Hiniker 8160 User manual

8160
OPERATOR’S MANUAL
DO NOT USE OR OPERATE THIS EQUIPMENT UNTIL THIS MANUAL
HAS BEEN READ AND THOROUGHLY UNDERSTOOD
PART NUMBER 39300030 Rev. E


TITLE
TABLE OF CONTENTS
39300030 Rev. E 12/10 Manual/39300030RevE
SAFETY..................................................................................................................................................................................3
TO THE PURCHASER...........................................................................................................................................................4
SYSTEM OVERVIEW .......................................................................................................................................................5-11
8160 CONSOLE................................................................................................................................................................6-11
Switches and Indicators........................................................................................................................................................6
Boom Switches.................................................................................................................................................................6
Run/Hold Switch...............................................................................................................................................................6
Rate Select Switch ...........................................................................................................................................................6
Warning Light ...................................................................................................................................................................6
Horn..................................................................................................................................................................................6
Keyboard..............................................................................................................................................................................7
POWER Key.....................................................................................................................................................................7
VOLUME Key...................................................................................................................................................................7
AREA Key.........................................................................................................................................................................7
SPEED Key......................................................................................................................................................................7
SET, , Keys...............................................................................................................................................................7
RATE Key.........................................................................................................................................................................7
ERROR Key .....................................................................................................................................................................7
Display.............................................................................................................................................................................8-10
TARGET RATE.................................................................................................................................................................8
MANUAL...........................................................................................................................................................................8
ACTUAL RATE / % RATE.................................................................................................................................................8
SPEED/VOLUME/AREA...................................................................................................................................................8
ERROR MESSAGES ............................................................................................................................................................9
LOW BATTERY CONDITION...........................................................................................................................................9
HOLD................................................................................................................................................................................9
MAN ERR.........................................................................................................................................................................9
+++%...............................................................................................................................................................................9
---%...................................................................................................................................................................................9
MIN...................................................................................................................................................................................9
SIM.................................................................................................................................................................................10
LOW SPEED..................................................................................................................................................................10
LOW FLOW....................................................................................................................................................................10
ZERO WIDTH.................................................................................................................................................................10
OVER .............................................................................................................................................................................10
System Connections...........................................................................................................................................................11
Power Connector............................................................................................................................................................11
Speed Connector............................................................................................................................................................11
Flow Connector ..............................................................................................................................................................11
Boom Connector.............................................................................................................................................................11
Servo Connector.............................................................................................................................................................11
Run/Hold Connector.......................................................................................................................................................11
Serial Channel Connector ..............................................................................................................................................11
OPERATION....................................................................................................................................................................12-25
Operating Guidelines.................................................................................................................................................12-13
Variable Rate..................................................................................................................................................................13
Menu..........................................................................................................................................................................14-15
Navigating The Menu ..................................................................................................................................................14
Selecting operating mode...............................................................................................................................................15
Spray Setup....................................................................................................................................................................16
NH3 Setup......................................................................................................................................................................17
Options Menu............................................................................................................................................................18-19
Speed Sensor Calibration............................................................................................................................................20
Distance Measurement...............................................................................................................................................21
Remote Run/Hold.......................................................................................................................................................22
Horn Control...............................................................................................................................................................22
Minimum Flow ............................................................................................................................................................23
Serial Protocol............................................................................................................................................................24
Valve Prole................................................................................................................................................................24
Speed Simulator.........................................................................................................................................................24
Test Input Routine.......................................................................................................................................................25
Display Smoothing......................................................................................................................................................25
Table of Contents 1

2 Table of Contents
INSTALLATION ...............................................................................................................................................................26-41
BASIC UNIT ..................................................................................................................................................................26-27
Console Mounting...........................................................................................................................................................26
8150 Adapter..................................................................................................................................................................27
Power Cable..............................................................................................................................................................27-33
SPEED SENSORS.............................................................................................................................................................28
Hub Plate Speed Sensor...........................................................................................................................................28-29
Radar Adapters..........................................................................................................................................................30-31
GPS Speed Sensor...................................................................................................................................................32-33
SPRAYER APPLICATIONS...........................................................................................................................................34-41
Introduction.....................................................................................................................................................................34
Inline System..................................................................................................................................................................35
Bypass System...............................................................................................................................................................36
Typical Wiring-Sprayer ...................................................................................................................................................37
Flowmeter.......................................................................................................................................................................38
Servo Valve ....................................................................................................................................................................39
Boom Valve ....................................................................................................................................................................40
Remote Run/Hold...........................................................................................................................................................41
ANHYDROUS AMMONIAAPPLICATIONS.....................................................................................................................42-43
Introduction.....................................................................................................................................................................42
Remote Run/Hold...........................................................................................................................................................42
Typical Wiring-NH3.........................................................................................................................................................43
TROUBLESHOOTING ....................................................................................................................................................44-55
Console Symptoms and Possible Causes......................................................................................................................45
Using Test Inputs............................................................................................................................................................46
Cable and Connector.................................................................................................................................................46-48
Speed Sensor.................................................................................................................................................................48
HM860 Flowmeter.....................................................................................................................................................49-50
Flow Meter Calibration Test............................................................................................................................................51
Servo Valve ...............................................................................................................................................................52-54
Remote Run/Hold...........................................................................................................................................................55
APPENDIX......................................................................................................................................................................56-62
Serial Communication Specications ........................................................................................................................56-61
Hiniker Protocol.........................................................................................................................................................56-59
Generic Protocol........................................................................................................................................................59-61
Parts Breakdown............................................................................................................................................................62
Swath Control.................................................................................................................................................................63
GENERAL INFORMATION.............................................................................................................................................64-70
Chemical Application......................................................................................................................................................64
Over Application .............................................................................................................................................................64
Under Application ...........................................................................................................................................................64
Determining Gallons Per Acre........................................................................................................................................64
Nozzle Spacing............................................................................................................................................................65
Pressure Affects ..........................................................................................................................................................65
Tractor Speed..............................................................................................................................................................65
Nozzle Type....................................................................................................................................................................65
Boom Height...................................................................................................................................................................66
Spray Angle....................................................................................................................................................................66
Spray Coverage..............................................................................................................................................................66
Nozzle Selection........................................................................................................................................................67-69
Band Spraying................................................................................................................................................................69
Before You Go To The Field ...........................................................................................................................................70
After Spraying.................................................................................................................................................................70
Care of Spray Equipment...............................................................................................................................................70
GLOSSARY....................................................................................................................................................................71-72
DEFAULT VALUES..............................................................................................................................................................72
WARRANTY...............................................................................................................................................Inside Rear Cover

