapter 5. INSTALLATION p. 5).
The HANSEN P4 gear unit is shipped without oil.
All grease lubrication points are factory filled.
2.2. PAINTING
The standard external paint for HANSEN gear units is an epoxy primer with
high solids content, corresponding to the German Standard RAL 5021, water
blue.
This paint system offers a 5 year protection for indoor installation provided
the gear unit is not subjected to humid or chemical aggressive atmospheric
conditions.
Overcoating is possible with most paints based on alkyd-, epoxy or
polyurethane resins.
2.3. PRESERVATION
The inner parts of the gear units are sprayed with rust preventing mineral oil.
The breather plug (standard, dust-proof, anti-humidity) is neither removed nor
sealed.
The shaft extensions are protected with a rust preventing grease and waxed
paraffin paper. The hollow shafts and all unpainted machined surfaces are
coated with an anti-oxidizing waxy varnish.
This standard system offers corrosion protection during transport and/or
storage for up to one year indoors.
3. STORAGE
Always store gear units in their originally sup-
plied shipping conditions.
Gear units should not be stored near vibrating
machines in order to avoid damage to bearings.
3.1. SHORT TERM STORAGE
Up to one year indoors. Always store units in their originally supplied
shipping conditions.
3.2. LONG TERM STORAGE
Max. 5 years indoors or 6 months outdoors.
•The protection should be kept intact if long term storage was specified at
order placement.
• In all other cases the gear unit must be filled with a small amount of
mineral oil containing a volatile corrosion protection additive. All gear
unit openings (dipstick, breather etc.) should be hermetically sealed.
Some additives may be added to the normal oil. Consult your oil
supplier.
4. HANDLING
The Hansen P4 gear units are easy to handle and to install. Make use of in-
tegral oval lifting eyes (horizontal mount) and lifting eye nuts or integral rods
(vertical mount).
For equal load sharing make use of all lifting eyes and use adequate tools.
Lifting eye nuts must not be removed and must
be fully engaged before lifting.
Never lift units with slings wrapped around the
shafts.
Particular circumstances might dictate the temporary removal of thermostat(s),
pressure gauge(s) and/or part of the oil feed piping. After removal of the lat-
ter elements, one should take special care to avoid ingress of moisture,etc...
into the lubrication system of subject gear unit(s).
4
ansen
TRANSMISSIONS
ansen
®

n
5. INSTALLATION
5.1. FITTING OF ACCESSORIES
The metric shaft extensions are equipped with keyways according to
ISO/R773-1969 and DIN 6885 "Blatt 1 - Form N1 or N3".
Threaded centre holes in these shafts according to DIN 332 Teil 2 Form D.
Recommended bore tolerance for the couplings or other components to be
mounted is K7 (as per ISO 286).
The inch shaft extensions are equipped with keyways according to USAS
B17.1-1967.
Recommended bore tolerance :
- 0.0005" to - 0.001" for diameters ≤1 1/2"
- 0.001" to - 0.002" for diameters > 1 1/2"
Remove protection from shaft extensions and check keyfit and keyway height
in component to be mounted onto shaft. Heating the component to 80-100°C
(175-210°F) will be helpful. Threaded centre hole in shaft to assist in moun-
ting components onto shaft may be used.
Never mount components by impact as this may
cause damage to the bearings.
Never use rigid couplings except on free end machine shafts (e.g. mixers,
aerators) or in executions with a torque arm.
5.2. EXTERNAL LOADS
If external loads act on the gear unit, thrust blocks must be installed against
the unit's feet, to prevent gear unit from shifting. Components transmitting
radial load to the shaft should be mounted as close as possible to the hous-
ing.
Avoid exaggerated tension in transmission belts mounted on input or output
shafts. On gear units with built-on motor and V-belt drive, tension has been
factory set. Tension should be rechecked after 24 hours service. Chain trans-
missions must be mounted without preliminary tension.
In case a pinion is mounted on the shaft extension of the gear unit, care
should be taken to have normal required backlash between pinion and gear
and good contact pattern must be assured.
5.3. ERECTION
5.3.1. Levelling
Always mount gear unit in position for which it
was ordered.
Before altering this position or inverting the unit, please consult HANSEN.
It may be necessary to readapt the lubrication system.
5.3.2. Alignment
Align gear unit as accurately as possible with driving and driven machinery.
Install gear unit level to better than 5 mm per 1 m (5/32 inch per 3 feet or
5mrad or 17 arc minutes) or within the limits indicated on the outline
drawing for positions other than horizontal.
Maximum allowable misalignment depends on the couplings fitted on the
shaft extension, please refer to data provided with coupling.
Use three fixation points of gear unit for alignment. Adjust other fixation
points by shimming to 0,1 to 0,2 mm (0.004 to 0.008 inch), depending on
the size of the gear unit.
5.4. SECURING OF SOLID SHAFT GEAR UNIT
Gear unit must be mounted onto a rigid and stable bedplate or foundation in
order to avoid vibrations.
Use fixation holes indicated on dimensional drawing.
After correct alignment and shimming of all points, fix gear unit solidly onto
its foundation with appropriate size bolts, grade 8.8 according to DIN 267
or SAE grade 5 for bolts 1 1/2" and smaller, ASTM.A-354 grade BC for
bolts larger than 1 1/2". Dimensions and tightening torques: see table.
Note: for some horizontal executions with parallel shaft and fans, the
protection hood of the fan must be removed (and remounted afterwards) to
enable tightening of the bolts.
Horizontal mount
- Single stage gear units (type QHP.1)
- Multi stage gear units (type QH...)
Vertical mount
- Multi stage gear units (type QV...)
(1) size G : 2-stage unit
(2) size G : 3- and 4-stage unit
The alignment of the complete drive packages mounted on a bedplate have
been carefully checked before shipment. It is nevertheless required to check
that the bedplate has not been deformed during transport or erection.
Therefore check again alignment of couplings or other elements after final
installation.
5.5 SECURING OF HOLLOW SHAFT GEAR UNITS
5.5.1. Hollow shaft gear unit with shrink disc
connection
The HANSEN supplied shrink disc is ready to be
installed.
Therefore do not dismantle shrink disc prior to first mounting.
The HSD-type is used as standard (fig. 1c, page 6).
Upon request the SD-type is possible (fig. 1d, page 6).
Mounting (fig. 1a)
- Clean and degrease contact surfaces (a) and (b)
- Smear surface (b) - and not surface (a) - with "Molykote D321R" or
similar.
- After the applied coating has hardened, slide the O-ring (c) onto the shaft.
- Draw the gear unit onto the shaft of the machine using threaded rod (e),
nut (f) and distance ring (g) until faces (h) and (i) make contact.
- Fit shrink disc (s). A locating groove on the shaft indicates the position of
the shrink disc. Tighten bolts (ZS) with a torque wrench. The required
tightening torque for the HSD-type is shown in table 1 (page 6) .
For the SD-type it can be found on the dimensional drawing.
NOTE : Never tighten bolts when shrink disc is
unmounted.
ansen
Gear unit size C D E F G
ISO M20 M24 M24 M30 M30
UNC 3/4" 7/8" 1" 1 1/8" 1 1/4"
Nm 285 450 660 830 1150
lbf.in 2500 4000 5800 7300 10000
Tightening
torque
Bolt size
Gear unit size C D E F-G(1) G(2)-H-J-K L-M-N-P-Q R-S-T
ISO M24 M30 M30 M36 M42 M48 M56
UNC 1" 1 1/8" 1 1/4" 1 1/2" 1 3/4" 2" 2 1/4"
Nm 660 830 1150 2000 2500 3500 5300
lbf.in 5800 7300 10000 18000 22000 31000 47000
Tightening
torque
Bolt size
a
cb
h
is
ZS
e
f
g
•
•
ZY
gl
•
•
1 b
FIG. 1
1 a
TRANSMISSIONS
ansen
®
Gear unit size A B C D E-F G-H-J-K L-M N-P-Q R-S-T
ISO M16 M20 M24 M24 M30 M36 M42 M48 M56
UNC 5/8" 3/4" 7/8" 1" 1 1/4" 1 1/2" 1 3/4" 2" 2 1/4"
Nm 165 285 450 660 1150 2000 2500 3500 5300
lbf.in 1450 2500 4000 5800 10000 18000 22000 31000 47000
Tightening
torque
Bolt size
DISMOUNTING
5
MOUNTING

6
HSD type (fig. 1c)
The tightening torques (TA) are indicated in table 1 and on the name plate (p).
Tightening bolts are prestressed to the right level when outer ring (o) and inner
ring (n) are flush (optical check).
SD type (fig. 1d)
The tightening torques are indicated on the name plate (p) and on the dimen-
sional drawing.
Remove spacers, attached for shipping, from between outer rings (o). When
mounting and during tightening make sure that outer faces remain parallel.
HSD + SD type
Tighten bolts (ZS) in indicated sequence (q) one by one, progressively over
several rounds, until required tightening torque (TA) is reached.
Do not tighten bolts crosswise.
Mount protection hood.
Securing in case of axial load
If the axial load is not absorbed by the shoulder of the machine shaft,
a distance ring (g) must be included (see fig. 2b, page 7).
Dismounting (fig. 1b, page 5)
- Loosen all tightening bolts (ZS) uniformly, one by one in a continuous
sequence, about a quarter of a turn per round.
- Should outer and inner ring of the HSD-type not release themselves, one
can remove some tightening bolts and install them in tapped holes (r), in
the inner ring, to trigger separation of both rings.
- Remove shrink disc from hollow shaft.
- Mount the distance ring (g) on the hollow shaft by means of bolts (ZY)
(dimensions of ZY: see dimension drawing).
- Place the disassembly bolt (l) into the central hole in the distance ring (g).
- Remove the gear unit from the shaft by tightening the disassembly bolt (l).
Note
The parts e,f,g,l and ZY are not included as standard. They can be supplied
upon special request.
For technical data, refer to catalogue or certified drawing.
Cleaning and greasing
Dismounted shrink discs do not have to be taken apart for cleaning and
regreasing prior to reinstallation, unless they have been used in a very dirty
environment.
After cleaning, recoat the tapered surfaces using a solid lubricant with a
friction coefficient of 0,04 , e.g. Molykote D321R or similar.
ansen
Shrink discs TA
Nm
TA
lbf.in
HSD 110-81x110 121 1070
HSD 125-81x125 121 1070
HSD 140-81x140 193 1700
HSD 165-81x165 295 2600
HSD 185-81x185 295 2600
HSD 220-81x220 570 5000
HSD 240-81x240 570 5000
HSD 260-81x260 570 5000
HSD 280-81x280 570 5000
HSD 320-81x320 980 8600
HSD 340-81x340 980 8600
HSD 360-81x360 980 8600
HSD 390-81x390 1450 12800
HSD 420-81x420 1450 12800
HSD 440-81x440 1450 12800
HSD 480-81x480 1450 12800
HSD 500-81x500 1970 17400
HSD 530-81x530 1970 17400
Table 1
1
2
3
4
5
67
8
9
1
2
3
4
5
6
78
9
1 c
1 d
n
o
p
q
a
ZS
SD TYPE
q
o
r
ZS
n
a
p
HSD TYPE
FIG. 1
n
TRANSMISSIONS
ansen
®

