HMH MIREL RM1 Setup guide

© 1999 - 2018
278RM1 : 181112
(278-00-SW-4P-RM)
MAINTENANCE
AND
DIAGNOSTICS
MANUAL
MIREL RM1
Speed Recorder

278RM1 : 181112
2 / 25
Additional source files:
No. File Page Pages Description
1
2
3
Changes:
Code Date Description Approved by
010821 21.08.2001 Document introduction Ing. Horváth
130215 15.02.2013 Document updated based on technical condi-
tions Ing. Šajben
171018 17.10.2017 Changing of D4 prophylactic checkl conditions Ing. Michalec
180115 15.1.2018 Changing of assembly and disassembly condi-
tions Ing. Michalec
180208 8.2.2018 Changing of D4 conditions for RM1.1 Ing. Michalec
180411 11.4.2018 Update of terms Ing. Michalec
180507 31.5.2018 Update conditions for TEST mode Ing. Michalec
181112 12.11.2018 Update of fault codes list Ing. Michalec

278RM1 : 181112
3 / 25
Contents
Contents ....................................................................................................................3
Document Definition ..................................................................................................4
General Characteristics.............................................................................................5
Configuration of the Equipment.................................................................................6
Central Processing Unit...................................................................................................................7
Indication Unit.................................................................................................................................9
Identification Unit...........................................................................................................................10
Equipment Diagnostics........................................................................................... 11
D1 – Start-up self-diagnostic check of the equipment....................................................................12
D2 – Continuous self-diagnostic check of the equipment...............................................................13
D3 – Functional test......................................................................................................................15
D4 – Prophylactic check................................................................................................................16
Equipment Maintenance......................................................................................... 18
S1 – Operational repairs ...............................................................................................................19
S2 – Maintenance repairs .............................................................................................................20
Fault Signalling....................................................................................................... 21
Equipment Configuration........................................................................................ 23
Installation and Removal of the Equipment............................................................ 24
Notes ...................................................................................................................... 25

278RM1 : 181112
4 / 25
Document Definition
This document defines the scope, method and conditions for conducting diagnostics and
maintenance, conducting operating and maintenance repairs of the MIREL RM1 speed re-
corder.
This document is related to the following documentation:
Number Version Name
[1] 297RM1 150325 MIREL RM1 - Technical conditions
[2] 342RM1 180501 MIREL RM1 - Protocol on completed D3 functional test
[3] 357RM1 180411 MIREL RM1 - Operating manual
[4] 499RM1 170118 MIREL RM1 - Protocol on completed D4 prophylactic check
[5] 547MAP 160229 MIREL KAM - Operating manual
The document is intended for the following staff:
Of the manufacturer as reference documentation for the installation, configuration, start
up and maintenance of the MIREL RM1 speed recorder
Of the operator as reference documentation for the installation, configuration, start up
and maintenance of the MIREL RM1 speed recorder

278RM1 : 181112
5 / 25
General Characteristics
The MIREL RM1 speed recorder is equipment specifically designed for use on railway loco-
motives in all forms of tractive power. The RM1 secures three basic functions: measurement
of instantaneous speed, indication of instantaneous speed and additional information, regis-
tration of instantaneous speed and other operating and technical data in relation to a time
and route-independent scale.
The MIREL RM1 speed recorder is composed of a central processing unit, two indicator
devices and two identification devices located at the engineer's stations. The interconnection
of individual equipment is via a data line with serial data transmission. Alternatively the RM1
can be operated with only one indicator device or without one. The same applies for the
identification devices.
Power for the MIREL RM1 speed recorder is connected to the locomotive's battery source.
Configuration of the MIREL RM1 is dependent upon the voltage of the battery source. Ser-
vice of the speed recorder is performed exclusively from the engineer's station via the identi-
fication devices and control elements on the locomotive's control panel. Functionality of the
identification instrument may be integrated into the control unit of a cooperating system. No
entry into the locomotive's mechanical room or into the central processing unit of the equip-
ment is required to operate the MIREL RM1 speed recorder.
The MIREL RM1 speed recorder is an electronic digital system designed on the basis of the
latest electrical components where each instrument is controlled by a separate processor.
The components used in the central processing unit meet demanding criteria for reliability
and robustness. The central processing unit contains a processor module, power supply,
registration module, module for measuring frequency inputs and a module for galvanically
isolated digital inputs and outputs. The registration module is designed on the basis of large
capacity semiconductor memory chips that ensure the storage of data even if disconnected
from the locomotive's battery source for an extended period of time. The indication equip-
ment contains the actual pseudo-analogue indication instrument and a digital indicator of
instantaneous speed. The identification equipment comprises a 32-character alphanumeric
display and a 12-button keyboard.
The MIREL RM1 speed recorder performs regular self-diagnostics and enables the perfor-
mance of functional tests to re-test the correct functionality of all control system components
and locomotive equipment that works with it. The equipment is maintenance free apart from
performing functional tests.