TITLE
SAFETY
THIS IS THE SAFETY ALERT SYMBOL.
IT ALERTS AN OPERATOR TO INFOR-
MATION CONCERNING PERSONAL
SAFETY. ALWAYS OBSERVE, AND HEED
THESE SYMBOLS AND INSTRUCTIONS, OTH-
ERWISE DEATH, OR SERIOUS INJURY CAN
RESULT!
Operator safety is a principle concern in equip-
ment design and distribution. However, many ac-
cidents occur because a few seconds of thought,
and a more careful approach to handling, were
ignored.
Throughout this manual, and on all safety relat-
ed decals, a safety alert symbol, along with the
signal word CAUTION, WARNING, or DANGER
will be found. These are dened as follows:
CAUTION: A reminder for proper safe-
ty practices and directs attention to
following them. Decals of this class
are yellow and black.
WARNING: Areminder for proper safe-
ty practices and what can happen if
they are ignored. This has a more seri-
ous consequence than CAUTION. Decals of
this class are yellow and black.
DANGER: Denotes the most serious
safety hazard. It is a reminder for ob-
serving the stated precautions and
what can happen if they are ignored. Decals
of this class are red and white.
CAUTION: For your own protection
we very strongly recommend that you
read, understand, and heed the follow-
ing information.
CAUTION: If you and your operator(s)
are not intimately familiar with proper
handling procedures for Anhydrous
Ammonia, contact your supplier for informa-
tion, and read all safety precautions found in
the “HINIKER ANHYDROUS AMMONIA MONI-
TORING AND CONTROL SYSTEM MANUAL”
Refer to manual part number 360-000-246 Re-
vision E or later for heat exchanger manufac-
tured prior to 2007. These are painted gray.
Or, refer to manual part number 39300035 for
heat exchanger manufactured in 2007 or af-
ter. These are painted white. Additional man-
uals may be obtained from your local dealer.
ACCIDENTS CAN BE AVOIDED BY KNOW-
ING, AND FOLLOWING, THE PRECAUTIONS
CITED IN THIS MANUAL.
GENERAL
1. If the Operator’s Manual is missing from this
equipment, obtain a replacement from your
HINIKER dealer. If you sell this equipment,
ensure the new owner acknowledges receipt
of this manual.
2. Read this manual thoroughly. Make sure the
operator understands it and knows how to
operate this equipment safely. Farm equip-
ment can kill or injure an untrained, or care-
less operator.
3. Do not attempt to handle and service this
equipment, or direct others to do the same,
unless you know how to do it safely.
4. Don’t be in a hurry.
HinikerCompanyreservestherighttochange
prices, standard features, specications or
designs, and options at any time without no-
tice and without incurring the obligation to
install such changes on machines previously
manufactured.
Safety 3

TITLE
Congratulations for joining the ranks of agribusi-
nessmen who acknowledge the importance of
accurate and controllable application of chemi-
cals.
This product will insure that the proper recom-
mended application rate is maintained. This will
not only save you money lost by overapplication,
but safeguard that your yields are not being ad-
versely affected by underapplication.
As an added bonus your operation will become
more environmentally responsible, by you be-
ing able to know that only the proper amounts of
chemicals required for your application are be-
ing used.
This product is designed and manufactured to
give years of dependable service, when used for
the purpose for which it was intended.
Never allow anyone to operate this equipment
until they fully understand the complete con-
tents of the manual. It is the responsibility of the
owner’s who do not operate this equipment, to
insure that the operator is fully instructed, and
is fully aware, and understands, the contents of
this manual.
Important information is contained in this manual
to help insure safe and efcient operations.
If you have any questions about this manual,
or equipment discussed therein, contact your
HINIKER dealer.
4 To The Purchaser
THIS IS THE SAFETY ALERT SYMBOL.
IT ALERTS AN OPERATOR TO INFOR-
MATION CONCERNING PERSONAL
SAFETY. ALWAYS OBSERVE, AND HEED
THESE INSTRUCTIONS, OTHERWISE DEATH,
OR SERIOUS INJURY CAN RESULT.
NOTE: All references to “LEFT” and “RIGHT”
are meant to mean viewing the equipment from
the rear and facing the tractor.
ALWAYS OBTAIN ORIGINAL HINIKER SER-
VICE PARTS BECAUSE SUBSTITUTE PARTS
COULD ADVERSELY AFFECT EQUIPMENT
PERFORMANCE AND WARRANTY.
Record the following information for later refer-
ence when obtaining service parts.
Purchase Date________________________
Name_______________________________
Dealer’s Name________________________
Console Serial No._____________________
Flowmeter Serial No.___________________
Servo Valve Serial No.__________________
TO THE PURCHASER

TITLE
The Hiniker 8160 is a computerized system that will
enable you to apply liquid chemicals, includingAnhy-
drous Ammonia at a predetermined rate.
The 8160 console allows you to individually set up
and calibrate two separate console congurations,
one for spray applications and one for NH3 applica-
tions. There is no need to recalibrate when changing
applications. All data and Set-Up information is per-
manently stored for each application.
The8160consoleinconjunctionwithaspeedsensor,
owmeter, and servo valve perform the necessary
calculations and adjustments to perform “on-the-go”
adjustments to the selected rate of application.
The console uses the inputs of actual ow, speed,
and user selected functions to calculate the actual
Volume PerArea (VPA). This is then compared to the
rate selected by the operator to generate a percent-
error signal. This signal then causes the Servo Valve
to make corrections to the ow. This continues until
the VPA error is zero. See drawing 5791.
The following is a list of features available with this
system.
– Dual Modes: Set-Up, Calibration, and Data are
stored separately for Spray and NH3 modes.
– Non-Volatile Memory; Set-Up Data, Volume and
Area are stored in permanent memory; no exter-
nal power is required.
– Inline and bypass system congurations.
– The Servo Valve response rate is adjustable.
– One, two, or three section control using motor-
ized ball valves or electric solenoids for individual
boom control.
– Boom section widths are individually set.
– Selection of Rate 1, Rate 2, Manual or Variable
Rate control.
– Display smoothing adjustable from 1 to 10%.
– Warning lamp and horn activates when applica-
tion error is greater than 10%.
– A settable minimum ow to prevent poor spray
patterns when slowing down at low speeds.
– Abuilt in speed simulator for setting up the spray-
er.
– Diagnostics for testing the Speed, Flow, and Run/
Hold inputs.
– The ability to measure Distance.
– Run/Hold feature.
– The Remote Run/Hold option is available at the
console and the implement.
– A 2 line display with ve display selections avail-
able. Target Rate (Always Displayed), Actual
Rate, % Error, Speed, Volume, and Area.
– The 8160 is backward compatible with the 8150
system wiring and bracket using a simple adapter.
SYSTEM OVERVIEW
System Overview 5
DWG. NO. 5791