n
7
5.5.3. Mounting of the torque arm
After fitting and securing the gear unit to the driven shaft (see par.5.5.1 and
5.5.2), fix unit by means of the optionally supplied torque arm to a fixed
torque reaction point. Refer to the certified drawing or catalogue for torque
arm location on gear unit.
The connection between torque arm and reaction point must remain flexible
and resilient. This is achieved by preloading the disc springs of the torque arm.
The preload of the disc springs (A) will be adjusted as follows:
- Determine the spacing S (fig. 3a), this is the spacing of the disk springs in
unloaded and unmounted condition.
- Screw the nuts until spacing S1 (spacing between gear unit and fixed
point) is reached, where S1 = S - ∆S (fig. 3b, 3c, 3d)
∆S = spacing obtained after compression of the disk springs
(table 2, 3 and 4) due to the weight of the gear unit and
tightening of the nuts.
- When the prescribed spacing S1 is obtained, lock the nuts by tightening
outer nut against inner nut.
5.5.2. Hollow shaft gear unit with keyway
connection
Mounting (fig. 2a)
- Coat mating faces (b) of the machine shaft with sealing compound.
- Slide the O-ring (c) onto the machine shaft.
- Place supplied mounting key (d) into keyway of machine shaft, with the boss
against the shaft face.
- Place the gear unit into position on the machine shaft. Make sure that the
keyways are correctly positioned.
- Press the gear unit on the shaft, using a threaded rod (e), a nut (f), and a
distance ring (g) until the mounting key (d) and the distance ring (g) make
contact.
- Remove the nut (f), the distance ring (g) and the mounting key (d).
- Ensure that key (m) has sufficient clearance on top.
- Fit the key (m) into the shaft (≠mounting key).
- Remount the distance ring (g) and the nut (f).
- Draw the gear unit further onto the shaft until the faces (h) and (i) make
contact.
- Remove the nut (f), the distance ring (g) and the threaded rod (e).
Securing (fig. 2b)
- Mount the distance ring (g) again on the machine shaft using correct
fixation bolts (J).
- Install the protection cover (k).
In case of external axial loads on the shaft, please refer to specific instruc-
tions on the outline drawing.
Dismounting (fig. 2c)
- Remove the protection cover (k) and the fixation bolts (J).
- Mount the distance ring (g) on the hollow shaft by means of bolts (ZY)
(dimensions of ZY: see dimensional drawing).
- Place the disassembly bolt (l) into the central hole in the distance ring (g).
- Remove the gear unit from the shaft by tightening the disassembly bolt (l).
Note
The parts e,f,l and ZY are not included as standard, but can be supplied
upon special request.
For technical data, refer to catalogue or certified drawing.
ansen
DISMOUNTING
b
h
i
cd
e
f
g
•
•
FIG. 2
MOUNTING
k
J
g
m
•
•
2b
SECURING
ZY
l
g
m
•
•
2c
FIG. 3
AS
Table 2
Table 3
3a
Q*: number of disc springs
Q*: number of disc springs
PR
S1= S - S
PT
D
3b
DPT PR max ∆S A
±5mm inch mm inch Q* DIN 2093
QH.A2 35 M16 40 1.57 0,7 0.028 2 x 2 A 80
QH.B2 35 M20 50 1.97 0,7 0.028 2 x 2 A 80
QH.C2 45 M24 60 2.36 0,9 0.035 2 x 2 A 100
QH.D2 45 M24 60 2.36 0,9 0.035 2 x 3 A 100
QH.E2 60 M30 75 2.95 1,0 0.039 2 x 3 A 125
QH.F2 60 M30 75 2.95 1,0 0.039 2 x 3 A 125
QH.G2 60 M36 90 3.54 1,0 0.039 2 x 4 A 125
QH.H2 60 M36 90 3.54 1,0 0.039 2 x 4 A 125
Gear unit
size
S1= S - S
PR
PT
D
3c
DPT PR max ∆S A
±5mm inch mm inch Q* DIN 2093
QH.C3 35 M20 50 1.97 0,7 0.028 2 x 3 A 80
QH.D3 - QH.D4 45 M24 60 2.36 0,9 0.035 2 x 2 A 100
QH.E3 - QH.E4 45 M24 60 2.36 0,9 0.035 2 x 3 A 100
QH.F3 - QH.F4 60 M30 75 2.95 1,0 0.039 2 x 2 A 125
QH.G3 - QH.G4 60 M36 90 3.54 1,0 0.039 2 x 3 A 125
QH.H3 - QH.H4 60 M36 90 3.54 1,0 0.039 2 x 3 A 125
Gear unit
size
TRANSMISSIONS
ansen
®
2a

!
M
6.2.2. Pressure lubrication
The service manual of the lubrication and cooling system gives detailed
information about the pressure lubrication system.
6.2.3. Instrumentation and settings
For detailed information on lubrication system, instrumentation and settings,
refer to the certified drawing, the service manual of the lubrication and cooling
system and/or separate leaflets on instrumentation, supplied with this manual.
Settings stated on the certified drawing have been
set during testrun by HANSEN and should not be
altered without written authorisation.
Presettings, if stated, are recommended values set by HANSEN, but may be
altered according to local conditions.
6.3. OIL SELECTION
Mineral oils containing EP additives, which increase oil film load capacity,
should be used.
Always use oil of the type and with viscosity
characteristics corresponding to those given on
gear unit's nameplate.
The viscosity has been selected according to operating conditions specified in
the order.
For conversion from ISO viscosity class VG to other viscosity units see table of
corresponding lubricants p. 36.
The table is not exhaustive; equivalent brands can be used.
The oil suppliers are responsible for the selection and composition of their
products.
Synthetic oils may be used only after written au-
thorisation from the HANSEN Engineering Depart-
ment.
Only synthetic oils of the polyalpha-olefine type (SHF-type, Synthetic Hydrocar-
bon Fluid) containing EP additives may be used. Due to the good oxidation-
durability of synthetic oils their life expectancy is longer than that of mineral oils
of the same viscosity and for the same working conditions. A longer use is on-
ly permitted if an oil analysis is made regularly (every 4000 hours) by the oil
supplier or a qualified laboratory, in order to determine the exact life-time of
the oil.
6.4. OIL QUANTITY (see fig. 5, page 9)
The oil level is determined by min. and max.
markings on the dipstick.
An oil level glass or an oil level switch is optionally available.
THREADED DIPSTICKS SHOULD BE CHECKED IN
PLUGGED POSITION.
The oil level must be checked when the gear unit is
out of operation.
On systems with filters and coolers, oil level must
be checked with lubrication and cooling system
filled with oil and after short test run.
The lubrication and cooling system, including the cooler, is automatically
utilized when the oil bath temperature rises above 60°C (140°F).
If oil filling is required to take place earlier, manual ventilation of the cooler
must be carried out whilst the pump is in operation.
The oil quantity mentioned on the nameplate of the gear unit is an approximate
value given only for procurement purposes.
F
P
Mf •
••
•
8
6. LUBRICATION
Lubrication serves four main functions :
- prevents metal to metal contact in gears and bearings
- reduces friction losses
- dissipates the generated heat from gears and bearings
- prevents corrosion
Different lubrication systems can be used, depending on
- gear velocity
- gear unit mounting position
- operating conditions
HANSEN gear units use one of following systems :
- splash lubrication
- forced feed lubrication: - circulation lubrication
- pressure lubrication
These systems can be completed with auxiliary cooling in different forms (see
COOLING).
6.1. SPLASH LUBRICATION
Splash lubrication is standard with horizontal shaft gear units and for speeds
between 750 and 1800 min-1 at the high speed shaft. Gears and output
shaft bearings are lubricated by immersion in the oil bath. Oil splash from
gears fill oil pockets in the housing, assuring gravity circulation lubrication of
the bearings via channels in housing and covers.
For other speeds at the high speed shaft, refer to HANSEN.
6.2. FORCED FEED LUBRICATION
All rotating elements above oil bath level are lubricated by a gear pump
forcing the oil through pressure lines.
Pumps can be either of the integral type, driven by one of the gear unit
shafts, or a motorpump. The integral type pumps are always provided with a
built-in reversing device for operation in both directions.
In case of motorpumps the direction of rotation is always indicated.
Built-on pumps reach their normal operating capacity already after a few sec-
onds. However, in order to avoid unwanted alarm during the start-up period,
we recommend to delay the triggering of the warning signal by 5 to 10
seconds.
Motorpumps should be switched on at least one
minute before starting the gear unit.
6.2.1. Circulation lubrication
- With integral pump (fig.4).
The circulation lubrication system consists of
- a pump P
- a filter F with bypass (standard from gear unit size G onwards)
- a flow switch Mf (standard from gear unit size G onwards)
Flow switch must be wired in a circuit to automa-
tically stop the main drive motor when oil flow
drops below alarm setting.
- With motorpump
The service manual of the lubrication and cooling system gives detailed
information about the circulation lubrication system with motorpump.
ansen
Q*: number of disc springs
FIG. 4
S1= S - S
PR
PT
D
3d
Table 4
D PT PR max ∆SA
±5mm inch mm inch Q* DIN 2093
QH.J3 - QH.J4 80 M42 105 4.1 1,4 0.055 2 x 3 A 160
QH.K3 - QH.K4 80 M42 105 4.1 1,4 0.055 2 x 3 A 160
QH.L3 - QH.L4 80 M48 120 4.7 1,4 0.055 2 x 4 A 160
QH.M3- QH.M4 80 M48 120 4.7 1,4 0.055 2 x 4 A 160
Gear unit
size
TRANSMISSIONS
ansen
®

6.5. THE FIRST OIL FILLING (see fig. 5)
Fill units only after final installation, especially gear units with vertical
downwards shafts, to prevent oil splashing over drywell during handling.
Fill the gear unit exclusively through the oil filling open-
ing which is provided in the inspection cover for that
purpose. In that way, all bearings are lubricated with
fresh oil.
Note :
- Additional oil filling of the bearing housing.
4-stage horizontal gear units with right angle shafts
(QHR.4) and 3- and 4-stage vertical gear units with
right angle shafts (QVR.3 + QVR.4) require on initial
oil filling also an additional oil filling of the bearing
housing.
See special sticker on gear unit.
The additional oil quantity is mentioned on the
certified drawing and on the sticker.
M
M
M
M
M
M
- Oil filling of a gear unit with M1 or M3 motor base.
Units with horizontal shafts (QH ..) equipped with a motorbase M1 and
M3 must be filled on initial filling with a small quantity of oil through the
inspection cover located in the top face of the gear unit (see special sticker
on gear unit).
If easy access to the oil filler plug is prevented through lack of space
between the motor base and the gear unit upper face, the motor base
should be raised following removal of the belt.
For gear units with M1 motor base the normal oil filling plug is located at
the side of the output shaft, opposite the side where the dipstick is
located.
For gear units with M3 motor base the normal oil filling plug is located at
the side of the dipstick.
If the gear unit is filled with storage oil, it has to be drained and it may in
some instances be necessary to rinse the gear unit with the selected oil before
starting up. Check with the oil supplier.
6.6. GREASE SELECTION (see table page 36)
Use only high quality greases, with EP-additives and consistency
NLGI-Grade 3.
Greases with EP-additives and consistency NLGI-Grade 2 may be used for re-
greasable labyrinth type seals and grease lubricated lower bearing of the
low speed shaft.
6.7. GREASE LUBRICATION POINTS (see fig. 5)
All greasing points for bearings which are not oil lubricated and for labyrinth
seals are equipped with nipples according to DIN 71412 and have been
filled before shipment.
The total number of nipples is indicated on the nameplate.
Some built-on backstops are grease lubricated.
For detailed information refer to appropriate leaflet supplied with this
manual.
6.8. OIL DRAINING (see fig. 5)
Drain the oil while unit is still warm. To facilitate oil drai-
ning, remove dipstick. Drain units having a large oil volume through drain
plug. Use portable pump. With some executions a small quantity of oil
remains beneath the high speed bearings. This oil can be drained by means
of a second drain plug (1).
6.9. VENTILATION (see fig. 5)
To prevent pressure build-up, the gear unit is provided with a breather which
is generally integrated in the dipstick.
Take care and check regularly that this breather
does not become clogged.
For some applications, the dipstick with breather hole is replaced by one
without breather hole in combination with an anti-dust or anti-humidity
breather.
7. COOLING
Heat generated in the gear unit due to friction and churning of the oil, must
be dissipated through the housing into the environment.
It is important not to decrease the heath dissipation capacity of the housing.
Regularly clean the surface of the housing.
7.1. SEPARATE AIR COOLING
7.1.1. Fans
One or two fans may be mounted on gear unit shafts.
Check regularly that the air inlet and the air
outlet are not obstructed.
Fans need no special maintenance, except occasional cleaning.
7.1.2. Air-oil coolers
The service manual of the lubrication and cooling system gives detailed
information about the air-oil cooler.
7.2. SEPARATE WATER COOLING
All water cooling systems must be connected to a non-calcareous water
supply. See also service manual on lubrication and cooling system and/or
technical leaflets on specific instrumentation. The use of seawater must be
specified with the order; coolers suited for use of seawater are available.
When unit is not operating and freezing temperatures may occur, water must
be drained from cooling system. Drain facilities have to be provided by end
user.
Unless otherwise stipulated, the water flow indicated on the dimensional
drawing is the required rate for water at 20 C (70 F).
According to load, ambient temperature and the water temperature a lower
rate will suffice. Adjust waterflow to obtain an oil working temperature bet-
ween 60 and 80 C (140 and 180 F).
9
ansen
dipstick
oil filling
oil draining
ventilation
grease lubrication
points
Type and position of the
stickers : refer to certified
drawing and gear unit
FIG. 5
TRANSMISSIONS
ansen
®
- Single stage gear units
(1) see 6.8
QHP.1 QHP.1W
- Multi stage gear units
M
n