278RM1 : 181112
6 / 25
Configuration of the Equipment
The basic schematic for connecting the components of the MIREL RM1 speed recorder and
cooperating equipment on board the locomotive includes:
Basic components:
Central processing unit 1x
Indication unit 2 x
Identification unit 2x
Cooperating equipment:
Incremental rotation sensor 1x
Control switch at engineer's station 2x (or 1x)
Train control system
Optional cooperating equipment:
ARR
Control system
etc.
Schematic for connecting the equipment to the locomotive:
MIREL
RM1
VZ ARR RS
Spínače
riadenia
Binárne a spojité
signály HKV
Snímač
otáčok
Speed
sensor Control
switches
Binary and continous
signals of the locomotive
VZ ARR RS
MIREL
RM1
Schematic for connecting MIREL RM1 speed recorder units:
ZJ
ID1 ID2IN1 IN2
Basic block diagram of the test sample
engine room
2 engineer’s cab.1. engineer’s cab
RS485RS485
RS485RS485

278RM1 : 181112
7 / 25
Central Processing Unit
The central processing unit secures all the operating functions of the MIREL RM1 speed
recorder.
Measuring and filtering impulses from the impulse rotation sensor
Calculating speed
Calculating the distance travelled
Evaluating the distance travelled
Variables required for registration
Reading digital and analogue inputs
Controlling digital outputs
Communication with the indication and identification units at engineer stations
Communication with connected cooperating equipment on board the locomotive
Auto-diagnostics
Indication on the front panel
The central processing unit is furnished in two different configurations according to the type
of processor and registration module:
Basic configuration (8 MB registration module capacity), central processing unit type
RM1ZJ.0.xxxxx (MIREL RM1 with type marking RM1.0.XXXX)
Expanded registration module memory (16GB registration module capacity), central
processing unit type RM1ZJ.1.xxxx (MIREL RM1 with type marking RM1.1.XXXX).
A more detailed description is given in the 297RM1 technical conditions.
A set of 16 LED indicators is installed on the front panel of the central processing unit. No
control elements are located on the central processing unit and there is no need for the op-
erator to interfere with the central processing unit during operation of the speed recorder.
The central processing unit is powered from the locomotive's battery source. Power is pro-
vided through a separate breaker dedicated for the speed recorder and installed with other
breakers for the locomotive or in another specific location depending on the specific type of
locomotive. The other components of the MIREL RM1 speed recorder are powered by the
central processing unit.
The indication elements and a 15-pin DB type connector for reading the registration unit are
installed on the front panel.

278RM1 : 181112
8 / 25
The central processing unit is constructed with a 19" width to comply with the IEC 297
standard for rack-mounted equipment. The height is defined as 3U pursuant to the standard
(module U = 44.45 mm). The modules of the central processing unit are installed in an AL
cabinet. A 72-pin DD type industrial connector and a 25-pin DB type connector are located
on the rear panel. The central processing unit will operate in any position. The central pro-
cessing unit is installed inside the locomotive based on the specific type of locomotive. Ac-
cess to the front panel without requiring any disassembly is sufficient for ordinary operating
conditions and when maintenance is required.