TITLE
DWG. NO. 5795
SWITCH AND INDICATORS
The 8160 control console has all the necessary
functions to allow you to set-up and control sys-
tems tailored to your specic needs. A detailed de-
scription of the console follows.
BOOM SWITCHES
Three separate Boom Switches are available to
control three motorized ball valves or three electric
solenoid valves. The width of each boom is pro-
grammed in during Set-Up.
If any boom is not needed set its width to zero and
leave the boom switch off.
In the Automatic mode, the rate is automatically
adjusted as the Boom Switches are turned on and
off. When all three Boom switches are turned off,
the Boom valves will shut off and the console will
be in the Hold Mode.
Area is only counted for Booms that are on. Area
is not counted while in the Hold Mode.
RUN/HOLD SWITCH
The Run/Hold switch is the master control switch.
When “Run” is selected, power is applied to the
boom switches and the console is in the “Run
Mode”. This is the normal operating mode.
When “Hold” is selected, power is removed from
the Boom switches and the console is in the “Hold
Mode”. This is the standby mode where there is no
automatic control and the Volume and Area totals
stop accumulating.
6 System Overview
8160 CONSOLE
RATE SELECTOR SWITCH
The Rate switch allows you to select one of two ap-
plication rates or manual operation. The application
rate for Rate 1 and Rate 2 is programmed in during
Set-Up. When the selector switch is in the center po-
sition (Manual), the automatic control is off and the
Servo Valve can then be adjusted manually. To make
this adjustment, press and hold the “ ” or “ ” keys.
The Rate Switch must be in Rate 1 to use the Vari-
able Rate Mode.
WARNING LIGHT
The warning light will ash whenever the console is
in the Run Mode, and the difference between theTar-
get andActual application rate is greater then +-10%
error.
The light will also ash when the errors that cause
suspension of the Run Mode such as LOW FLOW,
LOW SPEED, and ZERO WIDTH are being dis-
played.
The warning light will be on steadily when the con-
sole is in Hold Mode.
HORN
The horn will beep under the same conditions as the
Warning light with the exception that it is not on dur-
ing the Hold mode.
The horn will also beep each time a key is pressed to
acknowledge the key press.
The horn may be turned off for the error conditions by
selecting HORN IS OFF in the options menu.

System Overview 7
DWG. NO. 5801
KEYBOARD
POWER KEY
To power up the console, press and hold the
POWER key for two seconds. Then release the
key when the warning light ashes and the horn
beeps.
To power down the console, press and hold the
POWER key for two seconds while the console is
powered on.
VOLUME KEY
The Volume key has two functions, the rst time
it is pressed it will display Total Volume, pressed
again and it will display Flow in Volume Per Min-
ute.
Press the VOLUME key to view the Total Volume.
The 8160 will always keep track of the Total Vol-
ume applied. Volume will not accumulate when in
the Hold Mode. To clear Total Volume to zero press
and hold the VOLUME key until the displayed Vol-
ume is zero. The horn and the warning light will
warn you that you are about to clear the data.
Note: Once cleared the data cannot be recov-
ered.
VOLUME has an additional feature, which enables
it to recalculate the Total Volume whenever the
Flowmeter Calibration Number is changed.
AREA KEY
The 8160 will keep track of the Total Area. To view
the Total Area, press the AREA key. Area is accu-
mulated only when the console is in the Run Mode.
Area will not accumulate when in the Hold Mode.
The 8160 will automatically correct for the change
in implement width when one or two of the Boom
switches are turned off.
Area has an additional feature, which enables it
to recalculate the Total Area whenever the Speed
Sensor Calibration Number is changed.
ToclearTotalAreatozeropressand hold theAREA
key until the displayed Area is zero. The horn and
the warning light will warn you that you are about
to clear the data.
Note: Once cleared the data cannot be recovered
SPEED KEY
The 8160 will calculate and display speed any time
the SPEED key is pressed.
The console must be calibrated to the speed sen-
sor before using. An incorrect speed calibration
will affect Speed, Rate, Percent Error, and Area
computations.
SET, , , KEYS
The SET key is used to enter the MAIN MENU.
To do so, press and hold the SET key for two sec-
onds. The SET key is also used as an “Enter” key
to select the displayed options or answers.
The and keys are used to change values and
answers. The or keys are also used during
manual operation to control the Servo Valve.
RATE KEY
To display the Actual Rate being applied press the
RATE key.
ERROR KEY
To display the Percent Error press the ERROR key
This ERROR function computes and displays the
difference between the Actual and Target applica-
tion rate as a percentage.

