Hirschmann HC3901 User manual

HIRSCHMANN
Load Moment Indicator
for Crawler Crane
HC3901
Operator’s Manual
Hirschmann Electronics(Shanghai)Co.,Ltd
Suite 12A, Huamin Empire Plaza, No.726, West Yan An Road, Shanghai, P.R.China
Tel: 021-51082780
Fax: 021-52375899
Zipcode: 200050
Website: http://www.hirschmann.com

Copyright
This document contains propriety information which is protected by copyright, and all rights are
reserved. No part of this manual may be photocopied, reproduced or translated to another language
without prior written approval of Hirschmann Electronics (Shanghai) Co., Ltd.
Declaration
All information in this document is subject to change without notice.
Hirschmann makes no warranty of any kind with regard to this material, including, but not limited to,
the implied warranties of merchantability and fitness for a particular purpose.
Hirschmann will not be liable for errors contained herein or for incidental or consequential damages
in connection with reference to, and performance or use of this manual.
Applied Scope
This manual is made for the following crane manufacturer
Zoomlion
This manual can be applied to the following types of crawler cranes manufactured by the partner:
ZCC1100H
Rev. Date Prepared Checked Modifications
01 2014-08-04 Guo Tao Zhou Fei First issue, English
HC3901for Zoomlion ZCC1100H
Special Notice
Using components of LMI rather than from Hirschmann may cause problems of inaccuracy and
even malfunction of the LMI system. We recommend you use genuine Hirschmann components and
parts during repairing and service. Hirschmann is not liable of any responsibilities in case genuine parts
are not used.

Table of Contents
1. GENERAL INFORMATION....................................................................................................................1
2. IMPORTANT NOTES ..............................................................................................................................2
3. SYSTEM DESCRIPTION.........................................................................................................................3
3.1 HC3901 Controller .............................................................................................................................4
3.2 WG Angle Sensor ...............................................................................................................................5
3.3 Force Sensor........................................................................................................................................6
4. OPERATION AND DISPLAY INTERFACE ..........................................................................................7
4.1 Data display(values are only for example)....................................................................................8
4.2 EN13000 .............................................................................................................................................8
4.3Weight status bar..................................................................................................................................9
4.4 Indicator light......................................................................................................................................9
5. OPERATION METHOD and PROCESS (only for example) ................................................................10
5.1 Reeving Setting.................................................................................................................................11
5.2 Function Setting................................................................................................................................12
5.3 Error Code Information ....................................................................................................................15
5.4 Angle Limit Setting...........................................................................................................................16
6. SYSTEM FUNCTIONS ..........................................................................................................................17
6.1 Warning.............................................................................................................................................17
6.2 Prohibition ........................................................................................................................................17
7 INSPECTION MAINTENANCE AND CONSIDERATIONS ...............................................................18
7.1 Inspection before Operation .............................................................................................................18
7.2 Routine Maintenance ........................................................................................................................18
7.3 Routine Consideration ......................................................................................................................18
7.4 Buzzer Alarms ..................................................................................................................................18
7.5 Angle Sensor Adjustment .................................................................................................................18
8. TROUBLESHOOTING ..........................................................................................................................19

1
1. GENERAL INFORMATION
The load moment indicator HC3901 (hereinafter referred to as LMI) is applicable to the telescopic
boom crane, lattice boom crane, all- terrain crane and other types of cranes.
The HC3901 LMI can provide the crane operator with essential information required to operate the
crane within its design parameters. Using different sensors, LMI can provide the crane operator with
information on real time basis regarding boom length, boom angle, working height, working radius, rated
load and actual weight being lifted by the crane
The system operates on the principle of reference/real comparison. The boom angle is measured by
angle sensor that is mounted on the boom. The crane load is measured by force transducers attached to the
boom pendants. The real value, resulting from all the sensors measurement is compared with the
reference data, stored in the controller. If non-permitted conditions are approached, the LMI will warn the
operator by audible alarm, warning light and at the same time, some dangerous movements such as lifting
and luffing down will be stopped with the help of the crane control system.
This manual only gives guide for the LMI operation. Please refer to the Crane Operator’s Manual
provided by the crane manufacturer for detailed operating procedures of the crane.