278RM1 : 181112
9 / 25
Indication Unit
The indication unit ensures that the following data is displayed at the engineer's station:
Instantaneous speed - a pseudo-analogue gauge, digital indicator
Maximum allowed speed - red signal (in conjunction with MIREL VZ1)
Pre-set speed – green signal (in cooperation with the automatic speed regulation mod-
ule)
The indication unit is a single purpose computer. This computer contains a gauge indicator,
number indicator, 2 signals and 3 indication LEDs and a light intensity sensor. The instru-
ment cluster is permanently backlit with brightness regulation. The brightness of the number
indicator and the signals themselves is also regulated. The unit is connected to the central
processing unit with a four-conductor cable that powers the indication unit and secures data
communication between the central processing unit and the indication unit.
The indication unit is constructed in the form of a plastic box intended for integration into the
desk at the engineer's station. The indication components are installed on the front face of
the box with a 7-position terminal strip located on the back. The equipment can be installed
in any suitable manner based on the construction of the locomotive so long as the indication
components are visible.
The digital speed indicator for the locomotive displays the instantaneous speed with maxi-
mum accuracy thanks to the speed recorder. The function of the pseudo-analogue dial
gauge is to provide the operator with an instantaneous indication when checking the instan-
taneous speed.
OIxIN4 číslicový ukazovateľokamžitej rýchlosti
OIxIN1 pseudoanalógová ručičková indikácia okamžitej rýchlosti
OIxIN2 svetelná stopa maximálnej povolenej rýchlosti
OIxIN3 svetelná stopa predvolenej rýchlosti
OIxIN5 OK indikácia správnej činnosti indikačnej jednotky
OIxIN6 AR indikácia zaplnenia registračného archívu
OIxIN7 ERR indikácia poruchy zariadenia
OIxIN3
OIxIN2 Indicator of maximum allowed speed
OIxIN4 Digital display of actual speed
Indicator of preset speed
OIxIN1 Indicator of actual speed
OIxIN5
OIxIN6
OIxIN7
Correct function indicator of indication unit
Full memory indicator of the juridical recorder unit
Equipment fault of system
OK
AR
ERR

278RM1 : 181112
10 / 25
Identification Unit
The identification unit is used to enter the engineer's data and to provide alpha-numeric in-
formation on the display. The identification unit can also be used to display the following, in
addition to the login prompt:
Instantaneous speed - numeric information
Maximum speed - numeric information
Pre-set speed - numeric information
Calendar date and time in hours, minutes and seconds
Total distance travelled in km
Total daily distance travelled in km
Percentage of used recording registration capacity
Entering the engineer's identification number
Entering the train number
Entering train weight
1)
Entering the carrier identification number
1)
Entering the operating mode
1)
1)
only for the configuration with expanded memory in the registration module (MIREL RM1 with type
marking RM1.1.XXXX)
The identification unit is a single purpose computer. It contains a 32-character alpha-
numeric display (2 x 16 characters), 12-button keyboard, 3 LED indicators and a light inten-
sity sensor. Display and LED brightness is regulated. The unit is connected to the central
processing unit with a four-conductor cable that powers the identification unit and secures
data communication between the central processing unit and the identification unit.
The identification unit is constructed in the form of a plastic box intended for integration into
the desk at the engineer's station. The indication elements and the keyboard are located on
the front side. A 7-position terminal strip is located on the rear side. The identification unit
can be installed in any suitable manner based on the construction of the locomotive so long
as the indication components are visible and the keyboard is accessible.
OIxID1 displej
OIxID2 klávesnica
OIxID3 OK indikácia správnej činnosti indikačnej je
OIxID4 AR indikácia zaplneniaregistračného archí
v
OIxID5 ERR indikácia poruchy zariadenia
OIxID1 Display
OIxID2 Keyboard
OIxID3
OIxID4
OIxID5
Correct function indicator of identification unit
Full memory indicator of the juridical recorder unit
Equipment fault of system
OK
AR
ERR