8 System Overview
DISPLAY
The display is used to provide to the user impor-
tant information on the operation of the system
and its components.
TARGET RATE
The left side of the top line on the display will
normally show the Target Application Rate. The
Target Application Rate is determined by the se-
lected position of the Rate Switch, either Rate 1
or Rate 2. The Target Rate will change to show
the current rate when using the Variable Rate
feature.
DWG. NO. 5804
MANUAL
In Manual position MANUAL will be displayed.
DWG. NO. 5805
ACTUAL RATE / %ERROR
The right side of the top line will display either
the Actual Rate or % Error depending on wheth-
er the RATE or ERROR key was pressed.
DWG. NO. 5806
DWG. NO. 5807
SPEED/VOLUME/AREA
Speed, Volume, or Area data will be displayed
on the bottom line depending on whether the
SPEED, VOLUME, or AREA key was pressed.
DWG. NO. 5808
DWG. NO. 5809
DWG. NO. 5859
DWG. NO. 5810

+++%
With the ERROR key selected the +++% mes-
sage will be displayed if the calculated percent
error between the target rate and the actual rate
is greater then +99%. In this condition you are
over applying by more then 99%.
DWG. NO. 5814
---%
With the ERROR key selected the ---% message
will be displayed if the calculated percent error
between the target rate and the actual rate is
greater then -99%. In this condition you are un-
der applying by more then 99%.
DWG. NO. 5815
MIN
Whenever the ow is reduced to the Minimum
Flow level, the display will ash “MIN” to indi-
cate that the console will not reduce the ow any
further. You will be over-applying to keep a good
spray pattern.
DWG. NO. 5835
ERROR MESSAGES
Most error messages are displayed on the right
half of the display to inform the operator of spe-
cic conditions. Following is a description of
those messages.
LOW BATTERY CONDITION
This message is displayed whenever the battery
voltage at the console drops below ten volts. The
console suspends all operations until the normal
operating voltage level is resumed.
DWG. NO. 5811
HOLD
When displayed this reminds the operator that
the 8160 is in the Hold Mode and is no longer
doing any control. All boom valves are turned off
and Area and Volume stop accumulating.
DWG. NO. 5812
MAN ERR
This is displayed when the ERROR key is se-
lected and the Rate switch is in the “Manual” po-
sition.
DWG. NO. 5813
System Overview 9

10 System Overview
SIM
“SIM”will be displayed whenever theSpeed Sim-
ulator has been activated. The Speed Simulator
can be turned on and the speed set or turned off
in the Options menu. The simulated speed will
be displayed if the SPEED key is pressed.
DWG. NO. 5836
LOW SPEED
The LOW SPEED message will ash to warn
that the console can no longer operate in the
Run Mode. The Run Mode is suspended. The
console will no longer control the servo valve
automatically but all the “switched on” booms
will be left on. Although Area does not accumu-
late, Volume will continue to accumulate while
this message is displayed. Either increase your
speed or switch to manual operation.
DWG. NO. 5817
LOW FLOW
The LOW FLOW message will ash to warn that
the console can no longer operate in the Run
Mode. The Run Mode is suspended. The console
will no longer control the servo valve automatical-
ly but all the “switched on” booms will be left on.
DWG. NO. 5818
Although Volume does not accumulate, Area will
continue to accumulate while this message is
displayed. Either increase ow (speed) or switch
to manual.
Note: The LOW FLOW and LOW SPEED mes-
sages will alternately ash if both warnings are
active.
ZERO WIDTH
The ZERO WIDTH message will ash to warn
that the console can no longer operate in the
Run Mode.
This message indicates that the total width of the
“on” Boom switches is equal to zero. Zero inches
was entered into one or more of the boom widths
and these are the only boom switches turned on.
This message is only displayed while in the Run
Mode (including manual). The Run Mode is sus-
pended. The console will no longer control the
servo valve automatically but all the “switched
on” booms will be left on. Although Area does
not accumulate, Volume will continue to accu-
mulate while this message is displayed.
DWG. NO. 5816
OVER
This is short for overow. This indicates the 8160
has calculated a number greater than allowed.
Clear Area or Volume back to zero or ignore this
message.
DWG. NO. 5819

DWG. NO. 5802
SYSTEM CONNECTIONS
POWER CONNECTOR
The Power cable connects to the battery to sup-
ply power to operate the system.
SPEED CONNECTOR
This is the Speed input. It connects to an ap-
propriate Speed sensor.
FLOW CONNECTOR
This is the Flow input. It connects to the
Flowmeter.
BOOM CONNECTOR
This is the connection for the Boom control
valves. It has all the connections for connect-
ing up to three motorized ball valves or solenoid
valves. The connector also contains the connec-
tions for the Remote Run/ Hold.
SERVO CONNECTOR
This is the connection for the Motorized Control
Valve (Servo Valve)
RUN / HOLD CONNECTOR
This is an alternate Run/Hold input connection.
This input and the Run/Hold input in the Boom
connector are electrically connected to the same
input.
SERIAL CHANNEL CONNECTOR
This is a 9-pin Sub-D connector to connect to an-
other device using RS-232 communications and
the Hiniker Protocol or Generic Protocol for Vari-
able Rate Applications. This connector is located
on the back of the console.
System Overview 11

TITLE
OPERATING GUIDELINES
The purpose of this section is to provide some
general guidelines and recommendations for op-
erating the 8160 in the eld.
The console must be congured for the mode
(Spray or NH3) you are going to operate in be-
fore starting the application. Perform both the
Set-up procedure and the Distance Calibration
procedure before attempting to use this console.
Failure to do this will result in faulty control and
inaccurate Volume, Area, and Speed data.
When not applying chemical the console should
be put into the Hold Mode. Move the Run/Hold
switch on the console to the Hold position. This
will shut off the Boom Valves and stop accumu-
lating Volume and Area. This may also be ac-
complished by using a Remote Run/Hold switch.
Using the Remote Run/Hold feature can reduce
the number of operations the operator must per-
form when starting and stopping the applica-
tion.
To apply chemical move the Run/Hold switch to
the Run position as you reach the place in the
eld where you want to start the application. It
is best to start moving before activating the Run
Mode and to reach the operating speed as soon
as possible. Return the Run/Hold switch to Hold
at the end of the eld. It is best not to slow down
signicantly before putting the console into Hold.
This will prevent the Servo Valve from moving to
far from its normal operating position. This re-
duces the time it takes to reach the proper ap-
plication rate as you again start applying.
The Boom switches may be used to shut off
Booms not required such as on end rows. The
console will make the necessary corrections to
insure proper application rates.
The 8160 console will allow you to determine
what is going on with your system. The keyboard
has ve keys labeled RATE, ERROR, SPEED,
VOLUME, AREA.
Pressing one of the ve keys will display that
selection. The top line of the display will always
show the Target Rate along with either Actual
Rate or % Error as selected by the operator. The
bottom line will display SPEED, VOLUME, or
AREA as selected by the operator. The operator
is free to select whichever selection he desires,
however, the following is a list of recommenda-
tions.
It is important to insure that the 8160 is control-
ling your sprayer properly. The RATE and ER-
ROR keys will show this.
Pressing the RATE key will display the actual
Volume per Area. Pressing the ERROR key will
display the actual error between the Target and
Actual application rates. This is displayed as a
percentage.
The console must be in the Run Mode and be re-
ceiving Speed and Flow signals to display RATE
or % ERROR. Although any calculated errors
less than 10% are considered good The 8160
will control the servo valve until the error falls
below ±1%. The warning light will ash when the
error exceeds ±10%.
The 8160 will automatically adjust the ow
whenever Rate 1 or Rate 2 is selected. Switch-
ing between Rate 1 and Rate 2 can be done at
any time and as often as desired. The 8160 will
change to the new application rate very quickly
and maintain that rate very accurately.
It is highly recommended that the operator take
advantage of the dual rate control. Signicant
chemical savings can be made if Rate 2 is pro-
grammed to a higher rate for weedy spots, and
ONLY used when eld conditions require it. All
the rest of the time the operator can stay at the
lower Rate 1 and save chemicals.
When required putting the Rate switch in the
center position (Manual) will turn the automatic
control off. Pressure can then be adjusted man-
ually.
OPERATION
12 Operation