7.2.1. Water-oil coolers
Refer to certified drawing for connection of the water-oil cooler to the
coolant.
The service manual of the lubrication and cooling system gives detailed
information about the water-oil coolers.
7.2.2. Cooling coils
Direction of waterflow is optional.
The cooling coils are suited for fresh as well as for seawater.
Maximum allowable water pressure : 0,8 MPa (8 bar, 116 psi).
Connection of cooling coil to water supply.
Warning: In order to avoid torsioning of cooling coil, hold premounted
connection with suitable wrench as shown in fig. 6 below.
8. BACKSTOPS
Backstops are safety devices and have to be inspected at regular time
intervals .
The periodical inspection is to be carried out by authorised personnel and
according to the instructions described in the specific service leaflet supplied
with the gear unit .
Carefully read these service and inspection instructions before starting any
intervention on the backstop.
The frequency of the inspections depends on the type of application.
The following table lists the maximum interval between 2 inspections for a
number of applications, other applications require at least one inspection
every year.
In case of transport of people: the user has to follow local legislation re.
inspection of safety devices.
An inspection of the backstop is also required in the following
circumstances :
- In case of disassembly of the gear unit or one of its components
- In the event that abnormal wear or material break-out of gears, bearings or
any other component or pollution of the oil has been detected in the gear
unit, since this may have affected the condition of the sprags and raceways
of the backstop.
The outcome of the periodical inspection is to be reported in a log book.
Never loosen any part of the backstop while the
gear unit is loaded: loosening the backstop may
cause reversal of the drive and running back of
the load. Prior to loosening the backstop remove
the load and secure the drive against unwanted
movement.
8.1. STANDARD BACKSTOP INTEGRATED IN THE
GEAR UNIT
These backstops are lubricated by the oil bath of the gear unit and require,
apart from the regular inspections indicated above, no further maintenance.
8.2. EXTERNALLY FITTED BACKSTOP
In case the gear unit is equipped with an externally fitted backstop, please
refer to the corresponding additional Service Manual for maintenance and in-
spection. The above instructions for inspection remain valid.
Alteration of the direction of rotation of a
backstop may only be carried out by authorised
personnel and according to the instructions
shown in the relevant instruction leaflet.
9. STARTING-UP
9.1. ALL GEAR UNITS
Before starting-up, check oil level with dipstick
and make sure that all points are lubricated.
Although all greasing points have been greased before delivery, it is
advisable to give a few shots with a grease gun before starting-up.
Check all fixation points between gear unit and foundation.
They may require retightening after some running time.
The alignment of the complete drive packages mounted on a bedplate has
been carefully checked before shipment. It is nevertheless required to check
that the bedplate has not been deformed during transport or erection.
Therefore check again alignment of couplings or other elements after final
installation.
Make sure that protection hoods and air guiding plates, if any, in case of fan
cooling are properly fitted.
Gear units may rotate in both directions except when direction of rotation is
indicated.
On gear units equipped with backstops, check
whether direction of motor rotation corresponds
to backstop freewheeling direction, before
coupling motor to unit.
In case of complete drives, the direction of rotation of the motor has to be
checked by means of a phase meter.
Rotation of gear unit in reverse direction, even
momentarily, may damage the backstop, and
consequently is not allowed.
Units equipped with heaters must not be started before oil temperature is
above 5°C (40°F). Heaters are automatically disconnected when oil tempera-
ture is above 15°C (60°F).
Temperature of oilbath will rise with increased load. Continuous operating
temperature of 95°C (200°F) is allowable for a standard gear unit filled with
mineral oil.
9.2. GEAR UNITS WITH FORCED FEED
LUBRICATION
For the different parts of the lubrication system, refer to service manual of the
lubrication and cooling equipment and/or the technical leaflets concerning
the specific components.
9.3. GEAR UNIT DRIVEN BY A TWO SPEED MOTOR
When switching from the higher to the lower speed, first decelerate so that
the motor must accelerate when switched on at the lower speed. In this way
high synchronisation peak torques can be avoided.
10
ansen
TRANSMISSIONS
ansen
®
Application Maximum time interval
Hoist drives Every year
Conveyors Every two years
Elevators Every two years
Cooling towers (QVP.2) Every two years
Cooling towers (QVR.2) Every five years
Screw pump drives Every two years
FIG. 6
cooling coil
n
!
!
n

!
M
M
M
n
n
n
10. MAINTENANCE
Maintenance operations are limited to check oil level, to regular oil change,
to regrease the lubrication points and filter cleaning.
Oil quantity : see paragraph 6.4, page 8.
Oil draining : see paragraph 6.8, page 9.
Read also points in the other paragraphs.
10.1. INSPECTION AND MAINTENANCE
Rotating parts may cause harm and damage.
For inspection and maintenance always de-
energize the drive and make sure that the drive
is secured against inadvertent switch-on or
movement.
10.2. OIL CHANGE
The first oil change should be carried out preferably after 100 hours and not
later than 800 hours of operation. The removed oil may be used again after
filtering. Filter the oil volume at least 10 times. Use a 10 µm filter or smaller.
Subsequently the oil should be renewed after 4000 to 8000 hours or max.
18 months of operation depending on working conditions. Use clean oil out
of clean drums. Entrance of abrasive particles and water must be avoided.
The water content should be kept below 0,05%.
If the lubrication system has an oil filter, change the filter cartridge every 800
hours of operation.
Operating procedure and specifications are mentioned in the service manual
of the lubrication and cooling equipment and / or the technical leaflets con-
cerning the specific instrumentation.
Only steel mesh filter cartridge may be used again if thoroughly cleaned in a
solvent.
When operating continuously either at oil temperatures of 80°to 95°C (175°
to 200°F) or in dusty or humid atmosphere, it is recommended to have oil
analyses by oil supplier or qualified laboratory at least after 4000 hours in
order to define exact lifetime of oil bath.
10.3. GREASE LUBRICATION POINTS
Regrease all lubrication points after every 800 hours of operation.
Recommended greases are given in lubricant table. (page 36)
For longer lubrication intervals: consult HANSEN.
10.4. MAINTENANCE FREE OIL-LOCKTM SEAL
The high speed shaft is equipped as standard with an OIL-LOCKTM oil seal.
The high and low speed shaft of the Hansen P4 single stage gear units are
equipped with an OIL-LOCKTM seal. This oil seal is wear resistant and
maintenance free due to its centrifugal operating principle. The dual purpose
labyrinth seal also prevents the entrance of dirt and moisture.
Disassembly of the OIL-LOCKTM seal should only be carried out by skilled
personnel.
10.5. EXTENDED PERIODS OF STANDSTILL
When gear units are at standstill for an extended period, the protective oil
film containing anti corrosion additives gradually disappears and the unpro-
tected internal parts become subject to corrosion. Adverse ambient condi-
tions such as humid, marine, tropical and chemically aggressive environ-
ments will accelerate the process.
A periodic visual inspection through the inspection cover is required.
Corrosion of the internals can be avoided by letting run the gear unit for a
few minutes every two weeks (depending on the ambient conditions) thus
allowing the formation of a new oil film.
Install a special breather (marked with the label shown below) to prevent
moisture from entering the gear unit.
If it is not possible to run the unit regularly and the risk for corrosion is immi-
nent, during extended periods of standstill the unit must be protected as
follows :
- an oil soluble concentrate including corrosion inhibitors which are active
both in the liquid and in the vapour phase has to be added. A 2% volume
concentration is considered to be normal. Consult your oil supplier about
lifetime, compatibility with the actual oil and about volume concentration.
- seal all gear unit openings (dipstick, breather etc.) hermetically .
10.6. SERVICE AFTER SALES
For technical assistance or additional information, the HANSEN sales centres
are at your disposal. When you contact them, please specify the complete
type code and the manufacturing number mentioned on the gear unit's name-
plate.
10.7. REPAIRS
Any repair should only be carried out by skilled personnel.
Only original HANSEN spares should be used.
11
ansen
TRANSMISSIONS
ansen
®
M

!
!
2.1. ETAT DES REDUCTEURS A LA LIVRAISON
Sauf stipulation contraire, les appareils sont livrés non emballés, mais
éventuellement fixés sur des palettes en bois et protégés par une caisse à
claire-voie.
Certains éléments, comme une cartouche de réserve de filtration, sont embal-
lés séparément. L'utilisateur réalisera l'installation correcte de ces éléments
(voir chapitre 5. INSTALLATION page 13)
Les réducteurs HANSEN P4 sont livrés sans huile.
Les points de graissage sont garnis de la graisse nécessaire.
2.2. PEINTURE
La peinture extérieure standard des réducteurs HANSEN est un primaire
époxy à extrait sec élevé de couleur bleu marin, correspondant à la
spécification allemande RAL 5021.
Cette peinture garantit une protection durant 5 ans, si le réducteur est installé
à l'intérieure et n'est pas sujet à une ambiance humide ou agressive.
La peinture est recouvrable par la plupart des peintures à base de résines
alkydes, époxydiques et polyuréthanes.
2.3. PROTECTION
Les organes intérieurs sont arrosés d'une huile anti-rouille. Le reniflard
(standard, anti-poussière ou anti-humidité) reste sur place et n'est pas fermé.
Les bouts d'arbres sont enduits d'une couche de graisse anti-rouille et
protégés par du papier huilé. Les arbres creux et toutes les faces usinées non
peintes sont munis d'une couche cireuse anti-rouille.
Ce système standard garantit une protection pendant le transport et/ou pour
un entreposage durant 1 an à l'intérieure.
3. ENTREPOSAGE
Entreposer le réducteur muni de son emballage
original. Ne jamais placer le réducteur près de
machines vibrantes, ceci pour éviter des domma-
ges aux roulements.
3.1. DUREE REDUITE
Un an maximum, à l'intérieur. Lors de l'entreposage, laisser intact l'état de
préservation des appareils.
3.2. LONGUE DUREE
Max. 5 ans à l'intérieure ou 6 mois en plein air.
• Au cas d'une demande d'entreposage de longue durée lors de la
commande, laisser intactes les mesures de protection.
• Dans tous les autres cas, remplir le réducteur d'une petite quantité
d'huile minérale contenant un additif volatil anti-rouille et fermer
hermétiquement les ouvertures de la jauge d'huile, du reniflard, etc.
Certains additifs peuvent être ajoutés à l'huile normalement utilisé;
consulter votre fournisseur d'huile.
4. MANUTENTION
La manutention et l'installation des réducteurs Hansen P4 sont aisées grâce
à l'utilisation des yeux de levage ovales intégrés pour les exécutions horizon-
tales et des écrous à anneau ou tiges intégrées pour les exécutions verticales.
Utiliser toujours les yeux de levage prévus au moyen d' outillage approprié
pour garantir un bonne distribution de la charge.
Les écrous à anneau ne peuvent être écartés et
doivent être complètement vissés avant levage
du réducteur.
Ne jamais soulever un réducteur par ses arbres.
La manutention d'appareils équipés d'un système de lubrification suppose
une attention spéciale. Dans certains cas il peut être nécessaire de démonter
les thermomètres, manomètres et une partie de la tuyauterie. Lors d'une telle
opération, veiller à ce qu'aucun corps étranger ne s'introduise dans le systè-
me.
12
ansen
n
OBJET
Ce manuel d'entretien donne les instructions préconisées pour l'installation, le
fonctionnement, la lubrification et l'entretien adéquats des réducteurs de vites-
se standard Hansen P4.
Tout renseignement supplémentaire peut être obtenu en contactant l'un des
centres de vente de HANSEN (p. 2-3)
La manutention, l'entreposage, l'installation, la
mise en marche, l'inspection et l'entretien d'un
groupe de commande seront réalisés par du
personnel qualifié et matière d'équipement méca-
nique industriel et - où d'application - d'équipe-
ment électrique.
1. GENERALITES
1.1. INSTRUCTIONS GENERALES
Avant d'installer le réducteur, lire attentivement ce manuel.
L'application systématique des instructions préconisées assurera au réducteur
un fonctionnement sans problèmes pendant de longues années.
Contrôler la conformité du matériel par rapport aux documents de livraison et
vérifier qu'aucun dégât apparent ne se soit produit lors du transport. Tout
manquement, dégât ou non-conformité doit être signalé immédiatement à
HANSEN.
1.1.1. Garantie
La clause de garantie stipulée dans les "Conditions Générales de Vente"
s'applique aux unités installées et entretenues suivant les instructions décrites
dans ce manuel et les instructions complémentaires jointes au réducteur, pour
autant que le réducteur fonctionne dans les conditions de service et de
puissance spécifiées dans l' "Accusé de Réception de Commande" et sur les
plans d'encombrement.
La clause de garantie concerne toutes les pièces du réducteur à l'exception
des pièces qui sont sujettes à l'usure.
La garantie expire si le dégât qui peut se présenter est la conséquence d'un
non-suivi de ces instructions, d'un choix inadéquat du lubrifiant ou d'un man-
que d'entretien.
1.1.2. Sécurité
Il est interdit d'utiliser le réducteur pour d'autres
applications et d'autres conditions d'utilisation
que celles mentionnées à la commande.
L'utilisateur est responsable pour l'installation
correcte de l'ensemble et pour l'approvisionne-
ment de dispositifs de protection et de sécurité
qui répondent aux prescriptions de sécurité
locales.
Les réchauffeurs et refroidisseurs d'huile, les alarmes électriques et autres
appareils de contrôle et de sécurité, livrés par HANSEN avec ou sans
l'équipement, doivent être installés et connectés par l'utilisateur suivant les in-
structions reprises dans le document technique correspondant.
1.2. SPECIFICATIONS GENERALES
Pour les spécifications telles que dimensions, poids, schémas de
raccordement, se référer au plan d'encombrement du réducteur et/ou aux
catalogues des réducteurs standard Hansen P4.
1.3. IDENTIFICATION
Chaque réducteur est identifié par sa plaque signalétique. Elle mentionne en-
tre autres la dénomination complète du type, le numéro de fabrication, la
puissance et /ou le couple, la vitesse et des indications concernant la lubrifi-
cation.
Toute demande concernant un réducteur doit mentionner la dénomination
complète du type et le numéro de fabrication.
Ces informations sont essentielles afin d'identifier avec certitude le réducteur
livré par HANSEN.
2. LIVRAISON
Avant expédition tout réducteur a été contrôlé et agréé par le service
CONTROLE QUALITÉ et ce sur la base des spécifications de la commande.
A cet effet le réducteur subit des essais de fonctionnement à vide pendant
plusieurs heures, dans sa position normale et à la vitesse indiquée sur la pla-
que signalétique.
TRANSMISSIONS
ansen
®