Operator’s Manual
2
2. IMPORTANT NOTES
The LMI and control system is an operational aid that warns a crane operator of approaching
overload conditions and of over-hoist conditions that could cause damage to equipment and personnel.
The device is not, and shall not, be a substitute for good operator judgment, experience and use of
accepted safe machine operating procedures.
The responsibility for safe operation shall remain with the crane operator who shall ensure that all
warnings and instructions supplied are fully understood and observed, Prior to operating the crane ,the
operator must carefully and thoroughly read and understand the information in this manual to ensure
that he knows the operation and limitations of the LMI.
The LMI can only protect overload of the crane in boom vertical range without crane overturn
resulted from non-vertical lifting, ground inclination, derailed wheel etc. Therefore, the operators
should not neglect the crane safety management and operation regulation even if the crane is equipped
with LIM.
The LMI can only work correctly after all adjustments have been properly set. To prevent material
damage and serious or even fatal accidents, operating mode, reeving and limit data have to be properly
set up before operating the crane.
If there is any change in the crane’s configuration data, the LMI needs to be re-calibrated.
Make sure to disconnect the power supply of the LMI from the crane before applying any welding
work on the crane body or booms. The pulse may cause damage to the electrical and electronics parts.
Hirschmann shall not be liable for any damage caused by this.
Make sure to disconnect the power supply of the LMI during thunderstorm weather. Hirschmann
shall not be liable for any damage caused by lightning.
This system can be equipped with an external key-operated switch located in the crane operator's
cab. This key-operated switch overrides control lever function switch-off by the LMI or by the hoist
limit switch system.
This switch may only be used during emergency situations, and even then only by authorized
personnel. Failure to observe these instructions could result in damage to property and severe or even
fatal injuries to personnel.
If the LMI in use fails or is not properly functioning, please do stop the operation of the crane, and
contact the service of Hirschmann or crane manufacturer. Hirschmann does not assume any
responsibility for undesirable consequences resulted from the continued operation!
CAUTION
WARNING
DANGER

3
3. SYSTEM DESCRIPTION
Components of LMI System
Generally, the LMI system consists of
1. HC3901 Controller 1 pc
2. WG103 Angle Sensor 1 pc
3. KMD force Sensor 1 pc
1
2
3

Operator’s Manual
4
3.1 HC3901 Controller
HC3901 controller uses 16 bit high performance processors and the CANopen communication
technology. It is the safety protector specially designed to meet the required safety standards under the
harsh environment.
Technical data:
Operating temperature: –20°C ~+70°C.
Operating voltage: 11 ... 36V DC
Operating current: 200mA@24V
Communication interface: 1×CANopen, 1×RS232
Installation: External and horizontal
Display Size: 5.7 inch
Program memory: 2 x 2 MB
Data memory: 2 x 1 MB
Communiacation interface: 1×SAEJ1939,1×CANopen2.0B,2×RS232
Input analog: 6
Input digital: 6
Output digital: 6 (It can be set to PWM output, but it will reduce the no. of output digital.)
Relay output: 1 (max. 5A)
Protection class: IP65
Installation:
When the system is on, it’s forbidden to plug and unplug the cable connecting with the controller.
Before implementing any welding work on the crane body, the operator must take off cables
connecting the controller in order to avoid damage.
This system uses scaffolding installation.