278RM1 : 181112
11 / 25
Equipment Diagnostics
Diagnostics of the MIREL RM1 speed recorder is conducted at four levels
D1 Start-up self-diagnostic test of the equipment
D2 Continuous self-diagnostic checks
D3 Functional test
D4 Prophylactic check
The first two levels (D1 and D2) are conducted automatically by the equipment itself. If a
fault is detected, the operator is notified of such fact and the equipment is placed into safe
mode. If the discovered fault prevents subsequent activity of the speed recorder, actions are
taken to prevent subsequent operation. Operational repairs of the equipment (S1) must be
conducted in the event a fault is detected. Maintenance repairs (S2) must be conducted in
the event of a repeated fault.
The functional test (D3) of the equipment is conducted by staff trained by the operator. The
functional test checks the overall functionality of the equipment, meaning the functionality of
all indication elements and keyboards, the functionality of all input and output circuits and
cooperation with other equipment on the locomotive (including driving controls, impulse rota-
tion sensors, etc.). Operational repairs of the equipment (S1) must be conducted when a
fault is detected. Maintenance repairs (S2) must be conducted in the event of a repeated
fault.
Prophylactic check (D4) of the equipment is performed periodically by the manufacturer of
the speed recorder or by another entity or individual trained and authorized to conduct such
checks. In addition to performing the functional test, an in-depth control of the entire equip-
ment is conducted (measuring input filters, reading variable readouts from the speed re-
corder, checking input/output circuits and checking the devices that work in conjunction with
the speed recorder). This check is conducted in order to verify the complete functionality of
the equipment and for any wear and tear. Service repairs (S2) must be conducted if a fault is
detected.
Every person conducting diagnostics of the speed recorder must be instructed with regards
to occupational safety and must be verifiably trained to perform such activities with proof of
certification to perform the individual levels of equipment diagnostics.

278RM1 : 181112
12 / 25
D1 – Start-up self-diagnostic check of the equipment
Executed:
By the speed recorder automatically and without any intervention by the operator or mainte-
nance
Schedule:
Every time the MIREL RM1 speed recorder is powered on
Description:
The speed recorder is placed into operation when the locomotive's battery source is pow-
ered up. Every time the speed recorder is powered up, it conducts the D1 self-diagnostic
test, which checks the integrity of the equipment itself, correct configuration parameters and
the basic functionality of the equipment. The self-diagnostic test itself takes around 1 second
to complete. The D1 self-diagnostic test is executed automatically and no intervention on the
part of the operator is needed.
Tests conducted within the start-up self-diagnostic check:
Program integrity check – the equipment calculates the checksums in memory containing
the saved programs and compares them to the expected values. The equipment will display
the error messages E02, E08 or E09 if a memory error is detected. The equipment is not
functional during this test.
Configuration parameter integrity check – the equipment calculates the checksums in
memory containing the configuration parameters and compares them to the expected val-
ues. The equipment will display the error messages E33 or E08 if .a memory error is detect-
ed. The equipment is not functional during this test.
Completion protocol:
Not issued.
Resolving any discovered faults:
If any fault is discovered during the start-up self-diagnostic test, simply switch off the breaker
for the speed recorder for at least 1 second and then re-energize the equipment to re-
initialize the equipment. If the fault is displayed after re-initializing the equipment, the
fault is such that it prevents subsequent activity of the speed recorder. Operational
repairs (S1) are required.