Operation 13
Driving too slow will cause the servo valve to
end stop (fully close). When this happens, your
pressure gauge will show minimum PSI. The
console can no longer maintain the selected ap-
plication rate and will display LOW FLOW and
stop controlling.
To prevent a “LOW FLOW” message as you slow
down the 8160 can automatically stop reducing
the ow at a preset minimum ow rate. This pre-
vents a poor spray pattern from your nozzles.
This option can be turned on and the Minimum
Flow Rate set in the OPTIONS Menu. This is only
available for the Spray Mode. Keep in mind that
you are OVERAPPLYING to maintain a spray
pattern at very low speeds. Whenever the ow is
reduced to the Minimum Flow level, the display
will ash “MIN” to indicate that the console will
not reduce the ow any further.
NOTE: The following procedure can be used as
an alternative to using the Minimum Rate fea-
ture. After slowing down the console does not
control the servo valve but instead displays
“LOW FLO”, change the Rate switch to manual
and press “ ” key until you achieve operating
ow. Increase your speed then select rate 1 or
rate 2. The 8160 will again control your ow as
you increase your speed. Keep in mind that you
are OVERAPPLYING to maintain a spray pat-
tern at very low speeds.
VARIABLE RATE
The 8160’s Rate 1 can be changed “on the go”
by using the Variable Rate feature. An external
source must provide Application Rate informa-
tion to the 8160 in real time.
The information must be provided through the
RS232 port on the rear of the 8160 using either
the Hiniker Protocol or the Generic Protocal.
These protocols are listed in the appendix.
The external rate input will override the RATE 1
application rate data. The Rate Switch must be
in the Rate 1 position.
The Rate 1 Application Rate that was pro-
grammed in during Set-Up is not changed. The
console will use the variable Rate data until pow-
er is switched off. When the console is powered
back on, the original Rate 1 data will be used.
Note: If you go into the Set-Up routine before
powering down, the 8160 will save the current
displayed Rate 1 data for Rate 1 when you exit
Set Up.
The console will display the current Rate on the
upper left of the display.
The 8160 will continue to apply at the rate speci-
ed in the last received message until it receives
a new message specifying a new application
rate.
Switching to MANUAL or RATE 2 will override
the external rate input.
Turning the console off will reset the Variable
Rate Data to the Rate 1 data that was originally
programmed in.
Cables are available for connecting to most Pre-
cision Farming Systems. Refer to the Hiniker
Parts Book for specic information. Refer to
the Manual supplied with the Precision Farm-
ing equipment for programming their console for
third party controllers.
The Hiniker Protocol requires a Null modem se-
rial cable.
If using the Generic protocol, program the Preci-
sion Farming Console as if you were connecting
to a Raven 440.
Do not divide the ow calibration number by 10
as instructed in some manuals. Use the calibra-
tion number listed on the Hiniker owmeter.
For proper operation software version 3.0 or
higher is required. If you have earlier versions
the 8160 will need to have the software updated.
The software version is shown on the display
each time the 8160 is powered up.

MENU
The 8160 is constructed to allow for maximum
exibility when changing between Spray and
NH3 applications. The console will be cong-
ured individually for each application Set-up. The
menu will allow you to easily access and change
the conguration of each Set-up without effect-
ing the other.All calibration information and user
preference settings are stored separately for the
Spray and NH3 congurations.
IS THIS SPRAY
APPLICATION? NO
GPA RATE 1 20.0
GPA RATE 210.0
LEFT BOOM 120”
CENTER BOOM 120”
RIGHT BOOM 120”
SERVO VALVE
RESPONSE = 6
FLOWMETER
PULSES/GAL = 72.0
DISTANCE CAL.#
PULSES/FT - 2.00
IS THIS AN INLINE
SYSTEM? Y
8160 MENU SYSTEM
MAIN MENU
IS THIS NH3
APPLICATION? Y
PPA RATE 1 180.0
PPA RATE 2 150.0
LEFT BOOM 510”
CENTER BOOM 0”
RIGHT BOOM 0”
SERVO VALVE
RESPONSE = 6
FLOWMETER
PULSES/LB = 16.9
DISTANCE CAL. #
PULSES/FT - 2.00
GO TO OPTIONS MENU? N
ENTER BASED ON
CURRENT OPERATING
MODE WHEN SET
WAS PRESSED
NO
8160 MENU SYSTEM
MAIN MENU
YES YES
SPRAY NH3
NO NO
EXIT EXIT
TO SPRAY
OPTIONS MENU TO NH3
OPTIONS MENU
14 Operation
To enter the Main Menu press and hold the SET
key for 2 seconds.
Upon entering the main menu the current select-
ed mode will be displayed, either Spray or NH3.
To change to the other mode (Spray or NH3)
press the key to change the answer to NO
then press SET.
Navigating the Menu
Three keys are used to navigate the menu. They
are the SET, the key and key.
NOTE: Pressing any other key except SET, , ,
will provide a shortcut out of the menu system.
The and keys are used to change a Value or
anAnswer that is being displayed. The key will
increase a Value or change the answer to Yes
(Y). The key will decrease a Value or change
the answer to No (N). These keys are also used
to control the Servo Valve when in Manual.
The SET key is the same as the ENTER key on
a computer keyboard and performs the same
function. Pressing the SET key will cause the
console to accept whatever is currently being
displayed. This could be a Value, such as “LEFT
BOOM 120”, or the answer (Y or N) to a question
such as “GO TO OPTIONS MENU? “N“.
There are two types of menu items. The rst are
items that require a “Value”. Examples are “GPA
RATE 1 20.0” or “FLOWMETER PULSES/GAL
= 72.0” Use the and keys to change the
“Value” then press the SET key to accept these
changes and proceed to the next menu item.
The second type of menu items are those that
require an “answer” to a question. An example
would be “IS THIS SPRAY APPLICATION? Y”.
Use the key to answer “Y” (YES) or the key
to answer “N” (NO) then press the SET key to
accept these changes and proceed to the next
menu item. Which menu item will be displayed
next is based on your answer to the question. In
the example above, if the answer were changed
to “N”, then the next item displayed would be
“PPA RATE 1 180.0” on the NH3 menu. If it was
answered “Y” the next item would be “GPARATE
1 20.0” in the Spray menu.