5
3.2 WG Angle Sensor
Angle sensor WG accurately measures the boom angle. The high sealed housing keeps the inside
component away from the influence of temperature, humidity etc.
Technical data
Measuring range: 0-90°
Output signal: 4-20mA
Linearity tolerance: <±0.2°
Hysteresis tolerance: <±0.1°
Operating temperature: -25~+70
Storing temperature: -40~+70
Protection class: IP65
Installation
The correct positioning is important for installing angle sensors.
The angle sensors are usually installed along the right side boom, at the inner side of boom base, if
it’s viewed from the boom base to boom tip. (as shown below).
Make sure the horizontal line of sensor is parallel to the horizontal center line of the boom. Adjust the
bolts of the sensor to reduce the angle deviation between actual measured boom angle and displayed
boom angle on the console.
Angle Sensor Installation Graph
Angle Sensor Installation Graph
Boom bottom Angle sensor
Horizontal center line
of the boom

Operator’s Manual
6
3.3 Force Sensor
Force sensor KMD is perfectly designed for static and dynamic tensile force measurements.
The sensor stands out for high overload capacity, high fatigue strength, good corrosion resistance
and maintenance-free operation.
Technical data:
Nominal load range: from 1T up to 500T
Charge of measuring body: 200%
Charge of measuring body up to flow limit: 300%
Safe to breaking point: 500%
Linearity: < 0.3% typ.
Hysteresis: < 0.5% typ.
Protection class: IP65
Operating temperature range: -40℃to +70℃
Installation
KMD force sensor is measuring unit, it should require the conscientious and careful treatment.
Be sure to obtain the fittings and the relative tolerance data suggested by KMD force sensor.
Observe the installation situation to make sure that no elastic parts are used in the force transmission
which might affect the measurements.
The bores in the locking pins must be in alignment.
Make sure force sensor not to bear side force.
KMD Force Sensor Installation Graph

7
4. OPERATION AND DISPLAY INTERFACE
1.Data display(see 4.1)
2.Indicator light
3.Function keys: from left to right, menu key/buzzer key/back key/confirmation key.(the function keys
have one-to-one relationships with the key symbols on the display.)
4.Rotary button:They can be used to select function items on the display by rotating the button and
confirm the selection by pushing the button.
12
4 33

Operator’s Manual
8
4.1 Data display(values are only for example)
1. Height status bar and percentage display
2. Jib angle
3. Jib length
4. Height
5. OM information display
6. Reeving
7. OM code
8. Date and Time
display(year/month/day/hour/minute/second)
9. OM information setting
10. Function setting key symbol
11. Error code information key symbol
12. Upper and low angle setting
13. Main Hook/ Subhook Switch
14. Wind speed
15. Upper and low angle
16. Rated load weight
17. Actual load weight
18. Boom angle
19. Radius
20. Boom length
21. Error code information
16 15
1
17
2
18
19
21
345
6
7 8
9
10
11
12
13
14
20

9
4.2 EN13000
The yellow icon is force-active warning icon: when the crane is forced to be active, corresponding
warning icon will display on the main interface to remind that the crane is at force-active state now and
LMI will not have corresponding protection function.
LMI override activated
SET-UP mode activated
SET-UP mode activated alarm
Derricking in activated
Rope limit override activated
A2B switch activated
Slewing limit alarm
Main hoist three times protection alarm
Auxiliary hoist three times protection
alarm
Third hoist three times protection alarm
A2B switch on the main hoist alarm
A2B switch on the auxiliary hoist alarm
Main Boom luffing angle limit alarm

Operator’s Manual
10
4.3Weight status bar
The weight percentage status bar indicates the relationship between the actual load weight and the
rated load weight during the crane operation and the weight percentage value is subject to the relationship
changes.
Green zone: safe range (weight percentage0-90%)
Yellow zone: pre-warning range (weight percentage 90-100%)
Red zone: over-load warning range (weight percentage exceeding100%)
4.4 Indicator light
Prewarning light
This yellow prewarning light comes up when the load on the machine amounts to more than 90%
of the respective nominal carrying load, which indicates that an overload situation is
immediately pending.
For the operator, this means that the machine work can continue only with the greatest amount of
caution
Overloadwarninglight
This red Overload warning light indicates to the machine operator that an overload condition
has occurred. It lights up when the crane load has reached 100% of maximum load carrying
capacity permitted for the current operating status. The acoustic alarm sounds. The
load-moment-increasing crane movements are switched off at the same time
A2Bswitchlamp
This red warning light lights up when the heavy bob and spreader of A2B switch meet each
other and are hoisted. In the meanwhile, the buzzer alarms, which indicates the hook block has
arised the height maximum. Combining with the electric system, the crane movements from
hoisting and extending boom to luffing down are stopped. Please check A2B switch before operating the
crane in order to prevent human body and the crane from being injured.
Attention: Since A2B switch signal does not input into LMI system, this A2B switch lamp is used
invalid.