Exécution horizontale
- Réducteurs à un étage (type QHP.1)
- Réducteurs à plusieurs étages (type QH...)
Exécution verticale
- Réducteurs à plusieurs étages (type QV...)
(1) taille G : réducteur à 2 trains d'engrenages
(2) taille G : réducteur à 3 et 4 trains d'engrenages
L'alignement de groupes de commande livrés sur châssis est soigneusement
contrôlé avant expédition. Il importe pourtant de vérifier si le châssis n'a pas
été déformé pendant le transport ou l'implantation. A cet effet, contrôler de
nouveau l'alignement des accouplements ou d'autres organes après
l'installation définitive.
5.5. FIXATION DES REDUCTEURS A ARBRE CREUX
5.5.1. Réducteur à arbre creux avec frette de
serrage
La frette de serrage livrée par HANSEN est prête
à être installée.
Il est déconseillé de défaire la frette avant montage.
Utilisation standard du type HSD (fig. 1c, page 14). L'utilisation du type SD
est possible sur demande (fig. 1d, page 14).
Montage (fig. 1a)
- Nettoyer et dégraisser les surfaces de contact (a) et (b).
- Traiter la surface (b) - jamais la surface (a) - avec du
"Molykote D321R" ou un produit analogue.
- Après durcissement de la couche appliquée, glisser le joint torique (c) sur
l'arbre.
- Tirer le réducteur sur l'arbre de la machine à l'aide d'une tige filetée (e),
d'un écrou (f) et d'une entretoise (g), jusqu'à ce que les faces (h) et (i)
soient en contact.
- Placer la frette (s). Une rainure marquée sur l'arbre indique le bon
positionnement de la frette de serrage.
Serrer les boulons (ZS) à la clé dynamométrique. Le couple de serrage
maxi est indiqué dans le tableau 1 pour le type HSD. Pour le type SD le
couple de serrage est indiqué sur le plan d'encombrement.
NOTE : Ne jamais serrer les vis d'une frette non
montée.
5. INSTALLATION
5.1. MONTAGE D'ACCESSOIRES
Clavetage dans les bouts d'arbre suivant ISO/R773-1969 et DIN 6885
"Feuille 1 - Form N1 ou N3" pour les arbres à dimensions métriques.
Trous taraudés dans les arbres suivant DIN 332 Teil 2 Form D.
Tolérance recommandée des alésages des accouplements ou des éléments à
monter : K7 (suivant ISO 286).
Les rainures de cale dans les bouts d'arbre en pouce sont usinées suivant les
normes USAS B17.1-1976.
Tolérance recommandée pour alésages:
- 0,0005" jusqu à - 0,001" pour diamètre ≤1 1/2"
- 0,0001" jusqu à - 0,002" pour diamètre > 1 1/2"
Enlever la protection des bouts d'arbre et vérifier l'ajustage de la clavette et
la hauteur de la rainure de clavette de l'élément à monter. Réchauffer l'élé-
ment à monter jusqu'à 80-100°C sera suffisant. Lors du montage des
éléments quelconques sur les bouts d'arbre, le trou taraudé dans ceux-ci faci-
litera l'opération.
Éviter de monter à coups de marteau, car les rou-
lements pourraient être abîmés.
L'emploi d'accouplements rigides est à prohiber sauf sur des arbres entraînés non
guidés (p.ex. agitateurs, aérateurs) et pour des exécutions à bras de réaction.
5.2. CHARGES EXTERIEURES
Au cas où le réducteur est appelé à être sollicité par des charges extérieures,
poser des butées contre les pieds du réducteur pour prévenir tout déplace-
ment. Des éléments transmettant des charges radiales au bout d'arbre
doivent être montés le plus près possible du carter.
Éviter une tension exagérée des courroies d'une transmission montée sur
l'arbre d'entrée ou de sortie. Pour les ensembles moteur, transmission par
courroies et réducteur, la tension des courroies est réglée avant livraison.
Vérifier de nouveau la tension après 24h de service.
Monter des transmissions par chaîne sans tension préalable.
Lorsqu'un pignon est à monter sur le bout d'arbre du réducteur, veiller à ce
que le jeu normalement requis entre le pignon et la roue dentée, soit respecté
et vérifier si les dents portent sur toute leur largeur.
5.3. IMPLANTATION
5.3.1. Mise à niveau
Monter le réducteur uniquement dans la position
prévue lors de la commande.
Consulter HANSEN pour l'installer dans une autre position car le dispositif
de lubrification pourrait devoir être adapté.
5.3.2. Alignement
L'alignement horizontal du réducteur envers le moteur et la machine
conduite doit être aussi correct que possible et à mieux que 5 mm au 1 m
(5/32 pouce au 3 pieds ou 5 mrad ou 17 minutes d'arc) ou dans les limites
indiquées au plan d'encombrement pour les positions hors horizontales.
L'erreur d'alignement maxi admissible entre arbres dépend du type d'accou-
plement monté sur les bouts d'arbre : voir les instructions propres à l'accou-
plement utilisé. Utiliser seulement 3 points d'appui pour le réglage de l'ali-
gnement. Régler ensuite les autres points d'appui au moyen d'épaisseurs et
ce jusqu'à un jeu de 0,1 à 0,2 mm, selon la taille du réducteur.
5.4 FIXATION DES REDUCTEURS A ARBRES PLEINS
Installer les appareils sur des châssis ou socles rigides et stables afin d'éviter
des vibrations. Faire usage des points d'appui indiqués sur le plan d'encom-
brement. Après alignement correct et réglage des tous les points d'appui au
moyen de cales d'épaisseur, fixer le réducteur solidement sur sa fondation en
utilisant des boulons, qualité 8.8 suivant DIN 267 ou SAE degré 5 pour les
boulons jusqu'à et y compris 1 1/2", ASTM.A-354 degré BC pour les bou-
lons au-delà de 1 1/2". Dimensions et couples de serrage: voir tableau.
Remarque: Pour certaines exécutions à arbres parallèles et ventilateurs, le
capot de protection du ventilateur doit être démonté afin de permettre le
serrage des boulons. Remonter le capot de protection par après.
ansen
Taille du réducteur C D E F-G(1) G(2)-H-J-K L-M-N-P-Q R-S-T
ISO M24 M30 M30 M36 M42 M48 M56
UNC 1" 1 1/8" 1 1/4" 1 1/2" 1 3/4" 2" 2 1/4"
Nm 660 830 1150 2000 2500 3500 5300
lbf.in 5800 7300 10000 18000 22000 31000 47000
Couple de
serrage
Dimension
boulon
a
cb
h
isZS
e
f
g
•
•
ZY
gl
•
•
FIG. 1a
TRANSMISSIONS
ansen
®
Taille du réducteur C D E F G
ISO M20 M24 M24 M30 M30
UNC 3/4" 7/8" 1" 1 1/8" 1 1/4"
Nm 285 450 660 830 1150
lbf.in 2500 4000 5800 7300 10000
Couple de
serrage
Dimension
boulon
Taille du réducteur A B C D E-F G-H-J-K L-M N-P-Q R-S-T
ISO M16 M20 M24 M24 M30 M36 M42 M48 M56
UNC 5/8" 3/4" 7/8" 1" 1 1/4" 1 1/2" 1 3/4" 2" 2 1/4"
Nm 165 285 450 660 1150 2000 2500 3500 5300
lbf.in 1450 2500 4000 5800 10000 18000 22000 31000 47000
Couple de
serrage
Dimension
boulon
MONTAGE
13
DEMONTAGE
FIG. 1b
n

Type HSD (fig. 1c)
Le couple de serrage (TA) est indiqué dans le tableau 1 et sur la plaque signa-
létique (p).
Un serrage correct de la frette suppose que les faces frontales des anneaux ex-
térieur (o) et intérieur (n) soient dans le même plan. Un contrôle visuel permet
de vérifier si cela est le cas.
Type SD (fig. 1d)
Les couples de serrage sont indiqués sur la plaque signalétique (p) et sur le
plan d'encombrement.
Retirer les intercalaires de transport placés entre les anneaux extérieurs (o). Lors
du montage et du serrage s'assurer que les deux faces des anneaux extérieurs
restent parallèles entre eux.
Types HSD + SD
Serrer les vis (ZS) une àune dans un ordre continu (q) et progressivement en
plusieurs reprises, jusqu'àobtention du couple de serrage requis. Ne pas
serrer les vis diamétralement.
Prévoir capot de protection.
Fixation en cas de charge axiale
Lorsque la charge axiale n'est pas reprise par le collet de l'arbre, le montage
d'une entretoise est nécessaire. (voir fig. 2b, page 15).
Démontage (fig. 1b, page 13)
- Desserrer uniformément d'un quart de tour toutes les vis de serrage (ZS) et
ceci dans un ordre continu en plusieurs stades.
- Au cas oùles anneaux extérieur et intérieur du type HSD ne se dégagent pas
d'eux-mêmes, l'on peut enlever quelques vis de serrage et les introduire dans
les trous taraudés (r) prévus dans l'anneau extérieur.
La poussée des vis provoquera la séparation et le dégagement des deux
anneaux.
- Retirer la frette de serrage de l'arbre creux.
- Fixer l'entretoise (g) sur l'arbre creux àl'aide de boulons (ZY).
(Dimensions de ZY: voir plan d'encombrement)
- Placer le boulon de démontage (l) dans le trou central de l'entretoise (g).
- Serrer le boulon (l) pour démonter le réducteur de l'arbre entraîné.
Remarque
Les pièces e,f,g,l et ZY ne font pas partie de notre livraison, mais peuvent être
livrées sur demande. Données: voir catalogue ou plan d'encombrement.
Nettoyage et regraissage
Les frettes retirées ne doivent pas être démontées pour nettoyage ou regraissa-
ge avant réemploie, sauf si elles ont étéutilisées dans un environnement très
sale.
Après nettoyage, enduire les surfaces coniques d'un lubrifiant solide ayant un
coefficient de friction de 0,04 (p.e. Molykote D321R ou équivalent).
14
ansen
Frettes de serrage TA
Nm
TA
lbf.in
HSD 110-81x110 121 1070
HSD 125-81x125 121 1070
HSD 140-81x140 193 1700
HSD 165-81x165 295 2600
HSD 185-81x185 295 2600
HSD 220-81x220 570 5000
HSD 240-81x240 570 5000
HSD 260-81x260 570 5000
HSD 280-81x280 570 5000
HSD 320-81x320 980 8600
HSD 340-81x340 980 8600
HSD 360-81x360 980 8600
HSD 390-81x390 1450 12800
HSD 420-81x420 1450 12800
HSD 440-81x440 1450 12800
HSD 480-81x480 1450 12800
HSD 500-81x500 1970 17400
HSD 530-81x530 1970 17400
Tableau 1
1
2
3
4
5
67
8
9
1
2
3
4
5
6
78
9
1 c
1 d
n
o
p
q
a
ZS
SD TYPE
q
o
r
ZS
n
a
p
HSD TYPE
FIG. 1
n
TRANSMISSIONS
ansen
®