Operation 15
To navigate the menu, change the “Value” or the
“answer” to the question, then press SET. The
new “Value” will be saved and you will advance
to the next menu item based on your answer.
NOTE: The default answers to the menu items
are set to allow you to press SET repeatedly
without changing any values or jumping to other
menus or routines. This is to prevent uninten-
tional changes and to allow for speedy access
to each item.
SELECTING OPERATING MODES
There are two separate modes for the 8160, the
Spray mode, and the NH3 mode. All calibration
numbers, all settings, and the Area and Volume
totals are stored separately for each mode. As
an example, if you perform the Distance Calibra-
tion while in the Spray mode you would need
to perform the Distance Calibration again after
switching to the NH3 mode.
HOW TO SELECT AND CHANGE OPERATING MODES
DISPLAY COMMENTS and ACTIONS
Press and hold SET key for Two seconds to enter Set-Up
IS THIS A SPRAY
APPLICATION? Y
Or
IS THIS AN NH3
APPLICATION? Y
The Display will always show the current operating mode and “Y’ as the default
answer. Pressing SET will allow access to the menu for the current mode. To
change Operating Modes and access it’s Set-up Menu, press the key to
change the answer to “N” then press SET.
Pressing any key except SET, , or will provide a shortcut out of Setup and
return you to the current operating mode. For instructions on setting up an ap-
plication see Spray Mode Set-up or NH3 Mode Set-Up.

SPRAY MODE SET-UP
This section is for Sprayer Set-Up only. Refer to
the NH3 Set-Up section for Anhydrous Ammonia
applications.
To enter the Main Menu press and hold the SET
key for 2 seconds.
Upon entering the main menu the current select-
ed mode will be displayed, either Spray or NH3.
If the NH3 mode is displayed then press the
key to change the answer to NO then press SET.
This will take you to the Spray Menu.
16 Operation
SPRAY MODE SET-UP
DISPLAY * COMMENTS and ACTIONS
To select the operating mode see “HOW TO SELECT AND CHANGE OPER-
ATING MODES” See NH3 MODE SET-UP for NH3 applications.
GPA RATE 1 20.0 Press the and keys to adjust the value for Rate 1 then press SET.
GPA RATE 2 10.0 Press the and keys to adjust the value for Rate 2 then press SET.
LEFT BOOM 120” Press the and keys to adjust the width, in inches, for the Left Boom Sec-
tion, then press SET
CENTER BOOM
120” Press the and keys to adjust the width, in inches, for the Center Boom
Section, then press SET.
RIGHT BOOM 120” Press the and keys to adjust the width, in inches, for the Right Boom Sec-
tion, then press SET.
SERVO VALVE
RESPONSE= 6 Press the and keys to adjust the Valve Response, then press SET. The
higher the number the faster the response.
FLOWMETER
PULSES/GAL =
72.0
Press the and keys to adjust the Flowmeter Calibration number, then
press SET.
DISTANCE CAL. #
PULSES/FT= 2.00 You may enter the Calibration number manually here or perform the “Distance
Calibration Procedure” later to have it calculated automatically. To enter it man-
ually press the and keys to adjust the Distance Calibration number, then
press SET. To continue without changing the Calibration number just press
SET.
IS THIS AN INLINE
SYSTEM? Y If this is an In-line System press the key to change the answer to “Y”, then
press SET. For a By-pass System press the key to change the answer to
“N”, then press SET.
GO TO OPTIONS
MENU? N The OPTIONS MENU contains optional features and Settings such as Distance
Calibration, Remote Run/Hold control, and Minimum flow control. See “OP-
TIONS MENU” for further information. To go to the OPTIONS MENU press the
key to change the answer to “Y”, then press SET. To exit the Spray Mode
menu now press SET.
* Note: Display values shown are factory default values. Values shown will be the current settings.

Operation 17
NH3 MODE SET-UP
This section is for NH3 Set-Up only. Refer to the
Spray Set-Up section for Spray applications. To
enter the Main Menu press and hold the SET key
for 2 seconds.
Upon entering the main menu the current select-
ed mode will be displayed, either Spray or NH3.
If the Spray mode is displayed then press the
key to change the answer to NO then press SET.
This will take you to the NH3 Menu.
NH3 MODE SET-UP
DISPLAY * COMMENTS and ACTIONS
To select the operating mode see “HOW TO SELECT AND CHANGE OPER-
ATING MODES” See SPRAY MODE SET-UP for Spray applications.
PPA RATE 1 180.0 Press the and keys to adjust the value for Rate 1 then press SET. This is
pounds of actual N per Acre.
PPA RATE 2 150.0 Press the and keys to adjust the value for Rate 2 then press SET. This is
pounds of actual N per Acre.
LEFT BOOM 510” Press the and keys to adjust the width, in inches, for the Left BoomSection,
then press SET. If using only one boom enter the entire Boom Width here.
CENTER BOOM 0” Press the and keys to adjust the width, in inches, for the Center Boom
Section, then press SET. If using only one boom leave at “0” and turn center
boom switch off.
RIGHT BOOM 0” Press the and keys to adjust the width, in inches, for the Center Boom
Section, then press SET. If using only one boom leave at “0” and turn center
boom switch off.
SERVO VALVE
RESPONSE= 6 Press the and keys to adjust the Valve Response, then press SET. The
higher the number the faster the response.
FLOWMETER
PULSES/LB = 16.9 Press the and keys to adjust the Flowmeter Calibration number, then
press SET.
DISTANCE CAL. #
PULSES/FT= 2.00 You may enter the Calibration number manually here or perform the “Distance
Calibration Procedure” later to have it calculated automatically. To enter it man-
ually press the and keys to adjust the Distance Calibration number, then
press SET. To continue without changing the Calibration number just press
SET.
GO TO OPTIONS
MENU? N The OPTIONS MENU contains optional Features and Settings such as Dis-
tance Calibration, Remote Run/Hold control, and Minimum flow control. See
“OPTIONS MENU” for further information. To go to the OPTIONS MENU press
the key to change the answer to “Y”. Then press SET. To exit the Spray
Mode menu now press SET.
* Note: Display values shown are factory default values. Values shown will be the current settings.