11
5. OPERATION METHOD and PROCESS (only for example)
When controller and console of the system is powered on, the data initialization automatically starts.
This progress cannot be directly observed, but a welcoming display (Logo display) will appear at the
console to present the manufacturer and the initializing status.
The crane drivers shall be very familiar with the operation of LMI system and correctly adjust it
before start to work.
Power on
Operate the crane to work.
Choose the same Reeving by
Reeving buttons
N
O
Self Checking System
Confirm OM
Choose the same OM by OM
buttons
N
O
Look up the error code list to solve
YES
Is the displayed
OM the same as
the actual one?
Is the showed
Reeve the same
as the actual
Error or Not?

Operator’s Manual
12
5.1 Set OM and Reev
Reeving setting is to set the LMI reeving identical to the actual reeving.Operators shall carefully
adjust the displayed reeving equal to the actual reeving before start to work.
The Reeving must be set equal to the actual reeving, otherwise the LMI may not be able to work properly.
At the main display, select icon by rotary button, press it or confirmation key to enter into
“Set OM and Reev” Display1 as followed:
Back to the previous display.
Confirm the select value.
Back to the main display.
In the “Set OM and Reev” Display1, circumgyrate the rotary button, press it or confirmation key to
enter into the “Set OM and Reev” Display2 (Self_assembly OM enter into the main display directly) as
followed:
After selecting OM parameter by pressing and rotating rotary button, press the confirmation key
twice to enter into main interface, then OM setting succeeds. After pressing confirmation key, press turn
back key, which means that setting is cancelled and OM can be reset.
WARNING

13
Two switchable OMs can be selected by default OM option.
5.2 Function Setting
At the main display, select icon by rotate button, press the button or confirmation key to enter
into ”Function Page” as followed:
Back to the previous display.
Confirm the select value.
Back to the main display.
5.2.1 System setting
At the “Function Display”, select “System Set” icon by rotary button, press it or confirmation key to
enter into ”System info” as followed:
Back to the previous display.
Confirm the select value.
Back to the main display.

Operator’s Manual
14
Time Setting
Before setting time, the first step is to input the password. If the display shows the wrong time,
please connect with the manufacture first. DO NOT set time yourself.
The setting steps are as followed:
At first, select “Time Set” icon by rotating button at the “Function Display”, press the button or
confirmation key to enter into “Input Password” as the following:
Back to the previous display.
Confirm the select value.
Back to the main display.
At the “Input Password”, the first password “ * ” is showed automatically number “0”. Operator can
select the correct number by rotate button, then press it or confirmation key, the system will transfer to the
second “ * ”.
After inputting four numbers, press the button or confirmation key to enter into “Time Set Display”
as the following:
Back to the previous display.
Confirm the select value.
Back to the main display.
In “Time setting”, when the year number turns blue, select actual year number by rotating button and
press it or confirmation key, the next number will automatically become blue.
After setting all numbers, “Confirm?” will appear on the interface. Press button or confirmation key,
and the “current time” will be modified to the actual time.