n
5.5.3. Montage du bras de réaction
Après montage du réducteur sur l'arbre entraîné (voir par. 5.5.1 et 5.5.2),
fixer le réducteur au point d'appui à l'aide du bras de réaction livré en option.
Le point de fixation du bras de réaction au réducteur est indiqué sur le plan
d'encombrement ou dans le catalogue.
La liaison entre le bras de réaction et le point d'appui est flexible et résiliante
grâce à la précontrainte des rondelles Belleville du bras de réaction.
La précontrainte est réglée par la compression des rondelles.
La précontrainte des rondelles Belleville est réglée de la façon suivante :
- Déterminer la distance S (fig. 3a), c'est la hauteur des rondelles Belleville
non soumises a une compression et non montées.
- Serrer les écrous jusqu'à l'obtention de la distance S1 (distance entre le
réducteur et le point de fixation) où S1 = S - ∆S (fig. 3b, 3c, 3d)
∆S = l'enfoncement des rondelles (tableaux 2, 3 et 4)
obtenu par le poids du réducteur et le serrage des écrous
- Après réglage de la distance S1, verrouiller les écrous en serrant l'écrou
extérieur et le contre-écrou l'un contre l'autre.
5.5.2. Réducteur à arbre creux avec liaison par
clavette
Montage (fig. 2a)
- Enduire les faces de fixation (b) de pâte de montage.
- Glisser le joint torique (c) sur l'arbre.
- Placer la clavette de montage (d) dans la rainure de clavette de l'arbre
machine, avec l'arrêt de la clavette contre la face de l'arbre.
- Placer le réducteur sur l'arbre machine. Veiller à ce que les rainures de
clavette soient positionnées correctement l'une vis-à-vis de l'autre.
- Monter le réducteur sur l'arbre machine à l'aide d'une tige filetée (e), d'un
écrou (f) et d'une entretoise (g) jusqu'à ce que la clavette de montage (d) et
l'entretoise (g) se touchent.
- Enlever l'écrou (f), l'entretoise (g) et la clavette de montage (d).
- Vérifier si le jeu au-dessus de la clavette (m) est suffisant.
- Introduire la clavette (m) dans la rainure (≠clavette de montage).
- Remonter l'entretoise (g) et l'écrou (f).
- Tirer le réducteur plus loin sur l'arbre jusqu'à ce que les faces (h) et (i) se
touchent.
- Enlever l'écrou (f), l'entretoise (g) et la tige filetée (e).
Fixation (fig. 2 b)
- Remettre l'entretoise (g) à l'aide des boulons de fixation (J) prévus.
- Monter le capot de protection (k).
Au cas ou l'arbre creux est soumis à une force axiale externe, consulter les
instructions spécifiques mentionnées sur le plan d'encombrement.
Démontage (fig. 2 c)
- Enlever le capot de protection (k) et les boulons de fixation (J).
- Fixer l'entretoise (g) sur l'arbre creux à l'aide des boulons (ZY)
(Dimensions de ZY: voir plan d'encombrement).
- Monter le boulon de démontage (l) dans le trou central de l'entretoise (g).
- Serrer le boulon (l) pour enlever le réducteur de l'arbre machine.
Remarque
Les pièces e,f,l et ZY ne font pas partie de la livraison, mais peuvent être
livrées sur demande.
Pour plus de détails: voir catalogue ou plan d'encombrement
15
ansen
DEMONTAGE
b
h
i
cd
e
f
g
•
•
FIG. 2
MONTAGE
k
J
g
m
•
•
2b
FIXATION
ZY
l
g
m
•
•
2c
FIG. 3
AS
Tableau 2
Tableau 3
3a
Q*: nombre de rondelles Belleville
Q*: nombre de rondelles Belleville
2a
PR
S1= S - S
PT
D
3b
DPT PR max ∆S A
±5mm inch mm inch Q* DIN 2093
QH.A2 35 M16 40 1.57 0,7 0.028 2 x 2 A 80
QH.B2 35 M20 50 1.97 0,7 0.028 2 x 2 A 80
QH.C2 45 M24 60 2.36 0,9 0.035 2 x 2 A 100
QH.D2 45 M24 60 2.36 0,9 0.035 2 x 3 A 100
QH.E2 60 M30 75 2.95 1,0 0.039 2 x 3 A 125
QH.F2 60 M30 75 2.95 1,0 0.039 2 x 3 A 125
QH.G2 60 M36 90 3.54 1,0 0.039 2 x 4 A 125
QH.H2 60 M36 90 3.54 1,0 0.039 2 x 4 A 125
Réducteur
Taille
S1= S - S
PR
PT
D
3c
D PT PR max ∆S A
±5mm inch mm inch Q* DIN 2093
QH.C3 35 M20 50 1.97 0,7 0.028 2 x 3 A 80
QH.D3 - QH.D4 45 M24 60 2.36 0,9 0.035 2 x 2 A 100
QH.E3 - QH.E4 45 M24 60 2.36 0,9 0.035 2 x 3 A 100
QH.F3 - QH.F4 60 M30 75 2.95 1,0 0.039 2 x 2 A 125
QH.G3 - QH.G4 60 M36 90 3.54 1,0 0.039 2 x 3 A 125
QH.H3 - QH.H4 60 M36 90 3.54 1,0 0.039 2 x 3 A 125
Réducteur
Taille
TRANSMISSIONS
ansen
®

!
6. LUBRIFICATION
La lubrification assure les quatre fonctions principales suivantes:
- prévenir le contact métal-métal entre les dentures et dans les
roulements
- réduire les pertes de friction
- dissiper la chaleur générée par les engrenages et les roulements
- empêcher la corrosion.
Différents systèmes de lubrification peuvent être utilisés. Le choix dépend de
- la vitesse de rotation
- la position de montage
- le régime
Les réducteurs HANSEN sont équipés d'un des systèmes suivants:
- lubrification par barbotage:
- lubrification forcée: - lubrification par circulation forcée
- lubrification sous pression
Chaque système comporte éventuellement un refroidisseur d'huile sous
différentes formes (voir REFROIDISSEMENT).
6.1. LUBRIFICATION PAR BARBOTAGE
Le système de lubrification par barbotage est standard sur tous les réducteurs
àarbres horizontaux et pour une vitesse entre 750 min-1 et 1800 min-1 à
l'arbre grande vitesse.
Tous les engrenages et les roulements de l'arbre PV sont lubrifiés par immer-
sion dans le bain d'huile. Le barbotage des engrenages projette l'huile dans
des poches aménagées dans le carter d'oùl'huile est conduite par gravité
vers les roulements àtravers des canaux aménagés dans le carter et les
couvercles.
Pour d'autres vitesses àl'arbre grande vitesse, consulter HANSEN.
6.2. LUBRIFICATION FORCEE
Chaque élément rotatif se situant au-dessus du bain d'huile est lubrifiépar
une pompe àengrenages àtravers un réseau de canalisations.
La pompe peut être du type intégré, entraînée par un des arbres du
réducteur, soit du type moto-pompe.
Les pompes du type intégrésont toutes équipées d'un système inverseur à
l'intérieur de la pompe qui assure le fonctionnement correct dans les deux
sens de rotation.
En cas de moto-pompe, le sens de rotation est toujours indiqué.
Des pompes accolées atteignent leur débit max. déjàaprès quelques secon-
des. Cependant, il est àconseiller de retarder le signal d'alarme de 5 à10
sec., afin d'éviter le déclenchement de l'alarme pendant le démarrage.
Les moto-pompes doivent fonctionner au mini-
mum 1 min. avant le démarrage du réducteur.
6.2.1. Lubrification par circulation forcée
- Avec pompe intégrée (fig. 4)
Le système de lubrification par circulation forcée avec pompe intégrée
comprend:
- une pompe P
- un filtre d'huile F avec by-pass (standard àpartir de la taille G)
- un contrôle de débit Mf (standard àpartir de la taille G)
Le contrôle de débit doit être branchéàun circuit
électrique qui coupe le moteur principal au cas où
le débit d'huile descend sous son niveau
d'alarme.
- Avec moto-pompe
Le manuel d'entretien des systèmes de lubrification et de refroidissement
contient l'information détaillée concernant le système de lubrification par
circulation forcée avec moto-pompe
M
6.2.2. Lubrification sous pression
Le manuel d'entretien des systèmes de lubrification et de refroidissement
contient l'information détaillée concernant le système de lubrification sous
pression.
6.2.3. Instruments et leurs réglages
Pour des informations détaillées concernant le système de lubrification, les
instruments et leurs réglages, voir le plan d'encombrement, le manuel d'entre-
tien des systèmes de lubrification et de refroidissement et les notices séparées
livrés avec ce manuel.
Les réglages mentionnés sur le plan
d'encombrement ont étéétablis lors des essais
par HANSEN et ne peuvent être modifiés sans
autorisation écrite.
Par contre les préréglages sont des valeurs recommandées et peuvent être
modifiés d'après les conditions locales.
6.3. CHOIX DE L'HUILE
Utiliser des huiles minérales qui comportent des additifs "EP" qui augmentent
la capacitéde charge des films lubrifiants.
Utiliser uniquement des huiles dont type et indice
de viscositécorrespondent aux données de la
plaque signalétique. Cette viscositéa étédéterminée sur base des
conditions de fonctionnement spécifiées dans la commande.
Pour la conversion de la viscositéISO classe VG en d'autres unités de viscosi-
té, voir le tableau des lubrifiants (p.36). Celui-ci n'est pas restrictif, d'autres
marques équivalentes conviennent également.
Les fournisseurs de lubrifiants sont responsables pour la sélection et la compo-
sition de ses produits.
L'utilisation d'huiles synthétiques n'est permise
qu'après l'autorisation écrite du département
"Engineering" de HANSEN.
Utiliser uniquement des huiles synthétiques du type polyalpha-olefine (type
SHF, "Synthetic Hydrocarbon Fluid") qui contiennent des additifs EP. La bon-
ne stabilitéanti-oxidation de l'huile synthétique permet d'obtenir une durée
de vie supérieure àcelle de l'huile minérale de même viscositédans les mê-
mes conditions. L'utilisation d'une huile synthétique pour une durée de vie su-
périeure est permise àcondition de faire analyser l'huile àun intervalle régu-
lier (période de 4000 heures) par le fournisseur des lubrifiants ou par un
laboratoire qualifiéqui peuvent déterminer la durée de vie exacte du bain
d'huile.
6.4. QUANTITE D'HUILE (voir fig. 5, page 17)
Les niveaux d'huile mini et maxi sont déterminés
par des marques sur la jauge.
Un voyant d'huile ou un interrupteur de niveau est livrable sur demande.
LES JAUGES A BOUCHON VISSE DOIVENT ETRE
CONTROLES EN POSITION VISSEE. Le niveau d'hui-
le doit être contrôlélorsque le réducteur est hors
service.
Dans les systèmes de lubrification comportant
des filtres et des refroidisseurs d'huile, le niveau
d'huile doit être contrôléavec tous les éléments
remplis d'huile et après un essai de courte durée
de l'installation de refroidissement.
Le remplissage du système de lubrification et de refroidissement, y-inclus le
refroidisseur, se fait automatiquement dès que la température du bain d'huile
atteint 60 C. Si un remplissage plus rapide est requis, il y a lieu de purger le
refroidisseur pendant que la pompe est en fonction.
La quantitémentionnée sur la plaque signalétique d'un réducteur n'est qu'une
valeur approximative, donnée àtitre d'indication en vue de
l'approvisionnement.
16
ansen
Q*: nombre de rondelles Belleville
F
P
Mf •
••
•
FIG. 4
S1= S - S
PR
PT
D
3d
Tableau 4
DPT PR max S A
5mm inch mm inch Q* DIN 2093
QH.J3 - QH.J4 80 M42 105 4.1 1,4 0.055 2 x 3 A 160
QH.K3 - QH.K4 80 M42 105 4.1 1,4 0.055 2 x 3 A 160
QH.L3 - QH.L4 80 M48 120 4.7 1,4 0.055 2 x 4 A 160
QH.M3- QH.M4 80 M48 120 4.7 1,4 0.055 2 x 4 A 160
Réducteur
Taille
TRANSMISSIONS
ansen
®