OPTIONS MENUS
There are two “Options” menus. They are iden-
tical except that the Minimum Flow Feature is
not available for NH3 applications. The settings
for each of these option menus are stored sepa-
rately for each operating mode (Spray or NH3).
Changing a setting while in one operating mode
has no effect on the settings in the other mode.
The Options menu is located at the end of the
Main menu for each operating mode.
The Options menu contains the following options
and procedures:
1. Distance Calibration
2. Distance Measurement
3. Remote Run/Hold Enable
4. Horn Control
5. Minimum Flow Control (Spray Mode Only)
6. Protocol selection, Logging, and Field #.
7. Valve Prole selection
8. Speed Simulator
9. Test Inputs for Speed, Flow, and Run/Hold
10. Display Smoothing
18 Operation
Table of contents
Other Hiniker Controllers manuals
Popular Controllers manuals by other brands
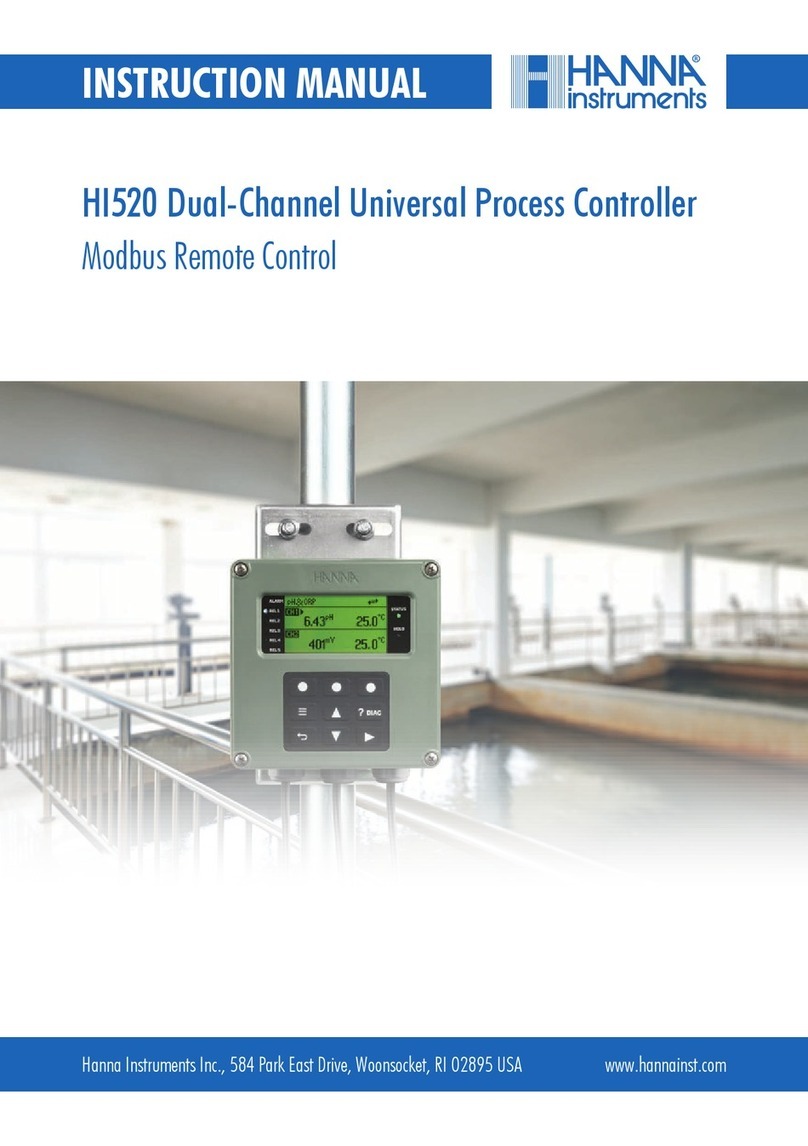
Hanna Instruments
Hanna Instruments HI520 instruction manual
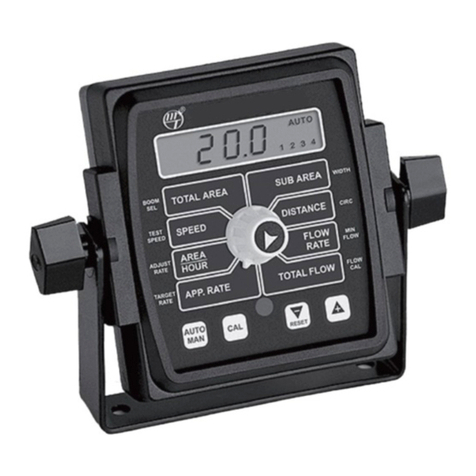
micro-trak
micro-trak MT-2405 FTW Reference manual
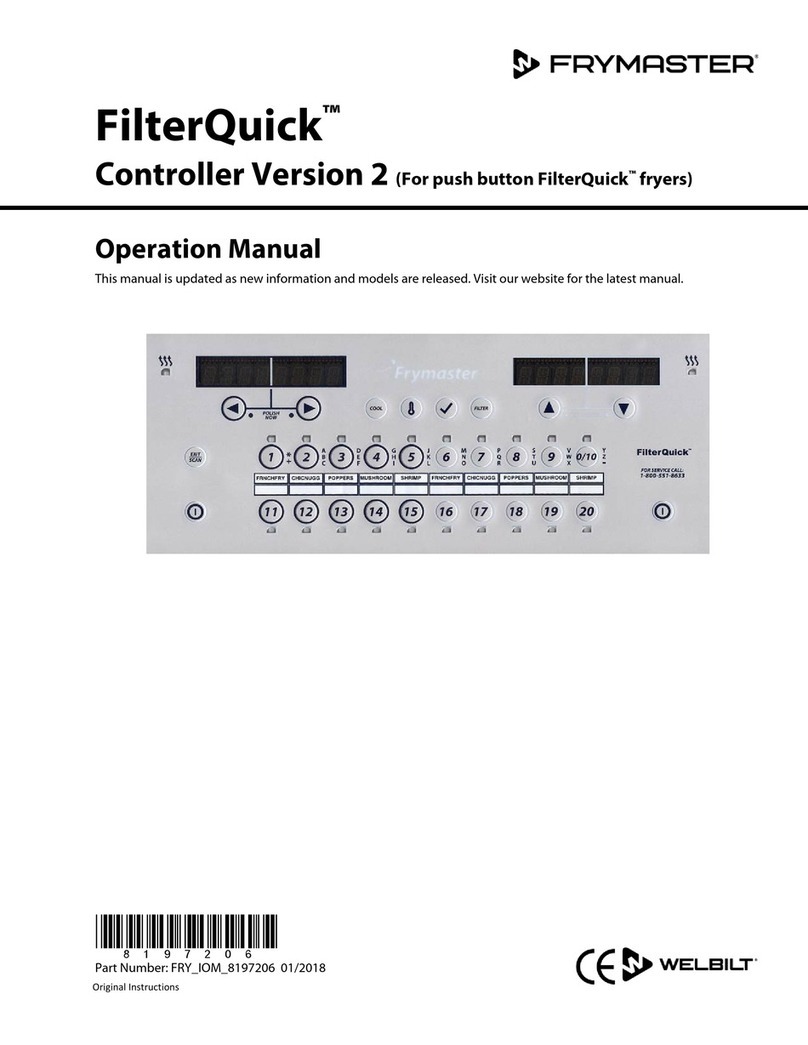
Frymaster
Frymaster FilterQuick Version 2 Operation manual
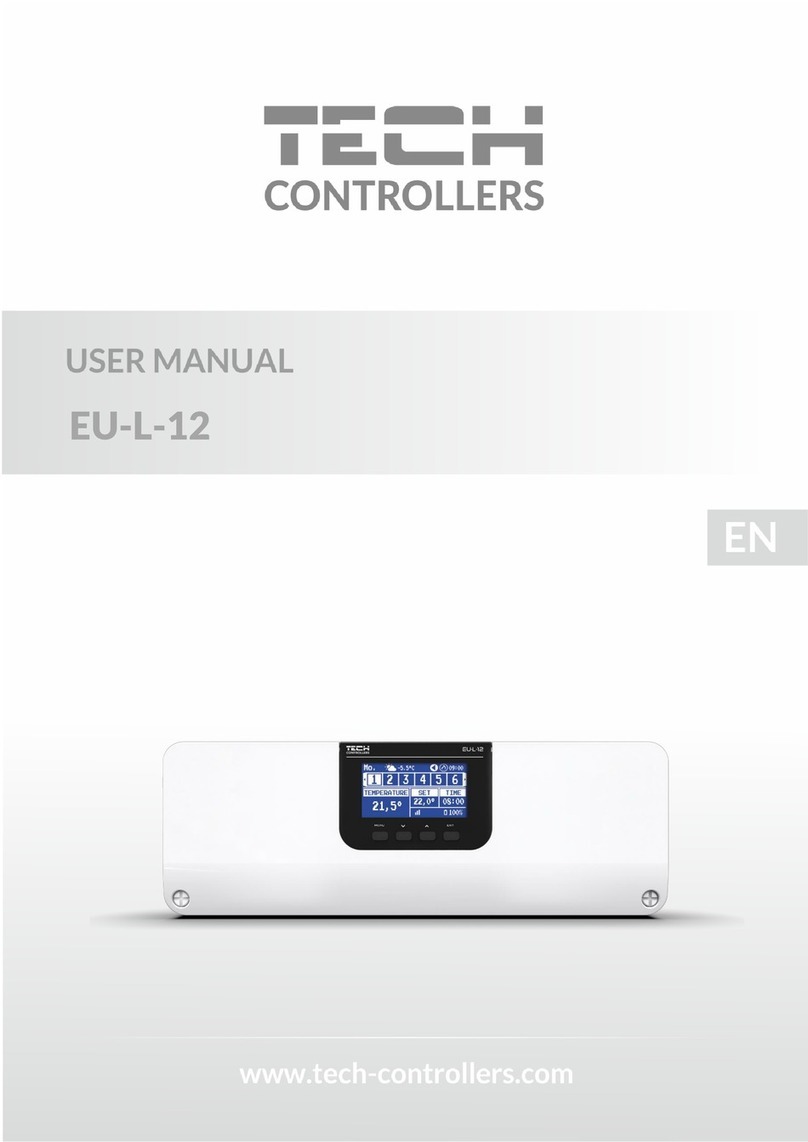
Tech Controllers
Tech Controllers EU-L-12 user manual
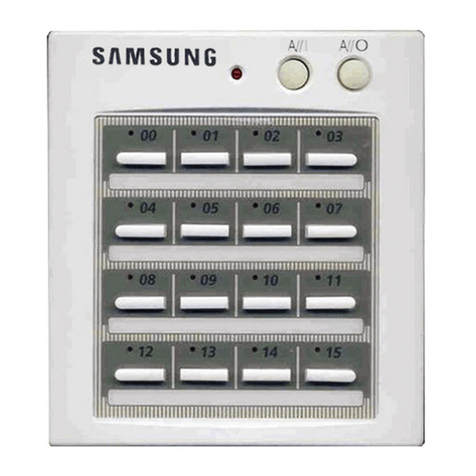
Samsung
Samsung MCM-A202DN installation manual

Emerson
Emerson Fisher 4660 instruction manual