15
5.2.2 CANbus Status Overview
At the “Function Display”, select “Can Bus” icon by rotary button, press it or confirmation key to
enter into ”CANbus Status Overview Display” as followed:
Back to the previous display.
Confirm the select value.
Back to the main display.
At this display:
If the pane shows green, it means working normally.
If the pane shows yellow, it means preparing.
If the pane shows red, it means error or not-in-use status. At this moment, operators need to check
the system.
5.2.3 I/O Port Inquiry
At the main display, select “port inquiry” icon by rotate button, press the button or confirmation key
to enter into “I/O Port Inquiry Display” as followed:
Back to the previous display.
transfer to Analog Input Port Display
Back to the main display.
This display shows the information of Digital I/O port.The state pane shows green, it means high
level, DIN stands for digital input and DOUT is digital output.
If operators want to inquire analog information, please press menu key which represents icon
and transfer to “Analog Value” as followed:

Operator’s Manual
16
Back to the previous display.
Back to the main display.
5.2.4 Load Inquriy
At the “Function Display”, select “Load Chart” icon by rotary button, press it or confirmation button
to enter into the “OM select” display:
Back to the previous display.
Confirm the select value.
Back to the main display.
Select the OM by rotary button, press the confirmation button to enter into the”load chart” display,
as the followed:
Select the BM length by the rotary button, press the confirmation button ,then transfer to the
corresponding load data.
Note:All values in the chart are only for example.

17
5.3 Error Code Information
When the system appears malfunction, the error code would appear at the main display.Through the
error code information, crane operators and service engineers can better understand what the error code
stands for, and quickly find out the fault reasons and suggested solutions. (Operators can inquire the error
code by two ways: The error code inquiry in the display and the “troubleshooting” item in the menual.)
At the main display, select icon by rotary button, press the button or confirmation key to
enter into “Fault Help” as followed:
Back to the previous display.
Back to the main display.
Switch to query cause and elimination of different fault by rotarying button.
5.4 Angle Limit Setting
At the main display, select icon by rotary button, press the button or confirmation key to enter
into “Angle Limit Setting” as followed:
Back to the previous display.
Confirm the select value.
Back to the main display.
After the transformer to the maximum(minimum) in the main boom Angle, according to the
confirmed limit Angle value.
Table of contents
Other Hirschmann Measuring Instrument manuals
Popular Measuring Instrument manuals by other brands
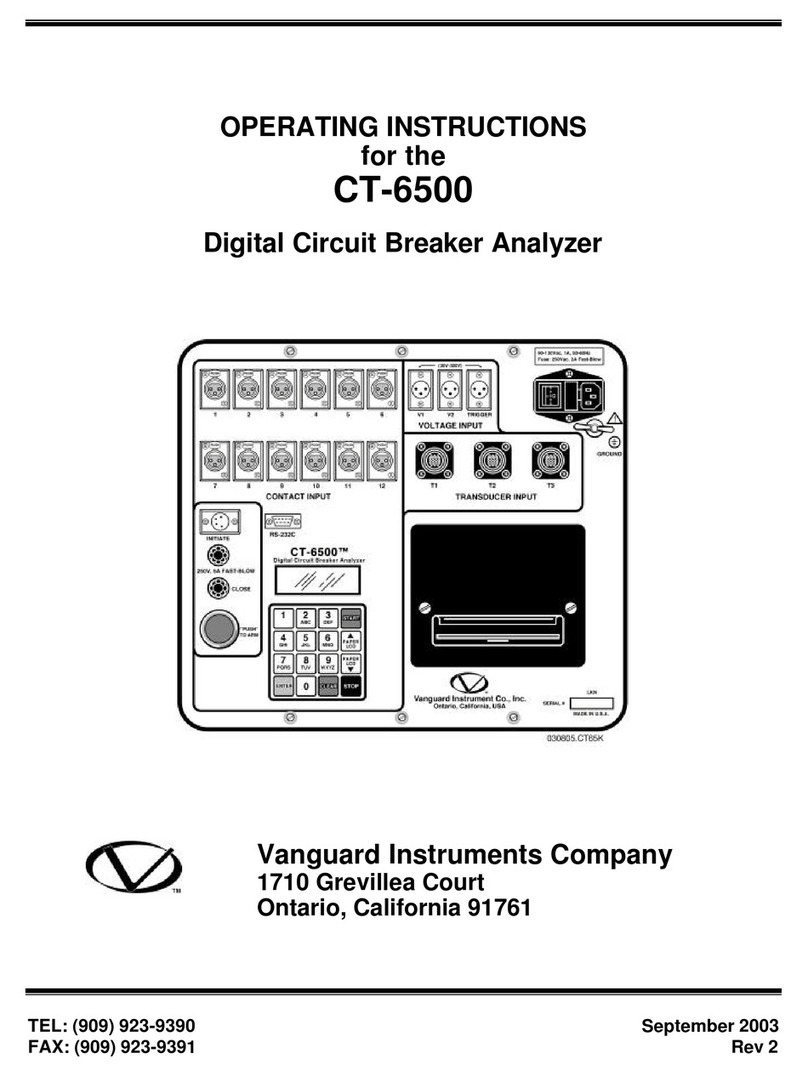
Vanguard Instruments Company
Vanguard Instruments Company CT-6500 operating instructions