278RM1 : 181112
13 / 25
D2 – Continuous self-diagnostic check of the equipment
Executed:
By the speed recorder automatically and without any intervention by the operator or mainte-
nance
Schedule:
Continuously when the speed recorder is operational
Description:
The speed recorder conducts continuous self-diagnostic checks using the two watchdog
circuits and conducts other diagnostic tests. If a serious fault in communicating with the indi-
cation or identification unit at the active station (the station at which the control switch is on)
is detected the speed recorder will prevent subsequent operation. The equipment can oper-
ate in a limited manner if the communication fault involves the indication and identification
units at the inactive station. The speed recorder requires operational repairs in such case.
Tests conducted during continuous self-diagnostic checks:
Watchdog test – the processor module in the central processing unit, the registration mod-
ule and each indication and identification unit is equipped with a pair of watchdog circuits.
One monitors the proper operation of the processor itself and the second monitors the oper-
ation of the processor in cooperation with the other circuits of the given equipment. The
watchdog circuits monitor the proper operation of the processors, correct execution of the
program, timer activity and the functionality of processor interruption systems. The watchdog
circuits operate with a time base of 16 ms and 100 ms. When a watchdog fault is detected,
the given functional block is re-initialized and an error message is generated for the entire
component. The error code for a fault involving the processor module of the central pro-
cessing unit is E01. The error code for a fault in the active indication unit is E08, while a fault
in the active identification unit is indicated as code E09.
Configuration parameter integrity check – the equipment calculates the checksums in
memory containing the configuration parameters and compares them to the expected val-
ues. The equipment will display the error messages E33 or E08 if a memory error is detect-
ed. The equipment is functional during this test.
Communication check between processor module of the central processing unit and
the registration module – the registration module transmits a message to start communi-
cation with the processor module of the central processing unit. If communication is not
started within 100 seconds the error code is E34. The equipment is functional during this
test.
Communication check between the central processing unit and the indication and
identification units – the processor module of the central processing unit transmits a SYNC
message to start communication with the indication and identification units. If communication
is not started at the active station within around 4 seconds, the error code that is displayed is
E04, E05, E06 or E07. The equipment is functional during this test.
Communication functionality test – each unit continuously monitors the functionality of
data communication on the SPI and RS485 links. If successful communication is not noted
on the communication lines for a period of longer than around 4 seconds and error code is
displayed. The equipment will indicate one of the following error codes: E04, E05, E06, E07,
E08, E09 or E34.

278RM1 : 181112
14 / 25
Date check in the registration module – the equipment tests the correctness of data from
the registration module and indicates an E40 error when a fault involving real time is discov-
ered.
Speed measurement test – speed measurements are completed using the four-channel
incremental rotation sensor. Instantaneous speed is calculated from measurement channels
1, 2, 3 and 4. The calculated speeds are compared and the two highest calculated speeds
are used by the system. If the difference between the calculated speeds is larger than 5
km.h
-1
for 3 second the equipment displays the E20 error code.
Actual direction of travel evaluation test – compliance with regards to the actual direction
of travel is also tested, the same as for speed measurements. If the evaluated directions do
not match for 3 seconds the equipment displays the E21 error code.
Incremental rotation sensor power test – the equipment uses a comparator to test the
power to the incremental rotation sensor. If the voltage exceeds the permitted range, the
equipment indicates the E22 error code.
Completion protocol:
Not issued.
Resolving any discovered faults:
If any fault is discovered during the start-up self-diagnostic test, simply switch off the breaker
for the speed recorder for at least 1 second and then re-energize the equipment to re-
initialize the equipment. If the fault is displayed after re-initializing the equipment, the
fault is such that prevents subsequent activity of the speed recorder. Operational re-
pairs (S1) are required.

278RM1 : 181112
15 / 25
D3 – Functional test
Executed:
By trained staff of the speed recorder operator
Schedule:
Regularly at 6-month intervals with a tolerance of ± 1 months. Execution of the prophylactic
check is a substitute for the functional test. The functional test must be executed at least 3
times in the 24-month cycle for the prophylactic check. The six-month term re-starts if an
unplanned functional test is executed.
Description:
The goal of the functional test is to ensure proper operation of all basic functions of the
speed recorder. The functional test is completed based on the methodology described in
the following document:
342RM1
depending on the requisite modifications based on the sys-
tem configuration.
Completion protocol:
The completion protocol for the functional test must contain the following details:
Date and time
Location
The serial numbers of all components of the speed recorder
The number of the locomotive on which the equipment is installed (if so installed)
The name and position of the person who conducted the test
The result of the functional test (no defects / with defects)
A description of all faults must be provided
The signature of the person who conducted the test
ES operating mode activation for basic configuration (RM1.0.XXXX):
In the identification operation mode, the acknowledgement button is held on ID and control
switch is operated.
The selection of the individual steps of the system functional test is possible via the Identifi-
cation Unit buttons. The next step of the functional test can be selected press the button 0,
the previous step press the ESC button. Perform the test step if necessary by pressing the
ENTER button.
ES IN operating mode activation for configuration with expanded
memory (RM1.1.XXXX):
The test operating mode is activated so far, as within 2s from power supply start the steering
control switch is switched ON and OFF.
The selection of the individual steps of the system functional test is possible via the Identifi-
cation Unit buttons. The next step of the functional test can be selected press the button 0,
the previous step press the ESC button. Perform the test step if necessary by pressing the
ENTER button. Switching between individual test steps of the indication unit occurs auto-
matically.
Resolving any discovered faults:
Operational repairs of the equipment (S1) must be conducted when a fault is detected.
Maintenance repairs (S2) must be conducted in the event of a repeated fault.