M
M
M
M
M
M
M6.5. REMPLISSAGE INITIAL (voir fig. 5)
Remplir les appareils seulement après leur implantation définitive. Ce conseil
vaut plus particulièrement pour les réducteurs à arbre de sortie vertical dirigé
vers le bas muni d'une buselure à rebord dans laquelle l'huile pourrait
s'introduire lors de la manutention.
Remplir le réducteur d'huile via l'orifice prévu
dans le couvercle d'inspection. Ainsi tous les rou-
lements seront pourvus d'huile fraîche.
Remarque :
- Remplissage d'huile supplémentaire dans le
pallier.
Les réducteurs horizontaux à arbres perpendicu-
laires et à 4 étages de réduction (QHR.4) et les
réducteurs verticaux à arbres perpendiculaires
et à 3 et 4 étages de réduction (QVR.3 + QVR.4)
nécessitent un remplissage d'huile supplémen-
taire dans le palier.
Voir autocollant sur le réducteur.
La quantité d'huile à introduire dans le palier est
mentionnée sur le plan d'encombrement et sur
l'autocollant.
- Remplissage d'un réducteur avec base moteur
M1 ou M3
Les réducteurs à arbres horizontaux (QH..) équipés d'une base moteur M1
et M3 doivent être remplis d'une petite quantité d'huile lors du premier
remplissage d'huile à travers le couvercle d'inspection situé dans la face
supérieure du carter (voir auto-collant au réducteur).
Si l'espace disponible entre la base moteur et la face supérieure du
réducteur est insuffissant pour effectuer le remplissage d'huile, il faudra
lever la base moteur quelque peu après démontage des courroies.
Pour les réducteurs équipés d'une base moteur M1, le bouchon de
remplissage est situé côté arbre grande vitesse, c.a.d. côté opposé de la
jauge d'huile.
Pour réducteurs avec base moteur M3, le bouchon de vidange normal est
situé du côté de la jauge d'huile.
Vidanger le réducteur s'il a été rempli d'huile antirouille. Il y a lieu dans cer-
tains cas de rincer le réducteur, avant la mise en marche, avec l'huile sélec-
tionnée. Vérifier avec le fournisseur d'huile.
6.6. SELECTION DE LA GRAISSE (voir tableau page 36)
Utiliser uniquement des graisses de bonne qualité contenant des additifs
"EP", ayant une consistance NLGI grade 3. Une graisse de consistance NLGI
grade 2 contenant des additifs "EP" peut être utilisée pour lubrifier les garni-
tures à labyrinthe regraissables ou le cas échéant exclusivement le roulement
inférieur de l'arbre petite vitesse.
6.7. POINTS DE GRAISSAGE (voir fig. 5)
Les points de graissage des roulements non lubrifiés par le bain d'huile et
ceux des garnitures à labyrinthe sont munis de graisseurs suivant DIN 71412
et sont remplis de graisse avant livraison. Leur nombre est marqué sur la pla-
que signalétique.Certains antidévireurs accolés sont lubrifiés à la graisse.
Consulter le manuel approprié (ci-joint) pour de plus amples informations.
6.8. VIDANGE (voir fig. 5)
Vidanger pendant que le réducteur est encore
chaud. L'opération est facilitée en enlevant au préalable la jauge. Pour vi-
danger des appareils à bain d'huile volumineux, connecter à l'orifice de vi-
dange le tuyau d'aspiration d'une pompe portative.
Pour certaines exécutions, une petite quantité d'huile reste dans la cavité
au-dessous des roulements grande vitesse. Un deuxième bouchon de
vidange (1) est prévu pour assurer la vidange de cette huile.
6.9. AERATION (voir fig. 5)
Une surpression est évitée grâce à l'utilisation d'un bouchon reniflard
intégré ou non à la jauge d'huile.
Contrôler régulièrement si le reniflard n'est pas
bouché.
Dans certains cas la jauge d'huile avec reniflard intégré est remplacée par
une jauge d'huile sans reniflard. Le réducteur est alors muni d'un reniflard an-
ti-humidité ou d'un reniflard anti-poussière à protection contre l'eclaboussure
d'eau.
7. REFROIDISSEMENT
La chaleur produite par la friction et le barbotage dans le réducteur, sera dis-
sipée vers l'environnement par le carter. N'augmenter point la résistance
thermique du carter. Nettoyer régulièrement la surface du réducteur.
7.1. REFROIDISSEMENT FORCE PAR AIR
7.1.1. Ventilateurs
Un ou deux ventilateurs peuvent être montés sur les arbres du réducteur.
Vérifier régulièrement que l'entrée et la sortie ne
soient pas bouchées.
Les ventilateurs ne demandent pas de soins particuliers. Il suffit de les nettoyer
à l'occasion.
7.1.2 Systèmes de refroidissement air-huile
Le manuel d'entretien des systèmes de lubrification et de refroidissement
contient l'information détaillée concernant le systèmes de refroidissement
air-huile.
17
ansen
jauge d'huile
remplissage
vidange
aération
point de graissage
Type et position
des autocollants: voir
plan d'encombrement
et réducteur
TRANSMISSIONS
ansen
®
- Réducteurs à un étage
QHP.1 QHP.1W
- Réducteurs à plusieurs étages
FIG. 5
(1) voir 6.8
n

7.2. REFROIDISSEMENT FORCE PAR CIRCULATION
D'EAU
Les systèmes de refroidissement par eau doivent être raccordés à un réseau
d'eau non calcaire.
Voir également le manuel d'entretien des systèmes de lubrification et de re-
froidissement et/ou des feuilles techniques sur des instruments spécifiques.
L'utilisation d'eau de mer doit être spécifiée à la commande, des refroidis-
seurs spéciaux sont disponibles.
Lorsqu'un réducteur hors service risque d'être exposé au gel, il y a lieu de
vidanger l'eau du refroidisseur. Le matériel nécessaire à cet effet est à prévoir
par l'utilisateur.
Le débit d'eau mentionné correspond à une température d'eau de 20°C sauf
mention différente sur le plan d'encombrement. Une quantité inférieure est
admissible mais ceci dépend de la charge mise en oeuvre, de la température
ambiante et de la température d'eau. Régler le débit de manière à ce que la
température de l'huile se situe entre 60 et 80°C pendant le fonctionnement.
7.2.1. Systèmes de refroidissement eau-huile
Consulter le plan d'encombrement pour connecter le refroidisseur au réfrigé-
rant. Le manuel d'entretien des systèmes de lubrification et de refroidissement
contient l'information détaillée concernant le système de refroidissement eau-
huile.
7.2.2. Serpentins de refroidissement
Le sens de circulation de l'eau est facultatif au choix.
Les serpentins de refroidissement se prêtent tant à l'utilisation d'eau douce
qu'à d'eau de mer.
Pression d'eau maximum admissible : 8 bar.
Raccorder le serpentin à l'alimentation d'eau.
Avertissement: Pour éviter la torsion du serpentin, il est indispensable de
maintenir la pièce de raccord avec une clef appropriée à la réalisation du
raccord (voir fig. 6 ci-dessous).
8. ANTIDEVIREURS
Les antidévireurs sont des éléments de sécurité et doivent être inspectés par
intervalles réguliers.
Les inspections périodiques doivent s' effectuer par du personnel qualifié et
suivant les instructions du manuel d'entretien spécifique fourni avec le réduc-
teur.
Lisez attentivement les instructions de manipulation et d'inspection avant de
commencer l'intervention à l'antidévireur.
La fréquence d'inspection dépend de l'application.
Le tableau ci-dessous indique l'intervalle maximum entre deux inspections
pour quelques applications. Les autres applications exigent au moins une in-
spection annuelle de l'antidévireur.
Pour les ascenseurs, l'inspection se fera suivant les instructions de la législa-
tion locale concernant l'inspection d'éléments de sécurité.
L'inspection de l'antidévireur est également requis dans les cas suivants:
- en cas de démontage du réducteur ou d'un de ses composants;
- en cas d'usure anormale ou de rupture des engrenages, des roulements ou
tout autre élément, ou en cas de constatation d'encrassement de l'huile.
Ces incidents peuvent affecter l'état des galets et des pistes de blocage
de l'antidévireur.
Les résultats de l'inspection périodique doivent être inscrits dans le livre de
bord.
Ne jamais démonter aucune partie de l'antidévi-
reur lorsque le réducteur est chargé:
le démontage de l'antidévireur peut provoquer
l'inversion du sens de rotation du réducteur et le
retour de la charge.
Avant le démontage de l'antidévireur, libérer le
réducteur de sa charge et empêcher qu'il ne se
produise aucun mouvement non voulu.
8.1. L'ANTIDEVIREUR STANDARD INTEGRE
AU REDUCTEUR
Cet antidévireur est lubrifié par l'huile du réducteur et ne nécessite aucun en-
tretien, sauf inspection périodique comme stipulé ci-dessus.
8.2. L'ANTIDEVIREUR ACCOLE AU REDUCTEUR
Au cas ou le réducteur est muni d'un antidévireur accolé, consulter le manuel
de service spécifique pour réaliser l'entretien et l'inspection de l'antidévireur.
L'inversion du sens de rotation de l'antidévireur
ne peut s'effectuer que par du personnel compé-
tent et suivant les instructions dans le manuel de
service spécifique.
9. MISE EN MARCHE
9.1. TOUT REDUCTEUR
Avant démarrage du réducteur, contrôler le
niveau de l'huile en utilisant la gauche d'huile et
vérifier si tous les points sont lubrifiés.
Bien que les points de graissage aient été munis de graisse avant livraison, il
est à conseiller de donner quelques coups de pompe avant de démarrer.
Contrôler également la fixation du réducteur sur sa fondation : un resserrage
des boulons peut être nécessaire après quelque temps de fonctionnement.
L'alignement de groupes de commande livrés sur châssis est soigneusement
contrôlé avant expédition. Il importe pourtant de vérifier si le châssis n'a pas
été déformé pendant le transport ou l'implantation. A cet effet, contrôler de
nouveau l'alignement des accouplements ou d'autres organes après
l'installation définitive.
Contrôler que tous les capots de protection et l'eventuelle coiffe de circulation
d'air du ventilateur soient correctement montés.
Le réducteur peut fonctionner dans les deux sens de rotation sauf si le sens est
indiqué.
Avant d'accoupler le moteur à un réducteur
équipé d'un antidévireur, vérifier que le sens de
rotation de ce dernier correspond à celui du
moteur.
Pour des groupes de commande, le sens de rotation du moteur sera vérifié à
l'aide d' un phase-mètre.
L'entraînement du réducteur dans le sens de blo-
cage - même momentanément - peut endomma-
ger l'antidévireur, et par conséquent n'est pas ad-
mis.
Le réducteur équipé d'un réchauffeur d'huile ne peut être mis en marche que
lorsque la température d'huile est supérieure à 5°C. Le réchauffeur d'huile est
automatiquement déconnecté quand la température d'huile est supérieure à
15°C.
La température du bain d'huile augmentera en fonction de la charge mise en
oeuvre. Une température du bain d'huile de maximum 95°C est permise pour
un réducteur standard rempli d'huile minérale.
9.2. REDUCTEUR A CIRCULATION D'HUILE FORCEE
Pour de plus amples informations concernant les éléments des systèmes de lu-
brification, consulter le manuel d'entretien des systèmes de lubrification ou de
refroidissement ou les manuels techniques des composants.
9.3. REDUCTEUR ACTIONNE PAR MOTEUR A DEUX
VITESSES
En cas de changement de la haute vers la basse vitesse il est indispensable
que l'installation ralentisse de telle façon que le moteur puisse accélérer à
l'enclenchement. Cette procédure est requise pour éviter des couples de poin-
te importants dû à la synchronisation.
18
ansen
TRANSMISSIONS
ansen
®
Application Intervalle maximum
Treuils Chaque année
Transporteurs Tous les deux ans
Elévateurs Tous les deux ans
Tours de réfrigération
(Type de réducteur QVP.2) Tous les deux ans
Tours de réfrigération
(Type de réducteur QVR.2) Tous les cinq ans
Pompes à vis Tous les deux ans
FIG. 6
serpentin de refroidissement
n
!
!
n