Bayer HealthCare
Bayer HealthCare RapidPoint 400 Series Service manual
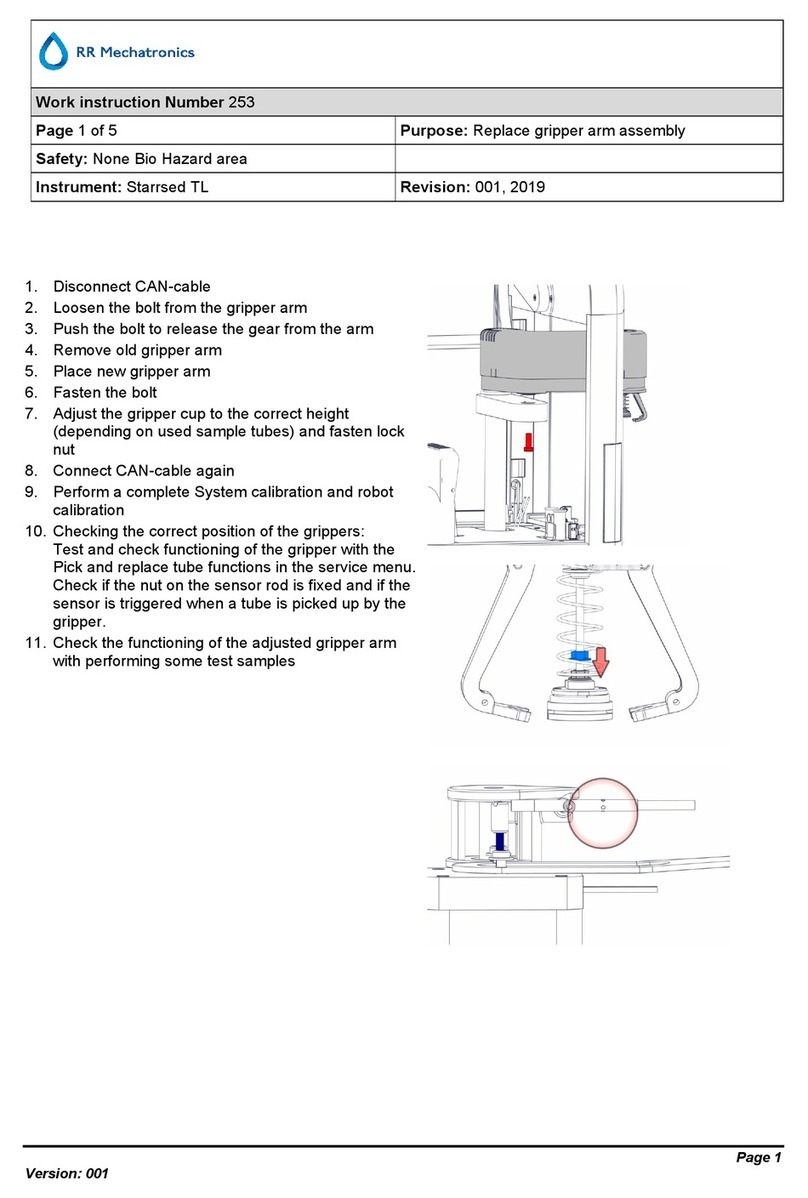
RR Mechatronics
RR Mechatronics STARRSED TL Work instructions