278RM1 : 181112
16 / 25
D4 – Prophylactic check
Executed:
Trained manufacturer staff, or another trained person for this purpose, provably authorized
by manufacturer.
Schedule:
If the previous D4 prophylactic check was performed in the Base Range, the following D4
prophylactic control is performed after 24 months with a tolerance of 2 months. If a previous
D4 prophylactic check was carried out in an Extended Range, the following prophylactic D4
check is performed on the main repair of vehicle. In specific cases, if the periodicity of the
major vehicle repairs exceeds 10 years, the prophylactic D4 check must be carried out at
the latest 120 months. D4 prophylactic control in the Extended Range can only be per-
formed for the RM1.1 registration speedometer version.
The first term of prophylactic check D4 begins with the date of the checkout, when the com-
ponents of system are removed from the manufacturer’s store. If the components of system
are not removed at the same time, the term D4 prophylactic check begins with the first one.
In the case of unplanned D4 prophylactic check, a new interval begins to run.
If the D4 prophylactic check is not performed as a whole within a one single service, but at
different times on the individual components of the system, including verification of system
compatibility with the locomotive, the counting of the new D4 prophylactic check interval
begins to run according to the D4 section that was performed first.
If the MIREL RM1 speed recorder is placed out of service for a period of longer than 12
months, the D4 prophylactic check must be completed in full before the equipment can be
placed back into service. The term "out of service" means that the speed recorder (or its
components) are not installed on any locomotive or are installed but no power has been
connected to the equipment.
Place of performance:
The D4 prophylactic check of the MIREL RM1 system can be done in one of the following
ways:
on the locomotive
prophylactic check of the equipment will be performed in the manufacturer's service
center. Prophylactic check of system compatibility with the locomotive will be per-
formed on the vehicle. Prophylactic check D4 does not include assembly or disassem-
bly of equipment.
Description:
The execution of the prophylactic check is subject to the provisions of a specific internal pro-
cedure issued by the manufacturer for in-depth checks of the equipment. The methodology
for performing the D4 prophylactic check is adapted to the different installation conditions for
individual classes of locomotives on which the MIREL RM1 speed recorder has been in-
stalled. Any future installations with conditions and differences that have an impact on the
scope and procedure for executing the D4 prophylactic check shall be incorporated into the
methodology used for conducting the D4 prophylactic check.
The prophylactic check is only conducted in full. The D4 prophylactic check involves the
complete verification of the equipment in terms of metrology. All of the components that are
affected by the accuracy of speed measurements are checked. The prophylactic check does
not include verification of the proper settings for the diameter of the measured axle.

278RM1 : 181112
17 / 25
Completion protocol:
The completion protocol for the prophylactic test must contain the following details:
Date and time
Location
Serial number of the speed recorder
The number of the locomotive on which the equipment is installed
The name and position of the person who conducted the test
The results of the prophylactic check
A description of all faults must be provided
The signature of the person who conducted the test
Resolving any discovered faults:
Operational repairs of the equipment (S1) must be conducted when a fault is detected.
Maintenance repairs (S2) must be conducted in the event of a repeated fault.