M
M
M
M
n
n
n
10. ENTRETIEN
L'entretien se limite au contrôle du niveau d'huile, au renouvellement régulier
du lubrifiant, à des ajouts de graisse et au nettoyage de filtres éventuels.
Quantité d'huile : voir paragraphe 6.4 page 16-17
Vidange d'huile : voir paragraphe 6.8 page 17
Lire également les points des autres paragra-
phes.
10.1. INSPECTION ET ENTRETIEN
Des pièces tournantes peuvent causer des dom-
mages.
Avant inspection et entretien, toujours déclencher
le groupe de commande et s'assurer que le
groupe de commande soit protégé contre toute
possibilité d'enclenchement ou de mouvement
non voulue.
10.2. RENOUVELLEMENT DU LUBRIFIANT
Remplacer la première huile après 100 heures de fonctionnement effectif et
pas plus tard que 800 heures. Cette huile peut être réutilisée après filtrage
ad hoc (filtre de 10 µm ou inférieure). Filtrer le volume d'huile au moins dix
fois.
Ensuite, renouveler l'huile après 4000 à 8000 heures ou 18 mois de service,
selon les conditions de fonctionnement.
Utiliser de l'huile propre provenant d'un tonneau propre. La pénétration de
particules abrasives et d'eau doit être évitée. L'huile ne peut pas contenir plus
de 0,05% d'eau.
Si le système de lubrification comprend un filtre d'huile, renouveler la cartou-
che toutes les 800 heures d'utilisation.
La procédure de renouvellement et les spécifications sont décrites dans le ma-
nuel d'entretien des systèmes de lubrification ou de refroidissement ou dans
les manuels techniques des instruments. Uniquement la cartouche en toile mé-
tallique peut être réutilisée après nettoyage approfondi dans un solvant.
Lorsque les températures de régime se situent constamment entre 80°à 95°C
ou en cas d'une atmosphère poussiéreuse ou humide, il est à conseiller de
faire analyser - après 4000 heures de service - un échantillon du lubrifiant
par son fournisseur ou un laboratoire qualifié qui pourra déterminer la durée
de vie exacte du bain d'huile.
10.3. POINTS DE GRAISSAGE
Ajouter de la graisse toutes les 800 heures de service; voir tableau des grais-
ses (p.36).
Pour des intervalles de lubrification plus longs: consulter HANSEN.
10.4. SYSTEME D'ETANCHEITE OIL-LOCKTM NE
NECESSITANT AUCUN ENTRETIEN
L'arbre grande vitesse est équipé comme standard d'un système d'étanchéité
OIL-LOCKTM. L'arbre petite et grande vitesse des réducteurs Hansen P4 à un
train d'engrenage sont équipés d'un système d'étanchéité OIL-LOCKTM.
La bague d'étanchéité est résistante à l'usure et ne nécessite aucun entretien
grâce au système d'opération centrifuge. Ce labyrinthe à double effet
empêche l'entrée de poussière et d'humidité.
Le démontage de la bague OIL-LOCKTM ne peut être exécuté que par du
personnel qualifié.
10.5. REDUCTEUR HORS SERVICE PENDANT UNE
PERIODE PROLONGEE
Lorsque, après installation sur site, le réducteur est à l’arrêt pendant une
période prolongée, le film d’huile protectif disparaît petit à petit et les
surfaces intérieures risquent d’être sujettes à la formation de rouille.
Ce risque dépend fortement des conditions ambiantes (milieu humide,
maritime, tropical, ou un milieu chimique agressif).
L'état des composants intérieurs doit être contrôlé périodiquement. A cet effet
il faut effectuer une inspection visuelle par le couvercle de contrôle du
réducteur.
Afin d'éviter le risque de corrosion il y a lieu de faire tourner le réducteur
pendant quelques minutes tous les quinze jours (la fréquence dépend des
conditions ambiantes), permettant ainsi la formation d’un nouveau film
d’huile. Monter un reniflard spécial (marqué par l'autocollant indiqué ci-
dessous) pour éviter la pénétration d'humidité dans le réducteur.
Au cas où le risque de formation de rouille est élevé et s’il n’est pas possible
de faire tourner le réducteur régulièrement, les mesures de protection
suivantes sont à prendre durant la période prolongée hors service:
- ajouter à l’huile, pour obtenir une concentration de 2%, un liquide soluble
dans l’huile et contenant des substances anti-corrosives qui sont actives tant
à l’état fluide que gazeux. Consulter le fournisseur d’huile concernant la
durée de vie, la concentration requise et la compatibilité du liquide avec
l’huile utilisée.
- toutes les ouvertures du réducteur (jauge d'huile, reniflard etc. ) doivent être
fermées hermétiquement.
10.6. SERVICE APRES VENTE
Pour assistance technique et informations supplémentaires, les centres de ven-
te HANSEN sont à votre disposition. En les contactant, veuillez communiquer
le type complet et le numéro de fabrication mentionnés sur la plaque signalé-
tique du réducteur.
10.7. REPARATIONS
Toute réparation doit être exécutée par du personnel qualifié.
Uniquement des pièces originales HANSEN peuvent être utilisées.
19
ansen
TRANSMISSIONS
ansen
®
!