Martin Professional
Martin Professional The Wife user manual
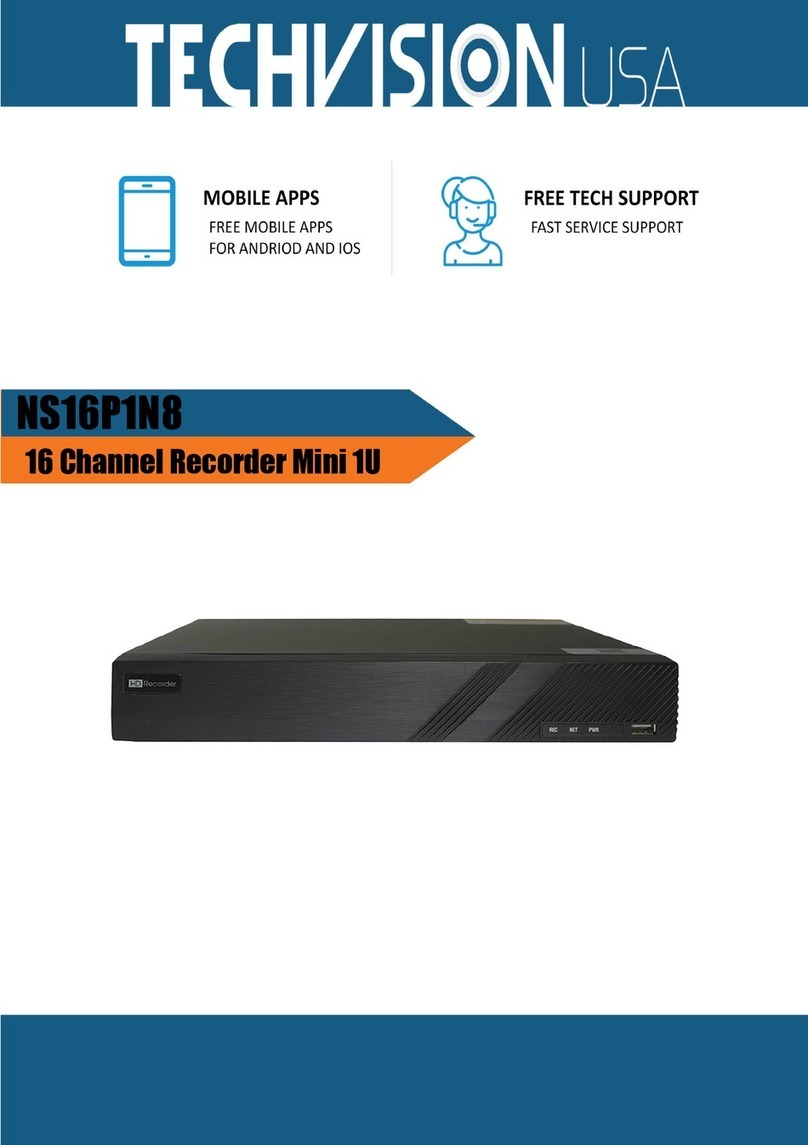
TechVision
TechVision NS16P1N8 manual
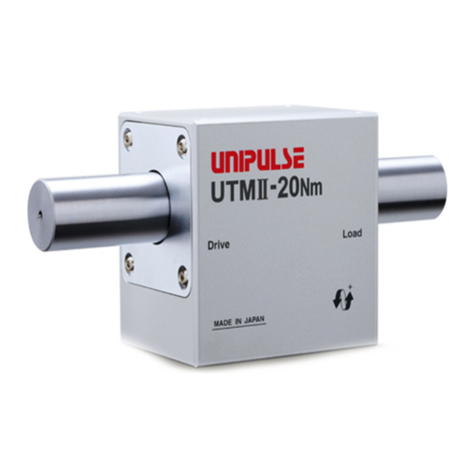
Unipulse
Unipulse UTM II-20Nm Operation manual