278RM1 : 181112
18 / 25
Equipment Maintenance
All components of the speed recorder are maintenance-free. No component needs to be
replaced, tuned, or otherwise configured at any time.
MIREL RM1 speed recorder maintenance involves two levels
S1 Operational repairs
S2 Maintenance repairs
Operational repairs (S1) are conducted by trained operator staff. An inspection is performed
if any speed recorder defects are detected by any of the diagnostic checks (D1 to D4) or in
connection with a defect indicated during operation of the speed recorder. The goal of oper-
ational maintenance is to remedy defects in cabling, power connections, connections to co-
operating equipment on the locomotive, etc. During the maintenance inspection no interven-
tion inside the central processing unit, indication unit or identification unit takes place.
Maintenance repairs (S2) must be conducted in the event of a repeated fault.
Maintenance repairs (S2) are performed by the manufacturer or an individual or entity
trained and authorized by the manufacturer. Maintenance repairs are conducted if a defect
cannot be resolved by performing operational repairs (S1). Maintenance repairs are always
conducted on the basis of replacement (replacing the central processing unit or identification
unit and subsequent repair by the manufacturer). The goal of the maintenance repairs is to
remedy defects in the central processing unit of the speed recorder and in the indication and
identification units.
Every person conducting maintenance of the MIREL RM1 speed recorder must be instruct-
ed with regards to occupational safety and must be verifiably trained to perform such activi-
ties with proof of certification to perform the individual levels of equipment maintenance.

278RM1 : 181112
19 / 25
S1 – Operational repairs
Executed:
By trained staff of the speed recorder operator
Schedule:
If any speed recorder defects are detected by any of the diagnostic checks (D1 to D4) or in
connection with a defect indicated during operation of the speed recorder.
Description:
The goal of operational repairs is to remedy defects in:
Power to the central processing unit
Power to the indication and identification units
Cabling
Connection of the incremental rotation sensor
Connectors
Connections of input and output circuits
Mechanical anchors
The portions of the D3 functional test that can be of assistance in more precisely determin-
ing the exact defects involved should be performed before proceeding to S1 operational
repairs. Defects involving the central processing unit of the central processing unit, the indi-
cation unit or the identification unit are resolved by replacing the specific component. Staff
must have approved technical documentation for the equipment when conducting operation-
al repairs and must follow the provisions of this technical documentation and the mainte-
nance module during such work.
S2 maintenance repairs must be conducted on the speed recorder if the defects cannot be
resolved with S1 operational repairs. A functional test of the equipment must be completed if
the S1 operational repairs remedy the defects.
Completion protocol:
The completion protocol for the maintenance inspection must contain the following details:
Date and time
Location
Serial number of the speed recorder
The number of the locomotive on which the equipment is installed (if so installed)
The name and position of the person who conducted the operational repairs
Description of the defects that have been resolved and their causes (if known)
Description of the defects that could not be resolved by the operational repairs
The serial numbers of the removed and installed components
The signature of the person who conducted the repairs

278RM1 : 181112
20 / 25
S2 – Maintenance repairs
Executed:
Trained manufacturer staff
Schedule:
If speed recorder defects occur that cannot be remedied with operational repairs
Description:
The goal of the maintenance inspection is to remedy defects in:
The central processing unit of the speed recorder
Indication and identification units
Cooperation between the speed recorder and peripheral equipment and other compo-
nents of the locomotive that could not be remedied with the S1 operational repairs
The D3 functional test must be completed after the maintenance repairs and a protocol on
the completion of such test must be issued.
Completion protocol:
The completion protocol for the maintenance repairs must contain the following details:
Date and time
Location
Serial number of the speed recorder
The serial number of locomotive on which the equipment is installed (if so installed)
The name and position of the person who conducted the maintenance repairs
Description of the defects that have been resolved and their causes (if known)
The serial numbers of removed and installed components if any components are re-
placed
The signature of the person who conducted the repairs
Table of contents
Popular Measuring Instrument manuals by other brands