n
!
!
GEGENSTAND
Diese Betriebsvorschrift ist eine Anleitung für Aufstellung, Betrieb, Schmierung
und Wartung der Hansen P4 Normgetriebe.
Für zusätzliche Auskunft, steht ein HANSEN Vertriebnetz zu Ihrer Verfügung
(S. 2-3).
Das für die Handhabung, Lagerung, Aufstellung,
Inbetriebnahme, Kontrolle und Wartung des An-
triebs eingesetzte Personal muss für industrielle
mechanische und ggf. elektrische Ausrüstungen
qualifiziert sein.
1. ALLGEMEINES
1.1. ALLGEMEINE ANWEISUNGEN
Lesen Sie diese Betriebsanleitung vor dem Einbau des Getriebes bitte
sorgfältig durch. Eine genaue Befolgung der Anweisungen garantiert Ihnen
einen langen und einwandfreien Betrieb.
Überprüfen Sie zunächst, ob das Material den Versanddokumenten entspricht
und keine Transportschäden aufweist. Benachrichtigen Sie HANSEN bitte
sofort bei Mängeln, Schäden oder fehlenden Teilen.
1.1.1. Garantie
Die in den "Allgemeine Verkaufsbedingungen" aufgeführte Garantieklausel
gilt nur für Getriebe, die gemäß den Vorschriften dieser Betriebsanleitung
und sonstigen Anleitungen die ggf. mit dem Getriebe mitgeliefert sind,
installiert und gewartet wurden und die entsprechend den in der Auftragsbe-
stätigung und auf den Maßzeichnungen erwähnten Betriebsbedingungen
eingesetzt werden.
Die Garantie erlischt jedoch, wenn sich herausstellen sollte, daßder Schaden
die Folge des nicht Beachtens der Vorschriften, einer unfachmännischen
Schmiermittelwahl oder einer mangelhaften Wartung ist.
Diese Garantieklausel bezieht sich also auf alle Getriebeteile bzw. alle zum
Getriebe gehörenden Teile, ausgenommen Verschleißteile.
1.1.2. Sicherheit
Es ist nicht gestattet, das Getriebe für andere An-
wendungszwecke oder in anderen Betriebsum-
ständen als für die, wofür es bestellt wurde, zu
benutzen.
Der Benutzer ist verantwortlich für die fachgemä-
ße Aufstellung der gesamten Ausrüstung und für
die Beistellung der Schutzhauben und anderer
Sicherheitsvorrichtungen, die den örtlichen Sicher-
heitsvorschriften entsprechen.
Heizungselemente, Kühl-, Sicherheits- und Überwachungssysteme, die von
HANSEN zu dem Getriebe mitgeliefert werden, müssen wie in den betreffen-
den Dokumenten beschrieben, montiert und angeschlossen werden.
1.2. ALLGEMEINE DATEN
Allgemeine Daten wie Abmessungen, Gewicht, und Anschlußdiagramme sind
der betreffenden Maßzeichnung und/oder den Katalogen für die Hansen P4
Normgetriebe zu entnehmen.
1.3. KENNZEICHNUNG
Jedes Getriebe ist mit einem Typenschild versehen. Auf diesem Typenschild
sind u.a. der vollständige Getriebetyp , die Herstellungsnummer, die Leistun-
gen und/oder das Drehmoment, Drehzahlen und Schmierangaben aufge-
führt.
Sollten sich Fragen zu dem gelieferten Getriebe ergeben, so mußstets der
vollständige Getriebetyp und die Herstellungsnummer angegeben werden.
Anhand dieser Daten kann man bei HANSEN genau feststellen, um welches
Getriebe es sich handelt.
2. LIEFERUNG
Jedes Getriebe wird vor dem Versand von der QUALITÄTSKONTROLLE-
ABTEILUNG mit den Bestellangaben überprüft. Zu diesem Zweck werden die
Getriebe mehrere Stunden lang einem unbelasteten Probelauf unterzogen,
wobei die spätere Aufstellungsart und die auf dem Typenschild erwähnten
Drehzahlen berücksichtigt werden.
2.1. GETRIEBE BEI LIEFERUNG
Wenn nicht anders bestellt, werden die Getriebe unverpackt, eventuell auf
Paletten befestigt und durch eine Lattenkiste geschützt zum Versand gebracht.
Ggf. gesondert mitgelieferte Teile , wie Ersatzelemente für Filter, sind vom
Verwender zu montieren (siehe auch Abschnitt 5. AUFSTELLUNG, S.21).
Die HANSEN P4 Getriebe werden ohne Ölfüllung
geliefert.
Alle Fettschmierstellen werden jedoch vor dem Versand mit Fett gefüllt.
2.2. ANSTRICH
Als Standard-Außenanstrichsystem für HANSEN Getriebe wird eine Epoxyd-
Grundfarbe, Farbton RAL 5021 (wasserblau), mit hohem Festkörpergehalt
verwendet.
Dieser Anstrich bietet einen 5-jährigen Schutz wenn das Getriebe Innen
aufgestellt ist und keinen feuchten oder aggressiven Umgebungseinflüssen
ausgesetzt ist.
Überstreichen mit den meisten Farben auf Alkyd-, Epoxyd- oder
Polyuretanharzbasis ist möglich.
2.3. SCHUTZ
Die Getriebe-Innenflächen werden mit einem rostschützenden Mineralöl
besprüht. Die Entlüftungsschraube (Standard, staubdicht oder für feuchte
Umgebung) wird weder entfernt noch verschlossen.
Die Wellenzapfen werden mit einem rostschützenden Fett auf Mineralbasis
eingestrichen und mit Ölpapier geschützt.
Die Hohlwellen und sämtliche blanken, bearbeiteten Flächen werden mit
einem wachsartigen Rostschutzmittel behandelt.
Dieses Standardschutzsystem bietet einen ausreichenden Korrosionsschutz für
Transport und/ oder eine 12 monatige Lagerung, in einem geschlossenen
Raum.
3. LAGERUNG
Das Getriebe in der Originalverpackung lagern.
Das Getriebe darf niemals in der Nähe von
vibrierenden Maschinen gelagert werden, so daß
kein Vibrationsverschleißder Lager auftreten
kann.
3.1. KURZFRISTIGE LAGERUNG
Max. 12 Monate in einem geschlossenen Raum.
Die Schutzmittel dürfen nicht entfernt werden.
3.2. LANGFRISTIGE LAGERUNG
Max. 5 Jahre in einem geschlossenen Raum oder 6 Monate im Freien.
•Wenn eine langfristige Lagerung bei der Bestellung vereinbart war, muß
die angebrachte Konservierung unberührt bleiben.
•In allen anderen Fällen das Getriebe mit einer kleinen Menge Mineralöl
mit einem rostschützenden verflüchtigenden Additiv füllen und alle
Öffnungen des Getriebes (Ölstabschraube, Entlüftungsschraube usw.)
hermetisch verschließen.
Bestimmte Additive können dem normalen Betriebsöl hinzugefügt
werden. Bitte bei Ihrem Öllieferanten nachfragen.
4. TRANSPORT
Die Hansen P4 Getriebe sind einfach zu handhaben und aufzustellen dank
der ovalen Hebeaugen bei den horizontalen Einbaulagen und der Ringmut-
tern oder der integrierten Stangen bei den vertikalen Einbaulagen.
Immer alle vorgesehenen Hebeaugen und geeignete Werkzeuge verwenden
damit eine korrekte Lastverteilung gesichert sei.
Die Ringmutter dürfen nicht entfernt werden und
müssen zum Heben des Getriebes komplett ein-
geschraubt sein.
Die Getriebe dürfen niemals an den Wellen ange-
hoben werden.
Besonders vorsichtige Behandlung erfordern Getriebe mit
Pumpenschmierung. In gewissen Fällen ist es zweckmäßig, Thermometer,
Manometer und einige Rohrleitungen zu demontieren. Es ist dafür zu sorgen,
daßkeine Fremdkörper in das System gelangen.
20
ansen
TRANSMISSIONS
ansen
®
Other manuals for P4
3
Table of contents
Languages:
Popular Microphone System manuals by other brands
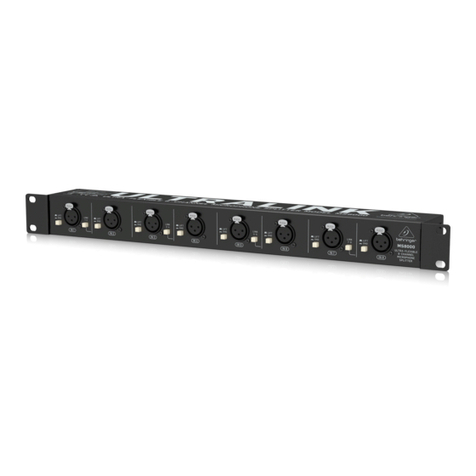
UltraLink Products
UltraLink Products Ultralink ms8000 quick start guide
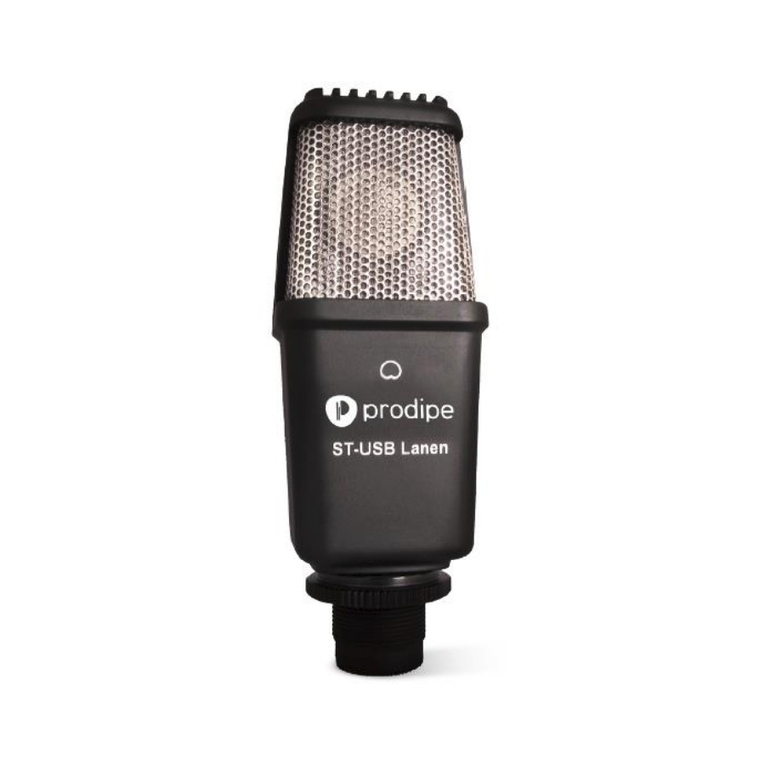
Prodipe
Prodipe ST-USB Lanen user guide
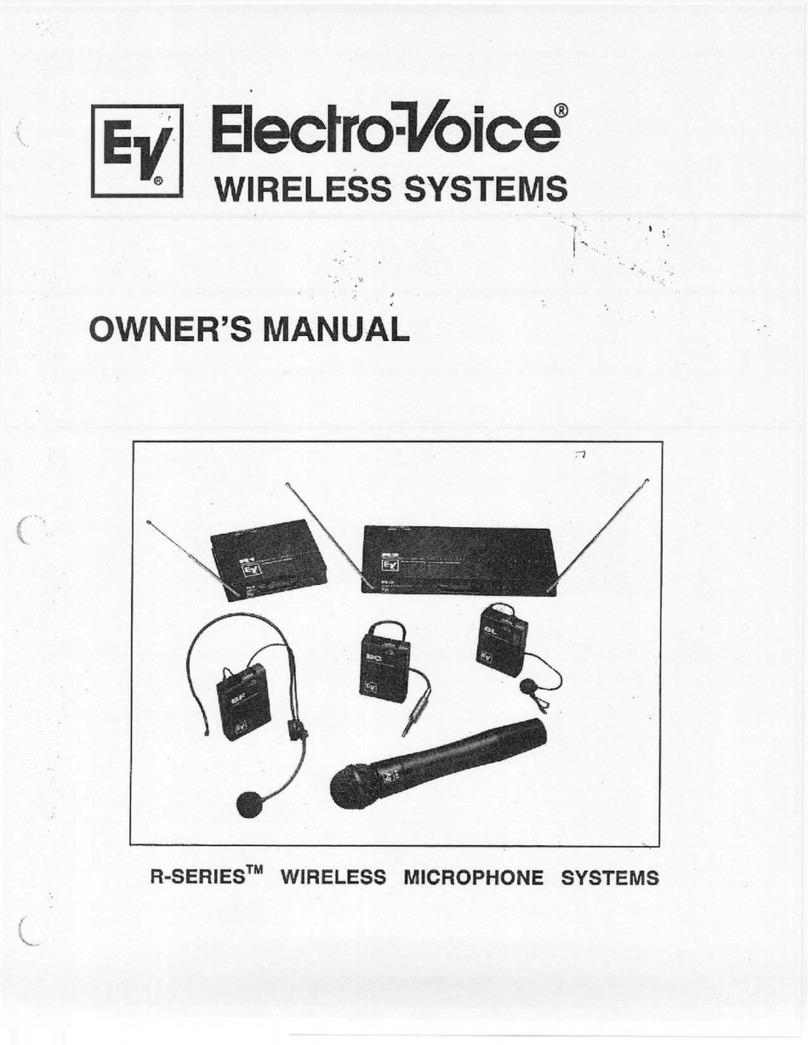
Electro-Voice
Electro-Voice R-Series owner's manual
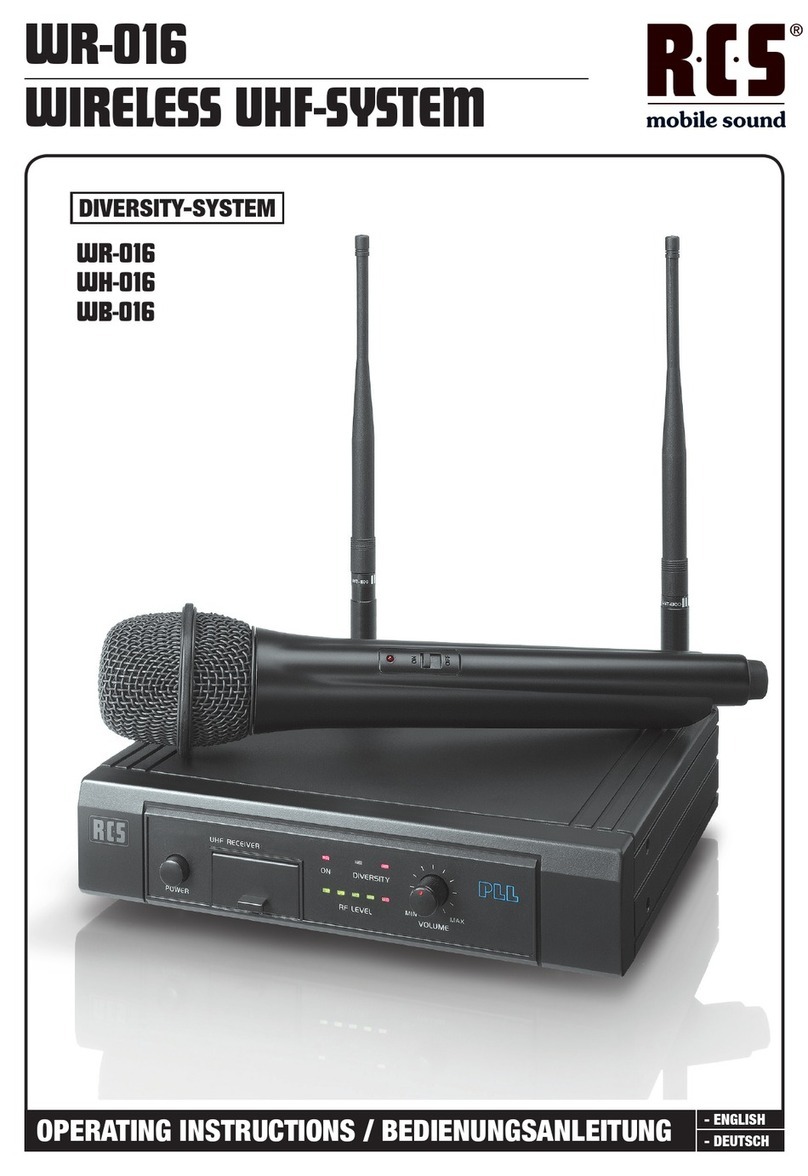
RCS
RCS WR-016 operating instructions
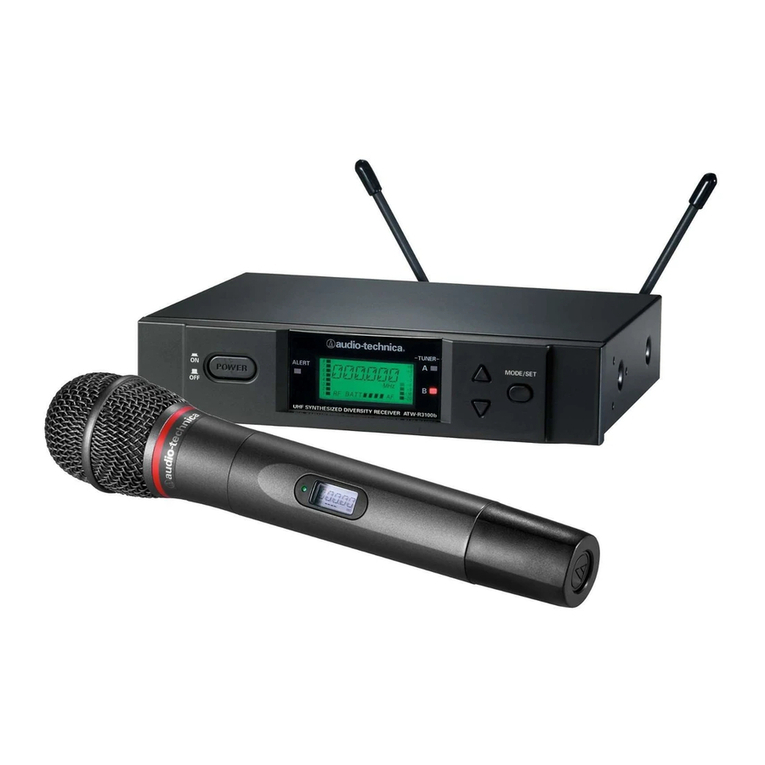
Audio Technica
Audio Technica 3000 Series Installation and operation guide

Sony
Sony DWZ-B50GB quick start guide