IFM Electronic
IFM Electronic ecomot200 FR-2 operating instructions
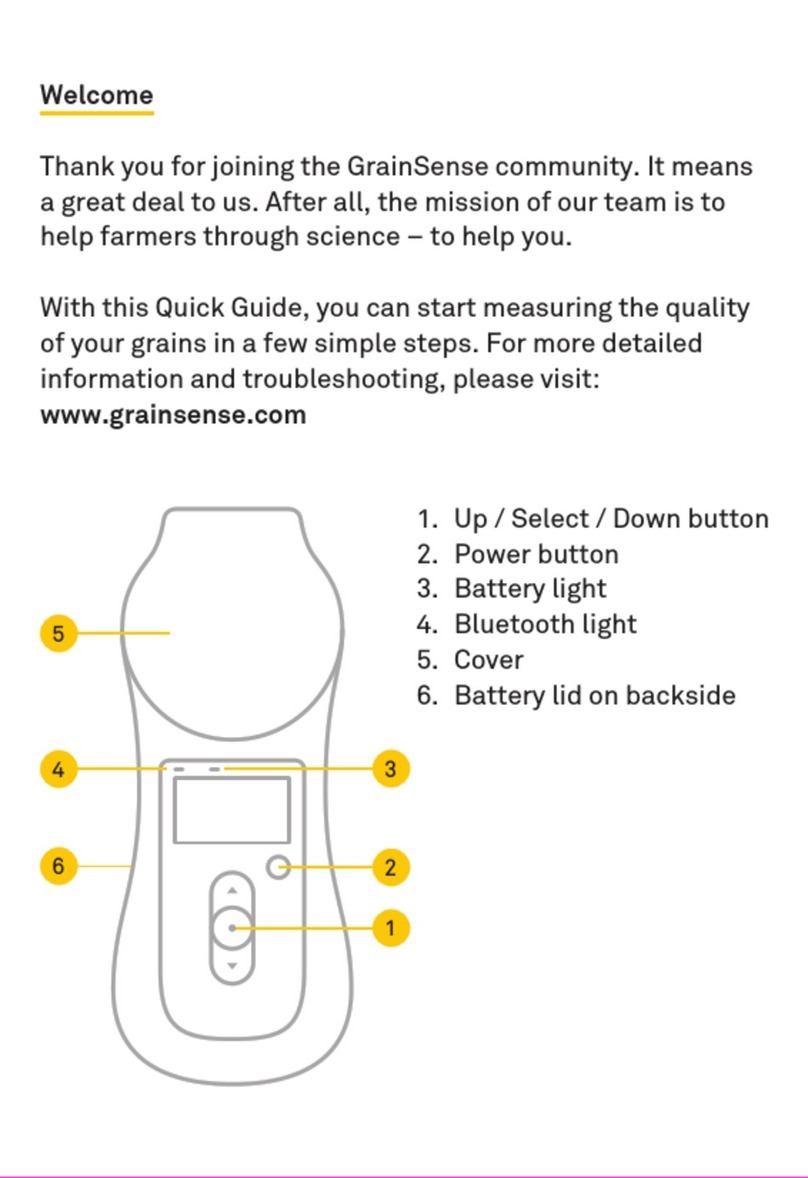
GrainSense
GrainSense GS-ANLZR-A-2 quick start guide
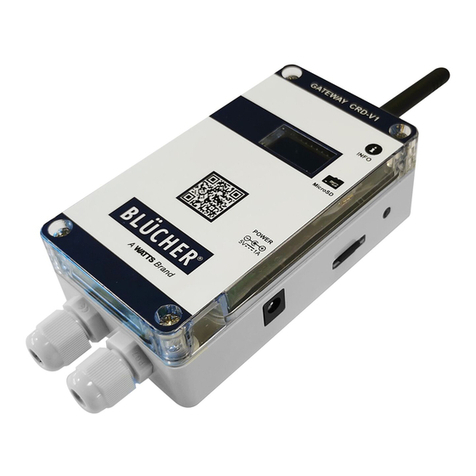
Watts
Watts BLUCHER Connected Roof User manual & installation guide

Extech Instruments
Extech Instruments 461995 user manual

SICK
SICK GM35 operating instructions

Seres OL
Seres OL TOPAZ Total Alkalinity Operator's manual